- Concrete Materials and Structural Integrity Research Unit (CoMSIRU), Department of Civil Engineering, University of Cape Town, Cape Town, South Africa
This study investigated the properties of fine recycled aggregates (FRA), with a view to enhancing their properties for structural concrete applications. The study explored several approaches including mixing; curing; systematic screening of FRA particles below 1.18 mm to reduce the adhered cement paste (ACP) content; and the use of fly ash as 30% cement replacement to modify the microstructure of FRA concrete. To test these approaches, two series of concrete mixes were prepared at 0.45 and 0.55 w/b ratio, with FRA replacing natural sand at 0, 25, and 50% by mass, and tests were carried out after 3, 28, and 180 days of curing. Results show that the combination of ACP reduction and fly ash treatment significantly enhanced the compressive strength and elastic modulus of FRA concrete, especially at 180 days, through microstructure modification and pozzolanic reactions.
Introduction
Sand and gravel are presently mined at twice the rate at which these aggregate sediments are deposited by all the rivers of the world (Peduzzi, 2014). This has led to environmental issues at mining sites, such as coastal erosion, loss of biodiversity in riverbeds, and damage to coastal infrastructure (Gavriletea, 2017; Torres et al., 2017). These issues can be partly mitigated through the use of fine recycled aggregates (FRA) as a replacement for natural sand resources. FRA is produced by crushing concrete components of construction and demolition waste (CDW) to sizes below 4.75 mm. Ordinarily, CDW is deposited in landfills which may result in environmental pollution, cost, and increased CO2 emission in the transport phase, as well as social nuisance around the dump site. Therefore, recycling CDW can address these issues in addition to promoting a circular economy where products (concrete) at the end of their service life are not considered waste but are repurposed for new applications (Ginga et al., 2020).
However, the use of FRA in structural concrete is limited because it does not meet certain strict requirements for structural concrete in the fresh and hardened state. FRA can be idealized as a two-phase composite material comprising the original natural aggregate (NA) and a relatively porous layer of adhered cement paste (ACP) originating from the crushed concrete. When FRA is used for new concrete production, another layer of mortar is attached to the NA and ACP; thereby, creating multiple interfacial transition zones (ITZs) in the concrete matrix. The presence of ACP reduces the overall stiffness of FRA concrete, increases the water absorption, and reduces the density of FRA concrete (de Juan and Gutiérrez, 2009; Kisku et al., 2017), while the multiple ITZs increase the transport properties of the concrete (Beushausen et al., 2021b). Consequently, the fresh properties as well as mechanical and durability properties of FRA concrete may be impacted, when compared to conventional natural aggregate concrete (NAC). Additionally, the quantity of ACP and the source of FRA may vary, thus introducing variability to the concrete properties, which may further limit the application of FRA concrete for structural application.
The challenge, therefore, is how to effectively improve the properties of FRA by reducing the overall ACP content and porosity of FRA, as well as modifying the ACP of FRA in a practical and sustainable way. The improvement technique must consider sustainability metrics such as cost, energy requirement, environmental impact, and industry practicality. Several improvement techniques exist in literature; of these, the use of supplementary cementitious material such as fly ash offers a sustainable alternative. Fly ash improves RA concrete workability, long term strength, elastic modulus, shrinkage, chloride resistance, and thus the durability of RA concrete, owing to the additional pozzolanic reaction between fly ash and the Ca(OH)2 of RA (Kou et al., 2007; Ann et al., 2008; Kou and Poon, 2009; Kou et al., 2011; Wang et al., 2013).
Fly ash is a by-product of coal-fired power plants, which are present in over 80 countries of the world and account for about 34% of global electricity supply as of 2020 (Broadbent, 2021). Even though coal-fired power plants are being phased out, this is expected to still take several decades (with the by-products from these plants being available for an even longer time), considering the global energy demand and the cost of alternative (greener) power technologies. Consequently, using the fly ash for concrete production could contribute to a circular economy, reduce waste as well as offset some of the impact of CO2 emissions associated with coal-fired power plants.
However, it is worth noting that there may be a disparity in the global availability of fly ash in the long term given that while hundreds of power plants have been or are being phased out in Europe and North America, Asia particularly China and India have witnessed a net growth in such coal-fired power plants currently in operation (Varadhan and Sheldrick, 2021; CarbonBrief, 2022; Statista, 2022). For regions with depleting fly ash supply, the use of calcined clay, slag, and agricultural waste as supplementary cementitious materials are being explored.
In the South African context, coal-fired power plants account for 77% of generated electricity (Mdhluli and Harding, 2021), and as such, huge quantities of fly ash are produced. According to the Department of Environmental Affairs (2018), fly ash and bottom ash from coal-fired power stations accounted for 75% of the 67 million tons of hazardous waste generated in South Africa in 2017. Of this figure, only 7% of the fly ash and bottom ash was utilized by the construction industry for the manufacture of cement-based products, with a significant percentage of the fly ash being deposited in landfills (Department of Environmental Affairs, 2018). This practice poses environmental, health, and social concerns.
Therefore, this research is timely as it addresses the overall sustainability of concrete through the conservation of virgin aggregate resources and recycling of CDW as fine aggregates, as well as enhancing the recycled aggregate properties using “waste” fly ash.
State-of-the-Art Overview
The two main techniques of enhancing the properties of recycled aggregates (RAs) are removing or strengthening the adhered cement paste (ACP). Mechanical processing, presoaking in acid, and heat treatment are examples of ACP removal procedures. Carbonation treatment, polymer impregnation, and use of supplementary cementitious materials are typical examples of ACP strengthening techniques.
Mechanical processing may involve multiple crushing, grinding, and ball-milling procedures to remove the ACP of recycled aggregates (RA). These procedures can be carried out in a drum concrete mixer (Dimitriou et al., 2018), an abrasion machine (Dilbas et al., 2019), or a crushing machine (Ulsen et al., 2013; Pedro et al., 2015). Mechanical processing aims at improving the density, water absorption, shape, and texture of RA, and consequently the fresh and hardened properties of the concrete. However, these mechanical procedures can cause microcracks in RA (Shi et al., 2016), which may increase the penetrability of recycled aggregate concrete (RAC), thereby reducing the potential durability of concrete made with these recycled aggregates. Additionally, mechanical processing is more suited for coarse recycled aggregates (CRA), the processing of which typically yields a large amount of fines that can be sieved out and discarded. Applying these mechanical procedures to fine recycled aggregates will result in pulverized ACP and FRA particles that still fall within the fine aggregate size spectrum. From a practical perspective, sorting the pulverized ACP from the FRA particles may be challenging.
