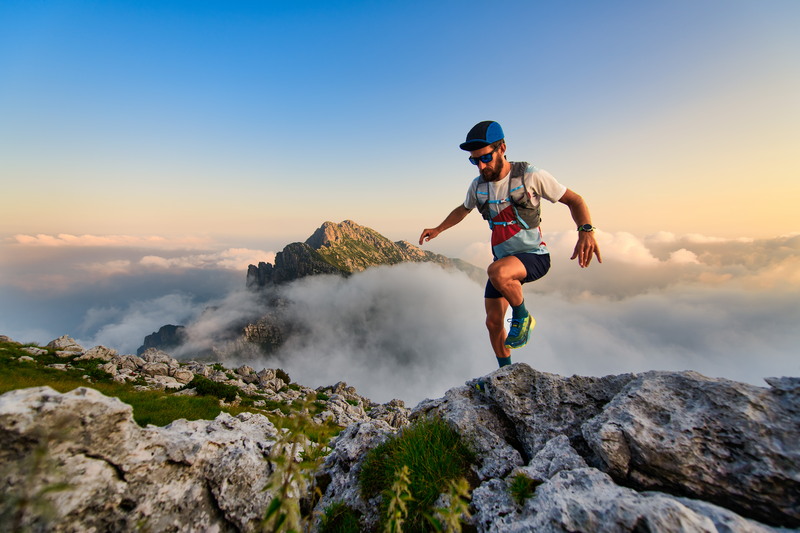
95% of researchers rate our articles as excellent or good
Learn more about the work of our research integrity team to safeguard the quality of each article we publish.
Find out more
ORIGINAL RESEARCH article
Front. Mater. , 12 January 2022
Sec. Structural Materials
Volume 8 - 2021 | https://doi.org/10.3389/fmats.2021.810535
This article is part of the Research Topic Non-BF Slag-based Green Cementitious Materials View all 20 articles
In this study, we investigated the impact of aluminium ion (Al3+) incorporation on the microstructure and the phase transformation of the magnesium silicate hydrate system. The magnesium silicate hydrate system with aluminium was prepared by mixing magnesium oxide and silica fume with different aluminium ion contents (the Al/Si molar ratios of 0.01, 0.02, 0.05, 0.1, 0.2) at room temperature. The high degree of polymerization of the magnesium silicate hydrate phases resulted in the limited incorporation of aluminium in the structure of magnesium silicate hydrate. The silicon-oxygen tetrahedra sites of magnesium silicate hydrate layers, however, were unable to substitute for silicon sites through inverted silicon-oxygen linkages. The increase in aluminium ion content raised the degree of polymerization of the magnesium silicate hydrate phases from 0.84 to 0.92. A solid solution was formed from residual aluminum-amorphous phases such as hydroxyl-aluminum and magnesium silicate hydrate phases. X-ray diffraction (XRD), field emission scanning electron microscope (F-SEM), and 29Si and 27Al MAS NMR data showed that the addition of Al3+ promotes the hydration process of MgO and has an obvious effect on the appearance of M-S-H gel. The gel with low aluminum content is fluffy, while the gel with high aluminum content has irregular flakes. The amount of Al3+ that enters the M-S-H gel increased with the increase of Al3+ content, but there was a threshold: the highest Al/Si molar ratio of M-S-H gel can be maintained at about 0.006.
