- 1The Biological Materials Group, Biomimetics, Faculty 5, Hochschule Bremen - HSB - City University of Applied Sciences, Bremen, Germany
- 2Fraunhofer-Institut für Werkstoffmechanik IWM, Freiburg, Germany
- 3NOVACOM Verstärkte Kunststoffe GmbH, Aachen, Germany
The most common studies in the literature are those analyzing fatigue life under cyclic loading for flax fiber-reinforced composites. A novel type of staple fiber yarn made from flax tow with almost unidirectional fiber orientation and a quasi-unidirectional fabric was developed for composite applications. Additionally, a hybrid material made of flax and glass was produced for a demonstrator component (an axle tie of a narrow-gauge railway). For such an application, the investigation of fatigue strength is of particular importance. Therefore, the fatigue behavior of flax, glass, and hybrid flax/glass composites was investigated in the high cycle fatigue range. A total of 106 load cycles were carried out. From about 7³ to 8³ loading cycles, the flax laminate was found to have higher fatigue strength than the glass fiber-reinforced composite. The hybrid materials tend to show a higher fatigue strength than the glass type from approximately 2 × 105 load cycles. Results based on a finite element method also demonstrate better fatigue properties at an increased number of load cycles for flax-based composites than the glass fiber-reinforced component. The flax/glass component’s fatigue strength ranged between the flax values and the glass fiber-reinforced composites. Overall, the hybrid material shows significantly better static bending and impact characteristics than flax and considerably better fatigue properties than the glass fiber-reinforced composite making the hybrid material attractive for an application in an axle tie.
1 Introduction
For the mechanical design of fiber-reinforced components, it is essential to consider and understand the fatigue behavior of this type of material. This is even more important if the relatively young material group of natural fiber–reinforced composites in structural components is intended to be used. The analysis of the fatigue behavior of, e.g., glass fiber–reinforced plastics (GFRP) under cyclic loading has been researched for a long time (Bledzki and Gassan, 1998; Keusch et al., 1998; Bernasconi et al., 2007; Towo and Ansell, 2008a; Lemanski and Sutcliffe, 2010; Shahzad et al., 2019). Natural fiber–reinforced plastics (NFRP) have become increasingly important in recent years, and especially, flax fiber–reinforced composites are increasingly used for applications subject to higher mechanical loads, such as sports equipment and higher loaded construction materials (Misra et al., 2011; Alkbir et al., 2016; More, 2021; Rahman, 2021). However, dissemination is still limited (Staiger et al., 2008). The most prominent application area remains in nonstructural parts with randomly oriented fibers in the automotive and construction industry and is mainly driven by the lower price and environmental concerns rather than the reinforcing effect of the fibers (Karus and Kaup, 2002; Parikh et al., 2002; Dunne et al., 2016). Besides this, a problem with natural fibers exists in more variables, such as growing conditions and environmental influences, that determine their final properties and performance for composite applications (Misra et al., 2011; Baley et al., 2020).
Nevertheless, the processability of natural fibers and the development of high-quality semifinished products are enhanced considerably in recent years. Meanwhile, most of the processing methods used for GFRP can also be applied to natural fiber-reinforced composites, such as prepreg tape laying, winding, pultrusion, resin transfer molding, compression molding, or thermoforming (Jauhari et al., 2015). A major problem in the further spread of natural fibers for higher loaded technical products is the high price of semifinished products. The effort required to prepare natural fibers for high-quality semifinished products is high, and the price can approach the costs of semifinished carbon fiber products and, thus, does not represent an alternative for many industries (Deimann, 2020). Therefore, the development of semifinished products from cheaper fibers, leading to comparable reinforcement, e.g., high-quality flax rovings available on the market, may help establish natural fiber–reinforced plastics in higher loaded products (Deimann, 2020; Graupner et al., 2021).
In recent years, the fatigue and damping behavior of natural fiber–reinforced composites are increasingly investigated, and this led to interesting results. Natural fibers were found to have good damping properties, often exceeding those of glass fibers (Gassan and Bledzki, 1999; Rahman et al., 2016; Dhanraj et al., 2019; Liu et al., 2021; Rahman, 2021). Fatigue is a phenomenon causing progressive damage to materials under cyclic loading. The damage is induced by cracks and deformation and eventually leads to the final failure of the composite (Burhan and Kim, 2018). Plastics reinforced with different cellulose-based fibers are studied regarding fatigue strength, such as flax (Gassan, 2002; Liang et al., 2012; Shah et al., 2013; El Sawi et al., 2014; Liang et al., 2014; Bensadoun et al., 2015; Ueki et al., 2015; Bensadoun et al., 2016; Berges et al., 2016; Sodoke et al., 2016; Kumar et al., 2018; Mahboob and Bougherara, 2018; Nagabhooshanam et al., 2018; Habibi et al., 2019; Haggui et al., 2019; Jeannin et al., 2019; Malloum et al., 2019; Feng et al., 2020; Hallak Panzera et al., 2020; Islam and Ulven, 2020; Mahboob and Bougherara, 2020; Li et al., 2020; Szebényi et al., 2020; Liber-Kne´c et al., 2015; Bambach, 2020), hemp (Yuanjian and Isaac, 2007; Shahzad and Isaac, 2009; Fotouh and Wolodko, 2011; de Vasconcellos et al., 2014; Fotouh et al., 2014; Shahzad and Isaac, 2014; Barbière et al., 2018), kenaf (Abdullah et al., 2012; Asumani and Paskaramoorthy, 2020), jute (Gassan and Bledzki, 2000; Alia et al., 2018; Bambach, 2020), sisal (Towo and Ansell, 2008a; Towo and Ansell, 2008b; Belaadi et al., 2013; Kanny and T.P., 2013), coir (Osti de Moraes et al., 2015), cotton (Petrucci et al., 2015), cactus fibers (Bouakba et al., 2013), Caryota urens fibers (Prakash et al., 2020), birch fibers (Mejri et al., 2018), oil palm fruit bunch fibers (Kalam et al., 2005), or regenerated cellulose fibers (Ranganathan et al., 2016; Müssig et al., 2020).
The fatigue strength at 106 cycles is often used as an endurance limit to design infinite fatigue life in the high cycle fatigue (HCF) range (Shah, 2014). However, very high cycle fatigue (VHCF) investigations of up to 108 cycles are also performed (Jeannin et al., 2019). The results from fatigue tests are usually processed in S-N (Wöhler) curves (fatigue strength as a function of the number of cycles). Cyclic loading can occur in tension–tension, tension–compression, compression–tension, and compression–compression (Burhan and Kim, 2018). In the field of natural fiber–reinforced plastics, most cyclic lifetime analyses are induced under tension–tension loading. Only a few describe the cyclic loading induced by compression (e.g., (Lemanski and Sutcliffe, 2010; Bambach, 2020)). An increasing stress ratio leads to flatter S-N curves, indicating that the fatigue life was improved, which is attributed to the reduction in stress amplitude leading to less damage to the structure (Feng et al., 2020). Loading frequencies of 5 and 30 Hz have not significantly influenced the S-N curves of flax/epoxy composites under high cycle loading (Jeannin et al., 2019).
The fatigue behavior of NFRP is dependent on internal (material) variables, such as the matrix, which may be brittle or ductile; the surface treatment of the fiber; fiber content; and the effect of physical/chemical modification of fiber and/or matrix and external variables, such as stress amplitude or stress intensity factor (Misra et al., 2011; Abdullah et al., 2012; Shah et al., 2013; Mahboob and Bougherara, 2018). As described for GFRP (Subramanian et al., 1995; Keusch et al., 1998; Towo and Ansell, 2008a), good fiber/matrix adhesion also leads to higher long-term durability in the case of cellulose fiber–reinforced composites (Gassan, 2002; Shahzad and Isaac, 2009; Liang et al., 2014; Shahzad et al., 2019; Asumani and Paskaramoorthy, 2020; Feng et al., 2020; Müssig et al., 2020). Besides the strength of the composite, fiber orientation significantly influences durability. Composites with higher static strength are generally more durable; the fatigue endurance strength of NFRP is proportional to their tensile strength (Gassan, 2002; Shah et al., 2013; Shah, 2014; Bensadoun et al., 2016). A deviation of the fiber orientation from the longitudinal axis leads to a lower fatigue strength (Bernasconi et al., 2007; Haggui et al., 2019; Feng et al., 2020). Usually, the best fatigue properties are achieved with unidirectional (UD) fiber orientation (Gassan, 2002; Feng et al., 2020). These composites are less sensitive to fatigue-induced damage than woven-reinforced composites (Gassan, 2002; Haggui et al., 2019). The constitution of the semifinished product also plays an important role. When using woven fabrics, the integration of the weft threads or the crimp of the threads significantly influences the fatigue damage and the critical collapse load of a composite (Lemanski and Sutcliffe, 2010; Feng et al., 2020). Minimized yarn crimp improves resistance to fatigue damage (Shah et al., 2013; Asgarinia et al., 2015; Bensadoun et al., 2015; Lessard et al., 2015; Bensadoun et al., 2016; Feng et al., 2020), whereas stiffness degradation is not clearly affected by the crimp (Haggui et al., 2019). The textile architecture and fiber content significantly influence the static composite properties, but they have little impact on the slope of the S–N curves (Shah et al., 2013). The S–N curves show no apparent differences between composites reinforced with woven fabrics and cross-ply laminates nor between the UD and quasi-UD reinforced composites (Bensadoun et al., 2016). Flax/epoxy composites show a larger energy dissipation in the early cycles as shown by the analysis of hysteresis loops in tension–tension (Bensadoun et al., 2015). Additionally, they offer delayed damage initiation and increased fatigue life with a reduced damage propagation rate combined with higher energy dissipation in the early stages of fatigue loading compared to glass fiber–reinforced composites (Bensadoun et al., 2016). It should be noted that a reinforcing effect with natural fibers is usually achieved up to approximately 40%–50% fiber volume fraction. Above this critical limit, mechanical performance starts to drop (Feng et al., 2020).
Different results are discussed in the literature when comparing the fatigue behavior of NFRP and GFRP. It should be considered that natural fibers have an irregular shape compared with glass fibers. Natural fibers refer to both fiber bundles consisting of single fiber cells and single fibers (single cells). In general, the smaller the fiber bundle, the better the mechanical properties. Accordingly, small fiber bundles have higher strength than coarse fiber bundles, whereby the single cells have the best characteristic values due to size effects, making a direct comparison of results difficult when natural fibers from different processing stages are used (Müssig et al., 2010). Some studies report comparable fatigue behavior of NFRP compared with GFRP (Yuanjian and Isaac, 2007; Bensadoun et al., 2016; Mahboob and Bougherara, 2018) or even better (Liang et al., 2012; Mahboob and Bougherara, 2018); other authors describe that the absolute fatigue performance of GFRP is far superior to NFRP. However, the fatigue strength degradation rates of NFRPs are lower, indicating a lower fatigue sensitivity (Shah et al., 2013; Shahzad and Isaac, 2014), which is evident by a steeper slope of the S-N curve of GFRP compared with NFRP (Abdullah et al., 2012; Liang et al., 2012; Shah et al., 2013; Shahzad and Isaac, 2014). The structure and composition of natural fibers usually lead to slower damage, fatigue strength, and stiffness degradation than for GFRP (Shahzad et al., 2019). Microscopic analyses show for NFRP that damage mechanisms appear with cracks first nucleating through the interface between the single fibers within the bundles, suggesting that the bonding agent pectin is the weakest component in the flax/epoxy composite (El Sawi et al., 2014); cracks then propagate through the fiber/matrix interphase to the matrix with an increasing number of fatigue cycles (Shahzad et al., 2019). In contrast, fatigue failure in UD-oriented GFRP is described as occurring throughout the material volume. Debonding of the fiber and matrix, fiber breakage, matrix cracking, delamination, and transverse ply cracking occur either interactively or independently. The difference in the structure and composition of natural fibers compared with glass fibers results in different behavior in fatigue loading of the composites. Fracture mechanisms and modes are the same for composites made from different bast fibers but depend on fiber content, textile architecture, and stress ratios (Shah et al., 2013).
