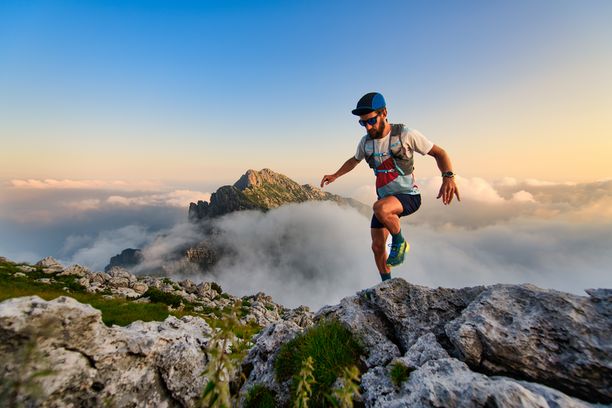
95% of researchers rate our articles as excellent or good
Learn more about the work of our research integrity team to safeguard the quality of each article we publish.
Find out more
ORIGINAL RESEARCH article
Front. Mater., 25 April 2022
Sec. Environmental Degradation of Materials
Volume 9 - 2022 | https://doi.org/10.3389/fmats.2022.895263
This article is part of the Research TopicMachining Technology and Environmental Degradation Mechanism of Surface Microstructure of Special MaterialsView all 10 articles
In order to realize the uniform distribution in the abrasive flow polishing of the titanium alloy workpiece with curved surface, a novel method based on the liquid metal-abrasive flow machining technology is proposed in this study. Based on the SST k-ω model, Preston model and fluid flow particle tracking model, the COMSOL software is employed to study the dynamic characteristics of liquid metal-abrasive flow under different AC electric field conditions, and the two-phase flow field is used to simulate the liquid state, the movement of liquid metal particles on the surface of the workpiece and the varitation of the Pv value in the near-wall region. It is found from numerical simulation results that the average Pv value in the strong flow field is 23,718.8 W/m2, and that in the weak flow field is 5,427.3 W/m2. By the assistance of the electric filed with the voltage of AC 36 V, the average Pv value of the liquid metal particles in the weak flow field is found to be 10,948.6 W/m2 with an increase of 101.7%. Therefore, to properly control the electric field strength, the movement of liquid metal in the flow field can be found to be controlled, and hence improving the uniformity of the turbulent kinetic energy on the workpiece surface and improving the processing quality.
With the development of aerospace science and technology, the performance requirements of aero-engine has been greatly improved. As one of the core components in aero-engine, aviation blades play an important role in improving the overall performance of the engine (Huang et al., 2021). The profile accuracy of the blade has an important impact on its aerodynamic performance, and the aero-engine blade with poor profile accuracy would result in its fatigue failure, deformation or fracture under high-temperature and high-pressure environments (Huai et al., 2017; Yao et al., 2020).
To ensure the stability of the airflow field and reduce the energy loss of airflow, the aero-engine blade has a gradually increasing twist angle from the blade root to the blade tip, which makes the curvature of blade surface and is a typical non-uniform curvature surface part. The workpiece with non-uniform curvature surface mainly has special characteristics, such as a certain curvature with the concavity and convexity. At present, the workpiece with non-uniform curvature surfaces is mainly processed by manual polishing, grinding wheel polishing, and belt polishing. Manual polishing has disadvantages of low efficiency, high labor intensity and unstable machining quality (Zhu et al., 2021). However, the processing accessibility of the grinding wheel for the complex inner surface is not suitable, and in the grinding wheel polishing process, the grinding heat will be generated in the contact area and the thermal damage will often occur on the target surface (He et al., 2018; Huai et al., 2019; Xian et al., 2020). Moreover, due to the elastic contact between the belt grinding and workpiece, there are many factors affecting the material removal process, and hence leading to the difficulty in controlling the material removal rate by belt grinding (Luo et al., 2020).