As we all know, the hydration product of CaO-SiO2-H2O system is calcium silicate hydrate (C-S-H) gel, like C-S-H, at normal temperatures and pressures, and the main hydration product of MgO-SiO2-H2O system is magnesium silicate hydrate (M-S-H)gel(Li et al., 2014; Jia et al., 2017a). The molecular structures of magnesium silicate hydrate (M-S-H) and calcium silicate hydrate (C-S-H) phases are significantly different. The former is an amorphous precursor of talc or sepiolite with layered silica structure (Lothenbach et al., 2015; Bernard et al., 2019), while the latter is a silica-deficient solid solution and is a precursor of two crystalline phases, tobernorite and jennite (Maruyama et al., 2014; Li et al., 2020a). Various studies show that the system has many excellent properties, such as excellent adsorptive properties, especially for heavy metal ions like Cu, Ni (Jia et al., 2016). The M-S-H has a similar structure with sepiolite: it has a large specific surface area and there are unique nano-scale pores in molecular structure, and it has the ability to adsorb heavy metals (Ji et al., 2014; Jia et al., 2017b; Jia et al., 2019; Liu et al., 2021). Magnesium silicate hydrate (M-S-H) phases can be considered as a potential cementitious material for nuclear waste immobilization (Walling et al., 2015) owing to its moderate pH value (varying from ∼9.5 to ∼10.5) and the Radionuclide (Cs, Sr) sorption potential (Li et al., 2014; Zhang et al., 2020).
The interface region between cement-based material and clay can be observed in the generation of M-S-H, the main components of clay are SiO2 and Al2O3 (Bonen and Cohen, 1992; Santhanam et al., 2020). This study aims to understand the influence of Al3+ content on the phase transformation and the structural change of M-S-H. However, the impact of Al3+ on the reaction processes during the hydration of M-S-H is poorly investigated. On the contrary, in the presence of Al3+, the molecular structure of C-S-H will change (Song et al., 2021). According to Richardson et al.(Richardson, 1999) the incorporation of aluminium ions (Al3+) could change the molecular structure of the C-S-H phase. For example, tetrahedrally coordinated Al3+ [Al (Bernard et al., 2019), Al for tetra-coordination] can substitute for silicon sites in the structure of tobermorite, occupying the bridging tetrahedra sites of C-S-H chains (Bernard et al., 2020; Li et al., 2020b). Magnesium silicate hydrate is formed by reacting MgO with silica fume (SF) and MgO dissolved in water, with one part disassociating with Mg2+ and the other part hydrated with water to form Mg(OH)2, and at the same time the SiO2 dissociates in water to form H2SiO42−, and finally the Mg(OH)2, SiO2, and H2SiO42− react to form M-S-H (Li et al., 2014; Tang and Chen, 2020). The MgO dissolves slowly in water and forms a poorly soluble weak electrolyte, and the Mg(OH)2 is incomplete, which leads to a decrease in the hydration rate of M-S-H (Bernard et al., 2017). The hydration rate of M-S-H can be increased by adding Al3+ and thereby can increase the early strength of M-S-H (Li et al., 2019). The M-S-H hydration product was prepared by mixing the reactive MgO, silica fume (SF) and Al(NO3)3, and the synthesized solids were characterized after 300 days. Advanced testing methods were used to characterize the M-S-H phases prepared under different Al3+ contents.
Light burned technical grade MgO (Martin Marietta Magnesia Specialties, United States) and SF (Elkem, China) were used to synthesize M-S-H phase. Aluminium nitrate (Al(NO3)3, (Chempur, China) was used as the aluminium salt. The chemical composition data of the raw materials as reported by the manufacturers are presented in Table 1. The median particle sizes of the MgO and silica fume were 3.5 and 0.5 μm respectively.
The aluminium magnesium silicate hydrate (AMSH) specimens were prepared by mixing the aqueous solutions of MgO, SF, and Al(NO3)3 at Mg/Si molar ratio of 1:1 and Al/Si molar ratios of 0.01, 0.02, 0.05, 0.1, and 0.2 were presented in Table 2. Complete hydration was obtained by adopting a water/solids (W/S) ratio of 10, where S was the total mass of MgO and SF.
