- 1Department of Automobile Engineering, Noorul Islam Centre for Higher Education, Kumaracoil, India
- 2Department of Aerospace Engineering, Karunya Institute of Technology and Sciences, Coimbatore, India
- 3Department of Aeronautical Engineering, Kumaraguru College of Technology, Coimbatore, Tamil Nadu, India
- 4Al-Amarah University College, Amarah, Iraq
- 5Iraqi Ministry of Oil, Midland Refineries Company, Najaf Refinery, Najaf, Iraq
- 6Section of Mathematics, International Telematic University Uninettuno, Corso Vittorio Emanuele II, Rome, Italy
- 7School of Mathematics and Information Science, Henan Polytechnic University, Jiaozuo, China
- 8School of Engineering, Computing and Mathematics, University of Plymouth, Plymouth, United Kingdom
- 9Chemical Engineering and Petroleum Industries Department, Al-Mustaqbal University College, Babylon, Iraq
Lightweight materials are being employed in aeronautical and automobile industries for high strength, lower weight, and energy consumption. Attention is needed to control pollution through the usage of harmful synthetic composites globally. In this work, coconut shell nanofillers are reinforced in the development of various palm fiber (leaf stalk, leaf sheath, leaf-spine, and fruit) composites using the hand layup technique. Mechanical and morphological effects of the addition of nano-coconut-shell-powder to the composites are addressed. The palm fibers are sandwiched within the glass fiber to improve the strength of composites. The addition of coconut shell nanoparticles in the composites improves the tensile, flexural, impact, hardness, and water absorption characteristics. SEM image observations on the composite indicate the buildup of nanomodified matrix residues around the fiber bundle. The adhesive property of the composite is confirmed by Fourier transform infrared spectroscopy examination, which reveals the presence of one additional alcohol/phenol OH stretch, one less alkyl CH stretch, and aromatic CH bending functional groups. The inclusion of palm fibers during the fabrication of composites facilitated the pushing of curves to higher temperatures with considerable degradation temperatures, thereby increasing thermal stability and making them suitable for thermal applications. Development of the eco-composite changes environmental impact factors aiming sustainability.
1 Introduction
Over the past 2decades, natural fiber reinforcement polymer composites (NFRPCs) have witnessed significant expansion in the automobile sector. NFRPCs are used to make dashboards, door panels, doors, spoilers, hoods, headliners, deck lids, and other automotive components for compact and large vehicles. When NFRPCs are used rather than steel, there is considerable weight reduction during production. NFRPCs are used to manufacture printed circuit boards in the electronics sector, transformer housing in the power business, bone plates for fracture fixation/implants in the medical area, and oil sucker rods for raising subsurface oil in the oil industry. After learning their particular physical, mechanical, and thermal features, they have been utilized in many industrial devices, such as oxygen tanks, step ladders, and transmission shafts (Stevens, 2002) . Putting NFRPCs to practical use requires professional design practice and appropriate process developments. The first composite pedestrian bridge was built at Aberfeldy, Scotland, in 1992. At McKinleyville, the United States built the first FRP concrete bridge decks in 1996 (Robert, 2004).
Binhussain and El-Tonsy (Binhussain and El-Tonsy, 2013) investigated the use of recycled plastic wood and date palm leaf waste composites to manufacture wood. Tensile strength, modulus, and maximum load were measured using a universal testing machine with ASTM D638M-93 standard. The maximum tensile strength was 4.82MPa, and the modulus occurred at 1.31GPa. The impact strength is 1.95 kJ/m2 , and the flexural modulus is 1.91GPa.
Melo et al. (Melo et al., 2012) developed a biodegradable composite from carnauba leaf fibers of carnauba palm tree reinforced with polyhydroxybutyrate matrix. Different fiber treatments were carried out on fibers using peroxide, potassium permanganate, and acetylation. The tensile strength is 25–36MPa. The thermal stability of fibers was observed using the TGA 2050 model.
Exposure to the electron beam in polyethylene-based wood plastic composites boosted ultimate strength, modulus of elasticity (MOE), and moisture content (Palm et al., 2015). The tensile and in-planar characteristics of three-dimensional needled textile reinforcement on ceramic matrix composites (3DN CMCs) were investigated by Xu et al. (Xu et al., 2015). Chemical vapor infiltration was used to make these 3DN CMCs. Tensile and compressive loads were applied using a servo-hydraulic mechanical tester.
Romanzini et al. (Romanzini et al., 2013) investigated the mechanical properties and dynamic-mechanical properties of glass/ramie fiber reinforced polymer composites. Dynamic modulus and damping behavior were estimated by the dynamic mechanical analysis. The mechanical properties were improved owing to the rich fiber content.
Hoyos and Vazquez (Gomez Hoyos and Vazquez, 2012) investigated the tensile and flexural characteristics of treated fique/epoxy/C30B montmorillonite composites subjected to three kinds of environmental conditions: water, saturated calcium hydroxide solution, and mortar. The fiber treatment and the addition of montmorillonite improved the tensile/flexural modulus and strength of composites by 40% and 34%, respectively. Furthermore, the qualities of composites before and after aging were superior to the properties of traditional wood employed in composite construction.
Mishra and Biswas (Mishra and Biswas, 2013) studied the characterization of physical and mechanical properties of jute fiber epoxy composite using the hand layup technique. Hardness was measured using a Rockwell-hardness tester, tensile tests, and flexural tests using a universal testing machine, and the impact strength by the impact tester, using ASTM D256 standards.
Sethi et al. (Sethi et al., 2014) examined polymer composites, which are extensively utilized in aerospace, marine, automotive and structural applications owing to their dependability, high specific strength, high performance, fatigue endurance, stiffness, abrasion resistance, and superior corrosion resistance. Their interfacial and failure modes were evaluated using a three-point short beam shear test for fiber such as glass/carbon/Kevlar/epoxy polymer composites. The volume fraction was 60%, and the epoxy and hardener ratio was 10:1. Also, they attained high tensile strength and modulus.
