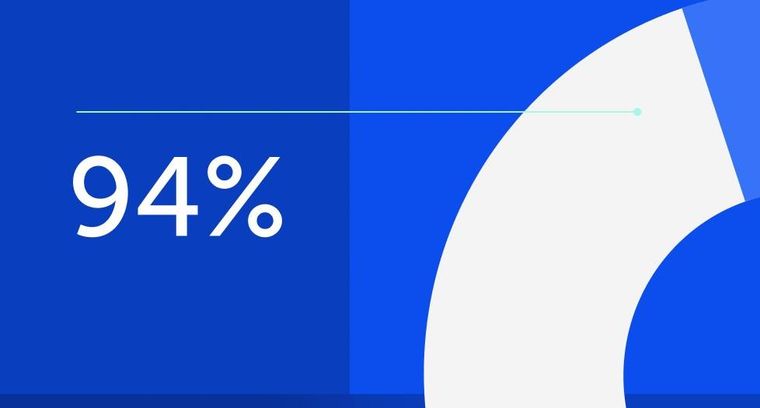
94% of researchers rate our articles as excellent or good
Learn more about the work of our research integrity team to safeguard the quality of each article we publish.
Find out more
REVIEW article
Front. Mater., 21 March 2022
Sec. Polymeric and Composite Materials
Volume 9 - 2022 | https://doi.org/10.3389/fmats.2022.805131
This article is part of the Research TopicHorizons in MaterialsView all 10 articles
During last decades a plethora of high temperature materials have been developed to work as a Thermal Protection System (TPS). Carbon based materials such as graphite, which possesses low density, high heat capacity and high energy of vaporization, have been used as TPS material. However, graphite has relatively poor mechanical properties, but exhibits low resistance to the thermal shocks. Accordingly, to bypass the limitation of graphite, carbon fibers are typically introduced in a carbon matrix to produce Carbon/Carbon Composites (CCCs). Among the different families of TPS solutions, Polymeric Ablative Materials (PAMs), produced combining high char yield matrices - mainly phenolic resins - and Carbon Fibers (CFs) are used to manufacture Carbon/Phenolic Composites (CPCs) i.e. the most important class of fiber reinforced PAM. Carbon fibers are traditionally produced from Polyacrylonitrile (PAN), Rayon and Pitch. Some limited researches also aimed to use cyanate-esters, bismaleimides, benzoxazines matrices in combination with ex-PAN-CFs, ex-Rayon-CFs, and ex-Pitch-CFs. In our paper, after covering the science and technology of these state-of-the-art fiber reinforced TPS materials, a review of current challenges behind the manufacturing of new, high char yield matrices and carbon fibers derived from alternative precursors will be provided to the reader. In particular, the possibility to produce CFs from precursors different from PAN, Rayon and Pitch will be reported and similarly, the technology of non-oil based phenolics, bismaleimides, cyanate-esters and benzoxazines will be discussed. The effect of the use of nanosized fillers on these matrices will also be reported. More in detail, after a preliminary section in which the state of the art of technologies behind carbon/phenolic composites will be covered, a second part of this review paper will be focused on the most recent development related to non-oil based phenolics and biomass derived carbon fibers. Finally, an outlook focused on the maturity of the lab-scale protocols behind the researches at the base of these non-traditional raw materials from an industrial point of view will conclude this review paper.
During last decades, a plethora of high temperature and Thermal Protection System (TPS) materials have been developed and optimized for different applications. TPS materials are used to manufacture propulsion systems, such as liquid rocket engines, Solid Rocket Motors (SRMs) and, more recently, Hybrid Rocket Motors (HRMs) (Sutton and Biblarz, 2000). They are also used to manufacture the heat shields which protect probes and vehicles during the hypersonic flight through an atmosphere (D’Aelio GF, 1971). In addition to Refractory Metals (RMs) and Ultra High Temperature Ceramics (UHTCs), carbon based materials such as graphite, which possesses high heat capacity and high energy of vaporization, have been widely used as TPS material. However, even though graphite has a substantially lower density than RMs and UHTCs, it has the drawback to possess relatively poor mechanical properties and to exhibit problems in terms of resistance to thermal shocks. Accordingly, carbon fibers are typically introduced in a carbon matrix to produce Carbon/Carbon Composites (CCCs) (Fitzer and Manocha, 1998). These materials are used in the throat region of SRMs which is exposed to the harshest conditions generated by modern aluminized propellants and where the heat flux easily exceeds ∼1,000 W/cm2 (Koubek, 1971). Among TPS materials, Polymeric Ablative Materials (PAMs) possess the highest versatility in terms of properties tunability. Ablation is a self-regulating heat and mass transfer process in which the incident thermal energy is dissipated through a sacrificial material which undergoes endothermic degradation reactions.
In general, among PAMs, composite materials are produced combining high char yield matrices with high performance fibers. To this purpose, in order to produce high char yield and performance composite formulations, many researches aimed at use matrices such as cyanate-esters, bismaleimides, benzoxazines in combination with different types of fibers (silica, glass, carbon, etc.). Each type of fiber is optimized to work in a certain hyperthermal environment (Natali et al., 2016). Unfortunately, a series of problems - mainly related to the costs and the processing - tends to hinder the use of these matrices. As a result, the data available on literature on the use of these matrices are very limited. Phenolics are the most important resins used to produce high char yield and performance composite formulations. Consequently, Carbon/Phenolic Composites (CPCs) are the most studied and versatile class of fiber reinforced PAMs. Due to their high mechanical properties, high thermal resistance, low density, Carbon Fibers (CFs) are the most important class of reinforcements for high char yield composites. Carbon/phenolic composites are used to produce many parts of a nozzle (such as the cowl in a submerged configuration or the exit cone) since the erosive phenomena are smaller as compared to the throat region.
Figure 1 reports the exploded view of the Submarine Launched Ballistic Missile (SLBM) UGM-73 Poseidon first stage (Ellis, 1975). It is possible to identify thermoset based PAMs such as the carbon/phenolic composites known as MX-4926 (Natali et al., 2016) that will be discussed in details in Section 3. Moreover, through the use of a series of carbonization, graphitization and re-impregnations cycles, carbon/phenolic composites are converted into carbon/carbon composites (Fitzer and Manocha, 1998). Depending on the re-entry or flight conditions, carbon/phenolic composites are also used to manufacture the heat shields of re-entry objects; as an example, a carbon/phenolic composite was used to manufacture the heat shield of the Galileo probe which entered in the Jupiter atmosphere and underwent one of the highest heat flux ever recorded (∼30,000 kW/cm2) (Milos, 1997). For these reasons, carbon/phenolic composites are virtually the most important class of TPS materials. One of the last efforts of NASA to systematically investigate high temperature composites has been done within the Next Generation Launch Vehicle (NGLV) program (Smith, 2019). In this framework, the development of out-of-autoclave processing techniques for carbon/phenolic composites has also been faced. However, for over 60 years, space agencies such as National Aeronautics and Space Administration (NASA) spent millions and substantial efforts to investigate carbon/phenolic composites (Natali et al., 2016). Moreover, hundreds of papers and reports on carbon/phenolic composites have been reported and made readily available mostly through the NASA Technical Reports Server (NTRS). In the next sections we will first provide an introduction to the raw materials used to produce high temperature composites i.e. the matrices - mainly focusing the attention on phenolics - and the carbon fibers (ex-PAN, ex-Rayon, ex-Pitch). Then the efforts of our survey will be focused on non-oil based phenolics and carbon fibers derived from biomass, also highlighting the current limitations and the potential of these renewable raw materials.
FIGURE 1. Typical nozzle assembly of a solid rocket motor. In this figure it is possible to see the complex structure of all components of the nozzle assembly of a SLBM Poseidon C-3 first stage. The item indicated in figure as 1-5 are made of carbon/phenolic composites (from Ellis, 1975, credit NASA).
Due to the high temperature properties of carbon, the creation of a carbonaceous residue - char - on the surface of the ablated material is essential (Allen, 1958). In fact, carbon possesses a high heat capacity and high energy of vaporization combined with high heat of ablation. In this case, the PAM is based on the use of charring precursors. When the matrix is exposed to a non-oxidizing hyperthermal environment and it is not subjected to mechanical erosion, it is converted into a charred layer obtained from the carbon atoms present in the molecules of the organic precursor (Schmidt, 1968a; Schmidt, 1968b; Schmidt, 1971; D’Aelio GF, 1971; Wen et al., 1971); the carbon based-residue can still partly operate as a binder of the fillers used in the formulation of the ablative. In addition with their superb thermal stability and char yield, phenolics have a remarkable dimensional stability due the high density of highly aromatic rings in the molecular structure of these resins (Schmidt, 1968a; Schmidt, 1968b; Schmidt, 1971; D’Aelio GF, 1971; Wen et al., 1971). Once the polymeric binder is charred it works as thermal insulator for the virgin matrix. Different precursors have been evaluated as binders of PAMs but, among common matrices, phenolics remain the most versatile infiltrants. In fact, in addition to phenolic matrices, other high char yield polymers have been evaluated as binders of high temperature composite (Schmidt, 1971; Pilato et al., 2008; Vincent, 1971; Lurie et al., 1971; Marks and Rubin, 1971; Dickey et al., 1969; Minges, 1971). Among them, it is worth to mention cyanate-esters, bismaleimides, and benzoxazines (Natali et al., 2016). However, when compared to phenolics, they generally tend to exhibit limitations mainly in terms of processability and costs - they are typically one order of magnitude more expensive than phenolics. For these reasons, most of efforts of these review paper on the non-oil based high char yield matrices will be focused on phenolics.
Phenol-formaldehyde resins are synthetic polymers obtained by the reaction of phenol and formaldehyde. The molar ratio between these two organic compounds and the acidity (or basicity) of the environment in which they are allowed to react can lead to various and versatile families of phenolic resins (Gardziella et al., 2013). Heat reactive phenolic resins known as resols are obtained under basic conditions, and the molar ratio between formaldehyde and phenol can vary from equimolar to values in excess of formaldehyde. On the other hand, when less than an equimolar amount of formaldehyde to phenol is maintained under acidic conditions, a novolac resin is obtained. In general, when compared to other polymers in which the chemistry of the cure is based on a single main process, the crosslinking of phenolics is very complex and involves a wide series of competing reactions which are deeply influenced by experimental conditions. An additional factor that complicates the chemistry of the cure of phenolics is due to the possibility to obtain crosslinking reaction by either or both the ortho- and para-positions of the phenol. As a result, depending on the position of the functional group and as a function of the steric spacing in which the molecules can intertwine, a wide number of isomeric products having different reactivity is created.
Resols are readily cured mainly by acid aiders or thermal conditions. The polymerization is a poly-condensation reaction where the oxygen atom in the formaldehyde molecule reacts with a hydrogen atom on each of two phenol molecules. Water is the product of the reaction. The two phenol molecules are then joined by the residual carbon atom in the formaldehyde (Askeland, 1996). Methylene links connect phenol rings along with methoxy-type ether links produced during the initial reactions that are still present due to shielding from subsequent heating conditions, and phenoxy-type ether links occasionally formed between adjacent phenol hydroxy groups. In both cases, the ether groups are vulnerable to dehydration or oxidation. Post-curing at temperature higher than 200 °C will remove all the ether links as formaldehyde is generated (Lee, 2007). The mechanism of cure for novolac involves benzoxazine intermediates that are converted into benzyl amines, amides/imides, imines, methyl phenol, benzaldehyde. Curing reaction of novolac with hexamine results in a polymer network, especially when sufficient hexamine is available for full cure and reaction of all available novolac sites. Hexamethylenetetramine (HMTA or hexa) is by far the most important curing agent for novolac: typically, about (5–10) % of hexamine is added to novolac. When heat is applied to novolac, the hexamine added to the uncured resin decomposes, enabling the production of methylene bridge bonds to form the crosslinked structure. (Smith and Hashemi. 2006). Complete cure of phenol-formaldehyde resin leads to a polymeric material characterized by high elastic modulus, high crosslink density, moderately high glass transition temperature; the material exhibits excellent moisture, electrical and heat resistance (Smith and Hashemi. 2006; Kim et al., 1997). The dimensional and thermal properties of phenolics are widely covered in (Natali et al., 2016).
Cyanate esters (CE) matrices consist of a variety of bisphenols as well as phenolic novolac resins with the cyanate (-O-C=N) functional group appended to the phenolic hydroxyl (Hamerton, 2012; Hamerton and Hay, 1998). Chemically speaking, this family of thermo-setting monomers and their prepolymers are prepared by reacting the phenolic containing materials with cyanogen halide to form the resulting cyanate ester in the presence of a base (Hamerton and Hay., 1998). At elevated temperatures cyanate esters convert to a thermoset polymer via cyclotrimerization to form three-dimensional networks of oxygen-linked triazine (or cyanurate) and bisphenyl units called poly (cyanurate) s (Hamerton and Hay, 1998). The cured polymer exhibits high Tg, excellent mechanical properties, heat resistance, low volume shrinkage, and low water absorption (Pilato, 2010).
Bismaleimides monomers are usually synthesized from maleic anhydride and an aromatic diamine and then, the resulting bismaleamic acid is cyclo-dehydrated to a bismaleimide resin (Bibin & Reghunadhan Nair, 2014). The double bond of maleimide is very reactive and can promote chain-extension reactions. When bismaleimide is heated above 200°C, a polymerization by an addition mechanism with the formation of a cross-linked network occurs. A basic catalyst such as diazabicyclooctane or 2-methylimidazole can be used to polymerize bismaleimides by an anionic mechanism (Sillion, 1996). or, Bismaleimides can provide a higher service temperature than epoxies maintaining epoxy-like processing glass transition temperatures in excess of 260°C and a continuous-use temperature of 200–230°C. These matrices mainly find applications in high-performance structural adhesives for high temperature application (Bibin & Reghunadhan Nair, 2014).
Benzoxazines can be considered as a novel type of phenolic resins, even though they differ from traditional phenolics, because the phenolic moieties are connected through the formation of a cyclic structure from the phenolic hydroxyl to the ortho position [–O–CH2–N(R)–CH2–] rather than a methylene [–CH2–] bridge associated with traditional phenolics (Ning & Ishida, 1994; Takeichi & Agag, 2006; Blyakham et al., 2001; Ghosh et al., 2007). The molecule of monomer consists in oxazine ring (a hetero-cyclic six-membered ring with oxygen and nitrogen atom) attached to a benzene ring. There are several benzoxazine structures that depend on the position of the heteroatoms. Benzoxazines can be readily produced by a combination of a phenolic derivative, formaldehyde, and a primary amine and any combination of them can be used. Like epoxies and cyanate esters, both monomers and oligomeric benzoxazine materials are available by reaction of bisphenols or novolac with primary amines and formaldehyde (Cortopassi, 2012). Polymerization occurs through the ring opening of the cyclic component by heat treatment with or without catalyst and, without the generation of by-products/volatiles. In addition to flame retardant properties and high heat resistance, the material exhibits characteristics that are not showed in traditional phenolic resins, such as low water absorption (Ishida, 2011).
