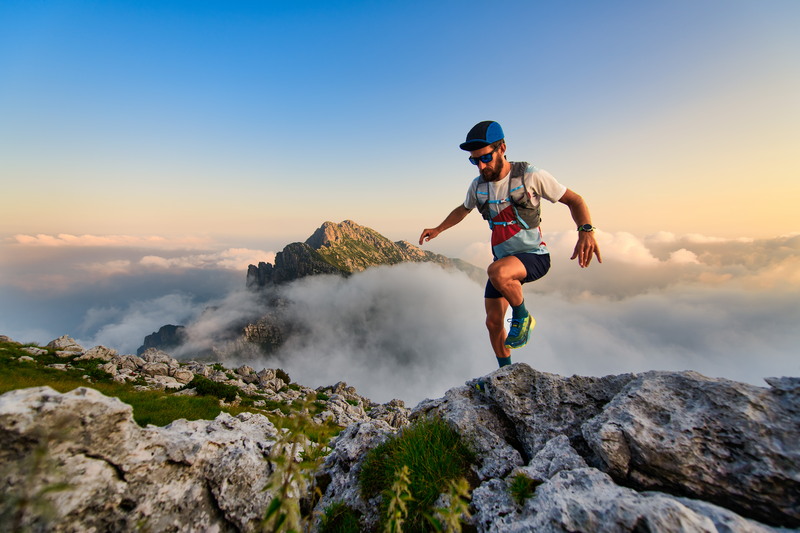
95% of researchers rate our articles as excellent or good
Learn more about the work of our research integrity team to safeguard the quality of each article we publish.
Find out more
ORIGINAL RESEARCH article
Front. Mater. , 10 May 2022
Sec. Environmental Degradation of Materials
Volume 9 - 2022 | https://doi.org/10.3389/fmats.2022.896346
This article is part of the Research Topic Machining Technology and Environmental Degradation Mechanism of Surface Microstructure of Special Materials View all 10 articles
Metal is the primary substrate for fabricating flexible sensors, and its surface quality has a significant effect on the performance of these sensors. The traditional lapping-polishing technology has the disadvantages of being time-consuming and presenting difficulty in controlling the uniformity. In this paper, a liquid metal lapping-polishing plate with a self-shaping function is proposed and developed, which can realize high quality and low surface damage in the processing of the metallic substrate. It is found from the fundaments of the liquid metal lapping-polishing plate that the temperature generated by the friction between the workpiece and plate plays an important role in affecting the processing performance, and then a numerical study of the temperature field on the liquid metal lapping-polishing plate surface has been carried out, and it is found that the temperature increase with the increment of the pressure and rotation speed of the lapping-polishing plate on the target surface. Finally, it is found from experiments that the experimental results have shown to be in good agreement with the corresponding experimental data for the highest temperature under specific conditions and the processing performance has been significantly improved as well.
With the increasing demand for sensors in some extreme environments, the requirements for range, accuracy, and stability are increasingly strict, such that sensors with the desirable characteristics of being flexible, freely bending, foldable, and wearable have attracted many researchers to investigate this field (Elashery et al., 2022; Maciel et al., 2022). Currently, there are a large number of materials being considered as the substrates of flexible sensors, such as metal, ultra-thin glass, and organic polymer substrates (Ren et al., 2020; Sayginer et al., 2021). The ultra-thin glass and organic polymer substrates have disadvantages of poor resistance to high temperatures, and poor water and oxygen barrier ability (Garner et al., 2019; Guan et al., 2022), while the metal substrates possess advantages of good high-temperature resistance, low coefficient of thermal expansion, and exemplary performance in heat resistance (Li et al., 2020; Liu et al., 2021; Goswami and Gupta, 2022).
