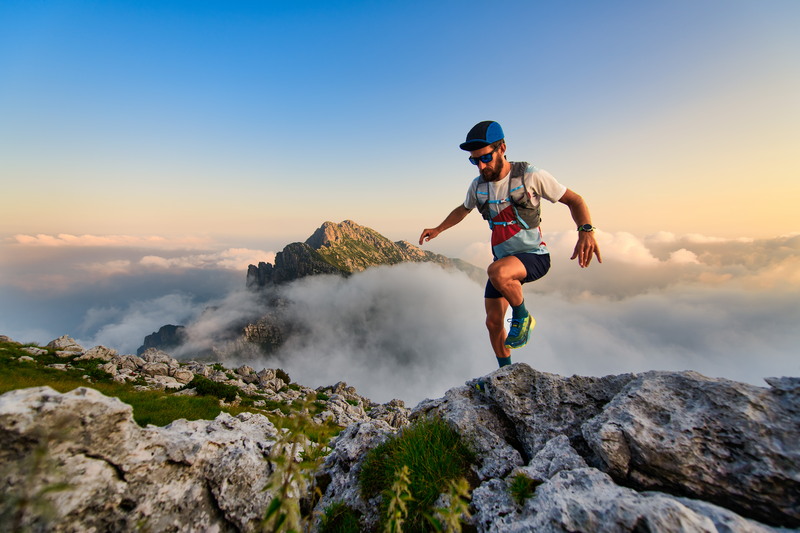
95% of researchers rate our articles as excellent or good
Learn more about the work of our research integrity team to safeguard the quality of each article we publish.
Find out more
ORIGINAL RESEARCH article
Front. Mater. , 26 April 2022
Sec. Polymeric and Composite Materials
Volume 9 - 2022 | https://doi.org/10.3389/fmats.2022.883184
This article is part of the Research Topic Advanced Technologies for Electrical Engineering View all 6 articles
Polychlorotrifluoroethylene (PCTFE) is one of the earliest developed and commercialized fluoropolymers and has been used in high-frequency communication, anti-corrosion, and medical packaging fields. However, relatively poor processability and mechanical performances resulting from high molecular regularity and crystallinity limited its broader applications. Herein, the pristine PCTFE was physically modified by blending with its pyrolysis products (FCO). It was demonstrated that the addition of FCO accelerated the molecular relaxation and retarded the crystallization process of PCTFE, leading to the distinct improvement of processability and mechanical performances. When 10% FCO was loaded, the equilibrium torque was decreased by 20%; the elongation at break and impact strength were enhanced by 3.6 and 10.6 times in comparison to those of PCTFE. Additionally, because of the good compatibility of the components, the blend also maintained ultralow dielectric constant/loss, good transparency, and high water-vapor barrier performances. Accordingly, this work paved an effective route to prepare high-performance PCTFE materials, which may play an important role in high-frequency communication field.
Polychlorotrifluoroethylene (PCTFE) is one of the thermoplastic fluoropolymers with chemical corrosion resistance, high and low temperature resistance, low dielectric constant and loss (Scott et al., 1962; Hara, 1967; Longhenry et al., 1997; Hosseini et al., 2012), low water vapor permeability (Yavari et al., 2018), high transparency (Gardiner, 2014; Hosseini et al., 2016; Khameneh-asl et al., 2016; Walther et al., 2020), etc. Although PCTFE has been used in anti-corrosion, high-frequency communication, and medical package fields, poor processability and mechanical performances limit its broader applications (Zou et al., 2022).
It is known that the carbon chains of PCTFE are closely wrapped by fluorine and chlorine atoms preventing the backbone from being exposed to ambient media (water, air, acid, alkali, salt, solvent, etc.). Therefore, the PCTFE resins can only be dissolved in certain type of solvents and in most cases were prepared through melt processing technologies. However, the narrow window of processing temperature and high melt viscosity inevitably lead to the difficulty of the melt processing. On the other side, the high crystallinity and large crystal size originated from the regular chain structure undesirably cause PCTFE products to possess a poor toughness. Accordingly, it is of significance to introduce effective modification on PCTFE for optimizing its processability and mechanical performances.