Many matrices have been tested in PAMs but, among common polymers, phenolics resins still remain the preferred and most widely used charring binders. An important example of a phenolic resin used to produce PAMs is the SC-1008 (Hexion, 2015b). This resin has been used in many of the phenolic based composite formulation. The SC-1008 resin is a resol diluted in isopropyl alcohol whit a solid content close to (60–64) % and a viscosity of (180–300) mPas.
Even though matrices such as phenolics possess a carbon yield higher than 50%, the residual char of the polymeric precursor is a relatively weak medium. When the polymer is converted into char a substantial amount of heat is absorbed by the degradation processes and the char works as a heat sink. However, the char i.e. the residue of the organic precursor can be removed by the high pressure and temperature of the combustion products of solid rocket motor propellants or by the interaction with the atmosphere gases during the re-entry flight (Allen, 1958). As a result, since the polymeric matrix needs to be combined with some reinforcement. Once converted into a carbonaceous residue, the retention of the charred matrix is then promoted and consequently the ablation process can proceed effectively - the material can continue to endothermically absorb heat.
When compared to reinforcements made of refractory oxides (such as glass or silica fibers), in not oxidizing conditions, carbon based filaments tend to possess lower density and a substantially higher ablation resistance (Natali et al., 2016). Different precursors have been generally used to produce carbon fibers: CFs are typically produced from Rayon, Polyacrylonitrile (PAN), and Pitch (Rossi & Wong, 1996). Since the introduction of fibers also helps to anchor the charred material on the virgin region which is undergoing pyrolysis, the delamination phenomena tend to be mitigated. A fiber with a high thermal conductivity tends to increase the in-depth penetration of the charring phenomena and consequently a wider degradation of the bonding capability of the virgin matrix. If the pyrolysis gases cannot escape, the fibers can suffer severe in depth de-bonding or pull-out from the matrix (Allen, 1958). In fact, entrapped pyrolysis gases in the charring matrix can cause pore pressure build-up, and also produce a wide series of erosion phenomena such as ply lift, sub-char ply separations, pocketing, etc. (Schmidt. 1968a). These erosion processes can significantly affect the performance of the PAM. Moreover, the reinforcements embedded in the composite material also undergo many endothermic processes. As an example, carbon fibers can also undergo sublimation (Natali et al., 2016). Accordingly, fibers should possess the lowest thermal conductivity and the highest heat capacity.
The virtually most important carbon/phenolic composite used in rocketry and to manufacture nozzle components is Cytec MX-4926 (density 1.45 g/cm3) (Minges, 1971; Koo, 2006; Cortopassi, 2012; Cortopassi et al., 2009, Hexion, 2015a). It consists of 50 wt% carbon reinforcements, 35 wt% phenolic resin (Hexion SC-1008) and 15 wt% carbon black which help to reduce the shrinkage of the resin pocket, due to the carbonization and loss of volatiles from the matrix. During the firing of the motor (Mathis & Laramee, 1970), the inner layers of the nozzle wall start to char (Figure 2A, in red) dramatically reducing the local Inter Laminar Shear Strength (ILSS) (over 90%); as a result, the structural integrity of the nozzle wall is enabled by the virgin portion (Figure 2A, in green) of the overlapping fiber layers. The charred part does not contribute to the structural integrity of the nozzle wall which is subjected to ply-lift (Figure 2B). Depending on the combustion time, every design and layout of the fibers have to keep into account the fact that a certain portion of the carbon/phenolic composite wall has to be left virgin to avoid the failure of the nozzle. That’s the reason why it is imperative to have carbon/phenolic composites with the highest ILSS and the lower thermal conductivity. The part of throat evidenced in the circular red area of Figure 2C is completely charred as compared to other portions of the same part which still possess a certain level of virgin material - as resumed in Figure 1A. In Figure 2C, the triangular part evidenced in red is the portion that does not possess any virgin material and thus is completely removed.
FIGURE 2. Charring phenomena within the nozzle of a solid rocket motor. (A) Ply-lift of a carbon/phenolic composite. (B) Post burning appearance of a composite segmented submerged nozzle assembly and phenomena of erosion. (C) It is possible to also evidence the portion of the throat made of MX-4926 (image produced starting from an image taken from (Mathis & Laramee, 1970), credit NASA).
Moreover, different researchers reported the effect of the use of nanostructured phenolic matrices (Natali et al., 2016; Natali et al., 2012; Rallini at al., 2017; Natali et al., 2011a;, Natali et al., 2011b) on the ablation resistance of the derived carbon/phenolic laminates. Among these researches, some efforts were successfully spent to identify special fillers or chemical modifiers aimed at improve the ILSS of carbon/phenolic composites (Yeh et al., 2006; Lyashenko et al., 2013; Abramovitch et al., 2015; Wang et al., 2006; Wolf et al., 2012; Srikanth et al., 2010).
NASA and other US agencies spent decades to study carbon/phenolic composite materials. On the base of these studies, most of the European countries and US allied in the pacific area such as South Korea and Japan set up their corresponding efforts to produce high temperature carbon/phenolic composites. Randy Lee at NASA Marshall Space Flight Center (MSFC) carried out the most comprehensive investigation on the effect of the use of different carbon fibers for carbon/phenolic composites [Lee, 2009; Lee, 2010; Lee, 2014.]. In these papers, the benefits and demerits of ex-Rayon based Carbon Fibers (R-CFs) - which are typically used to produce carbon/phenolic composites and carbon/phenolic composites - and common ex-polyacrylonitrile (PAN) based Carbon Fibers (P-CFs) - i.e., T300-like fibers which are typically used to produce high performance Carbon/Epoxy Composites (CECs) - were highlighted.
Pitch-based CFs were also evaluated as fibers to produce high char yield composites. However, Pitch based carbon fibers possess a thermal conductivity too high so tend to promote in depth charring (i.e. pyrolysis of the resin) and hence are not suitable to produce carbon/phenolic composites (Rossi and Wong, 1996). P-CFs, however, have been evaluated as alternative reinforcement for nozzle insulators for more than 20 years with NASA, Air Force, and Navy funding. Thermal conductivity of P-CFs, a critical performance property, was found to be adjustable by varying the carbonization temperature. A comparison of thermal conductivity for various carbon fibers is reported in Table 1 (Towne, 1989). By dropping carbonization temperature below 1400°C, P-CFs thermal conductivity values can be reduced to about one-half of standard P-CFs (T300-like), but are still two to three times the value of R-CFs.
TABLE 1. Thermal conductivity values of carbon fibers derived from different precursors. From (Towne, 1989).
Due to the intrinsic properties of Rayon based carbon fibers (Lee, 2010; Lee, 2009; Lee, 2014), the ILSS properties for R-CF-based laminates are much higher than P-CF based counterparts. However, P-CFs represent most of the carbon fiber production worldwide and many suppliers of R-CFs have ceased production, also due to the increasingly stringent environmental constraints [https://parkaerospace.com/our-company]. As a result, over the past 30 years, new cellulose based R-CFs had to be qualified for the production of carbon/phenolic composites (Lee, 2010; Lee, 2009; Lee, 2014). Below, the history of R-CFs in US and Europe will be covered in detail.
Most launch vehicle based on SRMs originally relied on R-CFs produced by North American Rayon Company (NARC) (Mills, 2008). But environmental and economic challenges resulted in NARC stopping the production of Rayon fibers in 1998. In November 2002, Snecma Propulsion Solide (SPS, France) announced that FiberCote (now known as Nelcote, a subsidiary of Park Electrochemical, US) would be SPS’s exclusive marketer and distributor of Raycarb C2 carbonized Rayon fabric in North America, Asia and Israel and SPS’s global partner for Raycarb C2™ ablative grade prepregs (Berdoyes et al., 2005; Peake et al., 2006; Peake et al., 2007). The new grade R-CFs known as Raycarb C2™ fiber cloth is currently used by large firms in US and France (as an example, in the Ariane and Vega programs). The Raycarb C2™ is stocked in the US and France.
However, since Raycarb C2™ is manufactured in Europe, the launch vehicle systems in the United States depend on foreign sources. It would be helpful to report the text of one Small Business Innovation Research (SBIR) call for proposal released by the US Missile Defense Agency (MDA) in 2016. In particular the topic entitled “Rayon Replacement for High Temperature Materials” (MDA16-020) [https://www.sbir.gov/node/1188777.] reported: “Rayon-based fibers continue as the industry standard for ablative and non-ablative insulators in applications such as nozzles and reentry vehicles. In recent decades, environmental constraints have limited availability since rayon is no longer domestically produced. Many aerospace programs have stockpiled heritage material or utilize foreign sources. This topic focuses on domestically available replacement materials, such as structural or ablative insulators, with performance properties comparable to or exceeding rayon based high temperature composites. In order to address domestic supply issues, many manufacturers have used Polyacrylonitrile (PAN) fibers as reinforcement for high temperature composites. However, PAN based fibers do not have the same thermal properties as rayon based fibers, and some PAN based materials have exhibited aging issues. New fibers, such as cellulose based fiber, have demonstrated properties very similar to rayon in the carbonized form. The thermal conductivity of carbonized rayon fiber is close to 5 W/mK and on the order of 1 W/mK for some rayon based composites. Other precursor fibers may also provide a viable domestic source for high temperature composites. Utilization of new fiber precursors could significantly decrease thermal conductivity of ablative and/or structural insulators. In addition, new fiber based architectures (braids, weaves, etc.) could improve mechanical and thermal properties. Efforts should demonstrate the feasibility of producing either structural or ablative insulator components (valve components, nozzle components, etc.) with improved thermal properties. Process technologies should be appropriate for modest production volumes, be repeatable, and offer significant potential for enhancing performance properties while improving producibility”. A careful reader would immediately understand that Department of Defense (DoD) agencies such as the MDA are struggling to overcome the problems due to the procurement of carbon fibers for PAMs. As a result, the US government promoted the evaluation of new cellulose based fibers as a replacement of Raycarb C2™. Lyocell, a cellulose-based fiber like Rayon that is manufactured using an environmentally-friendly process, has been evaluated as a replacement of traditional Rayon derived carbon fiber (Gasch et al., 2016; Gradl & Valentine, 2017). The product, marketed under the trade name Tencel, is produced in Mobile, Alabama and Lenzing, Germany. Lyocell (Wu and Pa, 2002; McCorsley, 1980; Lenz et al., 1994), which has been commercialized under the trademark of Tencel, is a new 100% cellulosic fiber spun from wood or cotton pulp in a closed amine oxide solvent system, a unique, environmentally friendly production process. Lyocell showed to be an excellent candidate for making high performance carbon fibers (Wu & Pa, 2002; McCorsley, 1980). Due to the increasing importance of Lyocell-like fibers in the production of carbon/phenolic composites, section will provide more details on the science and technology of cellulose based carbon fibers.
However, in order to bypass the procurement problems related to R-CFs, some P-CFs were qualified as a replacement of R-CFs (Williams & Murray, 2008). It was noted that P-CFs are readily available and used extensively for composite fabrication in the aircraft industry. These fibers exhibited low erosion, good char integrity, and thermal stability. According to Canfield et al. (Canfield & Koenig, 1989), in general, P-CFs based carbon/phenolic composites erode less, char deeper and weigh more. P-CFs based carbon/phenolic composites are more thermally stable, char cracking and spallation is minimized. P-CFs based carbon/phenolic composites also exhibit low thermal expansion, high purity, and uniform erosion. Because of their good erosion properties, (T300-like) P-CFs should be considered as candidates for high erosion areas, such as the throat and entrance sections. In 2005, Alliant Techsystems (ATK) (now Northrop Grumman Innovation Systems, NGIS) reported a series of delamination issues on one of their program to produce SRM nozzle components based on P-CFs (Orion Stage I Vectorable Nozzle Separations, 2005). Mills and coauthors (Mills, 2008; Mills et al., 2011) indicated that a carbon/phenolic composites made of common (T300-like) P-CFs and a SC-1008 matrix could be manufactured with properties that met the characteristics of the R-CFs based carbon/phenolic formulations, such as MX-4926, thereby establishing a new source of composite materials for ablative nozzle fabrication and/or military applications. This conclusion was reached in part by using the method of photomicrography to compare the micro-crack densities of specimens cut from R-CFs/SC-1008 and P-CFs/SC-1008 composite plates.
Moreover, with the aim to produce a carbon fiber with a reduced thermal conductivity - as compared to the values of standard P-CFs - and consequently, able to mimic the values of R-CFs, special low-fired stretch-broken P-CFs have been developed. In fact, in addition to the low thermal conductivity, due to the intrinsic properties of Rayon-based carbon fibers (Natali et al., 2016; Lee, 2010; Lee, 2009; Lee, 2014) such as high surface roughness, and chemical affinity with phenolics, the Inter Laminar Shear Strength (ILSS) properties of R-CF-based laminates are much higher than P-CF based counterparts (Lee, 2010; Lee, 2009; Lee, 2014). Aerojet’s experiences with low-fired stretch-broken P-CFs began in 2001 with a material called Lewcott LR1406 (Williams & Murray, 2008). The test results showed that the Lewcott LR1406 has performance characteristics that are comparable to the R-CFs based carbon/phenolic composites. Other studies confirmed these results (Katzman et al., 1994). Thus, a new generation of carbon/phenolic composites made from the so called Naxeco® 3D reinforcement (Berdoyes et al., 2011), impregnated with a high char yield matrix (a phenolic resin) using the Resin Transfer Molding (RTM) process has been developed and flight validated by SPS in the Ariane five program. Unfortunately, both due to their dual use nature, materials such as the Raycarb C2™ as well as the Naxeco® 3D are available only to the large US and French players. In fact, most of these state-of-the-art aerospace-qualified R-CF-based carbon/phenolic composites (such as the MX-4926) as well as the low thermal conductivity PAN-CF-based-carbon/phenolic composites (such as the LR-1406 (Williams & Murray, 2008; Shields, 1976) or the LR-1750) are restricted under International Traffic in Arms Regulations (ITAR) which controls the export and import of defense-related material (Cortopassi, 2012; Martin, 2013) and so it is extremely difficult to produce a review paper on this topic.
To summarize, at this point of the researches on T300-like P-CFs based carbon/phenolic composites, it can be concluded that most of the problems related to the delamination issues of these high temperature composites can be dramatically mitigated acting on: 1) the composition of the high char yield matrix; 2) the processing parameters of the curing cycle in terms of temperatures, heating rates, length of the plateau, as well as pressure applied during the consolidation of the composite material; 3) the removal of the by-products of the reaction of the phenolic matrix. The following section will help to understand the reason why the difference among PAN derived carbon fibers and Rayon based counterparts can influence the properties of the final carbon/phenolic composites. This section will also help to further understand the reason why many researches are focused on new non-oil based cellulose derived fibers such as the Lyocell.
