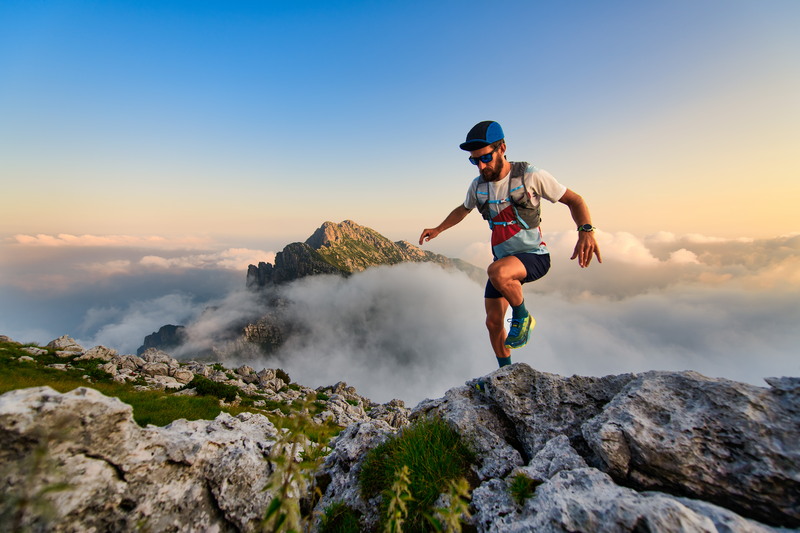
95% of researchers rate our articles as excellent or good
Learn more about the work of our research integrity team to safeguard the quality of each article we publish.
Find out more
ORIGINAL RESEARCH article
Front. Mater. , 18 May 2022
Sec. Environmental Degradation of Materials
Volume 9 - 2022 | https://doi.org/10.3389/fmats.2022.897900
This article is part of the Research Topic Materials Corrosion in High Temperature Molten Salt Environments View all 6 articles
The cubic polycrystal of SiC (3C-SiC) coating on the quartz glass (QG) surface was successfully prepared via a two-step chemical vapor deposition (CVD) by introducing a thin PyC coating as a buffer layer. Through combining the intake system of CVD PyC and CVD SiC, the SiC/PyC composite coating can be in-situ prepared on the QG without halfway in-and-out chamber. The results showed that the SiC/PyC composite coating possesses highly uniform, dense, and continuous features, while the pure SiC coating exhibits many cracks, implying that the internal stress between the SiC coating and the QG can be relieved by adding the PyC buffer coating. The average hardness of the SiC/PyC/QG is measured to be 46.8 GPa, and its calculated modulus is 416.3 GPa by using a nanoindentation technique. Compared to the pure QG, the friction coefficient of the SiC/PyC/QG is slightly increased to 1.47 vs. 1.45. Moreover, the SiC/PyC/QG displays the excellent anti-acid corrosion in the 5%HF and 5%HCl mixed solution with the weight loss of about 33% lower than the pure QG after 8 h acid test at 80°C.
Quartz glass (QG) is widely used in the field of the compound semiconductor community as the boat for the growth of CdTe, InTe and CdZnTe single crystal in the field of the compound semiconductor community due to the advantage of resistance to high temperature, excellent anti-acid corrosion except hydrofluoric acid (HF), good thermal stability etc. (Rabinovich 1985; Shetty et al., 1995; Schlesinger et al., 2001; Hoshide and Hirano 2010). But the raw materials of Te and Cd would react with the QG during the single crystal growing process, resulting in the as-prepared product adhered to the QG. Thus, the single crystal would be contaminated by the QG and hard to get off the QG. Furthermore, the QG needs to be cleaned in HF to remove the sediment, while the QG shows poor anti-HF corrosion. Therefore, the QG or quartz fiber coated with a protective material has been extensively studied to improve its chemical durability and other physical properties (Shetty et al., 1995; Hoshide and Hirano 2010; Zheng and Wang 2011; Hoshide et al., 2013). The cubic polycrystal of SiC (3C-SiC) is one of the most important protective materials and drawing significant attention attributing to its high hardness and strength, good corrosion resistance, and easy of deposition (Hu et al., 2019; Fares et al., 2020a; Fares et al., 2020b; Hsu et al., 2020; Zheng et al., 2021; Liu et al., 2022a). However, to the best of our knowledge, the 3C-SiC protective coating on the QG surface is still lacking mainly due to the high internal stress and high thermal expansion coefficient mismatch between QG and SiC. The introduction of the pyrolytic carbon (PyC) as the buffer layer is widely used to alleviate thermal stress due to the interlaminar slippage of PyC and the large thermal expansion coefficient mismatch between the coating and the substrate (Long et al., 2013; Liu et al., 2020; Tong et al., 2021; Liu et al., 2022b).
