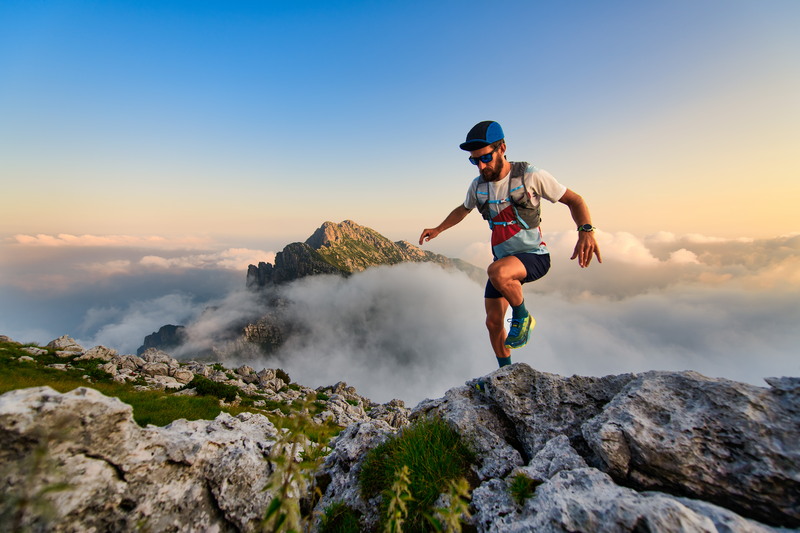
95% of researchers rate our articles as excellent or good
Learn more about the work of our research integrity team to safeguard the quality of each article we publish.
Find out more
ORIGINAL RESEARCH article
Front. Mater. , 28 January 2022
Sec. Mechanics of Materials
Volume 8 - 2021 | https://doi.org/10.3389/fmats.2021.778631
This article is part of the Research Topic 2022 Retrospective: Mechanics of Materials View all 7 articles
Copper–graphite sandwich composites are new functional composites with excellent tribological and mechanical properties. More and more researchers prepare the sandwich composites by accumulative roll-bonding processes due to severe plasticity deformation. The microstructure and properties of copper–graphite sandwich composites prepared by continual annealing and accumulative roll-bonding processes for eight rolling cycles were investigated. The results showed that with the increase of rolling cycles, the dispersion of graphite particles between two copper layers along a rolling direction became more uniform, the pores at the interface between graphite particles and the Cu matrix gradually disappeared, and the hardness of copper–graphite composites gradually increased. After eight rolling cycles, the Vickers hardness of the composites increased by 140.8% as compared with that of annealed pure copper. During friction, the steel balls can meet some graphite particles in the composites rolled by four cycles. The friction coefficient and wear loss of copper–graphite composites gradually decreased with the increase of rolling cycles. Compared with the composites rolled by one cycle, the friction coefficient and wear loss of the composites rolled by eight cycles were reduced by 32.5 and 49.0%, respectively. The main wear mechanism gradually evolved from fatigue wear and abrasive wear to adhesive wear, and then to fatigue wear.
Copper–graphite composites (CGCs) have attracted much attention in recent years. Due to their excellent thermal and electrical conductivity and significant friction and wear properties, CGCs have been widely used as electrical brush and bearing materials in many fields (Wang et al., 2017a; Zhang et al., 2019a; Xu et al., 2019). The wettability between graphite and copper is poor, and the bonding between the two phases is rather weak, which reduces the mechanical and electrical properties of CGCs (Zhou et al., 2019; Cui et al., 2020; Zhu et al., 2020). Accordingly, many researchers have been committed to improving the interfacial bonding between graphite particles and the copper matrix (Jiang et al., 2018; Sun et al., 2021; Wang et al., 2021). Nowadays, a popular method is to coat a certain metal on the surface of graphite particles, such as Cu, Ni, or Cu and Ni (Liu et al., 2014; Wang et al., 2017b; Chen et al., 2017; Yuan et al., 2020). The metal coating can effectively improve the bonding interface between graphite particles and the copper matrix, but it is difficult to control the uniformity and amount of coating on the surface of graphite particles (Wang and Liang, 2011; Shanaghi et al., 2013). Moreover, the metal coating is a kind of complex process that always includes plating pretreatment (activation, sensitization, etc.), plating, and post-cleaning. Therefore, in order to simplify the process and achieve similar effects, some researchers have also tried to dope some metal elements during ball milling, such as Ti (Zhang et al., 2017), Cr (Ren et al., 2018), and Zr (Zhang et al., 2019b), whereas the doping process is not economical because the milling time is long. At the same time, in order to form a close combination between graphite particles and the copper matrix, some researchers have tried to apply some pressure or heat to them. In recent years, several new processes have also been derived, such as HPS (hot pressured sintering), HIP (hot isostatic pressing), and SPS (spark plasma sintering). Ren et al. (2016) found that a high sintering temperature can reduce these pores at the interface between graphite flakes and the copper matrix during vacuum hot-pressing sintering. Wang et al. (2020) studied the effects of pressure and holding time on the interfacial bonding for diamond–copper composites through SPS and found that high pressure was conducive to strengthening the interface bonding. Generally, the pressure value in an HIP process is higher than that in other processes. For example, Kovacik et al. (2015) prepared CGCs by the HIP process under an