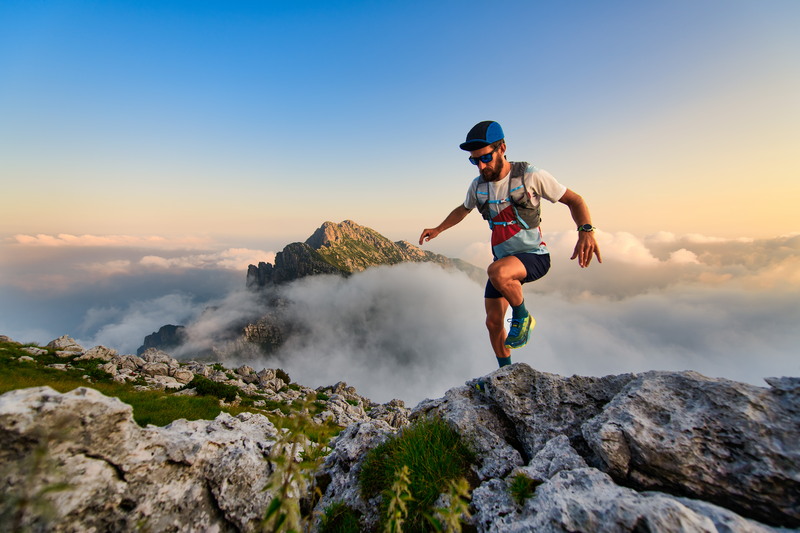
94% of researchers rate our articles as excellent or good
Learn more about the work of our research integrity team to safeguard the quality of each article we publish.
Find out more
MINI REVIEW article
Front. Mater. , 02 September 2022
Sec. Polymeric and Composite Materials
Volume 9 - 2022 | https://doi.org/10.3389/fmats.2022.990773
Carbon fiber reinforced polymer (CFRP) laminates are featured by superior mechanical properties and excellent structural functions, which have been a promising alternative to conventional alloys and steels in diverse industrial fields. Mechanical drilling is a compulsory operation to shape fibrous composites to desired workpiece quality and target dimensional accuracy. Progressive tool wear is an extremely crucial issue when drilling CFRPs as it may result in undesired machining consequences such as increased force generation, elevated temperatures, and deteriorated surface quality. Despite great endeavors already made to address the wear issues, a complete review of the wear phenomena for CFRP drilling is still significantly lacking. The present paper aims to report the key research advances in tool wear aspects when drilling CFRPs. The wear phenomena, wear modes, and tool failure mechanisms are carefully reviewed. The effects of wear progression on various drilling outputs of CFRP laminates, such as drilling forces, cutting temperatures, and surface quality attributes, are discussed. A particular focus is placed on the quantification and assessment of tool wear during drilling CFRPs. Some research prospects for both academia and industry are outlined. The paper intends to offer a comprehensive understanding of wear mechanisms controlling the drilling of CFRP laminates.
In recent years, carbon fiber reinforced polymers (CFRPs) are becoming increasingly popular in various industrial fields such as aerospace, automotive, and energy in view of their superior mechanical properties and excellent structural functions (Abrão et al., 2007; Liu et al., 2012; Che et al., 2014; Aamir et al., 2019; Geier et al., 2019; Xu et al., 2022). These fibrous composites have been a promising alternative to conventional alloys and steels as they provide the merits of structural functions meeting specific industrial design requirements. Although most CFRP components are fabricated into net shapes, mechanical drilling using cutting tools is a compulsory procedure to achieve desired workpiece quality and target dimensional accuracy for assembly purposes (Liu et al., 2012; Che et al., 2014; Fleischer et al., 2018; Aamir et al., 2019). However, it is rather challenging to drill CFRP materials with satisfied quality due to the extremely high abrasiveness and hardness of the reinforcing fibers and the rubbery matrix base. Even though tool wear is not a binding issue for the use of CFRPs in structural applications, it is still essential to address it to achieve high-efficiency drilling of CFRPs. Rapid tool wear is a very crucial factor that accounts for the decreased machining efficiency and increased costs for the drilling of CFRP composites. Particularly in a drilling operation, the tool edge segments rotate periodically to interact with the fibers and matrix alternately, leading to the nonuniform distribution of cutting load and heat generation along the tool edges during the material removal process. The highly abrasive reinforcing fibers then mechanically abrade and erode the drill edges while the soft matrix rubs against the tool surfaces, resulting in the blunting and dulling of the drill bits (Xu et al., 2021). To date, some investigations have pointed out the dominance of abrasion wear governing the wear progression of drill bits during the CFRP machining operations (Faraz et al., 2009; Mkaddem et al., 2013; Wang et al., 2013; Kuo et al., 2018; Xu et al., 2019; Xu et al., 2021). Additionally, process parameters, tool materials, and geometries are critical factors affecting the severity of drill wear for CFRPs. The cumulative wear extents can also initiate premature failures of cutting tools during the CFRP drilling, such as microchipping or edge fracture, accounting for a large proportion of tool rejection and the increase of machining costs. Another detrimental effect of tool wear arises from its negative impact on the drilling outputs of CFRP laminates. It is reported that tool wear plays a vital role in increasing cutting forces, elevating machining temperatures, and deteriorating surface quality and accuracy. Various undesirable consequences can be easily produced when the cutting tool becomes dulled or blunted. The increased tool wear can also exacerbate the generation of various composite damages during the drilling operations. Delamination, burrs, and tearing are critical issues associated with the drilling of CFRPs, which are greatly affected by the wear extent of drill bits. Excessive tool wear can lead to unacceptable interlaminar delamination, exit burrs, and surface tearing, accounting for a large proportion of composite part rejections. To date, although a lot of efforts have been made to evaluate the drilling tool performances for composite laminates, still very limited studies have paid attention to the tool wear issues for CFRP machining. A complete understanding of the complicated wear phenomena and effects is urgently required to guide the control of tool wear for CFRP drilling. Moreover, there are no review articles available in the scientific literature to deal with the drill wear issues for CFRP laminates.