The ACP of RA can also be removed by presoaking RA in an acid solution to dissolve the cement hydration products and hardened cement paste, and thereafter washing RA in water to remove the acid (Tam et al., 2007; Al-Bayati et al., 2016). The major drawbacks of this technique include physical damage on the surface of RA, which is relevant when using limestone aggregates, as well as health and safety hazards related to the use of acid. Also, a significant quantity of water is required, and the disposal of used water that contains traces of acid can constitute a major environmental concern. Furthermore, residual acid on RA surfaces can reduce the overall pH of RAC, thereby leading to possible deleterious effects in the concrete. Based on these factors, the acid presoaking technique may, overall, not be environmentally friendly, economical, or practical for application on an industrial scale, and therefore not sustainable.
Heat treatment entails heating RA to high temperatures to dehydrate and embrittle the ACP so that it can easily be removed by washing, mill-grinding, or mechanical scrubbing. Studies by Al-Bayati et al. (2016) show that ACP losses increased from 3% at 250°C to 9% at 500°C; thereafter, ACP loss increased steeply to 41% at 750°C. The high ACP loss at 750°C can be attributed to limestone decomposition which begins to occur at about the same temperature. However, aggregates heated to 750°C, despite having the highest ACP loss, experienced the highest degree of degradation due to thermal expansion, thermal stresses, and the development of microcracks. Other major disadvantages of heat treatment that raise doubt concerning its industry practicality and sustainability include high energy requirements, long processing times, as well as associated high cost, and high degree of impracticality.
Methods of strengthening (or modifying) the ACP of RA are aimed at filling the micro-voids to reduce RA porosity, reduce the size of the ITZ, and increase the bond between cement paste and aggregate in the RAC matrix. One such method involves impregnating the pore network of RA with hydrophobic polymers such as polyvinyl alcohol (PVA), polydiorganosiloxanes (siloxane), and alkylalkoxysilanes (silane). Kou and Poon (2010) reported that CRA treated with a 10% PVA solution reduced the water absorption of CRA by 70%, and the compressive and tensile strength of the concrete produced were comparable to natural aggregate concrete (NAC). Similarly, Spaeth and Djerbi Tegguer (2013) investigated the effectiveness of polymer-based treatment using six polymers and reported significant improvements in water absorption and abrasion resistance properties of the treated CRA. The drawbacks of this technique are, again, high costs and poor industry practicality. Also, there is a dearth of literature on the application of polymer impregnation for FRA, and hence, considerable doubt about the benefits that can be obtained with this technique.
Carbonation treatment mainly involves the reaction of carbon dioxide
The mechanism of supplementary cementitious material treatment involves coating and soaking RA with one or more fine materials such as cement, fly ash, silica fume, GGBS, metakaolin, and the like. The aim is to densify the ACP and strengthen the old and new ITZs in the RA matrix through cement hydration products formed by the pozzolanic reaction. Tam and Tam (2008) demonstrated the effectiveness of this technique on CRA concrete properties using cement and silica fume slurry, and a modification of the two-stage mixing approach (TSMA) developed by Tam et al. (2005). The compressive strength, flexural strength, splitting tensile strength, and elastic modulus of the CRA concrete improved substantially (Tam and Tam, 2008). In a related study, Kong et al. (2010) compared the effect of normal mixing, TSMA, and a novel triple mix method (TM) on the performance of CRA concrete using fly ash and GGBS. Results indicate that the microstructure, compressive strength, and chloride ion penetration resistance of CRA concrete were significantly improved. Similar results were obtained by Wang et al. (2020) using cement and fly ash slurry. Based on its superior economy, promising performance, and industry practicality, as well as its potential to offer sustainable solutions for the improvement of FRA concrete, this method was adopted for the research project discussed in this paper.
Presently, there is a paucity of literature on the combination of techniques to enhance the properties of recycled aggregate concrete, particularly FRA concrete. This research investigated the combined effect of overall ACP reduction through the systematic screening of FRA particles less than 1.18 mm and the use of fly ash as an SCM to modify and strengthen the microstructure of FRA concrete. Previous studies have shown that the amount of ACP by mass of aggregate increases as the RA size reduces; therefore, incorporating finer fractions of RA may negatively impact the fresh and hardened concrete properties (Angulo et al., 2009; Bianchini et al., 2005; de Juan and Gutiérrez, 2009; Li et al., 2021; Li et al., 2019). Consequently, some researchers have carried out investigations on ACP reduction through the systematic screening of FRA for mortar (Li et al., 2019; Zhao et al., 2015) and concrete production (Li et al., 2021). Some limitations exist for these studies. The approach adopted by Li et al. (2019) did not provide an equal basis for comparing results, owing to the disparity in the FRA content for the different size fractions. For instance, to maintain a constant grading curve for the fine aggregate, Li et al. (2019) integrated different percentages of FRA into the various experimental mixes as shown in Table 1. Thus, the 4.75–0.075 mm FRA mortars contained 100% FRA as against 25% of FRA present in the 4.75–1.18 mm mortar. Similar limitations were observed in the work of Zhao et al. (2015), where only single-sized fractions were investigated, that is, 0/0.63, 0.63/1.25, 1.25/2.5, and 2.5/5 mm. The research introduced in this study seeks to address these shortcomings as well as introduce fly ash into the FRA concrete as part of the enhancement procedure. Furthermore, the screened particles (<1.18 mm) can be repurposed for use in clinker production as well as cement replacement material in concrete, owing to their high ACP content (Angulo et al., 2009; Ren et al., 2020). Research is being carried out in this area, in a separate study by the authors.
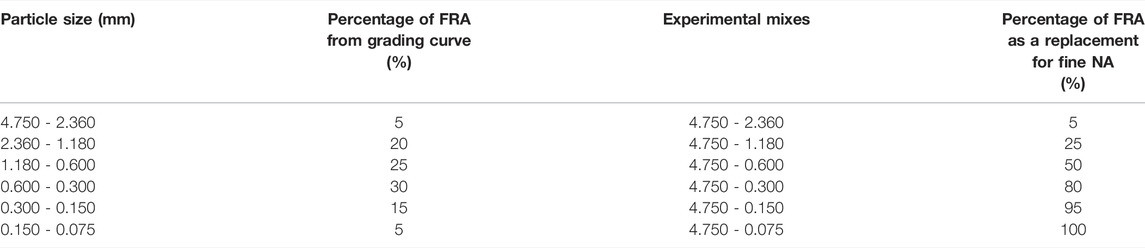
TABLE 1. Systematic substitution of different FRA sizes in a mortar (Li et al., 2019).
