- Chongqing Industry Polytechnic College, Chongqing, China
During gas well cementing operation, the erosion of acidic formation corrosive medium will destroy the cementation between the cement slurry and the sidewall in the well sealing section, reduce the mechanical properties of the cement paste, cause problems such as sidewall collapse and casing damage, seriously endanger the normal exploitation of oil and gas resources, and cause major safety accidents. Therefore, improving the corrosion resistance of cement paste is the key to ensuring long-term stable cementing of high-temperature sour gas wells. This paper summarizes the influencing factors, corrosion mechanism, corrosion test methods and research status of anti-corrosion oil well cement additives, discusses the advantages and disadvantages of each anti-corrosion additive, summarizes the latest progress and challenges of anti-corrosion oil well cement, and aims to provide some reference for researchers in related fields.
1 Introduction
With the continuous development of the petroleum industry and the increasing exploitation of upstream oil and gas resources, the exploitation direction is gradually changing from simple reservoirs to complex reservoirs, from conventional oil and gas resources to unconventional reservoirs, and from single reservoirs to special reservoirs, which makes the existence of CO2, H2S and other acidic gases in oil and gas reservoirs an important feature of oilfield development in various countries (Ma et al., 2021; Li et al., 2018; Madirisha et al., 2022). In addition to the presence of the original acid gas in the reservoir, some stimulation measures (gas drive, acid fracturing, etc.) will also introduce corrosive gas and fluid in the formation into the cement sheath, resulting in the cement sheath sealing failure, which greatly reduces the cementing quality. The corrosion process is shown in Figure 1. The CO2 gas enriched in the formation dissolves in the formation fluid under a certain temperature and pressure, and then these acidic fluids gradually diffuse into the cement sheath. With the occurrence of a corrosion reaction, the concentration of the corrosion medium gradually decreases, and the corrosion products are different. If there is a large amount of corrosive medium, there will be a small concentration change, and the corrosion will continue. Finally, the casing will be corroded. In this process, the cement slurry formula must be adjusted (Lubaś et al., 2012; Xu et al., 2015; Szott and Miłek, 2021). Therefore, it is very necessary to introduce additives with certain anti-corrosion abilities into the cement slurry formulation system. Because the quality of the formula directly determines the durability and safety of the cement paste in the acidic formation environment, people have made some simple attempts and achieved certain results. Zhao et al. (2021) prepared a single-graded copolymer-modified permeable cement paste with styrene butadiene rubber (SBR). It was found that after adding SBR, the frost resistance of cement paste was improved and the mass loss rate was reduced. Compared with ordinary cement paste, double latex cement concrete has higher sulfate corrosion resistance and lower dry shrinkage strain. Shi. (2009) use broken waste glass as the main aggregate of cement slurry and use soda lime glass aggregate to react with alkaline substances in cement to improve the corrosion resistance of cement paste. Tian et al. (2021). prepared HSCRM cement slurry with hydrophobically modified tire particles as cement slurry additive. Compared with self-compacting cement slurry (SCM), the water absorption of HSCRM decreased by 72.1%, and the corrosion resistance of HSCRM was significantly improved. In addition, the 28 d modulus of rupture, compressive strength, and splitting tensile strength are 18.9%, 32.3%, and 17.2% lower than the uniaxial tensile strength respectively. However, conventional physical acid-resistant fillers (rubber, natural latex, plastic particles, etc.) are difficult to meet the current complex and special construction requirements (deep layer, high temperature, and high pressure, etc.), because their mixing effect with cement slurry is poor, and their mechanical properties are significantly deteriorated (Bergen et al., 2022; Omosebi et al., 2017a). Therefore, how effectively selecting and developing cement slurry with good corrosion resistance has become a new problem.
Based on the latest research reports in the field of petroleum cementing, this paper integrates some research results of anti-corrosion additive materials that have been proven effective or are still in the early stage of exploration. This paper summarizes the influencing factors, corrosion mechanism, corrosion test methods, and research status of anti-corrosion oil well cement additives, discusses the advantages and disadvantages of each anti-corrosion additive, summarizes the latest progress and challenges of anti-corrosion oil well cement, and aims to provide some reference for researchers in related fields (Table 1). At the same time, it also provides some solutions to the existing problems of oilfield cementing corrosion.
2 Analysis of cement stone corrosion factors
2.1 Liquid solid ratio
The liquid-solid ratio is the basic parameter that determines the compressive strength, durability, and a series of other physical properties of cement paste. The liquid-solid ratio affects the rheological property, cohesive structure of cement slurry, and the density of the hardened matrix by controlling the hydration water demand and particle spacing of cement particles per unit volume. Generally speaking, take the cement paste as an example. With the increase of the liquid-solid ratio, the cement paste is gradually diluted, the fluidity is improved, the thixotropy is weakened, the compressive strength is gradually reduced, and the water loss is gradually increased. In the presence of an acidic medium, the higher the liquid-solid ratio is, the larger the micropore in the cement matrix is, which is more conducive to the penetration of a corrosive medium, thus accelerating the damage rate of the matrix and increasing the degree of carbonation of cement paste.
2.2 Environmental factors
Among the environmental factors, temperature and pressure are two important parameters that affect the corrosion degree of cement paste. In addition, there are other parameters such as solution ion type and ion concentration that also affect the corrosion process of cement paste (Michelle et al., 2018; Li et al., 2021). However, in terms of the selection of cement paste corrosion factors under actual working conditions, these secondary parameters usually need to be ignored. To better simulate the corrosion environment of cement paste under actual working conditions, it is necessary to master the solubility relationship of CO2 acid corrosion medium under different temperatures and pressures to ensure the effectiveness of corrosion test results. The changing relationship of CO2 solubility under different temperatures and pressures is shown in Figure 2.
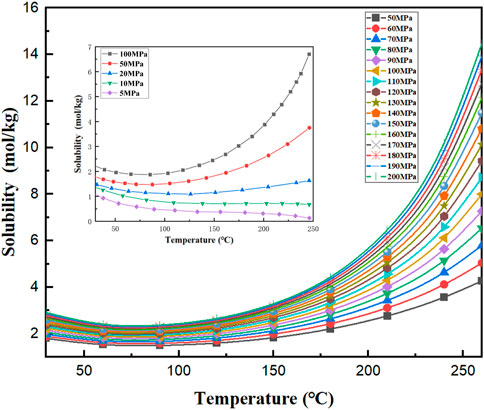
FIGURE 2. Solubility relationship of CO2 in pure water (Duan and Sun, 2003; Jasperson et al., 2015).
It can be seen from Figure 2 that under the same pressure, with the continuous increase of temperature, the solubility of CO2 in pure water decreases first and then increases. Under the conditions of constant pressure, high temperature/ultra-high temperature, the solubility of CO2 is affected by temperature. The solubility of CO2 increases regularly with the increase in temperature.
