- Department of Materials and Ceramic Engineering, CICECO-Aveiro Institute of Materials, University of Aveiro, Aveiro, Portugal
The demand for products derived from the pulp and paper industry has been increasing over the past years and is projected to further increase over the coming decades. Although being one of Portugal’s most relevant industrial activities, contributing to nearly 2.3% of the GDP, this sector is known to generate a variety of wastes including fly ashes, exhausted bed sands, green liquor dregs, grits, lime muds, biological and pulp and paper mill sludges, which have been mostly disposed of in landfills. This strategy is not aligned with the circular economy vision, and therefore it is imperative to develop new recycling routes for the different waste streams. This scenario has driven a significant research effort in the attempt to design sustainable recycling alternatives for the distinct wastes. This study summarizes the investigations focusing on the valorisation of these wastes in a wide range of applications, including the production of low carbon footprint binders or mortars for the construction sector, but also the production of novel materials for high added-value applications such as wastewater treatment and pH regulation. The present work also highlights the main bottlenecks and future prospects for the studied wastes.
1 Introduction
Pulp and paper (P&P) production is one of the largest industrial activity in the world (Bajpai, 2017), and the fifth-largest energy consumer worldwide, behind industries such as chemical, iron and steel, and oil and gas refining (EIA, 2019). The demand for P&P products is increasing and, in 2020, its market size was evaluated at 355 billion € (FBI, 2021) with an expected annual growth rate of 4.08% from 2022 to 2026 (Cision, 2022). The new markets and applications P&P products such as cardboard, tissue paper, textile applications, or pulp for personal care products (Cherian and Siddiqua, 2019) have contributed to this growth. Further, the need to replace plastic (produced from non-renewable sources) with paper in packaging applications is also responsible for the expectable growth.
The members of the Confederation of European Paper Industries (CEPI) reached a total consumption of primary energy, in 2019, of 1.3 million TJ, which includes the use of biomass and process residues (62%), gas (32%), coal (3%), fuel oil (1%) and other fuel sources. Electricity generated through combined (on-site) heat and power plants accounts for 96% of total electricity consumption (CEPI, 2021) and, for this reason, these industries are considered energy-intensive manufacturers (EIA, 2019). According to CEPI, the 495 pulp, paper and cardboard producing companies in 18 countries in Europe produced 36.2 million tons of pulp and 85.2 million tons of paper and cardboard in 2020 (CEPI, 2021). CEPI members account for 92% of the European P&P industries and represent 21% of the total world pulp production. Portugal is the third-largest European pulp producer, behind Sweden and Finland, being P&P production one of the most vital industrial activities. In terms of wood consumption for pulp manufacturing, 72% are softwood (such as pine and spruce) and 28% are hardwood, such as birch, eucalyptus, beech, ash, aspen, maple, acacia, oak, among others (CEPI, 2021).
2 Pulp manufacturing process
Pulp derived from wood is the main raw material in the production of different types of paper. Further, the pulp is also used as an absorbent material in diapers and other sanitary products (Cabrera, 2017). Considering the use of new wood materials, which represent a large share of pulp production, the process can be divided into three main steps: preparation of raw materials, separation of the fibres and bleaching process. The recovery of chemicals is also an important step that, although not directly in the pulp production process, contributes to its success and sustainability. The Kraft process is the most used pulping process by P&P industries worldwide (Santos et al., 2013) mainly because the pulp produced has superior strength, higher resistance to aging and the bleaching process is simplified.
2.1 Preparation of the raw materials and separation of fibres
Before the pulping process, the raw materials (softwoods, hardwoods and non-woody biomasses) are prepared, converting them into appropriate size and shape for the following processing. The logs are debarked and cleaned with water because the bark is a contaminant in the chemical pulping process. The clean logs are cut into identical small chips, maximizing in this way the efficiency of the process. Typically, very small or large chips are separated and used for energy recovery (biomass burning) or are reprocessed for further treatment (Kramer et al., 2009).
In the pulp-producing process, lignin, a resin that binds the wood fibres tightly, must be eliminated and only fibres (cellulose) must be extracted. Thus, the treatment process aims to separate the biomass components, namely, cellulose (40–50 wt.%), hemicellulose (25–30 wt.%) and lignin (25–30 wt.%), into individual components (Naqvi et al., 2010). After separation, the fibres are suspended in a slurry, to be used in the papermaking process. The treatment process is performed by separation or solubilization of the lignocellulosic components. Pulping processes can be divided into mechanical, semi-chemical and chemical, according to the methodology and instruments used (Kumar et al., 2020). Chemical pulping is the most common pulping process used worldwide, possibly due to the high removal efficiency of lignin (Takada et al., 2020). In fact, in this route, the majority of the lignin and hemicellulose contents are removed, resulting in low pulp yields (40–55 wt.%), with a high degree of cellulose fibres (Meyer and Edwards, 2014). In this process, the lignin is separated from the remaining materials in a digester under pressure and using cooking chemicals. In the “cooking” of raw materials, such as wood chips, an aqueous chemical solution called “white liquor” is used, at high temperatures and pressure, to extract the pulp fibres. The three main chemical pulping processes are soda pulping (alkaline), sulphite pulping (acid) and Kraft or sulphate pulping (alkaline).
2.2 Kraft pulping process
A flowchart of the Kraft pulping process integrated into a P&P mill is presented in Figure 1. The process comprises chemical recovery steps, including the energy production from chemicals and biomass burning, and the connection between the pulp manufacture, the bleaching process and the paper manufacture. In addition, the main effluent and solid wastes generated in the process are highlighted in Figure 1.
The Kraft process was developed with the main goal of removing lignin while preserving carbohydrates. The “cooking” of wood is performed with the addition of white liquor, an alkaline mixture of sodium hydroxide and sodium sulphide, to promote lignin dissolution. The use of such chemicals is advantageous in terms of the final fibre strength but it leads to relatively low pulp yields, caused by the instability and degradation of carbohydrates during the alkaline reaction (Santos et al., 2013). The cooking of the wood chips is performed at elevated temperatures (150–170°C) and pressure. The lignin structure is modified and depolymerized by the action of the strong alkaline solution and the presence of hydrosulphide ions. In this digestion process, 90–95 wt.% of the lignin is solubilized in the pulping liquor. A wide variety of wood species can be processed by the Kraft pulping process and the exact conditions of the process depend on the type of wood used (softwood or hardwood) (Gellerstedt, 2015). After cooking for 2–4 h, the liquor and the pulp mixture are discharged from the digester. They are separated into a series of washers and, after the washing step, the pulp (fibres) is ready to be submitted to the bleaching process. The content in lignin of softwood pulps is about 5 wt.%, and this residual lignin is removed in the bleaching process, obtaining a bright and high-quality pulp.
The Kraft process is the pulping process with maximum chemical recovery efficiency. The chemicals are collected after pulping and are set to the chemical recovery circuit. Figure 1 includes the three steps in the chemical recovery process, namely the black liquor concentration, the combustion of organic compounds and the causticizing and calcination. These steps are vital to the environmental and economic sustainability of the P&P industries, as they allow the reduction of costs and of the environmental impact of waste material (mainly black liquor), with the minimization of the raw materials used and with the recycling of chemical materials (Mesfun et al., 2014). In addition, the recovery of chemicals has the asset of co-generating steam and power, which is used as energy in the P&P mill.
In Kraft (and soda) pulp mills, the liquor from the cooking step is called “weak black liquor” and contains wood lignin, organic materials, oxidized inorganic compounds (such as Na2SO4 and Na2CO3) and white liquor (cooking chemicals such as NaOH—soda—or a mixture of NaOH and Na2S—Kraft). The concentration of weak black liquor is performed by a series of evaporators, to increase the solids content from 12–15 wt.% to ≈65 wt.%. It forms the so-called “strong black liquor,” capable of being combusted in the recovery furnace (Verma et al., 2019), in the next chemical recovery step. The condensate from the evaporators contains high concentrations of methanol and is sent to the treatment plant (Meyer and Edwards, 2014). The combustion of organic compounds is performed in the recovery boiler, where “strong black liquor” is burned and the inorganic chemicals are reduced to a molten smelt, enriched with Na2S and Na2CO3, after lignin decomposition. They are recovered from the bottom of the boiler and refined (Kramer et al., 2009). This combustion process generates energy in the form of electricity, which, in combination with the energy produced by the power combustor (wood burning), is used in the plant. The inorganic salts recovered in combustion are dissolved in the weak wash water and form the “green liquor” (Naqvi et al., 2010), which is filtered/clarified to remove the green liquor dregs. “Green liquor” is causticized with the addition of lime, to convert the Na2CO3 into NaOH (dos Santos et al., 2019). The calcium carbonate formed is removed as lime mud (He et al., 2009) and it is washed and the lime is regenerated in the lime kiln. The “white liquor” recovered is filtered and reused in the wood cooking process.
Typically, about 3.5 kg of steam is produced when 1 kg of black liquor solids is burned, depending on the efficiency of the recovery boiler. After the steam generation, it passes through a turbine to generate electricity and the amount generated depends on the turbine type and the quality of the steam. A mill, which produces 1000 ton/d of Kraft pulp, can generate 25–35 MW of electricity by burning 1500 ton/d of black liquor dry solids in the recovery boiler (Tran and Vakkilainnen, 2008).
2.3 Bleaching process
After chemical or mechanical pulping processes, the pulp obtained still contains high amounts of lignin and other coloured compounds. To produce high-grade final products, the pulp must be bleached to remove the pulp colour caused by the presence of residual lignin, thus obtaining a light-coloured or white paper, preferred for many products and applications. The same bleaching process or sequence can be applied to any of the pulping processes (mechanical, semi-chemical, or chemical). The addition of two or more chemicals and the sequence in which they are used depends on several factors, including costs, the type of pulp to be bleached and the requirement for the final product. The addition of chemicals to the previously washed pulp is performed in stages in the bleaching towers. Between each stage, bleaching chemicals are removed from the washers. From these successive washes, the effluents generated are collected and sent to the wastewater treatment plant (EPA, 2010).
2.4 Wastes generated
In the P&P industry, several wastes are produced at different steps of the process and the amount of waste generated depends on the pulping process implemented (Cherian and Siddiqua, 2019). The Kraft pulping process generates about 100 kg of waste per ton of air-dry pulp (kg/tAD), whereas the semi-chemical and mechanical pulping process generates only about 60 kg/tAD (Monte et al., 2009). With the new approaches considered in recent years for waste management, the use of different wastes generated in P&P mills as resources is a step towards green energy and environmental sustainability, moving from the conventional linear concept to the circular economy.
Figure 2 shows images of the main solid wastes generated in the P&P process. For the Kraft process, including the chemical recovery cycle, the main wastes generated are fly ashes (FA), exhausted sands (ES) from biomass boilers (CT) and co-generation plant (CA), dregs (also called green liquor sludge) from clarification of green liquor, grits from the regeneration of CaO after calcination in a lime kiln, lime mud from the causticizing process, biological sludge and mill sludge from the P&P mill wastewater treatment plant, as presented in Figure 1. Barks and other wood residues are burned for energy production, therefore, they are not considered wastes (Simão et al., 2018).
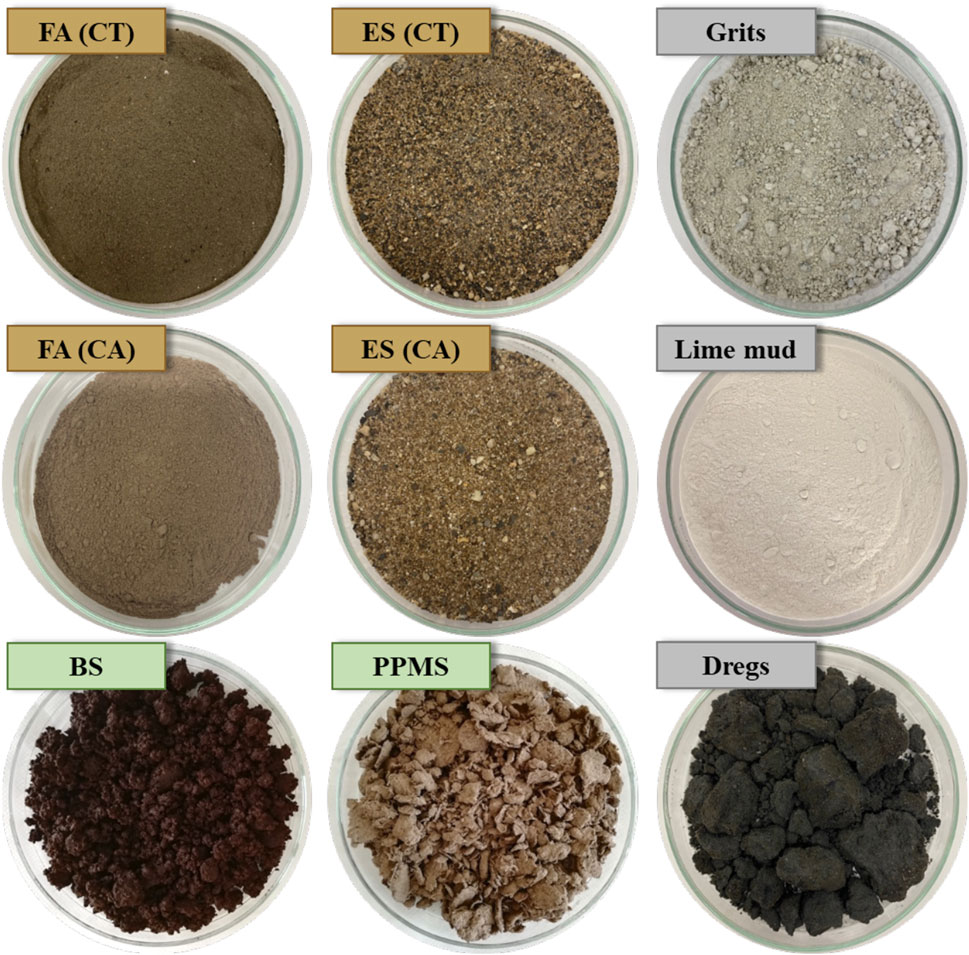
FIGURE 2. Images of the main solid wastes generated in the P&P industry. Highlighted in brown: wastes from the boilers; grey: wastes from the recovery cycle; green: wastes from the wastewater treatment plant. FA, fly ash; ES, exhausted sands; BS, biologic sludge; PPMS, pulp and paper mill sludge.