Experimental Details
Materials
Greywacke aggregate from a local quarry was used as coarse aggregate (see Figure 1). The fine aggregate comprised conventional fine aggregate and FRA. The conventional fine aggregate was a blend of crushed greywacke and natural dune sand. The purpose of blending, which is industry practice in this region, is to overcome deficiencies such as poor grading of the dune sand and related excessive bleeding and lack of cohesion in fresh concrete.
The FRA was produced by crushing parent concrete obtained from culvert slabs and wing walls used on parts of a regional highway upgrade construction project. The crushing process was carried out using jaw crushers and hammer mills, in an industrial crushing facility. Before crushing the concrete elements, cylindrical specimens measuring 70 ± 1 mm in height by 70 ± 1 mm in diameter were cored and tested for compressive strength in accordance with SANS 5865. The strength varied between 37 and 75 MPa, with an average strength of 55 MPa and a standard deviation of 11.5 (see Figure 2).
Two FRA samples were used for this study, namely, FRA 1 containing FRA particle sizes 1.18 mm − 4.75 mm and FRA 2 containing FRA particle sizes below 4.75 mm (see Figure 1). The purpose of screening FRA particles below 1.18 mm was to reduce the adhered cement paste content of the FRA matrix and, subsequently, limit its influence on concrete properties.
The physical properties of the aggregates used in this study are shown in Table 2. The water absorption of the fine aggregates was determined according to SANS 5844:2014. To minimize the cohesion of FRA fines and ACP, the use of hexametaphosphate solution as described by Rodrigues et al. (2013) was adopted.
CEM II/A-L 52.5N was used as a binder. Class F fly ash was used as supplementary cementitious material, at 30% cement replacement. The material properties as determined by X-ray fluorescence (XRF) analysis are shown in Table 3. Additionally, X-ray diffraction (XRD) analysis was used to determine the mineralogical phases of the materials used in this study (see Table 4.
A polycarboxylate ether (PCE) superplasticizer was used, where necessary, to attain the design slump of 75 ± 25 mm.
Methods
The mix proportions of the concretes are given in Table 5. The quantity of coarse aggregate for each w/b was kept constant. However, there was a slight variation in the actual quantity of coarse aggregate within each w/b series because the densities and fineness moduli of the fine aggregate blend change with increasing FRA content. All aggregates were used in an air-dried state in accordance with findings by Poon et al. (2004) and Zhao et al. (2015). To characterize these aggregates, however, the moisture content was measured and is reported in Table 2.
Two w/b ratios of 0.55 and 0.45 were used for this study. For each w/b, the water content and total binder content were kept constant. No additional water was introduced to improve workability, as this has been demonstrated to have a negative effect on the hardened properties of concrete (Ferreira et al., 2011). To attain the design slump value of 75 ± 25 mm, a superplasticizer was used where necessary. The superplasticizer was dosed as a percentage of the cement. The superplasticizer dosages were applied at not more than the minimum (manufacturer’s specified dosage) to limit its influence on the measured concrete properties (see Table 5). Similarly, no water reduction was applied for mixes that contained a superplasticizer (Table 5).
The concrete of each w/b comprised a control mix and FRA-modified mixes. Conventional fine aggregate in the control mix comprised a 50%–50% blend of crushed greywacke and dune sand (that is, 0% FRA). For the modified mixes, the dune sand content was kept constant at 50% of total fine aggregates, while the FRA (FRA 1 or FRA 2) was introduced at 25% and 50% of total fine aggregates content, that is, FRA directly replaced 50% and 100% of crusher sand, respectively. These FRA replacement levels were chosen to study the influence of varying FRA content in concrete. All the fine aggregate blends used for this study complied with the grading limits of ASTM 33, aiming at eliminating the effect of different particle gradings on the test results. See Figures 3, 4 for the particle grading of the individual and blended aggregates, respectively.
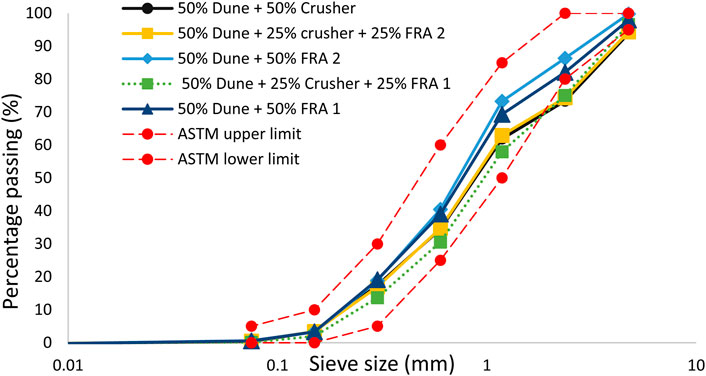
FIGURE 4. Particle size distribution of blended fine aggregates. For referencing purposes, the mixes are denoted as X-Y-Z.
For referencing purposes, the mixes are denoted as X-Y-Z. Where:
X could be A or B, where A and B represent 0.55 w/b and 0.45 w/b, respectively.
For experimental mixes containing FRA 1 and FRA 2, the numbers 1 and 2 are attached to A and B, respectively.
Y is the replacement level of natural sand with FRA. This could be 0, 25, or 50%.
Z could be any of P for plain concrete or F for concrete with fly ash.
For instance, mix A-0-P relates to reference plain concrete (0% FRA) for 0.55 w/b.
Similarly, mix A1-25-F relates to 0.55 w/b concrete with 25% FRA 1 containing fly ash.
Mix B2-50-P relates to 0.45 w/b plain concrete with 50% FRA 2.
The mixing procedure used for this study was an adaptation of the modified two-stage mixing approach (TSMA) developed by Tam and Tam (2008) (see Figure 5. Studies have shown that this procedure improves the interaction and bonding between the recycled aggregate and binder, the densification action of the binder, and consequently the strength and durability properties of recycled aggregate concrete (Tam et al., 2005; Tam and Tam, 2008; Li et al., 2009; Kong et al., 2010).
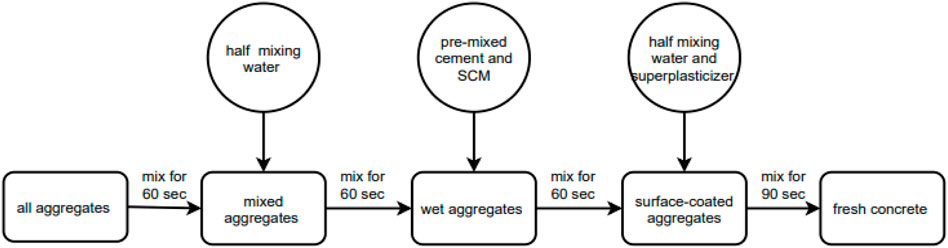
FIGURE 5. Mixing procedure adapted from Tam and Tam (2008).
