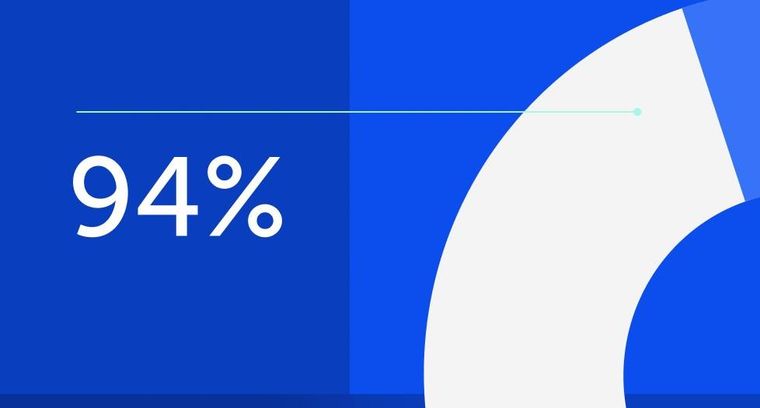
94% of researchers rate our articles as excellent or good
Learn more about the work of our research integrity team to safeguard the quality of each article we publish.
Find out more
ORIGINAL RESEARCH article
Front. Mater., 26 September 2022
Sec. Polymeric and Composite Materials
Volume 9 - 2022 | https://doi.org/10.3389/fmats.2022.951515
A novel flame retardant hexa (4- (9,10-dihydro-9-oxa-10-phosphaphenanthrene-10 -sulfide)-hydroxymethylphenoxy) cyclotriphosphazene (HAP-DOPS) with double functional groups was synthesized, and poly (lactic acid) (PLA) composites were prepared by melt extrusion. The flame retardancy and thermal degradation behavior of flame retardant PLA composites were studied by limiting oxygen index (LOI), vertical burning test (UL-94), cone calorimeter test (CCT), and thermogravimetric-infrared spectroscopy analysis (TG-IR). The experimental results showed that HAP-DOPS had a good flame-retardant effect on PLA. At flame retardant content of 5 wt%, the PLA/HAP-DOPS composite achieved a V-0 rating (UL-94, 3.2 mm) and a LOI value of 26.6%. The heat release rate (HRR) and total heat release (THR) of PLA composites were decreased by adding HAP-DOPS. The flame retardancy index (FRI) of PLA/HAP-DOPS-7.5 wt% was 1.0257, which showed good flame retardancy. The results of TG-IR showed that HAP-DOPS mainly had a gas-phase flame-retardant effect in PLA.
Poly (lactic acid) (PLA) is an environment-friendly polymer material with good biodegradability and compatibility. Also, it is widely used in biomedical materials, packaging materials, automobiles and electronic appliances, and other fields because of its wide range of raw materials, excellent mechanical properties, and easy processing and molding (He et al., 2020; Yang et al., 2020; Gong et al., 2020; Tawiah et al., 2020; Laoutid et al., 2018; Vahabi et al., 2018; Xue et al., 2021; Kervran et al., 2022). However, PLA is extremely flammable and accompanied by serious dripping during combustion, which cannot meet the requirements of terminal products in the field of automobile parts and electronic and electrical appliances, thus limiting its application scope (Xue et al., 2011; Li et al., 2019; Feng et al., 2020; Muhammad et al., 2020). Therefore, it is essential and important to improve the flame-retardant properties of PLA, and great attempts have been made to develop fire-retardant PLA materials (Liu et al., 2022; Guo et al., 2017; Yu et al., 2022; Feng et al., 2022; Xu S. et al., 2020; Yang et al., 2021; Rad et al., 2019; Vahabi et al., 2018).
In the organophosphorus flame-retardant research in PLA, 9,10-dihydro-9-oxa-phospha- phenanthrene-10-oxide (DOPO) and its derivatives have been widely and deeply studied due to their environmental friendliness, high carbon content, and durable flame retardancy (Salmeia and Gaan, 2015; Wang et al., 2016). It has been demonstrated that DOPO and its derivatives exhibit excellent flame-retarding effects in polymers due to their positive actions in the gas phase (as a flame inhibitor) and condensed phase (by char formation) (Wen et al., 2020). 9,10-dihydro-9-oxa-10-phosphaphenanthrene-10-sulfide (DOPS) was successfully synthesized by a simple one-step reaction of DOPO and phosphorus pentasulfide (P2S5). It has been shown that introduction of sulfur into the DOPO flame retardant can enhance the flame-retardant effect of phosphorus on the one hand and provide excellent flame-retardant properties in the condensed phase (Huo et al., 2018; Xu X. D. et al., 2020); on the other hand, the reactivity of the P-H bond is increased, and it is easier to undergo addition reactions with unsaturated groups, which facilitates the generation of a series of DOPS derivatives (Rakotomalala et al., 2011; Chen et al., 2017).
