- 1National Engineering Laboratory for High Efficiency Recovery of Refractory Nonferrous Metals, School of Metallurgy and Environment, Central South University, Changsha, China
- 2Anhui Winking New Material Technology Co., Ltd., Fuyang, China
- 3State Environmental Protection Key Laboratory of Urban Ecological Environment Simulation and Protection, South China Institute of Environmental Sciences, Ministry of Ecology and Environment (MEE), Guangzhou, China
- 4Special Glass Key Lab of Hainan Province, School of Materials Science and Engineering, Hainan University, Haikou, China
Lithium-ion batteries (LIBs) account for the majority of energy storage devices due to their long service life, high energy density, environmentally friendly, and other characteristics. Although the cathode materials of LIB led by LiFePO4 (LFP), LiCoO2 (LCO), and LiNixCoyMn1-x-yO2 (NCM) occupy the majority of the market share at present, the demand of LiMn2O4 (LMO) cathode battery is also increasing year by year in recent years. With the rising price of various raw materials of LIBs and the need of environmental protection, the efficient recycling of spent LIBs has become a hot research topic. At present, the recycling of spent LIBs mainly focuses on LFP, LCO, and NCM batteries. However, with the continuous improvement of people’s safety of LIBs, LiMnxFe1-xPO4 (LMFP) batteries show better potential, which also improves the recycling value of LMO batteries. Therefore, this paper reviews current methods of spent LMO recovery, focusing on the characteristics of the recovery and separation process, which can serve as a reference for subsequent research on LMO recovery, increasing environmentally friendly recovery routes. Finally, the future development direction of LIBs recycling is prospected. Overall, this review is helpful to understand the current progress of LMO battery recycling.
1 Introduction
The increasingly prominent contradiction between economic development and environmental protection means that the traditional structure of fossil fuels cannot sustainably support the development of human society (Palmer, 2019). In recent years, countries have recognized the development and use of renewable energy as a vital tool for reforming the energy structure and have intensified the use of wind and solar power, among others (Nematollahi et al., 2016; Zhang et al., 2017). According to the International Energy Agency, 70% of the world’s electricity will come from wind and photovoltaics by 2050 (I E Agency, 2021). After adjusting the energy structure, the annual carbon dioxide emissions equivalent is shown in Figure 1A. However, new energy power generation is characterized by instability, intermittency, and supply and demand mismatch (Yuan et al., 2021). Electrochemical energy storage and conversion devices are widely considered the most effective solution to address supply-side instability.
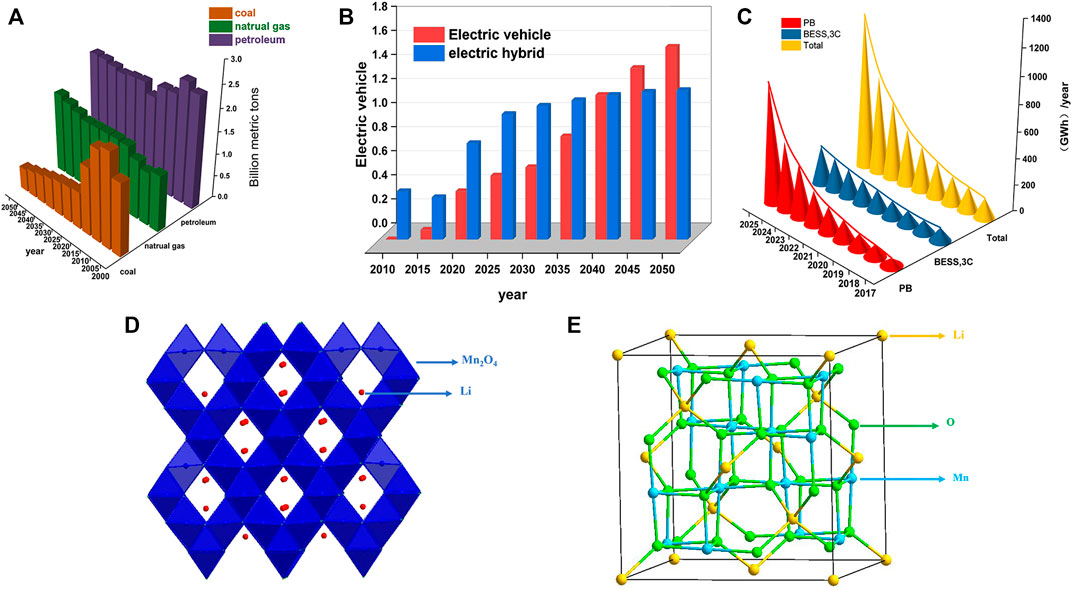
FIGURE 1. (A) CO2 emissions from different energy fuels in different years; (B) The number of hybrid vehicles and electric vehicles of different years; (C) statistics and forecast of the installed capacity of LIBs in the world from 2017 to 2025; (D) Spinel structure of the LMO; (E) The position of Li, Mn, and O in the LMO.
In China, the new increment of new energy storage exceeded 1 million Kw in 2020, further accelerating its growth to 2.45 million kW in 2021. By the end of 2021, the cumulative installed capacity of new energy storage in China was 5.37 million kW (Yan et al., 2022), among which lithium batteries, as the focus of electrochemical energy storage technology, occupied 80% of the electrochemical energy storage market (Li et al., 2021). Besides, LIBs also bring vitality to the car industry (Kim et al., 2019). New energy vehicles equipped with lithium batteries are high in energy conversion and low in exhaust emissions, leading the entire automobile industry in an environmentally friendly direction (Kumar and Revankar, 2017; Zhao J. et al., 2021). The number of hybrid vehicles and electric vehicles will increase year by year as predicted in Figure 1B. The International Energy Agency estimates that, based on current and anticipated policies, the global market for new energy vehicles is likely to reach 4 million in 2020 and 245 million in 2030, with an annual growth of about 41% and a market cap between 13 billion and 130 billion US dollars (Xiaowei et al., 2022). In addition, the installed quantity of energy storage installed in major countries around the world is shown in Table 1, the whole show an explosive growth trend. In summary, the global demand for lithium batteries is increasing rapidly. Figure 1C shows the statistics and forecast of the installed capacity of LIBs in the world from 2017 to 2025.
According to the US Geological Survey, global Li, Co, Ni, Mn, Fe, and graphite (natural) reserves are 22 million tons, 145 million tons, over 95 million tons, over 1,500 million tons, 230 billion tons and 320 million tons, respectively. In 2021, the global production of major LIB metals Li, Ni, Co, and Mn will be 100 Kilotons, 2,700 Kilotons, 170 kilotons and 20 million tons respectively. It is predicted that in 2040, under the scenario of taking the green road, the demand of LIB for Li, Ni, Co, and Mn will be 1,247 kilotons, 5,616 kilotons, 713 kilotons and 2,357 kilotons respectively (Maisel et al., 2023). The global lithium market has expanded since 2018. By 2021, the global lithium market size will have reached 545 GWh (C. Consulting, 2022). In addition, the global demand for lithium batteries is estimated to be 1,223 GWh by 2025 (Zhou, 2022). However, the service life of lithium batteries is 3–5 years (Chen et al., 2017), which means that in the future, due to the extensive use of non-renewable lithium batteries in the energy storage and automotive industries, there will be a large number of spent lithium batteries, in which there are a large number of heavy metal elements: copper, iron, nickel, cobalt, and so on (Meshram et al., 2019; Windisch-Kern et al., 2022). This raises two key issues: the disposal of discarded lithium batteries, which, if not correctly disposed of, will cause massive environmental pollution and endanger people’s health (Leal et al., 2022). The second problem lies in the waste of valuable metals. In LIBs, cathode materials are the most expensive of all components (Garole et al., 2020). According to the types of cathode materials, batteries can be divided into: LCO, LFP, NCM, and LMO (Li M. et al., 2018). The cathode materials contain a lot of valuable metals such as lithium, nickel, cobalt, etc., (Xie et al., 2021; Luo et al., 2022). With the vigorous development of the lithium battery market, by 2022, the price of battery-grade lithium carbonate, cobalt, and nickel will be 85,532 $ t−1, 49,623 $ t−1, and 32,118 $ t−1, respectively. Therefore, we can foresee that the recycling of LIBs has enormous market potential.
Industrial recovery mainly focuses on recovering LFP and ternary lithium battery materials, primarily using hydrometallurgical and pyrometallurgical processes (Ciez and Whitacre, 2019). In 2021, China’s LMO cathode material shipments were 110 kilotons, up 32.5% year on year. The crystal structure of LiMn2O4 is spinel type, belonging to Fd3m space group. As shown in Figures 1D, E, Li+occupies 8a, while the positions of 16d and 32e are manganese ion and O2-, respectively. With the development of lithium manganese iron phosphate material, the recovery and regeneration value of LMO has been further improved. In contrast, there are few research and reviews on LMO. Here we summarize the existing articles on LMO recycling, classify and summarize the recovered products according to their different types, and propose a future development strategy for LMO recycling.
2 Treatment of different spent LMO
Currently, the sources of spent LIBs on the market are inconsistent, leading to various compositions of collected waste cathode materials in different manufacturers. Some waste cathode materials contain certain amounts of impurities such as Ca, Mg, Al, Cu, etc., among them, the elements of Ca and Mg primarily come from contact with the soil during the placement process, while the collectors mainly produce the elements of Al and Cu in the batteries (Zhu et al., 2021). In addition, some spent LIBs cathode materials contain one or more LMO, LCO, NCM, and LFP materials, which significantly reduces the classification difficulty in the pretreatment stage. However, this kind of hybrid spent materials must change the recycling method to adapt to the recycling impact. Some LIBs are disassembled, and the cathode is mixed with the anode, resulting in too much carbon in the cathode electrode materials (Zhang et al., 2018; Wuschke et al., 2019). Under the circumstances, the recycling of such materials by carbothermal reduction can achieve a good result and efficiently use the potential resources. In the following sections, we will discuss the recycling status of LMO with low impurity content, mixed LMO spent materials, and LMO with high carbon content, respectively.
