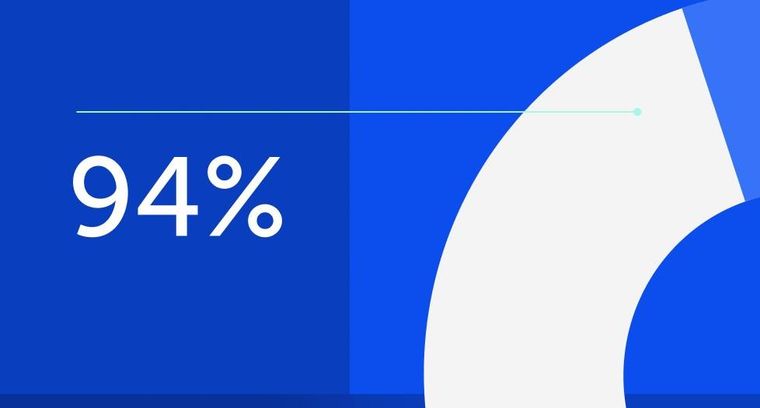
94% of researchers rate our articles as excellent or good
Learn more about the work of our research integrity team to safeguard the quality of each article we publish.
Find out more
ORIGINAL RESEARCH article
Front. Mater., 10 August 2022
Sec. Structural Materials
Volume 9 - 2022 | https://doi.org/10.3389/fmats.2022.959935
This article is part of the Research TopicLow Carbon Emissions, Carbonation Fixation and High Energy Efficiency in Building Related MaterialsView all 4 articles
In recent years, microbial repair materials have received widespread attention for their advantages such as stable products and good compatibility with cementitious materials. However, the current construction process of microbial repair materials is mainly by immersion, which limits the more widespread application. Therefore, this study proposed a coating construction process with sodium alginate as the carrier. The effects of sodium alginate concentration and dosing on the fundamental properties of microbial repair materials (CaCO3 content, mechanical properties, water absorption ratio, and heating shrinkage rate) and their effects on mortar repair effects (macroscopic morphology and surface water absorption ratio) were investigated. The repair effects were further verified by combining thermogravimetric analysis of repair products and scanning electron microscopy. The results showed that 1) the microbial repair material had better basic properties when sodium alginate solution with a mass concentration of 1.5% was used, and its solution-to-bacterial solution volume ratios were 8:2, 7:3, and 6:4; 2) using the coating technique, the microorganisms were fixed in the cracks on the mortar surface by using sodium alginate as the carrier. Only twice of repair could generate a mixture of calcium alginate and calcium carbonate crystals in the cracks by close adhesion. The surface water absorption of the repaired specimens was 67% lower than before the repair, which is a significant effect of the repair.
Concrete materials are affected by the complex surrounding environment during long-term use, and their surfaces are prone to local damages such as loosening and tiny cracks. After concrete damage, aggressive media continuously penetrate from the material surface into the interior, which eventually causes continuous deterioration of concrete durability performance (Nain et al., 2019; Ruan et al., 2019; Sakakihara, 2020). Compared with traditional concrete crack repair materials, the technique of repairing concrete cracks using microbial deposition of calcium carbonate uses microorganisms to induce the generation of mineral deposits to fill and repair concrete defects (Souradeep and Kua, 2016; Seifan et al., 2018; Hu et al., 2020). The product of which is one of the most stable minerals in nature, and its use as a repair material is beneficial for improving the strength and durability of cementitious materials (Joshi et al., 2017; Li et al., 2018).
In recent years, a large number of scholars have conducted systematic research on the mechanical and durability properties of concrete after repairing cracks by microbial-induced mineralization technology (De Muynck et al., 2008; Qian et al., 2009; Wiktor and Jonkers, 2011; Wu et al., 2019). However, the process of microbial repair of concrete cracks needs to ensure sufficient nutrients and calcium sources for microbial reproduction and growth as well as the mineralization process. It leads to existing studies mainly adopting the immersion process, which limits the application of this technology. Therefore, researchers have already investigated the use of polymers to protect microorganisms from highly alkaline environments during microbial repair of concrete cracks (Lv et al., 2016; Lv et al., 2020). Van Tittelboom (Van Tittelboom et al., 2010) used silica gel to sequester bacteria and injected them into concrete cracks after mixing them well with the necessary nutrients and calcium sources. With the extension of curing time, the mineralized materials will serve to bridge the cracks. Cracks with a width of 0.3 mm or less can be completely repaired; Wang Ruixing (Wang and Qian, 2008) used agar as a carrier to sequester bacterial strains and nutrients on the surface of cement stone, which could closely adhere to calcium carbonate film on the surface of cement stone after 7 days. Its surface water absorption rate could be reduced to less than 15% of that before the coating. Studies have shown that sodium alginate has coagulability, viscosity and stability, and good film formation and is nontoxic and nonhazardous, which makes it widely used in many aspects such as biology, medicine, and food (Gheorghita Puscaselu et al., 2020). However, sodium alginate is less used in microbial repair. Therefore, this study proposed a coating process using sodium alginate as a carrier instead of the actual immersion process. The carrier enabled microorganisms to complete the process of mineralizing and depositing calcite in situ to repair defects in cement-based materials. It solved the technical problems in practical applications and promoted the development and application of microbial repair technology.
