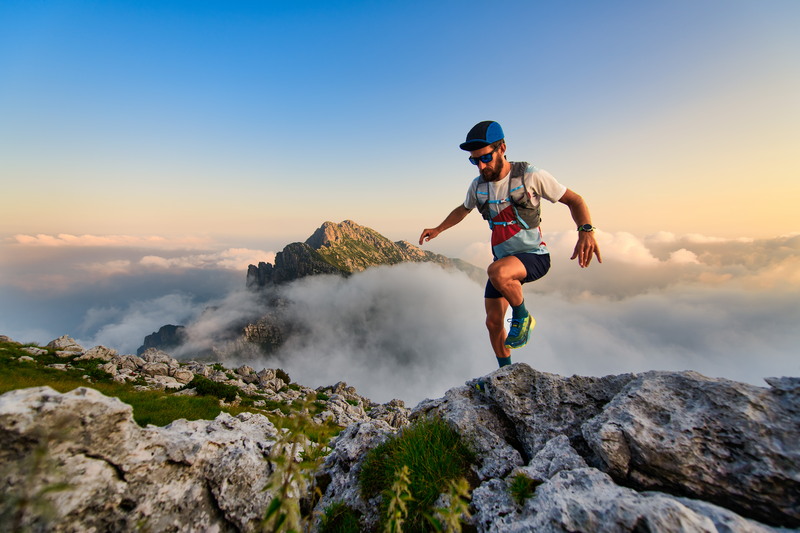
95% of researchers rate our articles as excellent or good
Learn more about the work of our research integrity team to safeguard the quality of each article we publish.
Find out more
ORIGINAL RESEARCH article
Front. Mater. , 26 October 2022
Sec. Smart Materials
Volume 9 - 2022 | https://doi.org/10.3389/fmats.2022.1053847
This article is part of the Research Topic Editors' Showcase: Smart Materials View all 5 articles
Electrorheological (ER) polishing as a new type of polishing technique has flexibility and controllability. However, ER polishing cannot be widely used in actual processing because the present ER polishing fluid is usually prepared by simple mixing abrasive materials into ER fluid, which is easy to occur phase separation and decreased ER performance. This paper develops a new type of ER polishing material based on cerium-doped titanium dioxide. As a classic abrasive, the cerium oxide not only has high polishing performance but also can enhance ER performance of titanium dioxide by doping effect, which endows the cerium-doped titanium dioxide with high ER polishing efficiency compared to ER polishing fluid prepared by a simple mixing method. Cerium-doped titanium dioxide particles were prepared by the sol-gel method. The size, surface morphology and elemental distribution were characterized. The ER properties were tested. The effects of different concentrations, machining gap, voltage and rotation speed on polishing performance were studied. Under the conditions of a 0.2 mm machining gap, 3 kV voltage and 200 r/min rotation speed, the surface roughness (Ra) of the copper workpiece decrease from 136 nm to 14.4 nm after 0.5 h of polishing, which is far higher than the polishing efficiency of simple mixed ER polishing fluid.
Ultra-precision machining has become an important part of the development of many fields such as machinery, especially ultra-precision polishing technology (Yuan et al., 2017). Ultra-precision polishing technology can reduce the surface roughness to a few nanometers and obtain an ultra-smooth surface (Xu et al., 2022). This ultra-smooth surface greatly reduces surface defects and improves service characteristics such as fatigue resistance, corrosion resistance. In particular, it can increase electrical conductivity (Piao et al., 2019a). Such ultra-smooth surfaces have been difficult to achieve through traditional contact polishing processes. Some new non-contact polishing techniques have been proposed and studied extensively, including laser polishing (Chen et al., 2021), ultrasonic polishing (Li et al., 2021), electro-chemical polishing (Wang S. F. et al., 2021a), solid jet polishing (Sun et al., 2018), liquid suspension polishing (Piao et al., 2019b), magnetorheological polishing (Wang et al., 2019), electrorheological (ER) polishing (Zhao et al., 2021), and so on.
