- 1Institute for Mechanics of Materials and Structures (IMWS), TU Wien (Vienna University of Technology), Vienna, Austria
- 2Department of Materials Science, Polytechnic University of Madrid (UPM), Madrid, Spain
Computational homogenization based on FEM models is the gold standard when it comes to homogenization over a representative volume element (RVE), of so-called complex material microstructures, i.e., such which cannot be satisfactorily represented by an assemblage of homogeneous subdomains called phases. As a complement to the aforementioned models, which depend on the boundary conditions applied to the representative volume element and which, as a rule, do not give direct access to the macro-micro-relations in terms of concentration tensors, we here introduce a Green’s function-based homogenization method for arbitrary inhomogeneous microstructures: Inspired by the ideas underlying traditional phase-based homogenization schemes, such as the Mori-Tanaka or the self-consistent model, the new method rests on mapping, through the strain average rule, the microscopic strain fields associated with an auxiliary problem to the macroscopic strains subjected to the RVE. Thereby, the auxiliary problem is defined on a homogeneous infinite matrix subjected to homogeneous auxiliary strains and to inhomogeneous (fluctuating) polarization stresses representing the fluctuations of the microstiffness field, i.e., the complex microstructure within the RVE. The corresponding microscopic strains appear as the solution of a Fredholm integral equation, delivering a multilinear operator linking the homogeneous auxiliary strains to the microscopic strains. This operator, together with the aforementioned mapping, eventually allows for completing the model in terms of concentration tensor and homogenized stiffness quantification. This is illustrated by example of a sinusoidally fluctuating microstructure, whereby the corresponding singular convolution integrals are analytically evaluated from the solution of the Poisson’s equation, and this evaluation strategy is then analytically verified through a Cauchy principal value analysis, and numerically validated by a state-of-the-art FFT homogenization procedure. For the given example, the novel analytical method is several thousand times faster than an FTT-based computational homogenization procedure.
Highlights
• Macrostrains are imposed on elastic material volumes with arbitrary inhomogeneous microstructures.
• Corresponding microstrain distributions are determined in a semi-analytical fashion.
• It involves a homogeneous infinite domain with polarization stress distributions.
• This leads to a Fredholm integral equation involving the elastic Green’s function.
• The solution gives access to homogenized stiffness tensors of arbitrary inhomogeneous microstructures.
1 Introduction–Motivation and scope
The main problem in the wide field of micromechanics of materials (Hill, 1963; Zaoui, 2002) is to quantify the effect of mechanical property distribution throughout the microstructures filling a so-called representative volume element (RVE), on the overall mechanical properties of this RVE, i.e., the properties linking the macroscopic strains (being the average over the microscopic strains inside the RVE) to the macroscopic stresses (being the average over the microscopic stresses inside the RVE). Restricting the present contribution to the case of linear elasticity, the problem comprises the following mathematical relations (Zaoui, 2002):
• geometrical boundary conditions prescribed at the boundary of the RVE, SRVE, in the form proposed by Hashin (1983)
with
where ɛ denotes the microscopic linearized strain tensors, defined as the symmetric part of the microscopic gradient of the displacement field
• the microscopic elastic law being a function of the microstructural position vector
with the microscopic stress tensor σ and the microscopic stiffness tensor
• equilibrium conditions
where
• the equivalence of macroscopic and microscopic expressions for virtual power densities of internal forces (Jiménez Segura et al., 2022), which, together with Eq. 5, yields the well-known stress average rule as (Hill, 1963; Zaoui, 2002)
• the strain concentration (or downscaling) relation linking, in a multilinear way, the macroscopic to the microscopic strain field (Hill, 1963; Zaoui, 2002)
where
• the macroscopic elastic law, which follows from Eq. 4 and Eqs. 6, 7 as
with the homogenized stiffness tensor reading as (Hill, 1963; Zaoui, 2002)
The classical approach for making the problem of Eqs. 1–9 tractable is to restrict the discussion to Nr homogeneous subdomains or phases within the RVE. Accordingly, the general microstiffness distribution
Besides this classical approach, it proved useful to introduce, within an RVE, infinitely many (non-spherical) phases, being associated with infinitely many space directions quantified through longitudinal and latitudinal Euler angles, and to associate infinitely many Eshelby problems to each of these directions (Fritsch et al., 2006). After an appropriate discretization of the involved integral expression, the microstrain state within the RVE can be represented sufficiently precisely, so as to allow for upscaling of brittle failure states from the phase-scale, up to the RVE-scale; and this has been shown again for construction and biomedical materials (Fritsch et al., 2009a; Fritsch et al., 2009b; Pichler and Hellmich, 2011; Pichler et al., 2013; Fritsch et al., 2013; Buchner et al., 2022).
Another extension of the classical composite mechanics estimates refers to coated inclusions being embedded in material matrices. A well-known way to approach this problem concerns the extension of Eshelby’s matrix-inclusion problem to a coated inclusion (where the coating may consist of numerous layers, forming an n-layered assemblage (Hervé and Zaoui, 1993; Lipinski et al., 2006)), and then resort to classical combination with the strain average rule, the latter being fed with the inclusion (or core) strains, the layer strains, and the matrix strains. Such models have been very helpful to decipher the mechanical behavior of bone-scaffold composites in tissue engineering (Bertrand and Hellmich, 2009) and of the interfacial transition zone in concrete (Königsberger et al., 2018). Recently, Xu and co-workers proposed a surprisingly simple mathematical alternative to the use of the multiply coated inclusion problem, namely, the repeated use of the Mori-Tanaka estimate, with sequential homogenization of, at a time, one inclusion and one layer playing the role of a matrix; and they successfully applied this strategy to polymer nanocomposites (Xu et al., 2017; Xu et al., 2018), mortar (Xu et al., 2019), and concrete (Xu et al., 2018; Guo et al., 2022).