3 Corrosion mechanism of cement paste
3.1 Dissolution and decalcification of hydration products
In the corrosive curing environment, the cement paste is not only eroded by an acidic corrosion medium but also dissolved and decalcified by hydration products caused by ion exchange with the solution. When the solution does not contain acid corrosion medium or the medium concentration is low, because the Ca(OH)2 in the cement paste has a high solubility, after contact with deionized (Ca2+ concentration is 0) water, the difference between the internal and external concentration makes Ca2+ in the pores of the cement paste diffuse to the water, causing the Ca2+ concentration in the pores to gradually reduce; When there is a certain concentration of acid corrosion medium, Ca(OH)2 will suffer double effects of self-dissolution and acid corrosion, resulting in a large loss of Ca2+. To balance the concentration difference between the pores inside the cement paste and the solution, C-S-H in the cement paste matrix will release Ca2+ into the pore solution and retain the by-product amorphous SiO2, which is called decalcification (Berner, 1988; Berner, 1992; Reardon, 1992; Kulik and Kersten, 2010). Equations 1 and 2 describe the decalcification process of Ca(OH)2 and C-S-H in a pore solution.
The dissolution of Ca(OH)2 and the decalcification of C-S-H cause the loss of Ca2+ in the cement paste matrix, which will lead to the decline of the mechanical properties of the cement paste and the increase of porosity/permeability. Although this process is very slow, the presence of acidic corrosion media in the solution will accelerate this process (Zhang et al., 2022).
3.2 Corrosion mechanism
3.2.1 High-temperature corrosion mechanism of cement paste without silica fume
The main structures of hardened cement paste that form strength and plasticity are C-S-H and Ca(OH)2 respectively. The destruction of cement sheath structure in acid gas/fluid formation is mainly caused by a series of physical and chemical reactions between the acid medium and the main structure of cement paste (Eldin et al., 2009; Santra et al., 2009; Lecolier et al., 2010).
First, under the influence of the formation environment, gaseous CO2 gradually dissolves and diffuses into formation fluid. The reaction equation is as follows:
Subsequently, the hydration products of cement paste react with the corrosion medium to generate calcium carbonate (CaCO3) (Equations 5, 6, in which Ca(OH)2 will corrode before C-S-H, which is the main reason why the main product of cement paste in the early stage of corrosion is calcite type CaCO3. When C-S-H is completely corroded, a completely corroded area will be formed, which will reduce the internal porosity of cement paste, and increase the strength of the cement paste matrix when a small amount is generated. Based on the temperature and pressure changes in the corrosion process, the generated CaCO3 will exist in the form of calcite, aragonite, vaterite, and calcium carbonate hexahydrate (Bertos et al., 2004; Šavija and Luković, 2016).
With the continuous corrosion process of cement paste, the corrosion product CaCO3 formed previously gradually dissolves into Ca(HCO3)2 (Equation 7). At the same time, the acid corrosion medium will continue to consume Ca(OH)2 inside the cement paste to form leaching, while Ca(HCO3)2 will continue to react with residual Ca(OH)2 inside the cement paste to form CaCO3 again (Equation 8).
Based on the above corrosion process, the dynamic cycle of CaCO3 precipitation generation dissolution is established (Figure 3). With the consumption of Ca(OH)2 and the dissolution of CaCO3, the strength of the cement paste gradually declines, and the porosity and permeability of the cement paste matrix continue to increase until there is only amorphous/porous SiO2 left in the cement paste, resulting in the loss of the structural integrity of the cement paste, and ultimately leading to the failure of the interlayer sealing under the actual cementing conditions (Huet et al., 2011; Omosebi et al., 2017a).
Given the influence of temperature, pressure, and other factors on cement paste during corrosion. Therefore, the total reaction equilibrium equation of cement paste chemical degradation is established:
In this dynamic change process, a higher pressure value can improve the solubility of CO2 gas in an aqueous solution, which is conducive to the continuous progress of the total reaction equilibrium equation, thus improving the corrosion rate of cement paste. The influence of temperature on the corrosion process of cement paste is mainly reflected in the following two aspects: first, the change of temperature affects the hydration degree and chemical shrinkage of cement paste, the structural transformation of calcium silicate hydrate, the thermal expansion of cement matrix, the dissolution of Ca(OH)2 and the decalcification of C-S-H. Second, the temperature rise will change the phase state of CO2 and its solubility in the solution. Depending on the temperature and pressure, CO2 can exist in the form of supercritical, gaseous, liquid, or solid, and the corrosion form and degree of cement paste under different conditions are different.
3.2.2 High-temperature corrosion mechanism of cement paste mixed with silica fume
Different from the corrosion mechanism of cementing cement paste under medium and low-temperature corrosion environments, under ultra-high temperature corrosion conditions, since the addition of silicon powder in the formula can react with Ca(OH)2 inside the cement paste to generate silicate products (Equation 10), which weakens and eliminates the source of ion exchange for corrosion to a certain extent, and increases the content of cementitious components in the cement paste. In addition, silica fume will not transform with cement paste under high temperatures α-C2SH reaction generates strength crystals (Equations 11, 12, which leads to the better corrosion resistance of cement paste at higher temperatures.
Under ultra-high temperature conditions, some hydrated portland in the cement paste reacts with acidic corrosive media to generate CaCO3 and amorphous SiO2, which weakens the gel structure inside the cement paste, and the other part of the hydrated portland changes into a more stable high-temperature conversion phase (HC) due to temperature rise. With the continuous infiltration of an acidic corrosive medium, Ca(OH)2 in the cement paste matrix has been consumed by siliceous additives. Therefore, after a period of corrosion, there are both a corrosive crystalline phase and a hydrated silicate high-temperature conversion phase in the corrosion area. The process can be expressed by the following equation:
* HC(s) often contains wollastonite (Ca7(Si6O18) (CO3)·2H2O), fluorcarletonite (Ca4Si2O6(OH)2CO3), spurrite (Ca5(SiO4)2CO3) and tilleyite (Ca5(Si2O7) (CO3)2), etc (Zhang et al., 2013).
In combination with the corrosion process of cement paste without adding silica fume, the overall description of the corrosion process of cement paste under an ultra-high temperature environment is as follows: in the early stage of corrosion curing, due to the slow process of Ca(OH)2 consumption of silica admixture, the outer layer of cement paste contains a small amount of Ca(OH)2. When the cement paste contact with a large amount of water-wet CO2 solution, CO2 first reacts with the hydration product Ca(OH)2 of the surface layer of cement paste, The dense carbonization layer generated effectively improves the permeability of the cement paste and slows down the infiltration rate of the acidic medium. However, with the continuous infiltration of the acidic medium, Ca(OH)2 in the cement paste matrix has been completely consumed by siliceous additives, and the formation rate of ultra-high temperature hydration products has been greatly increased, and the density of the matrix has been further improved. At this time, there are only C-S-H and its high-temperature conversion phase HC in the cement paste, and the corrosion rate of C-S-H and HC is lower than that of Ca(OH)2 due to the corrosion difficulty of the corrosion medium on C-S-H and HC. With the continuous corrosion curing process, the leaching effect of the corrosion medium makes the surface layer of the cement paste loose and porous, and will continue to penetrate the cement paste matrix, react with C-S-H and HC, and completely consume them, generating CaCO3 crystals with large molar volume and amorphous SiO2 with poor cementation performance, causing serious damage to the cementation performance and compressive strength of the cement paste.
