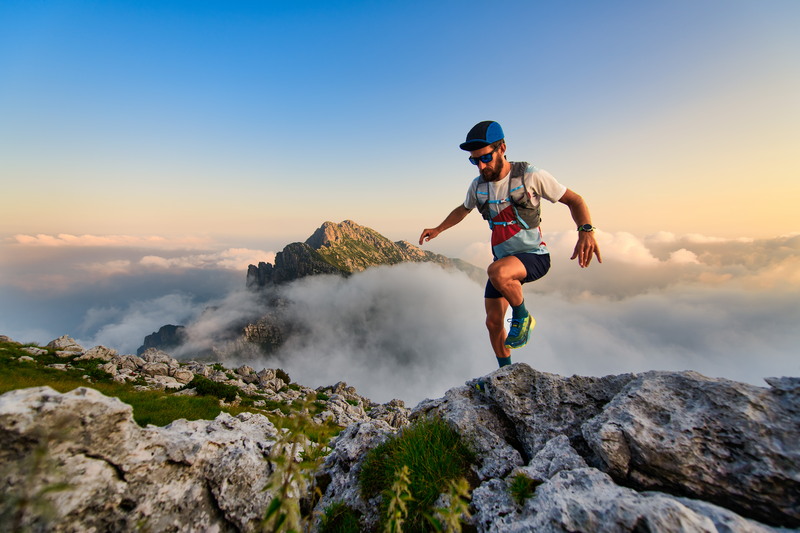
95% of researchers rate our articles as excellent or good
Learn more about the work of our research integrity team to safeguard the quality of each article we publish.
Find out more
ORIGINAL RESEARCH article
Front. Mater. , 27 January 2022
Sec. Structural Materials
Volume 8 - 2021 | https://doi.org/10.3389/fmats.2021.801464
This article is part of the Research Topic 2022 Retrospective: Structural Materials View all 5 articles
Researchers have conducted numerous investigations on various repair techniques to restore the mechanical properties of fire-damaged concrete. However, most of the techniques are either expensive or require high technical skills. As a continuous work, this study involved an experimental investigation of the effects of various low-cost repair techniques to restore the mechanical properties of fire-damaged concrete. Sixty cylindrical concrete samples were subjected to heat ranging from 400°C to 800°C in a propane gas furnace. The samples were categorized into six groups, including the following: undamaged, fire-damaged, and fire-damaged and repaired using water curing; fire-damaged and repaired using cement-based slurry injection; re-curing fire-damaged and repaired with steel wire mesh along with epoxy resin wrapping; and fire-damaged and repaired using epoxy injection. The samples were tested for non-destructive and destructive tests, including ultrasonic pulse velocity, rebound hammer, and compressive strength. The results showed that the use of cement-based slurry injection along with the water-curing repair technique could regain almost 90% of its ultimate strength and secant stiffness, making it the most effective low-cost repair technique for fire-damaged concrete exposed up to 700°C.
Despite having good thermal resistance, concrete undergoes physical and chemical changes when exposed to high temperatures, thus reducing its mechanical and structural properties. However, it is very rare for structures to collapse entirely due to fire loading (Industry 2008; J.; Ingham 2009; Mostafaei et al., 2009). The main reason for the least collapses is the low thermal conductivity of concrete that maintains the lower temperature at the core of the concrete and load transfer due to changes in relative stiffness. Studies from natural fires (Berry 1991; Nene and Kavle 1991; Morales 1991; Sivagnanam 2002; Dilek 2005; Srinivasan et al., 2006; Smart 2006; J. P.; Ingham 2007) have shown that the fire-damaged structures perform pretty well and failures at both local and global structure levels are rare. The structures can be repaired and brought back to their original conditions in most cases. A variety of solutions have also been developed to improve the fire resistance of structures (Cai et al., 2021).
The compressive strength of concrete is found to be unaffected by temperatures below 300°C (Noumowe et al., 1996; Phanl 2001; V. I.; Korsun et al., 2014; V.; Korsun and Baranov 2020) or, in some cases, slightly increased due to water evaporation, resulting in hydration of unhydrated cement (Xu et al., 2001; Xiao and Gert, 2004; Ma et al., 2015). When the concrete temperature approaches 400°C, it loses a significant amount of compressive strength (Chan et al., 1996; Handoo et al., 2002). When the temperature surpasses 500°C, the residual strength is reduced to 50% of its original strength (Xu et al., 2001) and further reduced to 30% when the temperature approaches 800°C (Poon et al., 2001). At temperatures above 1,000°C, the concrete loses practically all its strength (Husem 2006). The change in mechanical properties of concrete due to the influence of high temperatures can be attributed to non-uniform thermal gradient causing shrinkage of cement paste and expansion of coarse aggregates (Wang 2008), hydrates decomposition due to the decomposition of C-S-H gel and portlandite (Alonso and Fernandez 2004), loss of the bound water resulting in the formation of voids and coarsening of pore structure (Peng and Huang 2008), the vapor pressure causing the pore pressure inside the closed pores (Ai et al., 2001), and cracking that is developed due to the rehydration of the lime. Important residual fracture properties of normal and high-strength concrete also decrease at high temperatures (Zhang and Bicanic 2002; Yu et al., 2015; Yu et al., 2016).
As a result, several repair and rehabilitation procedures were devised to restore the original design strength. To date, the principal repair methods for concrete structure strengthening are section enlargement, bolt-plating reinforcement, and fiber-reinforced polymer (FRP) reinforcement (Greepala and Nimityongskul 2008; Yaqub and Bailey 2011; L. Z.; Li et al., 2013; Yaqub et al., 2013; Jiang et al., 2017; Z.; Li et al., 2019). Recently, the FRPs to repair concrete elements have been reported as one of the successful approaches for restoring the compressive strength of fire-damaged concrete (Yaqub 2010; Bisby et al., 2011; Yaqub and Bailey 2011; Yaqub et al., 2013; Roy et al., 2016). However, the stiffness properties of fire-damaged concrete could not be restored significantly (Yaqub 2010; Kai et al., 2011; Yaqub et al., 2013; Roy et al., 2016; Usman et al., 2021), which is the main shortcoming of using FRPs, as the damaged structures should regain both their strength and stiffness. In addition, FRPs are expensive and require high technical expertise for their application (von Reden et al., 2019).