Still, there is interest in homogenizing over non-uniform stiffness distributions
Yet, directing our attention back to Eqs. 1–9, we observe that both FEM and FFT-based homogenization techniques primarily focus on the homogenized stiffness tensor
This motivates the present paper, presenting a novel way to derive strain concentration tensor fields
2 An auxiliary problem on an infinite domain, and its relation to the RVE
Traditional phase-based micromechanical approaches, such as the Mori-Tanaka or the self-consistent estimates, are built on the solution of Eshelby’s matrix-inhomogeneity problem, where an ellipsoidal inhomogeneity of a specific stiffness is embedded into an infinite matrix of yet another stiffness. The latter matrix is remotely subjected to some auxiliary strains E0. The solution of Eshelby (1957) then relates the auxiliary strains to the homogeneous strains ɛI in the inhomogeneity, according to
with
However, as we presently wish to go beyond phase assemblages, we need to extend the auxiliary problem of Eq. 10 beyond homogeneous ellipsoidal domain-related strain ɛI and, instead, introduce a general strain field of the form
with
with
and comparison of Eq. 13 with Eq. 7 yields the strain concentration tensor as
and when considering, in addition, Eq. 9, the homogenized stiffness tensor is eventually retrieved as
see Figures 1E, F. Eq. 15 can be reformulated by setting
We are left with the determination of
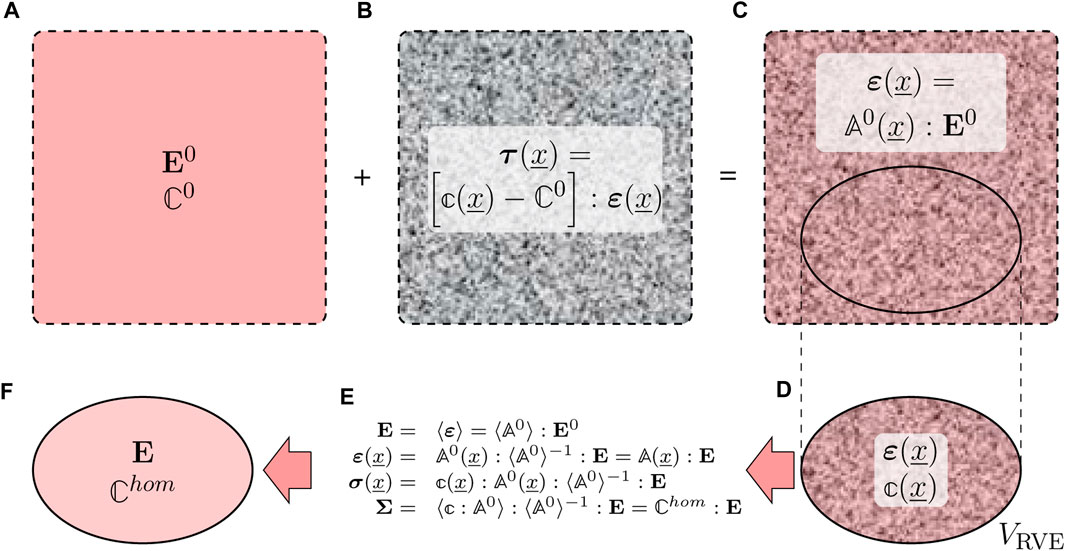
FIGURE 1. Illustration of elements making up the new homogenization scheme: (A) infinite homogeneous elastic matrix of stiffness
3 Green’s function-based solution to the auxiliary problem of the infinite matrix with arbitrary inhomogeneous microelasticity distributions
In order to determine the concentration tensor field
Equating Eq. 17 with Eq. 4 yields
see Figure 1B. Inserting the displacement-to-strain conversion relation of Eq. 3 into the equivalent constitutive law of Eq. 17, followed by inserting the corresponding result into the equilibrium condition of Eq. 5 yields
The solution of the linear partial differential Eq. 19,
whereby
• the homogeneous solution
with the inhomogeneous boundary conditions
• and the particular solution
with homogeneous boundary conditions
The homogeneous solution reads as
The particular solution can be given in the form
where
with boundary conditions
In Eq. 27, 1 denotes the second-order identity tensor and δ denotes the Dirac function, with the following properties.
The last term in Eq. 26 can be transformed by means of the chain rule, the divergence theorem, and the boundary condition given through Eq. 28, yielding
Insertion of Eq. 32 into Eq. 26, adding the respective result to Eq. 25, and using the obtained expression
In Eq. 33, the following gradients of the Green’s functions were explicitly introduced
Considering cases where, in Eq. 33, the effect of polarization stresses clearly outweighs that of volume forces, and inserting the polarization stress expression of Eq. 18 into Eq. 33 yields
Eq. 36 is an implicit integral equation for the microscopic strain field, as the latter appears both as a separate term and part of an integrand in a volume integral over the infinite elastic domain. More precisely, the microstrains are the solution of a Fredholm equation of the second kind (Fredholm, 1900). The solution of Eq. 36 is found by means of an infinitely often repeated substitution process concerning
As a starting point, Eq. 36 is specified for
In order to come up with an expression for
Insertion of Eq. 38 into Eq. 37 yields
where
In more detail, the concentration tensor field reads as
where
and, for n > 1,
The residual term after N iterations reads as
Note that for N → ∞,
for an arbitrary α.
4 Green’s function-based expression of the RVE-related strain concentration tensor field in an arbitrarily inhomogeneous microstructure
After obtaining an analytic expression for the auxiliary strain concentration tensor field
Thus, a comprehenive integral format for the strain concentration tensor field is obtained from inserting Eqs. 41–43 and Eq. 46 into Eq. 14, yielding
Lastly, the homogenized stiffness tensor, in terms of Green’s functions, is obtained inserting Eq. 47 into Eq. 15. The resulting expression can be simplified by the substitution of
5 Illustrative example: Microstructure with sinusoidally fluctuating bulk moduli
5.1 Complex microstructure with sinusoidally fluctuating microscopic bulk modulus
In order to illustrate the applicability of the novel integral expressions of Eqs. 41–43, we resort to the Green’s function for an infinitely extended isotropic elastic body with bulk modulus k0 and Poisson’s ratio ν0; it reads as (Dvorak, 2012)
where, with respect to the actual formula (4.5.12) given on page 107 of (Dvorak, 2012), we consider
where x1, x2, and x3 are the components of location vector
5.2 Normal strain-related components of
The auxiliary strain downscaling tensor
In order to retrieve the components G1111, G1122, and G1133, we start with the general expression for the components of the Green’s function of Eq. 49, reading as
The fourth-order Green’s function gradient according to Eq. 35 exhibits the following components
In order to evaluate Eq. 53, it is useful to recall the following properties of the spatial derivatives of the norm
revealing the interesting property
The first derivative of the inverse of the norm
revealing the interesting property
Eq. 55 and Eq. 57 allow for re-writing Eq. 53 as
so that the components occurring in Eq. 51 read as
The sum of Eqs. 59–61, to be calculated in Eq. 51, can be further simplified through an identity which follows from deriving Eq. 54 with respect to the components of the location vector,
Namely, Eq. 62 entails the following identity
twofold derivation of which yields an identity comprising the derivatives of the norm
Insertion of Eqs. 59–61 into Eq. 51, while considering Eq. 64, yields
A change of variable to
Transforming Eq. 66 by means of
and considering the second derivative of the inverse of the norm of
as well as that the even and odd functions appearing as factors in the integral expression of Eq. 66 imply vanishing integrals
we arrive at
Noting that
where the auxiliary function
Eq. 72 exhibits two remarkable properties. Firstly, its format
is the solution of the Poisson’s equation
Secondly, Eq. 72 is symmetric in the sense of
Use of the latter relations in Eq. 74, while accounting for the structure of f according to Eq. 72 and Eq. 73, yields
where we made use of Eq. 75. Solving the equation for
The second term of the series for the auxiliary concentration tensor for the considered sinusoidal isotropic micro-stiffness distribution follows from insertion of Eq. 50 into Eq. 43, so that its component 1111 is obtained as
Specification of Eq. 78 for Eq. 58, while considering the identity of Eq. 64, yields
Considering the last integral in Eq. 79 as the Green’s function solving the Poisson’s equation
yields
Recalling from Eq. 65 and Eq. 77 that
for any
Repeating this derivation for the 1111-component of any other member of the series, i.e., for
Moreover, because of the symmetry of the considered micro-stiffness distribution,
The components of the auxiliary strain downscaling tensor
is applied to
5.3 Shear strain-related components of
Next, we turn to the shear-related components of the concentration tensor, i.e., to Aijkℓ with i ≠ j or k ≠ ℓ. The concentration tensor is driven by the micro-stiffness fluctuation around the base stiffness
Combining Eq. 88 with Eq. 41 implies that
and
Let us now turn to the remaining non-vanishing shear-related components of the concentration tensor, i.e., to
Insertion of Eq. 58 into Eq. 91, while considering the identity resulting from derivation of Eq. 63 with respect to xi and xj, reading as
yields
Introducing the variable
and the corresponding consequence of even and odd functions
Eq. 93 can be transformed to
with i,j,l = 1,2,3, whereby i ≠ j and k ≠ i,j. Introducing the microstructure-related variable change
with i,j,l = 1,2,3, whereby i ≠ j and k ≠ i,j. Considering
with K1 being the modified Bessel function of the second kind, Eq. 97 can be re-written as
with i,j,l = 1,2,3, whereby i ≠ j and k ≠ i,j. Applying a transformation towards polar coordinates,
with i,j,l = 1,2,3, whereby i ≠ j and k ≠ i,j. Thanks to the trigonometric identity
with i,j,l = 1,2,3, whereby i ≠ j and k ≠ i,j. Thus, integrating over ρ yields
with i,j,l = 1,2,3, whereby i ≠ j and k ≠ i,j. The integral remaining in Eq. 102 amounts to
with i,j,l = 1,2,3, whereby i ≠ j and k ≠ i,j.
