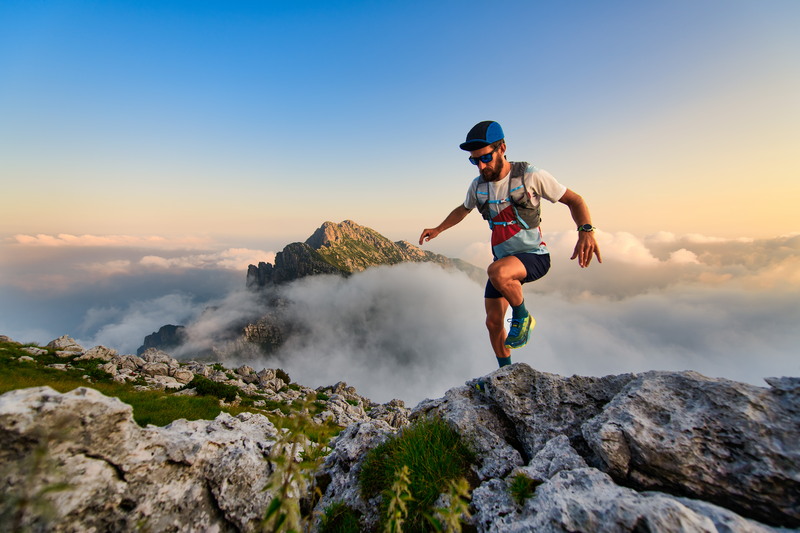
95% of researchers rate our articles as excellent or good
Learn more about the work of our research integrity team to safeguard the quality of each article we publish.
Find out more
ORIGINAL RESEARCH article
Front. Mater. , 07 July 2023
Sec. Polymeric and Composite Materials
Volume 10 - 2023 | https://doi.org/10.3389/fmats.2023.1138652
This article is part of the Research Topic Challenges and Emerging Issues on Firefighter’s Toxic Chemical Exposure: Smoke Chemicals, Contaminated PPE, and Off-gassing View all 10 articles
The concern for firefighters’ occupational exposure to harmful contaminants is growing due to the increase in health issues in the firefighting community. At such times, effective decontamination of personnel and equipment is an essential component of a hazard mitigation strategy. The current decontamination practices used for firefighter protective clothing have been shown to not be very effective. Hence, the scientific community is looking for several alternatives to conventional washing procedures. Liquid carbon dioxide (CO2) has been used in laundering and has distinct advantages over conventional dry-cleaning solvents such as perchloroethylene. The following study is aimed to assess how different washing procedures affect the durability of the turnout material. The study includes using three washing procedures on different samples: 1) conventional washing procedure, 2) liquid CO2 washing procedure, and 3) a high-temperature washing procedure. Samples for durability testing were constructed from a common aramid fabric used in firefighter turnout ensembles. These swatches were subjected to different washing techniques. The durability assessment was performed for physical testing of the samples, visual inspection, water repellency, and quantifying color changes using spectrophotometric analysis. The conventional wash and high-temperature washing affected the durability of the outer shell material in a significant manner. The liquid CO2 process did not affect the samples’ water repellency or physical strength. In contrast, conventional and high-temperature washing significantly affected the durability of the outer shell material. However, all samples met the criteria for tearing strength outlined in the NFPA 1971 standard subsection 7.1.11.
Firefighting is a challenging profession that includes working in a hazardous and dynamic environment. Protective clothing is the firefighter’s last line of defense to reduce the risk of injury in this environment. The coats and pants, which are referred to as turnout or bunker gear, are typically constructed from three layers of materials: an outer shell, a moisture barrier, and a thermal liner. The design and performance requirements for these materials are specified in the NFPA 1971Standard on Protective Ensembles for Structural Firefighting and Proximity Firefighting (NFPA, 1971; 2020). The outer shell protects firefighters from abrasion,cuts, and thermal threats. The most common fabrics used in turnouts include blends of polybenzimidazole (PBI), meta-aramid, and para-aramid fibers. To provide protection from splashes/sprays of water and flammable liquids, durable water and oil repellents finishes are applied to the outer shell materials. The moisture barrier, which offers protection from penetration of water, some chemicals, and bodily fluids, is made of polytetrafluoroethylene (PTFE) and polyurethane (PU) attached or laminated to a support fabric. The thermal liner is the innermost layer that provides thermal protection from heat (NFPA, 1971; 2020). The supplementary accessories include reflective trims, product labels, zippers, buckles, and hook-and-loop attachment points. The trim is an important element of the turnout gear as it aids the wearer’s ability to be noticed by fellow firefighters during fire suppression activities as well as roadside visibility when responding to motor vehicle accidents. The product label provides instructions to help firefighters take care of the turnout suits. Thus, the elements enhance the functionality of the turnout gear.