In order to speed up the reaction process and make sure the samples were homogenized, the prepared samples were placed in a horizontal oscillator to oscillate for 7 days, and then the solutions were stored at room temperature (25 ± 1 C) in 250 ml sealed polyethylene bottles for up to 300 days. After 300 days the granular residue was separated by filtration and the collected solids were soaked in absolute ethyl alcohol for 24 h to inhibit further hydration, and then dried at 40°C for 48 h. The specimens were characterized using multiple techniques, such as X-ray diffraction analysis (XRD D/Max 2400 V diffractometer with Cu Kα radiation at a scan rate of 0.5 2θ min−1), thermo-gravimetric and derivative thermo-gravimetric analysis (TGA/DTG, alumina crucibles were used and sample were heated in a nitrogen atmosphere between 50°C and 1,000°C at 10°C/min), and field emission scanning electron microscopy (F-SEM: NOVA Nano-SEM 450) on gold coated samples that had been sputter coated for 2 min using 15 mA and 30 Pa pressure and 29Si/27Al nuclear magnetic resonance spectroscopy (NMR).
Figure 1 shows the phases transformation in the MgO-SiO2-H2O system with different Al3+ content curing for 1 day and 300 days. Curing for 1 day it is obvious that with the increase of the dosage of Al (NO3)3, the content of residual MgO in the system decreases greatly, while the content of Mg (OH)2 increases gradually, which indicates that the addition of Al3+ promotes the hydration of MgO and the formation of Mg (OH)2 (Figure 1A). At the same time, a dispersion peak appears around 2θ about ∼10.6o and it is gradually obvious with the increase of Al3+ content, it indicates that there was the formation of a new phase and amorphous type of micro-crystalline hydroxy aluminium. By the later stage of hydration (300 days), the crystalline phases were completely transformed to the amorphous phases due to the reaction of MgO and Mg (OH)2 with silica fume (SF) (Figure 1B). The cementitious system is all amorphous phase; and the characteristic peak of M-S-H gel at the broad diffraction at 22–30° becomes weaker with the increase of the dosage of Al3+, which may be the result of the change of molecular structure. The broad diffraction at 20–28°, 33–40° and 58–62° ranges are attributable to the M-S-H phases (Zhang et al., 2014; Jia et al., 2016) (Figure 1B) while the diffraction peak between 8° and 12° represents the Al-amorphous phases (Figures 1A,B).
FIGURE 1. The XRD patterns of magnesium silicate hydrate (M-S-H) samples with different Al3+ contents after curing for (A) 1 day and (B) 300 days.
Three weight loss stages occurred during the curing of M-S-H for 300 days (Figure 2). The first weight loss occurred in the temperature range from 50 to 200°C and is attributed to the removal of free/bound water. The second and third weight losses in the 200–320°C and 320–700°C ranges are attributed to the removal of constitutional water in aluminum hydroxide (Al-amorphous phases) and M-S-H phase respectively (Jia et al., 2016; Nied et al., 2016) (Figure 2A). As the dosage of Al3+ increases, the weight loss of the phase in the cementitious system increases gradually in the weight loss range of 200°C–400°C, and the weight loss phase in this range may be amorphous or microcrystalline hydroxyl aluminum. According to the weight loss data, the contents of free water and bound water in different samples are basically consistent, indicating that the addition of Al3+ did not affect the generation of M-S-H gel when the curing age is long enough and the initial ratio of Al/Si is less than 0.20. As the mass of free and bonding water depends on the porous channel in the MgO-SiO2-H2O system but not on the aluminium incorporated, the original structure of the M-S-H phase was unaffected by the incorporated aluminium (Figure 2B). The mass percents of various components in AMSH samples after curing for 300 days were shown in Table 3.
FIGURE 2. (A) Thermo-gravimetric (TG) and (B) Derivative thermo-gravimetric (DTG) data for MSH samples with different Al3+ contents after curing for 300 days.