The following element of the series
After application of Poisson’s Eq. 74 and Eq. 104 can be expressed as follows, when using
Proceeding with an analogous process to the one carried out to obtain
with i,j,l = 1,2,3, whereby i ≠ j and k ≠ i,j. Similarly, the third element was computed as
with i,j,l = 1,2,3, whereby i ≠ j and k ≠ i,j.
For the following terms
These terms can be computed in the same manner as the previous ones, converging rapidly due to the factor
5.4 Tensorial link between auxiliary and real macrostrains: Access to strain concentration tensor field
For the present case, the RVE is regarded as any assembly of a finite number of fluctuations which are periodically repeated, i.e.,
with nλ as the number of stiffness waves along edge directions of a box-shaped RVE with a sinusoidal microstructure. The concentration tensor associated with this microstructure,
Like in the previous sections, the components of tensor
Clearly, the term in square brackets is equal to 1, while we must focus on the other integral expression
Proceeding with a change of variable
Solving the integral for
where
where K(a) is the complete elliptic integral of the first kind with parameter a, and
is characteristic for each microstructure. The value of I, see Eq. 115, has been obtained numerically by means of different integration methods, including the trapezoidal or Simpson’s rule (Whittaker and Robinson, 1967; Horwitz, 2001), for several values of χ. The value of I is equal to 1 for χ = 0, and increases non-linearly with increasing χ, see Figure 2. Thus, from Eq. 111,
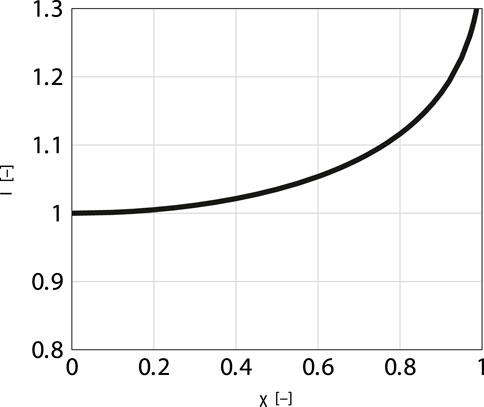
FIGURE 2. Numerical value of I, see Eq. 115, obtained for several values of
The next components to be considered are
The shear components read as
and
Thus, the auxiliary-to-RVE tensor reads as
Lastly, the real strain concentration tensor field is computed according to Eq. 14 as
where
see Eq. 115 and Figure 2 for I(χ).
5.5 Homogenized stiffness of sinusoidally fluctuating microstructure
From Eq. 16, the difference between the homogenized stiffness and the background stiffness
One more time, the components of this tensor will be obtained individually. The only non-vanishing components ΔChom,ijkℓ are those with i = j and k = ℓ, due to Eq. 122 and
Therefore, the components ΔChom,iikk read as
Thus, inserting Eq. 123 and Eq. 124 into Eq. 127 and applying
Integrating Eq. 128 with respect to
whereby we have made use of Eq. 114. Clearly, for the stiffness field of Eq. 50, the remaining components vanish, considering Eq. 122 and Eq. 126.
6 Discussion
It is worthwhile to discuss key characteristics of the convolution integral-type mathematical relations for the concentration tensor fields introduced in the present paper. We start by mentioning that Eq. 48 is, to our best knowledge, the first-ever explicit integral formulation for the concentration tensor fields arising from a general microstiffness field. Actually, in the pertinent literature, see, e.g., the review of Zaoui (2002), the mathematical existence of such a field is mentioned, while any corresponding explicit expression is missing.
Our new expression, Eq. 48, provides a common basis for the treatment for virtually any type of microstructure, be they general harmonic microstructures, with microelasticity distributions which can be represented by means of Fourier series, as described in Section 6.5, or even distributions with discontinuities, allowing for the consideration of classical composite material morphologies, arising from the assembly of a finite number of microstructural domains with uniform stiffnesses, normally referred to as “material phases”. Accordingly, the novel method is also apt for large volume fractions of one of the aforementioned domains, i.e., to the so-called “large concentration composition”.
As it is well known that the Green kernel occurring in the aforementioned integral expressions is singular at the point
Alternatively, one may wish a numerical confirmation of our new analytical approach to strain concentration tensor fields, and we provide such a confirmation in terms of FFT-based computational homogenization, in the second subsection of the present Discussion section.
It is also instructive to compare our approach to earlier suggestions for the use of a Fredholm integral equation similar to Eq. 36, often referred to as the Lippmann-Schwinger equation; in particular so concerning the domain over which the convolution integral is evaluated, the type of polarization field considered, and the relation of the Fredholm integral equation to the macroscopic strain associated with the RVE. This is the topic of the third subsection of the present Discussion section.
Finally, we discuss the range of validity of the Fredholm integral Eq. 36, and the practical evaluation of the concentration tensor expressions in the case of microstructures which are more general than that with the sinusoidally fluctuating microscopic bulk moduli covered in Section 5. Corresponding deliberations conclude the present Discussion section.
