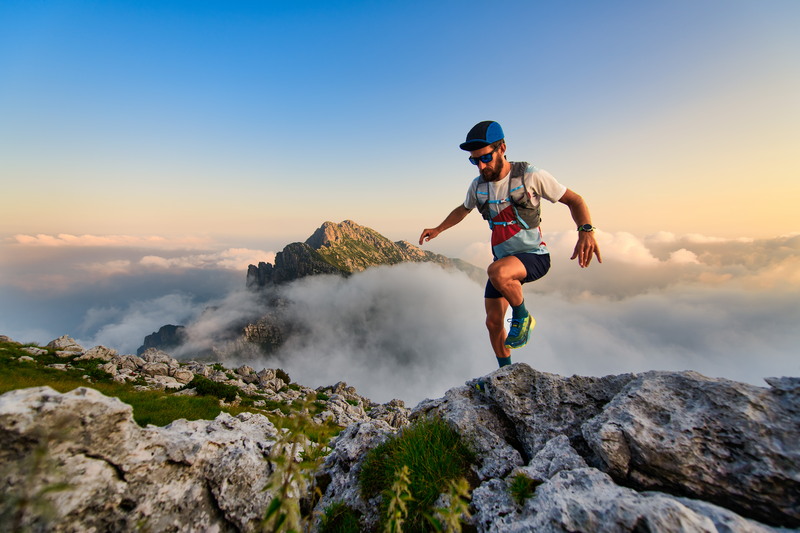
95% of researchers rate our articles as excellent or good
Learn more about the work of our research integrity team to safeguard the quality of each article we publish.
Find out more
ORIGINAL RESEARCH article
Front. Mater. , 27 July 2023
Sec. Polymeric and Composite Materials
Volume 10 - 2023 | https://doi.org/10.3389/fmats.2023.1153259
Pyrolytic carbon black (CBp) is the main by-product of waste tire pyrolysis. CBp has high ash content and poor surface activity which leads to the composites reinforced with CBp has lower performance than composites reinforced with commercial carbon black, making it difficult to meet the requirements of tire. In order to realize the application of CBp in tires, the effect of surfactants on the properties of rubber composites prepared by wet mixing of CBp/natural latex was investigated. In the experimental process, sodium stearate (C17H35COONa), sodium dodecylbenzene sulfonate (C18H29NaO3S), and sodium p-styrenesulfonate (C8H7NaO3S) were used to improve the surface activity and uniform dispersion of the CBp in the natural rubber matrix. The experimental results showed that the dispersity of C18H29NaO3S and C8H7NaO3S modified CBp in rubber matrix has [X] and [Y] values of 7.5 and 7.9, and 9.3 and 9.5, respectively, and the dispersion of these rubber composites is significantly better than that of C17H35COONa. The rubber composites prepared by C18H29NaO3S and C8H7NaO3S surfactants has the better physical and mechanical properties. The rubber composite prepared by C18H29NaO3S has the highest tensile strength of 25.63 MPa, which increment in tensile strength is 15.6% compare to the rubber composite prepared by C17H35COONa. Meanwhile the dynamic mechanical properties of rubber composites prepared by modifying CBp with C18H29NaO3S and C8H7NaO3S are better than CBp with C17H35COONa. The C8H7NaO3S modified CBp/rubber composite has the lowest loss factor (tanδ) value at 60°C, and the C18H29NaO3S modified CBp/rubber composite has the highest tanδ value at 0°C.
A lot of tires must be made each year as car items have become a necessity in people’s life (Zhang et al., 2020). As a result, there are more used tires ending up in landfills every year. Tire waste poses major environmental risks since its components are not decompose in the natural environment (Aboelkheir et al., 2019). One of the most efficient processes for dealing with waste tires is thermal pyrolysis, which may transform scrap tires into tire pyrolysis oil (TPO), pyrolysis carbon black (CBp), and steel (Tian et al., 2021; Tian et al., 2022a; Tian et al., 2022b). TPO can be converted into high-value chemical materials or fuels after treatment and it is the main product of waste tire pyrolysis (Williams, 2013; Mohan et al., 2019). Regulating the quality of pyrolysis oil through the pyrolysis process is the main goal of waste tire pyrolysis treatment.
