- 1School of Materials Science and Chemical Engineering, Ningbo University, Ningbo, China
- 2Key Laboratory of Marine Materials and Related Technologies, Zhejiang Key Laboratory of Marine Materials and Protective Technologies, Ningbo Institute of Materials Technology and Engineering, Chinese Academy of Sciences, Ningbo, China
- 3Center of Materials Science and Optoelectronics Engineering, University of Chinese Academy of Sciences, Beijing, China
- 4College of Ocean Science and Engineering, Shanghai Maritime University, Shanghai, China
- 5Advanced Nano-processing Engineering Lab, Mechanical Engineering, Kogakuin University, Tokyo, Japan
A highly thermally conductive heat spreader for applications in electronic devices is becoming increasingly demanding, and therefore the removal of excess heat requires an efficient heat dissipating device. Boron nitride nanosheets (BNNSs) were prepared as thermally conductive fillers using hexagonal boron nitride (h-BN) powder as raw material by a water exfoliation method. A composite film was prepared by vacuum filtration using cellulose nanofibers (CNFs) as the substrate with an in-plane thermal conductivity (TC) of 82.4 W m−1 K−1, thermal conductivity enhancement increasing by 9,486% compared to pure cellulose film. Thus, CNF/BNNS composite films are promising as effective thermal interface materials (TIMs) in electronic devices and electronic component applications.
Introduction
In recent years, with the continuous improvement of technology, high-power electronic devices and highly integrated electronic components are also developed towards more precision and miniaturization. However, a lot of problems, such as waste heat, have also arisen. When the heat generated by a device is not effectively removed during prolonged periods of high workload, the device’s efficiency, service life, and reliability suffer significantly. The air gap between the heat sink and the heat-generating device has a very low thermal conductivity, resulting in a relatively high contact thermal resistance. Thermal interface materials can bridge this air gap, lowering contact thermal resistance and improving thermal transportation performance. The development of heat spreader with efficient heat dissipation properties to remove excess heat has therefore become a hot topic of research (Cui et al., 2020; Yan et al., 2021a). Efficient heat dissipation will be a critical factor in developing devices and electronic components.
Anisotropic insulating 2D materials have a high thermal conductivity along the planar aspect compared to isotropic conductive materials, effectively blocking the influence between components (Yang et al., 2021b). The two-dimensional (2D) BNNS has been widely used as thermal conductivity due to its high thermal conductivity (Yan et al., 2021b), excellent electrical insulation, and low dielectric constant (Wang et al., 2018; Hou et al., 2021). The thermal conductivity of BNNS has been reported to be in the range of 1700–2000 W m−1 K−1 (Zeng et al., 2011; Zeng et al., 2012). However, the high brittleness and low tensile strength of pure BNNS (∼17 MPa) (Wu et al., 2017) limit its application. For the electronic miniaturization components, a thermal interface material with better mechanical properties and thermal conductivity is needed. Filling BNNS with polymers that serve as adhesive can build up a thermally conductive network, which is a reliable way to reduce the brittleness and increase the tensile strength of the composite.
Cellulose nanofibres (CNF) are low-cost, all-natural, inexhaustible polymeric materials prepared from the cellulose of plant origin. Due to its excellent mechanical and thermal properties (Zhou et al., 2016), cellulose is increasingly being used as a substrate for thin film research (Wu et al., 2017; Wu et al., 2018). It has previously been reported that two-dimensional BNNS can be dispersed in aqueous suspension by electrostatic repulsion and spatial site resistance (Zhu et al., 2014; Li et al., 2015).
