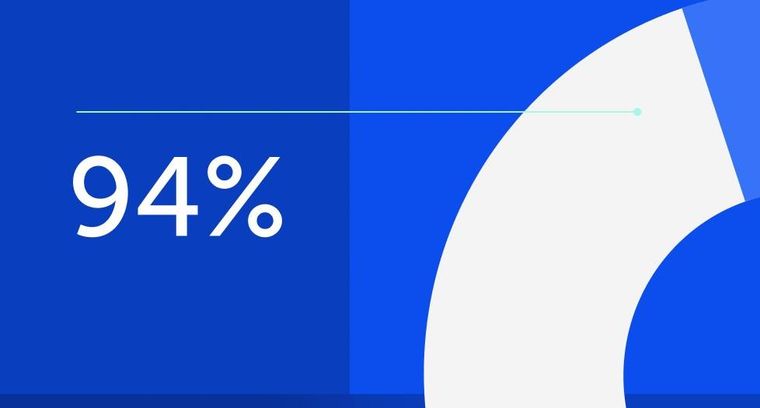
94% of researchers rate our articles as excellent or good
Learn more about the work of our research integrity team to safeguard the quality of each article we publish.
Find out more
ORIGINAL RESEARCH article
Front. Mater., 20 December 2022
Sec. Polymeric and Composite Materials
Volume 9 - 2022 | https://doi.org/10.3389/fmats.2022.1049202
We evaluated the effects of hydration heat inhibitors on the early hydration heat release process of cement and its main mineral components. We used a microcalorimetric method to determine the effects of various proportions and properties of hydration heat inhibitors on the hydration of portland cement, tricalcium silicate, and tricalcium aluminate: concentration (C) = 40% m/m hydroxydiphosphonic acid (HEDP) (1-hydroxyethylidene-1,1-diphosphonic acid) and C = 40% m/m diethylene triamine pentonyphosphonic acid (DTPMPA) (diethylenetriaminepentamethylene phosphonic acid). We also analyzed and tested the heat release rate and cumulative heat release during the hydration of cement and its main mineral components. The hydration heat inhibitors decreased the heat release rate of cementitious materials by means of adsorption, chelation, precipitation, complex formation, and control of calcium hydroxide crystals. Among these materials, the hydration heat inhibitor had the most substantial effect on the composition of tricalcium silicate clinker, reducing the peak temperature at the initial stage of hydration and delaying its occurrence time. These results are pertinent to controlling and selecting the early hydrothermal release process of cement systems.
The appearance of cracks in bulk cement-based concrete in response to high temperatures is one of the most challenging problems affecting construction engineering (Aitcin, 2000; Ju, 2002; Zhu, 2003; Zhu, 2014). Yang (2007) studied the effects of raw materials on the cracking of concrete and reported that the heat of hydration of the cement is the primary factor that affects the temperature increase. Zhu et al. (2018) investigated heat evolution in various cementitious material systems and found that using low-heat portland cement or ordinary portland cement (OPC) with inactive mineral admixtures can reduce the heat of hydration. However, some admixtures might affect the performance of cement. Li et al. (2018) and Liu et al. (2009) found that mineral admixtures such as mineral powder and fumed silica can reduce heat generation but also increase the self-shrinkage of concrete, thus increasing the risk of cracking; in particular, there is a risk of damaging the concrete mass.
In the early 1920s, researchers began to investigate approaches for mitigating high internal temperatures in bulk concrete by, for example, installing cooling water pipes inside the concrete to remove heat (Qian et al., 2012; Liu et al., 2015; Dash et al., 2018; Maanser et al., 2018; Tasri et al., 2019; Conceição et al., 2020; Idrees et al., 2021; Lu et al., 2021). However, installing cooling water pipes—and their associated increases in materials and costs—does not meet current requirements for energy conservation, carbon emission reduction, or environmental protection.
In recent years, researchers have designed materials to inhibit temperature increases during the hydration of concrete. Mixing cement-based concrete with an appropriate quantity of such materials can reduce the exothermic rate during the cement hydration acceleration period, while the total hydration heat of cement remains unchanged (Chen et al., 2021; Chen et al., 2021; Dong et al., 2021; Gu et al., 2021; Liu et al., 2021; Yu et al., 2021). Solving the problem of temperature cracks in mass concrete is an active area of research. For example, Jia et al. (2013; 2021) developed the hydration heat of concrete expansion agent for restraining (HCSA-R), which regulates the hydration of cement in a manner that extends the heat release process and delays the occurrence time of the peak temperature. Lv et al. (2015) prepared a starch-based cement hydration heat regulation material that can also gradually release the hydration heat and reduce the maximum temperature produced inside the concrete by the high heat inside. In their study of calcium aluminosilicate cement mixed with hydroxydiphosphonic acid (HEDP) and diethylene triamine pentonyphosphonic acid (DTPMPA), Li et al. (2020) found that the two admixtures did not affect the hydration process of cement slurry but did prolong the hydration time; the exothermic state of hydration should be further studied. The mechanism of these materials is generally the same: they gradually dissolve in alkaline concrete and adsorb on the surface of the hydration products on the cement particles, thus inhibiting the cement hydration rate in the initial and accelerated stages (Hao et al., 2017). Many studies indicate that the exothermic curve for hydration is a means of studying the exothermic law and the hydration process in determining the effects of admixtures on cement-based materials. The Krstulovic–Dabic model (2000) of hydration dynamics is based on a thorough analysis of a hydration heat-release profile of cement-based materials. The model contains several parameters that reflect the macroscopic and microscopic processes involved in the hydration of the cemented material. The heat release of hydration is related to the active substances in the cementitious materials, and there is no means of reducing the total heat produced during the hydration process.