Because of this, different ratios of sodium alginate-based microbial repair materials were prepared. It utilized different mass concentrations of sodium alginate as a carrier and varied the volume ratio of sodium alginate solution to bacterial solution. First, the effects of sodium alginate on the fundamental properties of microbial repair materials were studied, including CaCO3 content, mechanical properties, water absorption ratio, and heating shrinkage rate. It was used to determine the optimal concentration and dosing of sodium alginate solution. Second, the effects of sodium alginate-based modified microbial repair materials on the macroscopic morphology and surface water absorption ratio of the repaired mortar were investigated. Their effects on the repair of mortar cracks were analyzed in-depth with the material changes and microstructures of the repair products.
Bacillus sphaericus was chosen for the study. The microbial medium (De Muynck et al., 2008) was 1 L of deionized water containing 19 g of nutrient broth, 2.12 g of sodium bicarbonate, and 10 g of urea. The medium was inoculated at 2.0% by volume and incubated in a shaker at 28°C (oscillation rate of 100 r/min) for 24 h before use.
The M30 mortar specimens were prepared as shown in Table 1. The mortar specimens with the molding size of 40 mm × 40 mm × 160 mm were cured for 28 days under the standard conditions of temperature 20°C ± 2°C and relative humidity ≥95%. According to DL/T 5251-2010 (2010), when the crack width is greater than 0.2 mm, it needs to be treated under all kinds of environmental conditions, except for indoor and open-air environments, which can be left untreated. Therefore, the mortar flexural testing machine (DKZ-5000, China) was used to make the mortar specimens wholly broken. The broken specimens were fixed artificially by using tapes and rubber bands, and the crack width was measured using the GTJ-FKY crack width tester (Figure 1), which was determined to be approximately 0.2 mm, to be used in the repair test.
Sodium alginate is a linear anionic polysaccharide under CAS No. 9005-38-3, which can form a viscous gel–like liquid when dissolved in water. Its viscosity will rise with the increase of sodium alginate concentration. The Na+ attached to the carboxyl groups of two adjacent α-L-guluronic (G-unit) in sodium alginate can have a replacement reaction with Ca2+ to form a gel with a tightly packed structure. It can provide a suitable environment for cell immobilization and is an excellent bacterial carrier.
This experiment added 1.0, 1.5, and 2.0 g of sodium alginate powder to 100 ml of deionized water, set at 80°C using a thermostatic heating magnetic stirrer (DF-101S, China). The solution was stirred in a water bath until it was clarified and then cooled for use, and the solutions of sodium alginate with mass concentrations of 1.0%, 1.5%, and 2.0% were obtained.
Component A consisted of sodium alginate, bacteria, and urea. The microbial repair material component A with mass concentrations of 1.0%, 1.5%, and 2.0% of sodium alginate solution was recorded as A1, A2, and A3, respectively. Another mixed solution of sodium alginate and microorganisms was prepared, and the volume mixing ratios of sodium alginate solution and bacterial solution were 10:0, 9:1, 8:2, 7:3, 6:4, and 5:5, respectively. Then, 2.0 mol/L of urea was added to the mixed solution and stirred well to obtain sodium alginate–based microbial repair material components A-0 to A-5. A1-1 indicates that the sodium alginate solution with a mass concentration of 1.0% was mixed with the bacterial solution in the ratio of 9:1, and 2.0 mol/L of urea was added and stirred well to obtain the microbial repair material component A based on sodium alginate.
Component B consisted of calcium acetate and deionized water; 3.16 g of calcium acetate was added to 10 ml of deionized water and stirred well to obtain the microbial repair material component B based on sodium alginate −2 mol/L calcium acetate solution.
The microbial repair material based on sodium alginate consisted of the above two components. The repair products generated by mixing and reacting with component A and component B were recorded as CM, such as CM1-1 indicating the repair products generated by mixing and reacting with repair material component B of component A1-1.