The NFPA 1851 Standard on Selection, Care, and Maintenance of Protective Ensembles for Structural Fire Fighting and Proximity Fire Fighting (referred to as the SCAM document) requires the retirement of the ensembles and elements no more than 10 years from the manufacturing date (NFPA, 2020; 2020). Thus, the turnout gear’s durability and continued performance is a critical parameter. The NFPA 1851 standard recommends washing guidelines from the durability perspective. The guidelines included in the standard for washing are: 1) temperature of the washing should not be greater than 40°C (105°F), 2) the G-force should be less than 100 G and the pH of the detergent should be between 6 and 10.5, and 3) the surfactant should not contain chlorine or oxidizing agents since oxidation can damage the aramid fibers of the outer shell. The standard has added a requirement for the turnout to receive at least two advanced cleaning per year (NFPA, 2020; 2020). All these guidelines make washing procedures less damaging to the gear but can also result in less effective cleaning processes.
The interim report of Research Foundation, NFPA in 2018 was based on research project to understand the cleaning practices. The report indicated shortcomings of the current turnout laundering practices (Research Foundation, 2018). Since then, a limited number of studies have been performed to assess the decontamination efficacy of the current the practices (Fent et al., 2017; Mayer et al., 2019; Mayer et al., 2020; Banks et al., 2021). Most of these studies marked the presence of polycyclic aromatic hydrocarbons (PAH)s and phthalates. These studies showed that decontamination of the turnout suits using current laundering practices is inefficient. The inefficiency is basically an incomplete removal of the foreground contaminants.
The NFPA 1851 standard has added cleaning validation of the laundering practices for independent service providers (ISP)s. The cleaning efficiency is calculated by measuring the differences of the pre-wash and post-wash concentration of the selected contaminants (NFPA, 2020; 2020). The sole purpose of any laundering practice is to maximize the removal of the contaminants. These findings led to investigations into alternative cleaning solutions such as modifying parameters including temperature and time, developing improved surfactants, and assessments of specialized cleaning such as liquid CO2 (Girase et al., 2022).
Along with chemical exposures, firefighters are also exposed to biological contamination when responding to fires as well as emergency medical situations. Along with chemical exposures, firefighters are also exposed to biological contamination. Bacterial contamination such as Staphylococcus aureus and Enterococcus faecalis has been reported in the occupational environment (Roberts, 2014; Farcas et al., 2019; McGuire-Wolfe, 2020). These bacteria can pose a risk to the health of firefighters, and it is essential to remove them from PPE during the cleaning process. However, removing contaminants from the personal protective ensemble (PPE) can be challenging, and several factors affect the removal of contaminants: temperature, time, chemistry, and mechanical action. Temperature is one of the important parameters that significantly impact cleaning and has shown a significant increase in the logarithmic reduction of microorganisms on fabric surfaces (Wiksell et al., 1973). So higher temperatures might seem a viable option to improve biological decontamination. But its impact on the physical properties of the turnout suits needs to be considered first.
Dry cleaning is a process of removing soil from textiles using a non-aqueous solvent. Perchloroethylene (PER) has been used conventionally in dry cleaning, but it is highly toxic to the human body (Sutanto et al., 2013). The environmental and health hazards due to PER led to producing “clean” technologies with fewer environmental concerns like low toxicity and low energy consumption. Carbon dioxide (CO2) gas is abundantly available in nature and at high pressure and low temperature, it turns into a supercritical liquid which offers several advantages, such as low viscosity surface tension that facilitates its penetration into the interstices of the fabric and improves cleaning efficiency (Dutschk et al., 2013). Liquid CO2 has been shown to effectively remove targeted foreground contamination from the outer shell material compared to the conventional washing method (Girase et al., 2022).
None of the above studies have assessed the impact of these laundering practices on the life of the PPE. Several questions remain unanswered, such as.
(1) What happens to the physical properties of the outer shell material after repeated laundering?
(2) What happens to the turnout suit if washed at a higher temperature?
