- 1Faculty of Engineering, Department of Civil Engineering, Zonguldak Bulent Ecevit University, Zonguldak, Turkey
- 2Faculty of Engineering, Department of Civil Engineering, Necmettin Erbakan University, Konya, Turkey
- 3Faculty of Engineering and Natural Sciences, Department of Civil Engineering, Konya Technical University, Konya, Turkey
- 4Peter the Great St. Petersburg Polytechnic University, St. Petersburg, Russia
- 5Don State Technical University, Rostov-on-Don, Russia
The performance of waste marble powder as a partial replacement for cement is examined with the aim to achieve more sustainable concrete. Pursuant to this goal, a total of 15 specimens were manufactured and then tested to examine the bending behavior. The effects of longitudinal reinforcement ratio and waste marble powder ratio were selected as variables. The experimental results showed that different proportions of tension reinforcement and waste marble powder had different crack and bending impacts on reinforced concrete beams. As the waste marble powder amount in the concrete mixture is increased from 0% to 40%, it was detected that the crack type changes from a shear crack from to a flexural crack as the amount of waste marble powder increases in the mixing ratio. The experimental findings revealed that the waste marble powder can be successfully used as 10% of the partial replacement of cement. Increasing the waste marble powder ratio by more than 10% can significantly decrease the capacity of the beams, especially when longitudinal reinforcement ratio is high. The influence of waste marble as partial replacement on the capacity decreases as the longitudinal reinforcement ratio decreases. Therefore, 10%–20% marble waste can be utilized as a replacement for cement when the longitudinal reinforcement ratio is close to the balanced ratio and more than 20% waste marble ratio should be avoided for any cases.
1 Introduction
The continuous increase in population in the globalizing world causes a rapid decrease in limited raw material resources. For this reason, the most economical use of existing resources has become even more critical. In parallel with the discovery of new products, the amount of new waste generated is also increasing. Therefore, studies on wastes obtained from industrial raw materials in the construction sector continue (Adesina et al., 2022; Ahmad et al., 2022; Karalar et al., 2022a; Aksoylu et al., 2022; Alani et al., 2022; Arbili et al., 2022; Karalar et al., 2022b; de Azevedo A et al., 2022; de Azevedo et al., 2022; Martínez-García et al., 2022; Qaidi et al., 2022; Zeybek et al., 2022; Çelik et al., 2022). One of them is the marble wastes that occur significantly after manufacturing in marble processing factories (Basaran et al., 2022; El-Mandouh et al., 2022; Khan et al., 2022; Mangi et al., 2022; Nayak et al., 2022; Oza et al., 2022). During the extraction and processing of the marble blocks, two types of waste are generated, namely in the form of pieces and dust, and these wastes cause various adverse effects on the environment.
In Turkey, approximately 40% of the world’s marble reserves are produced (Çelikten and Canbaz, 2021). However, 7 million tons of marble are processed every year in Turkey. Therefore, millions of tons of marble waste are also formed together with the finished marble (Ulubeyli and Artir, 2015). During the production of block marble, 40%–60% of the production is obtained as waste on average (Çelik, 1996; Gürer and Akbulut, 2005). Although it is impossible to store these wastes, their disposal into the environment also brings ecological problems (Alyamaç and Ince, 2009). Therefore, the recycling of these wastes has become very important. In this way, it is precious that the wastes are brought into the economy, the storage problem is reduced, and they can be reused. For this purpose, researchers investigated the suitability of substituting these wastes for cement in mortar or concrete production (Ünal and Kibici, 2001; Uygunoğlu et al., 2014). Aruntaş et al. (2010), instead of cement, concrete samples were produced by using marble dust up to 10% by weight in increments of 2.5%. In this way, they investigated the effect of waste marble dust in different proportions on the mechanical properties of concrete. As a result, they stated that waste marble dust could be safely used as a cement substitute in concrete at rates of up to 10%. Aliabdo et al. Ibrahim et al. (2014) produced concrete mixtures by substituting 5%, 7.5%, 10%, and 15% waste marble dust separately instead of sand and cement. They stated that concrete’s mechanical properties improved with the material of waste marble dust. Khodabakhshian et al. (2018) produced concrete samples using 5%, 10%, and 20% waste marble dust instead of cement in their studies. As a result, they stated that using more than 10% of waste marble dust instead of cement has a negative effect on the mechanical properties of concrete. However, it was stated that mechanical properties were improved in concretes where waste marble dust was used instead of cement at 10% and lower replacement rates. Mashaly et al. (2016) produced concrete mixtures by using up to 40% marble dust instead of cement. At the end of the study, it was stated that the compressive strength of concrete increased up to 20% marble dust content, but content of waste marble dust higher than this percentage led to significant decreases in strength. Vardhan et al. (2015) conducted a series of experimental studies on the mortar obtained by substituting marble powder in different proportions instead of cement. They emphasized that the compressive strength of the mortars they produced did not change significantly with 10% waste marble dust content, and it was suitable for workability. However, it was stated that the content of marble dust higher than this rate significantly reduced the strength of the mortar.
Also, the negative effect of the addition of marble dust introduced instead of part of the cement in an amount of 10% or more is confirmed by a number of the following studies (Adesina et al., 2022; Basaran et al., 2022; Nayak et al., 2022): A decrease in the strength characteristics of concrete is noted, as well as a decrease in the workability of self-compacting concrete mixes.