The modification of PCTFE generally focused on the chemical copolymerization and physical blending. The copolymerization can be realized by free radical polymerization. The types of comonomers included ethylene, vinylidene fluoride, vinyl acetate, etc. (Boschet and Ameduri, 2014). Although these CTFE-based copolymers exhibited distinct improvement or promotion on certain performances in comparison to those of PCTFE, the preparation technique and product cost restricted their further commercialization and application. In contrast, physical blending (Huang et al., 2021; Su et al., 2021) has been widely employed as a convenient route to modify thermoplastics. It is well recognized that foreign components may contribute their good performances to the matrix polymer through their interfaces. Unfortunately, due to the high concentration of fluorine atoms in PCTFE, its surface energy is ultralow, so that only a few components can be chosen to establish necessary interfacial adhesion in a blending system for transferring or dissipating mechanical energy. For example, Feng et al. (Na et al., 2014) toughened PCTFE by melt blending it with core-shell acrylate copolymer (ACR). It was reported that the inclusion of ACR reduced the crystallinity and crystal size of PCTFE, which contributed to the increase of impact strength. In addition, Shen et al. (Ruoyu et al., 2021) disclosed that introducing 10 wt% a kind of vinylidene fluoride copolymer (Co-PVDF) could also restrain the crystallization of PCTFE. As a result, the impact strength of the blend reached about 40 kJ/m2, almost four times higher than that of the pristine PCTFE. Meanwhile, the processability was also improved and accompanied with the reduction of shear viscosity and plasticizing period. Although the blending strategy seems to be effective on modifying the processability and mechanical toughness of PCTFE, the addition of foreign components with limited compatibility would inevitably remove the original perfect chemical stability, light transparency, water-vapor barrier, and dielectric characteristics (Sun et al., 2020; Wang et al., 2020; Wang et al., 2021; Zhou et al., 2021).
Based on the fundamental knowledge of polymer physics, the flowing and mechanical behaviors of a polymer material is the response of its molecular chains to the external stress (Rubinstein and Colby, 2003). Once the molecular structure and type are determined, the molecular weight would be a critical factor. It is well regarded that the polymer with high molecular weight tends to have higher mechanical strength and rigidity, whereas the one with low molecular weight may have better fluidity and flexibility. A good solution to achieve balanced comprehensive performances would be to produce a multimodal distribution of molecular weight, taking polyethylene products for instance (Tohi et al., 2004; Shen et al., 2011; Lafleur et al., 2018; Szántó et al., 2019). For PCTFE, its poor processability and mechanical toughness are originated from the slow response and long relaxation time of tightly arranged molecular chains under the stress. Therefore, the introduction of a low molecular weight component with similar chain segments of PCTFE to tailor the molecular relaxation behavior may provide a promising direction for PCTFE modification.
In this study, the pristine PCTFE was physically modified by melt-blending with the component with low molecular weight produced through the pyrolysis of PCTFE. The influence of the mass ratios on the rheological and crystalline behaviors was investigated. As a result, the optimal composition owning the desired comprehensive performances was obtained and the mechanism related to the regulation of molecular relaxation was addressed, which thereby paved a facile and effective route to prepare high-performance PCTFE materials which are of potential application in high-frequency communication field.
The PCTFE granules (MF301), with the viscosity-average molecular weight of 11.8×104 and the melt flow rate of 2.5 g/10 min (240°C, 2.16 kg), were offered by Sichuan Yinlewei Technology Co., Ltd. (China). The component (FCO21) with the viscosity-average molecular weight of 8.5×103 and the density of 1.91 g/cm3 was denoted as FCO and provided by Chengdu Talent-Win New Materials Technology Co., Ltd (China).
Prior to melt blending, both the PCTFE granules and FCO were dried at 60°C in a vacuum oven for 8 h, respectively. Then, the FCO with different amounts was physically mixed with the granules together forming a series of mixing systems, the formulation of which is presented in Table 1. For each system, the melt-blended sample was prepared through an RM-200C torque rheometer (Harbin Hapu Electric Technology Co., Ltd., China) at 240°C and 30 rpm for 5 min, and finally was hot compressed into a sheet at 240°C and 10 MPa for characterization.
The phase morphologies of each specimen were observed using a JSM-5900LV electron microscope (JEOL, Japan). It was prepared by cryofracturing in liquid nitrogen. A thin layer of gold was sprayed on the fractured surface prior to observation. The acceleration voltage was 5 KV.
The dynamic rheological behavior of the samples was tested using an AR2000EX advanced extended rheometer (TA, United States). Each sample was cut into 25 mm diameter and 1 mm thickness discs. Then, it was placed between the parallel plate rotors and preheated for 5 min. The testing temperature was set at 240 °C. The range of shearing rate was 0.1–100 rad/s and the strain amplitude was 1% guaranteeing the test to be performed in linear viscoelastic zone.
Differential scanning calorimeter (DSC) measurements were carried out using a model Q800 differential scanning calorimeter (TA, United States). Approximately 5–8 mg of each specimen was weighed and sealed in a 40 μL aluminum crucible. The temperature was increased from 40 to 240 °C at a rate of 10°C/min in a nitrogen gas flow of 50 ml/min. The heat history was eliminated at 240°C of 5 min and then lowered to 40°C at a rate of 10°C/min. The melting peak area of each specimen was integrated and its crystallinity (
where
The isothermal crystallization process of each specimen was observed using a Bx-51 Polarizing microscope (Shimadzu, Japan). A thin slice of about 15 μm thickness was cut from the specimen. The slice was first heated to 240°C on a hot table to eliminate its heat history for 5 min. Then, it was quickly cooled to 200°C at 100°C/min and maintained for enough time to complete the crystallization. The crystallization process was captured using a digital camera.