2.1 Recovery of LMO with low impurity content
The low impurity content of the LMO, means that there is no other lithium-ion cathode material in the scrap unless LMO. It can be regarded as a single chemical LiMn2O4. The LMO’s low impurity often comes from the binder’s stripping and sintering processes. Too high impurity will lead to a long metal extraction process, resulting in the loss of valuable metals. LMO can use hydrometallurgy, pyrometallurgy, and direct recovery to recover valuable metals like other cathode-processing treatments (He et al., 2017; Barrios et al., 2022). Since there are only two kinds of metal elements in LMO, it is easy to achieve efficient separation and recovery of Li and Mn.
The recovery strategies of valuable metals from spent LIBs cathode materials can be divided into hydrometallurgical and pyrometallurgical processes (Huang et al., 2018). In earlier times, smelting was the primary method in pyrometallurgy, when the temperature could reach more than 1,200°C, which usually caused the loss of lithium resources (Guoxing et al., 2016; Ren et al., 2017). Currently, the mainstream pyrometallurgy recovery method mainly uses the salt-assisted roasting method. The spent cathode material and roasting additives are mixed after the roasting agent and materials react at high temperatures. In the reaction process, water-soluble lithium salt or transition metal salt is produced, and then water leaching separation extracts valuable metals. Compared with smelting, the roasting temperature in this way is only 200°C–900°C, and simultaneously achieving lower energy consumption and higher metal recovery. This method is widely used in recycling LFP, LCO, NCM, NCA (Zhang B. et al., 2021; Chang et al., 2022). As a salt-assisted, Na2SO4 was mixed with LFP in a ratio of 2:1 and calcined for 3 h at 800°C. Under this optimized consideration, we can achieve a high leaching rate of Li exceeding 99% and a low leaching rate of Fe 0.03% and P 0.11%, respectively (Zhang J. et al., 2022). LiNi0.6Co0.2Mn0.2O2(NCM622) can also be roasted at low temperatures using metal salts as auxiliary calciners. By calcinating ammonium sulfate and NCM622 for 1.5 h at 350°C in air, NCM622 converts to sulfate through water leaching, which achieves a sulfation rate of over 98.5% (Tang et al., 2021). This method shows an excellent recovery rate. At present, many researchers focus on seeking suitable auxiliary salt for roasting with waste cathode materials. The goal is to reduce the reaction temperature and time; the most important is environmental protection cost.
Paulino et al. (2008) directly mixed battery materials (including anode and cathode, LiPF6 electrolyte) with a and roasted at 500°C for 5 h. Afterward, NaOH is added to the solution, manganese or cobalt is deposited in hydroxides, and the lithium is precipitated using saturated KF solution, which realizes the separating of Mn and Li. However, the introduction of F− will bring about subsequent environmental problems.
He and Liu (2020b) demonstrated a salt-assisted low-temperature roasting method to recover Li and Mn from waste LMO cathode. In this case, a molar ratio of n (2Li + Mn): n (NH4)2SO4 = 1:1.1 is placed in the air atmosphere for 45 min at 600°C. Afterward, the roasted product is leached in water and converted to two sulfate solutions. When ammonium sulfate exceeds the theoretical dosage of 10%, Li and Mn recovery can reach approximately 100% and 96.73%, respectively. To explore the mechanism of the reaction, the phase composition and morphology characteristics of calcined products and water-leaching products under different calcined conditions were analyzed. The analysis shows that the high energy H+ generated by ammonium sulfate at high temperatures plays a vital role in breaking the Mn-O bond in LMO. The mechanism of the reaction is shown in Figures 2A, B. Ultimately, Li and Mn are present in the solution as Li2Mn2(SO4)3 and MnSO4. The author then performed the separation steps of the substances in the solution were carried out (He and Liu, 2020a). The kinetics and thermodynamics of solution manganese precipitation were analyzed in the Mn2+-Li+-SO2- 4-NH3-NH+ 4-CO2- 3-H2O solution system. Under the best conditions, 99.96% of Mn appears in precipitation with the addition of a precipitant.
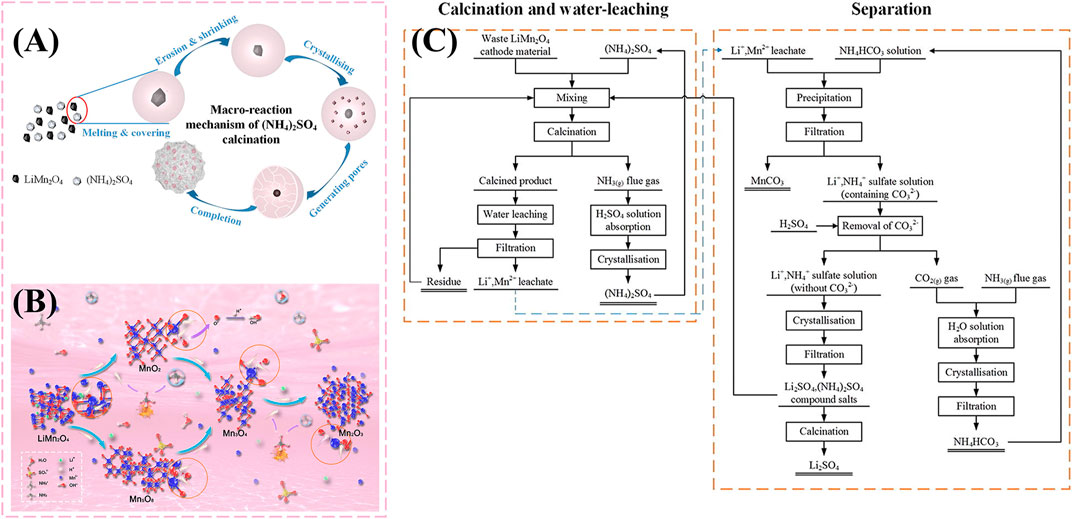
FIGURE 2. The mechanisms of spent LMO cathode material calcined with (NH4)2SO4: (A) Macro-reaction mechanism; (B) Micro-reaction mechanism; (C) Flowchart of the recovery process of spent LMO cathode material.
Meanwhile, double-sulfate salts formation includes Li(NH4)SO4 and (NH4)2SO4. Li2SO4 can be obtained by roasting double sulfates at high temperature, because (NH4)2SO4 has the property of easy decomposition by heating, while Li2SO4 has better thermal stability. In this method, Li2SO4 and MnCO3 products can be obtained through a series of technological processes. However, this strategy has a prolix process and complex precipitation system, which need to control a relatively precise precipitation conditions, the process diagram of the recovery process is shown in Figure 2C. In addition, the complex system may also have a certain impact on the purity of the product.
Hydrometallurgy also plays an important process in addition to pyrometallurgy, which usually exhibits excellent metal recovery rates (Li et al., 2018b). In the selection of leaching agent, inorganic acid (H2SO4, HCl, HNO3, etc.,) (Xuan et al., 2019; Chen et al., 2021; Fan et al., 2021), organic acid (formic acid, malonic acid, glycolic acid, etc.,) (Liu et al., 2019; Fan et al., 2020; Ji et al., 2021), or the combination of acid and oxidant or reductant. Wang et al. (2019) use phytic acid to treat LMO and convert the manganese in it to Mn2P, which can be used as a nanofiller in polyethylene oxide matrix to improve Li+ conductivity and transference in all-solid-state batteries vastly. Chart of recycling spent batteries saw Figure 3A. Batteries assembled from this material have excellent electrochemical properties, cycling performance of LiFePO4|PL-Mn2P5|Li cell at 0.1 C saw in Figure 3B. Interestingly, by mixing sulfuric acid with LMO with different stoichiometric numbers, Zhang Y. et al. (2022) obtained MnO2 with varying crystal structures, α- MnO2, λ- MnO2, β- MnO2, Different crystal structure of MnO2 were shown in Figures 3C–E. It can be used for valuable production to absorbents for Co removal. Besides, the lithium in the solution is recovered as a precipitate of lithium phosphate. These two methods recycle manganese into other valuable products, Mn2P and MnO2, realizing the value-added utilization of spent LIBs. Despite their outstanding performance in other areas, the best final destination for the spent LIBs is a closed-loop synthesis of cathode materials. Furthermore, most of the spent cathode material contains other impurities that need to be decontaminated before it can be used as a product. The recovered product must be a kind of product that can be used universally. The product that can only be used in a specific field will inevitably limit the broad application of this method.

FIGURE 3. (A) Schematic of recycling process and assembly of Li |PL-Mn2P| LiFeO4 batteries; (B) Cycling performance of LiFePO4|PL-Mn2P5|Li cell at 0.1°C; Crystal structure of (C) λ-MnO2, (D) γ-MnO2 and (E) β-MnO2. Purple sphere, Mn; Red spheres, O.
Electrochemical metallurgy technology also plays a vital role in the metallurgy process, which is also divided into high-temperature molten salt electrolysis and solution electrochemistry. The former is mainly used in treating some active metal oxides or other compounds, while the latter is more used in removing impurities in metal refining. LMO can be regarded as a metal oxide, so Liang et al. (2021) placed it in NaCl-CaCl2 melt at 750°C for an electrolytic reduction study and found that by constantly increasing the voltage, Mn metal finally appeared when the voltage reached 2.6 V. In molten salt electrolysis, Mn successfully realizes its valence state’s transformation and instructs it to become an elementary metal substance. Other intermediates are produced in this process, for example, CaMn2O4, MnO, (MnO)x (CaO)1-x. The mechanism diagram of electrolysis is shown in Figure 4A. This is undoubtedly a new idea for the recovery of lithium manganate by introducing high-temperature molten salt. But the final product separation is a huge problem, and environmental requirements are also high in the process of high-temperature electrolysis equipment. Similarly, Li et al. (2019) carry out a new method for recovering LMO from an electrolytic slurry. The LMO is mixed with sulfuric acid and placed in the cathode chamber connected to the battery’s cathode by the graphite. Afterward, Mn2+ is oxidized and deposited in the anode region, and Li+ and a little bit of Mn2+ stay in the solution. In Figure 4B, we can see the transformation mechanism diagram of Li and Mn. After the impurity removal conversion, the final products are Li2CO3 and MnO2. The product obtained by this method has a high purity and uses electrical energy as the “fuel” for the reaction.
