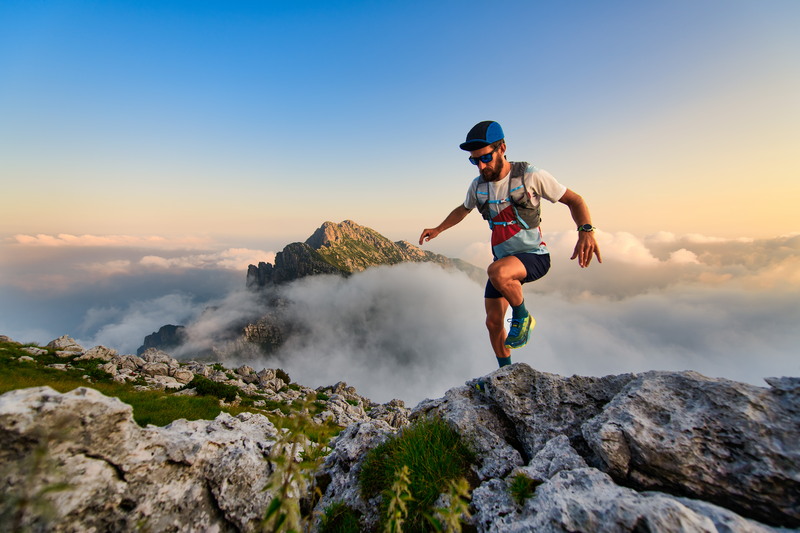
95% of researchers rate our articles as excellent or good
Learn more about the work of our research integrity team to safeguard the quality of each article we publish.
Find out more
ORIGINAL RESEARCH article
Front. Mater. , 22 March 2022
Sec. Structural Materials
Volume 9 - 2022 | https://doi.org/10.3389/fmats.2022.869875
This article is part of the Research Topic 2022 Retrospective: Structural Materials View all 5 articles
To effectively apply slag-gypsum binder (SGB) to most modern mines. An experimental study is conducted to investigate the feasibility and reliability of slag-gypsum binder (SGB) to replace cement in the mine backfill to effectively apply SGB in modern mines. The optimum parameters of aggregate and SGB fineness were investigated on a laboratory basis and the effect of concentration on the workability was analyzed. Also, industrial tests were carried out to study the cementitious properties of SGB and compared to cement. Finally, the hydration properties of SGB were analyzed using XRD and SEM. The results indicated that the main hydration products of SGB are C-S-H gel and ettringite, while Ca(OH)2 is consumed during the hydration process. In addition, the structure formed in the later stage of SGB is more compact. SGB is beneficial to the strength of the waste rock mixture. The sample prepared with the waste rock-rod milling sand-river sand mixture has a maximum strength of 7.54 MPa at 28 d. Reducing fineness is beneficial to form early strength. However, a specific surface area exceeding 510 m2/kg will harm the later strength. Surface area is less (400 m2/kg), the sample strength decreases when the dosage increases. Comparing the workability of SGB slurry and cement slurry, it is found that there is no essential difference between them under different mass concentration conditions. SGB slurry shows better fluidity and stability at a mass concentration of 80–82%. Industrial backfill experiments show the 3-, 7-, and 28-d strengths of SGB samples under 80% mass concentration conditions are 0.91 times, 1.43 times, and 1.2 times the cement samples. Therefore, using SGB instead of cement to backfill is a good application prospect.
1) SGB is beneficial to the industrial backfill of waste rock mixed coarse aggregate.
2) The effect of SGB on the workability of the slurry was studied.
3) Reasonable SGB fineness can effectively improve the strength of backfilled samples.
4) The hydration behavior of SGB is quite different from cement.
Resource development and utilization are accompanied by a large amount of waste rock, tailings and metallurgical slag, and other solid waste discharge. Waste stacking not only occupies many lands but also seriously pollutes the environment and destroys the ecological balance. Moreover, mining underground ore bodies not only destroys the groundwater environment but also easily causes geological disasters (Benzaazoua et al., 2008; Chen et al., 2022; Dai et al., 2022). Backfill mining is an important way to realize waste utilization, geological hazard control, and safe production (Kesimal et al., 2005; Wang et al., 2022; Yan et al., 2022). The cemented paste backfill (CPB) technology is to mix the collected waste rock, tailings, and other solid wastes with cementing materials and water to form a paste, and then transport the paste to the goaf along the pipeline. The paste will form a strong and integral filling in the goaf, protecting mining activities (Cui and Fall 2015; Yilmaz et al., 2015; Qi et al., 2018). CPB technology can also increase resource recovery rate and reduce ore dilution rate to reduce the permanent loss of non-renewable minerals (Bell et al., 2000).
Binder is the core material in mine backfill (Tilmaz et al., 2010; Helinski et al., 2011). Traditional low-concentration backfill and high-concentration paste backfill both use ordinary Portland cement as a binder (Tariq and Yanful, 2013). However, cement still has many shortcomings in the mining backfill. First, cement cost is expensive (Souza et al., 1997; Hassani et al., 2007). According to statistics, the cost of cement materials alone accounts for 1/3 of the entire filling cost. At present, CPB technology focuses on finding alternatives to cement without reducing its backfill strength (Carlsson et al., 1986). Second, the cement industry consumes a lot of energy and resources and causes pollution (Shi and Qian, 2000). China’s cement production consumes nearly 100 million tons of coal each year, and consumes nearly 400 million tons of limestone. Third, a large amount of carbon dioxide will emit during cement production (Flatt et al., 2012; Rashad, 2013; Tariq and Yanful, 2013). It is estimated that every ton of cement clinker produced will emit about 1 ton of carbon dioxide.
