- 1MSc Candidate at Civil Engineering Graduate Program, Federal University of Espírito Santo, Vitória, Brazil
- 2Associate Professor at School of Civil Engineering, Architecture and Urbanism, University of Campinas, Campinas, Brazil
- 3Technology Manager, Brazilian Portland Cement Association, São Paulo, Brazil
- 4Researcher at the Institute of Structural Design, Graz University of Technology, Graz, Austria
- 5Professor at Department of Civil Engineering and Civil Engineering Graduate Program, Federal University of Espírito Santo, Vitória, Brazil
The synergistic effect of combining supplementary cementitious materials (SCMs) as partial substitutes for clinker improves cement properties and reduces its clinker factor and, hence, its carbon footprint. Limestone-calcined clay cement (LC3)—a family of clinker, calcined clay, and limestone filler mixes—is studied worldwide for its properties equivalent to those of Portland cement. Although slag and fly ash are no longer sufficient to keep up with current commercial blended cements, in the long run, these SCMs can support the development of optimized formulations for the future. By relating the environmental and the mechanical performances, the GHG emission intensity offers a broader assessment and selection perspective. In this article, 13 blended cements were evaluated: ternary, quaternary, and multi-admixture (i.e., OPC plus 4 SCMs) blends with clinker factor between 40 and 50%, composed of—in addition to calcined clay and limestone filler—blast furnace slag and fly ash. Compressive strength was measured at 3, 7, 28, 91, and 365 days. The greenhouse gas (GHG) emissions were estimated through life cycle assessment and related to the blends’ compressive strength unit. Quaternary and multi-addition cements consistently outperformed after 3 days of age, demonstrating the benefits of the synergistic effect between SCMs jointly on GHG emissions and compressive strength. Such an effect enables reducing not only the clinker factor and carbon footprint but also the GHG emission intensity, which relates both. This study showed that the formulated cements, particularly those composed of multi-additions (Series D), are potential alternatives for reducing the GHG emissions, whilst preserving mechanical performance demanded by construction market practices. From a multidisciplinary analysis standpoint, durability assessments are necessary to complement the reported findings, as low clinker contents can affect the pH of the concrete’s pore solution and carbonation which ultimately lead to deterioration.
1 Introduction
Given global climate change concerns, the cement industry has explored strategies to mitigate its environmental impacts and meet internationally agreed-upon goals, such as those of the Paris Agreement (UNFCC, 2021), and supply the growing demand for cement in the market.
The cement industry is responsible for approximately 7% of anthropic CO2 emissions (IEA et al., 2018). Such emissions arise mainly from the production of Portland clinker, which also requires high energy input (Schneider, 2019). Mitigation strategies include energy efficiency, use of alternative fuels, clinker substitution, and carbon capture and storage. From these results, the partial replacement of clinker by supplementary cementitious materials (SCMs) has great potential for the next 20 years (Scrivener K. et al., 2018).
The use of SCMs in cements is already practiced worldwide, standardized by, for example, prEN 197-1:2018 (E) in Europe, ABNT NBR 16697:2018 in Brazil, and ASTM C 595:2019 in the United States. However, the synergistic effect of combining supplementary cementitious materials (SCMs) as partial substitutes for clinker enables reducing the clinker factor and, hence, the carbon footprint, while maintaining the standardized requirements of cements. This motivates research on new cement formulations considering varied combinations of SCMs, such as calcined clay and limestone filler (Scrivener K. L. et al., 2018), calcined clay or natural pozzolan, limestone filler, and blast furnace slag (Makhloufi et al., 2015; Wang et al., 2021), and blast furnace slag, fly ash, and limestone filler (Schöler et al., 2015).
Limestone-calcined clay (LC3), a family of clinker, calcined clay, and limestone filler mixes, is being widely studied for achieving mechanical performance equivalent to ordinary Portland cement by using widely available constituents (Scrivener K. L. et al., 2018). Kaolinite content in the natural clay, calcination temperature, and calcined clay fineness directly interfere with the compressive strength development of cement (Avet and Scrivener, 2018; Ferreiro et al., 2018). For results comparable to those of ordinary Portland cement, it is recommended that clays have a minimum of 40% kaolinite content (Scrivener K. L. et al., 2018).
When calcined clay and limestone filler are combined, the pozzolanic reaction between the calcined clay and portlandite forms C-A-S-H, and the alumina in the calcined clay reacts with the carbonate supplied by the limestone filler. The hydrated carboaluminate precipitates and increases the hydrated phase volume and matrix density, with mechanical strength and durability benefits (Antoni et al., 2012; Puerta-Falla et al., 2015). The more compact microstructure improves the chloride penetration resistance and permeability relative to ordinary Portland cement (Dhandapani et al., 2018; Zolfagharnasab et al., 2021).
It is well-known from the literature that the low clinker content can affect the pH of the concrete’s pore solution, which directly relates to the stability of the passive film on the reinforcement–that controls the corrosive processes in the structure–and is responsible for the stability of the cement paste hydrates, contributing to the overall durability of the concrete (Taylor, 1997; Shah and Bishnoi, 2018; Cascudo et al., 2021). However, Cascudo et al. (2021) observed that carbonation and the use of mineral additions reduce the electrical conductivity of the concrete pore solution.
Other alumina-rich SCMs, such as blast furnace slag and fly ash, can also be combined with limestone filler to explore the beneficial synergistic effect on mechanical strength and durability (Parashar and Bishnoi, 2021). While the limestone filler favors hydration at early ages, blast furnace slag and fly ash hydrate more slowly (Menendez et al., 2003; Wang, 2018) and supply alumina to form carboaluminates (De Weerdt et al., 2011; Arora et al., 2016).
Although the available blast furnace slag and fly ash are not enough to keep up with the increased demand by the cement industry (Scrivener K. et al., 2018), their combination with calcined clay and limestone filler should be explored to maximize the synergistic potential (Wang et al., 2021).
Clay suitable for cement use is widely available. However, the pozzolanic properties are governed by its kaolinite content, to be converted into metakaolin through adequate calcination. Clays with higher kaolinite contents and calcined at higher temperatures potentially result in cement with higher mechanical strengths. Avet and Scrivener (2018) recommended clays with at least 40% kaolinite content for use in LC3. Temperatures between 600 and 800°C are needed to develop pozzolanic properties (Fernandez et al., 2011), and Ferreiro et al. (2018) indicate the 700-850°C temperature range for the greatest conversion of kaolinite into metakaolin. Hence, calcined clay’s contribution to reducing CO2 emissions is lower than that of blast furnace slag and fly ash, which are coproducts of steel production and power generation, respectively, in coal-fired thermoelectric plants (Saade et al., 2015).
