- Fibre and Particle Engineering Research Unit (FPERU), University of Oulu, Oulu, Finland
The construction and demolition waste generation is increasingly evolving with the rapid urbanization, with more than a quarter of the produced waste being landfilled without further treatment or recycling strategy. Hence, sustainable management and valorization methods such as recycling in construction materials is becoming increasingly essential to tackle the economic and environmental burdens of landfilling waste. Construction and demolition waste recycling has been intensively studied. However, the present study proposes a promising solution for recycling construction and demolition wastes (CDWs) from the precast concrete waste sludge and ashes from paper mill sludge and biomass. Artificial lightweight aggregates were designed and produced by alkali activating a mixture of 50–90 wt% of dried and milled CDW with 3–25 wt% of ash and 5–35 wt% of blast furnace slag. The properties of the produced aggregates were assessed via density, water absorption, porosity, and crushing tests, in addition to microstructural characterizations using XRD and scanning electron microscopy SEM analysis. The optimum NaOH concentration was 8M with the highest mechanical properties and lowest efflorescence. The produced aggregates revealed a high crushing force of 82 N at 28 days with 50 wt% CDW, 15 wt% biomass ash, and 25 wt% blast furnace slag presenting a possible recycling pathway for such side-stream materials.
1 Introduction
The construction industry is one of the substantial powers for the economy of several countries. This sector is a complex combination of several processes, significant number of specialists, organizations, and a large variety of raw materials and unique products (Zid et al., 2020). Therefore, it affects many sustainability aspects, including the economic, social, and environmental attributes. In addition to the economic and social benefits of the construction industry, its environmental drawbacks during the entire lifecycle of buildings represent huge challenges (Ruiz et al., 2020). The employment of a high volume of resources and the high amount of greenhouse emissions associated with Portland cement (PC) production make the construction field one of the main sectors contributing to climate change (Opoku, 2019; Zhou et al., 2021).
Portland cement production results in ∼8–9% of the world’s total CO2 emissions (Kang et al., 2019; Zhao et al., 2020). The consumption and depletion of several natural resources such as sand and gravel and other essential components for construction materials could be challenging for continuous growth. Furthermore, during the construction stage and the operations of the end of life phase of buildings, massive construction and demolition wastes (CDWs) are generated (Ghisellini et al., 2018; Ruiz et al., 2020). CDW is the most generated waste worldwide, counting 30–40% of total solid wastes (Jin et al., 2018). In 2018, about 838 million tons of CDW was generated in the European Union which is almost 35.9% of total solid side streams (Eurostat, 2018). The increase in the urbanization rate (54.3–55 % from 2016 to 2018) leads to excessive generation of construction and demolition waste, increasing the challenges of this sector in terms of sustainability (DESA, 2018; Aslam et al., 2020).
The generation and absence of a proper management plan of CDW represent significant environmental issues such as land deterioration, increased pollution, and resource depletion (Ram and Kalidindi, 2017; Zheng et al., 2017). Therefore, developing new circular economic strategies to reduce the landfilling of CDW while contributing to economic growth has become a priority for sustainable development plans (Lieder and Rashid, 2016). Several approaches have been proposed for CDW recycling worldwide. The reuse of different types of CDW, including crushed concrete, brick, mortars, and plaster as recycled aggregates, has been intensively studied (Bolouri Bazaz and Khayati, 2012; Xuan et al., 2012; Silva et al., 2014; Bravo et al., 2015; Martínez et al., 2016; Braga et al., 2017; Omary et al., 2018; Bandara et al., 2022; He et al., 2022). However, the crushed CDW suffers diverse drawbacks including high water absorption, low strength, significant quality fluctuation, and cracks compared to natural aggregates (Tam and Tam, 2007; Shi et al., 2019). Hence, their utilization leads to low-strength concrete, limiting their utilization to less than 50% (Etxeberria et al., 2006). Other investigations attempt to reuse the fine particles of ground CDW as raw materials for cement clinker production (Kim and Choi, 2012; Schoon, 2015). This recycling strategy is inadequate due to the high energy consumption and the high chemical composition variation between the different CDW samples. Furthermore, the CDW powder has been tested as a cement admixture for construction materials. The results show that no more than 10% of the CDW powder could be incorporated as cement admixture because of the high water demand of the CDW powder (Xiao et al., 2018; Shi et al., 2019). The production of lightweight aggregates from the construction and demolition wastes has been explored in some studies (Mueller et al., 2015; Liu et al., 2020; Nguyen et al., 2021).
Lightweight aggregates (LWAs) are natural or synthesized granular materials with a bulk density of less than 1,200 kg/m3 and a dry particle density below 2,000 kg/m3 (Liu et al., 2020). LWA manufacturing comprises the granulation phase using a pelletization or extrusion technique and the hardening step that could be performed at high temperature via sintering or autoclave, or at low temperature by cold bonding (Baykal and Döven, 2000). Pelletization is an agglomeration method used to amplify the size of the granules, which is controlled by the dosage of solid binder and binding liquid, and the duration of the agglomeration process (Geetha and Ramamurthy, 2010). The sintering process based on atomic diffusion at high temperatures from 1000 to 1200°C is commonly used to produce LWAs (Verma et al., 1998; Mueller et al., 2008).
Several raw materials are used to produce the LWAs, mainly clays (Juimo Tchamdjou et al., 2018; Contrafatto et al., 2020). Research has been directed to develop LWAs from alternative raw material sources, mainly industrial wastes such as paper mill waste, fly ashes, and mining wastes (Dondi et al., 2016; Ayati et al., 2019; Moreno-Maroto et al., 2019). Construction and demolition wastes have also been investigated as raw materials to manufacture LWAs through the sintering method. A range of temperature of 1220–1250°C was used to obtain LWAs with a granule density less than 1,000 kg/m3 (Nguyen et al., 2021). Also, a cold bonding technique was tested for the CDW based aggregates using different cement content and carbonation to enhance the mechanical properties (Shi et al., 2019). Thus, the employment of the so-called cold bonding pelletization technique with the optimization of the hardening time and the early strength of the aggregates could be a cost effective and environmentally friendly method of aggregate manufacturing.
The present work focuses on designing and developing artificial lightweight aggregates using construction and demolition wastes from precast concrete waste sludge by means of the cold bonding method and alkali activation technique. Blast furnace slag, biomass fly ash, and paper mill ash were used as cobinders, and a low-concentration alkaline solution was used as a binding agent. The composition of the cobinder was optimized first; then, the aggregates were prepared at the laboratory level with different proportions of CDW. The properties of LWAs, being the granule density, water absorption, and crushing strength, were assessed, and their mineralogy was studied via XRD analysis.