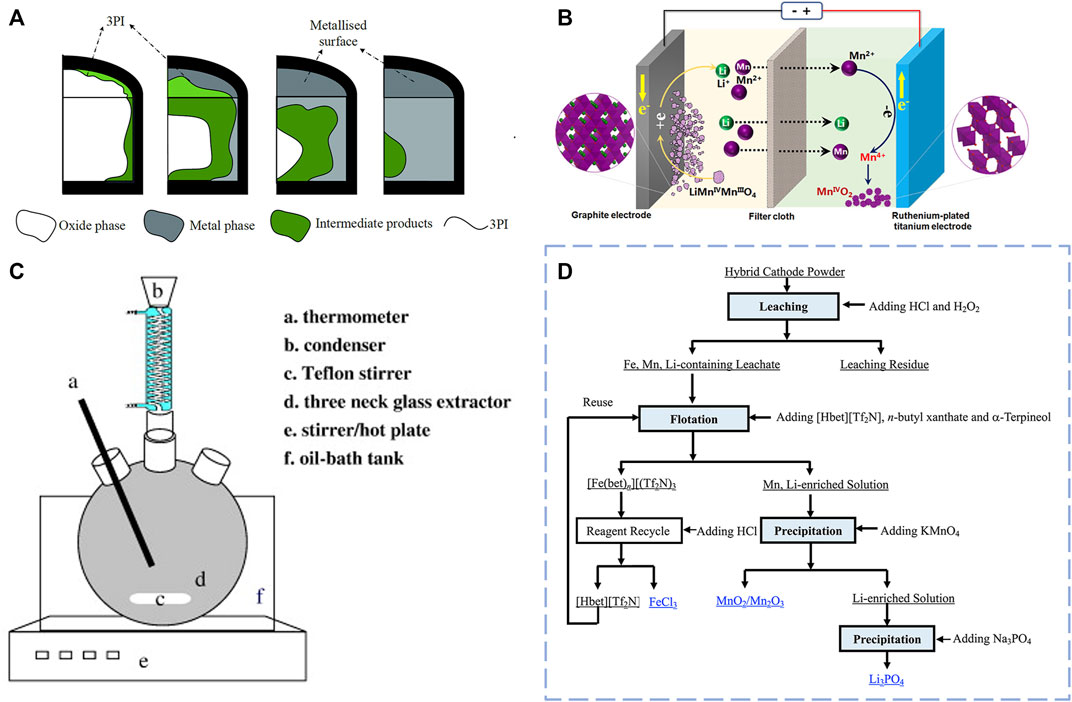
FIGURE 4. (A) Schematic diagram of LMO molten salt recovery process by high-pressure electrolysis; (B) Transformation mechanism diagram of Li and Mn during electrolytic recovery; (C) Experimental setup for leaching and recovery material processes; (D) Flowchart of hybrid material treatment and recovery.
2.2 Treatment of mixed LMO cathode materials
In the industry, recycling companies usually recycle more than a single LIB, which may include one or several types of LCO, LFP, and NCM. When these cathode materials are mixed together, they are called black powder because they appear black and their composition is unknown. The current researches mainly focus on the recovery of monomer materials, so it has poor practicability (Chen et al., 2015; Li et al., 2018a). Therefore, according to the demand of actual production, it is vital to study the mixture’s recycling.
Currently, the recovery methods of hybrid spent cathode materials mainly focus on hydrometallurgy, while there are few reports on pyrometallurgy because in the recycling of hybrid materials, it is necessary to consider the efficiency of the recovery of different metal elements. The hydrometallurgical process is a better treatment method to maximize waste disposal capacity, ensuring a high metal recovery rate. Wang et al. (2009) carry out a hydrochloric acid leach process, the conditions for leaching are 4 M hydrochloric acid solution, 80°C leaching temperature, 1 h leaching time and 20 mg·L−1 solid-to-liquid ratio, and the experimental setup for leaching and recovery material processes shown in Figure 4C. After leaching process, all the metal elements enter the solution as ions. Then different methods were used to extract different metal ions, firstly, KMnO4 is added to the solution as an oxidant with a certain stoichiometric ratio which the ratio of MnO−4 to Mn2+ is 2:3, and Mn2+ is oxidized to MnO2 and removed by filtration. Next, dimethylglyoxime (C4H8N2O2) is used to extract almost all nickel from the solution. In the case of ammonia complexation, the nickel-ammonium complexation ion will form a red solid with dimethylglyoxime, and the optimal reaction pH is 9, but too high a pH will cause side reaction. After nickel separation, ammonium cobalt complex ions were precipitated by chemical precipitation with a pH of 11. Cobalt can be almost completely separated by this method. The remaining solution is mainly LiCl, precipitated by Na2CO3 to obtain the product Li2CO3.
Similarly, Huang et al. (2016) also use HCl-assisted H2O2 to leach hybrid spent cathode (mixed LFP and LMO). After leaching, Fe3+, Mn2+/Mn3+, and Li+ ions coexist in the solution. The flow chart of the recycling process for different ions is shown in Figure 4D. In the first step of separation, [Tf2N] (ionic liquid structure precipitant), n-butyl xanthate, and α-Terpineol are added to the solution. In this process, Fe3+ translates into [Fe (bet)n] (Tf2N)3, which is sediment. The function of [Hbet] [Tf2N] is a kind of ionic liquid structure precipitant, n-butyl xanthate is the collector; meanwhile, α-Terpineol is used as a frother, which in order to better flotation [Fe (bet)n] (Tf2N)3. Then add HCl to convert it to FeCl3, the resulting [Hbet][Tf2N] recycling. Intriguingly, KMnO4 is used as an oxidizer to be added to the solution to react with Mn2+/Mn3+ to generate MnO2. At the same time, lithium is recovered as Li3PO4. This method allows the product to achieve a higher purity, the purity of lithium, ferrum, and manganese compounds can reach 99.32% ± 0.07%, 97.91% ± 0.05%, and 98.73% ± 0.05%, but this strategy has a low metal recovery rate of around 85%. It is not difficult to see from these two methods that the treatment of mixed materials is mainly to dissolve all the valuable metals in the mixed cathode materials and then take different measures to separate the metals. This seems to be a suitable method, but it is challenging to balance the recovery rate of metal ions and the product’s purity in the recycling process. The lengthy flow of processes leads to the loss of metal ions step by step, so we need to fig out a way to develop a recycling method that does both.
2.3 Treatment of LMO with high carbon content
It is well known that the composition of a LIB includes a cathode, anode, electrolyte, binder, and so on. Since the commercial use of LIBs, graphite has dominated the anode materials market due to its low cost and excellent performance (Zhang H. et al., 2021). Graphite reserves are relatively affluent, have a long service life, and have a high energy density, so it is widely used (Kravchyk and Kovalenko, 2019). Graphite not only has a high status as a material in LIBs, but also is an excellent reducing agent in LIBs recovery. Carbon is usually added as a reducing agent in the smelting of metals, depending on its excellent reducing properties and low price. According to the phase diagram, carbon has an excellent reducing effect on some metal oxides. Therefore, directly using the graphite in the anode material as a reducing agent to instantly recover the anode material is an environmentally friendly method. According to the level of carbon content in the target material, we can appropriately add carbon to ensure that the waste material can fully react. Figure 5A shows the process diagram of vacuum carbothermal reduction. Not only can graphite be directly added as a carbon source, but also natural carbon sources converted from biomass can be used.

FIGURE 5. (A) Schematic diagram of vacuum carbothermal reduction; (B) schematic diagram of LMO collapse mechanism and Li2CO3 formation during vacuum carbothermal reduction; Carbon, thermal reduction technology, can be carried out not only in a vacuum and low-pressure environment but also in an inert atmosphere. Lombardo et al.(Lombardo et al. (2019)) reported a method of recovering lithium carbonate in LCO, LMO and LNO by using carbon as reducing agent in a nitrogen atmosphere. The Ni, Co and Mn in it is successfully converted into metal or oxide. Lithium exists in the form of Li2CO3 and Li2O and is roasted at 700°C for 1.5 h. With the decomposition of the positive active material, the binder in it also completes the decomposition at high temperatures. However, during the pyrolysis process, the graphite was not completely reacted. Only a small part of the graphite participated in the reduction reaction, and the remaining graphite remained in the product.
Kondás et al. (2006) carry out an environmentally friendly roasted batteries operation. The scrap LIBs used in the recovery process are mainly a mixture of LMO, MnO2, graphite, and lithium metal, and the roasting process is achieved in a reduced pressure. In this process the lithium is converted into soluble Li2CO3 and insoluble MnO. The dissolved Li2CO3 in solution can be obtained by evaporation. However, in the process of evaporation, other salt impurities will also precipitate out synchronously, resulting in a decrease in the purity of Li2CO3.
Xiao et al. (2017b) also reported an oxygen-free roasting approach in which the scarp batteries were pulverized into powders less than 0.12 mm and roasted in an oxygen-free environment. During the roasting process, the organic binder breaks down to form a gas that is collected. After roasting, the product is treated with water, and the soluble Li2CO3 and residue can be obtained at 800°C for 45 min. Through XRD analysis of the product during roasting, Mn underwent a transformation from LiMn2O4 to Mn3O4 and then to MnO. In this process, graphite and carbon monoxide plays a key role in reducing manganese metal. The initial product of the reaction was analyzed by gas chromatography. The results showed that the CO2 content in the product decreased significantly and the CO content increased sharply in a small range between 727°C and 1,000°C. Under the synchronous action of carbon and CO, the transformation of Mn3O4 to MnO is realized. Interestingly, no phase of Li2CO3 was found in the product after vacuum sintering because Li2CO3 was highly dispersed in the product, and Li2CO3 could still be obtained after water leaching and evaporation. After vacuum reduction roasting, there is still graphite left in the residue, which is then removed and MnO converted into Mn3O4 product under the condition of oxidation and firing. In order to further investigate the reaction mechanism between graphite and overuse of LMO, the vacuum cleavage reduction process was studied in detail (Xiao et al., 2017a). Experimental results show that graphite and CO play a role in the process of Mn3O4 reduction to MnO, while CO has strong reducibility to reduce LMO to MnO at 600°C for 45 min. In addition, the reaction collapse mechanism of spinel structure LMO during the reaction was given by XRD. Firstly, some of the O atoms in the skeleton escape from their original positions, which causes the distorted Mn3O4 and Li2Mn2O4 to form at 400°C, which can be obtained from the XRD of the roasted product. Later, when the temperature rises to 600°C, a and b completely collapse to form MnO and the escaped O atom is captured by C/CO and Li to form Li2CO3, and diagram of this process is clearly shown in Figure 5B. Vacuum carbothermal reduction not only works on LMO, but also converts the lithium in NCM and LCO into Li2CO3 well. Carbon can play a very good role in the reduction of vacuum heating environment. The mechanism of the reaction process is described from the molecular lattice structure level, which is a good guide for the subsequent pyrometallurgical recovery LMO.