The molecular structure of the solid solution which included aluminum-amorphous phases (hydroxyl-aluminum) and M-S-H phases was characterized using the NMR. The coordination of the spectrum of 29Si NMR is usually expressed by Qn, where n represents the bridge oxygen number between each silicon-oxygen tetrahedral unit and other Si atoms. The chemical migration of 29Si in silicate minerals ranges from -60 to -120 ppm and according to different coordination, it can be divided into the following four intervals: -60 to -70 ppm represents a single free island silicate (Q0); -70 to -83 ppm represents the endpoint of p-silicate or chain silicate (Q1); -83 to -90 ppm represents the silicon-oxygen tetrahedron in the chain silicate (Q2); -90 to -100 ppm represents the silicon-oxygen tetrahedron in the chain silicate (Q3); -100 to -120 ppm represents the silicon-oxygen tetrahedron in the three-dimensional reticular silicate (Q4) (Wei et al., 2006; Wei et al., 2011). The transformation of the microstructure of the M-S-H phase is indicated by the peaks at -85.5 ppm (Q3-a) and -92.9 to -95.1 ppm (Q3-b) (Figure 3A). In Figure 3A, Q3-a indicates the Si unit via inverted Si-O-Si linkages, while Q3-b reflects the Si unit in the Si-O tetrahedral layer (Tonelli et al., 2016). Figure 3B shows that the coordination of a few Al3+ that entered the structure of the M-S-H phase and changed to the tetrahedral coordination [Al (Bernard et al., 2019)]. The chemical shift from -92.9 to -95.1 ppm suggests that Al3+ only occupied the Q3-b tetrahedra sites of the M-S-H layers and did not substitute for the Si4+ via inverted Si-O-Si linkages (Q3-a). Although the initial structure of the M-S-H phases was remained unchanged the average condensation degree was increased from 0.84 to 0.92 after the incorporation of Al3+ (Figure 3C).
FIGURE 3. 29Si NMR chemical shifts of MSH samples with different Al3+ contents after curing for 300 days (A) silica (B) aluminum (C) changes of the average condensation degree.
Using the deconvolution technique to fit the data of the NMR Test curve, we can figure out the percentage of Si and Al with different coordinations, and the specific data are shown in Table 4. After curing for 300 days, the polymerization average degree of M-S-H and Al/Si molar ratio
Where n is the initial Al/Si molar ratio in M-S-H, I(AlIV) is the percentage of moles of tetrahedral-Al.
TABLE 4. 29Si NMR chemical shifts (ppm) and relative intensities (%) from de-convolution of the29Si/27Al NMR spectra for the AMSH-2 ∼ 5 samples after curing for 300 days.
According to Figure 3C, with the increase of Al3+ incorporation, the polymerization average degree of M-S-H increase from 0.85 to 0.93, but obviously the adding amount of Al3+ is still low. When the initial Al/Si molar ratio exceeds 0.1, both the adding amount of Al3+ and the polymerization average degree of M-S-H remain at a constant value. The adding of Al3+ plays a filling role, as it connects the silicon oxygen tetrahedron chains together and increases the degree of polymerization of the stratified structure. The molecular structure of M-S-H was already highly aggregated, which limits the adding amount of Al3+. It also shows that the number of Si sites in the silicon oxygen tetrahedral chain replaced by Al3+ is not large, and that the main function is to connect.
The F-SEM data show that the M-S-H phase has honeycomb morphology and grown on the surface of the SF particles extending to the gaps (Figure 4A). The Mg/Si molar ratio of pure M-S-H phases was 0.95. After the incorporation of Al3+, the Mg/Si molar ratio remained unchanged in the M-S-H phases grown on the surface of SF particles, however, increased to 1.24 in M-S-H phases grown in the gaps (Figures 4A,B). After curing for 300 days, samples AMSH-1 and AMSH-5 both A and B had only amorphous specimens. The amorphous substance in sample AMSH-1 was still M-S-H gel with villous shape, the villi size was about 10–20 nm and there were a lot of nano-scale pores between the villi. Aluminium incorporation changed the morphology of M-S-H phases from honeycomb to petaline shape (Figure 4B).