4 Research status of corrosion curing experimental methods
Different corrosion conditions correspond to different rules of cement paste corrosion. In addition to research on anti-corrosion materials, it is also necessary to set corrosion simulation conditions. Due to the complexity and variety of the actual corrosion status of cement paste in the well, to directly reflect the actual corrosion status of cement paste, the main parameters such as temperature, pressure, curing age, etc. in the well are simulated indoors.
Moroni et al. (2009) carried out indoor cement paste corrosion simulation experiments in the high-concentration CO2 environment in Kashagan Oilfield, Kazakhstan, under the experimental conditions of 93°C, 14 MPa, and 3 MPa CO2 partial pressure. It is found that the paste cement paste will form a large amount of CaCO3 when exposed to CO2, which will produce huge expansion stress in the cement sheath and crack it during expansion. To better simulate the corrosion process of cement paste under static conditions, Brandl et al. (2011) carried out the corrosion simulation experiment of cement paste under the experimental conditions of 149°C and 21 MPa in an improved high-temperature high-pressure curing kettle designed based on the bottom air inlet. Although the device can be used for dynamic pressure compensation, the corrosion temperature is limited and further temperature rise tests cannot be carried out. To better test the performance of corrosion samples, Fakhreldin et al. (2010) prepared cement stone samples according to standard core specifications. The experimental conditions were set at 90°C and 28 MPa. The CO2/water ratio in the corrosion curing kettle was 10% and 90% of the kettle volume respectively. Liu et al. (2011a) solidified the cement slurry for 48 h and then transferred it to a specific corrosion curing kettle for corrosion simulation. The experimental conditions were set at 145°C and 10 MPa. The low partial pressure gas was supplemented first, then the high partial pressure gas was supplemented, and finally, the total pressure was supplemented with CH4 to increase the pressure to the specified value. Zeng and Zhou, 2016 based on the actual working conditions of Puguang Gas Field, carried out the simulation experiment of cement paste corrosion in the presence of H2S/CO2 two-component gas. The experimental conditions were 95°C–150°C and the total corrosion pressure was 15 MPa. In terms of multi-component acid gas injection, H2S and CO2 gas are premixed before partial pressure supplement instead of being injected separately by multiple pipelines.
To sum up, in the current research on the corrosion of cementing cement paste, the autoclave pressure under the simulated environment is above 14 MPa. Because of the international industry standard that the total pressure of cement paste needs to be maintained at 21 MPa for routine maintenance, to meet this condition to ensure that no large pressure loss will occur during the experiment, the autoclave pressure in the corrosion experiment should also be consistent with it.
5 Anti-Corrosion oil well cement additive
5.1 Corrosion-resistant powder
The compatibility of rubber and acid-resistant microparticles with cement paste is poor. The anti-corrosion powder has a perfect blending effect with cement paste and can effectively fill the micropores in the cement paste. This kind of anti-corrosion powder usually has a stable solid phase that is difficult to react with an acid medium or will not affect the basic performance of cement paste after reacting with the acid medium.
Srivastava et al. (2020) explored the effect of hydroxyapatite (HA) on the corrosion resistance of H-grade oil well cement paste under high temperature and high pressure and found that 5% HA can effectively inhibit the carbonation process of cement paste, but also reduce the compressive strength of cement paste (an average of 17%), and will cause cracks in the cement paste when it is above 220°C, causing the cement paste to expand. Mei et al. (2019) studied the effect of alkaline zinc carbonate (BZC) on oil well cement paste under the environment of high temperature and high-pressure H2S and found that the compressive strength of cement paste added with 1.5% BZC can still maintain more than 20 MPa after 28 days of corrosion. In the mechanism analysis, the presence of BZC makes H2S react with Zn first, reducing the dissolution of the Ca phase, and generating an insoluble ZnS phase effectively improving the internal volume density of cement paste, thus improving the corrosion resistance of cement paste. Mahmoud and Elkatatny, 2020 added olive residue to the Saudi G grade oil well cement formula and explored the properties of cement paste under 130°C and 10 MPa CO2. It is found that the carbonation depth of cement paste with 0.1% olive residue added 20 days after carbonation is 1469 µ m down to 1269 µ m. The permeability of cement paste is 33.9% lower than that of cement paste. This is because olive residue reduces the permeability of oil well cement paste and weakens the leaching of Ca2+, thus improving the corrosion resistance of cement paste in CO2-saturated brine. Xu et al. (2022) used natural zeolite as microporous filling material and stearic acid as surfactant to prepare a hydrophobic, corrosion-resistant super hydrophobic cement slurry. When the dosage of natural zeolite is 15%, the water absorption of super hydrophobic cement slurry is only 0.61%, and the wetting angle of water is greater than 150°. The addition of natural zeolite effectively improves the microstructure of cement paste, improves its anti-corrosion performance, and increases the compressive strength by 14%. Lei et al. (2022) explored the influence of hydrophobically modified waste clam shell powder (ACP) on the corrosion performance of cement paste, and found that the strong hydrophobicity of ACP (wetting angle greater than 150°) reduced the attraction of cement paste pores to water, and formed a hydrophobic film on the surface of cement paste to block corrosive ions. Compared with the conventional cement paste, the corrosion current density and corrosion tendency of the cement paste decreased significantly. Hussien et al. (2022) explored the influence of nano waste glass (NWG) on the corrosion performance of cement paste. They found that when 3% NWG was used to replace cement, the compressive strength of cement paste was increased by 32.4%, and the bending strength was increased by 13%. In addition, NWG effectively reduced the anodic and cathodic overpotentials, reduced the corrosion current density, and thus improved the corrosion resistance of cement paste.
The corrosion-resistant powder has good compatibility with the cement slurry, which is conducive to slurry preparation and pumping. However, since the corrosion-resistant powder does not have gelling properties, it will affect the mechanical properties of the cement stone when the dosage is increased, so it is reasonable to use it as an auxiliary anti-corrosion additive.