After mixing, the concrete was cast into 100 mm cubes, and 200 mm height by 100 mm diameter cylinder molds. They were covered with a plastic sheet to maintain a relative humidity of at least 90% and a temperature of 23 ± 2°C for 20–24 h, before demolding. Afterward, they were cured in a temperature-controlled water tank at 23 ± 2°C until test dates at 3, 28, and 180 days.
Testing
To measure the consistency of the fresh concrete, a slump test was done in accordance with SANS 5862–1:2006. A superplasticizer was used where necessary to attain the design slump of 75 ± 25 mm.
Compressive strength tests were done on 100 mm cubes after 3, 28, and 180 days of wet curing. Three cubes were tested for each parameter at each age, and the average result was recorded as the strength value. For all 20 concrete mixes, a total of 180 cubes were tested. The testing was carried out according to SANS 5863:2006.
Elastic moduli of the concrete were determined by averaging the results obtained on three cylinders of 100 mm in diameter by 200 mm in height, according to ASTM C469. These tests were carried out after 3, 28, and 180 days of wet curing. For all 20 concrete mixes, a total of 180 cylinders were tested.
The compressive strength and elastic modulus results are reported in this article as these are general indicators of concrete properties and microstructure. They also provide an indirect insight into the influence of FRA on pore structure, as well as the influence of pozzolanic reaction on the strength and stiffness of FRA concrete. Furthermore, durability tests are ongoing in the laboratory to assess the performance of the enhancement techniques on FRA concrete durability.
Results and Discussion
Slump
Results of the slump test, shown in Table 5, indicate that all concrete mixes were within the design slump. Generally, it was observed that the 0.45 w/b mixes had a lower slump than the 0.55 w/b mixes, owing to the higher binder content of the 0.45 w/b mixes. It can also be observed that, for each w/b, FRA 2 mixes required more superplasticizer than FRA 1 mixes. This can be attributed to the presence of fines in FRA 2 mixes which raised water demand. This observation was also made by Li et al. (2019), where it was shown that finer fractions of FRA had high water demand for FRA mortars due to their high ACP and fine content.
Mixes with fly ash required the least dosage of superplasticizer to attain the design slump. This is due to the spherical nature of fly ash that lubricates the fresh concrete, thus improving workability (Thomas, 2007). Similar results were observed by Kou et al. (2011) in their study of CRA concrete using fly ash.
Note that for all mixes, the superplasticizer dosage ranged from 0 to 0.32%. These dosages were generally below the limit of 0.3 to 3% by mass of binder, as specified by the manufacturers. While this might limit the influence of the superplasticizer on hardened concrete properties, in general, superplasticizers are beneficial by helping to disperse finer particles in the mix. The result also indicates that FRA concrete can achieve a moderate design slump, with little or no superplasticizer, particularly with mixes incorporating fly ash.
Compressive Strength
The average compressive strength (
Results show that for all FRA1 mixes without fly ash,
A much steeper rise in compressive strength from 3 days to 180 days was observed for mixes containing fly ash (see Figures 6, 7). For FRA 1 mixes,
It can be observed that for the 0.55 w/b mixes without fly ash, the compressive strength reduces slightly as the FRA level increases from 0 to 50%, with mix A1-25-P having the highest compressive strength (see Figure 6). This may be attributed to the increase of the less stiff FRA from 0 to 50% in the concrete mix. Compared to FRA 1, mixes with FRA 2 consistently had lower compressive strength at all testing ages. This can be attributed to the porous and less stiff finer fractions of FRA 2. Similar results were obtained by Li et al. (2019) where it was demonstrated that the incorporation of finer particles of FRA negatively impacted the compressive strength of cementitious mortars.
For 0.45 w/b mixes, it can be observed that at 28 and 180 days of testing, the compressive strength of all mixes up to 50% FRA replacement level was comparable to the control NAC concrete (Figure 7). This may be attributed to the initial high water absorption rate of FRA in fresh concrete (Evangelista and De Brito, 2014) which may have induced a moisture movement from the cement matrix to the FRA, thereby reducing the effective w/b and consequently improving the ITZ and strength (Poon et al., 2004; Zhao et al., 2015).
Elastic Modulus
Table 7 shows the average elastic modulus (E) and the standard deviation (σ) measured at 3, 28, and 180 days for the various concrete mixes. For plain concrete mixes without fly ash, there is generally a consistent decrease in the elastic modulus as FRA levels increase from 0 to 50% (see Figures 8, 9). For both w/b ratios and at all testing ages, the change in elastic modulus (ΔE) at 25% and 50% FRA levels are -15 to -0.8% and -19.3 to -5.7%, respectively (see Table 7). The decrease in elastic modulus with increasing FRA replacement level can be attributed to a combination of factors, namely the quantity and stiffness of the binder phase, volume and stiffness of aggregates, and the nature of the interfacial transition zone (ITZ) between the aggregates and paste (Beushausen et al., 2021a). Generally, as the FRA replacement level increases, the ACP amount and consequently the overall paste content of the concrete increases, leading to a corresponding decrease in elastic modulus (Pedro et al., 2017). This also explains why, at all FRA replacement levels, FRA 2 mixes have a lower elastic modulus compared to the corresponding FRA 1 mixes, owing to the higher volume but less stiff ACP and fines content in the FRA 2 mixes. Additionally, the presence of multiple and porous ITZs originating from the old ACP and new cement paste, in the FRA concrete matrix, may introduce additional points of weakness in the concrete and, therefore, lead to a reduction in the elastic modulus as the FRA content increases.
Comparing the trend of compressive strength to the elastic modulus of plain concrete for different FRA replacement levels, it can be observed that while strength may increase due to added ACP and subsequently, additional nucleation sites for hydration, the elastic modulus is consistently reduced with an increase in FRA content at all test ages of 3, 28, and 180 days. Concrete stiffness generally decreases due to a higher amount of porous phases, in this case, a higher amount of ACP and increased ITZ (Beushausen et al., 2021a).