The main way to reduce the backfill production cost is to find cost-effective alternatives to cement, which may replace cement (Chen et al., 2018; Yılmaz et al., 2018). New low-cost binders have undoubtedly become the focus of many scholars’ attention. The new binder is different from cement in that it uses an alkali, salt, or composite activator to excite the active pozzolanic material and make the pozzolanic material hydraulic (Li et al., 2017; Jiang et al., 2019). Relevant scholars have carried out a lot of research and found that the solid waste blast furnace slag produced in the metal smelting process is a kind of polymer formed by the active glass phase and crystalline phase (Deb et al., 2014). The active glass phase content in the slag reaches more than 80%. After grinding the slag to cement fineness, clinker, calcium hydroxide, or gypsum can activate it. It is a good substitute for cement (Xue et al., 2018; Sun et al., 2020; Zhang et al., 2021). The application of slag-based adhesives can effectively reduce the mine backfill cost. At the same time, it also solves the problem of solid waste accumulation and environmental pollution during cement production (Gorai et al., 2003; Jiang et al., 2020).
Although paste filling technology has been successfully applied, high material costs and low solid waste utilization are challenges for the Jinchuan Mine. The feasibility and reliability of slag-gypsum binder (SGB) as a substitute for cement in mine backfill were studied. To achieve this goal, the adaptability of SGB to a variety of aggregates in the Jinchuan Mine was tested by taking rod milling sand, river sand, and waste rock mixed aggregate as samples. Tests were performed to analyze the influence of SGB fineness on strength and study the SGB slurry conveying characteristics. The SGB hydration was studied by scanning electron microscope (SEM) and X-ray diffraction (XRD). An industrial backfill experiment was carried out to compare the SGB actual application effect. The research results will lay a theoretical foundation for the mines’ economic exploitation.
Jinchuan Mine is a large-scale polymetallic symbiotic copper-nickel sulfide mine in Gansu Province, China. Due to the high in-situ stress, deep burial, large ground pressure, and unstable rock mass of the Jinchuan deposit, higher early backfill strength is required. Rod milling sand and cement are the main fillers in the Jinchuan Mine, but the following two problems arise in the mine production process. 1) High backfill cost. Large cement content is required to ensure that the backfill body achieves the strength required by the Jinchuan Mine, resulting in a cost of 185 yuan per ton of backfill material. In recent years, the international nickel price has been sluggish, and the high cost of cemented backfill mining mode has brought serious economic problems to Jinchuan. 2) The solid waste utilization rate is low. According to the “Resource Investigation Report” of the Jinchuan Mine, the annual output of solid waste by all departments is about 10 million tons. Most of the solid wastes cannot use rod milling sand effectively when rod milling sand is the main filling material. The solid waste can only be dumped in a designated location, which has a serious impact on the surrounding environment.
Due to the geographical location of the Jinchuan Mine, the slag produced by Jiu Steel Group (Gansu, China) during the smelting process was selected as the main raw material. The chemical composition and quality coefficient of slag are shown in Table 1. The activity coefficient of Jiugang slag is Mn = 0.321 > 0.25, which belongs to the pozzolanic material with higher activity; the basic coefficient M0 = 0.93 < 1.0 belongs to acidic slag (Wang et al., 1994); the slag quality coefficient K = 1.41 < 1.6 belongs to low-quality slag (Li and Sun, 2000). For the active substances in the slag, cement clinker and desulfurized gypsum are used for composite activation. Grinding aids and early strength agents are added to improve the comprehensive performance of SGB. The detailed configuration of SGB is shown in Table 2. SGB was handed over to Xijin Energy-Saving Building Materials Co., Ltd. (Gansu, China) for industrial trial production, with an initial specific surface area of 400 m2/kg. The SGB cost per ton is only 218 RMB. Compared with Jinchuan’s early-strength cement (345 RMB per ton), its material cost is reduced by 37%. At the same time, SGB effectively utilizes the waste resources around the Jinchuan Mine, reduces carbon emissions, and is conducive to promoting the construction of green mines.
The cement clinker was selected from Qilianshan Cement Plant (Gansu, China), which has a CaO and SiO2 content close to 90%. Cement clinker is a strong active alkaline activator, which can effectively induce and accelerate the slag hydration reaction (Tariq and Nehdi, 2007). The desulfurized gypsum comes from the Hexibao Power Plant (Gansu, China). Its main component is calcium sulfate dihydrate (CaSO4.2H2O), and the content of SO3 is greater than 40%. Grinding aid is produced by Yuanxin Tongxin Technology Co., Ltd. (Beijing, China), and the model is SA117 with polyol and triethanolamine as main components. Grinding aid can obviously improve the flow state of the material in the mill, prevent the agglomeration of fine particles, and improve grinding efficiency.
Jinchuan Mine has carried out a variety of aggregate collocation since its establishment. At present, the filling aggregates are mainly composed of waste rock, rod milling sand, and river sand. The specific physical and chemical properties are as follows.