High-grade metakaolin commonly used as SCM is of limited availability and applicable to other industries, hence costly (Juenger et al., 2019). So, the potential use of clays with kaolinite content below recommendations has been also investigated by, for example, Zolfagharnasab et al. (2021), who observed improvements in permeability and chloride penetration resistance for varied kaolinite contents, and Cardinaud et al. (2021), who concluded that calcined clays with low (21%) and high (68%) metakaolin contents are likely to result in similar long-term hydration degree and products.
Given the importance of the synergistic effect between SCMs to obtain cement with satisfactory mechanical performance and reduced environmental impact, this article studies the interaction of different SCMs in thirteen composite cements, divided into four series: Series A, formed by the combination of calcined clay and limestone filler; Series B, formed by the combination of blast furnace slag and limestone filer; Series C, formed by the combination of fly ash and limestone filler, and Series D, formed by quaternary and multi-addition cements composed of calcined clay, blast furnace slag, fly ash and limestone filler. For each cement, the compressive strength was determined at 3, 7, 28, 91, and 365 days. The GHG emissions (expressed in CO2eq) embodied in each blend were estimated through life cycle assessment and related to the blends’ compressive strength unit.
2 Materials and Methods
2.1 Materials
The materials used were Portland cement of high initial strength (CP-V-ARI), equivalent to CEM I 42.5R, blast furnace slag, fly ash, calcined clay, and limestone filler, provided by different cement industries in Brazil. The cement used is composed of approximately 89% clinker, 6% limestone filler, and 5% gypsum. The calcined clay and the fly ash were milled in laboratory facilities. For the calcined clay, a ball mill was used for 5 h, with a 50 kg load and without dispersant. After this time no significant reduction in fineness was observed. For the fly ash, a ring mill was used for 4 min. The remaining constituents followed the granulometry practiced by the Brazilian cement industry, with Dv,50 close to 10 µm. Table 1 presents the chemical composition, determined by X-Ray Fluorescence (FRX) (NexGo–Rigaku) and the main physical characteristics of the materials used. Figure 1 shows the particle size distribution, determined by laser granulometry (CILAS–1090 LD). Figure 2A shows the minerals present in each SCM, identified from X-Ray Diffraction with molybdenum radiation (Ultima IV Ray diffractometer), while Figure 2B presents the particle morphologies observed by Scanning Electron Microscopy (SEM) (EVO MA 10–Zeiss).
According to the Brazilian cement manufacturer that supplied the calcined clay, its kaolinite content was around 32% and the calcination temperature ranged between 450-500°C, which is below the recommendations to maximize the conversion of kaolinite into metakaolin. This calcined clay is currently used to produce commercial pozzolanic cement, for its pozzolanic activity (601.54 mg Ca(OH)2/g) determined by the modified Chapelle method (ABNT NBR 15895:2010) complies with the required consumption of 436 mg Ca(OH)2/g to be considered a pozzolanic SCM (Raverdy et al., 1980).
The fly ash used presented the pozzolanic activity of 708.36 mg Ca(OH)2/g) according to the modified Chapelle method, and also complies with the requirement for pozzolanic mineral additions. The vitrification degree (98%), refraction index (1.65), and CaO/SiO2 ratio (>1) confirmed that the studied blast furnace slag’s reactivity was compatible with use in cement production (Silva et al., 2017).
2.2 Mix Design
Table 2 shows the composition, by mass, of the studied blended cements. Thirteen composite cements with at least two SCMs were proposed. The combinations were defined based on international standards, such as the European standard prEN 197-1: 2018; on the forecasts presented by the Technology Roadmap: Low-Carbon Transition in the Cement Industry (IEA et al., 2018) and by the Cement Technology Roadmap–Carbon Emissions Reduction Potential in Brazilian Cement Industry by 2050 (SNIC, 2019); and on the literature review on ternary and quaternary cements (Adu-Amankwah et al., 2017; Scrivener K. L. et al., 2018; Wang, 2018; Wang et al., 2021).
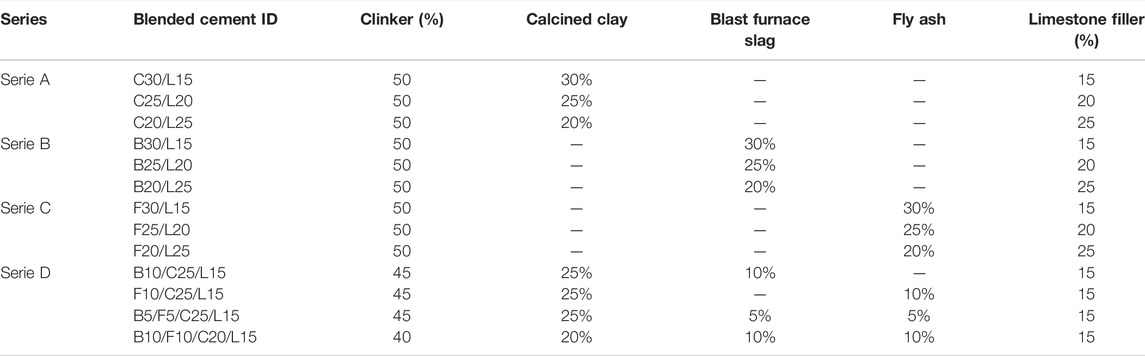
TABLE 2. Proportions of constituents used in the blended cements (% by mass). All cements contain 5% gypsum.
The gypsum content can affect the hydration, phase assemblage, porosity, and strength in cementitious materials and varies according to clinker, SCM, and gypsum characteristics (Andrade Neto et al., 2021). All blended cements are composed of 5% of gypsum in a mass of cement. This is in line with the recommendation for the LC3 (Scrivener K. et al., 2018) and is also used in Brazilian cements. The cement CP-V-ARI, equivalent to CEM I 42.5R, was used as a clinker supplier in the formulations, so extra gypsum was added until the 5% content in mass was achieved by each blend. The clinker proportion is the complement to reach the total blend mass.
Considering the average 5% gypsum content, in mass, Brazilian commercial cements may have up to 75% of blast furnace slag and up to 50% of fly ash, i.e., clinker factors of about 20 and 45%, respectively. Clinker factors around 50% in cements with different SCMs help to minimize the reduction in mechanical properties compared to those without mineral additions (Bohác et al., 2014; Avet and Scrivener, 2018). Thus, a 50%-clinker factor was adopted in the formulation of three series of blended cements. A fourth group (Series D), with a clinker factor between 40 and 45%, was designed to explore the effect of combining blast furnace slag and fly ash, two SCMs traditionally used in cement production, but insufficient to meet the growing demand of the industry–with other SCMs (calcined clay and limestone filler). The Technology Roadmap: Low-Carbon Transition in the Cement Industry (IEA et al., 2018) foresees a global average cement with 18% limestone filler in 2050. The Brazilian equivalent study (SNIC, 2019) predicts an even higher limestone filler content (25%) in the average cement expected for that same year. Such expectations were accounted for in the studied cement formulations, which present limestone filler contents between 15 and 25%.