Another unique feature of NFRP under cyclic load is the stiffening effect (Ueki et al., 2015; Feng et al., 2020), which could be related to the straightening of the microfibrils in the fiber cell wall (Liang et al., 2012; Liang et al., 2014). Stiffness change over the fatigue life in NFRP is lower than in GFRP and is shown to be complex (Shahzad and Isaac, 2014). Structural changes in the single fiber cell wall and damage development in the composite often have competing effects on the stress–strain curves. As a result, the design of components must be adapted due to the different stiffness evolution of NFRP compared with GFRP (Shah, 2016). It is shown that flax fiber–reinforced composites offer a more stable cyclic performance than GFRP (Liang et al., 2012). The stiffness degradation of flax and GFRP exhibit no dependence on the loading level (Liang et al., 2012). However, a linear relationship is found between the stiffening effect and the residual strain, and it is revealed that the frequency of cyclic loading influences the fatigue behavior. Lower frequencies lead to a higher stiffening effect and a shorter fatigue life, which means that fatigue damaging progresses simultaneously with the stiffening effect and is, therefore, essential to involve creep damaging to the failure criteria for these composites (Ueki et al., 2015). A further study investigates whether fatigue tests could also demonstrate this effect under strain control. All specimens show stiffness degradation, contradicting previous studies. The degradation is a function of applied load, leading to a proportional relationship between strain-rate and measured modulus. It is reported that the stiffening effect described in the literature does not reflect any physical improvement of material stiffness but is a consequence of stress-amplitude controlled loading conditions (Mahboob and Bougherara, 2020). For jute fiber–reinforced polypropylene, it is shown that a strong interface leads to a higher dynamic modulus and lower stiffness degradation with increasing load cycles and applied maximum stresses. However, the specific damping capacity results in higher values for the composites with weak fiber/matrix adhesion (Gassan and Bledzki, 2000). De Vasconcellos et al. identify three different zones in the hysteresis curves as a function of load cycles: 1) significant initial slope at the beginning of the curves, which is related to transverse matrix cracks through the thickness and initial fiber breakages; 2) almost constant slope, which is related to the period during which the matrix cracks may couple together and grow, especially along the interfaces; and 3) the slope gradually increases again just before failure, and fiber breaks initiated in phase 1) lead to strand breaks (de Vasconcellos et al., 2014).
Fiber-reinforced composites are used, e.g., in components subject to mechanical cyclic loads, such as in leaf springs (Rajesh et al., 2016); even NFRP were used for this product (Mouleeswaran, 2012; Kumar et al., 2018). Hybrid composites made of natural and glass fibers are also increasingly used for such applications (Graupner et al., 2021). The mechanical properties of hybrid composites depend on several factors, including fiber content and stacking configuration (Feng et al., 2020). Hybrid composites usually display higher mechanical properties than NFRP (Lessard et al., 2015; Sharba et al., 2015; Sharba et al., 2016; Feng et al., 2020) regardless of the type of hybrid composites (Feng et al., 2020). However, studies present better properties when the stronger and stiffer industrial made fibers enclose the less strong and stiff natural fibers in a thermosetting matrix (Asgarinia et al., 2015; Sivakumar et al., 2018). Nevertheless, the failure of the structure often starts in the interphase between GFRP and NFRP (Manteghi et al., 2019). Due to the lower sensitivity of natural fibers against fatigue load compared with glass fibers, the fatigue life performance is enhanced by hybridization (Feng et al., 2020). Hybrid jute and GFRP show that incorporating jute fiber within the hybrid composite reduced the fatigue sensitivity and stiffness degradation with increasing jute fiber content (Mostafa, 2019). In the case of flax/basalt hybrid composites, the normalized fatigue resistance was improved compared with the pure basalt composite due to the deflection of cracks by the presence of flax fibers. The mechanical properties of the hybrid material are in between those of NFRP and GFRP (Seghini et al., 2020).
A new type of staple fiber yarn with almost UD fiber orientation made of flax tow was developed for composite materials in a previous study. A unique feature of these yarns is that they are made from low-cost flax tow and provide reinforcement effects comparable to very high-quality and more expensive long flax rovings. The yarns were processed in quasi-UD fabrics, composite laminates from flax and glass, and a hybrid material for use in a demonstrator component (leaf spring or, more precisely, an axle tie of a narrow-gauge railway) was manufactured (Graupner et al., 2021). The shape of the axle tie was developed in a previous project for GFRP (Schönhuber et al., 2019). The practical suitability of this bogie made of GFRP has already been proven by numerical calculations of the strength and dynamic behavior. The fatigue strength is essential when investigating the use of flax fibers for the axle tie. Therefore, the fatigue properties of flax, glass, and hybrid flax/glass laminates were investigated in this study. To investigate the use in an axle tie, simulation calculations were carried out with regard to the load-bearing capacity and fatigue behavior. It is hypothesized that the hybrid materials of flax and glass have better static properties than the flax laminate and that the fatigue performance is better than that of a GFRP laminate.
2 Materials and Methods
2.1 Composite and Axle Tie Manufacture
Yarns, the quasi-UD fabrics and composites, were produced from field-retted flax from a longitudinal fiber line of scutched tow provided by SachsenLeinen GmbH (Markkleeberg, DE) as described in Graupner et al. (2021). Yarns were produced from the flax slivers at 30 m/min. The fibers in the yarns were wound with a polyamide polyfil (78 dtex, 20 individual continuous fibres). The following two yarns were processed into quasi-UD fabrics and composites (Graupner et al., 2021) and investigated within this study:
• Flax yarn V2, Aγ2, 213 tex, sliver (yarn V2).
• Flax yarn V9, Aγ9, 200 tex, restretched sliver (yarn V9).
Both yarns were manufactured from the same flax fiber bundles. Differences are that the sliver used to produce yarn V9 has been restretched to increase the uniformity of the yarn. As reference samples, a commercially available Lincore flax roving type FR 500 with a fineness of 500 tex and a density of 1.35 g/cm³ (Depestele, Bourguébus, FR) and a glass fiber roving type EC16 200 TD22C with zero-twist and a fineness of 200 tex (Saint-Gobain Vetrotex, Aachen, DE) were used. As a matrix, a bio-based epoxy resin PTP-L (polymer material made of triglycerides and polycarbon acid anhydrides; density 1.1 g/cm³) produced by company Biocomposites and More (B.A.M., Ipsheim, DE)1 was used for the production of composite laminates by a vacuum injection method in an autoclave from quasi-UD fabrics. The manufacturing process is described in Graupner et al. (2021). Five different composite laminates having a thickness of around 2 mm were produced in this manner from the quasi-UD fabrics (compare Graupner et al., 2021):
• Lincore flax: five layers
• Flax (yarn V2): five layers, fabric prepared from a flax yarn version 2 at the beginning of the project
• Flax (yarn V9): five layers, fabric prepared from a flax yarn version 9 at the end of the project
• Hybrid (flax yarn V9 and glass roving): 2 × 2 glass outer layers and 3 × flax inner layers
• Glass: nine layers
The manufactured demonstrator—an axle tie for a bogie of a narrow-gauge railway—shown in Figure 1 was produced at Novacom Verstärkte Kunststoffe GmbH (Aachen, Germany) using resin transfer molding (RTM) with an epoxy resin (type Epikote RIMR 135 with hardener Epikure RIMH 137, Momentive Specialty Chemicals B.V., Rotterdam, Netherlands; mixing ratio 100:30; density 1.15 g/cm³) from the fabrics. Twenty-one fabric layers were used for the axle tie made of glass fibers; 14 for the one made of flax and four outer layers of glass on each side in combination with nine inner layers of flax were used to manufacture the flax/glass hybrid component. The fabrics were placed in a sub-mold and coated with a release agent. The upper mold was placed on top, and both forms were braced together, and the resin was added under pressure. After curing, the axle tie was demolded.
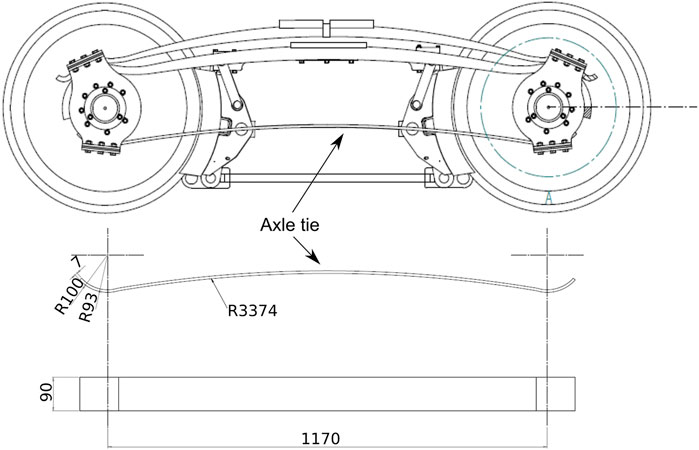
FIGURE 1. Axle tie for a narrow-gauge light railway bogie (dimensions in mm) (Graupner et al., 2021. changed).
2.2 Static Mechanical Properties
The composite laminates were tested after climatic conditioning according to the DIN EN ISO 291 standard (Deutsches Institut für Normung, 2005).
Bending tests of the composite laminates were carried out for eight specimens, each with a width of 15 mm and a length of 100 mm following the DIN EN ISO 14125 standard (Deutsches Institut für Normung, 2003). A universal testing machine (Zwick/Roell Z020, Zwick/Roell GmbH, Ulm, Germany) was operated at a span length of 45 mm and a test speed of 1 mm/min. The flexural modulus was determined between 0.05% and 0.25% flexural strain via linear regression (strain was calculated from the traverse path of the testing machine).
The interlaminar shear strength (ILSS) of the composite laminates was determined following standard 14130 (Deutsches Institut für Normung, 1998) on eight test specimens, each with a width of 10 mm and a length of 20 mm using the Zwick/Roell Z020 testing machine. The span length was set individually for each test series and resulted from five times the sample thickness at a test speed of 1 mm/min.
Tensile tests of composite laminates of eight specimens per test series with a width of 25 mm and a length of 250 mm according to DIN EN ISO 527-2 (Deutsches Institut für Normung, 1996) were carried out with the Zwick/Roell universal testing machine equipped with a 20 kN load cell and a Galdabini Quasar 250 universal testing machine (Galdabini (S.P.A.), Cardano Al Campo VA, IT, load cell 250 kN) with a test speed of 2 mm/min. The Young’s moduli of all composite laminates were determined using the Zwick/Roell universal testing machine. The elongation was recorded with a video extensometer (VideoXtens, Zwick/Roell GmbH, Ulm, DE) between 0.05% and 0.25% strain after reaching a preload of 50 N. The tensile tests of the flax-reinforced composites were performed with the Zwick/Roell universal testing machine at a testing speed of 2 mm/min until breakage. Due to the higher required forces, the GFRP and the hybrid materials were run to break on the Galdabini testing machine with the same testing speed of 2 mm/min.
2.3 Fatigue Strength
The fatigue strength of the composite laminates was characterized in Wöhler-type tensile fatigue experiments with a load ratio of
where
• Lincore
• Flax (yarn V2)
• Hybrid (flax yarn V9 and glass roving)
• Glass
2.4 Fatigue Analysis for an Axle Tie of a Light Railway Bogie
As a structural example to demonstrate the capabilities of the proposed flax fiber–reinforced and hybrid materials, the axle tie for a narrow-gauge light railway bogie, according to Figure 1, is considered. The same component was briefly presented in a previous paper (Graupner et al., 2021). The axle tie connects the lower ends of the bogie’s axle boxes. Under in-service conditions, the mass of the railcar body acts vertically on the top part of the bogie. The bending deformation of this part causes the axle bearings to rotate, resulting in a horizontal shift of their centers. The axle tie constrains the rotation and the lateral movement. It is deformed by bending with superimposed lateral stretching in the initial deformation range, resulting in limited reaction loads onto the axle boxes. After a complete stretching of the axle tie, a transition to a stretching dominated mode occurs, resulting in high reaction loads and, thus, high constraints to a further movement of the axle boxes.
