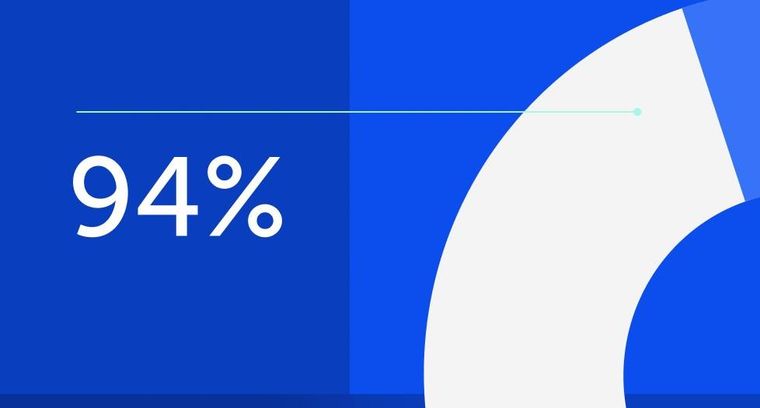
94% of researchers rate our articles as excellent or good
Learn more about the work of our research integrity team to safeguard the quality of each article we publish.
Find out more
REVIEW article
Front. Mater., 10 August 2022
Sec. Smart Materials
Volume 9 - 2022 | https://doi.org/10.3389/fmats.2022.907858
This article is part of the Research TopicEnergy Harvesting by Smart MaterialsView all 4 articles
Energy harvesting and thermal management in spacecraft refer to the adjustment, distribution, and comprehensive use of uniform adjustment, allocation, and integrated use of the spacecraft and subsystems, which have the advantages of reducing energy consumption and improving the overall performance of the spacecraft. The study is first briefly elaborated on the research progress of energy harvesting and thermal management, and then introduces the key thermal control technology of thermal management, mainly thermal bus systems, heat pump technology, and passive thermal control technology. Finally, the future development direction and research focus of thermal management are proposed, which lays a foundation for the future development of energy harvesting and thermal management technology.
Energy harvesting and thermal management in spacecraft refer to the unified adjustment, allocation, and comprehensive use of the thermal environment and the thermal behavior of subsystems related to spacecraft, and the collection, conversion, and discharge of heat, so as to improve the comprehensive utilization of heat, reduce energy consumption, reduce costs, and improve the overall performance of the spacecraft (Herrmann and Tleimat, 1994; Bartsev, 1997).
The energy balance of the spacecraft in space is mainly achieved through the use of solar energy. Solar panels absorb the solar energy, converting it into electricity and supplying it to subsystems on the spacecraft. Solar cells were first used in aerospace in 1958 on the PIONEER 1 satellite. For the operation of spacecraft, in addition to the supply of energy, energy distribution and recovery are equally important. The main task of the spacecraft thermal control subsystem is to ensure the working temperature of each component on the spacecraft, which is generally divided into active thermal control technology and passive thermal control technology. The active thermal control technology is to raise or maintain the temperature of equipment through an automatic control system, which requires energy consumption. The passive thermal control technology is to change thermal resistance through heat conduction and heat insulation measures to control heat transfer or discharge to cold and black space. Different components or devices have different requirements for heat. For example, electronic devices need to dissipate heat and optical components need to be heated. Therefore, for spacecraft, energy recovery and utilization can improve the comprehensive utilization rate of energy. For general spacecraft, especially small spacecraft, because of the energy consumption, small size, the cost of heat recovery, and reuse is too high, the application is more local through high thermal conductivity materials to achieve homogenization to improve the efficiency of energy. For large spacecraft, such as the space station, due to the large energy consumption and size, heat recovery and utilization can significantly improve the overall utilization of energy and improve overall performance.
The concept of thermal management was proposed by the United States in 1979 for the manned space station. Since then, various countries have carried out theoretical and experimental studies for various large spacecraft and space stations, mainly including the International Space Station (Merhoff et al., 1993; Cannon and Winters, 1995), Space Station Freedom (Bellmore, 1993), Hermes Space Shuttle (Ferro and Costamagna, 1988), and Project Moonbas (Ewert et al., 1996; Woo, 2012). In addition, the Mcdonnell Aviation Company applied heat pipes to the aviation field and successfully developed an aircraft waste energy recovery management system, which achieved good results (Herring and Collins, 1990). Therefore, thermal management technology can be used not only for large multi-module space stations but also for single-module space stations, space stations and spacecraft docking complexes, and aviation systems. It is of great research significance to simplify the system, improve the overall performance of the space station, and reduce energy consumption (Guo et al., 2001).
Energy harvesting and thermal management should first establish a thermo-fluid model, as shown in Figure 1. Based on this, the corresponding thermal control design should be carried out, not only to control the temperature of different requirements but also to consider energy harvesting and comprehensive utilization of various heat. Therefore, thermal control technology is the core of thermal management research. For example, heat collected by the fluid circuit is applied to the low-heating propellant chamber to reduce the electrical heating power required to maintain the temperature of the equipment in the chamber. On the other hand, the heat load of the radiator can be reduced, and the size and weight of the radiator reduced.
The function of the thermal bus is to connect the heating equipment in each cabin organically through heat exchangers, cold plates, and other forms to form the trunk circuit so that waste heat can be transferred to the central radiating radiator and discharged into space through the heat transfer medium in the thermal bus (Edelstein and Brown, 1984), as shown in Figure 2. The heat transfer characteristic of the fluid circuit is the collection of scattered heat. Compared with the radiation heat transfer, the heat transfer capacity is stronger and the temperature control accuracy is higher, which can realize the long-distance transmission of heat (Khrustalev and Faghri, 1995). For example, the Russian module of the International Space Station designed in 1994 uses a two-phase thermal transmission system as a thermal common loop with a maximum capacity of 30 kW and a transmission distance of 50 m (Ferro and Costamagna, 1988; Bellmore, 1993). Two single-phase ammonia loops driven by pumps are used in Liberty Space Station as common thermal loops to achieve thermal management of each cabin (Ferro and Costamagna, 1988). The thermal bus is not only suitable for the large multi-module space station but also suitable for manned spacecraft and lunar bases.