The blends were named using letters that represent the SCMs used (“B” for blast furnace slag, “F” for fly ash, “C” for calcined clay, and “L” for limestone filler), followed by their percentage in the cement composition.
In cements of Series A, cement C30/L15 replicates the same proportions of the best performing LC3 studied by Antoni et al. (2012) and is, therefore, a relevant analytic reference. Blends C25/L20 and C20/L25 seek to evaluate the influence of increased limestone filler content while reducing the calcined clay content. Calcined clay was replaced by blast furnace slag in Series B, and by fly ash in Series C, maintaining the composition percentages of Series A cements. The cements B30/L15, B25/L20, F30/L15, and F25/L20 are already standardized by the European standard prEN 197-1:2018 (E) through the cements CEM II/C-M (S-L) and CEM II/C-M (V-L).
As mentioned, Series D cements B10/C25/L15 and F10/C25/L15 were formulated to evaluate the interaction of calcined clay and limestone filler with blast furnace slag and fly ash, respectively. Cements B5/F5/C25/L15 and B10/F10/C20/L15 seek to evaluate the joint effect of all the SCMs studied.
2.3 Test Methods
2.3.1 Mechanical Performance Assessment
The compressive strength of the cements was determined in cylindrical mortar specimens with a diameter of 5 cm, height of 10 cm, water/binder ratio of 0.48, and sand: cement ratio of 3:1 (ABNT NBR 7215:2019). The specimens were kept submerged in saturated lime water and the determination of compressive strength was performed at the ages of 3, 7, 28, 91, and 365 days. The results were statistically treated by applying analysis of variance (ANOVA) with a 5% significance level to identify similar or different groups and then applying the Tukey test for comparison of means to identify groups with higher and lower compressive strengths. For each series, the interaction between SCM content and age was verified. Subsequently, all cements were evaluated by age to verify which ones present higher and lower compressive strengths and which ones are statistically similar. The statistical analyses were performed using Statistica v.10.0 software.
2.3.2 Environmental Performance Assessment
The eco-intensity of a product or service is an indicator for the “use of nature” (materials/energy/pollution generated) per unit of “value added or output” and it is the inverse of eco-efficiency. Eco-efficiency can be improved by reducing the environmental impact of the material’s production, improving its performance, or by doing both.
Eco-intensity herein refers to the GHG emissions for producing one tonne of cement per unit of compressive strength at each testing age (3, 7, 28, 91, and 365 days, expressed in CO2eq/MPa. This GHG emission intensity enables jointly analyzing environmental and mechanical performance and to identify optimal cement combinations (Damineli et al., 2010; Malacarne et al., 2021). For comparison sake, cement GHG emission intensity was normalized relative to the C30/L15 (LC3).
The life cycle GHG emissions cover a single environmental issue (global warming), and were modeled from “cradle to gate” using the Ecoinvent v. 2.2 databases, substituting the energy matrix for the Brazilian matrix in cases where local data were not available, and the life cycle impact assessment (LCIA) method CML baseline 2001. A clinker GHG emission factor (Efclínker) of 902.47 kgCO2eq per tonne produced was based on datasets in the Ecoinvent 2.2 database (Silva et al., 2017). The GHG emission factor of each cement constituent is presented in Table 3. Based on those values, the GHG emissions embodied in each blend were calculated according to the following equation:
where Efconst is the emission factor (in CO2eq) of each cement constituent, and Pc is its corresponding proportion (%) of the blended cement.
3 Results and Discussion
3.1 Mechanical Performance
Figure 3 shows how the combinations of SCMs influence the mechanical strength of cements. In all combinations studied, the compressive strength increased with advancing age due to clinker hydration and reactions involving the SCMs, as identified by Yu et al. (2021).
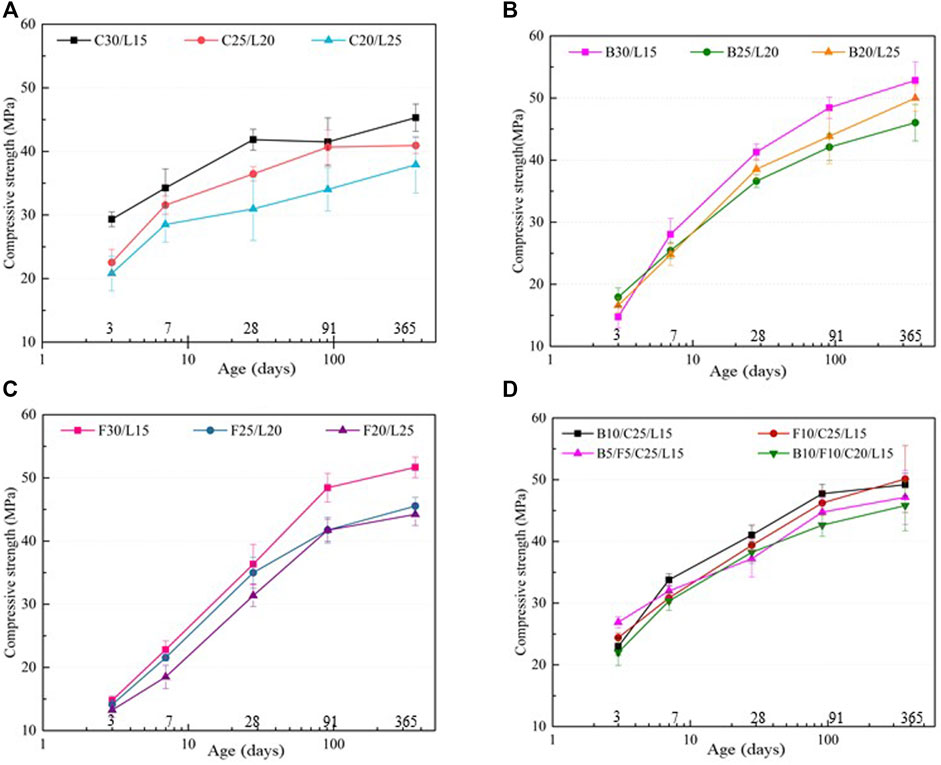
FIGURE 3. Compressive strength of blended cement using (A) calcined clay and limestone filler, (B) blast furnace slag and limestone filler, (C) fly ash and limestone filler and (D) multiple additions at 3, 7, 28, 91 and 365 days.