However, the surface quality of the metal substrate has an essential effect on the performance of flexible sensors (Khalid and Chang, 2022). Abrasive machining technology has been extensively used in the precision and ultra-precision machining of almost any materials with high efficiency and quality (Qi et al., 2021; Cheng et al., 2022; Hu et al., 2022; Qi et al., 2022). Efforts have been contributed by many scholars to improve the abrasive lapping-polishing performance (Li et al., 2019; Jin et al., 2020). Kim et al. prepared self-corrected polishing pads, which were mainly composed of a mixture of alumina abrasive particles and hydrophilic polymers, and compared with the traditional polishing pads, possesses good viscoelasticity and can extend the processing time, thus improving the processing quality (Kim et al., 2004). Zhao et al. proposed a semi-solid abrasive polishing method, which mainly employed the trap effect to reduce the defects caused by the large abrasive particles impacting the target surface during the polishing process and improve the processing quality (Zhao et al., 2011). Choi and Jeong used UV light to treat the hydrophilic polymers, by which they developed a polishing pad with self-healing and hydrophilic functions, and three types of the diamond abrasive polishing pads were fabricated to polish the die steel, which eventually reduced the surface roughness to be about 15.1 nm (Choi and Jeong, 2004). The above abrasive machining methods could realize the precision polishing of substrates with good surface quality, but the efficiency should be considered as well. In general, the abrasive lapping process is used to realize the fast thinning of the substrate, and the abrasive polishing process is employed to realize the high surface finishing of the substrate (Jin et al., 2020; Zhao et al., 2020). The liquid metal with characteristics of high electrical conductivity, low viscosity, and large tension has shown good performance in jet printing or carrying the abrasive particles to realize the machining of complicated structures (Wang et al., 2018; Zhang et al., 2022).
Thus, in this paper, the processing method of the metallic substrate using a liquid metal lapping-polishing plate is proposed to realize the combination of the abrasive lapping and polishing processes. The fundaments of the liquid metal lapping-polishing process are first analyzed, and the numerical study of the temperature field on the liquid metal lapping-polishing plate surface is then conducted to explore the effect of processing parameters on the distribution of the temperature. Finally, the corresponding experiments have been carried out to verify the numerical model and explore the processing performance.
A liquid metal lapping-polishing plate with the self-shaping function is first proposed and analyzed, as shown in Figure 1, where the liquid metal lapping-polishing plate consists of the binder, abrasive particles, and liquid metal whose hardness varies with respect to the temperature. During the lapping-polishing process, heat can be generated due to the mechanical friction between the lapping-polishing plate and the target surface, and this heat could result in the increase of temperature in the lapping-polishing plate which in turn decreases the harness of liquid metal, such that the surface shape of the liquid metal lapping-polishing plate would be changed.
FIGURE 1. Schematic of the liquid metal lapping-polishing plate. (A) Original plate, (B) Temperature increased plate.
To be specific, the liquid metal lapping-polishing plate possesses originally high hardness due to the addition of liquid metal where the large abrasive particle is higher than the small abrasive particle that may cause the large surface damage on the target surface, as shown in Figure 1A, but during the lapping-polishing process, the hardness of liquid metal reduces with the increase of temperature, so that the large abrasive particle could recede to a certain depth under the pressure of workpiece (Li et al., 2016; Shrivastava et al., 2021). When the height of the large abrasive particle is equal to other small abrasive particles, the pressure of the workpiece is uniformly distributed by the abrasive particles on the surface of the lapping-polishing plate, as shown in Figure 1B, so that in this way the liquid metal lapping-polishing plate could realize the combination of the abrasive lapping and polishing processes due to its self-shaping function, and hence, significantly reducing the surface damage caused by the large abrasive particle, enhancing the surface form accuracy and improving the processing efficiency.
In the lapping-polishing process, the variation of temperature on the surface of the lapping-polishing plate would have an essential effect on the hardness of the liquid metal, hence, affect the processing quality. The heat mainly comes from the mechanical friction between the workpiece and the lapping-polishing plate, and the temperature field on the surface of the lapping-polishing plate is mainly affected by various processing parameters, such as the lapping-polishing pressure and the rotation speed of the lapping-polishing plate. Thus, it is necessary to get an insight into the distribution of temperature field on the liquid metal lapping-polishing plate surface, such that the related numerical simulation has been first conducted in ANSYS to explore the underlying sciences, as detailed below.