The second by-product of the pyrolysis of scrap tires is CBp. The composition of CBp is significantly complex, which contains the original carbon black, inorganic compounding fillers (SiO2), and vulcanization aids (ZnO) including their processing-related derivatives (ZnO transformed to ZnS) (Berki and Karger-Kocsis, 2016). Many researchers have explored the differences in the performance of different types of rubber composites reinforced by CBp and commercial carbon black (Norris et al., 2014; Moulin et al., 2017; Sagar et al., 2018; Martinez et al., 2019; Verma et al., 2019; Lai et al., 2020). CBp has high ash content and poor surface activity which leads to the composites reinforced with CBp has lower performance than composites reinforced with commercial carbon black, making it difficult to meet the requirements of tire. A novel approach which is atomization dispersion and high-temperature sputtering drying to achieve uniform dispersion of CBp in rubber matrix has been made by Wang (Tian et al., 2021) for improving the properties of CBp rubber composite materials through processing methods. Meanwhile, some researcher modify the CBp surface using surfactants as reported to enhance the interaction between CBp and rubber matrix. Zhou Jie (Jie et al., 2010) found that the treatment of CBp with titanate coupling agent resulted in a strong interaction between the treated CBp and the polyisoprene chain. Berenice (González-González et al., 2020) found that the surface area of CBp treated with sulfuric acid (H2SO4) increased, while the oxygen content of CBp treated with potassium hydroxide (KOH) increased.
In this study, in order to realize the reapplication of CBp in rubber composites, a variety of surfactant, namely, sodium stearate (C17H35COONa), sodium dodecylbenzene sulfonate (C18H29NaO3S), and sodium p-styrene sulfonate (C8H7NaO3S), was used to improve the surface activity of CBp. Meanwhile, the degree of dispersion of the modified CBp in the rubber composite could be improved by wet blending of natural latex and CBp. The main objective of this study is to investigate the effect of surfactants on the properties of rubber composites prepared from CBp/natural latex via wet blending method.
C18H29NaO3S, C8H7NaO3S, and C17H35COONa were used to treat CBp in the experimental process to investigate the best surface activator for CBp, and then the treated CBp was used to prepare rubber composites by wet blending method. Table 1 shows the components, suppliers, and formulation of the rubber composites.
TABLE 1. Formulation of the rubber composites (phra).
In this paper, the wet mixing of natural latex and CBp was used to improve the homogenous dispersion of CBp in rubber matrix (Tian et al., 2021). This method mainly includes two processes: Preparation of CBp/natural latex masterbatch and preparation of CBp/rubber composite. The specific experimental process is shown in Figure 1.
FIGURE 1. Carbon black surface modification and CBp/natural latex mixing process diagram illustrate.
The CBp and nature latex were treated to achieve uniform dispersion of CBp in the process of preparation of CBp/natural latex masterbatch.
Pretreatment of the CBp: The grounded CBp and surfactant were added in deionized water with 1:5 surfactant to CBp ratio. The suspension was stirred with an ultrasonic dispenser (VCY-1500, Shanghai Yanyong Chaosheng Equipment Co., Ltd., Shanghai, China; experimental parameters: ultrasonic power, 1000 W) for 5 min.
Pretreatment of the natural latex: Natural latex and deionized water were mixed in the ratio of 1:1 and stirred with an ultrasonic dispenser for 3 min.
The natural latex and CBp slurry was mixed with a high-speed disperser (T 25 easy clean digital, German IKA company, Staufen im Breisgau, Germany; rotation rate: 400 rpm) for 5 min. A 5% concentration of acetic acid solution was prepared and added slowly into the CBp/natural latex slurry to flocculate the CBp/natural latex mixture.
