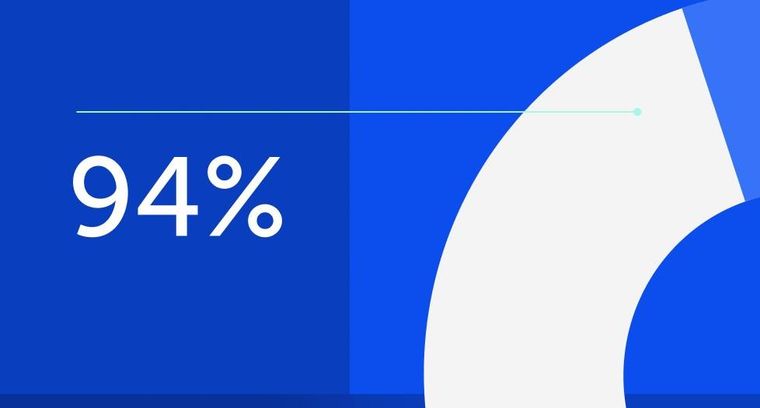
94% of researchers rate our articles as excellent or good
Learn more about the work of our research integrity team to safeguard the quality of each article we publish.
Find out more
MINI REVIEW article
Front. Mater., 01 April 2022
Sec. Mechanics of Materials
Volume 9 - 2022 | https://doi.org/10.3389/fmats.2022.889771
This article is part of the Research TopicHigh entropy alloy design concept enabled emerging novel materials with enhanced mechanical propertiesView all 7 articles
Introduction of high entropy alloys or multi-principal element alloys around 15 years ago motivated revising conventional alloy design strategies and proposed new ways for alloy development. Despite significant research since then, the potential for new material discoveries using the MPEA concept has hardly been scratched. Given the number of available elements and the vastness of possible composition combinations, an unlimited number of alloys are waiting to be investigated! Discovering novel high-performance materials can be like finding a needle in a haystack, which demands an enormous amount of time and computational capacity. To overcome the challenge, a systematic approach is essential to meet the growing demand for developing novel high-performance or multifunctional materials. This article aims to briefly review the challenges, recent progress and gaps, and future outlook in accelerated alloy development, with a specific focus on computational high-throughput (HT) screening methods integrated with the Calculation of Phase Diagrams (CALPHAD) technique.
Alloy development is one of the main pillars of technological advancement in many strategic sectors such as energy and transportation. Concerning structural applications, conventional alloy development strategies include various strengthening mechanisms such as grain boundary strengthening, work-hardening, solid solution strengthening and transformation strengthening. With increasing demands for new technologies, such material design strategies seem to be reaching their intrinsic limits, and there has been a need to revise the material development routines. Introduction of high entropy alloys (HEAs) or multi-principal element alloys (MPEAs) in 2004 (Yeh et al., 2004; Cantor et al., 2004), with their exceptional properties, motivated revisiting conventional alloy design strategies and offered new ways for alloy design and development. Traditionally, HEAs were defined as alloy systems with increased entropy that favours a thermodynamically stable single-phase solid solutions with equal proportions of five or more principal elements. Later, non-equimolar multi-principal compositions also showed great potential, which led to a more “relaxed” term of MPEA or compositionally complex alloys (CCA), including more multi-phase alloys with “slightly decreased configurational entropy” compared to HEAs (Pradeep et al., 2015). As an example, Miracle et al. (2014) elaborated the essence of developing HEAs containing particles as a secondary strengthening mechanism that is crucial for improved high-temperature stability, especially for structural applications in the transportation and energy sectors. Given the vastness of composition-particle combinations, this suggests an astronomical number of alloys waiting to be discovered and investigated.
Despite significant research efforts since 2004, the potential for new material discoveries using the MPEA concept has hardly been scratched! As Miracle et al. (Miracle et al., 2014) stated, “the vastness (of opportunities) is frightening, and it beckons”! This vastness offers excellent potential for new discoveries, but at the same time, it is the biggest obstacle for alloy design since it demands an enormous amount of time and computational capacity even before proceeding to the experimental validation.
In the industrial context, imagine a case for developing existing lightweight alloys (e.g., Al-Si alloys) for mechanical stability at elevated temperatures; a fascinating research question. But considering the vastness of compositional space (elemental choices and the amount for each element to be added/modified in the composition), the alloy modification/development will be a very tedious and time-consuming job.