In this paper, we demonstrate a simple water exfoliation method to obtain BNNS (Wang et al., 2018) and introduce BNNS into a cellulose substrate to prepare a composite film by vacuum filtration. Firstly, we prepared CNF/BNNS composite films by controlling the suspension concentration at 0.15% and increasing the BNNS filler content. We found that the thermal conductivity of the CNF/BNNS composite films increased with increasing BNNS filler content. When the BNNS filler concentration was 90%, the CNF/BNNS composite films had the highest thermal conductivity of 70.4 W m−1 K−1. Secondly, to further improve the thermal conductivity of the CNF/BNNS composite films, we consider making the BNNS in the CNF/BNNS composite films have a more regular horizontal arrangement to form a better heat conduction path. We decided to control the same BNNS filler content at 90% and change the different suspension concentration for comparison. It was found that the suspension concentration had a significant effect on the CNF/BNNS composite films, with a significantly higher thermal conductivity of 82.4 W m−1 K−1 at a suspension concentration of 0.1%. We have investigated the in-plane thermal conductivity of the CNF/BNNS composite films in these two ways, particularly the effect of varying the suspension concentration with a 90% BNNS filler content. The composite films show good thermal conductivity and can be used as a heat spreader for electronic devices (Yang et al., 2021a; Zhang et al., 2021).
Experimental
Materials
Hexagonal boron nitride (lateral size 1–5 μm) powder from ESK Ceramics (Germany). Cellulose raw material obtained from Guilin Qihong Technology Co. (Product model CNF-P, Content of 1.1 wt%, The raw material is wood pulp, diameter of 4–10 nm, length of 1–3 μm, suspension PH value of 7–8).
Preparation of BNNS
The h-BN powder (80 g) and 4,000 ml of deionized water were dispersed. This dispersion was subjected to the first step of the stripping process with a cutting-edge ultrasound machine, which ultrasonicated the h-BN micronized powder for 120 min. After sonication, stand for 5 h and separate into layers, then pour out the upper dispersion and dry to obtain BNNS. And it should be noted at this point that the 80 g of h-BN powder was not completely exfoliated. The solvent of the sediment below could be reused as the original solvent in another liquid stripping process. It means that the residue can be re-dispersed in 4,000 ml of deionized water, sonicated, filtered. The above procedure is repeated after several cycles to achieve complete exfoliation.
Preparation of Composite Films
Herein, the vacuum filtration method was used to prepare CNF/BNNS composite films. We used CNF/BNNS composite films with a suspension concentration of 0.1 wt% and 90 wt% BNNS content as an example. In the first step, 0.09 g BNNS and 1.0 g cellulose slurry were dispersed in 99 ml of deionized water in a mixing cylinder with a speed mixer (Shanghai Acclaim International Trading Co. Model: DAC 150.1 FVZ-K) at 3,500 rpm, where the deionized water was added twice. The purpose of this is to prevent BNNS from sticking to the wall of the mixing cylinder and causing uneven dispersion of BNNS. In the second step, the prepared dispersion was further dispersed in the sonicator for another 30 min to obtain the final suspension by adding 33 ml and vacuum filtering through a polycarbonate membrane with a pore size of 0.22 μm to obtain a CNF/BNNS composite film with a thickness of about 30 μm. The preparation procedure of CNF/BNNS composite film was shown in Figure 1.
Characterization
Both BNNS and composite films were observed with a Regulus 8230 scanning electron microscope (HITACHI, Regulus 8230, Japan). In order to prevent charge accumulation on the cross section of the composite film, we pre-sprayed a layer of platinum on the surface of the composite film. Transmission electron microscope (Thermo Fisher Scientific, Talos, MA, United States). Atomic force microscope (AFM, SPM Dimension 3100, Veeco, NY, United States). Raman spectroscopy using a laser confocal micro Raman spectrometer (HORIBA FRANCE SAS, LabRAM Odyssey, Japan) with a laser wavelength of 532 nm. The crystalline structure and surface chemical compositions were determined using X-ray diffractometer (XRD, D8 Discover/GADDS, Bruker, Germany) with Cu Kαradiation. Infrared spectroscopy was performed using a FTIR spectrometer (Thermo, Nicolet is 50, MA, United States). The thermal conductivity of the composite film was determined using the LFA 467 Nanoflash (NETZSCH, Germany). Infrared photos were taken by an infrared camera (Fluke, Ti400, WA, United States).