Figure 3A shows the effect of the combinations of calcined clay and limestone filler on the development of the compressive strength of the Series A cements. The compressive strength is related to the proportion of calcined clay and limestone filler. As the limestone filler content increases (and that of calcined clay decreases), it causes a dilution effect that reduces the compressive strength (Wang et al., 2019). As the calcined clay content decreases, less alumina is available to react with calcium carbonate and form Hemi- and monocarboaluminate (Tang et al., 2019). In absolute terms, the best compressive strength results were obtained for the 2:1 ratio (calcined clay: limestone filler), a composition similar to LC3.
When evaluating the compressive strength evolution over time, the major compressive strength development occurred up to 28 days. From 3 to 28 days, the increase in strength was 43, 62, and 49% for the C30/L15, C25/L20, and C20/L25 cements, respectively. Between 28 and 365 days, the strength increased by only 8% for C30/L15, 12% for C25/L20, and 22% for C20/L15. Similar results were reported by Zolfagharnasab et al. (2021): the compressive strength of low-grade calcined clay and limestone filler blends mostly developed in the first 28 days, with an additional ∼ 20% increase between 28 and 360 days. The initial compressive strength gain is due to the rapid chemical reactions between the alumina from the calcined clay and the carbonate from the limestone filler, resulting in carboaluminate phases that densify the matrix (Antoni et al., 2012; Puerta-Falla et al., 2015; Scrivener K. L. et al., 2018).
Figure 3B shows the compressive strength of cements with blast furnace slag and limestone filler (Series B). The three combinations showed a similar trend. At 3 and 7 days, the results overlap and are statistically equal for each age. The difference begins to show at ages 28, 91, and 365 days, for which the B30/L15 cement outperforms.
Considering the mean compressive strength values, at ages 3 and 7 days, cements B25/L20 and B20/L25, which have more limestone filler, presented higher compressive strengths than B30/L15. This is reversed after 28 days, when B30/L15, with a higher content of blast furnace slag, shows higher compressive strength. This trend was also identified by Makhloufi et al. (2015) and demonstrates the positive influence of limestone filler on hydration at three and seven days and how the hydration of blast furnace slag outperforms the effect of limestone filler with advancing age. According to those authors, at three and seven days, the limestone filler particles act as nucleation points that favor the clinker’s hydration and, consequently, the mechanical strength development.
Compared with the interaction of calcined clay and limestone filler, the combination of blast furnace slag and limestone filler shows lower compressive strengths at 3 and 7 days, similar values at 28 days, and continuous growth at later ages (Parashar and Bishnoi, 2021). From 3 to 28 days, the increase in compressive strength was 180, 102, and 132% for the B30/L15, B25/L20, and B20/L25 cements, respectively. Between 28 and 365 days, the increment ranged from 25 to 30% for the three cements studied. The long-term compressive strength development could be associated with the hydration of blast furnace slag and hydrated product formation, as demonstrated by Parashar and Bishnoi (2021) and Wang et al. (2021). When studying the same combination of blast furnace slag and limestone filler, Parashar and Bishnoi (2021) observed that blast furnace slag hydration and conversion of Hemi- to mono-carboaluminate contribute to the long-term strength development. Wang et al. (2021) observed that the consumption of CH in cements with blast furnace slag and limestone filler occurred mainly between 28 and 91 days, which explains the long-term strength development.
The interaction of limestone filler with blast furnace slag also forms carboaluminates. However, this effect is not as intense as in the combination of limestone filler with calcined clay, because the alumina supplied by blast furnace slags is less reactive (Adu-Amankwah et at., 2017; Parashar and Bishnoi, 2021). Furthermore, Adu-Amankwah et al. (2017) identified the presence of belite in pastes of cements containing blast furnace slag and limestone filler up to 180 days of age, whose hydration can justify the strength gain registered at 365 days.
Figure 3C shows the compressive strength of the combinations of fly ash and limestone filler (Series C). As in the blends with blast furnace slag, the strengths at 3 and 7 days were lower than the strength achieved by the calcined clay combination, and strength development was observed up to 365 days, due to the slow pozzolanic reactions, in line with observations of Wang, 2018 and Yu et al., 2017. At 3, 7, and 28 days, the compressive strengths achieved for the three cements are statistically similar. However, at 91 and 365 days, the compressive strength of F30/L15 is statistically higher than the other two cements. Thus, it can be concluded that no significant changes in compressive strength were observed for the combinations with limestone filler contents ranging between 20 and 25%. Despite the small alterations, in relation to F30/L15, the compressive strength decreased with the increase in limestone filler content and reduction of fly ash content. The same behavior was identified by De Weerdt et al. (2011) and Jiang et al. (2020) in cements with high clinker factors.
Figure 3D shows the compressive strength of Series D blends, which contain more than four SCMs. The results show the synergistic effect between the SCMs used: even with a lower clinker factor than the cements of Series A, B, and C, the compressive strengths at 3 and 7 days overcame those of all other cements, except C30/L15. At 28 days, the strengths obtained for Series D cements were similar to those of C30/L15 and B30/L15. Compressive strength growth was still observed between 91 and 365 days. Thus, the progress of blast furnace slag and/or fly ash hydration can improve the compressive strength development at later ages and complement the early compressive strength benefits brought by calcined clay and limestone filler. The compressive strengths of the cements of Series D at each age showed no statistically significant difference.
Among the different cements composed of calcined clay, limestone filler and blast furnace slag studied by Wang et al. (2021), one follows SCMs proportions close to B10/C25/L15. Its compressive strengths at 28 ( ∼ 43 MPa) and 91 days ( ∼ 47 MPa) were similar to those of B10/C25/L15, despite the higher kaolinite content (49%) in the clay used by Wang et al. (2021) relative to that herein used (32%). According to those authors, the rapid reaction of the calcined clay, associated with the nucleation effect of the limestone filler, compensates for the slow hydration of the blast furnace slag, while the blast furnace slag continues to contribute to long-term strength development. Wang et al. (2021) also showed that the consumption of CH in cements with blast furnace slag and limestone filler occurred mainly between 28 and 91 days, whereas in calcined clay blends, the consumption of CH occurred between 3 and 91 days.
In Figure 4, the compressive strength of the studied cements was normalized relative to the compressive strength of cement LC3 C30/L15 at 3, 7, 28, 91, and 365 days. C30/L15 presented the highest compressive strength at 3 days (29.3 MPa). At 7 and 28 days, the Series D cements achieved approximately 90% of the strength of C30/L15, and B10/C25/L15 stood out. Slight changes in the fineness of SCMs (Ferreiro et al., 2017), as well as optimal sulfate content (Adu-Amankwah et al., 2018) could further improve Series D cements results. At 91 and 365 days, almost all Series B, C, and D blends outperformed C30/L15, demonstrating the influence of blast furnace slag hydration and fly ash pozzolanic reactions on long-term strength development.