Systematic accelerated metallurgy is essential to meet the growing demand for developing novel high-performance or multifunctional materials. The current article briefly reviews the challenges, recent progress and gaps, and future outlook in accelerated alloy development with a specific focus on computational high-throughput screening methods integrated with the Calculation of Phase Diagrams (CALPHAD) technique.
Data-driven modelling and machine learning (ML) can offer the possibility to extract sound and sometimes unexpected results from sparse datasets. ML methods have been gaining interest due to their intrinsic ability to construct complex non-linear relationships between input and output data. Recent developments in ML for alloy design have been appealing with the promise of exploring the phase formation, phase stability and properties of metallic materials (Abu-Odeh et al., 2018; Qu et al., 2019; Qiao et al., 2021a; Choi et al., 2021; Li et al., 2021; Nassar and Mullis, 2021; Xiong et al., 2021; Zhao et al., 2021; Yang et al., 2022), as well as processability of the alloys such as castability and 3D printability (Seede et al., 2021). These methods usually provide a reasonable calculation accuracy of typically >85%. As an example, Subedi et al. (2021) have recently developed a python-based multi-principal element alloys laboratory toolkit based on an artificial neural network (ANN) to predict phase formation in MPEAs. The toolkit was claimed to be able to predict phase formations in MPEAs based on the given composition and properties of the constituent elements. Besides ANNs, other machine learning models such as support vector machines (SVMs) and decision trees (DTs) have been widely used in literature (Frydrych et al., 2021). New methods such as deep learning (DL) has also been gaining attention, eventually making machine learning a promising tool for material discovery, as well as material property prediction (Qiao et al., 2021a). Generally, unsupervised ML aims at finding the internal structure and the relationship among data, and supervised ML is used to compare the prediction results with the actual training data. Learning-based models can predict properties of undiscovered materials and thus could be used as an efficient tool to bypass direct experiments or calculations for exploring the territory of unknown materials (Jin et al., 2021; Wu et al., 2022). One of the main challenges in ML, though, is that the credibility partly depends on the vastness of training data, for which a combination of experimental and simulation data could be used. The main drawback of ML, in general, is the limited explored composition spaces based on experimental data (Sorkin et al., 2021a; Zeng et al., 2021).
ML can be combined with any calculation method, such as empirical models, CALPHAD, and DFT, to rapidly screen and predict properties. Some recent examples are provided here. Zeng et al. (2021) combined ML and CALPHAD to explore the selection rules of single FCC and BCC phases of HEAs. Arora and Aidhy (2020) used ML and DFT to predict the Stacking Fault Energy (SFE) based on the alloy composition. Yan et al. (2021) used ML combined with empirical models to design single-phase refractory HEAs (R-HEAs) for high-temperature applications and elaborated the relative importance of different empirical models for designing R-HEAs. Huang et al. (Huang et al., 2021) used ML combined with empirical models to study the effect of solid solution hardening on the overall mechanical behaviour of HEAs. Guo et al. (2021) proposed integrating Molecular Dynamic (MD), ML and generic algorithms for predicting the stiffness and critical resolved shear stress of HEAs. Dewangan and Kumar (2022) recently used ANN to predict high-temperature oxidation behaviour in HEAs.
Each calculation method has its own uncertainty that is added to that of the ML; e.g., first-principle calculations sometimes have a disagreement with experiment or even CALPHAD. The reasons for this disagreement is still controversial, but it could be partly due to the sluggish diffusion in HEAs that makes it difficult for the alloy to reach the “equilibrium” state. These challenges, along with the essence for further improving calculations’ credibility and extending the screening methods to non-equiatomic compositions, is an urgent and exciting research topic for more profound development.
Although powerful, to become efficient tools for accelerated alloy design, ML methods require a boost both for rapid validation and for providing the data for training. Computational and experimental high-throughput (HT) screening methods are powerful tools to overcome these challenges.
While there has been some progress in computational HT screening, the experimental HT (HT alloy production and testing) requires much more development to reach the same level of maturity. For computational HT, ongoing efforts try to integrate novel machine learning and artificial intelligence with alloy design models; calculations can be conducted in various scales from atomic (first principle, such as density functional theory; DFT) to nano/micro (Molecular Dynamics; MD), micro/macro (CALPHAD), and macro (Finite Element Modelling; FEM) (Lederer et al., 2018; Li et al., 2020; Qiao et al., 2021a; Sorkin et al., 2021b; Yaqi, 2021). Table 1 summarises the capabilities and limitations of each method and the typical scale each method is applicable in. Combining these methods would provide a superior multi-scale modelling toolkit for material discovery, although the associated cost and required computational power remain a challenge.