In the sense of a case study, a fatigue analysis of the axle tie was performed, taking this component as a demonstrator. In a comparative analysis, the reference case of a GFRP for the axle tie was compared with two cases in which either a neat flax fiber–reinforced composite or a hybrid composite consisting of flax fiber-reinforced (inner layers) and glass fiber–reinforced plies (outer layers) were considered. The fatigue analysis of the component was carried out in the usual way using a linear elastic static analysis of the component, representing a single load cycle. Assuming that no substantial stiffness degradation of the material is induced during most of the fatigue life, this load cycle represents all load cycles at the considered load level. An assessment of the fatigue life can then be performed based on the local stresses at all spatial positions representing the stress range
It should be noted that this type of analysis is limited to cases in which linear elasticity without substantial material nonlinearities due to flow and degradation provides a reasonable assumption for the material response. Nevertheless, due to the relatively low load levels in the HCF range, this is usually the case for FRP components under HCF loading scenarios. Therefore, the assumption of linear elasticity does not constitute any substantial limitation here.
For the analysis, the axle tie was meshed with standard four-node displacement-based finite shell elements with a size of 10 mm × 10 mm. The axle boxes were modeled as rigid bodies clamped to the axle tie in the center of the screwed connection they have with the axle tie in reality. The top ends of the rigid bodies representing the axle boxes were assumed to be pivoted in the range of their connection with the bogie frame. To keep the simulation effort within reasonable limits, the lateral movement of the axle box tops due to the bending deformation of the bogie frame was assumed to be of minor importance and, thus, was neglected. The finite element model was loaded by a prescribed rotation
• Glass fiber–reinforcement (reference case): 21 plies with 0.3 mm thickness each.
• Flax fiber–reinforcement: 14 plies with 0.5 mm thickness each.
• Hybrid-reinforcement: four glass-reinforced plies with 0.3 mm thickness at top and bottom and nine flax fiber–reinforced plies with 0.5 mm thickness in the center.
The material was modeled using the orthotropic formulation of Hooke’s law with the material properties determined in the experimental investigation. All finite element analyses were performed within the geometrically nonlinear framework to account for the equilibrium in the deformed configuration.
As mentioned above, a fatigue strength evaluation of the static analysis was performed to compare the three axle-tie material options. Assuming a harmonic fatigue load with a load ratio of
3 Results and Discussion
3.1 Static Mechanical Properties
The fabrics made from yarns and rovings were processed by autoclave injection to test composite laminate processability and mechanical properties (details can be found in Graupner et al. (2021)). The influence of the development of semifinished products and fiber properties on the composite characteristics is also described in (Graupner et al. 2021). Hybrid materials made from flax and glass fabrics were produced to use the composite materials in an axle tie of a narrow-gauge railway bogie to combine the positive properties of both fiber types (resistance against environmental influences of glass and good damping properties of flax). Lincore flax and a glass fabric were processed into composite laminates for comparison. The fiber volume fractions were calculated as 48% for the Lincore laminate, 53% for the flax laminate (yarn V2), 51% for the flax laminate (yarn V9), 43% for the glass laminate, and 47% for the hybrid composite laminate (Graupner et al., 2021).
Results of the unnotched Charpy impact strength are shown in Figure 4. It becomes apparent that the glass and hybrid laminate have significantly higher impact strength values than the flax-based laminates. Furthermore, it is evident that a more advanced structure of the semifinished product positively affects the impact strength. The laminate made of yarn V9 has a higher impact strength than the laminate of yarn V2. The yarn V9 fabric laminate (42 kJ/m2) is comparable to the laminates made from the Lincore fabric (39 kJ/m2). The impact strength of the hybrid composite is much closer to the GFRP values than to the flax fiber–reinforced composite.
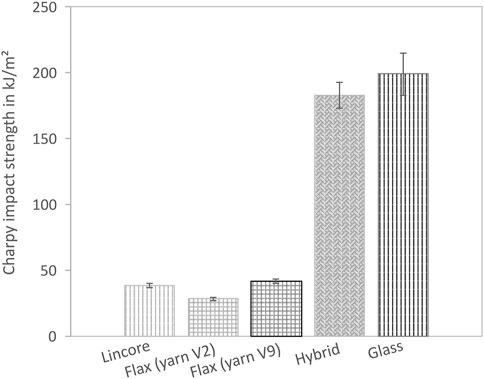
FIGURE 4. Unnotched Charpy impact strength of composite laminates (mean value ± standard deviation).
The results of the flexural tests are shown in Figure 5. By improving the yarn structure from yarn V2 to yarn V9 (restretching the flax sliver), the flexural properties were enhanced, but the reinforcing effect of the Lincore fabric was not achieved. The hybrid materials show significantly better flexural properties than the flax laminates. In particular, the flexural modulus was highly increased and closer to the values of the GFRP than to the flax fiber–reinforced composite.
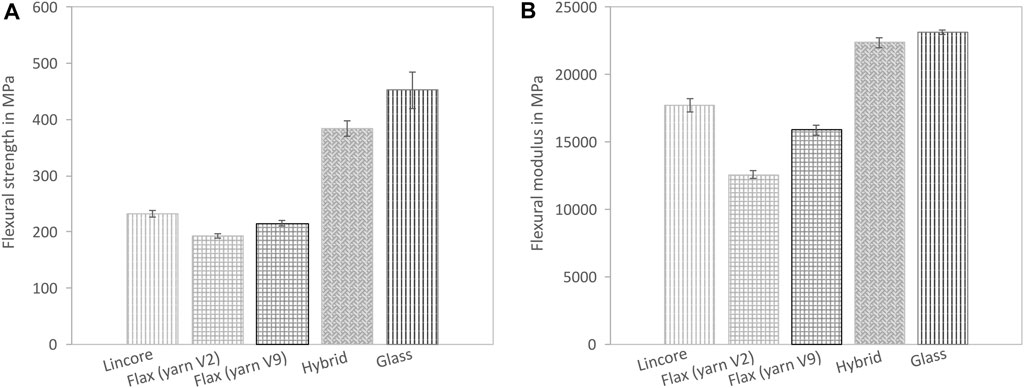
FIGURE 5. Flexural strength (A) and flexural modulus (B) of composite laminates (mean value ± standard deviation).
Fiber/matrix adhesion was characterized by short beam shear tests to determine the apparent interlaminar shear strength (ILSS). The performance trend is similar to the flexural properties; the difference is that the ILSS of the glass and the hybrid laminate do not deviate as much from the flax-based materials (Figure 6).
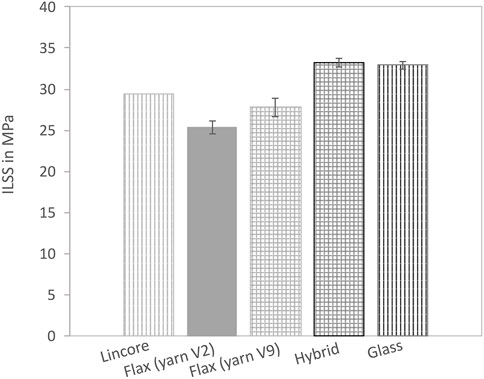
FIGURE 6. Interlaminar shear strength (ILSS) of composite laminates (mean value ± standard deviation).
Again, improved fiber/matrix adhesion was observed from flax laminate (yarn V2) to flax laminate (yarn V9), which can be attributed to the more uniform yarn properties due to the restretching of the sliver. Restretching resulted in a reduction of fiber ondulation and better fibre orientation in the yarn.
The tensile properties are summarized in Figure 7. By improving yarn V2 to yarn V9, tensile strength (Figure 7A) and tensile modulus (Figure 7B) were significantly increased; however, the values of the Lincore laminate were not reached. The GFRP laminate displays the highest characteristic values, followed by the hybrid material; compared with the flexural properties, the tensile properties of the hybrid material are significantly lower than those of the GFRP laminate.
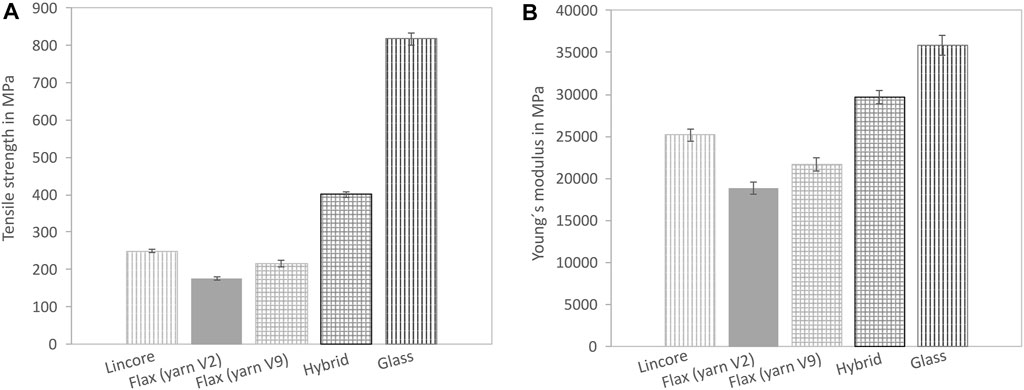
FIGURE 7. Tensile strength (A) and Young’s modulus (B) of composite laminates (mean value ± standard deviation).
The optimization of the yarns by restretching the sliver can be summarized as follows: Concerning the impact strength (Figure 4), flexural properties (Figure 5), tensile characteristics (Figure 7), and even the interlaminar shear strength (Figure 6), it is shown that the optimization of the yarn structure from V2 to V9 led to a significant increase in the mechanical properties of the laminates. Our previous study shows that the fiber properties (tensile characteristics and length of the fibre bundles) did not show any significant differences. The increase in the characteristic values can be solely attributed to the yarn and fabric structure as the composite production and the fiber volume fraction were identical. It was found that fiber ondulation was present in yarn V2, which was almost eliminated in yarn V9 by restretching the sliver. Even with this optimization, it was impossible to achieve the composites’ property profile from the Lincore roving completely.
Previous work shows that flax yarn V9 achieves the same reinforcing effects as Lincore roving in UD-reinforced pultruded rods (Graupner et al., 2021). To understand why, despite the same reinforcement potential between Lincore roving and yarn V9, the properties in the fabric-based composites differ, further analyses were carried out. The fabrics based on yarn V9 showed some crimp and, thus, a deviation of the fiber orientation from the longitudinal axis. In contrast, no crimp was visible in the Lincore fabrics, which justifies a better reinforcement effect in the fabric-reinforced laminates. It is well-known that a deviation of fiber orientation from the load direction leads to a considerable reduction of strength and stiffness in the composite (Goutianos et al., 2006; Baets et al., 2014; Scida et al., 2017). It is expected that by eliminating the crimp in future research, the reinforcement effect can be significantly increased.
The hybrid materials show significantly improved flexural and impact properties compared with the flax laminates and significantly better density-related properties, especially in terms of flexural stiffness, in comparison to the GFRP (Graupner et al., 2021). Several authors describe comparable results (Calabrese et al., 2019; Fiore et al., 2018; Jusoh et al., 2017; Selver et al., 2018; Cerbu and Botis, 2016). The presence of external layers of glass fabric in a hybrid glass/flax/epoxy laminate positively influences the mechanical performance. In our study, the flexural modulus was clearly increased, and the values were closer to the GFRP than to the flax fiber–reinforced composite (Figure 5B). This trend is more pronounced for the flexural modulus than for the tensile modulus (Figure 7B), which the loading direction may explain: The outer glass layers in the hybrid material are mainly loaded on the compression and tension side. Under tensile load, the entire cross-section of the specimen is loaded, which is also described in the work of Selver et al. (2018) for flax/glass hybrid composites. Selver et al. found that a changing stacking sequence did not significantly affect the tensile strength and Young’s modulus of composites. Nevertheless, they realized notable differences in flexural strength of composites when the outer layers contained glass fibers. The flexural modulus of the hybrid composite was even comparable to that of the pure GFRP. When using flax as outer layers and glass as inner layers, flexural modulus and strength were considerably lower (Selver et al., 2018).
