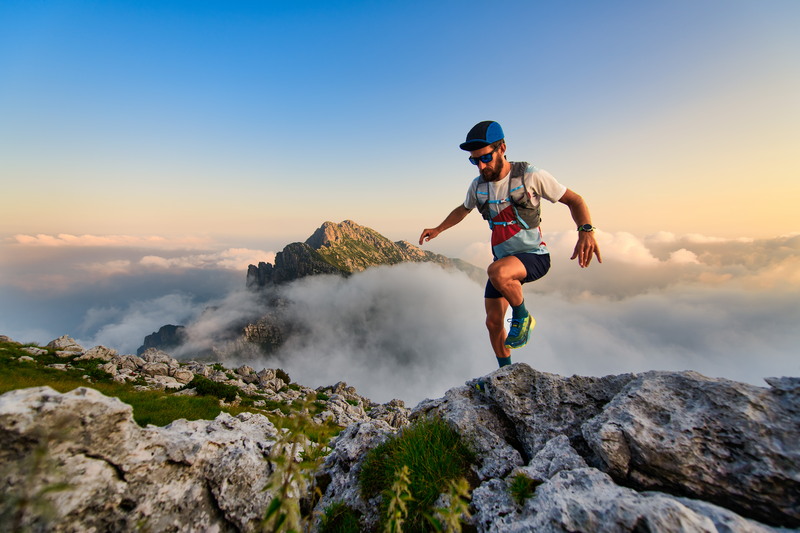
94% of researchers rate our articles as excellent or good
Learn more about the work of our research integrity team to safeguard the quality of each article we publish.
Find out more
EDITORIAL article
Front. Mater. , 15 February 2022
Sec. Polymeric and Composite Materials
Volume 9 - 2022 | https://doi.org/10.3389/fmats.2022.843571
This article is part of the Research Topic Carbon Nanomaterial Filled Polymer Composites for Functional Applications: Processing, Structure, and Property Relationship View all 13 articles
Editorial on the Research Topic
Carbon Nanomaterial Filled Polymer Composites for Functional Applications: Processing, Structure, and Property Relationship
Carbon nanomaterials, such as carbon nanotubes and graphene, are able to transfer their excellent thermal and electrical conductivity to polymers while retaining or even improving their original mechanical performance. Polymer/carbon nanomaterial composites are increasingly applied in aerospace, automotive and electronic industries for electromagnetic interference (EMI) shielding, electrostatic dissipation (ESD), sensors etc., when flexibility or light weight is required. Up to date, many researchers have conducted a lot of studies on the development of functional polymer/carbon nanomaterial composites. How processing affects the structuring and properties of these nanocomposites is usually ignored, while it is very significant to their applications. The aim of the current Research Topic is to cover novel research in the processing-structure-property relationship of functional polymer/carbon nanomaterial composites, including the property and structure tuning of nanocomposites in processing.
In recent years, 3D printing (also called as additive manufacturing), as a rapid development method of no mold, low-cost, high-precision and rapid preparation in recent years, has attracted a lot of attention in carbon nanomaterials filled polymers based flexible strain sensors. To summarize the latest progress, Liu et al. presented a dedicated mini-review on high-performance flexible strain sensors of conductive polymer composites by employing different 3D printing technologies, involving Direct Ink Writing (DIW), Selective Laser Sintering (SLS), Fused Filament Fabrication (FFF) and Digital Light Processing (DLP) and printing materials in recent years. The authors also summarized the development direction of high-performance flexible strain sensor based on 3D printing. Golbang et al. made a comparative study on FFF and injection moulding of high-performance inorganic fullerene tungsten sulphide (IF-WS2)/poly ether ether ketone (PEEK) composites, including dispersion, crystallinity and mechanical properties. It was concluded that IF-WS2 nanoparticles doped with PEEK can improve the mechanical properties of PEEK prepared by FDM.
Mokhtari et al. prepared antistatic, high-performance composites of PEEK and expanded graphite (EG) through twin-screw extrusion and injection molding. The morphological, rheological, electrical, mechanical, thermal and wear properties of the EG/PEEK composites were studied. The results indicated that the mechanical properties of the composites could be improved by annealing. The introduction of 5 vol% EG increased the flexural and tensile modulus of PEEK from 3.55 to 3.84 GPa to 4.40 and 4.15 GPa, respectively. Compared with the neat PEEK, the wear resistance of the composite with 3 vol% EG was increased by 37%.
Biaxial stretching is also another effective method to prepare high-performance carbon nanomaterials filled polymer composites. In the mini-review by Chen et al., the influence of biaxial stretching on the structure and properties of nanocomposites containing different nanofillers was presented. In addition, their applications were summarized, and the future prospects and challenges of this technology were discussed. The reported work could promote future research for the development of high-performance polymer nanocomposites with high productivity. Mayoral et al. investigated the effects of biaxial stretching and graphene nanoplatelets (GNPs) loading on the bulk properties of polypropylene (PP)/GNP nanocomposites. It is shown that the electrically conductive composites were obtained with the addition of GNPs (>5 wt%) due to the generation of numerous conductive paths. The GNP resulted in enhanced modulus and strength and increased crystallinity of polymer. Biaxial stretching further enhanced the mechanical properties of nanocomposites wihle the electrical conductivity was slightly reduced.
