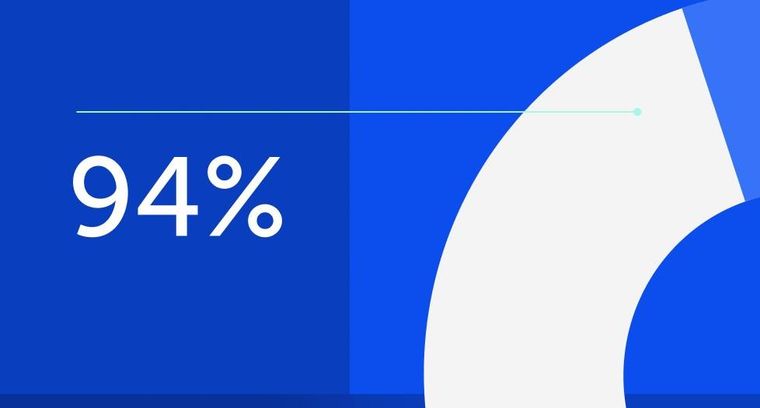
94% of researchers rate our articles as excellent or good
Learn more about the work of our research integrity team to safeguard the quality of each article we publish.
Find out more
ORIGINAL RESEARCH article
Front. Mater., 06 June 2023
Sec. Structural Materials
Volume 10 - 2023 | https://doi.org/10.3389/fmats.2023.1164693
This article is part of the Research TopicMultiscale Characterization of Advanced Pavement MaterialsView all 10 articles
Redundant wind turbine blades (WTBs) retired from wind power facilities produce substantial waste annually and induce challenging environmental problems. As the most widely used materials for high-grade pavement construction, asphalt mixtures must have excellent high- and low-temperature performance, as well as water damage resistance, since pavement is subjected to complex loading, temperature, and humidity changes. This study proposed an asphalt mixture with the addition of two types of recycled WTB (rWTB): rWTB powders of granular sizes below 0.075 mm and rWTB fibers in the size range of 0.075–9.5 mm. First, the thermogravimetric analysis results indicated the accepted thermal stability of rWTB material for the requirement of compaction, paving, and service condition of asphalt mixtures. Second, the properties of the asphalt mixtures modified by using (i) rWTB powder (5 wt%, 10 wt%, and 15 wt% in fine filler), (ii) rWTB fiber (0.1 wt%, 0.2 wt% and 0.3 wt% in fine aggregate), and (iii) both rWTB powder and fiber were investigated by wheel tracking tests at 60°C, three-point bending tests at −10°C, and Marshall immersion tests. The experimental results showed that the rWTB asphalt mixtures could improve the overall road performance of asphalt mixtures, and that an optimal pavement performance could be obtained by the synergistic addition of rWTB powder and fiber. In addition, it was indicated that the improving mechanism of the rWTB material on the asphalt mixture was mainly attributed to its good compatibility with the asphalt binder, allowing the rWTB to strengthen asphalt mortar and improve the high- and low-temperature performance of the asphalt mixture.
Wind power is the most important clean energy. The installed capacity of wind energy is dramatically increased with the rising demand of clean energy, with which the number and length of wind turbine blades (WTBs) are both substantially raised. However, the designed service life of a wind turbine is 20–25 years, leading to a vast number of decommissioned products each year (Jensen and Skelton, 2018). The WTB waste is estimated to reach more than 2 million tons by 2050 (Liu and Barlow, 2017). The majority of raw materials for wind turbine blades are made of glass fiber reinforced plastics (GFRPs) that consisted of 60%–70% of fiber and 30%–40% of cross-linked thermoset polymer formed in an irreversible process, increasing the reclaiming difficulty (Morales et al., 2020). Currently, the most mature recycle technique is mechanical crushing, through which the size of end-of-life WTB articles is decreased progressively, and the recyclates in the various shapes are obtained, mostly in the form of fiber and powder (Majewski et al., 2022). With the mechanical crushing, the practical reuse of recycled WTB (rWTB) or the recycled GFRP (rGFRP) portion of rWTB has become another major focus of research. The mechanically recycled GFRP has been used as fiber reinforcement or fillers in the production of artificial wood (Demura et al., 1995), block/sheet molded materials BMC/SMC (Pickering, 2006; Palmer et al., 2009), wood–plastic board (Conroy et al., 2006), and rubber pavement blocks (Itoh and Kaneko, 2002). To improve the value and consumption of reuse, scholars further explored the application of rGFRP in composites (Mamanpush et al., 2018), concrete (Asokan et al., 2010), and asphalt mixture (Qiaoet al., 2020).