As for geopolymer concretes, there is a fairly large number of experimental studies confirming the positive impact of the use of various types of stone dust on the strength characteristics of these concretes. For example, in (Mangi et al., 2022), the authors of the research found that the use of marble dust reduces the setting time of the geopolymer composite and increases its strength characteristics. In (Khan et al., 2022), according to the results of experiments, it was found that the use of various types of stone flour, including marble dust, accelerates the geopolymer reaction and increases the compressive strength by more than 10%.
With the literature research, it has been seen that there is not yet a common result concerning the rate of use of waste marble dust instead of cement. This may be due to the difference in marble cutting, waste storage, and raw material content. For this reason, it is crucial to investigate the suitability of the use of local marble waste in cement-based binders and in what proportions it can be used instead of cement. In addition, when the literature is examined, it is seen that there are very limited studies on the shear and bending behavior of reinforced concrete beams. Rajkumar et al. (2021) used by weight of cement and sand by marble powder are 20, 15, 10, 5, and 0%. They analyzed the mechanical properties such as compressive and split tensile strength for conventional and modified concretes at 7, 14, and 28 days. A total of five RC beams with dimensions 150 × 200 × 1,500 mm were cast and tested under four-point loading. The results show that marble powder can be used as an alternate construction material at lower percentage replacement levels. For this reason, in this study, tests were carried out on a small scale (100 × 150 × 1,000 mm) bending beams by substituting marble powder in different proportions for cement. The tests carried out aimed to determine the amount of marble dust suitable for use in the concrete mixture and its contribution to the concrete.
Thus, the main problem of the study is formulated. The scientific problem is the lack of a systematic knowledge base and data on structure formation, properties, and their fundamental and applied relationships between modifiers in the form of marble waste for concrete and the characteristics of reinforced concrete elements made on the basis of such modifiers and concrete. An applied research problem is the lack of systematic data on the possibilities of recycling marble powders and marble flour as a component of concrete. The aim of the study is to establish fundamental dependencies at the micro and macro levels, as well as to determine the relationship between the structure and properties of concrete and reinforced concrete products based on them using marble powder. The objectives of the study are:
- determination of the fundamental possibility of using marble powder for environmentally friendly concrete and reinforced concrete products based on them;
- experimental determination and mathematical justification of the optimal dosages of such a modifier to obtain concrete of the highest quality structure and the highest properties;
- determination of structural and applied aspects of the manufacture of reinforced concrete products based on the obtained concrete with improved structure and properties, determination of the actual characteristics of such reinforced concrete products and structures, and determination of their practical applicability and scope.
2 Materials and methods
To ensure the verification of the data obtained and the purity of the experiment, those initial components were selected that made it possible to assess the degree and level of influence of the modifier in the form of marble powder on the properties and structure of the resulting concrete with improved characteristics and increased environmental friendliness. Methods for manufacturing samples, as well as their testing, were determined, the main raw materials mainly from those raw materials sources that are located in the Turkish region, however, allowing for assessing the degree of influence of modifiers in general.
In the experimental study, waste marble powder shown in Figure 1 was added as a replacement for cement. Amounts of 10%, 20%, 30%, and 40% of marble powder were included instead of cement. Three different longitudinal reinforcement ratio was also considered. All specimens had a stirrup spacing of 100 mm. The reinforcement layout is illustrated in Figure 2. In Figure 2, only the tension rebars change to Ф12, Ф10, and Ф8, respectively. All specimens had a dimension of 150 × 100 × 1,000 mm. The properties of the specimens are shown in Table 1. The specimens were tested under a four-point bending load, as shown in Figure 3. The shear span to effective depth was 3.1.
In order to produce the beams, CEM I 32.5 type of Portland cement was utilized. The chemical properties of this cement are given in Table 1. The water-cement ratio utilized was 0.6. Waste marble powder used in this study was obtained from the Ankara region, Turkey. Furthermore, to obtain the performance parameters of waste marble powder, a concrete pressure test was carried out. As a result of this test, these values were found 21.9 MPa for 0%, 21.4 MPa for 10%, 17.9 MPa for 20%, 13.2 MPa for 30%, and 11.5 MPa for 40% waste marble powder. The cement aggregate ratio was 0.22.
3 Empirical results and discussion
In this part of the study, the effect of different amounts of tension reinforcement and waste marble powder on the fracture and bending attitude of RCBs is obviously presented and estimated in detail. For this reason, the RCBs that are produced in the lab are tested to examine the fracture and bending attitude. As stated above, for this purpose, a total of 15 test samples were manufactured. After 15 different RCBs were prepared in the lab, these RCBs were subjected to fracture and bending tests. These fractures in the RCBs were estimated in detail and it is clearly recognized that each waste marble powder amount had a dissimilar fracture and bending influences on the RCBs. Furthermore, while performing studies; different bends were found for each RCB with dissimilar waste marble powder amounts. Each RCB had dissimilar load-carrying capabilities and these capacities are very noteworthy for the evaluation of the impact of waste marble powder amount on the fracture and bending attitude of concrete structures. In this study, 15 different RCBs were tested as shown in Table 1.
3.1 Impact of different proportions of tension reinforcement on waste marble powder
In this part, the effect of different amounts of tension reinforcement on the fracture and bending behavior of RCBs is obviously estimated in detail as follows.