Results and Discussion
Characterizations of BNNS
As shown in Figure 2A the size distribution of BNNS is from 1 to 5 μm with a flat and regular surface, proving the BNNS was successfully exfoliated from h-BN. A clear lattice can be seen in the HRTEM image in Figure 2B, indicating that the exfoliated BNNS still maintains an ordered structure. The top right inset of Figure 2B shows a magnified view of the crystal lattice, which presents the crystal lattice spacing of 0.22 nm. The thickness of BNNS was measured by an atomic force microscope (AFM). The scanned profile is shown in Figure 2C with a thickness of 3.1 nm for BNNS (Li et al., 2016; Zhu et al., 2016). The crystal structure and surface functional groups of BNNS have been studied to provide more information on the exfoliation of BNNS. The characteristics of BNNS by Raman spectral frequencies in the G-band of the original h-BN and the stripped BNNS are shown in Figure 2D. Compared to the original h-BN (1,364 cm−1), the BNNS (1,366 cm−1) is blue shifted and has an increased G-band frequency. As the number of boron nitride layers decreases, the in-plane strain in the boron nitride layer increases, and the inter-layer interaction weakens, resulting in an increase in the G-band frequency. A good correspondence between h-BN and BNNS can be seen in the XRD diffraction peaks of Figure 2E, which are related to the (002), (100), (101), (102), and (004) surfaces, respectively, and it can be seen that h-BN is well exfoliated into BNNS. The FTIR spectra of h-BN and BNNS in Figure 2F show a small peak at 816 cm−1 belonging to the B-N stretching vibration (E1umode) and a broad peak at 1,373 cm−1 belonging to the B-N-B out-of-plane bending deformation (A2umode) (Shi et al., 2010; Lee et al., 2015). A peak at 3,440 cm−1 is due to -OH vibration(Pan et al., 2021).
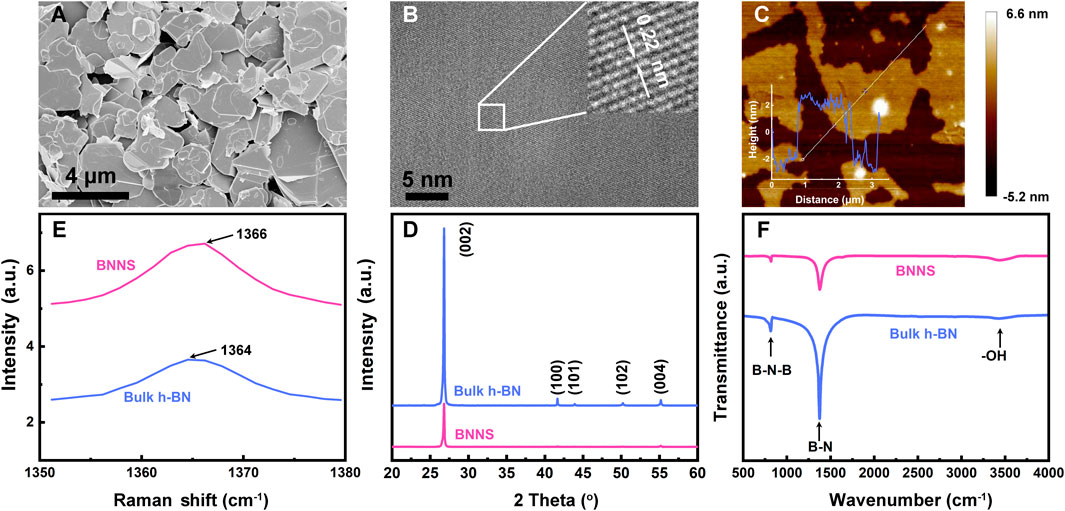
FIGURE 2. Characterization of BNNS and BN powders: (A) SEM, (B) TEM, (C) AFM, (D) Raman, (E) XRD, and (F) FTIR spectra.