Nabinejad et al. (Nabinejad et al., 2014) studied the nature of polymer biocomposite development using unsaturated polyester resin. Flexural loading and tensile tests were carried out using a universal tensile machine, and its maximum values of tensile and flexural strengths were 43.41 and 63.4MPa, respectively. Thermogravimetric analysis was used to compute the thermal degradation of the composite from 370°C to 418°C.
Boronat et al. (Boronat et al., 2014) examined the thermal, mechanical, and rheological properties of polymer matrix composites. The stiffness, hardness, the flexural and tensile modulus of composites, and their mechanical properties yield reasonable results. The polymer matrix composite flexural modulus was 1350MPa, tensile strength was 29MPa, hardness was 64, and Izod impact strength was 25J/m at a temperature of 124°C.
Karaduman et al. (Karaduman et al., 2014) performed the dynamic mechanical analysis to analyze features such as dynamic mechanical and viscoelastic properties in jute fiber-reinforced polypropylene composites. The result demonstrates that the storage modulus of the composite rose as the jute fiber content increased, as measured by dynamic mechanical characteristics.
Composite repairs have become one of the most popular and widely used external metal repair methods. Wrapping (Djukic et al., 2015), is a part of the mending process (Djukic et al.). The composite repairs for manufacture and the testing of leak containment have been applied successfully.
Gopinath et al. (Gopinath et al., 2014) estimated the jute-reinforced polyester and epoxy composites using mechanical properties. Because of its superior mechanical qualities, low density, lightweight, and stiffness, jute is often utilized in applications such as automotive, marine, aerospace, and sports goods. In this, jute fibers are used for preparing fiber-reinforced composites, and their fiber length is 5–6mm. The weight percentage ratio of fiber resin is 18:82 for composite synthesis. The results showed that the mechanical properties are better for jute-reinforced epoxy composites than for jute-polyester composites. Alkbir et al. (Alkbir et al., 2016) explored the physical and mechanical properties of natural fiber-reinforced composites. Natural fibers such as wood fibers with composites and coir have high Young’s modulus and tensile strength and have been studied by researchers (Sobczak et al., 2012; Stevens et al., 2022). A number of researchers examined the mechanical, static, and dynamic properties of jute/palm leaf stalk epoxy composites using the hand layup method.
Esnaola et al. (Jawaid et al., 2012; Jawaid et al., 2012; Abdellaoui et al., 2014; Esnaola et al., 2015) developed the energy absorption technology for E-glass, hybrid E-glass/basalt with polyester, and basalt composites in automotive crash applications using quasi-static compression tests. The stacking sequence of E-glass fibers determines the specific energy of the composite.
Polymer composites usually exist with synthetic fiber and thermoset matrices, which of course limit the environmental benefits. They can be prepared as biocomposites when reinforced with natural fibers instead of synthetic fibers. The reliability and durability of the composites in the automotive and aeronautical sectors are discussed (Kim, 2012).
The stiffness and lack of strength of biocomposites make the material less usable for high-strength applications. A better arrangement in placing the fibers at specific locations and a suitable configuration can tackle these problems.
Palm fibers belong to natural fiber resources mainly used for handicrafts and whose potential as reinforcement in polymer composite has not been explored completely.
Naturally available palm fibers form aggregates with polymer matrix during processing, and also, their poor resistance to moisture reduces the potential of using them as reinforcement in the polymer matrix. Fiber pretreatments can reduce this overall incompatibility, convert long fibers into short ones, and reinforce fibers in the form of mats.
In this work, various treated/nontreated fibers of palm are used to manufacture composites with/without the addition of nano-coconut-fillers, and the properties are tested and presented.
2 Materials and methods
This work elaborates on the various materials used, experimental methods, and testing adopted for composite fabrication. Figure 1 presents the stages involved in preparing the composite.
2.1 Description of materials
Figure 2 depicts the different materials employed in the manufacture of composites in this study.
2.1.1 Palm fiber preparation
Palm fibers are taken from various parts (Figure 2.) of palm trees, viz., leaf stalk (PLst), leaf sheath (PLsh), leaf-spine or petiole (PLsp), and fruit (PFrt). To eliminate any undesired organic compounds on the surfaces of the fibers, they are washed with pressured water. These fibers are spread upon a waterproof sheet and kept in an enclosed shed to minimize moisture content and prevent fungus attacks. After Two weeks, the long fibers are chopped into short fibers in a mixer to remove fleshy outer skins. Thus, powder and thin, short uniform fibers are obtained.
All of the fibers are approximated to be 10–30mm in length width 1–1.5mm in width (Serrano et al., 2014; Subash et al., 2022). The fiber dimensions result from single fiber pull-out tests (Joseph et al., 1996). To get rid of the tiny particles, the fibers are once again rinsed with pressured water. The fibers are air-dried in sunlight un at normal room temperature.
Alkalization treatment or mercerization (Kabir et al., 2012; Ram Kumar et al., 2014; Cruz and Fangueiro, 2016) is the best chemical treatment carried on natural fibers before their reinforcement of thermoplastics or thermosets. The surface roughness and mechanical interlocking increase with the quantity of cellulose exposed on the fiber surfaces to help the matrix attach itself (Fiore et al., 2016).
Figures 3A-D show the treated and chopped palm fibers used in this work. Because hydrogen bonds in the fibers’ network structures are disrupted by the treatment, the surface roughness of the fibers is increased. This treatment removes a certain amount of lignin, wax, and oils covering the external surface of the fiber cell wall; depolymerizes cellulose; and exposes the short-length crystallites (He et al., 2015). The cellulose is often depolymerized during treatments and exposed to short-length crystallites.