After flocculation, the CBp/rubber compound were cut and placed in an oven at 70°C for 4 hours. Subsequently, the CBp/rubber compound was flattened with an open refiner, and placed in an oven at 60°C for 8 h.
Mooney viscosity of the CBp/rubber compound was tested by the Mooney viscometer (Mooney viscometer, PremierMV, Alpha Technology Co., Ltd., Akron, United States) according to the standard ISO 289–1: 1994, and the temperature was set at 100°C. After the actual temperature reached the set temperature, the sample was put in and tested after closing the mold.
Rheological properties of the CBp/rubber compound were tested by a rotorless rheometer according to the standard ISO 6502:1991, and the temperature was set at 150°C.
CBp/rubber composite were made by adding fillers such as zinc oxide to the masterbatch of CBp/natural latex through the internal mixer, which produces a strong shearing effect on the rubber by the rotor of the internal mixer to achieve uniform dispersion of the CBp in the rubber matrix. Then, the CBp/rubber composite was prepared by vulcanization. The specific process was shown in Table 2.
TABLE 2. Preparation process of the rubber composite (Tian et al., 2020a).
Dispersion of the filler was measured using carbon black dispersity analyzer (DisperGRADER, Alpha Corporation America) according to ISO 11345. The dispersion calculation threshold was set to 23 μm and the exposure time was set to 40 ms.
The Payne effect of the composite was tested by a rubber processing analyzer (Rubber Processing Analyzer, RPA 2000, Alpha Technologies, Inc., Akron, United States). The frequency was 1Hz, the strain range was between 0.28% and 40%, and the temperature was set at 60°C.
Shore A hardness was tested using a shore hardmeter (LX-A, Shanghai Liuling Instrument Factory, Shanghai, China) according to ISO 7619–2: 2004. The sample was tested after stacking three tensile specimens. The tensile specimens shape is a dumbbell shape, with a length of 115 mm and a width of 25 mm.
The tensile and tear properties of the vulcanized rubber were tested using a universal testing machine (TS 2005 b, GOTECH TESTING MACHINES CO., Ltd., Taichung, Taiwan) at a drawing rate of 500 mm/min according to the standards ISO 37: 2005 and ISO 34–1: 2004, respectively. Five specimens were tested for each sample type.
The abrasion of the rubber vulcanizates were evaluated using a DIN wear machine (GT-2012-D, GOTECH TESTING MACHINES CO., Ltd., Taichung, Taiwan) according to GB/T 1689–1998.
The viscoelastic mechanical properties of the vulcanizates were evaluated using a dynamic thermomechanical analyzer (EPLEX-OR-150N, Gabo Qualimeter Testanlagen GmbH, Ahlden, Germany), in which the test temperature range was −65°C t
o 65°C, the heating rate was 2 K/min, the vibration frequency was 10 Hz, the static strain was 5%, the static force was 70 N, the dynamic strain was 0.25%, and the dynamic stress was 60 N.
Processability is an essential indicator of the properties of rubber compound (Tian et al., 2020a; Tian et al., 2020b). It is usually characterized by Mooney viscosity and rheological properties. Among them, t10 is the scorch time of the rubber compound; t90 is the positive vulcanization time of the rubber compound; MH and ML represent the highest torque and the lowest torque of the rubber compound, respectively. Table 3 presents the processing performance data of CBp/rubber compound with different surfactants.
The three rubber composite with surfactant-modified CBp have sufficient scorch time, which can ensure the safety of rubber compound processing. The positive vulcanization time of C18H29NaO3S and C8H7NaO3S is longer than that of C17H35COONa modified rubber composite. C18H29NaO3S and C8H7NaO3S are sulfonates. The sulfonic acid reacts easily with the amine ion in the amine accelerator, reducing the reactivity of the accelerator and thus increasing the positive vulcanization time of the CBp/rubber composite (Wang et al., 2019). The MH-ML value of the rubber composite prepared by C8H7NaO3S modified CBp is the largest, indicating that the rubber composite has the highest crosslinking degree. Meanwhile, the ML of the rubber composites prepared by C18H29NaO3S modified CBp is the smallest, indicating that the CBp/rubber compound has better fluidity and low Mooney viscosity.