Microstructure of CNF/BNNS Composite Films
The dispersion of the BNNS filler in the CNF matrix is an important influence on the properties of the composite (Wu et al., 2017; Wu et al., 2018). The morphologies of the fractured surface of the composite films were investigated by scanning electron microscopy (SEM). Figures 3A,A', exhibit a CNF/BNNS composite film with a 10 wt% BNNS filler. Only a small amount of BNNS can be seen on the surface. With the increase of BNNS, more ordered BNNS appears on the fracture surface of the film, which provides more information for the improvement of the thermal conductivity of the composite film, as shown in Figures 3B–D. Figures 3B'-D' shows more details of Figures 3B–D. Firstly, we increased the BNNS filling amount by controlling the suspension concentration. Then change the suspension concentration under the same BNNS filling content, as shown in (Figures 4A,D') Figures 4A,A',B,B',C,C'D,D') are suspension concentrations of 0.1 wt%, 0.15 wt%, 0.3 wt% and 0.5 wt% respectively. Figures 4A'–D' shows that as the suspension concentrations increase, the in-plane orientation of BNNS deteriorates, which is a key factor affecting the in-plane thermal conductivity of the CNF/BNNS composite film.
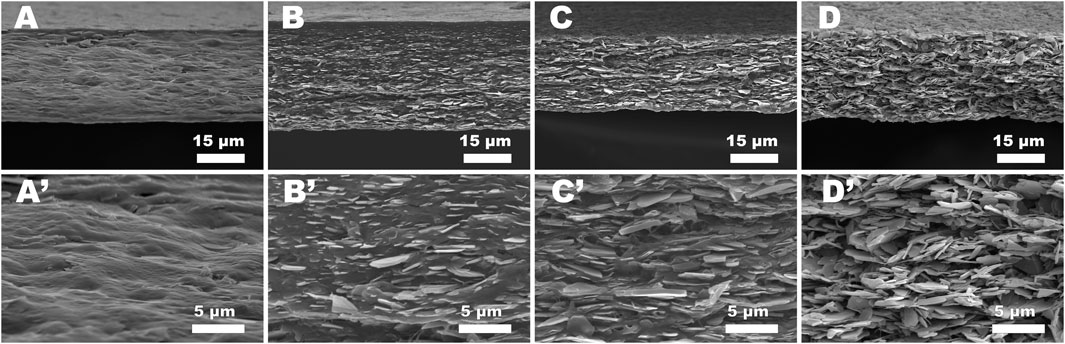
FIGURE 3. Where (A'–D') is the (A–D) high magnification SEM image, which shows more clearly the BNNS arrangement in the composite films.
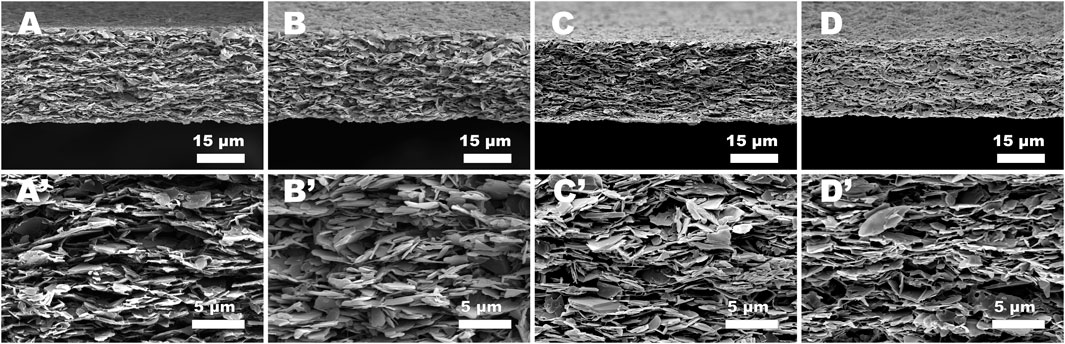
FIGURE 4. Where (A'–D') is the (A–D) high magnification SEM image, which shows more clearly the BNNS arrangement in the composite films with different suspension concentrations.