3.1.1 Case 1: Fracture and load-bending attitude of RCB (Ф12-M0%,Ф10-M0%,Ф8-M0%)
As detailed by empirical results, it is noticed that there were remarkable bending cracks in the reference RCB depending on the vertical load. Under vertical load, the maximum bending in the RCBs was measured by LVDT gadget and these bendings were clearly presented in this part as shown in Figure 4. It is presented in Figure 4 that serious cracks might be noticed in RCBs under strong loads and remarkable bending cracks are presented in Figure 4. These places of cracks are obviously presented as where vertical cracks can take place in the RCB. In addition, the maximum distance between the vertical cracks was 145 mm in the Ф8-M0% RCB (Figure 4). According to Figure 4, it is noticed that the maximum shear cracks inception from the location where the load is applied to the RCB and these cracks carry on to the bottom of RCB. To attain the numerical records about how much bending takes place in the RCB depending on vertical loads, the LVDT gadget is situated under the RCB during the test. In Figure 5, a load-displacement diagram is gained for RCBs. According to Figure 5, bending increased as a rectilinear line until an exact stage and end of this rectilinear line relates to 29.53 kN, 41.62 kN, and 65.26 kN for Ф8-M0%, Ф10-M0%, Ф12-M0%. Then, 4.28 cm, 5.51 cm, and 10.73 cm bending are noticed at maximum vertical load for Ф8-M0%, Ф10-M0%, Ф12-M0%. After these loads, though the load is reduced, the bending is considerably increased. 62.47 cm, 41.57 cm, and 30.12 cm maximum bending for Ф8-M0%, Ф10-M0%, Ф12-M0% were perceived at end of the test and RCB lost its load-carrying ability at these bending values. These results certainly display significant information about the load-carrying ability of the RCBs (Ф8-M0%, Ф10-M0%, Ф12-M0%).
3.1.2 Case 2: Fracture and load-bending attitude of RCB (Ф12-M10%,Ф10-M10%,Ф8-M10%)
As indicated by experimental results for Ф8-M10%, Ф10-M10%, and Ф12-M10%, it was noticed that there were noteworthy bending cracks in the RCB depending on the vertical load. As presented in Figure 6, the bendings in the RCB are identified under the vertical loads. According to Figure 6, it is recognizably offered that important cracks (vertical and shear) are noticed in the RCB. The cracking of the RCBs taking place in the bending zone depending on the vertical load is realized in Figure 6. This crushing is significant because of the impact of the defending behavior of stirrups and reinforcements on the bending behavior of RCBs. In Figure 6, significant vertical cracks are found in the middle of the RCB and these cracks are so significantly vital to estimate the crack behavior of RCBs with different amounts of tension reinforcement. As noticed in Figure 7, deformations recorded by LVTD are presented clearly and this graph is very remarkable to estimate the load-bending attitude of RCB with different amounts of tension reinforcement. According to Figure 7, bendings increased as a rectilinear line until an accurate stage and end of this rectilinear line relates to 41.35 kN, 43.86 kN, and 51.84 kN for Ф8-M10%, Ф10-M10%, Ф12-M10%. Then, 6.59 cm, 7.60 cm, and 9.89 cm bending are noticed at maximum vertical load for Ф8-M10%, Ф10-M10%, and Ф12-M10%. After these loads, though the load is reduced, the bending is considerably increased. 57.21 cm, 21.14 cm, and 22.83 cm maximum bending for Ф8-M10%, Ф10-M10%, and Ф12-M10% were noticed at the ultimate of the test and RCB lost its load-carrying ability at this bending values. These results unquestionably demonstrate considerable important information about the load-carrying ability of the RCBs (Ф8-M10%, Ф10-M10%, Ф12-M10%). Additionally, these consequences appearance the impact of different amounts of tension reinforcement on the bending-load attitude of the RCB. Whereas compared RCB with different amounts of tension reinforcement, important cracks and bendings changes are noticed under the vertical load. Furthermore, less bending is noticed in the RCB for Ф10-M10%, as compared with Ф8-M10% and Ф12-M10%.
3.1.3 Case 3: Fracture and load-bending attitude of RCB (Ф12-M20%,Ф10-M20%,Ф8-M20%)
As indicated by experimental results for Ф8-M20%, Ф10-M20%, Ф12-M20%, it is noticed that there were remarkable shear and bending cracks in the RCB depending on the vertical load. As presented in Figure 8, the bendings in the RCB are noticed under the vertical loads. According to Figure 8, it is recognizably offered that remarkable cracks (vertical and shear) are observed in the RCB. The cracking of the RCBs taking place in the bending zone depending on the vertical load is realized in Figure 8. According to Figure 9, bendings increased as a rectilinear line until an accurate stage and ultimate of this rectilinear line relates to 30.74 kN, 44.58 kN, and 41.81 kN for Ф8-M20%, Ф10-M20%, Ф12-M20%. Then, 5.25 cm, 7.46 cm, and 8.29 cm bending are noticed at maximum vertical load for Ф8-M20%, Ф10-M20%, and Ф12-M20%. After these loads, though the load diminished, the bending is considerably increased. Values of 40.08 cm, 26.85 cm, and 23.58 cm maximum bending for Ф8-M20%, Ф10-M20%, and Ф12-M20% were observed at the end of the test and RCB lost its load-carrying ability at this bending values. These results absolutely demonstrate considerable important information about the load-carrying ability of the RCBs (Ф8-M20%, Ф10-M20%, Ф12-M20%).