6.1 Singular convolution integrals–Analytical validation by means of Cauchy principal value
All integral expressions defining concentration tensor fields, such as Eq. 14, Eqs. 41–43, Eq. 51, Eq. 65, and Eq. 70, exhibit singularities at
Denoting the small spherical domain as Vϵ, the integral in Eq. 70 can be recast as, see, e.g., Buryachenko (2007), p. 54,
whereby
is fully in line with the developments of Eq. 72 and Eq. 73. As stated before, we are interested in the limit case of ϵ → 0 where
so that
whereby we made use of the divergence theorem, with
the integrand in the surface integral of Eq. 133 can be transformed to
Then, the surface integral in Eq. 133 is preferably evaluated in spherical coordinates, where.
so that use of Eqs. 135–138 in the surface integral of Eq. 133 yields an expression which becomes independent of ϵ, and hence, of the limiting process. In mathematical detail, we have
and hence, since f (0) = 1,
The result of Eq. 140 is fully equivalent with evaluating Eq. 76 for
The situation is totally different when it comes to the shear-related concentration tensor components according to Eq. 93. There, the Cauchy principal value needs to be multiplied by sin (0) = 0 so that the integration over the small sphere delivers zero, and it is the domain outside the small sphere, which solely contributes to the integral in Eq. 93. A procedure for solving this regular integral was presented, see Eqs. 94–103.
6.2 Strain concentration tensor fields and homogenized stiffness: Numerical confirmation by means of FFT homogenization
In order to gain further confidence into our novel method, we evaluate the analytically defined strain concentration tensor fields of Eq. 123 and Eq. 124 for a particular numerical choice of sinusoidal microelasticity field, see Table 2 for this choice, and then compare this evaluation to suitably chosen microstrain fields computed by means of the classical FFT homogenization methods proposed by Moulinec and Suquet (1994), Moulinec and Suquet (1998), and widely expanded and used thereafter (Lucarini et al., 2021).
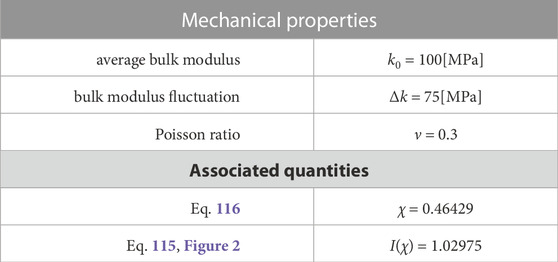
TABLE 2. Mechanical properties and quantities associated to the particular microelastic material, see Eq. 50.
The key idea of FFT homogenization is to start with an estimate for the microstrain fields, to compute a corresponding estimate for the polarization stress field, then test the latter estimate on the Fourier transform of Eq. 33 with
with the wave vector
Namely, prescribing the polarization stress on the right-hand side of Eq. 141 yields a new estimate of microstrain field in the wave domain, which needs to be back-transformed into the traditional location space domain. This new estimate allows for computation of an improved estimate of the polarization stress fields, as described before. The sequential estimation of the polarization stress field (in the location space) and the microstrain field (in the wave space) is repeated until two successive strain estimates differ only very slightly from each other. This algorithm becomes especially appealing if both the Fourier transform and the inverse Fourier transform are realized discretely, on a finite number of locations given by the voxels making up an image. As such a discrete transform can be set up to deliver results in a particularly fast fashion, it is called Fast Fourier transformation, abbreviated as FFT (Cochran et al., 1967), and accordingly, the aforementioned algorithm is referred to as FFT homogenization.
In order to get access to the strain concentration tensor field (which is not the standard target of an FFT homogenization study), we identify the component Aiiii, with i = 1, 2, 3, as the microstrain field component ɛii, with i = 1, 2, 3, which arises from a macroscopic strain tensor of the format
Different, increasingly fine, FFT discretizations of the investigated sinusoidal microelasticity distribution deliver strain tensor concentration fields which very satisfactorily converge to the analytical solution of Eq. 123 and Eq. 124, see Figure 3 and Figure 4. Accordingly, the FFT-determined homogenized stiffness properties agree virtually perfectly with the analytical results according to Eq. 129, see Table 3. At the same time, our new analytical solution strategy is remarkably efficient from the viewpoint of CPU time: on a Core i5-1035G1 processor in a Lenovo Ideapad S340-15IIL computer, the numerical evaluation of the integral I(χ) according to Eq. 115, the only operation needing non-negligible computer time, lasts for only 0.004 s, while FFT solution processes for 1003 voxels last by a factor of over 6,500 longer, namely, for 26.7 s.
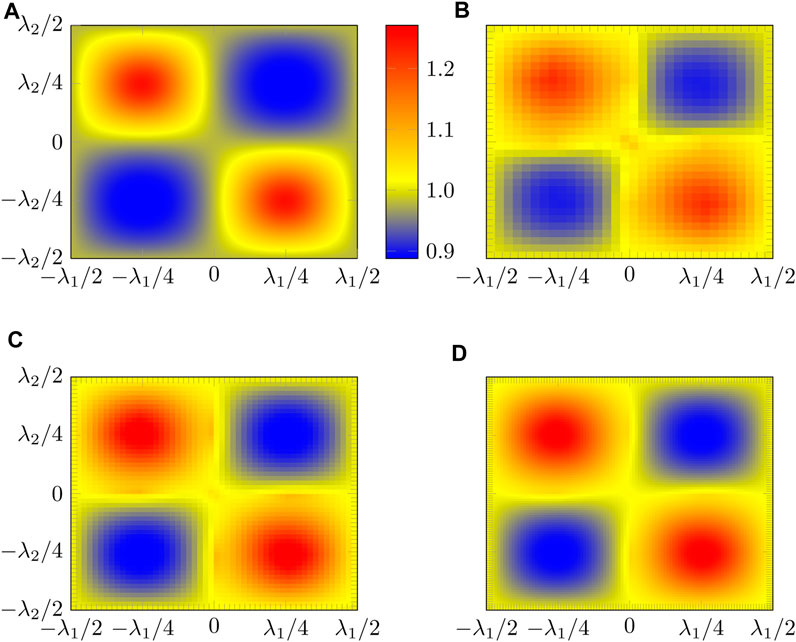
FIGURE 3. Strain concentration field
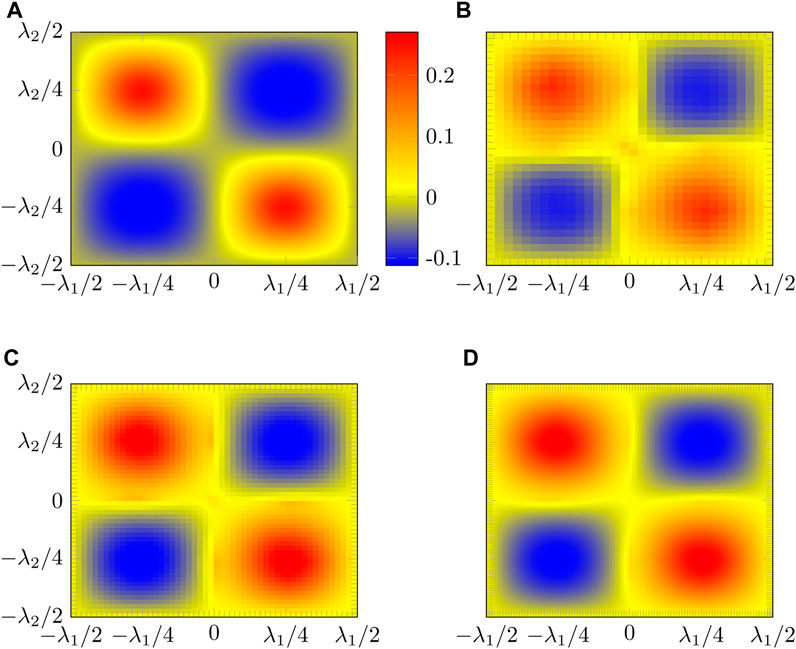
FIGURE 4. Strain concentration field

TABLE 3. Numerical value of stiffness tensor components of the benchmark example calculated by means of the proposed analytical model, see Eq. 129, and by FFT with different discretizations.