Our novel research has identified two main sources of hydration heat in cement-based materials and their main mineral components [tricalcium silicate (C3S) and tricalcium aluminate (C3A)] and has revealed their mechanisms by collecting early heat release data during the hydration of active minerals in cement. The purpose of this study is to provide technical support for the thermal cracking control of bulk concrete by selecting and regulating the hydration heat inhibitor in a manner that affects the heat generation and the heat release rate of the hydration process.
In accordance with the main effects and properties of the hydration heat inhibitor, we selected hydroxydiphosphonic acid (HEDP) (1-hydroxyethylidene-1,1-diphosphonic acid) and diethylene triamine pentonyphosphonic acid (DTPMPA) (diethylenetriaminepentamethylene phosphonic acid), both of which can interfere in the exothermic process of the thermal hydration of cement-based gel materials by different means (Li et al., 2020). Table 1 summarizes the characteristics of the selected hydration heat inhibitors, and Figure 1 shows their molecular structures.
The tests were conducted with P·I 42.5 portland cement (number average size Dv50 = 13.02 μm). The specific surface area was 350 m2/kg. Table 2 summarizes the composition. Deionized water was used in all trials at a water-to-cement ratio of 0.4.
To prepare the C3S and C3A single minerals, we followed the method developed by Li (2018). The synthetic materials incorporated anhydrous calcium carbonate from VWR (China, Shanghai) and silica from Sigma-Aldrich (China, Shanghai), as well as Al2O3. These reagents were mixed in accordance with various synthetic ratios and calcined five times in a Borel furnace at ≥1700°C. The product was then ground into a powder with a disk grinder (Hibtek). Single C3S and single C3A minerals were obtained after controlling the transient synthesis reaction with gypsum reagents (Sigma-Aldrich). These C3S and C3A single ores were >99% pure, and they both had an average size of Dv50 = 13.02 μm and a specific surface area of 350 m2/kg. They were sealed and stored for use in subsequent trials. Table 3 summarizes the chemical compositions of the alite samples. Figure 2 shows X-ray diffraction (XRD) distribution maps of the C3S and C3A single minerals. As can be seen from Figure 2, the produced C3S and C3A single minerals have high X-ray diffraction peaks and good crystal development, with high phase content and high purity.
The exotherms of the cement and single ores were measured by microcalorimetry with a TAM air isothermal calorimeter from TA Instruments. The duration of each continuous test was >168 h. The experimental environment was 20°C ± 1°C. The temperature control of this device was stable within ±0.02°C, with a short-term noise of <±4 μW, and a baseline drift of ≥25 µW per 24 h.
Two types of inhibitors—HEDP, with a strong retarding effect, and DTPMPA, with a strong cooling effect—were selected for the test. The total mass of a single test sample was 7 g, including 5 g of solid (cement or C3A, C3S) and 2 g of water. The quantity of inhibitor was 0.01%, 0.03%, or 0.05% of the mass of the cement, C3A, or C3S (Table 4) (i.e., 0.0005 g, 0.0015 g, 0.0025 g of C = 40% m/m HEDP or C = 40% m/m DTPMPA). The weighed inhibitor was added to 2 g of water, then the prepared solution was mixed with the solid material for 60s for testing. These mixtures were then placed in two parallel channels and recorded simultaneously. The non-meaningful increase of heat flow caused by opening the channel could disturb the integration of cumulative heat at a very early age. Here, we started the integration from 0.75 h to minimize the possible error.
As indicated by the heat release rate curve of the C3S hydration reaction (Figure 3), the time to reach the peak heat flow varied substantially at various inhibitor doses (Table 5).
FIGURE 3. Heat flow data obtained from C3S combined with the following: (A) HEDP, (B) DTPMA, and (C) HEDP + DTPMA.
Regarding the test data for the C3S single-ore hydration reaction, in the case of the unhydrated heat inhibitors, the peak heat flow was higher and the time to form the heat flow peak was relatively brief. The heat flow peak decreased after HEDP inhibitor incorporation, compared with the blank control group. In the trial with a low incorporation dose (0.01%), the time to form the heat flow peak decreased by nearly 13 h, and the peak heat release rate decreased by 40.5%. By increasing the incorporation dose, the peak heat release rate decreased by ca. 57%, but the heat flow peak delay was not obvious. These results indicate that adding HEDP during the hydration of C3S single ore delayed the formation time of the heat flow peak at a lower dose of HEDP and decreased the peak heat release rate. The increased HEDP dose did not delay the peak formation time but did decrease the peak heat release rate by ca. half.