It has been reported as the longitudinal tensile strength of carbonized P-CFs laminates is in general 4/5 times higher than the corresponding of composites made with R-CFs (Rossi and Wong, 1996; Lee, 2010). Indeed, the tenacity of isolated P-CFs is only 2/3 times higher than R-CFs, but because Rayon derived fibers are crimped along their lengths during the fiber manufacturing process, the tensile strength of the corresponding laminates is then reduced. Moreover, the Young modulus of isolated PAN derived carbon fibers can be 6/10 times higher than the values of R-CFs (Rossi & Wong, 1996; Lee, 2010). As a result, in the in-plane direction, P-CFs-based laminates tend to be significantly stronger and significantly stiffer than R-CFs counterpart composites. These differences are mainly due to the morphology differences generated during the fiber manufacturing process leading to composite laminates in which the R-CF fabric layers are highly interacting while the P-CF layers are not. Thus, the Rayon laminas are more interacting, but overall, the resulting composite is softer and weaker. P-CF-based laminated tend to fulfill the structural requirements in many regards, but the composite layers are flat, smooth and weakly-interacting leading to out-plane properties. As reported in previous section, due to the widespread use of P-CFs, this issue is of extreme importance and often tops the list of research efforts under pursuit.
One of the principal factors leading to the formation of weak interfaces in laminated composite systems is related to the residual stresses embedded in the laminate during the manufacturing. Two types of stresses are of extreme relevance. Stresses associated with the difference in terms of Coefficient of Thermal Expansion (CTE) between the constituents which develop during thermal processing and those associated with constituent material properties of the mold tooling, especially in presence of complex article geometries.
In the case of composite based on R-CFs, the shape of the fiber is a key factor: crimps and bends are generated along the length of the R-CFs. During the coagulation step the R-CF will develop an inner core of unprecipitated viscose bounded by a peripheral area of fully polymerized and solidified precursor. The shrinking periphery tends to produce patterns - also known as crenulations - around the circumference of the fiber. In Figure 3 [Nasa Grant NAGS-545, 1988] the straight pattern of PAN derived carbon fibers (a) is evidenced as compared to the longitudinal crimping shape of Rayon based counterparts (b).
FIGURE 3. Through section microscopy image of a carbon/phenolic composite based on PAN derived fibers. (A) Through section microscopy image of a carbon/phenolic composite based on Rayon derived fibers. (B) (from [Nasa Grant NAGS-545, 1988], credit NASA).
As a result, a typical Rayon fiber possesses morphology - both longitudinally and laterally - that traditional P-CFs do not exhibit. These features are key attributes in the distinction between R-CFs and P-CFs in terms of ILSS as well as of interlaminar nesting. Longitudinal crimps and lateral crenulations are unique to Rayon derived fibers, however, the introduction of roughness such as pores and irregularities has been demonstrated, to varying degree, with fibers deriving from PAN (Tiwari & Bijwe, 2014; Yuan et al., 2012). However, in order to maintain the high mechanical properties of PAN derived reinforcements, these etching protocols tend to be detrimental for the final properties of the fiber.
The interlaminar nesting is characterized by the interweaving of fabric features from one layer to the next. The 2D weaving of the fabric determines the pattern of the meshing features across the x-y fabric (in-plane) and along with the 3D z-directional (out-of-plane). The ply-to-ply nesting can also be influenced by the fiber surface roughness. The degree of matrix interaction with the fiber morphology is dependent on several factors. Among them it is worth to mention: 1) the hydrophobicity/hydrophilicity of the fibers, the sizing surfactants coupling and wetting agents; 2) resin viscosity and resin solvent(s); 3) the processing parameters - time/temperature/pressure curing profiles. In terms of manufacturing, the curing profile can influence the degree of nesting and also the level of induced damages. However, an excessively pressures can damage and shift the nesting features of the laminate. Indeed, high pressure cured laminates of both R-CFs and P-CFs have been documented to exhibit reduced interlaminar properties (Lee, 2010). It has been repeatedly showed that the autoclave pressures of less than about 80–100 psi for both R-CF and P-CFs-based laminates produce the optimal mechanical properties (Warga, 1970) and the high ILSS values.
The polymer science at the base of the production of Rayon- and PAN-derived carbon fibers is well documented in literature (Lee, 2010). Similarly, the manufacturing steps behind the fiber spinning processes for both precursors be documented (Lee, 2010; Morgan, 2005). For wet solution spinning, the raw fiber precursor is dispersed in a proper solvent to create a solution which by means of a spinneret is immersed in a coagulation bath. Rayon fibers are cellulose derivative from wood pulp that is dissolved in a strong acid solution which reacts with carbon disulfide to obtain a viscous liquid called viscose. Once the viscose starts to gel, the outer regions are polymerized and the Rayon fiber starts to form. The fiber is forced to pass through several coagulation baths having decreasing concentrations of sulfuric acid and zinc salt. As a result, the degree of coagulation is the driving force that promotes the creation of the crenulations in the Rayon derived fibers. These lateral and longitudinal features are consequently intrinsically possessed by the Rayon filaments and as a result in the 2D woven fabrics as well as in the carbonization steps. Figures 4A,B report the (viscose) Rayon fiber cross-sectional view and also the corresponding fiber longitudinal surface (Chen, 2015).
FIGURE 4. Viscose Rayon fiber cross-sectional view. (A) Viscose rayon fiber longitudinal view. (B) Lyocell rayon fiber cross-sectional view. (C) Lyocell rayon fiber longitudinal view. (D) Reprinted with permission from (Chen, 2015).
Relaxation occurs at the end of this process resulting in the formation of sine wave-like crimps along the length of the fiber (Figure 4B). In order to bypass the environmental constraints that basically killed the industry of the old Rayon derived carbon fibers, it has been found that cellulosic wood pulp can be effectively dissolved in certain organic solvents (such as N-methylmorpholine N-oxide) leading to the formation of higher tenacity filaments without undesirable waste products (ee, 2010). The most well-known cellulosic fiber product from this method is Lyocell (Morgan, 2005). Figures 4C,D report the (viscose) Lyocell fiber cross-sectional view and also the corresponding fiber longitudinal surface (Chen, 2015). One of the major differences between Rayon and PAN is that the initial PAN feedstock is already fully polymerized before the fiber spinning process even begins. Thus, smooth lateral surfaces generally define the predominant morphology of PAN derived carbon fibers.
In terms of microstructure, Lyocell polymers exhibit higher crystal-like order than conventional regenerated Rayon. PAN structures are also expected to show high order due to the extensive nitrile-nitrile interactions. For Rayon derived carbon fibers, bundles (tow) of regenerated polymer fiber are carbonized/graphitized at temperatures in the range (1200–3,000)°C depending on the final desired properties (Morgan, 2005). A protective atmosphere of nitrogen or other inert gases is required in this step of the process. On the other hand, PAN derived fibers are typically spun, stabilized, carbonized, bundled into tow and then woven. A comprehensive review of the manufacturing processes of carbon fibers is provided in (Morgan, 2005). Low temperature processed PAN derived carbon fibers ∼(1100–1400) °C exhibit low modulus whilst high modulus, high temperature PAN derived carbon fibers ∼(2,200–2,800)°C are more stiff and brittle. Prior to weaving, carbonized PAN fibers are usually exposed to chemical/physical surface treatments. Some of these phases could involve surface etching with reactive gases (such as air or CO2) and/or strong acids (such as nitric) (Tiwari & Bijwe, 2014; Yuan et al., 2012) that cause the formation of surface morphology features (roughness) along the fiber surfaces as previously described. Figure 5 reports some PAN derived carbon fibers once treated with nitric acid at different times.
FIGURE 5. SEM micrographs of untreated and nitric acid treated PAN derived carbon fibers: (A) untreated (B) 30 (C) 60 (D) 90 (E) 120 (F) 180 min of treatment. Reprinted with permission from (Chen, 2015).
These chemicals not only physically etch the surface, but lead to the formation of active functional groups and allow establishing the principal interface coupling mechanism for matrix-to-fiber chemical bonding in the composite system. Since most of the PAN derived fibers manufactured worldwide are destined for use in epoxy-based composites, they are intentionally treated to contain mostly carboxyl groups, then it is now possible to understand the reason why fiber-to-matrix chemical bonding in carbon/phenolic composites is relatively insignificant. Moreover, PAN derived fibers manufactured worldwide are treated with coupling agents (sizing) aimed at optimize the adhesion with epoxies, evidencing again the reasons why traditional T300-like P-CFs are not simple to be used in the production of carbon/phenolic composites.
As reported in previous sections, high performance and char-yield thermosetting matrices (especially phenolics) are essential in many crucial aerospace applications, which require materials such as carbon/phenolic or carbon/carbon composites. For a series of reasons - mainly related to very severe military standards used to certify these aerospace materials and due to the cost of the qualification of a new product - this industry only relies on well-known and industrially established petroleum-based materials. As an example, the phenolic resin known as SC-1008 has been used for over 50 years to produce the most important American carbon/phenolic composite formulation i.e. the MX-4926. On the other hand, the US government has been forced to spend millions to requalify new materials (such as novel cellulose derived carbon fibers) which are compatible with the environmental constraints.
Nevertheless, the latest developments in the materials science of polymers suggest that sustainable thermosetting polymers can display similar performances than traditional counterparts (Cywar, et al., 2021). Additionally, in order to overcome the problems due to the procurement of raw materials, considering the increasing demand of materials at the base of the space access and of the homeland security activities, the high char yield matrices (and carbon fibers) derived from renewable feedstock have to meet the very specific and stringent requirements of the aerospace industries (Mauck et al., 2017; Derradji et al., 2021; Wan et al., 2020). The purpose of these researchers would be to identify new paths aimed at avoid problems such as the ones found in the production of the Rayon derived carbon fibers which, due to the environmental constraints, has been discontinued by most companies. As a result, in order to satisfy these environmental constraints, the possibility to produce a polymer (and a fiber) partially based on bio raw materials, but also having its mechanical and thermal behavior preserved, has been sought in these researches (Dotan, 2014).
In light of the ever more stringent environmental constraints, a lot of efforts have been spent to advance in the study of materials coming from truly renewable resources. Obviously, these bio based alternative raw materials have to be economically viable and able to produce products with properties comparable to current technologies. The use of renewable resources requires that bio-based compounds with distinct chemical characteristics should be obtained through careful transformations of plant and other non-fossil materials (Liu et al., 2021): in line with this requirement, considerable efforts have been finalized to produce bio-based polymers that could directly substitute those of fossil origin (Cywar et al., 2021; Selvaraj & Raghavarshini, 2021). On the other hand, biomass constituents should be chemically transformed to obtain desired compounds for crosslinked polymers (monomers, oligomers and resins) starting from bio-based phenolic monomers (i.e., vanillin, eugenol, tannins, lignins) and these operations require a series of chemical reactions and purification processes which are also energy intensive and economically not favorable (Paipa-Álvarez et al., 2020; Quirino et al., 2021). In fact, it should be also considered that every additional step brings a decrease in the yield of subsequent product, resulting into higher process costs (Khoo et al., 2016; Mahajan et al., 2020). Following the requirements of the aerospace sector, an overview on the main biosourced thermosetting polymers that could potentially replace the oil based counterparts is reported. It is essential to remark that the following survey will be mostly focused on the experimental routes reported in literature aimed at synthesizing the non-oil based high char yield matrices as well as on their processability, thermal stability and char yield (and of their carbon fiber derived composites). Moreover, the experimental routes reported in literature aimed at synthesizing the non-oil based carbon fibers will also be covered.
Polybenzoxazines are high-performance materials possessing exceptional thermomechanical and chemical properties (Kiskan et al., 2011). They are produced by the combination of derivative phenols, primary amines and formaldehyde (Zhang et al., 2019). The ring-opening polymerization of benzoxazines, that take place at high temperature, is able to produce polymers having both phenolic hydroxyl and tertiary amine functionalities (Trejo-Machin et al., 2018). It is reported in the literature that biobased benzoxazines can be prepared from guaiacol (from lignin source), paraformaldehyde (from oxidized biomethanol), and furfurylamine (from furfural). Rising interest has been also originated by the possible use of cardanol, having reactivity similar to phenol, due to the existence of the hydroxyl group in its structure. Vanillin, that brings both para formyl and ortho methoxy group, is industrially obtained from the processing of lignin, and it can be used as a precursor for the synthesis of benzoxazines (Lochab et al., 2021; Froimowicz et al., 2016). Eugenol, due to its availability and low cost, has also attracted much interest, even if, owing to its blocked ortho and para positions, has limited reactivity and consequently low cross-linked networks. Other bio-phenols can be used for the preparation of benzoxazine monomers: examples can be found in the case of coumaric, ferulic and phloretic acid (Comí et al., 2013). Nonetheless, the presence of additive chemical functionality on monomers may also affect the overall processability of monomers and related polymers. For example, position of functional groups, steric hindrance or limited processing window may strongly hinder the processing and polymerization of the benzoxazines. To surpass such difficulties frequently faced in presence of monomers synthetized with bio-based phenols, some research groups reported the synthesis of asymmetric benzoxazines monomers (eugenol/phenol, vanillin/cardanol) (Verge et al., 2017). This methodology is moving the research toward more processable high performance bio-based benzoxazines (Kirubakaran et al., 2020). More recently, even if the majority of the research on bio-based benzoxazine has been dedicated almost entirely to the selection of phenolic and amine compounds, few groups also considered the possibility of synthesizing a fully bio-based benzoxazine in which all three reactants necessary to synthesize it, comprising the aldehyde, are from renewable sources for the first time (Machado et al., 2021).
The intrinsic molecular-design flexibility of benzoxazines, their chemical structures and properties open their use to tailored and dedicated applications, so they have been widely applied in the field of space and military applications due to low moisture absorption, high charring ability, limited shrinkage after polymerization, worthy chemical resistance, and high glass transition temperature. High crosslinking degree, that brings high charring ability, can be promoted, for example, by incorporation of diphenolic acid and furfurylamine (Feng et al., 2020): in the reported paper, the authors found that decarboxylation during heating was effectively blocked by the better cross-linking, in details the char yield at 800°C for PBA film, measured at ∼30%, increased to ∼43 and about 54%, respectively, for PDA and PDF, due to the enhanced cross-linking density of cured PDA and PDF films, where PBA, PDA and PDF are the cured films of benzoxazine samples based on different combination of diphenolic acid and furfurylamine (Figure 6A). Lu et al. (2020) also found that the increasing thermal stability of cross-linked main-chain-type benzoxazine polymers (poly (propylene glycol) bis(2-aminopropyl ether):furfurylamine molar ratio = 3:14 showed ∼54% wt. residual weight at 800°C) can be attributed to the participation of furan moiety in the polymerization at high temperatures.