Pindar and Dhawan (2019) graphite was used to reduce the hybrid spent of LCO and LMO in an air atmosphere. After roasting at 800°C for 45 min, the transformation of excessive metal into metal and metal oxide was completed in this process, and lithium was successfully transformed into Li2CO3 and LiF, the Li2CO3 produced by this process is only 90% pure, with some LiF mixed in. The carbothermal reduction reaction can be achieved not only by heating, but also by microwave heating (Pindar and Dhawan, 2020a). After microwave treatment with 900 w power for 10 min, carbothermal reduction was completed and Li2CO3, MnO, Co, CoO and the remaining graphite were formed. After water leaching, separation and evaporation, a could still be obtained. The remaining water leaching products can be separated by different magnetic properties of the product. This strategy provides an efficient method for extracting lithium by carbothermal reduction in a short time with high treatment efficiency. But there is still the problem of low purity. On the basis of this, additional purification optimization steps of subsequent products may make the process more competitive. Furthermore, the author also proposed a kind of carbon heat plus acid leaching process specifically for LMO (Pindar and Dhawan, 2020b). Raw materials and graphite are roasted in Muffle furnace at 800°C for 30 min, then leached and separated, and product Li2CO3 can be obtained by evaporative crystallization of the obtained solution. The remaining residue is separated into a mixture of manganese oxide and graphite. After thermal exposure, the leaching rate of manganese oxide using organic acid solvent was greatly increased from 9% to 81%. Efficient metal recovery from leached slag and lithium in the form of Li2CO3 was achieved.
Makuza et al. (2021) also proposed a carbothermal reduction method to recover the mixed cathode active material, mainly composed of LCO, LMO, LNO, and the anode graphite. After roasting in a vacuum at 600°C for 30 min, the mixed raw material is converted into Li2CO3, Ni, Co, CoO, and MnO. To make the lithium in the roasted product better leached, the product was ball milled at 3,000 rmp for 1 min after roasting, and carbon dioxide was continuously pumped into the product during the water leaching process accompanied by ultrasound. Li2CO3 is converted into LiHCO3, which is more soluble in water. In this process, the leaching efficiency of lithium is improved. The resulting purity of a can reach 99.2%, with very little impurity content. The remaining metals and their oxides can be entirely dissolved by acid leaching. This method provides an excellent strategy to enhance the water-leaching process of the calcination products. After the conventional vacuum reduction, a series of operations such as dry grinding, carbon dioxide conversion, and ultrasonic greatly enhance the lithium recovery. In conclusion, the carbon thermal reduction method not only has a good effect in the process of treating pure LMO cathode materials but also hybrid materials.
3 Closed loop recycling of spent LMO
In order to achieve the sustainable development of the battery industry, it is necessary to attain closed-loop recycling, which uses recycled materials to regenerate battery materials and is in line with the current trend of resource recycling and sustainable utilization (Doose et al., 2021). Even so often, under different recycling methods, the treatment of spent cathode materials will produce other products, such as some transition metal sulfates, chlorides, nitrates, etc., (Tang et al., 2021; Barrios et al., 2022). In some cases, some research methods first separate lithium to achieve selective lithium extraction and then treat the rest of the metal compounds (Lin et al., 2020). Some researchers are turning recycled battery materials into valuable products (various sulfates, lithium carbonate, or other value-added products). Some of these valuable products can be used as raw materials for battery production, while some are made into other products (Huang et al., 2021). However, the best destination for the metal recovered from LIBs is still made into LIBs material, forming closed-loop recycling. This step requires higher recycling requirements (low impurity content of recycled raw materials and good electrochemical performance of the prepared battery). The excellent performance of a battery largely depends on the purity of spent batteries, treatment conditions, impurities disposal, and other factors (Huang et al., 2023). The following sections will discuss several methods of current regeneration from three aspects: regeneration of mixed waste, regeneration after separation and extraction, and direct renewal.
3.1 Mixed regeneration of spent LIBs
The mixed regeneration of waste lithium batteries refers to using two or more waste LIBs as raw materials to regenerate into new LIBs. This mixed regeneration mode has two significant advantages: First, it can simultaneously treat various waste LIBs, significantly improving recovery efficiency. Second, this method reduces the number of valuable metals added in the regeneration process, saves the cost of the regenerated lithium battery, and increases the profit space to realize its industrial feasibility.
In large-scale industrial recycling, the shorter the process, the more conducive to industrialization. Nie et al. (2019) reported a simple method to recover the cathode of the waste lithium manganate battery: After the waste lithium manganate battery is manually disassembled, the waste lithium manganate battery cathode is simply heat treated at 850°C, and the obtained product can be recycled as the cathode of the sodium ion battery. In this process, the purpose of heat treatment is to recrystallize the waste lithium manganate material on the one hand and volatilize impurities such as carbon black and PVDF in the material, on the other hand, to provide more pure cathode materials for sodium-ion batteries. Interestingly, the regenerated sodium cathode is assembled into a sodium ion battery for electrochemical testing. Its discharge capacity can gradually increase to 163.2 mAh·g−1 over 50 cycles at 100 mA·g−1, and the highest reversible capacity is up to 176.3 mAh·g−1 at 20 mA·g−1. The electrochemical tests show that the recycled LiMn2O4 as cathode material in SIBs has superior electrochemical properties such as high reversible capacity and excellent rate capability. This process utilizes the spontaneous ion exchange process during the battery cycle and simultaneously completes the two steps of removing Li from the cathode material and replenishing Na. The cathode material evolves from a spinel structure to a layered structure, which speeds up the diffusion rate of ions.
In addition, a more thorough material recovery can be achieved from spent LIBs. Meng et al. (2019) proposed a traditional mechanochemical Activation assisted solid-state technique to recover LMO and regenerate nano LiMnPO4/C, the flow chart is shown in Figure 6A. They dissolved the spent LMO polymer, NH3H2PO4, Li2CO3, and polyvinyl alcohol in proportion to ethyl alcohol, thoroughly mixed them, and dried them to obtain the precursor. LiMnPO4/C active material was finally acquired by calcining the precursor in an argon atmosphere at 650°C for 6 h and dropping to room temperature at a rate of 3°C/min. Electrochemical tests show that the active cathode material has promising electrochemical discharge capacity and excellent cycling performance. The traditional recycling and regeneration method often involves the removal of PVDF and conductive carbon in the battery to ensure the outstanding performance of the regenerative battery. This method makes full use of PVDF and conductive carbon, which were previously considered as “impurities”, so that The whole process has no separation and purification steps such as leaching and extraction, which significantly simplifies the process flow.
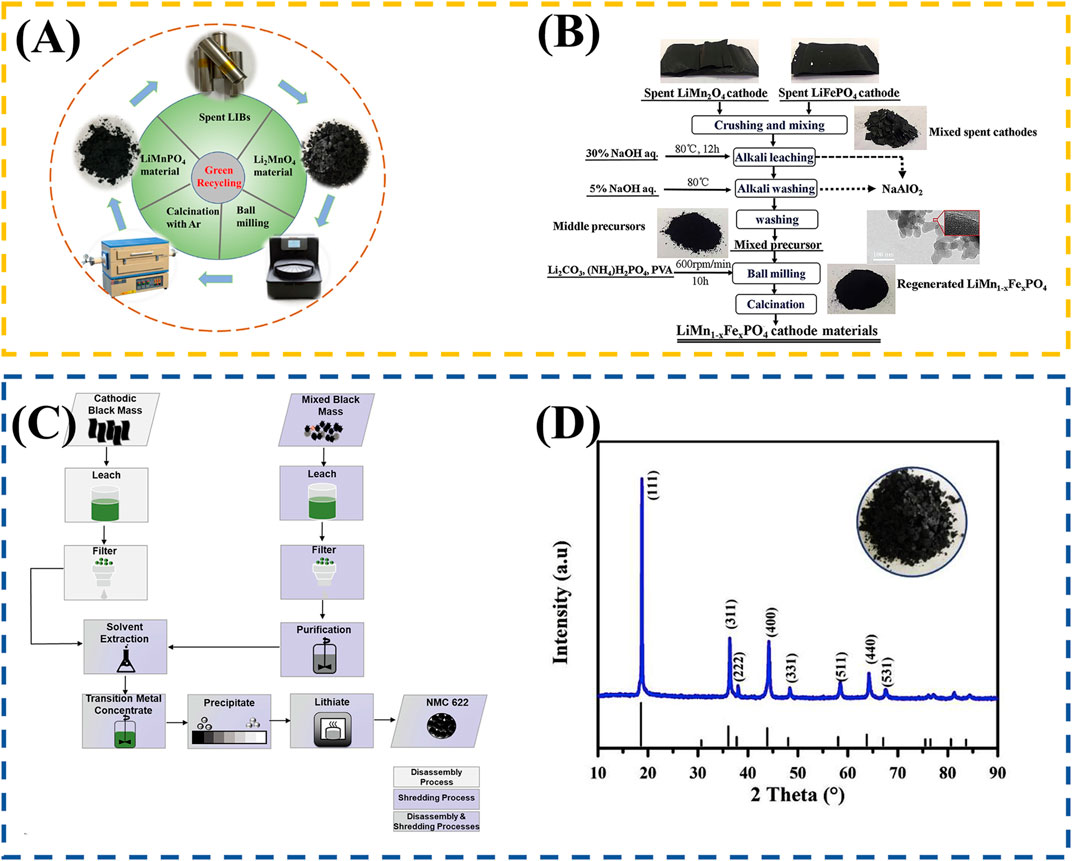
FIGURE 6. (A) Schematic of spent LMO and nano-LiMnPO4/C. (B) Schematic of the LMO and LFP recycling process; (C) Diagram of disassembly and shredding process applied for cathode black mass recovery; (D) XRD profiles of the spent LMO cathode materials.