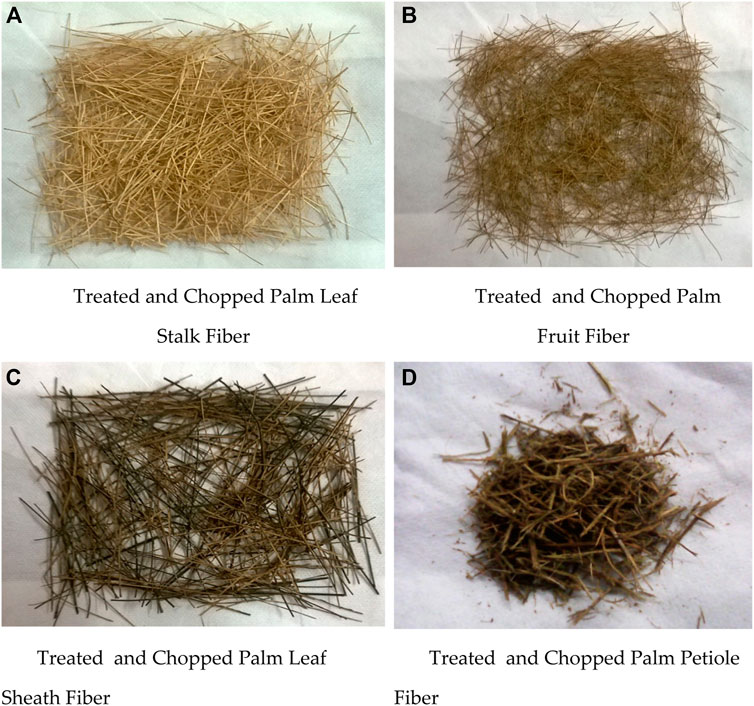
FIGURE 3. Treated and chopped fibers used in this work. (A) Treated and chopped palm leaf stalk fiber, (B) treated and chopped palm fruit fiber, (C) treated and chopped palm leaf sheath fiber, and (D) treated and chopped palm petiole fiber.
Permanganate causes grafting reactions between the polyester matrix and the natural palm fibers. The usage of permanganate, such as potassium permanganate, forms mechanical interlocks with the matrix and roughens the surface of natural fibers.
The permanganate treatment promotes the palm fibers with a rough surface and strengthens the interfacial connection between the fiber and the polyester matrix. The treatment of permanganate causes the synthesis of cellulose radicals by the creation of MnO−3 ions.
i) Chemical Properties
Standard tests were performed to estimate the chemical content, cellulose, hemicellulose, and lignin contained in the fibers. Cellulose, hemicellulose, and lignin in fibers possess positive effects, while the moisture content shows negative effects for reinforcement. The fibers were dried in an oven at 104°C for 4h to prepare them for testing, after which the weight change was measured in an electronic weighing machine to determine the moisture content. Through laboratory-based chemical testing, the additional qualities are approximated.
Table 1 shows the chemical analysis results of palm fibers. The palm fibers have a high cellulose concentration of 28%–53%, which accounts for the lengthy fiber chain.
ii) Physical Properties
The fiber density is calculated by comparing the density of palm fibers with the density of a standard substance (toluene) using a pycnometer. The relationship for calculating the density of palm fibers is given in Equation 1.
Palm fiber density (g/cm3) = {(mass of empty pycnometer − mass pycnometer plus fiber)/[(mass of pycnometer plus toluene − mass of empty pycnometer) × (mass of pycnometer plus fiber and toluene − mass of pycnometer plus fiber)] × density of toluene} ………. (1).
Tensile testing was done on fibers with a constant crosshead speed of 0.1mm/min in an environment with an R.H. of 65% and temperature of 20°C. The physical characteristics of palm fibers are shown in Table 2.
2.1.2 Properties of E-glass fiber
The glass fibers are sandwiched between palm fibers. The type of glass fiber used in reinforcement for this study is E-glass fiber (Figure 4).
2.2 Polyester resin
Polyester is a thermosetting resin that is often employed in composite materials. It has strong chemical resistance and minimal shrinkage that varies on curing. Unsaturated polyester chips are transported as solid resin after being dissolved in styrene solvent monomer.
The density of the polyester resin is 1.35g/cc, and its elastic modulus is 3.25GPa. Unsaturated polyester resin refers to polyester that has double chemical bonds and ester functional groups in its main chain. In contrast to thermoplastics, which may be created at high temperatures, these plastics are referred to as thermosetting plastics. They have the ability to bind things together tightly.
Polyester resins are created to have a variety of characteristics, from being soft and ductile to rigid and brittle. Low cost and viscosity and quick curing are some of its benefits. Polyester resins are harmless.
2.2.1 Methyl ethyl ketone peroxide (MEKP)
MEKP is an organic peroxide derivative added to the polyester resin at a level of 0.5–1.5% as a common resin cure initiator. It is a colorless liquid and stable under storage.
This compound is unstable when added to resin and decomposes to give free radicals. Typically, MEKP solutions that are 30–60 percent diluted start the curing process by generating free radicals at the unsaturated bonds of polyester resin. The unsaturated bonds of nearby molecules reach a chain reaction that links them together. Industrialists and hobbyists use MEKP as a catalyst to cure unsaturated polyester resins in the manufacture of fiber-reinforced plastics or casting.
MEKP is highly irritative to human skin and causes blindness. Excessive use of catalyst causes ignition or fracture of product or formation of rubbery material. The “accelerator” introduced to the resin catalyzes the breakdown of the initiator in the event of a room-temperature cure.
2.2.2 Cobalt naphthenate
A typical accelerator to break down the initiator is cobalt naphthenate. Typically, 0.5 percent of the accelerator is applied to the polyester resin. This stimulates the cross-linking of polyester resins and speeds up the breakdown of the organic peroxide initiators. The temperature of the initiator influences the resin’s pace of curing. It is soluble in organic solvents with a molecular weight of 401.27g per mole, a density of 960kg/m3, and a melting point of 140°C. It initiates the cure rate of the polymer resin-cast system at 25°C.
i) Wax Polish
For easier removal of manufactured components from metal, wooden, cardboard, or plastic molds and mandrels, wax polish, a semisolid, serves as a mold release agent. When making composites using polyester, hard, greasy paraffin wax is used as a mold release agent.
Laminates made of polyester resin are cured using mold release agents with silicone bases. Before utilizing a mold, many coats of wax are applied. A single coat of wax is applied after each release. Wax buildup on the mold surface prevents resin from curing properly, causing a hazy finish.
ii) Mold Box
A rectangular box of 20mm × 200 mm × 300mm is prepared using a glass of 5mm thickness. The top of the box is a separable lid, which facilitates the removal of the composite plate.