Some recent researches have shown that fire-damaged concrete can be restored to its original strength and stiffness if it is exposed to damp conditions for a long period of time (Crook and Murray 1970; Poon et al., 2001; Henry et al., 2014; Q.; Li et al., 2014; Khan et al., 2020; Usman et al., 2021; Noman and Yaqub 2021). This process of recovery of properties is referred to as the post-fire curing technique. During this process, the rehydration of the dehydrated cement matrix occurs due to the supply of water, thus reversing the deterioration caused by chemical changes due to the fire (Alonso and Fernandez 2004; Xuan and Shui 2011; L.; Li et al., 2020). A thorough literature assessment reveals that post-fire curing leads to outstanding recovery of mechanical, chemical, and durability properties and pore and crack recovery in concrete (L. Li et al., 2020). Usman et al. (Usman et al., 2021) investigated the mechanical properties of fire-damaged and repaired concrete. They found that the strength and stiffness can both be regained when CFRPs are used along with supplementary materials, including re-curing.
To the best of the authors’ knowledge, no study has been carried out to investigate the comparison of various low-cost repairing techniques for regaining the strength and stiffness of fire-damaged concrete. In this paper, different low-cost-repair techniques such as post-fire curing (WCR), cement-based slurry injection along with re-curing (SIWCR), steel wire mesh along with epoxy resin wrapping (SMER), and epoxy injection repair (EPI) methods are employed to regain the original strength and stiffness of fire-damaged concrete. The heating regime of 400°C–800°C is chosen for noticeable deterioration and effectiveness of the repair. The damaged samples were tested for both non-destructive [weight loss, ultrasonic pulse velocity (UPV), and rebound hammer] and destructive tests (load-deformation, ultimate compression, and stiffness) to assess the effectiveness of repair techniques on fire-damaged concrete. Eventually, this study proposes an effective, low-cost repair technique in the restoration of fire-damaged concrete.
The material used for casting the samples is coarse aggregates, fine aggregates, cement, and drinkable water. Margalla crush as coarse aggregate (siliceous) with a maximum size of ½ inches (12.7 mm) is used. The summary of properties determined by testing the coarse and fine aggregates is provided in Table 1. The physical and chemical properties of the cement supplied by the manufacturer are shown in Table 2. The concrete samples were prepared with a mix design proportion of 1:1.5:3 (cement:sand:crush), with a water–cement ratio of 0.45. A total of 63 cylinders having a size of 6 inches (150 mm) × 12 inches (300 mm) were cast.
After fire damage, the samples were repaired using various techniques. The repair material included epoxy resin mortars, epoxy injection liquid, and steel wire mesh. The properties of epoxy resin mortar and epoxy injection liquid provided by the supplier (Sika Pvt. Limited, Pakistan) are given in Table 3 and Table 4. The steel wire mesh is used to enhance the load-carrying capacity of the concrete. The steel wire mesh used in this research has properties shown in Table 5.
Some of the specimens were exposed to high temperatures (400°C, 600°C, 700°C, and 800°C) in a custom-built furnace without the application of any load (unstressed condition). The selection of the range of 400°C–800°C is based on the literature, at which noticeable deterioration can occur (Lin et al., 1996; Khoury 2000; Kodur 2014; Ma et al., 2015). A special-purpose propane gas furnace was constructed for testing cylinders. The clear inside length of the furnace was 8 ft (2.438 m) and a clear width of 3.5 ft (1.06 m). The clear height of the furnace was 3 ft (0.914 m). The furnace lining was made from 9-inch-thick (228.6 mm) brick walls and prestressed slabs at the top. On the inside, the furnace lining was covered with 2-inch-thick (50 mm) ceramic wool, a very high fire resistance (maximum temperature resistance 1,400°C) mineral insulation material. The purpose of insulation was to contain the fire, and no heat loss could occur. The furnace was manually operated by controlling the gas supply from high-pressure gas cylinders. Figure 1 shows the placement of concrete cylinders inside the furnace.
An average of 15 thermocouples installed within the furnace was used to determine the temperature. One day before the fire test, the specimens were subjected to a temperature of 150°C for 2 h to eliminate any capillary water present inside the concrete, preventing spalling. After reaching the target temperature, the temperature was kept constant for 1 h to ensure that the external temperature was homogeneous from the surface to the core. The adjusted average time-temperature curves for each temperature are shown in Figure 2. The maximum temperature at the cores was observed to be 782°C, 680°C, 591°C, and 393°C for the target temperatures of 800°C, 700°C, 600°C, and 400°C, respectively. After the target temperature, the furnace fuel supply was terminated, and the samples could cool down inside the furnace. Figure 3 and Figure 4 shows the top view and side view of the damaged specimens after exposure to elevated temperatures, respectively. The crack pattern is a clear indication of the damage to the specimens. The samples were removed from the furnace after 24 h of the fire test and placed in the laboratory, stacked for 2 months before further testing/repairing can be performed. Few of the samples that were spalled during fire tests were discarded for any further testing.
The samples were categorized into six different groups, including both unheated and heated samples. Four of the six groups were repaired using different repairing techniques, including water re-curing for 28 days (WCR), cement-based slurry injection + water curing for 28 days (SIWCR), steel wire mesh with epoxy resin mortar (SMER), and epoxy injection (EPI). The repairing of samples was carried as per the standard procedures and manuals provided by the chemical manufacturers. Table 6 shows the total number of samples, including undamaged, fire-damaged, and fire-damaged and repaired samples.
The concrete surfaces were cleaned with a steel wire brush, and the surface was cleaned with a high-pressure air blower. The micro-cracks, voids, spalled surfaces, cavities, and any reduction of the cross section of the concrete cylinder due to heating at high temperatures were filled with the epoxy resin mortar (Sikadur 31 CF slow). The epoxy resin mortar material is supplied in two boxes called components A and B. The components A and B are mixed in the ratio of 2:1 by weight, respectively, as specified by the manufacturer (ref: Figure 5A). The components were mixed for 3 min until a uniform greyish color was obtained and consistency became smooth. The cavities on the surface of the concrete specimens produced by high temperatures were filled with 5 mm of the epoxy resin mortar with the help of a trowel and spatula.