The CBp/rubber composite prepared by treating CBp with surfactant are tested by carbon black dispersity analyzer. The value of [X] represents the degree of dispersion of carbon black, and the value of [Y] represents the degree of dispersion of large particles of carbon black. The larger the value of [X] and [Y], the better the dispersion of carbon black in the rubber compound. Table 4 presents the value of [X] and [Y] of CBp/rubber composite with different surfactants.
From Table 4, the dispersion of C18H29NaO3S and C8H7NaO3S modified CBp in the rubber composite matrix is significantly better than that of C17H35COONa. C18H29NaO3S has been found to be effective in dispersing carbon black, and the lower the degree of sulfonation function, the better the dispersion of carbon black. Lignosulfonate mainly enhances colloidal stability by electrostatic repulsion, and the likely mechanism of stabilization is a combination of electrostatic repulsion and steric hindrance (Subramanian and Øye, 2021). C8H7NaO3S and C18H29NaO3S have the same functional groups, but the molecular weight of C18H29NaO3S (348.47 g/mol) is larger than that of C8H7NaO3S (206.19 g/mol) (Kurt et al., 1995). By adding the same mass of surfactant, the number of effective functional groups of C18H29NaO3S will be less than that of C8H7NaO3S, making the dispersion effect of CBp in rubber matrix slightly lower than that of C8H7NaO3S.
According to Table 5, the △G′ values of C18H29NaO3S and C8H7NaO3S modified CBp composites are 238.89 kPa and 237.27kPa, respectively. These values are lower than the △G′ value of 264.7 kPa for the C17H35COONa modified CBp rubber composite. A smaller △G′ value indicates a better interaction between CBp and rubber, with reduced CBp-CBp interaction (Tian et al., 2021). This suggests that CBp is more effectively dispersed in the rubber composite. The addition of C18H29NaO3S and C8H7NaO3S surfactants improves the wettability and uniform dispersion of CBp in natural latex, reducing the CBp-CBp interaction (Zhu et al., 2020). C18H29NaO3S and C8H7NaO3S are sulfonates and exhibit higher activity compared to C17H35COONa (Subramanian and Øye, 2021). Although C8H7NaO3S and C18H29NaO3S possess the same functional groups, the molecular weight of C18H29NaO3S (348.47 g/mol) is greater than that of C8H7NaO3S (206.19 g/mol) (Kurt et al., 1995). When the dosage is the same, C8H7NaO3S has a higher number of hydrophilic functional groups than C18H29NaO3S, resulting in a stronger surface modification effect on CBp. The enhanced dispersion of CBp in the presence of C18H29NaO3S and C8H7NaO3S is supported by higher [X] and [Y] values, as reported in Table 4.
Figure 2 illustrates that the C18H29NaO3S modified CBp rubber composite exhibits the highest modulus. C17H35COONa, C18H29NaO3S, and C8H7NaO3S belong to metal soap salts derived from fatty acids. These compounds consist of hydrophilic functional groups and hydrophobic carbon chains (Kerenkan et al., 2016). The hydrophobic carbon chains align to form micelles within the rubber, providing internal lubrication. The hydrophilic functional groups react with the surface groups of pyrolytic carbon black, serving as a means of surface modification (Wang et al., 2017). C18H29NaO3S and C8H7NaO3S, which are sulfonic acid metal soap salts, exhibit higher activity than C17H35COONa (Subramanian and Øye, 2021). The modification of CBp using C18H29NaO3S and C8H7NaO3S improves CBp dispersion and enhances CBp-rubber interaction. Additionally, the presence of a benzene ring in C18H29NaO3S reduces the flexibility of its molecular chain, resulting in a more effective internal lubrication effect compared to C8H7NaO3S (Shahabuddin et al., 2021). The combined effects of these factors contribute to the highest modulus observed in rubber composites containing C18H29NaO3S -modified CBp.