argon pressure of 150 MPa. Some other researchers formed CGCs by using HPS or SPS at about 40 Mpa (Zhu et al., 2016; Nie et al., 2020). Although these processes can improve the bonding interface to some extent, the pressure exerted on these sintered samples is very limited to prevent the deformation of mold at high temperature. Therefore, in these processes, the deformation degree of copper particles is not enough to make them completely welded together. However, as a severe plastic deformation process, accumulative roll bonding (ARB) has been widely used to prepare some composites reinforced by second-phase particles, such as Cu/Al2O3 (Jamaati and Toroghinejad, 2010a), Al/Al2O3 (Jamaati and Toroghinejad, 2010b; Alizadeh and Salahinejad, 2015), Al/SiC (Alizadeh and Paydar, 2009; Jamaati et al., 2011; Hosseini et al., 2013), and Al/B4C (Yazdani et al., 2011; Alizadeh and Paydar, 2012; Yaghtin et al., 2012). Some reports showed that during the ARB process, the bonding interface can be improved between second-phase particles and metal matrix, and these particles did not agglomerate together; instead, they distributed uniformly in the matrix (Liu et al., 2012; Khoramkhorshid et al., 2016). Jamaati and Toroghinejad (2010b) found that after seven rolling cycles, the interface bonding between Al2O3 particles and the Cu matrix was still weak, and there were a lot of pores in the second-phase particle clusters. When the number of rolling cycles increased to nine, these pores decreased gradually or even disappeared and the bonding became stronger. Therefore, the interfacial bonding between second-phase particles and matrix can be improved through the ARB process. However, for the CGC prepared by ARB process, there are few reports about the bonding interface between graphite particles and the Cu matrix at different rolling cycles.
Excellent friction and wear performance is one of the important characteristics of metal matrix composites. So far, many researchers have studied the friction and wear properties of some composites prepared by ARB. For example, Darmiani et al. (2013) found that for Al/SiC composites prepared by ARB, their friction coefficient and wear loss were lower than those of pure aluminum and could be reduced by increasing the number of rolling cycles. Liu et al. (2013) also obtained a similar result for Al/WC composites prepared by using the ARB process, that is, as the number of rolling cycles increased, the wear loss was reduced. However, there has not been any report on the friction and wear properties for these copper–graphite sandwich composites prepared by ARB.
In this work, the purpose was to investigate the dispersion of graphite particles between two copper layers during the ARB process and the bonding interface between graphite particles and the copper matrix under different rolling cycles and then to introduce the friction and wear performance of copper–graphite sandwich composites for the first time.
The raw materials in this work contain pure copper plates (purity 99.95%, Jiangxi Copper Industry Co., Ltd., Nanchang, China), with a thickness of 1.0 mm, and natural graphite flakes (purity 99.9%, average particle size 25 μm; Nanjing Xianfeng Nano Material Technology Co., Ltd., Nanjing, China). The plates were cut into strips of 60 mm length and 30 mm width, and then annealed at 600°C for 2 h in argon atmosphere.
ARB includes the following steps: 1) cleaning the annealed copper strips. The grease on their surfaces was eliminated by ultrasonic wave in acetone for 10 min; 2) removing the oxide scale on their surfaces by using hydrochloric acid; 3) polishing these surfaces to a fresh Cu matrix with a steel wire brush; 4) smearing a certain amount of graphite particles to the surfaces (about 0.3 vol.%); 5) rolling more than 50% reduction by a two-roller mill (roller diameter, 200 mm) at a rolling speed of 0.5 m/min (the relationship between rolling cycles, plate thickness, layer number, and layer thickness is shown in Table 1); 6) annealing these rolled samples at 550°C for 1 h in argon atmosphere, and then cutting off at the middle of them, and repeating these above steps. The schematic route of the ARB process is shown in Figure 1. Graphite particles were added only in the first rolling cycle. In order to avoid the oxidization of those fresh copper surfaces after polishing, the whole process from surface treatment to rolling was completed within 100 s. A total of eight cycles was performed, and the number of cycles was recorded as N.