2 Materials and Methods
2.1 Materials
The construction and demolition waste used was a precast concrete waste sludge produced by the sawing hollow core slabs from Jaro Betongsystemer AS (Norway). Blast furnace slag (BFS) was provided by Finnsementti, with a mean particle size of 10.21 µM. Two ashes were added to the BFS to form the cobinders: biomass ash (FA) and paper mill ash (PMA) collected from a paper sludge and paper waste incineration process from the Bag house filter. Blast furnace slag is one of the high reactive precursors for alkali activated materials production, thus, it was added to the ashes to adjust the chemical composition of the raw materials and improve its reactivity (Fernández-Jiménez et al., 2017; Torres-Carrasco and Puertas, 2017). NaOH pellets (product code: 28245.460) supplied by the VWR was used to prepare the activating solution/binder liquid.
The utilized raw materials in the present study have different particle size distributions (Figure 1 and Table 1). The median particle size ranges from 5.21 to 24 µM. The paper mill ash is the finest material with approximately 90% of the particles less than 34.5 µM and a mean particle size of 13 µM. Then, the CDW and FA have a mean particle size of 20.11 and 37.39 µM, respectively. The grain size and distribution highly impact the reactivity of the raw materials toward alkaline activation. A high share of fine particles might increase the reactivity of the material. However, it can also induce a high-water demand. The blast furnace slag, provided by Finnsementti, has a mean particle size of 10.21 µM. A detailed characterization of the blast furnace slag could be found in the previous study (Perumal et al., 2021).
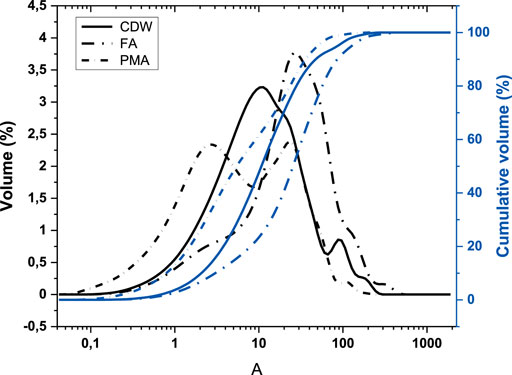
FIGURE 1. Particle size distribution of CDW, biomass ash (FA), and paper mill ash (PMA). The curves in black and blue correspond to the passing volume and cumulative passing volume, respectively.
The CDW and BFS consist mainly of silica and calcium oxide with magnesium oxide in the BFS (Table 1). The biomass ash is mainly composed of SiO2 with about 10 wt% of CaO and a high content of K2O (9.6 wt%). In comparison, the paper mill ash showed a high LOI indicating the high calcite content (29.4 wt% of CaO) with the possible existence of the organic material, and a low SiO2 of 8 wt%. The paper mill ash represents a high content of Na2O (14 wt%) and Cl (8 wt%). The presence of high sodium oxide in the paper mill ash could enhance the alkali activation reaction rate by increasing the alkalinity. Furthermore, the Al2O3 content was low for all the samples and varied from 5 to 9.8 wt%.
The samples show different mineral phases (Figure 2). Calcite and quartz phases are observed for all samples. The CDW also contains albite and gypsum phases, while anorthite, mica, and potassium chloride phases are observed in the biomass ash. The high sodium and chloride in the paper mill ash are present as sodium chloride, sodium carbonate, and calcium sodium aluminum oxide phases. In addition, the PMA contain gehlenite, lime, portlandite, and calcium sulfate phases. It is worth noting that the characteristic peaks of calcite were very intense for the PMA sample, indicating a high amount of this phase, which justifies the LOI observed in the PMA. The FA sample is composed mainly of calcite, quartz, anorthite, phlogopite, laumontite, and sylvite phases.
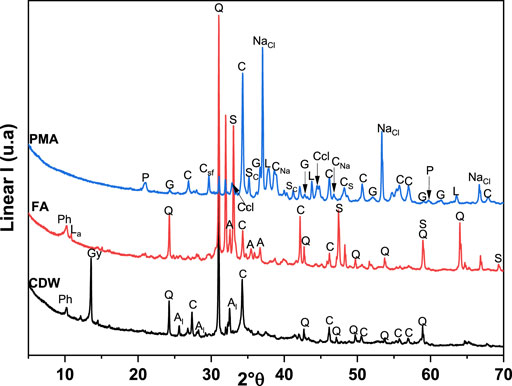
FIGURE 2. XRD patterns of the utilized raw materials (CoKα radiation). Ph: phlogopite (01-070-2125), Gy: gypsum (04-009-3817), La: laumontite (04-015-4254), Q: quartz (04-014-7568), A: anorthite (04-011-2514), Al: albite (04-017-1022), C: calcite (04-008-0198), S: sylvite (04-007-3113), P: portlandite (04-014-8866), G: gehlenite (01-079-2421), CSf: calcium sulfate (04-007-4744), CCl: calcium chloride hydroxide (04-013-0465), SC: sodium carbonate (04-011-4108), L: lime (04-011-9020), CNa: calcium sodium aluminum oxide (04-010-2766), and NaCl: sodium chloride (04-002-1178).
The TGA results of the samples (Figure 3) show that the CDW exhibited three to four main weight losses, the first one up to 200°C associated with water departure and gypsum decomposition. Then, a continuous weight loss is observed up to 600°C including portlandite dihydroxylation (400–450°C), which is not clearly observed and the decomposition of C-S-H phases (Gallucci et al., 2013) was observed. The third and main transformation is calcite decarbonization taking place in the temperature range of 600–700°C (Kucharczyk et al., 2019). The ashes exhibit three to four thermal transformations. The weight loss up to 300°C corresponds to structural water departure. From 400 to 550°C, the portlandite decomposition occurs mainly for the PMA samples (Vassilev et al., 2013). For FA, a dihydroxylation reaction of the laumontite phase occurs in the temperature range of 550–650°C. After that, the decarbonization reaction is happens between 650 and 800°C. In addition, the NaCl melting and evaporation induces weight loss for the PMA beyond 800°C (Fraissler et al., 2009).