FIGURE 6. Chemical structures (A) and TGA (A’) curves of PBA, PDA, PDF, cured films of benzoxazine samples DF, DA, and BA (A) and proposed crosslinked structures for m-substituted polybenzoxazines derived from monobenzoxazines considering only reactions on the phenolic ring (B) Reprinted with permission from (Feng et al. 2020; Martos et al., 2020)
Even if the current common approach to have highly crosslinked polybenzoxazines is related to the selection of bifunctional monomers, monobenzoxazines are simpler to formulate and are more flexible, having the possibility to introduce substituents into their structures giving special properties to final materials: in their research, Martos et al. (2020) described the effect of monobenzoxazines substitution in meta positions on Tg and crosslinking density (Figure 6B): the results confirm that higher char yields and increased Tg can be obtained, proposing also the successful incorporation of this type of benzoxazine into other benzoxazine mixtures (as doping material) to increase the final crosslinking network (Wen et al., 2021). Zhang et al. (2021) also found that diamine derived from furfurylamine (PDFA), when able to react with cardanol/eugenol, had a char yield of ∼65% at 850°C.
The thermal stability of highly crosslinked polybenzoxazines can be also enhanced when the biobased matrix is combined with other polymers or specific fillers. As an example (Gao et al., 2019), Gao et al. studied the behavior of a new silicon rubber based composite containing benzoxazine resins and ZrO2: the limited ablation rate (∼0.11 mm/s) of the control sample was reduced to ∼0.06 mm/s with a 20% resin formulation. In their work, Subramani et al. (Devaraju et al., 2019), prepared polybenzoxazines-by using cardanol and furfurylamine and further hybridization with silica was considered, by means of thiol-ene click reaction, with the main aim of enhancing thermal stability and fire resistance of the reference material. The same authors also developed hybrid poly (benzoxazine-co-epoxy) composites using cardanol based benzoxazine, commercial bisphenol-F epoxy and functionalized bio-silica (Devaraju et al., 2021). Data acquired from thermal studies confirmed that the bio-silica reinforced hybrid composite showed flexibility, enhanced thermal stability and properties and flame-resistance characteristics.
A comprehensive review on nanostructured natural-sourced polybenzoxazine matrices has been reported by Prof. Ishida (Lyu & Ishida, 2019). In this paper, virtually all the possibilities offered by the combination of benzoxazines with other polymers for the preparation of biobased composites, has been summarized. However, even if it is possible to find papers on the ablation response of nanostructured polybenzoxazine/carbon fiber composites (Rao et al., 2021a) or in general, for high temperature applications (Comer et al., 2019; Wolter et al., 2020), to our knowledge, no papers on the use of non-oil based matrices for the production of high char yield laminates has been documented in literature.
Bismaleimide (BMI) resins, that hold outstanding thermal, mechanical and chemical properties, have been considered for many applications, comprehensive of the aerospace sector. Since bismaleimide resins are cured by following polymerization by addition, volatile by-products are produced during the curing process, providing in this way high strength and rigidity to the matrix. (Prasanaa Iyer & Arunkumar, 2020). They can be processed at rather low temperatures (i.e. < 170°C) and then post cured at high temperatures to yield highly cross-linked networks with high glass transition temperatures, but limited toughness is reached in these conditions. Efforts have been spent to overwhelm those problems by incorporating micro sized elastomers or thermoplastic polymers or copolymerizing them with nanomaterials (Jiang et al., 2020) and same energies have been spent to find valuable solutions for the replacement of fossil based monomers with biobased counterparts (Ge et al., 2017) (Figure 7A).
FIGURE 7. Impact strengths and flexural moduli of BA and BD resin (4,4′-bismaleimidodiphenylmethane (BDM) and renewable bis(5-allyloxy)-4-methoxy-2-methylphenyl)methane (ABE) from bio-based lignin derivative as a function of allyl to imide molar ratio (n) (A); Biobased thermosetting resins based on bismaleimide and allyl-etherified eugenol derivatives (B); Tg and renewable carbon contents of BTP, BD and other eugenol derived BMI resins (C); TGA curves of cured AEG/BMI (EB) (allyl-etherified eugenol prepolymerized with 4,4′-bismaleimidodiphenylmethane, with allyl/maleimide unit ratios of 1/1, 1/2 and 1/3 (D) Reprinted with permission from (Neda et al. 2014; Miao et al., 2019; Ge et al., 2017).
Generally, these resins can be synthetized by copolymerizing bismaleimide monomers with 2,2′-diallyl bisphenol A (DBA) in a two reactions mechanism, namely Diels–Alder (DA) and/or ene reactions (Iredale et al., 2016). Shibata and his group have reported the development of biobased BMI (Shibata et al., 2016; Shibata & Hashimoto, 2017), and the literature on these materials essential relies on the attempts they made to replace or modify the DBA fraction with eugenol-based allylphenyl compound (Figures 7B,C) (Shibata et al., 2011a; Shibata et al., 2013a), tung oil (Shibata et al., 2011b), difurfurylidenecyclopentanone and dicinnamylidene cyclopentanone (Shibata & Miyazawa, 2016), and cardanol (Shibata et al., 2013b).
Gu’s group also prepared a modified BMI resin using a phosphorus-containing allylphenyl compound by linking eugenol to hexachlorocyclotriphosphazene: these BMI resins have demonstrated excellent flame retardancy and high Tg values (∼250–270°C) (Figure 7D) (Miao et al., 2019). Explorative experiments were also performed to investigate the potential of itaconimides synthesized from itaconic anhydride, confirming that life extension and full recyclability can be achieved with this system (Lejeai & Fischer, 2020).
A series of papers reported the combination of BMIs with carbon fibers (Morgan et al., 1993; Spratt & Akay, 1995; Sun et al., 2011; Li et al., 2019; Yang et al., 2021). Ning et al., 2020 reported the preparation of bio-based BMI resins in combination with carbon fibers. The authors synthesized hydroxymethylated eugenol (MEG) and poly-MEG (PMEG) to modify BMI: carbon-fabric laminate composites based on eugenol/maleimide (1:0.3) had the highest Tg (above ∼400°C), high flexural strength (>570 MPa) and modulus (>57 GPa), in the meantime the achieved renewable fraction was the highest (57%) among all the prepared composites. The same authors (Ning et al., 2019) previously considered the preparation of 4,4′-bismaleimidodiphenylmethane (BMI) modified by eugenol and various contents of 4,4′-diphenylmethane diisocyanate (MDI), showing a 5% weight loss temperatures around 300°C and char residue of 42% at 900°C for MDI-EG-BMI resins. However, the limited scientific literature on this subject clearly evidences that the progress on the preparation of bio-based high performance-modified BMI composites is certainly a great challenge.
Cyanate ester (CE) are obtained by reacting phenols with cyanogen halides to give reactive cyanate groups (-OCN) linked to an aromatic ring. The major part of cyanate esters industrially produced are aromatic polymers with strong rigidity of their cured phase, so blending with other thermosets to improve their processability in the composite industry is needed (Nair et al., 2001; Kandelbauer, 2014). The literature reports the effect of different nanofillers on the cure of CE resin (Amirova et al., 2021), in particular the introduction of silica (Bershtein et al., 2021), POSS (Li et al., 2021) was widely investigated. Combination of carbon fibers and nanofillers for ablative purposes have been recently considered in the paper of Rao et al., 2021b, where the authors studied the effect of organo-modified Montmorillonite (o-MMT) addition (0, 1, 2, 4, 6 wt%) on thermal stability of carbon fiber reinforced cyanate ester resin composites, confirming the possibility of using o-MMT for improvement of mechanical properties of CE composites.
In this context, research has moved towards obtaining cyanate ester thermosets by using anethole, resveratrol, vanillin, eugenol, and other lignin derivatives. Harvey and co-workers studied the synthesis of cyanate ester thermosets from vanillin (Meylemans et al., 2013; Harvey et al., 2011), by showing that, even if a decreased thermal stability was observed, vanillin-based resins showed other properties comparable to the petroleum-based commercial counterparts (Llevot et al., 2016). In a recent review, Randani et al. reported about the design and production of biobased cyanate esters from various bioresources, giving a widespread overview of the current advances in the synthesis of these products and discussing their properties and applications (Ramdani et al., 2021). They reported that, in the case of aliphatic bio-precursors, the cyanate ester monomers revealed large processing windows and limited water uptake, while cyanate esters based on aromatic bio-precursors- demonstrated higher thermal properties and stiffness. As in the case of fossil based CE, the introduction of different nanofillers has been considered (Zhan et al., 2011), the available results generally show that the incorporation of reactive fillers can accelerate the initial step of curing process, but decreasing at the same time the final degree of conversion after isothermal curing. On the other hand, no reports have been found on the use of carbon fiber reinforced CE from biobased sources. Actually, the high price requested for chemical modification, limited availability of bio-based raw materials for synthesis are some of the crucial problems to be solved before reaching a decent technological maturity.
Phenolic resins (PF) are the result of a step-growth polymerization of a mixture of phenol and formaldehyde using acidic or basic conditions. Phenolic are highly cross-linked and thermally stable thermosets, due to their aromatic structure and high cross-linking densities. As discussed in the previous sections, their high degradation temperatures and high char yields make phenolic thermosets key and ideal materials for aerospace applications (Granado et al., 2019) However, phenolics present several drawbacks that still need to be surpassed. From an environmental perspective, phenol and formaldehyde are hazardous substances: thus in order to develop no-oil based high thermal performance resins, efforts need to be focused on finding alternative strategies to replace both of them, (Sarika et al., 2020). The replacement of formaldehyde is the main challenge. Hydroxymethylfurfural (Zhang et al., 2015; Xu et al., 2019), furfuryl alcohol (Conejo et al., 2017), glyoxal [Van Nieuwenhove et al., 2020] and vanillin (Foyer et al., 2016b) are few of the bio-based precursors that have been considered and investigated for the replacement of formaldehyde in PF resin synthesis.
In light of the high performance required by the aerospace sector, a potential substitute of formaldehyde should show good reactivity and low molecular weight to accomplish with high cross-linking degrees and final densities (Figure 8A). Hence, phenolic networks with nontoxic aromatic dialdehydes (Foyer et al., 2016a), such as terephthalaldehyde (TPA), showing the best reactivity, should be considered. TPA can react with phenols (in addition and condensation reactions that can be realized on both aldehyde moieties), yielding highly cross-linked and aromatic dense configurations (Granado et al., 2018) (Figure 8B). On the other hand, solutions for phenol substitution in different formulations still have to be found. In order to achieve suitable high charring networks, phenolic blocks must possess high aromatic content and enough activated positions for available reactions. Phenolic blocks can be provided from lignin (Dongre & Bujanovic, 2021), hydrolysable and condensed tannins (Pizzi, 2019), plant oils (Kim, 2015), moreover guaiacol is a possible candidate in the synthesis of phenolic biobased thermosets.
FIGURE 8. Sustainable alternatives for the synthesis of high thermal performances phenolic networks (A); probable reactions of pre-polymerization and curing between phenol and terephthalaldehyde (B); macroscopic morphologies of the front and side views of (A) neat carbon fiber phenolic, (B,C) carbon fiber phenolic +0.2% graphitic C3N4 and (D,E) carbon fiber phenolic 0.2% wt. of graphene oxide after oxyacetylene flame test. The red parabola represents the ablation depth distribution, while the yellow line represents the ablation central zone (C); SEM fractographs of C-Ph composites and TiBr2/C-Ph composites tested at 1000°C and their TG/DTG curves (D) Reprinted with permission from (Granado et al. 2019; Granado et al. 2018; Ma et al., 2019; Ding et al., 2019).
Phenolic resins from biomasses have been indeed developed and studied extensively in recent decades, but the search for biobased alternative to standard phenolic in the specific sector of high charring matrices is still ongoing (Loganathan et al., 2021), even though it is predictable that the properties of resin synthesized from bioresources are lower than the raw material derived from oil (Ipakchi et al., 2020; Ma et al., 2020; Guo et al., 2021; Gruber et al., 2021). One example of nanofiller reinforced phenolic composites for ablative purposes comes from the paper of Ma et al., where the authors found that the addition of graphene oxide or graphitic carbon nitride (Figure 8C) (Ma et al., 2019) increased the char yield graphitization level during ablation, helping heat dissipation and thereby increasing the ablation resistance. Other nanoscaled fillers, such as carbon nanotubes, silica, ZrB2, ZrSi2,TiB2 (Figure 8D) have been also studied (Ding et al., 2019): as a representative result, TiB2 particles included in carbon–phenolic (T/C-Ph) composites prepared by compression moulding reacted, at high temperature, with oxygen-containing molecules, by coating the residue of phenolic after pyrolysis with glassy B2O3, assuring in this way improved mechanical performance at high temperature. Nano-modified carbon fabric represents another opportunity to enhance the ablation behavior of these materials (Xu et al., 2020a; Xu et al., 2020b).
The current methods for manufacturing carbon fibers are slow and energy-consuming, thus making their production very expensive. Additionally, the high cost of precursors keep CF a niche market with applications restricted essentially to high-performance and structural applications (e.g., aerospace): regardless these assumptions, alternative precursors to reduce the realization cost for CF and need for no-fossil feedstock have been investigated and are still under exploration (Xu et al., 2020a). These include biomass-derived precursors such as cellulose (Zaitsev et al., 2021), lignin (Wang et al., 2021), lignin/cellulose blends (Byrne et al., 2018; Bengtsson, et al., 2020), glycerol, and lignocellulosic sugars.
Production and properties of carbon fibers obtained by the different biomasses (mainly lignin ad its blends) will be revised: since the precursor of the carbon fiber contributes to about half of the total cost of the final product, some experimental researches on the possibility to use bio-based CFs has been carried out (Ogale et al., 2016; Frank et al., 2014). However, some disadvantages are typical of these fibers: differently from PAN based carbon fibers, biomass typically contains a major amount of ash/minerals, particularly harmful for the tensile strength of the resulting CFs, additionally biomass-based CFs give low carbon yield in carbonization when compared to commercial PAN-based CFs (the maximum theoretical carbonization yield for a cellulose precursor is ∼44% (corresponding to the formal loss of five molecules of water per anhydroglucose unit), that decreases to the actual value of 15% without any pre-treatment (oxidative pretreatment, use of a reactive atmosphere, application of carbonization aids, inclusion of catalysts for dehydration and crosslinking reagents).
CF from cellulose (natural or man-made) has been detailed in their manufacturing and properties in the previous sections, while here we will introduce the benefits coming from the selection of lignin biosource. Benefiting of its high intrinsic aromatic content, lignin is certainly attractive for the obtainment of high carbon yield following a high-temperature treatment, conditions which makes lignin a suitable precursor for producing carbon-based materials (Qu et al., 2021). Lignin is an abundant biomass with millions of tons produced every year as a by-product of the pulping industry, its cost is less than PAN, additionally it also shows a significantly theoretical high carbon yield when compared with cellulose (62 vs. 44%) (Frank et al., 2014). However, the current main drawback and limitation for the massive production of carbon fibers by starting from lignin is related to the time-consuming stabilization time, which makes its use largely impractical for industrial production (Bengtsson et al., 2019). Additionally, they have limited mechanical properties, restricting their use to sectors where structural functionality is not stringent (Collins et al., 2019). It has been recently claimed that improvements in mechanical performance can be obtained by means of the optimization of chemical reactions during the stabilization and carbonization processes, through the addition of cross-linkers, miscible thermoplastic biopolymers (Culebras et al., 2019) and optimized thermal processing regimes.