The loop system used by the thermal bus is divided into a single-phase loop and a dual-phase loop. The working medium is the key point of the thermal common loop. The thermal loop inside the cabin, especially the manned module, generally uses water as the medium, and the thermal loop outside the cabin generally uses ammonia as the medium.
The applications of MPSL in aerospace include the “Gemini” spacecraft of the United States, the “Skylab,” the “Soyuz” spacecraft of the former Soviet Union, the International Space Station, and the Tiangong Station. In the International Space Station, two MPSLs using water as the medium are used in the American cabins. The two loops work at different temperatures. One works at 4°C for heat transmission of the survival system and the other works at 17°C for heat transmission of electrical devices. Two single-phase loops are also used in the Mars Exploration Rover (MER), and the maximum heat transport capability of 2150 W is achieved. As a mature technology, the MPSL is also used in Tiangong Station. Compared with the International Space Station, Tiangong Station solved the problem that heat transmission cannot be realized between different modules for thermal loops with different mediums.
With the increase of thermal load, the two-phase fluid circuit technology has become the main research direction of thermal control technology.
MPTL takes the pump as the driving element and the precise temperature control liquid storage device as the temperature control element. The closed-loop temperature control technology absorbs the heat of the heating element in the evaporation section and releases the heat in the condensing section. The technology is suitable for the thermal control system with high load and high precision, and multiple heat sources or complex distributed heat sources.
Currently, there are few applications of the MPTL technology in the aerospace field. The internal tracker of the Alpha Magnetic Spectrometer (AMS-02) on the International Space Station uses pump-driven two-phase fluid loop calculation using CO2 as a working medium for the thermal control system (TTCS) (Jie et al., 2008; Zhang et al., 2011). The main principle of the TTCS is that its evaporator is composed of four rings of thin tubes, all of which are directly connected with the thin tubes through the electronic circuit board through the copper thermal conductivity bridge. After the heat is absorbed by the evaporation of the liquid in the tube, it is carried to the condenser by steam, and finally, the heat is discharged to the space by the heat radiator. After cooling and condensing, the steam becomes a supercooled liquid, which is pumped back to the evaporator, and so on.
The selection of a working medium for the pumped two-phase fluid circuit is an important research direction. NLR, a Dutch company, carried out an MPTL test and simulation analysis study based on the CO2 working medium (Jie et al., 2008; Huang et al., 2009). The experiment showed that using CO2 as a circulating working medium greatly reduced the temperature gradient in the evaporation section, reduced the design size of the system, and improved the stability and reliability of operation. In addition, ammonia has better performance than CO2 in many aspects, such as higher critical temperature, lower freezing point, and lower vapor pressure. However, ammonia is toxic and smelly, and the high volume ratio of steam to liquid brings great flow resistance and uneven and unstable temperature during evaporation heat transfer, which requires further specific analysis.
CPL is a high heat transfer device with high reliability. CPL is mainly composed of a liquid reservoir, a parallel evaporator (heat source), and a condenser (cold source). The heat source and cold source are connected by a steam or liquid pipeline. The main working principle includes three steps: steam through the steam pipe into the condenser, condensing heat in the condenser, and condensing liquid back to the evaporator through the liquid pipe, and in this form in the loop of the reciprocating cycle, the power of the cycle comes from the capillary suction generated by the capillary structure in the evaporator.
CPL conducted numerous ground tests and numerous space flight tests in the 1980s and 1990s. In 1999, the CPL was successfully applied for the first time on NASA’s Earth Observing System TERRA (McIntosh et al., 1998). A total of six CPLS were used for thermal control of each of the three instruments on TERRA, allowing each instrument to be placed in the most favorable viewing position regardless of temperature. Another example of CPL application is on the refrigerator of the Hubble Space Telescope (Ku et al., 2004), which achieves refrigerator’s cooling capacity of 8 W and needs to dissipate 300–400 W of heat.
So far, the CPL has not been widely used in spacecraft, especially in high-power spacecraft, but more LHP technology is introduced in the following chapter.
The principle of LHP and CPL is basically the same; the biggest difference is that the evaporator and compensator of LHP are connected together, and there is no separate reservoir.
LHP is mainly used in the thermal control of spacecraft and heat transfer elements of the expandable radiator. In 1994, Obzor launched by Russia for the first time applied three LHPs to thermal control optical instruments with the working medium of propylene and ammonia (Goncharov et al., 1995). In 1999, HPL was first applied to an expanded radiator in Hughes HS702 in the United States. In 2004, LHP was used for the thermal control of Bat devices on Swift launched by the United States (Choi, 2004). In 2014, China’s Chang‘e-5 built a new thermal control system for small re-entry and return spacecraft based on an LHP “thermal switch” for thermal control of IMU equipment (Ning et al., 2015; Ning et al., 2017). In 2013, Chang ‘e-3 attempted isotope binding two-phase fluid loop technology for the first time in the global space field (Liu et al., 2014; Xiang et al., 2015). The main working principle is that during the moonlight night, the pressure difference between the liquid side and the steam side is formed to drive the circulating flow of the working medium, and the heat energy of the isotope heat source is transferred to the roof of the rover to provide heat for the equipment insulation. During the day and moon, the two-phase fluid circuit stops working, and the heat energy of the isotope heat source is dissipated to outer space by means of radiative heat dissipation.
At present, LHP technology is widely used in spacecraft thermal control systems at home and abroad, and LHP technology has become a hot topic in spacecraft thermal control systems.
Generally speaking, the heat reuse approach of space systems is to use a phase change medium to recycle the heat of spacecraft from heat source to cold source so as to improve energy utilization efficiency and reduce energy consumption demand. At present, heat is utilized mainly through the aforementioned fluid loop technology (air and liquid) or heat pipe technology to achieve.