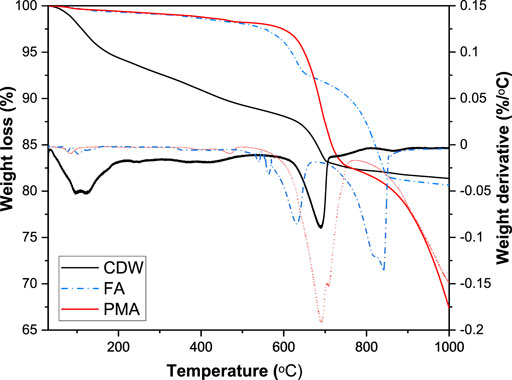
FIGURE 3. TGA results of construction and demolition waste (CDW), biomass ash (FA), and paper mill ash (PMA).
2.2 Artificial Lightweight Aggregate Production
2.2.1 Optimizing the Cobinder
The first step in the experiments was optimizing the cobinder composition consisting of a mixture of blast furnace slag and biomass ash or paper mill ash. Different BFS percentages were employed (40, 50, and 70 wt%), and the mixtures were alkali-activated with NaOH solution at different concentrations (8 and 12 M) (Table 2). The activator to binder ratio was constant (0.5) for all mixtures. The pastes were mixed for 2 min and then poured in 2 cm diameter and 2 cm height cylindrical molds. The mechanical properties of the hardened pastes were assessed via the compressive strength test. Then, the best mixes were chosen as the cobinder of CDW to manufacture the artificial lightweight aggregates.
2.2.2 Granulation of Construction and Demolition Waste Fines
The second phase consists of producing and characterizing the artificial lightweight aggregates made from the CDW and the previously optimized cobinders. Only the cobinders containing 50 and 70% of slag (50 and 30% of ash) are chosen as optimum to prepare the LWAs. Twelve different granulation batches of 200 g each were designed by variating the BFS to ash ratio in the cobinder and the cobinder to the CDW ratio (Table 3). The dry powders were first homogenized, then the aggregates were produced using a laboratory-scale high-shear granulator (Eirich & Co., Germany). Drops of NaOH solution were added until the desired granule size of 5–8 mm by diameter was achieved. The NaOH solutions were prepared by dissolving sodium hydroxide pellets in distilled water. The granulator was equipped with a 5 L rotating drum and impeller with a diameter of 10 cm. The rotating speed was 300 rpm, and the tilting angle was 40°, optimized by preliminary studies. The elaborated wet granules were cured in the oven at 60°C for 24 h. After that, each batch was sealed in air-tight bags and stored at room temperature before testing.
2.3 Characterization Methods
The particle size distribution of the raw materials was measured by a laser diffraction analyzer (Beckman Coulter LS 13320) using the Fraunhofer model and a wet procedure (isopropanol). The chemical composition was determined using X-ray fluorescence spectroscopy (Omnian Pananalytics Axiosmax 4 kV) for pressed pellets, and the LOI was determined by thermogravimetric analysis (TGA). The TGA was carried out using the Precisa PrepASH 129 thermogravimetric analyzer with a heat rate of 10°/min, and the samples were heated from 25°C up to 1000°C under N2 atmosphere. The mineralogical composition of the raw materials and the aggregates at 28 days was performed by X-ray diffraction (XRD) using a Rigaku SmartLab 9 kW XRD diffractometer with a Co Kα radiation (40 kv and 135 mA) Kα (Kα1 = 1.78892 Å; Kα2 = 1.79278 Å; Kα1/Kα2 = 0.5). The XRD analysis was carried out in the range of 10–70° 2-Theta with a scanning rate of 0.02°2θ/step. The phase identification was obtained using the PDXL2 software associated with the PDF-4 2015 database. The microstructure of the developed aggregates was assessed through SEM in a Zeiss Ultra Plus apparatus (Germany). The pasted samples were platinum-coated, and the accelerating voltage used was 5 kV.
2.3.1 Characterization of Granulated Aggregate
The crushing tests were performed after 1, 7, and 28 days with a Zwick Z100 Roell testing machine (ZwickRoell, Germany) to determine the aggregates’ engineering properties. The compression speed was 0.01 mm/s, and the pre-load force was 5 N. The crushing forces of ten granules of each batch were measured, and the mean and standard deviation were calculated. The crushed samples after strength test were immersed in isopropanol solution for three days in order to stop the chemical reactions for further analysis.
The loose bulk density and water absorption capacity were measured according to the SFS-EN-1097-3 (1998). At first, the samples were dried in the oven at 60°C until constant mass. Then, the density was calculated.
The measured values of dry mass and saturated surface-dry mass after 24 h water immersion were used to calculate the water absorption (WAC). The water absorption was determined using the following equation:
where wet weight is the mass of the granules after the 24 h water immersion and dry weight is the initial mass of the granules.
The particle density of the aggregate was measured using a gas pycnometer Accupyc II [Micromeritics Instruments Corporation (United States)]. Before the test, the granules were milled in a vibratory disc mill for 30 s at 700 rpm. The porosity of the granules was determined according to the bulk and particle density results using the following equation:
where bulk density is the value determined by Eq. 1 and particle density is the density of the powdered material measured by using a gas pycnometer.
The mechanical and physical test results were correlated to the granules’ mineralogy and microstructure obtained by the scanning electron microscopy (SEM) and X-ray diffraction (XRD) analyses. The microstructure of the produced aggregates was characterized by using an equipped Zeiss Sigma microscope.
3 Results and Discussion
3.1 Optimization of the Cobinder
The blends of BFS-ash were first tested as a cobinder for the lightweight aggregates. The results of the mechanical properties (Figure 4) show that low concentration sodium hydroxide solution revealed higher mechanical properties for both the blends with biomass ash and paper mill ash. The increase of alkali concentration up to 12 M NaOH induced a drop in the sample’s strength. Generally, increasing the alkali concentration promotes the destruction of the BFS bonds Ca–O, Mg–O, Si–O–Si, Al–O–Al, and Al–O–Si and the formation of more C-(A)-S-H gel (Pacheco-Torgal et al., 2008; Thunuguntla and Gunneswara Rao, 2018). However, an excess of alkali has detrimental effects hindering the formation of the alkali activation reaction products (Pacheco-Torgal et al., 2008; Hashim et al., 2015).