Abrasive flow polishing is an effective surface processing method, which has the good profiling properties and is suitable for processing the non-uniform curvature surface. However, under the strong action of the abrasive flow, the machined surface will leave processing stripes with obvious directionality, and it will also cause the workpiece to be deformed (Hu et al., 2022; Qi et al., 2022). In addition, the non-uniform curvature of the workpiece makes the flow field to be uneven on the target surface, which would result in the insufficient-polishing at the weak flow field surface while the over-polishing at the strong flow field, and hence affecting the quality of the machined surface (Wang et al., 2018).
To improve the uniformity of the abrasive flow polishing process, Zhai et al. combined the vibration with the chemical mechanical polishing for improving the polishing uniformity of silicon wafer during the chemical mechanical polishing process (Zhai et al., 2017). By adding the ultrasonic vibration into the abrasive flow, Beaucamp et al. increased the turbulence intensity of the flow field for improving the surface polishing quality (Beaucamp et al., 2018). Moreover, Liu proposed the electrochemical assisted abrasive flow polishing method, which used electrochemical dissolution to improve the polishing efficiency and uniformity (Liu, 2018). Zhu proposed a novel abrasive flow polishing method by using the magnetic particles, and it could use the effective magnetic field control to determine the movement of magnetic particles and then improving the polishing uniformity (Zhu, 2020).
In this paper, a novel liquid metal-abrasive flow polishing method which consists of the gallium-based liquid metal, weak viscous fluid and abrasive particles is proposed to overcome the difficulties in polishing non-uniform curvature surfaces of titanium alloy. A liquid metal-abrasive flow model is first developed, and then the dynamic characteristics of liquid metal under the action of the flow field and electric field are tracked and analyzed numerically, by which the mechanism of liquid metal-abrasive flow polishing process can be further investigated. Gallium-based liquid metal has been widely used due to its good fluidity, high chemical stability, excellent electrical conductivity and non-toxicity (Daeneke et al., 2018). Gallium-based liquid metal is a liquid at room temperature, which has a small cutting effect on the target surface, and its driving characteristics under the action of the electric field can be used to realize the controlled flow of liquid metal particles, so as to increase the kinetic energy of abrasive particles and improve the uniformity of the overall polishing.
In the abrasive flow polishing process, due to the characteristics of the curved surface, the flow field on the target surface is not uniform, which could result in a certain difference in terms of the turbulent kinetic energy at different regions of the workpiece, and the average of turbulent kinetic energy
where N is the number of workpiece surface elements and
Liquid metal-abrasive flow machining combines the gallium-based liquid metal particles with the abrasive flow. By applying an electric field at the weak flow field, it would enhance the movement of abrasive particles in the weak flow field and improve their cutting performance. The abrasive particles could move randomly under the action of the liquid carrier in the turbulent flow channel, and perform the random cutting actions on the target surface, thereby realizing the polishing of the target surface. The principle of liquid metal-abrasive flow polishing is shown in Figure 1.
FIGURE 1. Principle of liquid metal-abrasive flow polishing: 1-Abrasive particle, 2-Electrode, 3-Liquid metal particle, 4-Workpiece, a-Inactive area, b-Buffer area, c-Active area.
According to the influence of electric field on liquid metal particles, three areas can be divided as shown in Figure 1, i.e., inactive area, buffer area and active area. In the inactive area, the effect of the electric field on liquid metal particles is weak, which can be considered as particles only affected by the flow field. When the liquid metal particles are close to the electric field, that is, entering the buffer area these particles begin to be affected by the electric field, and the interactions between the liquid metal particles and the abrasive particles become frequently, which can increase the kinetic energy of the abrasive particles. The, when the liquid metal particles enter the active area, the effect of the electric field on these particles is significantly enhanced, and a large number of collisions occur between the liquid metal particles and abrasive particles, which makes the impacts of abrasive particles on the target surface more frequently, thereby further improving their cutting performance.