Through molecular design, our research group would introduce the phosphazene group and DOPS into the same molecule and successfully synthesize the flame retardant hexa (4-(9,10-dihydro-9-oxa-10-phosphophene-10-sulfide)-hydroxymethyl-phenoxy) cyclotriphos- phazene (HAP-DOPS) with double functional groups. The flame retardant efficiency of DOPS would be improved by using the potential char forming characteristics of phosphazene compounds, and the flame-retardant materials with excellent flame retardancy would be obtained through the synergistic effect of double functional groups so as to build a new high-efficient flame retardant system.
In this study, the flame retardant HAP-DOPS with double functional groups was synthesized from hexa-(4-aldehyde-phenoxy)-cyclotriphosphazene (HAP) and DOPS. The structure was characterized by Fourier transform infrared (FT-IR) spectrum, nuclear magnetic resonance (NMR), and high-resolution mass spectrometry (HR MS). Then, the flame retardant HAP-DOPS was added into PLA by melt blending. Finally, the effects of the flame retardant HAP-DOPS on the flame retardant properties and thermal degradation behavior of PLA were investigated by limiting oxygen index (LOI), vertical burning test (UL-94), cone calorimeter test (CCT), and thermogravimetric-infrared spectroscopy analysis (TG-IR).
PLA (4032D) was purchased from Natureworks (United States). DOPS (Chen et al., 2017) and HAP (Bao et al., 2018) were prepared in our laboratory according to references. Other reagents of analytical grade were purchased from Sinopharm Chemical Reagent Co. Ltd. (Shanghai, China).
2.32 g (10 mmol) DOPS and 30 ml tetrahydrofuran were added into a 250 ml three-necked glass flask equipped with a reflux device and mechanical stirrer and stirred with nitrogen for 20 min. After the DOPS was completely dissolved, 0.86 g (1 mmol) HAP was dissolved in 10 ml of tetrahydrofuran and slowly added dropwise to the abovementioned reaction system. After the dropwise addition, the temperature was increased to 80°C and the reaction lasted for 24 h. After the system was cooled to room temperature, the supernatant was poured off and washed several times with ethyl acetate. Finally, 1.6 g of white powder solid (yield of 71%) was obtained. The synthetic route of flame retardant HAP-DOPS with double functional groups is shown in Figure 1A.
FIGURE 1. (A) Synthesis of flame retardant HAP-DOPS with double functional groups. (B) FT-IR spectrum of the compounds HAP、DOPS and HAP-DOPS. (C) 1H NMR spectrum of HAP-DOPS. (D)31P NMR spectrum of HAP-DOPS. (E) TG-DTG curves of HAP-DOPS.(F) TG curves of PLA and PLA composites.(G) DTG curves of PLA and PLA composites.
The flame retardant PLA composites were prepared by the melt extrusion method. First, both PLA and HAP-DOPS were dried for 6 h under vacuum at 80 °C before use. Then, PLA and HAP-DOPS (5,7.5,10 wt%) were mixed uniformly in a high-speed mixer. Next, the mixture was separately extruded by a two-screw extruder (CTE 35, Coperion Keya Machinery Manufacturing Co., Ltd., China) at a temperature of 155–175°C and screw speed of 300 rpm. Finally, the extruded pellets were molded into standard samples for testing on a miniature injection molding machine (SZS-20, Wuhan Ruiming Experimental Machinery Manufacturing Co., Ltd., China) at 160–180°C.
FT-IR spectra were recorded on a Nicolet 6,700 infrared spectrometer (thermo, United States), and the samples were prepared by KBr pellets. 1H and 31P nuclear magnetic resonance (NMR) characterized on an AVANCEⅢHD 400 MHz spectrometer (Bruker, Switzerland) was performed using DMSO (δ 3.33ppm(H)) as the solvent and neat H3PO4 (δ 0.0 ppm) was used as an internal standard for 31P NMR. In the MS test, the relative molecular mass of the flame retardant was determined by MS analysis with dichloromethane as the solvent.
The LOI test was performed on a JF-3 oxygen index meter (Nanjing Jiangning Analysis Instrument Company, China) according to the GB/T 2406.1–2008 standard with a sample dimension of (80 ± 5) mm × (10.0 ± 0.5) mm × (4.0 ± 0.25) mm.
The UL-94 test (CZF-5, Jiangsu Zhuoheng Measurement & Control Technology Co., Ltd., China) was carried out according to the GB/T 2408–2021 standard, with a sample size of (125 ± 5) mm × (13 ± 0.3) mm × (3 ± 0.2) mm.