The present paper attempts to carry out a rigorous literature survey and briefly summarize the state-of-the-art advances achieved in the aspects of drill wear for CFRP composites. It is aimed at addressing the fundamental wear issues associated with the CFRP drilling operations and at providing a complete understanding of wear mechanisms for the composites manufacturing community. The paper firstly illustrates the machinability behaviors of CFRP laminates. Then, the fundamental wear phenomena and mechanisms governing CFRP drilling are discussed. Afterward, the effects of tool wear on the CFRP drilling CFRP responses and wear monitoring are elaborated. Finally, some perspectives for both academic research and industrial development are proposed to guide the wear control for CFRP drilling.
The term “machinability” characterizes how difficult a workpiece material is to machine with desired quality and accuracy. Since CFRP laminates are anisotropic in behavior and heterogenous in architecture, their machinability is much poorer compared with conventional metallic materials. Additionally, due to the disparate properties between the carbon fibers and the polymer matrix, the chip removal of CFRPs is much more complicated than traditional homogeneous materials. A lot of investigations have revealed that most CFRP laminates undergo no plastic deformation during the cutting process, and brittle fracture governs the chip removal of the fibrous composites. The fibers tend to be separated without experiencing distinct plastic deformation, resulting in powdery chips in the form of dust for drilling operations (Chen, 1997; Rawat and Attia, 2009). Additionally, the dominance of brittle fracture also makes the tool-chip contact length too short to induce crater wear onto the rake face of drills during the drilling process. Since chips are mainly resected within the tool edge radius zone, abrasion wear becomes prevalent in the tip zone. Due to the directionality of CFRP laminates, the material separation mechanisms are highly dependent on the fiber layup or stacking sequences of the plies. Moreover, the fundamental mechanisms controlling the separation of CFRPs mainly include compression-induced shearing, bending-induced shearing, interfacial debonding, and fiber fracture (Sreejith et al., 2000; Gordon and Hillery, 2003). Koplev and Bunsell (1980) and Koplev et al. (1983) were among the earliest to investigate the chip removal mechanisms of UD-CFRPs using the quick-stop technique. The work showed that brittle fracture dominates the CFRP cutting process, and the composite chips are mainly short and discontinuous. The fiber layup was also found to play a key role in the CFRP chip formation. Wang et al. (1995) conducted the orthogonal cutting experiments of UD-CFRP laminates and studied the impacts of tool geometries and cutting parameters on fiber/matrix removal. The results showed that the composite chips mainly exist in a discontinuous form, and the chip formation involves fiber cutting, fiber shearing, and interfacial fracture. Iliescu et al. (2010b) utilized the discrete element method to inspect the orthogonal cutting mechanisms of UD-CFRPs. The results showed that when the fiber orientation is 0°, fiber fracture is mainly dominated by compression, bending, and delamination modes. When the fiber orientation is 45°, the fibers residing within the machined surface are prone to spring back following the tool advancement, which will cause severe scratches on the tool flank surface and thus aggravate the abrasion wear. However, when the fiber orientation is 135°, fiber fracture is mainly caused by the extrusion and bending of the cutting tool, and the tool wear becomes very minimal, but the composite material is prone to crucial defects such as fiber pullouts and matrix loss. Feito et al. (2018) developed numerical models to inspect the drilling mechanisms of CFRPs using step drills. Results indicated that the step drills could produce much lower thrust forces and delamination factors at low feed rates than the conventional twist drills. Additionally, the use of the supporting back plate also greatly decreased the drilling-induced damages for CFRPs. Su (2019) studied the effect of the cutting speed on the machining mechanisms of CFRPs at the micro level via the numerical simulation method. The author developed a three-dimensional finite element model of orthogonal cutting CFRPs and revealed that increasing the cutting speed could effectively decrease the fiber deformation, resin cracking and extension degree. In addition, the specific energy gap for different chip formation modes also becomes smaller and smaller with the increase of the cutting speed. Yan et al. (2019) investigated the energy dissipating mechanisms in orthogonal cutting of CFRP composites and found that dissipated energies associated with various failure modes and friction varied with the fiber orientation. Additionally, the surface roughness of cut composites was firmly related to the fiber damage and the direction of propagation of fiber-matrix debonding. Shu et al. (2021) also addressed the effects of special drill bits on the cutting mechanisms of CFRPs. The results indicated that the shear cutting often became dominant in the drilling with properly designed rake angles, while the crushing/compression was dominant with the conventional drill bit. Besides, the conductive nature of reinforcing fibers could also significantly affect the thermal aspects in drilling fibrous composites (Erturk et al., 2019; Liu et al., 2020; Erturk et al., 2021; Sorrentino et al., 2022). Sorrentino et al. (2022) stated that the low conductive nature of the FRP compared to aluminum determined a thermal energy concentration near the tool/composite interface. Moreover, some other scholars (Arola et al., 2002; Venu Gopala Rao et al., 2008; Rentsch et al., 2011; Santiuste et al., 2011; Calzada et al., 2012; Usui et al., 2014; Anand and Patra, 2017; Li et al., 2017; Shetty et al., 2017; Yan et al., 2019) also conducted investigations on the cutting mechanisms of CFRPs. Since the chip removal mechanism is the key factor determining the actual tool-composite interaction and wear development conditions, more intensive work concerning the optimization of the CFRP machining process and the correlation between the chip removal and tool wear should be performed.