Using the repair process of bottom and top coating, the bacteria were firmly attached to the cracks on the mortar surface for growth by multiple coats, so that they mineralized and deposited CaCO3 in situ, in the specific manner shown in Figure 2: First, a layer of repair material component A–sodium alginate solid–loaded bacteria and urea formulated gelatinous liquid was applied to the cracks on the mortar surface. Then, the repair material component B–calcium acetate solution was applied to its top layer and placed at room temperature for maintenance. When completely dry (approximately 3 h), a second coat was applied according to the above steps to observe its repair effect.
In a beaker, 10 ml of component B was taken, and using a syringe, 10 ml of component A was aspirated. The piston was slowly pushed to make it drop into component B in the form of liquid droplets to make it fully react. The EDTA titration test (Wang, 2017) was used to test the change of Ca2+ content in the solution of the repair material within 4 days of the reaction. When glyoxalbis was used as an indicator and EDTA solution was added to the solution to be tested near the end point, the color of the solution changed from the original burgundy color to the pure blue color of glyoxalbis itself (Figure 3). The acid wash test (Yang et al., 2021) was used to test the CaCO3 content of the precipitate in the beaker after 4 days of reaction.
FIGURE 3. Schematic diagram of the color change of ethylenediaminetetraacetic acid titration test solution.
The tensile mechanical properties of the microbial repair material based on sodium alginate were tested using an intelligent electronic tensile tester with reference to GB/T 23445-2009 (2009). It was added to the mold in the order of component A followed by component B according to the volume ratio of 1:1, and the reaction was performed under standard conditions for 24 h. The repair product after the reaction was made into rectangular films of 90 mm × 20 mm, held on the testing machine with a holding length of 70 mm, and tested for tensile mechanical properties at a tensile speed of 200 mm/min. The above experiments were repeated three times, and the tensile strength and elongation at the break of the repair materials were calculated.
Referring to JG/T 337-2011 (2011), cube concretes of 100 mm × 100 mm × 100 mm were used for the water absorption ratio test. In which concretes, specimens were applied in the order of component A followed by component B and then placed under standard conditions for 24 h. The specimens were then dried at 50°C for 24 h and removed and cooled to room temperature. The rest of the steps and calculations were performed according to the specifications.
Refer to JC/T 864-2008 (2008), in accordance with the volume ratio of 1:1, first component A after component B in the order of adding it to the mold, stood reaction 24 h after demolding. Three pieces of 30 mm × 300 mm specimens were cut for testing, which were placed in an electric blast dryer at a constant temperature of (50°C ± 2°C). The rest of the steps and calculations were performed according to the specifications.
A digital camera (Nikon D750) was used to take pictures of the cracks on the mortar surfaces before and after the restoration to visualize the restoration’s effects.
The effects of repairing cracks on the surface of mortar specimens were characterized by the reduction of water absorption on the surface of the specimens (Wang and Qian, 2008). The repaired surface of the mortar specimens was kept only in the area of 4 cm of the middle crack. The other areas of the repaired surface and the remaining four surfaces other than the repaired surface and their opposite surfaces were sealed with epoxy paint. The specimens were dried at a constant temperature of 50°C for 24 h in an oven, and the drying mass m0 was measured. The specimens were then immersed in (20 ± 2) mm water with the repaired surface facing downward, and the water level was maintained. Then, the specimens were removed every 1 h and dried around the water, and the mass meter was weighed for mt, according to the following formula (Eqs 1–2), to calculate the water absorption rate Et on the surface of the specimens and the water absorption rate reduction coefficient S on the surface of the specimens.
where Et,1 is the water absorption rate of mortar specimen surface after repair and Et,2 is the water absorption rate on the surface of unrepaired mortar specimens of the same age.
The repair products were prefrozen in a refrigerator (−20°C) for 24 h. They were dried using a freeze dryer (FD-1A-80, China) for 48 h and ground into powder. The weight losses of the repair products were examined using a simultaneous thermal analyzer (TA-Q600, United States) with a temperature increase rate of 20°C/min. The freeze–dried repair products were plated with gold using a JEC-3000FC AUTO FINE COATER, and then, their microstructures were analyzed using a JSM-7800F scanning electron microscope.