3.1.4 Case 4: Fracture and load-bending attitude of RCB (Ф12-M30%,Ф10-M30%,Ф8-M30%)
As observed by experimental results for Ф12-M30%,Ф10-M30%,Ф8-M30%, it was detected that there were significant bending cracks in the RCB depending on the vertical load as presented in Figure 10. The cracking of the RCBs occurring in the bending zone depending on the vertical load is realized in Figure 9. According to Figure 11, bendings escalated as a rectilinear line until an accurate stage and ultimate of this rectilinear line relates to 30.92 kN, 37.38 kN, and 37.65 kN for Ф8-M30%, Ф10-M30%, Ф12-M30%. Then, 5.80 cm, 9.62 cm, and 7.87 cm bending was noted at maximum vertical load for Ф8-M30%, Ф10-M30%, and Ф12-M30%. After these loads, though the load is reduced, the bending is considerably increased. When observing the results, it is observed that 38.79 cm, 20.36 cm, and 21.88 cm maximum bending for Ф8-M30%, Ф10-M30%, Ф12-M30% were noticed at ultimate of the test and RCB lost its load carrying ability at this bending values. In these results, it is observed that the impact of different amounts of tension reinforcement on the bending-load attitude of the RCB.
3.1.5 Case 5: Fracture and load-bending attitude of RCB (Ф12-M40%,Ф10-M40%,Ф8-M40%)
As observed by experimental results for Ф12-M40%, Ф10-M40%, and Ф8-M40%, it is noticed that there were important bending cracks in the RCB depending on the vertical load as offered in Figure 12. The cracking of the RCBs occurring in the bending zone depending on the vertical load is seen in Figure 12. According to Figure 13, bendings increased as a rectilinear line until an accurate stage and ultimate of this rectilinear line relates to 21.66 kN, 22.4 kN, and 25.32 kN for Ф8-M40%, Ф10-M40%, Ф12-M40%. At that point, 7.74 cm, 4.74 cm, and 5.34 cm of bending is observed at maximum vertical load for Ф8-M40%, Ф10-M40%, Ф12-M40%. After these loads, though the load is reduced, the bending is considerably increased. When observing the results, it is observed that 28.61 cm, 25.89 cm, and 25.43 cm maximum bending for Ф8-M40%, Ф10-M40%, and Ф12-M40% were noticed at ultimate of the test and RCB lost its load carrying ability at this bending values.
The results obtained correlate well with the results of the authors in (Çelikten and Canbaz, 2021; El-Mandouh et al., 2022).
3.2 Impact of different proportions of waste marble powder
In this part of the study, the impact of different proportions of waste marble powder on the fracture and bending attitude of RCBs is evidently examined in detail as follows.
3.2.1 Case 1: Fracture and load-bending attitude of proportion of waste marble powder for ϕ12 tension reinforcement
The effect of different proportions of waste marble powder on the fracture and bending behavior of RCBs is apparently considered. For this reason, proportions of waste marble powder are used as 0%, 10%, 20%, 30%, and 40% while tension reinforcement in the RCB is used constantly as 2ϕ12. As indicated by experimental results for Ф12-M0%, Ф12-M10%, Ф12-M20%, Ф12-M30%, and Ф12-M40%, it is observed that there were noteworthy bending cracks in the RCB depending on the vertical load as shown in Figure 14. According to Figure 15, bendings escalated as a rectilinear line until an accurate stage and ultimate of this rectilinear line relates to 59.97 kN, 51.52 kN, 41.92 kN, 36.10 and 26.86 kN for Ф12-M0%, Ф12-M10%, Ф12-M20%, Ф12-M30%, and Ф12-M40%. At that point, 8.20 cm, 9.39 cm, 8.79 cm, 8.56 cm, and 6.08 cm bending is noticed at maximum vertical load for Ф12-M0%, Ф12-M10%, Ф12-M20%, Ф12-M30%, and Ф12-M40%. After these loads, though the load is reduced, the bending is considerably increased. When observed the results, it is observed that 30.13 cm, 22.83 cm, 23.54 cm, 22.20 cm, and 25.43 cm maximum bending for 12-M0%, Ф12-M10%, Ф12-M20%, Ф12-M30%, and Ф12-M40% were noticed at ultimate of the test and RCB lost its load carrying ability at these bending values. These results are indubitably important data about the load-carrying ability of the reinforcement RCBs (12-M0%, Ф12-M10%, Ф12-M20%, Ф12-M30%, and Ф12-M40%) for different amounts of waste marble powder. As noticed from the experimental results as presented in Figure 15, for all amounts of waste marble powder used in the RCB, it is noticed that shear-type bending occurs in all RCBs.
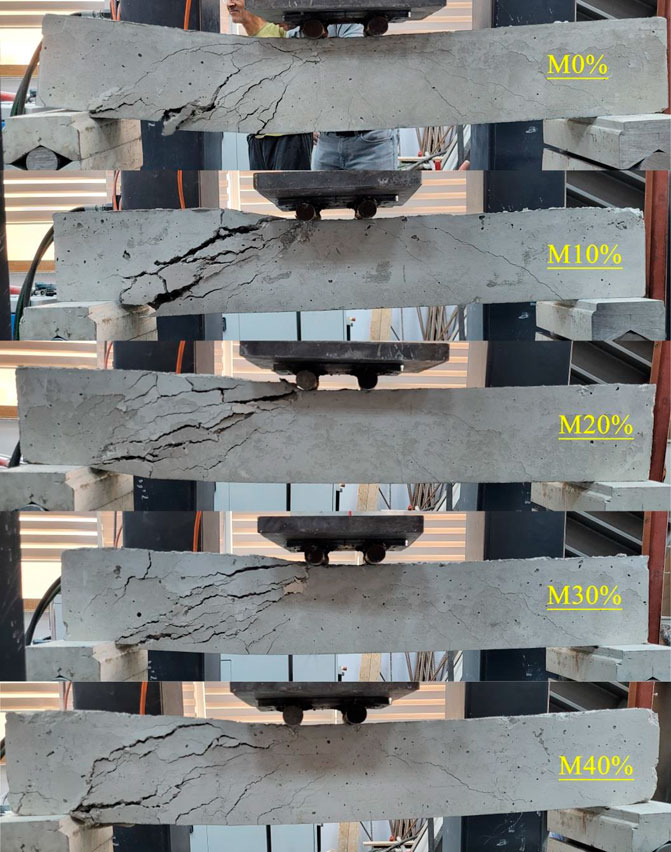
FIGURE 14. Fracture and bending attitude of RCB for Ф12-M0%, Ф12-M10%, Ф12-M20%, Ф12-M30%, and Ф12-M40%.