FIGURE 5. Application of epoxy resin mortar with steel wire mesh on fire-damaged concrete cylinders. (A) Mixing of component A&B (B,C) Application of epoxy resin mortar on cylinders.
After that, the samples were placed in a water curing tank for 28 days. The curing method proved to be the easiest and most economical method of all other repair techniques, except that it consumes much time (28 days of curing). The samples were immersed completely in the curing tank for 4 weeks, with the water temperature that is set equal to room temperature. The samples were taken from the water curing tank after 28 days and stacked for further testing.
The drill holes of 6 mm diameter and 63.5 mm deep for cement slurry injection were introduced with the drill machine. A total 18, 14, 9, and 8 holes were created in each cylinder heated at 400°C, 600°C, 700°C, and 800°C, respectively. The number of holes was decided upon the extent of damage of the post-heated cylinders. The drilling process requires mechanical forces to the specimen; therefore, the number of holes in the specimens was decided to be reduced with increasing temperature to avoid further damage. Supplementary Appendix S1A describes the location of holes for each in fire-damaged concrete cylinders. The holes and surface were then cleaned using a wire brush and blower. Then, before slurry injection, the cylinders were immersed in water for initially saturating the surface for 5 to 10 min. The filling of the holes and repairing spalled surfaces were done with a workable cement slurry having a water/cement ratio of 1. The slurry was injected into the drilled holes with the help of a scrapper without any external pressure. The slurry moved into the hole smoothly due to the gravity.
The repaired cylinders were placed under an open environment for 10 h for the initial setting and then submerged for 28 days in a water tank for final setting and re-curing.
First, holes were drilled in the specimens, and epoxy resin mortar (Sikadur 31 CF Slow) was used to fill them. A single mesh with 1.4-mm-thick diameter wires, and a mesh size of 19 mm was winded around the cylinder (see Table 5 for wire and mesh properties). A 12.5-mm gap was left from the top and bottom, and a 150-mm overlap in the running direction was provided as splice length. Then, the 5- to 7-mm-thick layer of the same mortar was applied, and the surface was prepared before (see Figure 5B,C). The concrete cylinder’s average cross-sectional (diameter) increase was 12.5 mm. The repaired cylinders were placed under an open environment for 10 h for the initial setting and then submerged for 28 days in a water tank for final setting and re-curing. Testing the cylinders in this group was performed after 5 weeks of final repairing.
The specimens, separated for epoxy injection, were initially drilled one 62.5 mm deep and in 13-mm-diameter hole in each, and Steel Nozzle (Steel Packer) in the slanting position was installed for Epoxy Injection (Sikadur 52 LP). Epoxy was injected under pressure ranging between 17 and 20 MPa with the help of a pump having a pressure capacity up to 68 MPa. The leakage of the epoxy was then stopped by the epoxy resin mortar (Sikadur 31 CF Slow). After 24 h, the extruded part of the nozzle was removed using the cutting machine, and the surface of the cylinders was finished by using Epoxy resin mortar. The compression test on repaired and strengthened cylinders was performed after 5 weeks of repairing so that the setting of the repair materials (Epoxies and Mortars) for proper bonding can be ensured.
The cost of each restoration approach was determined for a single concrete cylinder, as shown in Table 7. The pricing includes both the material and labor costs associated with the application on the specimen. It should be mentioned that, of all the procedures, the cement-based slurry injection and water curing technique proved to be the most cost-effective.
The compressive strength of all the specimens was evaluated with reference from ASTM C805 (ASTM-International 2018) before and after heating them to four different temperatures, using Schmidt Hammer, as shown in Figure 6A. Schmidt Hammer G-896-Digi Schmidt, manufactured by Proceq, Switzerland, was used for this purpose. Twenty readings of rebound number on each specimen were taken, and then, the strength from an average of 20 was the strength considered. In this way, for one specimen final, the NDT strength noted was the average of two strengths.
FIGURE 6. Testing of concrete cylinders. (A) Schmidt hammer testing. (B) Ultrasonic pulse velocity testing. (C) Compression testing: (i) LVDT for lateral deformation and (ii) LVDT for axial deformation.
The concrete cylinders were also tested for their quality using 58-E4800 UPV tester by the Controls Group. The UPV is a non-destructive technique to determine the cracks, voids, honeycombs, and other non-homogeneity in concrete. The measurement comprises of the time taken by wave pulse to travel into concrete from the transmitter end to the receiver end. The grease or petroleum oil is applied to the surface of the concrete for smooth and effective transfer of the ultrasonic waves. The cylinders were tested for UPV as per ASTM C597 (ASTM-International 2016). The UPV was calculated using the following equation:
where
Before the compression testing, the cylinders were properly capped with sulfur using the ASTM C617 (ASTM-International 2015b) standard method to ensure a smooth surface for load application. The destructive testing was carried out on Universal Testing Machine (UTM) by Besmak, Turkey, with a compression capacity of 1,500 kN. The testing was carried out using the ASTM C39 (ASTM-International 2020) standard method with a controlled loading rate of 0.25 MPa/s. The axial and lateral deformations were measured using LVDTs with a gauge length of 50 mm attached to the compressometer, as shown in Figure 6C.
The test results indicated that the weights of the specimens upon averaging the weights of 33 (3 + 15+15), unheated, and post-heated (exposed to) 400°C and 600°C were 13.22, 12.53, and 12.22 kg, respectively. On the other hand, the weights determined from the average results of 30 (15 + 15) specimens exposed to 700°C and 800°C were 12.11 and 11.96 kg, respectively. It is very clear from Figure 7 that as the concrete is being exposed to a higher temperature, the loss in weight increases, which indicates that the internal degradation of the concrete increases as the water from the concrete is lost with the increasing temperature.