The rod milling sand used in the test was selected from the sand bin of the Longshou Mine Filling System. The rod milling sand used for backfill is to crush the collected pebbles and screen them into coarse aggregate with particle size less than 25 mm, which is then ground into fine sand with the standard of −3 mm (Figure 1A). The specific gravity of rod frosting is 2.67 g/cm3, the bulk density is 1.585 g/cm3, and the porosity is 40.64%. Rod milling sand has a uniformity coefficient of 8.96 and a curvature coefficient of 1.12 (Table 3), which has a good particle size distribution (Yin et al., 2020a).
FIGURE 1. The particle size composition of backfill materials: (A) rod milling sand, (B) waste rock, (C) river sand.
The underground waste rock in the mining area is crushed by a jaw crusher, and the crushed particle size reaches the standard of −12 mm before being put into use (Figure 1B). The specific gravity of waste rock is 2.87 g/cm3, the bulk density is 1.593 g/cm3, and the porosity is 40.11%. River sand is the Gobi aggregate collected in the open air. After screening, the standard −5 mm river sand aggregate (Figure 1C) is obtained. Its density is 2.75 g/cm3, the bulk density is 1.612 g/cm3, and the porosity is 41.6%. The particle size distribution of waste rock and river sand was determined by the sieving method. Table 3 shows the characteristic particle size of river sand and waste rock. It can be seen that waste rock is a poor-grading backfill material.
The chemical composition of rod milling sand, waste rock, and river sand is mainly SiO2 (Table 4), and their chemical properties are relatively stable. However, a large amount of MgO in river sand will harm the late strength.
The particle size distribution of the filling material was measured using a laser particle size analyzer (Winner 2000; Winner Particle, China). XRD analyzer was used to test backfill materials’ chemical composition (MiniFlex, Rigaku, Japan). SEM was used to test the micromorphology of filling material (FE SEM, JSM-6701F, JEOL, Japan). Mechanical properties of backfill samples were tested by a pressure testing machine (WEW-600D, SFMIT, China). The slurry consistency was tested by a consistency meter (SC-145, Luchen, China). The slurry divergence was measured using a cement fluidity meter (NLD-3, Jietai Mechanical, Chian). SGB with different fineness was made by a small ball mill (SN-TQM12, Shinuo, China). A specific surface area tester was used to measure SGB fineness (FBT-9, SenZhong, China). The slump test was carried out following the method described by Clayton (Clayton et al., 2003). The measurement of bleeding rate adopts the static method.
Five group experiments (Table 5) were conducted to study the feasibility and reliability of SGB to replace cement. The filling materials adaptability, SGB fineness and dosage, SGB slurry workability, and SGB industrial filling strength were analyzed. Among them, industrial filling strength testing of SGB filler was carried out at the western filling station (as shown in Figure 2) in the Longshou Mine area. The slurry was sampled at the discharge port of the filling station pipeline, and then three-layer molds of 10 × 10 × 10 cm were used to produce samples of the filler at 3-, 7-, and 28-d curing ages. The demolded sample is cured under natural conditions. The other four groups were all indoor experiments, and backfill samples were cured under the condition of 75 ± 2% humidity and 20 ± 1°C temperature. All experiments were repeated three times, and three experiments’ average value was taken as the result.
Given the unique diversity and uncertainty of filling aggregate in the Jinchuan Mine, the adaptability test of SGB to filling aggregate was carried out. It lays a foundation for the promotion and application of SGB. The slurry with a mass concentration of 80% and a cement-sand ratio of 1:4 was used as the experimental sample. The aggregate configuration is rod milling sand, river sand, waste rock-rod milling sand (0.5:0.5), and waste rock-rod milling sand-river sand (0.5:0.25:0.25). The influence of SGB on the strength of different aggregates is shown in Figure 3. Figure 3 indicates that the 3-d strength of the backfill sample with river sand as the aggregate is 1.14 MPa, and the 28-d strength is 4.81 MPa, both of which are lower than the design value. Obviously, the adaptability of river sand to SGB is poor, so it cannot be used as a single filling aggregate in the Jinchuan Mine.
Backfill samples under other aggregate configuration conditions can meet the strength requirements of the Jinchuan Mine at different curing ages. At curing ages of 3, 7, and 28 d, the average strength of the rod milling sand backfill sample is 1.86, 4.0, and 5.94 MPa, respectively, which meets the backfill standard (Yin et al., 2020a). But its strength is less than the waste rock mixture. After filling with waste rock-rod milling sand aggregate, the maximum strength reaches 7.54 MPa at 28 d. This behavior is explained as follows. At the same time, waste rock contains a lot of CaO (16.39%), which is easy to participate in hydration (Yin et al., 2020b). The following reactions lead to the improvement of strength. CaO and MgO content in waste rock is high (Table 4), which is easy to participate in hydration (Eqs 1–4) and plays a positive role in strength development.
At the same time, the inhomogeneity coefficient of river sand is 1.8 less than 5, which indicates its poor grading, resulting in low strength of backfill samples at all curing ages. Both rod mill and waste rock have good gradation because their non-uniformity coefficient is greater than 5. At this time, the backfill sample can form a dense structure with good strength at all curing ages. Particle size characteristics of rod milling sand are smaller than that of waste stone, and the mixed aggregate of the two can form a denser structure. Rod-milling sand further fills the pores of the waste rock, while the large particle size of the waste rock contributes to the strength. River sand has the largest particle size, and the mixing of the three aggregates significantly improves the gradation of river sand, while the river sand contributes significantly to the later strength. However, the poor gradation of the river sand itself resulted in the strength of the three mixed aggregate samples being inferior to that of the waste rock-rod milling sand binary mix. Therefore, it is recommended that the mine use waste rock-rod milling sand mixed coarse aggregate for filling, which will further increase the utilization of waste rock, save filling costs, and protect the surrounding environment of the mine.