Since the determination of the modulus takes place in the linear-elastic initial slope at relatively low forces, it is assumed that the influence of the outer glass layers is more substantial under bending load. An increasing number of outer glass layers in a hybrid material with flax increases strength and modulus (Saidane et al., 2016).
To sum up, the hybridization of flax and glass was successful in our work. For most mechanical properties, the characteristic values are close to those of the GFRP, especially under bending and impact stress. Both properties are essential for an axle tie element. Besides improving mechanical properties, water absorption or swelling of the flax laminate are hindered by the outer glass layers (Calabrese et al., 2019). In addition, the presence of flax is shown to improve the damping of the hybrid material compared with a pure GFRP (Selver et al., 2018; Liu et al., 2021). The authors determined the damping by dynamic mechanical analysis and found that NFRPs and some hybrid composites had higher damping characteristics than GFRPs, whereas the described effect seems to apply independently of the material pairing. Studies on hybrid materials made of stiffer bast fibers and more ductile regenerated cellulose fibers show that the tensile properties do not change significantly due to the layer arrangement. The toughness of the composites could only be increased when the stiffer bast fibers are used as outer layers and the tougher regenerated cellulose fibers as inner layers. A reversed layer structure led to a reduction in toughness, showing that using stiffer outer layers can significantly improve the mechanical performance of the composite (Graupner et al., 2017a; Graupner et al., 2017b).
3.2 Fatigue Strength of Composite Laminates
The results of the fatigue experiments for the four materials considered here are presented in Figure 8 in a double logarithmic representation. Symbols mark the individual experimental results. The static strength results, converted to nominal cyclic stress range
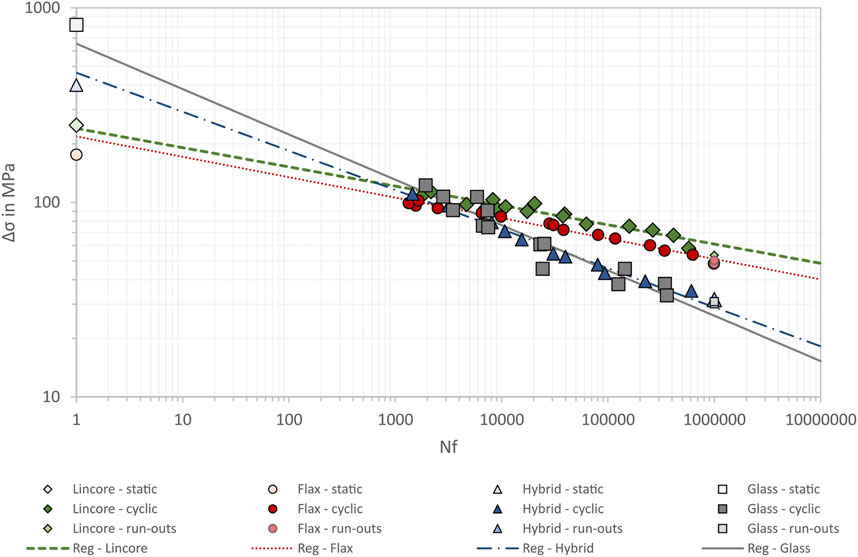
FIGURE 8. Results from the fatigue tests for the glass fiber–reinforced composite, the hybrid composite made of flax and glass (2 × 2 outer glass layers + 3 flax layers in the core) and the composite made of the Lincore flax roving and the flax staple fiber yarn V2.
At higher cycle numbers, i.e., above 7³ to 8³ load cycles, the fatigue strength of the composite laminates made of flax is higher than that of the GFRP (Figure 8). On the one hand, this finding of higher fatigue strength of flax than glass is particularly important for the use of cyclically loaded components. On the other hand, the flax fiber–reinforced materials are outperformed by their GFRP and hybrid counterparts in the low cycle fatigue and static ranges. Although quantitatively less distinct, similar effects are observed compared with the GFRP and hybrid composites. The hybrid materials tend to show higher fatigue strength than the GFRP from about 2 × 105 load cycles.
Figure 8 shows a steeper slope of the S–N curve of GFRP compared to the NFRP, which is also reported by different authors (Liang et al., 2012; Shah et al., 2013; Abdullah et al., 2012; Shahzad and Isaac, 2014). The results of the fatigue tests show a lower decrease in strength at a higher number of load cycles for the flax laminates compared with the glass laminate and the hybrid material (Figure 8). In general, the lower slopes of the flax fiber–reinforced composites indicate that flax as the main load-carrying constituent is less sensitive to fatigue than glass fibers. From the literature, it is known that bast fiber–reinforced composites tend to have lower fatigue sensitivity and lower stiffness degradation with an increasing number of loading cycles and a higher resistance to crack propagation in fatigue tests compared with GFRP (Abdullah et al., 2012; Liang et al., 2012; Shah et al., 2013; Shahzad and Isaac, 2014). Flax fiber–reinforced composites offer a more stable cyclic performance than GFRP (Liang et al., 2012). Qualitatively similar results are obtained from the fatigue tests from the present study.
As already shown in the static mechanical properties, the laminate made of Lincore flax also displays better fatigue properties compared with the laminates made of flax yarn. For the interpretation, it should be taken into account that the laminates made from flax yarn V2 also had lower static mechanical properties than laminates made from yarn V9. When comparing the Lincore roving with the yarn results, it is important to remember that the flax yarn laminate exhibits some crimp in the fabric (Graupner et al., 2021), which negatively affects the fatigue properties. These hypotheses can be confirmed with a literature comparison: (Bernasconi et al., 2007; Shah et al., 2013; Asgarinia et al., 2015; Bensadoun et al., 2015; Lessard et al., 2015; Bensadoun et al., 2016; Haggui et al., 2019; Feng et al., 2020). Unidirectional fiber orientation leads to the best properties (Gassan, 2002; Feng et al., 2020), and it is shown that minimized crimp in the yarns significantly increases the resistance to fatigue damage (Shah et al., 2013; Asgarinia et al., 2015; Bensadoun et al., 2015; Lessard et al., 2015; Bensadoun et al., 2016; Feng et al., 2020). Furthermore, the critical collapse load of the composite is strongly dependent upon the magnitude of the waviness of a fabric (Lemanski and Sutcliffe, 2010; Feng et al., 2020).
Figure 9A shows a comparison of flax-reinforced composites made from different semifinished products and with different orientations; data of this study are compared with data from the literature. The ultimate tensile strength (UTS) of different materials is plotted as a function of loading cycles. The UD-reinforced materials display the highest absolute fatigue strength values. The properties of the composites reinforced with quasi-UD fabrics from the present study are slightly lower. Composites with 0/90° or ± 45° still show low results, and the lowest values are for composites with a fiber orientation of 90°. In Figure 9B, the fatigue strength is related to the static strength in percent, and no clear trends depend on the fiber orientation. This trend is also justified in the literature because the textile architecture significantly influences the static properties but only slightly changes the slope of the S–N curves (Shah et al., 2013; Bensadoun et al., 2016).
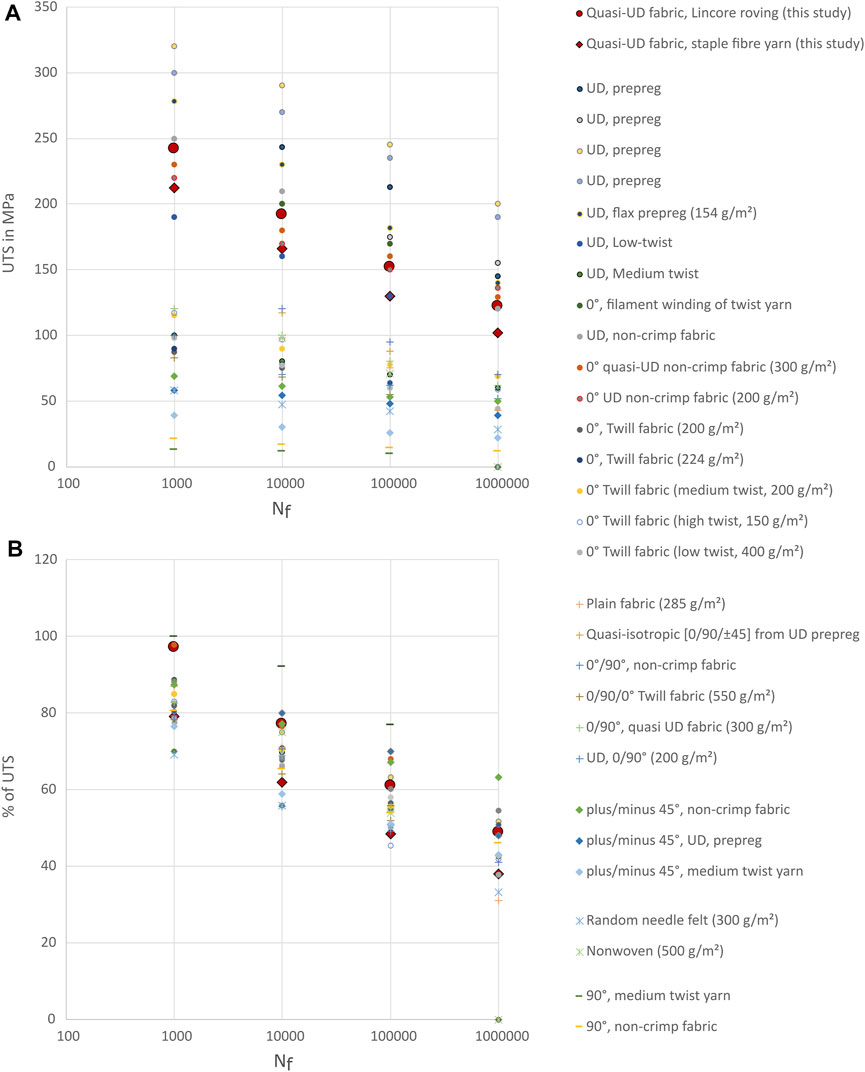
FIGURE 9. A comparison of flax composites with different fiber orientations from the literature (red circles and diamonds are the results of our test series); (A) the absolute strength is shown; (B) the relative strength in relation to the static strength is presented. The absolute values show a considerable difference between UD and differently oriented fibers. The data were summarized from (Liang et al., 2012; Shah et al., 2013; El Sawi et al., 2014; Liang et al., 2014; Asgarinia et al., 2015; Ueki et al., 2015; Bensadoun, 2016; Bensadoun et al., 2016; Berges et al., 2016; Sodoke et al., 2016; Habibi et al., 2019; Jeannin et al., 2019; Ameur et al., 2020; Hallak Panzera et al., 2020) in a revised form.
There is further potential to improve the fatigue behavior of laminates made of flax yarn V2. Due to the improved mechanical characteristics and the higher fiber orientation of the laminates produced from yarn V9, it is expected that the fatigue strength can also be further increased since higher static strength usually leads to higher resistance to fatigue loads (Gassan, 2002; Shah et al., 2013; Shah, 2014; Bensadoun et al., 2016). Additionally, improvement in fiber/matrix adhesion can be used to increase fatigue strength (Gassan, 2002; Shahzad and Isaac, 2009; Liang et al., 2014; Shahzad et al., 2019; Asumani and Paskaramoorthy, 2020; Feng et al., 2020; Müssig et al., 2020). As Figure 6 shows, the interlaminar shear strength of the flax yarn V9 laminate is higher than that of the flax yarn V2 laminate. Taking into account these considerations, it is reasonable to expect that using the V9 yarn increases fatigue strength.