2.3 Preparation of nano-coconut-shell-fillers
Coconut shell powders are selected as filler material and are prepared from matured coconut shells.
Due to its consistency in quality and chemical composition, coconut shell powder is preferred over other alternative materials on the market such as bark and peanut shell powders, since it offers greater capabilities in terms of water absorption and resistance to fungus attacks. It is widely used as a phenolic extruder in the manufacturing of plywood and laminating board industries (Dhakal et al., 2012; Saba et al., 2016; Hemath et al., 2020; Chand and Fahim, 2021; Jenish et al., 2022).
The filler is prepared by mesh size, ranging from 80 to 200 approximately. Coconut shells are broken into small pieces after removing the contaminating coir pith and fed into the pulverizer. The pulverized powders are fed through a cyclone, where the parallel products are separated and collected on bag filters. The shell powders are fed through a vibrating sieving device and packaged in accordance with the mesh size specifications for the different applications.
Using a titanium ball mill (PM 100 Retch, Germany) (Figure 5), the coconut shell micropowder was converted into nanopowder. The machine consists of a horizontal-type ball mill with rotating cylinders and two cabins and is operated by gears. The micropowders are fed spirally and evenly into the first cabin of the machine.
When the barrel body rotates, it produces centrifugal force. During this time, titanium balls are lifted and then dropped to make a strike for grinding. After grinding, in the first cabin, the powder is then fed into the second cabin for regrinding with the titanium ball. Then, these fine powders are collected.
The particle size is analyzed by a particle size analyzer (DC 12000, CPS instruments, United States) (Figure 6). These analyzed particles range from 10 to 2000nm. The light visualizes the samples of the particles and is scattered when illuminated. The analysis time is 30 s.
Each particle’s motion is traced into each frame when the light is dispersed by the particles using a digital camera. The rates of particle movements are related to the sphere equivalent to the hydrodynamic radius and are calculated by the Stokes–Einstein equation. Figure 7 depicts the plot from the particle size analyzer.
The tensile, flexural, impact, hardness, and water absorption characteristics are improved by the inclusion of coconut shell nanoparticles (Figure 8). The addition of filler content helps to increase the tendency of filler–matrix interactions. Table 3 shows the properties of the prepared coconut shell nano-powder.
3 Experimentation
A rectangular glass box measuring 20mm × 200mm x 300mm is employed to make a mold. In order to facilitate the release of the composite without it adhering to the mold walls after curing, wax (a releasing agent) is placed on the methyl ethyl ketone peroxide (as a hardener), followed by the integration of 0.5% cobalt naphthenate (as an accelerator), which is well combined to create a homogenous mixture. After the resin is correctly mixed and prepared to cure, the reinforcing gets completed. For a well-cured and good-quality composite, the polyester resin is mixed smoothly and slowly for 10mins with the hardener.
The required amount of polyester resin mix prepared is poured into the mold box carefully and uniformly spread along the bottom surface; the glass fiber mat is placed over this as the first layer, thereby forming the bottom layer of the composite. Using the hand rollers, the layer is compacted, and this also removes the trapped air bubbles. Similarly, the successive layers are constructed with palm-fiber mats, and the layers are once again compacted. The final closing layer is completed using glass fiber mats so as to obtain a glass/palm sandwich composite.
An 80kg weight is used to condense the whole sandwich composite within the molds, and after curing for 24h, they are removed from the molds. After being removed from the mold, this cast is post-cured for a further 24h in the open air. This technique is used to fabricate the composite samples from A to D without coconut shell nanoparticulate fillers.
For the remaining composite samples E to R, the resin mix was slightly modified by incorporating 0.05 weight fraction of coconut shell nanoparticulate fillers and blending thoroughly in a mixer before reinforcement with fiber mats. All of the other techniques remain the same for fabrication. The detailed combination and composition of the composites are presented in Table 4.
The cured sandwich composites are released from the mold in the form of plates (Figures 9, 10) and are converted into specimens of suitable (ASTM standard) dimensions before testing.
Using the theory of mixtures for a mixture of 70% polyester, 20% palm leaf stalk fiber, and 10% E glass fiber, the elastic modulus and tensile strength values were found to be 10.519 GPa and 433.2MPa, respectively.
4 Results and discussion
4.1 Mechanical tests on developed composites
The mechanical properties (hardness and tensile strength) of the developed composite are studied using the ASTM D standard test procedure.
4.1.1 Hardness measurement
Hardness is one of the most important factors that govern any material’s use in a practical and relatively tough environment. It is the indentation resistance offered by one material over another. Rockwell hardness machine is used to measure the hardness values of various natural palm fiber reinforced composites.
A standard load is uniformly applied to make a minimum of five observations at various locations on the test sample, and the mean value records the hardness value of the material. Table 5 shows the hardness values. The values of hardness are in the range between 45HR and 56 HR for raw fiber composites (A, B, C, and D) and in the range between 52 HR and 56 HR for treated fiber composites (E, F, G, and H). The fiber treatment (with KMnO4) of the palm fibers is free from impurities and increases the surface roughness, providing a good mechanical interlocking between fiber and matrix.
The fiber treatment increased the average values of hardness in the treated fiber composites by 5% approximately. Considering the treated fiber composites with added coconut shell nanofiller (I, J, K, and L), the values slightly increase in the range between 53HR and 65HR. The hardness values increased a few more percent for these coconut shell nanofiller-added composites. This is because the tendency to form voids inside the composite during fabrication is highly eliminated by the uniformly dispersed phase of the resin/filler system. However, the improvement also depends on other factors, such as the size and shape of the filler material used.
The hardness values for the treated palm fibers with the addition of coconut shell nanofiller composite (P, Q, and R) remained uniform at 68HR. It makes sense to reason that uniqueness is attained because these composites overcome the negative characteristics of the other. Also, this fiber combination (P, Q, and R) increased the average values of hardness by 8% approximately when compared with raw fiber composites (A, B, C, and D).