In recent studies, the combination of lignin and cellulose has been considered for the realization of composite fibers, where the main aim was the overcoming of disadvantages typical of cellulose and lignin (low carbon yield and long stabilization time, respectively). Le et al. (2021), Trogen et al. (2021) considered the production of cellulose-lignin fibers with a different weight ratio, stabilized at different temperature, by using organosolv or spruce lignin, revealing that one of the main factors affecting the performance of the CF from lignin is the extraction method and/or source of the biomass. Initial structural differences between lignins cause varying rheological and thermal behavior which need to be studied and optimized to create tailored feedstock appropriate fiber spinning processing windows. It is known that more reactive lignins have a greater tendency to form direct ring-to-ring cross-links and this is very significant for the properties of CF as this leads to higher orientation of graphitic planes and subsequently higher mechanical properties of the final CFs (Demiroğlu Mustafov and Seydibeyoğlu, 2019) (Figure 9A).
FIGURE 9. Reported mechanical properties of lignin-based carbon fibers (A) and residue weight at 900°C of various carbon materials as reported in literature (B)—reprinted with permission from (Wang et al., 2021) (Xu et al., 2014).
By changing the reactivity of precursor, the thermal stability of the lignin-based carbon fibers can be also significantly enhanced. Xu et al. [Xu et al., 201491–102] synthesized lignin-based carbon fibers doped with CNTs obtained by catalysis of Fe or Pd: results suggested that the hybrid structure, containing CNTs, showed at 950°C the highest thermal stability when Pd catalyst was considered (∼98% residual weight at 950°C), and the residual weights kept to be stable at 90% even after 1 h of isothermal heating at this temperature (Wang et al., 2021) (Figure 9B): such nanoparticles were able to convert amorphous carbon to graphitic carbon and enabled the growth of CNTs, while carbon fibers without the presence of metallic nanoparticles showed limited thermal stability, essentially due to the lack of amorphous carbon conversion to a graphitic structure.
It has been concluded that, considering current environmental constraints, lignin precursors show also cost savings over conventional PAN precursors. In particular, it has been estimated that lignin carbon fiber can save $260 per ton from CO2 environmental impact compared to PAN fibers (Ismail & Akpan, 2019). On the other hand, even though the chemistry of lignin deserves to be further investigated, in terms of performance, the mechanical properties of lignin carbon fibers made with current experimental lab-scale protocols do not meet the requirements of the aerospace industry.
The access to the space changed our lives in so many ways that it is very difficult to fully grasp the nature of this revolution; considering all the technological returns, new materials, patents, and breakthroughs related to the space activity, then it is practically impossible to draft a comprehensive list. The space sector is also a very profitable market: in “The Space Report 2020” released by The Space Foundation it was estimated that in 2019 the global space economy reached a value of $424 billion worldwide as compared to about $384 billion in 2017. The US Chamber of Commerce reported that this sector will increase from approximately $424 billion of 2019 to at least $1.5 trillion by 2040. As a result, the development of the space economy is intimately related to the space access. Liquid, and especially Solid Rocket Motors (SRMs) provide most of the thrust necessary to reach Low Earth Orbit (LEO). By virtue of their common nature, the materials used for SRMs are also used to manufacture the heat shield which protects the structure, the aerodynamic surfaces, of missiles, probes, and space vehicles from the severe heating encountered during the re-entry flight through the atmosphere. In fact, due to the interaction of the re-entry item with the atmosphere, its kinetic energy can be dissipated via re-radiation and ablation. Thermal Protection System (TPS) materials such as Carbon/Phenolic Composites (CPCs) and Carbon/Carbon Composites (CCCs) are also essential to enable all homeland security programs. Accordingly, the strategic importance of TPS materials now appears in its full extension.
Among the different families of TPS solutions, Polymeric Ablative Materials (PAMs) such as carbon/phenolic composites possess the highest versatility. As a result, more in general, the combination with high char matrices such as phenolics, bismaleimides, cyanate-esters, benzoxazines with Carbon Fibers (CFs) derived from Polyacrylonitrile (PAN), Rayon and Pitch allow to produce the most advanced high temperature fiber reinforced composites. For a series of reasons - mainly related to very severe military standards used to certify a given aerospace material and due to the cost of the qualification of a new product - this industry only relies on well-known and industrially established petroleum-based materials. In general, in order to be used in a launch vehicle, an SRM and its materials - such as the carbon/phenolic composites - need to be tested for validation of required technical specifications. Any changes in the SRM or its components may have need of supplementary testing and, if the deviations are significant or if there are multiple variations, then the re-testing of the entire launch vehicle could be mandatory and thus, a re-qualification process, very expensive and time-consuming, should be necessary.
In our paper, after covering the science and technology of these state-of-the-art fiber reinforced TPS materials, a review of current challenges behind the manufacturing of new, high char yield matrices and carbon fibers derived from non-oil based precursors has been carried out. As a result, in terms of possibility to replace current raw materials, used to manufacture high temperature composites with non-oil based counterparts, the most relevant conclusions of our review work are the following:
1) The latest developments in the materials science of polymers suggest that, in terms of thermal stability and char yield, the non-oil based thermosetting polymers seem to display comparable properties/performances than traditional counterparts. In line with these requirements, substantial efforts have been invested to produce non-oil based polymers that are chemically identical and could directly replace those from petroleum;
2) In order to address the challenges to minimize supply concerns, considering the increasing demand of high temperature materials for the space access and for to the homeland protection activities - taking into account the efforts aimed at solve the dramatic problems experienced during last 40 years by countries such the US and France related to the possibility to establish a stable and cost effective source of cellulose derived carbon fibers - the new non-oil based high char yield matrices (or fibers) have to depend on renewable feedstock able to meet the ever specific and very stringent demands of these industries;
3) Accordingly, the purpose of the researchers would be to identify new paths aimed at mitigate the problems such as the ones found in the production of the cellulose derived carbon fibers which has been discontinued by most companies due to the environmental constraints. As a result, in order to satisfy the continuously more stringent environmental constraints, the possibility to produce polymer (or fibers) partially based on bio raw materials but also having the mechanical and thermal behavior preserved, has been sought in these researches. Moreover, in light of these ever more stringent environmental constraints, a lot of efforts have to be spent to the development of materials coming from fully renewable resources. Obviously, these bio based alternative raw materials have to be economically viable and able to produce products with properties comparable to the current technologies;
4) With aim to introduce raw materials which can be of real interest for the high tech companies involved in the production of ablative materials, it is necessary to identify more uniform and efficient processes able to ensure the manufacturing of materials having the same quality, repeatability and reproducibility than current counterparts. To make it very short, the Technology Readiness Level (TRL) level of the non-oil based matrices has to match the ones associated with the traditional solutions. Due to the intrinsic limitations related to the use of renewable feedstock, it is also questionable whether or not this TRL level will be reached in future;
5) Finally, due to the dual use of technologies related to high temperature composite materials, and in light of the concerns related to the current geopolitical situation related to the commodities, in order to produce non-oil based materials, which are of real interest for the aerospace and homeland security programs, the renewable raw materials should be obtained from domestically available feedstock.
At the end of our literature survey it is possible to conclude that further researches are worth to be done in some very specific areas. However, in terms of performance, it has been showed that the non-oil based materials made with current experimental lab-scale protocols are not able to meet the extremely demanding technology readiness level required by the aerospace industry. Moreover, in terms of real benefits on the environmental impact of the processing technologies related the these non-oil based materials, mixed or questionable results have also been reported in the available literature (Bilow and Miller, 1969; Cyanate Ester Resins Market, 2018; D’ Alelio GF, 1971; Parkaerospace; Rayon Replacement; Nasa Grant NAGS-545, 1988; Van Nieuwenhove et al., 2020; Yongjian Xu et al., 2020).
DP, MR, MN wrote the first draft. LT added notes and revised the manuscript. All authors contributed to the article and approved the submitted version.
The authors declare that the research was conducted in the absence of any commercial or financial relationships that could be construed as a potential conflict of interest.
All claims expressed in this article are solely those of the authors and do not necessarily represent those of their affiliated organizations, or those of the publisher, the editors and the reviewers. Any product that may be evaluated in this article, or claim that may be made by its manufacturer, is not guaranteed or endorsed by the publisher.
Abramovitch, I., Hoter, N., Levy, H., Gedanken, A., Wolf, A., Eitan, A., et al. (2015). Effects of the 3D Sizing of Polyacrylonitrile Fabric with Carbon Nanotube-SP1 Protein Complex on the Interfacial Properties of Polyacrylonitrile/phenolic Composites. J. Compos. Mater. 50 (8), 1031–1036. doi:10.1177/0021998315586080
Allen, H. J. (1958). Hypersonic Flight and the Re-entry Problem: The Twenty-First Wright Brothers Lectureflight and the Re-entry Problem: the Twenty-First Wright Brothers Lecture. J. Aerospace Sci. 25 (4), 217–227. doi:10.2514/8.7600
Amirova, L., Brauner, C., Grob, M., Gort, N., Schadt, F., Pantelelis, N., et al. (2021). Online Cure Monitoring and Modelling of Cyanate Ester-Based Composites for High Temperature Applications. Polymers (Basel) 13 (8), 3021. doi:10.3390/polym13183021
Askeland, D. R. (1996). “Polymers,” in The Science and Engineering of Materials (Boston, MA: Springer). doi:10.1007/978-1-4899-2895-5_15
Bengtsson, A., Bengtsson, J., Sedin, M., and Sjöholm, E. (2019). Carbon Fibers from Lignin-Cellulose Precursors: Effect of Stabilization Conditions. ACS Sust. Chem. Eng. 7 (9), 8440–8448. doi:10.1021/acssuschemeng.9b00108
Bengtsson, A., Hecht, P., Sommertune, J., Ek, M., Sedin, M., and Sjöholm, E. (2020). Carbon Fibers from Lignin-Cellulose Precursors: Effect of Carbonization Conditions. ACS Sust. Chem. Eng. 8 (17), 6826–6833. doi:10.1021/acssuschemeng.0c01734
Berdoyes, M., Broquere, B., Loison, S., and Dauchier, M. (2005). “Sustainable C2 Rayon-Based Carbon Cloth for the Ariane 5 SRM Nozzle,” in Proceeding of the 41st AIAA/ASME/SAE/ASEE Joint Propulsion Conference & Exhibit, Tucson, AZ, July 2005, 3795. doi:10.2514/6.2005-3795
Berdoyes, M., Dauchier, M., and Just, C. (2011). “A New Ablative Material Offering SRM Nozzle Design Breakthroughs,” in Proceeding of the 47th AIAA/ASME/SAE/ASEE Joint Propulsion Conference & Exhibit, San Diego, California, July - August 2011, 6052.
Bershtein, V. A., Grigoryeva, O. P., Yakushev, P. N., and Fainleib, A. M. (2021). The Nature of the Exceptional Impact of Ultra-low Silica Contents on the Properties of Cyanate Ester Resin-Based Nano- and Subnanocomposites. Polym. Composites 42 (12), 6777–6784. doi:10.1002/pc.26338
Bibin, J., and Reghunadhan Nair, C. P. (2014). “Syntactic Foams,” in Handbook of Thermoset Plastics. Editors H. Dodiuk, and S. H. Goodman. Third Edition (William Andrew Publishing), 511–554.
Bilow, N., and Miller, L. J. (1969). Thermosetting Polyphenylene Resin its Synthesis and Use in Ablative Composites. J. Macromolecular Sci. A - Chem. 3 (3), 501–525. doi:10.1080/10601326908053825
Blyakhman, Y., Tontisakis, A., Senger, J., and Chaudhari, A. (2001). “Novel High Performance Matrix Systems,” in Proceeding of the 46th International SAMPE International Symposium, 533–545.
Byrne, N., De Silva, R., Ma, Y., Sixta, H., and Hummel, M. (2018). Enhanced Stabilization of Cellulose-Lignin Hybrid Filaments for Carbon Fiber Production. Cellulose 25 (1), 723–733. doi:10.1007/s10570-017-1579-0
Canfield, A. R., and Koenig, J. (1989). “Development of PAN Precursor Materials for Solid Propellant Rocket Motor Nozzles,” in Proceeding of the AIAA/ASME/SAE/ASEE 25th Joint Propulsion Conference, Monterey, CA, July 1989, 2654.
Chen, J. (2015). “Synthetic Textile Fibers,” in Textiles and Fashion Materials, Design and Technology. Editor R. Sinclair (Woodhead Publishing Series in Textile), 79–95. doi:10.1016/B978-1-84569-931-4.00004-0
Collins, M. N., Nechifor, M., Tanasă, F., Zănoagă, M., McLoughlin, A., Stróżyk, M. A., et al. (2019). Valorization of Lignin in Polymer and Composite Systems for Advanced Engineering Applications - a Review. Int. J. Biol. Macromolecules 131, 828–849. doi:10.1016/j.ijbiomac.2019.03.069
Comer, A. J., Ray, D., Clancy, G., Obande, W. O., Rosca, I., McGrail, P. T., et al. (2019). Hydrothermal In-Plane-Shear Strength of Carbon Fibre/benzoxazine Laminates Manufactured Out-Of-Autoclave by Liquid-Resin-Infusion. Compos. Structures 213, 261–270. doi:10.1016/j.compstruct.2019.01.069
Comí, M., Lligadas, G., Ronda, J. C., Galià, M., and Cádiz, V. (2013). Renewable Benzoxazine Monomers from "Lignin-like" Naturally Occurring Phenolic Derivatives. J. Polym. Sci. Part. A: Polym. Chem. 51 (22), 4894–4903. doi:10.1002/pola.26918
Conejo, L. S., Costa, M. L., Oishi, S. S., and Botelho, E. C. (2017). Degradation Behavior of Carbon Nanotubes/phenol-Furfuryl Alcohol Multifunctional Composites with Aerospace Application. Mater. Res. Express 4 (10), 105701. doi:10.1088/2053-1591/aa8f60
Cortopassi, A. C., Boyer, E., and Kuo, K. (2009). “Update: a Subscale Solid Rocket Motor for Characterization of Submerged Nozzle Erosion,” in Proceeding of the 45th AIAA/ASME/SAE/ASEE Joint Propulsion Conference & Exhibit, Denver, Colorado, August 2009, 5172. doi:10.2514/6.2009-5172
Cortopassi, A. C. (2012). Erosion of Carbon-Cloth Phenolic Nozzles in Rocket Motors with Aluminized Solid Propellant. A Ph.D. dissertation in Mechanical Engineering. The Graduate School, College of Engineering The Pennsylvania State University.