Due to the peculiar structure of the fiber/matrix system, drilling CFRPs entails specific wear mechanisms during the chip removal process. In general, excessive tool wear is firmly associated with mechanical erosions and abrasions arising from the hard contact between the tool edges and the carbon fibers. As the actual tool-chip contact length is very narrow to trigger crater wear, abrasion wear occurring in the vicinity of the edge radius zone becomes very prevalent during the composite separation process. Then, numerous hard carbon fibers tend to rub the edge radius zone aggressively and may cause the enlargement of the cutting-edge radius (CER). Additionally, abrasion wear can leave apparent signatures onto the drill flank regime in the form of dislodging tool particles from the tool surface during the intensive tool-work interaction. The phenomenon is attributed to the spring back of bent carbon fibers that mechanically abrades the tool flank zone. Besides, abrasion wear may operate following a two-body or a three-body mode depending on the relative hardness between the cutting tool and the carbon fibers (Rawat and Attia, 2009). Most scientific literature has pointed out that abrasion wear in the form of CER is the key wear mechanism governing the drilling of CFRPs despite some differences observed in terms of varying tool materials and geometries (Ref. Table 1) (Faraz et al., 2009; Rawat and Attia, 2009; Wang et al., 2013; Cadorin and Zitoune, 2015; Hrechuk et al., 2018; Kuo et al., 2018; Xu et al., 2019; Xu et al., 2021). Due to cumulative abrasion wear effects, microchipping, edge fracture, or coating delamination may take place, resulting in the premature failures of cutting tools. Figure 1 shows the main wear morphologies of different drills during the machining of CFRP laminates, in which abrasion wear marks, CER phenomena and microchipping failures are noted around the cutting edges. For instance, Rawat and Attia (2009) stated that chipping and abrasion were the main mechanisms controlling the deterioration of WC drills when drilling woven CFRP laminates. During the primary and secondary wear stages, wear on the flank face of the main cutting edges was identified to be dominant, while adhesion of carbon occurred along with abrasion in the tertiary zone. Faraz et al. (2009) highlighted the CER phenomena of drill bits due to abrasion wear during the drilling of CFRP laminates. Cadorin and Zitoune (2015) revealed that abrasion on the flank face and delamination of the coating layers were respectively the main wear mode and failure pattern for diamond-coated twist drills when drilling CFRPs. Kuo et al. (2018) identified that chipping and coating delamination dominate the failures of double point angle drills, while progressive abrasion wear, scoring, and severe three-body abrasion along the cutting lips on the first, second, and the third facets govern the wear of multi-facet drills for the drilling of woven CFRPs. Moreover, Xu et al. (2021) emphasized the unevenly-distributed flank wear signatures for drills during the CFRP machining. The authors pointed out that for all the cutting tools examined, the drill edge segments residing close to the tool periphery basically undergo the most severe abrasion wear due to the highest instantaneous cutting speed involved. Such findings revealed the fundamental flank wear features of drill edges during the drilling of CFRPs and highlighted the vital role of the instantaneous cutting speed on the wear extents. Barik and Pal (2022) addressed the tool wear progression of different tools when drilling woven CFRP composites. The results indicated that the flank wear was increased with an increase in the number of holes irrespective of the tool type. The worn-out tool normally produced moderately enhanced thrust directly responsible for severe delamination damage. Qiu et al. (2022) analyzed the wear behaviors of different drills in CFRP drilling and found that the maximum tool wear position often existed at the outer corner of tools, and the reverse edge compound drill yielded the longest tool life compared with the double point angle drill and the stepped drill. Moreover, Kim et al. (2022) also studied the wear issues of diamond-coated tools in high-feed drilling of CFRPs and found that coating peeling and chipping of tool substrate were the main modes governing the failure of diamond-coated drills.
FIGURE 1. The wear morphologies of different tools during the CFRP drilling: (A) multi-facet drills (Kuo et al., 2018); (B) diamond-coated drills (Wang et al., 2013).
Additionally, unlike the machining of metallic alloys, drilling CFRP laminates is likely to produce lower magnitudes of cutting temperatures due to the fracture-dominated cutting, which makes it difficult to induce crater wear or diffusion wear during the chip removal process. In some cases, adhesion wear due to temperature rise at the aggressive tool-composite interaction may occur but not be as dominant as abrasion wear during the CFRP drilling (Rawat and Attia, 2009). Moreover, it is worth mentioning that size effects can easily take place during the wear process of cutting tools for CFRP drilling. Since abrasion wear and CER are fundamental wear phenomena, the enlarged CER due to progressively blunted tools can entail a high risk of being larger than the used feed rate. Then, all the chips will be separated only within the edge radius zone, which makes the material removal more difficult to proceed. As a consequence, plowing action becomes a dominant mode instead of shearing for composite separation. Then, uncut chips will cause severe extrusion and squeezing onto the drill edges, exacerbating the wear progression and deteriorating the machined surface quality. To avoid the detrimental size effects, a careful selection of process parameters and a strict control of wear development should be undertaken when carrying out the drilling operations of CFRP laminates.
The main factors influencing the wear progression of drills for CFRP laminates include cutting parameters, tool geometries/materials, and cutting environments. Cutting speed and feed rate are two critical parameters controlling the drilling kinematics of CFRP laminates as they determine the actual tribo-mechanical interaction between the cutting tool and the workpiece specimen. Increasing the cutting speed is confirmed to accelerate the wear progression of drills during the CFRP machining (Rawat and Attia, 2009). The phenomenon is attributed to the elevated sliding velocity between the drill edges and the composite material that exacerbates the mechanical interaction of the tool-composite system. Additionally, elevating the feed rate also exacerbates the wear degree as the tool-work interaction gets intensified owing to the increased uncut chip volume (Dogrusadik and Kentli, 2019b).
Tool materials affect the wear development of drills as they influence the mechanical properties of the tool-composite interaction governing the CFRP drilling. Conventional tungsten carbide drills are widely demonstrated incapable of withstanding progressive abrasion wear during the CFRP machining, yielding a rather short tool life. However, superior tool coating with high wear resistance can effectively reduce the wear severity and prolong the tool life. Normally, the use of diamond coating can yield a decreased extent of edge rounding wear and extended drill life during the machining of CFRP laminates (Iliescu et al., 2010a; Wang et al., 2013). Additionally, polycrystalline diamond (PCD) tools can be a promising alternative to resist intensive wear during CFRP drilling because of their extremely high hardness and superior thermal behavior (Hrechuk et al., 2018). Apart from tool materials, tool geometries denoting the geometrical structures of cutting edges can also influence the progression of drill wear for CFRP machining. To date, various types of special drills differing in geometrical features have been developed for CFRP cutting with the aim of improving the hole quality and decreasing the tool wear (Karpat et al., 2012; Xu et al., 2013; Karpat et al., 2014; Raj and Karunamoorthy, 2016; Kuo et al., 2018; Xu et al., 2019). The advantages of functionally-designed tools lie in their ability to disperse the drilling forces around the peripheral edges to alleviate the intensive tool-composite interaction during CFRP drilling (Hocheng and Tsao, 2003; Hocheng and Tsao, 2005, 2006; Tsao, 2006, 2008).