The effect of sodium alginate on the CaCO3 content of the microbial repair material is shown in Figure 4, where Figures 4A,C,E show the changes of Ca2+ content in the solution of the repair material from 0 to 4 days of the reaction, and Figures 4B,D,F show the CaCO3 content in the precipitate in the beaker after 4 days of the reaction. As shown in Figures 4A,C,E, the repair material component A was mixed with component B, and the sodium alginate in its component A could be rapidly colocalized with component B–calcium acetate solution and kept stable. The Ca2+ concentration in the solution gradually decreased as the reaction time was prolonged. That was due to the continuous microbial-induced mineralization, and the bacteria used urease to decompose urea to produce CO32−, which gradually combined with Ca2+ in the solution to produce CaCO3 crystals (Putri et al., 2020). In addition, as shown in Figures 4A,C,E, the Ca2+ concentration in the beaker solution decreased faster as the percentage of bacterial solution in the repair material component A increased, in which the Ca2+ concentration in A-2, A-3, A-4, and A-5 could decrease from the baseline 2.0 to 0 mol/L after 120, 108, 72, and 48 h, respectively. The reason for the above phenomenon was that as the percentage of the bacterial solution increased, the amount of CO32− formed by decomposing urea would increase, and then, the combination with Ca2+ in the solution would increase, thus making the Ca2+ concentration in the solution decrease faster.
FIGURE 4. Effect of sodium alginate on CaCO3 content of microbial repair materials [(A) Calcium concentration (1.0% Sodium alginate), (B) CaCO3 content (1.0% Sodium alginate), (C) Calcium concentration (1.5% Sodium alginate), (D) CaCO3 content (1.5% Sodium alginate), (E) Calcium concentration (2.0% Sodium alginate), (F) CaCO3 content (2.0% Sodium alginate)].
As shown in Figures 4B,D,F, when the concentration of sodium alginate was 1.0%, the CaCO3 content generated gradually increased with the increase of the percentage of bacterial solution in component A. By contrast, when the concentration of sodium alginate was 1.5% and 2.0%, the CaCO3 content first increased, then decreased, and then increased with the increase of the percentage of bacteria. On the one hand, the above phenomenon was due to the gradual increase of microbial-induced mineralization reaction, and on the other hand, it was due to the reaction between sodium alginate and Ca2+ in the solution to produce calcium alginate gel. It wrapped some microorganisms and affected the mineralization reaction of microorganisms and then caused the decrease in CaCO3 content. However, when the percentage of the bacterial solution reached half, the mineralization reaction of microorganisms was stronger than the wrapping effect of calcium alginate, so the CaCO3 content increased again.
Tensile strength and elongation at break are the indicators to evaluate the deformation behavior of the repair materials. The effects of sodium alginate on the tensile strength and elongation at the break of microbial repair materials are shown in Figures 5 and 6, respectively. Combining the results of Figures 5 and 6, it can be seen that the tensile strength and elongation at the break of the repair material largely increased with the increase of sodium alginate concentration. Combined with the experimental procedures, the concentration of 1.0% sodium alginate was too low, the film solution was dilute, the film formation was poor, and the tensile strength was small. 1.5% and 2.0% sodium alginate solutions were easier to apply, and the tensile strength and elongation at break were higher after film formation. Therefore, the concentration of sodium alginate was chosen to be 1.5% or 2.0% depending on the film-forming state of the repair material component A.
In addition, Figures 5 and 6 show that the film-forming property gradually deteriorated as the percentage of sodium alginate solution in the repair material component A decreased. The tensile strength and elongation at the break of the repair material after film formation gradually decreased as the percentage of bacterial solution continued to increase. The above phenomenon was, on the one hand, due to the increase of CO32− generated by microorganisms using urease to decompose urea, which continuously combined with Ca2+ in the solution, and the deposited CaCO3 generated gradually increased, whereas CaCO3 did not have tensile properties. On the other hand, it was due to the decrease of the proportion of sodium alginate in component A, and the reaction with Ca2+ in solution to generate calcium alginate gel became less, which in turn caused its poor tensile properties.
The water absorption ratio is an effective indicator for evaluating the impermeability of repair materials (Zhu et al., 2002). The effect of sodium alginate on the water absorption ratio of microbial repair materials is shown in Figure 7. As shown in Figure 7, the water absorption ratios of all groups of repair materials were lower than 100%. Thus, it was proved that the water absorption was reduced compared with the uncoated repair materials regardless of the concentration of sodium alginate and the ratio of component A. This indicated that the coating of microbial repair materials based on sodium alginate acting on the mortar structural substrate gradually became dense during the film formation process. It was able to play a certain role in waterproofing and impermeability. In addition, because of the hydrophilic nature of sodium alginate, the overall water absorption of concrete increased with the increase of sodium alginate concentration.