The fineness and dosage of cemented material are important factors affecting backfill strength (Xiao et al., 2019), so the comprehensive influence of SGB fineness and dosage on strength was tested. A sample with a mass concentration of 80% was prepared by waste rock-river sand-rod milling sand aggregate (0.5:0.25:0.25), in which the fineness of SGB was expressed by specific surface area. Different SGB fineness can be obtained by controlling the grinding time of a small ball mill. The corresponding relationship between grinding time and fineness is shown in Table 6. Moreover, dosage of SGB was 290, 300, and 310 kg/m3, respectively.
The change curve of backfill strength under different SGB fineness conditions (SGB dosage is 300 kg/m3) is shown in Figure 4. Figure 4 indicates that increasing the SGB fineness can significantly improve the backfill samples’ early strength, which is the same as Chindaprasirt’s results (Chindaprasirt et al., 2004). In the backfill sample with curing ages of 3 and 7 d, the SGB surface area has a positive linear correlation with the increase of mechanical properties. The explanation for this behavior is as follows. On the one hand, finer SGB can effectively fill the pores of the aggregated particles. Refine the macropores and capillary pores, make the backfill body denser, and improve the strength. Moreover, when the specific surface area of the SGB material increases, the slag will be mechanically activated and stimulated. As the number of active particles per unit volume increases, the hydration reaction speeds up, thus improving the early strength of the backfill sample. However, the results show that when the fineness of the SGB is too large, it will adversely affect the later strength. After the specific surface area of SGB increased from 510 to 530 m2/kg, the 28-d strength decreased to 6.54 MPa, and the strength drop was 11.97%. This is due to the fine cementitious material, resulting in rapid early hydration and a large number of hydration products. These hydration products deposit on the surface of slag particles and restrict the further hydration of slag. The hydration of the slag is the main source of the backfill specimens’ late strength, and its slow hydration process will lead to late strength reduction (Erdogdu and Turker, 1998).
The relationship between the SGB dosage and the 28-d strength of the backfill sample is shown in Figure 5. Figure 5 indicates that the 28-d strength of SGB (400 m2/kg) without ball milling decreases with increasing dosage. The reason is that there are more coarse particles in SGB without ball milling. Although SGB dosage increased, the degree of hydration remained unchanged, and the increased hydration products were limited. In addition, with the increase of SGB dosage, the embedded locking effect between coarse aggregate particles is weakened, and some coarse aggregates are completely wrapped by fine particles, which is not conducive to the formation of a stable structure (Meddah et al., 2010). An increase in dose will result in a loose structure and strength deterioration of the sample.
After SGB is ball milling, the backfill body strength increases with the SGB dosage. This is because milling increases the fineness of SGB, which improves its hydration and forms more hydration products that are more conducive to cementing coarse aggregate particles (Wang et al., 2019). However, when the SGB fineness changes, the strength increase rate is also different. The finer SGB material reacts more fully with water. Based on a comprehensive analysis of the early and late strength to backfill samples, it was found that the best mechanical properties were obtained when the specific surface area was 510 m2/kg and the dosage was 310 kg/m3. Under the same experimental conditions, the strength of the backfilled sample with cement as the binder is only 7.1 MPa, which is 0.85 times that of the SGB sample. Therefore, reasonable SGB fineness and dosage can effectively improve the strength of backfill material.
Slurry has good workability, which is a necessary condition for replacing cement with SGB (Collins and Sanjayan, 1999; Chen et al., 2009). Waste rock mixture was used as a sample to prepare backfill slurry. Slump, consistency, and bleeding rate were tested to evaluate the workability of the SGB slurry. The test results are shown in Figure 6. Figure 6 indicates that the SGB slurry layering and segregation phenomenon is serious at a mass concentration of 78%. The slump, consistency, and bleeding rate relatively are higher, which are 30.6 cm, 12.1 cm, and 13.1%, respectively, indicating the poor stability of slurry. The reason for this is the low viscosity of the paste formed by SGB and water, which leads to coarse aggregate settling and slurry segregation. When the mass concentration increases to 80∼82%, the fluidity is relatively good. In this case, the slump is 27–28 cm, the consistency is 11–12 cm, and the bleeding rate is less than 10%. It shows good stability and meets the requirements of high-concentration slurry gravity transportation.
The workability of SGB slurry and cement slurry was compared, and it was found that both slump and consistency decreased with the increase of mass concentration, which is the same as Jiang’s result (Jiang et al., 2016). However, since the cementing effect of SGB is better than that of cement, the slump and consistency of SGB slurry are slightly lower than cement slurry. At a lower mass concentration (78∼80%), the fluidity of two slurries is basically the same, and the difference in a slump is only 5.6 and 3.9%. Similarly, when the concentration is less than 80%, the slump of both is more than 30 cm, so the slurry segregation degree is relatively large. Compared with SGB slurry, the bleeding rate of cement slurry under the same concentration condition is 1∼3% lower. It shows that the water retention capacity of cement mortar is stronger. But relatively speaking, the SGB slurry with a high bleeding rate has better concentration adaptability and can still maintain better fluidity under high-concentration filling conditions. To sum up, there is no essential difference between SGB slurry and cement slurry in terms of fluidity and stability. SGB can replace cement for pipeline filling and conveying systems, and it will give play to the advantages of low cost and high benefit.