Finally, cutting environments entailing the use of MQL coolants, air cooling, or cryogenic conditions are essential parameters to affect the wear progression of drills in machining CFRPs (Xia et al., 2016; Kerrigan and Scaife, 2018; Wang et al., 2018; Kim et al., 2019; Iqbal et al., 2021). This is attributed to their ability to modify the lubricating and cooling conditions of the tool-composite interaction during the chip removal, thus altering the wear development. In most cases, cryogenic cooling shows benefits on reducing the CER and outer corner wear of drill bits for CFRP drilling (Xia et al., 2016). The use of nano-solid lubrication was also confirmed effective in reducing abrasion wear and in eliminating chipping compared with the dry drilling environments (Kim et al., 2019) due to the decreased friction of the tool-work interaction. To minimize the drill wear and prolong the tool life for CFRP laminates, more intensive research works should be focused on optimizing process parameters, developing superior special drills, and applying favorable cutting environments.
Quantifying the severity of tool wear in drilling CFRPs is a very challenging task due to the nonuniform wear signatures distributed along the worn drill surfaces as well as the abrasion-dominated wear mode. Measuring either the average flank wear width or CER represents the most-preferred method (Faraz et al., 2009; Rawat and Attia, 2009; Xia et al., 2016; Kuo et al., 2018; Iqbal et al., 2021). As each edge segment is subjected to different cutting speeds during the composite drilling operation, the drill edge segments residing far away from the drill tip zone tend to experience a larger extent of wear due to the higher instantaneous speed involved, while the edge segment close to the tip zone undergoes the lower degree of wear. Therefore, measuring the average flank wear width can ensure a fair evaluation of tool performance and its serving life. Since such a measurement can be done manually via an optical microscope, it has become a convenient means being extensively used in various studies (Inoue et al., 1997; Ogawa et al., 2012, 2015; James and Sonate, 2018; Dogrusadik and Kentli, 2019a; Dogrusadik and Kentli, 2019b; Kim et al., 2019; Fu et al., 2020; Huang et al., 2021; Kim et al., 2021). However, since the flank wear land around drill edges is often nonuniform and irregular, flank wear width may not be a perfect indicator to quantify the actual drill wear severity during drilling of CFRP laminates. Then, the CER could be a promising alternative for the drill wear assessment as abrasion wear dominates the dulling of cutting edges. It was reported that the CER could be more effective in quantifying the tool wear progression as it correlated well with the composite drilling outputs (Faraz et al., 2009). However, measuring the CER is not very easy and can be easily constrained by existing equipment. Therefore, to realize the convenient and accurate tool wear evaluation, more endeavors need to be made in the future to develop comprehensive indicators and automated systems adapted to drill wear measurement.
Tool wear is a detrimental issue for high-quality drilling of CFRP laminates, which can result in various undesired drilling responses such as elevated cutting forces/temperatures, exacerbated surface damages, and deteriorated hole quality. Progression of tool wear will definitely cause a significant increase of cutting forces and temperatures due to the increased friction between the tool and the composite specimen (Rawat and Attia, 2009; Wang et al., 2013; Xia et al., 2016; Xu et al., 2021). Additionally, tool wear can also significantly affect the chip formation due to the changes in the tool-composite interaction, in which shorter chips are produced by a worn cutting edge rather than a fresh cutting edge (Xu and Zhang, 2018). Drilling-induced damages can be affected by progressive wear during the machining of CFRPs due to the exacerbated thermo-mechanical interaction of the tool-workpiece system. For instance, delamination (Bonnet et al., 2015; Li et al., 2015; Gaugel et al., 2016; Voß et al., 2016), burrs (Hintze et al., 2011; Hosokawa et al., 2014), and subsurface damages (Sahraie Jahromi and Bahr, 2010; Haddad et al., 2014; Turki et al., 2014; Henerichs et al., 2015) that are recognized as critical issues for CFRP drilling are all affected by the wear extent. It has been extensively confirmed that an increased wear extent will lead to a dramatic elevation of the aforementioned drilling damages for CFRP laminates irrespective of the varying tool materials or geometries (Rawat and Attia, 2009; Xu and Zhang, 2018). Additionally, hole dimensional accuracy attributes involving hole diameter, circularity or cylindricity errors are also greatly impacted by the tool wear. It is reported that an increased tool wear extent will deteriorate the hole dimensional accuracy, such as increasing the diameter error or cylindricity errors due to the inability of worn drill edges to shape smoothly the hole walls (Rawat and Attia, 2009). Despite the extensive studies performed, physical models depicting the correlations between the tool wear progression and various drilling responses of CFRPs are still significantly lacking. More efforts need to be made on this regard in the future.
Since tool wear is a key factor influencing the CFRP drilling operations, its monitoring and control are of vital importance to the current manufacturing sectors. Tool wear monitoring can be roughly divided into direct and indirect monitoring (Zhou et al., 2022). Direct measurements mainly involve the optical image method, the contact resistance method and the radiometric method. However, these methods require a stoppage to detect the tool and have no real-time monitoring function. The measurement results are also affected by cutting fluids, lighting and chips (Zhou et al., 2022). In contrast, the indirect measurement method uses the effect of the state of the tool when it is worn or about to break with specific working parameters. Various signals reflecting tool wear and breakage can be collected by means of sensors and the mapping between them, and the tool wear can be analyzed to obtain the tool wear state. For instance, Ramirez et al. (2014) have reported that the tool wear shows a close relationship with the cutting forces and temperatures during the CFRP drilling, which can be used as indirect parameters to monitor the wear status of drill bits. To minimize the detrimental effects of progressive tool wear during the CFRP drilling, in-situ monitoring and active control of wear progression would be an effective strategy that should be rigorously undertaken in both academia and industry. Currently, with the development of artificial intelligence, online monitoring and RUL prediction technology based on the big data, data-driven algorithms, and self-learning intelligent machining equipment start to emerge and will become the future research trends in the fields of tool wear monitoring for CFRP drilling.