Fly ash and exhausted bed sand CT are generated in the combustion process of the power combustors, see Figures 1, 2. Herein, the fused particles of volatile matter and impurities are carried upwards with the flue gases and, as they approach the low-temperature zones, solidify to form fly ashes. These fine ashes are captured from the flue gases in the bag filters and electrostatic precipitators. The remaining residue is recovered at the bottom of the boiler and is called exhausted bed sand CT. Fresh sand (inert particles) is added to the fluidized bed biomass boiler which is a type of boiler recommended for biomass burning. The temperature of the bed ranges from 800°C to 900°C and the O2 concentration in the flue gas varies between 4 and 7 vol.% (dry basis) (Modolo et al., 2013). Fly ash and exhausted bed sands CA are generated in the co-generation power plant where heat and power are produced. Here, only eucalyptus barks are used whereas in the power boiler wood and forest residues are used. The worldwide amount of biomass fly ashes produced is estimated to be 10 million tonnes/year (Lamers et al., 2019).
Dregs are mainly composed of sodium and calcium carbonates, sodium sulphide, a low organic fraction that was not burned in the recovery boiler, and other salts from the pulp production process (Modolo et al., 2010; Novais et al., 2018f). Grits are a mixture of calcium carbonate and lime that did not react in the slaker (where causticization takes place). During causticization, the reaction between Na2CO3 (in the green liquor) and lime (from the lime kiln) produces NaOH and calcium carbonate, which are the main components of the lime mud (Modolo et al., 2010). The pH of this waste is strongly alkaline (between 10.0 and 12.8) due to the presence of alkaline oxides (Manskinen et al., 2011).
Several wastewaters’ streams with different compositions and volumes are generated in the different pulp and paper production stages. The bleaching process generates up to 85% of the total volume of effluent discharged in a P&P mill. These effluents formed in the pulp bleaching process have different characteristics, depending on the bleaching agent and generation stage, and are considered highly toxic (Kamali and Khodaparast, 2015). These effluents from the bleaching process are rich in dissolved lignin, carbohydrates, colour, organic matter, adsorbable organic halogens (AOX) and inorganic chloride compounds, chlorophenols and halogenated hydrocarbons (Meyer and Edwards, 2014; Kamali and Khodaparast, 2015). The most problematic effluents are generated during the bleaching process with chlorine dioxide, due to the formation of complex and persistent organochlorine compounds, which can be genotoxic and are known to bioaccumulate in the aquatic food chain, mainly in the body fat of animals of higher trophic levels (Kamali et al., 2016). Usually, the alkaline effluent generated in the bleaching process is called Ep and is generated in an alkali extraction step (e.g., using hydrogen peroxide) (Saeli et al., 2019c).
The typical wastewater treatment processes used in these plants are primary clarification by sedimentation and floatation followed by biological treatment (Faubert et al., 2016). These methods allow the removal of suspended and floating materials and toxic compounds from the wastewater streams that constitute the pulp and paper mill sludge (PPMS) (Kamali and Khodaparast, 2015), a mixture of primary and biological sludge. PPMS presents high composition variability, contains a large amount of water, and is produced in large quantities. It was estimated that 0.3–1 m3 of primary sludge is generated per ton of produced paper (Veluchamy and Kalamdhad, 2017) while the biological or secondary sludge (BS) is produced in less quantity than the primary sludge (Faubert et al., 2016).
3 Wastes characterization from a Portuguese paper and pulp industry
3.1 Fly ashes and exhausted sands
The chemical composition of fly ashes and sand waste reported in the literature and measured by X-ray fluorescence (XRF) is presented in Table 1. Results show that the main components of both FA, CT and CA, are silica (SiO2), alumina (Al2O3) and calcium (CaO). Saeli et al. observed that, in CT, the sum of SiO2 and Al2O3 amounts was ∼53 wt% and that iron was also present with an amount of 5.94 wt.% (Saeli et al., 2019b). The loss on ignition (LOI) at 1000°C was also determined in several works and vary between 6.39 and 14.3 wt.%. This wide range is mainly due to the type of material that is burned which can represent a drawback in the recycling route of this waste. X-ray diffraction (XRD) showed that the main crystalline phases of FA are: α–quartz, calcite, mica group mineral (like muscovite) and microcline, in agreement with the XRF results. Considering the particle size distribution, the mean particle size obtained for CT was 39 μm with a specific surface area (BET) of 3 m2/g (Saeli et al., 2019b) and for CA was 306.40 μm (Capela et al., 2021).
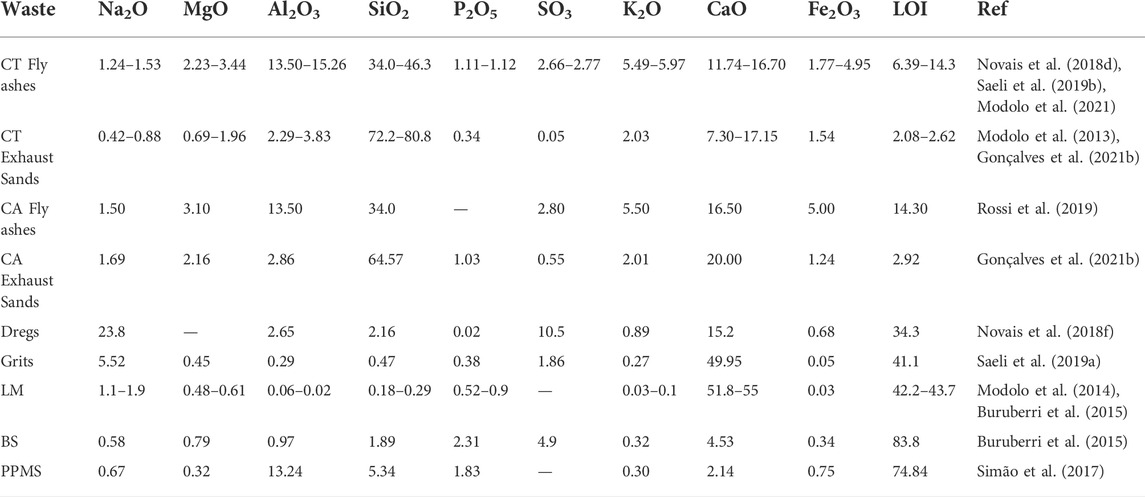
TABLE 1. Chemical composition of the wastes: fly ashes, sand, dregs, grits, lime mud, P&P mill sludge.
Regarding the exhausted sands (ES), the most abundant oxide, as expected, is SiO2 which varies between 65 and 81 wt.%. CaO is also present, 7.3 to 20 wt.%, see Table 1. Another noteworthy factor is the LOI values, 2 to 2.9 wt.% which are much higher than the reference sand, 0.28 wt.%, probably due to its chemical composition (presence of CaCO3 and/or organic matter). The particle size distribution of the as-received sands was performed in the work of (Gonçalves et al., 2021b). The authors observed that the highest mass content was obtained for the fraction higher than 500 μm, 62%–71% of the total mass of the sands, CA and CT, respectively. For the reference sand the value was 57%.
3.2 Dregs and grits
XRF analysis shows that the dominant oxides of dregs are MgO, CaO, Na2O and SO3 (8.13, 15.2, 23.8 and 10.5 wt.%, correspondently) with a high LOI value (34.3 wt.%). These results are in line with the calcination of calcite and pirssonite, as well as some of the organic content present in such waste. The authors also raise concerns about SO3 amount identified by XRF that suggests a poor deduction of the sulphur content in the boiler. The particles are irregular but very fine in size: all below 20 µm being the mean particle size near 6 µm (Novais et al., 2018f). It is also important to state that dregs contain, in its composition, several heavy metals as Novais et al. demonstrated (Novais et al., 2019a). Chromium, cobalt, copper, lead, nickel and zinc were all identified by XRF, at a ppm level between 50 and 150 except Cu which was found in much higher amount, around 3075 ppm (Novais et al., 2019a). This will have an impact on potential recycling methodologies as the possible heavy metals leaching from the wastes might limit their applications range for this challenging waste stream. Nevertheless, as it will show later in this review, recent studies suggest the feasibility of incorporating fairly high amounts of dregs in geopolymers, while trapping the hazardous components inside the binders’ framework.
Grits were fully characterized by Saeli et al. Saeli et al. (2019a), Saeli et al. (2019b), Saeli et al. (2018). This residue presented a moisture content of ∼7 wt.%. By XRF CaO is found to be the main constituent (49.45 wt.%) followed by Na2O (5.52 wt.%), while the other components are detected in much lower amounts (below 2 wt.%, as can be seen in Table 1. The LOI value of the waste was found to be 41.1 wt.%, attributed to the high-temperature decomposition of calcium carbonate and sodium bicarbonate. By XRD it was found that grits are mainly (>95 wt.%) constituted by calcium carbonate (CaCO3), also presenting some minor amounts of sodium bicarbonate (NaHCO3), results that are in accordance with the ones obtained by XRF. Grits presented a broad particle size distribution, ranging from 1 to 12.5 mm, but showing just a small percentage (2 wt.%) of particles with a diameter inferior to 1 mm.
3.3 Lime mud, biologic sludge and P&P mill sludge
Lime mud (LM) is mainly composed of CaO (51–55 wt.%). XRF analysis also identifies a large loss on ignition (LOI) at 1000°C (42–43.7 wt.%) associated with the thermal decomposition of calcium carbonate. In fact, differential thermal analysis shows a strong endothermic band centered at 828°C, typical of calcite decomposition (Modolo et al., 2014; Buruberri et al., 2015). In line with the XRF, the XRD analysis only showed the presence of calcite (CaCO3). Further, LM is composed of finer particles, with a mean value of around 10–12 µm and a maximum size of 26 µm.
Biologic sludge (BS) concentration of solids was found to be 17.2 wt.%. BS’s main chemical components are: SO3 (4.90 wt.%), CaO (4.53 wt.%), P2O5 (2.3 wt.%), and SiO2 (1.89 wt.%), see Table 1. BS shows high LOI values (83.80 wt.%), due to the presence of volatile components and organic compounds (Buruberri et al., 2015). BS particle size distribution was not evaluated because after being dried the sample was predominantly formed by aggregates.
PPMS is mainly composed of Al2O3 (13.24 wt.%), SiO2 (5.24 wt.%), CaO (2.14 wt.%), and P2O5 (1.83 wt.%) (Simão et al., 2017). PPMS presented a lower LOI than BS (74.84 wt.%). The water content of PPMS is very high, ∼86 wt.%, therefore a drying step is needed. PPMS showed low crystallinity, even so, quartz and calcite were detected. Its D50 value was found to be 20.7 µm.
Figure 3 presents the micrographs of some of the P&P wastes: fly ashes, exhausted bed sands, dregs and lime mud. Both FA and dregs are composed of irregularly shaped particles, presenting a rough surface and a broad particle size range (between a few microns and >100 μm) (Novais et al., 2018f; Capela et al., 2021). Further, it can also be observed that CA presents much bigger particles than CT which is in accordance with the laser diffraction results (Capela et al., 2021).