To consider the experimental work that has been stated in Section 4.1 where the single-side planetary lapping-polishing machine is used to carry out the experiments, and the associated model geometry in simulation is shown in Figure 2. The stainless steel is selected as the workpiece with a radius of 18 mm and thickness of 1.5 mm, and a Bismuth-based alloy with a melting point of 40°C is selected as the liquid metal that is used to model the lapping-polishing plate with a radius of 50 mm and thickness of 7.8 mm. Moreover, the major material properties used in the simulation are given in Table 1 according to the corresponding experimental measurements, and the processing parameters considered in the simulation are as follows: four levels of the lapping-polishing pressure (P) at 6, 9, 12, 15 KPa are considered, four levels of rotation speed of the lapping-polishing plate (rp) at 70, 100, 130, 160 r/min are selected, the rotation speed of workpiece (rw) is set to be 130 r/min, and all the experiments are carried out at room temperature. Thus, by using a full factorial design 16 simulation test conditions can be considered for further analysis (Xie et al., 2021).
Figure 3 presents the typical distribution of the temperature field on the liquid metal lapping-polishing plate with respect to the different processing times, t, at p = 12 kPa, rp = 130 r/min, and rw = 130 r/min. It can be seen from Figure 3A that the temperature increases quickly at the beginning of the lapping-polishing process and presents an obvious track on the surface of the lapping-polishing plate. With the further increase in the processing time the temperature shows a gradual increase due to the frictional heat consumption in the air convection, heat conduction in the lapping-polishing plate, and the radiation to the outside environment (Lee et al., 2013; Totolin et al., 2016), as can be seen from Figures 3B–D. Additionally, it is also noticed from Figure 3 that the distribution of the temperature on the lapping-polishing plate shows a ring shape, in which the temperature shows a gradually increasing trend from the center to the outer. It is attributed to the fact that the heat dissipation and transfer near the center of the lapping-polishing plate are faster, while in the outer area the temperature is higher because of the relatively higher linear speed.
FIGURE 3. Distribution of the temperature field on the liquid metal lapping-polishing plate with respect to the different processing time. (A) t=5 s, (B) t=10 s, (C) t=15 s, (D) t=20 s.
A quantitative analysis of the variation of the temperature on the fixed-point A (see Figure 3A) on the lapping-polishing plate, which is the center of the workpiece, with respect to the processing time has been conducted. It can be seen from Figure 4 that the mechanical friction occurs between the workpiece and the lapping-polishing plate in the early stage of the lapping-polishing process, which makes the heat continuously accumulated and to be transferred into the lapping-polishing plate, thus resulting in the fast increase of the temperature on the surface of the lapping-polishing plate. However, with the further increment of the processing time, the generation of the heat from the mechanical fraction and the consumption of the heat by the air convection, heat conduction in the lapping-polishing plate, and the radiation to the outside environment would achieve a dynamic balance, so that the variation of the temperature tends to be stable as shown in Figure 4.
Since the lapping-polishing pressure would affect the contact force resultant fraction between the workpiece and the lapping-polishing plate which may induce the variation of the temperature in the lapping-polishing process, it is necessary to investigate the effect of pressure on the temperature field. Figure 5 shows the distribution of the temperature field on the lapping-polishing plate with respect to different pressures at rp = 130 r/min, rw = 130 r/min, and t = 20 s. It can be seen from Figure 5 that after the processing time of 20 s, the distribution of the temperature field on the lapping-polishing plate seems to be stable, and with the increase of pressure, the average temperature on the surface of the lapping-polishing plate gradually increases while along the radial direction of the lapping-polishing plate the temperature gradually decreases. It is also found from the simulation that the temperature in the region between the outer ring of the workpiece and the lapping-polishing plate is a little higher than in the other regions, which is attributed to the reason that there is more relative friction between the outer ring and the workpiece in unit time as compared with the inner ring. However, the overall distribution of the temperature in the processing region is relatively uniform. Figure 6 shows the quantitative analysis of the relation between the pressure and temperature on the lapping-polishing plate, and it is found that the highest temperature on the surface of the lapping-polishing plate reached about 38.671°C, 40.907°C, 42.489°C, and 44.545°C at the corresponding pressure of 6, 9, 12, 15 kPa, respectively.