(3) How durable are the water-repellent finishes applied on the outer shell material?
(4) How do specialized cleaning practices such as liquid CO2 affect the turnout suits?
Our previous research evaluated the comparative cleaning efficacy of conventional laundering and a liquid CO2 process (Girase et al., 2022). This follow on study aimed to assess the impact of multiple washing cycles of various techniques on the durability of the turnout suits. The comparative analysis of conventional and liquid CO2 to assess the cleaning efficiency was done; hence both these methods were kept consistent with the study described in (Girase et al., 2022). The outer shell material is accessorized with reflective trims and product labels to ensure the firefighters’ complete safety and instructions to maintain their turnout suits. The turnout suits need to last more than 5 years since they are very expensive. Thus, before incorporating any changes in the cleaning procedure, its impact on durability needs to be investigated.
To study the impact of various washing methods on the durability of the turnout suits and their accessories, outer shell swatches (26-inch × 26-inch) were constructed from a common PBI/aramid-based firefighter protective clothing material (7 oz) with a fluorinated durable water and oil repellent finish. These swatches were used to simulate the turnout suits in a controlled manner. The yellow-silver reflective trims were given by a major manufacturer and stitched to the outer shell material. An example of a finished swatch is shown in Figures 1A. The product labels were heat-pressed on the trim’s opposite side (assumed as an inner side) at 400°F for 10 s, as shown in Figures 1B. Every set contained five swatches, all accessorized with trims, and four of those were accessorized with product labels due to the limited availability of the product labels.
The swatches in every set were subjected to 30 washes for the respective method. It was decided that if there were any significant damage for 30 washes, another set of fabrics would be subjected to 15 washes using the same method to compare the results. Ballast material was used to make up the volume of 30 lbs. The ballast material for conventional and modified washing included outer shell material jackets. All ballast material was washed and air-dried before using them in the process. For liquid CO2, information about ballast material was not available. The objective was to assess the impact of the washing on the garment, and the assumption was that the turnout suits receive washing once every month. A separate set of four swatches was prepared, kept unwashed, and used as a controlled sample for future measurements. The sampling distribution is provided in Table 1.
The washing methods were as follows.
The conventional method was set up according to the NFPA 1851 guidelines (Table 2). A 45 lb capacity washer extractor (UNIMAC) was set to 40°C with a 60-min wash duration. A d-limonene-based commercial detergent (CD-1) was chosen due to its popularity in the firefighting community. The volume of the detergent used in each cycle was 120 mL based on the weight of the material washed. The amount of detergent was decided based on manufacturer’s recommendation. The cycle included 60 min of washing followed by 10 min of rinsing. This meant that the surfactant solution was in contact with the garment for a total of 60 min. In practice, the surfactant solution contact time experienced in cleaning by turnout cleaners or fire departments can vary from 20 to 40 min, and then rinsing with fresh water is followed. The period of contact was kept at 60 min to be consistent with our previous cleaning efficacy study (Girase et al., 2022) and to eliminate the variations in the volume of water during rinsing cycles.
The modified conventional method was added to assess the impact of higher washing temperatures on outer shell material. Hence, the washer extractor cycle was set to 65°C for 60 min. This was a significant increase in the temperature from the conventional washing technique. All other parameters were kept consistent with the conventional washing method (Table 2).
For liquid CO2 cleaning, two sets of swatches were shipped to Tersus Solutions (Denver, CO). One set was subjected to 15 washes, and other was subjected to 30 washes. Post-washing, all the samples were sent back for analysis. All the samples were stored in brown zip-lock bags and in the box to mitigate light exposure. The details of the method are provided in Table 3.
The outer shell material is the primary line of defense for firefighters. The outer shell material protects the firefighters from cuts, abrasion, etc. Thus, it is important to assess the tearing and breaking strength of the outer shell material. The test method covered the measurement of the tearing strength of the fabric by the trapezoid procedure. For tearing strength, the ASTM D5587 method was used (ASTM International, 2019). Ten swatches (5 in the warp direction and 5 in the weft direction) of size 3-inch × 6-inch were cut randomly from every set.
For breaking strength, the ASTM D5034 method was used (ASTM International, 2021). The test method determined the breaking force for the fabric. Ten swatches (5 in the warp direction and 5 in the weft direction) of size 4-inch × 6-inch were cut randomly from every set.