In addition, increasing the BFS content of the blends up to 50 wt% leads to strengthening the hardened pastes for both the kinds of ash blends. Similar results have been found for alkali-activated BFS-fly ash blends with NaOH solution (Puertas et al., 2000). BFS is more reactive under mild alkaline conditions than fly ash. Moreover, fly ash requires the presence of soluble silicates to initiate the polycondensation reaction and promote the aluminosilicate gel formation that strengthens the structure (Yang et al., 2013). Further increase of the BFS content up to 70 wt% has a slight positive effect on the mechanical properties of the pastes. The effect of the curing time on the compressive strength of the samples was not significant for the biomass-based blends. At the same time, the paper mill ashes developed strength with time showing the continuous alkali activation reaction with time. It is worth noting that the biomass ashes-based pastes revealed higher mechanical properties compared to the paper mill ash-based ones due to the higher aluminosilicates content in the biomass ash. Also, the high-water absorption character of the paper mill ash could be one of the factors reducing its reaction rate.
Based on the abovementioned compressive strength results, the blends containing 50 wt% and 30 wt% of each ash were chosen to be used as the cobinder with construction and demolition waste for lightweight aggregate manufacturing, and 8M NaOH solution was chosen to be utilized as the activating solution.
3.2 Lightweight Aggregate Characterization
3.3.1 Lightweight Aggregate Strength
The mechanical properties of the produced lightweight artificial aggregates have been assessed via the crushing test. The crushing force of the aggregates showed a positive correlation to the percentage of the cobinder used (Figure 5). The samples with 10 wt% of the cobinder showed a very mediocre crushing strength variating in the range of 4–15 N and 24–39 N at one and 28 days, respectively. This low strength indicates the low reactivity of the CDW that acts as a filler rather than a binder. Generally, the strength of the binders increases with the binder to filler ratio and is negatively proportional to the filler content (Thomas and Harilal, 2015; Tang and Brouwers, 2017), which is evidenced by the increase in the aggregates crushing strength (28 days) ranging from 32 to 178 % when the cobinder percentage increased from 10 to 50 wt%.
It can be noticed that the strength development of the aggregates follows an evolutive trend with time opposing to the cobinder behavior discussed in the section previously due to the presence of CDW as a filler that delays the complete alkali activation reaction of the BFS-ash binder. An increase of strength up to 400% was observed from 1 to 28 days of curing. Moreover, the aggregates containing the biomass ash revealed a higher strength than those with the paper mill ash, which is in good agreement with the cobinder strength results. All the samples with 50 wt% cobinder (50-30FA, 50-50FA, 50-30PMA, and 50-50PMA) and the samples with biomass ash and 30 wt% cobinder (30-30PMA and 30-50PMA) exhibited a similar or higher 28 days crushing force than the commercial sintered Leca© aggregates (54 N). Overall, the elaborated aggregates revealed a high strength of up to 82 N of crushing force at 28th day, indicating the efficiency of the cold bonding palletization method.
3.3.2 Physical Properties of the Lightweight Aggregates
The bulk densities of the aggregates are below the upper limit for the lightweight aggregates according to the SFS-EN 13055 (2016) standard (1200 kg/m3) and vary in the range of 618–829 kg/m3 (Figure 6A). The density results show that increasing the cobinder addition rate leads to higher densities and corresponds to the higher strength measured. The increase of the cobinder percentage promotes the formation of more binding products and induces denser structures which positively affects the mechanical properties (Manikandan and Ramamurthy, 2008; Thomas and Harilal, 2015). Furthermore, a linear correlation between the granule density and water absorption is observed for most of the studied blends except for the mixtures with 50 wt% biomass ash, for which the R2 of its linear trendline was less than seven. However, increasing the cobinder addition percentage results in lower water absorption for most blends. Overall, the water absorption values of the prepared aggregates (13–19%) are comparable with the commercial ones (19.7%) and similar to the values found by previous studies involving aggregates from powdered materials (Cioffi et al., 2011; Ferone et al., 2013; Colangelo et al., 2015). Moreover, a linear correlation between the porosity and mechanical properties of the aggregates is noted (Figure 6B). The porosity of the aggregates varies between 18.9 and 25.6%. The porosity results are consistent with the mechanical properties. The samples containing high amount of construction and demolition waste (10 wt% cobinder) revealed the lowest crushing force and highest porosity.
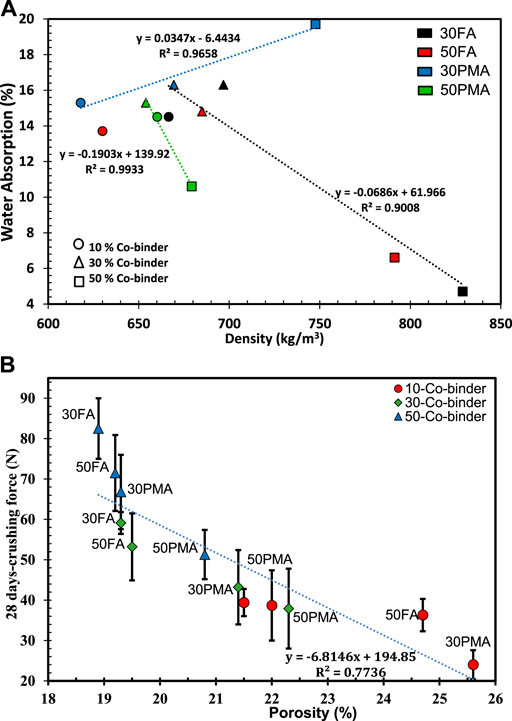
FIGURE 6. Correlation between the hardened properties of the aggregates (A) between the water absorption and density; (B) between the crushing strength and porosity.
3.3.3 Mineralogy and Morphology of the Lightweight Aggregates
The XRD patterns of the aggregates at 28 days (Figure 7) show that the mineralogical composition of the mixtures has been altered by alkali activation due to the dissolution of some initial phases and the formation of other new crystalline phases. Quartz, albite, phlogopite, and calcite phases persisted to the alkali activation. At the same time, the characteristic peaks of gypsum, sylvite, gehlenite, lime, and sodium calcium chloride have disappeared, indicating their dissolution during the alkaline activation reaction. In addition, the formation of sodium calcium aluminum silicate phase has been observed for all the samples as a secondary reaction product of the alkali activation of the blends (Fayed et al., 2021). The formation of thermonatrite (sodium carbonate hydrate) and portlandite phases has been detected for all the samples with a higher intensity for the samples with high ashes content. The portlandite phase is formed by the hydration of free lime from the ashes, whereas the sodium carbonate hydrate phase is formed due to the reaction of excess sodium with the CO2 from air, indicating a lower sodium consumption with high ash content and, hence, a lower alkali activation reaction rate. The obtained results are in good agreement with the strength test results, demonstrating an increase in the sample’s strength with a decrease in ash content. The characteristic hump of the amorphous alkali activation reaction products is observed at 25–40° 2 theta range. However, no variation of its position or intensity has been detected with the CDW or ash content variation.