5.2 Alkali-activated mineral
Alkali-activated cement is also called geopolymer cement, which is rich in silica, alumina, and calcium. At present, the commonly used alkali-activated minerals include fly ash, slag, and metakaolin. The commonly used alkali active agents include sodium silicate, potassium silicate, and sodium hydroxide. Alkali-activated minerals have a three-dimensional network structure in which [SiO4] and [AlO4] tetrahedrons are randomly distributed. The basic structural unit of this network is a silicon aluminum oxide chain (Si-O-Al-O-Si-O-Si-O-), etc (Figure 4). It is precise because alkali-activated minerals have a chain structure similar to organic polymerization, and can form chemical bonds with [SiO4] and [AlO4] tetrahedrons on the surface of mineral particles through dehydrogenation, which has the common characteristics of inorganic and organic compounds (Kong et al., 2009; Zheng et al., 2019; Du et al., 2018). Alkali-activated minerals will also form recrystallized phase after being activated by the activator and then fill into the hydration pores, thus reducing the overall permeability of cement stone (Wang and Noguchi, 2020).
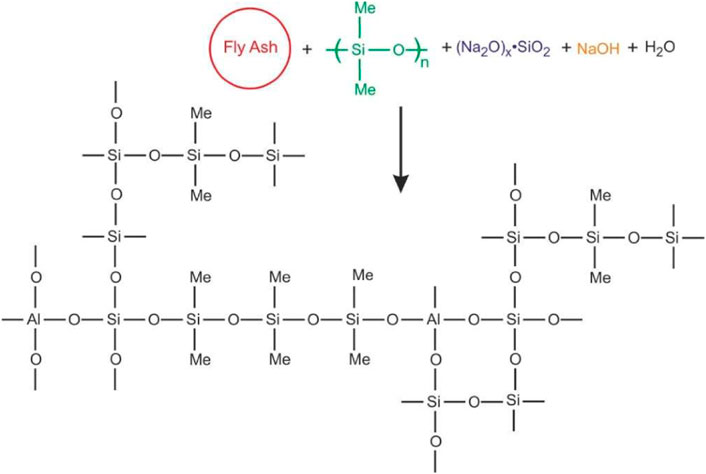
FIGURE 4. Schematic diagram of bonding reaction in the alkali activation process of fly ash (Roviello et al., 2015).
Bechar and zerrouki et al. (2018) explored the influence of natural pozzolanic ash (NP) on the corrosion resistance of oil well cement paste. Replacing cement with NP has a beneficial effect on durability. They found that the addition of NP can form calcium silicate hydrate (C-S-H) and calcium aluminate hydrate (C-A-H) by consuming free Ca(OH)2, which is helpful to improve the compactness of cement paste. When the addition of NP is 20%, the porosity of cement paste decreases by 4%, and the penetration of chloride is reduced by more than 50%. Lau et al. (2019) pointed out that the addition of slag reduces the CaO content in oil well cement, and reacts with silicate components to form C-S-H gel, thus reducing the permeability of cement stone and improving its CO2 corrosion resistance. Meanwhile, Suppiah et al. (2020) experiments found that slag can effectively reduce the elastic modulus of cement stone and improve its deformation resistance. Zhao et al. (2022) studied the corrosion of alkali-activated slag cement paste in different acidic media and found that the slag cement paste in acetic acid was more deteriorated than that in sulfuric acid. They believed that this was mainly caused by the products and structure of the corrosion layer, because the cement paste would form a high porosity corrosion layer in acetic acid, while in sulfuric acid, because of the presence of CaO in the cement paste matrix, it could form crystals with the pore filling effect. Ridha et al. (2020) analyzed the changes in the corrosion process of alkali-activated fly ash cement and found that the main framework of geopolymer cement is Si-O-Al-O-Si, and the formation of carbonation products will not affect the strength of cement paste. Pandey and Kumar, 2020 used rice straw ash (RSA) and micro silica (MS) as cement anti-corrosion additives, and found that the strength loss rate and quality loss rate of cement paste mixed with 10% RSA and 5% MS (R2M3) were 3.69% and 2.19% respectively after 28 and 58 days of corrosion, showing good corrosion resistance. Dacuan et al. (2021) explored the influence of bamboo leaf ash (BLASH) on the corrosion performance of cement paste, and found that the initial compressive strength of cement paste decreased when 10% BLASH was added, but it showed good corrosion resistance. The mass loss in acid medium was only 0.5%, and the reduction rate of compressive strength was only 0.03%. In addition, alkali-activated cementitious materials such as metakaolin, steel slag, and silica fume also have good application effects in improving the matrix strength of cement paste, improving the internal pore distribution of cement paste, and reducing the permeability (Bu et al., 2016; Liu et al., 2021).
Alkali-activated minerals have good compatibility with oil well cement and can form secondary gelling after cement stone is consolidated, to fill the cement stone micropores. However, the amount and type of activator will affect the generation time of the secondary cementitious structure, which usually needs to be adjusted in combination with the cement slurry construction formula. In addition, minerals such as fly ash will reduce the density of cement slurry, so it also needs to be considered appropriate.
5.3 Aqueous polymer
Water-soluble polymers are widely used in medicine, biology, the chemical industry, and other fields. The curing process of polymers, such as water-soluble polymers of acrylamide, mainly uses macromolecular straight-chain monomers in combination with crosslinking agents and initiators to solidify them into a honeycomb or network-like gelling structure system (Figure 5). These gelling structures can effectively cover the easily corroded hydration product matrix, thus preventing the invasion of corrosive media (Sun et al., 2012). In addition, the cured polymer will also fill the pores of the cement stone to reduce its permeability and further improve the corrosion resistance of the cement stone (Liu et al., 2011b). At the same time, the polymer can also be combined with certain additives (thixotropic agent, constant rheology agent, etc.) to significantly improve the toughness of cement paste and improve the cementing performance between the cementing cement sheath and the first and second interface layers (Guo et al., 2020; Bu et al., 2022).
Chen et al. (2011) used self-developed water-soluble linear crosslinked polymer (FH) as an anti-corrosion additive and used FH to undergo a polycondensation reaction with acid to form a network membrane structure, thus preventing the corrosion of acid and alkali substances. Zhi et al. (2022) explored the influence of polyacrylamide on the carbonation behavior of cement paste, and found that polyacrylamide promoted the formation of calcite with small crystal size and CaCO3 with poor crystallinity, and transformed coarse pores into gel pores, thereby reducing porosity, improving the compactness of cement paste matrix, and thus improving the corrosion resistance of cement paste. Yuan et al. (2018) used the film-forming and filling effects of nano silica latex (NL) to reduce the original permeability of cement paste and weakened the penetration and expansion effects in the corrosion process. In addition, NL can also consume Ca(OH)2 in the cement matrix to reduce the Ca/Si ratio of cement paste. It was found that the compressive strength of cement paste with 4% NL was slightly improved, and the original permeability, specific surface area, and average pore diameter were significantly reduced by 3.35 times, 23.14% and 35.38%, respectively. Li et al.(2021)a added nano silica suspension into acrylic acid lotion to prepare nano modified polymer anti-corrosion material (PMC), and measured the impact of this material on the corrosion performance of cement paste. It was found that PMC can effectively fill the internal micropores of cement paste, reduce the porosity. When the addition of nano SiO2 was 0.5%, the chloride ion corrosion resistance rate of cement paste was reduced by 7.1 times. Zhang et al. (2020) prepared a soap-free lotion (PSAC) with a core-shell structure using sodium phenylene sulfonate (SSS) and nano-SiO2 (SSS/SiO2) as raw materials. The results under CO2 corrosion showed that the pore volume (>50 nm) of cement decreased by 0.24 times, and a C-S-H gel structure with a low Ca/Si ratio and high polymerization degree was formed in the cement stone matrix. Zhang et al. (2021) used self-synthesized new material Environmental Responsive Microspheres (ERPM) as the anti-corrosion additive for oil well cement. ERPM has good environmental response characteristics and temperature resistance and can be converted into membrane form in an acidic environment. Based on the acid response characteristics, the polymer film formed by ERPM effectively shields the direct contact between the corrosion medium and the hydration products, maintains the structural integrity of the hydration products, and improves the corrosion resistance of the cement paste.