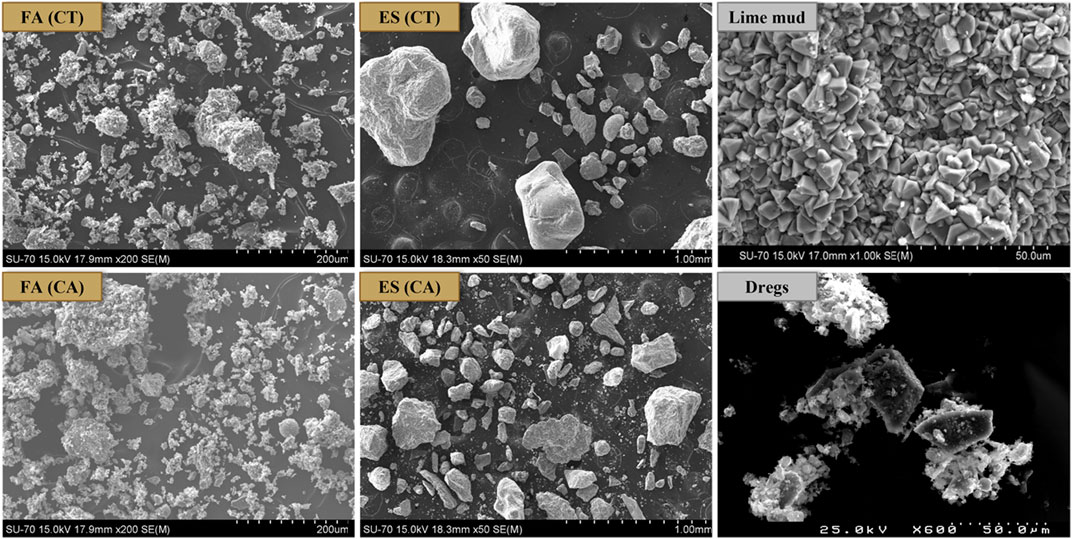
FIGURE 3. Microstructure of the fly ashes [adapted from Capela et al. (2021)], exhausted bed sands, dregs and lime mud [adapted from Modolo et al. (2014)].
Gonçalves et al. (2021b) compared the exhausted sands with the commercial sand and, as observed in Figure 3, the waste sands are composed of irregular grains whereas the commercial sand has more regular rounded forms. However, as ES will be introduced as aggregate these forms might not have a negative influence on the mortar’s properties. Lime mud presents crystals in its microstructure being those related to its composition, calcium carbonate (Modolo et al., 2014).
4 Possible applications for the P&P waste streams
The cement production process is, nowadays, responsible for up to 5% of the total CO2 emissions (Statista, 2020a; 2020b). Hence, to turn this process more sustainable and meet the net zero emissions by 2050, lower carbon footprint materials have been investigated (Vass et al., 2021).
An overview of the different types of applications is described in the following section which is divided into subsections: 4.1 cement-based materials including clinker and dense materials; 4.2 alkali-activated materials including dense and porous materials, adsorption of pollutants, pH control; and 4.3 other applications.
4.1 Cement-based materials
4.1.1 Clinker
Buruberri et al. studied the utilization of lime mud (LM), biological sludge (BS) and fly ash (FA) as secondary raw materials in the synthesis of belitic and Portland clinkers (Buruberri et al., 2015). For the clinker synthesis, eleven compositions were tested, starting from the mixture of different quantities of LM, BS and FA. The formulations were developed based on three principles: obtain a clinker with a composition rich in belite or Portland-type, maximize the incorporation of BS and lessen the moisture content. LM was used as the main source of CaO, BS besides adding energy to the system acted as a fluxing agent, and FA behaved as a fluxing agent and provided CaO, SiO2, Al2O3 and Fe2O3. The prepared compositions were fired at four temperatures (1300, 1350, 1390 and 1455°C). The authors concluded that belitic and Portland clinkers were obtained from some of the tested formulations. It should be stressed that the obtained Portland clinker was fired at 1390°C, which represents a major energy gain compared to the temperature currently used in the industry (∼1450°C). The obtained belite-based clinker was used to prepare CEM II A-L cement according to EN197-1:2011 (CEN: European Committee for Standardization, 2011) by being blended with LM and gypsum. This cement was then successively tested in the production of mortars with a slump value of 167 ± 2 mm, proper for indoor and outdoor plastering applications, that were cured for 7, 28, and 90 days. The authors observed an increase of the compressive strength of the mortars with the rise of the curing time: 6.1, 10.2 and 13.3 MPa for 7, 28 and 90 days, respectively. Their density increased up to 28 days of curing and then remained unchanged, 2.03 g/cm3. It was concluded that the hardening of the mortars was caused by the clinker reaction with water that formed hydrated aluminates and silicates. After 7 days of curing the achieved compressive strength already meet the requirements for interior and exterior applications (6 N/mm2). The hardened mortars did not show the formation of efflorescences or other deterioration signs that could compromise their durability.
Simão et al. (2017) evaluated the preparation of clinker from LM, FA and pulp and paper mill sludge (PPMS). For the clinker synthesis, five formulations were prepared based on lime saturation factor, Bogue equations, moisture content and maximizing the content of the waste streams in the compositions. The formulations were fired at three temperatures (1350, 1400, and 1455°C). The obtained clinkers were mainly constituted of belite and alite but other phases like tricalciumaluminate, ferrite and, in some samples, lime were also present. These crystalline phases are those commonly found in commercial clinkers. A clinker that was prepared with the three wastes, heat-treated at 1455°C, presented a high amount of alite and the best fitting in the Rietveld quantification, was the one chosen to produce eco-cement. It was blended (95 wt.%) with gypsum (5 wt.%) and its strength development was tested in a mortar formulation. For comparison purposes, mortars with ordinary Portland cement were also prepared. The used water to binder ratio (w/b) of the cement-based mortars was 0.48. In the case of the eco-cement-base mortars, to achieve identical workability, the w/b had to be 0.75. Eco-cement-based mortars presented a compression strength of ∼16 and 21 MPa after 7 and 28 days of curing, respectively. Lower values than the ones achieved by the cement-based mortars, ∼32 MPa for 7 days of curing and 43 MPa for the longer curing time. The higher amount of water used in the preparation of eco-cement-based mortars was pointed out as the main factor responsible for the lower compression strength values. Nevertheless, the obtained results were considered satisfactory since eco-cement was produced, exclusively, from waste.
4.1.2 Dense mortars
Rajamma et al. (2009) studied the replacement of Ordinary Portland cement (OPC) type I by different amounts of biomass fly ashes (10, 20 and 30 wt.%). The formulation with fly ash CA exhibited a heat of hydration similar to that of the pure cement paste and the hydration rate and phases formation depend on the alkali content and the water to binder ratio. The authors concluded that the replacement, up to 20 wt.%, of OPC by fly ash does not compromise the mechanical properties of the material. Alkali-silica reaction is an undesired process as it causes the degradation of concrete structures. The effect of the presence of fly ash in the mitigation of the alkali-silica reaction was studied by (Esteves et al., 2012). The mortars were prepared with 20 and 30 wt.% of fly ash as a cement replacement. The following trends were reported: 1) the expansion of the mortars tend to reduce with the FA incorporation; 2) fly ash CA is more effective than CT, as the mortars prepared with CA present higher mechanical (compressive and flexural) strength; and 3) the addition of 10 wt.% of metakaolin increased the properties of the mortars and also significantly improved the expansion results mitigating the alkali-silica reactions. These findings suggest the feasibility of incorporating biomass fly ashes in concrete (Esteves et al., 2012).
Continuing the previous work, Rajamma et al. (2015) studied the effect of biomass fly ashes on the flow behaviour (workability and rheology), setting time, temperature of hydration and electrical resistivity. The authors observed that by increasing the percentage of fly ash more water was required to attain the same fresh conditions due to the smaller particle size of the FA, tendency to agglomerate and retention/absorption of water molecules. The setting time was also increased and the impedance measurements showed a lower resistivity than the reference when FA were used. This tendency might be explained by the higher concentration of mobile species, namely sodium ions, introduced by the FA. The authors also observed that the differences between the two types of ashes (CA and CT) are not expressive in the workability and setting time behaviour of the fresh pastes. Regarding the hydration temperature, the replacement of cement by FA decreased the hydration temperature which might indicate a delay in the hydration process. Concerning the hardened state properties, no significant differences were observed. Therefore, the authors concluded that the overall performance is acceptable and the incorporation of biomass fly ashes is a viable solution (Rajamma et al., 2015).
More recently, Capela et al. (2021) studied the recycling of biomass fly ash (FA), CA and CT, as supplementary cementitious material in a commercial screed mortar. A pre-treatment of the FA was conducted (sieving and grinding) and its impact was evaluated. The authors observed that the workability decreases with the increase of the FA content, either using FA as received or sieved. Increasing FA levels contributed to lower density, higher water absorption and lower strengths (compressive and flexural), coherent with porosity enhancement. When using grounded FA, this tendency is attenuated, this being related to the better homogeneity of the mixtures that resulted in better compactness. Density and water absorption values are closer to the ones of the standard composition. The samples proved to be resistant to 25 freeze-thaw cycles and the replacement of 17% of OPC with FA met the technical requirements for compressive strength (10 MPa) as well as for flexural strength (3 MPa) without any pre-treatment (Capela et al., 2021).
Modolo et al. (2013) evaluated the utilization of exhausted bed sands CT, produced from bubbling fluidized bed combustion of forest biomass residues, as a substitute of one of the aggregates (coarser sand) in a rendering mortar formulation. The ES was sieved (between 250 and 1000 µm) to obtain a particle size distribution similar to that of the commercial virgin sand and then washed in an industrial plant. By washing the ES its soluble chloride content was reduced by about 60%. This was an important achievement since Cl concentration determines the amount of ash that can be incorporated into a mortar/concrete formulation. According to EN 998-1:2016 the Cl content of a mortar/concrete formulation should be lower than 0.1 wt.%. Mortars with 0, 50 and 100 wt.% substitution of the coarser sand by the two types of pretreated ES were prepared. In all the ash-containing mortars, the onset of setting started slightly earlier, and the time interval between the beginning and final setting time was shortened, compared to the standard composition. This behavior was attributed to the higher content of chlorides in the ash than in the sand. In the hardened state, the sample’s compressive strength, elasticity modulus and shrinkage were evaluated. The incorporation of ash induced small variations in the studied properties, with all formulations accomplishing the required specifications. From the obtained results it was assumed that the ES particles are not as inert as the sand. Nevertheless, further studies on the durability of the samples were suggested.
In a later work, Modolo et al. (2015) performed the physical, chemical and mineralogical characterization of ES CT, towards its landfilling classification and its valorization in an adhesive mortar formulation as a coarser sand replacement. Based on the obtained results ES was classified as a non-hazardous material for landfilling, according to 2003/33/CE (European Parliament and of the Council, E.C., 2003) and Decree-Law no 152/2002 Decree-Law 152/2002-Solid wastes (2002). The ES was sieved (between 250 and 1000 µm) and adhesive mortars with 0, 25, 50 and 100 wt.% of sand replacement by ES were produced. The ash containing formulations showed a lower water demand to get suitable workability (measured by the slump test). The ES containing mortars showed higher wettability than the standard formulation. From the transference test, it was observed that the non-filled area of the tiles covered with the standard formulation was higher than that of the ones covered with the ash containing mortars. For all the tested replacement percentages the values obtained for the transference capacity were superior to 70% after 40 min of testing. The observed results were attributed to physical differences between the ES and the sand. Namely, ES has particles with a rough surface and a higher percentage of smaller particles compared to commercial sand. In the hardened state, tensile adhesion strength was evaluated, and it was observed that it improved with the increase of ES content in samples with three storage conditions: standard, wet and heat. This result was attributed to the improved interfacial contact between the adhesive and the ceramic tile, due to the observed increase in wetting and transfer capability demonstrated by the ash-containing samples. This tensile adhesion strength improvement led to a change in the failure pattern, from the tile–adhesive interface to a cohesive failure inside the adhesive.
Modolo et al. (2014) also studied the incorporation of LM in mortars. The samples containing 30 wt.% LM exhibited the highest torque and yield stress values, while the plastic viscosity remained almost constant. The spreading of these mortars decreased by about 15% compared with the reference. The setting time was also reduced but LM did not significantly influence the hydration kinetics. The compressive strength of the LM samples increased by around 8% at 28 days of curing (compared to the control sample) but in the mixtures with 30 wt.% there was a slight reduction after 28 days of curing. Although to use LM in dry-mixed industrial mortars, it is necessary to eliminate its moisture, it is possible to use this residue thus improving the economic and environmental aspects related to waste management and saving virgin raw materials (Modolo et al., 2014).