Contact angle measurements were used to study the impact of different washing procedures when subjected multiple times to the water-repellent finish. The Analytical Services Laboratory at Wilson College of Textiles was contracted for this testing. The Goniometer FDS Corporation Data physics optical contact angle system (Charlotte, NC) was used. For every set, 18 replicates of the fabrics were used of 1 cm diameter.
The working conditions of the firefighters are very harsh. The conspicuity of the firefighter is very important during fire rescue operations. The fluorescence of reflective trims enhances the conspicuity, which is important during partial light, night time work. The color measurement of the samples was performed on a spectrophotometer: Spectro-Guide sphere gloss S (Model 68-15-10) (BYK instruments, Chester, NY). For every set, the ΔE values were measured for the outer shell material, the reflective trim (yellow and silver strip), and the whiteness of the product label measured using L*. Every measurement was an average of measurements taken from random places on the sample. Due to limited availability of the resources, the retroreflectivity and the fluorescence testing was not performed on the trims.
Microsoft Excel was used to plot the bar graphs for all the testing data. The statistical analysis was done using JMP Pro® statistical software (15.2.0, SAS Institute Inc., Cary, NC) to perform the Shapiro-Wilks test to check the data’s normal distribution. Once the normality was confirmed, the singled tail t-test was done at a p-value of 0.05, assuming unequal variances. The tearing force was measured in Newtons, and to have a comprehensive analysis, the average of warp and weft directions were taken for statistical analysis.
The testing results are illustrated in Figure 2 (mean values with error bars representing standard errors). All the results were compared with the unwashed (control) samples. There was a significant drop in the tearing strength of the samples washed with conventional and modified methods. The Shapiro-Wilks test showed that the data was normally distributed. The p-values are shown in Table 4. The t-test results shown in Table 4 showed that the conventional and modified wash results were statistically significant. The results indicated that the surfactant solution could damage the fabric when kept for a longer period in contact with the fabric. The tearing strength decreased by 34.22% for conventionally washed samples and 32.04% for modified-washed samples. Generally, the conventional aqueous wash would have less than 60 min of contact time with the fabric. These results indicated the worst-case scenario for a conventional wash. For liquid CO2, there was no significant damage in the tearing strength. The liquid CO2 set washed 15 times did show a loss (4.44%) in the tearing strength compared to the 30 washes set that showed a 0.59% increase, which was inconsistent and was attributed to a research artifact. According to the criteria described in NFPA 1971 subsection 7.1.11 for the tearing strength (strength >100 N), all the fabrics passed the test (NFPA, 1971; 2020).
TABLE 4. Statistical test results for tearing strength (average of warp and weft direction) (p-values).
The peak load for the breaking strength testing was calculated in Newtons, and the results are illustrated in Figure 3 (arithmetic mean values with error bars representing standard errors). All the fabrics exceeded the performance requirements for breaking strength (>623 N) according to subsection 7.1.5 in NFPA 1971 (NFPA, 1971; 2020). For the grab test, the major hindrance was calculating peak load because the machine kept measuring the load even after the fabric was torn apart since some of the filaments were still intact. For conventionally washed samples, the breaking strength did not decrease much (0.08%), while the modified washed samples showed a significant decrease (29.28%) in the breaking strength. When the modified wash was considered, the only difference between the modified wash and conventional wash parameters was the higher washing temperature (65°C) in the modified wash. Thus, the higher temperature has an adverse effect on the breaking strength of the outer shell material. The results were statistically significant (p < 0.05) compared to control samples. The liquid CO2-washed samples showed a 6.47% decrease for 15-wash and a 6.97% decrease for 30 washes. This indicates that after a significant initial drop, liquid CO2 did not affect much subsequent washing. The p-values in Table 5 showed that results for modified washed samples are statistically significant.
TABLE 5. Statistical test results for breaking strength (average of warp and weft direction) (p-values).
The results from the contact angle measurements are illustrated in Figure 4. The water droplet schematics are shown in Figure 5. The control (unwashed) samples demonstrated high levels of water repellency. The fabrics washed multiple times using conventional and modified wash demonstrated hydrophilicity hence there were no measurements available. This showed that the washing process removed or damaged the water-repellent finish after multiple cycles. The important point to consider here is that this was longer than the usual-contact period of surfactant with the fabric for the conventional wash, demonstrating an extreme case for a conventional wash. This loss in repellency may be due to the adsorption of surfactants onto the surface of the fiber or the fabric’s abrasion also may have caused fragmentation of the fibers that can cause a loss in finishes (Arunyadej et al., 1998; Abdullah et al., 2006). It also meant that the conventional wash could affect the water-repellent finish over the years. The liquid CO2-washed fabrics demonstrated comparable results with the control samples. The water droplet did not absorb on the fabric surfaces washed with liquid CO2. Thus, the liquid CO2 wash used in this process did not impact the water-repellant finish applied to the outershell material. The goniometer results shown in Figure 4 for liquid CO2-15 washes and 30 washes indicate a very insignificant decline as the number of washes increased.