The S–N curves between the GFRP laminate and the hybrid material show no significant differences (Figure 8). However, the hybrid material tends to reach higher fatigue strength with more load cycles; the slope of the regression line is lower. For the interpretation, it is essential to consider that the hybrid material consisted of four layers of glass and three layers of flax. In contrast to the static properties, the fatigue behavior is not increased by a higher number of glass layers. It is hypothesized that the fatigue strength can be further improved by using more layers of flax or by reducing the number of glass by two layers. The hybrid material investigated contains approx. 27 vol% flax and 21 vol% glass (Graupner et al., 2021).
A comparison of the results at different numbers of loading cycles of flax/glass hybrid materials and GFRP with data from the literature is shown in Figure 10A; an influence of the fiber orientation is less evident than for the flax laminates shown in Figure 9A (when comparing, the different amount of data must be taken into account). The data from the present study show that at a lower number of cycles, the GFRP has higher strength, whereas the hybrid material achieves a higher strength at a higher number of cycles. Other hybrid materials from literature show significantly lower values at a lower number of cycles but converge at a higher number of cycles. Hybrid materials tend to offer the highest values in the relative representation (fatigue strength related to static strength) (Figure 10B). For GFRPs, no clear trend can be identified depending on the fiber orientation. From the literature, it can be generally concluded that plant fibers can improve the damping behavior of composite materials. Ashby plots can be created in which different fatigue properties are plotted to select appropriate fibers, making it possible to find the compromise between loss factor and stiffness for engineering design considerations (Liu et al., 2021).
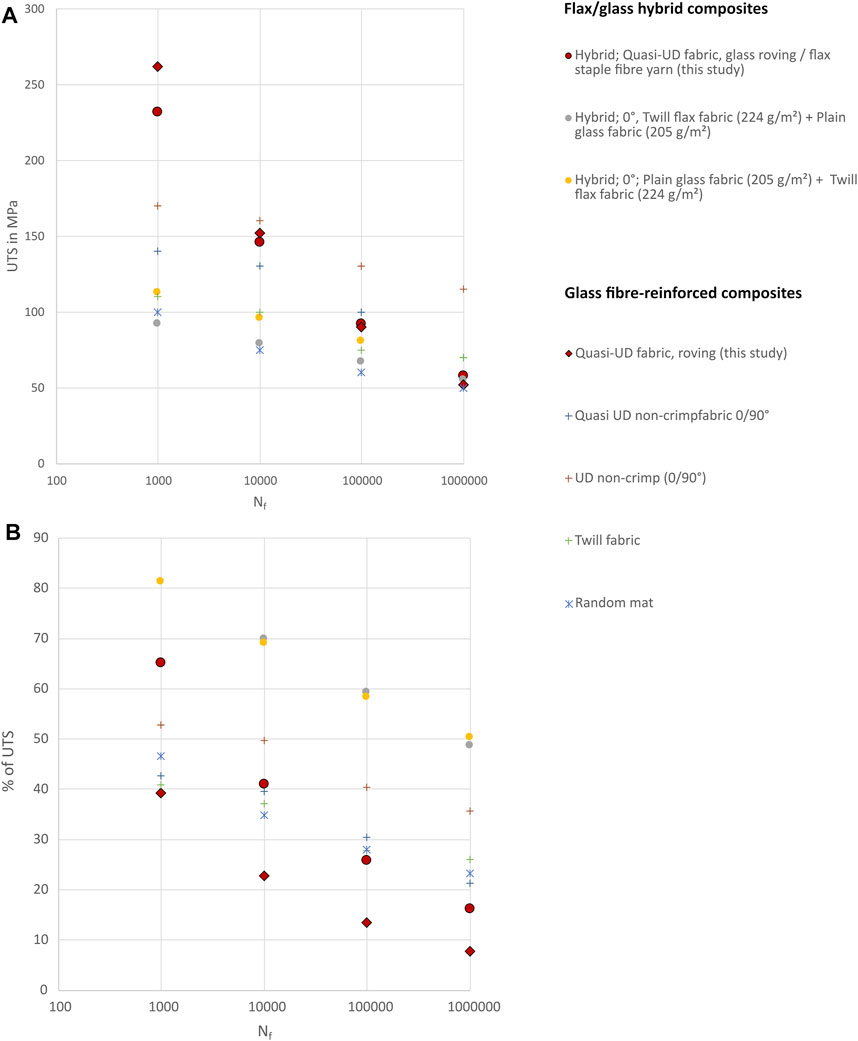
FIGURE 10. Comparison of hybrid (flax/glass) and glass in the literature (red circles and diamonds are the results of our test series); (A) the absolute strength is presented; (B) the percentage strength in relation to the static strength is shown. In the percentage representation, our hybrid shows clear advantages compared with GFRP. The data were summarized in revised form from (Liang et al., 2012; Asgarinia et al., 2015; Bensadoun, 2016).
3.3 Fatigue Analysis for an Axle Tie of a Light Railway Bogie
The demonstrator components produced in the RTM process are presented in Figure 11; Figure 11A shows an axle tie made from quasi-UD flax (top) and glass fabric (bottom). Figures 11B,C represent detailed views from the top and bottom. The cross-section of the axle tie is shown in part (Figure 11D), on which the warp threads (white) are visible. The composite manufacturing of the flax and the flax/glass hybrid material was straightforward compared with the GFRP processing.
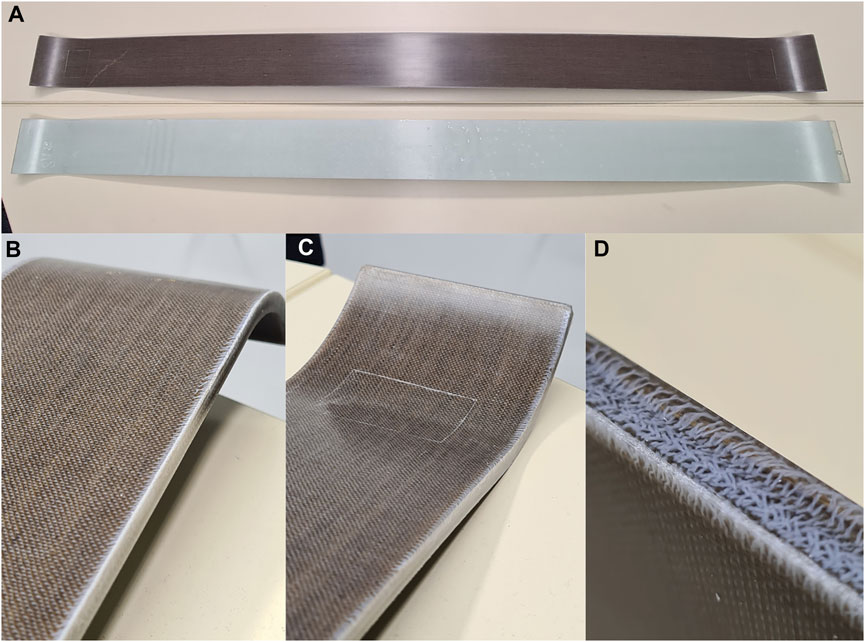
FIGURE 11. The lower axle tie of the bogie of a narrow-gauge railway, manufactured using the RTM process. (A) Flax/epoxy axle tie (top) compared with the conventional glass fiber–reinforced axle tie (bottom), (B,C) detailed views of the curved ends of the axle tie, (D) detailed view on the side of the axle tie (component thickness: 70 mm, length approx. 1.2 m).
Theoretical component
The distributions of the levels of the longitudinal normal stress
For similar levels
The resulting component related
In the initial part of the low-cycle fatigue range below approximately
The
3.4 Assessment of the Different Material Options in Numerical and Experimental Studies
In general, composites having higher static strength are more durable, and the fatigue endurance strength of NFRPs is proportional to their tensile strength (Gassan, 2002; Shah et al., 2013; Shah, 2014; Bensadoun et al., 2016). The results of the fatigue tests and the simulation show that flax fiber–reinforced composites display superior characteristics to the GFRP beyond a specific number of load cycles despite their lower static strength as reported in the literature (Gassan and Bledzki, 1999; Liang et al., 2012; Rahman et al., 2016; Mahboob and Bougherara, 2018; Dhanraj et al., 2019; Liu et al., 2021; Rahman, 2021). The low cycle fatigue strength of flax composites is slightly lower than that of GFRP but still in the same order of magnitude. In this sense, the results of the fatigue experiments on GFRP and flax-reinforced specimens are in line with the simulation data of the axle tie although the loading of the component in the case study was different from the neat tension–tension fatigue on specimen level (see Sections 2.3 and 2.4). As described for the fatigue tests of the laminates, the axle tie made of GFRP exhibits significantly higher strengths than the axle tie with flax fiber-reinforcement at a lower number of load cycles (Nf < 500) in the LCF range (Figure 8). This effect might be caused by the different load types and higher bending deformation of the (woven) flax fibers under tension with a lower sensitivity to fatigue under bending than glass fibers.
In the literature, it is reported that the fatigue strength degradation rates of NFRP are lower, indicating a lower fatigue sensitivity (Shah et al., 2013; Shahzad and Isaac, 2014). Other authors carried out microscopic analyses and show that fatigue cracks are nucleated at the interfaces between the single fibers and the matrix within fiber bundles. The assumption is made that the pectin bonding agent, in the middle lamella of the fiber bundle, is the weakest component in the flax/epoxy composite (El Sawi et al., 2014) and the crack further propagates through the fiber/matrix interphase to the matrix with an increasing number of fatigue cycles (Shahzad et al., 2019). In contrast, fatigue failure in UD GFRP is described to occur throughout the material volume. Debonding between fiber and matrix, fiber breakage, matrix cracking, delamination, and transverse ply cracking occur either interactively or independently. In general, matrix cracking and delamination start early, whereas fiber/matrix debonding and fiber fracture begin during the component life but accumulates rapidly toward the end, leading to the final failure (Subramanian et al., 1995). However, it should be noted that the damage mechanism of crack propagation through the different plies has not been considered in the numerical case study where, in the sense of the weakest link model, failure was assumed once the first material point is predicted to experience failure.
In the fatigue tests, the hybrid material only shows a higher fatigue strength at a high number of load cycles (∼2 × 105) compared with the case of the GFRP material. The hybrid material’s S-N curve was closer to the GFRP laminate than the flax fiber–reinforced laminate curve. In the simulation, the curve of the hybrid material was between the curve of the glass fiber–reinforced axle tie and that of the flax fiber–reinforced axle tie (Figure 14). As discussed in Section 3.2, the hybrid laminate with a thickness of approximately 2 mm consists of a total of four layers of glass fiber reinforcement and three layers of flax fiber reinforcement. On the other hand, the demonstrator consists of eight layers of glass and nine layers of flax fiber reinforcement, respectively, which means that the volume proportion of flax fiber reinforcement in the axle tie is higher than for the laminate resulting in better damping of the hybrid material.
Particularly under bending stress, the outer glass fiber–reinforced layers are subjected to tensile stress and, thus, carry a large portion of the load, which is also shown by the results of the impact and bending tests. On the one hand, the characteristic values of the hybrid material are closer to the values of the GFRP laminate (Figures 4, 5). On the other hand, the specimen’s cross-section is loaded more uniformly under tensile load. Thus, the glass and flax fibers are loaded simultaneously. The characteristic values range between those of flax fiber–reinforced and GFRP laminates (Figure 7). In addition to the higher proportion of flax fiber reinforcement in the demonstrator compared with the laminate, the type of loading used in the simulation can lead to the hybrid material having a significant advantage over the GFRP material in terms of fatigue resistance. Compared to the literature, a hybrid composite made of flax and carbon fibres resulted in improved fatigue performance and fatigue resistance with an increasing carbon fibre content. But the damping ratio and the fatigue life increase with a higher flax fiber volume fraction [103]. This finding makes the use of hybrid materials with flax particularly interesting for the application of a cyclically loaded axle tie in a bogie, also because of the improved lightweight construction potential compared to GFRP.