Thermal Transportation Properties of CNF/BNNS Composite Films
We measured the thermal diffusion of the sample by laser flash at room temperature and pressure and then derived the thermal conductivity by the equation:
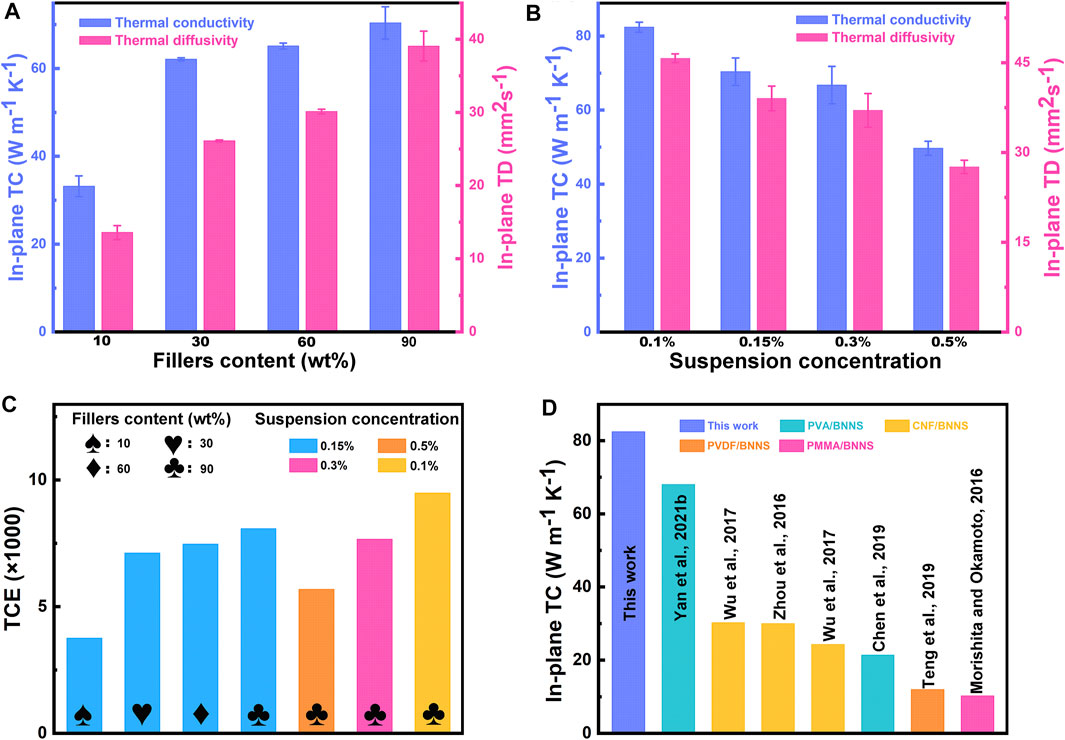
FIGURE 5. Thermal properties of CNF/BNNS composite films: (A) Thermal conductivity (TC) and thermal diffusivity (TD) of CNF/BNNS composite films at different BNNS filler contents at a suspension concentration of 0.15 wt%, (B) Thermal conductivity and thermal diffusivity of CNF/BNNS composite films with 90 wt% BNNS filler content at different suspension concentrations, (C) Thermal conductivity enhancement (TCE), and (D) Comparison between our samples and BNNS/polymer composite films reported in the literature.
Figure 6A shsows a pure cellulose film on the left and a CNF/BNNS composite film with 90 wt% BNNS filler content at a suspension concentration of 0.1 wt% on the right. Figure 6B displayed a model of the system configuration when we took the IR images. Our sample, the ceramic heater, and the copper stage are from top to bottom. Figure 6C has been displayed IR images of CNF/BNNS composite films in I and pure cellulose films in II. The heating process is from 10 to 70s, and the cooling process is from 70 to 110 s. Figures 6D,E display the heating and cooling curve, respectively. The values of the heating and cooling curves come from the white marked points at the 10 s position in I and II, as shown in Figure 6C. It represents the process of a temperature change as the temperature spreads from the central point to the marked white point. It can be seen that the heating rate of our sample is much higher than that of pure cellulose film.