Mechanical drilling is a critical procedure prior to the final application of CFRP laminates in diverse industries. Tool wear has been a crucial issue that must be carefully controlled and minimized in order to achieve damage-free composite parts. The key wear mechanism controlling the drilling of CFRP laminates is progressive abrasion wear in the form of CER due to the highly abrasive carbon fibers and the poor machinability of the fiber/matrix system. Tool wear is strongly affected by various input process parameters and shows detrimental effects on the composite drilling outputs, especially the quality attributes. To date, although great endeavors have been made to address the wear issues during CFRP drilling, a complete understanding of wear phenomena at the micro-scale level and a rigorous quantification of correlations between tool wear and various drilling responses are still significantly lacking. To effectively control tool wear and minimize its detrimental effects, monitoring tool conditions would be a promising means for the manufacturing community. With the development of artificial intelligence, various algorithms (e.g., artificial neural network, hidden Markov model, support vector machine, etc.) have been successfully applied to predict tool wear state during the drilling of CFRPs. However, to realize high-accuracy monitoring of tool wear, more efforts are still required to develop both high-reliable equipment and algorithms. Furthermore, to improve the wear resistance and service life of drill bits, more attention must be paid to optimizing tool geometries and developing high-performance tool materials for the CFRP laminates.
JX drafted the entire manuscript.
The work was funded by the National Natural Science Foundation of China (Grant No. 52175425) and the ninth Sino-Hungarian Intergovernmental Scientific and Technological Cooperation Project (Grant No. 2021-07).
The author declares that the research was conducted in the absence of any commercial or financial relationships that could be construed as a potential conflict of interest.
All claims expressed in this article are solely those of the authors and do not necessarily represent those of their affiliated organizations, or those of the publisher, the editors and the reviewers. Any product that may be evaluated in this article, or claim that may be made by its manufacturer, is not guaranteed or endorsed by the publisher.
Aamir, M., Tolouei-Rad, M., Giasin, K., and Nosrati, A. (2019). Recent advances in drilling of carbon fiber–reinforced polymers for aerospace applications: A review. Int. J. Adv. Manuf. Technol. 105 (5), 2289–2308. doi:10.1007/s00170-019-04348-z
Abrão, A. M., Faria, P. E., Rubio, J. C. C., Reis, P., and Davim, J. P. (2007). Drilling of fiber reinforced plastics: A review. J. Mat. Process. Technol. 186 (1-3), 1–7. doi:10.1016/j.jmatprotec.2006.11.146
Anand, R. S., and Patra, K. (2017). Mechanistic cutting force modelling for micro-drilling of CFRP composite laminates. CIRP J. Manuf. Sci. Technol. 16, 55–63. doi:10.1016/j.cirpj.2016.07.002
Arola, D., Sultan, M. B., and Ramulu, M. (2002). Finite element modeling of edge trimming fiber reinforced plastics. J. Manuf. Sci. Eng. 124 (1), 32–41. doi:10.1115/1.1428329
Barik, T., and Pal, K. (2022). Prediction of TiAlN- and TiN-coated carbide tool wear in drilling of bidirectional CFRP laminates using wavelet packets of thrust–torque signatures. J. Braz. Soc. Mech. Sci. Eng. 44 (8), 364. doi:10.1007/s40430-022-03673-x
Bonnet, C., Poulachon, G., Rech, J., Girard, Y., and Costes, J. P. (2015). CFRP drilling: Fundamental study of local feed force and consequences on hole exit damage. Int. J. Mach. Tools Manuf. 94, 57–64. doi:10.1016/j.ijmachtools.2015.04.006
Cadorin, N., and Zitoune, R. (2015). Wear signature on hole defects as a function of cutting tool material for drilling 3D interlock composite. Wear 332-333, 742–751. doi:10.1016/j.wear.2015.01.019
Calzada, K. A., Kapoor, S. G., DeVor, R. E., Samuel, J., and Srivastava, A. K. (2012). Modeling and interpretation of fiber orientation-based failure mechanisms in machining of carbon fiber-reinforced polymer composites. J. Manuf. Process. 14 (2), 141–149. doi:10.1016/j.jmapro.2011.09.005
Che, D., Saxena, I., Han, P., Guo, P., and Ehmann, K. F. (2014). Machining of carbon fiber reinforced plastics/polymers: A literature review. J. Manuf. Sci. Eng. 136 (3), 034001. doi:10.1115/1.4026526
Chen, W. C. (1997). Some experimental investigations in the drilling of carbon fiber-reinforced plastic (CFRP) composite laminates. Int. J. Mach. Tools Manuf. 37 (8), 1097–1108. doi:10.1016/s0890-6955(96)00095-8
Dogrusadik, A., and Kentli, A. (2019a). Effect of support plates on the micro-drilled hole form quality in CFRP laminates. Mater. Test. 61 (5), 467–476. doi:10.3139/120.111343
Dogrusadik, A., and Kentli, A. (2019b). Experimental investigation of support plates’ influences on tool wear in micro-drilling of CFRP laminates. J. Manuf. Process. 38, 214–222. doi:10.1016/j.jmapro.2019.01.018
Erturk, A. T., Vatansever, F., Yarar, E., Guven, E. A., and Sinmazcelik, T. (2021). Effects of cutting temperature and process optimization in drilling of GFRP composites. J. Compos. Mat. 55 (2), 235–249. doi:10.1177/0021998320947143
Erturk, A. T., Vatansever, F., Yarar, E., and Karabay, S. (2019). Machining behavior of multiple layer polymer composite bearing with using different drill bits. Compos. Part B Eng. 176, 107318. doi:10.1016/j.compositesb.2019.107318
Faraz, A., Biermann, D., and Weinert, K. (2009). Cutting edge rounding: An innovative tool wear criterion in drilling CFRP composite laminates. Int. J. Mach. Tools Manuf. 49 (15), 1185–1196. doi:10.1016/j.ijmachtools.2009.08.002
Feito, N., Díaz-Álvarez, J., López-Puente, J., and Miguelez, M. (2018). Experimental and numerical analysis of step drill bit performance when drilling woven CFRPs. Compos. Struct. 184, 1147–1155. doi:10.1016/j.compstruct.2017.10.061