The UPV results suggest that the quality of concrete is reduced from excellent (4.62 km/s) to good (3.63 km/s), doubtful (2.90 km/s), doubtful (2.12 km/s), and doubtful (1.91 km/s) when exposed to elevated temperatures 400°C, 600°C, 700°C, and 800°C, respectively (see Figure 6). The UPV results further showed that the concrete quality has improved to good (4.23 km/s), good (3.76 km/s), good (3.50 km/s), and medium (3.11 km/s), when the samples were cured in a water tank for 28 days after their relevant exposure temperatures. The percentage of damage determined for fire-damaged specimen compared to the repaired specimen through UPV is shown in Figure 8. The regain of strength indicates the reduction of microcracks due to rehydration of the unhydrated cement.
The average compressive strengths as determined by the Schmidt rebound hammer test, i.e., NDT strengths are 27.2 MPa for unheated, and 22.3, 18.2, 16.89, and 14.58 in MPa for Post-heated exposed to 400°C, 600°C, 700°C, and 800°C respectively. Unconfined compressive strengths obtained from averaging compression test results of two or three specimens are 28.48 MPa for unheated and 18.45, 12.7, 9.9, and 5.66 in MPa for post-heated, exposed, to 400°C, 600°C, 700°C, and 800°C, respectively.
From Figure 9, it can be seen that the percentage difference in the unconfined compressive strength of post-heated specimens w.r.t. those unheated, when determined from the non-destructive testing method, also increases with the increasing temperature. The rebound hammer calculates the surface compressive strength of the concrete. In case of fire damage, the concrete’s surface is more damaged than the core. The increase in the difference of compressive strengths and rebound hammer non-destructive test between controlled samples and heated samples show that the rebound hammer testing can indicate loss of compressive strength but cannot determine the realistic strength value at higher temperatures.
FIGURE 9. Comparison between non-destructive and destructive testing for heated and unheated specimens.
The structural behaviors of repair members cannot be considered good when the deformations in the members exceed beyond the permissible range even if the structure is still in sound condition. The effect of exposure temperatures on the load-deformation curves of unrepaired post-heated and unheated concrete is shown in Figure 10. It can be noticed that, when the specimens were heated from 400°C to 800°C, their load-carrying capacity and deformability decreased significantly compared to unheated specimens. In addition, as presented in Figure 10A, the load-carrying capacities and deformability of post-fire water cured (WCR) concrete cylinders have increased significantly, demonstrating that the technique is extremely effective at increasing load-carrying capacity and deformability.
FIGURE 10. Load deformation curves of (A) heated, unheated, and repaired with WCR (B) heated, unheated, and repaired with SIWCR (C) heated, unheated, and repaired with SMER.
Figure 10B indicates that the slurry injected and water curing repair (SIWCR) technique is highly effective at restoring load carrying capacity and deformability at 400°C; the deformation produced at the corresponding load is less than that produced by water cured samples that have been post-heated to 400°C. The regained load carrying capacity for the repaired sample after 400°C and 600°C is even more than the original capacity of the undamaged samples. Compared to unheated cylinders, the load-carrying capacity and deformability of concrete cylinders post-heated to 700°C and 800°C were lowered for the cement slurry injected.
Figure 10C shows that the SMER technique increases the load-carrying capacity of the concrete specimens when exposed to an elevated temperature of 400°C–800°C. The increased cross section and confining action of the steel were responsible for higher load-carrying capacity in the SMER technique. However, the deformations were significantly greater than those in the unheated cylinders. The epoxy injection repair technique produced the worst results in terms of load capacity and deformation. The high pressure of the epoxy injection and compromised concrete owing to fire damage were the most likely causes.
Figure 11 shows the loss in ultimate compressive strength of concrete cylinders exposed to high temperatures. Temperatures of 400°C, 600°C, 700°C, and 800°C for 1 h resulted in losses of 35.22%, 55.40%, 65.23%, and 80.13% of concrete final compressive strengths, respectively. For temperatures ranging from 400°C to 600°C, the residual strength of concrete was less than half of the original strength.
FIGURE 11. Comparison of ultimate compressive strengths for various repair techniques and temperature exposures.
The compressive strength can be reinstated to some extent using the technique of post-fire curing, as is evident from Figure 11. Just by re-curing the fire-damaged concrete cylinders for 28 days in the curing tank, the regain of 96.57%, 87.43%, 77.49%, and 75.50% of the original compressive strength was observed for the exposure temperatures of 400°C, 600°C, 700°C, and 800°C for 1 h, respectively. The regain of original strength is possibly due to rehydration of the dehydrated cement under the supply of moist conditions. It is also noteworthy that the trend of regaining strength through post-fire curing decreases little with the increase in exposure temperature.
Cement-based slurry injection and water curing repair technique (SIWCR) showed the most promising results. This repair technique regained 109.39%, 104.42%, 99.35%, and 94.39% of the original compressive strength even after exposure to temperatures of 400°C, 600°C, 700°C, and 800°C for 1 h, respectively, as shown in Figure 11. The regain in compressive strength can be due to an increase in the strength of concrete due to slurry injection combined with rehydration of unhydrated cement, thus filling the microcracks developed due to high-temperature exposures. Figure 11 shows the highest trend of this repairing technique.
Steel wire mesh with epoxy resin mortar repaired (SMER) technique also showed much increase in regaining of the compressive strength or even more than the required strength at 400°C. However, the extent of regaining was found to be lesser as compared to the SIWCR technique. This repair technique regained 105.96%, 93.29%, 89.28%, and 80.48% of the original compressive strength even after exposure to temperatures of 400°C, 600°C, 700°C, and 800°C for 1 h, respectively. The trend line for the decrease of compressive strength can be seen in Figure 11.
The epoxy injected (EPI) post-heated concrete cylinders exhibited a lower compressive strength improvement compared to the other repair techniques. The modest increase is attributed to the fact that, when post-heated concrete cylinders were subjected to pressure for epoxy injection, the tensile stresses within the concrete cylinders increased, resulting in the formation of more cracks and consequently causing a decrease in compressive strength.