The WAXD work was done using an Ultima IV X-ray diffractometer, manufactured by Rigaku Denki, the target material was copper, the scanning mode was theta, Cu Kα radiation (λ = 0.1542 nm) was used, and the X-ray powder patterns were measured in the 2θ ranges of 10°–25°.
The mechanical properties including tensile strength and elongation at break were measured in accordance with GB/T1040.2-2006 (China) at 25°C using an Instron 5567 universal material testing machine (United States) at a strain rate of 50 mm/min. At least of five specimens for each sample were tested and the average value was calculated.
The impact strength was measured in accordance with GB/1843-2008 (China) at 25°C by using an XJUD-22 cantilever beam impact testing machine (Chengde Jinhe Instrument Manufacturing Co., Ltd.). At least of five specimens for each sample were tested and the average value was calculated.
The dynamic mechanical analysis (DMA) of each sample was tested through a Q800 Dynamic Mechanical Tester (TA instrument, United States) using tensile mode. The sample with the size of 20 mm × 4 mm × 1 mm was heated from −50 to 170°C at a heating rate of 3°C/min. The testing frequency was 10 Hz and the strain was 0.1%.
The dielectric properties of the blend samples were measured through the strip-line method by using a vector network analyzer (Agilent, America). Each sample was cut into a rectangular shape with the size of 70 mm (L) × 30 mm (W) × 1.2 mm (T). Two identical samples were adhered to a resonant conduction band with a width (ω) of 1.6 mm. Their outer surfaces were adhered to a metal sheet and compressed with 350 kg load. The schematic of this measurement was exhibited in Figure 1. The dielectric constant and dielectric loss were collected in the frequency range of 3–18 GHz at room temperature (23°C).
FIGURE 1. Schematic representation of the strip-line method for measuring high-frequency dielectric properties.
The water vapor barrier was evaluated by using a PERME W3/031 water vapor transmission tester (Jinan Languang Electromechanical Technology Co., Ltd., China). The thickness of each sample was 1 mm, and its water vapor permeability (WVP) was calculated by the following formula:
where w is the weight change of the test cup in t time, x is the thickness of each sample, A is the test area, and ∆P is the interval time after the weight change is stable.
The light transmittance and haze were measured through an HGM-2DP fog meter (Shimadzu Company, Japan). The test area of the sample was 5 cm × 5 cm and the thickness was 1 mm. Each sample was tested at five points and the average value was calculated.
When the PCTFE and PCO were melt blended, their compatibility could be intuitively examined through SEM observation. As exhibited in Figure 2, the phase morphologies of neat PCTFE (FM0) and PCTFE/FCO blend (FM10) were compared at the same magnification (×12,000). It is clearly shown that both morphologies of these two specimens are integrated without any observable phase separation, except that the cryofractured surface of the blend is rougher in appearance. This suggests that the components in the blend system should have a good compatibility and the addition of FCO may be capable of improving the mechanical toughness of the matrix polymer.
The compatibility between PCTFE and FCO was further evaluated through dynamic mechanical spectra. The loss factors of neat PCTFE and PCTFE/FCO blends with different compositions in the range of −50 and 160°C were measured and recorded through DMA instrument. As seen from Figure 3, all samples show two peaks, the higher one corresponds to the glass transition of PCTFE (Tg) and the lower one is the secondary relaxation (Tβ). The Tg of PCTFE is 116°C, which is consistent with that reported previously (Brown et al., 2006). With the increase of FCO content, the peak of glass transition moved toward low temperature side and became broader. In order to compare more clearly, Table 2 lists the values of Tg, Tβ, and the width of the half peak of glass transition (Wg) for each sample. In comparison to those of neat PCTFE, the Tg was dramatically decreased from 116.4 to 69.9°C and meanwhile the Wg was enlarged from 48.9 to 77.4°C when 10% FCO was incorporated into PCTFE. This evidences that the FCO plays a distinct role in the plasticization of PCTFE, due to their good compatibility and high mobility of FCO molecules. Accordingly, a part of segment motion of PCTFE could be defrosted at lower temperature and a broader distribution of glass transition was created, which is commonly believed to be favorable for absorbing more mechanical energy and improving impact toughness.