ER polishing technology is a flexible ultra-precision polishing method under an electric field. It is suitable for both conductive and non-conductive workpieces (Zhao et al., 2021). A controllable flexible polishing head is produced using the ER effect, which can realize the adaptive polishing of a complex surface. Compared with the complex equipment required by other new polishing processes such as magnetorheological polishing, the device of ER polishing is much simpler and easier to operate, which is more likely to achieve digital precision machining (He et al., 2012). In 1998, Akagami et al. (1998) for the first time proposed the application of ER fluid in the polishing field and designed a device to achieve ER polishing. In 2011, Chen et al. (2011) proposed an ER polishing tool combining cathode and anode, which was used to perform polishing experiments on K9 glass, and the surface roughness decreased from 8.46 nm to 2.53 nm after 30 min of polishing. In 2016, Su et al. (2016) achieved the polishing of tiny parts with a wheel electrode by using an ER polishing fluid composed of cerium dioxide abrasive particles, starch and silicon oil. In 2017, Yang et al. (2017) used ER polishing technology to polish optical elements, and the results showed that ER polishing had a good effect in eliminating directional texture and suppressing texture light emphasis. In 2022, Liu et al. (2022) introduced ER polishing fluid into ultrasonic polishing and realized the polishing of the IN625 workpiece. In the same year, Chen et al. (2022) prepared an electromagnetic two-phase composite particle and explored the polishing behavior of the particles under the electromagnetic field. The results showed that the electromagnetic rheological fluid under the electromagnetic field had better dispersion than that under the single magnetic field. However, the conventional ER polishing fluids are usually prepared by simple mixing of abrasive particles and ER particles. Under the action of electric field and shear field, phase separation is easy to occur due to the difference in ER effect between ER particles and abrasive particles. This separation is easy to further lead to uneven distribution of abrasive particles and reduces the ER effect of ER particles. As a result, the polishing performance decreases. In 2021, our group developed a kind of composite ER polishing particles composed of ER active polymerized ionic liquid (PIL) particles encapsulated with alumina abrasive particles by Pickering emulsion polymerization (Wang J. et al., 2021b). Different from the ER polishing materials prepared by simple mixing, the composite polishing particles have been demonstrated to solve the phase separation problem by integrating the ER effect and polishing performance into a particle system. As a result, the polishing efficiency of ER polishing fluid with the composite particles as dispersed phase is obviously higher than that of ER polishing fluid with a simple mixture as the dispersed phase. However, due to the poor ER properties of alumina itself, the shear stress value of the composite ER polishing fluid and the polishing efficiency is still too low for the actual application.
As a high dielectric constant material, titanium dioxide has been widely studied as the dispersed phase of ER fluid. However, the ER properties of ER fluid prepared with ordinary titanium dioxide particles are not good. Later, the different morphologies of titanium dioxide, doped titanium dioxide, organic or inorganic composite titanium dioxide were studied to enhance ER effect (Ma et al., 2015; Sun et al., 2020; Wang L. et al., 2021c; Liang et al., 2022). In particular, it has been reported that cerium-doped titanium dioxide shows significantly enhanced ER effect (Yin et al., 2001). On the other hand, titanium dioxide and cerium dioxide themselves are also environmentally friendly abrasive (Cui et al., 2013). Therefore, using cerium-doped titanium dioxide as an ER polished particle seems to be a good option. However, there have been no studies reporting on the application of doped titanium dioxide in ER polishing.
In this paper, we prepared cerium-doped titanium dioxide and use it as a new ER polishing material. It found that this kind of material has excellent ER effect and polishing performance. Under the conditions of 0.2 mm machining gap, 3 kV voltage and 200 r/min rotation speed, the surface roughness (Ra) of red copper workpiece decreases from 136 nm to 14.4 nm after 0.5 h of polishing, which is far higher than the polishing efficiency of simple mixed ER polishing fluid. We present the preparation of the cerium-doped titanium dioxide particles, structure characterization, ER effect and ER polishing effect. The influences of particle concentration, machining gap, voltage and speed on polishing performance were studied.
Butyl titanate (TBT, Tianjin Kermeo Chemical Reagent Co., Ltd.), Anhydrous cerium chloride (CeCl3, Shanghai Aladdin Biochemical Technology Co., Ltd.), titanium dioxide (Sinopharm Chemical Reagent Co., Ltd., China), cerium oxide (Shanghai Aladdin Biochemical Technology Co., Ltd.), anhydrous ethanol (Anhui Ante Food Co., Ltd.), silicone oil (Shin-Etsu Chemical Co., Ltd.) were used without further purification. Deionized water was made by our laboratory.
Cerium-doped titanium dioxide particles were prepared by the sol-gel method (Yin et al., 2001). Its ER performance is best when Ce/Ti is 0.07. First, TBT was added to anhydrous ethanol and stirred for 20 min to form solution A. Then, CeCl3 was dissolved into ethanol, stirred until dissolved, and deionized water was added to form solution B. Under continuous vigorous agitation, solution A was quickly poured into solution B under stirring to form a transparent sol. The resulting sol was placed in a blast drying box at 40°C for 2–3 days to give a wet gel. The wet gel was dried at 120°C for 12 h to get a dry gel. The dry gel was ground into a powder. Finally, the powder was calcined at 200°C for 2 h, 400°C for 2 h and 500°C for 2 h in a muffle furnace to obtain yellow cerium-doped titanium dioxide fine powder.
The cerium-doped titanium dioxide powder was vacuum-dried at 150°C for 12 h, and the density of cerium-doped titanium dioxide particles was determined to be 3.8 g/cm3 by densitometry. Cerium-doped titanium dioxide particles were dispersed in silicone oil to obtain ER polishing fluid with volume fractions of 6%, 10% and 20%. At the same time, pure titanium dioxide (density: 3.9 g/cm3), pure cerium oxide (density: 7.13 g/cm3) and their simple mixture (cerium mole content: 0.07) were dispersed in silicone oil, respectively, and three kinds of ER polishing fluid with volume fraction of 10% were obtained for comparison.