The development of interlayer dielectric materials with low dielectric loss factor (Df) and dielectric constant (Dk) has attracted the attention of much researchers in order to achieve low delay and high fidelity characteristics in high-frequency signal transmission. The dielectric loss mechanism of polymer composites and the resins usually used in high-frequency copper-clad laminates were summarized by Wang et al. How to reduce the dielectric constant and dielectric loss of composites was discussed from the aspects of nanofiller selection and molecular structure design.
The out-of-plane mechanical performance of glass fiber reinforced polymer (GFRP) composites still need further improvement to achieve the practicability of GFRP in the field of oil and gas. Yao et al. fabricated GNP/GFRP composites by two methods combining either vacuum mixing or spray coating with vacuum-assisted resin infusion. A severe filtering effect was observed in the former method, where the GNPs were not uniformly dispersed in the resulted composite, whereas the latter led to a uniform GNP dispersion on the glass fabrics. The flexural strength and modulus of GFRP were respectively increased by 6.8 and 1.6% with an optimal content of 0.15 wt% GNPs.
Kyei-Manu et al. investigated the thermo-mechanical properties of carbon black filled natural and styrene butadiene rubbers under rapid adiabatic conditions. The results showed a strong correlation among the temperature rise, mechanical hysteresis, modulus and crystallinity of the rubbers measured in tensile extension with strain amplification factors. This highlighted the effect of matrix overstraining on microstructural evolution of the rubbers during extension. Analysis of the thermal measurements of the rubber compounds during extension and retraction and contrasting between non-crystallizing and crystallizing rubbers indicated that a substantial irreversible heat generation happened during the rubber compounds extension.
Carbon nanotube (CNT) composites are promising candidates for structural power composites due to their high surface area, mechanical and electrical properties. Koliolios et al. explored the nail penetration behaviors of supercapacitors with carbon nanotube-polyaniline (CNT/PANI) electrodes. It was shown that the wet cells with the electrolyte and the dry cells without electrolyte exhibited a piece-wise nonlinear relationship and a power law behavior, respectively. The cyclic voltammetry indicated the significant capacitance loss, resulting in the transition of cell behavior from capacitor to resistor-like manner.
Laser welding is a critical manufacturing technology for various plastic products including medical devices, automotive components and consumer goods. Determining a set of optimal parameters for laser transmission welding (LTW) technique of thermoplastics and composites could be quite challenging due to a higher heat density of the LTW. was used A 3D transient thermal model for LTW of isotactic polypropylene (iPP) and its composites with CB was built by Ali et al. using the finite element method (FEM)-based software COMSOL Multiphysics to investigate the effect of carbon black along other control parameters for high-speed welding. It was observed that the composites with 0.5 wt% and 1 wt% of CB were successfully welded with neat iPP.
DX Completed this editorial article.
The author declares that the research was conducted in the absence of any commercial or financial relationships that could be construed as a potential conflict of interest.
All claims expressed in this article are solely those of the authors and do not necessarily represent those of their affiliated organizations, or those of the publisher, the editors and the reviewers. Any product that may be evaluated in this article, or claim that may be made by its manufacturer, is not guaranteed or endorsed by the publisher.
The author would like to thank all the reviewers and handling editors for every success in this Research Topic.
Keywords: carbon nanomaterials, polymer composites, functional nanocomposites, processing, structure, property relationship
Citation: Xiang D (2022) Editorial: Carbon Nanomaterial Filled Polymer Composites for Functional Applications: Processing, Structure, and Property Relationship. Front. Mater. 9:843571. doi: 10.3389/fmats.2022.843571
Received: 26 December 2021; Accepted: 27 January 2022;
Published: 15 February 2022.
Edited by:
Guilherme Mariz de Oliveira Barra, Federal University of Santa Catarina, BrazilReviewed by:
Claudia Merlini, Federal University of Santa Catarina, BrazilCopyright © 2022 Xiang. This is an open-access article distributed under the terms of the Creative Commons Attribution License (CC BY). The use, distribution or reproduction in other forums is permitted, provided the original author(s) and the copyright owner(s) are credited and that the original publication in this journal is cited, in accordance with accepted academic practice. No use, distribution or reproduction is permitted which does not comply with these terms.
*Correspondence: Dong Xiang, ZHhpYW5nMDFAaG90bWFpbC5jb20=
Disclaimer: All claims expressed in this article are solely those of the authors and do not necessarily represent those of their affiliated organizations, or those of the publisher, the editors and the reviewers. Any product that may be evaluated in this article or claim that may be made by its manufacturer is not guaranteed or endorsed by the publisher.
Research integrity at Frontiers
Learn more about the work of our research integrity team to safeguard the quality of each article we publish.