An industrial backfill test was carried out at the mine filling station. The waste rock mixture was used as a sample to prepare a filling slurry with a mass concentration of 80%. Among them, the binder is SGB and cement, respectively. The specific surface of cementitious material is 510 m2/kg, and the aggregate collocation method is waste rock-river sand-rod milling sand (0.5:0.25:0.25). The mechanical properties of two kinds of cementitious materials at different curing ages were compared and analyzed to evaluate the feasibility and reliability of industrial backfilling with SGB instead of cement.
Test results of backfill sample strength under different cementitious material conditions are shown in Figure 7. Figure 7 shows that the SGB sample 28-d strength is lower than the cement sample at a mass concentration, which is 79%. However, with the increase of mass concentration, the 28-d strength becomes higher than the cement sample. It shows that SGB has good adaptability to the high-concentration slurry. The sample with 80% mass concentration was taken as a case to discuss. Under the same test conditions, the 3-d strength of the SGB backfill sample is slightly lower than the cement sample. However, the strengths of 7 and 28 d are higher than the cement backfill sample. The 3-, 7-, and 28-days strength of the SGB backfill sample are 0.91 times, 1.43 times, and 1.2 times the cement sample. They are 1.68 times, 2.42 times, and 1.95 times the design strength of the Jinchuan Mine, respectively. The 3-d strength of the SGB backfill sample is slightly lower than the cement but greater than the design strength, which is within an acceptable range. Meanwhile, the 7- and 28-d strengths are more than 1.2 times the strength of cement. The minimum safety factor of SGB backfill sample strength is more than 1.68 times mine design strength. It is proved that SGB with high safety and low cost can replace cement in mine backfilling under higher concentration conditions.
The hydration process of SGB material is as follows. The first is activator hydration. Tricalcium silicate (C3S), tricalcium aluminate (C3A), and tetra calcium aluminate (C4AF) in cement clinker rapidly undergo hydration reactions. C3S hydrates to form hydrated calcium silicate and calcium hydroxide, while C3A hydrates to form plate hydrates C2AH8 and C4AH13. C4AH13 reacts with desulfurized gypsum to produce hydrated calcium silicate and ettringite (AFt) to provide early strength. Then there is the slag activation. The cement clinker is continuously hydrated to form calcium hydroxide, which increases the basicity and OH−concentration of slurry. After the active glass structure in the slag is destroyed, Ca2+ and silicate ions are released. The Ca2+ and SO42− produced by the continuous dissolution of desulfurization gypsum combine with other ions in the slurry to form the hydration products mainly composed of C-S-H gel and ettringite. Due to the joint action of the cement clinker and desulfurized gypsum hydration products, the active ingredient CaO in the slag dissolves faster, which promotes the rapid progress of the slag hydration reaction.
Figure 8 shows XRD patterns of SGB and cement hydration products. It can be seen that the hydration products of the SGB are mainly (d = 0.490, 0.311, 0.263, 0.193, 0.179, 0.169, 0.148), ettringite crystal (AFt-Ca6 [Al(OH)6]2·(SO4)3·26H2O) (d = 0.560, 0.387, 0.221), and calcium sulfoaluminate crystal (C4AH13) (d = 0.182) (Haha et al., 2012). At the same time, gypsum (CaSO4) (d = 0.427) and dicalcium silicate that has not undergone hydration reaction can also be observed in the diffraction spectrum.
Different from the cement hydration reaction, the diffraction peak of Ca(OH)2 was not detected in the XRD spectrum of SGB. In addition, peak values of ettringite increased with the increase of curing age. The main reason is that the amount of cement clinker is small, and the Ca(OH)2 produced by hydration does not form crystals and separate. Instead, it participates in slag hydration and forms C-S-H gel. In summary, the chemical reaction of SGB in the curing process is the pozzolanic reaction between the active part of SiO2, Al2O3, and Ca(OH)2 in the slag. The calcium aluminate hydrate formed by the pozzolanic reaction continues to react with the desulfurized gypsum to form ettringite crystals. The ettringite crystals formation consumes a large amount of calcium aluminate hydrate. Calcium aluminate hydrate is the main hydration product after slag hydration, so this process accelerates slag hydration reaction. The main chemical reactions are as follows.
SEM microscopic images of SGB backfill body slices at different curing ages are shown in Figure 9. Figure 9 shows that the hydration products of SGB are mainly C-S-H gel and short rod-shaped ettringite (Yin et al., 2021), which are significantly different from the acicular AFt and flake or prismatic calcium hydroxide crystal structures of cement hydration products. As the curing time increases, the SGB hydrated product crystals become more and more, and the crystal diameter increases significantly. Finally, the C-S-H gel wrapped the ettringite, and rod-shaped ettringite is more difficult to observe. C-S-H and AFt form very dense gel that fills the space between the aggregates, which binds the aggregates together to form a whole with greater mechanical properties.
FIGURE 9. SEM micrographs of samples after curing for 3, 7, and 28 d, where (A-1–A-3) the binder is SGB and (B-1–B-3) the binder is cement.