The crystal structure of cerium-doped titanium dioxide was characterized by x-ray diffraction (XRD, D2 PHASER X). The size and morphology of cerium-doped titanium dioxide particles were characterized by scanning electron microscopy (SEM, Verios G4) and transmission electron microscopy (TEM, FEI Talos F200X) equipped with an energy dispersive X-ray spectrometer (EDS), and the element distribution was analyzed. The sizes of pure titanium dioxide, pure cerium dioxide and cerium doped titanium dioxide particles were characterized by particle size analyzer (Nano-ZS90).
The ER effect was measured by an electrorheometer (HAAKE RS600) equipped with a parallel plate system with a diameter of 35 mm, a gap of 1 mm and a DC high voltage power supply. The rheological curves of shear stress-shear rate were measured in a controllable shear rate mode with a rate range of 0.1–1,000 s−1 at room temperature. Prior to each test, the ER polishing fluid was pre-sheared for 60 s at a rate of 300 s−1 to eliminate structural history. An electric field was applied to the ER polishing fluid for 30 s to make it form a stable chain structure, and then shearing was applied.
Polishing experiments were performed on a self-made ER polishing device. Figure 1 shows a diagram of an ER polishing device. The polishing device consists of an adjust-able speed disk, parallel plate tool electrodes (width 10 mm, plate gap 1 mm) and a DC high voltage power supply. The workpiece to be polished was fixed in an insulating container on the turntable, and then the distance between the parallel plate tool electrode and the workpiece surface was adjusted by fine-tuning the helical structure, and the parallelity between the bottom end of the electrode and the workpiece surface was maintained. The electrostatic polishing solution was poured into an insulated container so that the workpiece and the front section of tool electrodes were immersed in the polishing fluid, then a voltage was applied, and finally, the turntable was rotated to polish. Because cerium-doped titanium dioxide particles are anatase whose Mohs hardness is about 5.5–6.0, the cerium-doped titanium dioxide ER polishing fluids can mainly be used to polish the materials with Mohs hardness below 3.0 according to the traditional polishing theory. The workpiece selected in this paper is copper (Mohs hardness is 1.0). The surface roughness measuring instrument (Shaanxi Wale Electromechanical Technology Co., SR2000) was used to measure the surface roughness of the workpiece before and after polishing. The measuring length is 0.4 mm. The atomic force micro-scope (AFM, Bruker Dimension Icon) was used to characterize the microscopic morphology of the surface of the workpiece before and after polishing.
Figure 2 shows the XRD patterns of cerium-doped titanium dioxide (Ce/Ti = 0.07) and pure titanium dioxide. It can be seen that after calcination at 500°C, cerium-doped titanium dioxide forms a perfect anatase crystal, and its spectrum is consistent with the standard spectrum of pure titanium dioxide. The particles are composed of nano-crystalline and the grain size can be calculated to be 30 nm by the Scherler formula.
FIGURE 2. XRD patterns of pure titanium dioxide (A) and cerium-doped titanium dioxide (Ce/Ti = 0.07) (B).
Figure 3 shows the SEM image of cerium-doped titanium dioxide particles and EDS analysis. As can be seen from Figure 3A, the prepared cerium-doped titanium dioxide particles are irregular powder with a particle size between 0.3 μm and 3 μm. This result is consistent with that characterized by particle size analyzer. As shown in Figure 3E, the mean size of cerium-doped titanium dioxide particles is about 754 nm. In addition, the mean sizes of pure titanium dioxide and pure cerium dioxide particles are 805 nm and 784 nm, respectively. Figure 3B shows the edge of the cerium-doped titanium dioxide particle is very sharp, which is beneficial to the cutting effect as abrasive. The EDS analysis in Figures 3C,D show the particles containing titanium and cerium elements. Titanium dioxide is used as the matrix material, and a large number of titanium elements are evenly distributed on the particle surface. As a doping element, the cerium element is uniformly distributed on the surface of the particles too.
FIGURE 3. SEM image (A) (B) of cerium-doped titanium dioxide particles, EDS analysis (C) (D) and particle size distribution map (E).
Figure 4 shows the TEM image and element distribution of cerium-doped titanium dioxide particles. The particles are nanocrystalline. The EDS analysis showed that cerium was uniformly doped in titanium dioxide.
Figure 5 shows the relationship between shear stress and electric field strength of cerium-doped titanium dioxide ER polishing fluid (10% and 20%), pure titanium dioxide ER polishing fluid (10%), pure cerium oxide ER polishing fluid (10%) and ER fluid containing a simple mixture of the latter two (10%). It can be seen that with the increase of electric field strength, the shear stress of fluid increases, and this change is most obvious when the electric field strength changes from low (1 kV/mm) to high (2 kV/mm). Under the same condition, the ER effect of pure titanium dioxide ER polishing fluid (10%), pure cerium dioxide ER polishing fluid (10%) and their simple mixture ER polishing fluid (10%) are almost the same. However, when the electric field intensity is 3 kV/mm, the shear stress of cerium oxide fluid does not increase significantly compared with that of 2 kV/mm. This may be because cerium oxide has a very weak ER effect, and the strength of the particle chain formed by polarization is similar to the high electric field. For the ER polishing fluid of pure titanium dioxide, the simple addition of cerium oxide does not affect its ER performance because the content of cerium oxide is small, and their particle sizes are similar. Compared with these three kinds of fluids, cerium-doped titanium dioxide ER polishing fluid has obvious stronger ER effect, which is about three times that of the pure titanium dioxide fluid. When cerium ions enter the titanium dioxide lattice, the larger atomic radius of cerium atoms will inevitably lead to lattice distortion and a large number of defects, which will greatly change the dielectric and conduction properties of particles. As a result, the doped titanium dioxide is more prone to polarization under the action of the electric field, so it has a stronger ER effect (Yin, et al., 2001). At the same time, we compared the ER effect of cerium-doped titanium dioxide ER polishing fluid with different particle concentration. It can be seen that the shear stress of fluid is greatly improved with the increase of concentration. This is because under the same conditions, the greater the concentration of ER fluid, the more particles involved in polarization, the denser the particle chain formed by polarization, and the higher the shear stress.