The reuse of rWTB is more complex, due to the highly composited properties of WTB containing various materials, including polymer foams, balsa wood, and metals (Jensen and Skelton, 2018). Beauson et al. (2016) applied the shredded composite (SC) from WTBs in new thermoset composites and found that chemical treatments of SC were necessary for improving its adhesion with the resin matrix (Beauson et al., 2016). The glass fiber below 0.4 mm length was reclaimed from the waste wind turbine blades and pelletized with polylactic acid (PLA) to produce recycled glass fiber reinforced filament (RGFRF) for 3D printing. The Young’s modulus of the 3D-printed RGFRF was 8% higher than that of pure PLA (Rahimizadeh et al., 2019). The application of rWTB or rGFRP in concrete is the mostly studied topic, which focused on the influences of the size, contents, and shapes on the workability and mechanical properties of concrete (Asokan et al., 2009; García et al., 2014; Mastali et al., 2016; Zhou et al., 2021). The rGFRP fiber and powder are separately used in concrete as fiber reinforcement and filler, respectively. In most research, the mechanical strength of concrete can be improved by the addition of recycled fiber, especially when the fibers are properly classified and appropriate additives are added to modify the workability (Rodin et al., 2018; Zhou et al., 2021). However, chemical treatment is necessary to improve the alkaline resistance of the recycled GFRF fiber for longer durability of the reinforced concrete (Kimm et al., 2020). On the other hand, the addition of rGFRP powder with proper treatment at appropriate content could slightly increase the compressive and flexural strengths of concrete, while the problem of excessive fresh-state expansion or drying shrinkage is still concerned due to the ultrafine particle size, lightweight nature, and high content of metallic oxide residues (Asokan et al., 2010; Tittarelli and Shah, 2013; Farinha et al., 2019).
Asphalt mixture is the most important engineering material for high-grade pavement, which faces the challenge of various and frequently occurring early diseases, e.g., rutting, cracks, and water damage, seriously limiting the service life of the pavement structure (Gu et al., 2015; Wang et al., 2016). To solve these problems, the high- and low-temperature performance of asphalt mixture is improved by adding polymer modifiers to the binder, such as SBS, SBR, and EVA (Lu et al., 2003; Yildirim, 2007; Sengoz and Isikyakar, 2008) and adding various reinforcements to asphalt mixture, including basalt fiber, glass fiber, waste tires, and waste glass powder materials (Cao, 2007; Abtahi et al., 2010). It was found that adding fiber with appropriate size can effectively improve the rheological properties of asphalt mixture at different temperatures and the flexural strength under medium- and low-temperature conditions (Wu et al., 2007; Wu et al., 2008; Morea and Zerbino, 2018). In addition, the mesoscopic composition of the aggregate skeleton and the geometric shape of the particles will affect the damage development and deformation behavior of asphalt material (Wang et al., 2019; Li et al., 2023). The mining and production costs of gravel aggregates and mineral fillers, with huge consumption in road engineering, are continuously increasing due to the impact of environmental protection factors. These years, many scholars have begun to focus on the use of recycled materials to improve the performance of mixtures from multiple scales. Yang et al. recycled WTB chips from the components of airplane cabins and investigated the effects of crushed chips on the performance of bitumen. Since the bridging function and specific pull-out behavior of the WTB chips, the stiffness, rutting resistance, low-temperature cracking resistance, and water resistances of bitumen were all increased, with the optimum diameter of 0.5–0.71 mm, length of 10–12 mm, and mass content of 5% (Qiaoet al., 2020). Followed by this study, Jin et al. processed the recycled WTB into powders to partially replace limestone filler in asphalt mortars. The recycled WTB powder improved the medium-to high-temperature performance and anti-aging property of the asphalt mortars, while decreased the resistance to low-temperature cracking (Lin et al., 2022). However, the synergistic utilization of recycled fiber and powder for asphalt mixture to against rutting and cracking has never been explored.
In this study, the recycled WTB (rWTB) powder and fiber were added to partially replace the fine filler (<0.075 mm) in asphalt mortar and fine aggregates (0.075–9.5 mm) in the asphalt mixture. The effect of the content of the rWTB powder (5 wt%, 10 wt%, and 15 wt%) and that of rWTB fiber (0.1 wt%, 0.2 wt%, and 0.3 wt%) on the high-temperature rutting, low-temperature cracking resistance, and water stability was evaluated with wheel tracking tests (WTTs) at 60°C, three-point bending tests at −10°C, and Marshall immersion tests, respectively. In addition, the rWTB powder and fiber were added to synergistically modify the viscoelastic properties of asphalt mortar and the macro-performances of the asphalt mixture. Furthermore, the microstructure of the asphalt mixture was characterized to investigate the reinforcing mechanism of the rWTB fiber. The findings in this study were beneficial for developing new techniques to reuse the WTB wastes and sustainable reinforcing materials for extending the service life of the asphalt pavement.
The rWTB materials were obtained by cutting, crushing, and grinding the waste WTB, as shown in Figures 1A, B. Based on sieve analysis (Figure 1E), the rWTB materials were classified into powder (remained on 0.075-mm mesh) and fiber (passed 0.075-mm mesh). The rWTB powder mainly consisted of small resin particles and short glass fiber, and the rWTB fiber consisted of rod-like glass fiber bundle partially wrapped with epoxy resin and a small amount of wood fiber, as shown in Figure 1E. The inorganic oxide composition of the rWTB was determined via X-ray florescence (XRF), as tabulated in Table 1, which mainly consisted of SiO2 and CaO, since the GFRP portion of WTB was made of glass fiber, resin (i.e., epoxy resin and butyral resin), and auxiliary materials (i.e., calcium carbonate and talcum powder (Seydibeyoglu et al., 2017)).