Culebras, M., Geaney, H., Beaucamp, A., Upadhyaya, P., Dalton, E., Ryan, K. M., et al. (2019). Bio-derived Carbon Nanofibres from Lignin as High-Performance Li-Ion Anode Materials. ChemSusChem 12 (19), 4516–4521. doi:10.1002/cssc.201901562
Cyanate Ester Resins Market (2018). Cyanate Ester Resins Market by End-Use Industry (Aerospace & Defense, Electrical & Electronics), Application (Composites, Adhesives), and Region (North America, Europe, APAC, MEA, and South America) - Global Forecast to 2022. Report ID: 4542902.
Cywar, R. M., Rorrer, N. A., Hoyt, C. B., Beckham, G. T., and Chen, E. Y.-X. (2021). Bio-based Polymers with Performance-Advantaged Properties. Nat. Rev. Mater. 7, 83–103. doi:10.1038/s41578-021-00363-3
D'alelio, G. F. (1971). “Structural Design and Thermal Properties of Polymers,” in Ablative Plastics. (Editors) G. F. D'alelio, and J. A. Parker (New York, NY: Marcel Dekker Inc.), 85–123.
Demiroğlu Mustafov, S., and Seydibeyoğlu, M. Ö. (2019). “Surface Treatment of Lignin Sourced Carbon Fibers: Principles, Processes, and Challenges,” in In: Sustainable Lignin for Carbon Fibers: Principles, Techniques, and Applications. Editors E. Akpan, and S. Adeosun (Cham: Springer), 427–439. doi:10.1007/978-3-030-18792-7_10
Derradji, M., Mehelli, O., Liu, W., and Fantuzzi, N. (2021). Sustainable and Ecofriendly Chemical Design of High Performance Bio-Based Thermosets for Advanced Applications. Front. Chem. 9, 691117. doi:10.3389/fchem.2021.691117
Devaraju, S., Krishnadevi, K., Sriharshitha, S., and Alagar, M. (2019). Design and Development of Environmentally Friendly Polybenzoxazine-Silica Hybrid from Renewable Bio-Resource. J. Polym. Environ. 27 (1), 141–147. doi:10.1007/s10924-018-1327-z
Devaraju, S., Krishnamoorthy, K., Eeda, N., Salendra, S., and Achimuthu, A. K. (2021). Development of Highly Flexible Sustainable Bio-Silica Reinforced Cardanol Based Poly (Benzoxazine-co-epoxy) Hybrid Composites. J. Macromolecular Sci. A, 1–7. doi:10.1080/10601325.2021.1981764
Dickey, R. R., Lundell, J. H., and Parker, J. A. (1969). The Development of Polybenzimidazole Composites as Ablative Heat Shields. J. Macromolecular Sci. Part A - Chem. 3 (4), 573–584. doi:10.1080/10601326908053830
Ding, J., Sun, J., Huang, Z., and Wang, Y. (2019). Improved High-Temperature Mechanical Property of Carbon-Phenolic Composites by Introducing Titanium Diboride Particles. Composites B: Eng. 157, 289–294. doi:10.1016/j.compositesb.2018.08.124
Dongre, P., and Bujanovic, B. (2021). “Lignin-based Thermoset Resins. Chapter 6,” in What to Know about Lignin. Editor M. González Alriolset al. (Hauppauge, NY: Nova Science Publishers, Inc.), 249–301.
Dotan, A. (2014). Handbook of Thermoset Plastics, 577–622. doi:10.1016/B978-1-4557-3107-7.00015-4Biobased Thermosets
Ellis, R. A. (1975). “Solid Rocket Motor Nozzles,” in NASA Space Vehicle Design Criteria (Chemical Propulsion) (Washington, D.C.: NASA SP8115).
Feng, Z., Zeng, M., Meng, D., Chen, J., Zhu, W., Xu, Q., et al. (2020). A Novel Bio-Based Benzoxazine Resin with Outstanding thermal and Superhigh-Frequency Dielectric Properties. J. Mater. Sci. Mater. Electron. 31 (5), 4364–4376. doi:10.1007/s10854-020-02995-7
Fitzer, W., and Manocha, L. M. (1998). Carbon Reinforcements and Carbon/carbon Composites. Springer Science & Business Media. 9783540629337.
Foyer, G., Chanfi, B.-H., Boutevin, B., Caillol, S., and David, G. (2016a). New Method for the Synthesis of Formaldehyde-free Phenolic Resins from Lignin-Based Aldehyde Precursors. Eur. Polym. J. 74, 296–309. doi:10.1016/j.eurpolymj.2015.11.036
Foyer, G., Chanfi, B.-H., Virieux, D., David, G., and Caillol, S. (2016b). Aromatic Dialdehyde Precursors from Lignin Derivatives for the Synthesis of Formaldehyde-free and High Char Yield Phenolic Resins. Eur. Polym. J. 77, 65–74. doi:10.1016/j.eurpolymj.2016.02.018
Frank, E., Steudle, L. M., Ingildeev, D., Spörl, J. M., and Buchmeiser, M. R. (2014). Carbon Fibers: Precursor Systems, Processing, Structure, and Properties. Angew. Chem. Int. Ed. 53 (21), 5262–5298. doi:10.1002/anie.201306129
Froimowicz, P., R. Arza, C., Han, L., and Ishida, H. (2016). Smart, Sustainable, and Ecofriendly Chemical Design of Fully Bio-Based Thermally Stable Thermosets Based on Benzoxazine Chemistry. ChemSusChem 9 (15), 1921–1928. doi:10.1002/cssc.201600577
Gao, J., Li, Z., Li, J., and Liu, Y. (2019). Ablation Behavior of Silicone Rubber-Benzoxazine-Based Composites for Ultra-high Temperature Applications. Polymers 11 (11), 1844. doi:10.3390/polym11111844
Gardziella, A., Pilato, L. A., and Knop, A. (2013). Phenolic Resins: Chemistry, Applications, Standardization, Safety and Ecology. Berlin: Springer.
Gasch, M., Stackpoole, M., White, S., and Boghozian, T. (2016). “Development of Advanced Conformal Ablative TPS Fabricated from Rayon- and PAN-Based Carbon Felts,” in Proceeding of the 57th AIAA/ASCE/AHS/ASC Structures, Structural Dynamics, and Materials Conference, San Diego, CA., January 2016, 1414. doi:10.2514/6.2016-1414
Ge, M., Miao, J.-T., Yuan, L., Guan, Q., Liang, G., and Gu, A. (2017). Building and Origin of Bio-Based Bismaleimide Resins with Good Processability, High thermal, and Mechanical Properties. J. Appl. Polym. Sci. 135 (10), 45947. doi:10.1002/app.45947
Ghosh, N. N., Kiskan, B., and Yagci, Y. (2007). Polybenzoxazines-new High Performance Thermosetting Resins: Synthesis and Properties. Prog. Polym. Sci. 32 (11), 1344–1391. doi:10.1016/j.progpolymsci.2007.07.002
Gradl, P. R., and Valentine, P. (2017). “Carbon-Carbon Nozzle Extension Development in Support of In-Space and Upper-Stage Liquid Rocket Engines,” in Proceeding of the 53rd AIAA/SAE/ASEE Joint Propulsion Conference, Atlanta, GA, July 2017, 5064. doi:10.2514/6.2017-5064
Granado, L., Tavernier, R., Foyer, G., David, G., and Caillol, S. (2018). Comparative Curing Kinetics Study of High Char Yield Formaldehyde- and Terephthalaldehyde-Phenolic Thermosets. Thermochim. Acta 667, 42–49. doi:10.1016/j.tca.2018.06.013
Granado, L., Tavernier, R., Henry, S., Auke, R. O., Foyer, G., David, G., et al. (2019). Toward Sustainable Phenolic Thermosets with High Thermal Performances. ACS Sust. Chem. Eng. 7 (7), 7209–7217. doi:10.1021/acssuschemeng.8b06286
Gruber, U., Öttinger, O., Baur, W., and Fischer, L. (2021). “12.2 Carbon Fiber Reinforced Carbon*,”. Industrial Carbon and Graphite Materials. Editors H. Jäger, and W. Frohs, Vol. I, 740–824. doi:10.1002/9783527674046.ch12_2
Guo, Z., Xu, Z., Dong, Z., Zhang, M., Chi, Z., Li, M., et al. (2021). High-performance Thermosets with Tailored Properties Derived from Multi-Arm Stared Vanillin and Carbon Fiber Composites. J. Appl. Polym. Sci. 138 (25), 50588. doi:10.1002/app.50588
Hamerton, I., and Hay, J. N. (1998). Recent Developments in the Chemistry of Cyanate Esters. Polym. Int. 47 (4), 465–473. doi:10.1002/(sici)1097-0126(199812)47:4<465::aid-pi88>3.0.co;2-s
Hamerton, I. (2012). “Introduction to Cyanate Ester Resins,” in Chemistry and Technology of Cyanate Ester Resins. Editor I. Hamerton (Springer Science & Business Media), 1–6.
Harvey, B. G., Wright, M. E., Compel, S., Guenthner, A. J., Lamison, K., Cambrea, L., et al. (2011). Cyanate Ester Composite Resins Derived from Renewable Polyphenol Sources, Cyanate Ester Composite Resins Derived from Renewable Polyphenol Sources. Naval Air Warfare Center Weapons Div China Lake.
Ipakchi, H., Shegeft, A., Rezadoust, A. M., Zohuriaan-Mehr, M. J., Kabiri, K., and Sajjadi, S. (2020). Bio-resourced Furan Resin as a Sustainable Alternative to Petroleum-Based Phenolic Resin for Making GFR Polymer Composites. Iran Polym. J. 29 (4), 287–299. doi:10.1007/s13726-020-00793-w
Iredale, R. J., Ward, C., and Hamerton, I. (2017). Modern Advances in Bismaleimide Resin Technology: A 21st century Perspective on the Chemistry of Addition Polyimides. Prog. Polym. Sci. 69, 1–21. doi:10.1016/j.progpolymsci.2016.12.002
Ishida, H. (2011). “Overview and Historical Background of Polybenzoxazine Research,” in Handbook of Benzoxazine Resins. Editors H. Ishida, and T. Agag (Elsevier), 3–81. doi:10.1016/B978-0-444-53790-4.00046-1
Ismail, S. O., and Akpan, E. I. (2019). “Lignin Carbon Fibres: Properties, Applications and Economic Efficiency,” in Sustainable Lignin for Carbon Fibers: Principles, Techniques, and Applications. Editors E. Akpan, and S. Adeosun (Cham: Springer), 395–426. doi:10.1007/978-3-030-18792-7_9
Jiang, H., Li, Z., Gan, J., Wang, L., and Li, Y. (2020). Improved thermal and Mechanical Properties of Bismaleimide Nanocomposites via Incorporation of a New Allylated Siloxane Graphene Oxide. RSC Adv. 10 (60), 36853–36861. doi:10.1039/D0RA06621D
Kandelbauer, A. (2014). “Cyanate Esters,” in Handbook of Thermoset Plastics, 425–457. doi:10.1016/B978-1-4557-3107-7.00011-7
Katzman, H. A., Adams, P. M., Le, T. D., and Hemminger, C. S. (1994). Characterization of Low Thermal Conductivity Pan-Based Carbon Fibers. Carbon 32, 379–391. doi:10.1016/0008-6223(94)90158-9
Khoo, H. H., Ee, W. L., and Isoni, V. (2016). Bio-chemicals from Lignocellulose Feedstock: Sustainability, LCA and the green Conundrum. Green. Chem. 18 (7), 1912–1922. doi:10.1039/C5GC02065D
Kim, J-S. (2015). Production, Separation and Applications of Phenolic-Rich Bio-Oil-Aa Review. Bioresour. Technol. 178, 90–98. doi:10.1016/j.biortech.2014.08.121
Kim, M., Wu, Y., and Amos, L. W. (1997). Structure of Cured Alkaline Phenol Formaldehyde Resole Resins with Respect to Resin Synthesis Mole Ratio and Oxidative Side Reactions. Polymer 38, 5835–5848. doi:10.1002/(SICI)1099-0518(19971115)35:15<3275::AID-POLA21>3.0.CO;2-7
Kirubakaran, R., Sharma, P., Manisekaran, A., Bijwe, J., and Nebhani, L. (2020). Phloretic Acid: a Smart Choice to Develop Low-Temperature Polymerizable Bio-Based Benzoxazine Thermosets. J. Therm. Anal. Calorim. 142 (3), 1233–1242. doi:10.1007/s10973-019-09228-y
Kiskan, B., Ghosh, N. N., and Yagci, Y. (2011). Polybenzoxazine-based Composites as High-Performance Materials. Polym. Int. 60, 167–177. doi:10.1002/pi.2961
Koo, J. H. (2006). in Polymer Nanocomposites: Processing, Characterization, and Applications (McGraw-Hill Professional), 159–176.
Koubek, F. J. (1971). “A Review of Ablative Studies of Interest to Naval Applications,” in Ablative Plastics. Editors G. F. D’Alelio, and J. A. Parker (New York: Marcel Dekker), 69–83.
Le, N.-D., Trogen, M., Ma, Y., Varley, R. J., Hummel, M., and Byrne, N. (2021). Understanding the Influence of Key Parameters on the Stabilisation of Cellulose-Lignin Composite Fibres. Cellulose 28 (2), 911–919. doi:10.1007/s10570-020-03583-y
Lee, R. (2007). Phenolic Resin Chemistry and Proposed Mechanism for Thermal Decomposition. Washington: NASA Marshall Space Flight Center, 7–13.
Lee, R. (2009). Fiber Surface Treatments and Matrix Interface Effects. Huntsville, AL: NASA Marshall Space Flight Center.
Lee, R. (2010). Interlaminar Factors in Rayon vs. PAN-Based Laminated Composites. Huntsville, AL: NASA Marshall Space Flight Center.
Lee, R. (2014). Interlaminar Strengthening Concepts for Polymer Matrix Composites - A Survey of New and Improved Techniques for Advancing the State-Of the Art in Composite Design and Manufacturing. Huntsville, AL: NASA Marshall Space Flight Center.
Lejeail, M., and Fischer, H. R. (2020). Investigations on the Replacement of Bismaleimide by the Bio-Based Bisitaconimide for Recyclable Thermoset Composites Based on Thermo-Reversible Diels-Alder Cross-Links. Eur. Polym. J. 131, 109699. doi:10.1016/j.eurpolymj.2020.109699
Lenz, J., Schurz, J., and Eichinger, D. (1994). Properties and Structure of Lyocell and Viscose-type Fibres in the Swollen State. Lenzinger Berichte 74, 19–25.