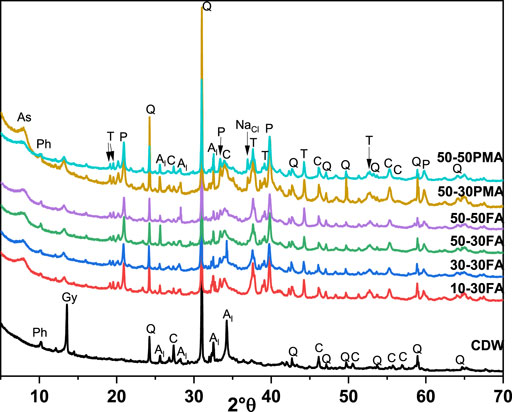
FIGURE 7. XRD patterns of the elaborated aggregates compared to the raw CDW (CoKα radiation). As: sodium calcium aluminum silicate (00-019-1183), Ph: phlogopite (01-070-2125), Gy: gypsum (04-009-3817), Q: quartz (04-014-7568), Al: albite (04-017-1022), C: calcite (04-008-0198), P: portlandite (04-014-8866), G: gehlenite (01-079-2421), T: thermonatrite (sodium carbonate hydrate) (00-008-0448), L: lime (04-011-9020), and NaCl: sodium chloride (04-002-1178).
The microstructure of the cross-section of the aggregates has been visualized by the mean of SEM (Figure 8). The effect of the cobinder can be detected from Figures 8A–D. Increasing the cobinder and decreasing the CDW content leads to more dense and less porous aggregates. The microstructure of the aggregates is characterized by the pores covering the visualized surface. The increase of the ash content induces an increase in the number of pores and holes and a less dense structure (Figures 8C,E). In addition, the samples containing the paper mill ash show more interconnected pores, indicating a weak structure compared to the samples with the biomass ash (Figures 8E,F), which is consistent with the mechanical properties results of the aggregates.
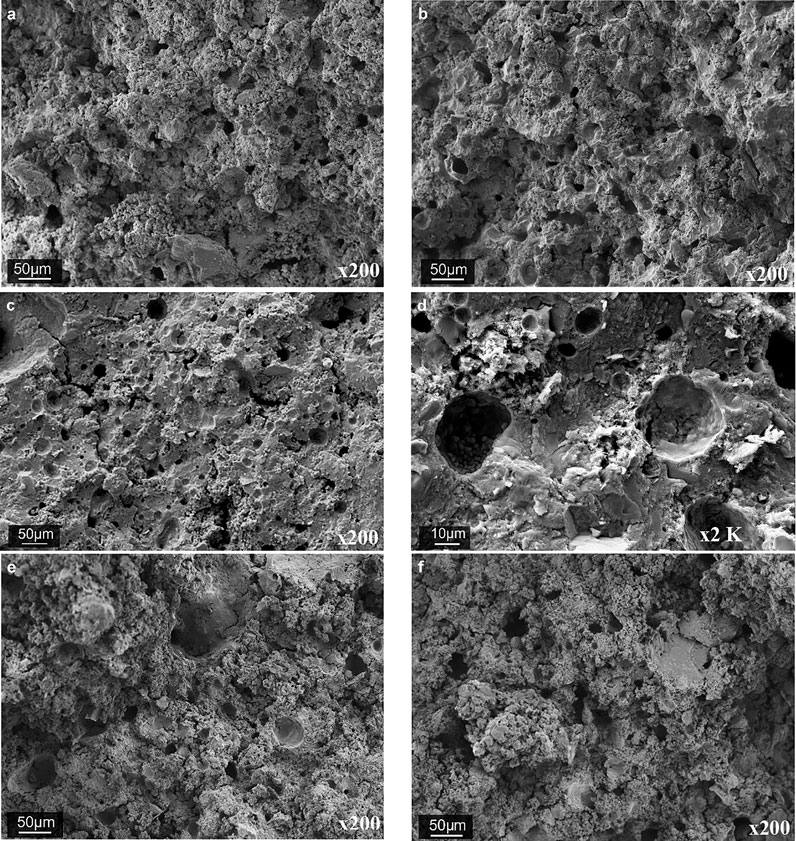
FIGURE 8. SEM images of the cross section of the elaborated aggregates. (A) 10-30FA, (B) 30-30FA, (C,D) 50-30FA, (E) 50-50-FA, and (F) 50-50PMA.
4 Conclusion
The feasibility of lightweight aggregate production by cold pelletization of alkali-activated construction and demolition waste blended with BFS and ash has been investigated. The effects of the CDW content and the composition of the cobinder used on the properties of the aggregates have been studied. The results indicate that the BFS content of the cobinder and the type of ash have a high impact on the strength development of the aggregates. Increasing the cobinder content as well as the BFS ratio and using biomass ash leads to a dense structure and increased crushing force of the elaborated aggregates. In addition, an approximatively linear correlation between the aggregate’s strength and porosity and between the density and water absorption has been detected. The mineralogical and microstructural analyses of the samples were in agreement with the physical properties indicating a higher alkali activation reaction when the biomass ash is used and with an increase in BFS content. Overall, the lightweight aggregates with a higher crushing force than the commercial sintered aggregates have been successfully produced. The optimum mixture revealing the highest strength (82 N) comprises of 50 wt% CDW, 35 wt% BFS, and 15 wt% biomass ash alkali-activated with 8M NaOH solution.
Data Availability Statement
The original contributions presented in the study are included in the article/Supplementary Material, further inquiries can be directed to the corresponding author.
Author Contributions
SM: conceptualization, methodology, validation, formal analysis, investigation, visualization, and writing—original draft preparation, review, and editing. KK: conceptualization, methodology, validation, formal analysis, and writing—original draft preparation. PP: conceptualization, methodology, validation, and writing—review and editing. KO: writing—review and editing, funding acquisition, and project administration. MI: conceptualization, writing—review and editing, funding acquisition, and project administration. All authors contributed to the article and approved the submitted version.