Mechanical Activation assisted solid-state technique can be used not only for LMO recycling, but also both LMO and LFP recycling. Shi et al. (2020) continued to study the application of the above methods in the presence of two different types of LIBs, The whole process is shown in Figure 6B. Different from recycling, when only a single lithium battery type exists, this process further considers the impact of Al on the recycling process. It uses metallurgy-inspired aluminum leaching to remove the aluminum foil in the waste anode so that the Al content in the purified product is less than 300 ppm. The electrochemical test results show that LiMnxFe1-xPO4/C cathode material produced by co-recovery has good cycle stability and electrochemical capacity. This method provides a new idea for mixed recycling of multiple batteries and is a promising recycling idea for industrialization. Actually, in the recycling of waste lithium batteries, there is often more than one type of lithium battery, and the recycling process will be more complex, which is one of the reasons why more and more scholars have focused on the recycling of mixed LIBs in recent years. Gastol et al. (2022) recycled and regenerated the black mass obtained by shredding and disassembling, respectively. The disassembly and comminution process for cathode black block recovery is shown in Figure 6C. The black mass obtained by different means contains LMO and LiNi0.8Co0.15Al0.05O2. However, the difference is that the black mass obtained by shredding contains more aluminum and copper. The black mass obtained through disassembly is first treated by hydrometallurgy: excess sulfuric acid (95% w/w) and hydrogen peroxide (30% w/w) are used to dissolve transition metals and current collectors, and solid-liquid separation is carried out. The obtained liquid (containing dissolved metal solution) is extracted by liquid-liquid extraction to separate Al and Cu. The pure solution forms NCM hydroxide by adding 47% sodium hydroxide. The hydroxide is dissolved in sulfuric acid and added into nickel, cobalt, and manganese sulfate salts according to the stoichiometric ratio to reach Ni: Mn: Co = 6:2:2. Then, the regenerated cathode material is obtained through co-recycling and lithiation step. The recovery and regeneration steps for the black mass obtained through shredding are exactly the same as above, but there are two recovery situations: Impurity removal and non-impurity removal. The feasibility of process recovery is evaluated by comparing the purity of recovered substances in different processes, the regeneration performance, and the energy consumption of the whole process. It is worth noting that Al and Cu significantly impact the regenerated battery’s specific capacity. After multiple purifications, the performance of the regenerated battery is almost the same as that of the battery manufacturer.
3.2 Single-type regeneration of spent LIBs
Recycling lithium batteries is feasible after extracting and separating valuable substances from waste lithium batteries. Because the impurities introduced in the recycling process often affect the purity of the recovered material, to ensure the regenerated battery’s good electrochemical performance and better material utilization efficiency, other high-purity materials can often be added according to the recycling of battery waste to regenerate the battery.
Zhang et al. (2019) note that it could recover spent lithium-battery to regenerate lithium-battery with a promising electrochemical performance by using a process that contains leaching and co-precipitation. The whole process can be included as the next steps: spent LMO powder was attained by conventional detaching process, then a leaching process using HNO3(2 mol·L−1) and H2O2 (5% vol) as leaching was used to achieve precipitation as Mn source, and the filtrate enriched a large amount of Li. In this process, the high valence Mn (Mn3+and Mn4+) in the solid phase will be transformed into Mn2+and enter the liquid phase. Finally, after adding Ni source and Co source into the filtrate, coprecipitate to obtain Mn0.7Ni0.2Co0.1CO3 precursors, after adding Li, calcine to obtain regenerated cathode material. The recovered cathode material exhibit a promising electrochemical performance. However, there is no impurity removal step before co-recycling, which may make room for further improved battery performance. The XRD profiles of spent LiMO cathode materials are shown in Figure 6D.
Regeneration after extraction and separation has a thorny problem: secondary pollution caused by the use of inorganic acids in extraction. Yao et al. (2021) used citric acid as the leaching agent and glucose as the reducing agent to efficiently and environmentally leach the waste LMO, and re-synthesized LMO cathode materials by using the valuable ions in the leaching solution through the sol-gel method. XRD, TEM, and XPS were used to study the influence of different calcination temperatures on the structural morphology and surface chemical properties of the resynthesized LMO cathode materials. The Figure 7A exhibits the HRTEM image of resynthesized LMO. No other impurities were introduced in the whole process. The crystal morphology of the cathode material calcined at 650∼750°C was intact. The electrochemical performance test showed that the regenerated cathode material had an excellent electrochemical performance, and the discharge curves of LiMn2O4 have been shown in Figure 7B. Similarly, Wang J. et al. (2022) used citric acid and sol-gel method to regenerate LMO batteries but did not use glucose as a reducing agent. It explored the influence of citric acid concentration, leaching time, and solid-liquid ratio on the leaching process. Finally, under the condition of 1.0 M citric acid leaching for 60 min and solid-liquid ratio of 60 g·L−1, the leaching rate of metal Li and Mn was more than 94%. The action process of Mn (C6H6O7)·H2O in the leaching process was revealed by XRD, SEM, and XPS. After leaching, the sol-gel synthesized the LMO cathode material. It was found that the Jahn-Teller effect was suppressed under the action of trace Al, making the battery have good electrochemical performance.
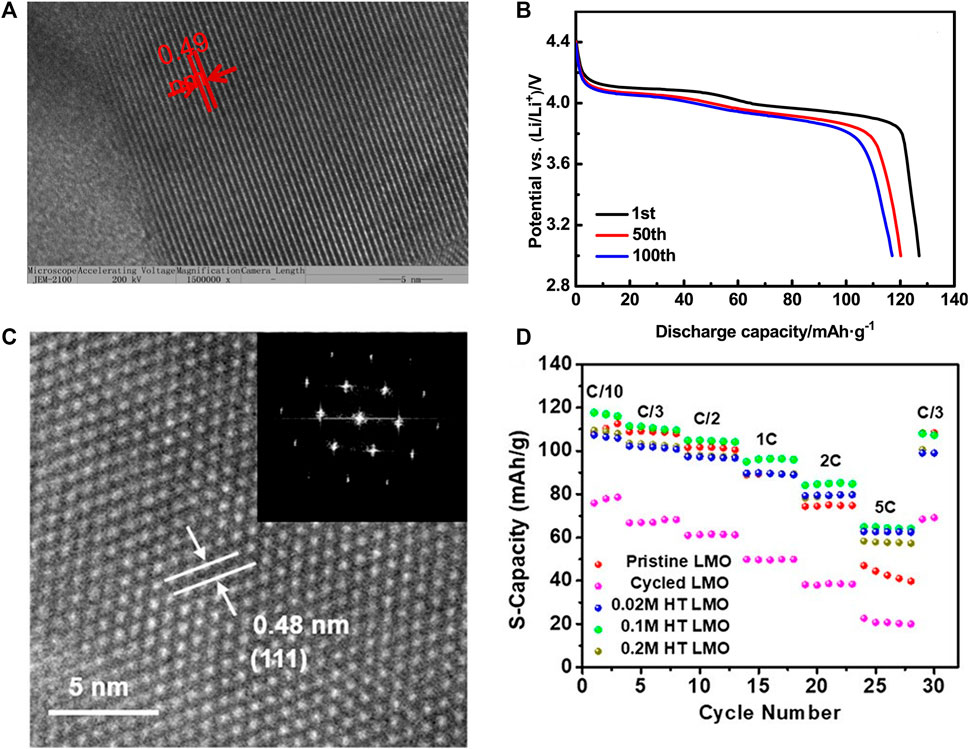
FIGURE 7. (A) HRTEM image of resynthesized LMO; (B) The discharge curves of LMO-750 at 1st, 50th, and 100th; (C) HRTEM images and FFT patterns of regenerated LMO particles in the bulk region; (D) Rate performance of different LMO samples.
3.3 Direct regeneration of LMO
In traditional hydrometallurgy, pyrometallurgy, and electrochemical metallurgy, the structure of the cathode material is almost destroyed, and all the valuable elements are separated. However, in the overused cathode materials of LIBs, some complete structures are destroyed by traditional methods, and the value of these structures is not reflected (Georgi-Maschler et al., 2012). Therefore, for some cathode materials with relatively complete structures, we can adopt this direct regeneration method to repair or supplement the damaged structure or the absence of some elements in the material to make it complete as before (Jiang et al., 2020). Therefore, this section mainly introduces some research methods on direct regeneration.
It is well known that the cathode material of LIB is attached to the collector by the polyvinylidene fluoride (PVDF) binder, which possesses low electrical conductivity and negatively affects the regeneration process (Zhao Y. et al., 2021). Before regeneration, the binder must be removed to ensure that the obtained material has excellent electrochemical properties. Liu et al. (2020) reported a hydrometallurgical LMO regeneration technology. The main idea of this technology is first to dissolve the P included in the LMO with a solvent, the solvent chosen here is N-methyl-2-pyrrolidone, then calcination of the treated material at 500°C for 12 h. In the process of hydrometallurgy regeneration, 86.7% of the active substance can be dissolved from the scrap at 60°C, stirring time 50 min, and solid-liquid ratio 80 g·L−1. The cathode material obtained after calcination also has good electrochemical performance.
Gao et al. (2020) developed a method of hydrothermal remediation of spent LMO, which first pretreats the waste cathode materials to remove the binder, carbon and other substances. The separated material was then placed together with a dilute solution and heated to 180°C in a Teflon-lined autoclave for 12 h, the optimum concentration of lithium hydroxide for the hydrothermal reaction was 0.1 M, and the regenerated cathode material was obtained. HRTEM image and FFT patterns of regenerated LMO particles in the bulk region is exhibited in Figure 7C. Not surprisingly, the repaired LMO material has a good phase structure. This method can be used to improve the LMO in one step, and the regenerated LMO has excellent electrochemical performance. The electrochemical performance is on par with that of commercial LMO. Figure 7D shows the rate performance of different LMO samples. The use of dilute LiOH solution and hydrothermal treatment to achieve material regeneration without using any acid and base is an excellent future development direction.