In this work, it was attempted to deposit the 3C-SiC coating on the QG surface by a two-step CVD using the PyC coating as the buffer coating without halfway in-and-out chamber. In comparison to the pure QG, the resulting product shows the remarkably improved hardness, modulus, friction coefficient, and the anti-acid corrosion in the 5%HF and 5%HCl mixed solution.
Commercial QG (25 mm*45 mm*3 mm) was ultrasonically cleaned in ethanol and deionized water several times. The pretreated QG was dried under vacuum at 60°C for 12 h and then employed as a substrate for CVD PyC coating and CVD SiC coating in a chamber of a vertical type hot-wall CVD (Hunan Advanced Corporation for Materials and Equipments, ACME, China). The CVD PyC was deposited at 1,000°C in an Ar flow of 300 ml/min and C3H6 flow of 200 ml/min for 2 h under the pressure of 2000 Pa. Then, the intake system of the PyC deposition was shut down, while the temperature was kept at 1,000°C. For the CVD SiC coating, a mixture of dilution H2 flow of 2.0 L/min and dilution Ar flow of 2.5 L/min was introduced into the chamber. Meanwhile, the liquid methyltrichlorosilane (MTS) as the Si and C source was delivered to the chamber through continuous bubbling methods with an H2 flow of 1.0 L/min as a carrier gas. The total pressure was controlled to be 1,000 Pa, and the deposition time was 5 h. The anti-acid corrosion character of the samples was test in the mixed solution of 5%HF and 5%HCl at 80°C. The samples were submerged into the acid solution completely for each 2 hours, and then weighted after ultrasonic cleaning in deionized water and drying.
A roughness tester (TR210, Shanghai Lingyi Company, China) was used to measure the surface roughness (Ra) of the samples. X-ray diffraction (XRD, Rigaku SmartLab-SE, Japan) with Cu Kα radiation and scanning electron microscopy (SEM, Carl Zeiss G500) were carried out to characterize the crystal structure and the morphology of the products, respectively. X-ray photoelectron spectroscopy (XPS) analysis was obtained by a Thermo Fisher Scientific Esca Lab 250XI spectrometer using a monochromatic Al anode X-ray source. The mechanical properties of the samples were investigated by the conventional method (Vickers, Duramin-40 M1 Struers), the nanoindentation test with a diamond Berkovich indenter (three-sided pyramid), and the friction test on a HT1000 wear test machine with a Si3N4 ceramic ball was used as the counter material.
The synthesis produce of the SiC/PyC/QG is illustrated in Figure 1. Firstly, a thin and uniform PyC coating was prepared on the QG surface via a CVD method using C3H6 as the carbon source. Afterwards, the SiC coating could be in-situ grown on the PyC/QG surface just by closing the intake system of the CVD PyC, and then turning on the intake system of the CVD SiC. Therefore, the SiC/PyC composite coating can be continually deposit on the QG surface by a two-step CVD process without halfway in-and-out chamber.
The crystallographic structure and morphology of the QG based products were investigated by XRD and SEM, respectively. The identified diffraction peaks in Figure 2A are indexed to the SiO2 structure (JCPDS: 39-1425), and the wide peak around 2θ = 22° in the XRD pattern is attributed to the amorphous QG. No obvious peaks of the PyC could be identified owing to the strong background peaks of the QG and the thin PyC coating. The main phase of the SiC coating is ascribed to 3C-SiC (JCPDS: 29-1129), and the sharp diffraction peak demonstrates that the SiC deposits were well-crystallized (Figure 2B).
FIGURE 2. XRD pattern of (A) the PyC/QG, and (B) the SiC/PyC/QG; (C) cross section of the low-magnification and (D) the high-magnification SEM images of the SiC/PyC/QG.