The prohibitive cost and low strength of backfill material is a challenge for Jinchuan’s mine filling system. The feasibility of slag-gypsum binder replacing cement for mining backfill is discussed emphatically. Based on these results, the following conclusions can be drawn.
1) SGB is beneficial to the industrial backfill of waste rock mixed coarse aggregate. The 28-d strength of the waste rock mixture sample is 7.54 and 7.31 MPa, which are much higher than other aggregate samples.
2) Reasonable SGB fineness can effectively improve the strength of backfilled samples. Increasing the fineness of SGB has a positive effect on early strength. However, when the specific surface area is greater than 510 m2/kg, it harms the late strength.
3) Substituting SGB for cement has little effect on workability. Both have the same trend of variation, and the difference of slump and consistency is less than 10%. Although the bleeding rate of SGB samples is high, they can still maintain good fluidity under high-concentration filling conditions.
4) SGB can improve the safety and reliability of backfill mining. Industrial backfilling tests show that under higher concentration conditions, the 3-d strength of SGB samples is slightly lower, while the 7- and 28-d strengths are 1.2 times the cement samples and have a safety reserve of 1.68 times the design strength.
5) The hydration performance of SGB is different from cement. Through XRD and SEM analysis, it is found that the Ca(OH)2 generated by SGB is directly consumed during the hydration, and no crystals are formed. In addition, the SGB hydration product has a denser structure.
Despite these results, the following work is expected to be carried out to better understand the cementing properties of SGB: 1) mechanical properties of SGB-CPB under high stress in deep ground; 2) effect of temperature on thixotropy of fresh SGB-CPB.
The original contributions presented in the study are included in the article/Supplementary Material, further inquiries can be directed to the corresponding author.
YX: Writing—review and editing. YZ: Data curation, writing—original draft. LW: diting and writing. WL: E Conceptualization. YS: Methodology.
This research was supported by the China National Science Fund for Fundamental Research Funds for the Central Universities (FRF-TP-20-039A1); funded by Open Foundation of State Key Laboratory of Mineral Processing (BGRIMM-KJSKL-2021-18), China Postdoctoral Science Foundation—funded project (2021M690363), and thanks to all reviewers’ valuable comments to promote this paper significantly.
The authors declare that the research was conducted in the absence of any commercial or financial relationships that could be construed as a potential conflict of interest.
All claims expressed in this article are solely those of the authors and do not necessarily represent those of their affiliated organizations, or those of the publisher, the editors, and the reviewers. Any product that may be evaluated in this article, or claim that may be made by its manufacturer, is not guaranteed or endorsed by the publisher.
Bell, F. G., Stacey, T. R., and Genske, D. D. (2000). Mining Subsidence and its Effect in the Environment: Some Differing Examples. Environ. Geol. 40, 135–152. doi:10.1007/s002540000140
Benzaazoua, M., Bussière, B., Demers, I., Aubertin, M., Fried, É., and Blier, A. (2008). Integrated Mine Tailings Management by Combining Environmental Desulphurization and Cemented Paste Backfill: Application to Mine Doyon, Quebec, Canada. Miner. Eng. 21, 330–340. doi:10.1016/j.mineng.2007.11.012
Carlsson, L. A., Gillespie, J. W., and Pipes, R. B. (1986). Effect of Fly Ash Composition on Sulfate Resistance of Cement. J. Proc. 83, 994
Chen, J. C., Rau, H., Sun, C. J., Stzeng, H. W., and Chen, C. H. (2009). Workflow Design and Management for Ic Supply Chain. IEEE, 697
Chen, Q., Zhang, Q., Qi, C., Fourie, A., and Xiao, C. (2018). Recycling Phosphogypsum and Construction Demolition Waste for Cemented Paste Backfill and its Environmental Impact. J. Clean. Prod. 186, 418–429. doi:10.1016/j.jclepro.2018.03.131
Chen, S., Wang, W., Yan, R., Wu, A., Wang, Y., and Yilmaz, E. (2022). A Joint Experiment and Discussion for Strength Characteristics of Cemented Paste Backfill Considering Curing Conditions. Minerals 12, 211. doi:10.3390/min12020211
Chindaprasirt, P., Homwuttiwong, S., and Sirivivatnanon, V. (2004). Influence of Fly Ash Fineness on Strength, Drying Shrinkage and Sulfate Resistance of Blended Cement Mortar. Cem. Concr. Res. 34, 1087–1092. doi:10.1016/j.cemconres.2003.11.021