In addition to the fluid loop technology and heat pipe technology, the phase change heat exchange technology is also used for heat reuse as a mature technology.
The phase change temperature control technology developed from phase change energy storage technology as a new thermal control technology, with high reliability, lightweight, no energy consumption, and other advantages. Phase change materials can be divided into solid–solid, solid–liquid, gas–liquid, and gas–solid phase change materials according to the form of phase change. Currently, solid–liquid phase change materials are widely used in the thermal control design of spacecraft, which can be effectively used for heat recovery and dissipation of spacecraft electronic equipment.
The principle of phase change temperature control technology of spacecraft shows that when the spacecraft enters into the sunny area or the internal heat source starts to work, the phase change material absorbs heat, heats up, and melts. When the spacecraft enters the shadow area or the internal heat source stops working, the phase change material releases heat, cools, and condenses. Therefore, the temperature of the spacecraft in the orbit will be guaranteed, reducing the influence of external heat flow and internal heat source on the spacecraft.
In 1976, a dual-phase change system using methyl ethyl ketone and n-heptane as phase change materials was applied for the first time in aerospace electronic equipment (Keville, 1977), which verified the reliability of the phase change temperature control technology. Since then, the phase change temperature control technology has been gradually applied in space systems. Three phases of the phase change temperature control (PCM) technology were used on the U.S. Apollo Lunar Rover. During each walk, PCM materials absorbed the heat generated by each working part of the rover. After the walking task, heat dissipation is carried out by opening the blinds on the radiator or removing the heat insulation plate, and the phase change material is cooled and solidified again, which is ready for the next task (Biswas, 1977). The successful application of the phase change temperature control technology in the field of temperature control makes a large number of scholars research phase change temperature control technology. Gaofen-6 satellite combines phase change material with aluminum alloy radiator, encapsulates n340 hexadecane phase in aluminum alloy box through good structure, and dissipates electronic heat through the outer surface of aluminum box. Through this measure, the electronic heat is recovered by phase change material and then discharged, which significantly reduces the size and weight of the radiator, and also reduces the power consumption of the electric heating.
The main difficulty in the thermal control design of the LEO large planar space-based radar antenna is how to keep its temperature in the shadow area. The antenna structure plate made of carbon fiber/epoxy resin composite was filled with carbon foam containing phase change material (melting point of 3°C, latent heat of 240 kJ/kg). Foamed carbon can not only enhance the thermal conductivity of the phase change material but also ensure the structural strength of the antenna. After using the phase change material, the temperature fluctuation of the antenna drops from 80−120° C to 20−30°C. In addition, the use of phase change temperature control technology can effectively reduce weight. Fixler conducted a comparative study on the phase change material device and other heat dissipation methods. From the mass index per unit area: for OGO (Orbiting Geophysical Observatory) spacecraft, eicosane is used. The phase change material is 0.840 kg/m2, the shutter is 2.9 kg/m2, and the fluid loop circulation system is 2.442 kg/m2.
The heat pipe has the advantages of high thermal conductivity and high reliability, and is fully suitable for space microgravity environments. In 1968, the American GEOS-II satellite adopted heat pipe technology for the first time (Harkness, 1969). Since then, heat pipe technology has been widely used in the spacecraft.
The thermal control system of Chang’e-1 probe realized the thermal coupling between + Y and -Y decks in the lower chamber using the heat pipe (Zijun and Canghai, 2008; Shao, 2008); that is, three axial heat pipes are externally attached to the outside of the battery mounting plate, and the externally attached heat pipes and the embedded heat pipes in the deck form a heat pipe network, forming + Y-board -Y The strong thermal coupling between plates and the temperature difference between battery groups require Shenzhou-7 to adopt 30 channel heat pipes to conduct isothermal design on the wall of the re-entry capsule (Bingqing and Wei, 2009). HJ-1C Satellite adopts 24 heat pipes embedded in the mounting plate to achieve isotherm (Huitao, 2009).
Heat pipe with variable heat transfer coefficient can control the working temperature of heat pipe by changing the length of condensing section. MAROTS Satellite adopts radiators composed of heat pipes with variable heat transfer coefficients to achieve the temperature requirements of amplifier temperature of 30 ∼ 40° C and temperature difference between amplifiers less than 5°C (Savage et al., 1979). The lander of Chang’e-3 uses 14 heat pipes with variable heat transfer coefficients to achieve the thermal control of instruments and equipment in the module in the Earth–Moon transfer phase, circumlunar phase, lunar day phase, and lunar night phase (Liu et al., 2014).
The heat pipe technology realizes the isothermal design of the space system, saves energy, improves the energy utilization efficiency of the system, and becomes an indispensable technology for thermal control systems.
The heat pump is a device that transfers heat from the heat source to the heat sink. It consists of an evaporator, compressor, condenser, throttling element, and other components, as shown in Figure 3. It is a pump-driven single-phase/two-phase fluid loop. According to the working principle of a heat pump, it can be generally divided into steam compression type, absorption type, thermoelectric type, and other forms. The steam compression heat pump has the advantages of stable system operation, simple component structure, and high system operation efficiency, and is widely used at present.
Heat pump technology is mainly suitable for heat dissipation in ultrahigh power loads and high-temperature environments. By increasing the radiation temperature of the radiator, the area of the radiator required under the same heat dissipation is greatly reduced. The temperature level of each component of the thermal control system based on the heat pump technology is shown in Figure 4. In the thermal control system, in the space radiator, quality accounts for more than 50% of the whole system quality (Wang et al., 2005), heat the radiator based on heat radiation way to discharge at the same time, and the direct ratio with the temperature of heat released is four; therefore, improving the work of the radiator temperature can significantly reduce the area of the radiator and quality, and improve the efficiency of radiator emissions. Through calculation and comparison, it is found that the higher the heat consumption is, the more obvious the advantage of the heat pump technology is. When the heat consumption reaches 10KW, the heat pump technology can reduce the quality of the thermal control system by 27%, and when the heat consumption reaches 100KW, the heat pump can reduce the quality of the thermal control system by 39% (Dexter and Haskin, 1984).