The peak heat release rates could be decreased after incorporating DTPMPA inhibitor compared with the blank control. In trials with a low added dose (0.01%), the peak heat release rate could be decreased by 78%, but the formation time of the peak temperature and the increased added dose changed negligibly. These results indicate that adding DTPMPA to the hydration process of C3S single ore did not delay the formation time of the peak temperature but did reduce the peak heat release rate. At the low incorporation dose (0.01%), the peak heat release rate was the most decreased; therefore, the incorporation dose of DTPMPA in the hydration process of C3S single ore should not be too high.
After incorporating the mixed HEDP + DTPMPA inhibitor, the peak heat flow formation time in the case of the low incorporation dose (0.01%) decreased by 37.8% compared with the blank control group. This result does not differ greatly from that of incorporating an HEDP inhibitor at a dose of 0.01%. By adjusting the HEDP + DTPMPA incorporation dose to 0.03%, the peak heat flow formation time was close to that of the blank control group, and the peak heat release rate could be substantially decreased to 73%. When the HEDP + DTPMPA incorporation dose increased to 0.05%, the peak heat release formation time was close to that of the blank control group and the decrease in the peak heat release rate was greatest (83.8%). These results indicate that HEDP played a major role at 0.01%. The decrease in the peak heat release rate was limited but could delay the manifestation of the peak heat release. As the incorporation dose of HEDP + DTPMPA increased to 0.03%, DTPMPA played a prominent role. The decrease in the peak heat release rate gradually intensified, and the manifestation of the peak heat flow was slightly delayed. By further increasing the incorporation dose to 0.05%, we reduced the peak heat release rate most substantially to ca. one-sixth of the blank control group, but the formation time of the peak heat flow did not change.
As is evident from the comparison curve of C3S (Figure 4), under the conditions of various dosages of the inhibitors, the cumulative release of the hydration heat gradually increased within 1 w, but the increase was faster in the early stage and slower in the later stage (Table 6).
FIGURE 4. Heat of hydration data obtained from C3S combined with the following: (A) HEDP, (B) DTPMA, and (C) HEDP + DTPMA.
Regarding the test data for the C3S single mineral hydration reaction, the cumulative calorific value of the hydration heat at 24 h was 115 J/g, accounting for 57.5% of the cumulative calorific value of the first 7 days (200 J/g). Only 45 J/g was released after 48 h, representing 75% of the cumulative calorific value within the first 7 days.
After incorporating the HEDP inhibitor, the first 7 days’ cumulative calorific value was slightly increased at the HEDP incorporation dose of 0.01%, but there was a decreasing trend with increasing HEDP incorporation doses. The test results indicate that the cumulative calorific value of the first 7 days was 20% lower at the 0.03% incorporation dose and 40% lower at the 0.05% incorporation dose. The cumulative calorific value at 24 or 48 h decreased to different extents. The cumulative calorific value at 24 h at the 0.03% incorporation dose decreased the most: 65%.
All the cumulative calorific values in the first 7 days exhibited large degrees of reduction compared with the blank control group, but the decreasing trend abated with increasing doses of DTPMPA. The cumulative calorific values at 24 or 48 h decreased to varying extents. At the incorporation dose of 0.01%, the 24 h cumulative calorific value decreased the most substantially: >50%.
Using the HEDP + DTPMPA mixed inhibitor slightly increased the cumulative calorific value in the first 7 days at 0.01% incorporation, but there was a decreasing trend with increasing HEDP incorporation. At an added dose of 0.05%, the 7-day calorific value reached 65%. The cumulative calorific value at 24 and 48 h was less than half of the cumulative calorific value for the first 7 days at the same incorporation dose.
As evident from the heat release rate curve of the C3A hydration reaction (Figure 5), the peak of the heat flow and the time of the heat flow peak formation changed negligibly after incorporating various or no inhibitors and various doses of inhibitors (Table 7).
Regarding the test data for the C3A single-ore hydration reaction, it is evident that there was a C3A single ore after hydration in water. The hydration reaction was fast and formed a heat flow peak at ca. 2 min. The temperature peak manifested early and disappeared quickly, and the concentrated heat release time was short. The test indicates that incorporating the hydration heat inhibitor had little impact on the hydration heat release process; the time delay of the formation of the hydration heat flow peak was <5–8 min, which does not essentially decrease the heat flow peak.
As evident from the cumulative release curve of the C3A hydration heat (Figure 6), the cumulative release of C3A hydration heat was 77% within 5 min and 85% within 10 min. After 10 min, the cumulative release increase gradually abated. At various incorporation doses of various inhibitors, the cumulative release of the hydration heat changed negligibly compared to the release without the inhibitors (Table 8).