CCT (VOUCH 6810, Suzhou Yangyi Volchi Company Co., Ltd, China) was conducted with the ISO 5660-1-2002 standard. The specimens were prepared with sizes of (100 ± 5) mm× (100 ± 5) mm× (6 ± 0.5) mm and tested under a heat flux of 50 kW/m2.
TG-FTIR analysis was performed on the TG 209F3 thermogravimetric analyzer (Netzsch, Germany) and TENSOR27 infrared spectrometer (Bruker, Germany). The sample of 5–10 mg was heated from room temperature to 700°C with a heating rate of 20 °C/min under a nitrogen atmosphere, and the gas flow rate was 60 ml/min. The real-time FT-IR spectra were recorded.
The flame retardancy index (FRI) (Vahabi et al., 2019) is a simple and universal, dimensionless criterion defined from cone calorimetry data for thermoplastic composites and quantifies the flame retardancy of different polymer composites on a reliable set of data. Its calculation formula is as follows:
THR—total heat release rate; PHRR—the maximum heat release rate; TTI—the ignition time.
The chemical structure of HAP-DOPS was characterized by FT-IR, 1H, 31P NMR, and HRMS. The FT-IR, 1H, and 31P NMR spectra of HAP-DOPS are shown in Figures 1B–D, respectively. FT-IR (KBr) ν (cm−1) 3,388.71 (O—H), 3,061.60 (CAr —H), 1,581.37 (P— Ph), 1,473.35–1,428.99 (C—CAr), 1,199.51–1,160.94 (P = N), 954.10 (P = S). 1H NMR (400 MHz, DMSO - d6): δ (ppm) 8.25–7.99 (m, 12H), 7.98–7.32 (m, 24H), 7.32–7.09 (m, 24H), 6.97 (d, J = 36.0 Hz, 12H), 6.70–6.27 (m, 6H), 5.25 (d, J = 61.1 Hz, 6H) ppm. 31P NMR (160 MHz, DMSO - d6): δ (ppm) 83.27, 7.91. MS(ESI) (m/z): [MH]+calcd for C114H84N3O18P9S6 2,255. Found:2,255. All the abovementioned characterization results with the FT-IR, NMR, and MS confirmed that HAP-DOPS had been synthesized.
The thermal stability of flame retardants affects the thermal stability and flame-retardant effect of the substrates to a certain extent. Figure 1E shows the TG-DTG curve of HAP-DOPS under a nitrogen atmosphere. The TG curve shows that the initial decomposition temperature (T5%) of HAP-DOPS is 336.8°C, which indicates that HAP-DOPS has good thermal stability indicates that HAP-DOPS has good thermal stability. HAP-DOPS has only one thermal weight loss stage, which occurs from 330 to 600°C. The maximum decomposition temperature (Tmax, DTG peak maximum) of the compounds occurred at 446.5°C. It may be due to the dehydration cross-linking reaction of intramolecular and intermolecular hydroxyl groups and the breakage of P-C bonds resulting in the phosphaphenanthrene group decomposing to generate some volatile substances. When the temperature reaches 550°C, the TG curve tends to level off, and the char residues at 700°C were 54.14%. It can be seen that HAP-DOPS has good char forming ability and meets the processing requirements of PLA.
The effects of HAP-DOPS on the thermal stability of PLA were investigated using TG. The TG and DTG curves of PLA and PLA/HAP-DOPS are shown in Figures 1F,G, and the corresponding data are listed in Table 1. The T5% and Tmax values of PLA/HAP-DOPS are lower than those of neat PLA. When the addition of HAP-DOPS reached 10 wt%, the T5% value of PLA/HAP-DOPS decreased from 332.5 to 318.0°C, which was about 14.5°C, because the bond energy of the P-C bond was only 272 kJ/mol and the P-C bond in HAP-DOPS is first decomposed when heated, producing phosphorus-containing compounds that promote the thermal decomposition of PLA, resulting in a T5% reduction of PLA/HAP-DOPS. With the temperature increasing, the flame retardant HAP-DOPS further decomposes, releasing non-flammable gases such as NH3, H2O, and CO2, which dilute the O2 and combustible materials nearby, producing a flame-retardant effect in the gas phase. In addition, the residues of PLA/HAP-DOPS-5 wt%, PLA/HAP-DOPS-7.5 wt%, and PLA/HAP-DOPS-10 wt% show a slight increase at 700°C from 0% (neat PLA) to 1.9, 2.1, and 2.4%, respectively. Moreover, according to the DTG curve, the Rmax values of PLA/HAP-DOPS decrease, indicating that HAP-DOPS has an inhibiting effect on the decomposition of PLA composites.