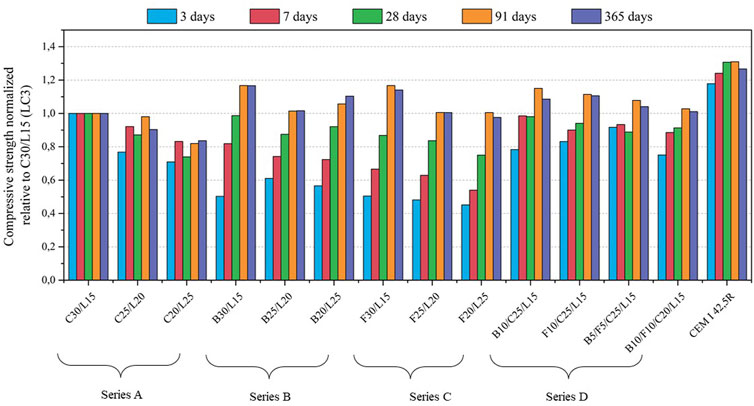
FIGURE 4. Compressive strength of blended cements normalized relative to C30/L15(LC3) at 3, 7, 28, 91 and 365 days.
The analysis of variance by age showed that the p-value was less than 0.05 for all ages, indicating a significant interaction between the composition of cements and compressive strength, i.e., that cements are in distinct groups of compressive strength. At three days, C30/L15 and B5/F5/C25/L15 compose the cements subset with the highest compressive strength. In turn, cements with fly ash and limestone filler are in the lowest compressive strength subgroup. At 7 days, the cements C30/L15, C25/L20, B10/C25/L15, F10/C25/L15, and B5/F5/C25/L15 compose the subgroup of cement with compressive strength statistically superior to the other cements. At 28 days, C30/L15, B30/L15, B20/L15, B10/C25/L15, F10/C25/L15, and B10/F10/C20/L15 had statistically superior compressive strength, while the cements with fly ash and limestone filler pertained to the subgroup with the lowest values of compressive strength.
At 91 and 365 days, the cements B30/L15, B20/L25, F30/L15, B10/C25/L15, F10/C25/L15, and B5/F5/C25/L15 form the subgroup with the highest compressive strengths. This means that the fly ash and blast furnace slag hydration reactions continued to occur and increased the compressive strength over time. In contrast, the cements containing calcined clay and limestone filler, which were in the subgroups with the highest compressive strengths up to 28 days, shifted to the subgroups with the lowest compressive strengths at later ages.
3.2 Environmental Performance
Figure 5A shows the GHG emissions (in CO2eq) per tonne of each composite cement. The emissions of CEM I 42.5R cement are included for reference. In Figure 5B, the GHG emissions were normalized relative to blend LC3 C30/L15.
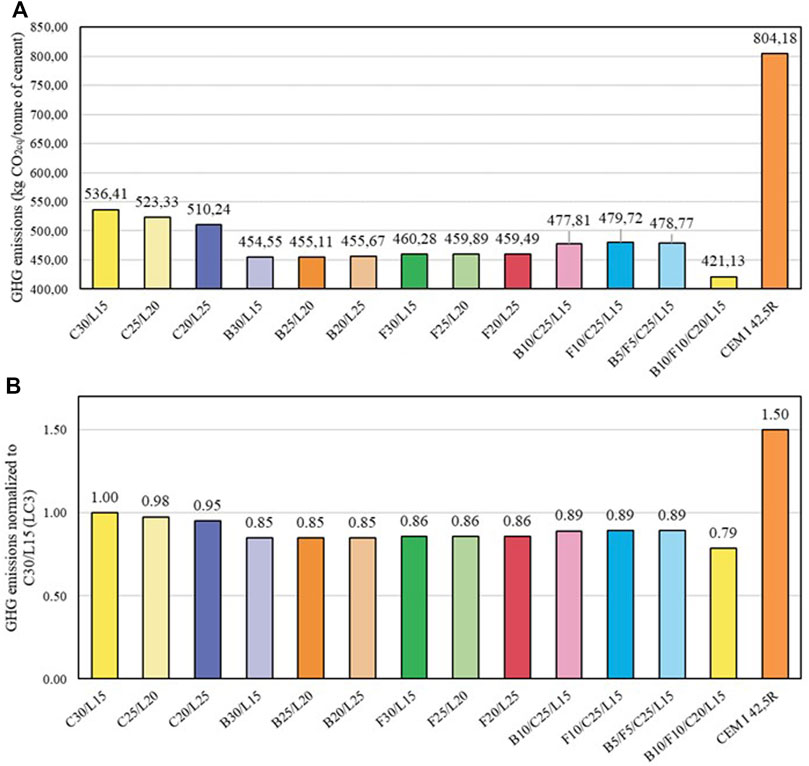
FIGURE 5. (A) cements'GHG emissons (in CO2eq); (B) GHG emissions normalized relative to GHG emissions of C30/L15 (LC3).
The cement CP-V-ARI, equivalent to CEM I 42,5R, has the highest clinker content of all Brazilian commercial cements and presents the highest GHG emissions of the cements herein studied: approximately 50% higher than that of LC3 C30/L15. From the cements with SCMs, Series A cements emit the most GHG due to clay calcination. Cements in Series B and C had similar GHG emissions, as the clinker factor was maintained, and the constituent proportions varied little. Replacing calcined clay with blast furnace slag and fly ash reduces GHG emissions by approximately 15%. Hence, cements in Series D had lower GHG emissions for its lower clinker factor (40-45%) relative to Series A to C and for using SCMs with lower GHG emissions to achieve it. Cement B10/F10/C20/L15 stood out for reducing GHG emissions by 21% when compared to C30/L15.
Figure 6 presents the GHG emissions intensity (in CO2eq/MPa) at 3, 7, 28, 91 and 365 days, normalized relative to LC3 C30/L15 (GHG emissions intensity = 1,0). Series D cements consistently demonstrated the benefits of the interaction of SCMs jointly on GHG emissions and compressive strength. Within that series, the multi-addition blend B5/F5/C20/L15 and B10/F10/C20/L15 stand out. After 7 days, B10/F10/C20/L15 outperforms all other formulations. At 3 days, all other cements performed worse than LC3 C30/L15. Hence, cements with low-GHG emission SCMs, like those with blast furnace slag (Series B) and fly ash (Series C), may not be the best options in terms of GHG emissions intensity if the strength development is slow.