The gallium-based liquid metal reacts slowly with NaOH to produce [Ga(OH)4]- ions, which carries a large amount of negative charge on the surface of liquid metal droplets. These charges will form an electric double layer corresponding to the free ions. When there is no voltage applied externally, these negative ions are uniformly distributed on the surface of the liquid metal droplet, where the surface tension of the liquid metal droplet is symmetric. When the external electric field is applied, the surface charge of the liquid metal is redistributed due to the good conductivity of the liquid metal, and the electric equilibrium state can be reached according to the Lippmann equation:
Where
The electric field driving force
where n is the number of surface units with the same area and capacitance divided by the surface of liquid metal particles, S is the surface area of liquid metal particles,
where R is the radius of curvature,
where
The Preston equation is an empirical formula widely used in developing the material removal model in the abrasive machining technology, which can be taken from:
where
In the liquid metal-abrasive flow polishing process, both the liquid metal particle size and the abrasive particle size will have a certain influence on kp. When the liquid metal particles are too large, they will be deposited at the bottom of the flow field, and the driving effect of the abrasive particles in the weak flow field decrease, thereby reducing the material removal amount. If the diameter of the liquid metal particles is too small, the driving force for the abrasive particles is small and the control effect seems not good. The liquid metal-abrasive flow polishing method mainly uses the solid-liquid two-phase flow in a turbulent state to produce abrasive cutting actions on the target surface. During this process, when the diameter of the abrasive particles is large, the force on the target surface is large, but it is not conducive to the formation of turbulent flow with large abrasive particles, so that the abrasive particles should be of appropriate size.
When the abrasive particles contact with the target surface, the abrasive particles will squeeze the contact point and generate the contact pressure, which can be expressed as:
where
Since the hardness of liquid metal particles is much less than the hardness of abrasive particles, so that when these two particles collide with each other, the liquid metal particles will be deformed. The physical model of soft collision is equivalent to a set of spring-damper-slider, which considers the elastic effect, buffering effect, friction slip, rolling and locking of solid particles during the collision. In the soft collision model, it is assumed that the shape of particles remains unchanged during the collision, but overlaps with each other, as shown in Figure 3, in which
In the soft collision process, the normal force received by the abrasive particle consists of two parts which are spring force and damping force. Combined with Hertzian contact theory, the normal force received by the abrasive particle is expressed as:
Where
During the liquid metal-abrasive flow polishing process, the velocity of abrasive particle is affected by multiple forces, as shown in Figure 4, and it can be expressed as:
Where G is gravity,
In the liquid metal-abrasive flow polishing process, the collision between the liquid metal particles and abrasive particles can change the relative velocity of the abrasive particles in the near-wall area. The schematic of the collision between the liquid metal particles and the abrasive particles is shown in Figure 5, where
The velocity S of the liquid metal particles relative to the abrasive particles is:
The normal unit vector n when the liquid metal particle collides with the abrasive particle is:
Where
Assuming that the liquid metal particles and abrasive particles do not rotate during the collision, and the tangential vector before and after the collision remains unchanged, then there is:
The velocity after the normal collision is:
Thus, it can be concluded that the velocity of the abrasive particles after the collision is:
Where
In summary, the material removal model of the liquid metal-abrasive flow polishing process under the electric field is taken from:
Where
In the liquid metal-abrasive flow polishing process, the fluid is considered as the carrier to take the abrasive particles and the liquid metal particles. Based on the characteristics of liquid metal-abrasive flow, the SST k-ω turbulence model is selected in COMSOL software to simulate the flow field in this study. Further, the simulation in this paper is composed of upper and lower electrodes, thin-walled curved parts and abrasive flow channels. In order to study the processing of non-uniform curvature surfaces by liquid metal-abrasive flow polishing, the minimum structural unit of non-uniform curvature surface with the same curvature and concave-convex properties is selected, and the thickness of the surface structure is 2 mm. The upper surface of the workpiece is divided into region I and region II, as shown in Figure 6, and the parameters of model geometry are given in Table 1. According to previous simulation and calculated algorithm related to the abrasive flow machining process (Zhang et al., 2019; Xie et al., 2021; Ji et al., 2022), in this simulation the simulation parameters are given in Table 2.
FIGURE 6. (A) Flow channel meshing in simulation, (B) Titanium alloy workpiece, (C) Schematic representation of inside flow channel: 1-Flow field entrance, 2- Electrode, 3- Titanium alloy thin-walled curved parts, and 4- Flow field exit.