Clayton, S., Grice, T. G., and Boger, D. V. (2003). Analysis of the Slump Test for On-Site Yield Stress Measurement of mineral Suspensions. Int. J. Miner. Process. 70, 3–21. doi:10.1016/s0301-7516(02)00148-5
Collins, F. G., and Sanjayan, J. G. (1999). Workability and Mechanical Properties of Alkali Activated Slag concrete. Cem. Concr. Res. 29, 455–458. doi:10.1016/s0008-8846(98)00236-1
Cui, L., and Fall, M. (2015). A Coupled Thermo-Hydro-Mechanical-Chemical Model for Underground Cemented Tailings Backfill. Tunn. Undergr. Sp. Technol. 50, 396–414. doi:10.1016/j.tust.2015.08.014
Dai, X., Ren, L., Gu, Xi., Yilmaz, E., Fang, K., and Jiang, H. (2022). Strength Analysis and Optimization of Alkali Activated Slag Backfills through Response Surface Methodology. Front. Mater., 844608. doi:10.3389/fmats.2022.844608
Deb, P. S., Nath, P., and Sarker, P. K. (2014). The Effects of Ground Granulated Blast-Furnace Slag Blending with Fly Ash and Activator Content on the Workability and Strength Properties of Geopolymer concrete Cured at Ambient Temperature. Mater. Des. 62, 32–39. doi:10.1016/j.matdes.2014.05.001
Erdogdu, K., and Turker, P. (1998). Effects of Fly Ash Particle Size on Strength of portland Cement Fly Ash Mortars. Cem. Concr. Res. 28, 1217
Flatt, R. J., Roussel, N., and Cheeseman, C. R. (2012). Concrete: An Eco Material that Needs to Be Improved. J. Eur. Ceram. Soc. 32, 2787–2798. doi:10.1016/j.jeurceramsoc.2011.11.012
Gorai, B., Jana, R. K., and Premchand, (2003). Characteristics and Utilisation of Copper Slag - A Review. Resour. Conserv. Recycl. 39, 299–313. doi:10.1016/s0921-3449(02)00171-4
Haha, M. B., Lothenbach, B., Saout, G. L., and Winnefeled, F. (2012). Influence of Slag Chemistry on the Hydration of Alkali-Activated Blast-Furnace Slag - Part II: Effect of Al2O3. Cem. Concr. Res. 42, 74–83. doi:10.1016/j.cemconres.2011.08.005
Hassani, F., Razavi, S. M., and Isagon, I. (2007). A Study of Physical and Mechanical Behaviour of Gelfill. CIM Bull. 100, 1
Helinski, M., Fahey, M., and Fourie, A. (2011). Behavior of Cemented Paste Backfill in Two Mine Stopes: Measurements and Modeling. J. Geotech. Geoenvironmental Eng. 137, 171–182. doi:10.1061/(asce)gt.1943-5606.0000418
Jiang, H., Han, J., Li, Y., Yilmaz, E., Sun, Q., and Liu, J. (2020). Relationship between Ultrasonic Pulse Velocity and Uniaxial Compressive Strength for Cemented Paste Backfill with Alkali-Activated Slag. Nondestruct. Test. Eval. 35, 359–377. doi:10.1080/10589759.2019.1679140
Jiang, H., Mamadou, F., and Liang, C. (2016). Yield Stress of Cemented Paste Backfill in Sub-zero Environments: Experimental Results. Miner. Eng. 92, 141. doi:10.1016/j.mineng.2016.03.014
Jiang, H., Qi, Z., Yilmaz, E., Han, J., Qiu, J., and Dong, C. (2019). Effectiveness of Alkali-Activated Slag as Alternative Binder on Workability and Early Age Compressive Strength of Cemented Paste Backfills. Constr. Build. Mater. 218, 689–700. doi:10.1016/j.conbuildmat.2019.05.162
Kesimal, A., Yilmaz, E., Ercikdi, B., Alp, I., and Deveci, H. (2005). Effect of Properties of Tailings and Binder on the Short-And Long-Term Strength and Stability of Cemented Paste Backfill. Mater. Lett. 59, 3703–3709. doi:10.1016/j.matlet.2005.06.042
Li, X., Du, J., Gao, L., He, S., Gan, L., Sun, C., et al. (2017). Immobilization of Phosphogypsum for Cemented Paste Backfill and its Environmental Effect. J. Clean. Prod. 156, 137–146. doi:10.1016/j.jclepro.2017.04.046
Li, Y., and Sun, Y. (2000). Preliminary Study on Combined-Alkali-Slag Paste Materials. Cem. Concr. Res. 30, 963–966. doi:10.1016/s0008-8846(00)00269-6
Meddah, M. S., Zitouni, S., and Belâabes, S. (2010). Effect of Content and Particle Size Distribution of Coarse Aggregate on the Compressive Strength of concrete. Constr. Build. Mater. 24, 505–512. doi:10.1016/j.conbuildmat.2009.10.009
Qi, C., Chen, Q., Fourie, A., Zhao, J., and Zhang, Q. (2018). Pressure Drop in Pipe Flow of Cemented Paste Backfill: Experimental and Modeling Study. Powder Technol. 333, 9–18. doi:10.1016/j.powtec.2018.03.070
Rashad, A. M. (2013). A Comprehensive Overview about the Influence of Different Additives on the Properties of Alkali-Activated Slag - A Guide for Civil Engineer. Constr. Build. Mater. 47, 29–55. doi:10.1016/j.conbuildmat.2013.04.011
Shi, C., and Qian, J. (2000). High Performance Cementing Materials from Industrial Slags - A Review. Resour. Conserv. Recycl. 29, 195–207. doi:10.1016/s0921-3449(99)00060-9
Souza, E. D., Archibald, J. F., and Degagne, D. (1997). Glassful - an Environmental Alternative for Waste Glass Disposal. CIM Bull. 90, 58
Sun, Q., Wei, X., Li, T., and Zhang, L. (2020). Strengthening Behavior of Cemented Paste Backfill Using Alkali-Activated Slag Binders and Bottom Ash Based on the Response Surface Method. Materials (Basel) 13, 855. doi:10.3390/ma13040855