From these investigations, the maximum hardness value was recorded for treated and (in between hybrid) palm fibers with coconut shell nanofiller composite as 68 HR. Hence, it is evident that improvement in the hardness of the composite was achieved through the incorporation of natural palm fiber after treatment and hybridization. The addition of glass fiber as a sandwich (for the top and bottom layers of the composite) and coconut shell nanofiller in resin resulted in better performance. The resulting composite has attributes of good fiber–matrix interaction, lesser voids, and uniform dispersion among phases.
4.1.2 Tensile strength observations
Tensile strength is the ability of a material to be elastic. This is the most important attribute that attracts any material for practical usage in elastic behavior applications. The tensile strength of various natural palm fiber reinforced composites is observed using a universal testing machine. Load is applied uniformly after clamping the test sample into the fixture grips, which gives the value, and the mean value of a minimum of five samples records the tensile strength value of the material. Table 6 shows the tensile strength values obtained.
The values of tensile strength range between 98.6 and 103.92MPa for raw fiber composites (A, B, C, and D) and 70.69 and118.6MPa for treated fiber composites (E, F, G, and H). The fiber treatment (with KMnO4) made the surface of the palm fibers free from impurities, and improvement in fiber and matrix adhesion was achieved.
This fiber treatment increased the average values of tensile strength in the treated fiber composites by 18%. Also, the samples prepared with palm sheath fibers show a very small improvement when compared with the other samples. This is due to the increased diameter of the sheath fibers that resulted in weak fiber–matrix adhesion.
For treated fiber composites with coconut shell nanofiller addition (I, J, K, and L), the tensile strength values range between 78.8 and 127.3MPa. The tensile strength values increased rapidly for samples made with palm leaf stalk, spine, and fruit fibers.
This may be due to the possibility of void formation inside the composite during fabrication being highly eliminated by the uniformly dispersed phase of the resin/filler system (Vinod et al., 2020). However, the improvement is in the size and shape of the filler material used.
The tensile strength values for the treated palm (in between hybridized with added coconut shell nanofiller) fiber composites (P, Q, and R) varied ranging between 132.8 and 142.8MPa. Also, this fiber combination (P, Q, and R) increased the average values of tensile strength by 30% compared with raw fiber composites (A, B, C, and D). The composite made by combining palm leaf-spine and stalk fibers yields the maximum tensile strength value.
The hybridizing of fiber increased the tensile strength of the composite specimen Q. The reason for this is that the mixing of various fibers added the tensile values resulting in a better composite with high tensile strength. The specimen Q records a maximum tensile strength value of 142.8MPa.
4.1.3 SEM of fractured tensile specimen
The microstructural changes (cavities, pits, and porosity) and the morphology of the polymer composite surface were studied with microscopic observation. The composite surface is coated (with 100Å thick platinum) before placing for observation in the electron chamber of the microscope. For obtaining better image resolution, secondary electron imaging with a voltage of 15KV was used by varying the scan magnification.
As seen from the micrographs (Figures 11, 12), a large amount of resin was adhered to the fiber surface with fewer gaps between the resin and the fibers. These indicate the improved adhesion between the resin and the fibers.
The tendency to form voids is reduced by the addition of nanococonut-shell-fillers. Also, the fiber pullout shows improved tensile and flexural strength. The reason behind this is that the fiber treatment improved the fiber strength. Hence, the micrographs agree with the mechanical test results (Nagalingam et al., 2010; Pradeepand and Edwin Raja Dhas, 2015; Obi Reddy et al., 2016; Pradeep and Edwin Raja Dhas, 2016; Verma et al., 2016; Bino Prince Raja et al., 2017; Bino Prince Raja and Jones Retnam, 2019; Raj Kumar. et al., 2019; Mohamed Bak et al., 2020; Venkatesan et al., 2020; Raj et al., 2021; Sonia et al., 2021; Vijayanandh et al., 2021; Vinay et al., 2021).
4.2 FTIR study of the composite
FTIR observation identifies the chemical bond or functional group contained in the composite. Its spectra of pure compounds are similar in molecular fingerprint, and those of organic compounds are rich in details. The identification of the spectrum of an unknown compound is easier while comparing it with a known compound. Here, specimen Q is the unknown compound in the form of a powder (Figure 13).
The sample is passed through a focused beam of infrared light, which captures the infrared spectrum. A portion of the radiation is absorbed, while the remaining portion passes through the sample. Transmitted light reveals the energy of the absorbed wavelength. As a result, transmittance and absorbance readings are plotted against wave number, and a spectrum is created. The infrared wavelength at which absorption takes place is detected by this spectrum. Absorption occurs when the bond’s vibrational frequency and the IR frequency are the same.
As a result, the sample’s FTIR list reveals the precise existence of organic functional groups. In this analysis, a pure potassium bromide pellet is the reference compound. A tiny ball is prepared by mixing both the composite powder sample and potassium bromide powder. To obtain the IR spectra and plot transmittance vs. wave number, the pellet is retained in the sample holder of the FTIR system. Figure 14 shows the result of the FTIR study for palm fiber-based polyester composites (specimen Q), and Figure 15 reveals the FTIR graph of the palm leaf fiber.
The curves in Figure 14 show an additional alcohol/phenol OH stretch, a decrease in the stretch of an alkyl group, and an increase in the bend of an aromatic group, which confirms the inclusion of palm fibers and nanococonut-shell-filler in the polyester resin. Also, the arrangement has better adhesion with pure resins.
4.2.1 Thermogravimetric analysis for the developed composite
The equipment measures the weight loss in the specimen with respect to an increase in temperature. Figure 16 shows the thermal analyzer (TG/DTA, SIINT- 6300 Japan) used in this study. The sample material is uniformly heated at a constant rate. This analytical method determines the thermal stability and volatile materials present in a material. Observations are performed in an inert nitrogen environment by changing weights as a function of increasing temperature.
The TGA for the best composite (specimen Q) is performed using the thermal analyzer. The samples of resin matrix and composites are analyzed separately, having masses ranging from 5 to 10mg. The rate of heating maintained is 10°C/min, and the temperature ranges from 30 to 400°C in a nitrogen atmosphere.