TABLE 1. The relationship between rolling cycle and layer number, plate thickness, and layer thickness.
The rolling direction–transverse direction (RD-TD) surface and rolling direction–normal direction (RD-ND) surface of composites were polished with different mesh sandpapers, and then the RD-ND surface was etched by using the solution [FeCl3 (5 g) + HCl (10 g) + H2O (100 ml)]. The distribution of graphite particles in the Cu matrix on the RD-TD surface was obtained by a metallographic microscope (AXIO SCOPE A1). The bonding states between different Cu layers, graphite particles, and the Cu matrix were observed by a field-emission scanning electron microscope (SEM) (FEI MLA650F). The energy-dispersive spectrometer attached with the SEM was used to analyze the distribution of Cu and C elements at the interface between graphite particles and the Cu matrix. The high magnification morphology and selected area electronic diffraction (SAED) of the composites after eight rolling cycles were observed by a transmission electron microscope (FEI TALOS F200X). The specimens for TEM observation were sliced from bulk materials, ground into thin foils about 200 μm thickness, and punched into circular foils with a diameter of 3 mm. These foils were electropolished in a twin-jet electro-polisher and then ion-thinned in an ion-milling machine. The electrolytic polishing solution consisted of 35 vol.% HNO3 and 65 vol.% C2H5OH. The working voltage and temperature were 40 V and −35°C, respectively.
A high-speed reciprocating friction and wear tester (MFT-R4000) was used to measure the friction coefficient (load 20 N, frequency 5 HZ, wear scar length 5 mm, test time 20 min). The GCr15 steel balls with a diameter of 5 mm were used as friction pairs. Before a wear test, the surfaces of these samples needed mechanical polishing with sandpapers. The depth of wear scars was obtained by a three-dimensional profiler (NanoMap 500LS), and the morphologies of these worn surfaces were observed by an SEM (FEI MLA650F). Wear loss was calculated by the bulk density formula (the density of composites was taken as 8.9 g/cm3). A Vickers hardness tester (HVS-5) was used to measure the hardness of composites (testing load 0.2 kg, holding time 10 s, measuring seven times, and averaging), and these samples tested in this research were not annealed after rolling.
Figure 2 expresses the distribution of graphite particles on the RD-TD surface between two copper layers of copper–graphite sandwich composites for different rolling cycles. After the fourth rolling cycle, most graphite particles did not distribute uniformly; instead, they agglomerated together (red arrows in Figure 2A). The reason may be that these graphite particles could not be uniformly smeared on the surface of copper strips before rolling, and some particles moved forward along the rolling direction due to their good lubrication performance during rolling, resulting in their agglomeration. After seven rolling cycles, the distribution of graphite particles was very uniform (Figure 2B). Some similar results were also obtained when Ghaderi et al. (2013) and Jamaati and Toroghinejad (2010b) prepared a kind of particle-reinforced composites by the ARB method. These second-phase particles could be uniformly distributed after six rolling cycles. There are two reasons for this phenomenon. Firstly, with the increase of rolling cycles, the number of copper layers increases, which reduces the thickness of these graphite flakes and improves their distribution (Yao et al., 2016). Secondly, these graphite clusters would decompose under shear stress during rolling, and the injection of metal matrix into these graphite clusters would promote their dispersion under the normal direction pressure of rollers [26] (Alizadeh and Salahinejad, 2015). Some tiny Cu grains (white arrows in Figure 2A) can be found in graphite clusters. During the next rolling cycles, the Cu grains will deform and separate these graphite particles in the clusters.
FIGURE 2. Distribution of graphite particles on RD-TD surface: (A) four cycles and (B) seven cycles.
The morphologies of the RD-ND surface of copper–graphite sandwich composite samples rolled by different cycles are given in Figure 3. In order to observe the bonding interface, these samples were etched by the solution [FeCl3 (5 g) + HCl (10 g) + H2O (100 ml)]. After one rolling cycle, the interface bonding between two copper strips was very weak, and only a few positions were welded together (arrows in Figure 3). With the increase of rolling cycle number, the cumulative deformation of composites became more and more severe. After four rolling cycles, the bonding quality between two adjacent copper layers was obviously improved. The thickness of copper layers reached a very small value after seven cycles, about 3.0 μm (Table 1). It can also be found that the bonding quality was further improved. Some graphite particles were intermittently distributed, and a part of the copper layers showed a kind of wave shape (arrows in Figures 3B,E) due to uneven plastic deformation. Besides, some graphite particles were broken up and became thinner (arrows in Figure 3E). According to the film theory, some thin brittle oxides on the surface of two metal layers would crack under rolling pressure and some fresh metals would be exposed and combined with each other under high strain energy (Vaidyanath et al., 1959; Mohamed and Washburn, 1975). In this experiment, graphite particles would hinder the contact of these fresh copper points from two adjacent layers and reduce the bonding quality at the first rolling cycle. With the increase of rolling cycles, the bonding quality is improved because the pores at the interface gradually disappear under large plastic deformation (Jamaati and Toroghinejad, 2010a). In addition, the continual annealing could enhance the deformation capacity of metal matrix, making some fresh metals easily exposed and welded together (Ghaderi et al., 2013).