Funding
The authors acknowledge the financial support received for the project DeConcrete Eco-Efficient Arctic technologies cooperation funded by the Kolarctic CBC initiative of the European Union (KO 4068).
Conflict of Interest
The authors declare that the research was conducted in the absence of any commercial or financial relationships that could be construed as a potential conflict of interest.
Publisher’s Note
All claims expressed in this article are solely those of the authors and do not necessarily represent those of their affiliated organizations, or those of the publisher, the editors, and the reviewers. Any product that may be evaluated in this article, or claim that may be made by its manufacturer, is not guaranteed or endorsed by the publisher.
Acknowledgments
The authors would like to thank Durgaprasad Ramteke and Marcin Selent for their contribution to characterizing the materials.
References
Aslam, M. S., Huang, B., and Cui, L. (2020). Review of Construction and Demolition Waste Management in China and USA. J. Environ. Manage. 264, 110445. doi:10.1016/j.jenvman.2020.110445
Ayati, B., Molineux, C., Newport, D., and Cheeseman, C. (2019). Manufacture and Performance of Lightweight Aggregate from Waste Drill Cuttings. J. Clean. Prod. 208, 252–260. doi:10.1016/j.jclepro.2018.10.134
Bandara, H. M. S. C. H., Thushanth, G., Somarathna, H. M. C. C., Jayasinghe, D. H. G. A. E., and Raman, S. N. (2022). Feasible Techniques for Valorisation of Construction and Demolition Waste for Concreting Applications. Int. J. Environ. Sci. Technol. 1–16. doi:10.1007/s13762-022-04015-z
Baykal, G., and Döven, A. G. (2000). Utilization of Fly Ash by Pelletization Process; Theory, Application Areas and Research Results. Resour. Conservation Recycling 30, 59–77. doi:10.1016/S0921-3449(00)00042-2
Bolouri Bazaz, J., and Khayati, M. (2012). Properties and Performance of Concrete Made with Recycled Low-Quality Crushed Brick. J. Mater. Civ. Eng. 24, 330–338. doi:10.1061/(asce)mt.1943-5533.0000385
Braga, A. M., Silvestre, J. D., and de Brito, J. (2017). Compared Environmental and Economic Impact from Cradle to Gate of concrete with Natural and Recycled Coarse Aggregates. J. Clean. Prod. 162, 529–543. doi:10.1016/j.jclepro.2017.06.057
Bravo, M., De Brito, J., Pontes, J., and Evangelista, L. (2015). Mechanical Performance of concrete Made with Aggregates from Construction and Demolition Waste Recycling Plants. J. Clean. Prod. 99, 59–74. doi:10.1016/j.jclepro.2015.03.012
Cioffi, R., Colangelo, F., Montagnaro, F., and Santoro, L. (2011). Manufacture of Artificial Aggregate Using MSWI Bottom Ash. Waste Manage. 31, 281–288. doi:10.1016/j.wasman.2010.05.020
Colangelo, F., Messina, F., and Cioffi, R. (2015). Recycling of MSWI Fly Ash by Means of Cementitious Double Step Cold Bonding Pelletization: Technological Assessment for the Production of Lightweight Artificial Aggregates. J. Hazard. Mater. 299, 181–191. doi:10.1016/j.jhazmat.2015.06.018
Contrafatto, L., Lazzaro Danzuso, C., Gazzo, S., and Greco, L. (2020). Physical, Mechanical and thermal Properties of Lightweight Insulating Mortar with Recycled Etna Volcanic Aggregates. Construction Building Mater. 240, 117917. doi:10.1016/j.conbuildmat.2019.117917
DESA (2018). World urbanization prospects: The 2014 revision. United Nations Department of Economics and Social Affairs. New York, NY, USA: Population Division, 41.
Dondi, M., Cappelletti, P., D’Amore, M., de Gennaro, R., Graziano, S. F., Langella, A., et al. (2016). Lightweight Aggregates from Waste Materials: Reappraisal of Expansion Behavior and Prediction Schemes for Bloating. Construction Building Mater. 127, 394–409. doi:10.1016/j.conbuildmat.2016.09.111
Etxeberria, M., Vázquez, E., and Marí, A. (2006). Microstructure Analysis of Hardened Recycled Aggregate concrete. Mag. Concrete Res. 58, 683–690. doi:10.1680/macr.2006.58.10.683
Eurostat, (2018). Waste Statistics. Available at: https://ec.europa.eu/eurostat/statistics-explained/index.php?title=Waste_statistics#Total_waste_generation.
Fayed, E. K., El-Hosiny, F. I., El-Kattan, I. M., Al-Kroom, H., Abd Elrahman, M., and Abdel-Gawwad, H. A. (2021). An Innovative Method for Sustainable Utilization of Blast-Furnace Slag in the Cleaner Production of One-Part Hybrid Cement Mortar. Materials 14, 5669–5725. doi:10.3390/ma14195669
Fernández-Jiménez, A., Cristelo, N., Miranda, T., and Palomo, Á. (2017). Sustainable Alkali Activated Materials: Precursor and Activator Derived from Industrial Wastes. J. Clean. Prod. 162, 1200–1209. doi:10.1016/j.jclepro.2017.06.151
Ferone, C., Colangelo, F., Messina, F., Iucolano, F., Liguori, B., and Cioffi, R. (2013). Coal Combustion Wastes Reuse in Low Energy Artificial Aggregates Manufacturing. Materials 6, 5000–5015. doi:10.3390/ma6115000
Fraissler, G., Jöller, M., Brunner, T., and Obernberger, I. (2009). Influence of Dry and Humid Gaseous Atmosphere on the thermal Decomposition of Calcium Chloride and its Impact on the Remove of Heavy Metals by Chlorination. Chem. Eng. Process. Process Intensification 48, 380–388. doi:10.1016/j.cep.2008.05.003
Gallucci, E., Zhang, X., and Scrivener, K. L. (2013). Effect of Temperature on the Microstructure of Calcium Silicate Hydrate (C-S-H). Cement Concrete Res. 53, 185–195. doi:10.1016/j.cemconres.2013.06.008
Geetha, S., and Ramamurthy, K. (2010). Reuse Potential of Low-Calcium Bottom Ash as Aggregate through Pelletization. Waste Manage. 30, 1528–1535. doi:10.1016/j.wasman.2010.03.027