Table 6 shows the physical and mechanical properties of CBp/rubber composites modified by different surfactants.
TABLE 6. Physical and mechanical properties of CBp/rubber composites modified with different surfactants.
The C18H29NaO3S surfactant-modified CBp/rubber composite has the highest tensile strength of 25.63 MPa, followed by C8H7NaO3S and C17H35COONa, with 24.74 MPa and 22.17 MPa, respectively. The C18H29NaO3S surfactant-modified CBp/rubber composite has 15.6% increment in tensile strength compared to C17H35COONa surfactant-modified CBp/rubber composite. There are three surfactants used in this study, the functional group of C17H35COONa is carboxyl group, while the functional group of The C18H29NaO3S and C8H7NaO3S is sulfo group. From Table 6, surfactants with sulfo functional group have higher tensile strength compare to carboxyl functional group surfactant. The presence of sulfonate group increases the water solubility of the C18H29NaO3S and C8H7NaO3S, and its surface charged functional groups contribute to the uniform dispersion of CBp in natural latex (Zhu et al., 2020), which enhances the compatibility of CBp with rubber and thus increases the tensile strength of rubber composites. In general, the more uniform the dispersion of CBp and the stronger the CBp-rubber interaction, the greater the tensile strength of the composite (Alex et al., 2013). This is also the main reason for the high tear strength and resilience value of the C18H29NaO3S and C8H7NaO3S surfactant-modified CBp/rubber composites. The C18H29NaO3S surfactant-modified CBp/rubber composites has the lowest hardness of 59°, followed by C8H7NaO3S and C17H35COONa, with 65° and 67°, respectively. The hardness of rubber composites generally related to the dispersion of the modified CBp and the degree of crosslinking of CBp/rubber composite. Typically, the higher MH-ML value and the more uniform the dispersion of CBp, the higher the crosslinking degree of the rubber composite (Shan et al., 2023). The higher degree of crosslinking enhanced the mechanical properties of rubber composite (Sun et al., 2022). This could be the primary contribution of the higher hardness values of the C8H7NaO3S and C17H35COONa surfactant-modified CBp/rubber composites. These findings show that the CBp can be uniformly dispersed in natural latex after being treated with C18H29NaO3S, resulting in better comprehensive mechanical properties of the composite.
The dynamic mechanical properties of the composites refer to the mechanical response of composites under the action of alternating force. Usually, the dynamic mechanical properties of composites are studied through the changes in storage modulus and loss modulus under the influence of temperature and vibration frequency. Loss factor (tanδ) refers to the ratio of loss modulus G″ to storage modulus G′, which is an essential parameter of rubber composites and directly reflects the internal friction of rubber compounds. To a certain extent, it can characterize the dispersion of fillers in the rubber compound, the network degree of fillers, and the rolling resistance and wet skid resistance of the rubber compound. Typically, the higher the peak value of the loss factor (tanδ), the better the dispersion of the filler and the lower the degree of networking of the filler (Tian et al., 2021).
It can be seen from Figure 3 that the rubber composite prepared by C8H7NaO3S modified CBp has the highest tanδ peak, followed by C18H29NaO3S modified CBp composite, and C17H35COONa modified CBp composite has the lowest tanδ peak. This shows that C8H7NaO3S modified CBp has the best dispersibility in rubber composite and the weakest filler network effect, this is also in agreement with the payne effect and the dispersion properties of the composite. Besides, the C8H7NaO3S modified CBp/rubber composite has the lowest tanδ value at 60°C, and the C18H29NaO3S modified CBp/rubber composite has the highest tanδ value at 0°C. In the industry, tanδ at 0°C is commonly used to characterize the wet skid resistance of rubber composites. The larger the value, the better the wet skid resistance of the rubber composite. The rolling resistance of rubber composites is characterized by tanδ at 60°C. The smaller the value, the better the rolling resistance of the rubber composite (Tian et al., 2021). CBp modified by C8H7NaO3S improves the surface activity of the CBp and makes it evenly dispersed in the rubber composite, thereby improving the dynamic mechanical properties of the rubber composite (Dong et al., 2017).