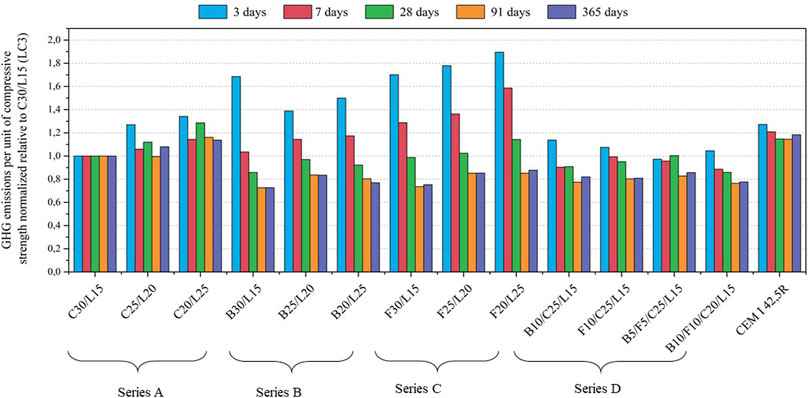
FIGURE 6. GHG emissions per unit of compressive strength normalized relative to C30/L15 (LC3) at 3, 7, 28, 91 and 365 days.
Long-term GHG emission intensities are similar for Series A, B, and C. Series B and C reach similar strengths at 28 days and especially at later ages, but Series D offers an important practical advantage of starting from higher initial strengths and offering balanced mechanical and environmental performance at all ages.
4 Conclusion
The global cement industry is aware of the limited availability of SCMs with adequate quality, which is unlikely to increase in the upcoming years, and of the need to reduce the environmental impacts of cements. Exploring the viability of other SCMs and their combinations becomes critical. Optimal formulations of these additions can combine low GHG intensity with the mechanical performance demanded by the market practice.
The combination of calcined clay and limestone filler resulted in the highest compressive strength at 3 days, which developed pronouncedly between 3 and 28 days and subtly at later ages. This behavior differs from both blast furnace slag plus limestone filler blends and fly ash plus limestone filler formulations, in which the compressive strength was low at 3 days but showed observable growth up to 365 days.
Quaternary and multi-addition cements (Series D), in which the clinker factor was reduced and blast furnace slag and/or fly ash were added to the calcined clay and limestone filler, showed a combination of effects resulting from the characteristics of the SCMs. The four cements in Series D showed similar trends: 1) compressive strength at 3 days was higher than ternary blast furnace slag and limestone filler (Series B) or fly ash and limestone filler (Series C) cements, due to the insertion of calcined clay, which, in the presence of limestone filler, contributes to the rapid hydration reactions; and 2) compressive strength development continued until 365 days due to the slower hydration reactions of blast furnace slag and fly ash. The cement B10/C25/L15 stood out for equaling the strengths of LC3 C30/L15 at 7 and 28 days and surpassing them at 91 and 365 days, even with 5% less clinker. The lower clinker factor in multi-addition cements enabled a reduction of up to 21% (B10/F10/C20/L15) in GHG emissions compared to LC3 C30/L15. Due to the calcination process, cements with calcined clay and limestone filler had higher GHG emissions than those with other SCMs.
The GHG emission intensity relates to the environment and the mechanical performances of cements and offers a broader perspective for their selection. Series D cements consistently outperformed after 3 days of age, demonstrating the benefits of the synergistic effect between SCMs jointly on GHG emissions and compressive strength. Such an effect enables not only reduce the clinker factor and GHG emissions but also the GHG emission intensity, which relates to both. This study showed that the formulated cements, particularly those in Series D, are potential alternatives for reducing the GHG emissions, whilst preserving mechanical performance demanded by construction market practices.
From a multidisciplinary analysis standpoint, durability assessments are necessary to complement the reported findings, as low clinker contents can affect the pH of the concrete’s pore solution and carbonation which ultimately lead to deterioration.
Data Availability Statement
The original contributions presented in the study are included in the article/Supplementary Material; further inquiries can be directed to the corresponding author.
Author Contributions
ALMVR: Methodology, investigation, writing—original draft, formal analysis, and writing—review and editing. ÁÁFM: Methodology, investigation, writing—original draft, formal analysis. VG: Resources, funding acquisition; methodology, formal analysis, and writing—review and editing. AFB: Resources, funding acquisition, methodology, writing—review. MRMS: Methodology, writing—review. MGDS: Conceptualization, resources, project administration, funding acquisition, methodology, formal analysis, writing—review and editing, supervision.
Funding
This study was financed in part by the Coordenação de Aperfeiçoamento de Pessoal de Nível Superior - Brasil (CAPES) - Finance Code 001 and by the National Council for Scientific and Technological development - CNPq (grant #313409/2021-8).
Conflict of Interest
The authors declare that the research was conducted in the absence of any commercial or financial relationships that could be construed as a potential conflict of interest.
Publisher’s Note
All claims expressed in this article are solely those of the authors and do not necessarily represent those of their affiliated organizations, or those of the publisher, the editors, and the reviewers. Any product that may be evaluated in this article, or claim that may be made by its manufacturer, is not guaranteed or endorsed by the publisher.
Acknowledgments
The authors thank the Civil Engineering Graduate Program of the University of Campinas, the Civil Engineering Graduate Program of the Federal University of Espirito Santo, the Laboratory for Testing of Building Materials of the Federal University of Espírito Santo and the Brazilian Portland Cement Association for supporting this research.
References
Adu-Amankwah, S., Black, L., Skocek, J., Ben Haha, M., and Zajac, M. (2018). Effect of Sulfate Additions on Hydration and Performance of Ternary Slag-Limestone Composite Cements. Constr. Build. Mater. 164, 451–462. doi:10.1016/j.conbuildmat.2017.12.165
Adu-Amankwah, S., Zajac, M., Stabler, C., Lothenbach, B., and Black, L. (2017). Influence of Limestone on the Hydration of Ternary Slag Cements. Cem. Concr. Res. 100, 96–109. doi:10.1016/j.cemconres.2017.05.013
American Society for Testing and Materials (ASTM) (2019). ASTM C 595: Standard Specification for Portland Cement. West Conshohocken: ASTM.
Andrade Neto, J. d. S., De la Torre, A. G., and Kirchheim, A. P. (2021). Effects of Sulfates on the Hydration of Portland Cement - A Review. Constr. Build. Mater. 279, 122428. doi:10.1016/j.conbuildmat.2021.122428
Antoni, M., Rossen, J., Martirena, F., and Scrivener, K. (2012). Cement Substitution by a Combination of Metakaolin and Limestone. Cem. Concr. Res. 42, 1579–1589. doi:10.1016/j.cemconres.2012.09.006
Arora, A., Sant, G., and Neithalath, N. (2016). Ternary Blends Containing Slag and Interground/blended Limestone: Hydration, Strength, and Pore Structure. Constr. Build. Mater. 102, 113–124. doi:10.1016/j.conbuildmat.2015.10.179
Associação Brasileira de Normas Técnicas (2018). NBR 16697: Cimento Portland - Requisitos. Rio de Janeiro: ABNT.