The addition of FCO may not only promote the glass transition of PCTFE, but also affect its melting and crystallization behaviors which are dependent on long-range order of macromolecular chains. Figures 4A,B record the melting and non-isothermal crystallization curves of neat PCTFE and its blending samples with different FCO contents, respectively. The corresponding parameters including melting temperature (Tm), crystallization degree (Xc), and crystallization temperature (Tc) are listed in Table 3. It is clearly shown that blending with FCO tends to weaken the ability of crystallization of PCTFE. All aforementioned parameters were decreased synchronously, accompanied with the increase of FCO content. When 10% FCO was incorporated, the Tm, Tc, and Xc were reduced by 7°C, 10°C and 11% in contrast with those of neat PCTFE. This result presents a significant effect of FCO on controlling and tuning the condensed structure of PCTFE, which was seldom reported previously in other PCTFE-based system to the authors’ best knowledge. As mentioned previously, low surface energy and poor adhesion of PCTFE make it difficult to find a component with certain compatibility and thereby limit its blending modification.
FIGURE 4. Melting and non-isothermal crystallization curves of neat PCTFE and its blending samples with different FCO contents: (A) Cooling curves with the cooling rate of 10°C/min; (B) second heating curves with the heating rate of 10°C/min.
The crystalline structure of PCTFE and its blending system was detected through X-ray technique. Figure 5 shows the WAXD spectra which were collected in the range of 10–25°. The characteristic peaks of neat PCTFE crystals located at 16.3°, 16.7°, and 17.4° corresponds to the (101), (102), and (103) planes, respectively. When PCTFE was blended with FCO, all those peaks shifted to smaller angles as recorded in Table 4, indicating the enlargement of interplanar spacing according to the Prague’s formula(5). This result evidences that the introduction of the compatible FCO component may disrupt the original ordered molecular arrangement and closely-packed crystal structure in PCTFE, so that the low-molecular-weight component distinctly reduced the crystallization capacity and perfection of the high-molecular weight matrix.
The crystallization process of FM0 and the FM10 was further compared by using a POM equipped with a heating cell. Each specimen was isothermally crystallized at 200°C for 10 min and the growth of crystals was captured by a digital camera synchronously. As recorded in Figure 6, the crystals appeared in pristine polymer at 20 s, but nearly none could be observed in FM10 at the same time. After experiencing another 20 s, some bright spots started to emerge in FM10, whereas the whole area in neat PCTFE has almost been occupied by crystals. When the whole crystallization process lasted for 10 min, it was clearly shown that the crystals in FM0 were much larger and greater in number than those in FM10 observed at the same magnification. This intuitively substantiates that the addition of FCO is of retarding effect on the crystallization of the PCTFE, including the crystallization rate, degree, and dimensions, which is consistent with the result obtained from DSC and WAXD.
The influence of incorporating FCO on the melt processing performance of PCTFE was directly examined by blending them in a torque rheometer. The torque versus time curves of each system was recorded. As presented in Figure 7, the torque of neat PCTFE is the maximum, indicating that more mechanical energy is required for initiating plasticization. With the increase of FCO contents, the torque peak was substantially reduced below 50 N m, and the equilibrium torque also showed gradual decline. This tendency demonstrates a distinct improvement on the melt processability of PCTFE by blending with FCO, and signifies that the rheological behavior of the blending system could be modified by varying its compositions.
The rheological behavior of the PCTFE/FCO blending system was further studied by utilizing dynamic oscillatory rheometer. The dependence of storage modulus (G′), loss modulus (G″), and complex viscosity (|η*|) on angular frequency (ω) for the samples with different compositions is shown in Figure 8A,B,C, respectively. It can be observed that with the increase of FCO content in the blend, all of these dynamic rheological parameters decreased gradually in the range of 0.1-100 rad/s, the result of which was consistent with those systems filled with lubricants (Luan et al., 2011; Dai et al., 2019). Since the PCTFE and FCO have a similar CTFE segmental structure, they have a good compatibility with each other. The low-molecular-weight FCO can perfectly wet the PCTFE and easily move into the interchain space promoting the mobility of macromolecular chains.
FIGURE 8. (A) Storage modulus, (B) loss modulus, and (C) complex viscosity of PCTFE and PCTFE/FCO blends as a function of angular frequency measured at 240°C; (D) characteristic frequency and relaxation time of PCTFE and PCTFE/FCO blends; (E) Cole–Cole curves of PCTFE and PCTFE/FCO blends.