FIGURE 5. Distribution of the temperature field on the liquid metal lapping-polishing plate with respect to the different pressures in simulation. (A) P=6 KPa, (B) P=9 KPa, (C) P=12 KPa, (D) P=15 KPa.
Furthermore, the effect of the rotational speed of the lapping-polishing plate on the temperature has been also qualitatively and quantitatively analyzed according to the simulation results. Figure 7 shows the distribution of the temperature field on the lapping-polishing plate with respect to different rotation speeds of the lapping-polishing plate at p = 12 kPa, rw = 130 r/min, and t = 20 s. It can be seen from this figure that in general the overall temperature on the surface of the lapping-polishing plate increases with an increment of the rotation speed of the lapping-polishing plate, and it is due to the fact that increasing the rotation speed of the lapping-polishing plate the relative speed between the workpiece and the lapping-polishing plate increase as well, which results in the increase of the heat generation by the mechanical fraction. Similarity, it can be found from the quantitative analysis of the relation between the rotation speed of the lapping-polishing plate and temperature showing that the highest temperature on the surface of the lapping-polishing plate reached about 36.734°C, 40.114°C, 43.635°C, 48.186°C at the corresponding rotation speed of 70, 100, 130, 160 r/min, respectively.
FIGURE 7. Distribution of the temperature field on the liquid metal lapping-polishing plate with respect to the different rotation speeds in simulation. (A) rp=70 r/min, (B) rp=100 r/min, (C) rp=130 r/min, (D) rp=160 r/min.
The in-house developed liquid metal lapping-polishing plate which consists of the Bismuth-based alloy with the melting point of 40°C and SiC abrasive particles with a size of 3,000 mesh is fixed in the MP-1B lapping-polishing machine to realize the single-side planetary lapping-polishing of the stainless steel substrate, as shown in Figure 8, and the rotation speed of the lapping-polishing plate can be exactly controlled in the range of 50–1,000 r/min. Thus, the processing parameters considered in the experiment are similar to that in simulation, where four levels of P at 6, 9, 12, 15 KPa are selected, four levels of rp at 70, 100, 130, 160 r/min are considered, rw is set to be 130 r/min and all the experiments are carried out at room temperature. Again, a full factorial design is considered for P and rp and it results in 16 tests in the experiment. In order to verify the numerical model and explore the processing performance, the temperature is real-time measured by using Fluke Tix640 Infrared Camera and the surface morphology is observed by using Keyence 3D Microscope VHX600.
Figure 9; Figure 10 present the real-time measurement of temperature on the surface of the lapping-polishing plate with respect to different P and rp at t = 20 s, and the highest temperature point on the surface is measured for each condition in units of ℉, so that the comparison between the simulating and experimental results can be obtained as shown in Figure 11. It can be seen from Figures 9, 10 that with the increase of P and rp, the temperature on the surface of the lapping-polishing plate increases as well, which indicates similar trends to the numerical results. It is also found from Figure 9A that the processing area shows a typical ring temperature and the temperature decreases to both sides of the processing area, which is also agreed with the numerical findings in Section 3.2. In addition, the quantitative comparison in Figure 11 shows that the simulating trends of the temperature with respect to different P and rp are similar to that in the experiment, and the model predictions have shown to be in good agreement with the corresponding experimental data for the highest temperature under specific conditions. Therefore, it may be deduced that the numerical model has been correctly developed for use to simulate the temperature field on the liquid metal lapping-polishing plate surface.
FIGURE 9. Distribution of the temperature field on the liquid metal lapping-polishing plate with respect to the different pressures in the experiment. (A) P=6 KPa, (B) P=9 KPa, (C) P=12 KPa, (D) P=15 KPa.
FIGURE 10. Distribution of the temperature field on the liquid metal lapping-polishing plate with respect to the different rotation speeds in the experiment. (A) rp=70 r/min, (B) rp=100 r/min, (C) rp=130 r/min, (D) rp=160 r/min.
FIGURE 11. Comparison of simulating and experimental results. (A) Under different lapping-polishing pressures, (B) Under different lapping-polishing rotation speed.