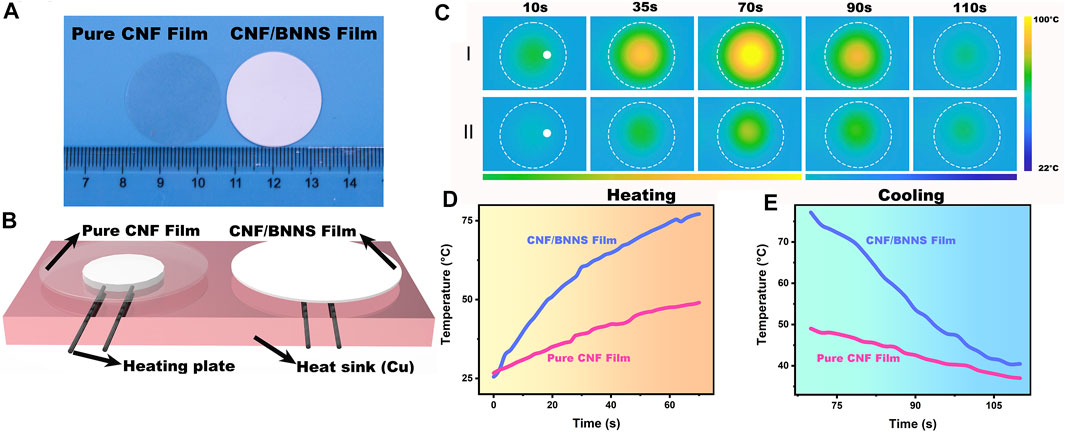
FIGURE 6. (A) Photographs of pure CNF film and 90 wt% BNNS content composite film, (B) Test model for IR images, (C) IR images of CNF/BNNS composite film with 90 wt% BNNS content at a suspension concentration of 0.1 wt% and pure CNF films heated and cooled with a ceramic heating plate heat source, (D) The heating curve and (E) the cooling curve as functions of time.
Conclusion
In summary, two-dimensional hexagonal boron nitride nanosheets as lateral heat spreaders were fabricated by a simple infiltrating method. Ultrahigh in-plane thermal conductivity of 82.4 W m−1 K−1 was obtained at 90 wt% BNNS filler content, which corresponds to a thermal conductivity enhancement increasing by 9,486% compared to pure CNF film. The high thermal conductivity of the composite film can be used as a heat spreader for electronic components and devices.
Data Availability Statement
The raw data supporting the conclusion of this article will be made available by the authors, without undue reservation.
Author Contributions
XK: Conceptualization, Methodology, Data Curation, Writing Original Draft. LL: Visualization, Investigation. ML: Investigation. JX: Investigation. YW: Resources. XW: Visualization. SX: Investigation. PG: Resources. ZP: Investigation, Resources XW: Resources. TC: Investigation. KN: Resources. TC: Validation. CL: Validation. NJ: Conceptualization, Supervision. JY: Conceptualization, Supervision, Writing—Review and Editing.
Conflict of Interest
The authors declare that the research was conducted in the absence of any commercial or financial relationships that could be construed as a potential conflict of interest.
Publisher’s Note
All claims expressed in this article are solely those of the authors and do not necessarily represent those of their affiliated organizations, or those of the publisher, the editors and the reviewers. Any product that may be evaluated in this article, or claim that may be made by its manufacturer, is not guaranteed or endorsed by the publisher.