Biomass fly ash has been studied as supplementary cementitious material, as it can present pozzolanic activity. This behaviour is related to the sum of SiO2, Al2O3, and Fe2O3 amounts available in its chemical composition (Rajamma et al., 2009; Berra et al., 2015; Capela et al., 2021), and to what extent these three oxides are present in the fly ash amorphous phase (Berra et al., 2015). Fly ash particle size reduction can also enhance the ashes’ reactivity (Capela et al., 2021). The pozzolanic reaction is characterized by the reaction during cement hydration, of Ca(OH)2 from clinker with SiO2 and Al2O3 from fly ash, producing hydrated calcium aluminate (C-A-H) and hydrated calcium silicate (C-S-H) (Capela et al., 2021). Some biomass fly ash can possess hydraulic activity (Rajamma et al., 2009; Esteves et al., 2012; Capela et al., 2021), which can also contribute to mechanical strength development (Esteves et al., 2012). Like a hydraulic binder, it chemically reacts with water, sets, hardens and is capable of maintaining its strength and stability even beneath water, EN 197–1:2011 (CEN: European Committee for Standardization, 2011).
Modolo et al. (2015) concluded that LM particles agglomeration or tridimensionality structures formation can affect mortars’ workability. Furthermore, LM incorporation will affect the pH of the hydration solution and influence the hydration mechanism. Other factors that may impact the setting mechanism, such as the presence of Cl− ions on LM, the reaction between Cl− ions and C3A (tricalcium aluminate) or C4AF (tetracalcium aluminoferrite) implies in the chloroaluminates formation that tend to expand and increase the amount of porosity.
4.2 Geopolymers
4.2.1 Dense materials
Saeli et al. (2019c) tested another pulp and paper industry residue in the production of geopolymeric binders and mortars for construction, the alkaline effluent. The effluent replaced the distilled water used to dissolve NaOH pellets in the activator solution and several NaOH/Na2SiO3 ratios and water to alkaline effluent substitutions were tested. The formulation with 70 wt% Biomass fly ash (BFA), 30 wt% MK, prepared with a solid/liquid ratio of 0.78 and a sodium hydroxide/sodium silicate ratio of 1:3 presented the best results and the differences between the samples prepared with alkaline effluent (instead of water) were not substantial, presenting environmental benefits. Mortars with the best binder and commercial sand were studied and the best formulation, with binder to aggregate ratio of 1:3, showed good workability and compressive strength higher than 20 MPa, being in class M20. Nevertheless, all the formulations were at least class M10 (Saeli et al., 2019c).
Saeli et al. (2019a) tested lime slaker grits as aggregate and biomass fly ash as precursor/binder of geopolymeric mortars. The influence of the aggregate granulometry and binder/aggregate ratio was accessed: the maximum size of the used grits was 12.5 mm. The use of finer grits decreases the consistency of the geopolymer mortars. The decrease of aggregates amount, by increasing the binder to aggregate ratio, improves the consistency. The same increase or the size enhancement improves the bulk density, while the water absorption decreases, and the capillary coefficient increases. As expected, the increase in the relative amount of aggregate decreases the compressive strength of the mortars. Anyway, the majority of formulations show compressive strength above 10 MPa, the limit for use in construction (Saeli et al., 2019b).
Another study conducted by the same authors (Saeli et al., 2019a) tested the use of BFA as a partial substitute of MK in the precursor mixture, while grits were used as aggregate with different binder/aggregate (B/A) ratios. To keep the same aggregate particle size distribution commercial siliceous sand was also used. The authors observed that geopolymer mortars with the incorporation of residues presents lower compressive strength than pure binder. The formulation that showed the highest mechanical resistance were the ones with 1:5 B/A ratio for both grits or grits + sand, 18.89 ± 1.26 MPa and 23.17 ± 1.17 MPa, respectively. The authors also observed that by increasing the aggregate amount, and by decreasing the binder to aggregates ratio, a more homogeneous paste and higher compressive strength values were obtained. All tested compositions are suitable for masonry applications in construction because mechanical strength higher than 10 MPa at 28 days of curing were achieved. Nevertheless, the authors propose the use of additional components in order to improve the workability of the paste, setting time, shrinkage and on the main engineering properties of the materials. Biomass fly ash, an aluminosilicate material, can act as a source of reactive silica and alumina in the production of geopolymer binders. Nevertheless, the reactivity of this waste stream is lower than that seen when using virgin and high purity precursors such as calcined kaolin.
Saeli et al. (2020) used lime mud (LM) as filler in geopolymeric mortars for construction. The experimental work was divided in two parts: 1) one with the addition of LM with no water adjustment to correct the workability; 2) the second one with water adjustment. The maximum LM amount was 12.5 wt% in the first case. The use of 7.5–12.5 wt% of LM proved to be beneficial to the mechanical strength of the material since it improves the classification of the mortars from M20 to M25. 10% LM assures a good compromise between workability and mechanical strength. The water adjustment to correct the workability allowed the use of higher LM amounts but then hardened properties were negatively affected (Saeli et al., 2020).
The grits coarser fractions were tested as aggregates of geopolymeric concrete (70% fly ash +30% metakaolin) by (Saeli et al., 2018). Two distinct granulometric fractions were used, one between 0.5 and 1.5 mm and the other from 0.5 to 5 mm. The authors also studied the influence of binder: aggregate ratio (1:1, 1:2 and 1:3). The use of coarser fractions will minimize the bending resistance, while the compressive strength tends to increase. As expected, the use of lower binder: aggregate ratios diminish the compressive strength of the samples. Samples prepared with 1:1 ratio show resistance values over 15 MPa (M15 classification). All other samples belong to M10 class.
The incorporation of dregs as filler in geopolymeric mortars was first considered in (Novais et al., 2018f), while a follow-up study evaluated also the heavy metals leaching by the dreg-containing geopolymers (Novais et al., 2019a). Results showed that increasing the amount of dregs affects the workability of the mortars and this was attributed to the fine particles of the dregs that absorbs water and reduces workability (Novais et al., 2019a). Interestingly, the addition of dregs enhanced the compressive strength of the specimens. The formulation containing the highest amount of dregs (100 wt%) achieved a compressive strength of roughly 13 MPa at the 270th day of cure, and this without the appearance of efflorescences. Regarding the hazardous leached elements, the samples’ proved to be capable of effectively immobilizing them within the geopolymer matrix. Only minor amounts of Cr and Cu were leached out, well below the contamination limit in soils (Novais et al., 2019a). Actually, samples containing an increasing amount of dregs show lower release of some toxic elements, namely As and Cr (notice that As is not present on dregs but in the fly ash), probably due to the achieved compactness increment. Novais et al. (2019a) showed that dregs are not involved in geopolymerization reaction once XRD of dregs-containing mortars clearly shows the presence of pirssonite, already detected in the waste. However, the major concern with this waste is its sodium content due to the possible formation of efflorescence. Through EDS analyses, no microstructural modification was observed. Further, even after water immersion followed by ambient drying, none of the prepared mortars showed the presence of efflorescence (Novais et al., 2018f). Consequently, the authors concluded that dregs do not negatively affect the geopolymer microstructure and that stable long-term geopolymers were produced.
Novais et al. (2017a) studied the influence of glass fiber fabric (GFF) waste incorporation as a reinforcement agent on the properties of a metakaolin-based geopolymer. The used GFF comes from off-cuts generated in wind turbine blade production. The authors observed that the introduction of the fibers improved the ductility of the hardened samples and inhibited their complete fracture. Further, the incorporation of fibers improved the compressive and tensile strength of the samples, the best results being achieved with the utilization of 6 mm fibers. The incorporation of 2 wt.% of these fibers promoted an increase in the tensile strength of ̴ 77%, while with 3 wt.% the compressive strength raises ̴ 162% when compared to results obtained for samples prepared without fibers. Based on these good results, the authors produce geopolymer-fiber composites using BFA as the main (70%) silica and alumina source blended with metakaolin (30%). The GFF was used as a reinforcement layer embedded in the geopolymer matrix. To evaluate the influence of the GFF amount on the properties of the cured samples, four formulations were prepared. One without the GFF (only the geopolymer matrix), and the other three containing one, two, and three layers of GFF arranged parallel to the base of the specimen and inserted between binder layers. In the 28 days cured samples it was observed that the density of the samples decreased with the addition of the GFF while the obtained values for the water absorption were similar in all samples. The authors also noticed that the introduction of the GFF layers improved the flexural strength (up to 144%) when compared to the specimen prepared only with the geopolymer matrix. It was verified that the flexural strength of the samples increased with the increment of the number of GFF layers and that its presence avoided the complete fracture/failure of the samples and increased their ductility.
Senff et al. (2020) concluded that the GFF 6 mm cuts can be used as a reinforcement agent in porous mortars formulations without negatively impacting their thermal conductivity. For that, the authors evaluated the influence of aluminum powder (AP), as a porogenic agent, and GFF, as a reinforcement agent, in the properties of geopolymeric porous mortars. Based on previous works (Novais et al., 2017a; Novais et al., 2018d), for the mortars production BFA was employed as the main aluminosilicate source and the GFF was used cut to 6 mm length fibers. From the flow table results, the incorporation of AP and fibers was limited to 0.2 and 2.0 wt.%, respectively. In the hardened samples, it was noticed that the increment in the added AP content ruled the observed decrease in the bulk density, and the increase in the total porosity and water absorption of the mortars. The 2.0 wt.% fibers incorporation ameliorated the flexural (23%) and compressive strength (30%) of the mortars prepared with 0.2 wt.% of AP. This behavior was explained by the fibers, by being randomly dispersed in the geopolymeric porous matrix, formed a holding frame that stabilized the microstructure.
Gonçalves et al. (2021b) investigated one-part alkali activated materials (AAMs) using only blast furnace slag as the solid precursor, and sodium metasilicate, as the solid activator. The authors developed, for the first time, mortars in which the commercial sand was replaced by exhausted bed sands from biomass burning boilers. The mortars prepared with commercial sand presented high compressive strength, 79 MPa, values obtained after 28 days of curing. The mortars developed with exhausted sands exhibit outstanding compressive strength values, from 70 to 86 MPa, not affecting the other material’s properties (setting time, apparent density, and water absorption). This work suggests the feasibility of using exhausted bed sands, from biomass boilers, as aggregates in AAMs mortars production.
Table 2 presents a comparison of the main properties of all works described above (samples cured for 28 days) and reports the classes of resistance of the materials, according to EN 998-2. Each class have a specific application being: M2.5—non-load-bearing, M5—all types of exterior and interior walls, M10—masonry applications like indoor and outdoor wall, M15—structural reinforcement of masonry structures and M20.
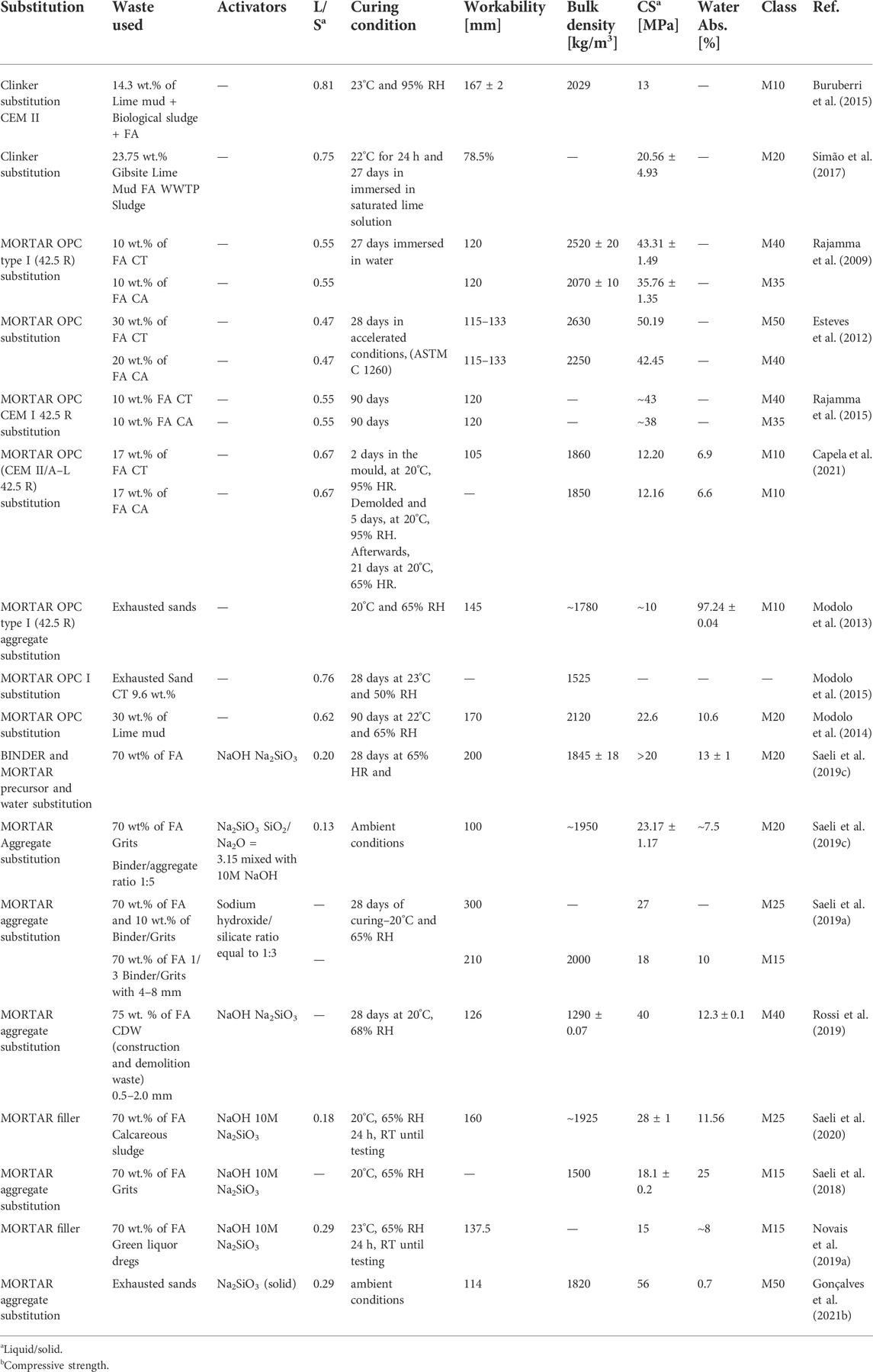
TABLE 2. Comparison of the main properties and estimated classes of resistance (EN 998-2) of geopolymers synthesised using P&P wastes.