FIGURE 4. Field emission scanning electron microscope (F-SEM) images of samples with different Al/Si molar ratios after curing for 300 days: (A) 0 and (B) 0.2.
The hydration process of MgO in the magnesium silicate hydrate system was accelerated by the addition of Al3+, and the rate of conversion from MgO to Mg(OH)2 increases with the increase of Al3+ content. However, it does not influence the formation of hydration products (M-S-H phases) and it slows down the M-S-H generation. According to TGA/DTG we know that Mg(OH)2 crystals with amorphous hydroxy aluminum are mixed together, which led to the position of weight loss peak being offset, and the increase of the weight loss range from 200°C to 300°C proved that there is a new phase formation in the M-S-H.
Irrespective of the amount of Al3+ doped, a limited amount of Al3+ entered the structure of the M-S-H phase, consequently, the initial molecular structure of the M-S-H remained unchanged. Aluminium ions occupied the Q3-b tetrahedra sites of the M-S-H layers and did not substitute for Si4+ via inverted Si-O-Si linkages (Q3-a). The average condensation degree and the Mg:Si molar ratio of the M-S-H phase raised with the increase of Al3+ content. Hydroxyl-aluminum, a residual aluminium amorphous phase, and the M-S-H phases formed a solid solution. The addition of Al3+ morphology of the M-S-H phase from honeycomb-like to petal-like.
The original contributions presented in the study are included in the article/Supplementary Material, further inquiries can be directed to the corresponding author.
YJ: Conception and design of study. YZ and XZ: Drafting the manuscript. YJ and FL: analysis and/or interpretation of data. WM, HY and RH: revising the manuscript critically for important intellectual content.
This work was supported by the National Natural Science Foundation of China (Grant No. 51808217), the Natural Science Foundation of Hebei Province (Grant No. E2019209403), the S and T Program of Hebei Province (Grant No. 19273803D), and the Research Project of Hebei Province (Grant No. B2019003028).
HY and RH was employed by China Railway 14th Bureau Group 2nd Engineering Co., Ltd.
The remaining authors declare that the research was conducted in the absence of any commercial or financial relationships that could be construed as a potential conflict of interest.
All claims expressed in this article are solely those of the authors and do not necessarily represent those of their affiliated organizations, or those of the publisher, the editors and the reviewers. Any product that may be evaluated in this article, or claim that may be made by its manufacturer, is not guaranteed or endorsed by the publisher.
Bernard, E., Lothenbach, B., Cau-Dit-Coumes, C., Pochard, I., and Rentsch, D. (2020). Aluminum Incorporation into Magnesium Silicate Hydrate (M-S-H). Cement concrete Res. 128, 105931. doi:10.1016/j.cemconres.2019.105931
Bernard, E., Lothenbach, B., Chlique, C., Wyrzykowski, M., Dauzères, A., Pochard, I., et al. (2019). Characterization of Magnesium Silicate Hydrate (M-S-H). Cement concrete Res. 116, 309–330. doi:10.1016/j.cemconres.2018.09.007
Bernard, E., Lothenbach, B., Rentsch, D., Pochard, I., and Dauzères, A. (2017). Formation of Magnesium Silicate Hydrates (M-S-H). Phys. Chem. Earth, Parts A/B/C 99, 142–157. doi:10.1016/j.pce.2017.02.005
Bonen, D., and Cohen, M. D. (1992). Magnesium Sulfate Attack on portland Cement Paste - II. Chemical and Mineralogical Analyses. Cement Concrete Res. 22, 707–718. doi:10.1016/0008-8846(92)90023-o
Ji, X. Y., Guan, W., and Pei, L. (2014). Effect of Polyethylene Glycol Modification on Microstructure and Solubility of Hydrated Calcium Silicate. J. Funct. Mater. 45 (1), 1089–1094. doi:10.3969/j.issn.1001-9731.2014.01.020
Jia, S. B., Zhang, X. X., and Li, Y. Y. (2019). Experimental Study on Strength and Leaching Characteristics of Alkali Activated Cement Stabilized Heavy Metal Contaminated Soil. Ind. Construction 49 (08), 142–146. doi:10.13204/j.gyjz201908023
Jia, Y., Wang, B. M., Wu, Z. L., and Zhang, T. T. (2017). Effect of CaO on the Reaction Process of MgO-SiO2-H2o Cement Pastes. Mater. Lett. 192, 48–51. doi:10.1016/j.matlet.2017.01.072
Jia, Y., Wang, B. M., and Zhang, T. T. (2017). Study on Reaction Mechanism of MgO-SiO2-H2o Cementing System under the Action of NA-HMP and CaO. Dalian: Dalian University of Technology.