FIGURE 1. Images of (A) decommissioned turbine blade, (B) cut WTB panel, (C) crushing equipment, (D) vibration sieves, and (E) particle size distribution of rWTB.
SBS-modified asphalt with a penetration grade of 70 was adopted in this study. Its basic performance indices, including penetration, ductility, and softening point, obtained through the ASTM standards are listed in Table2.
In this study, the rWTB fiber and powder were engaged in the design of asphalt mixture. Table 3 shows the aggregate gradation of all the mixtures. The mass proportion of the asphalt binder to the mixture was 5.3%, obtained according to the Marshall method (ASTM D6927).
Three asphalt mixture experimental groups (GXP, GXF, and GXFP) were prepared in this study to verify the feasibility of incorporating rWTB materials in asphalt mixtures and investigate their impact on pavement performance under different content ratios. In the mixture design, the mineral filler (<0.075 mm) was partially replaced by the rWTB powder with the mass ratios of 5%, 10%, and 15%, and the aggregate under 9.5 mm was replaced with the rWTB fiber in three levels of 0.1%, 0.2%, and 0.3%. As illustrated in Table 4, the group labels of GXP and GXF represent the asphalt mixture containing rWTB powder and rWTB fiber, respectively, and the third group of GXFP indicates that both powder and fiber were used.
Three types of samples with different dimensions were prepared with the asphalt mixtures, as listed in Table 4, for WTT (300 mm × 300 mm × 50 mm panel), three-point bending tests (250 mm × 30 mm × 35 mm beam), and Marshall immersion tests (Φ101.6 × 63.5 mm cylinders). The asphalt binder was placed in the temperature-controlled chamber at 165°C for at least 2 h, and the fine powder, fine aggregates, and coarse aggregates were heated in an oven at 180°C for at least 4 h before sample preparation. The asphalt binder, fine filler, and aggregates were mixed at 170°C according to the mix design shown in Tables 3, 4. The 300 mm × 300 mm × 50 mm panels were prepared by the rolling method using an asphalt mixture rut sample-forming machine. The 250 mm × 30 mm × 35 mm beams were cut from the rut panels, and the Φ101.6 × 63.5 mm cylinders were prepared by using the compacting method.
Laboratory tests were conducted to characterize the physicochemical properties of rWTB and determine the resistance of the rWTB-modified asphalt mixture to high-temperature rutting, low-temperature cracking, and water stability.
The micromorphology of rWTB powder, fibers, and the corresponding asphalt mortar was imaged using an environmental scanning electron microscope, Quanta 450 FEG, to explore the reinforcing mechanism of the rWTB fiber and powder.
Since the compaction, paving, and service conditions of asphalt mixtures require high-temperature conditions, a thermogravimetric (TG) analysis was performed using a simultaneous thermal analyzer, TA SDT650 DSC/TGA system, to further investigate the thermal stability of rWTB materials and the feasibility of incorporating rWTB materials in asphalt mixtures, through the obtained TG curve, differential thermogravimetric (DTG) curve, and differential scanning calorimetry (DSC) curve. The rWTB particle sample was exposed to N2, with the testing temperature range of 0–1,000°C and at the heating rate of 20°C/min.
The resistance to high-temperature rutting of rWTB asphalt mixtures was investigated by the WTT with the dynamic stability (DS) value under 60°C as an indicator of mixture properties. A SYD-0719A Wheel Rutting Tester was used in this test, and more than three specimens for each mixture group were prepared before testing. The WTT specimens were subjected to repeated axle loads of 0.7 MPa at a rate of 42 passes/min, as shown in Figures 2A, B, while the DS was calculated according to Eq. 1 (JTG E20-2011):
where V is the repeated loading rate of 42 passes/min; t1 and t2 are the two time nodes during loading, which are 45 min and 60 min, respectively; and d1 and d2 are the vertical rutting deformation values corresponding to t1 and t2, respectively, in mm.
FIGURE 2. Images of (A) the WTT sample preparation process, (B) WTT sample panel, (C) beam sample, and (D) three-point bending tests of asphalt mixtures.
The mean value was obtained through three parallel tests conducted for each asphalt mixture group to evaluate their resistance to high-temperature rutting.
The resistance of asphalt mixtures to low-temperature cracking was investigated by three-point bending tests.
Five beam specimens for each mixture group were prepared in this test. The beam specimens were loaded using a universal testing machine (IPC UTM-100) at a temperature of −10°C. The loading process is illustrated in Figures 2C, D. The load PB (N) and the corresponding displacements d were recorded during the loading process at a speed of 50 mm/min until the beam cracked. The bending tensile strength RB (MPa) and the failure strain εB (10−6 mm/mm) of the samples were calculated according to Eqs 2, 3:
where b and h are, respectively, the width and height of the mid-span sections of the beams, in mm; and L is the span of the beam specimens, in mm.
All the beam specimens were placed in the environmental chamber of the UTM at a temperature of −10°C for over 5 h prior to testing. The mean value was obtained based on the results of five parallel tests conducted for each asphalt mixture group to determine their resistance to low-temperature cracking.