It is well recognized that the aforementioned dynamic rheological parameters reflect the viscoelastic behavior of the blending system. According to the Maxwell model, the G′ and G″ can be fitted as follows (Friedrich, 1991):
where G∞ is the storage modulus when ω approaches to infinity and τ is the relaxation time. The curve intersection of G′ and G″ is defined as the transformation of viscosity and elasticity, where the blending system exhibits elastic characteristic at high-frequency side and viscous characteristic at low-frequency side. More significantly, the τ can be quantitatively got from the reciprocal of the characteristic frequency (ωc) located at the curve intersection. The results included in Figure 8D display that the increase of the FCO content leads to the increase of ωc and the reduction of τ, demonstrating that the introduction of the low-molecular weight component playing a positive role in accelerating the molecular relaxation of the blending system. The Cole–Cole curve is the relation between the real part and the imaginary part of the complex viscosity. For the current system, all curves shown in Figure 8E display a semi-circular pattern, which signifies that there is nearly no distinct phase separation occurring in the current blending system as demonstrated in dynamic mechanical spectra.
The variation of the microstructure and molecular relaxation of PCTFE by introducing FCO may inevitably influence the macroscopic mechanical properties, which would determine the application of the materials. In this study, the stretching and impacting tests were performed to explore the relationship between mechanical parameters and the FCO content.
The stretching properties of the PCTFE and the PCTFE/FCO blends are shown in Figure 9A. All samples deformed in a ductile manner with distinct yield necking, but without strain-hardening phenomenon. Thus, the yield strength is the maximum tensile stress that each material needs to bear in unit area. For neat polymer, its yield strength is 31 MPa similar to that of isotactic polypropylene, but its elongation at break is only around 50% which characterizes a poor flexibility. In contrast, a gradually enlarged stretching extension was achieved by increasing the FCO content. The elongation at break was almost enhanced by 360% when 10% FCO was blended, although the yield strength was moderately reduced by 30%. The elevated mobility of macromolecular chains was considered to contribute the improvement of the flexibility during stretching (Egorov and Zhizhenkov, 1982).
FIGURE 9. (A) Yield strength and elongation and (B) impact strength of PCTFE and PCTFE/FCO blends (the fractured samples after stretching and impacting were also inserted); (C) SEM micrographs of the fractured surface of PCTFE and PCTFE/FCO blends after impacting.
The impact strength as a function of the FCO content is included in Figure 9B. It is clearly shown that the impact strength of PCTFE is only 5 KJ/m2, which could be fractured easily under rapid impact force. Different from the modification effect presented in the elongation at break, nearly no changes appeared in the impact strength unless more than 6% FCO was incorporated. Surprisingly, further increasing the FCO to 10%, the impact strength was raised to 58 KJ/m2, which was 10.6 times higher than that of PCTFE. The fractured surfaces of PCTFE and PCTFE/FCO blends were compared through SEM observation. As shown in Figure 9C, For the samples blended with no more than 6% FCO, their smooth surfaces indicate the characteristics of brittle fracture. A brittle-ductile transition gradually occurred when 8% FCO was added and eventually the classic characteristics of ductile fracture appeared in FM10, where the surface became much rougher and many filaments were pulled out. Therefore, it can draw a conclusion that the FCO is capable of toughening the PCTFE.
It is well known that PCTFE is featured by several unique and outstanding properties including low dielectric constant and loss, high transparency, and low water vapor permeability, which enable it to be employed in a variety of special application scenarios, such as high-frequency communication, new energy, and medical packaging, etc. However, in order to improve its processability and mechanical performances, the common co-polymerization or physical blending may inevitably cause the enormous sacrifice of above-mentioned properties. Therefore, from the perspective of practical applications, the influence of the FCO on the dielectric, optical, and barrier properties of PCTFE was investigated in this study.
Firstly, the dielectric parameters of PCTFE and its blends were measured in the range of 3–18 GHz by using the strip-line resonance method. The results of FM0, FM6, and FM10 are compared in Figures 10A,B. For pristine polymer, its dielectric constant is maintained around 2.26 and the dielectric loss exhibits a descending tendency with a maximum of 0.006, from 3 to 18 GHz. When the FCO was introduced, both the dielectric constant and loss were almost consistent with those of the PCTFE, irrespective of the FCO content. This indicates that the foreign component had a slight influence on the dielectric relaxation of molecular chains in high frequency range, which should be ascribed to the similar chemical structure between PCTFE and FCO. Accordingly, such low dielectric constant and loss enable the present blending system to be promising in PCB industry.
FIGURE 10. Other macroscopic properties of PCTFE and PCTFE/FCO blends: (A) Dielectric constant; (B) dielectric loss; (C) transmittance and haze; (D) water vapor permeability.