Fleischer, J., Teti, R., Lanza, G., Mativenga, P., Möhring, H.-C., and Caggiano, A. (2018). Composite materials parts manufacturing. CIRP Ann. 67 (2), 603–626. doi:10.1016/j.cirp.2018.05.005
Fu, G., Huo, D., Shyha, I., Pancholi, K., and Alzahrani, B. (2020). Experimental investigation on micromachining of epoxy/graphene nano platelet nanocomposites. Int. J. Adv. Manuf. Technol. 107 (7), 3169–3183. doi:10.1007/s00170-020-05190-4
Gaugel, S., Sripathy, P., Haeger, A., Meinhard, D., Bernthaler, T., Lissek, F., et al. (2016). A comparative study on tool wear and laminate damage in drilling of carbon-fiber reinforced polymers (CFRP). Compos. Struct. 155, 173–183. doi:10.1016/j.compstruct.2016.08.004
Geier, N., Davim, J. P., and Szalay, T. (2019). Advanced cutting tools and technologies for drilling carbon fibre reinforced polymer (CFRP) composites: A review. Compos. Part A Appl. Sci. Manuf. 125, 105552. doi:10.1016/j.compositesa.2019.105552
Gordon, S., and Hillery, M. T. (2003). A review of the cutting of composite materials. Proc. Inst. Mech. Eng. Part L J. Mater. Des. Appl. 217 (1), 35–45. doi:10.1177/146442070321700105
Haddad, M., Zitoune, R., Bougherara, H., Eyma, F., and Castanié, B. (2014). Study of trimming damages of CFRP structures in function of the machining processes and their impact on the mechanical behavior. Compos. Part B Eng. 57, 136–143. doi:10.1016/j.compositesb.2013.09.051
Henerichs, M., Voß, R., Kuster, F., and Wegener, K. (2015). Machining of carbon fiber reinforced plastics: Influence of tool geometry and fiber orientation on the machining forces. CIRP J. Manuf. Sci. Technol. 9, 136–145. doi:10.1016/j.cirpj.2014.11.002
Hintze, W., Hartmann, D., and Schütte, C. (2011). Occurrence and propagation of delamination during the machining of carbon fibre reinforced plastics (CFRPs) – an experimental study. Compos. Sci. Technol. 71 (15), 1719–1726. doi:10.1016/j.compscitech.2011.08.002
Hocheng, H., and Tsao, C. C. (2003). Comprehensive analysis of delamination in drilling of composite materials with various drill bits. J. Mat. Process. Technol. 140 (1-3), 335–339. doi:10.1016/s0924-0136(03)00749-0
Hocheng, H., and Tsao, C. C. (2005). The path towards delamination-free drilling of composite materials. J. Mat. Process. Technol. 167 (2-3), 251–264. doi:10.1016/j.jmatprotec.2005.06.039
Hocheng, H., and Tsao, C. C. (2006). Effects of special drill bits on drilling-induced delamination of composite materials. Int. J. Mach. Tools Manuf. 46 (12-13), 1403–1416. doi:10.1016/j.ijmachtools.2005.10.004
Hosokawa, A., Hirose, N., Ueda, T., and Furumoto, T. (2014). High-quality machining of CFRP with high helix end mill. CIRP Ann. 63 (1), 89–92. doi:10.1016/j.cirp.2014.03.084
Hrechuk, A., Bushlya, V., M’Saoubi, R., and Ståhl, J.-E. (2018). Experimental investigations into tool wear of drilling CFRP. Procedia Manuf. 25, 294–301. doi:10.1016/j.promfg.2018.06.086
Huang, X., Wang, C., Yang, T., He, Y., Li, Y., and Zheng, L. (2021). Wear characteristics of micro-drill during ultra-high speed drilling multi-layer PCB consisting of copper foil and ceramic particle filled GFRPs. Procedia CIRP 101, 326–329. doi:10.1016/j.procir.2020.10.007
Iliescu, D., Gehin, D., Gutierrez, M. E., and Girot, F. (2010a). Modeling and tool wear in drilling of CFRP. Int. J. Mach. Tools Manuf. 50 (2), 204–213. doi:10.1016/j.ijmachtools.2009.10.004
Iliescu, D., Gehin, D., Iordanoff, I., Girot, F., and Gutiérrez, M. E. (2010b). A discrete element method for the simulation of CFRP cutting. Compos. Sci. Technol. 70 (1), 73–80. doi:10.1016/j.compscitech.2009.09.007
Inoue, H., Aoyama, E., Hirogaki, T., Ogawa, K., Matushita, H., Kitahara, Y., et al. (1997). Influence of tool wear on internal damage in small diameter drilling in GFRP. Compos. Struct. 39 (1), 55–62. doi:10.1016/s0263-8223(97)00068-8
Iqbal, A., Zhao, G., Zaini, J., Jamil, M., Nauman, M. M., Khan, A. M., et al. (2021). CFRP drilling under throttle and evaporative cryogenic cooling and micro-lubrication. Compos. Struct. 267, 113916. doi:10.1016/j.compstruct.2021.113916
James, S., and Sonate, A. (2018). Experimental study on micromachining of CFRP/Ti stacks using micro ultrasonic machining process. Int. J. Adv. Manuf. Technol. 95 (1), 1539–1547. doi:10.1007/s00170-017-1298-6
Karpat, Y., Değer, B., and Bahtiyar, O. (2012). Drilling thick fabric woven CFRP laminates with double point angle drills. J. Mat. Process. Technol. 212 (10), 2117–2127. doi:10.1016/j.jmatprotec.2012.05.017
Karpat, Y., Değer, B., and Bahtiyar, O. (2014). Experimental evaluation of polycrystalline diamond tool geometries while drilling carbon fiber-reinforced plastics. Int. J. Adv. Manuf. Technol. 71 (5-8), 1295–1307. doi:10.1007/s00170-013-5592-7
Kerrigan, K., and Scaife, R. J. (2018). Wet vs dry CFRP drilling: Influence of cutting fluid on tool performance. Procedia CIRP 77, 315–319. doi:10.1016/j.procir.2018.09.024
Kim, J. W., Nam, J., and Lee, S. W. (2019). Experimental study on micro-drilling of unidirectional carbon fiber reinforced plastic (UD-CFRP) composite using nano-solid lubrication. J. Manuf. Process. 43, 46–53. doi:10.1016/j.jmapro.2019.04.022
Kim, J. W., Nam, J., Jeon, J., and Lee, S. W. (2021). A study on machining performances of micro-drilling of multi-directional carbon fiber reinforced plastic (MD-CFRP) based on nano-solid dry lubrication using graphene nanoPlatelets. Materials 14 (3), 685. doi:10.3390/ma14030685
Kim, G., Kim, T.-G., Lee, S.-W., and Min, B.-K. (2022). Effect of workpiece preheating on tool wear and delamination at the hole exit in high feed drilling of carbon fiber reinforced plastics with diamond-coated tools. J. Manuf. Process. 74, 233–243. doi:10.1016/j.jmapro.2021.12.013
Koplev, A., and Bunsell, A. (1980). “Cutting of CFRP with single edge tools,” in Proceeding of the 3rd International Conference of Advances in Composite Materials, Paris, France, Aug 1980 (Pergamon Press), 1597–1605.