6.3 Use of the Lippmann-Schwinger equation: Auxiliary problems, integration domains, and macroscopic strains associated with the RVE
From a terminological viewpoint, we note that equations of the format of Eq. 36, irrespective of the chosen integration domains or the format of the polarization stresses, are often referred to as the Lippmann-Schwinger equation, as a similar equation has been proposed by Lippmann and Schwinger (1950) in the field of quantum mechanics. In this context, it is interesting to compare our present contribution to earlier micromechanical applications of the Lippmann-Schwinger equation. A form which is virtually identical to Eq. 36 appears as Eq. 9 in (Molinari and El Mouden, 1996); except for a sign change stemming from the definition of the fourth-order Green operator as the twofold gradient with respect to
However, the actual use of Eq. 9 in (Molinari and El Mouden, 1996) is quite different from our present use of Eq. 36, as Molinari and El Mouden (1996) introduce an infinite number of uniform subfields of microscopic stiffnesses, representing strongly interacting “elastic inclusions” within an RVE of a composite material. At the same time, as a certain commonality of the approach of Molinari and El Mouden (1996) and our present contribution, we note that the latter authors’ strain ɛ0 plays exactly the role of our auxiliary strain E0: it is the strain applied to the auxiliary homogeneous, infinite matrix which undergoes polarization stresses. However, different from our approach to solve this auxiliary problem so as to provide the microscopic strains as a function of the auxiliary strains, Molinari and El Mouden (1996) apply the strain average rule directly to the Fredholm integral equation, i.e., to their Eq. 9, and this leads to their Eq. 16 linking auxiliary and RVE-related strains. On this basis, they then discuss explicit solutions for finite numbers of inclusions within a periodically repeating cubic cell. In this context, Molinari and El Mouden (1996) apply the strain average rule to an infinite domain, as can be seen from their Eq. 15, while our Eq. 12 is clearly related to the (finite) RVE, and hence to the average rule of Eq. 2, which arises from the Hashin displacement boundary conditions imposed onto the RVE according to Eq. 1. We also note that neither Eq. 9 nor Eq. 16 in (Molinari and El Mouden, 1996) give access to the concentration tensor fields - so that our expression according to Eq. 14, together with Eqs. 41–43, turn out as an interesting original aspect of the present paper.
Eq. 36 of the present paper is also reminiscent of Eq. 2.28 in (Torquato, 1997). However, different from our approach, Torquato (1997) restricts a non-vanishing polarization field to a finite domain within his infinitely large auxiliary problem subjected to some auxiliary strain ɛ0, the role of which is comparable to our auxiliary strain E0. In this context, he notes that the result of the corresponding convolution integral depends on the shape of the aforementioned finite domain, a situation which does not occur in our anaylsis in which the convolution integrals are evaluated throughout the unbounded auxiliary matrix. Eventually, Torquato (1997) lets his finite polarization domain coincide with the RVE of an anisotropic two-phase composite, for which he identifies stiffness series expansions in powers of “elastic polarizabilities”.
A further difference appears between Eq. 36 of the present contribution and the formally similar Eq. 4 of the famous paper of Moulinec and Suquet (1994), see also (Moulinec and Suquet, 1998). The latter authors introduce the convolution integral directly on the (finite) RVE, noting that a corresponding explicit Green’s function can only be given in the case of periodic displacement boundary conditions imposed onto the RVE, and of corresponding microscopic strains which fluctuate periodically around their average (i.e., around the macroscopic strain). Namely, it is under this periodicity condition, that an explicit solution for the convolution problem exists in the Fourier space, which, in turn, allows for the development of a very efficient algorithm for the mechanical treatment of images made up of pixels or voxels, with the polarization stress being constant throughout one pixel or voxel, respectively.
Green’s operators in convolution integrals over a finite volume (i.e., differing from our present integration over an infinite auxiliary domain) have been already introduced in the 1970s: In this context, Zeller and Dederichs (1973) noted that the corresponding Green’s functions read as
Our iterative scheme for solving the Fredholm integral Eq. 36 also bears some similarities with earlier contributions in the field: Kröner (1977) presents an iterative solution for the Lippmann-Schwinger equation formulated directly on the RVE, and Torquato (1997) proposes an iterative scheme which finally delivers the polarization stress as a function of the homogeneous auxiliary strain ɛ0.
6.4 Range of validity of Lippmann-Schwinger equation
The practical relevance of the case where the polarization stresses in Eq. 33 outweigh the effect of the microscopic volume forces, which is the prerequisite for the Lippmann-Schwinger Eq. 36 to hold, deserves further discussion: Within the RVE, the microscopic stresses σ fluctuate around their spatial average, which is the macroscopic stress Σ, and the characteristic length scale d of this fluctuation is scale-separated from the length of the RVE, ℓRVE, which reads mathematically as
Due to the mathematical structure of the microscopic equilibrium conditions, see Eq. 5, any microscopic volume forces leading to microscopic stress fluctuations are required to change their sign, i.e., their direction, over distances as small as d. Practically speaking, this is an exceptional case: Even in composites with high contrast in mass density, the corresponding gravitational forces of varying magnitude would always share the same direction; or in other words, practically relevant force fields are often parallel within the RVE. We note in passing, that such micro-parallel force field, directly implying the validity of Eq. 36, even fulfill a force field average rule (Jiménez Segura et al., 2022).