Wang and Whitacre (2018) simultaneously carried out experiments to repair LMO, which is solid-state and hydrothermal, and then compared the regeneration effects of these two methods. The solid-state phase method is mainly to ball mill and mixes the waste LMO at a molar ratio of 1:1, then roast the mixed material at 350°C for 2 h to repair the spent material. The residual lithium on the surface of the repaired material was cleaned, and afterward, it was annealed at 750°C for 6 h to get the final product. However, the hydrothermal reaction involves mixing LMO with a, dissolving it in deionized water, and heating it in a Teflon-lined stainless steel autoclave to 165°C for 24 h to get the final product. Comparing the electrochemical performance of regenerated LMO obtained by two different regeneration methods, the hydrothermal method has better electrochemical performance, similar to the commercial test results. Experiments show that the hydrothermal method has more flexibility and broader applicability in treating different resident lithium content of aged LMO compared with solid-state. The temperature of the solid-state process is only 350°C, at which all objects are in the solid phase. However, under high temperatures and high pressure in hydrothermal treatment, the solution strongly wraps the materials to be repaired, conducing to the regeneration process to a large extent and greatly helping to improve the performance of the recycled materials.
4 Future research directions
Currently, the installed quantity of LIBs equipped with olivine LFP, layered structure NCM and spinel structure LMO on the market is increasing yearly (Wang R. et al., 2022). After the service life of these batteries, they are bound to face severe treatment problems (Li et al., 2023). The number of spent cathode materials is enormous, a vast “urban mine” for present society. The main route is recycling spent battery materials with high efficiency, low energy consumption, and low pollution. Figure 8 shows the future development direction of spent battery recycling.
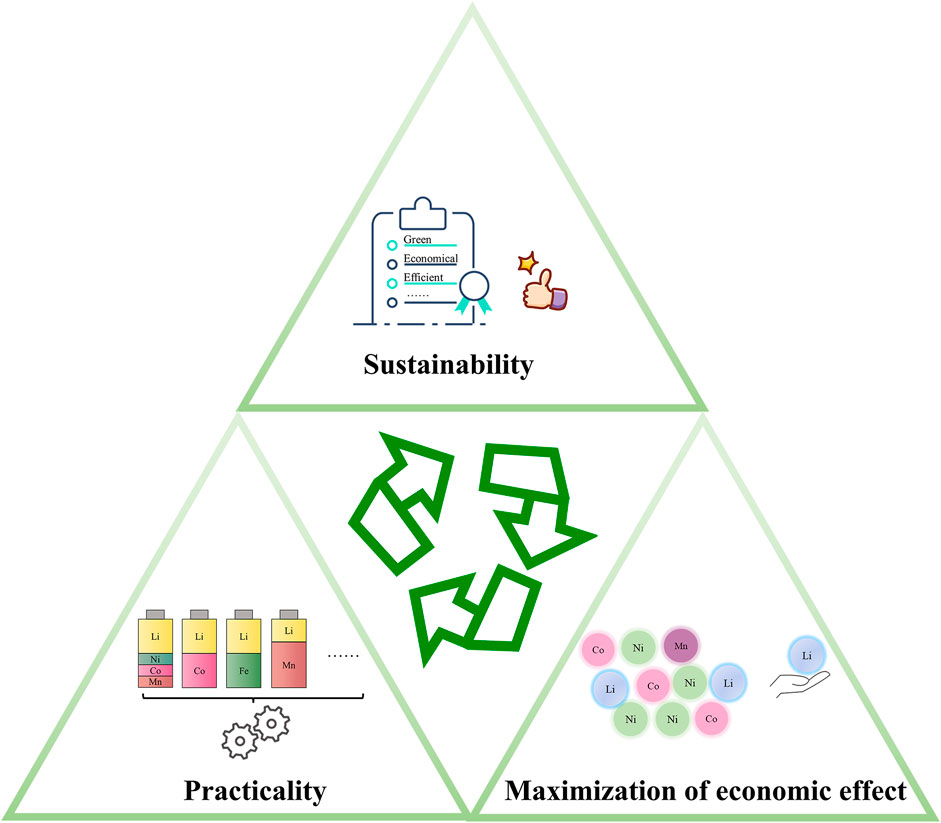
FIGURE 8. The future directions diagram for the future development direction of spent battery recycling.
4.1 Sustainability
Currently, there are many recycling methods in the laboratory research stage, but the premise of recycling is green chemistry (Jiang et al., 2021) and the sustainable recycling of resources is very important. In the face of increasingly severe environmental problems, this puts higher requirements for our research. In the recycling process, try to reduce the possible use of drugs that are harmful to the environment and as little as the potential discharge of sewage with high salt content. Carbon thermal reduction using local materials as reducing agent anode to achieve the best use of materials is a good development direction.
4.2 Maximization of economic effect
With the rapid production of LIBs, the demand for lithium resources is increasing, which directly leads to the rise of lithium carbonate, lithium hydroxide, and a series of related lithium product prices. Ministry of Industry and Information Technology of the People’s Republic of China has proposed a recycling standard for the industry in China, with a recovery rate of 85% for lithium and 98% for other metals element. The selective extraction of lithium first extracts the lithium, and the extraction rate of lithium can be over 94%. While other metals are present in the residue, then the residue is treated. This way can reduce the loss of lithium to a large extent, improving the utilization of resources and resulting in vigorous development, maximizing the economic effect.
4.3 Practicality
Nowadays, there is a variety of LIBs on the market. For different materials recycling, different recycling strategies should be adopted to fit it. However, in the face of such a wide variety of materials (high carbon content, high impurity content, more than two kinds of hybrid materials), developing a process for each raw material in the industry is difficult. The spent raw materials usually recovered by recycling enterprises are usually a mixture of a variety of positive electrode materials. Therefore, it is necessary to study the recycling strategy of mixed materials, improving the practicability of the process.
5 Conclusion
Based on the demand of LIBs for Li, Ni, Co, Mn and other metals, this review emphasizes the importance of recycling spent LIBs. The recovery methods of different components of the same LMO cathode material were summarized, and the advantages and disadvantages of different materials for different recovery processes were discussed. Finally, the future research directions have been provided for promoting the recycling of spent LIBs. Overall, this review plays an important role in helping to understand current LMO recycling processes.
Author contributions
XL organized and wrote the manuscript. ZL collected the data. JZ, DP, WH, YZ, PL, and LS discussed the results. XW, SW, and JZ guided the paper. All authors approved this manuscript.
Funding
This work was financially supported by National Natural Science Foundation of China (51902347 and 52202338).
Conflict of interest
Authors PL and SS were employed by Anhui Winking New Material Technology Co., Ltd.
The remaining authors declare that the research was conducted in the absence of any commercial or financial relationships that could be construed as a potential conflict of interest.
Publisher’s note
All claims expressed in this article are solely those of the authors and do not necessarily represent those of their affiliated organizations, or those of the publisher, the editors and the reviewers. Any product that may be evaluated in this article, or claim that may be made by its manufacturer, is not guaranteed or endorsed by the publisher.
References
Barrios, O. C., González, Y. C., Barbosa, L. I., and Orosco, P. (2022). Chlorination roasting of the cathode material contained in spent lithium-ion batteries to recover lithium, manganese, nickel and cobalt. Miner. Eng. 176, 107321. doi:10.1016/j.mineng.2021.107321
Chang, D., Yang, S., Shi, P., Jie, Y., Hu, F., Fang, G., et al. (2022). Selective recovery of lithium and efficient leaching of transition metals from spent LiNixCoyMnzO2 batteries based on a synergistic roasting process. Chem. Eng. J. 449, 137752. doi:10.1016/j.cej.2022.137752
Chen, H., Gu, S., Guo, Y., Dai, X., Zeng, L., Wang, K., et al. (2021). Leaching of cathode materials from spent lithium-ion batteries by using a mixture of ascorbic acid and HNO3. Hydrometallurgy 205, 105746. doi:10.1016/j.hydromet.2021.105746
Chen, X., Xu, B., Zhou, T., Liu, D., Hu, H., Fan, S., et al. (2015). Separation and recovery of metal values from leaching liquor of mixed-type of spent lithium-ion batteries. Sep. Purif. Technol. 144, 197–205. doi:10.1016/j.seppur.2015.02.006
Chen, X., Ma, H., Luo, C., and Zhou, T. (2017). Recovery of valuable metals from waste cathode materials of spent lithium-ion batteries using mild phosphoric acid. J. Hazard. Mater. 326, 77–86. doi:10.1016/j.jhazmat.2016.12.021
Ciez, R. E., and Whitacre, J. F. (2019). Examining different recycling processes for lithium-ion batteries. Nat. Sustain. 2 (2), 148–156. doi:10.1038/s41893-019-0222-5
Doose, S., Mayer, J. K., Michalowski, P., and Kwade, A. (2021). Challenges in ecofriendly battery recycling and closed material cycles: A perspective on future lithium battery generations. Metals 11 (2), 291. doi:10.3390/met11020291
Fan, E., Yang, J., Huang, Y., Lin, J., Arshad, F., Wu, F., et al. (2020). Leaching mechanisms of recycling valuable metals from spent lithium-ion batteries by a malonic acid-based leaching system. ACS Appl. Energy Mater. 3 (9), 8532–8542. doi:10.1021/acsaem.0c01166
Fan, X., Song, C., Lu, X., Shi, Y., Yang, S., Zheng, F., et al. (2021). Separation and recovery of valuable metals from spent lithium-ion batteries via concentrated sulfuric acid leaching and regeneration of LiNi1/3Co1/3Mn1/3O2. J. Alloys Compd. 863, 158775. doi:10.1016/j.jallcom.2021.158775
Gao, H., Yan, Q., Xu, P., Liu, H., Li, M., Liu, P., et al. (2020). Efficient direct recycling of degraded LiMn2O4 cathodes by one-step hydrothermal relithiation. ACS Appl. Mater Interfaces 12 (46), 51546–51554. doi:10.1021/acsami.0c15704
Garole, D. J., Hossain, R., Garole, V. J., Sahajwalla, V., Nerkar, J., and Dubal, D. P. (2020). Recycle, recover and repurpose strategy of spent Li-ion batteries and catalysts: Current status and future opportunities. ChemSusChem 13 (12), 3079–3100. doi:10.1002/cssc.201903213
Gastol, D., Marshall, J., Cooper, E., Mitchell, C., Burnett, D., Song, T., et al. (2022). Reclaimed and up-cycled cathodes for lithium-ion batteries. Glob. Challenges 6, 2200046. doi:10.1002/gch2.202200046
Georgi-Maschler, T., Friedrich, B., Weyhe, R., Heegn, H., and Rutz, M. (2012). Development of a recycling process for Li-ion batteries. J. Power Sources 207, 173–182. doi:10.1016/j.jpowsour.2012.01.152
Guoxing, R., Songwen, X., Meiqiu, X., Bing, P., Youqi, F., Fenggang, W., et al. (2016). “Recovery of valuable metals from spent lithium-ion batteries by smelting reduction process based on MnO-SiO2-Al2O3Slag system,” in Advances in molten slags, fluxes, and salts, 211–218.