Koplev, A., Lystrup, A., and Vorm, T. (1983). The cutting process, chips, and cutting forces in machining CFRP. Composites 14 (4), 371–376. doi:10.1016/0010-4361(83)90157-x
Kuo, C., Wang, C., and Ko, S. (2018). Wear behaviour of CVD diamond-coated tools in the drilling of woven CFRP composites. Wear 398-399, 1–12. doi:10.1016/j.wear.2017.11.015
Li, N., Li, Y., Zhou, J., He, Y., and Hao, X. (2015). Drilling delamination and thermal damage of carbon nanotube/carbon fiber reinforced epoxy composites processed by microwave curing. Int. J. Mach. Tools Manuf. 97, 11–17. doi:10.1016/j.ijmachtools.2015.06.005
Li, H., Qin, X., He, G., Price, M. A., Jin, Y., and Sun, D. (2017). An energy based force prediction method for UD-CFRP orthogonal machining. Compos. Struct. 159, 34–43. doi:10.1016/j.compstruct.2016.09.051
Liu, D., Tang, Y., and Cong, W. L. (2012). A review of mechanical drilling for composite laminates. Compos. Struct. 94 (4), 1265–1279. doi:10.1016/j.compstruct.2011.11.024
Liu, S., Yang, T., Liu, C., Jin, Y., Sun, D., and Shen, Y. (2020). Modelling and experimental validation on drilling delamination of aramid fiber reinforced plastic composites. Compos. Struct. 236, 111907. doi:10.1016/j.compstruct.2020.111907
Mkaddem, A., Ben Soussia, A., and El Mansori, M. (2013). Wear resistance of CVD and PVD multilayer coatings when dry cutting fiber reinforced polymers (FRP). Wear 302 (1), 946–954. doi:10.1016/j.wear.2013.03.017
Ogawa, K., Nakagawa, H., Hirogaki, T., and Aoyama, E. (2012). Micro-drilling of CFRP plates using a high-speed spindle. Key Eng. Mat. 523-524, 1035–1040. doi:10.4028/www.scientific.net/kem.523-524.1035
Ogawa, K., Nakagawa, H., Hirogaki, T., and Aoyama, E. (2015). Effects of diamondcoated tools in micro-drilling of CFRP plates using a high-speed spindle. Adv. Mater. Process. Technol. 1 (1-2), 192–200. doi:10.1080/2374068x.2015.1118992
Qiu, X., Li, P., Li, C., Niu, Q., Li, S., Ko, T. J., et al. (2022). Tool life evaluation of CFRP drilling with three kinds of drill. J. Mech. Sci. Technol. 36 (7), 3643–3651. doi:10.1007/s12206-022-0639-z
Raj, D. S., and Karunamoorthy, L. (2016). Study of the effect of tool wear on hole quality in drilling CFRP to select a suitable drill for multi-criteria hole quality. Mater. Manuf. Process. 31 (5), 587–592. doi:10.1080/10426914.2015.1004713
Ramirez, C., Poulachon, G., Rossi, F., and M'Saoubi, R. (2014). Tool wear monitoring and hole surface quality during CFRP drilling. Procedia CIRP 13, 163–168. doi:10.1016/j.procir.2014.04.028
Rawat, S., and Attia, H. (2009). Wear mechanisms and tool life management of WC-Co drills during dry high speed drilling of woven carbon fibre composites. Wear 267 (5-8), 1022–1030. doi:10.1016/j.wear.2009.01.031
Rentsch, R., Pecat, O., and Brinksmeier, E. (2011). Macro and micro process modeling of the cutting of carbon fiber reinforced plastics using FEM. Procedia Eng. 10, 1823–1828. doi:10.1016/j.proeng.2011.04.303
Sahraie Jahromi, A., and Bahr, B. (2010). An analytical method for predicting cutting forces in orthogonal machining of unidirectional composites. Compos. Sci. Technol. 70 (16), 2290–2297. doi:10.1016/j.compscitech.2010.09.005
Santiuste, C., Miguélez, H., and Soldani, X. (2011). Out-of-plane failure mechanisms in LFRP composite cutting. Compos. Struct. 93 (11), 2706–2713. doi:10.1016/j.compstruct.2011.05.034
Shetty, N., Shahabaz, S., Sharma, S., and Shetty, S. D. (2017). A review on finite element method for machining of composite materials. Compos. Struct. 176, 790–802. doi:10.1016/j.compstruct.2017.06.012
Shu, L., Li, S., Fang, Z., Kizaki, T., Kimura, K., Arai, G., et al. (2021). Study on dedicated drill bit design for carbon fiber reinforced polymer drilling with improved cutting mechanism. Compos. Part A Appl. Sci. Manuf. 142, 106259. doi:10.1016/j.compositesa.2020.106259
Sorrentino, L., Turchetta, S., and Parodo, G. (2022). Drilling of glare laminates: Effect of cutting parameters on process forces and temperatures. Int. J. Adv. Manuf. Technol. 120 (1), 645–657. doi:10.1007/s00170-021-08612-z
Sreejith, P. S., Krishnamurthy, R., Malhotra, S. K., and Narayanasamy, K. (2000). Evaluation of PCD tool performance during machining of carbon/phenolic ablative composites. J. Mat. Process. Technol. 104 (1), 53–58. doi:10.1016/s0924-0136(00)00549-5
Su, Y. (2019). Effect of the cutting speed on the cutting mechanism in machining CFRP. Compos. Struct. 220, 662–676. doi:10.1016/j.compstruct.2019.04.052
Tsao, C. C. (2006). Prediction of thrust force of step drill in drilling composite material by Taguchi method and radial basis function network. Int. J. Adv. Manuf. Technol. 36 (1-2), 11–18. doi:10.1007/s00170-006-0808-8