The Marshall immersion test was conducted to measure the resistance of asphalt mixtures to moisture damage. A WSY-101 Marshall Stability Tester was used in this test, and more than three specimens for each mixture group were prepared before testing. The Marshall stability results obtained after 48 h of immersion of the samples in water, which was conducted according to the standard Marshall test (ASTM D6927). The residual stability (RS) for each specimen was calculated according to Eq. 4:
where MS1 is the Marshall stability value after 48 h of immersion in water; and MS is the Marshall stability value obtained using the standard Marshall test. Three sets of parallel tests were conducted for each mixture group, and the mean value was calculated for analysis.
The microstructure images of rWTB powder are shown in Figure 3. The rWTB powder mainly consisted of ground resin particles and short glass fibers, with the particles presenting an angular and irregular surface and relatively uniform size and morphology. The rWTB fiber mixture consisted of a high proportion of glass fibers and a smaller proportion of resin particles. It contained lots of rod-like glass fibers with different sizes and directions in a spatial arrangement and fiber clusters wrapped or bonded together by resin.
FIGURE 3. SEM images of (A) rWTB powder, (B) rWTB fiber, and (C) ×2000 magnification of the surface morphology of rWTB fibers.
The heat stability of the rWTB particles was assessed with thermogravimetric analysis using TG, DTG, and DSC curves to ensure that rWTB would not be decomposed under the high-temperature condition during compaction and paving.
The TG curve can characterize the mass loss of the rWTB specimen with the increase of temperature, and the DTG curve represents the corresponding speed rate of mass loss. As shown in Figure 4, according to the TG and DTG curves of the rWTB powder, a significant weight loss of the sample occurred in the temperature range from 300°C to 450°C, peaking at approximately 350°C, which was due to the pyrolysis of epoxy resin. In addition, there was also an obvious mass loss at approximately 500–600°C, which was due to the oxidation of pyrolysis residual carbon in the air. Moreover, combined with the DSC curve, it can be found that the two peaks in the DTG curve presented an exothermic process, and the more severe one appeared at approximately 600°C, indicating the large energy absorbed by the rWTB for the decomposition of epoxy resin.
On the other hand, the weight loss of rWTB below 200°C was small and basically reflected in the TG curve with a level or near-plateau trend, illustrating the accepted stability for the construction of an asphalt pavement. Consistently, the energy change in the temperature range of 0–200°C was negligible, as shown in the DSC curve, illustrating almost no matter was decomposed below 200°C.
The dynamic stability values of the 10 rWTB asphalt mixtures are shown in Figure 5 to comprehensively compare the impact of adding rWTB powder, fiber, and a mixture of both on the resistance to high-temperature rutting.
FIGURE 5. Dynamic stability of mixtures with (A) rWTB powder, (B) rWTB fiber, and (C) the combination of both rWTB powder and fiber.
As shown in Figure 5A, the GXP samples with the sole addition of the rWTB powder (GXP-5%, GXP-10%, and GXP-15%) attained higher dynamic stability values than those of the GX specimens. The DS value rose remarkably in the GXP-5% and GXP-10% samples by 13.8% and 22.4%, respectively, while the DS value in the GXP-15% sample rose only slightly by 6.9%. This indicated that the partial replacement of mineral powder with rWTB powder improved the resistance to high-temperature rutting of asphalt mixtures, with the optimal ratio near 10%.
The dynamic stability values of the GXF samples with the sole addition of rWTB fiber also significantly increased compared to those of the GX samples. Unlike the findings of the GXP samples, the high-temperature rutting resistance of the GXF samples was found to rise progressively as fiber was added. In particular, the DS value of GXF-0.1% was close to that of the GX sample, while the DS values of the GXF-0.2% and GXF-0.3% mixtures increased by 17.2% and 54.4%, respectively, compared to those of the GX sample. This indicated that the addition of rWTB fiber to aggregates ranging from 0.075 mm to 9.5 mm can enhance the resistance of asphalt mixtures to high-temperature rutting.
The DS value of the GXFP samples gradually rose as rWTB powder and fiber were synergistically added, with the GXFP-0.3% mixture achieving the highest increasing rate of 44.5%. Compared to the results of the GXF samples with the sole addition of fiber, it was indicated that the DS values of the asphalt mixtures with the addition of 0.1% and 0.2% fiber of a size range of 0.075–9.5 mm were further improved with the addition of rWTB powder. This elucidated that the asphalt mixtures with the synergistic addition of rWTB powder and fiber, which modified and improved the materials in multiple scales, had the most significant enhancement of performance under high-temperature conditions.
The flexural strength and ultimate strain of the asphalt mixtures with different contents of rWTB fiber and powder under low-temperature conditions were compared as shown in Figures 6A–C. Compared to that of the GX sample, as shown in Figure 6A, the flexural strength of the GXP-5% and GXP-10% samples did not increase significantly. In contrast, the flexural strength of the GXP-15% specimen rose by 20% compared to that of the GX sample as more rWTB powder was added. On the other hand, the flexural strength of the asphalt mixtures did not improve with the addition of rWTB fiber in the size range of 0.075–9.5 mm, and the flexural strength of GXF-0.3% diminished as more fiber was added compared to that of the GX sample. In addition, a slight increase in the flexural strength was observed in the GXFP samples with the synergistic addition of rWTB powder and fiber, which were approximately 9.5%, 7.1%, and 4.8% for GXFP-0.1%, GXFP-0.2%, and GXFP-0.3%, respectively. In summary, the test results indicated that adding rWTB powder with particles below 0.075 mm in size could increase the flexural strength of the asphalt mixture, while the excessive addition of rWTB fiber in the size range of 0.075–9.5 mm had adverse influence on the flexural strength.