TABLE 1. Capabilities, limitations and the applicable scale for different modelling techniques used for alloy design.
HT screening has been developed and is more mature for functional materials such as magnetoelectrics, batteries, and photovoltaics (Hautier et al., 2010; Potyrailo et al., 2011; Chaudhary et al., 2021; Tu et al., 2022). For structural materials, these techniques require more development (Gao and Alman, 2013), while the main challenge is that besides the composition and phase fractions, structural properties also depend on microstructural coarseness and distribution of various phases.
One of the most commonly used and less costly calculation methods with a relatively good level of credibility is HT combined with CALPHAD (Zeng et al., 2021). CALPHAD is a very versatile semi-empirical tool. Many structural applications are related to phase formation and stability that can be evaluated using CALPHAD. It is also proven that CALPHAD can significantly reduce the number of experimental trials for discovering new alloys (Tazuddin et al., 2017).
The HT-CALPHAD technique has been used for developing various types of alloys, such as alloys with an austenitic matrix containing a secondary coherent phase that is stable at a wide range of temperatures (Tripathi et al., 2021), screening for alloys containing solid-solution (SS), intermetallic (IM), and SS + IM phases (Senkov et al., 2015a), HEAs with stable disordered single phases at low temperatures (Klaver et al., 2018), and to developing lightweight HEAs (Asadikiya et al., 2021).
In the following section, we present an overview of various steps for conducting HT-CALPHAD.
HT-CALPHAD can be divided into four distinct steps, as depicted in Figure 1.
Senkov et al. (2015b) and Miracle et al. (2014) suggested the first step for HT screening to be defining a palette of elements. A typical master list of non-toxic, non-gaseous and non-radioactive elements leads to a total of ∼57 elements. The alloy application can further shorten the list. For instance, if the target is high-temperature applications, the low melting point elements (e.g., Tm< 700 K) shall be excluded, which reduces the list to 45 elements. Only considering equimolar HEAs, this list of elements gives 106 possible 5-element compositions and 1011 possible 13-element compositions to be discovered and/or investigated. Including non-equimolar and multi-phase composition will easily lead to an almost endless number of possibilities! To date, it is estimated that less than 2000 MPEAs have been reported in the literature, which is just a tiny fraction of millions of possible compositions to be discovered. We normally choose a smaller set of elements for specific applications, which is called the “palette of elements” by Miracle (Miracle et al., 2014). The elements can be ranked within the palette based on their physical properties such as density, melting point, bonding energy, etc. This will give a better perspective on combining elements for specific applications, e.g., low density and high working temperature (high melting point). The ranking of elements can also be correlated to the processability of the alloys (castability, printability, etc.); for instance, alloys containing elements with a significantly different melting point might possess wide solidification intervals that in turn could lead to segregation or other casting/3D-printing defects (Qiao et al., 2021b). Very different atomic sizes might also lead to excessively strained crystal lattices that add to the residual stress after casting, 3D printing or welding.
The next step is to build the compositions from the palette of elements and evaluate them using CALPHAD. The number of compositions to be calculated would depend on the range of each element at%, the incremental step size of each element. The number of CALPHAD calculations also depends on the temperature range and the respective step size. In the algorithm we have been recently developing (Conway et al., 2022), the built compositions will be fed to the ThermoCalc software as a macro file (Python interface). Depending on the desired results, different modules of the ThermoCalc could be engaged in HT calculations.
This step aims not to evaluate all possible compositions but to quickly scan the interested palette and compositional range and identify workable subsets with the potential to be deeper evaluated. Recent developments in related software packages have facilitated such evaluations, e.g., TC-Python framework in Thermo-Calc (Yang et al., 2020; Tripathi et al., 2021).