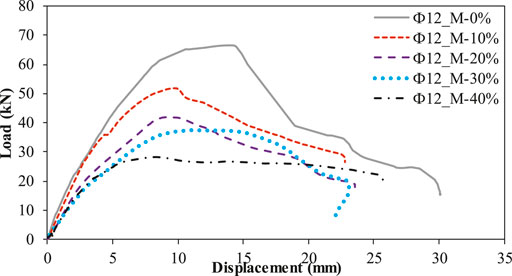
FIGURE 15. Load-Bending attitude of reference RCB for Ф12-M0%, Ф12-M10%, Ф12-M20%, Ф12-M30%, and Ф12-M40%.
3.2.2 Case 2: Fracture and load-bending attitude of proportion of waste marble powder for ϕ10 tension reinforcement
In this part of the examination, while tension reinforcement in the RCB is used constant as 2ϕ10, proportions of waste marble powder are changed as 0%, 10%, 20%, 30%, and 40% to investigate the impact of different proportions of waste marble powder on the fracture and bending attitude of RCBs. As comprehensive by experimental results for Ф10-M0%, Ф10-M10%, Ф10-M20%, Ф10-M30%, and Ф10-M40%, it is observed that there were significant shear and bending cracks in the RCB depending on the vertical load as shown in Figure 16. According to Figure 17, bendings increased as a rectilinear line until an accurate point and ultimate of this rectilinear line relates to 43.57 kN, 45.46 kN, 42.17 kN, 33.51 kN, and 22.4 kN for Ф10-M0%, Ф10-M10%, Ф10-M20%, Ф10-M30%, and Ф10-M40%. Then, 5.25 cm, 7.83 cm, 6.31 cm, 6.95, and 6.91 cm bending is observed at maximum vertical load for Ф10-M0%, Ф10-M10%, Ф10-M20%, Ф10-M30%, and Ф10-M40%. After these loads, though the load is reduced, the bending is considerably increased. When observing the results, it is detected that 41.57 cm, 25.06 cm, 26.85 cm, 20.08 cm, and 24.92 cm maximum bending for Ф10-M0%, Ф10-M10%, Ф10-M20%, Ф10-M30%, and Ф10-M40% were noticed at ultimate of the test and RCB lost its load carrying ability at this bending values. As noticed from the experimental results as shown in Figure 17, while amounts of waste marble powder are used as 0%, it is observed that flexural crack occurs in RCB. Additionally, it is observed that significant fractures and bendings differences are noticed under the vertical load when compared to RCB with different amounts of waste marble powder. It is observed that the crack type changes as shear crack as the amounts of waste marble powder increase the mixing ratio. Moreover, as observed from the experimental test results, it is found that the load-displacement ability of RCB decreases as the proportion of waste marble powder is increased for all amounts.
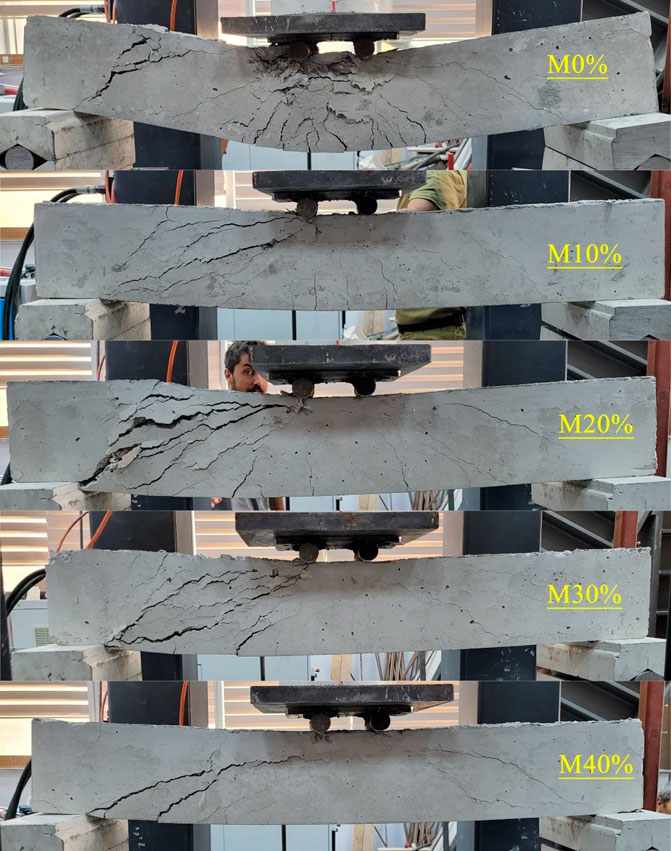
FIGURE 16. Fracture and bending attitude of RCB for Ф10-M0%, Ф10-M10%, Ф10-M20%, Ф10-M30%, and Ф10-M40%.