To investigate the flame ratardancy of polymer composites, the LOI and UL-94 tests are usually necessary (Qian et al., 2015; Long et al., 2018). The results of LOI and UL-94 vertical burning tests are listed in Table 2. As shown in Table 2, the LOI value of neat PLA was 21.6% and failed to pass the UL-94 test with the melt dripping phenomenon. However, with increasing content of HAP-DOPS, the LOI values of the PLA/HAP-DOPS composites showed an increasing trend, which reached the UL-94 V-0 flammability rating. At a flame-retardant content of 5 wt%, the LOI value of PLA/HAP-DOPS was 26.6%, and the average combustion time for the first and second flame combustion after the sample was removed from the fire was 0.61 and 1.20s, respectively, both less than 10 s. Moreover, the molten droplets produced did not ignite the absorbent cotton, and it achieved UL-94 V-0 flammability rating. At this time, the phosphorus content of the PLA/HAP-DOPS composite was only 0.62 wt%. When the addition of HAP-DOPS was increased to 7.5 wt%, the LOI value of the composites increased to 28.2%. But, when the addition was continually increased to 10 wt%, the LOI values remained unchanged, indicating that there may be an optimal addition amount of HAP-DOPS for PLA composites. In the tests, it was found that PLA/HAP-DOPS composites still produced molten droplet phenomena probably because the molten droplets would take away the heat generated during combustion and thus play a certain flame-retardant role (Long et al., 2017).
The effect of HAP-DOPS on the combustion properties of PLA composites was analyzed by CCT, and the heat release rate (HRR) and the total heat release (THR) curves are shown in Figures 2A,B. The HRR and THR values of PLA composites decreased after the addition of HAP-DOPS and showed a decreasing trend with the increase of HAP-DOPS addition. When the addition of HAP-DOPS was increased to 10 wt%, the peak HRR (PHRR) value decreased from 698.50 to 556.77 kW/m2, a decrease of 20.29%. The THR value decreased from 190.86 to 164.57 MJ/m2, a decrease of 13.77%. It indicated that the flame retardant HAP-DOPS with double functional groups could promote the formation of char in the polymer substrate and block the heat transfer within the material during combustion, reducing the combustion degree and the THR of the PLA/HAP-DOPS composites (Sun et al., 2022).
FIGURE 2. FIGURE 2 (A) HRR curves of PLA and PLA composites; (B) THR curves of PLA and PLA composites; (C), (D), (E) SEM images of char residues of PLA/HAP-DOPS-5 wt%, PLA/HAP-DOPS-7.5 wt% and PLA/HAP-DOPS-10 wt%; (F) The 3D TG-FTIR spectrum of PLA/HAP-DOPS; (G)The absorbance of pyrolysis products of PLA/HAP-DOPS at different temperatures.
According to the formula of FRI, FRI(PLA/HAP-DOPS-5 wt%) = 0.7463 < 1, 1 < FRI(PLA/HAP-DOPS-7.5 wt%) = 1.0257 < 10, FRI(PLA/HAP-DOPS-10 wt%) = 0.9590 < 1, that is, the flame retardancy of PLA/HAP-DOPS-7.5 wt% is good, while the flame retardancy of the other two composites is poor. The result is consistent with LOI and UL-94 tests, which indicate that there may be an optimal addition amount of HAP-DOPS for PLA composites to achieve good flame retardancy.
In order to analyze the mechanism of condensed phase flame retardancy, SEM was used to analyze the microscopic morphology of the char layer surface. As can be seen from Figures 2C–E, the char residue of PLA/HAP-DOPS-5 wt% is broken, with only a small continuous char layer and a rough surface. When the addition amount of HAP-DOPS was 7.5 wt%, the char layer began to be continuous with a large number of pore channels. Meanwhile, incomplete combustion flame retardant particles covering the surface of the carbon residue could be observed, which may indicate migration and accumulation of flame retardants during combustion. When the amount of the flame retardant reaches 10 wt%, the char layer becomes denser.