Figure 12 show that, after exposure to elevated temperatures, the stiffness of concrete has declined substantially. It is imperative to the survival of fire-damaged structures that their reinstatement and stiffness maintenance must be ensured because the loads in structures are always redistributed in accordance with the stiffnesses of the structural members. If the higher or lower stiffness is produced in the reinstated post-heated parts of the building and the unheated parts of the building, then overstressing and torsional effects under gravity and lateral loading cause the total structural stability in the building’s structure (Yaqub et al., 2013). The secant stiffness is calculated by dividing load at 85% of the ultimate axial load carried to the corresponding deformation measured during testing. It can be seen from Figure 12 that, with the increased exposure temperature, the axial stiffness values of the post-heated unconfined concrete cylinders were degraded significantly with a higher rate of degradation in stiffness with rising temperatures. The degradation of axial stiffness is attributed to the internal microcracking and the creation of voids in the post-heated concrete specimens.
Figure 12 indicates that the stiffness improvement after cement slurry injection and the water re-curing method was higher than all other techniques. It was also seen that the stiffness regained close to the undamaged specimens when the exposure temperature was 400°C. At exposure temperatures greater than 400°C, the stiffness improvement was slightly lower than that of the unheated. The improved stiffness is being reduced from a higher value to lower temperatures 600°C–800°C. A similar case was seen with the only water cured samples; however, the stiffness recovery compared to SIWCR samples is found lesser. At the temperature of 800°C, the WCR samples exhibit better stiffness properties than any other repair techniques. Figure 12 shows the trend of the effectiveness of these repairing techniques.
It is indicated that the stiffness improvement by epoxy resin mortar (Sikadur 31) filling and steel wire meshing with the epoxy resin mortar is ineffective in restoring the stiffness compared to the other techniques, i.e., only water curing technique and cement slurry injection with water curing.
It is pertinent to highlight that epoxy injection is used to restore or increase the axial stiffness of the post-heated concrete cylinders heated up to 400°C. It is important to note that, for temperatures higher than 400°C, the stiffness of the post-heated concrete cylinders was dropped further, and the epoxy injection does not contribute to restoring the stiffness of the post-heated concrete cylinders. Figure 12 shows that the stiffness of the epoxy-injected concrete cylinders was reduced for post-heated concrete cylinders exposed to temperatures greater than 400°C. The loss in stiffness is due to the fact that, when the concrete cylinders were exposed to temperatures above 400°C, the concrete grew weaker, spongier, and porous as the temperature increased. The epoxy injected pressure could not be tolerated by the cylinders exposed to temperatures above 400°C. The post-heated concrete cylinders were further cracked by the pressure applied to inject the epoxy. The epoxy injection pressure widened internal microcracks. As a result of the bond breakdown, the stiffness was further lowered and could not be restored to the level of the undamaged samples.
Cement slurry injection, along with water curing, is an effective technique for restoring the strength and stiffness of fire-damaged concrete structures. However, because submerging the entire structure in water is impossible, its practical application is limited. Various methods such as ponding (Zhutovsky and Kovler 2013), wet curing (Devadass 2019), and sprinkling (Devadass 2019) are examples of post-fire curing techniques that can be used in practical projects to restore fire-damaged concrete structures. The method to be used will be determined by the nature of the work and the weather conditions. The main disadvantage of this technique is its long repair duration. Further research should be undertaken to use forced mechanical techniques to speed up the curing process.
This study examined the effects of low-cost restoration procedures on the mechanical properties of fire-damaged concrete. In a propane gas furnace, 60 cylindrical concrete samples were heated from 400°C to 800°C. The samples were categorized into six groups, including the following: undamaged, fire-damaged, and fire-damaged and repaired using water curing; fire-damaged and repaired using cement-based slurry injection; re-curing fire-damaged and repaired with steel wire mesh along with epoxy resin wrapping; and fire-damaged and repaired using epoxy injection. Non-destructive and destructive tests, such as UPV, rebound hammer, and compressive strength, were performed on the samples. On the basis of the results, the following conclusions can be drawn:
1. The weight of concrete is reduced 5.22%, 7.56%, 8.40%, and 9.53% due to the evaporation of concrete moisture when exposed to the temperature of 400°C, 600°C, 700°C, and 800°C. The moisture loss decreases with increasing temperature beyond 600°C.
2. The UPV results also indicate the damage by reducing the velocity from 4.62 to 3.63, 2.90, 2.12, and 1.91 km/s when exposed to 400°C, 600°C, 700°C, and 800°C temperatures of in concrete; however, the rebound hammer test results are inefficient at higher temperatures.
3. Post-fire repair using the curing technique is effective in regaining most of the strength (97%, 87%, 77%, and 75% from 64%, 44%, 34%, and 19.87%) and stiffness (333, 279, 236, and 192 kN/mm from 308, 265, 214, and 177 kN/mm) properties at 400°C, 600°C, 700°C, and 800°C temperature. However, the effectiveness is reduced at temperatures beyond 600°C. The regain of strength is probably due to the reversed chemical changes (rehydration of the dehydrated cement matrix) due to water supply.
4. The performance in strength resistance of the SMER repair technique is better than WCR (106%, 93%, 89%, and 80% from 64%, 44%, 34%, and 19.87%). However, this technique is poor in regaining the stiffness (326, 265, 252, and 118 kN/mm from 308, 265, 214, and 177 kN/mm).
5. The epoxy injection repair technique is found to be an ineffective repair technique for both strength and stiffness regain when concrete is heated beyond 400°C temperature.
6. The SIWCR repair technique provides the best results in restoring the original strength (109%, 104%, 99%, and 94% from 64%, 44%, 34%, and 19.87%). As compared to other techniques, the stiffness is also considerably regained (509, 438, 390, and 119 kN/mm from 308, 265, 214, and 177 kN/mm) except for temperatures at 800°C.
7. Overall, the cement-based slurry injection, along with the water curing repair technique, is the best low-cost repair technique for restoring residual strength and stiffness for concrete damaged due to fire up to 700°C.
The original contributions presented in the study are included in the article/Supplementary Material. Further inquiries can be directed to the corresponding author.