FIGURE 6. Flexural strength and ultimate strain of the asphalt mixture with the addition of (A) and (B) rWTB powder, (C) and (D) rWTB fiber, and (E) and (F) the combination of both rWTB powder and fiber.
The ultimate strain of asphalt mixtures had also been selected as an important indicator in this study to measure the resistance of the materials to low-temperature cracking. As shown in Figures 6B, D, F, the ultimate strain of GXP-5%, GXP-10%, and GXP-15% rose by approximately 10% compared to that of the GX sample, with no significant fluctuation when more powder was added. For the rWTB fiber mixtures GXF-0.1%, GXF-0.2%, and GXF-0.3%, the ultimate strain increased with the addition of rWTB fiber in the size range of 0.075–9.5 mm. In particular, the ultimate strain of GXF-0.3% mixture increased by 28.2% compared to that of GX, indicating that adding a certain amount of rWTB fiber to the asphalt mixture can enhance the resistance to cracking by a higher strain tolerance. Meanwhile, the ultimate strain of the asphalt mixtures with synergistic addition of powder and fiber, i.e., GXFP-0.1%, GXFP-0.2%, and GXFP-0.3%, was further improved, and the ultimate strain was increased with the increase in fiber content, presenting the result that GXFP-0.3% showed the highest increase of 34.2% compared to GX.
In conclusion, the addition of rWTB powder and fiber in corresponding increments was found to improve the performance of asphalt mixtures under low-temperature conditions, according to the results of the flexural strength and ultimate strain results. Specifically, the addition of rWTB powder could impact the asphalt mortar and the binding between the mortar and aggregates and could further improve the flexural strength of asphalt mixtures, which depended on the added proportion. In addition, adding rWTB fiber of a larger grade range could improve the capacity of asphalt mixtures to withstand a larger deformation by its strengthening effect of the rod-like structure, which enhanced the stability of the materials. Moreover, the synergistic addition of rWTB powder and fiber to the mixtures had the most significant improvement of the performance of the asphalt mixture.
Combined with the results of the high-temperature rutting test, it can be found that the influence of the adding amount of rWTB powder or fiber on the road performance at different temperatures was consistent. This result indicated that both rWTB powder and fiber effectively strengthened the overall structure of the asphalt mixture on the mesoscopic scale, and this reinforcement can improve the high-temperature and low-temperature performance of the asphalt mixture at the same time, which was the critical precondition to having a longer service life of pavement structures.
The water stability of asphalt mixtures is one of the key indexes for measuring pavement performance. Figures 7A–C present the test results of the Marshall stability (MS), Marshall immersion stability (MS1), and the residual stability (RS) of the GXP, GXF, and GXFP sample groups.
FIGURE 7. Marshall stability and residual stability of the asphalt mixtures with the addition of (A) rWTB powder, (B) rWTB fiber, and (C) the combination of both rWTB powder and fiber.
The Marshall stability MS of the three rWTB powder mixtures (GXP-5%, GXP-10%, and GXP-15%) was decreased compared with that of the GX sample based on the standard Marshall test. Among the mixtures of the GXP group, the MS value of GXP-10% was the highest and attained a similar value to that of the GX sample. In addition, the RS values of the GXP samples after immersion in water for 48 h were all approximately 90% of the GX sample, and the RS value of GXP-10% was the highest (94.1%). To summarize, adding rWTB powder did not significantly reduce the water stability of the asphalt mixture.
In contrast, the test results of rWTB fiber mixtures GXF-0.1%, GXF-0.2%, and GXF-0.3% differed greatly from those of the GXP group, as shown in Figure 7B. The MS value of GXF-0.2% and GXF-0.3% mixtures increased by nearly 10% compared to that of the GX sample, while the RS values of the two mixtures decreased significantly as more rWTB fiber was added after the immersion in water for 48 h. Although the GXF-0.3% mixture maintained the highest MS value, its RS value became the lowest (70.3%) after water immersion. In addition, the MS value of the GXFP sample group GXFP-0.1%, GXFP-0.2%, and GXFP-0.3% presented in Figure 7C was similar to that of the GX sample and rose with the increase in the addition of fiber. On the other hand, the MS1 values of the three GXFP samples were also close but slightly lower than those of the GX sample and the GXFP group with the highest fiber content (0.3%) obtained the lowest RS value (80.2%), which presented a lower reduction to the results of the GXF sample group.
The experimental results comprehensively showed that no distinctive loss of the RS value or rise of the MS value was identified in asphalt mixtures with the addition of rWTB powder. In contrast, the addition of rWTB fiber effectively increased the MS value, while significantly reduced the RS value after water immersion. This indicated that the addition of rWTB fiber in the size range of 0.075–9.5 mm could reduce the water stability of the mixture, and that the synergistic addition of fiber and powder could decrease the loss of water stability.