Li, J., Fan, W., Ma, Y., Xue, L., Yuan, L., Dang, W., et al. (2019). Influence of Reinforcement Structures and Hybrid Types on Inter-laminar Shear Performance of Carbon-Glass Hybrid Fibers/Bismaleimide Composites under Long-Term Thermo-Oxidative Aging. Polymers 11 (8), 1288. doi:10.3390/polym11081288
Li, X., Huang, W., Sui, Y., Wang, G., Xiao, L., and Zhang, D. (2021). Curing Behaviors and Thermomechanical Properties of Novolac Cyanate-Polyhedral Oligomeric Silsesquioxane Copolymers. Composites Commun. 28, 100932. doi:10.1016/j.coco.2021.100932
Liu, J., Zhang, L., Shun, W., Dai, J., Peng, Y., and Liu, X. (2021). Recent Development on Bio-Based Thermosetting Resins. J. Polym. Sci. 59 (14), 1474–1490. doi:10.1002/pol.20210328
Llevot, A., Grau, E., Carlotti, S., Grelier, S., and Cramail, H. (2016). From Lignin-Derived Aromatic Compounds to Novel Biobased Polymers. Macromol. Rapid Commun. 37 (1), 9–28. doi:10.1002/marc.201500474
Lochab, B., Monisha, M., Amarnath, N., Sharma, P., Mukherjee, S., and Ishida, H. (2021). Review on the Accelerated and Low-Temperature Polymerization of Benzoxazine Resins: Addition Polymerizable Sustainable Polymers. Polymers 13, 1260. doi:10.3390/polym13081260
Loganathan, T. M., Burhan, I., Abdullah, S. K. B., Sultan, M. T. H., Karam Singh, S. S. A. L., et al. (2021). “Physical, Mechanical, Thermal Properties of Bio-Phenolic Based Composites,” in Phenolic Polymers Based Composite Materials, Composites Science and Technology. Editors M. Jawaid, and M. Asim, 169–190. doi:10.1007/978-981-15-8932-4_11
Lu, G., Dai, J., Liu, J., Tian, S., Xu, Y., Teng, N., et al. (2020). A New Sight into Bio-Based Polybenzoxazine: From Tunable Thermal and Mechanical Properties to Excellent Marine Antifouling Performance. ACS Omega 5 (7), 3763–3773. doi:10.1021/acsomega.0c00025
Lurie, R. M., D'urso, S. F., and Mullen, C. K. (1969). “Structural Ablative Plastics,” in Ablative Plastics. Editors G. F. D’Alelio, and J. A. Parker (New York: Marcel Dekker), 527–529. doi:10.1080/10601326908053826
Lyashenko, T., Lerman, N., Wolf, A., Harel, H., and Marom, G. (2013). Improved Mode II Delamination Fracture Toughness of Composite Materials by Selective Placement of Protein-Surface Treated CNT. Composites Sci. Tech. 85, 29–35. doi:10.1016/j.compscitech.2013.06.001
Lyu, Y., and Ishida, H. (2019). Natural-sourced Benzoxazine Resins, Homopolymers, Blends and Composites: A Review of Their Synthesis, Manufacturing and Applications. Prog. Polym. Sci. 99, 101168. doi:10.1016/j.progpolymsci.2019.101168
Ma, Y.-y., Yang, Y., Lu, C.-x., Lu, X.-x., Wu, S.-j., and Yu, Z. (2019). A Comparative Study of the Ablation Properties of Carbon Fiber-Reinforced Phenolic Resin Composites with a Matrix Modified with Graphene Oxide and Graphitic Carbon Nitride[J]. NEW CARBON MATERIALS 34 (1), 29–37.
Ma, Y., Du, Y., Zhao, J., Yuan, X., and Hou, X. (2020). Preparation and Characterization of Furan-Matrix Composites Blended with Modified Hollow Glass Microsphere. Polymers 12, 1480. doi:10.3390/polym12071480
Machado, I., Hsieh, I., Rachita, E., Salum, M. L., Iguchi, D., Pogharian, N., et al. (2021). A Truly Bio-Based Benzoxazine Derived from Three Natural Reactants Obtained under Environmentally Friendly Conditions and its Polymer Properties. Green. Chem. 23, 4051–4064. doi:10.1039/D1GC00951F
Mahajan, J. S., O’Dea, R. M., Norris, J. B., Korley, L. T. J., and Epps, T. H. (2020). Aromatics from Lignocellulosic Biomass: A Platform for High-Performance Thermosets. ACS Sust. Chem. Eng. 8 (40), 15072–15096. doi:10.1021/acssuschemeng.0c04817
Marks, B. S., and Rubin, L. (1969). “Ablative Resins for Hyperthermal Environments,” in Ablative Plastics. Editors G. F. D’Alelio, and J. A. Parker (New York: Marcel Dekker), 555–571. doi:10.1080/10601326908053828
Martin, H. T. (2013). Assessment of the Performance of Ablative Insulators under Realistic Solid Rocket Motor Operating Conditions. Ph.D. thesis. State College, PA: The Pennsylvania State University.
Martos, A., Soto, M., Schäfer, H., Koschek, K., Marquet, J., and Sebastián, R. M. (2020). Highly Crosslinked Polybenzoxazines from Monobenzoxazines: The Effect of Meta-Substitution in the Phenol Ring. Polymers 12, 254. doi:10.3390/polym12020254
Mathis, J. R., and Laramee, R. C. (19701970). Development of Low Cost Ablative Nozzles for Solid Propellant Rocket Motors, Vol. II. Brigham City, Utah: Thiokol Chemical Corporation Wasatch Division. NASA CR-72641.
Mauck, J. R., Yadav, S. K., Sadler, J. M., La Scala, J. J., Palmese, G. R., Schmalbach, K. M., et al. (2017). Preparation and Characterization of Highly Bio-Based Epoxy Amine Thermosets Derived from Lignocellulosics. Macromol. Chem. Phys. 218, 1700013. doi:10.1002/macp.201700013
McCorsley, C. C. (1980). Shaped Cellulose Article Prepared from a Solution Containing Cellulose Dissolved in a Tertiary Amine N-Oxide Solvent and a Process for Making the Article. Asheville, NC: U.S. Patent 4416698.
Meylemans, H. A., Harvey, B. G., Reams, J. T., Guenthner, A. J., Cambrea, L. R., Groshens, T. J., et al. (2013). Synthesis, Characterization, and Cure Chemistry of Renewable Bis(cyanate) Esters Derived from 2-Methoxy-4-Methylphenol. Biomacromolecules 14, 771–780. doi:10.1021/bm3018438
Miao, J.-T., Yuan, L., Liang, G., and Gu, A. (2019). Biobased Bismaleimide Resins with High Renewable Carbon Content, Heat Resistance and Flame Retardancy via a Multi-Functional Phosphate from Clove Oil. Mater. Chem. Front. 3, 78–85. doi:10.1039/C8QM00443A
Mills, V. P., Gilbert, J. A., and Ooi, T. K. (2011). “Quantification of Micro-crack Density for Fiber Based Composites,”. Experimental and Applied Mechanics. Editor T. Proulx, 6, 218–222. doi:10.1007/978-1-4614-0222-0
Mills, V. P. (2008). Viable Rayon Composite Replacement Micro-cracking in Polyacrylonitrile-Based Carbon-Phenolic Composites. Ph.D Dissertation. Huntsville, Alabama.
Milos, F. S. (1997). Galileo Probe Heat Shield Ablation experiment. J. Spacecraft Rockets 34, 705–713. doi:10.2514/2.3293
Minges, M. L. (1969). “Thermal Physical Characteristics of High-Performance Ablative Composites,” in Ablative Plastics. Editors G. F. D’Alelio, and J. A. Parker (New York: Marcel Dekker), 613–639. doi:10.1080/10601326908053832
Morgan, R. J., Jurek, R. J., Yen, A., and Donnellan, T. (1993). Toughening Procedures, Processing and Performance of Bismaleimide-Carbon Fibre Composites. Polymer 34 (4), 835–842. doi:10.1016/0032-3861(93)90371-G
Nair, C. P. R., Mathew, D., and Ninan, K. N. (2001). “Cyanate Ester Resins, Recent Developments,”. New Polymerization Techniques and Synthetic Methodologies. Advances in Polymer Science (Berlin, Heidelberg: Springer), Vol 155, 1–99. doi:10.1007/3-540-44473-4_1
Nasa Grant NAGS-545 (1988). Standardization of the Carbon-Phenolic Materials and Processes, Vol I. Huntsville, AL: Experimental Studies.
Natali, M., Kenny, J. M., and Torre, L. (2016). Science and Technology of Polymeric Ablative Materials for thermal protection Systems and Propulsion Devices: a Review. Prog. Mater. Sci. 84, 192–275. doi:10.1016/j.pmatsci.2016.08.003
Natali, M., Monti, M., Kenny, J., and Torre, L. (2011a). Synthesis and thermal Characterization of Phenolic Resin/silica Nanocomposites Prepared with High Shear Rate-Mixing Technique. J. Appl. Polym. Sci. 120, 2632–2640. doi:10.1002/app.33494
Natali, M., Monti, M., Kenny, J. M., and Torre, L. (2011b). A Nanostructured Ablative Bulk Molding Compound: Development and Characterization. Composites A: Appl. Sci. Manufacturing 42, 1197–1204. doi:10.1016/j.compositesa.2011.04.022
Natali, M., Monti, M., Puglia, D., Kenny, J. M., and Torre, L. (2012). Ablative Properties of Carbon Black and MWNT/phenolic Composites: A Comparative Study. Composites Part A: Appl. Sci. Manufacturing 43, 174–182. doi:10.1016/j.compositesa.2011.10.006
Neda, M., Okinaga, K., and Shibata, M. (2014). High-performance Bio-Based Thermosetting Resins Based on Bismaleimide and Allyl-Etherified Eugenol Derivatives. Mater. Chem. Phys. 148 (1-2), 319–327. doi:10.1016/j.matchemphys.2014.07.050
Ning, X., and Ishida, H. (1994). Phenolic Materials via Ring-Opening Polymerization: Synthesis and Characterization of Bisphenol-A Based Benzoxazines and Their Polymers. J. Polym. Sci. A. Polym. Chem. 32, 1121–1129. doi:10.1002/pola.1994.080320614
Ning, Y., Li, D. s., Wang, M. c., Jiang, L., and Jiang, L. (2019). Eugenol-Derived Bismaleimide High Performance Resins and Composites Using Diisocyanate as Property Modifier. Macromol. Mater. Eng. 304 (4), 1800713. doi:10.1002/mame.201800713
Ning, Y., Li, D. s., Wang, M. c., Chen, Y. c., and Jiang, L. (2020). Bio-based Hydroxymethylated Eugenol Modified Bismaleimide Resin and its High-Temperature Composites. J. Appl. Polym. Sci 138, 49631. doi:10.1002/app.49631
Ogale, A. A., Zhang, M., and Jin, J. (2016). Recent Advances in Carbon Fibers Derived from Biobased Precursors. J. Appl. Polym. Sci 133, 43794. doi:10.1002/app.43794
Orion Stage I Vectorable Nozzle Separations (2005). ATK Technical Interchange Meeting, 12 September 2005.
Paipa-Álvarez, H. O., Alvarado, W. P., and Delgado, B. M. (2020). Biodegradable Thermosets Polymers as an Alternative Solution to Pollution Generated by Plastics. J. Phys. Conf. Ser. 1672, 012013. doi:10.1088/1742-6596/1672/1/012013
Peake, S. L., Ellis, R. A., and Broquere, B. (2006). “Update: Sustainable Carbonized Rayon for Solid Rocket Motor Nozzles,” in Proceeding of the 42nd AIAA/ASME/SAE/ASEE Joint Propulsion Conference & Exhibit, Sacramento, California, July 2006, 4598. doi:10.2514/6.2006-4598
Peake, S. L., Ellis, R. A., and Broquere, B. (2007). “Update: Sustainable Carbonized Rayon for SRM Nozzles,” in Proceeding of the 43rd AIAA/ASME/SAE/ASEE Joint Propulsion Conference & Exhibit, Cincinnati, OH, July 2007, 5774.
Pilato, L. (2010). in Resin Chemistry in Phenolic Resins: A Century of Progress. Editor L. Pilato (Springer-Verlag Berlin Heidelberg), 68–70.
Pilato, L. A., Koo, J. H., Wissler, G. A., and Lao, S. (2008). A Review – Phenolic and Related Resins and Their Nanomodification into Phenolic Resin FRP Systems. J. Adv. Mater. 40, 5–16.
Pizzi, A. (2019). Tannins: Prospectives and Actual Industrial Applications. Biomolecules 9, 344. doi:10.3390/biom9080344
Prasanaa Iyer, N., and Arunkumar, N. (2020). Review on Fiber Reinforced/modified Bismaleimide Resin Composites for Aircraft Structure Application. IOP Conf. Ser. Mater. Sci. Eng. 923, 012051. doi:10.1088/1757-899x/923/1/012051
Qilin Wu, Q., and Ding Pan, . D. (2002). A New Cellulose Based Carbon Fiber from a Lyocell Precursor. Textile Res. J. 72, 405–410. doi:10.1177/004051750207200506
Qu, W., Yang, J., Sun, X., Bai, X., Jin, H., and Zhang, M. (2021). Towards Producing High-Quality Lignin-Based Carbon Fibers: A Review of Crucial Factors Affecting Lignin Properties and Conversion Techniques. Int. J. Biol. Macromolecules 189, 768–784. doi:10.1016/j.ijbiomac.2021.08.187
Quirino, R. L., Monroe, K., Fleischer, C. H., Biswas, E., and Kessler, M. R. (2021). Thermosetting Polymers from Renewable Sources. Polym. Int. 70, 167–180. doi:10.1002/pi.6132
Rallini, M., Wu, H., Natali, M., Koo, J., and Torre, L. (2017). Nanostructured Phenolic Matrices: Effect of Different Nanofillers on the thermal Degradation Properties and Reaction to Fire of a Resol. Fire Mater. 41, 817–825. doi:10.1002/fam.2425
Ramdani, N., Zaimeche, H., and Derradji, M. (2021). Biobased Thermally-Stable Aromatic Cyanate Ester Thermosets: A Review. Reactive Funct. Polym. 168, 105037. doi:10.1016/j.reactfunctpolym.2021.105037
Rao, G. R., Srikanth, I., and Reddy, K. L. (2021a). Mechanical, thermal and Ablative Behavior of Organo Nanoclay Added Carbon Fiber/cyanate Ester Resin Composites and Effect of Heat Flux on its Ablative Performance. Polym. Polym. Composites 29, S250–S261. 9_suppl: S250-S261. doi:10.1177/0967391121998833
Rao, G. R., Srikanth, I., and Reddy, K. L. (2021b). Effect of Organo Montmorillonite Nanoclay on Mechanical Properties Thermal Stability and Ablative Rate of Carbon Fiber Polybenzoxazine Resin Composites. Def. Sc. J. 71 (5), 682–690. doi:10.14429/dsj.71.16630
Rossi, R. C., and Wong, W. C. (1996). Availability of Aerospace Rayon for SRM Nozzle Insulators. Trw Inc San Bernardino Ca: American Institute of Aeronautics and Astronautics, 1–6.