The TG-FTIR was used to study the gaseous small-molecule compounds during the thermal degradation process of PLA/HAP-DOPS composites, and the test results are shown in Figures 2F,G. As can be seen from the figures, there were absorption peaks of hydroxyl groups in water molecules (3,571 cm−1), hydrocarbons (2,631∼2919cm−1) (Liang et al., 2017), CO2 (2,344 cm−1) (Xu et al., 2016), CO (2,180, 2091cm−1), and carbonyl compounds (1757 cm−1) (Chistyakov Evgeniy et al., 2019). The stretching vibration absorption peak of S=O was at 1,371 cm−1 (Yang et al., 2016). The absorption peak of 1,123 cm−1 was from SO2 (Battig et al., 2019), and 923 cm−1 was the absorption peak of P-O-C. At the initial stage of thermal degradation, PLA/HAP-DOPS composites showed a weak CO2 absorption peak. With the increase of temperature, the thermal degradation reaction began to intensify. When the temperature reached 352°C, the absorption peaks of hydrocarbons, carbonyl compounds, S=O, and SO2 appeared. At about 370 °C, the thermal degradation rate of PLA/HAP-DOPS reached its maximum, when the characteristic absorption peaks of various thermal degradation products were the strongest. When the temperature reached 400 °C, only the stretching vibration absorption peak of carbonyl compounds had a weak intensity. When the temperature increased to 450°C, the absorption peaks of thermal degradation gas basically disappeared, which indicated that PLA/HAP-DOPS composites had been completely degraded at this time. Furthermore, the characteristic peak of phosphorus-containing functional groups appeared at 923 cm−1 (Fang et al., 2017), which indicated that the phosphorus containing free radicals were generated in the gas phase, which captured free radicals such as H•, O•, or •OH. Also, it played the role of free radical quenching so that the flame retardant HAP-DOPS with double functional groups played the role of a flame retardant in the gas phase.
The mechanical properties of PLA/HAP-DOPS are shown in Table 3. With the increase of HAP-DOPS content, the mechanical properties of PLA/HAP-DOPS showed a decreasing trend, the bending strength decreased slightly, and the tensile strength and impact strength decreased significantly. When the HAP-DOPS content was 10 wt%, the tensile strength of the PLA/HAP-DOPS composite decreased from 66.89 to 37.99 MPa, which decreased by 43.20%. Its impact strength decreased from 3.54 to 2.24 kJ/m2, decreasing by 36.72%. This may be because the introduction of HAP-DOPS, a macromolecular flame retardant containing a large number of rigid groups, into the main chain of the polymer will lead to a decrease in the toughness of the material. In summary, when the addition of HAP-DOPS is 5 wt%, PLA/HAP-DOPS reaches a UL-94 V-0 rating and still maintains good mechanical properties. Its tensile strength, bending strength, and notch impact strength are 41.78 MPa, 83.02 MPa, and 3.02 kJ/m2, respectively.
A novel flame retardant HAP-DOPS with double functional groups was synthesized, and its structure was characterized by FT-IR, 1H-NMR, 31P-NMR, and MS. Then, the effect of HAP-DOPS on the flame retardancy and thermal degradation behavior of PLA was investigated. The results indicated that HAP-DOPS could decrease the PHRR, improve the LOI and UL-94 rating, and promote char formation. At a flame retardant content of 5 wt%, V-0 rating in the UL-94 test was achieved by PLA/HAP-DOPS. When the amount of HAP-DOPS was increased to 7.5 wt%, a high LOI value of 28.2% was obtained. FRI(PLA/HAP-DOPS- 7.5 wt%) was higher than the other two PLA composites. In addition, the PLA/HAP-DOPS composites decomposed earlier than neat PLA under N2 conditions. The TG-FTIR test results showed that HAP-DOPS played a flame-retardant effect through quenching free radicals in the gas phase. To sum up, when the addition of HAP-DOPS in PLA is 7.5 wt%, the composite can obtain better flame retardancy.
The original contributions presented in the study are included in the article/Supplementary Material; further inquiries can be directed to the corresponding author.
JW and ZH prepared materials and carried out experiments. ZX, XY, and YQ helped to analyze experimental data. SX, LL, ZW, and ZhuW helped to characterize materials. DB was responsible for writing and revising the article. All authors contributed to revise the manuscript, approved the final version, and agreed to be accountable for all aspects of this work.
We would like to acknowledge the financial support from the Natural Science Foundation of China (Grant No.51863004 and 52163001), Guizhou Provincial Science and Technology Projects (Grant No.[2020]1Y211, CXTD [2021]005), and the Polymer Composites Engineering Research Center of Guizhou Minzu University (Grant No.GZMUGCZX [2021]01).
The authors declare that the research was conducted in the absence of any commercial or financial relationships that could be construed as a potential conflict of interest.
All claims expressed in this article are solely those of the authors and do not necessarily represent those of their affiliated organizations, or those of the publisher, the editors, and the reviewers. Any product that may be evaluated in this article, or claim that may be made by its manufacturer, is not guaranteed or endorsed by the publisher.