Figure 17 shows the TGA between the best composite (specimen Q) and a pure polyester composite. The specimen Q loses just 0.53% of its starting weight to a temperature of 100°C (whereas pure polyester loses 2.41%). Weight loss of 2.8% at roughly 250°C is due to solvent removed from the polymer matrix (whereas pure polyester loses 5.8%). Further, 48.4% of weight was lost between 250oC and 470°C as a result of deterioration and volatilization of the polyester palm fibers used to make the composite (whereas pure polyester loses 35.8%). The composite continues to lose mass linearly up to 1000°C, where the final residue is 48.98% of the initial mass (whereas pure polyester loses 25.8%).
5 Conclusion
The investigation leads to the following conclusions.
• Palm fibers are used as a natural reinforcement to develop biobased composites after suitably bonding with the resin, resulting in the production of value-added products.
• Hand layup technique is used to fabricate various palm composites and, the mechanical and morphological effects of coconut shell nanofiller are studied.
• The surface treatment on natural palm fibers with potassium permanganate improves the mechanical characteristics such as hardness and tensile values. The sandwiching of palm fibers within the glass fiber layer combines the strength of both the natural and synthetic fibers serving as a strong reinforcing phase on the resulting biocomposite.
• Naturally available coconut shell nanofiller is added to the composite resin and disperses uniformly within the polyester resin, enhancing the overall characteristics of the composites.
• Mechanical characterization results showed that the developed natural palm composites exhibit better hardness and tensile properties compared to other results (44–46). This is achieved by the hybridization and inclusion of nanofiller components.
• The SEM image observations indicate the buildup of nanomodified matrix residues around the fiber bundle. Hence, it proves that effective fiber–matrix adhesion is maintained after the addition of the coconut shell nanofiller.
• The palm fiber-based composites’ FTIR spectroscopic investigation revealed one more alcohol/phenol OH stretch, one fewer alkyl CH stretch, and an aromatic CH bending functional group, which demonstrates the existence of palm fibers and their improved adherence to pure resin.
• From the TGA approach, it is inferred that the addition of nano-coconut-shell-powder for making the composite pushed the curves to higher temperatures with a noticeable degradation temperature, improving thermal stability and making the material acceptable for thermal applications.
The developed natural fiber-based composite is recommended for utilization by industries in the manufacture of biodegradable components with sustainable improvement, exploring new areas of applications.
Data availability statement
The original contributions presented in the study are included in the article/Supplementary Material; further inquiries can be directed to the corresponding authors.
Author contributions
JE, supervision; KA, investigation and draft preparation; KN, literature survey; HAL-b, validation; HA, draft editing and reviewing; S-WY, draft editing and reviewing; VR, methodology; and MA-B, draft preparation.
Conflict of interest
The authors declare that the research was conducted in the absence of any commercial or financial relationships that could be construed as a potential conflict of interest.
Publisher’s note
All claims expressed in this article are solely those of the authors and do not necessarily represent those of their affiliated organizations, or those of the publisher, the editors, and the reviewers. Any product that may be evaluated in this article, or claim that may be made by its manufacturer, is not guaranteed or endorsed by the publisher.
References
Abdellaoui, H., Bensalah, H., Echaabi, J., Bouhfid, R., and Qaiss, A. (2014). Fabrication, characterization and modelling of laminated composites based on woven jute fibers reinforced epoxy resin. Mater. Des. 68, 104–113. doi:10.1016/j.matdes.2014.11.059
Alkbir, M. F. M., Sapuan, S. M., Nuraini, A. A., and Ishak, M. R. (2016). Fibre properties and crashworthiness parameters of natural fibre-reinforced composite structure: A literature review. Compos. Struct. 148, 59–73. doi:10.1016/j.compstruct.2016.01.098
Binhussain, Mohammed A., and El-Tonsy, Maher M. (2013). Palm leave and plastic waste wood composite for out-door structures. Constr. Build. Mater. 47, 1431–1435. doi:10.1016/j.conbuildmat.2013.06.031
Bino Prince Raja, D., and Jones Retnam, B. S. (2019). Effect of short fibre orientation on the mechanical characterization of a composite material-hybrid fibre reinforced polymer matrix. Bull. Mat. Sci. 42 (111), 111–117. doi:10.1007/s12034-019-1813-5
Bino Prince Raja, D., Stanly Jones Retnam., B., and Edwin Raja Dhas., J. (2017). Mechanical characterization on woven bidirectional natural fiber reinforced polymer composites. Int. J. Future Revolut. Comput. Sci. Commun. Eng. 3 (9), 134–136.
Boronat, T., Fombuena, V., Garcia-Sanoguera, D., Sanchez-Nacher, L., and Balart, R. (2014). Development of a biocomposite based on green polyethylene biopolymer and eggshell. Mat. Des. 68, 177–185. doi:10.1016/j.matdes.2014.12.027
Chand, N., and Fahim, M. (2021). Tribology of natural fiber polymer composites. Sawston, United Kingdom: Woodhead Publishing.