FIGURE 6. Heat of hydration data obtained from C3A combined with the following: (A) HEDP and (B) DTPMA.
From the test data for the cumulative hydration heat release of the C3A single mineral hydration reaction, it is evident that most of the hydration heat was released within 5–20 min, and the cumulative heat release within 20 min did not increase much. Eighty-five to 90 percent of the cumulative heat release of hydration was not associated with the type or dose of the inhibitor.
As evident by the heat release rate curve of the OPC hydration reaction (Figure 7), the time and formation of the heat flow peak varied substantially under the incorporation of various doses and types of inhibitors (Table 9).
FIGURE 7. Heat flow data obtained from OPC combined with the following: (A) HEDP, (B) DTPMA, and (C) HEDP + DTPMA.
The peak heat flow (210 mW/g) was evident at 32 h after the hydration reaction of the cement clinker. Incorporating the HEDP inhibitor decreased the peak heat flow compared with that of the blank control group. In the trial with the low incorporation dose (0.01%), the time to form the heat flow peak was delayed by nearly 16 h and the peak heat release rate decreased by 35.5%. After increasing the incorporation dose, the peak heat release rate decreased by ca. 64%–70%, but the time delay of forming the peak heat flow was not obvious. These results indicate that the incorporation dose of HEDP in OPC also had a platform effect. The low incorporation doses of the HEDP inhibitors delayed the formation of the peak heat flow time and decreased the peak heat release rate. However, although increasing the incorporation dose of the HEDP inhibitor did not delay the formation of the peak heat flow, the peak heat release rate decreased by ca. two-thirds.
After incorporating the DTPMPA inhibitor, the peak heat release rate substantially decreased compared with the blank control group. In the trial with the low incorporation dose (0.01%), the peak heat flow decreased by 54.7%, the time for the formation of the peak heat flow was delayed by nearly 31 h, and the delay time was nearly twice that of the blank control group. By increasing the DTPMPA incorporation to 0.03%, the time to form the heat flow peak can be delayed by 104 h, which is more than 4× that of the blank control group. Regarding the 0.05% incorporation dose, the peak heat flow decreased by 90%. However, the time to form the peak heat flow was 12 h earlier compared with the blank control group. These results indicate that adding DTPMPA can delay the time of the formation of the peak temperature during the OPC hydration process and can substantially decrease the peak heat release rate. The peak heat release rate and the time to delay the formation of the peak heat flow can be adjusted to an optimal extent when the incorporation dose is appropriate.
With HEDP + DTPMPA (1:1) inhibitor mixing, the time to form the peak heat flow increased nearly 7 h earlier and the peak heat release rate decreased (in the trials of 0.01% and 0.03%) compared with the blank control group. When the HEDP + DTPMPA incorporation dose was 0.05%, the time for forming the heat flow peak was close to that of the blank control group but the peak heat release rate decreased by only 71.4%. These results indicate that we had added the HEDP + DTPMPA mixed inhibitor at 1:1 during OPC hydration. The peak heat release rate could be decreased by ca. 70%. However, the time of forming the heat flow peak could not be delayed.
As evident from the comparison curve of the cumulative release of the OPC hydration heat (Figure 8), the cumulative release of the hydration heat gradually increased over 1 w under the incorporation of various doses and types of inhibitors (Table 10).
FIGURE 8. Heat of hydration data obtained from OPC combined with the following: (A) HEDP, (B) DTPMA, and (C) HEDP + DTPMA.
Regarding the test data for the OPC hydration reaction, the cumulative release of the hydration heat over 24 h accounted for 22.2%, and the release over 48 h for 55.5%, of the cumulative release within the first 7 days. After incorporating HEDP or DTPMPA, the quantity of cumulative release at added doses of 0.01–0.03 was consistent with the blank control group, but the trend decreased with increasing added doses. Only at the 0.05 dose of DTPMPA incorporation was the cumulative release reduced to the greatest extent, at 76.6%.
After incorporating the HEDP + DTPMPA inhibitor mixture, the cumulative release within the first 7 days decreased ca. by one-third compared with that of the blank control group, and the size of the mixed dose of the HEDP + DTPMPA inhibitor did not affect the cumulative release within the first 7 days.
During the hydration of OPC, the cumulative release at 48 h substantially decreased compared with the blank control group, but the cumulative release could increase in accordance with a linear relationship after 48 h, indicating that the hydration heat release was relatively uniform.