The author contributions to the paper are as follows: MN and MY proposed the idea and designed the experimental program; MN and MU conducted the tests and analyzed the data; MN, MY, and MA wrote the paper. MM and NV arranged the funding and reviewed the final version of the manuscript. All authors reviewed the paper and accepted the final version for submission.
The research is partially funded by the Ministry of Science and Higher Education of the Russian Federation as part of the World-Class Research Center Program: Advanced Digital Technologies (contract no. 075-15-2020-934 dated November 17, 2020). The research is also partially funded by the Higher Education Commission (HEC) of Pakistan under grant number NRPU-10607.
The authors declare that the research was conducted in the absence of any commercial or financial relationships that could be construed as a potential conflict of interest.
All claims expressed in this article are solely those of the authors and do not necessarily represent those of their affiliated organizations or those of the publisher, the editors, and the reviewers. Any product that may be evaluated in this article, or claim that may be made by its manufacturer, is not guaranteed or endorsed by the publisher.
The Supplementary Material for this article can be found online at: https://www.frontiersin.org/articles/10.3389/fmats.2021.801464/full#supplementary-material
Ai, H., Young, J. F., and Scherer, G. W. (2001). Thermal Expansion Kinetics: Method to Measure Permeability of Cementitious Materials: II, Application to Hardened Cement Pastes. J. Am. Ceram. Soc. 84 (2), 385–391.
Alonso, C., and Fernandez, L. (2004). Dehydration and Rehydration Processes of Cement Paste Exposed to High Temperature Environments. J. Mater. Sci. 39 (9), 3015–3024. doi:10.1023/B:JMSC.0000025827.65956.18
ASTM-International (2015a). “ASTM C127-15, Standard Test Method for Relative Density (Specific Gravity) and Absorption of Coarse Aggregate,” in Annual Book of ASTM Standards (West Conshohocken, PA. http://www.astm.org/cgi-bin/resolver.cgi?C127-15.
ASTM-International (2019a). “ASTM C136/C136M-19, Standard Test Method for Sieve Analysis of Fine and Coarse Aggregates,” in Annual Book of ASTM Standards (West Conshohocken, PA. https://www.astm.org/Standards/C136.htm.
ASTM-International (2020). “ASTM C39/C39M-20, Standard Test Method for Compressive Strength of Cylindrical Concrete Specimens,” in Annual Book of ASTM Standards (West Conshohocken, PA. http://www.astm.org/cgi-bin/resolver.cgi?C39C39M-20.
ASTM-International (2016). “ASTM C597-16, Standard Test Method for Pulse Velocity through Concrete,” in Annual Book of ASTM Standards (West Conshohocken, PA. http://www.astm.org/cgi-bin/resolver.cgi?C597-16.
ASTM-International (2015b). “ASTM C617/C617M-15, Standard Practice for Capping Cylindrical Concrete Specimens,” in Annual Book of ASTM Standards (West Conshohocken, PA. http://www.astm.org/cgi-bin/resolver.cgi?C617C617M-15.
ASTM-International (2018). “ASTM C805/C805M-18, Standard Test Method for Rebound Number of Hardened Concrete,” in Annual Book of ASTM Standards (West Conshohocken, PA. http://www.astm.org/cgi-bin/resolver.cgi?C805C805M-18.
ASTM-International (2019b). “ASTM D4791-19, Standard Test Method for Flat Particles, Elongated Particles, or Flat and Elongated Particles in Coarse Aggregate,” in Annual Book of ASTM Standards (West Conshohocken, PA. http://www.astm.org/cgi-bin/resolver.cgi?D4791-19.
Berry, R. (1991). Restored Concrete Centre Exhibits Unique Repairs. Int. J. Construction Maintenance Repair 5 (4), 36–39.
Bisby, L. A., Chen, J. F., Li, S. Q., Stratford, T. J., Cueva, N., and Crossling, K. (2011). Strengthening Fire-Damaged Concrete by Confinement with Fibre-Reinforced Polymer Wraps. Eng. Structures 33 (12), 3381–3391. doi:10.1016/j.engstruct.2011.07.002
Cai, Z., Liu, F., Yu, J., Yu, K., and Tian, L. (2021). Development of Ultra-high Ductility Engineered Cementitious Composites as a Novel and Resilient Fireproof Coating. Construction Building Mater. 288, 123090. doi:10.1016/j.conbuildmat.2021.123090
Chan, S. Y. N., Peng, G.-f., and Chan, J. K. W. (1996). Comparison between High Strength Concrete and Normal Strength Concrete Subjected to High Temperature. Mat. Struct. 29 (10), 616–619. doi:10.1007/bf02485969
Crook, D. N., and Murray, M. J. (1970). Regain of Strength after Firing of Concrete. Mag. Concrete Res. 22 (72), 149–154. doi:10.1680/macr.1970.22.72.149
Devadass, T. (2019). Experimental Study on Replacement of Fine Aggregate in Concrete with Dissimilar Curing Conditions. Case Stud. Construction Mater. 11, e00245. doi:10.1016/j.cscm.2019.e00245
Dilek, U. (2005). Evaluation of Fire Damage to a Precast Concrete Structure Nondestructive, Laboratory, and Load Testing. J. Perform. Constr. Facil. 19 (1), 42–48. doi:10.1061/(asce)0887-3828(2005)19:1(42)
Greepala, V., and Nimityongskul, P. (2008). Structural Integrity of Ferrocement Panels Exposed to Fire. Cement and Concrete Composites 30 (5), 419–430. doi:10.1016/j.cemconcomp.2007.08.007
Handoo, S. K., Agarwal, S., and Agarwal, S. K. (2002). Physicochemical, Mineralogical, and Morphological Characteristics of Concrete Exposed to Elevated Temperatures. Cement Concrete Res. 32 (7), 1009–1018. doi:10.1016/S0008-8846(01)00736-0
Henry, M., Darma, I. S., and Sugiyama, T. (2014). Analysis of the Effect of Heating and Re-curing on the Microstructure of High-Strength Concrete Using X-Ray CT. Construction Building Mater. 67, 37–46. doi:10.1016/j.conbuildmat.2013.11.007
Husem, M. (2006). The Effects of High Temperature on Compressive and Flexural Strengths of Ordinary and High-Performance Concrete. Fire Saf. J. 41 (2), 155–163. doi:10.1016/j.firesaf.2005.12.002
Industry, C. (2008). Assessment, Design and Repair of Fire-Damaged Concrete Structures. London, UK: The Concrete Society.