The workpiece to be polished is with a non-uniform curvature surface, when the abrasive flow contacts with the target surface the relative velocity and pressure of the abrasive particles on the surface are different. As shown in Figure 7, the arrow direction indicates the direction of the flow field, and it can be seen from the figure that due to the structural characteristics of the workpiece, the turbulent flow energy in region II is less than that in region I. According to Preston equation, the amount of material removal is positively proportional to the relative velocity, v, and pressure, P, thus, in order to present the surface characteristics of the workpiece more clearly, the Pv value curve is calculated by considering the velocity and pressure values on the target surface, as shown in Figure 8, which is used to evaluate the polishing performance of surface in simulation.
FIGURE 7. Flow field characteristics: (A) Velocity distribution at inlet 1 m/s, (B) Velocity distribution at inlet 3 m/s, (C) Velocity distribution at inlet 5 m/s, (D) Pressure distribution at inlet 1 m/s, (E) Pressure distribution at inlet 3 m/s, (F) Pressure distribution at inlet 5 m/s.
In the liquid metal-abrasive flow polishing process, the electric field is mainly used to affect the liquid metal, thereby driving the abrasive particles to impact the target surface. The electric field has a gradual effect on the liquid metal particles, and its trajectory is affected by the flow field and the AC electric field as well. Figure 9 shows the trajectories of liquid metal particles under different voltages.
FIGURE 9. Trajectories of liquid metal particles under different voltages. (A) 0 V, (B) 6 V, (C) 12 V, (D) 24 V, (E) 36 V.
When there is no electric field applied, the liquid metal particles are not affected by the force induced by the electric field, and the trajectories of the liquid metal particles are only affected by the turbulence of flow field, as shown in Figure 9A. When the AC electric field is applied, the liquid metal particles are significantly affected, and it is found from Figure 9 that with an increase of the voltage the liquid metal particles would diverge in more directions when passing through the electric field.
Then, a quantitative analysis on the Pv values under different conditions has been conducted, as shown in Figure 10, where Pv1, Pv2, Pv3 are the average Pv values of pure flow field region I, pure flow field region II and region II under the with the liquid metal. It can be found from Figure 10 that Pv1 value is 23,718.8 W/m2, Pv2 value is 5,427.3 W/m2 and Pv3 value is 10,948.6 W/m2, which indicates that with the assistance of the liquid metal the average Pv value at the weak flow field increases by about 101.7%, and thus, according to the simulation results that the effect of liquid metal particles can significantly improve the polishing uniformity of the entire workpiece surface.
A novel liquid metal-abrasive flow polishing method was proposed in this study, and the material removal model of the liquid metal-abrasive flow polishing process has been theoretically developed. Then, according to the SST k-ω model, Preston model and fluid flow particle tracking model, the numerical investigation has been carried out in COMSOL to study the dynamic characteristics of liquid metal-abrasive flow under different AC electric field conditions, and the two-phase flow field has been used to simulate the liquid state, the movement of metal particles on the surface of the workpiece and the change of the Pv value in the near-wall area during the movement. It is found from numerical simulation results that the average Pv value in the strong flow field is 23,718.8 W/m2, and that in the weak flow field is 5,427.3 W/m2. By the assistance of the electric filed with the voltage of AC 36 V, the average Pv value of the liquid metal particles in the weak flow field is found to be 10,948.6 W/m2 with an increase of 101.7%. By adjusting the magnitude of the electric field strength, the movement of liquid metal in the flow field can be found to be controlled, and hence improving the uniformity of the turbulent kinetic energy on the workpiece surface and improving the processing quality. The related research work in this study could provide a good reference for the abrasive flow polishing of curved surface.
The raw data supporting the conclusion of this article will be made available by the authors, without undue reservation.
Conceptualization, LZ; Data curation, BZ; Formal analysis, BZ; Investigation, RJ; Software, WM; Paper Revision, YL; Writing-original draft, LZ; Writing-review and editing, YX.
This research was funded by the National Natural Science Foundation of China (No. U21A20122, 51575493), Zhejiang Provincial Natural Science Foundation of China (No. LGG19E050025).
The authors declare that the research was conducted in the absence of any commercial or financial relationships that could be construed as a potential conflict of interest.