Tsao, C. C. (2008). Experimental study of drilling composite materials with step-core drill. Mat. Des. 29 (9), 1740–1744. doi:10.1016/j.matdes.2008.03.022
Turki, Y., Habak, M., Velasco, R., Aboura, Z., Khellil, K., and Vantomme, P. (2014). Experimental investigation of drilling damage and stitching effects on the mechanical behavior of carbon/epoxy composites. Int. J. Mach. Tools Manuf. 87, 61–72. doi:10.1016/j.ijmachtools.2014.06.004
Usui, S., Wadell, J., and Marusich, T. (2014). Finite element modeling of carbon fiber composite orthogonal cutting and drilling. Procedia CIRP 14, 211–216. doi:10.1016/j.procir.2014.03.081
Venu Gopala Rao, G., Mahajan, P., and Bhatnagar, N. (2008). Three-dimensional macro-mechanical finite element model for machining of unidirectional-fiber reinforced polymer composites. Mater. Sci. Eng. A 498 (1-2), 142–149. doi:10.1016/j.msea.2007.11.157
Voß, R., Henerichs, M., Rupp, S., Kuster, F., and Wegener, K. (2016). Evaluation of bore exit quality for fibre reinforced plastics including delamination and uncut fibres. CIRP J. Manuf. Sci. Technol. 12, 56–66. doi:10.1016/j.cirpj.2015.09.003
Wang, D. H., Ramulu, M., and Arola, D. (1995). Orthogonal cutting mechanisms of graphite/epoxy composite. Part I: Unidirectional laminate. Int. J. Mach. Tools Manuf. 35 (12), 1623–1638. doi:10.1016/0890-6955(95)00014-o
Wang, X., Kwon, P. Y., Sturtevant, C., Kim, D., and Lantrip, J. (2013). Tool wear of coated drills in drilling CFRP. J. Manuf. Process. 15 (1), 127–135. doi:10.1016/j.jmapro.2012.09.019
Wang, F., Qian, B., Jia, Z., Cheng, D., and Fu, R. (2018). Effects of cooling position on tool wear reduction of secondary cutting edge corner of one-shot drill bit in drilling CFRP. Int. J. Adv. Manuf. Technol. 94 (9), 4277–4287. doi:10.1007/s00170-017-1103-6
Xia, T., Kaynak, Y., Arvin, C., and Jawahir, I. S. (2016). Cryogenic cooling-induced process performance and surface integrity in drilling CFRP composite material. Int. J. Adv. Manuf. Technol. 82 (1), 605–616. doi:10.1007/s00170-015-7284-y
Xu, J., An, Q., Cai, X., and Chen, M. (2013). Drilling machinability evaluation on new developed high-strength T800S/250F CFRP laminates. Int. J. Precis. Eng. Manuf. 14 (10), 1687–1696. doi:10.1007/s12541-013-0252-2
Xu, J., Li, C., Chen, M., El Mansori, M., and Ren, F. (2019). An investigation of drilling high-strength CFRP composites using specialized drills. Int. J. Adv. Manuf. Technol. 103 (9-12), 3425–3442. doi:10.1007/s00170-019-03753-8
Xu, J., Lin, T., Davim, J. P., Chen, M., and El Mansori, M. (2021). Wear behavior of special tools in the drilling of CFRP composite laminates. Wear 476, 203738. doi:10.1016/j.wear.2021.203738
Xu, J., Yin, Y., Davim, J. P., Li, L., Ji, M., Geier, N., et al. (2022). A critical review addressing drilling-induced damage of CFRP composites. Compos. Struct. 294, 115594. doi:10.1016/j.compstruct.2022.115594
Xu, W., and Zhang, L. (2018). Tool wear and its effect on the surface integrity in the machining of fibre-reinforced polymer composites. Compos. Struct. 188, 257–265. doi:10.1016/j.compstruct.2018.01.018
Yan, X., Reiner, J., Bacca, M., Altintas, Y., and Vaziri, R. (2019). A study of energy dissipating mechanisms in orthogonal cutting of UD-CFRP composites. Compos. Struct. 220, 460–472. doi:10.1016/j.compstruct.2019.03.090
Keywords: CFRP laminates, drilling process, tool wear, wear mechanisms, wear effects
Citation: Xu J (2022) A review on tool wear issues in drilling CFRP laminates. Front. Mater. 9:990773. doi: 10.3389/fmats.2022.990773
Received: 10 July 2022; Accepted: 03 August 2022;
Published: 02 September 2022.
Edited by:
Vincenzo Fiore, University of Palermo, ItalyReviewed by:
Luca Sorrentino, University of Cassino, ItalyCopyright © 2022 Xu. This is an open-access article distributed under the terms of the Creative Commons Attribution License (CC BY). The use, distribution or reproduction in other forums is permitted, provided the original author(s) and the copyright owner(s) are credited and that the original publication in this journal is cited, in accordance with accepted academic practice. No use, distribution or reproduction is permitted which does not comply with these terms.
*Correspondence: Jinyang Xu, eHVqaW55YW5nQHNqdHUuZWR1LmNu
Disclaimer: All claims expressed in this article are solely those of the authors and do not necessarily represent those of their affiliated organizations, or those of the publisher, the editors and the reviewers. Any product that may be evaluated in this article or claim that may be made by its manufacturer is not guaranteed or endorsed by the publisher.
Research integrity at Frontiers
Learn more about the work of our research integrity team to safeguard the quality of each article we publish.