FIGURE 5. The shear stress of cerium-doped titanium dioxide ER polishing fluid (10% and 20%), pure titanium dioxide ER polishing fluid (10%), pure cerium dioxide ER polishing fluid (10%) and a simple mixture of the latter two ER polishing fluid (10%) as a function of electrical strength (dc) at a shear rate of 1 s−1 and room temperature.
Figure 6 shows the shear stress changes with the shear rate of the cerium-doped titanium dioxide ER fluid with a volume fraction of 20% under different electric field strengths. When no electric field is applied, the ER fluid exhibits Newtonian fluid characteristics, and the shear strength changes linearly with the increase of shear rate. After the electric field is applied, a plateau appears in the curve, and the shear stress of the fluid no longer changes with the shear rate. At this time, the fluid is in the state of Bingham fluid. In other words, under the action of the electric field, the particles polarize along the direction of the electric field and form a fiber chain structure by electrostatic interaction between electrodes. At the same time, the particles are subjected to the action of shear field, and the fiber chain structure is constantly broken and recombined in this process, but the rate of recombination is higher than or equal to the rate of fracture, so the shear stress maintains a plateau state. When the electric field strength is low, the shear stress-shear rate curve of fluid can be divided into two region: Bingham fluid region and Newtonian fluid region. At high shear rate, the particle chain breaks faster than its recombination rate, the ER fluid is transformed from Bingham fluid to Newtonian fluid, and as the strength of electric field increases, the higher shear rate is required for the transition of the fluid state. When the electric field strength is high, the electrostatic interaction between particles is further enhanced, the strength of the chains formed by polarization is increased, and the recombination rate after fracture is very high. Therefore, the ER fluid has the ability to resist the centrifugal force generated by shear rate in a certain range after applying an electric field, which is determined by the nature of ER particles and the magnitude of the applied electric field. Cerium-doped titanium dioxide particles as ER polishing particles show excellent ER effect. When the volume fraction is 20%, the electric field is 3 kV/mm, and the shear rate is 1 s−1, the shear stress can reach 1.1 kPa, which is far higher than the maximum shear stress of PIL/alumina composite ER polishing particles previously reported (Wang, et al., 2021b). In addition, cerium-doped titanium dioxide has good hardness. Therefore, cerium-doped titanium dioxide will have a good application prospect as a new type of ER polishing material.
FIGURE 6. The rheological curves of shear stress-shear rate of the cerium-doped titanium dioxide ER polishing fluid with volume fraction of 20% under different electric field strengths.
As shown in Figure 1A, the workpiece is immersed in the ER polishing fluid, and the parallel plate electrode is loaded in the area to be polished. When a certain voltage is applied to the polishing electrode, there is a uniform electric field between the parallel plates and a non-uniform electric field around the tip of the plate. The polishing particles are polarized and form chains along the electric field lines, and a flexible polishing head is formed at the bottom of the polishing electrode, as shown in Figure 1B. The strength of particle chains in contact with the surface of workpiece can be controlled by adjusting the distance of the parallel plate electrode from the workpiece. In the polishing process, the polishing head and the workpiece occur a relative movement and the polishing particles and the surface of workpiece have a friction effect. When the shear force is greater than the yield stress of workpiece material, the abrasive particles can cut and remove the material of workpiece. In the polishing process, most of the abrasive particles are concentrated between the plates or coated on the plates. The particle chains between the polishing head and the plates are constantly broken and recombined, and the debris produced by processing will be carried away from the polishing area by the flowing polishing fluid. Because the shear field in the polishing experiment is provided by a speed-adjustable disk, the polished region is circle-like, and the area of polished region increases with the increase of the polishing electrode plate. The polished area in this paper is 25
Figure 7 shows the typical polishing results of ER polishing fluid containing cerium-doped titanium dioxide, pure titanium dioxide, pure cerium dioxide, and a simple mixture of the latter with 10% volume fraction. The experimental parameters were a voltage of 3 kV, a rotation speed of 200 r/min and a machining gap of 0.5 mm. The roughness of the polished surface was measured by a roughness instrument. It can be seen from the figures that the two-dimensional profile of the surface of the workpiece polished by cerium-doped titanium dioxide ER polishing fluid changes from obvious fluctuation to small fluctuation, and the surface quality is greatly improved. However, the two-dimensional surface profile of the workpiece polished by the other three ER polishing fluids does not change much, the surface roughness is only slightly reduced, and the polishing effect is limited.