An enormous amount of data could be extracted from the previous step, such as solidus temperature, solidification intervals, phase formation and stability at various temperatures, phase fractions, composition and lattice parameters of phases, solutionising window, etc. These results as a dataset will be used for ranking the compositions into islands of selected compositions. Based on the set criteria for alloy design and expected properties, the center of these compositional islands is selected (Conway et al., 2022). It is important to note that the screening may contain false-negative results (false rejection of compositions with development potential), which can be a concern since the very spirit of identifying potentially exceptional alloys may be hampered. Having false-positive results (compositions that have no potential for development) is also of great concern because more resources would be needed to deeper evaluate wrong results.
It is also important to note that the credibility of CALPHAD calculations must be considered for predictions. Senkov et al. (2015b) suggested a method to quantify the credibility of CALPHAD calculations. They looked at the available binary and ternary phase diagrams in the CALPHAD databases, through which they calculated the fraction of assessed binary diagrams (FAB) and the fraction of assessed ternary phase diagrams (FAT). The higher the FAB and FAT, the more credible the CALPHAD calculations would be. Ideally, the aim is to have FAB equal to one for reliable calculations. But it is common to have FAT less than one. It is debatable to state what shall be the acceptable value for FAB and FAT. According to the literature, it is reasonable to keep a minimum FAT value of 0.6 as followed in (Senkov et al., 2015b; Zeng et al., 2021). This is suggested to be considered as a decision-making factor for selecting which CALPHAD database to use and also a rejection factor for final compositions. It is to be noted that even usage of a database with a high FAT value has also occasionally reported discrepancies compared to experiments (Guruvidyathri et al., 2017), partly due to the deviation from the equilibrium states in real conditions.
Depending on the application, different rejection criteria could be set; e.g., for high-temperature applications, Miracle et al. (2014) and Senkov et al. (2015a) suggested having the solvus temperature of the alloy above its working temperature and having no first order phase transformation below the operating temperature, as the main decision-making criterion (Feng et al., 2021). Other physical properties of the alloy, such as density, elastic modulus or even cost of elements [rule of mixture (Senkov et al., 2015b)], and more importantly, sustainability factors, can also be used to narrow the selection criteria.
While we can extract ideal compositions within a multi-dimensional space, visualisation of the results is one of the most challenging steps because the multi-dimensional composition space is not easily imaginable in a 3D framework. Miracle and Senkov (2017) have suggested a few visual devices to tackle this challenge in 2D and 3D. However, the interpretation of results using these alternatives is not straightforward. Visualisation of mutli-dimensional space is a research field on its own, with most solutions typically reducing the importance of specific axis to colours or shapes in a 2D or 3D plot (Lowe and Matthee, 2020). This is still insufficient in alloy development as each axis typically carries equal importance. Artificial intelligence could provide a solution for transforming the hyper-dimensional results to 3D (Ventocilla and Riveiro, 2020).
Gorsse et al. (2017) conducted an alloy network analysis to categorise the alloys based on their intrinsic properties and/or desired application. Their method can be used as either a visual tool for elemental selection or an alternative for visualisation of the HT-CALPHAD results. An intermediate alternative we have proposed recently (Conway et al., 2022) includes binary visualisation of pair of elements.
A typical impression is that such HT calculations require sophisticated supercomputers or very high-performance computers. New codings have been developed to facilitate such calculations in conventional high-performance computers. Recently, we further developed the screening method initially proposed by Klaver et al. (2018), for screening and modifying the composition of equimolar HEAs to reduce the elemental costs and alloy density while maintaining the mechanical properties of the equimolar HEAs (Conway et al., 2022). Python coding was used to build the composition sets and create the macro files for ThermoCalc software. Using a typical 64 core computer, we have been able to conduct CALPHAD for ∼ a million compositions in a relatively wide range of temperatures in the course of only 2–3 days. This provides a flexible, quick, and relatively inexpensive method for alloy screening leading to a comprehensive dataset as results. We selected the optimum compositions as per the center of the “islands” of the compositional spaces, as suggested in reference (Klaver et al., 2018). Our HT algorithms are being further developed beyond just phase diagram calculations, and the aim is to integrate other ThermoCalc modules for precipitation and diffusion calculations. We are also expanding the codes for simultaneous calculation of other empirical models such as solid solution hardening, SFE, and other physical properties like density and elastic modulus.