In order to further investigate the modification mechanism of the rWTB asphalt mixtures from the test results of high-temperature rutting, low-temperature cracking, and water stability, the microscopic combination mode of rWTB and asphalt binder on the microscopic scale was characterized by SEM. The micromorphology of the cross sections of asphalt mixtures with 0.3% rWTB was imaged by SEM at 500 μm, 100 μm, and 30 μm, as shown in Figure 8A–C, respectively. It was revealed that the rWTB fiber is fully wrapped in a cluster by the asphalt mortar. No obvious breaks in the fiber were found at the cracks of the mixture, indicating that damage to fiber was mainly resulted from peeling under stress, which affected the strain behavior of fiber in the asphalt mixtures.
FIGURE 8. Microstructure of the asphalt mortar with rWTB fiber at magnifications of (A) 500 μm, (B) 100 μm, and (C) 30 μm.
As illustrated in Figure 8B, a complete interface and tight bond between the fiber and mortar was found, illustrating that the fiber could transfer the load and disperse the stress over the asphalt mixture by bridging the asphalt mixture, as well as improve its strength and resistance to deformation under low-temperature conditions. In Figure 8C, the asphalt binder has good compatibility with the resin, which can improve the dispersity of the rWTB fiber in the asphalt mortar and the formation of a uniform system between asphalt mortar and rWTB fiber. This improved the viscoelasticity of the modified asphalt mortar, thus enhancing the resistance to high-temperature rutting of asphalt mixtures.
To summarize, the performance test results of asphalt mixtures and microscopic characterization of rWTB powder and fiber elucidated that the good compatibility existed between rWTB materials and asphalt binder and that utilizing this advantage could effectively enlarge the specific surface area of fine fillers and small size aggregates within the mixture. As a result, the high stiffness of rWTB fiber can effectively improve the high-temperature rutting performance and ultimate flexural strain of asphalt mixtures through the bridging effect. However, the utilization of fiber was also found to potentially decrease the flexural strength and water stability of asphalt mixtures because the fibers with different particle sizes were distributed unevenly and displayed a spatial rod stacking tendency. It indicated that the amount and particle size range of the rWTB fiber should be considered when designing asphalt mixtures and that optimal material properties could be obtained by the synergistic incorporation of powder and fiber.
This study explored the feasibility of introducing rWTB material into the design of the asphalt mixture and investigated the performance of high-temperature rutting, low-temperature cracking, and water stability of the mixtures with different proportions of rWTB powder and fiber based on laboratorial experiments. The following conclusions were obtained:
a. The significant mass loss of rWTB particles occurred at approximately 350°C and 600°C in the thermogravimetric test and presented a high thermal stability below 200°C, including that it could be used in the process of asphalt mixture compaction, paving, and service condition.
b. The partial replacement of mineral powder with rWTB powder improved the resistance of asphalt mixtures to rutting deformation with the optimal ratio of approximately 10%, and the addition of rWTB fiber can also improve the high-temperature performance as more fiber was added.
c. rWTB powder could enhance the flexural strength of the asphalt mixture under low temperature conditions, while rWTB fiber could increase the ultimate strain of asphalt mixtures based on three-point bending tests.
d. The water stability of the asphalt mixture was not significantly affected by the addition of the rWTB powder, while the MS of rWTB fiber mixtures was increased obviously and had a lower RS after water immersion.
e. The synergistic addition of rWTB powder and fiber can further improve the performance of asphalt mixtures. The presence of rWTB particles in different scales modified the microstructure of the asphalt mortar and improved the strength and deforming properties of the mixture (ASTM, 2006a, ASTM, 2006b, ASTM, 2006c, ASTM, 2007, Ministry of Transport, 2011).
The original contributions presented in the study are included in the article/Supplementary Material; further inquiries can be directed to the corresponding author.
Conceptualization, XL and HW; methodology, TL and BW; formal analysis, JZ; investigation, BW and JZ; resources, HW; data curation, TL; writing—original draft preparation, BW and TL; writing—review and editing, TL and XL. All authors contributed to the article and approved the submitted version.
This research was funded by the Central Public-interest Scientific Institution Basal Research Fund (2020-9074) and the Scientific and Technological Innovation Special Fund of Research Institute of Highway Ministry of Transport (2019-I111 and 2020-C101).
The authors declare that the research was conducted in the absence of any commercial or financial relationships that could be construed as a potential conflict of interest.
All claims expressed in this article are solely those of the authors and do not necessarily represent those of their affiliated organizations, or those of the publisher, the editors, and the reviewers. Any product that may be evaluated in this article, or claim that may be made by its manufacturer, is not guaranteed or endorsed by the publisher.