4 Conclusion
The results presented show that flax is very well-suited as a reinforcing fiber for components under cyclic loads. It is particularly noteworthy that the flax composites have a significantly higher fatigue strength than GFRP at a higher number of loading cycles. These properties are often only achieved with very high-quality semifinished flax products. The present study shows that low-cost flax tow could be processed into low-twist yarns and fabrics with little ondulation and, in the composite, has comparable properties to composites made from higher quality and more expensive long flax rovings. Due to the lower strength of flax fiber-reinforced composites compared with GFRP, a hybridization is a suitable option for the considered application. Glass fibers in the outer part of the axle tie protect the inner flax fibers from moisture and lead to increased strength and stiffness of the entire component. The hypothesis stated at the beginning that hybridization of flax and glass fibers could achieve improved static properties compared with flax fiber–reinforced composites and improved fatigue properties at a higher number of load cycles than GFRP cannot be rejected. The present study demonstrates that the developed material is suitable for an axle tie. Therefore, the optimal ratio of glass to flax fibers for the mentioned component should be determined to achieve the best fatigue properties and lightweight potential in future work. It would also be fascinating to see the axle tie tested in a practical application.
Data Availability Statement
The original contributions presented in the study are included in the article. Further inquiries can be directed to the corresponding authors.
Author Contributions
Conceptualization: NG, JH, JM. Experimental studies: NG, MS, BR, DW, LB. Methodology: NG, JH, AB, JM. Project administration: NG, JM, JH. Validation: NG, JH, MS, BR. Writing–original draft: NG, JH, JM. Writing–review and editing: NG, JH, MS, BR, DW, JM.
Funding
The research project, Innovative yarn structures and their competitiveness as part of the project fibre-reinforced composites for structural applications based on novel, low-twist bast fibre yarns (NF-CompPlus), was carried out in the framework of the industrial collective research programme. This work was supported by the Federal Ministry of Food and Agriculture (BMEL) on the basis of a resolution of the German Bundestag (funding No. 22026215, 22014817 and 22015417). The funder was not involved in the study design, collection, analysis, interpretation of data, the writing of this article or the decision to submit it for publication. The fee for open-access publication is covered by the Bremen State and University Library.
Conflict of Interest
The company Novacom Verstärkte Kunststoffe GmbH received proportionate funding in the form of subcontracts from the Federal Ministry of Food and Agriculture (BMEL) and is represented by the authors LB and AB. Novacom Verstärkte Kunststoffe GmbH was responsible for the production of the axle tie and received proportionate funding in the form of a subcontract from the Federal Ministry of Food and Agriculture (BMEL). The remaining funding was provided by the companies in the form of machine and labour hours.
The remaining authors declare that the research was conducted in the absence of any commercial or financial relationships that could be construed as a potential conflict of interest.
Publisher’s Note
All claims expressed in this article are solely those of the authors and do not necessarily represent those of their affiliated organizations or those of the publisher, the editors and the reviewers. Any product that may be evaluated in this article, or claim that may be made by its manufacturer, is not guaranteed or endorsed by the publisher.
Acknowledgments
The research project, Innovative yarn structures and their competitiveness as part of the project fibre-reinforced composites for structural applications based on novel, low-twist bast fibre yarns (NF-CompPlus), was carried out in the framework of the industrial collective research programme. The authors would also like to thank the project partners, without whom the NF-CompPlus project could not have been implemented: Institut für Textiltechnik of RWTH Aachen University (Dr.-Ing. Karl-Heinz Lehmann, Erik Bell, Herbert Randerath), Wenzel and Hoos GmbH (Hans-Willi Hilgers, Stefan Kunst), INVENT GmbH (Isabell Walenta, Marc Joulian, Maik Wonneberger), SachsenLeinen GmbH (Torsten Brückner, Kay Kölzig) and BAFA neu GmbH (Bernd Frank).
Footnotes
1In memory and honour of Uwe Schönfeld, the PTP resin developer, who passed away much too early.
References
Abdullah, A. H., Alias, S. K., Jenal, N., Abdan, K., and Ali, A. (2012). Fatigue Behavior of Kenaf Fibre Reinforced Epoxy Composites. Ej 16 (5), 105–114. doi:10.4186/ej.2012.16.5.105
Alia, A., Fantozzi, G., Godin, N., Osmani, H., and Reynaud, P. (2018). “Mechanical Behaviour of Jute Fibre-Reinforcedpolyester Composite: Characterization of Damagemechanisms Using Acoustic Emission.” in Proceedings of the ECCM18 – 18th European Conference on Composite Material, Athens, Greece, June 2018 (Patras, Greece: ESCM – European Society for Composite Materials and University of Patras).
Alkbir, M. F. M., Sapuan, S. M., Nuraini, A. A., and Ishak, M. R. (2016). Fibre Properties and Crashworthiness Parameters of Natural Fibre-Reinforced Composite Structure: A Literature Review. Compos. Structures 148, 59–73. doi:10.1016/j.compstruct.2016.01.098
Ameur, M. B., El Mahi, A., Rebiere, J.-L., Beyaoui, M., Abdennadher, M., and Haddar, M. (2020). Experimental Fatigue Behavior of Carbon/flax Hybrid Composites under Tensile Loading. J. Compos. Mater. 55, 0021998320954903. doi:10.1177/0021998320954903
Asgarinia, S., Viriyasuthee, C., Phillips, S., Dubé, M., Baets, J., Van Vuure, A., et al. (2015). Tension-tension Fatigue Behaviour of Woven Flax/epoxy Composites. J. Reinforced Plastics Composites 34 (11), 857–867. doi:10.1177/0731684415581527
Asumani, O., and Paskaramoorthy, R. (2020). Fatigue and Impact Strengths of Kenaf Fibre Reinforced Polypropylene Composites: Effects of Fibre Treatments. Adv. Compos. Mater. 30 (0), 1–13. doi:10.1080/09243046.2020.1733308
Baets, J., Plastria, D., Ivens, J., and Verpoest, I. (2014). Determination of the Optimal Flax Fibre Preparation for Use in Unidirectional Flax-Epoxy Composites. J. Reinforced Plastics Composites 33 (5), 493–502. doi:10.1177/0731684413518620
Baley, C., Gomina, M., Breard, J., Bourmaud, A., and Davies, P. (2020). Variability of Mechanical Properties of Flax Fibres for Composite Reinforcement. A Review. Ind. Crops Prod. 145, 111984. doi:10.1016/j.indcrop.2019.111984
Bambach, M. R. (2020). Durability of Natural Fibre Epoxy Composite Structural Columns: High Cycle Compression Fatigue and Moisture Ingress. Composites C: Open Access 2, 100013. doi:10.1016/j.jcomc.2020.100013
Barbière, R., Touchard, F., and Chocinski-Arnault, L. (2018). “Fatigue Behaviour in Different Moisture Conditions Ofa Woven Hemp Fibre Reinforced Epoxy Composite,” in Proceedings of the ICCM18 – 18th European Conference on Composite Material, Athens, Greece, June 2018 (Patras, Greece: ESCM – European Society for Composite Materials and University of Patras).
Belaadi, A., Bezazi, A., Bourchak, M., and Scarpa, F. (2013). Tensile Static and Fatigue Behaviour of Sisal Fibres. Mater. Des. 46, 76–83. doi:10.1016/j.matdes.2012.09.048
Bensadoun, F. (2016). “In-service Behaviour of Flax Fibre Reinforced Composites for High Performance Applications,” (Leuven, Belgium: KU Leuven). PhD thesis.
Bensadoun, F., Vallons, K. A. M., Lessard, L. B., Verpoest, I., and Van Vuure, A. W. (2015). “Residual Properties and Damage Evolution of Flax-Epoxy Composites Subjected to Fatigue Loading.” in Proceedings of the ICCM20 – 20th International Conference on Composite Materials, Bella Center, Copenhagen, Denmark, July 2015. Editor O. T. Thomsen, Vol. 20. Aalborg University, Department of Mechanical and Manufacturing Engineering (Conference Chair).
Bensadoun, F., Vallons, K. A. M., Lessard, L. B., Verpoest, I., and Van Vuure, A. W. (2016). Fatigue Behaviour Assessment of Flax-Epoxy Composites. Composites A: Appl. Sci. Manufacturing 82, 253–266. doi:10.1016/j.compositesa.2015.11.003
Berges, M., Léger, R., Placet, V., Person, V., Corn, S., Gabrion, X., et al. (2016). Influence of Moisture Uptake on the Static, Cyclic and Dynamic Behaviour of Unidirectional Flax Fibre-Reinforced Epoxy Laminates. Composites Part A: Appl. Sci. Manufacturing 88, 165–177. doi:10.1016/j.compositesa.2016.05.029
Bernasconi, A., Davoli, P., Basile, A., and Filippi, A. (2007). Effect of Fibre Orientation on the Fatigue Behaviour of a Short Glass Fibre Reinforced Polyamide-6. Int. J. Fatigue 29 (2), 199–208. doi:10.1016/j.ijfatigue.2006.04.001
Bledzki, A. K., and Gassan, J. (1998). Dissipated Energy of Composite Materials - Part I: Cyclic Dynamic Stress. J. Test. Eval. 26 (5), 467–471.
Bouakba, M., Bezazi, A., Boba, K., Scarpa, F., and Bellamy, S. (2013). Cactus Fibre/polyester Biocomposites: Manufacturing, Quasi-Static Mechanical and Fatigue Characterisation. Composites Sci. Technol. 74, 150–159. doi:10.1016/j.compscitech.2012.10.009
Burhan, I., and Kim, H. S. (2018). S-N Curve Models for Composite Materials Characterisation: An Evaluative Review. J. Composites Sci. 2 (3), 38. doi:10.3390/jcs2030038
Calabrese, L., Fiore, V., Scalici, T., and Valenza, A. (2019). Experimental Assessment of the Improved Properties during Aging of Flax/glass Hybrid Composite Laminates for marine Applications. J. Appl. Polym. Sci. 136 (14), 47203. doi:10.1002/app.47203
Cerbu, C., and Botis, M. (2016). “Numerical Modeling of the Flax /Glass /Epoxy Hybrid Composite Materials in Bending.” in Proceedings of the 2017 10th International Conference Interdisciplinarity in Engineering, INTER-ENG 2016, Tirgu Mures, Romania, October 2016. 181, 3086–3157.
de Vasconcellos, D. S., Touchard, F., and Chocinski-Arnault, L. (2014). Tension-tension Fatigue Behaviour of Woven Hemp Fibre Reinforced Epoxy Composite: A Multi-Instrumented Damage Analysis. Int. J. Fatigue 59, 159–169. doi:10.1016/j.ijfatigue.2013.08.029
Deimann, F. Personal Communication with Mr. Friedrich Deimann about Prices for Biaxial Flax Fabrics from 13.11.2020. Bremen, 2020.
Deutsches Institut für Normung (1998). DIN EN 14130:1998 – Verstärkte Kunststoffverbundwerkstoffe – Bestimmung der scheinbaren interlaminaren Scherfestigkeit nach dem Dreipunktverfahren mit kurzem Balken, 2003. German version. Geneva, Switzerland: ISO.
Deutsches Institut für Normung, (2003). DIN EN ISO 14125:2003 – Faserverstärkte Kunststoffe - Bestimmung der Biegeeigenschaften, 2003. German version. Geneva, Switzerland: ISO.
Deutsches Institut für Normung, (2005). DIN EN ISO 291:2005 – Kunststoffe - Normalklimate für Konditionierung und Prüfung, 2006. Plastics–Standard atmospheres for conditioning and testing. German version. Geneva, Switzerland: ISO.
Deutsches Institut für Normung, (1996). DIN EN ISO 527-2:1996 – Kunststoffe: Bestimmung der Zugeigenschaften; Teil 2 Prüfbedingungen für Form- und Extrusionsmassen, 1996. Plastics–Determination of tensile properties – Part 2: Test conditions for moulding and extrusion plastics. German version. Geneva, Switzerland: ISO.