FIGURE 7. The two-dimensional profile of the surface of the workpiece after polishing with (A) cerium-doped titanium dioxide ER polishing fluid (10%), (B) pure titanium dioxide ER polishing fluid (10%), (C) pure cerium dioxide ER polishing fluid (10%) and (D) a simple mixed of the latter two ER polishing fluid (10%).
Figure 8 summarizes the variation of workpiece surface roughness with polishing time. It can be seen that under the above experimental parameters of polishing, the cerium-doped titanium dioxide ER polishing fluid has an outstanding polishing effect compared with other ER polishing fluids. This can be attributed to the fact the ER effect of cerium-doped titanium dioxide ER polishing fluid is far stronger than that of other ER polishing fluids, which makes the particle chains formed by cerium-doped titanium dioxide particles have a higher shear force to cut and remove the material of workpiece surface. The surface roughness of the workpiece gradually decreases with the increase of polishing time. The surface roughness reaches 60 nm after 0.5 h of polishing and 18 nm after 2 h of polishing. According to the slope change of the curve, it can be concluded that the polishing efficiency gradually decreases with the polishing time.
Figure 9 shows the microscopic morphology of the surface of workpiece before and after polishing with cerium-doped titanium dioxide ER polishing fluid. There are a lot of bumps and depressions on the surface of the unpolished workpiece, and the roughness is very large. After 3 h of ER polishing, a number of surface bumps are removed, the contour undulation is much gentler, the surface quality of the workpiece has been greatly improved, and the mirror finish can be observed. We can get a much smoother surface topography. Relative to the hardness of copper, the hardness of cerium-doped titanium dioxide particles should be far greater. From the surface topography after polishing, we can see obvious plastic cutting traces, and the distance between the traces is not equal; there is a very flat part between the scratches, which is because of the particle size of the particles we prepared is not uniform. Thus, we can infer a composition of the polishing head in the polishing process, which is composed of large particles mixed with small particles. Such a composition ensures that large particles bring high polishing efficiency while maintaining high surface quality.
FIGURE 9. The microscopic morphology of the surface of the workpiece before and after polishing with cerium-doped titanium dioxide ER polishing fluid (10%) as polishing agent.
In Section 3.2, we discussed the influence of concentration on ER effect. As the particle concentration increases, the number of particles involved in the chain formation of polarization increases. As a result, the shear stress also increases. According to this, we can draw the following conclusion: with the increase of the particle concentration, the hardness of the polishing head formed at the bottom of the tool electrode increases. Under the same machining gap, the high concentration can provide more shear force, and the polishing efficiency is higher. In order to verify the validity of this conclusion, we prepared three different concentrations of cerium-doped titanium dioxide ER polishing fluid with particle volume fraction of 6%, 10% and 20%. Under the experimental conditions of 3 kV voltage, 200 r/min rotation speed and 0.5 mm machining gap, we polished the copper workpiece for 3 h and investigated the influence of particle concentration on ER polishing effect.
Figure 10 shows the comparison of surface roughness of the copper workpiece before and after polishing with different concentrations of cerium-doped titanium dioxide ER polishing fluid. Under the conditions of 3 kV voltage, 200 r/min rotation speed and 0.5 mm machining gap, the ER polishing fluid with 6% volume fraction almost has no polishing effect. This may be because, when the concentration of ER fluid is lower than a certain critical value, the polishing particles are easy to gather around the tool electrode, and the strength of the flexible polishing head formed is insufficient or cannot touch the workpiece surface, so it is impossible to achieve effective polishing. Under the same experimental conditions, there is no significant difference in the roughness of the workpiece surface after polishing with ER polishing fluid with 10% and 20% concentration. The surface roughness of the workpiece polished with a 20% concentration of fluid is 8 nm lower than that of the workpiece polished with a 10% concentration of fluid after polishing 1 h. After 2 h of polishing, however, the surface roughness of the two workpieces tends to be the same. Here we need to look for an answer from the actual polishing experiment. The polishing process involves immersing the parallel plate tool electrode in ER polishing fluid, applying a voltage and then rotating the workpiece to complete the polishing. It is worth noting that we applied two fields successively: electric field and shear field. When no external field is applied, the ER polishing fluid in the entire container is liquid-like state. When the only electric field is applied, the ER polishing fluid between or around the tool electrodes of the parallel plate is in a solid-like state, while the ER polishing fluid far away from the tool electrode is still in a liquid-like state and the ER polishing particles are evenly dispersed in the silicone oil. In this case, a change in the concentration of the ER polishing fluid does result in the strength of the resulting polishing head. But when both the electric and shear fields are applied, the distance between the workpiece surface and the tool electrode is extremely small and filled with numerous chains of particles. The particle chains are constantly broken and recombined in the process of colliding with the convex surface of the workpiece. The ER polishing particles farther away from the tool electrode are also gathered around the tool electrode, resulting in an increase in the concentration of the local ER polishing fluid around the tool electrode until the number of particles that can be adsorbed around the tool electrode reaches saturation. This is why the polishing results of 10% and 20% ER polishing fluids are similar.