The PCTFE is not only a microwave transmitting material but also has perfect transparency with high light transmittance and low haze. Commonly, the physical blending would result in a remarkable reduction of light transparency because of the interfacial scattering and reflection caused by the different refractive index of the components (Loste et al., 2019). In the present system, both the transmittance and haze values were measured and collected in Figure 10C. With the increase of FCO content, the light transmittance was maintained around 90%, whereas the haze displayed a convex-pattern tendency and reached a maximum of 21% when 6% FCO was loaded. Although the FCO has a good compatibility with PCTFE matrix, their different refractive index still will induce the light scattering at the phase interfaces and the scattering angle is predominantly determined by the contour profile of the interface (Maruhashi and Iida, 2001; Hahn, 2009). As a result, the scattering angle was enlarged with the introduction of the FCO, leading to the increase of the haze. However, this value tended to decline when the content of FCO reached a certain amount due to the increased phase continuity and the homogeneous phase distribution (Luo et al., 2016). In addition, it is worth noting that the influence of the slight increase of the haze on the light transparency is within a limited and acceptable level. It can be seen from Figure 10C that the FM6 still owned a good transparency in comparison to other samples.
Finally, the water vapor permeability of pristine PCTFE and its blends was measured to evaluate the barrier property. The results are contained in Figure 10D. The water vapor permeability of PCTFE is 0.0032 g/m2∙24 h, which is regarded as the lowest value among those of thermoplastic polymers with a melting point below 300°C (Teng, 2012; Keller and Kouzes, 2017). Significantly, this value was further reduced to around 0.0012 g/m2∙24 h with the addition of FCO component. This demonstrated that the barrier property of the PCTFE/FCO blending system was even better than that of pristine PCTFE, which might be contributed by the incremental transmitting distances due to the increase of interfaces among components.
In this study, the PCTFE was physically modified by melt blending with its pyrolysis product FCO. Because they had similar chemical structure but different molecular weight, good compatibility was evidenced through integrated phase morphology and reduced glass transition temperature. The low-molecular-weight FCO could perfectly wet the PCTFE and easily moved into the interchain space promoting the relaxation of macromolecular chains. Therefore, the blending system could be plasticized with lower equilibrium torque. On the other side, the addition of FCO also effectively restrained the crystallization of the matrix polymer by breaking the compact stacking of lamella. By virtue of the accelerated molecular relaxation and the reduced crystallinity, both the processability and mechanical toughness of the blending system were remarkably improved. For FM10, the equilibrium torque was decreased by 20%, the elongation at break and impact strength were increased by 3.6 and 10.6 times in comparison to those of the pristine PCTFE. Meanwhile, the similar chemical structure and good compatibility also made the dielectric, optical, and water-vapor barrier properties be perfectly maintained, which overcame the constraints of the balance among various performances for previously-reported blending systems. Accordingly, the present work offered a facile and effective strategy for modifying the PCTFE materials.
The original contributions presented in the study are included in the article/Supplementary Material; further inquiries can be directed to the corresponding author.
MY wrote the first draft of the article. RX wrote sections of the manuscript. SG contributed to conception. JS contributed to conception design of the study and supervision. All authors contributed to article revision and have read and approved the submitted version.
The authors declare that the research was conducted in the absence of any commercial or financial relationships that could be construed as a potential conflict of interest.
All claims expressed in this article are solely those of the authors and do not necessarily represent those of their affiliated organizations, or those of the publisher, the editors, and the reviewers. Any product that may be evaluated in this article, or claim that may be made by its manufacturer, is not guaranteed or endorsed by the publisher.
The authors are grateful to the National Natural Science Foundation of China (51873132) for financial support of this work.
Boschet, F., and Ameduri, B. (2014). (Co)polymers of Chlorotrifluoroethylene: Synthesis, Properties, and Applications. Chem. Rev. 114 (2), 927–980. doi:10.1021/cr2002933
Brown, E. N., Rae, P. J., and Orler, E. B. (2006). The Influence of Temperature and Strain Rate on the Constitutive and Damage Responses of Polychlorotrifluoroethylene (PCTFE, Kel-F 81). Polymer 47 (21), 7506–7518. doi:10.1016/j.polymer.2006.08.032
Dai, L., Wang, X., Zhang, J., Wang, F., Ou, R., and Song, Y. (2019). Effects of Lubricants on the Rheological and Mechanical Properties of wood Flour/polypropylene Composites. J. Appl. Polym. Sci. 136 (25), 47667. doi:10.1002/app.47667
Egorov, E. A., and Zhizhenkov, V. V. (1982). NMR Studies of Molecular Mobility in Uniaxially Stretched Oriented Polymers. J. Polym. Sci. Polym. Phys. Ed. 20 (7), 1089–1106. doi:10.1002/pol.1982.180200701
Friedrich, C. (1991). Relaxation and Retardation Functions of the Maxwell Model with Fractional Derivatives. Rheola Acta 30 (2), 151–158. doi:10.1007/bf01134604
Gardiner, J. (2014). Fluoropolymers: Origin, Production, and Industrial and Commercial Applications. Aust. J. Chem. 68 (1), 13–22. doi:10.1071/CH14165
Hahn, D. W. (2009). Light Scattering Theory. Gainesville, FL: Department of Mechanical and Aerospace Engineering, University of Florida.