References
Chen, J., Wei, H., Bao, H., Jiang, P., and Huang, X. (2019). Millefeuille-Inspired Thermally Conductive Polymer Nanocomposites with Overlapping BN Nanosheets for Thermal Management Applications. ACS Appl. Mater. Inter. 11 (34), 31402–31410. doi:10.1021/acsami.9b10810
Cui, Y., Li, M., and Hu, Y. (2020). Emerging Interface Materials for Electronics thermal Management: Experiments, Modeling, and New Opportunities. J. Mater. Chem. C 8 (31), 10568–10586. doi:10.1039/c9tc05415d
Hou, X., Zhang, Z., Wei, X., Qin, Y., Song, G., Li, L., et al. (2021). Aluminum Borate/Boron Nitride Nanosheet Fibers for Enhancing the Thermal Conductivity of Polymer Composites. ACS Appl. Nano Mater. 4 (2), 2136–2142. doi:10.1021/acsanm.0c03429
Lee, D., Lee, B., Park, K. H., Ryu, H. J., Jeon, S., and Hong, S. H. (2015). Scalable Exfoliation Process for Highly Soluble boron Nitride Nanoplatelets by Hydroxide-Assisted ball Milling. Nano Lett. 15 (2), 1238–1244. doi:10.1021/nl504397h
Li, T., Wang, L., Zhang, K., Xu, Y., Long, X., Gao, S., et al. (2016). Freestanding Boron Nitride Nanosheet Films for Ultrafast Oil/Water Separation. Small 12 (36), 4960–4965. doi:10.1002/smll.201601298
Li, Y., Zhu, H., Shen, F., Wan, J., Lacey, S., Fang, Z., et al. (2015). Nanocellulose as green Dispersant for Two-Dimensional Energy Materials. Nano Energy 13, 346–354. doi:10.1016/j.nanoen.2015.02.015
Morishita, T., and Okamoto, H. (2016). Facile Exfoliation and Noncovalent Superacid Functionalization of Boron Nitride Nanosheets and Their Use for Highly Thermally Conductive and Electrically Insulating Polymer Nanocomposites. ACS Appl. Mater. Inter. 8 (40), 27064–27073. doi:10.1021/acsami.6b08404
Pan, D., Li, Q., Zhang, W., Dong, J., Su, F., Murugadoss, V., et al. (2021). Highly thermal Conductive Epoxy Nanocomposites Filled with 3D BN/C Spatial Network Prepared by Salt Template Assisted Method. Composites B: Eng. 209, 108609. doi:10.1016/j.compositesb.2021.108609
Shi, Y., Hamsen, C., Jia, X., Kim, K. K., Reina, A., Hofmann, M., et al. (2010). Synthesis of Few-Layer Hexagonal boron Nitride Thin Film by Chemical Vapor Deposition. Nano Lett. 10 (10), 4134–4139. doi:10.1021/nl1023707
Teng, C., Su, L., Chen, J., and Wang, J. (2019). Flexible, Thermally Conductive Layered Composite Films from Massively Exfoliated boron Nitride Nanosheets. Composites A: Appl. Sci. Manufacturing 124, 105498. doi:10.1016/j.compositesa.2019.105498
Wang, M., Jiao, Z., Chen, Y., Hou, X., Fu, L., Wu, Y., et al. (2018). Enhanced thermal Conductivity of Poly(vinylidene Fluoride)/boron Nitride Nanosheet Composites at Low Filler Content. Composites Part A: Appl. Sci. Manufacturing 109, 321–329. doi:10.1016/j.compositesa.2018.03.023
Wu, K., Fang, J., Ma, J., Huang, R., Chai, S., Chen, F., et al. (2017). Achieving a Collapsible, Strong, and Highly Thermally Conductive Film Based on Oriented Functionalized Boron Nitride Nanosheets and Cellulose Nanofiber. ACS Appl. Mater. Inter. 9 (35), 30035–30045. doi:10.1021/acsami.7b08214
Wu, K., Liao, P., Du, R., Zhang, Q., Chen, F., and Fu, Q. (2018). Preparation of a Thermally Conductive Biodegradable Cellulose Nanofiber/hydroxylated boron Nitride Nanosheet Film: the Critical Role of Edge-Hydroxylation. J. Mater. Chem. A. 6 (25), 11863–11873. doi:10.1039/c8ta03642j
Yan, Q., Alam, F. E., Gao, J., Dai, W., Tan, X., Lv, L., et al. (2021a). Soft and Self‐Adhesive Thermal Interface Materials Based on Vertically Aligned, Covalently Bonded Graphene Nanowalls for Efficient Microelectronic Cooling. Adv. Funct. Mater. 31 (36), 2104062. doi:10.1002/adfm.202104062