The effect of the different washes on the outer shell and reflective trim is shown in Figure 6. After 30 washes of the conventional wash method, the color of the outer shell faded, and the reflective trim peeled off. The peeling started after the 22nd wash, to be specific. The modified wash had a more severe effect on the reflective trim as more peeling was observed. Thus, temperatures as high as 65°C can damage the accessories of the outer shell material. There was no damage to the writing on the product labels, and they were legible from a 12-inch distance which is a requirement according to the NFPA 1971 standard subsection 8.41.4.2.2 (NFPA, 1971; 2020).
There was no damage to the product label due to conventional washing. Out of the four product labels, two of the product labels started to detach from the outer shell garment washed using a modified washing technique (Figure 7). This was at the end of the 27th washing cycle, to be specific. The instructions on the product labels were clear and easy to read for all the product labels.
For liquid CO2 washing, there was no significant color change in the outer shell material. The lack of mechanical agitation in the process can be a probable cause in the lack of physical damage to the accessories. However, the yellow color of the reflective trim was darkened. Even for 15 washes, the effect was visible. The whiteness of the product label was also lost somewhat for liquid CO2 washing, although the instructions were still discernible from a 12-inch distance.
The lightness index of the product labels is shown in Figure 8. The values for the conventional wash were comparable with control samples which illustrated that the conventional wash did not affect the whiteness of the product labels. Higher temperature affected the product label adversely, the lightness index was lost, and two out of four labels were detached from the outer shell. The lightness index of the product labels washed with the liquid CO2 technique was decreased, and there was a decreasing trend as the number of washes increased from 15 to 30 washes. There are two probable reasons for this: 1) An impurity was present either in the machine’s drum or in the particular batch of CO2 used for the washing cycle that was not filtered out efficiently. The point to ponder here is that if there was redeposition of a certain impurity, it was localized on trims and labels only since the outershell material did not show any color change. 2) The primary reason might be that the white dye used in the product label and the dyes in the product labels may be dissolved in the liquid CO2. Similarly, for the reflective trims (Figure 9), the color change was significant when washed with liquid CO2. The probable reasons are similar. The color change for the yellow stripe of the reflective trim was quantified using ΔE values relative to the control (unwashed) reflective trim. As seen from Figure 9, the ΔE values for the liquid CO2-washed reflective trim were higher as compared to the aqueous washes, which was evident from the visual comparisons as well. Further investigation into this matter is needed since only one kind of liquid CO2 process was used in the study. This change in the colors can also be situational.
The color change (ΔE) in the outershell materials for conventional and modified washing was higher (Figure 10). The mechanical agitation, longer surfactant contact time, and higher temperature all contributed to the color change. This might be because the agitation contributed to the fragmentation of the fibers that peeled off the dye and the finishes together. The inter-fabric friction, as well as continuous abrasion between the fabric and the drum part for a significantly longer duration, may have contributed to the color change of the fabric. For liquid CO2, there was no significant color change even after 30 washes. However, for the outer shell material, color change in the modified washed samples was higher. Thus, the aqueous wash with higher temperatures can adversely impact the outer shell material.
The durability study of the outer shell and its accessories showed that different washing techniques affect the outer shell and its accessories differently. The important outcome of this study was that repeated laundering has a significant impact on the physical properties of the PPE. In aqueous-based washing, the higher temperature both have an adverse effect on PPE. The mechanical agitation such as the frictional and abrasion among the fabrics and walls of the washing basket can contribute to degradation in the laundering process (Slater, 1991). The conventional wash used in this study was the representation of the effect of the surfactant solution on the garment if used for longer durations. If the duration for the contact of the surfactant solution to the conventional wash is considered an average of 30 min, then every single conventional wash represented in this study can be counted as double. Thus, the conventional wash of 30 times represents washing over 5 years if we consider the turnout suit receiving washing once every month. So, after 60 washes, the conventional wash can have an impact on the turnout suit and its accessories. Although the aqueous-based cleaning method showed decrease in the tearing strength, all the samples demonstrated tearing strength higher than the criteria set by the NFPA 1971 standard (tearing strength >100 N) (NFPA, 1971; 2020).