He, L. P., Sun, S. Y., Song, X. F., and Yu, J. G. (2017). Leaching process for recovering valuable metals from the LiNi1/3Co1/3Mn1/3O2 cathode of lithium-ion batteries. Waste Manag. 64, 171–181. doi:10.1016/j.wasman.2017.02.011
He, S., and Liu, Z. (2020a). Efficient process for recovery of waste LiMn2O4 cathode material precipitation thermodynamic analysis and separation experiments. Waste Manag. 113, 105–117. doi:10.1016/j.wasman.2020.05.042
He, S., and Liu, Z. (2020b). Efficient process for recovery of waste LiMn2O4 cathode material: Low-temperature (NH4)2SO4 calcination mechanisms and water-leaching characteristics. Waste Manag. 108, 28–40. doi:10.1016/j.wasman.2020.04.030
Huang, B., Pan, Z., Su, X., and An, L. (2018). Recycling of lithium-ion batteries: Recent advances and perspectives. J. Power Sources 399, 274–286. doi:10.1016/j.jpowsour.2018.07.116
Huang, T., Zhang, S. W., Zhou, L., Tao, H., and Li, A. (2021). Synergistic effect of ultrasonication and sulfate radical on recovering cobalt and lithium from the spent lithium-ion battery. J. Environ. Manage 305, 114395. doi:10.1016/j.jenvman.2021.114395
Huang, Y., Han, G., Liu, J., Chai, W., Wang, W., Yang, S., et al. (2016). A stepwise recovery of metals from hybrid cathodes of spent Li-ion batteries with leaching-flotation-precipitation process. J. Power Sources 325, 555–564. doi:10.1016/j.jpowsour.2016.06.072
Huang, Z., Liu, X., Zheng, Y., Wang, Q., Liu, J., and Xu, S. (2023). Boosting efficient and low-energy solid phase regeneration for single crystal LiNi0.6Co0.2Mn0.2O2 via highly selective leaching and its industrial application. Chem. Eng. J. 451, 139039. doi:10.1016/j.cej.2022.139039
Ji, G., Ou, X., Zhao, R., Zhang, J., Zou, J., Li, P., et al. (2021). Efficient utilization of scrapped LiFePO4 battery for novel synthesis of Fe2P2O7/C as candidate anode materials. Resour. Conservation Recycl. 174, 105802. doi:10.1016/j.resconrec.2021.105802
Jiang, G., Zhang, Y., Meng, Q., Zhang, Y., Dong, P., Zhang, M., et al. (2020). Direct regeneration of LiNi0.5Co0.2Mn0.3O2 cathode from spent lithium-ion batteries by the molten salts method. ACS Sustain. Chem. Eng. 8 (49), 18138–18147. doi:10.1021/acssuschemeng.0c06514
Jiang, Y., Chen, X., Yan, S., Li, S., and Zhou, T. (2021). Pursuing green and efficient process towards recycling of different metals from spent lithium-ion batteries through Ferro-chemistry. Chem. Eng. J. 426, 131637. doi:10.1016/j.cej.2021.131637
Kim, T., Song, W., Son, D.-Y., Ono, L. K., and Qi, Y. (2019). Lithium-ion batteries: Outlook on present, future, and hybridized technologies. J. Mater. Chem. A 7 (7), 2942–2964. doi:10.1039/c8ta10513h
Kondás, J., Jandová, J., and Nemeckova, M. (2006). Processing of spent Li/MnO2 batteries to obtain Li2CO3. Hydrometallurgy 84 (3-4), 247–249. doi:10.1016/j.hydromet.2006.05.009
Kravchyk, K. V., and Kovalenko, M. V. (2019). Rechargeable dual-ion batteries with graphite as a cathode: Key challenges and opportunities. Adv. Energy Mater. 9 (35), 1901749. doi:10.1002/aenm.201901749
Kumar, M. S., and Revankar, S. T. (2017). Development scheme and key technology of an electric vehicle: An overview. Renew. Sustain. Energy Rev. 70, 1266–1285. doi:10.1016/j.rser.2016.12.027
Leal, V. M., Ribeiro, J. S., Coelho, E. L. D., and Freitas, M. B. J. G. (2022). Review: Recycling of spent lithium-ion batteries as a sustainable solution to obtain raw materials for different applications. J. Energy Chem. 79, 118–134. doi:10.1016/j.jechem.2022.08.005
Li, L., Bian, Y., Zhang, X., Guan, Y., Fan, E., Wu, F., et al. (2018a). Process for recycling mixed-cathode materials from spent lithium-ion batteries and kinetics of leaching. Waste Manag. 71, 362–371. doi:10.1016/j.wasman.2017.10.028
Li, L., Bian, Y., Zhang, X., Xue, Q., Fan, E., Wu, F., et al. (2018b). Economical recycling process for spent lithium-ion batteries and macro- and micro-scale mechanistic study. J. Power Sources 377, 70–79. doi:10.1016/j.jpowsour.2017.12.006
Li M., M., Lu, J., Chen, Z., and Amine, K. (2018). 30 Years of lithium-ion batteries. Adv. Mater 30, e1800561. doi:10.1002/adma.201800561
Li, X., Liu, S., Yang, J., He, Z., Zheng, J., and Li, Y. (2023). Electrochemical methods contribute to the recycling and regeneration path of lithium-ion batteries. Energy Storage Mater. 55, 606–630. doi:10.1016/j.ensm.2022.12.022
Li, Y., Lv, W., Huang, H., Yan, W., Li, X., Ning, P., et al. (2021). Recycling of spent lithium-ion batteries in view of green chemistry. Green Chem. 23 (17), 6139–6171. doi:10.1039/d1gc01639c
Li, Z., He, L., Zhao, Z. w., Wang, D., and Xu, W. (2019). Recovery of lithium and manganese from scrap LiMn2O4 by slurry electrolysis. ACS Sustain. Chem. Eng. 7 (19), 16738–16746. doi:10.1021/acssuschemeng.9b04127
Liang, J., Wang, D., Wang, L., Li, H., Cao, W., and Yan, H. (2021). Electrochemical process for recovery of metallic Mn from waste LiMn2O4-based Li-ion batteries in NaCl−CaCl2 melts. Int. J. Minerals, Metallurgy Mater. 29 (3), 473–478. doi:10.1007/s12613-020-2144-7
Lin, J., Li, L., Fan, E., Liu, C., Zhang, X., Cao, H., et al. (2020). Conversion mechanisms of selective extraction of lithium from spent lithium-ion batteries by sulfation roasting. ACS Appl. Mater Interfaces 12 (16), 18482–18489. doi:10.1021/acsami.0c00420
Liu, B., Huang, Q., Su, Y., Sun, L., Wu, T., Wang, G., et al. (2019). Maleic, glycolic and acetoacetic acids-leaching for recovery of valuable metals from spent lithium-ion batteries: Leaching parameters, thermodynamics and kinetics. R. Soc. Open Sci. 6 (9), 191061. doi:10.1098/rsos.191061
Liu, D., Zhang, Y., and Su, Z. (2020). Hydrometallurgical regeneration of LiMn2O4 cathode scrap material and its electrochemical properties. ChemistrySelect 5 (22), 6697–6704. doi:10.1002/slct.201904792
Lombardo, G., Ebin, B., Foreman, St. J. M. R., Steenari, B.-M., and Petranikova, M. (2019). Chemical transformations in Li-ion battery electrode materials by carbothermic reduction. ACS Sustain. Chem. Eng. 7 (16), 13668–13679. doi:10.1021/acssuschemeng.8b06540
Luo, Y., Yin, C., Ou, L., and Zhang, C. (2022). Highly efficient dissolution of the cathode materials of spent Ni–Co–Mn lithium batteries using deep eutectic solvents. Green Chem. 24 (17), 6562–6570. doi:10.1039/d2gc01431a
Maisel, F., Neef, C., Marscheider-Weidemann, F., and Nissen, N. F. (2023). A forecast on future raw material demand and recycling potential of lithium-ion batteries in electric vehicles. Resour. Conservation Recycl. 192, 106920. doi:10.1016/j.resconrec.2023.106920
Makuza, B., Yu, D., Huang, Z., Tian, Q., and Guo, X. (2021). Dry grinding - carbonated ultrasound-assisted water leaching of carbothermally reduced lithium-ion battery black mass towards enhanced selective extraction of lithium and recovery of high-value metals. Resour. Conservation Recycl. 174, 105784. doi:10.1016/j.resconrec.2021.105784
Meng, Q., Duan, J., Zhang, Y., and Dong, P. (2019). Novel efficient and environmentally friendly recovering of high performance nano-LiMnPO4/C cathode powders from spent LiMn2O4 batteries. J. Industrial Eng. Chem. 80, 633–639. doi:10.1016/j.jiec.2019.08.051
Meshram, P., Pandey, B. D., and Abhilash, (2019). Perspective of availability and sustainable recycling prospects of metals in rechargeable batteries – a resource overview. Resour. Policy 60, 9–22. doi:10.1016/j.resourpol.2018.11.015
Nematollahi, O., Hoghooghi, H., Rasti, M., and Sedaghat, A. (2016). Energy demands and renewable energy resources in the Middle East. Renew. Sustain. Energy Rev. 54, 1172–1181. doi:10.1016/j.rser.2015.10.058
Nie, X.-J., Xi, X.-T., Yang, Y., Ning, Q.-L., Guo, J.-Z., Wang, M.-Y., et al. (2019). Recycled LiMn2O4 from the spent lithium ion batteries as cathode material for sodium ion batteries: Electrochemical properties, structural evolution and electrode kinetics. Electrochimica Acta 320, 134626. doi:10.1016/j.electacta.2019.134626
Palmer, G. (2019). Renewables rise above fossil fuels. Nat. Energy 4 (7), 538–539. doi:10.1038/s41560-019-0426-y
Paulino, J. F., Busnardo, N. G., and Afonso, J. C. (2008). Recovery of valuable elements from spent Li-batteries. J. Hazard Mater 150 (3), 843–849. doi:10.1016/j.jhazmat.2007.10.048