Sarika, P. R., Nancarrow, P., Khansaheb, A., and Ibrahim, T. (2020). Bio-Based Alternatives to Phenol and Formaldehyde for the Production of Resins. Polymers 12 (10), 2237. doi:10.3390/polym12102237
Schmidt, D. (1968a). “Hypersonic Atmospheric Flight,” in Environmental Effects on Polymeric Materials, Environments. Editors D. V. Rosato, and R. T. Schwartz (Interscience Publishers), 488–578.
Schmidt, D. (1968b). “Chemical Propulsion Exhaust,” in Environmental Effects on Polymeric Materials, Environments. Editors D. V. Rosato, and R. T. Schwartz (Interscience Publishers), 413–486.
Schmidt, D. (1971). “Ablative Polymers in Aerospace Technology,” in Ablative Plastics. Editors G. F. D’Alelio, and J. A. Parker (New York: Marcel Dekker), 1–35.
Selvaraj, V., and Raghavarshini, T. R. (2021). Development of High-Performance Hybrid Sustainable Bio-Composites from Biobased Carbon Reinforcement and Cardanol-Benzoxazine Matrix. Polym. Bull. 78, 4129–4148. doi:10.1007/s00289-020-03232-1
Shibata, M., and Hashimoto, Y. (2017). High Performance Thermosetting Bismaleimide Resins via Thiol-Maleimide "click" Reaction. Eur. Polym. J. 93, 561–571. doi:10.1016/j.eurpolymj.2017.06.032
Shibata, M., and Miyazawa, E. (2016). High-performance Bio-Based Thermosetting Bismaleimide Resins Utilizing Difurfurylidenecyclopentanone and Dicinnamylidene Cyclopentanone. Polym. Bull. 74 (6), 1949–1963. doi:10.1007/s00289-016-1815-z
Shibata, M., Teramoto, N., and Nakamura, Y. (2011a). High Performance Bio-Based Thermosetting Resins Composed of Tung Oil and Bismaleimide. J. Appl. Polym. Sci. 119, 896–901. doi:10.1002/app.32770
Shibata, M., Teramoto, N., Shimasaki, T., and Ogihara, M. (2011b). High-performance Bio-Based Bismaleimide Resins Using Succinic Acid and Eugenol. Polym. J. 43, 916–922. doi:10.1038/pj.2011.87
Shibata, M., Itakura, Y., and Watanabe, H. (2013a). Bio-based Thermosetting Resins Composed of Cardanol Novolac and Bismaleimide. Polym. J. 45, 758–765. doi:10.1038/pj.2012.195
Shibata, M., Tetramoto, N., Imada, A., Neda, M., and Sugimoto, S. (2013b). Bio-based Thermosetting Bismaleimide Resins Using Eugenol, Bieugenol and Eugenol Novolac. Reactive Funct. Polym. 73, 1086–1095. doi:10.1016/j.reactfunctpolym.2013.05.002
Shibata, M., Satoh, K., and Ehara, S. (2016). Thermosetting Bismaleimide Resins Generating Covalent and Multiple Hydrogen Bonds. J. Appl. Polym. Sci. 133, a–n. doi:10.1002/app.43121
Sillion, B. (1989). Polyimides and Other Heteroaromatic Polymers. Compr. Polym. Sci. Supplements 30, 499–532. doi:10.1016/B978-0-08-096701-1.00171-3
Smith, J. L. (2019). Building a Better Booster. Availablr from: https://www.thespacereview.com/article/3658/1 (accessed on line 10 29, 2021).
Smith, W. F., and Hashemi, J. (2006). Foundations of Materials Science and Engineering. McGraw-Hill.
Spratt, G. R., and Akay, M. (1995). High Temperature Stability of Bismaleimide Carbon Fibre Composite Materials. Kem 99-100, 3–10. doi:10.4028/www.scientific.net/kem.99-100.3
Srikanth, I., Daniel, A., Kumar, S., Padmavathi, N., Singh, V., Ghosal, P., et al. (2010). Nano Silica Modified Carbon-Phenolic Composites for Enhanced Ablation Resistancefied Carbon-Phenolic Composites for Enhanced Ablation Resistance. Scripta Materialia 63, 200–203. doi:10.1016/j.scriptamat.2010.03.052
Sun, P., Zhao, Y., Luo, Y., and Sun, L. (2011). Effect of Temperature and Cyclic Hygrothermal Aging on the Interlaminar Shear Strength of Carbon Fiber/bismaleimide (BMI) Composite. Mater. Des. 32, 4341–4347. doi:10.1016/j.matdes.2011.04.007
Sutton, P., and Biblarz, O. (2000). Rocket Propulsion Elements. Wiley-IEEE. 0471326429, 9780471326427.
Takeichi, T., and Agag, T. (2006). High Performance Polybenzoxazines as Novel Thermosets. High Perform. Polym. 18, 777–797. doi:10.1177/0954008306068254
Tiwari, S., and Bijwe, J. (2014). Surface Treatment of Carbon Fibers - A Review. Proced. Tech. 14, 505–512. doi:10.1016/j.protcy.2014.08.064
Towne, M. K. (1989). Structural and Thermal Properties of Rayon, Pitch and PAN Based Carbon/Graphite Fibers. El Segundo, CA: Seminar at the Aerospace Corporation.
Trejo-Machin, A., Puchot, L., and Verge, P. (2018). “Design and Synthesis of Bio-Based Benzoxazines,” in Synthetic Resins Publisher: InTechOpen. Editor L. Zhang. doi:10.5772/intechopen.76104
Trogen, M., Le, N.-D., Sawada, D., Guizani, C., Lourençon, T. V., Pitkänen, L., et al. (2021). Cellulose-lignin Composite Fibres as Precursors for Carbon Fibres. Part 1 - Manufacturing and Properties of Precursor Fibres. Carbohydr. Polym. 252, 117133. doi:10.1016/j.carbpol.2020.117133
Van Nieuwenhove, I., Renders, T., Lauwaert, J., De Roo, T., De Clercq, J., and Verberckmoes, A. (2020). Biobased Resins Using Lignin and Glyoxal. ACS Sust. Chem. Eng. 8 (51), 18789–18809. doi:10.1021/acssuschemeng.0c07227
Verge, P., Puchot, L., Vancaeyzeele, C., Vidal, F., and Habibi, Y. (2017). “Symmetric versus Asymmetric Di-bz Monomer Design,” in Advanced and Emerging Polybenzoxazine (Amsterdam, Netherlands: Sci. Technol.), 89–107. doi:10.1016/B978-0-12-804170-3.00007-X
Vincent, D. N. (1971). “Thermal Degradation and Curing of Polyphenylene,” in Ablative Plastics. Editors G. F. D’Alelio, and J. A. Parker (New York: Marcel Dekker), 159–173. doi:10.1080/10601326908053824
Wan, J., Zhao, J., Zhang, X., Fan, H., Zhang, J., Hu, D., et al. (2020). Epoxy Thermosets and Materials Derived from Bio-Based Monomeric Phenols: Transformations and Performances. Prog. Polym. Sci. 108, 101287. doi:10.1016/j.progpolymsci.2020.101287
Wang, S., Bai, J., Innocent, M. T., Wang, Q., Xiang, H., Tang, J., et al. (2021). Lignin-based Carbon Fibers: Formation, Modification and Potential Applications. Green Energy & Environment. doi:10.1016/j.gee.2021.04.006
Wang, W.-X., Dgany, O., Wolf, S. G., Levy, I., Algom, R., Pouny, Y., et al. (2006). Aspen SP1, an Exceptional Thermal, Protease and Detergent-Resistant Self-Assembled Nano-Particle. Biotechnol. Bioeng. 95, 161–168. doi:10.1002/bit.21010
Warga, J. J. (1970). Low Cost Fabrication Techniques for Solid Rocket Nozzles. Society of Automotive Engineers.
Wen, R. Y., Sonnabend, L. F., and Eddy, R. (1969). “The Synthesis and Characterization of Some Potential Ablative Polymers,” in Ablative Plastics. Editors G. F. D’Alelio, and J. A. Parker (New York: Marcel Dekker), 471–483. doi:10.1080/10601326908053823
Wen, Z., Bonnaud, L., Mincheva, R., Dubois, P., and Raquez, J.-M. (2021). Development of Low-Viscosity and High-Performance Biobased Monobenzoxazine from Tyrosol and Furfurylamine. Materials 14, 440. doi:10.3390/ma14020440
Williams, G., and Murray, J. (2008). “Status on Replacing Rayon Based Carbon Phenolic Ablatives in the MK-104 Motor,” in Proceeding of the 44th AIAA/ASME/SAE/ASEE Joint Propulsion Conference e Exhibit, Hartford, CT, July 2008, 5145.
Wolf, A., Buchman, A., Eitan, A., Fine, T., Nevo, Y., Heyman, A., et al. (2012). Improved Adhesives Containing CNT/SP1 Nano Fillers. J. Adhes. 88, 435–451. doi:10.1080/00218464.2012.660398
Wolter, N., Beber, V. C., Sandinge, A., Blomqvist, P., Goethals, F., Van Hove, M., et al. (2020). Carbon, Glass and Basalt Fiber Reinforced Polybenzoxazine: The Effects of Fiber Reinforcement on Mechanical, Fire, Smoke and Toxicity Properties. Polymers 12, 2379. doi:10.3390/polym12102379
Xu, X., Zhou, J., Jiang, L., Lubineau, G., Payne, S. A., and Gutschmidt, D. (2014). Lignin-based Carbon Fibers: Carbon Nanotube Decoration and superior thermal Stability. Carbon 80, 91–102. doi:10.1016/j.carbon.2014.08.042
Xu, Y., Guo, L., Zhang, H., Zhai, H., and Ren, H. (2019). Research Status, Industrial Application Demand and Prospects of Phenolic Resin. RSC Adv. 9 (50), 28924–28935. doi:10.1039/C9RA06487G
Xu, F., Zhu, S., Liu, Y., Ma, Z., and Li, H. (2020a). Ablation Behavior and Mechanism of TaSi2-Modified Carbon Fabric-Reinforced Phenolic Composite. J. Mater. Sci. 55, 8553–8563. doi:10.1007/s10853-020-04636-0
Xu, F., Zhu, S., Hu, J., Ma, Z., and Liu, Y. (2020b). Ablation Behavior of a Carbon Fabric Reinforced Phenolic Composite Modified by Surface-Decorated ZrB2/SiC. Materials 13 (2), 256. doi:10.3390/ma13020256
Yang, T., Zhao, Y., Liu, H., Sun, M., and Xiong, S. (2021). Effect of Sizing Agents on Surface Properties of Carbon Fibers and Interfacial Adhesion of Carbon Fiber/Bismaleimide Composites. ACS Omega 6 (36), 23028–23037. doi:10.1021/acsomega.1c01103
Yeh, M.-K., Tai, N.-H., and Liu, J.-H. (2006). Mechanical Behavior of Phenolic-Based Composites Reinforced with Multi-Walled Carbon Nanotubes. Carbon 44, 1–9. doi:10.1016/j.carbon.2005.07.005
Yongjian Xu, Y., Liu, Y., Chen, S., and Ni, Y. (2020). Current Overview of Carbon Fiber: Toward Green Sustainable Raw Materials. BioRes 15 (3), 7234–7259. doi:10.15376/biores.15.3.xu
Yuan, H., Wang, C., Zhang, S., and Lin, X. (2012). Effect of Surface Modification on Carbon Fiber and its Reinforced Phenolic Matrix Compositefication on Carbon Fiber and its Reinforced Phenolic Matrix Composite. Appl. Surf. Sci. 259, 288–293. doi:10.1016/j.apsusc.2012.07.034
Zaitsev, A., Moisan, S., and Poncin-Epaillard, F. (2021). Cellulose Carbon Fiber: Plasma Synthesis and Characterization. Cellulose 28, 1973–1988. doi:10.1007/s10570-020-03638-0
Zhan, G., Tang, X., Yu, Y., and Li, S. (2011). Biobased Cyanate Ester Composites with Epoxidized Soybean Oil and In Situ Generated Nano-Silica. Polym. Eng. Sci. 51 (3), 426–433. doi:10.1002/pen.21842
Zhang, Y., Yuan, Z., and Xu, C. C. (2015). Engineering Biomass into Formaldehyde-free Phenolic Resin for Composite Materials. Aiche J. 61 (4), 1275–1283. doi:10.1002/aic.14716
Zhang, K., Han, M., Liu, Y., and Froimowicz, P. (2019). Design and Synthesis of Bio-Based High-Performance Trioxazine Benzoxazine Resin via Natural Renewable Resources. ACS Sust. Chem. Eng. 7 (10), 9399–9407. doi:10.1021/acssuschemeng.9b00603
Zhang, S.-M., Zhao, J.-Q., Liu, Y., Liu, Y.-x., and Liu, C.-M. (2021). Renewable Furan-Derived Diamine as Primary Amine Source to Prepare Fully Bio-Based Bis-Benzoxazine Monomer under Solvent-free Condition. Reactive Funct. Polym. 165, 104957. doi:10.1016/j.reactfunctpolym.2021.104957
Available from: https://parkaerospace.com/our-company/History of the Company Park Aerospace Corp. (accessed on 29/10/2021)
Available from: https://www.sbir.gov/node/1188777Rayon Replacement for High Temperature Materials, Topic Number MDA16-020(accessed on 29/10/2021)
Keywords: thermal protection system (TPS), carbon/phenolic composites (CPCs), solid rocket motors (SRMs), traditional and non-oil based high char yield polymers, traditional and non-oil based carbon fibers (CFs)
Citation: Natali M, Rallini M, Torre L and Puglia D (2022) High Temperature Composites From Renewable Resources: A Perspective on Current Technological Challenges for the Manufacturing of Non-Oil Based High Char Yield Matrices and Carbon Fibers. Front. Mater. 9:805131. doi: 10.3389/fmats.2022.805131
Received: 29 October 2021; Accepted: 02 March 2022;
Published: 21 March 2022.
Edited by:
Patricia Krawczak, Institut Mines-Télécom, FranceReviewed by:
Mehdi Derradji, Ecole Militaire Polytechnique (EMP), AlgeriaCopyright © 2022 Natali, Rallini, Torre and Puglia. This is an open-access article distributed under the terms of the Creative Commons Attribution License (CC BY). The use, distribution or reproduction in other forums is permitted, provided the original author(s) and the copyright owner(s) are credited and that the original publication in this journal is cited, in accordance with accepted academic practice. No use, distribution or reproduction is permitted which does not comply with these terms.
*Correspondence: Debora Puglia, ZGVib3JhLnB1Z2xpYUB1bmlwZy5pdA==
Disclaimer: All claims expressed in this article are solely those of the authors and do not necessarily represent those of their affiliated organizations, or those of the publisher, the editors and the reviewers. Any product that may be evaluated in this article or claim that may be made by its manufacturer is not guaranteed or endorsed by the publisher.
Research integrity at Frontiers
Learn more about the work of our research integrity team to safeguard the quality of each article we publish.