4.2.2 Porous materials
4.2.2.1 Thermal insulation
The feasibility of using P&P wastes in the synthesis of low thermal conductivity geopolymers has been explored. The decrease in the geopolymers density can be achieved by the use of creating foaming agents, such as H2O2 or Al powder (Novais et al., 2016c; Novais et al., 2019c; Senff et al., 2020), or by the incorporation of porous aggregates like cork or construction and demolition waste (Rossi et al., 2018; Novais et al., 2021), or a combination of both strategies (e.g., multi-layered materials) (Novais et al., 2020d). Table 3 summarises the most recent studies carried out using P&P wastes.
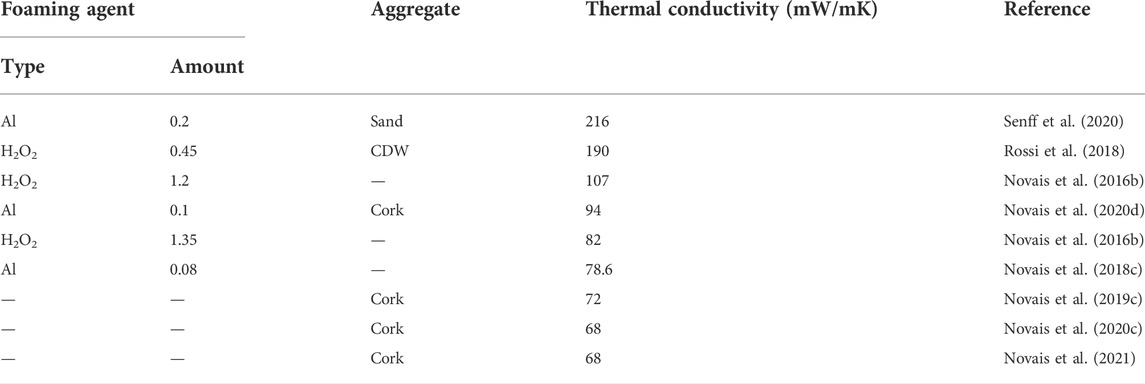
TABLE 3. Comparison of the thermal conductivity of the different alkali-activated materials reviewed.
In one of the first studies, Novais et al. used different amounts of H2O2 (0.03, 0.15, 0.30, 0.90 and 1.2 wt.%) to study the influence on thermal properties of FA based geopolymer. The XRD shows that increasing the amount of H2O2 has no major influence on the mineral phases’ formation. Nonetheless, the SEM and optical micrographs revealed strong microstructural changes, the increasing amount of H2O2 effects especially the porosity as well as the pore size distribution. The authors studied the relationship between pore forming agent and average pore size, number of pores, area ratio, water absorption, apparent density, and total porosity. Typically, all parameters increased with the concentration of pore forming agent, except the apparent density that decreased. The thermal conductivity decreased with the increasing amount of foaming agent reaching a value as low as 107 mW/m K (Novais et al., 2016b).
Novais et al. also studied the influence of NaOH concentration and the influence of water amount on the properties and microstructure on FA based geopolymers, again using H2O2 as a foaming agent. For that 0.72 wt.% and 1.35 wt.% of H2O2 were added, 8 M 10 M and 12 M NaOH solutions were used, and the water content was also changed. Results showed that the water content and NaOH concentration strongly affect the viscosity of the pastes, while the H2O2 content, at least in the studied range. The use of lower alkali concentration (NaOH) enhances the porosity and also changes the connectivity of the pores, as coalescence takes place resulting in a higher volume of open porosity. The thermal conductivity strongly decreased (up to 40%) when H2O2 is added. This property is also controlled by the NaOH molarity: lower molarities led to smaller thermal conductivities, being 82 mW/m.K the minimum value achieved. This effect was attributed to viscosity changes of the slurries in the early stage of geopolymer formation. The NaOH concentration highly affects the apparent density of the samples, with a direct correspondence in the thermal conductivity values. The attenuation of the thermal conductivity was more evident for compositions containing higher amounts of H2O2, which is consistent with the observed change in pore morphology (Novais et al., 2016a).
Rossi et al. (2018) also studied the influence of H2O2 on waste-based mortars. The binder was produced using FA waste as a solid precursor and CDW as aggregate. In order to produce lightweight geopolymers Rossi et al. kept the solid to liquid ratio at low levels, so the reference mortar shows high porosity, around 44%. Nonetheless, when 0.45 wt.% of H2O2 was added, the porosity increased to 55.9%. One of the major impacts was observed on the typical pore size of the samples that increased form 0.198 µm up to 31.88 µm with the highest amount of H2O2 (0.45 wt.%), which also represents an increment on BET surface area from 18.93 to 26.7 m2/g. As it is shown in Table 3 the lowest value of thermal conductivity seen in this study was 190 mW/m K.
The influence of aluminium powder and water amount on the thermal conductivity of FA-containing geopolymers was studied by Novais et al. (2018a). The lowest thermal conductivity being 78.6 mW/m K.
Cork-containing samples show thermal conductivities between 94 and 68 mW/mK (Novais et al., 2019c; Novais et al., 2020b; Novais et al., 2020d; Novais et al., 2021).
4.2.2.2 Moisture regulation
Moisture buffer value (MBV) tests were performed to verify the ability of samples to absorb and release water after exposure to daily/cyclic humidity fluctuations. In other words, MBV quantifies the amount of moisture (H2O) absorbed or released by a material when it is subjected to repeated daily fluctuations between two specified relative humidity levels. In the reviewed manuscripts, measurements were carried out according to the Nordtest protocol (Rode et al., 2005a), the equipment used was a climatic chamber (Fitoclima 300 EP10 from Aralab) and the mass variation was measured with a balance. The moisture buffer value is given by the mass variation that is adsorbed and released from a given area of the material under a specific moisture variation and is given by the following equation:
Where
De Rossi et al. used waste-based geopolymer mortars (CDW as aggregate) with different porosities; the MBV for such samples fluctuate from 0.80 g/m2 Δ % RH (reference mortar without foaming agent) to an impressive higher value of 5.61 g/m2 Δ%RH (for the sample with the highest amount of foaming agent); this value is one of the highest ever reported to date for this type of materials (Rossi et al., 2018). This demonstrates that an improvement in moisture buffering capacity can be achieved by increasing the amount of foaming agent. It is important to mention that these values were obtained in a cycle of 12 h at 50 %RH + 12 h at 75%RH.
Rossi et al. (2019) combined biomass fly ash with construction and demolition waste (CDW), to produce geopolymer mortars. BFA was used as precursor while CDW partially substitute a commercial sand as aggregate. The use of CDW as fine aggregate instead of sand increases the compressive strength by 78% and the flexural strength by 115%. Regarding the fresh state properties, the use of CDW reduces the spread, and this effect was attributed to the fineness of the waste and its higher water absorption.
Gonçalves et al. (2021a) used bi-layered AMMs where only the porous surface was exposed to environmental changes (humidity fluctuation). The MBV achieved was 2.71 g/m2 Δ % HR which is considerably lower than that reported by Rossi et al., nevertheless, it is considered “Excellent” which is the top classification according to the Nordtest protocol (Rode et al., 2005a). This shows that bi-layered AMMs can be a good method to maximise the multifunctional behaviour of the samples.
The authors also investigated the influence of different types of cork as aggregate on the MBV capacity. Novais et al. (2020c) used black expanded cork (around 6 mm in size) as a lightweight aggregate. Not surprisingly, by increasing the amount of cork, the apparent density decreases to a value almost 7 times lower than the reference geopolymer, as seen above. As for the MBV, increasing the amount of cork in the samples resulted in a higher MBV (above 1.37 g/m2% RH). With 75 vol.% cork MBV reached 1.89 g/m2% RH. The authors further enhanced the amount of cork, but with a negative effect on the specific MBV (lower values compared to the 75 vol.% sample); however, composites containing 87.5 and 90 vol.% cork show very reproducible absorption and desorption cycles, demonstrating a good ability to buffer the moisture fluctuations over time (Novais et al., 2020c).
In a similar work conducted by Novais et al. (2021), the authors investigated the influence of two types of cork “fine” and “coarse” (different sizes, 0.5 and 2 mm respectively). The incorporation of 20 vol.% of “coarse” cork resulted in a slightly higher MBV (1 g/m2 Δ % RH) compared to the reference sample (no cork added, 0.89 g/m2 Δ % RH). Increasing the cork content to 80 vol% has a major impact on the moisture regulation ability: the composite containing the smaller size granules has a MBV of 2.22 g/m2 Δ % RH, which is 2.5 times higher than the reference. Further increasing cork volume up to 85 vol% did not induce better performance (MBV = 1.97 g/m2 Δ % RH). In addition to cork volume, cork granule size was also found to have a large effect on moisture buffering capacity: the use of coarser granules resulted in lower MBV due to the lower storage and release capacity of these samples. However, it should be noted that although the performance is lower compared to the use of smaller sized cork granules, these composites still exhibit better buffering capacity compared to the reference matrix, not only in terms of practical MBV but also with respect to the absorption/desorption pattern.
These results show that geopolymeric foams or AAM composites have the potential necessary to be used as moisture regulators. Almost all samples show “good” or “excellent” MBV classification (1.0 < MBV <2.0 g/m2% RH), and MBV >2.0 g/m2% RH, respectively, according the Nordtest protocol (Rode et al., 2005b).
4.2.3 Adsorption of pollutants
4.2.3.1 Heavy metals
Geopolymers exhibit interesting properties and their chemical structure presents a negatively charged aluminosilicate framework and charge balancing cations (Na+, K+ or Ca2+). In fact, this property plays a fundamental role in the adsorption of heavy metals present in distinct streams (e.g., industrial wastewaters), where these cations can be exchanged with the positively charged metals present in the solution. This material is then converted into an environmentally acceptable waste for land disposal (Duxson et al., 2007). Heavy metals or dye molecules immobilization on a geopolymer matrix is a chemical and/or physical process and studies exploiting this potential were already conducted (Ji and Pei, 2019).
The first work conducted by our research group in this field involved the preparation of geopolymer monoliths, based on metakaolin and fly ash (FA), for lead adsorption. Since porosity plays a fundamental role in the adsorption process, hydrogen peroxide was used (between 0 and 1.2 wt%) as a foaming agent. The total porosities were successfully controlled, varying from 41.0 to 78.4%, while the corresponding apparent densities decreased from 1.21 to 0.44 g/cm3. Due to alkali leaching from geopolymer samples and their influence on the solution pH, samples were washed until neutral pH was reached. Non-washed samples were also used. Cylindrical discs of 22 mm diameter and 3 mm thickness were immersed and shaken during 24 h at room temperature and after fixed periods, aliquots were taken and the Pb2+ concentration was measured by atomic absorption spectrometry. The maximum lead adsorption, obtained with the higher porosity samples (prepared with 1.2 wt% H2O2), was 6.34 mglead/ggeopolymer. For desorption, samples were treated in water and acidic conditions. After 24 h, their recovery was not fully achieved, denoting strong fixation of lead onto the geopolymers matrix (Novais et al., 2016d). Another strategy involved the preparation of geopolymeric porous bulk-type samples for lead and zinc removal. These cubic samples presented total porosity of 84 vol% and bulk densities of 408 kg/m3 and 258 kg/m3 before and after washing, respectively. Metals removal by precipitation was obtained when using non-washes samples, while adsorption is the extraction mechanism when using the washed granules. Lead removal after 24 h of adsorption reached 16.5 mglead/ggeopolymer, while for zinc a value of 20.4 mg/g was obtained after 1 h precipitation.