For all mixes containing fly ash, the elastic modulus at 3 days was lower than the corresponding plain concrete mixes (see Figures 8, 9). This can be attributed to the slow pozzolanic reaction of fly ash. At 28 days, the elastic modulus values of mixes containing fly ash are comparable to the corresponding plain concrete mixes. At 180 days, all fly ash mixes had a higher elastic modulus than the corresponding plain concrete mixes. With reference to their 28-days results, the rate of increase at 180 days for the fly ash concrete is 14 to 19% while that of plain concrete mixes showed 4–10% increase. The mechanism of elastic modulus increase involved a combination of effects which include the densification of the multiple ITZ and microstructure of FRA concrete and the formation of additional hydration products through pozzolanic reaction and aluminate reactions, all of which increase the strength and stiffness of the FRA concrete. Furthermore, the silica- and alumina-rich calcium silicate hydrates (C–A–S–H), formed in fly ash mixes over time as reported by De Weerdt et al. (2011), can contribute to higher stiffness for fly ash concrete mixes when compared to mixes without fly ash.
It is generally observed for elastic modulus and compressive strength results, the most improvement for FRA concrete was observed for mixes containing FRA1 and fly ash (see Figures 6–9). This improvement which is more prominent in 0.55 w/b, and at 28 and 180 days of testing, indicates that the combination of ACP reduction and fly ash treatment is effective to enhance the strength and stiffness of FRA concrete.
Relationship Between Elastic Modulus and Compressive Strength
Figure 10 shows the scatter plot of elastic modulus against compressive strength results for FRA concrete mixes (no control mix) at test ages of 3, 28, and 180 days. It can be observed that elastic modulus generally increases as compressive strength increases. These data were compared with the South African model and Eurocode 2 (2004) model for predicting the elastic modulus of concrete.
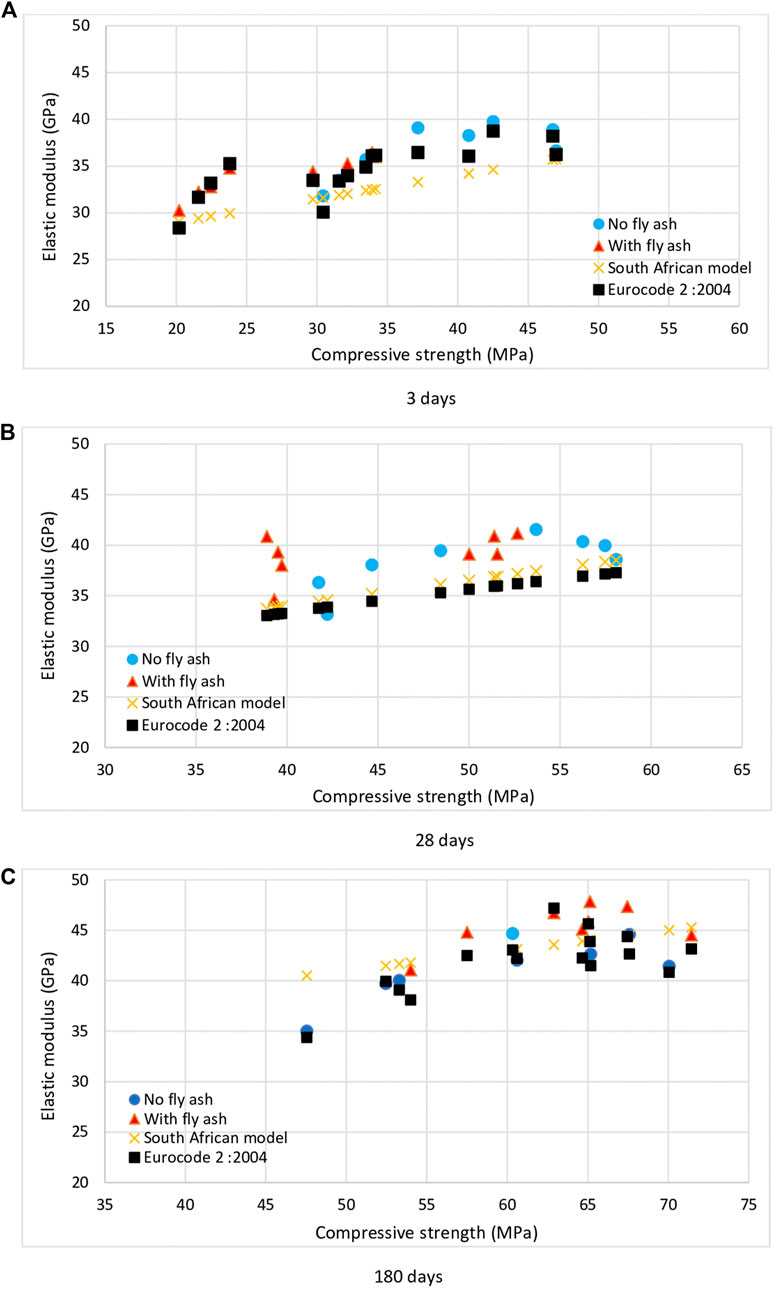
FIGURE 10. Relationship between elastic modulus and compressive strength of FRA concrete mixes at three test ages: (A) 3 days, (B) 28 days and (C) 180 days.
The South African model which is based on BS 8110-2, 1985, expresses elastic modulus as a function of concrete compressive strength and aggregate type (see Eq. (1)). This model was developed based on studies of local South African aggregates by Alexander, (1990), Alexander, (1991); Alexander and Davis, (1991), Alexander and Davis, (1992); (Beushausen et al., 2021b).
where E = elastic modulus in GPa at a given age.
α = coefficient that depends on the type of aggregate. For coarse greywacke aggregates at 3 days and 28 days,
The Eurocode 2 model is shown in Eqs 2, 3
where
For ages other than 28 days, Eurocode 2 gives the relationship:
where
From Figure 10A, it can be observed that at 3 days, the South African model underestimates the elastic modulus of FRA concrete, while the Eurocode model provides a better prediction, particularly for mixes containing fly ash. Figure 10B shows that at 28 days, both equations underestimate the elastic modulus of FRA concrete. In other words, the predicted 28-days elastic modulus using these models is less than the experimental elastic modulus for the same FRA concrete mix. From Figure 10C, it is observed that both the South African and Eurocode 2 models gave good prediction of the elastic modulus of FRA concrete.
From Figure 10, it is evident that further studies are required to correlate the elastic modulus and compressive strength of FRA concrete. Factors such as the volume and stiffness of FRA, the multiple interfacial bonds developed between the ACP, new mortar, and aggregates, as well as the densification action of binder on the ITZ of FRA concrete should be accounted for.
Conclusion
The study presented in this article used a multi-technique approach to enhance the properties of fine recycled aggregate concrete. These techniques included the systematic screening of FRA particles less than 1.18 mm to reduce the adhered cement paste content and the use of fly ash to modify the microstructure of FRA concrete. From the results of the study, the following conclusions can be drawn:
1 The rate of compressive strength gain, beyond 3 days for FRA concrete, is higher than NAC for up to 180 days of curing.