FIGURE 10. The surface roughness of workpiece polished with different concentrations of ER polishing fluid of 6%, 10% and 20% as a function of polishing time (3 kV voltage, 200 r/min rotation speed and 0.5 mm machining gap).
During the experiment, however, we found that when the machining gap was more than 1 mm, there was almost no polishing effect on the workpiece surface because the strength of the flexible polishing head in contact with the workpiece surface is too low to achieve the removal of the material surface bulge. When the machining gap was less than 0.2 mm, electrical breakdown between the polishing electrode and the workpiece was easy to occur. Therefore, the gap was selected in the range from 0.2 mm to 1.0 mm. Figure 11 shows the relationship between the surface roughness of the copper workpiece and the machining gap. It can be seen that the polishing efficiency and surface quality are greatly improved with the decrease in machining gap. Under the same conditions of other experimental parameters, such as the voltage of 3 kV, rotation speed of 200 r/min, polishing for half an hour, when the machining gap is 0.5 mm, the workpiece surface roughness is reduced to 60 nm, and when the machining gap is 0.2 mm, the workpiece surface roughness is reduced to 14.4 nm. Two reasons may be attributed to why the reduction of the processing gap can improve the polishing efficiency. One is that the closer to the tool electrode, the stronger the particle chain. The other is that the reduction of the processing gap makes the blocking effect more obvious, and the current polishing particles can gather around the tool electrode faster, reaching the saturation concentration and thus efficient polishing.
FIGURE 11. The workpiece surface roughness as a function of machining gap (3 kV voltage, 200 r/min rotation speed, 0.5 h polishing time and the cerium-doped titanium dioxide ER polishing fluid with volume fraction of 10%).
Figure 12 shows the relationship between surface roughness of copper workpiece and voltage. It can be seen that the roughness of the workpiece surface decreases with the increase of voltage. Similar to the effect of the machining gap, the increase of the voltage will in polishing bring a strong electric field between the electrode and workpiece surface. As a result, the strength of particle chains will be stronger and provide stronger surface friction force to cut and remove the material of workpiece. Since the breakdown voltage of cerium-doped titanium dioxide ER polishing fluid was 4 kV when the gap was 1.0 mm. Therefore, the highest operating voltage used in our polishing experiment was 3 kV. Wang et al. conducted an ER polishing experiment on copper using poly (ionic liquid)/aluminium oxide composite particles. The surface roughness decreased from 110.2 nm to 39.9 nm after 8 h polishing at a voltage of 3 kV and gap of 1 mm. At the same condition, we use cerium-doped titanium dioxide particles to polish copper and we can reduce the surface roughness from 120 nm to 14.4 nm after half an hour of polishing. It can be seen that cerium-doped titanium dioxide ER polishing fluid has better performance in both polishing efficiency and surface quality.
FIGURE 12. The workpiece surface roughness as a function of voltage (200 r/min rotation speed, 0.2 mm machining gap, 0.5 h polishing time and the cerium-doped titanium dioxide ER polishing fluid with volume fraction of 10%).
In order to further understand the effect of machining gap and voltage on polishing performance, we can approximate the parallel plate tool electrode as an electric dipole. The surface of the two parallel plates each carries an equal amount of heterogeneous charge, and the distance is very close; and this system can be regarded as two equal heterogeneous charges that are very close to each other, that is, electric dipoles (Volokobinskii et al., 1999). The moment μ of this electric dipole can be expressed as:
Where,
Where,
Combining Eqs. 1, 2, it can be seen that the charge quantity and the distance from the field point to the origin are the key factors affecting the field strength at the field point, and the distance has a more obvious influence on the field strength than the charge quantity. In the polishing experiment, the voltage determines the charge on the surface of parallel plates, and the machining gap determines the distance between the field point and the origin, which determines the hardness of the ER polishing head and affects the polishing efficiency.
Figure 13 shows the relationship between the surface roughness of the copper workpiece and rotational speed. The machining gap is 0.5 mm, the voltage is 3 kV, and the polishing time is 1 h. The workpiece surface roughness is 47 nm when the speed is 100 r/min and 15 nm when the speed is 300 r/min. It indicates that with the increase in rotational speed, the workpiece surface roughness decreases. This is because, with the increase of polishing speed, the relative velocity of ER polishing head and workpiece increases, the collision times of particle chain and workpiece surface increase, and the polishing efficiency increases. The maximum speed at which we test the rheological properties is 1,000 s−1.1000 s−1 is approximately equal to 180 r/min. So, we control the speed to be in the range of 100–300 r/min. For the workpiece with relatively low hardness, this rotation speed is sufficient.
FIGURE 13. The workpiece surface roughness as a function of voltage (3 kV voltage, 0.5 mm machining gap, 1 h polishing time and the cerium-doped titanium dioxide ER polishing fluid with volume fraction of 10%).