Hara, T. (1967). Dielectric Properties of Low Molecular Weight Polychlorotrifluoroethylene. Jpn. J. Appl. Phys. 6 (2), 135–146. doi:10.1143/jjap.6.135
Hosseini, M. G., Abdolmaleki, M., Ashrafpoor, S., and Najjar, R. (2012). Deposition and Corrosion Resistance of Electroless Ni-PCTFE-P Nanocomposite Coatings. Surf. Coat. Tech. 206 (22), 4546–4552. doi:10.1016/j.surfcoat.2012.04.083
Hosseini, M. G., Teymourinia, H., Farzaneh, A., and Khameneh-asl, S. (2016). Evaluation of Corrosion, Mechanical and Structural Properties of New Ni-W-PCTFE Nanocomposite Coating. Surf. Coat. Tech. 298, 114–120. doi:10.1016/j.surfcoat.2016.04.060
Huang, J., Zou, W., Luo, Y., Wu, Q-b., Lu, X., and Qu, J. (2021). Phase Morphology, Rheological Behavior, and Mechanical Properties of Poly (Lactic acid)/Poly (Butylene succinate)/Hexamethylene Diisocyanate Reactive Blends. ES Energ. Environ. 12, 86–94. doi:10.30919/esee8c1017
Keller, P. E., and Kouzes, R. T. (2017). Water Vapor Permeation in Plastics. United States.PNNL-26070; 45304036L.U.S.. Washington, D.C.: Department of Energy Office of Scientific and Technical Information.
Khameneh-asl, S., Farzaneh, A., Teymourinia, H., Mermer, O., and Hosseini, M. G. (2016). Preparation of a Ni-Mo-P-PCTFE Nanocomposite Coating and Evaluation of its Nano-Tribological, Mechanical and Electrochemical Performance. RSC Adv. 6 (82), 78774–78783. doi:10.1039/c6ra12970f
Lafleur, S., Berthoud, R., Ensinck, R., Cordier, A., De Cremer, G., Philippaerts, A., et al. (2018). Tailored Bimodal Ultra-high Molecular Weight Polyethylene Particles. J. Polym. Sci. Part. A: Polym. Chem. 56 (15), 1645–1656. doi:10.1002/pola.29037
Longhenry, J. L., Love, B. J., and Murthy, N. S. (1997). Cooling Rate-Induced Glass-Adhesion Variations Using Crystallizing Hot-Melt Adhesives. J. Mater. Sci. 32 (9), 2283–2289. doi:10.1023/a:1018576217355
Loste, J., Lopez-Cuesta, J.-M., Billon, L., Garay, H., and Save, M. (2019). Transparent Polymer Nanocomposites: An Overview on Their Synthesis and Advanced Properties. Prog. Polym. Sci. 89, 133–158. doi:10.1016/j.progpolymsci.2018.10.003
Luan, L., Wu, W., and Wagner, M. H. (2011). Rheological Behavior of Lubricating Systems in Polypropylene/seaweed Composites. J. Appl. Polym. Sci. 121 (4), 2143–2148. doi:10.1002/app.33940
Luo, S., Yi, P., Xiong, Y., Shen, J., and Guo, S. (2016). Light‐scattering Capacity of Ethylene–Vinyl Acetate Copolymers in Polypropylene: Toward High Haze and Transmittance. J. Appl. Polym. Sci. 133 (34), 42844. doi:10.1002/app.42844
Maruhashi, Y., and Iida, S. (2001). Transparency of Polymer Blends. Polym. Eng. Sci. 41 (11), 1987–1995. doi:10.1002/pen.10895
Na, F., Yu, G., Li, W., Jie, W., and Sun, S. (2014). Effect of Rare Earth Compound Stabilizer on Polytrifluorochloroethylene Materials. Plast. Sci. Technol. 42 (06), 109–112. doi:10.15925/j.cnki.issn1005-3360.2014.06.019
Ruoyu, X., Jiabin, S., and Shaoyun, G. (2021). Toughening Modification of Poly(trifluorochloroethylene) by Melt Blending. Polym. Mat Sci. Eng. 37 (07), 66–70+80. doi:10.3390/polym13121953
Scott, A. H., Scheiber, D. J., Curtis, A. J., Lauritzen, J. I., and Hoffman, J. D. (1962). Dielectric Properties of Semicrystalline Polychlorotrifluoroethylene. J. Res. Natl. Bur. Stan. Sect. A. 66A, 269–305. doi:10.6028/jres.066a.028
Shen, H.-W., Luan, T., Xie, B.-H., Yang, W., and Yang, M.-B. (2011). Rheological Behaviors and Molecular Weight Distribution Characteristics of Bimodal High-Density Polyethylene. J. Appl. Polym. Sci. 121 (3), 1543–1549. doi:10.1002/app.33698
Su, Y., Yin, H., Wang, X., Ma, Y., Vupputuri, S., Guo, Z., et al. (2021). Preparation and Properties of Ethylene-Acrylate Salt Ionomer/polypropylene Antistatic alloy. Adv. Compos. Hybrid Mater. 4 (1), 104–113. doi:10.1007/s42114-021-00219-y