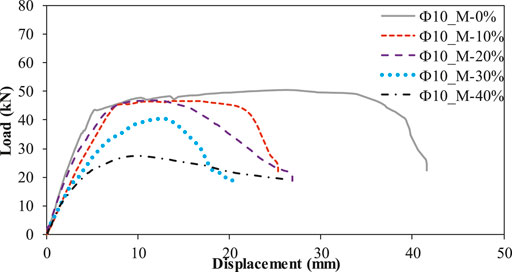
FIGURE 17. Load-Bending attitude of reference RCB for Ф10-M0%, Ф10-M10%, Ф10-M20%, Ф10-M30%, and Ф10-M40%.
3.2.3 Case 3: Fracture and load-bending attitude of waste marble powder for ϕ8 tension reinforcement
In this part of the study, while tension reinforcement in the RCB is used constant as 2ϕ8, proportions of waste marble powder are altered as 0%, 10%, 20%, 30%, and 40% to examine the effect of different amounts of waste marble powder on the fracture and bending attitude of RCBs. As comprehensive by experimental results for Ф8-M0%, Ф8-M10%, Ф8-M20%, Ф8-M30%, and Ф8-M40%, it is detected that there were noteworthy shear and bending cracks in the RCB depending on the vertical load as shown in Figure 18. According to Figure 19, bendings increased as a rectilinear line until an accurate point and ultimate of this rectilinear line relates to 28.91 kN, 31.41 kN, 31.92 kN, 33.51 kN, 31.41 kN and 22.21 kN for Ф8-M0%, Ф8-M10%, Ф8-M20%, Ф8-M30%, and Ф8-M40%. Then, 4.97 cm, 5.8 cm, 6.12 cm, 5.80 cm, and 5.09 cm bending is observed at maximum vertical load for Ф8-M0%, Ф8-M10%, Ф8-M20%, Ф8-M30%, and Ф8-M40%. After these loads, though the load is reduced, the bending is considerably increased. When observing the results, it is detected that 62.47 cm, 57.21 cm, 40.08 cm, 33.68 cm, and 27.96 cm maximum bending for Ф8-M0%, Ф8-M10%, Ф8-M20%, Ф8-M30%, and Ф8-M40% were observed at ultimate of the test and RCB lost its load carrying ability at this bending values. Furthermore, it is detected that significant fractures and bendings differences are noticed under the vertical load while comparing RCB with different amounts of waste marble powder. It is detected that the crack type changes from shear crack to flexural crack as the amounts of waste marble powder increase in the mix ratio. The reason behind it that as the inclination of the waste marble powder amount increases, the load capacity of the beams decreases, and the failure mode changes from flexure to shear even though the mechanical properties of the concrete, main, and shear reinforcement ratio are the same with the corresponding beams. Moreover, as observed from the experimental test results, it is found that the load-displacement ability of RCB decreases as the proportion of waste marble powder increases for all amounts.
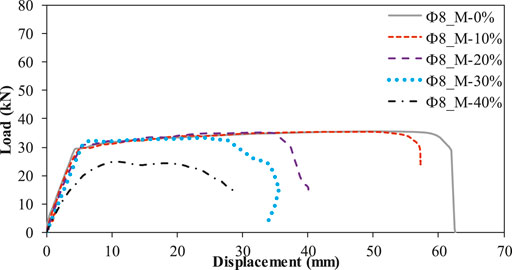
FIGURE 19. Load-Bending attitude of reference RCB for Ф8-M0%, Ф8-M10%, Ф8-M20%, Ф8-M30%, and Ф8-M40%.
4 Conclusion
In this study, experimental tests considered the bending-load behavior and crack behavior of various RCBs produced with waste marble powder. Three of these specimens were reference specimens without any waste marble powder, while the others consisted of Vf amounts of 10%, 20%, 30%, and 40% waste marble powder. After RCBs are prepared in the lab, these special RCBs are exposed to crack tests using a special device. Crack and bending behaviors of the RCBs are assessed according to the experimental tests in detail. These important results are evaluated below:
• According to slump test results, it is recognized that as the waste marble powder amount in the concrete mixture is increased, it is observed that there is a decrease in the compressive strength value of concrete.
• According to experimental test results, it can be indicated that the maximum load-carrying value in the RCBs decreases when the proportion of waste marble powder in the concrete mixture increases. Once reinforcement RCBs with different waste marble powder amounts are compared with each other, maximum bending in the middle of the RCB is observed for Ф8-M10%, waste marble powder RCBs.
• It is speciously recognized that the waste marble powder amount significantly affects the crack behavior of the RCBs. Significant vertical and bending cracks are noticed in the RCBs depending on waste marble powder. As the waste marble powder amount in the concrete mixture is increased from 0% to 40%, it is detected that the crack type changes as a shear crack from the flexural crack as the amounts of waste marble powder increase the mixing ratio.
• In this study, the effect of different amounts of tension reinforcement on the crack and bending behavior of RCBs is considered in detail. As observed from the experimental results, for all amounts of waste marble powder used in the RCB, it is noticed that flexural crack occurs in RCBs using 2ϕ8 tension reinforcement. For other sections, shear cracks occur in RCBs.
To surmise, 10% waste marble as a replacement for cement is recommended for overall performance. This ratio can be slightly increased to between 10%–20% waste marble when the longitudinal reinforcement ratio decreases. More than 20% of waste marble should be avoided as a partial replacement for cement.
In future studies, we aim to obtain a mathematical formula to describe the load-deflection curves depending on changes in marble waste utilizing statistical analysis and artificial intelligence studies.
Data availability statement
The raw data supporting the conclusion of this article will be made available by the authors, without undue reservation.