Abtahi, S. M., Sheikhzadeh, M., and Hejazi, S. M. (2010). Fiber-reinforced asphalt-concrete–a review. Constr. Build. Mater. 24 (6), 871–877. doi:10.1016/j.conbuildmat.2009.11.009
Asokan, P., Osmani, M., and Price, A. D. (2009). Assessing the recycling potential of glass fibre reinforced plastic waste in concrete and cement composites. J. Clean. Prod. 17 (9), 821–829. doi:10.1016/j.jclepro.2008.12.004
Asokan, P., Osmani, M., and Price, A. D. (2010). Improvement of the mechanical properties of glass fibre reinforced plastic waste powder filled concrete. Constr. Build. Mater. 24 (4), 448–460. doi:10.1016/j.conbuildmat.2009.10.017
Astm, (2007). ASTM D113-07, Standard test method for ductility of bituminous materials. https://www.astm.org/.doi:10.1520/D0113-07
Astm, (2006c). ASTM D36-06, Standard test method for softening point of bitumen (ring-and-ball apparatus).https://www.astm.org/. .doi:10.1520/D0036-06
Astm, (2006b). ASTM D5-06, Standard test method for penetration of bituminous materials. https://www.astm.org/.doi:10.1520/D0005-06
Astm, (2006a). ASTM D6927-06, Standard test method for Marshall stability and flow of bituminous mixtures. https://www.astm.org/.doi:10.1520/D6927-06
Beauson, J., Madsen, B., Toncelli, C., Brøndsted, P., and Bech, J. I. (2016). Recycling of shredded composites from wind turbine blades in new thermoset polymer composites. Compos. Part A Appl. Sci. Manuf. 90, 390–399. doi:10.1016/j.compositesa.2016.07.009
Cao, W. (2007). Study on properties of recycled tire rubber modified asphalt mixtures using dry process. Constr. Build. Mater. 21 (5), 1011–1015. doi:10.1016/j.conbuildmat.2006.02.004
Conroy, A., Halliwell, S., and Reynolds, T. (2006). Composite recycling in the construction industry. Compos. Part A Appl. Sci. Manuf. 37 (8), 1216–1222. doi:10.1016/j.compositesa.2005.05.031
Demura, K., Ohama, Y., and Satoh, T. (1995). “Properties of artificial woods using FRP powder,” in Disposal and recycling of organic and polymeric construction materials (Boca Raton, Florida, United States: CRC Press), 135–143. doi:10.1201/9781482294897
Farinha, C. B., de Brito, J., and Veiga, R. (2019). Assessment of glass fibre reinforced polymer waste reuse as filler in mortars. J. Clean. Prod. 210, 1579–1594. doi:10.1016/j.jclepro.2018.11.080
García, D., Vegas, I., and Cacho, I. (2014). Mechanical recycling of GFRP waste as short-fiber reinforcements in microconcrete. Constr. Build. Mater. 64, 293–300. doi:10.1016/j.conbuildmat.2014.02.068
Gu, X., Dong, Q., and Yuan, Q. (2015). Development of an innovative uniaxial compression test to evaluate permanent deformation of asphalt mixtures. J. Mater. Civ. Eng. 27 (1), 04014104. doi:10.1061/(ASCE)MT.1943-5533.0001038
Jensen, J. P., and Skelton, K. (2018). Wind turbine blade recycling: Experiences, challenges and possibilities in a circular economy. Renew. Sustain. Energy Rev. 97, 165–176. doi:10.1016/j.rser.2018.08.041
Kimm, M., Pico, D., and Gries, T. (2020). Investigation of surface modification and volume content of glass and carbon fibres from fibre reinforced polymer waste for reinforcing concrete. J. Hazard. Mater. 390, 121797. doi:10.1016/j.jhazmat.2019.121797
Li, J., Zhang, J., Yang, X., Zhang, A., and Yu, M. (2023). Monte Carlo simulations of deformation behaviour of unbound granular materials based on a real aggregate library. Int. J. Pavement Eng. 24 (1), 2165650. doi:10.1080/10298436.2023.2165650
Lin, J., Guo, Z., Hong, B., Xu, J., Fan, Z., Lu, G., et al. (2022). Using recycled waste glass fiber reinforced polymer (GFRP) as filler to improve the performance of asphalt mastics. J. Clean. Prod. 336, 130357. doi:10.1016/j.jclepro.2022.130357
Liu, P., and Barlow, C. Y. (2017). Wind turbine blade waste in 2050. Waste Manag. 62, 229–240. doi:10.1016/j.wasman.2017.02.007
Lu, X., Isacsson, U., and Ekblad, J. (2003). Influence of polymer modification on low temperature behaviour of bituminous binders and mixtures. Mater. Struct. 36 (10), 652–656. doi:10.1007/BF02479497
Majewski, P., Florin, N., Jit, J., and Stewart, R. A. (2022). End-of-life policy considerations for wind turbine blades. Renew. Sustain. Energy Rev. 164, 112538. doi:10.1016/j.rser.2022.112538
Mamanpush, S. H., Li, H., Englund, K., and Tabatabaei, A. T. (2018). Recycled wind turbine blades as a feedstock for second generation composites. Waste Manag. 76, 708–714. doi:10.1016/j.wasman.2018.02.050
Mastali, M., Dalvand, A., and Sattarifard, A. R. (2016). The impact resistance and mechanical properties of reinforced self-compacting concrete with recycled glass fibre reinforced polymers. J. Clean. Prod. 124, 312–324. doi:10.1016/j.jclepro.2016.02.148
Ministry of Transport, (2011). JTG E20-2011, Standard test methods of bitumen and bituminous mixture for highway engineering. Beijing, China: Ministry of Transport.