The SEM images of the SiC/PyC/QG are shown in Figure 2C and Figure 2D. The thickness of the PyC and SiC coatings was about 0.2 and 30 μm, respectively. It can be clearly seen that both the interfacial layers between PyC and QG, and SiC and PyC are uniform, dense, and continuous without obvious defects such as voids, cavities, and crack, implying that the interfacial adhesion was qualitatively excellent.
Figure 3A displays the typical picture of the frosted QG treated by sand blasting. The dense and continuous PyC and SiC coatings on the QG surface can be seen (Figures 3B,D) further revealing the uniform coatings coverage. However, many cracks appeared on the surface of the SiC coating without the PyC buffer layer (Figure 3C), indicating that the transition layer of PyC could relieve the internal stress between the SiC coating and the QG.
The surface chemical composition and bonding information of the SiC/PyC/QG are shown in Figure 4. It can be clearly seen in Figure 4A that the overall XPS spectrum of the as-prepared composites consists of only Si, C and O elements. The C 1s spectra (Figure 4B) shows four peaks located at 282.7, 284.8, 286.3 and 288.0 eV, corresponding to Si-C, C-C, C-O and C=O bonds, respectively (Zheng et al., 2021; Lu et al., 2019). The C-C bond is most likely to the PyC and the chemical bonding between SiC and PyC. Similarly, the C-O and C=O bonds may be also due to the PyC and the chemical bonding between SiC and PyC. In the Si 2p spectra (Figure 4C), Si 2p peak can be fitted into two peaks at 100.4 and 102.0 eV, which are assigned to the Si-C and Si-O bonds, respectively (Wei et al., 2020; Peng et al., 2018). In Figure 4D, O 1s spectra at 532.0 eV is assigned to the O-Si bond (Sun et al., 2017). The XPS results further confirmed the deposition of SiC coating on the PyC/QG surface.
Hardness and elastic modulus of the SiC/PyC/QG were studied by using a nanoindentation technique. The load-distance relationship is represented in Figure 5A, and three different points were selected to achieve a reliable result. The average hardness of the composites is 46.8 GPa, and the calculated modulus is 416.3 GPa, which are in agreement with other reported results (Lee et al., 2000). Figure 5B shows the variation of the friction coefficient with sliding time. Compared to the friction coefficient of the pure quartz (∼1.45), the friction coefficient of the SiC/PyC/QG is increased to 1.47. The surface roughness for the PyC coating on the QG was measured to be 3.54 um. The higher friction coefficient for the SiC coating is due to the large surface roughness for the SiC coating (4.07 µm) than that of the pure QG (2.83 µm).
FIGURE 5. (A) Load-distance curve of the SiC/PyC/QG; (B) Friction coefficient versus the sliding time (min) of the pure QG and the SiC coating’QG.
Figure 6 demonstrates the variation of the weight loss with the immersion time recorded for the pure QG and the SiC coated QG in the mixed solution of 5%HF and 5%HCl at 80°C. In the first 2 hours, the weight loss of the SiC/PyC/QG was 0.12%, slightly lower than that of the pure QG of 0.14%. Clearly, the weight loss of the pure QG increased to 0.34%, but the SiC coated QG displayed an excellent anti-acid corrosion with only weight loss of 0.19%. After 8 hours, the weight loss of the pure QG and the SiC/PyC/QG was 0.39% and 0.26%, respectively. The results indicated that the SiC coated QG possesses more outstanding anti-acid corrosion than the pure QG due to the unique characters of the SiC coating.
Integration of the CVD PyC and CVD SiC systems, the SiC/PyC composite coating was successfully in-situ prepared on the QG surface without halfway in-and-out chamber. The effects of the PyC buffer coating on the preparation of SiC coating on the QG surface were investigated. It was found that the SiC/PyC composite coating exhibited uniform, dense and continuous features by adding the PyC buffer coating, while the pure SiC coating on the QG surface displayed many cracks or even peeled off due to the high internal stress and big thermal expansion coefficient mismatch between the SiC coating and the QG. The hardness of the SiC/PyC/QG was 46.8 GPa, and its modulus was calculated to be 416.3 GPa. The friction coefficient of the SiC/PyC/QG was slightly higher than that of the pure QG with 1.47 vs. 1.45. The SiC coated QG displayed more excellent anti-acid corrosion than the pure QG in the 5%HF and 5%HCl mixed solution with the lower weight loss of 0.26% versus 0.39% after 8 h acid test.