6.5 Practical note concerning generally harmonic microstiffness fluctuations
Finally, we discuss which aspects of Section 5 hold beyond the restriction to sinusoidally fluctuating microstiffnesses, and how the semi-analytical solutions presented in this section may be generalized to generally harmonic microstiffness fluctuations. In this context, the key generalization step would be the representation of any, arbitrarily general continuous microstiffness distribution across a finite RVE by a three-dimensional Fourier series. Generalizing, in this way, the example distribution of Eq. 50 to an arbitrarily inhomogenous bulk modulus distribution Δk (x1, x2, x3) yields
with i now standing for the imaginary unit, and with the Fourier coefficients cklm being obtained from
In other words, sums of products of any three trigonometric functions, be they sine or cosine,—rather than the product of three sine or three cosine terms—would occur throughout the convolution integrals. However, the effect on the corresponding modifications of Eq. 66 and Eq. 93 are only minor: Thanks to Eq. 67 and
the structure of the integrals in Eq. 70 and Eq. 96 stays unaffected. This shows the considerable potential of our method for material investigation based on Fourier-representation of images (Chung et al., 2007)—as an interesting complement to the popular voxel-based FFT schemes.
7 Conclusion
In the present paper, it is for the first time that explicit integral expressions for the concentration tensor fields arising from generally non-uniform microelasticity distributions have been given. More precisely, the effects of elastic behavior at the microscale are represented by means of the Green’s function formalism, leading to Fredholm integral equations which provide novel, series-type integral expressions for the concentration tensor field. The latter may be analytically solved in cases where the involved integral expressions can be formulated as derivatives of the solutions of the Poisson equation, then providing an unprecedented direct access to macro-to-micro scale transition relations, as expressed by the concentration tensor expressions of Eq. 47, and Eqs. 122–124. This opens new avenues for exploring the mechanical effect of eigenstrains in hierarchical material systems with complex morphologies, as an interesting alternative to classical computational homogenization. The new approach also provides semi-analytical access to the homogenized stiffness, such as that calculated for a microstructure with sinusoidally fluctuating bulk moduli, see Eq. 16 and Eq. 129. Since I(χ) ≥ 1, see Figure 2, the resulting homogenized stiffness,
Besides its obvious fundamental knowledge-related and conceptual merits, the new methods appears as extremely advantegeous from a computational viewpoint, in particular if the microstructure can be represented by just a few elements of the series given in Section 6.5, because relevant computational power is needed only for the one-time determination of the Fourier coefficients and the value of the integral occurring in the function graphed in Figure 2; whereby the latter my be even represented by some suitably chosen fitting function.
Nevertheless, as regards classical composite microstructures, well-known homogenization methods based on the Eshelby-Laws matrix-inhomogeneity problem, such as suitable generalizations of the Mori-Tanaka method (Benveniste, 1987), accounting for symmetrization strategies if required (Sevostianov and Kachanov, 2014; Jiménez Segura et al., 2023), may turn out as more efficient than an approach starting from the general expression given in Eq. 48 and Eq. 49. This underlines the sustained success of advanced composite mechanics in the classical sense.
Data availability statement
The original contributions presented in the study are included in the article/Supplementary Material, further inquiries can be directed to the corresponding author.
Author contributions
NJ: investigation, methodology, formal analysis, computation, visualization, writing—original draft, review and editing. BP: supervision, conceptualization, funding acquisition, methodology, formal analysis, writing—original draft, writing—review and editing. CH: supervision, conceptualization, funding acquisition, methodology, formal analysis, writing—review and editing.
Funding
The authors gratefully acknowledge financial support in the framework of the European Union’s Horizon 2020 research and innovation programme under the Marie Skłodowska-Curie grant agreement No. 764691. The authors acknowledge TU Wien Bibliothek for financial support through its Open Access Funding Programme.
Conflict of interest
The authors declare that the research was conducted in the absence of any commercial or financial relationships that could be construed as a potential conflict of interest.
Publisher’s note
All claims expressed in this article are solely those of the authors and do not necessarily represent those of their affiliated organizations, or those of the publisher, the editors and the reviewers. Any product that may be evaluated in this article, or claim that may be made by its manufacturer, is not guaranteed or endorsed by the publisher.
References
Benveniste, Y. (1987). A new approach to the application of Mori-Tanaka’s theory in composite materials. Mech. Mater. 6, 147–157. doi:10.1016/0167-6636(87)90005-6
Benveniste, Y., Dvorak, G. J., and Chen, T. (1991). On diagonal and elastic symmetry of the approximate effective stiffness tensor of heterogeneous media. J. Mech. Phys. Solids 39, 927–946. doi:10.1016/0022-5096(91)90012-d
Bernard, O., Ulm, F.-J., and Lemarchand, E. (2003). A multiscale micromechanics-hydration model for the early-age elastic properties of cement-based materials. Cem. Concr. Res. 33, 1293–1309. doi:10.1016/s0008-8846(03)00039-5
Bertrand, E., and Hellmich, C. (2009). Multiscale elasticity of tissue engineering scaffolds with tissue-engineered bone: A continuum micromechanics approach. J. Eng. Mech. 135, 395–412. doi:10.1061/(asce)0733-9399(2009)135:5(395)
Brisard, S., and Dormieux, L. (2010). FFT-based methods for the mechanics of composites: A general variational framework. Comput. Mater. Sci. 49, 663–671. doi:10.1016/j.commatsci.2010.06.009
Buchner, T., Königsberger, M., Jäger, A., and Füssl, J. (2022). A validated multiscale model linking microstructural features of fired clay brick to its macroscopic multiaxial strength. Mech. Mater. 170, 104334. doi:10.1016/j.mechmat.2022.104334
Buryachenko, V. (2007). Micromechanics of heterogeneous materials. Springer Science and Business Media.
Cai, X., Brenner, R., Peralta, L., Olivier, C., Gouttenoire, P.-J., Chappard, C., et al. (2019). Homogenization of cortical bone reveals that the organization and shape of pores marginally affect elasticity. J. R. Soc. Interface 16, 20180911. doi:10.1098/rsif.2018.0911
Chung, M. K., Dalton, K. M., Shen, L., Evans, A. C., and Davidson, R. J. (2007). Weighted Fourier series representation and its application to quantifying the amount of gray matter. IEEE Trans. Med. Imaging 26, 566–581. doi:10.1109/tmi.2007.892519
Cochran, W., Cooley, J., Favin, D., Helms, H., Kaenel, R., Lang, W., et al. (1967). What is the fast Fourier transform? Proc. IEEE 55, 1664–1674. doi:10.1109/PROC.1967.5957
Eshelby, J. D. (1957). The determination of the elastic field of an ellipsoidal inclusion, and related problems. Proc. R. Soc. Lond. Ser. A Math. Phys. Sci. 241, 376–396.