The processing performance has also been analyzed by using the developed liquid metal lapping-polishing plate in this study. The original surface morphology of the stainless steel substrate is shown in Figure 12A with a surface roughness of about 0.132 μm, and large scratches can be obviously observed on the target surface. After the lapping-polishing process at p = 12 kPa, rp = 70 r/min, and t = 20 min, the surface morphology of the target surface is shown in Figure 12B, in which the surface roughness has been reduced to about 0.038 μm and the scale of the scratches on the target surface has been significantly reduced as well. Thus, the developed liquid metal lapping-polishing plate can be used to improve the abrasive lapping-polishing performance, and future work will be focused on the optimized design of the processing parameters during the liquid metal lapping-polishing process.
FIGURE 12. Comparison of surface morphologies before and after liquid metal lapping-polishing. (A) Original target surface, (B) Surface morphology after liquid metal lapping-polishing.
In this paper, the liquid metal lapping-polishing method has been proposed by using the lapping-polishing plate with the self-shaping function to realize the high quality and low surface damage in the processing of the metallic substrate. The underlying science of this method has been fundamentally explored and it is found that the temperature generated by the friction between the workpiece and plate plays an essential role in affecting the hardness of the liquid metal which could affect the distribution of abrasive particles on the surface of the plate and hence affecting the processing performance. Then, the effect of the processing parameters, including the lapping-polishing pressure and the rotation speed of the lapping-polishing plate, on the temperature field on the liquid metal lapping-polishing plate surface has been numerically carried out, and it is found from both qualitative and quantitative analysis that the temperature increases with the increment of the pressure and rotation speed of the lapping-polishing plate on the target surface. Finally, the in-house developed liquid metal lapping-polishing plate which consists of the Bismuth-based alloy with the melting point of 40°C and SiC abrasive particles with a size of 3,000 mesh is fixed in the MP-1B lapping-polishing machine to realize the single-side planetary lapping-polishing of the stainless steel substrate, and it is found from experiments that the experimental results have shown to be in good agreement with the corresponding experimental data for the highest temperature under specific conditions and the processing performance has been significantly improved as well. Therefore, the liquid metal lapping-polishing method proposed in this study could provide a reference for the development of the abrasive lapping-polishing process.
The raw data supporting the conclusion of this article will be made available by the authors, without undue reservation.
Conceptualization, LZ; Data curation, RJ; Formal analysis, YF; Investigation, LZ; Software, SL; Supervision, YL; Writing—original draft, RJ; Writing—review and editing, YL.
This research was funded by the National Natural Science Foundation of China (Nos. U21A20122 and 51575493), Zhejiang Provincial Natural Science Foundation of China (No. LGG19E050025).
The authors declare that the research was conducted in the absence of any commercial or financial relationships that could be construed as a potential conflict of interest.
All claims expressed in this article are solely those of the authors and do not necessarily represent those of their affiliated organizations, or those of the publisher, the editors and the reviewers. Any product that may be evaluated in this article, or claim that may be made by its manufacturer, is not guaranteed or endorsed by the publisher.