For experimental HT screening, new processing routes such as rapid alloy prototyping (Springer and Raabe, 2012), laser engineered net shaping (LENS) (Chaudhary et al., 2021), additive manufacturing (Vecchio et al., 2021) or preparing diffusion multiples (Wang et al., 2021), offer a good level of flexibility for producing chemical gradients (a number of alloy compositions) in a single sample to be characterised. Micro/nano-indentation on the diffusion multiples (Wang et al., 2021) or on micro-pillars could be a tool for evaluating the mechanical responses of the material (Miracle and Senkov, 2017). Nonetheless, these methods still do not provide the required speed and flexibility for various alloy development schemes. The demands for developing MPEAs is a great motivation and ideal platform for improving both computational and experimental HT techniques.
For HT-CALPHAD, it is crucial to improve the credibility by including more elements and more binary and ternary phase diagrams into databases.
Combining data-driven machine learning, artificial intelligence, and multi-scale simulation would be an excellent tool for correlating the composition and properties.
There are various degradation mechanisms in materials that are to be understood thoroughly as the base to define the criteria for material discovery for various applications, e.g., hydrogen-embrittlement resistance or high-performance catalysts for fuel-cells to improve efficiency and reduce the cost of hydrogen production.
Other empirical models can be integrated into HT-CALPHAD to strengthen the resultant dataset, such as solid solution hardening models, SFE calculation models, alloy costs, and sustainability aspects. To improve the credibility of calculations, it is required to revisit the empirical models and validate the accuracy.
Conceptualization, idea development, and the original draft preparation: EG; Visualization and revision of the manuscript PC.
The authors acknowledge the Strategic Innovation Program (SIP) Metalliska Material and Vinnova (projects ALigHT II, # 2018-02379; ALL4HYDRO # 2021-01918) and Knowledge Foundation (KK-Stiftelsen) (project NOVELA II, # 20200216), as well as the industrial partners for financially supporting the research and education environment on Knowledge Intensive Product Realization (SPARK) at Jönköping University, Sweden.
The authors declare that the research was conducted in the absence of any commercial or financial relationships that could be construed as a potential conflict of interest.
All claims expressed in this article are solely those of the authors and do not necessarily represent those of their affiliated organizations, or those of the publisher, the editors, and the reviewers. Any product that may be evaluated in this article, or claim that may be made by its manufacturer, is not guaranteed or endorsed by the publisher.
Abu-Odeh, A., Galvan, E., Kirk, T., Mao, H., Chen, Q., Mason, P., et al. (2018). Efficient Exploration of the High Entropy Alloy Composition-phase Space. Acta Materialia 152, 41–57. doi:10.1016/j.actamat.2018.04.012
Arora, G., and Aidhy, D. S. (2020). Machine Learning Enabled Prediction of Stacking Fault Energies in Concentrated Alloys, 10.Metals
Asadikiya, M., Yang, S., Zhang, Y., Lemay, C., Apelian, D., and Zhong, Y. (2021). A Review of the Design of High-Entropy Aluminum Alloys: a Pathway for Novel Al Alloys. J. Mater. Sci. 56, 12093–12110. doi:10.1007/s10853-021-06042-6
Cantor, B., Chang, I. T. H., Knight, P., and Vincent, A. J. B. (2004). Microstructural Development in Equiatomic Multicomponent Alloys. Mater. Sci. Eng. A 375-377, 213–218. doi:10.1016/j.msea.2003.10.257
Chaudhary, V., Chaudhary, R., Banerjee, R., and Ramanujan, R. V. (2021). Accelerated and Conventional Development of Magnetic High Entropy Alloys. Mater. Today 49, 231–252. doi:10.1016/j.mattod.2021.03.018