Portland cement undergoes solidification, as well as rapid condensation and hardening. Based on theoretical calculations (Cai,1995), the heat released by this reaction mainly derives from the C3S and C3A single ores in the mineral. The test results indicate that the C3A hydration reaction is fast, forming a peak heat flow (248 mW/g) in ca. 2 min, and has an instantaneous heat release peak and concentrated heat release. The hydration reaction of C3S is relatively mild, forming a peak heat flow (185 W/g) at ca. 11 h, with a long duration of heat release and a large cumulative heat release. Therefore, silicate cement, as well as C3S and C3A single ores, is commonly chosen when studying the hydration heat inhibitors that affect the early heat release of cement. Zhang et al. (2022) observed hydration heat inhibitors to have no effect on late hydration but to inhibit the early hydration of the C3A system. The test results indicate that the C3A hydration reaction releases heat quickly and that the inhibitor does not substantially reduce the instantaneous heat released or delay the rate of its heat release. There was no obvious effect on the early or late hydration of the C3A system. When studying the hydration heat problem of cement concrete, Chen et al. (2020) observed that C3A provides the heat for the development of the induction period, whereas C3S provides the heat for the early condensation and strength development period of concrete. These are all well-validated by the aforementioned test results. The C3S single ore in the OPC composition is the key factor in the early hydration heat of concrete.
According to Lu (2017), small organic phosphate molecules can substantially inhibit the hydration process of cement. Chen et al. (2021) indicate that using an appropriate quantity of such molecules can in theory substantially reduce the release rate of cement hydration acceleration. We selected the phosphate group, as well as the two compounds HEDP and DTPMPA, to investigate silicate cement and C3S/C3A hydration (in comparison with a control group). The results indicate that both of these hydration heat inhibitors can reduce the early hydration heat of cement.
Adding a certain quantity of HEDP inhibitor into the mineral hydration reaction for silicate cement or C3S alone can substantially extend the arrival time of the temperature peak, which is closely related to the slow coagulation characteristics of HEDP. HEDP inhibitors adsorb onto the surface of unhydrated cement or C3S particles and undergo hydration with Ca2+ ions in the cement slurry or C3S slurry. Calcium salts of low solubility in water precipitate to form impermeable thin layers on the surface of the unhydrated cement or C3S mineral, hindering the further hydration of portland cement or C3S. This condition is consistent with Li et al.’s (2020) investigation of the mechanism of incorporating cement into an HEDP retarder. Concomitantly, Ca2+ in the cement slurry or C3S slurry forms a semi-permeable film of a six-ring chelate with some functional groups in the hydration heat inhibitor (such as COO−), which can also enclose the surface of the cement particles or C3S in a manner that prevents the contact of water with the cement particles or C3S. These phenomena affect the speed of the hydration reaction, inhibit the formation and growth of AFt and CH, prolong the time of the hydration reaction and the formation of the heat flow peak, reduce the release rate, and delay the temperature increase of the concrete.
If a certain quantity of silicate cement or the C3S single mineral hydration undergoes a strong cooling effect because of the DTPMPA inhibitor, the arrival time of the temperature peak can be prolonged and the peak temperature and early accumulated heat release substantially reduced. The participation of DTPMPA in hydration has multiple effects: adsorption, chelation, and precipitation. The DTPMPA methyl phosphate group and calcium magnesium ions form a complex (Figure 9) that can enclose the unhydrated cement or C3S single ore particle surface, as well as inhibit C3S mineralization during CH (i.e., crystals of calcium dihydroxide) core growth and conventional CH precipitation hydration.
FIGURE 9. Schematic of the molecules in the complexation reaction and schematic of the molecules surrounded by the complexes on the surface of the single-ore particles without hydration reactions.
HEDP and DTPMPA are organophosphate products that are incorporated into the cement slurry, in addition to Ca2+, which can ionize hydrogen ions and coordinate oxygen atoms in the water. Ca2+, Mg2+, Al2+, and Fe2+ react to form stable phosphate chelates. The decomposition of these phosphates is endothermic; this energy is from the hydration of cement or C3S. Thus, the temperature peak and cumulative heat released by the hydration heat temperature increase are reduced, which inhibits the hydration heat.
Yu et al. (2021) found that to reduce the heat release rate of cement hydration in the accelerated period, the identity and quantity of the inhibitor are critical. Accordingly, we used a cross-combination scheme of various materials to investigate the temperature-control performance requirements of two hydration heat inhibitors, HEDP and DTPMPA. The results indicate the following.
In terms of delayed peak time of the heat flow, regarding C3S single ore, the single-incorporation of HEDP should not be too large. HEDP can substantially delay the formation time of the peak heat flow at 12 h and reduce the peak heat flow by 40.5%. However, with an increased incorporation dose, the formation time of the heat flow peak will no longer be extended but will return to the state without HEDP incorporation. When we tested the single incorporation of DTPMPA, the formation time of the peak heat flow was not delayed in the range of the 0.01%–0.05% incorporation dose. When HEDP and DTPMP inhibitors were mixed at a mass ratio of 1:1 and at a dose of 0.01%, the results were nearly the same as for HEDP alone. However, when the added dose was increased, the results were similar to that of DTPMPA alone. For portland cement, the time effect of delaying the peak heat flow with the combined dose of 0.03% was substantial, which can delay the formation time of the peak heat flow by ca. 4 days. Reducing the incorporation dose to 0.01% reduced the formation time of the delayed heat flow peak to 0.01%. Increasing the incorporation dose to 0.05% reduced the peak formation time rapidly, eventually by more than 10 h. The thermal peak was less obvious because of the large quantity of hydration heat to be balanced by the heat absorption effect of DTPMPA in the hydration reaction. When mixing HEDP, or HEDP and DTPMP, with two inhibitors at a mass ratio of 1:1, the effect was far less than that of DTPMPA incorporation alone. Therefore, an HEDP dose of ca. 0.01% or a DTPMPA dose of 0.03% is the ideal choice to reduce the heat release rate of hydration and delay the formation time of the peak heat flow.