Polymer anti-corrosion admixture has excellent film-forming and coating functions, and can effectively isolate the infiltration of the acid medium. It is also one of the main research directions of anti-corrosion admixture at present. However, polymer anti-corrosion admixture generally has poor temperature resistance and stability, so it needs to focus on temperature resistance modification and improve compatibility with cement slurry.
5.4 Aqueous resin
Epoxy resin has the advantages of high adhesive strength, good stability, low curing shrinkage, and excellent chemical resistance. In recent years, there have been cases of applying resin to the petroleum field (Li et al., 2021b). By blending epoxy resin into hydrophilic resin lotion, the mixing effect with cement slurry can be effectively improved (Figure 6). Compared with traditional polymer lotion, cured resin lotion has better mechanical properties, flexibility, and corrosion resistance, and has the potential to significantly improve the performance of cement slurry.
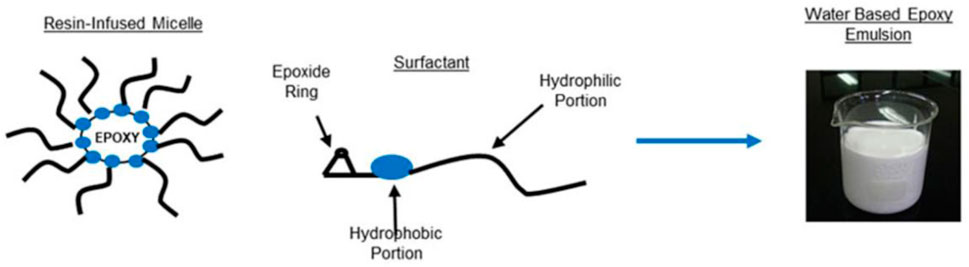
FIGURE 6. The basic composition of a high-performance water-based epoxy resin (Chemical Weekly Group., 2021).
Peng et al. (2022) used 2-Acrylamido-2- Methyl Propane Sulfonic Acid (AMPS) to modify epoxy resin (E-54) to obtain waterborne epoxy resin (WER). It was found in the experiment that the resin particles after WER curing were filled in the micropores of cement stone. The three-dimensional network structure formed after curing can separate the hydration products from the acidic medium, and improve the corrosion resistance of cement stone while reducing the permeability. Yang. (2021) grafted epoxy resin E-44 with AMPS as the modifying monomer, and the compressive strength reduction rate of the modified cement paste after corrosion was significantly reduced. Fu et al. (2021) prepared non-ionic water-based resin cement stone. The compressive strength is 2.5 times higher than that of pure cement stone, and the elastic modulus is reduced by 53.4%. After demulsification, the resin is uniformly distributed in the cement stone in the form of liquid film and partially cured gel. Qu et al. (2021) prepared super hydrophobic anion exchange resin cement slurry (S-AERC) by adding anion exchange resin and stearic acid surfactant. The resistance of different cement paste samples to chloride corrosion was measured by electrochemical and chloride ion distribution tests. It was found that S-AERC mortar had good corrosion resistance, and the corrosion resistance rate was 98.60%. Chi et al. (2020) used furfuryl glycidyl ether (FGE) and maleic anhydride modified polyethylene (D230-M) as reaction solvents to prepare a new environment-friendly in-situ crosslinked epoxy preservative through Diels Alder reaction. Due to its low viscosity, the epoxy preservative can effectively penetrate into the internal micro channels of the cement paste. The experiment also found that the epoxy preservative has low volatility, which can effectively improve the mechanical properties and corrosion resistance of the cement paste. Huo et al. (2022) prepared a waterborne resin anti-corrosion admixture (WEP) based on sodium styrene sulfonate and epoxy resin E-54. The experiment found that WEP had good thermal stability and self-emulsifying performance. After 90 days of corrosion curing at 180°C and 10 MPa partial pressure of CO2, its compressive strength decline rate was only 14.7% and CaCO3 content was only 0.25%. This is because WEP can form a coating film in the cement paste matrix, which can improve the corrosion resistance of cement paste by blocking the contact between hydrated cement and an acidic medium. In addition, the use of alkali-activated materials based on water-based resin is also a means to improve the corrosion resistance of cement paste (Du et al., 2016).
The development of resin-based anti-corrosion cement is still at the initial stage, but the application effect of resin-based anti-corrosion cement is very significant, especially under medium and low-temperature conditions. At the same time, the biggest difficulty of resin-based cement is similar to that of polymer cement, and the performance decline is obvious under high temperatures. The stability of water-based resin lotion and the blending effect of cement slurry will be the next development focus.
6 Conclusion
For a long time, the corrosion prevention of cement paste has been an important problem in the field of oil cementing. By summarizing the influencing factors, corrosion mechanism, corrosion test methods and research status of anti-corrosion oil well cement additives, Although the anti-corrosion powder and alkali-activated mineral belong to admixtures with good compatibility, the dosage of anti-corrosion powder should be reasonably controlled, and the type of alkali-activated mineral should be selected according to the actual working conditions of oil well cement (high density, low density, consolidation time, etc.). The water-based polymer anti-corrosion additive reduces the permeability of cement paste by film formation, but it also weakens the cross-linking degree between hydration products. Therefore, how to improve the corrosion resistance of cement paste while ensuring that the basic performance of cement paste is not affected. Resin-based anti-corrosion admixture has excellent anti-corrosion performance and can significantly improve the toughness and mechanical properties of cement stone. The next development difficulty will be to improve the high-temperature resistance of resin-based cement stone(Xinhua, 2021).
Author contributions
YZ investigated and processed the data, pointed out the framework of the paper, made a summary and analysis, and completed the writing of the article. At the same time, YZ reviewed the paper and supported the project. JW and XY conducted translation correction, and XZ conducted final review.
Funding
The authors would like to acknowledge the Doctoral Fund Project of Chongqing Institute of Industry and Technology (Grant No. 2022G2YBS2K2-12).