Morales, C. N., Claure, G., Álvarez, J., and Nanni, A. (2020). Evaluation of fiber content in GFRP bars using digital image processing. Compos. Part B Eng. 200, 108307. doi:10.1016/j.compositesb.2020.108307
Morea, F., and Zerbino, R. (2018). Improvement of asphalt mixture performance with glass macro-fibers. Constr. Build. Mater. 164, 113–120. doi:10.1016/j.conbuildmat.2017.12.198
Palmer, J., Ghita, O. R., Savage, L., and Evans, K. E. (2009). Successful closed-loop recycling of thermoset composites. Compos. Part A Appl. Sci. Manuf. 40 (4), 490–498. doi:10.1016/j.compositesa.2009.02.002
Pickering, S. J. (2006). Recycling technologies for thermoset composite materials—Current status. Compos. Part A Appl. Sci. Manuf. 37 (8), 1206–1215. doi:10.1016/j.compositesa.2005.05.030
Qiao, Y., Zhang, Y., Zhu, Y., Lemkus, T., Stoner, A. M., Zhang, J., et al. (2020). Assessing impacts of climate change on flexible pavement service life based on Falling Weight Deflectometer measurements. Phys. Chem. Earth 120, 102908. doi:10.1016/j.pce.2020.102908
Rahimizadeh, A., Kalman, J., Fayazbakhsh, K., and Lessard, L. (2019). Recycling of fiberglass wind turbine blades into reinforced filaments for use in Additive Manufacturing. Compos. Part B Eng. 175, 107101. doi:10.1016/j.compositesb.2019.107101
Rodin, H., Nassiri, S., Englund, K., Fakron, O., and Li, H. (2018). Recycled glass fiber reinforced polymer composites incorporated in mortar for improved mechanical performance. Constr. Build. Mater. 187, 738–751. doi:10.1016/j.conbuildmat.2018.07.169
Sengoz, B., and Isikyakar, G. (2008). Evaluation of the properties and microstructure of SBS and EVA polymer modified bitumen. Constr. Build. Mater. 22 (9), 1897–1905. doi:10.1016/j.conbuildmat.2007.07.013
Seydibeyoglu, M. O., Mohanty, A. K., and Misra, M. (2017). Fiber technology for fiber-reinforced composites. Sawston, United Kingdom: Woodhead Publishing. doi:10.1016/C2015-0-05497-1
Tittarelli, F., and Shah, S. P. (2013). Effect of low dosages of waste GRP dust on fresh and hardened properties of mortars: Part 1. Constr. Build. Mater. 47, 1532–1538. doi:10.1016/j.conbuildmat.2013.06.043
Wang, H., Fan, Z., and Zhang, J. (2016). Development of a full-depth wheel tracking test for asphalt pavement structure: Methods and performance evaluation. Adv. Mater. Sci. Eng. 2016. doi:10.1155/2016/1737013
Wang, Y., Peng, Y., Kamel, M. M., and Ying, L. (2019). Mesomechanical properties of concrete with different shapes and replacement ratios of recycled aggregate based on base force element method. Struct. Concr. 20 (4), 1425–1437. doi:10.1002/suco.201800261
Wu, S., Ye, Q., Li, N., and Yue, H. (2007). Effects of fibers on the dynamic properties of asphalt mixtures. J. Wuhan Univ. Technology-Mater. Sci. Ed. 22 (4), 733–736. doi:10.1007/s11595-006-4733-3
Wu, S., Ye, Q., and Li, N. (2008). Investigation of rheological and fatigue properties of asphalt mixtures containing polyester fibers. Constr. Build. Mater. 22 (10), 2111–2115. doi:10.1016/j.conbuildmat.2007.07.018
Yildirim, Y. (2007). Polymer modified asphalt binders. Constr. Build. Mater. 21 (1), 66–72. doi:10.1016/j.conbuildmat.2005.07.007
Keywords: asphalt mixture, highway performance, dynamic stability, Marshall stability, redundant wind turbine blade
Citation: Lan T, Wang B, Zhang J, Wei H and Liu X (2023) Utilization of waste wind turbine blades in performance improvement of asphalt mixture. Front. Mater. 10:1164693. doi: 10.3389/fmats.2023.1164693
Received: 13 February 2023; Accepted: 24 May 2023;
Published: 06 June 2023.
Edited by:
Hui Yao, Beijing University of Technology, ChinaReviewed by:
Jue Li, Chongqing Jiaotong University, ChinaCopyright © 2023 Lan, Wang, Zhang, Wei and Liu. This is an open-access article distributed under the terms of the Creative Commons Attribution License (CC BY). The use, distribution or reproduction in other forums is permitted, provided the original author(s) and the copyright owner(s) are credited and that the original publication in this journal is cited, in accordance with accepted academic practice. No use, distribution or reproduction is permitted which does not comply with these terms.
*Correspondence: Xu Liu, c2lrdWkyMDAzQG91dGxvb2suY29t
Disclaimer: All claims expressed in this article are solely those of the authors and do not necessarily represent those of their affiliated organizations, or those of the publisher, the editors and the reviewers. Any product that may be evaluated in this article or claim that may be made by its manufacturer is not guaranteed or endorsed by the publisher.
Research integrity at Frontiers
Learn more about the work of our research integrity team to safeguard the quality of each article we publish.