Cheng, Z., Qin, S., and Fang, Z. (2022). Numerical Modeling and Experimental Study on the Material Removal Process Using Ultrasonic Vibration-Assisted Abrasive Water Jet. Front. Mater. Accept. Publ. 9, 895271. doi:10.3389/fmats.2022.895271
Choi, J. y., and Jeong, H. d. (2004). A Study on Polishing of Molds Using Hydrophilic Fixed Abrasive Pad. Int. J. Mach. Tools Manuf. 44, 1163–1169. doi:10.1016/j.ijmachtools.2004.04.006
Elashery, S. E. A., Attia, N. F., and Oh, H. (2022). Design and Fabrication of Novel Flexible Sensor Based on 2D Ni-MOF Nanosheets as a Preliminary Step toward Wearable Sensor for Onsite Ni (II) Ions Detection in Biological and Environmental Samples. Anal. Chim. Acta 1197, 339518. doi:10.1016/j.aca.2022.339518
Garner, S., Chowdhury, D., and Lewis, S. (2019). Ultrathin Glass Substrates for Thin, Lightweight, Flexible OLED Lighting. Inf. Disp. 35, 9–13. doi:10.1002/msid.1045
Goswami, P., and Gupta, G. (2022). Recent Progress of Flexible NO2 and NH3 Gas Sensors Based on Transition Metal Dichalcogenides for Room Temperature Sensing. Mater. Today Chem. 23, 100726. doi:10.1016/j.mtchem.2021.100726
Guan, X., Yu, Y., Hou, Z., Wu, K., Zhao, H., Liu, S., et al. (2022). A Flexible Humidity Sensor Based on Self-Supported Polymer Film. Sensors Actuators B Chem. 358, 131438. doi:10.1016/j.snb.2022.131438
Hu, W., Teng, Q., Hong, T., Saetang, V., and Qi, H. (2022). Stress Field Modeling of Single-Abrasive Scratching of BK7 Glass for Surface Integrity Evaluation. Ceram. Int. 48, 12819–12828. doi:10.1016/j.ceramint.2022.01.153
Jin, M., Wang, L., Ye, S., Qi, H., Kang, J., Hong, T., et al. (2020). A Novel Functionally Graded Lapping and Polishing Method for the Improvement of Material Removal Uniformity. J. Manuf. Process. 50, 102–110. doi:10.1016/j.jmapro.2019.12.039
Khalid, M. A. U., and Chang, S. H. (2022). Flexible Strain Sensors for Wearable Applications Fabricated Using Novel Functional Nanocomposites: A Review. Compos. Struct. 284, 115214. doi:10.1016/j.compstruct.2022.115214
Kim, H., Park, B., Lee, S., Jeong, H., and Dornfeld, D. A. (2004). Self-conditioning Fixed Abrasive Pad in CMP. J. Electrochem. Soc. 151, G858–G862. doi:10.1149/1.1813951
Lee, S. J., Chen, Y. H., Liu, C. P., and Fan, T. J. (2013). Electrochemical Mechanical Polishing of Flexible Stainless Steel Substrate for Thin-Film Solar Cells. Int. J. Electrochem. Sci. 8, 6878–6888.
Li, W., Zhang, X., Kou, H., Wang, R., and Fang, D. (2016). Theoretical Prediction of Temperature Dependent Yield Strength for Metallic Materials. Int. J. Mech. Sci. 105, 273–278. doi:10.1016/j.ijmecsci.2015.11.017
Li, H. N., Yang, Y., Zhao, Y. J., Zhang, Z., Zhu, W., Wang, W., et al. (2019). On the Periodicity of Fixed-Abrasive Planetary Lapping Based on a Generic Model. J. Manuf. Process. 44, 271–287. doi:10.1016/j.jmapro.2019.05.036
Li, Z., Shan, Y., Wang, X., Li, H., Yang, K., and Cui, Y. (2020). Self-healing Flexible Sensor Based on Metal-Ligand Coordination. Chem. Eng. J. 394, 124932. doi:10.1016/j.cej.2020.124932
Liu, M.-Y., Hang, C.-Z., Zhao, X.-F., Zhu, L.-Y., Ma, R.-G., Wang, J.-C., et al. (2021). Advance on Flexible Pressure Sensors Based on Metal and Carbonaceous Nanomaterial. Nano Energy 87, 106181. doi:10.1016/j.nanoen.2021.106181
Maciel, C. C., De Lima, L. F., Ferreira, A. L., De Araujo, W. R., and Ferreira, M.Q. Development of a Flexible and Disposable Electrochemical Sensor Based on Poly (Butylene Adipate-Co-Terephthalate) and Graphite for Hydroquinone Sensing. Sensors Actuators Rep. 4, 100091. doi:10.1016/j.snr.2022.100091
Qi, H., Qin, S., Cheng, Z., Teng, Q., Hong, T., and Xie, Y. (2021). Towards Understanding Performance Enhancing Mechanism of Micro-holes on K9 Glasses Using Ultrasonic Vibration-Assisted Abrasive Slurry Jet. J. Manuf. Process. 64, 585–593. doi:10.1016/j.jmapro.2021.01.048