Yan, Q., Dai, W., Gao, J., Tan, X., Lv, L., Ying, J., et al. (2021b). Ultrahigh-Aspect-Ratio Boron Nitride Nanosheets Leading to Superhigh In-Plane Thermal Conductivity of Foldable Heat Spreader. ACS Nano 15 (4), 6489–6498. doi:10.1021/acsnano.0c09229
Yang, G., Zhang, X., Pan, D., Zhang, W., Shang, Y., Su, F., et al. (2021a). Highly Thermal Conductive Poly(vinyl Alcohol) Composites with Oriented Hybrid Networks: Silver Nanowire Bridged Boron Nitride Nanoplatelets. ACS Appl. Mater. Inter. 13 (27), 32286–32294. doi:10.1021/acsami.1c08408
Yang, G., Zhang, X., Shang, Y., Xu, P., Pan, D., Su, F., et al. (2021b). Highly Thermally Conductive Polyvinyl Alcohol/boron Nitride Nanocomposites with Interconnection Oriented boron Nitride Nanoplatelets. Composites Sci. Tech. 201, 108521. doi:10.1016/j.compscitech.2020.108521
Zeng, Z., Sun, T., Zhu, J., Huang, X., Yin, Z., Lu, G., et al. (2012). An Effective Method for the Fabrication of Few-Layer-Thick Inorganic Nanosheets. Angew. Chem. Int. Ed. 51 (36), 9052–9056. doi:10.1002/anie.201204208
Zeng, Z., Yin, Z., Huang, X., Li, H., He, Q., Lu, G., et al. (2011). Single-layer Semiconducting Nanosheets: High-Yield Preparation and Device Fabrication. Angew. Chem. Int. Ed. 50 (47), 11093–11097. doi:10.1002/anie.201106004
Zhang, X., Dong, J., Pan, D., Yang, G., Su, F., Ji, Y., et al. (2021). Constructing Dual thermal Conductive Networks in Electrospun Polyimide Membranes with Highly Thermally Conductivity but Electrical Insulation Properties. Adv. Compos. Hybrid Mater. 4 (4), 1102–1112. doi:10.1007/s42114-021-00335-9
Zhou, L., Yang, Z., Luo, W., Han, X., Jang, S.-H., Dai, J., et al. (2016). Thermally Conductive, Electrical Insulating, Optically Transparent Bi-layer Nanopaper. ACS Appl. Mater. Inter. 8 (42), 28838–28843. doi:10.1021/acsami.6b09471
Zhu, H., Li, Y., Fang, Z., Xu, J., Cao, F., Wan, J., et al. (2014). Highly Thermally Conductive Papers with Percolative Layered Boron Nitride Nanosheets. ACS Nano 8, 3606–3613. doi:10.1021/nn500134m
Keywords: boron nitride nanosheets, cellulose nanofibers, heat spreader, filtration, thermal conduction
Citation: Kong X, Li L, Li M, Xia J, Wang Y, Wei X, Xiong S, Gong P, Pan Z, Wu X, Cai T, Nishimura K, Lin C-T, Jiang N and Yu J (2022) Two-Dimensional Hexagonal Boron Nitride Nanosheets as Lateral Heat Spreader With High Thermal Conductivity. Front. Mater. 8:817061. doi: 10.3389/fmats.2021.817061
Received: 17 November 2021; Accepted: 31 December 2021;
Published: 21 January 2022.
Edited by:
Xiaoliang Zeng, Shenzhen Institutes of Advanced Technology (CAS), ChinaReviewed by:
Xuebin Wang, Nanjing University, ChinaPeng Ding, Shanghai University, China
Kang Zheng, Institute of Solid State Physics, Hefei Institutes of Physical Science (CAS), China
Chuntai Liu, Zhengzhou University, China
Copyright © 2022 Kong, Li, Li, Xia, Wang, Wei, Xiong, Gong, Pan, Wu, Cai, Nishimura, Lin, Jiang and Yu. This is an open-access article distributed under the terms of the Creative Commons Attribution License (CC BY). The use, distribution or reproduction in other forums is permitted, provided the original author(s) and the copyright owner(s) are credited and that the original publication in this journal is cited, in accordance with accepted academic practice. No use, distribution or reproduction is permitted which does not comply with these terms.
*Correspondence: Zhongbin Pan, cGFuemhvbmdiaW5AMTYzLmNvbQ==; Xinfeng Wu, eGZ3dUBzaG10dS5lZHUuY24=; Jinhong Yu, eXVqaW5ob25nQG5pbXRlLmFjLmNu
†These authors have contributed equally to this work