In terms of reducing the quantity of hydration heat release, silland cement is consistent with a C3S single ore after incorporation into HEDP. We observed that little was changed without HEDP or at 0.01% HEDP but that the cumulative hydration heat release in the first 7 days decreased with an increasing added dose, such as 35% at the 0.03% dose. The cumulative hydration heat release in the first 7 days decreased by 43% at the 0.05% dose. These data suggest that HEDP reduced the release of hydration heat only when the incorporation dose was relatively high. For the C3S single ore, the accumulated heat release decreased by 68.5% in the first 7 days when the dose was 0.01% after DTPMPA incorporation, but as the added dose increased, the first 7-d accumulated release was non-linearly correlated with the dose (i.e., 47.4% at 0.03% and 60% at the added dose of 0.05%). The quantity of cumulative heat release varied slightly at a dose of 0.01% after DTPMPA incorporation at 7 days compared with no DTPMPA incorporation (control group). With increasing incorporation doses, the cumulative quantity of heat release at 7 days was linearly correlated with the incorporation dose, decreasing by 35% at an incorporation dose of 0.03% and 76% at an incorporation dose of 0.05%. These characteristics indicate that the effect of DTPMPA cooling becomes increasingly obvious with increasing incorporation doses. If silicate cement or the C3S single ore was mixed with HEDP and DTPMP inhibitors at a mass ratio of 1:1, then different doses were not substantially different from the results of HEDP incorporation alone. For OPC, the cumulative release of the first 7 days could be reduced by 35%–43%, but it was not associated with the magnitude of the added dose. By considering the cumulative release of the hydration heat, such as 24 or 48 h of HEDP, we found that 0.01% HEDP or 0.03% DTPMPA of 0.03% decreased at 7 days. These results are consistent with the mechanisms by which HEDP and DTPMPA affect the exothermic process of OPC.
This study found that a reasonable choice of hydration heat inhibitor and dosage, for cement as an adhesive material of concrete (especially bulk concrete), can reduce the temperature difference of the concrete core and surface by reducing the hydration heat release and delaying the arrival of the temperature peak. In so doing, this study reduced the generation of early temperature stress in concrete and provided a means of minimizing the appearance of temperature cracks.
The inhibitors primarily interfered with the OPC hydration process, similar to the manner in which they affected the exothermic hydration of C3S. These results indicate that C3S might play a major role in generating the exothermic effect observed during OPC hydration. The inhibitors decreased the heat release during OPC hydration by a maximum of 77%. DTPMPA acted by forming complexes and controlling the production of CH (i.e., crystals of calcium dihydroxide). The phosphate groups in this molecule formed complexes with the calcium and magnesium ions that covered the surfaces of unhydrated C3S particles in a manner that inhibited hydration and CH− formation, achieving a cooling effect. Blending with a mixture of HEDP and DTPMPA delayed the onset of the peak heat flow, decreased the heating rate, and increased the cooling rate. Therefore, a synergistic effect was apparent. Increasing the inhibitor level to 0.03% resulted in a segmental heating phenomenon. The cooling performance caused an overall decrease in the heating rate, whereas the inhibition effect prolonged the overall temperature increase, leading to hydration heat generation with segmented heating and cooling. The temperature increases exhibited relatively small variations and the overall time span over which the heat of hydration was released increased by 50%.
The original contributions presented in the study are included in the article/Supplementary material, and further inquiries can be directed to the corresponding author.
JL designed the experiment and analyzed the main points. BT was a major contributor in terms of testing and writing the manuscript. LL and LQ helped to conduct tests and data examination. All the authors read and approved the final manuscript.
This research was supported by the National Key Scientific Instrument and Equipment Development Projects of China (2018YFB1600100) and the National Natural Science Foundation of China (52178428, 52178427, and 51908260).
The first author acknowledges support from the Ministry of Communications Highway Traffic Test Site, Beijing, China.
The authors declare that the research was conducted in the absence of any commercial or financial relationships that could be construed as a potential conflict of interest.
All claims expressed in this article are solely those of the authors and do not necessarily represent those of their affiliated organizations, or those of the publisher, the editors, and the reviewers. Any product that may be evaluated in this article, or claim that may be made by its manufacturer, is not guaranteed or endorsed by the publisher.
