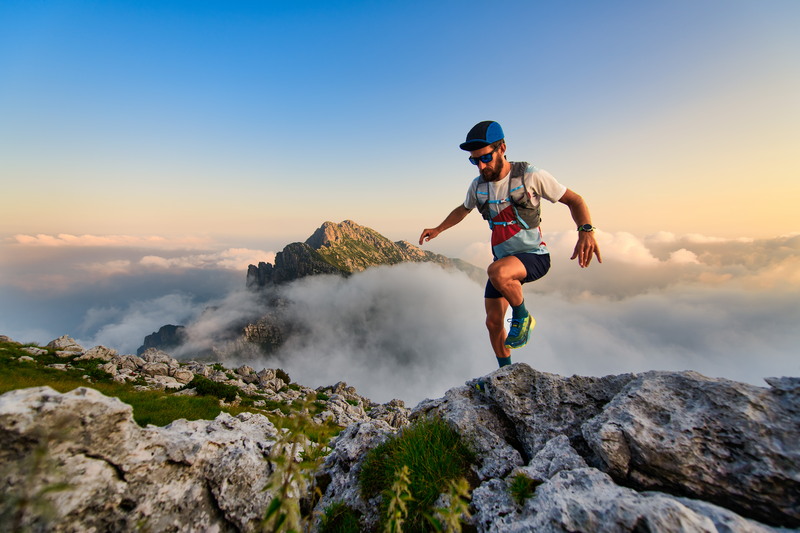
95% of researchers rate our articles as excellent or good
Learn more about the work of our research integrity team to safeguard the quality of each article we publish.
Find out more
EDITORIAL article
Front. Mater. , 08 June 2022
Sec. Mechanics of Materials
Volume 9 - 2022 | https://doi.org/10.3389/fmats.2022.945532
This article is part of the Research Topic Design and fabrication tools for advanced materials: applications in biomechanics and mechanobiology View all 6 articles
Editorial on the Research Topic
Design and Fabrication Tools for Advanced Materials: Applications in Biomechanics and Mechanobiology
The demanding requirements for new materials and structures in engineering, medicine, and robotics have spurred scientists to find novel strategies to develop advanced materials able to meet challenging goals such as adaptability, responsiveness, and multifunctionality. In analogy with biological materials, these characteristics could be introduced into synthetic systems by a fine-tuning of composition, structure, and material properties over multiple length scales. New additive manufacturing technologies are allowing the fabrication of functional components with peculiar internal architectures and material properties that are able to rearrange when triggered by external stimuli (i.e., responsive materials). The combination of new manufacturing routes, with artificial intelligence tools and mechanobiological concepts, can have disruptive results in terms of generating new responsive or adaptive materials, as well as optimizing existing mechanical systems in a large number of fields, also contributing to widely expand the design space.
A first review paper, written by Sharabi, provides an overview of the structural mechanisms occurring in soft fibrous tissues and how such mechanisms are connected to the structures of the tissues. The review aims to bridge the literature gap in soft tissues, whose structures are not gaining the same attention as the natural hard tissues. In particular, the paper identifies the different structural motifs common to collagenous tissues (e.g., tendons, ligaments, skin, blood) that contribute to their unique mechanical behavior at large deformations. While describing their complex hierarchical structure, the paper discusses the biomimetic challenges for developing synthetic analogs in order to use them as replacements in spite of autologous tissues. In particular, the author describes engineered soft composite applications that leverage structural motifs in order to mimic the structural and mechanical behavior of soft fibrous tissues, and shows new methodologies and materials that use biomimetic principles as a guide. The paper offers a dual point of view in the study of these soft materials, both for a better understanding of such tissues and the development of their tissue-mimic, via reverse biomimetics, and for development of novel bio-inspired tailor-made soft composites for various applications.
A second paper by Chiang et al., deals with the dicothomy between the emerging demand for high-efficient modeling tools for materials design and the need of high-accurate models, able to capture the mechanical properties and the fracture mechanisms. Although computationally intensive, lattice spring models, a coarse-grained particle spring networks, represent a powerful and effective tool to get insights into the fracture mechanism, and its use is limited for studies requiring a large design space. The authors implement a GPU-accelerated compute unified device architecture C++ code (CuLSM) that, along with image-to-particle conversion tool (Img2Particle), yields a rapid and versatile platform to characterize the elastic and fracture behaviors of materials, accelerating the computer-aided design to additive manufacturing design process. With the increasing demand for novel lightweight, smart and multi-functional materials and structures, such tailored and optimized modeling platform can have profound impacts on materials design, improving the quality control for 3D-printing via digital twin, enabling one to explore a vast design space and generating larger datasets for image-based generative machine learning models.