2 The ACP of FRA may increase the paste content of FRA concrete and subsequently increase the hydration and strength of FRA concrete, thereby making FRA concrete comparable to conventional concrete in the long term. The opposite effect is observed for elastic modulus, as an increase in FRA content increases the amount of porous phases—paste and ITZ—in the concrete matrix. At all test ages, elastic modulus decreased as the FRA replacement level increased.
3 Screening of the more porous and less stiff fine fractions of FRA, particles less than 1.18 mm, can improve the compressive strength and elastic modulus of FRA concrete.
4 The use of fly ash in FRA concrete can significantly enhance compressive strength and elastic modulus at 28 days and beyond. This is attributed to pozzolanic reactions between the alumina and silica of fly ash and the calcium hydroxide formed by Portland cement hydration. Additionally, the alumina content of fly ash reacts with the limestone in the cement to form hydrated aluminate phases which increase strength, particularly over long curing periods. Consequently, fly ash-treated FRA concrete will require a longer curing duration to optimize its benefits.
5 The combination of ACP reduction and fly ash treatment gave the most improvement in FRA concrete properties at 28 and 180 days of testing.
6 The South African model and Eurocode 2 model that correlate the elastic modulus and compressive strength of concrete are applicable to FRA concrete. However, further studies are required to account for factors that may affect the elastic modulus and compressive strength relationship of FRA concrete such as the volume and stiffness of FRA, the multiple interfacial bonds developed between the ACP, new mortar, and aggregates, as well as the densification action of binder on the ITZ of FRA concrete.
Data Availability Statement
The original contributions presented in the study are included in the article/Supplementary Material; further inquiries can be directed to the corresponding author.
Author Contributions
IA: lead author. HB: technical contributions and reviews. MA: technical contributions and reviews.
Funding
Concrete Materials and Structural Integrity Research Unit (CoMSIRU) provided the research funds. The research was carried out in the CoMSIRU laboratory. Postgraduate funding office (PGFO) provided financial assistance. The Electronic Research Administration (eRA) provided the publication fee.
Conflict of Interest
The authors declare that the research was conducted in the absence of any commercial or financial relationships that could be construed as a potential conflict of interest.
Publisher’s Note
All claims expressed in this article are solely those of the authors and do not necessarily represent those of their affiliated organizations, or those of the publisher, the editors, and the reviewers. Any product that may be evaluated in this article, or claim that may be made by its manufacturer, is not guaranteed or endorsed by the publisher.
Acknowledgments
The authors wish to thank the Postgraduate Funding Office (PGFO), University of Cape Town, for financial support.
Supplementary Material
The Supplementary Material for this article can be found online at: https://www.frontiersin.org/articles/10.3389/fmats.2022.893852/full#supplementary-material
References
Al-Bayati, H. K. A., Das, P. K., Tighe, S. L., and Baaj, H. (2016). Evaluation of Various Treatment Methods for Enhancing the Physical and Morphological Properties of Coarse Recycled Concrete Aggregate. Constr. Build. Mater. 112, 284–298. doi:10.1016/j.conbuildmat.2016.02.176
Alexander, M. G. (1991). An Experimental Critique of the BS 8110 Method of Estimating Concrete Elastic Modulus. Mag. Concr. Res. 43 (157), 291–304. doi:10.1680/MACR.1991.43.157.291
Alexander, M. G., and Davis, D. E. (1991). Aggregates in Concrete a New Assessment of Their Role. Concr. Beton 59, 10–20.
Alexander, M. G., and Davis, D. E. (1992). The Influence of Aggregates on the Compressive Strength and Elastic Modulus of Concrete. Civ. Eng. S. Afr. 34 (5), 161–170. doi:10.1002/j.1834-4461.1992.tb02391.x
Alexander, M. G. (1990). Properties of Aggregates in Concrete, Phase I and II, Research Reports Prepared for Hippo Quarries. Johannesburg, South Africa: University of the Witwatersrand, Department of Civil Engineering.
Angulo, S. C., Ulsen, C., John, V. M., Kahn, H., and Cincotto, M. A. (2009). Chemical-mineralogical Characterization of C&D Waste Recycled Aggregates from São Paulo, Brazil. Waste Manag. 29, 721–730. doi:10.1016/j.wasman.2008.07.009
Ann, K. Y., Moon, H. Y., Kim, Y. B., and Ryou, J. (2008). Durability of Recycled Aggregate Concrete Using Pozzolanic Materials. Waste Manag. 28 (6), 993–999. doi:10.1016/j.wasman.2007.03.003
Beushausen, H., Arito, P., van Zijl, G., and Alexander, M. G. (2021a). “Deformation and Volume Change of Hardened Concrete,” in Fulton’s Concrete Technology. Editor M. G. Alexander. 10th edn (Johannesburg, South Africa: Cement & Concrete SA), 265–342.
Beushausen, H., Otieno, M., and Alexander, M. G. (2021b). “Durability of Concrete,” in Fulton’s Concrete Technology. Editor M. G Alexander. 10th edn. (Johannesburg, South Africa: Cement & Concrete SA), 391–468.
Bianchini, G., Marrocchino, E., Tassinari, R., and Vaccaro, C. (2005). Recycling of Construction and Demolition Waste Materials: A Chemical-Mineralogical Appraisal. Waste Manag. 25, 149–159. doi:10.1016/j.wasman.2004.09.005
Broadbent, H. (2021). Top 25 Coal Power Countries in 2020 - Ember. Available at: https://ember-climate.org/commentary/2021/04/14/top-25-coal-power-countries-in-2020/(Accessed: February 17, 2022).
BS 8110-2 (1985). Structural Use of Concrete, Part 2: Code of Practice for Special Circumstances. London: British Standards Institution.
CarbonBrief (2022). Mapped: The World’s Coal Power Plants in 2020. Available at: https://www.carbonbrief.org/mapped-worlds-coal-power-plants (Accessed: March 27, 2022).
de Juan, M. S., and Gutiérrez, P. A. (2009). Study on the Influence of Attached Mortar Content on the Properties of Recycled Concrete Aggregate. Constr. Build. Mater. 23 (2), 872–877. doi:10.1016/j.conbuildmat.2008.04.012
De Weerdt, K., Haha, M. B., Le Saout, K. O., Justnes, H., and Lothenbach, B. (2011). Hydration Mechanisms of Ternary Portland Cements Containing Limestone Powder and Fly Ash. Cem. Concr. Res. 41 (3), 279–291. doi:10.1016/j.cemconres.2010.11.014
Department of Environmental Affairs (2018). South Africa State of Waste Report South Africa Second Draft Report. Pretoria: Department of Environmental Affairs.