Bao, D. M., Fang, L., Wen, Z., Long, G. H., Ren, Y., Hu, X. B., et al. (2018). Preparation and thermal decomposition kinetics of epoxy resin modified with cyclotriphosphazene. J. Funct. Mat. 49, 11089–11095. doi:10.3969/j.issn.1001-9731.2018.11.015
Battig, A., Markwart, J. C., Wurm, F. R., and Schartel, B. (2019). Sulfur's Role in the Flame retardancy of thio-ether-linked hyperbranched poly(phosphoesters) in epoxy resins. Eur. Polym. J. 122, 109390. doi:10.1016/j.eurpolymj.2019.109390
Chen, S. M., Lai, F., Li, P., Gong, W., Fu, H., Yin, X. G., et al. (2017). Synthesis of flame retardant based on phosphaphenanthrene and flame retardancy study of epoxy resin modified by intumescent flame retardant system composed of ammonium polyphosphate. Acta Polym. Sin. 8, 1358–1365. doi:10.11777/j.issn1000-3304.2017.16350
Chistyakov Evgeniy, M., Terekhov Ivan, V., Shapagin Aleksey, V., Filatov Sergey, N., and Chuev Vladimir, P. (2019). Curing of epoxy resin DER-331 by hexakis(4-Acetamidophenoxy) cyclotriphosphazene and properties of the prepared composition. Polym. (Basel). 11, 1191. doi:10.3390/polym11071191
Fang, Y. C., Zhou, X., Xing, Z. Q., and Wu, Y. R. (2017). An effective flame retardant for poly(ethylene terephthalate) synthesized by phosphaphenanthrene and cyclotriphosphazene. J. Appl. Polym. Sci. 34, 45246–45253. doi:10.1002/app.45246
Feng, J. B., Ma, Z. W., Xu, Z. G., Xie, H. Y., Lu, Y. X., Maluk, C., et al. (2022). A Si-containing polyphosphoramide via green chemistry for fire-retardant polylactide with well-preserved mechanical and transparent properties. Chem. Eng. J. 431, 134259. doi:10.1016/j.cej.2021.134259
Feng, J. B., Xu, X. D., Xu, Z. G., Xie, H. Y., Song, P. A., Li, L. J., et al. (2020). One-pot, solvent-and catalyst-free synthesis of polyphosphoramide as an eco-benign and effective flame retardant for poly (lactic acid). ACS Sustain. Chem. Eng. 8 (44), 16612–16623. doi:10.1021/acssuschemeng.0c05931
Gong, W. G., Fan, M., Luo, J., Liang, J., and Meng, X. (2020). Effect of nickel phytate on flame retardancy of intumescent flame retardant polylactic acid. Polym. Adv. Technol. 32, 1548–1559. doi:10.1002/pat.5190
Guo, Y. C., Chang, C. C., Xue, Y., Zuo, X. H., Pack, S., Zhang, L. X., et al. (2017). Engineering flame retardant biodegradable polymer nanocomposites and their application in 3D printing. Polym. Degrad. Stab. 137, 205–215. doi:10.1016/j.polymdegradstab.2017.01.019
He, W. T., Song, P. A., Yu, B., Fang, Z. P., and Wang, H. (2020). Flame retardant polymeric nanocomposites through the combination of nanomaterials and conventional flame retardants. Prog. Mat. Sci. 114, 100687. doi:10.1016/j.pmatsci.2020.100687
Huo, S. Q., Wang, J., Yang, S., Chen, X., Zhang, B., Wu, Q. L., et al. (2018). Flame-retardant performance and mechanism of epoxy thermosets modified with a novel reactive flame retardant containing phosphorus, nitrogen, and sulfur. Polym. Adv. Technol. 29, 497–506. doi:10.1002/pat.4145
Kervran, M., Vagner, C., Cochez, M., Poncot, M., Saeb, M. R., and Vahabi, H. (2022). Thermal degradation of polylactic acid (PLA)/polyhydroxybutyrate (PHB) blends: A systematic review. Polym. Degrad. Stab. 201, 109995 doi:10.1016/j.polymdegradstab.2022.109995
Laoutid, F., Vahabi, H., Shabanian, M., Aryanasab, F., Zarrintaj, P., and Saeb, M. R. (2018). A new direction in design of bio-based flame retardants for poly(lactic acid). Fire Mat. 42, 914–924. doi:10.1002/fam.2646
Li, D. F., Zhao, X., Jia, Y. W., He, L., Wang, X. L., and Wang, Y. Z. (2019). Simultaneously enhance both the flame retardancy and toughness of polylactic acid by the cooperation of intumescent flame retardant and bio-based unsaturated polyester. Polym. Degrad. Stab. 168, 108961. doi:10.1016/j.polymdegradstab.2019.108961