FIGURE 3. Graph of tan delta versus temperature for CBp/rubber composite produced from different surfactant-modified CBp.
In this study, C17H35COONa, C18H29NaO3S, and C8H7NaO3S were used to improve the surface activity and uniform dispersion of the CBp in the natural latex. The dispersity of C18H29NaO3S and C8H7NaO3S modified CBp in rubber matrix has [X] and [Y] values of 7.5 and 7.9, and 9.3 and 9.5, respectively, and the dispersion of these rubber composites is significantly better than that of C17H35COONa. The rubber composite contain of C18H29NaO3S surfactant-modified CBp has the highest tensile strength of 25.63 MPa, which increment in tensile strength is 15.6% compare to the rubber composite prepared by C17H35COONa. Moreover, the C8H7NaO3S modified CBp rubber composite has the lowest tanδ value at 60°C, and the C18H29NaO3S modified CBp compound has the highest tanδ value at 0°C. The above experimental results indicate that the mechanical properties and dynamic mechanical properties of CBp/natural latex composites prepared by modifying CBp with C18H29NaO3S and C8H7NaO3S have been significantly improved. The modified CBp is able to replace some of the commercial carbon black for reapplication in the tire preparation process. The reuse of CBp to prepare rubber composites can significantly reduce the production cost of rubber products and is of great significance to both resource conservation and environmental protection.
The raw data supporting the conclusion of this article will be made available by the authors, without undue reservation.
XT: Conceptualization, Methodology, Writing—Original Draft, Writing—Review and Editing. XS: Data Curation, Validation, Formal analysis. KW: Formal analysis. TS: Investigation, Data Curation. CW: Conceptualization, Methodology. All authors contributed to the article and approved the submitted version.
This work was sponsored by the Qingdao Science and Technology Benefits People Demonstration Guide Special Project (22-3-7-cspz-18-nsh), Natural Science Foundation of Shandong Province Key Projects (ZR2020KE037).
The authors declare that the research was conducted in the absence of any commercial or financial relationships that could be construed as a potential conflict of interest.
All claims expressed in this article are solely those of the authors and do not necessarily represent those of their affiliated organizations, or those of the publisher, the editors and the reviewers. Any product that may be evaluated in this article, or claim that may be made by its manufacturer, is not guaranteed or endorsed by the publisher.
Aboelkheir, M. G., Visconte, L. Y., Oliveira, G. E., Toledo Filho, R. D., and Souza, F. G. (2019). The biodegradative effect of Tenebrio molitor Linnaeus larvae on vulcanized SBR and tire crumb. Sci. Total Environ. 649, 1075–1082. doi:10.1016/j.scitotenv.2018.08.228
Alex, R., Sasidharan, K. K., and Kurian, T. (2013). Carbon black master batch from fresh natural rubber latex[J]. Plastics, Rubber and Composites.
Berki, P., and Karger-Kocsis, J. (2016). Comparative properties of styrene-butadiene rubbers (SBR) containing pyrolytic carbon black, conventional carbon black, and organoclay. J. Macromol. Sci. Part B 55 (7), 749–763. doi:10.1080/00222348.2016.1197511
Dong, A., Zhang, Z., Jia, H., Shou, J., Zhang, H., and Liu, Y. (2017). Effect of carbon black nature on dynamic mechanical properties and reinforcement of NR vulcanization by latex techniques. Rubber Chem. Technol. 90 (4), 611–620. doi:10.5254/rct.17.84828
González-González, R. B., González, L., Iglesias, S., González-González, E., Martinez-Chapa, S. O., Madou, M., et al. (2020). Characterization of chemically activated pyrolytic carbon black derived from waste tires as a candidate for nanomaterial precursor. J. Nanomater. 10 (11), 2213. doi:10.3390/nano10112213
Jie, Z., Yu, T., Wu, S., Xie, Z., and Yang, Y. (2010). Inverse gas chromatography investigation of rubber reinforcement by modified pyrolytic carbon black from scrap tires. Industrial Eng. Chem. Res. 49 (4), 1691–1696. doi:10.1021/ie9009217
Kerenkan, A. E., Béland, F., and Do, T. O. (2016). Chemically catalyzed oxidative cleavage of unsaturated fatty acids and their derivatives into valuable products for industrial applications: A review and perspective[J]. Catal. Sci. Technol. 6.