Choi, S., Yi, S., Kim, J., Shin, B., and Hyun, S. (2021). High-Entropy Alloys Properties Prediction Model by Using Artificial Neural Network Algorithm. Metals, 11. doi:10.3390/met11101559
Conway, P. L. J., Klaver, T. P. C., Steggo, J., and Ghassemali, E. (2022). High Entropy Alloys towards Industrial Applications: High-Throughput Screening and Experimental Investigation. Mater. Sci. Eng. A 830. doi:10.1016/j.msea.2021.142297
Dewangan, S. K., and Kumar, V. (2022). Application of Artificial Neural Network for Prediction of High Temperature Oxidation Behavior of AlCrFeMnNiWx (X = 0, 0.05, 0.1, 0.5) High Entropy Alloys. Int. J. Refractory Met. Hard Mater. 103. doi:10.1016/j.ijrmhm.2022.105777
Feng, R., Zhang, C., Gao, M. C., Pei, Z., Zhang, F., Chen, Y., et al. (2021). High-throughput Design of High-Performance Lightweight High-Entropy Alloys. Nat. Commun. 12, 4329. doi:10.1038/s41467-021-24523-9
Frydrych, K., Karimi, K., Pecelerowicz, M., Alvarez, R., Dominguez-Gutierrez, F. J., Rovaris, F., et al. (2021). Materials Informatics for Mechanical Deformation: A Review of Applications and Challenges, 14.Materials (Basel)
Gao, M., and Alman, D. (2013). Searching for Next Single-phase High-Entropy Alloy Compositions. Entropy 15, 4504–4519. doi:10.3390/e15104504
Gorsse, S., Miracle, D. B., and Senkov, O. N. (2017). Mapping the World of Complex Concentrated Alloys. Acta Materialia 135, 177–187. doi:10.1016/j.actamat.2017.06.027
Guo, T., Wu, L., and Li, T. (2021). Machine Learning Accelerated, High Throughput, Multi-Objective Optimization of Multiprincipal Element Alloys. Small 17, e2102972. doi:10.1002/smll.202102972
Guruvidyathri, K., Hari Kumar, K. C., Yeh, J. W., and Murty, B. S. (2017). Topologically Close-Packed Phase Formation in High Entropy Alloys: A Review of Calphad and Experimental Results. Jom 69, 2113–2124. doi:10.1007/s11837-017-2566-5
Hautier, G., Fischer, C. C., Jain, A., Mueller, T., and Ceder, G. (2010). Finding Nature's Missing Ternary Oxide Compounds Using Machine Learning and Density Functional Theory. Chem. Mater. 22, 3762–3767. doi:10.1021/cm100795d
Huang, X., Jin, C., Zhang, C., Zhang, H., and Fu, H. (2021). Machine Learning Assisted Modelling and Design of Solid Solution Hardened High Entropy Alloys, 211.Materials and Design
Jin, T., Park, I., Park, T., Park, J., and Shim, J. H. (2021). Accelerated crystal Structure Prediction of Multi-Elements Random alloy Using Expandable Features. Sci. Rep. 11, 5194. doi:10.1038/s41598-021-84544-8
Klaver, T. P. C., Simonovic, D., and Sluiter, M. H. F. (2018). Brute Force Composition Scanning with a CALPHAD Database to Find Low Temperature Body Centered Cubic High Entropy Alloys, Entropy (Basel) 20, 911. doi:10.3390/e20120911
Lederer, Y., Toher, C., Vecchio, K. S., and Curtarolo, S. (2018). The Search for High Entropy Alloys: A High-Throughput Ab-Initio Approach. Acta Materialia 159, 364–383. doi:10.1016/j.actamat.2018.07.042
Li, J., Xie, B., Fang, Q., Liu, B., Liu, Y., and Liaw, P. K. (2021). High-throughput Simulation Combined Machine Learning Search for Optimum Elemental Composition in Medium Entropy alloy. J. Mater. Sci. Technol. 68, 70–75. doi:10.1016/j.jmst.2020.08.008
Li, R., Xie, L., Wang, W. Y., Liaw, P. K., and Zhang, Y. (2020). High-Throughput Calculations for High-Entropy Alloys: A Brief Review. Front. Mater. 7. doi:10.3389/fmats.2020.00290
Miracle, D. B., and Senkov, O. N. (2017). A Critical Review of High Entropy Alloys and Related Concepts. Acta Materialia 122, 448–511. doi:10.1016/j.actamat.2016.08.081
Miracle, D., Miller, J., Senkov, O., Woodward, C., Uchic, M., and Tiley, J. (2014). Exploration and Development of High Entropy Alloys for Structural Applications. Entropy 16, 494–525. doi:10.3390/e16010494