Feng, T., Jia, M., Xu, W., Wang, F., Li, P., Wang, X., et al. (2022). Three-dimensional mesoscopic investigation of the compression mechanical properties of ultra-high performance concrete containing coarse aggregates. Cem. Concr. Compos. 133, 104678. doi:10.1016/j.cemconcomp.2022.104678
Fredholm, I. (1900). Sur les équations de l’équilibre d’un corps solide élastique. Acta Math. 23, 1–42. doi:10.1007/bf02418668
Fritsch, A., Dormieux, L., and Hellmich, C. (2006). Porous polycrystals built up by uniformly and axisymmetrically oriented needles: Homogenization of elastic properties. Comptes Rendus Mécanique 334, 151–157. doi:10.1016/j.crme.2006.01.008
Fritsch, A., Dormieux, L., Hellmich, C., and Sanahuja, J. (2009a). Mechanical behavior of hydroxyapatite biomaterials: An experimentally validated micromechanical model for elasticity and strength. J. Biomed. Mater. Res. Part A 88A, 149–161. doi:10.1002/jbm.a.31727
Fritsch, A., Hellmich, C., and Dormieux, L. (2009b). Ductile sliding between mineral crystals followed by rupture of collagen crosslinks: Experimentally supported micromechanical explanation of bone strength. J. Theor. Biol. 260, 230–252. doi:10.1016/j.jtbi.2009.05.021
Fritsch, A., Hellmich, C., and Young, P. (2013). Micromechanics-derived scaling relations for poroelasticity and strength of brittle porous polycrystals. J. Appl. Mech. 80, 020905. doi:10.1115/1.4007922
Fritsch, A., and Hellmich, C. (2007). ‘Universal’ microstructural patterns in cortical and trabecular, extracellular and extravascular bone materials: Micromechanics-based prediction of anisotropic elasticity. J. Theor. Biol. 244, 597–620. doi:10.1016/j.jtbi.2006.09.013
Grimal, Q., Raum, K., Gerisch, A., and Laugier, P. (2011). A determination of the minimum sizes of representative volume elements for the prediction of cortical bone elastic properties. Biomechanics Model. Mechanobiol. 10, 925–937. doi:10.1007/s10237-010-0284-9
Guo, W., Han, F., Jiang, J., and Xu, W. (2022). A micromechanical framework for thermo-elastic properties of multiphase cementitious composites with different saturation. Int. J. Mech. Sci. 224, 107313. doi:10.1016/j.ijmecsci.2022.107313
Hashin, Z. (1983). Analysis of composite materials—a survey. J. Appl. Mech. 50, 481–505. doi:10.1115/1.3167081
Hashin, Z. (1963). Theory of mechanical behavior of heterogeneous media. Philidelphia, Pa: Towne School of Civil and Mechanical Engineering, University of Pennsylvania.
Hashin, Z. (1965). Viscoelastic behavior of heterogeneous media. J. Appl. Mech. 32, 630–636. doi:10.1115/1.3627270
Hellmich, C., Barthélémy, J.-F., and Dormieux, L. (2004). Mineral–collagen interactions in elasticity of bone ultrastructure – A continuum micromechanics approach. Eur. J. Mech. - A/Solids 23, 783–810. doi:10.1016/j.euromechsol.2004.05.004
Hellmich, C., and Mang, H. (2005). Shotcrete elasticity revisited in the framework of continuum micromechanics: From submicron to meter level. J. Mater. Civ. Eng. 17, 246–256. doi:10.1061/(asce)0899-1561(2005)17:3(246)
Hervé, E., and Zaoui, A. (1993). inclusion-based micromechanical modelling. Int. J. Eng. Sci. 31, 1–10. doi:10.1016/0020-7225(93)90059-4
Hill, R. (1963). Elastic properties of reinforced solids: Some theoretical principles. J. Mech. Phys. Solids 11, 357–372. doi:10.1016/0022-5096(63)90036-x
Hofstetter, K., Hellmich, C., and Eberhardsteiner, J. (2005). Development and experimental validation of a continuum micromechanics model for the elasticity of wood. Eur. J. Mech. - A/Solids 24, 1030–1053. doi:10.1016/j.euromechsol.2005.05.006
Horwitz, A. (2001). A version of Simpson’s rule for multiple integrals. J. Comput. Appl. Math. 134, 1–11. doi:10.1016/s0377-0427(00)00444-1
Jiménez Segura, N., Pichler, B. L., and Hellmich, C. (2023). Concentration tensors preserving elastic symmetry of multiphase composites. Mech. Mater. 178, 104555. doi:10.1016/j.mechmat.2023.104555
Jiménez Segura, N., Pichler, B. L., and Hellmich, C. (2022). Stress average rule derived through the principle of virtual power. ZAMM - J. Appl. Math. Mech./Zeitschrift für Angewandte Math. und Mech. 102, e202200091. doi:10.1002/zamm.202200091
Kneer, G. (1965). Über die Berechnung der Elastizitätsmoduln vielkristalliner Aggregate mit Textur. Phys. Status Solidi (b) 9, 825–838. doi:10.1002/pssb.19650090319
Königsberger, M., Hlobil, M., Delsaute, B., Staquet, S., Hellmich, C., and Pichler, B. (2018). Hydrate failure in itz governs concrete strength: A micro-to-macro validated engineering mechanics model. Cem. Concr. Res. 103, 77–94. doi:10.1016/j.cemconres.2017.10.002
Korringa, J. (1973). Theory of elastic constants of heterogeneous media. J. Math. Phys. 14, 509–513. doi:10.1063/1.1666346
Kröner, E. (1958). Berechnung der elastischen Konstanten des Vielkristalls aus den Konstanten des Einkristalls [Calculation of the elastic constant of the multi-crystal from the constants of the single crystals]. Z. für Phys. 151, 504–518.
Kröner, E. (1977). Bounds for effective elastic moduli of disordered materials. J. Mech. Phys. Solids 25, 137–155. doi:10.1016/0022-5096(77)90009-6
Levin, V. M. (1967). Thermal expansion coefficient of heterogeneous materials. Mekhanika Tverd. Tela 2, 83–94.
Lipinski, P., Barhdadi, E. H., and Cherkaoui, M. (2006). Micromechanical modelling of an arbitrary ellipsoidal multi-coated inclusion. Philos. Mag. 86, 1305–1326. doi:10.1080/14786430500343868
Lippmann, B. A., and Schwinger, J. (1950). Variational principles for scattering processes. I. Phys. Rev. 79, 469–480. doi:10.1103/physrev.79.469
Lucarini, S., Upadhyay, M., and Segurado, J. (2021). Fft based approaches in micromechanics: Fundamentals, methods and applications. Model. Simul. Mater. Sci. Eng. 30, 023002. doi:10.1088/1361-651x/ac34e1
Moës, N., Cloirec, M., Cartraud, P., and Remacle, J. F. (2003). A computational approach to handle complex microstructure geometries. Comput. Methods Appl. Mech. Eng. 192, 3163–3177. doi:10.1016/s0045-7825(03)00346-3
Molinari, A., and El Mouden, M. (1996). The problem of elastic inclusions at finite concentration. Int. J. Solids Struct. 33, 3131–3150. doi:10.1016/0020-7683(95)00275-8
Mori, T., and Tanaka, K. (1973). Average stress in matrix and average elastic energy of materials with misfitting inclusions. Acta Metall. 21, 571–574. doi:10.1016/0001-6160(73)90064-3
Moulinec, H., and Suquet, P. (1994). A fast numerical method for computing the linear and nonlinear properties of composites. Comptes-Rendus l’Académie Sci. Série II 318, 1417–1423.