Ghisellini, P., Ji, X., Liu, G., and Ulgiati, S. (2018). Evaluating the Transition towards Cleaner Production in the Construction and Demolition Sector of China: A Review. J. Clean. Prod. 195, 418–434. doi:10.1016/j.jclepro.2018.05.084
Hashim, A. N., Hussin, K., Begum, N., Al Bakri Abdullah, M. M., Abdul Razak, K., and Ekaputri, J. J. (2015). Effect of Sodium Hydroxide (NaOH) Concentration on Compressive Strength of Alkali-Activated Slag (AAS) Mortars. Amm 754-755, 300–304. doi:10.4028/www.scientific.net/10.4028/www.scientific.net/amm.754-755.300
He, Z.-h., Zhang, M.-y., Yuan, Q., Shi, J.-y., and Zhan, P.-m. (2022). A Novel Development of green UHPC Containing Waste concrete Powder Derived from Construction and Demolition Waste. Powder Technol. 398, 117075. doi:10.1016/j.powtec.2021.117075
Jin, R., Yuan, H., and Chen, Q. (2019). Science Mapping Approach to Assisting the Review of Construction and Demolition Waste Management Research Published between 2009 and 2018. Resour. Conservation Recycling 140, 175–188. doi:10.1016/j.resconrec.2018.09.029
Juimo Tchamdjou, W. H., Cherradi, T., Abidi, M. L., and Pereira-de-Oliveira, L. A. (2018). Mechanical Properties of Lightweight Aggregates concrete Made with Cameroonian Volcanic Scoria: Destructive and Non-destructive Characterization. J. Building Eng. 16, 134–145. doi:10.1016/j.jobe.2018.01.003
Kang, S.-H., Kwon, Y.-H., Hong, S.-G., Chun, S., and Moon, J. (2019). Hydrated Lime Activation on Byproducts for Eco-Friendly Production of Structural Mortars. J. Clean. Prod. 231, 1389–1398. doi:10.1016/j.jclepro.2019.05.313
Kim, Y. J., and Choi, Y. W. (2012). Utilization of Waste concrete Powder as a Substitution Material for Cement. Construction Building Mater. 30, 500–504. doi:10.1016/j.conbuildmat.2011.11.042
Kucharczyk, S., Zajac, M., Stabler, C., Thomsen, R. M., Ben Haha, M., Skibsted, J., et al. (2019). Structure and Reactivity of Synthetic CaO-Al2O3-SiO2 Glasses. Cement Concrete Res. 120, 77–91. doi:10.1016/j.cemconres.2019.03.004
Lieder, M., and Rashid, A. (2016). Towards Circular Economy Implementation: A Comprehensive Review in Context of Manufacturing Industry. J. Clean. Prod. 115, 36–51. doi:10.1016/j.jclepro.2015.12.042
Liu, M., Guo, J., and Shao, Y. (2020). Effects of CaO and MgO Contents on the Properties of Lightweight Aggregate Produced from Municipal Solid Wastes. Construction Building Mater. 259, 120398. doi:10.1016/j.conbuildmat.2020.120398
López Ruiz, L. A., Roca Ramón, X., and Gassó Domingo, S. (2020). The Circular Economy in the Construction and Demolition Waste Sector - A Review and an Integrative Model Approach. J. Clean. Prod. 248, 119238. doi:10.1016/j.jclepro.2019.119238
Manikandan, R., and Ramamurthy, K. (2008). Effect of Curing Method on Characteristics of Cold Bonded Fly Ash Aggregates. Cement and Concrete Composites 30, 848–853. doi:10.1016/j.cemconcomp.2008.06.006
Moreno-Maroto, J. M., Camacho, P. N., Cotes-Palomino, T., García, C. M., and Alonso-Azcárate, J. (2019). Manufacturing of Lightweight Aggregates from Biomass Fly Ash, Beer Bagasse, Zn-Rich Industrial Sludge and clay by Slow Firing. J. Environ. Manage. 246, 785–795. doi:10.1016/j.jenvman.2019.06.059
Mueller, A., Schnell, A., and Ruebner, K. (2015). The Manufacture of Lightweight Aggregates from Recycled Masonry Rubble. Construction Building Mater. 98, 376–387. doi:10.1016/j.conbuildmat.2015.07.027
Mueller, A., Sokolova, S. N., and Vereshagin, V. I. (2008). Characteristics of Lightweight Aggregates from Primary and Recycled Raw Materials. Construction Building Mater. 22, 703–712. doi:10.1016/j.conbuildmat.2007.06.009
Nguyen, H. P., Mueller, A., Nguyen, V. T., and Nguyen, C. T. (2021). Development and Characterization of Lightweight Aggregate Recycled from Construction and Demolition Waste Mixed with Other Industrial By-Products. Construction Building Mater. 313, 125472. doi:10.1016/j.conbuildmat.2021.125472
Omary, S., Ghorbel, E., Wardeh, G., and Nguyen, M. D. (2018). Mix Design and Recycled Aggregates Effects on the Concrete's Properties. Int. J. Civ. Eng. 16, 973–992. doi:10.1007/s40999-017-0247-y
Opoku, A. (2019). Biodiversity and the Built Environment: Implications for the Sustainable Development Goals (SDGs). Resour. Conservation Recycling 141, 1–7. doi:10.1016/j.resconrec.2018.10.011
Pacheco-Torgal, F., Castro-Gomes, J., and Jalali, S. (2008). Alkali-activated Binders: A Review. Construction Building Mater. 22, 1305–1314. doi:10.1016/j.conbuildmat.2007.10.015
Perumal, P., Sreenivasan, H., Luukkonen, T., Kantola, A. M., Telkki, V.-V., Kinnunen, P., et al. (2021). High Strength One-Part Alkali-Activated Slag Blends Designed by Particle Packing Optimization. Construction Building Mater. 299, 124004. doi:10.1016/j.conbuildmat.2021.124004
Puertas, F., Martı́nez-Ramı́rez, S., Alonso, S., and Vázquez, T. (2000). Alkali-activated Fly Ash/slag Cements. Cement Concrete Res. 30, 1625–1632. doi:10.1016/S0008-8846(00)00298-2
Ram, V., and Kalidindi, S. N. (2017). Estimation of Construction and Demolition Waste Using Waste Generation Rates in Chennai, India. Waste Manag. Res. 35, 610–617. doi:10.1177/0734242X17693297
Saiz Martínez, P., González Cortina, M., Fernández Martínez, F., and Rodríguez Sánchez, A. (2016). Comparative Study of Three Types of fine Recycled Aggregates from Construction and Demolition Waste (CDW), and Their Use in Masonry Mortar Fabrication. J. Clean. Prod. 118, 162–169. doi:10.1016/j.jclepro.2016.01.059
Schoon, J. (2015). Portland Clinker from By-Products and Recycled Materials Out of the Building and Construction Sector.