Conflict of interest
The author declares that the research was conducted in the absence of any commercial or financial relationships that could be construed as a potential conflict of interest.
Publisher’s note
All claims expressed in this article are solely those of the authors and do not necessarily represent those of their affiliated organizations, or those of the publisher, the editors and the reviewers. Any product that may be evaluated in this article, or claim that may be made by its manufacturer, is not guaranteed or endorsed by the publisher.
References
Bechar, S., and Zerrouki, D. (2018). Effect of natural pozzolan on the fresh and hardened cement slurry properties for cementing oil well. World J. Eng. 15 (4), 513–519. doi:10.1108/WJE-10-2017-0337
Bergen, S., Zemberekci, L., and Nair, S. (2022). A review of conventional and alternative cementitious materials for geothermal wells. Renew. Sustain. Energy Rev. 161 (6), 112347–112414. doi:10.1016/j.rser.2022.112347
Berner, U. R. (1988). Modelling the incongruent dissolution of hydrated cement minerals. Radiochim. Acta 44 (452), 387–394. doi:10.1524/ract.1988.4445.2.387
Berner, U. R. (1992). Evolution of pore water chemistry during degradation of cement in a radioactive waste repository environment. Waste Manag. 12 (2–3), 201–219. doi:10.1016/0956-053X(92)90049-O
Bertos, M. F., Simons, S., Hills, C. D., and Carey, P. (2004). A review of accelerated carbonation technology in the treatment of cement-based materials and sequestration of CO2. J. Hazard. Mater. 112 (3), 193–205. doi:10.1016/j.jhazmat.2004.04.019
Brandl, A., Cutler, J., Seholm, A. J., Sansil, M., and Braun, G. (2011). Cementing solutions for corrosive well environments. SPE Drill. Complet. 26 (2), 208–219. doi:10.2118/132228-PA
Bu, Y., Du, J., Guo, S., Liu, H., and Huang, C. (2016). Properties of oil well cement with high dosage of metakaolin. Constr. Build. Mater. 112 (2), 39–48. doi:10.1016/j.conbuildmat.2016.02.173
Bu, Y., Xu, M., Liu, H., Zhou, A., Du, J., Yang, X., et al. (2022). A novel hydrophobically associating water-soluble polymer used as constant rheology agent for cement slurry. R. Soc. open Sci. 9 (2), 211170–211218. doi:10.1098/rsos.211170
Chemical Weekly Group (2021). Water-based epoxy technologies for metal coating applications. Chem. Wkly. 66 (23), 139–146.
Chen, D., Zhang, Y., Zhao, C., Wu, Z., and Yao, Y. (2011). Prevention of oil well cement h by water soluble polymer_ Study on H2S corrosion. Drill. Fluid & Complet. Fluid 28 (3), 56–59. doi:10.3969/j.issn.1001-5620.2011.03.017
Chi, J., Zhang, G., Xie, Q., and Ma, C. (2020). High performance epoxy coating with cross-linkable solvent via Diels-Alder reaction for anti-corrosion of concrete. Prog. Org. Coatings 139 (11), 105473–105477. doi:10.1016/j.porgcoat.2019.105473
Dacuan, C., Abellana, V., and Canseco, H. (2021). Assessment and evaluation of blended cement using bamboo leaf ash BLASH against corrosion. Civ. Eng. J. 7 (6), 1015–1035. doi:10.28991/cej-2021-03091707
Du, J., Bu, Y., Cao, X., Zhonghou, S., and Baojiang, S. (2018). Utilization of alkali-activated slag based composite in deepwater oil well cementing. Constr. Build. Mater. 186 (7), 114–122. doi:10.1016/j.conbuildmat.2018.07.068
Du, J., Bu, Y., Shen, Z., Hou, X., and Huang, C. (2016). Effects of epoxy resin on the mechanical performance and thickening properties of geopolymer cured at low temperature. Mater. Des. 109 (7), 133–145. doi:10.1016/j.matdes.2016.07.003
Duan, Z., and Sun, R. (2003). An improved model calculating CO2 solubility in pure water and aqueous NaCl solutions from 273 to 533 K and from 0 to 2000 bar. Chem. Geol. 193 (3-4), 257–271. doi:10.1016/S0009-2541(02)00263-2
Eldin, Y. F., Irvine-Fortescue, J., Grieve, J., Taoutaou, S., Jain, B., Kalbani, S., et al. (2009). “The use of specialized cement to ensure long term zonal isolation for sour wells in south Oman,” in Proceedings of the International Petroleum Technology Conference Society of Petroleum Engineers, 7–9.Doha, Qatar, December 2009 doi:10.2523/IPTC-13400-MS
Fakhreldin, Y. E., Al-Sharji, H. H., Ruwehy, A. A., Saadi, K., Taoutaou, S., and Al-Kalbani, S. (2010). Advanced cement system for acid gas injection wells. Soc. Petroleum Eng. doi:10.2118/132345-MS
Fu, H., Guo, X., Qu, X., Gu, T., and Li, M. (2021). High-quality cementing slurry with epoxy resin emulsion. Nat. Gas. Ind. 41 (11), 115–121. doi:10.3787/j.issn.1000-0976.2021.11.012
Guo, S., Bu, Y., Zhou, A., Du, J., and Cai, Z. (2020). A three components thixotropic agent to enhance the thixotropic property of natural gas well cement at high temperatures. J. Nat. Gas Sci. Eng. 84 (10), 103699–103724. doi:10.1016/j.jngse.2020.103699
Huet, B., Tasoti, V., and Khalfallah, I. (2011). A review of Portland cement carbonation mechanisms in CO2 rich environment. Energy Procedia 4 (6), 5275–5282. doi:10.1016/j.egypro.2011.02.507
Huo, H., Xie, T., Xu, J., Zhou, Z., and He, S. (2022). Preparation and evaluation of water-based epoxy resin on corrosion resistance enhancement for oil well cement. Fine Chem. 2 (10), 1–10. doi:10.13550/j.jxhg.20220399
Hussien, R., Abd el-Hafez, L., Mohamed, R., Faried, A. S., and fahmy, N. G. (2022). Influence of nano waste materials on the mechanical properties, microstructure, and corrosion resistance of self-compacted concrete. Case Stud. Constr. Mater. 16 (6), 008599–e917. doi:10.1016/j.cscm.2021.e00859
Jasperson, L. V., Kang, J. W., Lee, C. S., Macklin, D., Mathias, P. M., McDougal, R. J., et al. (2015). Experimental determination of the equilibrium water content of CO2 at high pressure and low temperature engineering. J. Chem. Eng. Data ACS J. Data 60 (9), 2674–2683. doi:10.1021/acs.jced.5b00320
Kong, D., Zhang, J., Ni, T., Jiang, J., and Fang, C. (2009). Research progress of alkali activated cementitious materials and concrete. J. Chin. Ceram. Soc. 37 (1), 151–159. doi:10.3321/j.issn:0454-5648.2009.01.029
Kulik, A., and Kersten, M. (2010). Aqueous solubility Diagrams for cementitious waste stabilization systems: II, EndMember stoichiometries of ideal calcium silicate hydrate solid solutions. J. Am. Ceram. Soc. 84 (12), 3017–3026. doi:10.1111/j.1151-2916.2001.tb01130.x
Lau, C., Duong, A., Taoutaou, S., Kumar, A., and Toha, R. (2019). “Successful application of slag based flexible cement for resilient and carbon dioxide corrosion resistance,” in Proceedings of the SPE Oil and Gas India Conference and Exhibition. Bali, Indonesia,October 2019.