When the concentration of sodium alginate solution was 2.0%, the water absorption ratios of A3-0, A3-1, A3-2, A3-3, A3-4, and A3-5 were 76.81%, 96.4%, 95.1%, 79.9%, 79.8%, and 73.1%, respectively. With the increase of the percentage of bacterial solution in the repair material component A, the water absorption ratios of concrete specimens showed an overall trend of first increasing and then decreasing. This was because when the percentage of the bacterial solution was less, the combination of calcium alginate produced by the colloidal association of sodium alginate and calcium solution and CaCO3 produced by microbial-induced mineralization was relatively loose, with more pores and greater water absorption. With the increase of the percentage of the bacterial solution, the microbial-induced mineralization was enhanced, and the generated CaCO3 crystals grew and filled the capillary pores inside the concrete. It gradually combined with calcium alginate, and the hydrophilicity of the repair material decreased, which in turn led to the decrease in water absorption of concrete specimens.
When the concentration of sodium alginate solution was 1.0%, the water absorption ratios of A1-0, A1-1, A1-2, A1-3, A1-4, and A1-5 were 91.8%, 60.2%, 83.6%, 57.1%, 77.0%, and 79.1%, respectively. When the concentration of sodium alginate solution was 1.5%, the water absorption ratios of the specimens were 77.6%, 87.6%, 85.2%, 64.5%, 66.5%, and 79.0%, respectively. With the increase of the percentage of bacterial solution in the repair material component A, the water absorption ratio of the specimen showed a trend of increasing, then decreasing, and then increasing. It reached the minimum value when the ratio of sodium alginate solution:bacterial solution was 7:3. The above phenomenon was due to the fact that when the concentration of sodium alginate itself was not high, the percentage of bacterial solution kept increasing. It made the viscosity and the integrity of the repair material become poor, resulting in uneven application and causing the water absorption to become large.
Heating shrinkage rate is a simple method to evaluate the high-temperature performance of repair materials in practical applications. The effect of sodium alginate on the heating shrinkage rate of microbial repair materials is shown in Figure 8. As shown in Figure 8, the heating shrinkage rate was reduced from 4.0% to 0.8% when the concentration of sodium alginate was 2.0%, from 2.6% to 0.7% when the concentration of sodium alginate was 1.5%, and from 1.3% to 0% when the concentration of sodium alginate was 1.0%. The heating shrinkage rate of the repair material gradually decreased as the percentage of bacterial solution in component A increased. The reason for the above phenomenon was that the increase in the number of bacteria led to the gradual increase of CaCO3 generated by microbial-induced mineralization deposition. CaCO3 continuously filled in the calcium alginate to play the role of skeleton support, which in turn limited the shrinkage of the repair materials and reduced the heating shrinkage rate of the repair materials.
In addition, Figure 8 shows that the concentration of sodium alginate had an important effect on the heating shrinkage of the repair material. When the ratio of sodium alginate solution:bacterial solution was 10:0, the heating shrinkage increased from 1.3% to 4.0% as the concentration of sodium alginate increased from 1.0% to 2.0%. As the concentration of sodium alginate increased, more calcium alginate was generated by the reaction between sodium alginate and Ca2+, which was susceptible to temperature. Then, it caused a greater heating shrinkage of the repair material. When the ratio of sodium alginate solution:bacterial solution was 5:5, with the increase of sodium alginate concentration from 1.0% to 2.0%, the heating shrinkage rate only increased from 0% to 0.8%. That was because the skeleton effect of CaCO3 precipitation generated by microbial mineralization gradually became larger and inhibited the shrinkage of calcium alginate.
Basic properties such as CaCO3 content, mechanical properties, water absorption ratio, and heating shrinkage rate of the repair materials were tested. It determined that the mass concentration of sodium alginate in component A of the sodium alginate–based microbial repair material for mortar surface cracks was 1.5%. The ratios of sodium alginate solution:bacterial solution were 8:2, 7:3, and 6:4.
The macroscopic morphologies of the mortar surface cracks before and after repair are shown in Figure 9. Figure 9 shows that a crack with an average width of 0.2 mm exists in the mortar specimens before repair. A2-2, A2-3, and A2-4 all showed a denser and continuous white film–like material at the mortar surface cracks, which completely covered the original mortar surfaces and bonded tightly with the mortar surfaces.
FIGURE 9. Macroscopic morphology of mortar surface cracks before and after repair [(A) A2-2, (B) A2-3, (C) A2-4].