The original contributions presented in the study are included in the article/Supplementary Material, further inquiries can be directed to the corresponding authors.
SQ: Data curation. TH: Formal analysis. JZ: Methodology. PZ: Investigation. YD, and DG: Supervision. All authors contributed to manuscript revision and read and approved the submitted versions.
This work has been supported by the Jiangxi Provincial Natural Science Foundation of China (No. 20192BAB216009), the Science and Technology Planning Project of Hunan Province, China (No. 2019WK 2051), and Science and Technology Project of Changsha, Hunan, China (No. kh2003023).
The authors declare that the research was conducted in the absence of any commercial or financial relationships that could be construed as a potential conflict of interest.
All claims expressed in this article are solely those of the authors and do not necessarily represent those of their affiliated organizations, or those of the publisher, the editors and the reviewers. Any product that may be evaluated in this article, or claim that may be made by its manufacturer, is not guaranteed or endorsed by the publisher.
Fares, C., Elhassani, R., Partain, J., Hsu, S. M., Craciun, V., Ren, F., et al. (2020). Annealing and N2 Plasma Treatment to Minimize Corrosion of SiC-Coated Glass-Ceramics. Mater. (Basel) 13, 2375–2387. doi:10.3390/ma13102375
Fares, C., Hsu, S. M., Xian, M., Xia, X., Ren, F., Mecholsky, J. J., et al. (2020). Esquivel-Upshaw, J., Demonstration of a SiC Protective Coating for Titanium Implants. Mater. (Basel) 13, 2375–2387. doi:10.3390/ma13153321
Hoshide, T., and Hirano, M. (2010). Evaluation of Strength for Borosilicate Glass Coated with Ceramic Materials by Sputtering. J. Mater. Eng. Perf. 19, 562–567. doi:10.1007/s11665-009-9520-9
Hoshide, T., Shimizu, S., and Tanaka, M. (2013). Fatigue Life Properties and Availability of Proof Testing in Ceramics-Coated Glass. J. Mater. Eng. Per. 23, 753–758. doi:10.1007/s11665-013-0844-0
Hsu, S. M., Ren, F., Chen, Z., Kim, M., Fares, C., Clark, A. E., et al. (2020). Novel Coating to Minimize Corrosion of Glass-Ceramics for Dental Applications. Mater. (Basel) 13, 1215–1225. doi:10.3390/ma13051215
Hu, Z., Zheng, D., Tu, R., Yang, M., Li, Q., Han, M., et al. (2019). Structural Controlling of Highly-Oriented Polycrystal 3C-SiC Bulks via Halide CVD. Mater 12, 390–399. doi:10.3390/ma12030390
Lee, K. S., Park, J. Y., Kim, W. J., Lee, M. Y., and Jung, C. H. (2000). Effect of Soft Substrate on the Indentation Damage in Silicon Carbide Deposited on Graphite. J. Mater. Sci. 35 (11), 2769–2777. doi:10.1023/A:1004778614890
Liu, J., Chen, Z., Chai, P., Wan, Q., and Shahzad, A. (2022). The Effect of Deposition Temperature on Microstructure and Mechanical Properties of SiC Coatings on Graphite. J. Au. Ceram. Soc. doi:10.1007/s41779-021-00699-7
Liu, X. L., Dai, Y., Wang, Z. J., and Wu, J. (2022). Research Progress on Tantalum Carbide Coatings on Carbon Materials. New Carbon Mater. 36, 1049–1061. doi:10.1016/S1872(21)60101-410.1016/j.carbon.2021.12.005
Liu, X., Xu, H., Xie, F., Yin, X., and Riedel, R. (2020). Light-Weight and Highly Flexible TaC Modified PyC Fiber Fabrics Derived from Cotton Fiber Textile with Excellent Electromagnetic Shielding Effectiveness. Chem. Eng. J. 387, 124085–104098. doi:10.1016/j.cej.2020.124085
Long, Y., Javed, A., Zhao, Y., Chen, Z. K., Xiong, X., and Xiao, P. (2013). Fiber/matrix Interfacial Shear Strength of C/C Composites with PyC–TaC–PyC and PyC–SiC–TaC–PyC Multi-Interlayers. Ceram. Inter. 39, 6489–6496. doi:10.1016/j.ceramint.2013.01.080