Kurt, G., Sevgi, F., and Mercimek, B. (1995). Amount of substance and the mole[J]. Chem. Int. -- Newsmag. IUPAC 31 (2), 3–7.
Lai, S.-M., Chu, Y.-L., Chiu, Y. T., Chang, M.-C., Hsieh, T.-Y., and Hsieh, M.-H. (2020). Effect of pyrolysis carbon black from waste tires on the properties of styrene–butadiene rubber compounds. Polym. Polym. Compos. 29 (2), 75–86. doi:10.1177/0967391120902882
Martinez, J. D., Cardona-Uribe, N., Murillo, R., Garcia, T., and Lopez, J. M. (2019). Carbon black recovery from waste tire pyrolysis by demineralization: Production and application in rubber compounding. Waste Manag. 85, 574–584. doi:10.1016/j.wasman.2019.01.016
Mohan, A., Dutta, S., and Madav, V. (2019). Characterization and upgradation of crude tire pyrolysis oil (CTPO) obtained from a rotating autoclave reactor. Fuel 250, 339–351. doi:10.1016/j.fuel.2019.03.139
Moulin, L., Da Silva, S., Bounaceur, A., Herblot, M., and Soudais, Y. (2017). Assessment of recovered carbon black obtained by waste tires steam water thermolysis: An industrial application. Waste Biomass Valorization 8 (8), 2757–2770. doi:10.1007/s12649-016-9822-8
Norris, C. J., Hale, M., and Bennett, M. (2014). Pyrolytic carbon: Factors controlling in-rubber performance. Rubber Compos. 43 (8), 245–256. doi:10.1179/1743289814y.0000000088
Sagar, M., Nibedita, K., Manohar, N., Kumar, K. R., Suchismita, S., Pradnyesh, A., et al. (2018). A potential utilization of end-of-life tyres as recycled carbon black in EPDM rubber. Waste Manag. 74, 110–122. doi:10.1016/j.wasman.2018.01.003
Shahabuddin, S., Shah, S. N. A., Sabri, M. F. M., and Pandey, A. (2021). Influence of SDBS surfactant on stability, thermal conductivity and viscosity of h-BN/EG based nanofluids. IOP Conf. Ser. Mater. Sci. Eng. 1127 (1), 012014. doi:10.1088/1757-899x/1127/1/012014
Shan, T., Bian, H., Zhu, D., Wang, K., Wang, C., and Tian, X. (2023). Study on the mechanism and experiment of styrene butadiene rubber reinforcement by spent fluid catalytic cracking catalyst. Polymers 15, 1000. doi:10.3390/polym15041000
Subramanian, S., and Øye, G. (2021). Aqueous carbon black dispersions stabilized by sodium lignosulfonates. Colloid Polym. Sci. 299, 1223–1236. doi:10.1007/s00396-021-04840-7
Sun, C., Fan, C., Kan, X., Ma, Y., Zhang, X., and Zhao, Y. (2022). Enhanced cross-linking performances and carbon black (cb) dispersion in solution styrene butadiene rubber (ssbr) filled with triazine-based graphdiyne (tgdy). Compos. Sci. Technol. 223, 109438. doi:10.1016/j.compscitech.2022.109438
Tian, X., Zhu, L., Li, K., Wang, K., Bian, H., Li, L., et al. (2020a). Effect of gear pump extrusion processing on the properties of fiber reinforced rubber composites. Polym. (Basel) 12 (4), 985. doi:10.3390/polym12040985
Tian, X., Han, S., Zhuang, Q., Bian, H., Li, S., Zhang, C., et al. (2020b). Surface modification of staple carbon fiber by dopamine to reinforce natural latex composite. Polym. (Basel) 12 (4), 988. doi:10.3390/polym12040988
Tian, X., Zhuang, Q., Han, S., Li, S., Liu, H., Li, L., et al. (2021). A novel approach of reapplication of carbon black recovered from waste tyre pyrolysis to rubber composites. J. Clean. Prod. 280, 124460. doi:10.1016/j.jclepro.2020.124460