The effects of sodium alginate on the surface water absorption rate Et of the specimens and the reduction coefficient S of the surface water absorption rate of the specimens are shown in Figure 10. As shown in Figure 10, A2-2, A2-3, and A2-4 have 60%, 67%, and 63% reduction of water absorption on the surface of the specimens compared with that before repair, respectively. The best repair effect was achieved by using the repair material with the ratio of sodium alginate solution:bacterial solution of 7:3 to repair the cracks on the surface of the mortar. The reasons for the above phenomenon were, on the one hand, the use of sodium alginate as a carrier under room temperature conditions. It could give full play to the viscous effect of alginate, thus firmly attaching the bacteria to the mortar surface cracks to grow so that they could induce mineralization in situ to generate CaCO3. On the other hand, sodium alginate and bacteria could fully react with calcium acetate solution, and its product calcium carbonate crystals were closely combined with calcium alginate.
FIGURE 10. Effect of sodium alginate on the surface water absorption rate Et of the specimens and the reduction coefficient S of the surface water absorption rate of the specimens [(A) Surface water absorption (Et), (B) Surface water absorption reduction factor (S)].
The thermogravimetric curves of the repair products are shown in Figure 11. As shown in Figure 11, the thermogravimetric curves of the repair products showed four stages of weight loss. In the first stage (50°C–180°C), it was mainly due to the loss of free water and bound water inside the samples. In the second stage (180°C–380°C), it was mainly due to the breakage of glycosidic bonds of calcium alginate macromolecules and the formation of more stable intermediate products as well as the dehydration reaction of adjacent hydroxyl groups. In the third stage (380°C–560°C), it was mainly the further oxidation and decomposition of intermediate products after heat, decarboxylation to release CO2 and some small molecules of volatile gases, and carbonization of some products. In the fourth stage (600°C–790°C), mainly calcium carbonate decomposed into calcium oxide and CO2 (Zhang, 2015).
The weight loss rates of A2-2, A2-3, and A2-4 in the second and third stages were 45.53%, 38.86%, and 39.58%, respectively, showing a trend of first decreasing and then increasing. The reason for the above phenomenon was that when the Ca2+ content was low, the calcium source required for microbial mineralization could be achieved by robbing Ca2+ of calcium alginate. It made the in situ coating of bacteria possible and provided a suitable environment for the growth and reproduction of microorganisms, which was conducive to the application of microbial repair technology in engineering. The weight loss rates of the fourth stage were 17.37%, 19.89%, and 23.56%, respectively. With the increase of the percentage of bacterial solution in the repair material component A, the enzymatic action of microorganisms continued, and the calcium carbonate crystals were more closely combined with calcium alginate. It indicated that microbial induced mineralization to produce calcium carbonate crystals was one of the keys to repairing the cracks.
The microstructures of the repair products are shown in Figure 12. As shown in Figure 12, with the increasing percentage of the bacterial solution, more calcium carbonate precipitation is generated by microbial-induced mineralization. The calcium alginate gel was wrapped around the calcium carbonate crystals, making them integral. The calcium carbonate was deposited on the mortar surface using the coating method because the strain of bacteria and nutrients was solidly loaded on the mortar surface by sodium alginate. It created a good environment for microbial-induced mineralization and gradually mineralized calcium carbonate particles in situ at the cracks on the mortar surface, with relatively fine particles, which was beneficial to the repair of the materials.
1) The overall CaCO3 content of the repair material increased with the increase in the mass concentration of sodium alginate and the percentage of bacterial solution. The highest CaCO3 content was 1.68 g when the mass concentration of sodium alginate was 2.0% and the volume ratio of sodium alginate solution and bacterial solution was 5:5.
2) The overall mechanical properties of the repair materials increased with an increase in the mass concentration of sodium alginate and the percentage of sodium alginate solution. The maximum tensile strength and elongation at break were 0.3 MPa and 37.9%, respectively, when the mass concentration of sodium alginate was 2.0% and the volume ratio of sodium alginate solution to bacterial solution was 9:1.
3) The overall water absorption ratio and heating shrinkage rate decreased with decreasing the mass concentration of sodium alginate and the percentage of sodium alginate solution. The minimum water absorption ratio was 57.1% when the mass concentration of sodium alginate was 1.0% and the volume ratio of sodium alginate solution to bacterial solution was 7:3.
4) The basic properties of the repair materials, such as CaCO3 content, mechanical properties, water absorption ratio, and heating shrinkage rate, were compared and tested. The mass concentration of sodium alginate was found to be optimal at 1.5%, and the ratio of sodium alginate solution to the bacterial solution was better at 8:2, 7:3, and 6:4.