Associação Brasileira de Normas Técnicas (2019). NBR 7.215: Cimento Portland – Determinação da resistência à compressão de corpos de prova cilíndricos. Rio de Janeiro: ABNT.
Avet, F., and Scrivener, K. (2018). Investigation of the Calcined Kaolinite Content on the Hydration of Limestone Calcined Clay Cement (LC3). Cem. Concr. Res. 107, 124–135. doi:10.1016/j.cemconres.2018.02.016
Briki, Y., Avet, F., Zajac, M., Bowen, P., Haha, M. B., and Scrivener, K. (2021). Understanding of the Factors Slowing Down Metakaolin Reaction in Limestone Calcined Clay Cement (LC3) at Late Ages. Cem. Concr. Res. 146, 106477. doi:10.1016/j.cemconres.2021.106477
Cardinaud, G., Rozière, E., Martinage, O., Loukili, A., Barnes-Davin, L., Paris, M., et al. (2021). Calcined Clay - Limestone Cements: Hydration Processes with High and Low-Grade Kaolinite Clays. Constr. Build. Mater. 277, 122271. doi:10.1016/j.conbuildmat.2021.122271
Cascudo, O., Pires, P., Carasek, H., de Castro, A., and Lopes, A. (2021). Evaluation of the Pore Solution of Concretes with Mineral Additions Subjected to 14 Years of Natural Carbonation. Cem. Concr. Compos. 115, 103858. doi:10.1016/j.cemconcomp.2020.103858
Damineli, B. L., Kemeid, F. M., Aguiar, P. S., and John, V. M. (2010), Measuring the Eco-Efficiency of Cement Use Cem. Concr. Compos., 32 (8). 555–562. doi:10.1016/j.cemconcomp.2010.07.009
De Weerdt, K., Kjellsen, K. O., Sellevold, E., and Justnes, H. (2011). Synergy between Fly Ash and Limestone Powder in Ternary Cements. Cem. Concr. Compos. 33 (1), 30–38. doi:10.1016/j.cemconcomp.2010.09.006
Dhandapani, Y., Sakthivel, T., Santhanam, M., Gettu, R., and Pillai, R. G. (2018). Mechanical Properties and Durability Performance of Concretes with Limestone Calcined Clay Cement (LC3). Cem. Concr. Res. 107, 136–151. doi:10.1016/j.cemconres.2018.02.005
El Fami, N., Ez-Zaki, H., Boukhari, A., and Diouri, A. (2021). Rheological Behaviour and Mechanical Properties of Moroccan Ternary Binder's Portland Clinker-Fly Ash-Limestone. Constr. Build. Mater., 279. 122513. doi:10.1016/j.conbuildmat.2021.122513
European Committee for Standardization (CEN) (2018). prEN 197-1: 2018 Cement – Part 1: Composition, Specifications and Conformity Criteria for Common Cements. Brussels, Belgium: CEN.
Fernández, Á., García Calvo, J. L., and Alonso, M. C. (2018). Ordinary Portland Cement Composition for the Optimization of the Synergies of Supplementary Cementitious Materials of Ternary Binders in Hydration Processes. Cem. Concr. Compos. 89, 238–250. doi:10.1016/j.cemconcomp.2017.12.016
Fernandez, R., Martirena, F., and Scrivener, K. L. (2011). The Origin of the Pozzolanic Activity of Calcined Clay Minerals: A Comparison between Kaolinite, Illite and Montmorillonite. Cem. Concr. Res. 41 (1), 113–122. doi:10.1016/j.cemconres.2010.09.013
Ferreiro, S., Canut, M. M. C., Lund, J., and Herfort, D. (2019). Influence of Fineness of Raw Clay and Calcination Temperature on the Performance of Calcined Clay-Limestone Blended Cements. Appl. Clay Sci. 169, 81–90. doi:10.1016/j.clay.2018.12.021
Ferreiro, S., Herfort, D., and Damtoft, J. S. (2017). Effect of Raw Clay Type, Fineness, Water-To-Cement Ratio and Fly Ash Addition on Workability and Strength Performance of Calcined Clay - Limestone Portland Cements. Cem. Concr. Res. 101, 1–12. doi:10.1016/j.cemconres.2017.08.003
Jiang, D., Li, X., Lv, Y., Zhou, M., He, C., Jiang, W., et al. (2020). Utilization of Limestone Powder and Fly Ash in Blended Cement: Rheology, Strength and Hydration Characteristics. Constr. Build. Mater. 232, 117228–228. doi:10.1016/j.conbuildmat.2019.117228
Juenger, M. C. G., Snellings, R., and Bernal, S. A. (2019). Supplementary Cementitious Materials: New Sources, Characterization, and Performance Insights. Cem. Concr. Res. 122, 257–273. doi:10.1016/j.cemconres.2019.05.008
Lin, R.-S., Lee, H.-S., Han, Y., and Wang, X.-Y. (2021). Experimental Studies on Hydration-Strength-Durability of Limestone-Cement-Calcined Hwangtoh Clay Ternary Composite. Constr. Build. Mater. 269, 121290. doi:10.1016/j.conbuildmat.2020.121290
Makhloufi, Z., Chettih, M., Bederina, M., Kadri, E. l. H., and Bouhicha, M. (2015). Effect of Quaternary Cementitious Systems Containing Limestone, Blast Furnace Slag and Natural Pozzolan on Mechanical Behavior of Limestone Mortars. Constr. Build. Mater. 95, 647–657. doi:10.1016/j.conbuildmat.2015.07.050
Menéndez, G., Bonavetti, V., and Irassar, E. F. (2003). Strength Development of Ternary Blended Cement with Limestone Filler and Blast-Furnace Slag. Cem. Concr. Compos. 25 (1), 61–67. doi:10.1016/S0958-9465(01)00056-7
Parashar, A., and Bishnoi, S. (2021). Hydration Behaviour of Limestone-Calcined Clay and Limestone-Slag Blends in Ternary Cement. RILEM Tech. Lett. 6, 17–24. doi:10.21809/rilemtechlett.2021.134
Puerta-Falla, G., Balonis, M., Le Saout, G., Falzone, G., Zhang, C., Neithalath, N., et al. (2015). Elucidating the Role of the Aluminous Source on Limestone Reactivity in Cementitious Materials. J. Am. Ceram. Soc. 98 (12), 4076–4089. doi:10.1111/jace.13806
Saade, M. R. M., Silva, M. G. d., and Gomes, V. (2015). Appropriateness of Environmental Impact Distribution Methods to Model Blast Furnace Slag Recycling in Cement Making. Resour. Conservation Recycl. 99, 40–47. doi:10.1016/j.resconrec.2015.03.011