Sun, L., Liang, L., Shi, Z., Wang, H., Xie, P., Dastan, D., et al. (2020). Optimizing Strategy for the Dielectric Performance of Topological-Structured Polymer Nanocomposites by Rationally Tailoring the Spatial Distribution of Nanofillers. Engineered Sci. 12 (5), 95–105. doi:10.30919/es8d1148
Szántó, L., Feng, Y., Zhong, F., Hees, T., van Ruymbeke, E., Mülhaupt, R., et al. (2019). Ultra-broad Molecular Weight Distribution Effects on Viscoelastic Properties of Linear Multimodal PE. J. Rheol 63 (5), 773–784. doi:10.1122/1.5109481
Teng, H. (2012). Overview of the Development of the Fluoropolymer Industry. Appl. Sci. 2 (2), 496–512. doi:10.3390/app2020496
Tohi, Y., Nakano, T., Makio, H., Matsui, S., Fujita, T., and Yamaguchi, T. (2004). Polyethylenes Having Well-Defined Bimodal Molecular Weight Distributions Formed with Bis(phenoxy-Imine) Zr Complexes. Macromol. Chem. Phys. 205 (9), 1179–1186. doi:10.1002/macp.200400039
Walther, H. C., Epstein, R. M., and Ferstandig, L. L. (2020). Polychlorotrifuoroethylene. Synthetics, Mineral Oils, and Bio-Based Lubricants Chemistry and Technology. Boca Raton: CRC Press. 217–226. doi:10.1201/9781315158150-12
Wang, P., Yang, L., Gao, S., Chen, X., Cao, T., Wang, C., et al. (2021). Enhanced Dielectric Properties of High Glass Transition Temperature PDCPD/CNT Composites by Frontal Ring-Opening Metathesis Polymerization. Adv. Compos. Hybrid Mater. 4 (3), 639–646. doi:10.1007/s42114-021-00287-0
Wang, Q., Zhang, J., Zhang, Z., Hao, Y., and Bi, K. (2020). Enhanced Dielectric Properties and Energy Storage Density of PVDF Nanocomposites by Co-loading of BaTiO3 and CoFe2O4 Nanoparticles. Adv. Compos. Hybrid Mater. 3 (1), 58–65. doi:10.1007/s42114-020-00138-4
Yavari, M., Okamoto, Y., and Lin, H. (2018). The Role of Halogens in Polychlorotrifluoroethylene (PCTFE) in Membrane Gas Separations. J. Membr. Sci. 548, 380–389. doi:10.1016/j.memsci.2017.11.043
Zhou, Y., Wang, P., Ruan, G., Xu, P., and Ding, Y. (2021). Synergistic Effect of P [MPEGMA-IL] Modified Graphene on Morphology and Dielectric Properties of PLA/PCL Blends. ES Mater. Manuf 11, 20–29. doi:10.30919/esmm5f928
Keywords: polychlorotrifluoroethylene, physical blending, processability, toughening, dielectric property
Citation: Yang M, Xu R, Guo S and Shen J (2022) Preparation and Modification of High-Performance Polychlorotrifluoroethylene Through Physical Blending. Front. Mater. 9:883184. doi: 10.3389/fmats.2022.883184
Received: 24 February 2022; Accepted: 23 March 2022;
Published: 26 April 2022.
Edited by:
Jun-Wei Zha, University of Science and Technology Beijing, ChinaReviewed by:
John Zhanhu Guo, University of Tennessee, United StatesCopyright © 2022 Yang, Xu, Guo and Shen. This is an open-access article distributed under the terms of the Creative Commons Attribution License (CC BY). The use, distribution or reproduction in other forums is permitted, provided the original author(s) and the copyright owner(s) are credited and that the original publication in this journal is cited, in accordance with accepted academic practice. No use, distribution or reproduction is permitted which does not comply with these terms.
*Correspondence: Jiabin Shen, c2hlbmpiQHNjdS5lZHUuY24=
Disclaimer: All claims expressed in this article are solely those of the authors and do not necessarily represent those of their affiliated organizations, or those of the publisher, the editors and the reviewers. Any product that may be evaluated in this article or claim that may be made by its manufacturer is not guaranteed or endorsed by the publisher.
Research integrity at Frontiers
Learn more about the work of our research integrity team to safeguard the quality of each article we publish.