The only difference between the aqueous washes was modified wash used a higher temperature, Thus, the study showed the effects of higher temperatures on the turnout suits and their accessories. This answered the question of using the higher temperature to wash out the turnout suits. The breaking, tearing strength, and hydrophobicity of the outer shell material was lost after 30 washes of the modified washing technique. This could happen when it is washed frequently at higher temperatures. The modified wash used in the study includes a high temperature of 65°C. Hence, further investigation of the optimization of the number of washes, higher optimized temperature, and its effects need to be studied.
The liquid CO2 washing technique used in this study showed that it did not have any significant effect on the tearing strength, breaking strength, or water-repellent finish applied to the outer shell material. However, it had an impact on the reflective trim and product labels. The color change can be attributed to localized cross-contamination or the dissolving of the dye. This might be the only drawback of the liquid CO2 technique.
Limitations of this study are centered on the single sample type used. Only one type of outer shell material, reflective trim, and product label were used. A further study comprising various outer shell materials, moisture barriers, thermal liners, and accessories from different manufacturers needs to be completed to gain a more comprehensive understanding of the effects of different washing techniques on turnout suits. The flame retardant (FR) properties need to be tested to study the effect of different washing techniques. Given the limitations of this study and considering the previously demonstrated cleaning performance (Girase et al., 2022) and minimal impacts on the PPE durability, cleaning turnout gear in a liquid CO2 process is a potential option that can be incorporated as specialized cleaning into the NFPA 1851.
The original contributions presented in the study are included in the article/Supplementary Material, further inquiries can be directed to the corresponding authors.
Conceptualization, DT and RO; methodology, AG; software, AG; validation, DT, RO, and AG; writing—original draft preparation, AG; writing—review and editing, AG, RO; project administration, RO; funding acquisition, RO and DT. All authors contributed to the article and approved the submitted version.
The following project is funded by the Assistance to Firefighters Grant Program (AFG)—Fire Prevention and Safety (FP&S) Research and Development Grants (EMW-2017-FP-00601).
The author acknowledges the support of Steve Madsen from Tersus Solutions and Bill Brooks from Unimac.
The authors declare that the research was conducted in the absence of any commercial or financial relationships that could be construed as a potential conflict of interest.
All claims expressed in this article are solely those of the authors and do not necessarily represent those of their affiliated organizations, or those of the publisher, the editors and the reviewers. Any product that may be evaluated in this article, or claim that may be made by its manufacturer, is not guaranteed or endorsed by the publisher.
Abdullah, I., Blackburn, R. S., Russell, S. J., and Taylor, J. (2006). Abrasion phenomena in twill tencel fabric. J. Appl. Polym. Sci.102, 1391–1398. doi:10.1002/app.24195
Arunyadej, S., Mitchell, R., Walton, J., and Carr, C. M. (1998). An investigation into the effect of laundering on the repellency behaviour of a fluorochemical-treated cotton fabric. J. Text. Inst.89, 696–702. doi:10.1080/00405000.1998.11090908
Astm International, (2021). Astm d5034-21: Standard test method for breaking strength and elongation of textile fabrics. West Conshohocken, Pennsylvania, United States: ASTM International.
Astm International, (2019). ASTM d5587-15 standard test method for tearing strength of fabrics by trapezoid procedure. West Conshohocken, Pennsylvania, United States: ASTM International.