Author contributions
Conceptualization, YOÖ and MK; methodology, YOÖ and CA; data curation, YOÖ; investigation, YOÖ. Writing-original draft preparation, YOÖ, MK, CA, AB, SS, ES, and MMSS; writing-review and editing, YOÖ, MK, CA, AB, SS, ES, and MMSS; funding acquisition, MMSS. All authors have read and agreed to the published version of the manuscript.
Funding
The research is partially funded by the Ministry of Science and Higher Education of the Russian Federation under the strategic academic leadership program “Priority 2030” (Agreement 075-15-2021-1333 dated 30.09.2021).
Conflict of interest
The authors declare that the research was conducted in the absence of any commercial or financial relationships that could be construed as a potential conflict of interest.
Publisher’s note
All claims expressed in this article are solely those of the authors and do not necessarily represent those of their affiliated organizations, or those of the publisher, the editors and the reviewers. Any product that may be evaluated in this article, or claim that may be made by its manufacturer, is not guaranteed or endorsed by the publisher.
References
Adesina, A., de Azevedo, A. R. G., Amin, M., Hadzima-Nyarko, M., Agwa, I. S., Zeyad, A. M., et al. (2022). Fresh and mechanical properties overview of alkali-activated materials made with glass powder as precursor. Clean. Mater. 3, 100036. doi:10.1016/j.clema.2021.100036
Ahmad, J., Martinez-Garcia, R., Algarni, S., de-Prado-Gil, J., Alqahtani, T., and Irshad, K. (2022). Characteristics of sustainable concrete with partial substitutions of glass waste as a binder material. Int. J. Concr. Struct. Mat. 16, 21–18. doi:10.1186/s40069-022-00511-1
Aksoylu, C., Özkılıç, Y. O., Hadzima-Nyarko, M., Işık, E., and Arslan, M. H. (2022). Investigation on improvement in shear performance of reinforced-concrete beams produced with recycled steel wires from waste tires. Sustainability 14, 13360. doi:10.3390/su142013360
Alani, A. A., Lesovik, R., Lesovik, V., Fediuk, R., Klyuev, S., Amran, M., et al. (2022). Demolition waste potential for completely cement-free binders. Materials 15, 6018. doi:10.3390/ma15176018
Alyamaç, K. E., and Ince, R. (2009). A preliminary concrete mix design for SCC with marble powders. Constr. Build. Mater. 23, 1201–1210. doi:10.1016/j.conbuildmat.2008.08.012
Arbili, M. M., Alqurashi, M., Majdi, A., Ahmad, J., and Deifalla, A. F. (2022). Concrete made with iron ore tailings as a fine aggregate: A step towards sustainable concrete. Materials 15, 6236. doi:10.3390/ma15186236
Aruntaş, H. Y., Gürü, M., Dayı, M., and Tekin, İ. (2010). Utilization of waste marble dust as an additive in cement production. Mater. Des. 31, 4039–4042. doi:10.1016/j.matdes.2010.03.036
Basaran, B., Kalkan, I., Aksoylu, C., Özkılıç, Y. O., and Sabri, M. M. S. (2022). Effects of waste powder, fine and coarse marble aggregates on concrete compressive strength. Sustainability 14, 14388. doi:10.3390/su142114388
Çelik, A. İ., Özkılıç, Y. O., Zeybek, Ö., Özdöner, N., and Tayeh, B. A. (2022). Performance assessment of fiber-reinforced concrete produced with waste lathe fibers. Sustainability 14, 11817. doi:10.3390/su141911817
Çelik, M. Y. (1996). Mermer artıklarının (Parça-Tozların) değerlendirilmesi. A.K.Ü, Afyon: Fen Bilimleri Enstitüsü.
Çelikten, S., and Canbaz, M. (2021). Atık andezit ve mermer tozunun çimento harçlarının dayanım özelliklerine etkisi. Eskişehir Osman. Üniversitesi Mühendislik ve Mimar. Fakültesi Derg. 29, 43–48. doi:10.31796/ogummf.709810
de Azevedo A, R. G., Amin, M., Hadzima-Nyarko, M., Saad Agwa, I., Zeyad, A. M., Tayeh, B. A., et al. (2022). Possibilities for the application of agro-industrial wastes in cementitious materials: A brief review of the Brazilian perspective. Clean. Mater. 3, 100040. doi:10.1016/j.clema.2021.100040
de Azevedo, A. R. G., Marvila, M. T., de Oliveira, M. A. B., Umbuzeiro, C. E. M., Huaman, N. R. C., and Monteiro, S. N. (2022). Perspectives for the application of bauxite wastes in the development of alternative building materials. J. Mater. Res. Technol. 20, 3114–3125. doi:10.1016/j.jmrt.2022.08.092
El-Mandouh, M. A., Hu, J-W., Mohamed, A. S., and Abd El-Maula, A. S. (2022). Assessment of waste marble powder on the mechanical properties of high-strength concrete and evaluation of its shear strength. Materials 15, 7125. doi:10.3390/ma15207125
Gürer, C., and Akbulut, H. (2005). Ocak atığı mermerler için alternatif bir atık değerlendirme yöntemi, 6. Ulusal çevre mühendisliği kongresi. Turkey: TMMOB Çevre Mühendisleri Odası, 195–202.