5) With the coating repair process, sodium alginate was used as a carrier to fix bacterial strains and nutrients on the mortar surface cracks to create a microenvironment for bacterial growth and enzymatic and calcium carbonate deposition. It could closely adhere to the cracks of the specimens to generate repair products only twice, and the calcium alginate was closely combined with CaCO3 crystals. The surface water absorption ratio could be reduced to 67% of that without repair, with a good repair effect. It increased the feasibility of the practical application of microbial-induced mineralization technology in engineering.
The original contributions presented in the study are included in the article/supplementary material; further inquiries can be directed to the corresponding authors.
HR: Conceptualization, Methodology, Resources, writing—review and editing. KH: Conceptualization, Methodology, Software, Formal analysis, Data curation, writing—original draft. GM: writing—review and editing. XZ: Writing—review and editing.
This work was supported by the National Nature Science Foundation of China (Grant Nos. 51978439, 52178264) and a project funded by the China Postdoctoral Science Foundation (Grant No. 2019M651000).
The authors declare that the research was conducted in the absence of any commercial or financial relationships that could be construed as a potential conflict of interest.
All claims expressed in this article are solely those of the authors and do not necessarily represent those of their affiliated organizations, or those of the publisher, the editors, and the reviewers. Any product that may be evaluated in this article, or claim that may be made by its manufacturer, is not guaranteed or endorsed by the publisher.
De Muynck, W., Debrouwer, D., De Belie, N., and Verstraete, W. (2008). Bacterial carbonate precipitation improves the durability of cementitious materials. Cem. Concr. Res. 38 (7), 1005–1014. doi:10.1016/j.cemconres.2008.03.005
DL/T 5251-2010 (2010). Technical code for detection and evaluation of hydraulic concrete structure. Beijing: Electric Power Press.
GB/T 23445-2009 (2009). Polymer-modified cement compounds for waterproofing membrane. Beijing: Standards Press of China.
Gheorghita Puscaselu, R., Gutt, G., and Amariei, S. (2020). The use of edible films based on sodium alginate in meat product packaging: An Eco-Friendly alternative to conventional plastic materials. Coatings 10 (2), 166. doi:10.3390/coatings10020166
Hu, Y., Liu, W., Wang, W., Jia, X., Xu, L., Cao, Q., et al. (2020). Biomineralization performance ofBacillus sphaericus under the action ofBacillus mucilaginosus. Adv. Mater. Sci. Eng. 2020, 1–9. doi:10.1155/2020/6483803
JC/T 864-2008 (2008). Polymer emulsion architectural waterproof coating. Beijing: China Building Materials Press.
JG/T 337-2011 (2011). Agents of surface coating for protection of concrete structures. Beijing: Standards Press of China.
Joshi, S., Goyal, S., Mukherjee, A., and Reddy, M. S. (2017). Microbial healing of cracks in concrete: A review. J. Ind. Microbiol. Biotechnol. 44 (11), 1511–1525. doi:10.1007/s10295-017-1978-0
Lv, L., Guo, P., Liu, G., Han, N., and Xing, F. (2020). Light induced self-healing in concrete using novel cementitious capsules containing UV curable adhesive. Cem. Concr. Compos. 105, 103445. doi:10.1016/j.cemconcomp.2019.103445
Li, W., Dong, B., Yang, Z., Xu, J., Chen, Q., Li, H., et al. (2018). Recent advances in intrinsic Self-Healing cementitious materials. Adv. Mat. 30 (17), 1705679. doi:10.1002/adma.201705679
Lv, L., Yang, Z., Chen, G., Zhu, G., Han, N., Schlangen, E., et al. (2016). Synthesis and characterization of a new polymeric microcapsule and feasibility investigation in self-healing cementitious materials. Constr. Build. Mat. 105, 487–495. doi:10.1016/j.conbuildmat.2015.12.185
Nain, N., Surabhi, R., Yathish, N. V., Krishnamurthy, V., Deepa, T., and Tharannum, S. (2019). Enhancement in strength parameters of concrete by application of Bacillus bacteria. Constr. Build. Mat. 202, 904–908. doi:10.1016/j.conbuildmat.2019.01.059
Putri, P. Y., Ujike, I., Sandra, N., Rifwan, F., and Andayono, T. (2020). Calcium carbonate in Bio-Based material and factor affecting its precipitation rate for repairing concrete. Crystals 10 (10), 883. doi:10.3390/cryst10100883