Jia, Y., Wang, B., Wu, Z., Han, J., Zhang, T., Vandeperre, L. J., et al. (2016). Role of Sodium Hexametaphosphate in MgO/SiO2 Cement Pastes. Cement concrete Res. 89, 63–71. doi:10.1016/j.cemconres.2016.08.003
Li, J., Geng, G., Myers, R., Yu, Y.-S., Shapiro, D., Carraro, C., et al. (2019). The Chemistry and Structure of Calcium (Alumino) Silicate Hydrate: A Study by XANES, Ptychographic Imaging, and Wide- and Small-Angle Scattering. Cement Concrete Res. 115, 367–378. doi:10.1016/j.cemconres.2018.09.008
Li, J., Zhang, W., Garbev, K., Beuchle, G., and Monteiro, P. J. M. (2020). Influences of Cross-Linking and Al Incorporation on the Intrinsic Mechanical Properties of Tobermorite. Cement Concrete Res. 136, 106170. doi:10.1016/j.cemconres.2020.106170
Li, J., Zhang, W., and Monteiro, P. J. M. (2020). Structure and Intrinsic Mechanical Properties of Nanocrystalline Calcium Silicate Hydrate. ACS Sustain. Chem. Eng. 8, 12453–12461. doi:10.1021/acssuschemeng.0c03230
Li, Z. H., Zhang, T. S., Hu, J., Tang, Y., Niu, Y. F., Wei, J. X., et al. (2014). Characterization of Reaction Products and Reaction Process of MgO-SiO2-H2o System at Room Temperature. Construction Building Mater. 61, 252–259. doi:10.1016/j.conbuildmat.2014.03.004
Liu, Y., Mao, Z., Y., Wang, Z., Y., He, Y., Yu, J., and Zhu, Y. (2021). Study on Preparation and Adsorption Properties of Dopamine Modified Sepiolite. Speciality Petrochemicals 38 (02), 50–56. doi:10.3969/j.issn.1003-9384.2021.02.010
Lothenbach, B., Nied, D., L'Hôpital, E., Achiedo, G., and Dauzères, A. (2015). Magnesium and Calcium Silicate Hydrates. Cement concrete Res. 77, 60–68. doi:10.1016/j.cemconres.2015.06.007
Maruyama, I., Nishioka, Y., Igarashi, G., and Matsui, K. (2014). Microstructural and Bulk Property Changes in Hardened Cement Paste during the First Drying Process. Cement concrete Res. 58, 20–34. doi:10.1016/j.cemconres.2014.01.007
Nied, D., Enemark-Rasmussen, K., L'Hopital, E., Skibsted, J., and Lothenbach, B. (2016). Properties of Magnesium Silicate Hydrates (M-S-H). Cement concrete Res. 79, 323–332. doi:10.1016/j.cemconres.2015.10.003
Richardson, I. G. (1999). The Nature of C-S-H in Hardened Cements. Cement concrete Res. 29, 1131–1147. doi:10.1016/s0008-8846(99)00168-4
Santhanam, M., Cohen, M. D., and Olek, J. (2020). Mechanism of Sulfate Attack: a Fresh Look: Part 1: Summary of Experimental Results. Cement concrete Res. 32, 915–921. doi:10.1016/s0008-8846(02)00724-x
Song, Q., Nie, J., Wu, D., Hu, Y. R., and Chen, Y. X. (2021). Effect of SO42−, Cl− and Mg2+ on the System of C-S-H and Ca(OH)2. Construction Building Mater. 285, 122955. doi:10.1016/j.conbuildmat.2021.122955
Tang, Y., and Chen, W. (2020). Effect of Magnesium on the Structure and Chemical Composition of Calcium Silicate Hydrate at Elevated Temperature. Construction Building Mater. 240 (C), 117925. doi:10.1016/j.conbuildmat.2019.117925