Ingham, J. P. (2007). “Assessment of Fire-Damaged Concrete and Masonry Structures, Evaluation and Repair of the Damage to Concrete,” in Special Publication SP-92 (Detroit, USA: American Concrete Institute).
Ingham, J. (2009). “Forensic Engineering of Fire-Damaged Structures,” in Proceedings of the Institution of Civil Engineers-Civil Engineering (Thomas Telford Ltd), 162, 12–17. doi:10.1680/cien.2009.162.5.12Proc. Inst. Civil Eng. - Civil Eng.
IS 2386 (1963). Method of Test for Aggregates for Concrete, Mechanical Properties, Part-4. New Delhi: Bureau of Indian Standards.
Jiang, C. J., Lu, Z. D., and Li, L. Z. (2017). Shear Performance of Fire-Damaged Reinforced Concrete Beams Repaired by a Bolted Side-Plating Technique. J. Struct. Eng. 143 (5), 4017007. doi:10.1061/(asce)st.1943-541x.0001726
Kai, X., Wang, G., Yu, J., and Lu, Z. (2011). “Flexural Strengthening of Fire-Damaged Reinforced Concrete Continuous T-Beams with CFRP Sheets,” in 2011 International Conference on Electric Technology and Civil Engineering (ICETCE) (IEEE), 372–379. doi:10.1109/icetce.2011.5774655
Khan, S., Yaqub, M., Noman, M., and Usman Rashid, M. (2020). “Experimental Research on Post-Fire Repair of RC T-Beams Using Method of Curing,” in 11th International Civil Engineering Conference (ICEC-2020) “Integrating Innovation and Sustainability in Civil Engineering” March 13-14, 2020, Karachi, Pakistan (Karachi, pakistan: ICEC), 238–246.
Khoury, G. A. (2000). Effect of Fire on Concrete and Concrete Structures. Prog. Struct. Engng Mater. 2 (4), 429–447. doi:10.1002/pse.51
Kodur, V. (20142014). Properties of Concrete at Elevated Temperatures. Int. Scholarly Res. Notices. doi:10.1155/2014/468510
Korsun, V. I., Vatin, N., Korsun, A., and Nemova, D. (2014). Physical-Mechanical Properties of the Modified Fine-Grained Concrete Subjected to Thermal Effects up to 200°С. Amm 633-634, 1013–1017. Trans Tech Publ. doi:10.4028/www.scientific.net/amm.633-634.1013
Korsun, V., and Baranov, A. (2020). “Mechanical Properties of High-Strength Concrete after Heating at Temperatures up to 400° C,” in International Scientific Conference on Energy, Environmental and Construction Engineering (Springer), 454–463.
Li, L., Shi, L., Wang, Q., Liu, Y., Dong, J., Zhang, H., et al. (2020). A Review on the Recovery of Fire-Damaged Concrete with Post-Fire-Curing. Construction Building Mater. 237, 117564. doi:10.1016/j.conbuildmat.2019.117564
Li, L. Z., Lo, S. H., and Su, R. K. L. (2013). Experimental Study of Moderately Reinforced Concrete Beams Strengthened with Bolted-Side Steel Plates. Adv. Struct. Eng. 16 (3), 499–516. doi:10.1260/1369-4332.16.3.499
Li, Q., Yuan, G., and Shu, Q. (2014). Effects of Heating/Cooling on Recovery of Strength and Carbonation Resistance of Fire-Damaged Concrete. Mag. Concrete Res. 66 (18), 925–936. doi:10.1680/macr.14.00029
Li, Z., Jiang, C. J., Jiang-Tao, Y., Wang, X., and Lu, Z. D. (2019). Flexural Performance of Fire-Damaged Reinforced Concrete Beams Repaired by Bolted Side-Plating. ACI Struct. J. 116 (3), 183–193. doi:10.14359/51712277
Lin, W. M., Lin, T. D., and Powers-Couche, L. J. (1996). Microstructures of Fire-Damaged Concrete. Mater. J. 93 (3), 199–205.
Ma, Q., Guo, R., Zhao, Z., Lin, Z., and He, K. (2015). Mechanical Properties of concrete at High Temperature-A Review. Construction Building Mater. 93, 371–383. doi:10.1016/j.conbuildmat.2015.05.131
Morales, E. M. (1991). “Rehabilitation of a Fire Damaged Building,” in Proceedings of ACI International Conference, Hong Kong.
Mostafaei, H., Vecchio, F. J., and Bénichou, N. (2009). “Seismic Resistance of Fire-Damaged Reinforced Concrete Columns,” in Improving the Seismic Performance of Existing Buildings and Other Structures (Reston, VA: American Society of Civil Engineers), 1396–1407. doi:10.1061/41084(364)128
Nene, R. L., and Kavle, P. S. (1991). Rehabilitation of a Fire Damaged Structure. Spec. Publ. 128, 1195–1212.
Noman, M., and Yaqub, M. (2021). Restoration of Dynamic Characteristics of RC T-Beams Exposed to Fire Using Post Fire Curing Technique. Eng. Structures 249 (July 2020), 113339. doi:10.1016/j.engstruct.2021.113339
Noumowe, A. N., Clastres, P., Debicki, G., and Costaz, J.-L. (1996). Transient Heating Effect on High Strength Concrete. Nucl. Eng. Des. 166 (1), 99–108. doi:10.1016/0029-5493(96)01235-6
Peng, G.-F., and Huang, Z.-S. (2008). Change in Microstructure of Hardened Cement Paste Subjected to Elevated Temperatures. Construction Building Mater. 22 (4), 593–599. doi:10.1016/j.conbuildmat.2006.11.002
Phanl, L. T. 2001. “Effects of Elevated Temperature Exposure on Heating Characteristics, Spailing, and Residual Properties of High Performance Concrete” 34 (March): 83–91. doi:10.1007/BF02481556
Poon, C.-S., Azhar, S., Anson, M., and Wong, Y.-L. (2001). Strength and Durability Recovery of Fire-Damaged Concrete after Post-Fire-Curing. Cement Concrete Res. 31 (9), 1307–1318. doi:10.1016/S0008-8846(01)00582-8
Roy, A. B. D., Sharma, U. K., and Bhargava, P. (2016). Confinement Strengthening of Heat-Damaged Reinforced Concrete Columns. Mag. Concrete Res. 68, 291–304. doi:10.1680/macr.15.00078
Sivagnanam, B. (2002). Damage Assessment and Rehabilitation of Concrete Structures: Three Case Studies. Indian Concrete J. 76 (12), 764–770.