Moulinec, H., and Suquet, P. (1998). A numerical method for computing the overall response of nonlinear composites with complex microstructure. Comput. Methods Appl. Mech. Eng. 157, 69–94. doi:10.1016/s0045-7825(97)00218-1
Pahr, D. H., and Zysset, P. K. (2008). Influence of boundary conditions on computed apparent elastic properties of cancellous bone. Biomechanics Model. Mechanobiol. 7, 463–476. doi:10.1007/s10237-007-0109-7
Pichler, B., Hellmich, C., Eberhardsteiner, J., Wasserbauer, J., Termkhajornkit, P., Barbarulo, R., et al. (2013). Effect of gel–space ratio and microstructure on strength of hydrating cementitious materials: An engineering micromechanics approach. Cem. Concr. Res. 45, 55–68. doi:10.1016/j.cemconres.2012.10.019
Pichler, B., and Hellmich, C. (2011). Upscaling quasi-brittle strength of cement paste and mortar: A multi-scale engineering mechanics model. Cem. Concr. Res. 41, 467–476. doi:10.1016/j.cemconres.2011.01.010
Rosen, B. W., and Hashin, Z. (1970). Effective thermal expansion coefficients and specific heats of composite materials. Int. J. Eng. Sci. 8, 157–173. doi:10.1016/0020-7225(70)90066-2
Sanahuja, J., Dormieux, L., Meille, S., Hellmich, C., and Fritsch, A. (2010). Micromechanical explanation of elasticity and strength of gypsum: From elongated anisotropic crystals to isotropic porous polycrystals. J. Eng. Mech. 136, 239–253. doi:10.1061/(asce)em.1943-7889.0000072
Scheiner, S., Sinibaldi, R., Pichler, B., Komlev, V., Renghini, C., Vitale-Brovarone, C., et al. (2009). Micromechanics of bone tissue-engineering scaffolds, based on resolution error-cleared computer tomography. Biomaterials 30, 2411–2419. doi:10.1016/j.biomaterials.2008.12.048
Sevostianov, I., and Kachanov, M. (2014). On some controversial issues in effective field approaches to the problem of the overall elastic properties. Mech. Mater. 69, 93–105. doi:10.1016/j.mechmat.2013.09.010
Ting, T. C. T., and Lee, V.-G. (1997). The three-dimensional elastostatic Green’s function for general anisotropic linear elastic solids. Q. J. Mech. Appl. Math. 50, 407–426. doi:10.1093/qjmam/50.3.407
Tonon, F., Pan, E., and Amadei, B. (2001). Green’s functions and boundary element method formulation for 3D anisotropic media. Comput. Struct. 79, 469–482. doi:10.1016/s0045-7949(00)00163-2
Torquato, S. (1997). Effective stiffness tensor of composite media—I. Exact series expansions. J. Mech. Phys. Solids 45, 1421–1448. doi:10.1016/s0022-5096(97)00019-7
Voigt, W. (1889). Über die Beziehung zwischen den beiden Elasticitätsconstanten isotroper Körper [On the relation between the elasticity constants of isotropic bodies]. Ann. Phys. 274, 573–587. doi:10.1002/andp.18892741206
Wang, H., Hellmich, C., Yuan, Y., Mang, H., and Pichler, B. (2018). May reversible water uptake/release by hydrates explain the thermal expansion of cement paste? — Arguments from an inverse multiscale analysis. Cem. Concr. Res. 113, 13–26. doi:10.1016/j.cemconres.2018.05.008
Whittaker, E., and Robinson, G. (1967). “The trapezoidal and parabolic rules,”in The calculus of observations: A treatise on numerical mathematics (Dover, New York: Cope Press), 156–158.
Willis, J. R. (1977). Bounds and self-consistent estimates for the overall properties of anisotropic composites. J. Mech. Phys. Solids 25, 185–202. doi:10.1016/0022-5096(77)90022-9
Wolfram, U., Peña Fernández, M., McPhee, S., Smith, E., Beck, R. J., Shephard, J. D., et al. (2022). Multiscale mechanical consequences of ocean acidification for cold-water corals. Sci. Rep. 12, 8052. doi:10.1038/s41598-022-11266-w
Xie, L., Zhang, C., Sladek, J., and Sladek, V. (2016). Unified analytical expressions of the three-dimensional fundamental solutions and their derivatives for linear elastic anisotropic materials. Proc. R. Soc. A Math. Phys. Eng. Sci. 472, 20150272. doi:10.1098/rspa.2015.0272
Xu, W., Wu, F., Jiao, Y., and Liu, M. (2017). A general micromechanical framework of effective moduli for the design of nonspherical nano- and micro-particle reinforced composites with interface properties. Mater. Des. 127, 162–172. doi:10.1016/j.matdes.2017.04.075
Xu, W., Wu, Y., and Gou, X. (2019). Effective elastic moduli of nonspherical particle-reinforced composites with inhomogeneous interphase considering graded evolutions of elastic modulus and porosity. Comput. Methods Appl. Mech. Eng. 350, 535–553. doi:10.1016/j.cma.2019.03.021
Xu, W., Wu, Y., and Jia, M. (2018). Elastic dependence of particle-reinforced composites on anisotropic particle geometries and reinforced/weak interphase microstructures at nano- and micro-scales. Compos. Struct. 203, 124–131. doi:10.1016/j.compstruct.2018.07.009
Zaoui, A. (2002). Continuum micromechanics: Survey. J. Eng. Mech. 128, 808–816. doi:10.1061/(asce)0733-9399(2002)128:8(808)
Zeller, R., and Dederichs, P. (1973). Elastic constants of polycrystals. Phys. Status Solidi (b) 55, 831–842. doi:10.1002/pssb.2220550241
Keywords: complex microstructure, Green’s function, concentration tensor, homogenized stiffness, Fredholm integral
Citation: Jiménez Segura N, Pichler BLA and Hellmich C (2023) A Green’s function-based approach to the concentration tensor fields in arbitrary elastic microstructures. Front. Mater. 10:1137057. doi: 10.3389/fmats.2023.1137057
Received: 03 January 2023; Accepted: 13 March 2023;
Published: 21 April 2023.
Edited by:
Marek Pawlikowski, Warsaw University of Technology, PolandReviewed by:
Wenxiang Xu, Hohai University, ChinaReinaldo Rodriguez-Ramos, University of Havana, Cuba
Copyright © 2023 Jiménez Segura, Pichler and Hellmich. This is an open-access article distributed under the terms of the Creative Commons Attribution License (CC BY). The use, distribution or reproduction in other forums is permitted, provided the original author(s) and the copyright owner(s) are credited and that the original publication in this journal is cited, in accordance with accepted academic practice. No use, distribution or reproduction is permitted which does not comply with these terms.
*Correspondence: Christian Hellmich, Y2hyaXN0aWFuLmhlbGxtaWNoQHR1d2llbi5hYy5hdA==