Liang, W. J., Zhao, B., Zhao, P. H., Zhang, C. Y., and Liu, Y. Q. (2017). Bisphenol-S bridged penta(anilino) cyclotriphosphazene and its application in epoxy resins: Synthesis, thermal degradation, and flame retardancy. Polym. Degrad. Stab. 135, 140–151. doi:10.1016/j.polymdegradstab.2016.11.023
Liu, L. N., Shi, B. B., Zhang, A. L., Xue, Y. J., Zhang, J. Z., Dai, J. F., et al. (2022). A polyphosphoramide-grafted lignin enabled thermostable and fire-retardant polylactide with preserved mechanical properties. Compos. Part A Appl. Sci. Manuf. 160, 107028. doi:10.1016/j.compositesa.2022.107028
Long, L. J., Chang, Q. F., He, W. T., Xiang, Y. S., Qin, S. H., Yin, J. B., et al. (2017). Effects of bridged DOPO derivatives on the thermal stability and flame retardant properties of poly(lactic acid). Polym. Degrad. Stab. 139, 55–66. doi:10.1016/j.polymdegradstab.2017.03.016
Long, L. J., Yin, J. B., He, W. T., Xiang, Y. S., Qin, S. H., and Yu, J. (2018). Synergistic effect of different nanoparticles on flame retardant poly(lactic acid) with bridged DOPO derivative. Polym. Compos. 40, 1043–1052. doi:10.1002/pc.24791
Muhammad, M., Fabian, L., and Gunnar, S. (2020). Investigation of melt spinnability of plasticized polylactic acid biocomposites-containing intumescent flame retardant. J. Therm. Anal. Calorim. 139, 305–318. doi:10.1007/s10973-019-08405-3
Qian, L. J., Qiu, Y., Wang, J. Y., and Wang, X. (2015). High-performance flame retardancy by char-cage hindering and free radical quenching effects in epoxy thermosets. Polymer 68, 262–269. doi:10.1016/j.polymer.2015.05.031
Rad, E. R., Vahabi, H., de Anda, A. R., Saeb, M. R., and Thomas, S. (2019). Bio-epoxy resins with inherent flame retardancy. Prog. Org. Coat. 135, 608–612. doi:10.1016/j.porgcoat.2019.05.046
Rakotomalala, M., Wagner, S., Zevaco, T., Ciesielski, M., Walter, O., and Döring*, M. (2011). Synthesis and reactivity of 6H-dibenzo[c, e] [1, 2]oxaphosphinine 6-sulfide, a novel thiophosphacyclic molecule. Heterocycles 83, 743–753. doi:10.3987/COM-10-12124
Salmeia, K. A., and Gaan, S. (2015). An overview of some recent advances in DOPO-derivatives: Chemistry and flame retardant applications. Polym. Degrad. Stab. 113, 119–134. doi:10.1016/j.polymdegradstab.2014.12.014
Sun, X. Y., Li, L. L., Yang, Y. B., Jia, C. F., Zhang, X. L., Wu, J. X., et al. (2022). Flame-retardant effect of hyperbranched phosphazene-based microspheres in poly(L-lactic acid). J. Mat. Sci. 57, 1516–1535. doi:10.1007/s10853-021-06719-y
Tawiah, B., Yu, B., Yuen, A. C. Y., and Fei, B. (2020). Facile preparation of uniform polydopamine particles and its application as an environmentally friendly flame retardant for biodegradable polylactic acid. J. Fire Sci. 38, 485–503. doi:10.1177/0734904120932479
Vahabi, H., Kandola, B. K., and Saeb, M. R. (2019). Flame retardancy index for thermoplastic composites. Polym. (Basel). 11 (3), 407. doi:10.3390/polym11030407
Vahabi, H., Shabanian, M., Aryanasab, F., Laoutid, F., Benali, S., Saeb, M. R., et al. (2018). Three in one: β-Cyclodextrin, nanohydroxyapatite, and a nitrogen-rich polymer integrated into a new flame retardant for poly (lactic acid). Fire Mat. 42 (6), 593–602. doi:10.1002/fam.2513
Vahabi, H., Shabanian, M., Aryanasab, F., Mangin, R., Laoutid, F., and Saeb, M. R. (2018). Inclusion of modified lignocellulose and nano-hydroxyapatite in development of new bio-based adjuvant flame retardant for poly(lactic acid). Thermochim. Acta 666, 51–59. doi:10.1016/j.tca.2018.06.004
Wang, J. Y., Qian, L. J., Huang, Z. G., Fang, Y. Y., and Qiu, Y. (2016). Synergistic flame-retardant behavior and mechanisms of aluminum poly-hexamethylenephosphinate and phosphaphenanthrene in epoxy resin. Polym. Degrad. Stab. 130, 173–181. doi:10.1016/j.polymdegradstab.2016.06.010
Wen, X., Liu, Z., Li, Z., Zhang, J., Wang, D. Y., Szymanska, K., et al. (2020). Constructing multifunctional nanofiller with reactive interface in PLA/CB-g-DOPO composites for simultaneously improving flame retardancy, electrical conductivity and mechanical properties. Compos. Sci. Technol. 188, 107988. doi:10.1016/j.compscitech.2019.107988