Dilbas, H., Çakır, Ö., and Atiş, C. D. (2019). Experimental Investigation on Properties of Recycled Aggregate Concrete with Optimized Ball Milling Method. Constr. Build. Mater. 212, 716–726. doi:10.1016/j.conbuildmat.2019.04.007
Dimitriou, G., Savva, P., and Petrou, M. F. (2018). Enhancing Mechanical and Durability Properties of Recycled Aggregate Concrete. Constr. Build. Mater. 158, 228–235. doi:10.1016/j.conbuildmat.2017.09.137
du Toit, G., van der Merwe, E. M., Kruger, R. A., McDonald, J. M., and Kearsley, E. P. (2022). Characterisation of the Hydration Products of a Chemically and Mechanically Activated High Coal Fly Ash Hybrid Cement. Minerals 12 (157), 1–23. doi:10.3390/min12020157
Eurocode 2 (2004). Design of Concrete Structures - Part 1-1 : General Rules and Rules for Buildings. London: British Standards Institution.
Evangelista, L., and De Brito, J. (2014). Concrete with Fine Recycled Aggregates: A Review. Eur. J. Environ. Civ. Eng. 18 (2), 129–172. doi:10.1080/19648189.2013.851038
Fernández-Jiménez, A., Garcia-Lodeiro, I., Maltseva, O., and Palomo, A. (2019). Mechanical-chemical Activation of Coal Fly Ashes: An Effective Way for Recycling and Make Cementitious Materials. Front. Mat. 6 (April), 1–12. doi:10.3389/fmats.2019.00051
Ferreira, L., De Brito, J., and Barra, M. (2011). Influence of the Pre-saturation of Recycled Coarse Concrete Aggregates on Concrete Properties. Mag. Concr. Res. 63 (8), 617–627. doi:10.1680/macr.2011.63.8.617
García-Lodeiro, I., Fernández-Jiménez, A., and Palomo, A. (2013). Variation in Hybrid Cements over Time. Alkaline activation fly Portl. Cem. blends’, Cem. Concr. Res. 52, 112–122. doi:10.1016/j.cemconres.2013.03.022
Gavriletea, M. D. (2017). Environmental Impacts of Sand Exploitation. Analysis of Sand Market. Sustain. Switz. 9 (7), 1–26. doi:10.3390/su9071118
Ginga, C. P., Ongpeng, J. M. C., and Daly, M. K. M. (2020). Circular Economy on Construction and Demolition Waste: A Literature Review on Material Recovery and Production. Materials 13 (13), 2970–3018. doi:10.3390/ma13132970
Kisku, N., Joshi, H., Ansari, M., Panda, S. K., Nayak, S., and Dutta, S. C. (2017). A Critical Review and Assessment for Usage of Recycled Aggregate as Sustainable Construction Material. Constr. Build. Mater. 131, 721–740. doi:10.1016/j.conbuildmat.2016.11.029
Kong, D., Lei, T., Zheng, J., Ma, C., Jiang, J., and Jiang, J. (2010). Effect and Mechanism of Surface-Coating Pozzalanics Materials Around Aggregate on Properties and ITZ Microstructure of Recycled Aggregate Concrete. Constr. Build. Mater. 24 (5), 701–708. doi:10.1016/j.conbuildmat.2009.10.038
Kou, S.-c., Poon, C.-s., and Agrela, F. (2011). Comparisons of Natural and Recycled Aggregate Concretes Prepared with the Addition of Different Mineral Admixtures. Cem. Concr. Compos. 33 (8), 788–795. doi:10.1016/j.cemconcomp.2011.05.009
Kou, S.-C., and Poon, C.-S. (2009). Properties of Concrete Prepared with Crushed Fine Stone, Furnace Bottom Ash and Fine Recycled Aggregate as Fine Aggregates. Constr. Build. Mater. 23 (8), 2877–2886. doi:10.1016/j.conbuildmat.2009.02.009
Kou, S.-C., and Poon, C.-S. (2010). Properties of Concrete Prepared with PVA-Impregnated Recycled Concrete Aggregates. Cem. Concr. Compos. 2 (8), 649–654. doi:10.1016/j.cemconcomp.2010.05.003
Kou, S.-C., Zhan, B.-j., and Poon, C.-S. (2014). Use of a CO2 Curing Step to Improve the Properties of Concrete Prepared with Recycled Aggregates. Cem. Concr. Compos. 45, 22–28. doi:10.1016/j.cemconcomp.2013.09.008
Kou, S. C., Poon, C. S., and Chan, D. (2007). Influence of Fly Ash as Cement Replacement on the Properties of Recycled Aggregate Concrete. J. Mat. Civ. Eng. 19 (9), 709–717. doi:10.1061/(asce)0899-1561(2007)19:9(709)
Li, B., Hou, S., Duan, Z., Li, L., and Guo, W. (2021). Rheological Behavior and Compressive Strength of Concrete Made with Recycled Fine Aggregate of Different Size Range. Constr. Build. Mater. 268, 121172. doi:10.1016/j.conbuildmat.2020.121172
Li, J., Xiao, H., and Zhou, Y. (2009). Influence of Coating Recycled Aggregate Surface with Pozzolanic Powder on Properties of Recycled Aggregate Concrete. Constr. Build. Mater. 23 (3), 1287–1291. doi:10.1016/j.conbuildmat.2008.07.019
Li, L., Zhan, B. J., Lu, J., and Poon, C. S. (2019). Systematic Evaluation of the Effect of Replacing River Sand by Different Particle Size Ranges of Fine Recycled Concrete Aggregates (FRCA) in Cement Mortars. Constr. Build. Mater. 209, 147–155. doi:10.1016/j.conbuildmat.2019.03.044
Mdhluli, F. T., and Harding, K. G. (2021). Comparative Life-Cycle Assessment of Maize Cobs, Maize Stover and Wheat Stalks for the Production of Electricity through Gasification vs Traditional Coal Power Electricity in South Africa. Clean. Environ. Syst. 3, 100046. doi:10.1016/j.cesys.2021.100046
Pedro, D., de Brito, J., and Evangelista, L. (2015). Performance of Concrete Made with Aggregates Recycled from Precasting Industry Waste: Influence of the Crushing Process. Mater Struct. 48 (12), 3965–3978. doi:10.1617/s11527-014-0456-7
Pedro, D., de Brito, J., and Evangelista, L. (2017). Structural Concrete with Simultaneous Incorporation of Fine and Coarse Recycled Concrete Aggregates: Mechanical, Durability and Long-Term Properties. Constr. Build. Mater. 154, 294–309. doi:10.1016/j.conbuildmat.2017.07.215