Within the framework of the artificial intelligence and material design, the work of Yang and Buehler focuses on neural networks as a possible route to design architected materials. The authors demonstrate that transformer neural networks, which are traditionally used in natural language processing, can be used to convert a descriptive text into a 3D printed material. This “word-to-matter” translation is a multistep process in which text is first converted into an image, essentially by integrating iterative algorithms to generate, score and classify images. The resulting text-based image is often quite complex and needs to be processed and simplified to be printable with standard additive manufacturing techniques such as fused deposition modeling and stereolithography. In parallel, the authors characterize the mechanical behavior of the virtual specimens by computer simulations to illustrate how words can be converted into a material with a tailored mechanical response. This pioneering work has the potential to become a standard approach in next-generation manufacturing, in which text or voice instructions can be used to generate tailored and optimized 3D printed objects for a large variety of applications.
Finally, considering functional and responsive materials such as scaffolds for tissue engineering, a possible approach to improve material design is the time-lapsed monitoring of material performance through advanced imaging combined with the application of external stimulation. This is particularly relevant when considering scaffolds for bone replacements, as demonstrated by the work of Shädli et al.. Firstly, the authors functionalize polymer nanocomposite scaffolds with barium titanate, which has attractive osteoinductive properties. Scaffolds having different barium titanate to hydroxyapatite ratios are seeded with cells, and their biological performance in terms of extracellular matrix formation and mineralization are monitored over time with micro-computed tomography, combined with advanced image processing. The additional role of external mechanical stimulation on scaffold performance is assessed by culturing cells upon cyclic loads in bioreactors. This work demonstrates the possibility to optimize mechanically-responsive scaffolds through time-lapsed monitoring and external physical stimulation, and it may help to overcome current limitations of in vitro bone regeneration.
In our Research Topic, we have given the opportunity to deliver the most recent progresses for developing advanced materials for the biomechanics and mechanobiology fields. Among the future challenges, we believe that a relevant application concerns the development of new methodologies to develop adaptive materials, i.e., materials able to react to internal and external stimulations in analogy with natural tissues and materials such as bone. In view of this, the synergistic employment of additive manufacturing technologies and artificial intelligence approach may widen the design palette, giving to scientists and companies the opportunity to deliver products especially for, but not limited to, the bioengineering field with optimized features and geometries non-achievable with traditional methodologies.
All authors listed have made a substantial, direct, and intellectual contribution to the work and approved it for publication.
The authors declare that the research was conducted in the absence of any commercial or financial relationships that could be construed as a potential conflict of interest.
All claims expressed in this article are solely those of the authors and do not necessarily represent those of their affiliated organizations, or those of the publisher, the editors and the reviewers. Any product that may be evaluated in this article, or claim that may be made by its manufacturer, is not guaranteed or endorsed by the publisher.
Keywords: advanced manufacturing, artificial intelligence, smart systems, modeling, biomechanics
Citation: Libonati F, Milazzo M and Ruffoni D (2022) Editorial: Design and Fabrication Tools for Advanced Materials: Applications in Biomechanics and Mechanobiology. Front. Mater. 9:945532. doi: 10.3389/fmats.2022.945532
Received: 16 May 2022; Accepted: 20 May 2022;
Published: 08 June 2022.
Edited and reviewed by:
Nicola Maria Pugno, University of Trento, ItalyCopyright © 2022 Libonati, Milazzo and Ruffoni. This is an open-access article distributed under the terms of the Creative Commons Attribution License (CC BY). The use, distribution or reproduction in other forums is permitted, provided the original author(s) and the copyright owner(s) are credited and that the original publication in this journal is cited, in accordance with accepted academic practice. No use, distribution or reproduction is permitted which does not comply with these terms.
*Correspondence: Flavia Libonati, ZmxhdmlhLmxpYm9uYXRpQHVuaWdlLml0; Mario Milazzo, bWlsYXp6b0BtaXQuZWR1; Davide Ruffoni, ZHJ1ZmZvbmlAdWxpZWdlLmJl
†These authors have contributed equally to this work
Disclaimer: All claims expressed in this article are solely those of the authors and do not necessarily represent those of their affiliated organizations, or those of the publisher, the editors and the reviewers. Any product that may be evaluated in this article or claim that may be made by its manufacturer is not guaranteed or endorsed by the publisher.
Research integrity at Frontiers
Learn more about the work of our research integrity team to safeguard the quality of each article we publish.