Smart, S. A. S. (2006). “Fire Damage Assessment Using Non-destructive Site Techniques–Case Studies. Concrete Solutions,” in Proceedings of the 2nd International Conference, St Malo, FranceWatford, UK (St. Malo, France: BRE Press).
Srinivasan, P., Chellappan, A., and Annamalai, S. (2006). Pre-Evaluation of Fire-Affected RC Framed Structure and its Post-Evaluation by Load Test after Repair- A Case Study. J. Struct. Eng. 33 (5), 419–427.
Usman, M., Yaqub, M., Auzair, M., Khaliq, W., Noman, M., and Afaq, A. (2021). Restorability of Strength and Stiffness of Fire Damaged Concrete Using Various Composite Confinement Techniques. Construction Building Mater. 272 (February), 121984. doi:10.1016/j.conbuildmat.2020.121984
von Reden, T., Schüppel, D., and Schüppel, Denny. (2019). Developments toward Cost-Effective CFRP. Lightweight des worldw 12 (1), 60–63. doi:10.1007/s41777-018-0062-4
Wang, H. Y. (2008). The Effects of Elevated Temperature on Cement Paste Containing GGBFS. Cement and Concrete Composites 30 (10), 992–999. doi:10.1016/j.cemconcomp.2007.12.003
Xiao, J., and König, G. (2004). Study on concrete at High Temperature in China-an Overview. Fire Saf. J. 39 (1), 89–103. doi:10.1016/S0379-7112(03)00093-6
Xu, Y., Wong, Y. L., Poon, C. S., and Anson, M. (2001). Impact of High Temperature on PFA Concrete. Cement Concrete Res. 31 (7), 1065–1073. doi:10.1016/s0008-8846(01)00513-0
Xuan, D. X., and Shui, Z. H. (2011). Rehydration Activity of Hydrated Cement Paste Exposed to High Temperature. Fire Mater. 35 (7), 481–490. doi:10.1002/fam.1067
Yang, H., Lin, Y., Hsiao, C., and Liu, J.-Y. (2009). Evaluating Residual Compressive Strength of Concrete at Elevated Temperatures Using Ultrasonic Pulse Velocity. Fire Saf. J. 44 (1), 121–130. doi:10.1016/j.firesaf.2008.05.003
Yaqub, M. 2010. Axial Compressive and Seismic Shear Performance of Post-Heated Columns Repaired with Composite Materials Doctor of Philosophy 2010.The University of Manchester. Available at: https://www.escholar.manchester.ac.uk/uk-ac-man-scw:101698.
Yaqub, M., Bailey, C. G., Nedwell, P., Khan, Q. U. Z., and Javed, I. (2013). Strength and Stiffness of Post-Heated Columns Repaired with Ferrocement and Fibre Reinforced Polymer Jackets. Composites B: Eng. 44 (1), 200–211. doi:10.1016/j.compositesb.2012.05.041
Yaqub, M., and Bailey, C. G. (2011). Repair of Fire Damaged Circular Reinforced Concrete Columns with FRP Composites. Construction Building Mater. 25 (1), 359–370. doi:10.1016/j.conbuildmat.2010.06.017
Yu, K., Yu, J., Lu, Z., and Chen, Q. (2015). Determination of the Softening Curve and Fracture Toughness of High-Strength Concrete Exposed to High Temperature. Eng. Fracture Mech. 149, 156–169. doi:10.1016/j.engfracmech.2015.10.023
Yu, K., Yu, J., Lu, Z., and Chen, Q. (2016). Fracture Properties of High-Strength/High-Performance Concrete (HSC/HPC) Exposed to High Temperature. Mater. Structures 49 (11), 4517–4532.
Zhang, B., and Bicanic, N. (2002). Residual Fracture Toughness of Normal-and High-Strength Gravel Concrete after Heating to 600 C. Mater. J. 99 (3), 217–226.
Keywords: fire-damaged concrete, post-fire curing, low-cost repair, non-destructive testing, stiffness
Citation: Noman M, Yaqub M, Abid M, Musarat MA, Vatin NI and Usman M (2022) Effects of Low-Cost Repair Techniques on Restoration of Mechanical Properties of Fire-Damaged Concrete. Front. Mater. 8:801464. doi: 10.3389/fmats.2021.801464
Received: 25 October 2021; Accepted: 14 December 2021;
Published: 27 January 2022.
Edited by:
Kequan Yu, Tongji University, ChinaReviewed by:
Shuai Fang, South China University of Technology, ChinaCopyright © 2022 Noman, Yaqub, Abid, Musarat, Vatin and Usman. This is an open-access article distributed under the terms of the Creative Commons Attribution License (CC BY). The use, distribution or reproduction in other forums is permitted, provided the original author(s) and the copyright owner(s) are credited and that the original publication in this journal is cited, in accordance with accepted academic practice. No use, distribution or reproduction is permitted which does not comply with these terms.
*Correspondence: Muhammad Abid, YWJpZGtoZ0BocmJldS5lZHUuY24=
Disclaimer: All claims expressed in this article are solely those of the authors and do not necessarily represent those of their affiliated organizations, or those of the publisher, the editors and the reviewers. Any product that may be evaluated in this article or claim that may be made by its manufacturer is not guaranteed or endorsed by the publisher.
Research integrity at Frontiers
Learn more about the work of our research integrity team to safeguard the quality of each article we publish.