Dhanraj, J. A., Kumar, D. G. S., Sivakumar, S., and Vishnuvardhan, R. (2019). Experimental Investigation on Mechanical Properties and Vibration Damping Frequency Factor of Kenaf Fiber Reinforced Epoxy Composite. SAE Tech. Pap. 10, 6. doi:10.4271/2019-28-0167
Dunne, R., Desai, D., Sadiku, R., and Jayaramudu, J. (2016). A Review of Natural Fibres, Their Sustainability and Automotive Applications. J. Reinforced Plastics Composites 35 (13), 1041–1050. doi:10.1177/0731684416633898
El Sawi, I., Fawaz, Z., Zitoune, R., and Bougherara, H. (2014). An Investigation of the Damage Mechanisms and Fatigue Life Diagrams of Flax Fiber-Reinforced Polymer Laminates. J. Mater. Sci. 49 (5), 2338–2346. doi:10.1007/s10853-013-7934-0
Feng, N. L., Malingam, S. D., Jenal, R., Mustafa, Z., and Subramonian, S. (2020). A Review of the Tensile and Fatigue Responses of Cellulosic Fibre-Reinforced Polymer Composites. Mech. Adv. Mater. Structures 27 (8), 645–660. doi:10.1080/15376494.2018.1489086
Fiore, V., Calabrese, L., Scalici, T., Bruzzaniti, P., and Valenza, A. (2018). Bearing Strength and Failure Behavior of Pinned Hybrid Glass-Flax Composite Laminates. Polym. Test. 69, 310–319. doi:10.1016/j.polymertesting.2018.04.041
Fotouh, A., Wolodko, J. D., and Lipsett, M. G. (2014). Fatigue of Natural Fiber Thermoplastic Composites. Composites B: Eng. 62, 175–182. doi:10.1016/j.compositesb.2014.02.023
Fotouh, A., and Wolodko, J. (2011). “Fatigue Behavior of Natural Fiber Reinforced Thermoplastic Composites in Dry and Wet Environments,” in Proceedings of the ASME 2011 International Mechanical Engineering Congress and Exposition, Denver, Colorado, November 2011. doi:10.1115/imece2011-64552
Gassan, J. (2002). A Study of Fibre and Interface Parameters Affecting the Fatigue Behaviour of Natural Fibre Composites. Composites Part A: Appl. Sci. Manufacturing 33 (3), 369–374. doi:10.1016/s1359-835x(01)00116-6
Gassan, J., and Bledzki, A. K. (1999). Possibilities for Improving the Mechanical Properties of Jute/epoxy Composites by Alkali Treatment of Fibres. Composites Sci. Technol. 59 (9), 1303–1309. doi:10.1016/s0266-3538(98)00169-9
Gassan, J., and Bledzki, A. K. (2000). Possibilities to Improve the Properties of Natural Fiber Reinforced Plastics by Fiber Modification – Jute Polypropylene Composites –. Appl. Compos. Mater. 7, 373–385.
Goutianos, S., Peijs, T., Nystrom, B., and Skrifvars, M. (2006). Development of Flax Fibre Based Textile Reinforcements for Composite Applications. Appl. Compos. Mater. 13 (4), 199–215. doi:10.1007/s10443-006-9010-2
Graupner, N., Labonte, D., Humburg, H., Buzkan, T., Dörgens, A., Kelterer, W., et al. (2017). Functional Gradients in the Pericarp of the green Coconut Inspire Asymmetric Fibre-Composites with Improved Impact Strength, and Preserved Flexural and Tensile Properties. Bioinspir Biomim 12, 026009. doi:10.1088/1748-3190/aa5262
Graupner, N., Labonte, D., and Müssig, J. (2017). Rhubarb Petioles Inspire Biodegradable Cellulose Fibre-Reinforced Pla Composites with Increased Impact Strength. Composites Part A: Appl. Sci. Manufacturing 98, 218–226. doi:10.1016/j.compositesa.2017.03.021
Graupner, N., Lehmann, K.-H., Weber, D. E., Hilgers, H.-W., Bell, E. G., Walenta, I., et al. (2021). Novel Low-Twist Bast Fibre Yarns from Flax Tow for High-Performance Composite Applications. Materials 14 (1), 105.
Habibi, M., Laperrière, L., and Hassanabadi, H. M. (2019). Effect of Moisture Absorption and Temperature on Quasi-Static and Fatigue Behavior of Nonwoven Flax Epoxy Composite. Composites Part B: Eng. 166, 31–40. doi:10.1016/j.compositesb.2018.11.131
Haggui, M., El Mahi, A., Jendli, Z., Akrout, A., and Haddar, M. (2019). Static and Fatigue Characterization of Flax Fiber Reinforced Thermoplastic Composites by Acoustic Emission. Appl. Acoust. 147, 100–110. doi:10.1016/j.apacoust.2018.03.011
Hallak Panzera, T., Jeannin, T., Gabrion, X., Placet, V., Remillat, C., Farrow, I., et al. (2020). Static, Fatigue and Impact Behaviour of an Autoclaved Flax Fibre Reinforced Composite for Aerospace Engineering. Composites Part B: Eng. 197, 108049. doi:10.1016/j.compositesb.2020.108049
Islam, M. Z., and Ulven, C. A. (2020). A Thermographic and Energy Based Approach to Define High Cycle Fatigue Strength of Flax Fiber Reinforced Thermoset Composites. Composites Sci. Technol. 196, 108233. doi:10.1016/j.compscitech.2020.108233
Jauhari, N., Mishra, R., and Thakur, H. (2015). Natural Fibre Reinforced Composite Laminates - a Review. Mater. Today Proc. 2 (4), 2868–2877. doi:10.1016/j.matpr.2015.07.304
Jeannin, T., Gabrion, X., Ramasso, E., and Placet, V. (2019). About the Fatigue Endurance of Unidirectional Flax-Epoxy Composite Laminates. Composites Part B: Eng. 165, 690–701. doi:10.1016/j.compositesb.2019.02.009
Jusoh, M. S. M., Santulli, C., Yahya, M. Y., Hussein, N. S., and Ahmad, H. (2017). Effect of Stacking Sequence on the Tensile and Flexural Properties of Glass Fibre Epoxy Composites Hybridized with basalt, Flax or Jute Fibres. Mater. Sci. Eng. Adv. Res. 1 (4), 19–25. doi:10.24218/msear.2015.19
Kalam, A., Sahari, B. B., Khalid, Y. A., and Wong, S. V. (2005). Fatigue Behaviour of Oil palm Fruit bunch Fibre/epoxy and Carbon Fibre/epoxy Composites. Compos. Structures 71 (1), 34–44. doi:10.1016/j.compstruct.2004.09.034
Kanny, K., and T.P., M. (2013). Surface Treatment of Sisal Fiber Composites for Improved Moisture and Fatigue Properties. Compos. Inter. 20 (9), 783–797. doi:10.1080/15685543.2013.819699
Karus, M., and Kaup, M. (2002). Natural Fibres in the European Automotive Industry. J. Ind. Hemp 7, 119–131. 13 Seiten, 4 Tabellen, 8 Quellen. doi:10.1300/j237v07n01_10
Keusch, S., Queck, H., and Gliesche, K. (1998). Influence of Glass Fibre/epoxy Resin Interface on Static Mechanical Properties of Unidirectional Composites and on Fatigue Performance of Cross Ply Composites. Composites: A: Appl. Sci. Manufacturing 29 (5-6), 701–705. doi:10.1016/s1359-835x(97)00106-1
Kumar, S. V., Rajagopal, A., and Madhappan, R. (2018). Study of Static and Fatigue Analysis of Flax/epoxy -leaf spring. IOP Conf. Ser. Mater. Sci. Eng. 8 (7), 1441–1448. doi:10.1088/1757-899X/388/1/012018
Lemanski, S. L., and Sutcliffe, M. P. F. (2010). “Effect of Waviness Defects on Plastic Microbuckling of Unidirectional Composites,” in Proceedings of the ECCM, 14. European Conference on Composite Materials, Budapest, ECCM14, Budapest, June 2010, 1–10.
Lessard, L., Asgarinia, S., Viriyasuthee, C., Phillips, S., Dubé, M., Baets, J., et al. (2015). “Fatigue Behaviour of Woven Flax/epoxy Composites,” in , Proceedings of the ICCM20 – 20th International Conference on Composite Materials, Bella Center, Copenhagen, Denmark, June 2015. Editor O. T. Thomsen, Vol. 20. Aalborg University, Department of Mechanical and Manufacturing Engineering (Conference Chair).
Li, Q., Li, Y., Ma, H., Cai, S., and Huang, X. (2020). Effect of Processing Temperature on the Static and Dynamic Mechanical Properties and Failure Mechanisms of Flax Fiber Reinforced Composites. Composites Commun. 20, 100343. doi:10.1016/j.coco.2020.04.009
Liang, S., Gning, P.-B., and Guillaumat, L. (2014). Properties Evolution of Flax/epoxy Composites under Fatigue Loading. Int. J. Fatigue 63, 36–45. doi:10.1016/j.ijfatigue.2014.01.003
Liang, S., Gning, P. B., and Guillaumat, L. (2012). A Comparative Study of Fatigue Behaviour of Flax/epoxy and Glass/epoxy Composites. Composites Sci. Technol. 72 (5), 535–543. doi:10.1016/j.compscitech.2012.01.011
Liber-Kneć, A., Kuźniar, P., and Kuciel, S. (2015). Accelerated Fatigue Testing of Biodegradable Composites with Flax Fibers. J. Polym. Environ. 23 (3), 400–406. doi:10.1007/s10924-015-0719-6
Liu, T., Butaud, P., Placet, V., and Ouisse, M. (2021). Damping Behavior of Plant Fiber Composites: A Review. Compos. Structures 275, 114392. doi:10.1016/j.compstruct.2021.114392
Mahboob, Z., and Bougherara, H. (2018). Fatigue of Flax-Epoxy and Other Plant Fibre Composites: Critical Review and Analysis. Composites Part A: Appl. Sci. Manufacturing 109 (March), 440–462. doi:10.1016/j.compositesa.2018.03.034
Mahboob, Z., and Bougherara, H. (2020). Strain Amplitude Controlled Fatigue of Flax-Epoxy Laminates. Composites Part B: Eng. 186, 107769. doi:10.1016/j.compositesb.2020.107769
Malloum, A., Mahi, A. E., and Idriss, M. (2019). The Effects of Water Ageing on the Tensile Static and Fatigue Behaviors of Greenpoxy-Flax Fiber Composites. J. Compos. Mater. 53 (21), 2927–2939. doi:10.1177/0021998319835596
Manteghi, S., Sarwar, A., Fawaz, Z., Zdero, R., and Bougherara, H. (2019). Mechanical Characterization of the Static and Fatigue Compressive Properties of a New Glass/flax/epoxy Composite Material Using Digital Image Correlation, Thermographic Stress Analysis, and Conventional Mechanical Testing. Mater. Sci. Eng. C 99, 940–950. doi:10.1016/j.msec.2019.02.041
Mejri, M., Toubal, L., Cuillière, J. C., and François, V. (2018). Hygrothermal Aging Effects on Mechanical and Fatigue Behaviors of a Short- Natural-Fiber-Reinforced Composite. Int. J. Fatigue 108, 96–108. doi:10.1016/j.ijfatigue.2017.11.004
Misra, M., Ahankari, S. S., and Mohanty, A. K. (2011). “Creep and Fatigue of Natural Fibre Composites,” in Interface Engineering of Natural Fibre Composites for Maximum Performance, Chapter 11, Woodhead Publishing Series in Composites Science and Engineering. Editor N. E. Zafeiropoulos (Sawston, United Kingdom: Woodhead Publishing), 289–340. doi:10.1533/9780857092281.2.289
More, A. P. (2021). Flax Fiber-Based Polymer Composites: a Review. Adv. Composites Hybrid Mater. 5, 1–20. doi:10.1007/s42114-021-00246-9
Mostafa, N. H. (2019). Tensile and Fatigue Properties of Jute-Glass Hybrid Fibre Reinforced Epoxy Composites. Mater. Res. Express 6 (8), 085102. doi:10.1088/2053-1591/ab21f9
Mouleeswaran, S. (2012). Materials Science and Technology, Chapter 4-Design, Manufacturing and Testing of Polymer Composite - A Review. Lomdon, UK: InTech, 59–73. doi:10.5772/32778
Müssig, J., Fischer, H., Graupner, N., and Drieling, A. (2010). Testing Methods for Measuring Physical and Mechanical Fibre Properties (Plant and Animal Fibres). chapter 13. 1. edition. Chichster, UK: John Wiley & Sons, 269–311.