FIGURE 4. Temperature level of each component of the thermal control system under heat pump technology.
Heat pump technology improves the emission efficiency of the radiation radiator, reduces waste heat emission, makes the heat energy use more reasonable, and improves the performance of the whole system.
To improve the efficiency of energy use and recovery, the thermal conductivity of materials should be improved as much as possible in the thermal control measures of various spacecraft equipment. Since 1990s, related research on carbon fiber and its composite materials has been carried out.
In the past 30 years, the thermal conductivity of high-modulus carbon fibers developed can reach 640 ⋅W/(m ⋅K), while the thermal conductivity of Thornel p-130x carbon fibers is 3 times that of copper (up to 1,180 ⋅W/(m ⋅K)), and the proportion is only 1/4 that of copper. The thermal conductivity of the composite material can reach 400 ⋅W/(m ⋅K), and the weight of the carbon fiber material can be reduced by 2/3. The thermal conductivity of carbon fiber K1100 can reach 1,100 ⋅W/(m ⋅K), and the specific gravity is 1/4 of copper, which is suitable for use as a heat diffuser. In addition, C-C composite materials can be used in space telemetry instruments and can be widely used in the cooling plate of satellite electronic devices. Since 2009, C-C composite material has been used in the 2009 Tianhui-I satellite to reduce the temperature difference caused by the heat flow outside the orbit to the star sensor (Liu, 2012). In 2018, C-C composite material has also been used in gaofen-6 satellite to improve the heat dissipation efficiency of the radiator in cold black space. Graphene aluminum matrix composites and graphene laminates were used on Gaofen-XX and an experimental satellite to improve heat transfer efficiency.
The application of high thermal conductivity materials on spacecraft improves the efficiency of heat dissipation, reduces the thermal resistance of the contact surface, and realizes the energy distribution design of the spacecraft.
In the vacuum environment of space, the surface temperature of an object largely depends on the solar absorption ratio and infrared emissivity of its surface. Currently, there are two kinds of thermal control coatings widely used: one is low absorption and emissivity thermal control coating, and the other is high absorption and emissivity thermal control coating. The thermal control coating with low absorption and high emission is the most widely used. The main parameters of some coatings are shown in Table 1.
In recent years, some new types of coating were studied, such as thermochromic intelligent thermal coating and electrochromic intelligent coating (Tachikawa et al., 2003; Douglas et al., 2002). Thermochromic intelligent thermal coating is the most ideal, namely, the emissivity of the coating with temperature change and automatically change, such as the temperature rises, the emission rate increase, or absorptance is reduced, to adjust the temperature automatically. LMO and VO2 thermochromic variable emissivity materials are widely studied at home and abroad. The hemispherical emissivity of the infrared band can greatly change with the change in the surface temperature of the substrate. It is found that when the surface temperature of the body changes from 150 K to 390 K, the emissivity increases from 0.2 to 0.65. However, the current thermochromic coating requires too much temperature change, and its application is too narrow.
The principle of the electrochromic intelligent coating is to change the inversion of the chemical components of the material under the action of the external electric field, which causes the emission characteristics of the material to be reversibly changed. Electrochromic coating of Ashwin-Ushas was fly-tested on NASA’s ST-5 satellite in 2006. In 2007, Eclipse Energy Systems developed a 5-layer electrochromic thin-film device and carried out an onboard flight test on the MidStar satellite, successfully verifying in-orbit performance (Douglas et al., 2002). The thin-film device has higher spatial stability and a wide infrared operating band. The average emissivity can vary from 0.06 to 0.77 when the color state changes to the bleaching state. WO3 electrochromic films have also been developed in China in recent years.
By changing the thermal radiation characteristics of the electrochromic coating, the energy dissipation of the spacecraft in the shadow region can be reduced, the electric heating load to maintain the temperature of the spacecraft can be reduced, the heat dissipation efficiency of the radiator to the cold black space can be improved, and the comprehensive performance of the spacecraft can be improved.
Intelligent thermal control devices refer to the self-regulation of emissivity through driving signals or their own physical and chemical properties, such as microthermal control shutters, microthermal switches, and intelligent repeatable expander radiators.
1) Micro Louver
Micro Louver is an electrically driven device that controls the overall emissivity by controlling the low emissivity blade to block the high emissivity heat dissipation meter, thus controlling the temperature of the spacecraft. St-5 satellite launched by NASA uses miniature thermal control shutters, whose emissivity varies from 0.3 to 0.6. In-orbit operation experiments show that no abnormality has been observed for 3 months, and the cycle life can reach 10,000–50,000 times (Osiander et al., 2004). In 2011, scholars developed a new “sandwich” micro-shutter structure with effective emissivity ranging from 0.36 to 0.79 (Shengzhu et al., 2011).
2) Micro Heat Switch
The microthermal switch has the ability to adjust the heat dissipation rate of the device by adapting to the external ambient temperature, and the temperature of each internal component can be individually controlled by selecting the appropriate heat exchange working temperature (Swanson and Birur, 2003). The American “Mars Rover” has adopted paraffin wax miniature heat switches, which can achieve a 30-fold change in thermal conductivity, up to 0.4 W/K, depending on the volume expansion during paraffin melting (Fan, 2007). In addition, the common microthermal switches include non-uniform expansion thermal switches, adjustable thermal layer switches, and electric wetting medium switches.
3) Electrostatic Switch Radiator
The electrostatic switch radiator controls the gap between the high emissivity thin-film surface and the low emissivity substrate surface through electrostatic force in vacuum, and then adjusts the emissivity change (Moghaddam et al., 2007). NASA conducted flight experiments on electrostatic switched radiators, and the results showed that the difference between the maximum and minimum emissivity was as high as 0.7 (Biter et al., 2002; Biter and Oh, 2007). Hyun (Kim et al., 2017) designed a miniature electric bead electrostatic switch radiator. By changing the direction of the electric field, the electric bead was moved to change the emissivity of the radiator, whose emissivity varied from 0.33 to 0.65.