Xu, M. J., Xu, G. R., Leng, Y., and Li, B. (2016). Synthesis of a novel flame retardant based on cyclotriphosphazene and DOPO groups and its application in epoxy resins. Polym. Degrad. Stab. 123, 105–114. doi:10.1016/j.polymdegradstab.2015.11.018
Xu, S., Zhang, M., Li, S. Y., Zeng, H. Y., Tian, X. Y., Wu, K., et al. (2020). Intercalation of a novel containing nitrogen and sulfur anion into hydrotalcite and its highly efficient flame retardant performance for polypropylene. Appl. Clay Sci. 191, 105600. doi:10.1016/j.clay.2020.105600
Xu, X. D., Dai, J. F., Ma, Z. W., Liu, L. N., Zhang, X. H., Liu, H. Z., et al. (2020). Manipulating interphase reactions for mechanically robust, flame-retardant and sustainable polylactide biocomposites. Compos. Part B Eng. 190, 107930. doi:10.1016/j.compositesb.2020.107930
Xue, Q. L., De, Y. W., Xiu, L. W., Li, C., and Yu, Z. W. (2011). Synthesis of organo-modified α -zirconium phosphate and its effect on the flame retardancy of IFR poly(lactic acid) systems. Polym. Degrad. Stab. 96, 771–777. doi:10.1016/j.polymdegradstab.2011.02.022
Xue, Y. J., Feng, J. B., Ma, Z. W., Liu, L. N., Zhang, Y., Dai, J. F., et al. (2021). Advances and challenges in eco-benign fire-retardant polylactide. Mat. Today Phys. 21, 100568. doi:10.1016/j.mtphys.2021.100568
Yang, H. T., Shi, B. B., Xue, Y. J., Ma, Z. W., Liu, L. N., Liu, L., et al. (2021). Molecularly engineered lignin-derived additives enable fire-retardant, UV-shielding, and mechanically strong polylactide biocomposites. Biomacromolecules 22 (4), 1432–1444. doi:10.1021/acs.biomac.0c01656
Yang, H. T., Yu, B., Xu, X. D., Bourbigot, S., Wang, H., and Song, P. A. (2020). Lignin-derived bio-based flame retardants toward high-performance sustainable polymeric materials. Green Chem. 22, 2129–2161. doi:10.1039/D0GC00449A
Yang, Y. Y., Liu, J., and Cai, X. F. (2016). Antagonistic flame retardancy between hexakis(4-nitro-phenoxy) cyclotriphosphazene and potassium diphenylsulfone sulfonate in the PC system. J. Therm. Anal. Calorim. 126, 571–583. doi:10.1007/s10973-016-5519-2
Keywords: poly(lactic acid), phosphaphenanthrene, cyclotriphosphazene, flame retardancy, thermal degradation behavior
Citation: Bao DM, Wang JH, Hou ZM, Xu ZY, Ye XL, Qi YZ, Xu SJ, Long LJ, Wu ZL and Wen Z (2022) Synthesis of a novel flame retardant with phosphaphenanthrene and phosphazene double functional groups and flame retardancy of poly (lactic acid) composites. Front. Mater. 9:951515. doi: 10.3389/fmats.2022.951515
Received: 02 June 2022; Accepted: 19 August 2022;
Published: 26 September 2022.
Edited by:
Henri Vahabi, Université de Lorraine, FranceReviewed by:
Mohammad Reza Saeb, Gdansk University of Technology, PolandCopyright © 2022 Bao, Wang, Hou, Xu, Ye, Qi, Xu, Long, Wu and Wen. This is an open-access article distributed under the terms of the Creative Commons Attribution License (CC BY). The use, distribution or reproduction in other forums is permitted, provided the original author(s) and the copyright owner(s) are credited and that the original publication in this journal is cited, in accordance with accepted academic practice. No use, distribution or reproduction is permitted which does not comply with these terms.
*Correspondence: Dong Mei Bao, ZG9uZ3RpYW4xMzE0NTIxQDE2My5jb20=
†These authors have contributed equally to this work
Disclaimer: All claims expressed in this article are solely those of the authors and do not necessarily represent those of their affiliated organizations, or those of the publisher, the editors and the reviewers. Any product that may be evaluated in this article or claim that may be made by its manufacturer is not guaranteed or endorsed by the publisher.
Research integrity at Frontiers
Learn more about the work of our research integrity team to safeguard the quality of each article we publish.