Pindar, S., and Dhawan, N. (2019). Carbothermal reduction of spent mobile phones batteries for the recovery of lithium, cobalt, and manganese values. Jom 71 (12), 4483–4491. doi:10.1007/s11837-019-03799-9
Pindar, S., and Dhawan, N. (2020a). Microwave processing of electrode active materials for the recovery of cobalt, manganese, and lithium. Min. Metallurgy Explor. 37 (4), 1285–1295. doi:10.1007/s42461-020-00230-9
Pindar, S., and Dhawan, N. (2020b). Recycling of discarded coin cells for recovery of metal values. Miner. Eng. 159, 106650. doi:10.1016/j.mineng.2020.106650
Ren, G.-x., Xiao, S.-w., Xie, M.-q., Pan, B., Chen, J., Wang, F.-g., et al. (2017). Recovery of valuable metals from spent lithium ion batteries by smelting reduction process based on FeO–SiO2 –Al2O3slag system. Trans. Nonferrous Metals Soc. China 27 (2), 450–456. doi:10.1016/s1003-6326(17)60051-7
Shi, H., Zhang, Y., Dong, P., Huang, X., He, J., Duan, J., et al. (2020). A facile strategy for recovering spent LiFePO4 and LiMn2O4 cathode materials to produce high performance LiMnxFe1-xPO4/C cathode materials. Ceram. Int. 46 (8), 11698–11704. doi:10.1016/j.ceramint.2020.01.201
Tang, Y., Qu, X., Zhang, B., Zhao, Y., Xie, H., Zhao, J., et al. (2021). Recycling of spent lithium nickel cobalt manganese oxides via a low-temperature ammonium sulfation roasting approach. J. Clean. Prod. 279, 123633. doi:10.1016/j.jclepro.2020.123633
Wang, H., and Whitacre, J. F. (2018). Direct recycling of aged LiMn2O4 cathode materials used in aqueous lithium-ion batteries: Processes and sensitivities. Energy Technol. 6 (12), 2429–2437. doi:10.1002/ente.201800315
Wang, J., Huang, K., Dong, H., Lu, Y., Liu, K., Chen, Z., et al. (2022). A green process for recycling and synthesis of cathode materials LiMn2O4 from spent lithium-ion batteries using citric acid. RSC Adv. 12 (36), 23683–23691. doi:10.1039/d2ra04391b
Wang, R.-C., Lin, Y.-C., and Wu, S.-H. (2009). A novel recovery process of metal values from the cathode active materials of the lithium-ion secondary batteries. Hydrometallurgy 99 (3-4), 194–201. doi:10.1016/j.hydromet.2009.08.005
Wang, R., Zhang, Y., Sun, K., Qian, C., and Bao, W. (2022). Emerging green technologies for recovery and reuse of spent lithium-ion batteries – A review. J. Mater. Chem. A 10 (33), 17053–17076. doi:10.1039/d2ta03295c
Wang, Y. Y., Diao, W. Y., Fan, C. Y., Wu, X. L., and Zhang, J. P. (2019). Benign recycling of spent batteries towards all-solid-state lithium batteries. Chemistry 25 (38), 8975–8981. doi:10.1002/chem.201900845
Windisch-Kern, S., Gerold, E., Nigl, T., Jandric, A., Altendorfer, M., Rutrecht, B., et al. (2022). Recycling chains for lithium-ion batteries: A critical examination of current challenges, opportunities and process dependencies. Waste Manag. 138, 125–139. doi:10.1016/j.wasman.2021.11.038
Wuschke, L., Jackel, H. G., Leissner, T., and Peuker, U. A. (2019). Crushing of large Li-ion battery cells. Waste Manag. 85, 317–326. doi:10.1016/j.wasman.2018.12.042
Xiao, J., Li, J., and Xu, Z. (2017a). Novel approach for in situ recovery of lithium carbonate from spent lithium ion batteries using vacuum metallurgy. Environ. Sci. Technol. 51 (20), 11960–11966. doi:10.1021/acs.est.7b02561
Xiao, J., Li, J., and Xu, Z. (2017b). Recycling metals from lithium ion battery by mechanical separation and vacuum metallurgy. J. Hazard Mater 338, 124–131. doi:10.1016/j.jhazmat.2017.05.024
Xiaowei, D., Wenkun, Z., Zhongkui, R., Min, X., Juan, C., and Xiaohan, R. (2022). Recycling of lithium batteries—a review. Energies 15, 1611. doi:10.3390/en15051611
Xie, J., Huang, K., Nie, Z., Yuan, W., Wang, X., Song, Q., et al. (2021). An effective process for the recovery of valuable metals from cathode material of lithium-ion batteries by mechanochemical reduction. Resour. Conservation Recycl. 168, 105261. doi:10.1016/j.resconrec.2020.105261
Xuan, W., Otsuki, A., and Chagnes, A. (2019). Investigation of the leaching mechanism of NMC 811 (LiNi0.8Mn0.1Co0.1O2) by hydrochloric acid for recycling lithium ion battery cathodes. RSC Adv. 9 (66), 38612–38618. doi:10.1039/c9ra06686a
Yan, G., Shaoyan, L., Songxu, X., and Jiali, Z. (2022). Status and Prospect of China's Energy Storage Development in 2021. Water Power 48, 4.
Yao, L., Xi, Y., Han, H., Li, W., Wang, C., and Feng, Y. (2021). LiMn2O4 prepared from waste lithium ion batteries through sol-gel process. J. Alloys Compd. 868, 159222. doi:10.1016/j.jallcom.2021.159222
Yuan, H., Tang, G., Liang, T., Guo, D., and Wang, Y. (2021). Toward net-zero base stations with integrated and flexible power supply in future networks. IEEE Netw. 35 (6), 50–56. doi:10.1109/mnet.011.2100252
Zhang, B., Qu, X., Chen, X., Liu, D., Zhao, Z., Xie, H., et al. (2021). A sodium salt-assisted roasting approach followed by leaching for recovering spent LiFePO4 batteries. J. Hazard. Mater. 424, 127586. doi:10.1016/j.jhazmat.2021.127586
Zhang, H., Yang, Y., Ren, D., Wang, L., and He, X. (2021). Graphite as anode materials: Fundamental mechanism, recent progress and advances. Energy Storage Mater. 36, 147–170. doi:10.1016/j.ensm.2020.12.027
Zhang, J., Hu, W., Zou, J., Wang, X., Li, P., Peng, D., et al. (2022). Directional high-value regeneration of lithium, iron, and phosphorus from spent lithium iron phosphate batteries. ACS Sustain. Chem. Eng. 10, 13424–13434. doi:10.1021/acssuschemeng.2c03997
Zhang, J., Li, B., Garg, A., and Liu, Y. (2018). A generic framework for recycling of battery module for electric vehicle by combining the mechanical and chemical procedures. Int. J. Energy Res. 42 (10), 3390–3399. doi:10.1002/er.4077
Zhang, X.-P., Ou, M., Song, Y., and Li, X. (2017). Review of Middle East energy interconnection development. J. Mod. Power Syst. Clean Energy 5 (6), 917–935. doi:10.1007/s40565-017-0335-7
Zhang, Y., Li, X., Chen, X., Koivula, R., and Xu, J. (2022). Tunnel manganese oxides prepared using recovered LiMn2O4 from spent lithium-ion batteries: Co adsorption behavior and mechanism. J. Hazard Mater 425, 127957. doi:10.1016/j.jhazmat.2021.127957
Zhang, Y., Zhang, Y., Zhang, Y., Dong, P., Meng, Q., and Xu, M. (2019). Novel efficient regeneration of high-performance Li1.2[Mn0.56Ni0.16Co0.08]O2 cathode materials from spent LiMn2O4 batteries. J. Alloys Compd. 783, 357–362. doi:10.1016/j.jallcom.2018.12.359
Zhao, J., Xi, X., Na, Q., Wang, S., Kadry, S. N., and Kumar, P. M. (2021). The technological innovation of hybrid and plug-in electric vehicles for environment carbon pollution control. Environ. Impact Assess. Rev. 86, 106506. doi:10.1016/j.eiar.2020.106506
Zhao, Y., Fang, L.-Z., Kang, Y.-Q., Wang, L., Zhou, Y.-N., Liu, X.-Y., et al. (2021). A novel three-step approach to separate cathode components for lithium-ion battery recycling. Rare Met. 40 (6), 1431–1436. doi:10.1007/s12598-020-01587-y
Zhou, Q. (2022). Analysis of China's lithium-ion battery (Li-ion battery) industry status in 2021. Available at: http://www.huaon.com/channel/trend/801313.html (Accessed.
Keywords: lithium-ion batteries, LMO cathode, solid waste disposal, recycling, regeneration, environmental protection
Citation: Lu X, Li Z, Zou J, Peng D, Hu W, Zhong Y, Li P, Su S, Wang X, Wang S, Zhao Z and Zhang J (2023) Spent lithium manganate batteries for sustainable recycling: A review. Front. Mater. 10:1152018. doi: 10.3389/fmats.2023.1152018
Received: 04 February 2023; Accepted: 01 March 2023;
Published: 20 March 2023.
Edited by:
Şaban Patat, Erciyes University, TürkiyeReviewed by:
Halil Şahan, Kayseri University, TürkiyeChengyan Wang, University of Science and Technology Beijing, China
Copyright © 2023 Lu, Li, Zou, Peng, Hu, Zhong, Li, Su, Wang, Wang, Zhao and Zhang. This is an open-access article distributed under the terms of the Creative Commons Attribution License (CC BY). The use, distribution or reproduction in other forums is permitted, provided the original author(s) and the copyright owner(s) are credited and that the original publication in this journal is cited, in accordance with accepted academic practice. No use, distribution or reproduction is permitted which does not comply with these terms.
*Correspondence: Xiaowei Wang, eWp5d3h3QGNzdS5lZHUuY24=; Zaowen Zhao, enp3NjY2QGhhaW5hbnUuZWR1LmNu; Jiafeng Zhang, eWp5empmQGNzdS5lZHUuY24=