FIGURE 3. SEM images of samples rolled by different cycles: (A) one cycle, (B) local amplification of sample rolled by one cycle, (C) four cycles, (D) seven cycles, and (E) local amplification of sample rolled by seven cycles.
Figure 4 further shows the three different states of these interfaces between graphite particles and the copper matrix on the RD-TD surface, revealing a change of the bonding interface during the ARB process. After two rolling cycles, the bonding quality was poor. There were some continuous pores at the interface (arrows in Figure 4A), which separated these graphite particles from the matrix. After four rolling cycles, these pores at the interface were significantly reduced and the bonding interface was improved (arrows in Figure 4B). As the number of rolling cycles increased to six, the graphite particles were tightly combined with the matrix and these pores almost disappeared. At the initial rolling cycles, it is difficult to completely embed these soft graphite particles into the copper matrix due to a small deformation degree, resulting in some pores at the interface between graphite particles and the copper matrix. The annealing after each rolling would soften the copper matrix and enhance its mobility. During the next rolling cycles, the soft copper matrix would move and fill these pores, thereby improving the bonding interface (Jamaati and Toroghinejad, 2010a). During the subsequent repeated rolling process, these pores gradually decreased or even disappeared, and a good bonding interface was finally achieved, as shown in Figure 4C. From the distribution of C and Cu elements in Figures 4D,E, it can be seen that there was a transition zone of Cu and C at the interface, which indicates that the interface bonding was very tight. After eight rolling cycles, these graphite particles were closely connected with the copper matrix. Additionally, some tiny graphite particles can also be found (arrow in Figure 4F).
FIGURE 4. The bonding interface between graphite particles and Cu matrix after different rolling cycles and the distribution of C and Cu elements: (A) two cycles, (B) four cycles, and (C) six cycles. (D) (E) The distribution of Cu and C elements in samples by six cycles and (F) eight cycles.
The high-magnification morphologies of graphite particles on the RD-TD surface of samples rolled by eight rolling cycles are presented in Figure 5. It can be found that these graphite particles were uniformly distributed in the copper matrix in granular shape and their average size was about 10 nm (Figure 5A). Figure 5B displays the typical SAED patterns of Cu and C phases, which proves the existence of graphite particles. However, due to the relatively low graphite content, the brightness of graphite diffraction spots was not very prominent.
FIGURE 5. TEM image of RD-TD surface and SEAD pattern at eight cycles: (A) high-magnification morphologies of graphite particles and (B) SEAD pattern.
Figure 6 shows the relationship between the Vickers hardness, rolling strain, and rolling cycles of CGCs. After one rolling cycle, the hardness value of CGCs significantly increased due to strain hardening, which was 2.1 times that of annealed pure copper. Then, the hardness value showed a relatively slow increase during these subsequent rolling cycles. After eight rolling cycles, the hardness value of the composites increases by 140.8% as compared with that of annealed pure copper. The reasons for these results can be listed as follows. First of all, some graphite particles in the copper matrix can inhibit the growth of these recrystallized grains during annealing after each rolling, and thus some fine recrystallized grains will occur. Their grain boundaries will hinder the movement of dislocations, which may lead to an increasing value of hardness. Secondly, the more the rolling cycles, the more uniform the distribution of graphite particles. The dispersion strengthening effect from the pining of dislocations and the hindering of their movement will be improved with the increase of the number of rolling cycles (Toroghinegad et al., 2014). Then, these pores between graphite particles and the Cu matrix almost disappear after several rolling cycles, which will be beneficial in increasing hardness. In addition, there is a little higher increase of hardness at the fifth rolling cycle due to a larger rolling strain. Some literatures (Jang et al., 2008; Shaarbaf and Toroghinegad, 2008) reported that the hardness of these composites did not always increase with the increase of the ARB cycles but would reach a stable state after a certain number of cycles due to the equilibrium between the hardening from strain and fine grain and the softening from dynamic recovery and recrystallization. In addition, the interface between layers hinders the propagation of dislocations and thus enhances hardness.