Tariq, A., and Nehdi, M. (2007). Developing Durable Paste Backfill from Sulphidic Tailings. Waste Resour. Manag. 160, 155–166. doi:10.1680/warm.2007.160.4.155
Tariq, A., and Yanful, E. (2013). A Review of Binders Used in Cemented Paste Tailings for Underground and Surface Disposal Practices. J. Environ. Manage. 131, 138–149. doi:10.1016/j.jenvman.2013.09.039
Tilmaz, E., Belem, T., and Benzaazoua, M. (2010). Assessment of the Modified CUAPS Apparatus to Estimate In Situ Properties of Cemented Paste Backfill. Geotech. Test. J. 33, 351. doi:10.1520/GTJ102689
Wang, A., Cao, S., and Yilmaz, E. (2022). Effect of Height to Diameter Ratio on Dynamic Characteristics of Cemented Tailings Backfills with Fiber Reinforcement through Impact Loading. Constr. Build. Mater. 322, 126448. doi:10.1016/j.conbuildmat.2022.126448
Wang, S. D., Scrivener, K. L., and Pratt, P. L. (1994). Factors Affecting the Strength of Alkali-Activated Slag. Cem. Concr. Res. 24, 1033–1043. doi:10.1016/0008-8846(94)90026-4
Wang, Y., Wen, Z., Yang, Z., and Gao, Q. (2019). Influence of Slag Fineness on the Strength of Cemented Backfill. J. Guangxi Univ. 44, 1149
Xiao, B., Yang, Z., Chen, D., and Gao, Q. (2019). Impacts of Slag-Based-Binder Fineness on Strength in Mining Backfill. Sci. Sin. Technol. 49, 402–410. doi:10.1360/n092018-00109
Xue, G., Yilmaz, E., Song, W., and Cao, S. (2018). Compressive Strength Characteristics of Cemented Tailings Backfill with Alkali-Activated Slag. Appl. Sci. 8, 1537. doi:10.3390/app8091537
Yan, B., Jia, H., Yilmaz, E., Lai, X., Shan, P., and Hou, C. (2022). Numerical Study on Microscale and Macroscale Strength Behaviors of Hardening Cemented Paste Backfill. Constr. Build. Mater. 321, 126327. doi:10.1016/j.conbuildmat.2022.126327
Yilmaz, E., Belem, T., Bussière, B., Mbonimpa, M., and Benzaazoua, M. (2015). Curing Time Effect on Consolidation Behaviour of Cemented Paste Backfill Containing Different Cement Types and Contents. Constr. Build. Mater. 75, 99–111. doi:10.1016/j.conbuildmat.2014.11.008
Yılmaz, T., Ercikdi, B., and Deveci, H. (2018). Utilisation of Construction and Demolition Waste as Cemented Paste Backfill Material for Underground Mine Openings. J. Environ. Manage. 222, 250–259. doi:10.1016/j.jenvman.2018.05.075
Yin, S., Chen, W., Zou, L., Kou, Y. yuan., and Liwen, X. (2020a). Optimization of the Effect and Formulation of Different Coarse Aggregates on Performance of the Paste Backfill Condensation. Chin. J. Eng. 42, 829. doi:10.13374/j.issn2095-9389.2019.07.14.005
Yin, S., Hou, Y., Chen, X., and Zhang, M. (2021). Mechanical, Flowing and Microstructural Properties of Cemented Sulfur Tailings Backfill: Effects of Fiber Lengths and Dosage. Constr. Build. Mater. 309, 125058. doi:10.1016/j.conbuildmat.2021.125058
Yin, S., Liu, J., Shao, Y., Zhang, H., Armelle, B., and Kou, Y. (2020b). Influence Rule of Early Compressive Strength and Solidification Mechanism of Full Tailings Paste with Coarse Aggregate. J. Cent. South. Univ. (Science Technol. 51, 478–488. doi:10.11817/j.issn.1672-7207.2020.02.021
Keywords: slag-gypsum binder, mine backfill, hydration products, slurry workability, mass concentration
Citation: Xiaobing Y, Zepeng Y, Weiguang L, Leiming W and Shenghua Y (2022) Effect of Slag Gypsum Binder as a Substitute to Cement on the Stability of Backfill Mining. Front. Mater. 9:869875. doi: 10.3389/fmats.2022.869875
Received: 05 February 2022; Accepted: 21 February 2022;
Published: 22 March 2022.
Edited by:
Faris Matalkah, Yarmouk University, JordanReviewed by:
Erol Yilmaz, Recep Tayyip Erdoğan University, TurkeyCopyright © 2022 Xiaobing, Zepeng, Weiguang, Leiming and Shenghua. This is an open-access article distributed under the terms of the Creative Commons Attribution License (CC BY). The use, distribution or reproduction in other forums is permitted, provided the original author(s) and the copyright owner(s) are credited and that the original publication in this journal is cited, in accordance with accepted academic practice. No use, distribution or reproduction is permitted which does not comply with these terms.
*Correspondence: Yan Zepeng, eWFuX3plcGVuZ0AxNjMuY29t
Disclaimer: All claims expressed in this article are solely those of the authors and do not necessarily represent those of their affiliated organizations, or those of the publisher, the editors and the reviewers. Any product that may be evaluated in this article or claim that may be made by its manufacturer is not guaranteed or endorsed by the publisher.
Research integrity at Frontiers
Learn more about the work of our research integrity team to safeguard the quality of each article we publish.