We can introduce the Preston equation to discuss the effect of rotating speed on ER polishing performance when other experimental parameters remain unchanged (Tellez et al., 2007). Preston equation is an empirical formula widely used in polishing. It only considers the abrasive particle velocity and the pressure of the abrasive particles on the workpiece surface, and all other factors are reduced to a proportionality constant k. According to the Preston equation, the material removal rate in ER polishing process can be expressed as:
Wherein, under certain experimental parameters,
In this paper, a cerium-doped titanium dioxide ER polishing fluid was prepared, and its polishing performance was studied by using a self-made ER polishing device. The effects of four experimental parameters including particle concentration, machining gap, voltage and rotation speed on the polishing performance were investigated. We draw the following conclusion:
(1) Compared with pure titanium dioxide, pure cerium oxide and their simple mixture ER polishing fluid, cerium-doped titanium dioxide ER polishing fluid has better ER effect and outstanding polishing performance under electric field.
(2) The particle concentration of ER polishing fluid has a special effect on polishing. Due to the attraction of the tool electrode to ER polishing particles, the concentration of the polishing fluid in the polishing area will gradually increase until saturation. Therefore, under the condition of sufficient ER polishing particles, the polishing effect of any concentration of ER polishing fluid tends to be consistent.
(3) Reducing the machining gap, increasing voltage and increasing rotation speed can improve the ER polishing efficiency and improve the surface quality of workpiece. Cerium-doped titanium dioxide ER polishing fluid has both high ER performance and polishing performance, which has strong practicability and provides a new research direction for the further development of ER polishing process.
The raw data supporting the conclusions of this article will be made available by the authors, without undue reservation.
Conceptualization, methodology and formal analysis, XH and JY; investigation, XH, HS, and ZY; writing—original draft preparation, XH; validation, resources and writing—review and editing, JY; funding acquisition, JY; supervision, XZ and JY. All authors have read and agreed to the published version of the manuscript.
This research was funded by the Science and Technology Planning Project of Shenzhen Municipality, grant number JCYJ20190806153009355. This research was also funded by the National Natural Science Foundation of China, grant number 51872243.
The authors declare that the research was conducted in the absence of any commercial or financial relationships that could be construed as a potential conflict of interest.
All claims expressed in this article are solely those of the authors and do not necessarily represent those of their affiliated organizations, or those of the publisher, the editors and the reviewers. Any product that may be evaluated in this article, or claim that may be made by its manufacturer, is not guaranteed or endorsed by the publisher.
Akagami, Y., Asari, K., Jeyadevan, B., and Fujita, T. (1998). Characterization of particle motion for polishing and texturing under AC field by using particle dispersion type ER fluid. J. intelligent material Syst. Struct. 9 (8), 672–675. doi:10.1177/1045389x9800900815
Chen, B., Cheng, H., Tam, H. Y., and Li, H. (2011). Design of integrated-electrode tool for electrorheological finishing of optical glasses. Front. Optoelectron. China 4 (4), 467–471. doi:10.1007/s12200-011-0183-4
Chen, B., Sun, S., Wang, X., Zhang, F. Y., Shao, Y., Zhang, L. L., et al. (2021). Research progress of laser polishing technology for material surface. China Surf. Eng. 34 (6), 74–89.
Chen, Z., Pan, J., Yan, Q., Huang, Z., Zhang, F., and Chen, S. (2022). Study on the rheological and polishing properties of electromagnetic two-phase composite particles with abrasive characteristics. Smart Mat. Struct. 31 (4), 045012. doi:10.1088/1361-665x/ac5478
Cui, H., Park, J. H., and Park, J. G. (2013). Environmentally clean slurry using nano-TiO2-abrasive mixed with oxidizer H2O2 for ruthenium-film chemical mechanical planarization. Appl. Surf. Sci. 282, 844–850. doi:10.1016/j.apsusc.2013.06.068
He, X. S., Gao, C. F., Wang, B., Luo, Z. Y., Zhang, Y., Zhu, X. L., et al. (2012). An ER uniform polishing device for inverse electrode.
Li, H., Ren, K., Yin, Z., Dai, C. W., Wang, Z. W., Wei, L., et al. (2021). Review of ultrasonic vibration-assisted abrasive flow polishing technology. J. Mech. Eng. 57 (9), 233–253.
Liang, Y. D., Huang, D. Y., Zhou, X. F., Wang, Z. Q., Shi, Q., Hong, Y. Y., et al. (2022). Efficient electrorheological technology for materials, energy, and mechanical engineering: From mechanisms to applications. Eng.. doi:10.1016/j.eng.2022.01.014
Liu, X., Wang, J., Teng, D., Liew, P. J., and Huang, C. (2022). Electrorheological fluid–assisted ultrasonic polishing for IN625 additively manufactured surfaces. Int. J. Adv. Manuf. Technol. 120 (1), 891–905. doi:10.1007/s00170-022-08838-5
Ma, L. M., Zheng, F. X., and Zhao, X. P. (2015). Sedimentation behaviour of hierarchical porous TiO2 microspheres electrorheological fluids. J. intelligent material Syst. Struct. 26 (14), 1936–1944. doi:10.1177/1045389x15586450
Piao, Z. Y., Wen, D. H., Yin, L. Z., and Meng-meng, Z. (2019b). Ultra-smooth Cu surface fabricated by hydrodynamic suspension polishing technique. Precis. Eng. 57, 189–194. doi:10.1016/j.precisioneng.2019.04.005
Piao, Z. Y., Zhou, Z. Y., Xu, J., and Wang, H. d. (2019a). Use of X-ray computed tomography to investigate rolling contact cracks in plasma sprayed Fe–Cr–B–Si coating. Tribol. Lett. 67 (1), 11–18. doi:10.1007/s11249-018-1126-7
Su, J., Cheng, H., Feng, Y., and Tam, H. Y. (2016). Study of a wheel-like electrorheological finishing tool and its applications to small parts. Appl. Opt. 55 (4), 638–645. doi:10.1364/ao.55.000638
Sun, P. F., Li, J., Zhang, L. X., Wang, Z. Y., Zhou, T., Ke, R., et al. (2018). “Investigation on the performance of fluid jet polishing using shear thickening slurry,” in Conference on Optical Manufacturing and Testing XII, San Diego, CA.