4) Variable Emissivity Radiator
Nagano (Nagano et al., 2006) developed a lightweight intelligent radiator, which is equipped with an environment adaptive capacity and a memory reversible radiator plate. The vacuum thermal performance test and vibration test were carried out on the intelligent repeatedly expanded radiator, and the results showed that the radiator plate could be repeatedly expanded from 0 to 140° within the temperature range of -30–30°C. The independent thermal control ability of the intelligent radiator changes with the change of power. Although the vibration test results caused slight damage to the device, they did not affect the structural integrity of the thermal control system (Hosei et al., 2009).
1) Pulsating Heat Pipe
The pulsating heat pipe is to inject working fluid into the curved capillary after vacuuming, and the working fluid exists in the tube in the form of a liquid plug and gas plug. When one end is heated and the other condenses, the liquid and gas plugs oscillate randomly under the pressure difference, thus transferring heat from the heating end to the condensing end (Mameli et al., 2014). According to the direction of the pipeline, pulsating heat pipes are divided into three types: loop type, open type, and loop type with a control valve (Han et al., 2016).
Pulsating heat pipes without small volume, simple structure, and good heat transfer performance (Zhang and Faghri, 2003; Brent et al., 2012), after studying the properties of the test, show that the pulsating heat pipe under microgravity is better than that under normal gravity, and the characteristics of supergravity can be used for long-term microgravity environment; thermal control equipment can be used for space (Gu et al., 2004), and in thermal control of space, electronic equipment has extensive application prospect.
2) Micro Heat Pipe
Micro heat pipes are usually used for heat dissipation of components with high heat flux (Vasiliev, 2008). Flow types are classified according to hydraulic diameter Dh, 50 um < Dh ≤ 600 um is the microchannel flow, 600 um < Dh ≤ 3 mm is the small channel flow, and Dh > 3 mm is the conventional channel flow (Ren et al., 2016; Chen et al., 2006).
The micro channel has the advantages of a high heat transfer coefficient and large heat transfer area per unit flow volume. The Chinese Academy of Space Technology has studied the heat transfer capacity of the micro heat pipe. The results show that the maximum heat transfer capacity of the micro heat pipe with diameter of φ3 mm can reach 3.2 W/m at 20°C, and the heat transfer coefficient of evaporation and condensation can reach
Spacecraft all adopt multilayer insulation materials to reduce the influence of space heat flux and heat dissipation to cold black space (Thome, 2004). Multilayer insulation material can be divided into a low temperature, medium temperature, high-temperature, multilayer, usually composed of double-sided low emissivity reflection screen and several units of low thermal conductivity spacers, has excellent thermal insulation performance under vacuum conditions, simple structure, lightweight, and is the most commonly used thermal control technology of spacecraft. The heat transfer performance of multilayer insulation materials has been analyzed in detail by scholars (Adelberg Black et al., 1960;, 1967; Cunnington and Tien, 1970; Tien and Cunnington, 1973), as shown in Table 2.
Several new multilayer insulation modules are also being used in orbit. A new type of polyurethane foam insulation material and variable density multilayer insulation material have been developed in China. Compared with traditional materials, the heat insulation capacity can be increased by 50 at low temperatures, and by more than 18 compared with ordinary multilayer heat insulation materials, which can prolong the low-temperature rocket’s in-orbit time to 30 days. The combined application of high thermal conductivity C-C composite materials and multilayer insulation materials has also been studied in China to further reduce the influence of heat flow outside orbit on the local spacecraft. The enhanced MLI scheme for space debris protection is also studied abroad. The main measures to enhance MLI debris protection are as follows: increasing the number of layers of multilayer insulation components, inserting reinforcement materials at different locations in the multilayer insulation assembly, and separating the multilayer insulation assembly from the mounting surface by spacing strips. The enhanced MLI was successfully deployed on RadarSAT.
Latent heat energy storage has been developed into the most potential energy storage method because the phase change materials have the advantages of approximately isothermal and absorbing or releasing a lot of latent heat during the phase change process. Phase change temperature control technology developed from phase change energy storage technology as a new thermal control technology, with high reliability, lightweight, no energy consumption, and other advantages.
Chang’e-1 satellite combines phase change material with a heat pipe to conduct a thermal control design for the CCD stereo camera. The configuration of the heat pipe with the phase change material is shown in Figure 5. Liquid ammonia is filled in the middle circular cavity, and two cavities filled with n-dodecane are inserted at both ends of the heat pipe. The heat pipe with the phase change material improves the thermal environment of the CCD stereo camera and solves the problem of temperature fluctuation when the element directs the heat to the heat dissipation surface through the heat pipe. Rover used paraffin phase change material to control and drive the thermal switch, and Rover used phase change material n-dodecane to control the temperature of the battery, eliminating the influence of environmental temperature fluctuations on the stability of the system (Birur et al., 2000).
Due to conventional phase change materials thermal conductivity is low, the difference of solid–liquid change expansion ratio, leakage rate, and other factors, in addition to the mix proportion of nanoscale metal or metal oxide particle research, research of new phase change materials has gradually become the research emphasis of phase change temperature control technology, such as the microcapsule of phase change materials and high porosity foam metal materials (Schossig et al., 2005; Hui-Bin et al., 2007). Microencapsulated phase change materials refer to the use of film-forming materials to wrap solid, liquid, or gas into tiny particles. The latent heat of the phase change material in the microcapsule increases the heat storage of the composite material significantly and improves the heat storage function. NASA in the United States uses microencapsulated phase change materials in spinning, made with temperature regulation function space suit. In addition, nano-capsule phase change materials can be added to the thermal control coating, which can play the role of heat insulation and temperature control. The high porosity foamed metal materials are mainly high porosity foamed metal materials, and the equivalent thermal conductivity of the composite phase change materials can be increased by eight times when the composite phase change materials are filled in.