Powdered materials show excellent pollutants removal efficiencies, but the experimental constraints in their collection post-use and the total cost are important drawbacks. Cm-size waste-based geopolymer foams (fly-ash based) were then prepared and tested for lead adsorption. In this case, NaOH molarity and the foaming agent content varied to evaluate the effect on the porosity. The highest removal efficiency was obtained with highly porous samples (100 ppm Pb2+, 4 h contact). Using 800 ppm Pb2+ solution, the lead uptake was maximal (105.9 mg/g), and corresponds to the best value ever reported for bulk-type geopolymer adsorbents. The possibility of reusing these foams was also studied, after mild-acidic treatment and water washing, after contact with 100 ppm Pb2+ solution. The samples with higher Pb2+ contents released 66.8% while the others containing lower Pb2+ concentrations released a lower amount (52.7% after 1 h immersion). With the obtained results the authors stated that mild acidic conditions promotes fast lead desorption, particularly in samples with high lead contents. After desorption, the samples were again reused in a Pb2+ 100 ppm solution during 4 h presenting similar adsorption behaviour to the first using cycle. This confirms the feasibility to reuse them as lead adsorbents (Novais et al., 2020a).
Recent work involved the preparation of 1 cm3 cubic foams and their performance as lead, copper, cadmium and zinc adsorbents in single, binary and multicomponent solutions. The foams were prepared considering previous studies by the authors (Novais et al., 2020a), using NaOH 8 M as activator agent. Regarding the physical properties of the cubic foams, the total porosity reaches 77.8% and bulk density is 0.53 g/cm3. The foams evaluation as heavy metals adsorbents was taken in 3 sorption tests: 1) single element (Pb2+, Cd2+, Cu2+ and Zn2+) with C0 between 1000 and 800 ppm and contact time of the adsorbent and the ion solution between 1 and 6 h; 2) binary systems with combination of two heavy metals, C0 = 10 ppm with 6 h contact time; 3) multicomponent systems with C0 = 10 ppm and 6 h contact time. Results showed that the removal efficiency is affected by the heavy metals nature and follows the sequence in terms of affinity in a single component system: Pb2+ > Cd2+ > Zn2+ > Cu2+. This tendency is related, among others, to the hydrated ionic radius and hydration enthalpy of the different heavy metals (Caetano et al., 2022).
4.2.3.2 Dyes
Colouring contamination of industrial effluents imposes serious threats on the environment and living organisms. Methylene Blue (MB) is a monovalent, cationic, aromatic organic compound, solid, basic, water-soluble and one of the most common dyes responsible for water contamination (Khan et al., 2022). Adsorption is a common method for dyes decontamination, turning porous geopolymers into feasible alternatives to be used as efficient precursors for dyes removal. The study by Li et al. (2006) was one of the first reports on the use of pulverized geopolymers in the removal of organic compounds from water, while the feasibility of using fly ash-based geopolymeric monoliths (not powders) was reported only in 2018 (Novais et al., 2018b). Geopolymers with distinct porosities were prepared and compared. As expected, especially for higher initial dye concentration (C0), highly porous samples exhibit higher adsorption performance, with uptake 3 times superior when the porosity doubles (from 40.7% to 80.6%). The reusability of these materials was also confirmed and after 5 cycles the removal efficiency was unaltered (Novais et al., 2018b). In a follow-up study, the preparation of geopolymer materials with higher specific surface area were studied. Fly ash-based geopolymeric spheres with 2.6 mm diameter were prepared and used as MB adsorbents from a synthetic wastewater. Higher uptake values were obtained when C0 increases, from 1.1 to 30.1 mg/g when MB concentration is 10 and 250 ppm, respectively. After 24 h contact with the spheres, uptake reached 79.7 mg/g, exceeding the values already reported for geopolymeric materials. Thermal regeneration allows the reuse of the material. After 8 cycles the removal efficiency decayed only 17%. (Novais et al., 2019b).
Also taking into consideration that once exhausted, the recovery of samples is easier than powdered adsorbents, Capela et al. developed inexpensive porous adsorbent monoliths prepared only with CA and aluminum powder (as porogenic agent), taking advantage of the FA’s self-hardening ability. The prepared monoliths were positively tested for MB adsorption. It was shown that the dye adsorption kinetics can be described by the pseudo-first-order equation and the adsorption process was characterised by the Type 2 Langmuir isotherm model with a maximum sorption capacity of ∼0.66 mg/g, determined for the samples with the higher total porosity, ∼72% (Capela et al., 2022).
In a distinct approach, activated carbon was produced from cork wastes and activated with a mixture of alkaline wastewater from the pulp and paper industry (50 vol%) and commercial sodium hydroxide. The obtained activated carbon owned a very high specific surface area (1670 m2/g). This adsorbent shows extraordinary removal efficiency (99.9% in 5 min) and MB uptake of 350 mg/g, being part of one of the most promising activated carbons produced for methylene blue removal. (Novais et al., 2018d).
4.2.4 pH buffering
In recent years, an innovative and greener alternative for pH regulation has been reported, involving the use of waste-containing geopolymer monoliths (Novais et al., 2016d) or spheres (Novais et al., 2017b). When immersed in water, these materials leach out significant amounts of hydroxyl ions from their structure. The presence of hydroxyl ions assures a prolonged pH adjustment, avoiding large fluctuations. Alkalis leaching from geopolymers can be controlled by the activator concentration (Zhang et al., 2014), nature of the binder (Novais et al., 2017b), solid-liquid ratio, and porosity (Novais et al., 2016d). Novais et al. (2016d) also suggested that the geometry of geopolymers has a major impact on their leaching behaviour, and the use of spheres instead of discs or cubes favoured the leaching of alkalis, due to the increase in the exposed area (Novais et al., 2016d). This pattern has been observed using both fly ash-based geopolymers and red mud-fly ash geopolymers, demonstrating an advantage of using mm size spheres as pH buffering materials (Novais et al., 2020c). Thus, waste-based geopolymers, including those prepared with P&P wastes, have the potential to be applied as pH buffering materials in systems such as anaerobic treatment for biogas production.
Novais et al. (2018g) studied the influence of the aluminosilicates source (metakaolin vs. fly ash) in the prolonged pH buffer of the complex anaerobic treatment of cheese whey. The authors tested the addition of spheres prepared from 33 wt.% of FA (MK-based spheres) and 75 wt.% of FA (FA-based spheres). After 70 days in an anaerobic digester, the addition of spheres assured pH stabilization at values close to those suitable for methane production by microorganisms (Gameiro et al., 2018). Also, the use of FA-based spheres improved the global methane production by 30% compared to methane production achieved with the use of MK-based spheres (Novais et al., 2018g).
The influence of the sphere’s porosity in long-term methane production from cheese whey by an anaerobic system was studied by Gameiro et al. (2019, 2021). The authors tested two anaerobic cycles, to evaluate the spheres’ capacity to continuously regulate the pH, even in stressful environmental conditions. The increased porosity of the FA-based spheres tested, induced by the addition of a foaming agent, enhanced the methane volume produced by two-fold and, in addition, improved the methane production rate by more than three-fold, leading to a stable anaerobic process after 87 days of operation (Gameiro et al., 2019). The authors also tested the performance of high porosity geopolymer spheres comparatively to the addition of alkaline chemicals for pH control. Once again, the spheres presented very good anaerobic performance after four cycles, with an improvement in methane yield produced of 25% (Gameiro et al., 2021).
Fly ash can also be used in the production of geopolymer spheres that incorporate bauxite residue (or red mud) in their composition (Novais et al., 2018e). The use of such spheres in anaerobic digestion systems was studied by Gameiro et al. (2020), which evaluate their performance in complex systems treating cheese whey, for 110 days. The use of red mud/fly ash geopolymer spheres promoted a prolonged pH stabilization, even after eleven anaerobic cycles, and improved by 94% the methane production, when compared with the addition of chemical alkalinity to stabilize the anaerobic system (Gameiro et al., 2020).
The use of fly ash-based geopolymer spheres for pH control and to promote the stability of anaerobic processes is an innovative and very promising strategy, thus contributing to the concept of circular economy, using wastes for the generation of new added-value products and obtaining sustainable energy sources, such as methane.
4.2.5 Other applications
Modolo et al. (2014) aimed to regenerate the ES from the fluidized bed in order to recirculate the material and partially substitute the fresh bed sand (FBS) in industrial bubbling fluidized bed combustors. The authors observed that physical, chemical and mineralogical characteristics of the FBS and ES are strongly dependent on the forest biomass used. Nevertheless, the authors state that by sieving the ES it is possible to recover almost 60% of the original ES particles (size between 0.3 and 1.0 mm), which have properties that allow its reuse as substitute of FBS for bed makeup in industrial bubbling fluidized bed combustors.
Rossi et al. (2019) synthetized faujasite and P zeolites through geopolymerization of biomass fly ash wastes at low temperature in a hermetic container. The raw materials were activated using a mixture of sodium silicate and sodium hydroxide, and then the specimens were cured at 60°C to obtain zeolite-containing geopolymers while hydrogen peroxide was used as a porogenic agent. XRD diffractograms showed the presence of faujasite zeolites regardless of the H2O2 content. P zeolite was formed without porogenic agent addition, resulting in an increase in the surface area (56.35 m2/g) in comparison with samples cured in room conditions (40.69 m2/g). The presence of zeolites and faujasite was affected by the curing time and temperature. The cure in hydrothermal conditions was crucial for the development of zeolites since the sample cured at room temperature did not show the formation of such phases. The zeolites presented a mechanical strength of up to ∼10 MPa which suggest applications as separation membranes or filters.
4 Conclusion
In this work, several case studies about possible valorisation strategies for the wastes generated in a pulp and paper mill, namely biomass fly ashes and exhausted sands from biomass boilers and co-generation plant, lime mud, grits and dregs from the chemical recovery cycle in the Kraft process, and biologic and P&P mill sludge from the wastewater treatment, were presented. The residues were successfully used in the laboratory production of new construction materials and adsorbents. The maximum incorporation or substitution content depends on the intended application but generally, 70 wt.% of wastes were used. Further, generically, no pre-treatment steps were applied to the wastes in order to ease its transition to an industrial application.
Despite the promising results presented here, it should be noted that one of the biggest constraints associated with the up-scaling of the various applications presented is related to the variation of the waste’s properties over time, mainly the chemical composition, as evidenced in the results shown in Table 1. These variations make it more difficult to incorporate, on an industrial scale, wastes whose composition varies over time into new products. A future approach involves life cycle assessment (LCA) studies, which may encourage the translation of many of these studies to an industrial scale. In addition, an economic and environmental analysis should be done to determine the maximum incorporation level of each waste for the intended application.
Nevertheless, this innovative approach is a more sustainable alternative to the commonly used landfilling, as it allows a reduction in the consumption of natural raw materials and contributes to the establishment of a circular economy model.
Author contributions
JL, MS, and RN contributed to conception, design and funding of the study. IV and TG wrote the first draft of the manuscript. MC, JC, AC, and CN wrote sections of the manuscript. All authors contributed to the final revision of the submitted version.
Funding
This work was developed within the scope of the project CICECO-Aveiro Institute of Materials, UIDB/50011/2020, UIDP/50011/2020 and LA/P/0006/2020, financed by national funds through the FCT/MEC (PIDDAC).
Acknowledgments
The authors would like to acknowledge the project ERA-MIN/0001/2019 (SMART-G—Smart Geopolymers) and MAXIMUM (PTDC-CTM-CTM-2205-2020) supported by Foundation for Science and Technology (FCT). JC (SFRH/BD/144562/2019) wish to thank Fundação para a Ciência e Tecnologia (FCT) for supporting his work.
Conflict of interest
The authors declare that the research was conducted in the absence of any commercial or financial relationships that could be construed as a potential conflict of interest.
Publisher’s note
All claims expressed in this article are solely those of the authors and do not necessarily represent those of their affiliated organizations, or those of the publisher, the editors and the reviewers. Any product that may be evaluated in this article, or claim that may be made by its manufacturer, is not guaranteed or endorsed by the publisher.