Qian, C. X., Wang, J. Y., Wang, R. X., and Cheng, L. (2009). Corrosion protection of cement-based building materials by surface deposition of caco3 by bacillus pasteurii. Mater. Sci. Eng. C 29 (4), 1273–1280. doi:10.1016/j.msec.2008.10.025
Ruan, S., Qiu, J., Weng, Y., Yang, Y., Yang, E., Chu, J., et al. (2019). The use of microbial induced carbonate precipitation in healing cracks within reactive magnesia cement-based blends. Cem. Concr. Res. 115, 176–188. doi:10.1016/j.cemconres.2018.10.018
Sakakihara, Y. (2020). Development of a microbial-based grouting material with calcium carbonate precipitates. Int. J. GEOMATE 18 (69), 18–23. doi:10.21660/2020.69.5616
Seifan, M., Ebrahiminezhad, A., Ghasemi, Y., Samani, A. K., and Berenjian, A. (2018). Amine-modified magnetic iron oxide nanoparticle as a promising carrier for application in bio self-healing concrete. Appl. Microbiol. Biotechnol. 102 (1), 175–184. doi:10.1007/s00253-017-8611-z
Souradeep, G., and Kua, H. W. (2016). Encapsulation technology and techniques in self-healing concrete. J. Mat. Civ. Eng. 28 (12), 4016165. doi:10.1061/(asce)mt.1943-5533.0001687
Van Tittelboom, K., De Belie, N., De Muynck, W., and Verstraete, W. (2010). Use of bacteria to repair cracks in concrete. Cem. Concr. Res. 40 (1), 157–166. doi:10.1016/j.cemconres.2009.08.025
Wang, C. L. (2017). Experimental study on microbial remediation of concrete cracks. Tianjin: Tianjin University. https://kns.cnki.net/kcms/detail/detail.aspx?FileName=1018059067.nh&DbName=CMFD2018.
Wang, R. X., and Qian, C. X. (2008). Restoration of defects on the surface of cement-based materials by microbiologically precipitated CaCO3. J. Chin. Ceram. Soc. 36 (4), 457–464. doi:10.14062/j.issn.0454-5648.2008.04.024
Wiktor, V., and Jonkers, H. M. (2011). Quantification of crack-healing in novel bacteria-based self-healing concrete. Cem. Concr. Compos. 33 (7), 763–770. doi:10.1016/j.cemconcomp.2011.03.012
Wu, M., Hu, X., Zhang, Q., Xue, D., and Zhao, Y. (2019). Growth environment optimization for inducing bacterial mineralization and its application in concrete healing. Constr. Build. Mat. 209, 631–643. doi:10.1016/j.conbuildmat.2019.03.181
Yang, S. M., Peng, J., Wen, Z. L., Leng, M., and Xu, P. X. (2021). Application of concentrated seawater as calcium source solution in sand reinforcement using MICP. Rock Soil Mech. 42 (03), 746–754. doi:10.16285/j.rsm.2020.0424
Zhang, L. (2015). Study on the extraction of human hair keratin, preparation of fibers and finishing of cotton fabrics. Qingdao: Qingdao University. https://kns.cnki.net/kcms/detail/detail.aspx?FileName=1016736736.nh&DbName=CDFD2017.
Zhu, H. X., Hu, F., and Li, Q. (2002). Research on new concrete waterproofing admixture. New Build. Mater. 10, 66–68. https://kns.cnki.net/kcms/detail/detail.aspx?FileName=XXJZ200210020&DbName=CJFQ2002
Keywords: microbial repair materials, sodium alginate, coating, mortar cracks, surface water absorption
Citation: Rong H, Hu K, Ma G and Zheng X (2022) Effect of sodium alginate on the properties of microbial repair materials and its repair effect on mortar crack. Front. Mater. 9:959935. doi: 10.3389/fmats.2022.959935
Received: 02 June 2022; Accepted: 11 July 2022;
Published: 10 August 2022.
Edited by:
Yuli Wang, Henan Polytechnic University, ChinaReviewed by:
Leyang Lv, Shenzhen University, ChinaCopyright © 2022 Rong, Hu, Ma and Zheng. This is an open-access article distributed under the terms of the Creative Commons Attribution License (CC BY). The use, distribution or reproduction in other forums is permitted, provided the original author(s) and the copyright owner(s) are credited and that the original publication in this journal is cited, in accordance with accepted academic practice. No use, distribution or reproduction is permitted which does not comply with these terms.
*Correspondence: Xinguo Zheng, MTUzMDk1MTI0QHFxLmNvbQ==
Disclaimer: All claims expressed in this article are solely those of the authors and do not necessarily represent those of their affiliated organizations, or those of the publisher, the editors and the reviewers. Any product that may be evaluated in this article or claim that may be made by its manufacturer is not guaranteed or endorsed by the publisher.
Research integrity at Frontiers
Learn more about the work of our research integrity team to safeguard the quality of each article we publish.