Tian, X., Han, S., Wang, K., Shan, T., Li, Z., Li, S., et al. (2022a). Waste resource utilization: Spent FCC catalyst-based composite catalyst for waste tire pyrolysis. Fuel 328, 125236. doi:10.1016/j.fuel.2022.125236
Tian, X., Wang, K., Shan, T., Li, Z., Wang, C., Zong, D., et al. (2022b). Study of waste rubber catalytic pyrolysis in a rotary kiln reactor with spent fluid-catalytic-cracking catalysts. J. Anal. Appl. Pyrolysis 167, 105686. doi:10.1016/j.jaap.2022.105686
Verma, A., Baurai, K., Sanjay, M. R., and Siengchin, S. (2019). Mechanical, microstructural, and thermal characterization insights of pyrolyzed carbon black from waste tires reinforced epoxy nanocomposites for coating application. Polym. Compos. 41 (1), 338–349. doi:10.1002/pc.25373
Wang, Y., Hou, B., and Cao, X. (2017). Interaction between polymer and anionic/nonionic surfactants and its mechanism of enhanced oil recovery[J]. J. Dispersion Sci. Technol. 39 (1), 2017, 1386112.
Wang, M., Zhu, J., Zhang, S., You, G., and Wu, S. (2019). Influencing factors for vulcanization induction period of accelerator/natural rubber composites: Molecular simulation and experimental study. Polym. Test. 80, 106145. doi:10.1016/j.polymertesting.2019.106145
Williams, P. T. (2013). Pyrolysis of waste tyres: A review. Waste Manag. 33 (8), 1714–1728. doi:10.1016/j.wasman.2013.05.003
Zhang, Y., Ji, G., Li, C., Wang, X., and Li, A. (2020). Templating synthesis of hierarchical porous carbon from heavy residue of tire pyrolysis oil for methylene blue removal. Chem. Eng. J. 390, 124398. doi:10.1016/j.cej.2020.124398
Keywords: waste tires, pyrolytic carbon black modification, surfactants, wet blending, rubber composite
Citation: Song X, Wang K, Shan T, Wang C and Tian X (2023) Effect of surfactants on the properties of rubber composites prepared from pyrolytic carbon black/natural latex via wet blending method. Front. Mater. 10:1153259. doi: 10.3389/fmats.2023.1153259
Received: 29 January 2023; Accepted: 19 July 2023;
Published: 27 July 2023.
Edited by:
Suresh Sagadevan, University of Malaya, MalaysiaReviewed by:
M. E. Ali Mohsin, King Faisal University, Saudi ArabiaCopyright © 2023 Song, Wang, Shan, Wang and Tian. This is an open-access article distributed under the terms of the Creative Commons Attribution License (CC BY). The use, distribution or reproduction in other forums is permitted, provided the original author(s) and the copyright owner(s) are credited and that the original publication in this journal is cited, in accordance with accepted academic practice. No use, distribution or reproduction is permitted which does not comply with these terms.
*Correspondence: Xiaolong Tian, dGlhbnhpYW9sb25nQHF1c3QuZWR1LmNu
Disclaimer: All claims expressed in this article are solely those of the authors and do not necessarily represent those of their affiliated organizations, or those of the publisher, the editors and the reviewers. Any product that may be evaluated in this article or claim that may be made by its manufacturer is not guaranteed or endorsed by the publisher.
Research integrity at Frontiers
Learn more about the work of our research integrity team to safeguard the quality of each article we publish.