References
Bajpai, P. (2017). “Anaerobic technology in pulp and paper industry,” in SpringerBriefs in applied sciences and Technology. 1st ed (Singapore: Springer Singapore). doi:10.1007/978-981-10-4130-3
Berra, M., Mangialardi, T., and Paolini, A. E. (2015). Reuse of woody biomass fly ash in cement-based materials. Constr. Build. Mat. 76, 286–296. doi:10.1016/j.conbuildmat.2014.11.052
Buruberri, L. H., Seabra, M. P., and Labrincha, J. A. (2015). Preparation of clinker from paper pulp industry wastes. J. Hazard. Mat. 286, 252–260. doi:10.1016/j.jhazmat.2014.12.053
Cabrera, M. N. (2017). “Pulp mill wastewater: Characteristics and treatment,” in Biological wastewater treatment and resource recovery (London, UK: InTech). doi:10.5772/67537
Caetano, A. P. F., Carvalheiras, J., Senff, L., Seabra, M. P., Pullar, R. C., Labrincha, J. A., et al. (2022). Unravelling the affinity of alkali-activated fly ash cubic foams towards heavy metals sorption. Materials 15, 1453. doi:10.3390/ma15041453
Capela, M. N., Cesconeto, F. R., Pinto, P. C., Tarelho, L. A. C., Seabra, M. P., and Labrincha, J. A. (2022). Biomass fly ash self-hardened adsorbent monoliths for methylene blue removal from aqueous solutions. Appl. Sci. Switz. 12, 5134. doi:10.3390/app12105134
Capela, M. N., Tobaldi, D. M., Tarelho, L. A. C., Seabra, M. P., and Labrincha, J. A. (2021). Development of a commercial screed mortar with low OPC content by incorporation of biomass fly ash. Appl. Sci. Switz. 11, 9630. doi:10.3390/app11209630
CEN (2011). EN 197-1:2011 Cement Part 1: Composition, specifications and conformity criteria for common cements. Brussels: European Committee for Standardization.
Cherian, C., and Siddiqua, S. (2019). Pulp and paper mill fly ash: A review. Sustainability 11, 4394. doi:10.3390/su11164394
Cision, P. N., 2022. Cision PR newswire, Available at: https://www.prnewswire.com/news-releases/pulp-market-share-to-register-a-growth-of-usd-47-45-billion-at-a-cagr-of-4-08-increased-consumption-of-chemical-wood-pulp-to-boost-market-growth--technavio-301539679.html, Accessed date: May 2022.
Decree-Law 152/2002-Solid wastes (2002). Landfills classification-Portuguese legislation (in Portuguese). Lisbon: Ministério do Ambiente e do Ordenamento do Território.
dos Santos, V. R., Cabrelon, M. D., de Sousa Trichês, E., and Quinteiro, E. (2019). Green liquor dregs and slaker grits residues characterization of a pulp and paper mill for future application on ceramic products. J. Clean. Prod. 240, 118220. doi:10.1016/j.jclepro.2019.118220
Duxson, P., Fernández-Jiménez, A., Provis, J. L., Lukey, G. C., Palomo, A., and van Deventer, J. S. J. (2007). Geopolymer technology : The current state of the art. J. Mat. Sci. 42, 2917–2933. doi:10.1007/s10853-006-0637-z
EIA (2019). International energy outlook 2019 with projections to 2050. Washington, DC: U.S. Department of Energy.
EPA (2010). Available and emerging technologies for reducing greenhouse gas emissions from the pulp and paper manufacturing industry. North Carolina, USA: U.S. Environmental Protection Agency.
Esteves, T. C., Rajamma, R., Soares, D., Silva, A. S., Ferreira, V. M., and Labrincha, J. A. (2012). Use of biomass fly ash for mitigation of alkali-silica reaction of cement mortars. Constr. Build. Mat. 26, 687–693. doi:10.1016/j.conbuildmat.2011.06.075
European Parliament and of the Council, E.C. (2003). 2003/33/CE: Criteria and procedures for the acceptance of waste at landfills. Brussels: Official Journal of the European Communities.
Faubert, P., Barnabé, S., Bouchard, S., Côté, R., and Villeneuve, C. (2016). Pulp and paper mill sludge management practices: What are the challenges to assess the impacts on greenhouse gas emissions? Resour. Conserv. Recycl. 108, 107–133. doi:10.1016/j.resconrec.2016.01.007
FBI, 2021. Fortune business insights, Available at: https://www.fortunebusinessinsights.com/pulp-and-paper-market-103447, Accessed date: March 2022.
Gellerstedt, G. (2015). Softwood kraft lignin: Raw material for the future. Ind. Crops Prod. 77, 845–854. doi:10.1016/j.indcrop.2015.09.040
Gameiro, T., Correia, C. L., Novais, R. M., Seabra, M. P., Labrincha, J. A., and Capela, I. (2019). “pH control in anaerobic bioreactors using fly-ash based geopolymers as buffer material,” in Proceedings of the 2019 International Conference on Green Energy and Environmental Technology, Paris, France, 24–26 July, 2019, 133.
Gameiro, T., Novais, R. M., Correia, C. L., Carvalheiras, J., Seabra, M. P., Labrincha, J. A., et al. (2020). Red mud-based inorganic polymer spheres: Innovative and environmentally friendly anaerobic digestion enhancers. Bioresour. Technol. 316, 123904. doi:10.1016/j.biortech.2020.123904
Gameiro, T., Novais, R. M., Correia, C. L., Carvalheiras, J., Seabra, M. P., Tarelho, L. A. C., et al. (2021). Role of waste-based geopolymer spheres addition for pH control and efficiency enhancement of anaerobic digestion process. Bioprocess Biosyst. Eng. 44, 1167–1183. doi:10.1007/s00449-021-02522-w
Gameiro, T., Novais, R., Seabra, M. P., Tarelho, L. A. C., Labrincha, J. A., and Capela, I. (2018). “Geopolímeros para controlo de pH: Aplicação em processos de digestão anaeróbia,” in Proceedings of the XI Conferência Internacional de Ambiente em Língua Portuguesa, Aveiro, Portugal, 8–10 May, 2018.
Gonçalves, M., Novais, R. M., Senff, L., Carvalheiras, J., and Labrincha, J. A. (2021a). PCM-containing bi-layered alkali-activated materials: A novel and sustainable route to regulate the temperature and humidity fluctuations inside buildings. Build. Environ. 205, 108281. doi:10.1016/j.buildenv.2021.108281
Gonçalves, M., Vilarinho, I. S., Capela, M., Caetano, A., Novais, R. M., Labrincha, J. A., et al. (2021b). Waste-based one-part alkali activated materials. Materials 14, 2911. doi:10.3390/ma14112911
He, J., Lange, C. R., and Dougherty, M. (2009). Laboratory study using paper mill lime mud for agronomic benefit. Process Saf. Environ. Prot. 87, 401–405. doi:10.1016/j.psep.2009.08.001
Ji, Z., and Pei, Y. (2019). Bibliographic and visualized analysis of geopolymer research and its application in heavy metal immobilization: A review. J. Environ. Manage. 231, 256–267. doi:10.1016/j.jenvman.2018.10.041
Kamali, M., Gameiro, T., Costa, M. E. V., and Capela, I. (2016). Anaerobic digestion of pulp and paper mill wastes - an overview of the developments and improvement opportunities. Chem. Eng. J. 298, 162–182. doi:10.1016/j.cej.2016.03.119
Kamali, M., and Khodaparast, Z. (2015). Review on recent developments on pulp and paper mill wastewater treatment. Ecotoxicol. Environ. Saf. 114, 326–342. doi:10.1016/j.ecoenv.2014.05.005
Khan, I., Saeed, K., Zekker, I., Zhang, B., Hendi, A. H., Ahmad, A., et al. (2022). Review on methylene blue: Its properties, uses, toxicity and photodegradation. Water (Basel) 14, 242. doi:10.3390/w14020242
Kramer, K. J., Masanet, E., Xu, T., and Worrell, E. (2009). Energy efficiency improvement and cost saving opportunities for the pulp and paper industry. Berkeley, CA: Environmental Energy Technologies Division.
Kumar, M., Morya, R., Gupta, A., and Thakur, I. S. (2020). “Anaerobic biovalorization of pulp and paper mill waste,” in Biovalorisation of wastes to renewable chemicals and biofuels (Amsterdam, Netherlands: Elsevier), 41–61. doi:10.1016/B978-0-12-817951-2.00003-1
Lamers, A. S. F., Cremers, M., Matschegg, D., Schmidl, C., Hannam, K., Hazlett, P., et al. (2019). Options for increased use of ash from biomass combustion and co-firing. IEA Bioenergy Task 32, 1–61.
Li, L., Wang, S., and Zhu, Z. (2006). Geopolymeric adsorbents from fly ash for dye removal from aqueous solution. J. Colloid Interface Sci. 300, 52–59. doi:10.1016/j.jcis.2006.03.062
Manskinen, K., Nurmesniemi, H., and Pöykiö, R. (2011). Total and extractable non-process elements in green liquor dregs from the chemical recovery circuit of a semi-chemical pulp mill. Chem. Eng. J. 166, 954–961. doi:10.1016/j.cej.2010.11.082
Mesfun, S., Lundgren, J., Grip, C.-E., Toffolo, A., Nilsson, R. L. K., and Rova, U. (2014). Black liquor fractionation for biofuels production – a techno-economic assessment. Bioresour. Technol. 166, 508–517. doi:10.1016/j.biortech.2014.05.062
Meyer, T., and Edwards, E. A. (2014). Anaerobic digestion of pulp and paper mill wastewater and sludge. Water Res. 65, 321–349. doi:10.1016/j.watres.2014.07.022
Modolo, R., Benta, A., Ferreira, V. M., and Machado, L. M. (2010). Pulp and paper plant wastes valorisation in bituminous mixes. Waste Manag. 30, 685–696. doi:10.1016/j.wasman.2009.11.005
Modolo, R. C. E., Ascensão, G., Senff, L., Ribeiro, F. R. C., Tarelho, L. A. D. C., Ferreira, V. M., et al. (2021). Recycling of ashes from forest biomass combustion as raw material for mortars. Mix Sustentável 7, 137–146. doi:10.29183/2447-3073.mix2021.v7.n2.137-146
Modolo, R. C. E., Ferreira, V. M., Tarelho, L. A., Labrincha, J. A., Senff, L., and Silva, L. (2013). Mortar formulations with bottom ash from biomass combustion. Constr. Build. Mat. 45, 275–281. doi:10.1016/j.conbuildmat.2013.03.093
Modolo, R. C. E., Senff, L., Labrincha, J. A., Ferreira, V. M., and Tarelho, L. A. C. (2014). Lime mud from cellulose industry as raw material in cement mortars. Mat. construcc. 64, e033. doi:10.3989/mc.2014.00214
Modolo, R. C. E., Silva, T., Senff, L., Tarelho, L. A. C., Labrincha, J. A., Ferreira, V. M., et al. (2015). Bottom ash from biomass combustion in BFB and its use in adhesive-mortars. Fuel Process. Technol. 129, 192–202. doi:10.1016/j.fuproc.2014.09.015
Monte, M. C., Fuente, E., Blanco, A., and Negro, C. (2009). Waste management from pulp and paper production in the European Union. Waste Manag. 29, 293–308. doi:10.1016/j.wasman.2008.02.002
Naqvi, M., Yan, J., and Dahlquist, E. (2010). Black liquor gasification integrated in pulp and paper mills: A critical review. Bioresour. Technol. 101, 8001–8015. doi:10.1016/j.biortech.2010.05.013
Novais, R. M., Ascensão, G., Buruberri, L. H., Senff, L., and Labrincha, J. A. (2016a). Influence of blowing agent on the fresh- and hardened-state properties of lightweight geopolymers. Mat. Des. 108, 551–559. doi:10.1016/j.matdes.2016.07.039
Novais, R. M., Ascensão, G., Ferreira, N., Seabra, M. P., and Labrincha, J. A. (2018a). Influence of water and aluminium powder content on the properties of waste-containing geopolymer foams. Ceram. Int. 44, 6242–6249. doi:10.1016/j.ceramint.2018.01.009
Novais, R. M., Ascensão, G., Tobaldi, D. M., Seabra, M. P., and Labrincha, J. A. (2018b). Biomass fly ash geopolymer monoliths for effective methylene blue removal from wastewaters. J. Clean. Prod. 171, 783–794. doi:10.1016/j.jclepro.2017.10.078
Novais, R. M., Buruberri, L. H., Ascensão, G., Seabra, M. P., and Labrincha, J. A. (2016b). Porous biomass fly ash-based geopolymers with tailored thermal conductivity. J. Clean. Prod. 119, 99–107. doi:10.1016/j.jclepro.2016.01.083
Novais, R. M., Buruberri, L. H., Seabra, M. P., Bajare, D., and Labrincha, J. A. (2016c). Novel porous fly ash-containing geopolymers for pH buffering applications. J. Clean. Prod. 124, 395–404. doi:10.1016/j.jclepro.2016.02.114
Novais, R. M., Buruberri, L. H., Seabra, M. P., and Labrincha, J. A. (2016d). Novel porous fly-ash containing geopolymer monoliths for lead adsorption from wastewaters. J. Hazard. Mat. 318, 631–640. doi:10.1016/j.jhazmat.2016.07.059