Peduzzi, P. (2014). Sand, Rarer Than One Thinks. Article Reproduced from United Nations Environment Programme (UNEP) Global Environmental Alert Service (GEAS). Environ. Dev. 11, 208–218. doi:10.1016/j.envdev.2014.04.001
Poon, C.-S., Qiao, X. C., and Chan, D. (2006). The Cause and Influence of Self-Cementing Properties of Fine Recycled Concrete Aggregates on the Properties of Unbound Sub-base. Waste Manag. 26 (10), 1166–1172. doi:10.1016/j.wasman.2005.12.013
Poon, C. S., Shui, Z. H., Lam, L., Fok, H., and Kou, S. C. (2004). Influence of Moisture States of Natural and Recycled Aggregates on the Slump and Compressive Strength of Concrete. Cem. Concr. Res. 34 (1), 31–36. doi:10.1016/s0008-8846(03)00186-8
Ren, P., Li, B., Yu, J.-G., and Ling, T.-C. (2020). Utilization of Recycled Concrete Fines and Powders to Produce Alkali-Activated Slag Concrete Blocks. J. Clean. Prod. 267, 122115. doi:10.1016/j.jclepro.2020.122115
Rodrigues, F., Evangelista, L., and Brito, J. d. (2013). A New Method to Determine the Density and Water Absorption of Fine Recycled Aggregates. Mat. Res. 16 (5), 1045–1051. doi:10.1590/S1516-14392013005000074
Shi, C., Li, Y., Zhang, J., Li, W., Chong, L., and Xie, Z. (2016). Performance Enhancement of Recycled Concrete Aggregate - A Review. J. Clean. Prod. 112, 466–472. doi:10.1016/j.jclepro.2015.08.057
Spaeth, V., and Djerbi Tegguer, A. (2013). Improvement of Recycled Concrete Aggregate Properties by Polymer Treatments. Int. J. Sustain. Built Environ. 2 (2), 143–152. doi:10.1016/j.ijsbe.2014.03.003
Statista (2022). Number of Coal Power Plants by Country 2022. Available at: https://www.statista.com/statistics/859266/number-of-coal-power-plants-by-country/(Accessed: March 27, 2022).
Tam, V. W. Y., Butera, A., and Le, K. N. (2016). Carbon-conditioned Recycled Aggregate in Concrete Production. J. Clean. Prod. 133, 672–680. doi:10.1016/j.jclepro.2016.06.007
Tam, V. W. Y., Gao, X. F., and Tam, C. M. (2005). Microstructural Analysis of Recycled Aggregate Concrete Produced from Two-Stage Mixing Approach. Cem. Concr. Res. 35 (6), 1195–1203. doi:10.1016/j.cemconres.2004.10.025
Tam, V. W. Y., and Tam, C. M. (2008). Diversifying Two-Stage Mixing Approach (TSMA) for Recycled Aggregate Concrete: TSMAs and TSMAsc. Constr. Build. Mater. 22 (10), 2068–2077. doi:10.1016/j.conbuildmat.2007.07.024
Tam, V. W. Y., Tam, C. M., and Le, K. N. (2007). Removal of Cement Mortar Remains from Recycled Aggregate Using Pre-soaking Approaches. Resour. Conservation Recycl. 50 (1), 82–101. doi:10.1016/j.resconrec.2006.05.012
Thomas, M. (2007). Optimizing the Use of Fly Ash in Concrete. Skokie, Illinois: Portland Cement Association, 24.
Torres, A., Brandt, J., Lear, K., and Liu, J. (2017). A Looming Tragedy of the Sand Commons. Science 357 (6355), 970–971. doi:10.1126/science.aao0503
Ulsen, C., Kahn, H., Hawlitschek, G., Masini, E. A., Angulo, S. C., and John, V. M. (2013). Production of Recycled Sand from Construction and Demolition Waste. Constr. Build. Mater. 40, 1168–1173. doi:10.1016/j.conbuildmat.2012.02.004
Varadhan, S., and Sheldrick, A. (2021). COP26 Aims to Banish Coal. Asia Is Building Hundreds of Power Plants to Burn it. Available at: https://www.reuters.com/business/energy/cop26-aims-banish-coal-asia-is-building-hundreds-power-plants-burn-it-2021-10-29/(Accessed: March 27, 2022).
Wang, H.-l., Wang, J.-J., Sun, X.-Y., and Jin, W.-L. (2013). Improving Performance of Recycled Aggregate Concrete with Superfine Pozzolanic Powders. J. Cent. South Univ. 20 (12), 3715–3722. doi:10.1007/s11771-013-1899-7
Wang, J., Zhang, J., Cao, D., Dang, H., and Ding, B. (2020). Comparison of Recycled Aggregate Treatment Methods on the Performance for Recycled Concrete. Constr. Build. Mater. 234, 117366. doi:10.1016/j.conbuildmat.2019.117366
Zhang, J., Shi, C., Li, Y., Pan, X., Poon, C., and Xie, Z. (2015). Performance Enhancement of Recycled Concrete Aggregates through Carbonation. J. Mater. Civ. Eng. 27 (5), 04015029-7. doi:10.1061/(ASCE)MT.1943-5533.0001296
Keywords: fine recycled aggregates, fly ash, compressive strength, elastic modulus, porosity, enhancement
Citation: Amadi IG, Beushausen H and Alexander MG (2022) Multi-Technique Approach to Enhance the Properties of Fine Recycled Aggregate Concrete. Front. Mater. 9:893852. doi: 10.3389/fmats.2022.893852
Received: 10 March 2022; Accepted: 25 April 2022;
Published: 08 June 2022.
Edited by:
Neven Ukrainczyk, Darmstadt University of Technology, GermanyReviewed by:
Diego Said Schicchi, Independent researcher, Basque Country, SpainDidier Snoeck, Université libre de Bruxelles, Belgium
Prannoy Suraneni, University of Miami, United States
Copyright © 2022 Amadi, Beushausen and Alexander. This is an open-access article distributed under the terms of the Creative Commons Attribution License (CC BY). The use, distribution or reproduction in other forums is permitted, provided the original author(s) and the copyright owner(s) are credited and that the original publication in this journal is cited, in accordance with accepted academic practice. No use, distribution or reproduction is permitted which does not comply with these terms.
*Correspondence: I. G. Amadi, YW1kaWNoMDAxQG15dWN0LmFjLnph