Lecolier, E., Rivereau, A., Ferrer, N., Audibert, A., and Longaygue, X. (2010). Durability of oilwell cement formulations aged in H2S-containing fluids. SPE Drill. Complet. 25 (1), 90–99. doi:10.2118/99105-MS
Lei, L., Wang, Q., Li, X., and Shi, Z. (2022). Fabrication of amphiphobic concrete coating with good abrasion resistance and anti-oil adhesion properties by using waste clam powder. Constr. Build. Mater. 327 (2), 126862–126910. doi:10.1016/j.conbuildmat.2022.126862
Li, G., Ding, Y., Gao, T., Qin, Y., Lv, Y., and Wang, K. (2021b). Chloride resistance of concrete containing nanoparticle-modified polymer cementitious coatings. Constr. Build. Mater. 299 (9), 123736–123812. doi:10.1016/j.conbuildmat.2021.123736
Li, M., Sun, K., and He, M. (2021a). Effects of waterborne epoxy resin on the mechanical properties and microstructure of oil-well cement. J. Dispersion Sci. Technol. 2021 (4), 2107–2114. doi:10.1080/01932691.2021.1915158
Li, W., Nan, Y., You, Q., and Jin, Z. (2021). CO2 solubility in brine in silica nanopores in relation to geological CO2 sequestration in tight formations: Effect of salinity and pH. Chem. Eng. J. 411 (5), 127626–127712. doi:10.1016/j.cej.2020.127626
Li, Y., Kang, Z., Xue, Z., and Zheng, S. (2018). Theories and practices of carbonate reservoirs development in China. Petroleum Explor. Dev. 45 (4), 712–722. doi:10.1016/S1876-3804(18)30074-0
Liu, H., Bu, Y., Zhou, A., Du, J., Zhou, L., and Pang, X. (2021). Silica sand enhanced cement mortar for cementing steam injection well up to 380°C. Constr. Build. Mater. 308 (11), 125142–125210. doi:10.1016/j.conbuildmat.2021.125142
Liu, Z., Wang, Q., Song, P., and Tian, L. F. (2011a). Influence of acrylamide on corrosion-resistance and strength of cement pastes. Adv. Mater. Res. 261-263 (1), 318–322. doi:10.4028/www.scientific.net/AMR.261-263.318
Liu, Z. Y., Sun, J., Nasr-El-Din, H. A., Shan, H., and Xiao, Z. (2011b). “Advanced cementing systems for deep sour gas wells,” in Proceedings of the SPE/DGS Saudi Arabia Section Technical Symposium and Exhibition. May 2011, Al-Khobar, Saudi Arabia, doi:10.2118/149063-MS
Lubaś, J., Szott, W., and Jakubowicz, P. (2012). Effects of acid gas reinjection on CO2 concentration in natural gas produced from borzęcin reservoir. Nafta-Gaz 68 (7), 405–410. doi:10.1002/(SICI)1097-0282
Madirisha, M., Hack, R., and Van der Meer, F. (2022). The influence of chelating agents on clays in geothermal reservoir formations: Implications to reservoir acid stimulation. Geothermics 99 (2), 102305–102313. doi:10.1016/j.geothermics.2021.102305
Mahmoud, A., and Elkatatny, S. (2020). Improved durability of Saudi Class G oil-well cement sheath in CO2 rich environments using olive waste. Constr. Build. Mater. 262 (11), 120623–120711. doi:10.1016/j.conbuildmat.2020.120623
Mei, K., Cheng, X., Zhang, L., Guo, X., Zhuang, J., and Zhang, C. (2019). Self-healing mechanism of Zn-enhanced cement stone: An application for sour natural gas field. Constr. Build. Mater. 227 (12), 116651–116710. doi:10.1016/j.conbuildmat.2019.08.032
Michelle, T., Raoof, G., and Ekhlasur, R. M. (2018). Cement degradation in CO2 storage sites: A review on potential applications of nanomaterials. J. Petroleum Explor. Prod. Technol. 9 (5), 329–340. doi:10.1007/S13202-018-0490-Z
Moroni, N., Santra, A. K., Ravi, K., and Hunter, W. (2009). “Holistic design of cement systems to survive CO2 environment,” in Proceedings of the SPE Annual Technical Conference and Exhibition.October 2009, New Orleans, LO, USA doi:10.2118/124733-MS
Omosebi, A., Ahmed, M., and Shah, N. (2017a). Mechanisms of cement degradation in HPHT carbonic acid environment. SPE International Conference on Oilfield Chemistry.OnePetro, Richardson, TX, USA doi:10.2118/184567-MS
Pandey, A., and Kumar, B. (2020). Investigation on the effects of acidic environment and accelerated carbonation on concrete admixed with rice straw ash and microsilica. J. Build. Eng. 29 (5), 101125–101213. doi:10.1016/j.jobe.2019.101125
Peng, Z., Lv, F., Feng, Q., and Zheng, Y. (2022). Enhancing the CO2-H2S corrosion resistance of oil well cement with a modified epoxy resin. Constr. Build. Mater. 326 (4), 126854. doi:10.1016/j.conbuildmat.2022.126854
Qu, L., Wang, Q., Mao, J., Xu, S., Zhang, H., Shi, Z., et al. (2021). Study of anti-chlorine corrosion of anion exchange resin based superhydrophobic cement mortar in chloride salt environment. Constr. Build. Mater. 313 (11), 125540–125610. doi:10.1016/j.conbuildmat.2021.125540
Reardon, J. (1992). Problems and approaches to the prediction of the chemical composition in cement/water systems. Waste Manag. 12 (2–3), 221–239. doi:10.1016/0956-053X(92)90050-S
Ridha, S., Setiawan, R., Pramana, A., and Abdurrahman, M. (2020). Impact of wet supercritical CO2 injection on fly ash geopolymer cement under elevated temperatures for well cement applications. J. Petroleum Explor. Prod. Technol. 10 (2), 243–247. doi:10.1007/s13202-019-0693-y
Roviello, G., Menna, C., Tarallo, O., Ricciotti, L., Ferone, C., Colangelo, F., et al. (2015). Preparation, structure and properties of hybrid materials based on geopolymers and polysiloxanes. Mater. Des. 87 (12), 82–94. doi:10.1016/j.matdes.2015.08.006
Santra, A., Reddy, B. R., Liang, F., and Fitzgerald, R. (2009). Reaction of CO2 with portland cement at downhole conditions and the role of pozzolanic supplements. SPE Int. Symposium Oilfield Chem. doi:10.2118/121103-MS