Aitcin, P. C. (2000). Cements of yesterday and today: Concrete of tomorrow. Cem. Concr. Res. 30, 1349–1359. doi:10.1016/S0008-8846(00)00365-3
Bing, Hao, Zhao, Wenli, and Zang, Sheng (2017). Study on the influence of hydration thermal inhibitors on the properties of mass concrete. Build. Technol. 4810, 1073–1075. doi:10.13731/j.issn.1000-4726.2017.10.021
Cai, Zhengyong (1995). Prevention of cement concrete alkali-aggregate reaction. Highw. Transp. Technol. 2, 65–67. doi:10.1617/s11527-006-9220-y
Chen, Weiyi, Zhou, Yuqi, Song, Li, and Yan, Peiyu (2021). Effects of hydration thermal inhibitors on cement-fly ash gel material hydration and concrete properties. J. Portland 49 (8), 1609–1618. doi:10.14062/j.issn.0454-5648.20200724
Conceição, José, Faria, Rui, Azenha, Miguel, and Miranda, Manuel (2020). A new method based on equivalent surfaces for simulation of the post-cooling in concrete arch dams during construction. Eng. Struct. 209, 109976. doi:10.1016/j.engstruct.2019.109976
Dash, Manoj K., and Patro, Sanjaya K. (2018). Effects of water cooled ferrochrome slag as fine aggregate on the properties of concrete. Constr. Build. Mater. 177, 457–466. doi:10.1016/j.conbuildmat.2018.05.079
Dong, Sufen, Wang, Xinyue, Xu, Huining, Wang, Jialiang, and Han, B. (2021). Incorporating super-fine stainless wires to control thermal cracking of concrete structures caused by heat of hydration. Constr. Build. Mater. 271, 121896. doi:10.1016/j.conbuildmat.2020.121896
Idrees, Maria, Ekincioglu, Ozgur, and Sonyal, Muhammad Sarmad (2021). Hydration behavior of calcium aluminate cement mortars with mineral admixtures at different curing temperatures. Constr. Build. Mater. 285, 122839. doi:10.1016/j.conbuildmat.2021.122839
Jia, Fujia, Yao, Yan, and Li, Changcheng (2021). Preparation and mechanism research of hydrationheat-inhibiting materials with microcapsule sustained-releasing Technology. J. Wuhan. Univ. Technol. Mat. Sci. Ed. 36 (5), 697–705. doi:10.1007/s11595-021-2462-2
Jia, Fujie, Zhang, Jiaqi, Nie, Fengyi, and Hu, Junyu (2013). Application of hydrothermal inhibitory expansion agent in engineering. Concr. Cem. Prod. 7, 70–73. doi:10.19761/j.1000-4637.2013.07.020
Koo, Jinrui, Liu, Xiaoqin, and Wang, Hailong (2021). Regulation of hydration heat inhibitors on cement hydration. New type Build. Mater. 8, 47–50+54. doi:10.3969/j.issn.1001-702X.2021.08.011
Krstulović, R., and Dabić, P. (2000). A conceptual model of the cement hydration process. Cem. Concr. Res. 30 (5), 693–698. doi:10.1016/S0008-8846(00)00231-3
Li, Lihui, Tian, Bo, Han, Gensheng, Zhao, Wenli, and Quan, Lei (2020). Influence of organic phosphonic acid on cement hydration characteristics at early age. J. Build. Mater. 2 (4), 247–254. doi:10.1016/j.jclepro.2021.130086
Li, Lihui, Wang, Junjie, Tian, Bo, and Quan, Lei, (2018). Study on mineral admixture on hydration and shrinkage properties of high strength concrete and high water absorption resin. Concrete 6, 80–83+88. doi:10.1016/j.jobe.2022.104763
Li, X., Ouzia, A., and Scrivener, K. (2018). Laboratory synthesis of C3S on the kilogram scale. Cem. Concr. Res. 108, 201–207.
Liu, Xinghong, Zhang, Chao, Chang, Xiaolin, Zhou, Wei, Cheng, Yonggang, and Duan, Yin (2015). Precise simulation analysis of the thermal field in mass concrete with a pipe water cooling system. Appl. Therm. Eng. 78, 449–459. doi:10.1016/j.applthermaleng.2014.12.050
LiuSun, JianzhongWei, Miao, Changwen, and Liu, Jiaping (2009). Effect of mineral admixture on dry shrinkage and self-shrinkage of low water gel ratio than concrete. J. Southeast Univ. Nat. Sci. Ed. 39.03, 580–585. doi:10.3969/j.issn.1001-0505.2009.03.030
Lu, Xiaochun, Chen, Bofu, Tian, Bin, Li, Yangbo, Lv, Congcong, and Xiong, Bobo (2021). A new method for hydraulic mass concrete temperature control: Design and experiment. Constr. Build. Mater. 302, 124167. doi:10.1016/j.conbuildmat.2021.124167
Lu, Zichen. (2017). Doctoral dissertation. China: Tsinghua University. Analysis of the influence law and mechanism of different functional group organic admixtures on cement hydration.