This study briefly describes the research progress of thermal management, introduces the key thermal control technology and concrete realization method in thermal management, and focuses on the thermal bus, loop heat pipe technology, liquid double loop heat transfer technology, heat pipe technology, and new thermal control materials and their applications. Based on the development of spacecraft at home and abroad, several development directions of spacecraft thermal management are discussed.
1) Dynamic research on the thermal management system: The two main factors that determine the energy balance of spacecraft are the change in the external thermal radiation environment and the operation mode of the internal equipment. Most of the research on thermal management regards the operation of each piece of equipment as independent, and the external environment of spacecraft generally takes several typical environments, but the operation of spacecraft is a dynamic process. In the systematic design of spacecraft thermal management, the dynamic process of the whole system should be taken into account, and the restriction and joint relations of each dynamic process should be fully studied.
2) Research on new phase change materials and ultrahigh thermal conductivity materials: At present, the spacecraft thermal management system is mainly realized by the liquid loop. Through the application of new phase change materials and high thermal conductivity materials, the passive thermal control design is adopted to fully recover and utilize the heat of electronic equipment to achieve local heat balance, significantly reduce the energy demand of thermal control, reduce the complexity of active thermal control, and improve the reliability. In the case of small spacecraft, the same method can be used to maintain the temperature of the entire spacecraft through energy recovery through electronics.
3) Research on new thermal control coatings and multilayer insulation materials: The thermal radiation parameters of thermal control coating directly determine the energy exchange between spacecraft and the space environment. The application of intelligent thermal control coating can control the energy absorption, transfer, and dissipation of spacecraft from whole to part, and greatly improve the adaptability and comprehensive performance of spacecraft. Multilayer insulation materials have excellent performance in vacuum insulation, through the research and application of new multilayer insulation materials, to achieve high strength, energy absorption, and storage capacity.
The original contributions presented in the study are included in the article; further inquiries can be directed to the corresponding author.
FJ and SZ have contributed to the acquisition data, analysis data, and drafting of the article. These two authors have contributed equally to this work. LW and SY have contributed to the analysis data and interpretation of data. HG and JL have contributed to revising the article. All the authors have contributed to the final proofreading and approval of the version for publication.
The authors declare that the research was conducted in the absence of any commercial or financial relationships that could be construed as a potential conflict of interest.
All claims expressed in this article are solely those of the authors and do not necessarily represent those of their affiliated organizations, or those of the publisher, the editors, and the reviewers. Any product that may be evaluated in this article, or claim that may be made by its manufacturer, is not guaranteed or endorsed by the publisher.
Adelberg, M. (1967). Effective Thermal Conductivity and Multilayered Insulation. Reston, USA: Effective Thermal Conductivity and Multilayered Insulation.
Bartsev, S. I. (1997). Life Support System Power Supply Optimization. SAE Trans. 1997, 517–520. doi:10.4271/972299
Bellmore, P. (1993). Integrated Active Thermal Control System Analysis of Space Station Freedom Operational Scenarios. SAE Trans. 1993, 1247–1254. doi:10.4271/932200
Bingqing, H. J. F. Y. L., and Wei, L. (2009). Design and On-Orbit Performance Evaluation of Thermal Control System for Shenzhou-7 Spaceship. Chin. Space Sci. Technol. 29, 1.
Birur, G. C., Johnson, K. R. J. R., and Novak, K. S. (2000). Thermal Control of Mars Lander and Rover Batteries and Electronics Using Loop Heat Pipe and Phase Change Material Thermal Storage Technologies. SAE Trans. 109, 555–564. doi:10.4271/2000-01-2403
Biswas, D. P. (1977). Thermal Energy Storage Using Sodium Sulfate Decahydrate and Water. Sol. Energy 19, 99. doi:10.1016/0038-092X(77)90094-9
Biter, W., Oh, S., and Hess, S. (2002). Electrostatic Switched Radiator for Space Based Thermal Control. AIP Conf. Proc. 608, 73. doi:10.1063/1.1449710
Biter, W., and Oh, S. (2007). Performance Results of the Esr from the Space Technology 5 Satellites. College Park, Maryland, USA: American Institute of Physics.
Black, I. A., Fowle, A. A., and Glaser, P. E. (1960). Development of High-Efficiency Insulation. Berlin, Germany: Springer.
Brent, S. T., Andrew, D. W., and Bruce, L. D. (2012). Review of Pulsating Heat Pipe Working Fluid Selection. J. Thermophys. Heat Transf. 26, 651.