Qi, H., Shi, L., Teng, Q., Hong, T., Tangwarodomnukun, V., Liu, G., et al. (2022). Subsurface Damage Evaluation in the Single Abrasive Scratching of BK7 Glass by Considering Coupling Effect of Strain Rate and Temperature. Ceram. Int. 48, 8661–8670. doi:10.1016/j.ceramint.2021.12.077
Ren, Y., Sun, X., and Liu, J. (2020). Advances in Liquid Metal-Enabled Flexible and Wearable Sensors. Micromachines (Basel) 11, 200. doi:10.3390/mi11020200
Sayginer, O., Iacob, E., Varas, S., Szczurek, A., Ferrari, M., Lukowiak, A., et al. (2021). Design, Fabrication and Assessment of an Optomechanical Sensor for Pressure and Vibration Detection Using Flexible Glass Multilayers. Opt. Mater. 115, 111023. doi:10.1016/j.optmat.2021.111023
Shrivastava, S. C., RamakantSrivastava, S., Srivastava, S., and Pandey, J. D. (2021). Computation of Thermophysical Properties of Liquid Metals and Alloys on the Basis of Generalized Version of Hole Theory. Chem. Phys. 549, 111284. doi:10.1016/j.chemphys.2021.111284
Totolin, V., Göcerler, H., Rodríguez Ripoll, M., and Jech, M. (2016). Tribo-electrochemical Study of Stainless Steel Surfaces during Chemical-Mechanical Polishing. Lubr. Sci. 28, 363–380. doi:10.1002/ls.1336
Wang, T., Kwok, T.-H., Zhou, C., and Vader, S. (2018). In-situ Droplet Inspection and Closed-Loop Control System Using Machine Learning for Liquid Metal Jet Printing. J. Manuf. Syst. 47, 83–92. doi:10.1016/j.jmsy.2018.04.003
Xie, Y., Gui, F. X., Wang, W. J., and Chien, C. F. (2021). A Two-Stage Multi-Population Genetic Algorithm with Heuristics for Workflow Scheduling in Heterogeneous Distributed Computing Environments. IEEE Trans. Cloud Comput.. doi:10.1109/tcc.2021.3137881
Zhang, L., Zheng, B., Xie, Y., Ji, R., Li, Y., and Mao, W. (2022). Control Mechanism of Particle Flow in the Weak Liquid Metal Flow Field on Non-uniform Curvature Surface Based on Lippmann Model. Front. Mater. Accept. Publ. 9, 895263. doi:10.3389/fmats.2022.895263
Zhao, P., Wang, Z., and Yuan, J. (2011). Analysis for Trap Effect Influence Factors of Semi-fixed Abrasive Plate. China Mech. Eng. 22, 2399–2403.
Keywords: liquid metal lapping-polishing plate, metallic substrate, temperature field, bismuth-based alloy, processing performance
Citation: Ji R, Zhang L, Zhang L, Li Y, Lu S and Fu Y (2022) Processing Method for Metallic Substrate Using the Liquid Metal Lapping-Polishing Plate. Front. Mater. 9:896346. doi: 10.3389/fmats.2022.896346
Received: 15 March 2022; Accepted: 06 April 2022;
Published: 10 May 2022.
Edited by:
Guijian Xiao, Chongqing University, ChinaReviewed by:
Yi Chen, Southeast University, ChinaCopyright © 2022 Ji, Zhang, Zhang, Li, Lu and Fu. This is an open-access article distributed under the terms of the Creative Commons Attribution License (CC BY). The use, distribution or reproduction in other forums is permitted, provided the original author(s) and the copyright owner(s) are credited and that the original publication in this journal is cited, in accordance with accepted academic practice. No use, distribution or reproduction is permitted which does not comply with these terms.
*Correspondence: Yanbiao Li, bHlicm9yeUB6anV0LmVkdS5jbg==
Disclaimer: All claims expressed in this article are solely those of the authors and do not necessarily represent those of their affiliated organizations, or those of the publisher, the editors and the reviewers. Any product that may be evaluated in this article or claim that may be made by its manufacturer is not guaranteed or endorsed by the publisher.
Research integrity at Frontiers
Learn more about the work of our research integrity team to safeguard the quality of each article we publish.