All claims expressed in this article are solely those of the authors and do not necessarily represent those of their affiliated organizations, or those of the publisher, the editors and the reviewers. Any product that may be evaluated in this article, or claim that may be made by its manufacturer, is not guaranteed or endorsed by the publisher.
Beaucamp, A., Katsuura, T., and Takata, K. (2018). Process Mechanism in Ultrasonic Cavitation Assisted Fluid Jet Polishing. CIRP Ann. 67, 361–364. doi:10.1016/j.cirp.2018.04.075
Daeneke, T., Khoshmanesh, K., Mahmood, N., De Castro, I. A., Esrafilzadeh, D., Barrow, S. J., et al. (2018). Liquid Metals: Fundamentals and Applications in Chemistry. Chem. Soc. Rev. 47, 4073–4111. doi:10.1039/c7cs00043j
Dong, Z. G. (2012). Research on Cutting Mechanism and Processing Technology of Abrasive Flow Machining. Taiyuan, China: Taiyuan University of Technology.
He, Q., Fu, Y., Chen, J., Zhang, W., and Cui, Z. (2018). Experimental Investigation of Cooling Characteristics in Wet Grinding Using Heat Pipe Grinding Wheel. Int. J. Adv. Manuf Technol. 97, 621–627. doi:10.1007/s00170-018-1881-5
Hu, W., Teng, Q., Hong, T., Saetang, V., and Qi, H. (2022). Stress Field Modeling of Single-Abrasive Scratching of BK7 Glass for Surface Integrity Evaluation. Ceramics Int. 48, 12819–12828. doi:10.1016/j.ceramint.2022.01.153
Huai, W., Tang, H., Shi, Y., and Lin, X. (2017). Prediction of Surface Roughness Ratio of Polishing Blade of Abrasive Cloth Wheel and Optimization of Processing Parameters. Int. J. Adv. Manuf Technol. 90, 699–708. doi:10.1007/s00170-016-9397-3
Huai, W., Shi, Y., Tang, H., and Lin, X. (2019). An Adaptive Flexible Polishing Path Programming Method of the Blisk Blade Using Elastic Grinding Tools. J. Mech. Sci. Technol. 33, 3487–3495. doi:10.1007/s12206-019-0643-0
Huang, Y., Li, S., Xiao, G., Chen, B., Zhang, Y., He, Y., et al. (2021). Research Progress of Aero-Engine Blade Materials and Anti-fatigue Grinding Technology. J. Aeronaut. Mater. 41, 17. doi:10.11868/j.issn.1005-5053.2021.000058
Ji, S., Li, C., Tan, D. P., Yuan, Q. L., Chi, Y. W., and Zhao, L. H. (2011). Study on Machinability of Softness Abrasive Flow Based on preston Equation. J. Mech. Eng. 47, 156–163. doi:10.3901/jme.2011.17.156
Ji, R., Zhang, L., Zhang, L., Li, Y., Lu, S., and Fu, Y. (2022). Processing Method for Metallic Substrate of Liquid Metal Lapping-Polishing Plates. Front. Mater. 9, 896346. doi:10.3389/fmats.2022.896346 Submitted for publication.
Li, X., Xie, J., Tang, S.-Y., Xu, R., Li, X., Li, W., et al. (2019). A Controllable Untethered Vehicle Driven by Electrically Actuated Liquid Metal Droplets. IEEE Trans. Ind. Inf. 15, 2535–2543. doi:10.1109/tii.2018.2870857
Liu, S. Y. (2018). Research on Hybrid Finishing Method of Electrochemical Machining Assisted by Freely Flowing Abrasive Particles. Nanjing, China: Nanjing University of Aeronautics and Astronautics.