Figure 7 presents the wear scar depth of composites under different rolling cycles and the surface state of the specimens rolled by four cycles. The sliding distance of steel ball was 5 mm during friction. It can be seen that the wear depth decreased with the increase of rolling cycles. After one rolling cycle (the first step was finished in Figure 1), the depth was about 60 um, far less than the copper layer thickness (450 μm, in Table 1). Therefore, the steel ball could not contact these graphite particles in the composites, which also means that the friction occurred on pure copper. For these composites rolled by four cycles, the scar depth was reduced to about 50 μm, approximate to the layer thickness (40 μm). Therefore, the steel ball may have met some graphite particles during the friction process, such as point 1 in Figure 7B. After seven and eight rolling cycles, these depths were both above 40 μm and much higher than the thickness of copper layers (Table 1). The steel ball would touch many small graphite particles, and these composites showed a better wear resistance after seven rolling cycles (Figure 7C). Moreover, the wear scar of the composites after eight rolling cycles became shallow due to high hardness (Figure 6). Therefore, graphite particles and high hardness are helpful to improve the friction properties of the composites (Rajkumar and Aravindan, 2013; Larionova et al., 2014).
FIGURE 7. Wear depth, wear surface image, and friction schematic diagram: (A) wear depth, (B) wear surface morphology for the sample rolled by four cycles, and (C) friction schematic diagram for the samples rolled by different cycles.
The friction coefficient of these copper graphite composites rolled by different cycles is depicted in Figure 8. The friction coefficient decreased with the increase of rolling cycles, indicating that their friction performance improved gradually. For the copper–graphite sandwich composites rolled by one cycle, the friction coefficient was about 0.4. Due to the thick copper layer, the steel balls cannot contact these graphite particles during the friction process (Figure 7A), thus bringing about a relatively high friction coefficient. After four rolling cycles, the friction coefficient of composites decreased from 0.40 to 0.36. The steel balls would meet a few graphite particles with good lubricating property, which was beneficial to reduce the friction coefficient. After seven rolling cycles, the friction coefficient of composites was about 0.30. The steel balls would penetrate at least 10 layers of the copper matrix (Table 1 and Figure 7A) and contact many fine graphite particles. Moreover, the composites with high hardness have a high deformation resistance, which can improve their friction performance. The friction of composites rolled by eight cycles was further reduced to about 0.27, which was 32.5% lower than that of the first cycle, showing a better friction property. After several rolling cycles, there is a good combination between graphite particles and the copper matrix. When the bonding is poor, some graphite particles will be separated from the friction surface and cannot produce a lubricating effect. With the increase of rolling cycles, the interfacial bonding becomes stronger and stronger, and these graphite particles become smaller and smaller, which is conducive to the formation of a lubricating film and the decrease of friction coefficient during the friction process.
Figure 9 shows the wear loss of composites during the friction process under a 20 N load. The wear loss showed the same tendency as the wear depth, decreasing with the increase of rolling cycles. The wear loss was 17.77 * 10−4g for the composites rolled by one cycle. After four rolling cycles, the loss decreased by 24.5% and was about 13.41 * 10−4g. The composites rolled by four cycles had a higher hardness and a lower friction coefficient than those composites rolled by one cycle, which could reduce the wear loss. Moreover, with the increase of rolling cycles, the bonding quality between the Cu layer and the Cu layer, graphite particles, and Cu layer was improved, which enhanced the deformation resistance of composites and reduced their wear loss. Compared with the composites rolled by one cycle, the wear loss of these composites rolled by eight cycles were reduced by 49.0%.
The worn surface morphologies for these composites rolled by different rolling cycles are shown in Figure 10. It can be seen that the worn surface of the composites rolled by one cycle mainly contained some cracks, grooves, wear debris, and small spalling pits. When the pressure from steel balls was higher than the stress limit of copper, these cracks would occur and propagate in the copper layers. After a period of friction, some metal chips would fall off from these cracks and became wear debris due to fatigue wear. Additionally, the reciprocal motion of these balls adhered by a few debris would produce some grooves. Therefore, the wear mechanism was fatigue wear and abrasive wear. For the composites after four rolling cycles, their surface presented different topography. The grooves disappeared, and there were some obvious delaminated layers on the worn surface of the composites. The moving steel ball was close to the interface between two copper layers (Table 1 and Figure 7A), resulting in these delaminated layers under the action of friction heat and pressure. Further, their edges were flipped up due to the adhesion of steel balls (see Figure 10B), indicating that the main wear mechanism was adhesive wear. At the same time, some graphite particles, about 30 μm, could be found on the worn surface. The amount of the graphite particles was small, about 0.3%, and even some particles stuck on the surface of the steel ball would drop off after a short period of friction. For these composites rolled by seven and eight cycles, there were some obvious spalling pits and cracks on their wear surfaces, but their wear loss was less than that of the first rolling cycle (Figure 9). The interface bonding of the composites rolled by several cycles became strong, preventing these spalled particles from falling off. After a certain time of friction, the cracks would become longer and the spalling pits turned larger. The wear mechanism was fatigue wear. Therefore, it can be seen that with the increase of rolling cycles, the wear mechanism evolves from fatigue wear and abrasive wear to adhesive wear, and then to fatigue wear.