Sun, W. J., Zheng, H. N., Ma, J. B., Xi, Z., Wang, B., and Hao, C. (2020). Preparation and electrorheological properties of eggshell-like TiO2 hollow spheres via one step template-free solvothermal method. Colloids Surfaces A Physicochem. Eng. Aspects 601, 125055. doi:10.1016/j.colsurfa.2020.125055
Tellez, A. L., Cordero, D. A., Robledo, S. C., and Cuautle-Cortes, J. (2007). Correction of the Preston equation for low speeds. Appl. Opt. 46 (9), 1408–1410. doi:10.1364/ao.46.001408
Volokobinskii, M. Y., and Yastrebov, A. S. (1999). Electric fields of dipole structures. Tech. Phys. 44 (7), 807–809. doi:10.1134/1.1259353
Wang, J., Sun, H., Yang, Z., Wang, Y., Zhao, X., and Yin, J. (2021b). Improved electrorheological polishing property of poly (ionic liquid)/Al2O3 composite particles prepared via pickering emulsion polymerization. ACS Appl. Polym. Mat. 3 (11), 5778–5787. doi:10.1021/acsapm.1c01021
Wang, J., and Xiao, Q. (2019). Research progress of magnetorheological polishing technology. Surf. Technol. 48 (10), 317–328.
Wang, L., Huang, C. C., Zhang, P., Liu, F., Zou, T., Li, Z., et al. (2021c). Preparation and electrorheological response of PAL/TiO2/PANI nanorods. J. Renew. Mater. 9 (10), 1707–1715. doi:10.32604/jrm.2021.013884
Wang, S. F., Wang, Y., Wen, J. C., Suo, H. L., Liu, Z. Z., Suo, W. H., et al. (2021a). Study on electrochemical polishing of TC4 alloy. Mat. Res. Express 8 (10), 106520. doi:10.1088/2053-1591/ac1f4c
Xu, L., Wang, L., Chen, H., Hang, W., Lyu, B. H., Yuan, J. L., et al. (2022). Research progress in ultra-precision polishing of tungsten and its alloys. Surf. Technol. 51 (4), 24–36.
Yang, H., Cheng, H., and Feng, Y. (2017). Improvement of high-power laser performance for super-smooth optical surfaces using electrorheological finishing technology. Appl. Opt. 56 (35), 9822–9829. doi:10.1364/ao.56.009822
Yin, J. B., and Zhao, X. P. (2001). Electrorheological effects of cerium-doped TiO2. Chin. Phys. Lett. 18 (8), 1144–1146. doi:10.1088/0256-307x/18/8/350
Yuan, J. L., Lyu, B. H., Hang, W., and Deng, Q. (2017). Review on the progress of ultra-precision machining technologies. Front. Mech. Eng. 12 (2), 158–180. doi:10.1007/s11465-017-0455-9
Keywords: ER polishing, cerium-doped titanium dioxide particles, surface roughness, electrorheology, suspension
Citation: Hu X, Sun H, Yang Z, Zhao X and Yin J (2022) Electrorheological polishing performance of cerium-doped titanium dioxide particles. Front. Mater. 9:1053847. doi: 10.3389/fmats.2022.1053847
Received: 26 September 2022; Accepted: 17 October 2022;
Published: 26 October 2022.
Edited by:
Weihua Li, University of Wollongong, AustraliaReviewed by:
Sarabjeet Singh Sidhu, Beant College of Engineering and Technology, IndiaCopyright © 2022 Hu, Sun, Yang, Zhao and Yin. This is an open-access article distributed under the terms of the Creative Commons Attribution License (CC BY). The use, distribution or reproduction in other forums is permitted, provided the original author(s) and the copyright owner(s) are credited and that the original publication in this journal is cited, in accordance with accepted academic practice. No use, distribution or reproduction is permitted which does not comply with these terms.
*Correspondence: Jianbo Yin, amJ5aW5AbndwdS5lZHUuY24=
Disclaimer: All claims expressed in this article are solely those of the authors and do not necessarily represent those of their affiliated organizations, or those of the publisher, the editors and the reviewers. Any product that may be evaluated in this article or claim that may be made by its manufacturer is not guaranteed or endorsed by the publisher.
Research integrity at Frontiers
Learn more about the work of our research integrity team to safeguard the quality of each article we publish.