Šavija, B., and Luković, M. (2016). Carbonation of cement paste: Understanding, challenges, and opportunities. Constr. Build. Mater. 117 (8), 285–301. doi:10.1016/j.conbuildmat.2016.04.138
Shi, C. (2009). Corrosion of glasses and expansion mechanism of concrete containing waste glasses as aggregates. J. Mater. Civ. Eng. 21 (10), 529–534. doi:10.1061/(ASCE)0899-1561(2009)21:10(529)
Srivastava, A., Ahmed, R., and Shah, S. (2020). Carbonic acid resistance of hydroxyapatite-containing cement. SPE Drill. Complet. 35 (1), 088–099. doi:10.2118/193585-PA
Sun, S., Xiao, Y., Fei, Y., and Zhao, Y. (2012). Research on anti-corrosion properties of polymer cement-based composite material. Surf. Technol. 41 (5), 60–63. doi:10.16490/j.cnki.issn.1001-3660.2012.05.018
Suppiah, R., Rahman, S., Shafiq, N., and Irawan, S. (2020). Uniaxial compressive strength of geopolymer cement for oil well cement. J. Petroleum Explor. Prod. Technol. 10 (1), 67–70. doi:10.1007/s13202-019-0704-z
Szott, W., and Miłek, K. (2021). Analysis of reservoir fluid migration in the process of CO2 sequestration in a partially depleted gas reservoir. Energies 14 (19), 6398–6423. doi:10.3390/en14196398
Tian, L., Qiu, L., and Liu, Y. (2021). Fabrication of integrally hydrophobic self-compacting rubberized mortar with excellent waterproof ability, corrosion resistance and stable mechanical properties. Constr. Build. Mater. 304 (10), 124684. doi:10.1016/j.conbuildmat.2021.124684
Wang, W., and Noguchi, T. (2020). Alkali-silica reaction (asr) in the alkali-activated cement (aac) system: A state-of-the-art review. Constr. Build. Mater. 252 (8), 119105–119114. doi:10.1016/j.conbuildmat.2020.119105
Xinhua, M. A. (2021). Extreme utilization” development theory of unconventional natural gas. Petroleum Explor. Dev. 48 (2), 381–394. doi:10.1016/S1876-3804(21)60030-7
Xu, Q., Li, Z., Zhang, H., and Cheng, X. (2015). Characterization of the unidirectional corrosion of oilwell cement exposed to H2S under high-sulfur gas reservoir conditions. Rsc Adv. 5 (87), 71529–71536. doi:10.1039/c5ra12481f
Xu, S., Wang, Q., Wang, N., Song, Q., and Li, Y. (2022). Effects of natural zeolite replacement on the properties of superhydrophobic mortar. Constr. Build. Mater. 348 (7), 128567–128613. doi:10.1016/j.conbuildmat.2022.128567
Yang, Q. (2021). Preparation and properties of water-based resin A-E44 for oil well cement anticorrosion. Chin. J. Synthetic Chem. 29 (11), 939–944. doi:10.15952/j.cnki.cjsc.1005-1511.21195
Yuan, B., Wang, Y., Yang, Y., Xie, Y., and Li, Y. (2018). Wellbore sealing integrity of nanosilica-latex modified cement in natural gas reservoirs with high H2S contents. Constr. Build. Mater. 192 (12), 621–632. doi:10.1016/j.conbuildmat.2018.10.165
Zeng, Y., and Zhou, S. (2016). “Study on corrosion mechanism of sour gas to cement stone,” in Proceedings of the IADC/SPE Asia Pacific Drilling Technology Conference.August 2016, Singapore doi:10.2118/180681-MS
Zhang, B., Zou, C., Peng, Z., Zheng, Y., and Zhang, J. (2020). Study on the preparation and anti-CO2 corrosion performance of soap-free latex for oil well cement. ACS omega 5 (36), 23028–23038. doi:10.1021/acsomega.0c02729
Zhang, J., Wang, C., and Peng, Z. (2021). Corrosion integrity of oil cement modified by environment responsive microspheres for CO2 geologic sequestration wells. Cem. Concr. Res. 143 (5), 106397. doi:10.1016/j.cemconres.2021.106397
Zhang, Y. Q., Radha, V., and Navrotsky, A. (2013). Thermochemistry of two calcium silicate carbonate minerals: Scawtite, Ca7(Si6O18)(CO3).2H2O, and spurrite, Ca5(SiO4)2(CO3). Geochimica Cosmochimica Acta 115 (8), 92–99. doi:10.1016/j.gca.2013.03.031
Zhang, Y., Xu, M., Song, J., Wang, C., Wang, X., and Hamad, B. A. (2022). Study on the corrosion change law and prediction model of cement stone in oil wells with CO2 corrosion in ultra-high-temperature acid gas wells. Constr. Build. Mater. 323 (3), 125879–125914. doi:10.1016/j.conbuildmat.2021.125879
Zhao, C., Jia, X., Yi, Z., Li, H., and Peng, Y. (2021). Mechanical performance of single-graded copolymer-modified pervious concrete in a corrosive environment. Materials 14 (23), 7304. doi:10.3390/ma14237304
Zhao, W., Fan, Z., Li, X., Kong, L., and Zhang, L. (2022). Characterization and comparison of corrosion layer microstructure between cement mortar and alkali-activated fly ash/slag mortar exposed to sulfuric acid and acetic acid. Materials 15 (4), 1527. doi:10.3390/ma15041527
Zheng, W., Zhou, M., and Wang, Y. (2019). Review of alkali activated cementitious materials. J. Build. Struct. 40 (1), 28–39. doi:10.14006/j.jzjgxb.2019.01.003
Keywords: anticorrosive, cement, CO2, acid medium, review
Citation: Zhang Y, Wen J, Yin X and Zhang X (2022) Application of anticorrosive materials in cement slurry: Progress and prospect. Front. Mater. 9:1110692. doi: 10.3389/fmats.2022.1110692
Received: 29 November 2022; Accepted: 09 December 2022;
Published: 20 December 2022.
Edited by:
Nadavala Siva Kumar, College of Engineering, King Saud University, Saudi ArabiaCopyright © 2022 Zhang, Wen, Yin and Zhang. This is an open-access article distributed under the terms of the Creative Commons Attribution License (CC BY). The use, distribution or reproduction in other forums is permitted, provided the original author(s) and the copyright owner(s) are credited and that the original publication in this journal is cited, in accordance with accepted academic practice. No use, distribution or reproduction is permitted which does not comply with these terms.
*Correspondence: Yihang Zhang, THVja3l6aGFuZ3loQGZveG1haWwuY29t