Salvi Malacarne, C., Rubens Cardoso da Silva, M., Danieli, S., Gonçalves Maciel, V., and Paula Kirchheim, A. (2021). Environmental and Technical Assessment to Support Sustainable Strategies for Limestone Calcined Clay Cement Production in Brazil. Constr. Build. Mater. 310, 125261. doi:10.1016/j.conbuildmat.2021.125261
Schneider, M. (2019). The Cement Industry on the Way to a Low-Carbon Future. Cem. Concr. Res. 124, 105792. doi:10.1016/j.cemconres.2019.105792
Schöler, A., Lothenbach, B., Winnefeld, F., and Zajac, M. (2015). Hydration of Quaternary Portland Cement Blends Containing Blast-Furnace Slag, Siliceous Fly Ash and Limestone Powder. Cem. Concr. Compos. 55, 374–382. doi:10.1016/j.cemconcomp.2014.10.001
Scrivener, K. L., John, V. M., and Gartner, E. M. (2018b). Eco-efficient Cements: Potential Economically Viable Solutions for a low-CO2 Cement-Based Materials Industry. Cem. Concr. Res. 114, 2–26. doi:10.1016/j.cemconres.2018.03.015
Scrivener, K., Martirena, F., Bishnoi, S., and Maity, S. (2018a). Calcined Clay Limestone Cements (LC3). Cem. Concr. Res. 114, 49–56. doi:10.1016/j.cemconres.2017.08.017
Shah, V., and Bishnoi, S. (2018), Carbonation Resistance of Cements Containing Supplementary Cementitious Materials and its Relation to Various Parameters of Concrete. Constr. Build. Mater. 178, 219–232. doi:10.1016/j.conbuildmat.2018.05.162
Silva, M. G., Battagin, A. F., and Gomes, V. (2017). “Cimentos Portland Com Adições Minerais,” in Materiais de Construção Civil e princípios de ciência e engenharia de materiais. Editor G. C. ISAIA. 3rd ed (São Paulo: Ibracon), 791–823.
SNIC (Sindicato Nacional da Indústria do Cimento) (2019). Cement Technology Roadmap: Carbon Emissions Reduction Potential in the Brazilian Cement. France: IEA. Industry by 2050, Rio de Janeiro. Available at: http://snic.org.br/relatorio-roadmap.php.
Tang, J., Wei, S., Li, W., Ma, S., Ji, P., and Shen, X. (2019). Synergistic Effect of Metakaolin and Limestone on the Hydration Properties of Portland Cement. Constr. Build. Mater. 223, 177–184. doi:10.1016/j.conbuildmat.2019.06.059
Taylor, H. F. W. (1997). Cement Chemistry. Second ed. London: Thomas Telford Publishing. doi:10.1680/cc.25929
UNFCC (2021). The Paris Agreement: Essential Elements. Available at: https://unfccc.int/process-and-meetings/the-paris-agreement/the-paris-agreement (accessed November 10, 2021).
Wang, D., Shi, C., Farzadnia, N., Jia, H., Zeng, R., Wu, Y., et al. (2019). A Quantitative Study on Physical and Chemical Effects of Limestone Powder on Properties of Cement Pastes. Constr. Build. Mater. 204, 58–69. doi:10.1016/j.conbuildmat.2019.01.154
Wang, D., Shi, C., Farzadnia, N., Shi, Z., Jia, H., and Ou, Z. (2018). A Review on Use of Limestone Powder in Cement-Based Materials: Mechanism, Hydration and Microstructures. Constr. Build. Mater. 181, 659–672. doi:10.1016/j.conbuildmat.2018.06.075
Wang, H., Hou, P., Li, Q., Adu-Amankwah, S., Chen, H., Xie, N., et al. (2021). Synergistic Effects of Supplementary Cementitious Materials in Limestone and Calcined Clay-Replaced Slag Cement. Constr. Build. Mater. 282, 122648. doi:10.1016/j.conbuildmat.2021.122648
Wang, X.-Y. (2018). Analysis of Hydration and Strength Optimization of Cement-Fly Ash-Limestone Ternary Blended Concrete. Constr. Build. Mater. 166, 130–140. doi:10.1016/j.conbuildmat.2018.01.058
Yu, J., Lu, C., Leung, C. K. Y., and Li, G. (2017). Mechanical Properties of Green Structural Concrete with Ultrahigh-Volume Fly Ash. Constr. Build. Mater. 147, 510–518. doi:10.1016/j.conbuildmat.2017.04.188
Yu, J., Wu, H.-L., Mishra, D. K., Li, G., and Leung, C. K. (2021). Compressive Strength and Environmental Impact of Sustainable Blended Cement with High-Dosage Limestone and Calcined Clay (LC2). J. Clean. Prod. 278, 123616. doi:10.1016/j.jclepro.2020.123616
Keywords: blended cements, supplementary cementitious materials, compressive strength, greenhouse gas emissions, eco-intensity, synergistic effect
Citation: Rodrigues ALMV, Mendes ÁÁF, Gomes V, Battagin AF, Saade MRM and Da Silva MG (2022) Environmental and Mechanical Evaluation of Blended Cements With High Mineral Admixture Content. Front. Mater. 9:880986. doi: 10.3389/fmats.2022.880986
Received: 22 February 2022; Accepted: 16 May 2022;
Published: 01 July 2022.
Edited by:
Ana Paula Kirchheim, Federal University of Rio Grande do Sul, BrazilReviewed by:
Edgardo Irassar, Centro de Investigaciones en Física e Ingeniería del Centro de la Provincia de Buenos Aires, ArgentinaVineet Shah, Callaghan Innovation, New Zealand
Copyright © 2022 Rodrigues, Mendes, Gomes, Battagin, Saade and Da Silva. This is an open-access article distributed under the terms of the Creative Commons Attribution License (CC BY). The use, distribution or reproduction in other forums is permitted, provided the original author(s) and the copyright owner(s) are credited and that the original publication in this journal is cited, in accordance with accepted academic practice. No use, distribution or reproduction is permitted which does not comply with these terms.
*Correspondence: Maristela Gomes Da Silva, bWFyZ29tZXMuc2lsdmFAZ21haWwuY29t, bWFyaXN0ZWxhLnNpbHZhQHVmZXMuYnI=