Ibrahim, A., Mahmoud, E., Yamin, M., and Patibandla, V. C. (2014). Experimental study on Portland cement pervious concrete mechanical and hydrological properties. Constr. Build. Mater. 50, 524–529. doi:10.1016/j.conbuildmat.2013.09.022
Karalar, M., Bilir, T., Çavuşlu, M., Özkılıç, Y. O., and Sabri Sabri, M. M. (2022). Use of recycled coal bottom ash in reinforced concrete beams as replacement for aggregate. Front. Mater. 9, 1064604. doi:10.3389/fmats.2022.1064604
Karalar, M., Özkılıç, Y. O., Deifalla, A. F., Aksoylu, C., Arslan, M. H., Ahmad, M., et al. (2022). Improvement in bending performance of reinforced concrete beams produced with waste lathe scraps. Sustainability 14, 12660. doi:10.3390/su141912660
Khan, K., Ahmad, W., Amin, M. N., Ahmad, A., Nazar, S., Alabdullah, A. A., et al. (2022). Exploring the use of waste marble powder in concrete and predicting its strength with different advanced algorithms. Materials 15, 4108. doi:10.3390/ma15124108
Khodabakhshian, A., De Brito, J., Ghalehnovi, M., and Shamsabadi, E. A. (2018). Mechanical, environmental and economic performance of structural concrete containing silica fume and marble industry waste powder. Constr. Build. Mater. 169, 237–251. doi:10.1016/j.conbuildmat.2018.02.192
Mangi, S. A., Raza, M. S., Khahro, S. H., Qureshi, A. S., and Kumar, R. (2022). Recycling of ceramic tiles waste and marble waste in sustainable production of concrete: A review. Environ. Sci. Pollut. Res. 29, 18311–18332. doi:10.1007/s11356-021-18105-x
Martínez-García, R., Jagadesh, P., Zaid, O., Șerbănoiu, A. A., Fraile-Fernández, F. J., de Prado-Gil, J., et al. (2022). The present state of the use of waste wood ash as an eco-efficient construction material: A review. Materials 15, 5349. doi:10.3390/ma15155349
Mashaly, A. O., El-Kaliouby, B. A., Shalaby, B. N., El–Gohary, A. M., and Rashwan, M. A. (2016). Effects of marble sludge incorporation on the properties of cement composites and concrete paving blocks. J. Clean. Prod. 112, 731–741. doi:10.1016/j.jclepro.2015.07.023
Nayak, S. K., Satapathy, A., and Mantry, S. (2022). Use of waste marble and granite dust in structural applications: A review. J. Build. Eng. 46, 103742. doi:10.1016/j.jobe.2021.103742
Oza, R. B., Kangda, M. Z., Agrawal, M. R., Vakharia, P. R., and Solanki, D. M. (2022). Marble dust as a binding material in concrete: A review. Mater. Today Proc. 60, 421–430. doi:10.1016/j.matpr.2022.01.278
Qaidi, S., Najm, H. M., Abed, S. M., Özkılıç, Y. O., Al Dughaishi, H., Alosta, M., et al. (2022). Concrete containing waste glass as an environmentally friendly aggregate: A review on fresh and mechanical characteristics. Materials 15, 6222. doi:10.3390/ma15186222
Rajkumar, R., Umamaheswari, N., Kumar, A., Kumar, M., Vineeth Gupta, L. R., and Pandey, R. (2021). Flexural behaviour of reinforced concrete beams with partial replacements of metakaolin and marble powder. Mater. Today Proc. 34, 550–555. doi:10.1016/j.matpr.2020.03.111
Ulubeyli, G. C., and Artir, R. (2015). Properties of hardened concrete produced by waste marble powder. Procedia - Soc. Behav. Sci. 195, 2181–2190. doi:10.1016/j.sbspro.2015.06.294
Ünal, O., and Kibici, Y. (2001). Mermer tozu atıklarının beton üretiminde kullanılmasının araştırılması. Türkiye III Mermer Sempozyumu Afyon. Bildir. Kitabı., 317–325.
Uygunoğlu, T., Topçu, İ. B., and Çelik, A. G. (2014). Use of waste marble and recycled aggregates in self-compacting concrete for environmental sustainability. J. Clean. Prod. 84, 691–700. doi:10.1016/j.jclepro.2014.06.019
Vardhan, K., Goyal, S., Siddique, R., and Singh, M. (2015). Mechanical properties and microstructural analysis of cement mortar incorporating marble powder as partial replacement of cement. Constr. Build. Mater. 96, 615–621. doi:10.1016/j.conbuildmat.2015.08.071
Keywords: reinforced concrete, beam, waste, marble powder, recycled
Citation: Karalar M, Özkılıç YO, Aksoylu C, Sabri Sabri MM, Beskopylny AN, Stel’makh SA and Shcherban’ EM (2022) Flexural behavior of reinforced concrete beams using waste marble powder towards application of sustainable concrete. Front. Mater. 9:1068791. doi: 10.3389/fmats.2022.1068791
Received: 13 October 2022; Accepted: 03 November 2022;
Published: 12 December 2022.
Edited by:
Peng Zhang, Zhengzhou University, ChinaReviewed by:
Sathish Kumar Veerappan, University of Split, CroatiaChunhua Lu, Jiangsu University, China
Copyright © 2022 Karalar, Özkılıç, Aksoylu, Sabri Sabri, Beskopylny, Stel’makh and Shcherban’. This is an open-access article distributed under the terms of the Creative Commons Attribution License (CC BY). The use, distribution or reproduction in other forums is permitted, provided the original author(s) and the copyright owner(s) are credited and that the original publication in this journal is cited, in accordance with accepted academic practice. No use, distribution or reproduction is permitted which does not comply with these terms.
*Correspondence: Yasin Onuralp Özkılıç, eW96a2lsaWNAZXJiYWthbi5lZHUudHI=