Cannon, T. M., and Winters, B. A. (1995). International Space Station Alpha External Thermal Control System Overview. SAE Trans. 1995, 1077–1085. doi:10.4271/951649
Chen, L., Tian, Y. S., and Karayiannis, T. G. (2006). The Effect of Tube Diameter on Vertical Two-phase Flow Regimes in Small Tubes. Int. J. Heat Mass Transf. 49, 4220–4230. doi:10.1016/j.ijheatmasstransfer.2006.03.025
Choi, M. (2004). “Thermal Vacuum/balance Test Results of Swift Bat with Loop Heat Pipe Thermal System,” in 2nd International Energy Conversion Engineering Conference, 5683. doi:10.2514/6.2004-5683
Cunnington, G., and Tien, C. (1969). A Study of Heat-Transfer Processes in Multilayer Insulations. Thermophys. Appl. Therm. Des. Spacecr. doi:10.2514/6.1969-607
Dexter, P., and Haskin, W. (1984). “Analysis of Heat Pumped Augmented Systems for Spacecraft Thermal Control,” in 19th Thermophysics Conference, 1757. doi:10.2514/6.1984-1757
Douglas, D. M., Swanson, T., Osiander, R., Champion, J., Darrin, A. G., Biter, W., et al. (2002). Development of the Variable Emittance Thermal Suite for the Space Technology 5 Microsatellite. AIP Conf. Proc. 608, 204–210. doi:10.1063/1.1449726
Edelstein, F., and Brown, R. (1984). Conceptual Design of a Thermal Bus for Large Space Platforms. SAE Trans. 1984, 609–620. doi:10.4271/840975
Ewert, M. K., Keller, J. R., and Hughes, B. (1996). Conceptual Design of a Solar Powered Heat Pump for Lunar Base Thermal Control System. SAE Trans. 1996, 833–844. doi:10.4271/961535
Ferro, C., and Costamagna, L. (1988). Preliminary Design Concepts for the Active Thermal Control of a European Spaceplane. SAE Trans. 1988, 73–81. doi:10.4271/880924
Goncharov, K., Nikitkin, M., Golovin, O., Fershtater, Y. G., Maidanik, Y. F., and Piukov, S. (1995). Loop Heat Pipes in Thermal Control Systems for “Obzor” Spacecraft. Tech. Rep. SAE Technical Paper. doi:10.4271/951555
Gu, J., Kawaji, M., and Futamata, R. (2004). Effects of Gravity on the Performance of Pulsating Heat Pipes. J. Thermophys. Heat Transf. 18, 370–378. doi:10.2514/1.3067
Guo, Z., Liang, X., and Zhang, X. (2001). Thermal Management of Space Stations. Chin. Sci. Bull. 46, 2019–2024. doi:10.1007/bf02901921
Han, X., Wang, X., Zheng, H., Xu, X., and Chen, G. (2016). Review of the Development of Pulsating Heat Pipe for Heat Dissipation. Renew. Sustain. Energy Rev. 59, 692–709. doi:10.1016/j.rser.2015.12.350
Herring, R. L., and Collins, P. K. (1990). Aircraft Subsystem Waste Energy Recovery and Management. SAE Trans. 1990, 434–452. doi:10.4271/901218
Herrmann, C. C., and Tleimat, B. (1994). A Comparison of Power/weight/space Requirements for Water-Recycling Processors. SAE Trans. 103, 1508–1513. doi:10.4271/941538
Hosei, N., Akira, O., Ken, H., and Yuji, N. (2009). Experimental Investigation of a Passive Deployable/stowable Radiator. J. Spacecr. Rockets. doi:10.2514/1.30170
Huang, Z., He, Z., Mo, D., Sun, X., Lu, S., Xiao, W., et al. (2009). Coupling between an Accumulator and a Loop in a Mechanically Pumped Carbon Dioxide Two-phase Loop. Microgravity Sci. Technol. 21, 23–29. doi:10.1007/s12217-009-9147-3
Hui-Bin, Y., Xue-Nong, G., Jing, D., et al. (2007). Cooling Technology of Electronic Device Based on Phase-Change Material with Rapid Thermal Response. J. South China Univ. Technol. Nat. Sci. Ed. 35, 52–57.
Huitao, M. A. (2009). Thermal Design and Flight Validation for Hj-1a/1b. Reston, USA: Spacecraft Engineering.
Jie, L., Nian-Qiang, P., Kai-Hua, G., Zhen-Hui, H., and Ting-Xuen, L. (2008). Experimental Investigation on a Mechanically Pumped Two-phase Cooling Loop with Dual-Evaporator. Int. J. Refrig. 31, 1176–1182. doi:10.1016/j.ijrefrig.2008.02.014
Keville, J. (1977). “Development of Phase Change Systems and Flight Experience on an Operational Satellite,” in 11th Thermophysics Conference, 436.
Khrustalev, D., and Faghri, A. (1995). Heat Transfer in the Inverted Meniscus Type Evaporator at High Heat Fluxes. Int. J. Heat Mass Transf. 38, 3091–3101. doi:10.1016/0017-9310(95)00003-r
Kim, T., Han, S.-H., and Oh, H.-U. (2017). Design and Performance Evaluation of Mems-Based Spaceborne Variable Emissivity Radiator Using Movement of Electrified Beads. J. Microelectromech. Syst. 26, 113–119. doi:10.1109/jmems.2016.2616168
Ku, J., Ottenstein, L., Butler, C. D., Swanson, T., and Thies, D. (2004). Thermal Performance of Capillary Pumped Loops Onboard Terra Spacecraft. Tech. Rep. SAE Technical Paper. doi:10.4271/2004-01-2504
Liu, Z., Xiang, Y., Si, D., Zhang, Y., Chen, J., Su, S., et al. (2014). Design and Verification of Thermal Control System for Chang’e-3 Probe. Sci. Sin. Technol. 44, 353–360.
Mameli, M., Araneo, L., Filippeschi, S., Marelli, L., Testa, R., and Marengo, M. (2014). Thermal Response of a Closed Loop Pulsating Heat Pipe under a Varying Gravity Force. Int. J. Therm. Sci. 80, 11–22. doi:10.1016/j.ijthermalsci.2014.01.023
McIntosh, R., Kaylor, M., Buchko, M., Kroliczek, E., and Smith, R. (1998). A Capillary Pump Loop Cooling System for the NICMOS Instrument. Tech. Rep. SAE Technical Paper. doi:10.4271/981814
Merhoff, P., Dellinger, B., Taggart, S., and Cornwell, J. (1993). Space Station Freedom Resource Nodes Internal Thermal Control System. SAE Trans. 1993, 993–1011. doi:10.4271/932148
Moghaddam, S., Lawler, J., Currano, J., and Kim, J. (2007). A Space-Based Experiment to Evaluate Performance of Electrostatic Switched Radiator (Esr). Am. Inst. Phys. 880, 66–72. doi:10.1063/1.2437442
Nagano, H., Nagasaka, Y., and Ohnishi, A. (2006). Simple Deployable Radiator with Autonomous Thermal Control Function. J. Thermophys. Heat Transf. 20, 856. doi:10.2514/1.17988
Ning, X., Jiang, F., Zhang, D., Wang, Y., Chen, Y., Xue, S., et al. (2017). An Integrated Thermal Management Scheme for Lunar Robotic Sampling and Return Probe. Spacecr. Environ. Eng. 34, 598–603.