Nassar, A. E., and Mullis, A. M. (2021). Rapid Screening of High-Entropy Alloys Using Neural Networks and Constituent Elements. Comput. Mater. Sci. 103, 199. doi:10.1016/j.commatsci.2021.110755
Potyrailo, R., Rajan, K., Stoewe, K., Takeuchi, I., Chisholm, B., and Lam, H. (2011). Combinatorial and High-Throughput Screening of Materials Libraries: Review of State of the Art. ACS Comb. Sci. 13, 579–633. doi:10.1021/co200007w
Pradeep, K. G., Tasan, C. C., Yao, M. J., Deng, Y., Springer, H., and Raabe, D. (2015). Non-equiatomic High Entropy Alloys: Approach towards Rapid alloy Screening and Property-Oriented Design. Mater. Sci. Eng. A 648, 183–192. doi:10.1016/j.msea.2015.09.010
Qiao, L., Bao, A., Lai, Z., Liu, Y., Zhu, J., and Wang, Y. (2021b). Alloy Design and Properties Optimization of Multi-Component alloy Based on Solidification Characteristics. Mater. Sci. Eng. A 877, 805. doi:10.1016/j.msea.2020.140576
Qiao, L., Liu, Y., and Zhu, J. (2021a). A Focused Review on Machine Learning Aided High-Throughput Methods in High Entropy alloy. J. Alloys Compd., 877. doi:10.1016/j.jallcom.2021.160295
Qu, N., Chen, Y., Lai, Z., Liu, Y., and Zhu, J. (2019). The Phase Selection via Machine Learning in High Entropy Alloys. Proced. Manufacturing 37, 7. doi:10.1016/j.promfg.2019.12.051
Seede, R., Ye, J., Whitt, A., Trehern, W., Elwany, A., Arroyave, R., et al. (2021). Effect of Composition and Phase Diagram Features on Printability and Microstructure in Laser Powder Bed Fusion: Development and Comparison of Processing Maps across alloy Systems. Additive Manufacturing 47. doi:10.1016/j.addma.2021.102258
Senkov, O. N., Miller, J. D., Miracle, D. B., and Woodward, C. (2015). Accelerated Exploration of Multi-Principal Element Alloys for Structural Applications. Calphad 50, 32–48. doi:10.1016/j.calphad.2015.04.009
Senkov, O. N., Miller, J. D., Miracle, D. B., and Woodward, C. (2015). Accelerated Exploration of Multi-Principal Element Alloys with Solid Solution Phases. Nat. Commun. 6, 6529. doi:10.1038/ncomms7529
Sorkin, V., Chen, S., Tan, T. L., Yu, Z. G., Man, M., and Zhang, Y. W. (2021b). First-principles-based High-Throughput Computation for High Entropy Alloys with Short Range Order. J. Alloys Compd. 882. doi:10.1016/j.jallcom.2021.160776
Sorkin, V., Tan, T. L., Yu, Z. G., and Zhang, Y. W. (2021a). High-throughput Calculations Based on the Small Set of Ordered Structures Method for Non-equimolar High Entropy Alloys. Comput. Mater. Sci. 188. doi:10.1016/j.commatsci.2020.110213
Springer, H., and Raabe, D. (2012). Rapid alloy Prototyping: Compositional and Thermo-Mechanical High Throughput Bulk Combinatorial Design of Structural Materials Based on the Example of 30Mn-1.2C-xAl Triplex Steels. Acta Materialia 60, 4950–4959. doi:10.1016/j.actamat.2012.05.017
Subedi, U., Kunwar, A., Coutinho, Y. A., and Gyanwali, K. (2021). pyMPEALab Toolkit for Accelerating Phase Design in Multi-Principal Element Alloys. Met. Mater. Int. 28, 269–281. doi:10.1007/s12540-021-01100-9
Tazuddin, N. P. G., Gurao, N. P., and Biswas, K. (2017). In the Quest of Single Phase Multi-Component Multiprincipal High Entropy Alloys. J. Alloys Compd. 697, 434–442. doi:10.1016/j.jallcom.2016.11.383
Tripathi, S., Fan, L. C., Titus, M. S., and Strachan, A. (2021). Automated Approach to Discover Coherent Precipitates in Multi-Component Shape Memory Alloys. Comput. Mater. Sci. 197. doi:10.1016/j.commatsci.2021.110651
Tu, D., Yan, J., Xie, Y., Li, J., Feng, S., Xia, M., et al. (2022). Accelerated Design for Magnetocaloric Performance in Mn-Fe-P-Si Compounds Using Machine Learning. J. Mater. Sci. Technol. 96, 241–247. doi:10.1016/j.jmst.2021.03.082