FIGURE 10. Worn surface morphologies of the composites rolled by different cycles: (A) one cycle, (B) four cycles, (C) seven cycles, and (D)) eight cycles.
1) Cu–graphite sandwich composites with a uniform dispersion of graphite particles between two copper layers can be prepared by the ARB process. With the increase of rolling cycles, the dispersion of graphite particles between two copper layers was improved, and the bonding interface with the copper matrix was improved.
2) The distribution of graphite particles and the rolling strain affect the Vickers hardness of CGCs. After eight rolling cycles, the hardness of the composite was 140.8% higher than that of annealed pure copper.
3) During friction, the steel balls can meet some graphite particles in the composite rolled by four cycles. Due to the lubrication of the graphite particles, the friction coefficient of the composites gradually decrease with the increase of rolling cycles.
4) With the increase of rolling cycles, the wear loss of the sandwich composites gradually decreases, and the wear mechanism evolves from fatigue wear and abrasive wear to adhesive wear and then to fatigue wear. The sandwich composites rolled by eight cycles show good wear resistance.
The raw data supporting the conclusion of this article will be made available by the authors, without undue reservation.
JL is the main contributor to this manuscript for methodology, investigation, formal analysis, writing, original draft, and editing. YD and WC carried out some experiments about the rolling of copper–graphite composites. LZ, XX, and JZ designed the experimental scheme and modified the manuscript. KS, SS, LG, JR, and ZS did some works about the preparation of raw materials, investigation, and experimental data curation.
This work was supported by the National Natural Science Foundation of China (No. 51761013, 52001146, and 51561008), the Education department of Jiangxi Province (No. GJJ160605, GJJ200811) and the Projects in Science and Technique Plans of Ningbo City (No. 2019B10083).
Author WC was employed by the company DongLiang Aluminum Co. Ltd.
The remaining authors declare that the research was conducted in the absence of any commercial or financial relationships that could be construed as a potential conflict of interest.
All claims expressed in this article are solely those of the authors and do not necessarily represent those of their affiliated organizations, or those of the publisher, the editors and the reviewers. Any product that may be evaluated in this article, or claim that may be made by its manufacturer, is not guaranteed or endorsed by the publisher.
The authors thank Weibin Xie and Huiming Chen from the National Copper Melting and Processing Engineering Center for their suggestion about experiment scheme. We are grateful to Yuyan Wu for her language help and valuable discussion.
Alizadeh, M., and Paydar, M. H. (2009). Fabrication of Al/SiCP Composite Strips by Repeated Roll-Bonding (RRB) Process. J. Alloys Compd. 477, 811–816. doi:10.1016/j.jallcom.2008.10.151
Alizadeh, M., and Paydar, M. H. (2012). High-strength Nanostructured Al/B4C Composite Processed by Cross-Roll Accumulative Roll Bonding. Mater. Sci. Eng. A 538, 14–19. doi:10.1016/j.msea.2011.12.101
Alizadeh, M., and Salahinejad, E. (2015). A Comparative Study on Metal-Matrix Composites Fabricated by Conventional and Cross Accumulative Roll-Bonding Processes. J. Alloys Compd. 620, 180–184. doi:10.1016/j.jallcom.2014.08.249
Chen, J., Ren, S., He, X., and Qu, X. (2017). Properties and Microstructure of Nickel-Coated Graphite Flakes/copper Composites Fabricated by Spark Plasma Sintering. Carbon 121, 25–34. doi:10.1016/j.carbon.2017.05.082