Shi, M., Ling, T.-C., Gan, B., and Guo, M.-Z. (2019). Turning concrete Waste Powder into Carbonated Artificial Aggregates. Construction Building Mater. 199, 178–184. doi:10.1016/j.conbuildmat.2018.12.021
Silva, R. V., De Brito, J., and Dhir, R. K. (2014). Properties and Composition of Recycled Aggregates from Construction and Demolition Waste Suitable for concrete Production. Construction Building Mater. 65, 201–217. doi:10.1016/j.conbuildmat.2014.04.117
Tam, V. W. Y., and Tam, C. M. (2007). Assessment of Durability of Recycled Aggregate concrete Produced by Two-Stage Mixing Approach. J. Mater. Sci. 42, 3592–3602. doi:10.1007/s10853-006-0379-y
Tang, P., and Brouwers, H. J. H. (2017). Integral Recycling of Municipal Solid Waste Incineration (MSWI) Bottom Ash Fines (0-2 Mm) and Industrial Powder Wastes by Cold-Bonding Pelletization. Waste Manage. 62, 125–138. doi:10.1016/j.wasman.2017.02.028
Thomas, J., and Harilal, B. (2015). Properties of Cold Bonded Quarry Dust Coarse Aggregates and its Use in concrete. Cement and Concrete Composites 62, 67–75. doi:10.1016/j.cemconcomp.2015.05.005
Thunuguntla, C. S., and Gunneswara Rao, T. D. (2018). Effect of Mix Design Parameters on Mechanical and Durability Properties of Alkali Activated Slag concrete. Construction Building Mater. 193, 173–188. doi:10.1016/j.conbuildmat.2018.10.189
Torres-Carrasco, M., and Puertas, F. (2017). La activación alcalina de diferentes aluminosilicatos como una alternativa al Cemento Portland: cementos activados alcalinamente o geopolímeros. Rev. Ing. Constr. 32, 05–12. doi:10.4067/s0718-50732017000200001
Vassilev, S. V., Baxter, D., Andersen, L. K., and Vassileva, C. G. (2013). An Overview of the Composition and Application of Biomass Ash. Part 1. Phase-mineral and Chemical Composition and Classification. Fuel 105, 40–76. doi:10.1016/j.fuel.2012.09.041
Verma, C. L., Handa, S. K., Jain, S. K., and Yadav, R. K. (1998). Techno-commercial Perspective Study for Sintered Fly Ash Light-Weight Aggregates in India. Construction Building Mater. 12, 341–346. doi:10.1016/S0950-0618(98)00022-1
Xiao, J., Ma, Z., Sui, T., Akbarnezhad, A., and Duan, Z. (2018). Mechanical Properties of concrete Mixed with Recycled Powder Produced from Construction and Demolition Waste. J. Clean. Prod. 188, 720–731. doi:10.1016/j.jclepro.2018.03.277
Xuan, D., Molenaar, A. A. A., and Houben, L. J. M. (2012). Compressive and Indirect Tensile Strengths of Cement-Treated Mix Granulates with Recycled Masonry and Concrete Aggregates. J. Mater. Civ. Eng. 24, 577–585. doi:10.1061/(asce)mt.1943-5533.0000401
Yang, T., Yao, X., Zhang, Z., and Wang, H. (2012). Mechanical Property and Structure of Alkali-Activated Fly Ash and Slag Blends. J. Sust. Cement-Based Mater. 1, 167–178. doi:10.1080/21650373.2012.752621
Zhao, Y., Qiu, J., Xing, J., and Sun, X. (2020). Recycling of Quarry Dust for Supplementary Cementitious Materials in Low Carbon Cement. Construction Building Mater. 237, 117608. doi:10.1016/j.conbuildmat.2019.117608
Zheng, L., Wu, H., Zhang, H., Duan, H., Wang, J., Jiang, W., et al. (2017). Characterizing the Generation and Flows of Construction and Demolition Waste in China. Construction Building Mater. 136, 405–413. doi:10.1016/j.conbuildmat.2017.01.055
Zhou, A., Zhang, W., Wei, H., Liu, T., Zou, D., and Guo, H. (2021). A Novel Approach for Recycling Engineering Sediment Waste as Sustainable Supplementary Cementitious Materials. Resour. Conservation Recycling 167, 105435. doi:10.1016/j.resconrec.2021.105435
Zid, C., Kasim, N., Raza Soomro, A., and Laidoune, A. (2020). “The Discrepancy in the Construction Industry of Malaysia: One of the Most Contributing Industries in Malaysia's Economy and the Highest Contributor of the Fatal Accidents,” in IOP Conference Series: Materials Science and Engineering. (Vol. 788, No. 1, p. 012034). Bristol: IOP Publishing. doi:10.1088/1757-899X/788/1/012034I
Keywords: construction and demolition (C and D) waste, biomass ash, paper mill ash, lightweight aggregate, alkali activation, cold bonding pelletization
Citation: Moukannaa S, Kursula K, Perumal P, Ohenoja K and Illikainen M (2022) Recycling of Precast Concrete Waste Sludge With Paper Mill and Biomass Ashes for Lightweight Granulated Aggregate Production. Front. Mater. 9:877160. doi: 10.3389/fmats.2022.877160
Received: 16 February 2022; Accepted: 21 March 2022;
Published: 13 April 2022.
Edited by:
Luca Valentini, University of Padua, ItalyReviewed by:
Ilenia Farina, University of Naples Parthenope, ItalyPaulo Ricardo de Matos, Federal University of Santa Maria, Brazil
Copyright © 2022 Moukannaa, Kursula, Perumal, Ohenoja and Illikainen. This is an open-access article distributed under the terms of the Creative Commons Attribution License (CC BY). The use, distribution or reproduction in other forums is permitted, provided the original author(s) and the copyright owner(s) are credited and that the original publication in this journal is cited, in accordance with accepted academic practice. No use, distribution or reproduction is permitted which does not comply with these terms.
*Correspondence: Samira Moukannaa, c2FtaXJhLm1vdWthbm5hYUBvdWx1LmZp