Luo, G., Zou, L., Huang, Y., and Gong, M. (2020). Study on Material Removal and Surface Quality in Titanium Alloy Grinding with Alumina Hollow-Sphere Abrasive Belt. China Mech. Eng. 31, 2363–2370. doi:10.3969/j.issn.1004-132X.2020.19.013
Qi, H., Shi, L., Teng, Q., Hong, T., Tangwarodomnukun, V., Liu, G., et al. (2022). Subsurface Damage Evaluation in the Single Abrasive Scratching of BK7 Glass by Considering Coupling Effect of Strain Rate and Temperature. Ceramics Int. 48, 8661–8670. doi:10.1016/j.ceramint.2021.12.077
Wang, A.-C., Cheng, K.-C., Chen, K.-Y., and Lin, Y.-C. (2018). A Study on the Abrasive Gels and the Application of Abrasive Flow Machining in Complex-Hole Polishing. Proced. CIRP 68, 523–528. doi:10.1016/j.procir.2017.12.107
Xian, C., Shi, Y., Lin, X., and Liu, D. (2020). Experimental Study on Energy Partition of Polishing Aero-Engine Blades with Abrasive Cloth Wheel. Int. J. Adv. Manuf Technol. 106, 1839–1853. doi:10.1007/s00170-019-04690-2
Xie, Y., Gui, F.-X., Wang, W.-J., and Chien, C.-F. (2021). A Two-Stage Multi-Population Genetic Algorithm with Heuristics for Workflow Scheduling in Heterogeneous Distributed Computing Environments. IEEE Trans. Cloud Comput., 1. doi:10.1109/tcc.2021.3137881
Yang, X., Tan, S., Yuan, B., and Liu, J. (2016). Alternating Electric Field Actuated Oscillating Behavior of Liquid Metal and its Application. Sci. China Technol. Sci. 59, 597–603. doi:10.1007/s11431-016-6026-1
Yao, S., Cao, X., Liu, S., Gong, C., Zhang, K., Zhang, C., et al. (2020). Two-sided Ultrasonic Surface Rolling Process of Aeroengine Blades Based on On-Machine Noncontact Measurement. Front. Mech. Eng. 15, 240–255. doi:10.1007/s11465-019-0581-7
Zhai, K., Ren, Y., Li, L., and He, Q. (2017). Realization of Polishing Uniformity in Megasonic Vibration Assisted Chemical Mechanical Polishing. Nanotechnology Precision Eng. 15, 538–544. doi:10.13494/j.npe.20160015
Zhang, L., Huang, Y., Chen, G., Xu, M., Xia, W., and Fu, Y. (2019). Experimental Study of Coverage Constraint Abrasive Flow Machining of Titanium alloy Artificial Joint Surface. Proc. Inst. Mech. Eng. B: J. Eng. Manufacture 233, 2399–2409. doi:10.1177/0954405419840553
Zhu, X. (2020). Research on Precision Machining Technology of Solid-Liquid Two-phase Abrasive Flow Containing Magnetic Particles. Changchun, China: Changchun University of Science and Technology.
Keywords: curved surface, abrasive flow polishing, gallium-based liquid metal, weak flow field, polishing uniformity
Citation: Zhang L, Zheng B, Xie Y, Ji R, Li Y and Mao W (2022) Control Mechanism of Particle Flow in the Weak Liquid Metal Flow Field on Non-Uniform Curvature Surface Based on Lippmann Model. Front. Mater. 9:895263. doi: 10.3389/fmats.2022.895263
Received: 13 March 2022; Accepted: 28 March 2022;
Published: 25 April 2022.
Edited by:
Guijian Xiao, Chongqing University, ChinaReviewed by:
Li Chen, China Jiliang University, ChinaCopyright © 2022 Zhang, Zheng, Xie, Ji, Li and Mao. This is an open-access article distributed under the terms of the Creative Commons Attribution License (CC BY). The use, distribution or reproduction in other forums is permitted, provided the original author(s) and the copyright owner(s) are credited and that the original publication in this journal is cited, in accordance with accepted academic practice. No use, distribution or reproduction is permitted which does not comply with these terms.
*Correspondence: Yi Xie, eGlleWlAbWFpbC56amdzdS5lZHUuY24=
Disclaimer: All claims expressed in this article are solely those of the authors and do not necessarily represent those of their affiliated organizations, or those of the publisher, the editors and the reviewers. Any product that may be evaluated in this article or claim that may be made by its manufacturer is not guaranteed or endorsed by the publisher.
Research integrity at Frontiers
Learn more about the work of our research integrity team to safeguard the quality of each article we publish.