Cui, Q., Chen, C., Yu, C., Lu, T., Long, H., Yan, S., et al. (2020). Effect of Molybdenum Particles on thermal and Mechanical Properties of Graphite Flake/copper Composites. Carbon 161, 169–180. doi:10.1016/j.carbon.2020.01.059
Darmiani, E., Danaee, I., Golozar, M. A., Toroghinejad, M. R., Ashrafi, A., and Ahmadi, A. (2013). Reciprocating Wear Resistance of Al-SiC Nano-Composite Fabricated by Accumulative Roll Bonding Process. Mater. Des. 50, 497–502. doi:10.1016/j.matdes.2013.03.047
Ghaderi, O., Toroghinejad, M. R., and Najafizadeh, A. (2013). Investigation of Microstructure and Mechanical Properties of Cu-SiCP Composite Produced by Continual Annealing and Roll-Bonding Process. Mater. Sci. Eng. A 565, 243–249. doi:10.1016/j.msea.2012.11.004
Hosseini, M., Yazdani, A., and Danesh Manesh, H. (2013). Al 5083/SiCp Composites Produced by Continual Annealing and Roll-Bonding. Mater. Sci. Eng. A 585, 415–421. doi:10.1016/j.msea.2013.07.077
Jamaati, R., Amirkhanlou, S., Toroghinejad, M. R., and Niroumand, B. (2011). CAR Process: A Technique for Significant Enhancement of As-Cast MMC Properties. Mater. Characterization 62, 1228–1234. doi:10.1016/j.matchar.2011.10.008
Jamaati, R., and Toroghinejad, M. R. (2010a). Application of ARB Process for Manufacturing High-Strength, Finely Dispersed and Highly Uniform Cu/Al2O3 Composite. Mater. Sci. Eng. A 527, 7430–7435. doi:10.1016/j.msea.2010.08.038
Jamaati, R., and Toroghinejad, M. R. (2010b). Manufacturing of High-Strength Aluminum/alumina Composite by Accumulative Roll Bonding. Mater. Sci. Eng. A 527, 4146–4151. doi:10.1016/j.msea.2010.03.070
Jang, Y., Kim, S., Han, S., Lim, C., and Goto, M. (2008). Tensile Behavior of Commercially Pure Copper Sheet Fabricated by 2- and 3-Layered Accumulative Roll Bonding (ARB) Process. Met. Mater. -Int. 14, 171–175. doi:10.3365/met.mat.2008.04.171
Jiang, X., Fang, H. C., Xiao, P., Liu, T., Zhu, J. M., Wang, Y. C., et al. (2018). Influence of Carbon Coating with Phenolic Resin in Natural Graphite on the Microstructures and Properties of Graphite/copper Composites. J. Alloys Compd. 744, 165–173. doi:10.1016/j.jallcom.2018.02.051
Khoramkhorshid, S., Alizadeh, M., Taghvaei, A. H., and Scudino, S. (2016). Microstructure and Mechanical Properties of Al-Based Metal Matrix Composites Reinforced with Al 84 Gd 6 Ni 7 Co 3 Glassy Particles Produced by Accumulative Roll Bonding. Mater. Des. 90, 137–144. doi:10.1016/j.matdes.2015.10.063
Kováčik, J., Emmer, Š., and Bielek, J. (2015). Thermal Conductivity of Cu-Graphite Composites. Int. J. Therm. Sci. 90, 298–302. doi:10.1016/j.ijthermalsci.2014.12.017
Larionova, T., Koltsova, T., Fadin, Y., and Tolochko, O. (2014). Friction and Wear of Copper-Carbon Nanofibers Compact Composites Prepared by Chemical Vapor Deposition. wear 319, 118–122. doi:10.1016/j.wear.2014.07.020
Liu, C. Y., Wang, Q., Jia, Y. Z., Zhang, B., Jing, R., Ma, M. Z., et al. (2012). Effect of W Particles on the Properties of Accumulatively Roll-Bonded Al/W Composites. Mater. Sci. Eng. A 547, 120–124. doi:10.1016/j.msea.2012.03.095
Liu, C. Y., Wang, Q., Jia, Y. Z., Zhang, B., Jing, R., Ma, M. Z., et al. (2013). Evaluation of Mechanical Properties of 1060-Al Reinforced with WC Particles via Warm Accumulative Roll Bonding Process. Mater. Des. 43, 367–372. doi:10.1016/j.matdes.2012.07.019
Liu, Q., He, X.-B., Ren, S.-B., Zhang, C., Ting-Ting, L., and Qu, X.-H. (2014). Thermophysical Properties and Microstructure of Graphite Flake/copper Composites Processed by Electroless Copper Coating. J. Alloys Compd. 587, 255–259. doi:10.1016/j.jallcom.2013.09.207
Mohamed, H. A., and Washburn, J. (1975). Mechanism of Solid State Pressure Welding. Weld. J. 54, 302–310.