Cruz, J., and Fangueiro, R. (2016). Surface modification of natural fibers: A review. Procedia Eng. 155, 285–288. doi:10.1016/j.proeng.2016.08.030
Dhakal, H. N., Zhang, Z. Y., and Bennett, N. (2012). Influence of fibre treatment and glass fibre hybridisation on thermal degradation and surface energy characteristics of hemp/unsaturated polyester composites. Compos. Part B Eng. 43, 2757–2761. doi:10.1016/j.compositesb.2012.04.036
Djukic, L. P., Siang Sumc, W., Leong, K. H., Hillier, W. D., Eccleshall, T. W., and Leong, A. Y. L. (2015). Development of a fibre reinforced polymer composite clamp for metallic pipeline repairs. Mat. Des. 70, 68–80. doi:10.1016/j.matdes.2014.12.059
Esnaola, A., Ulacia, I., Aretxabaleta, L., Aurrekoetxea, J., and andGallego, I. (2015). Quasi-static crush energy absorption capability of E-glass/polyester and hybrid E-glass-basalt/polyester composite structures. Mat. Des. 76, 18–25. doi:10.1016/j.matdes.2015.03.044
Fiore, V., Scalici, T., Nicoletti, F., Vitale, G., Prestipino, M., and Valenza, A. (2016). A new eco-friendly chemical treatment of natural fibres: Effect of sodium bicarbonate on properties of sisal fibre and its epoxy composites. Compos. Part B Eng. 85, 150–160. doi:10.1016/j.compositesb.2015.09.028
Gomez Hoyos, C., and Vazquez, A. (2012). Flexural properties loss of unidirectional epoxy/fique composites immersed in water and alkaline medium for construction application. Compos. Part B Eng. 43, 3120–3130. doi:10.1016/j.compositesb.2012.04.027
Gopinath, A., Senthil Kumar, M., and Elayaperumal, A. (2014). Experimental investigations on mechanical properties of jute fiber reinforced composites with polyester and epoxy resin matrices. Procedia Eng. 97, 2052–2063. doi:10.1016/j.proeng.2014.12.448
He, L., Li, W., Chen, D., Zhou, D., Lu, G., and Yuan, J. (2015). Effects of amino silicone oil modification on properties of ramie fiber and ramie fiber/polypropylene composites. Mat. Des. 77, 142–148. doi:10.1016/j.matdes.2015.03.051
Hemath, M., Rangappa, S. M., Kushvaha, V., Dhakal, H. N., and Siengchin, S. (2020). A comprehensive review on mechanical, electromagnetic radiation shielding, and thermal conductivity of fibers/inorganic fillers reinforced hybrid polymer composites. Polym. Compos. 41, 3940–3965. doi:10.1002/pc.25703
Jawaid, M., Abdul Khalil, H. P. S., Hassan, A., Dungani, R., and Hadiyane, A. (2012). Effect of jute fiber loading on tensile and dynamic mechanical properties of oil palm epoxy composites. Compos. Part B 45, 619–624. doi:10.1016/j.compositesb.2012.04.068
Jenish, I., Gandhi VeeramalaiChinnasamy, S., Basavarajappa, S., Indran, S., Divya, D., Liu, Y., et al. (2022). Tribo-Mechanical characterization of carbonized coconut shell micro particle reinforced with Cissusquadrangularis stem fiber/epoxy novel composite for structural application. J. Nat. Fibers 19 (8), 2963–2979. doi:10.1080/15440478.2020.1838988
Joseph, K., Thomas, S., and Pavithran, C. (1996). Effect of chemical treatment on the tensile properties of short sisal fibre-reinforced polyethylene composites. Polymer 37 (23), 5139–5149. doi:10.1016/0032-3861(96)00144-9
Kabir, M. M., Wang, H., Lau, K. T., and Cardona, F. (2012). Chemical treatments on plant-based natural fibre reinforced polymer composites: An overview. Compos. Part B Eng. 43 (7), 2883–2892. doi:10.1016/j.compositesb.2012.04.053
Karaduman, Y., Sayeed, M. M. A., Onal, L., and Rawal, A. (2014). Viscoelastic properties of surface modified jute fiber/polypropylene nonwoven composites. Compos. Part B Eng. 67, 111–118. doi:10.1016/j.compositesb.2014.06.019
Kim, Y. K. (2012). Natural fibre composites (NFCs) for construction and automotive industries. Handb. Nat. Fibres Process. Appl. 2, 254–279. doi:10.1533/9780857095510.2.254
Melo, J. D. D., Carvalho, L. F. M., Medeiros, A. M., Souto, C. R. O., and Paskocimas, C. A. (2012). A biodegradable composite material based on polyhydroxybutyrate (PHB) and carnauba fibers. Compos. Part B Eng. 43, 2827–2835. doi:10.1016/j.compositesb.2012.04.046
Mishra, V., and Biswas, S. (2013). Physical and mechanical properties of Bi-directional jute fiber epoxy composites. Procedia Eng. 51, 561–566. doi:10.1016/j.proeng.2013.01.079
Mohamed Bak, K., Raj Kumar, G., Ramasamy, N., and Vijayanandh, R. (2020). Experimental and numerical studies on the mechanical characterization of epdm/S-sbr nano clay composites. IOP Conf. Ser. Mat. Sci. Eng. 912, 052016. doi:10.1088/1757-899X/912/5/052016
Nabinejad, O., Sujan, D., Rahman, M. E., and Davies, Ian J. (2014). Effect of oil palm shell powder on the mechanical performance and thermal stability of polyester composites. Mat. Des. 65, 823–830. doi:10.1016/j.matdes.2014.09.080
Nagalingam, R., Sundaram, S., Jones Retnam, B. S., and Retnam, J. (2010). Effect of nanoparticles on tensile, impact and fatigue properties offibre reinforced plastics. Bull. Mat. Sci. 33 (5), Pp525–528. doi:10.1007/s12034-010-0080-2
Obi Reddy, K., Maheswari, C., Dhlamini, M., and Kommula, V. P. (2016). Exploration on the characteristics of cellulose microfibers from Palmyra palm fruits. Int. J. Polym. Analysis Charact. 21 (4), 286–295. doi:10.1080/1023666x.2016.1147799
Palm, A., Smith, J., Driscoll, M., Smith, L., and Scott Larsen, L. (2015). Influence of ionizing radiation on the mechanical properties of a wood-plastic composite. Phys. Procedia 66, 595–603. doi:10.1016/j.phpro.2015.05.079
Pradeep, P., and Edwin Raja Dhas, J. (2016). Comparison of mechanical properties for hybrid palm/glass/rare earth filler reinforced polymer composite. ARPN J. Earth Sci. 5 (1), 8–12.
Pradeepand, P., and Edwin Raja Dhas, J. (2015). Tensile and flexural characteristics of palm/glass sandwiched Polymer Composite. J. Mech. Mech. Eng. 1 (3), 1–9.
Raj Kumar., G., Senthil Kumar., M., Vijayanandh, R., Raja Sekar, K., Mohamed, Bak. K., and Varun., S. (2019). The mechanical characterization of carbon fiber reinforced epoxy with carbon nanotubes. Int. J. Mech. Prod. Eng. Res. Dev. ISSN(E) 9, 243–255.