Vecchio, K. S., Dippo, O. F., Kaufmann, K. R., and Liu, X. (2021). High-throughput Rapid Experimental alloy Development (HT-READ). Acta Materialia 221. doi:10.1016/j.actamat.2021.117352
Ventocilla, E., and Riveiro, M. (2020). A Comparative User Study of Visualization Techniques for Cluster Analysis of Multidimensional Data Sets. Inf. Visualization 19, 318–338. doi:10.1177/1473871620922166
Wang, Z., Zhang, L., Li, W., Qin, Z., Wang, Z., Li, Z., et al. (2021). A High-Throughput Approach to Explore the Multi-Component alloy Space: A Case Study of Nickel-Based Superalloys. J. Alloys Compd. 858. doi:10.1016/j.jallcom.2020.158100
Wu, C.-T., Lin, P.-H., Huang, S.-Y., Tseng, Y.-J., Chang, H.-T., Li, S.-Y., et al. (2022). Revisiting alloy Design of Low-Modulus Biomedical β-Ti Alloys Using an Artificial Neural Network, 21.Materialia
Xiong, J., Shi, S.-Q., and Zhang, T.-Y. (2021). Machine Learning of Phases and Mechanical Properties in Complex Concentrated Alloys. J. Mater. Sci. Technol. 87, 133–142. doi:10.1016/j.jmst.2021.01.054
Yan, Y., Lu, D., and Wang, K. (2021). Accelerated Discovery of Single-phase Refractory High Entropy Alloys Assisted by Machine Learning. Comput. Mater. Sci., 199. doi:10.1016/j.commatsci.2021.110723
Yang, C., Ren, C., Jia, Y., Wang, G., Li, M., and Lu, W. (2022). A Machine Learning-Based alloy Design System to Facilitate the Rational Design of High Entropy Alloys with Enhanced Hardness. Acta Materialia, 222. doi:10.1016/j.actamat.2021.117431
Yang, S., Lu, J., Xing, F., Zhang, L., and Zhong, Y. (2020). Revisit the VEC Rule in High Entropy Alloys (HEAs) with High-Throughput CALPHAD Approach and its Applications for Material Design-A Case Study with Al-Co-Cr-Fe-Ni System. Acta Materialia 192, 11–19. doi:10.1016/j.actamat.2020.03.039
Yaqi, W. (2021). Design and High-Throughput Screening of High Entropy Alloys. London, UK: Intechopen.
Yeh, J.-W., Chen, S.-K., Lin, S.-J., Gan, J.-Y., Chin, T.-S., Shun, T.-T., et al. (2004). Nanostructured High-Entropy Alloys with Multiple Principal Elements: Novel alloy Design Concepts and Outcomes. Adv. Eng. Mater. 6, 299–303. doi:10.1002/adem.200300567
Zeng, Y., Man, M., Bai, K., and Zhang, Y.-W. (2021). Revealing High-Fidelity Phase Selection Rules for High Entropy Alloys: A Combined CALPHAD and Machine Learning Study 202. Materials & Design
Keywords: phase diagram, high-throughput approaches, alloy design, high entropy alloy, machine learning
Citation: Ghassemali E and Conway PLJ (2022) High-Throughput CALPHAD: A Powerful Tool Towards Accelerated Metallurgy. Front. Mater. 9:889771. doi: 10.3389/fmats.2022.889771
Received: 04 March 2022; Accepted: 21 March 2022;
Published: 01 April 2022.
Edited by:
Praveen Sathiyamoorthi, Indian Institute of Technology (BHU), IndiaReviewed by:
K. Guruvidyathri, University of Hyderabad, IndiaCopyright © 2022 Ghassemali and Conway. This is an open-access article distributed under the terms of the Creative Commons Attribution License (CC BY). The use, distribution or reproduction in other forums is permitted, provided the original author(s) and the copyright owner(s) are credited and that the original publication in this journal is cited, in accordance with accepted academic practice. No use, distribution or reproduction is permitted which does not comply with these terms.
*Correspondence: Ehsan Ghassemali, ZWhzYW4uZ2hhc3NlbWFsaUBqdS5zZQ==
Disclaimer: All claims expressed in this article are solely those of the authors and do not necessarily represent those of their affiliated organizations, or those of the publisher, the editors and the reviewers. Any product that may be evaluated in this article or claim that may be made by its manufacturer is not guaranteed or endorsed by the publisher.
Research integrity at Frontiers
Learn more about the work of our research integrity team to safeguard the quality of each article we publish.