Ning, X., Su, S., Chen, Y., Miao, J., Zhang, D., Zheng, K., et al. (2015). Design and Implementation of Circumlunar Return and Reentry Spacecraft Thermal Control System. Sci. Sin. Technol. 45, 145–150. doi:10.1360/N092014-00475
Osiander, R., Firebaugh, S. L., Champion, J. L., Farrar, D., and GarrisonDarrin, M. A. (2004). Microelectromechanical Devices for Satellite Thermal Control. IEEE Sensors J. 4, 525–531. doi:10.1109/jsen.2004.830297
Ren, T., Zhang, G., Chen, X., and Ye, H. (2016). A Review of Small Heat Pipes for Electronics. Appl. Therm. Eng. Des. Process. Equip. Econ. 96, 1. doi:10.1016/j.applthermaleng.2015.11.048
Savage, C. J., Aalders, B. G. M., and Kreeb, H. (1979). A Variable-Conductance Heat Pipe Radiator for Marots-type Communication Spacecraft. J. Spacecr. Rockets 16, 176–180. doi:10.2514/3.57639
Schossig, P., Henning, H., Gschwander, S., and Haussmann, T. (2005). Micro-encapsulated Phase-Change Materials Integrated into Construction Materials. Sol. Energy Mater. Sol. Cells 89, 297–306. doi:10.1016/j.solmat.2005.01.017
Shao, X. (2008). Heat Pipe Applications and Test in Chang’e-1 Satellite.Reston, USA: Spacecraft Engineering.
Shengzhu, C., Xuekang, C., Gan, W., Jianping, Y., Rui, W., Lanxi, W., et al. (2011). Study on Design and Fabrication of Micro Thermal Control Louvers. Rare Metal Mater. Eng. 40, 249–251.
Swanson, T. D., and Birur, G. C. (2003). Nasa Thermal Control Technologies for Robotic Spacecraft. Appl. Therm. Eng. 23, 1055–1065. doi:10.1016/s1359-4311(03)00036-x
Tachikawa, S., Ohnishi, A., Shimakawa, Y., Ochi, A., Okamoto, A., and Nakamura, Y. (2003). Development of a Variable Emittance Radiator Based on a Perovskite Manganese Oxide. J. Thermophys. Heat Transf. 17, 264–268. doi:10.2514/2.6760
Thome, J. R. (2004). Boiling in Microchannels: A Review of Experiment and Theory. Int. J. Heat Fluid Flow 25, 128–139. doi:10.1016/j.ijheatfluidflow.2003.11.005
Tien, C. L., and Cunnington, G. R. (1973). Cryogenic Insulation Heat Transfer. Adv. Heat Transf. 9, 349–417. doi:10.1016/s0065-2717(08)70065-0
Vasiliev, L. L. (2008). Micro and Miniature Heat Pipes - Electronic Component Coolers. Appl. Therm. Eng. 28, 266–273. doi:10.1016/j.applthermaleng.2006.02.023
Wang, J., Yuan, W. X., Yuan, X. G., and Yu, H. M. (2005). Research on Vapor Compression Heat Pump for Space Use. Acta Aeronautica Astronautica Sinica-Series A B 26, 529.
Woo, T. (2012). “Safety Assessment for Lunar Nuclear Power Reactor in Cooling Accident,” in Atomic Information Technology (Berlin, Germany: Springer), 99–117. doi:10.1007/978-1-4471-4030-6_9
Xiang, Y., Chen, J., and Zhang, B. (2015). Thermal Control for Jade Rabbit Rover of Chang’e-3. J. Astronaut. 36, 1203–1209.
Yin, H., B., Gao, X. N., Ding , and J., and Zhang, Z. G. (2007). Cooling Technology of Electronic Device Based on Phase-Change Material with Rapid Thermal Response. J. South China Univ. Technol. Nat. Sci. Ed. 35, 52–57.
Zhang, Y., and Faghri, A. (2003). Oscillatory Flow in Pulsating Heat Pipes with Arbitrary Numbers of Turns. J. Thermophys. Heat Transf. 17, 340–347. doi:10.2514/2.6791
Zhang, Z., Sun, X.-H., Tong, G.-N., Huang, Z.-C., He, Z.-H., Pauw, A., et al. (2011). Stable and Self-Adaptive Performance of Mechanically Pumped Co2 Two-phase Loops for Ams-02 Tracker Thermal Control in Vacuum. Appl. Therm. Eng. 31, 3783–3791. doi:10.1016/j.applthermaleng.2011.07.015
Keywords: thermal management system, thermal control technology, energy harvesting, thermal bus, heat pump technology
Citation: Jiang F, Zhao S, Wang L, Yu S, Guan H and Liu J (2022) Energy Harvesting and Thermal Management System in Aerospace. Front. Mater. 9:907858. doi: 10.3389/fmats.2022.907858
Received: 30 March 2022; Accepted: 26 May 2022;
Published: 10 August 2022.
Edited by:
Wenai Shen, Huazhong University of Science and Technology, ChinaReviewed by:
Xu Tao, Shanghai Institute of Satellite Engineering, ChinaCopyright © 2022 Jiang, Zhao, Wang, Yu, Guan and Liu. This is an open-access article distributed under the terms of the Creative Commons Attribution License (CC BY). The use, distribution or reproduction in other forums is permitted, provided the original author(s) and the copyright owner(s) are credited and that the original publication in this journal is cited, in accordance with accepted academic practice. No use, distribution or reproduction is permitted which does not comply with these terms.
*Correspondence: Fan Jiang, Z2hvbGV0aGVAMTI2LmNvbQ==
†These authors have contributed equally to this work and share the first authorship
Disclaimer: All claims expressed in this article are solely those of the authors and do not necessarily represent those of their affiliated organizations, or those of the publisher, the editors and the reviewers. Any product that may be evaluated in this article or claim that may be made by its manufacturer is not guaranteed or endorsed by the publisher.
Research integrity at Frontiers
Learn more about the work of our research integrity team to safeguard the quality of each article we publish.