Lv, Zhifeng, Cheng, Yu, She, Weina, Wu, Jingzhi, Zhang, Jiangang, and Ran, Xianping (2015). Thermolysis and enzymelysis was prepared. New Build. Mater. 42 (5), 1–3+32. doi:10.3969/j.issn.1001-702X.2015.05.001
Maanser, A., Benouis, A., and Ferhoune, Noureddine (2018). Effect of high temperature on strength and mass loss of admixtured concretes. Constr. Build. Mater. 166, 916–921. doi:10.1016/j.conbuildmat.2018.01.181
Qian, Chunxiang, and Gao, Guibo (2012). Reduction of interior temperature of mass concrete using suspension of phase change materials as cooling fluid. Constr. Build. Mater. 26 (1), 527–531. doi:10.1016/j.conbuildmat.2011.06.053
(Roger) Chen, Hung-Liang, Mardmomen, Seyednavid, and Leon, Guadalupe (2021). On-site measurement of heat of hydration of delivered mass concrete. Constr. Build. Mater. 269, 121246. doi:10.1016/j.conbuildmat.2020.121246
Tasri, Adek, and Susilawati, Anita (2019). Effect of material of post-cooling pipes on temperature and thermal stress in mass concrete. Structures 20, 204–212. doi:10.1016/j.istruc.2019.03.015
Xiao, Liu, Xia, BaiBing, He, Rui, Song, Xiaofei, Luo, Qifeng, Wang, Ziming, et al. (2021). Research progress of hydration thermal control materials. J. Portland 49 (5), 980–987. doi:10.14062/j.issn.0454-5648.20200692
Yan, Yu, Alexandre, Ouzia, Cheng, Yu, Liu, Jiaping, and Scrivener, Karen L. (2020). Effect of a novel starch-based temperature rise inhibitor on cement hydration and microstructure development. Cem. Concr. Res. 129, 105961. doi:10.1016/j.cemconres.2019.105961
Yan, Yu, Scrivener, Karen L., Cheng, Yu, Alexandre, Ouzia, and Liu, Jiaping (2021b). Effect of a novel starch-based temperature rise inhibitor on cement hydration and microstructure development: The second peak study. Cem. Concr. Res. 141, 106325. doi:10.1016/j.cemconres.2020.106325
Yan, Yu, Wang, Rui, Liu, Jiaping, Tang, Jinhui, and Scrivener, Karen L. (2021a). Effect of a liquid-type temperature rise inhibitor on cement hydration. Cem. Concr. Res. 140, 106286. doi:10.1016/j.cemconres.2020.106286
Yan, Yu, Wang, Rui, Wang, Wenbin, Cheng, Yu, and Liu, Jiaping, (2021c). Effect of starch-based admixtures on the exothermic process of cement hydration. Constr. Build. Mater. 289–122903. doi:10.1016/j.conbuildmat.2021.122903
Yang, Heli (2007). Control of large concrete cracks in foundation. J. Wuhan Univ. Eng. Ed. S1, 349–354. doi:10.3969/j.issn.1001-523X.2007.04.018
Zhang, Xiaoping, and Chen, L. (2022). The influence of hydration heat inhibitor and retarder on cement single ore and cement hydration process. New Build. Mater. 49 (1), 76–80. doi:10.3969/j.issn.1001-702X.2022.01.018
Zhu, Bofang (2003). The equivalent thermal conduction equation considering the influence of external temperature. Water conserv. Newsp. 03, 49–54. doi:10.1016/j.applthermaleng.2014.03.058
Zhu, Bofang (2014). Thermal stresses and temperature control of mass concrete. Oxford: Butterworth-Heinemann. doi:10.1016/C2012-0-06038-3
Keywords: hydration heat inhibitors, cement hydration, C3S single mineral, C3A single mineral, hydration heat, heat release rate
Citation: Lv J, Tian B, Li L and Quan L (2022) Mechanisms of hydration heat inhibitors on the early heat release process of cement. Front. Mater. 9:1049202. doi: 10.3389/fmats.2022.1049202
Received: 20 September 2022; Accepted: 01 December 2022;
Published: 20 December 2022.
Edited by:
Anastasia Muliana, Texas A&M University, United StatesCopyright © 2022 Lv, Tian, Li and Quan. This is an open-access article distributed under the terms of the Creative Commons Attribution License (CC BY). The use, distribution or reproduction in other forums is permitted, provided the original author(s) and the copyright owner(s) are credited and that the original publication in this journal is cited, in accordance with accepted academic practice. No use, distribution or reproduction is permitted which does not comply with these terms.
*Correspondence: Jiaoyang Lv, Mzc4NDY0OTUxQHFxLmNvbQ==
Disclaimer: All claims expressed in this article are solely those of the authors and do not necessarily represent those of their affiliated organizations, or those of the publisher, the editors and the reviewers. Any product that may be evaluated in this article or claim that may be made by its manufacturer is not guaranteed or endorsed by the publisher.
Research integrity at Frontiers
Learn more about the work of our research integrity team to safeguard the quality of each article we publish.