Novais, R. M., Caetano, A. P. F., Seabra, M. P., Labrincha, J. A., and Pullar, R. C. (2018c). Extremely fast and efficient methylene blue adsorption using eco-friendly cork and paper waste-based activated carbon adsorbents. J. Clean. Prod. 197, 1137–1147. doi:10.1016/j.jclepro.2018.06.278
Novais, R. M., Carvalheiras, J., Capela, M. N., Seabra, M. P., Pullar, R. C., and Labrincha, J. A. (2018d). Incorporation of glass fibre fabrics waste into geopolymer matrices: An eco-friendly solution for off-cuts coming from wind turbine blade production. Constr. Build. Mat. 187, 876–883. doi:10.1016/j.conbuildmat.2018.08.004
Novais, R. M., Carvalheiras, J., Seabra, M. P., Pullar, R. C., and Labrincha, J. A. (2017a). Effective mechanical reinforcement of inorganic polymers using glass fibre waste. J. Clean. Prod. 166, 343–349. doi:10.1016/j.jclepro.2017.07.242
Novais, R. M., Carvalheiras, J., Seabra, M. P., Pullar, R. C., and Labrincha, J. A. (2020a). Highly efficient lead extraction from aqueous solutions using inorganic polymer foams derived from biomass fly ash and metakaolin. J. Environ. Manage. 272, 111049. doi:10.1016/j.jenvman.2020.111049
Novais, R. M., Carvalheiras, J., Seabra, M. P., Pullar, R. C., and Labrincha, J. A. (2018e). Innovative application for bauxite residue: Red mud-based inorganic polymer spheres as pH regulators. J. Hazard. Mat. 358, 69–81. doi:10.1016/j.jhazmat.2018.06.047
Novais, R. M., Carvalheiras, J., Senff, L., and Labrincha, J. A. (2018f). Upcycling unexplored dregs and biomass fly ash from the paper and pulp industry in the production of eco-friendly geopolymer mortars: A preliminary assessment. Constr. Build. Mat. 184, 464–472. doi:10.1016/j.conbuildmat.2018.07.017
Novais, R. M., Carvalheiras, J., Senff, L., Lacasta, A. M., Cantalapiedra, I. R., Giro-Paloma, J., et al. (2020b). Multifunctional cork – alkali-activated fly ash composites: A sustainable material to enhance buildings’ energy and acoustic performance. Energy Build. 210, 109739. doi:10.1016/j.enbuild.2019.109739
Novais, R. M., Carvalheiras, J., Senff, L., Seabra, M. P., Pullar, R. C., and Labrincha, J. A. (2019a). In-depth investigation of the long-term strength and leaching behaviour of inorganic polymer mortars containing green liquor dregs. J. Clean. Prod. 220, 630–641. doi:10.1016/j.jclepro.2019.02.170
Novais, R. M., Carvalheiras, J., Tobaldi, D. M., Seabra, M. P., Pullar, R. C., and Labrincha, J. A. (2019b). Synthesis of porous biomass fly ash-based geopolymer spheres for efficient removal of methylene blue from wastewaters. J. Clean. Prod. 207, 350–362. doi:10.1016/j.jclepro.2018.09.265
Novais, R. M., Gameiro, T., Carvalheiras, J., Seabra, M. P., Tarelho, L. A. C., Labrincha, J. A., et al. (2018g). High pH buffer capacity biomass fly ash-based geopolymer spheres to boost methane yield in anaerobic digestion. J. Clean. Prod. 178, 258–267. doi:10.1016/j.jclepro.2018.01.033
Novais, R. M., Pullar, R. C., and Labrincha, J. A. (2020c). Geopolymer foams: An overview of recent advancements. Prog. Mat. Sci. 109, 100621. doi:10.1016/j.pmatsci.2019.100621
Novais, R. M., Senff, L., Carvalheiras, J., and Labrincha, J. A. (2020d). Bi-layered porous/cork-containing waste-based inorganic polymer composites: Innovative material towards green buildings. Appl. Sci. Switz. 10, 2995. doi:10.3390/app10092995
Novais, R. M., Seabra, M. P., and Labrincha, J. A. (2017b). Porous geopolymer spheres as novel pH buffering materials. J. Clean. Prod. 143, 1114–1122. doi:10.1016/j.jclepro.2016.12.008
Novais, R. M., Senff, L., Carvalheiras, J., Lacasta, A. M., Cantalapiedra, I. R., and Labrincha, J. A. (2021). Simple and effective route to tailor the thermal, acoustic and hygrothermal properties of cork-containing waste derived inorganic polymer composites. J. Build. Eng. 42, 102501. doi:10.1016/j.jobe.2021.102501
Novais, R. M., Senff, L., Carvalheiras, J., Seabra, M. P., Pullar, R. C., and Labrincha, J. A. (2019c). Sustainable and efficient cork - inorganic polymer composites: An innovative and eco-friendly approach to produce ultra-lightweight and low thermal conductivity materials. Cem. Concr. Compos. 97, 107–117. doi:10.1016/j.cemconcomp.2018.12.024
Organization for Standardization, I. (2008). ISO 24353, hygrothermal performance of building materials and products — determination of moisture adsorption/desorption properties in response to humidity variation. Geneva, Switzerland: ISO.
Rajamma, R., Ball, R. J., Tarelho, L. A. C., Allen, G. C., Labrincha, J. A., and Ferreira, V. M. (2009). Characterisation and use of biomass fly ash in cement-based materials. J. Hazard. Mat. 172, 1049–1060. doi:10.1016/j.jhazmat.2009.07.109
Rajamma, R., Senff, L., Ribeiro, M. J., Labrincha, J. A., Ball, R. J., Allen, G. C., et al. (2015). Biomass fly ash effect on fresh and hardened state properties of cement based materials. Compos. Part B Eng. 77, 1–9. doi:10.1016/j.compositesb.2015.03.019
Rode, C., Peuhkuri, R. H., Hansen, K. K., Time, B., Svennberg, K., Arfvidsson, J., et al. (2005a). NORDTEST project on moisture buffer value of materials. In AIVC 26th conference: Ventilation in relation to the energy performance of buildings. Air Infiltration and Ventilation, 47–52.
Rode, C., Peuhkuri, R., Mortensen, L. H., Hansen, K. K., Time, B., Gustavsen, A., et al. (2005b). Moisture buffering of building materials. Technical University of Denmark, Department of Civil Engineering. BYG Report No. R-127.
Rossi, A., Carvalheiras, J., Novais, R. M., Ribeiro, M. J., Labrincha, J. A., Hotza, D., et al. (2018). Waste-based geopolymeric mortars with very high moisture buffering capacity. Constr. Build. Mat. 191, 39–46. doi:10.1016/j.conbuildmat.2018.09.201
Rossi, A., Ribeiro, M. J., Labrincha, J. A., Novais, R. M., Hotza, D., and Moreira, R. F. P. M. (2019). Effect of the particle size range of construction and demolition waste on the fresh and hardened-state properties of fly ash-based geopolymer mortars with total replacement of sand. Process Saf. Environ. Prot. 129, 130–137. doi:10.1016/j.psep.2019.06.026
Saeli, M., Novais, R. M., Seabra, M. P., and Labrincha, J. A. (2018). Green geopolymeric concrete using grits for applications in construction. Mat. Lett. 233, 94–97. doi:10.1016/j.matlet.2018.08.102
Saeli, M., Senff, L., Tobaldi, D. M., Carvalheiras, J., Seabra, M. P., and Labrincha, J. A. (2020). Unexplored alternative use of calcareous sludge from the paper-pulp industry in green geopolymer construction materials. Constr. Build. Mat. 246, 118457. doi:10.1016/j.conbuildmat.2020.118457
Saeli, M., Senff, L., Tobaldi, D. M., La Scalia, G., Seabra, M. P., and Labrincha, J. A. (2019a). Innovative recycling of lime slaker grits from paper-pulp industry reused as aggregate in ambient cured biomass fly ash-based geopolymers for sustainable construction material. Sustain. Switz. 11, 3481–3515. doi:10.3390/su11123481
Saeli, M., Senff, L., Tobaldi, D. M., Seabra, M. P., and Labrincha, J. A. (2019b). Novel biomass fly ash-based geopolymeric mortars using lime slaker grits as aggregate for applications in construction: Influence of granulometry and binder/aggregate ratio. Constr. Build. Mat. 227, 116643. doi:10.1016/j.conbuildmat.2019.08.024
Saeli, M., Tobaldi, D. M., Seabra, M. P., and Labrincha, J. A. (2019c). Mix design and mechanical performance of geopolymeric binders and mortars using biomass fly ash and alkaline effluent from paper-pulp industry. J. Clean. Prod. 208, 1188–1197. doi:10.1016/j.jclepro.2018.10.213
Santos, R. B., Hart, P., Jameel, H., and Chang, H. (2013). Wood based lignin reactions important to the biorefinery and pulp and paper industries. Bioresources 8. 1456. doi:10.15376/biores.8.1.1456-1477
Senff, L., Novais, R. M., Carvalheiras, J., and Labrincha, J. A. (2020). Eco-friendly approach to enhance the mechanical performance of geopolymer foams: Using glass fibre waste coming from wind blade production. Constr. Build. Mat. 239, 117805. doi:10.1016/j.conbuildmat.2019.117805
Simão, L., Hotza, D., Raupp-Pereira, F., Labrincha, J. A., and Montedo, O. R. K. (2018). Wastes from pulp and paper mills - a review of generation and recycling alternatives. Cerâmica 64, 443–453. doi:10.1590/0366-69132018643712414
Simão, L., Jiusti, J., Lóh, N. J., Hotza, D., Raupp-Pereira, F., Labrincha, J. A., et al. (2017). Waste-containing clinkers: Valorization of alternative mineral sources from pulp and paper mills. Process Saf. Environ. Prot. 109, 106–116. doi:10.1016/j.psep.2017.03.038
Statista, 2020a. Statista, Avaiable at: https://www.statista.com/statistics/276629/global-co2-emissions/, Accessed date: May 2022.
Statista, 2020b. Statista, Avaiable at: https://www.statista.com/statistics/1299532/carbon-dioxide-emissions-worldwide-cement-manufacturing/, Accessed date: May 2022.
Takada, M., Chandra, R., Wu, J., and Saddler, J. N. (2020). The influence of lignin on the effectiveness of using a chemithermomechanical pulping based process to pretreat softwood chips and pellets prior to enzymatic hydrolysis. Bioresour. Technol. 302, 122895. doi:10.1016/j.biortech.2020.122895
Tran, H., and Vakkilainnen, E. K., 2008. The Kraft chemical recovery process, in: Proceedings of the Tappi Kraft Pulping Short Course. St. Petersburg, FL, USA, 7–10 January, 2008, pp. 1.1:1–1.1:8.
Vass, T., Levi, P., Gouy, A., and Mandová, H., 2021. International energy agency, Avaiable at: https://www.iea.org/reports/cement, Accessed date: May 2022.
Veluchamy, C., and Kalamdhad, A. S. (2017). Influence of pretreatment techniques on anaerobic digestion of pulp and paper mill sludge: A review. Bioresour. Technol. 245, 1206–1219. doi:10.1016/j.biortech.2017.08.179
Verma, O. P., Manik, G., and Sethi, S. K. (2019). A comprehensive review of renewable energy source on energy optimization of black liquor in MSE using steady and dynamic state modeling, simulation and control. Renew. Sustain. Energy Rev. 100, 90–109. doi:10.1016/j.rser.2018.10.002
Keywords: waste upcycling, clinker, portland cement, geopolymer, adsorbent, PH regulator
Citation: Vilarinho IS, Gameiro T, Capela MN, Carvalheiras J, Caetano APF, Novo C, Novais RM, Seabra MP and Labrincha JA (2022) Review of recycling alternatives for paper pulp wastes. Front. Mater. 9:1006861. doi: 10.3389/fmats.2022.1006861
Received: 29 July 2022; Accepted: 06 October 2022;
Published: 18 October 2022.
Edited by:
Verónica de Zea Bermudez, University of Trás-os-Montes and Alto Douro, PortugalReviewed by:
Ping Duan, China University of Geosciences Wuhan, ChinaArkamitra Kar, Birla Institute of Technology and Science, India
Copyright © 2022 Vilarinho, Gameiro, Capela, Carvalheiras, Caetano, Novo, Novais, Seabra and Labrincha. This is an open-access article distributed under the terms of the Creative Commons Attribution License (CC BY). The use, distribution or reproduction in other forums is permitted, provided the original author(s) and the copyright owner(s) are credited and that the original publication in this journal is cited, in accordance with accepted academic practice. No use, distribution or reproduction is permitted which does not comply with these terms.
*Correspondence: Inês Silveirinha Vilarinho, inessvilarinho@ua.pt; João António Labrincha, jal@ua.pt