Müssig, J., Kelch, M., Gebert, B., Hohe, J., Luke, M., and Bahners, T. (2020). Improvement of the Fatigue Behaviour of Cellulose/polyolefin Composites Using Photo-Chemical Fibre Surface Modification Bio-Inspired by Natural Role Models. Cellulose 27 (10), 5815–5827. doi:10.1007/s10570-020-03170-1
Nagabhooshanam, N., Baskar, S., and Nagarajan, P. K. K. (2018). Sathish Kumar. Design and Fabrication of Fatigue Test Rig and Preliminary Investigation on Flax Composite Beam. Mater. Today Proc. 5 (5, Part 2), 11771–11779. doi:10.1016/j.matpr.2018.02.146
Osti de Moraes, D. V., Magnabosco, R., Bolognesi Donato, G. H., Prado Bettini, S. H., and Antunes, M. C. (2015). Influence of Loading Frequency on the Fatigue Behaviour of Coir Fibre Reinforced Pp Composite. Polym. Test. 41, 184–190. doi:10.1016/j.polymertesting.2014.12.002
Parikh, D. V., Calamari, T. A., Sawhney, A. P. S., Blanchard, E. J., Screen, F. J., Myatt, J. C., et al. (2002). Thermoformable Automotive Composites Containing Kenaf and Other Cellulosic Fibers. Textile Res. J. 72 (8), 668–672. doi:10.1177/004051750207200803
Petrucci, R., Nisini, E., Puglia, D., Sarasini, F., Rallini, M., Santulli, C., et al. (2015). Tensile and Fatigue Characterisation of Textile Cotton Waste/polypropylene Laminates. Composites Part B: Eng. 81, 84–90. doi:10.1016/j.compositesb.2015.07.005
Prakash, V. R. A., Xavier, J. F., Ramesh, G., Maridurai, T., Kumar, K. S., and Raj, R. B. S. (2020). Mechanical, thermal and Fatigue Behaviour of Surface-Treated Novel Caryota Urens Fibre-Reinforced Epoxy Composite. Biomass Convers. Biorefinery. doi:10.1007/s13399-020-00938-0
Puck, A., and Schürmann, H. (2002). Failure Analysis of Frp Laminates by Means of Physically Based Phenomenological Models. Composites Sci. Technol. 62 (12), 1633–1662. doi:10.1016/s0266-3538(01)00208-1
Rahman, M. Z., Mace, B., and Jayaraman, K. (2016). “Vibration Damping of Natural Fibre-Reinforced Composite Materials,” in Proceedings of the ECCM17 - 17th European Conference on Composite Materials, Munich, Germany, June 2016.
Rahman, M. Z. (2021). Mechanical and Damping Performances of Flax Fibre Composites - a Review. Composites Part C: Open Access 4, 100081. doi:10.1016/j.jcomc.2020.100081
Rajesh, S., Bhaskar, G. B., Venkatachalam, J., Pazhanivel, K., and Sagadevan, S. (2016). Performance of Leaf Springs Made of Composite Material Subjected to Low Frequency Impact Loading. J. Mech. Sci. Technol. 30 (9), 4291–4298. doi:10.1007/s12206-016-0842-x
Ranganathan, N., Oksman, K., Nayak, S. K., and Sain, M. (2016). Structure Property Relation of Hybrid Biocomposites Based on Jute, Viscose and Polypropylene: The Effect of the Fibre Content and the Length on the Fracture Toughness and the Fatigue Properties. Composites Part A: Appl. Sci. Manufacturing 83, 169–175. doi:10.1016/j.compositesa.2015.10.037
Saidane, E. H., Scida, D., Assarar, M., Sabhi, H., and Ayad, R. (2016). Hybridisation Effect on Diffusion Kinetic and Tensile Mechanical Behaviour of Epoxy Based Flax-Glass Composites. Composites Part A: Appl. Sci. Manufacturing 87, 153–160. doi:10.1016/j.compositesa.2016.04.023
Schönhuber, P., Lekue, J., Bruns, A., and Schindler, C. (2019) Numerische untersuchung eines innovativen drehgestellrahmens aus glasfaserverbundwerkstoff für schmalspurbahnen.” in Proceedings of the 2nd International Railway Symposium Aachen 2019, Aachen, Germany, December 2019, 563–574.
Scida, D., Bourmaud, A., and Baley, C. (2017). Influence of the Scattering of Flax Fibres Properties on Flax/epoxy Woven Ply Stiffness. Mater. Des. 122, 136–145. doi:10.1016/j.matdes.2017.02.094
Seghini, M. C., Touchard, F., Sarasini, F., Chocinski–Arnault, L., Ricciardi, M. R., Antonucci, V., et al. (2020). Fatigue Behaviour of flax-basalt/epoxy Hybrid Composites in Comparison with Non-hybrid Composites. Int. J. Fatigue 139, 105800. doi:10.1016/j.ijfatigue.2020.105800
Selver, E., Ucar, N., and Gulmez, T. (2018). Effect of Stacking Sequence on Tensile, Flexural and Thermomechanical Properties of Hybrid Flax/glass and Jute/glass Thermoset Composites. J. Ind. Textiles 48 (2), 494–520. doi:10.1177/1528083717736102
Shah, D. U. (2016). Damage in Biocomposites: Stiffness Evolution of Aligned Plant Fibre Composites during Monotonic and Cyclic Fatigue Loading. Composites Part A: Appl. Sci. Manufacturing 83, 160–168. Special Issue on Biocomposites. doi:10.1016/j.compositesa.2015.09.008
Shah, D. U. (2014). Natural Fibre Composites: Comprehensive ashby-type Materials Selection Charts. Mater. Des. (1980-2015) 62 (0), 21–31. doi:10.1016/j.matdes.2014.05.002
Shah, D. U., Schubel, P. J., Clifford, M. J., and Licence, P. (2013). Fatigue Life Evaluation of Aligned Plant Fibre Composites through S-N Curves and Constant-Life Diagrams. Composites Sci. Technol. 74, 139–149. doi:10.1016/j.compscitech.2012.10.015
Shahzad, A. (2019). “Investigation into Fatigue Strength of Natural/synthetic Fiber-Based Composite Materials,” in Mechanical and Physical Testing of Biocomposites, Fibre-Reinforced Composites and Hybrid Composites, Chapter 12, Woodhead Publishing Series in Composites Science and Engineering. Editors M. Jawaid, M. Thariq, and N. Saba (Sawston, United Kingdom: Woodhead Publishing), 215–239. doi:10.1016/b978-0-08-102292-4.00012-6
Shahzad, A., and Isaac, D. H. (2014). Fatigue Properties of Hemp and Glass Fiber Composites. Polym. Compos. 35 (10), 1926–1934. doi:10.1002/pc.22851
Shahzad, A., and Isaac, D. H. (2009). “Fatigue Properties of Hemp Fibre Composites,” in Proceedings of the 17th International Conference on Composite Materials, Edinburgh, UK, July 2009.
Sharba, M., Leman, Z., Sultan, M., Ishak, M., and Hanim, M. (2016). Partial Replacement of Glass Fiber by Woven Kenaf in Hybrid Composites and its Effect on Monotonic and Fatigue Properties. Bioresources 11, 2665–2683. doi:10.15376/biores.11.1.2665-2683
Sharba, M., Leman, Z., Sultan, M., Ishak, M. R., and Azmah Hanim, M. A. (2015). Effects of Kenaf Fiber Orientation on Mechanical Properties and Fatigue Life of Glass/kenaf Hybrid Composites. BioResources 11 (1), 1448–1465. doi:10.15376/biores.11.1.1448-1465
Sivakumar, D., Ng, L. F., Lau, S. M., and Lim, K. T. (2018). Fatigue Life Behaviour of Glass/kenaf Woven-Ply Polymer Hybrid Biocomposites. J. Polym. Environ. 26 (2), 499–507. doi:10.1007/s10924-017-0970-0
Sodoke, F. K., Toubal, L., and Laperrière, L. (2016). Hygrothermal Effects on Fatigue Behavior of Quasi-Isotropic Flax/epoxy Composites Using Principal Component Analysis. J. Mater. Sci. 51 (24), 10793–10805. doi:10.1007/s10853-016-0291-z
Staiger, M. P., and Tucker, N. (2008). “Natural-fibre Composites in Structural Applications,” in Properties and Performance of Natural-Fibre Composites, Chapter 8, Woodhead Publishing Series in Composites Science and Engineering. Editor K. L. Pickering (Sawston, United Kingdom: Woodhead Publishing), 269–300.
Subramanian, S., Reifsnider, K. L., and Stinchcomb, W. W. (1995). A Cumulative Damage Model to Predict the Fatigue Life of Composite Laminates Including the Effect of a Fibre-Matrix Interphase. Int. J. Fatigue 17 (5), 343–351. doi:10.1016/0142-1123(95)99735-s
Szebényi, G., Blößl, Y. G., HegedüsTábi, G., Tábi, T., Czigany, T., and Schledjewski, R. (2020). Fatigue Monitoring of Flax Fibre Reinforced Epoxy Composites Using Integrated Fibre-Optical Fbg Sensors. Composites Sci. Technol. 199, 108317. doi:10.1016/j.compscitech.2020.108317
Towo, A. N., and Ansell, M. P. (2008). Fatigue Evaluation and Dynamic Mechanical thermal Analysis of Sisal Fibre-Thermosetting Resin Composites. Composites Sci. Technol. 68 (3), 925–932. doi:10.1016/j.compscitech.2007.08.022
Towo, A. N., and Ansell, M. P. (2008). Fatigue of Sisal Fibre Reinforced Composites: Constant-Life Diagrams and Hysteresis Loop Capture. Composites Sci. Technol. 68, 915–924. doi:10.1016/j.compscitech.2007.08.021
Ueki, Y., Lilholt, H., and Madsen, B. (2015). “Fatigue Behaviour of Uni-Directional Flax Fibre/epoxy Composites,” in Proceedings of the 20th International Conference on Composite Materials, Copenhagen, Denmark, 19-24th July 2015.
Keywords: hybrid composite, flax, staple fibre yarn, axle tie, fatigue, finite element method, simulation
Citation: Graupner N, Hohe J, Schober M, Rohrmüller B, Weber D, Bruns L, Bruns A and Müssig J (2022) A Competitive Study of the Static and Fatigue Performance of Flax, Glass, and Flax/Glass Hybrid Composites on the Structural Example of a Light Railway Axle Tie. Front. Mater. 9:837289. doi: 10.3389/fmats.2022.837289
Received: 16 December 2021; Accepted: 15 February 2022;
Published: 13 April 2022.
Edited by:
Nicholas Fantuzzi, University of Bologna, ItalyReviewed by:
Alexandre Vivet, Université de Caen Normandie, FranceShun-Peng Zhu, University of Electronic Science and Technology of China, China
Copyright © 2022 Graupner, Hohe, Schober, Rohrmüller, Weber, Bruns, Bruns and Müssig. This is an open-access article distributed under the terms of the Creative Commons Attribution License (CC BY). The use, distribution or reproduction in other forums is permitted, provided the original author(s) and the copyright owner(s) are credited and that the original publication in this journal is cited, in accordance with accepted academic practice. No use, distribution or reproduction is permitted which does not comply with these terms.
*Correspondence: Nina Graupner, bmluYS5ncmF1cG5lckBocy1icmVtZW4uZGU=; Jörg Hohe, am9lcmcuaG9oZUBpd20uZnJhdW5ob2Zlci5kZQ==