Lu, W., Tarekegne, A. T., Ou, Y., Kamiyama, S., and Ou, H. (2019). Temperature-dependent Photoluminescence Properties of Porous Fluorescent SiC. Sci. Rep. 9, 16333–163342. doi:10.1038/s41598-019-52871-6
Peng, Y., Pan, N., Wang, D., Yang, J., Guo, Z., and Yuan, W. (2018). A Si–O–Si Bridge Assembled from 3-mercaptopropyltrimethoxysilane and Silicon Carbide for Effective Charge Transfer in Photocatalysis. J. Mater. Sci. 53, 12432–12440. doi:10.1007/s10853-018-2518-7
Rabinovich, E. M. (1985). Preparation of Glass by Sintering. J. Mater. Sci. 20, 4259–4297. doi:10.1007/BF00559317
Schlesinger, T. E., Toney, J. E., Yoon, H., Lee, E. Y., Brunett, B. A., and Franks, L. (2001). Cadmium Zinc telluride and its Use as a Nuclear Radiation Detector Material. Mater. Sci. Eng. 32, 103–189. doi:10.1016/S0927-796X(01)00027-4
Shetty, R., Wilcox, W. R., and Regel, L. L. (1995). Influence of Ampoule Coatings on Cadmium telluride Solidification. J. Cryst. Growth 153, 103–109. doi:10.1016/0022-0248(95)00149-2
Sun, X., Liu, H. T., and Cheng, H. F. (2017). Oxidation Behavior of Silicon Nitride Fibers Obtained from Polycarbosilane Fibers via Electron Beam Irradiation Curing. RSC Adv. 7, 47833–47839. doi:10.1039/c7ra09056k
Tong, M., Fu, Q., Liang, M., Feng, T., Hou, W., Sun, J., et al. (2021). Effect of PyC-SiC Double-Layer Interface on Ablation Behaviour of Impacted CVD-SiCnws/HfC Coating. Corros. Sci. 191, 109741–109752. doi:10.1016/j.corsci.2021.109741
Wei, J., Li, X., Wang, Y., Chen, B., Zhang, M., and Qin, C. (2020). Photoluminescence Property of Inexpensive Flexible SiC Nanowires Membrane by Electrospinning and Carbothermal Reduction. J. Am. Ceram. Soc. 103, 6187–6197. doi:10.1111/jace.17396
Zheng, X., Liu, Y., Fu, S., Cao, Y., and Zhang, Y. (2021). Effect of Deposition Temperature and Time on Microstructure of CVD SiC Coating on diamond Particles. Sur. Inter. 24, 109741–109752. doi:10.1016/j.surfin.2021.101076
Keywords: SiC coating, pyc coating, quartz glass, chemical vapor deposition, anti-acid corrosion
Citation: Wu J, Qian S, Huo T, Zheng J, Zhang P, Dai Y and Geng D (2022) Effect of PyC Inner Coating on Preparation of 3C-SiC Coating on Quartz Glass by Chemical Vapor Reaction. Front. Mater. 9:897900. doi: 10.3389/fmats.2022.897900
Received: 16 March 2022; Accepted: 29 March 2022;
Published: 18 May 2022.
Edited by:
Yakun Zhu, United States Department of Energy (DOE), United StatesCopyright © 2022 Wu, Qian, Huo, Zheng, Zhang, Dai and Geng. This is an open-access article distributed under the terms of the Creative Commons Attribution License (CC BY). The use, distribution or reproduction in other forums is permitted, provided the original author(s) and the copyright owner(s) are credited and that the original publication in this journal is cited, in accordance with accepted academic practice. No use, distribution or reproduction is permitted which does not comply with these terms.
*Correspondence: Yu Dai, ZGFpeXVAdmlwLjE2My5jb20=; Dongsheng Geng, ZGdlbmdAdXN0Yi5lZHUuY24=
Disclaimer: All claims expressed in this article are solely those of the authors and do not necessarily represent those of their affiliated organizations, or those of the publisher, the editors and the reviewers. Any product that may be evaluated in this article or claim that may be made by its manufacturer is not guaranteed or endorsed by the publisher.
Research integrity at Frontiers
Learn more about the work of our research integrity team to safeguard the quality of each article we publish.