Tonelli, M., Martini, F., Calucci, L., Fratini, E., Geppi, M., Ridi, F., et al. (2016). Structural Characterization of Magnesium Silicate Hydrate: towards the Design of Eco-Sustainable Cements. Dalton Trans. 45, 3294–3304. doi:10.1039/c5dt03545g
Walling, S. A., Kinoshita, H., BernalCollier, S. A. N. C., Collier, N. C., and Provis, J. L. (2015). Structure and Properties of Binder Gels Formed in the System Mg(OH)2-SiO2-H2O for Immobilization of Magnox Sludge. Dalton Trans. 44, 8126–8137. doi:10.1039/c5dt00877h
Wei, J. X., Chen, Y., and Li, Y. (2006). The Reaction Mechanism between MgO and Microsilica at Room Temperature. J. Wuhan Univ. Technology-Materialsà Sci. 21 (2), 88–91. doi:10.1007/bf02840848
Wei, J. X., Yu, Q. J., Zhang, W. S., and Zhang, H. T. (2011). Reaction Products of MgO and Microsilica Cementitious Materials at Different Temperatures. J. Wuhan Univ. Technology-Materials Sci. 4 (26), 745–748. doi:10.1007/s11595-011-0304-3
Zhang, T., Li, T., Zou, J., Li, Y., Zhi, S., Jia, Y., et al. (2020). Immobilization of Radionuclide 133Cs by Magnesium Silicate Hydrate Cement. Materials (Basel) 13, 1–17. doi:10.3390/ma13010146
Keywords: magnesium silicate hydrate system, hydroxyl-aluminum, phase transformation, microstructure, aluminium ion content
Citation: Jia Y, Zou Y, Zou X, Jiang Y, Li F, Ma W, Yan H and Hua R (2022) Effect of Aluminum Incorporation on the Reaction Process and Reaction Products of Hydrated Magnesium Silicate. Front. Mater. 8:810535. doi: 10.3389/fmats.2021.810535
Received: 07 November 2021; Accepted: 08 December 2021;
Published: 12 January 2022.
Edited by:
Lijie Guo, Beijing General Research Institute of Mining and Metallurgy, ChinaReviewed by:
Zhihong Zhang, Beijing University of Technology, ChinaCopyright © 2022 Jia, Zou, Zou, Jiang, Li, Ma, Yan and Hua. This is an open-access article distributed under the terms of the Creative Commons Attribution License (CC BY). The use, distribution or reproduction in other forums is permitted, provided the original author(s) and the copyright owner(s) are credited and that the original publication in this journal is cited, in accordance with accepted academic practice. No use, distribution or reproduction is permitted which does not comply with these terms.
*Correspondence: Yuan Jia, amlhMTMyMDEyQG5jc3QuZWR1LmNu
Disclaimer: All claims expressed in this article are solely those of the authors and do not necessarily represent those of their affiliated organizations, or those of the publisher, the editors and the reviewers. Any product that may be evaluated in this article or claim that may be made by its manufacturer is not guaranteed or endorsed by the publisher.
Research integrity at Frontiers
Learn more about the work of our research integrity team to safeguard the quality of each article we publish.