Raj, S. S., Pradeep, P., and Edwin, J. (2021). Parameter optimisation of a fibre reinforced polymer composite by RSM design matrix. Int. J. Comput. Aided Eng. Technol. 15, 375–384. doi:10.1504/ijcaet.2021.117134
Ram Kumar, K., Dhamodharan, A., Gopinathan, K., Alagarraja, K., and Mathan Raj, R. (2014). Fabrication and testing of fiber reinforced polymer composites material. IOSR J. Mech. Civ. Eng. (IOSR-JMCE), 27–34.
Romanzini, D., Lavoratti, A., Ornaghi, H. L., Amico, S. C., Zattera, A. J., and Zattera, A. J. (2013). Influence of fiber content on the mechanical and dynamic mechanical properties of glass/ramie polymer composites. Mat. Des. 47, 9–15. doi:10.1016/j.matdes.2012.12.029
Saba, N., Paridah, M. T., Abdan, K., and Ibrahim, N. A. (2016). Effect of oil palm nano filler on mechanical and morphological properties of kenaf reinforced epoxy composites. Constr. Build. Mater. 123, 15–26. doi:10.1016/j.conbuildmat.2016.06.131
Serrano, A., Espinach, F. X., Tresserras, J., Del Rey, R., Pellicer, N., and Mutje, P. (2014). Macro and micromechanics analysis of short fiber composites stiffness: The case of old newspaper fibers- polypropylene composites. Mat. Des. 55, 319–324. doi:10.1016/j.matdes.2013.10.011
Sethi, S., Rathore, D. K., and Ray, B. C. (2014). Effects of temperature and loading speed on interface-dominated strength in fiber/polymer composites: An evaluation for in-situ environment. Mater. Des. 65, 617–626. doi:10.1016/j.matdes.2014.09.053
Sobczak, L., Reinhold, W., and Haider, A. (2012). Polypropylene composites with natural fibers and wood – general mechanical property profiles. Compos. Sci. Technol. 72, 550–557. doi:10.1016/j.compscitech.2011.12.013
Sonia, S. R., Raja Dhas, J. E., and Jesuthanam, C. P. (2021). Challenges on machining characteristics of natural fiber-reinforced composites – a review. J. Reinf. Plastics Compos. 40 (1–2), 41–69. doi:10.1177/0731684420940773
Stevens, E. S. (2002). Green plastics, an introduction to the new science of biodegradable plastics. Princeton: Princeton University Press.
Stevens, S., Edwin Raja Dhas, J., Anton SavioLewise, K., Mohammad, A., and &Fahad, M. (2022). Investigations on chemical behaviours on mechanical properties of natural fiber Composites: An evaluation. Mater. Today Proc. 64, 410–415. doi:10.1016/j.matpr.2022.04.761
Subash, S., Stanly Jones Retnam, B., Jerin Happy, J., Edwin Raja Dhas, J., Anton SavioLewise, K., and Ganesh, M. (2022). Preparation and characterization of Silk/Bamboo/Glass nano polymer composites. Mater. Today Proc. 64, 298–301. doi:10.1016/j.matpr.2022.04.570
Venkatesan, K., Geetha, S., Vijayanandh, R., Raj Kumar, G., Jagadeeshwaran, P., and Raj Kumar, R. (2020). Advanced structural analysis of various composite materials with carbon nano-tubes for property enhancement. AIP Conf. Proc. 2270, 030005–030006. doi:10.1063/5.0019367
Verma, R. P., Verma, V. K., and Rai, A. K. (2016). Study of mechanical properties of natural fibre composite. Int. J. Des. Manuf. Technol. 7 (1), 1–6. doi:10.34218/ijdmt.7.1.2016.001
Vijayanandh, R., Raj Kumar, G., Jagadeeshwaran, P., Mathaiyan, V., Ramesh, M., and Dong, W. (2021). Comparative numerical analyses of different carbon nanotubes added with carbon fiber–reinforced polymer composite, nanomaterials and Nanocomposites: Characterization, processing, and applications. Boca Raton, Florida, United States: CRC Press, 139–165. doi:10.1201/9781003160946-12
Vinay, S. S., Sanjay, M. R., Siengchin, S., and Venkatesh, C. V. (2021). Effect of Al2O3 nanofillers in basalt/epoxy composites. Mech. Tribol. Prop. 42, 1727–1740. doi:10.1002/pc.259274
Vinod, A., Sanjay, M. R., Suchart, S., Jyotishkumar, P., and Jyotishkumar, P. (2020). Renewable and sustainable biobased materials: An assessment on biofibers, biofilms, biopolymers and biocomposites. J. Clean. Prod. 258 (10). doi:10.1016/j.jclepro.2020.120978
Keywords: NFRPC, polymer composite, natural fiber, nano powder, palm fiber, sustainability, glass fiber
Citation: Raja Dhas JE, Savio Lewise KA, Kumar KN, Raja V, AL-bonsrulah HAZ, Ahmad H, Yao S-W and Al-Bahrani M (2022) Effect of coconut shell nanopowder reinforcement in the development of palm fiber composites. Front. Mater. 9:986011. doi: 10.3389/fmats.2022.986011
Received: 04 July 2022; Accepted: 15 August 2022;
Published: 16 September 2022.
Edited by:
Yongqian Shi, Fuzhou University, ChinaReviewed by:
Bharath K. N, GM Institute of Technology, IndiaGang Tang, Anhui University of Technology, China
Sanjay Mavinkere Rangappa, King Mongkut’s University of Technology North Bangkok, Thailand
Copyright © 2022 Raja Dhas, Savio Lewise, Kumar, Raja, AL-bonsrulah, Ahmad, Yao and Al-Bahrani. This is an open-access article distributed under the terms of the Creative Commons Attribution License (CC BY). The use, distribution or reproduction in other forums is permitted, provided the original author(s) and the copyright owner(s) are credited and that the original publication in this journal is cited, in accordance with accepted academic practice. No use, distribution or reproduction is permitted which does not comply with these terms.
*Correspondence: Shao-Wen Yao, eWFvc2hhb3dlbkBocHUuZWR1LmNu