Banks, A. P. W., Wang, X., Engelsman, M., He, C., Osorio, A. F., and Mueller, J. F. (2021). Assessing decontamination and laundering processes for the removal of polycyclic aromatic hydrocarbons and flame retardants from firefighting uniforms. Environ. Res.194, 110616. doi:10.1016/j.envres.2020.110616
Dutschk, V., Sutanto, S., and Calvimontes, A. (2013). Cleanability of textile materials in liquid CO2. Tenside Surfactants Deterg.50, 21–25. doi:10.3139/113.110226
Farcas, D., Blachere, F. M., Kashon, M. L., Sbarra, D., Schwegler-Berry, D., Stull, J. O., et al. (2019). Survival of Staphylococcus aureus on the outer shell of fire fighter turnout gear after sanitation in a commercial washer/extractor. J. Occup. Med. Toxicol. Lond. Engl.14, 10. doi:10.1186/s12995-019-0230-4
Fent, K. W., Alexander, B., Roberts, J., Robertson, S., Toennis, C., Sammons, D., et al. (2017). Contamination of firefighter personal protective equipment and skin and the effectiveness of decontamination procedures. J. Occup. Environ. Hyg.14, 801–814. doi:10.1080/15459624.2017.1334904
Girase, A., Thompson, D., and Ormond, R. B. (2022). Comparative analysis of the liquid CO2 washing with conventional wash on Firefighters’ personal protective equipment (PPE). Textiles2, 632. doi:10.3390/textiles2040036
Mayer, A. C., Fent, K. W., Bertke, S., Horn, G. P., Smith, D. L., Kerber, S., et al. (2019). Firefighter hood contamination: Efficiency of laundering to remove PAHs and FRs. J. Occup. Environ. Hyg.16, 129–140. doi:10.1080/15459624.2018.1540877
Mayer, A. C., Horn, G. P., Fent, K. W., Bertke, S. J., Kerber, S., Kesler, R. M., et al. (2020). Impact of select PPE design elements and repeated laundering in firefighter protection from smoke exposure. J. Occup. Environ. Hyg.17, 505–514. doi:10.1080/15459624.2020.1811869
McGuire-Wolfe, , and Firefighters, C. (2020). Firefighters fighting germs - evaluation of a disinfecting protocol for use in the fire service. Infect. control Hosp. Epidemiol.41, s519–s520. doi:10.1017/ice.2020.1202
Nfpa, (2020). NFPA 1851 standard on selection, care and maintenance of PPE for structural and proximity firefighting. Quincy, MA, USA: NFPA.
Nfpa, (1971). Standard on protective ensembles for structural firefighting and proximity firefighting. Quincy, MA, USA: NFPA.
Research Foundation, N. (2018). PPE cleaning validation project interim report. Quincy, MA, USA: National Fire Protection Association.
Roberts, M. C., and No, D. B. (2014). Environment surface sampling in 33 Washington State fire stations for methicillin-resistant and methicillin-susceptible Staphylococcus aureus. Am. J. Infect. Control42, 591–596. doi:10.1016/j.ajic.2014.02.019
Sutanto, S., van Roosmalen, M. J. E., and Witkamp, G. J. (2013). Redeposition in CO2 textile dry cleaning. J. Supercrit. fluids81, 183–192. doi:10.1016/j.supflu.2013.05.013
Troynikov, O., Watson, C., Jadhav, A., Nawaz, N., and Kettlewell, R. (2016). Towards sustainable and safe apparel cleaning methods: A review. J. Environ. Manage.182, 252–264. doi:10.1016/j.jenvman.2016.07.078
Keywords: decontamination, liquid CO2, NFPA 1851, turnout, carcinogenic
Citation: Girase A, Thompson DB and Ormond RB (2023) Impact of conventional and advanced cleaning techniques on the durability of firefighter turnout ensembles. Front. Mater. 10:1138652. doi: 10.3389/fmats.2023.1138652
Received: 05 January 2023; Accepted: 26 June 2023;
Published: 07 July 2023.
Edited by:
Sabu Thomas, Mahatma Gandhi University, IndiaReviewed by:
Hafsa Jamshaid, National Textile University, PakistanCopyright © 2023 Girase, Thompson and Ormond. This is an open-access article distributed under the terms of the Creative Commons Attribution License (CC BY). The use, distribution or reproduction in other forums is permitted, provided the original author(s) and the copyright owner(s) are credited and that the original publication in this journal is cited, in accordance with accepted academic practice. No use, distribution or reproduction is permitted which does not comply with these terms.
*Correspondence: Arjunsing Girase, YWdnaXJhc2VAbmNzdS5lZHU=; R. Bryan Ormond, cmJvcm1vbmRAbmNzdS5lZHU=
Disclaimer: All claims expressed in this article are solely those of the authors and do not necessarily represent those of their affiliated organizations, or those of the publisher, the editors and the reviewers. Any product that may be evaluated in this article or claim that may be made by its manufacturer is not guaranteed or endorsed by the publisher.
Research integrity at Frontiers
Learn more about the work of our research integrity team to safeguard the quality of each article we publish.