Nie, Q., Wei, X., Qin, X., Huang, Y., Chen, G., Yang, L., et al. (2020). Microstructure and Properties of Graphite nanoflakes/Cu Matrix Composites Fabricated by Pressureless Sintering and Subsequent Thermo-Mechanical Treatment. Diamond Relat. Mater. 108, 107948. doi:10.1016/j.diamond.2020.107948
Rajkumar, K., and Aravindan, S. (2013). Tribological Behavior of Microwave Processed Copper-Nanographite Composites. Tribology Int. 57, 282–296. doi:10.1016/j.triboint.2012.06.023
Ren, S., Chen, J., He, X., and Qu, X. (2018). Effect of Matrix-Alloying-Element Chromium on the Microstructure and Properties of Graphite Flakes/copper Composites Fabricated by Hot Pressing Sintering. Carbon 127, 412–423. doi:10.1016/j.carbon.2017.11.033
Ren, S., Xu, H., Chen, J., and Qu, X. (2016). Effects of Sintering Process on Microstructure and Properties of Flake graphite-diamond/copper Composites. Mater. Manufacturing Process. 31, 1377–1383. doi:10.1080/10426914.2015.1103865
Shaarbaf, M., and Toroghinejad, M. R. (2008). Nano-grained Copper Strip Produced by Accumulative Roll Bonding Process. Mater. Sci. Eng. A 473, 28–33. doi:10.1016/j.msea.2007.03.065
Shanaghi, A., Chu, P. K., Xu, R., and Hu, T. (2013). Structure and Properties of TiC/Ti Coatings Fabricated on NiTi by Plasma Immersion Ion Implantation and Deposition. Vacuum 89, 238–243. doi:10.1016/j.vacuum.2012.05.023
Sun, H., Deng, N., Li, J., He, G., and Li, J. (2021). Highly thermal-conductive Graphite flake/Cu Composites Prepared by Sintering Intermittently Electroplated Core-Shell Powders. J. Mater. Sci. Tech. 61, 93–99. doi:10.1016/j.jmst.2020.05.044
Toroghinejad, M. R., Jamaati, R., Nooryan, A., and Edris, H. (2014). The Effect of Alumina Content on the Mechanical Properties of Hybrid Composites Fabricated by ARB Process. Ceramics Int. 40, 10489–10498. doi:10.1016/j.ceramint.2014.03.020
Vaidyanath, L. R., Nicholas, M. G., and Milner, D. R. (1959). Pressure Welding by Rolling. Br. Weld. J. 6, 13–28.
Wang, C., Li, H., Chen, M., Li, Z., and Tang, L. (2020). Microstructure and Thermo-Physical Properties of Cu Ti Double-Layer Coated diamond/Cu Composites Fabricated by Spark Plasma Sintering. Diamond Relat. Mater. 109, 108041. doi:10.1016/j.diamond.2020.108041
Wang, Q., Chen, M., Shan, Z., Sui, C., Zhang, L., Zhu, S., et al. (2017a). Comparative Study of Mechanical and Wear Behavior of Cu/WS 2 Composites Fabricated by Spark Plasma Sintering and Hot Pressing. J. Mater. Sci. Tech. 33, 1416–1423. doi:10.1016/j.jmst.2017.06.014
Wang, Q. X., and Liang, S. H. (2011). Investigation on Preparation and Diffusion Barrier Properties of W-Ti Thin Films. Vacuum 85, 979–985. doi:10.1016/j.vacuum.2010.12.012
Wang, Y., Gao, Y., Li, Y., Zhang, C., Sun, L., and Zhai, W. (2017b). Research on Nickel Modified graphite/Cu Composites Interface. Surf. Coat. Tech. 328, 70–79. doi:10.1016/j.surfcoat.2017.08.036
Wang, Z., Xu, L., Peng, J., Tang, Z., Han, Z., and Liu, J. (2021). Effect of the Microstructure and Properties of Graphite/copper Composites Fabricated by Microwave Sintering. J. Mater. Sci. 56, 9183–9195. doi:10.1007/s10853-021-05891-5
Xu, E., Huang, J., Li, Y., Zhu, Z., Cheng, M., Li, D., et al. (2019). Graphite Cluster/copper-Based Powder Metallurgy Composite for Pantograph Slider with Well-Behaved Mechanical and Wear Performance. Powder Tech. 344, 551–560. doi:10.1016/j.powtec.2018.12.059
Yaghtin, A. H., Salahinejad, E., and Khosravifard, A. (2012). Processing of Nanostructured Metallic Matrix Composites by a Modified Accumulative Roll Bonding Method with Structural and Mechanical Considerations. Int. J. Miner Metall. Mater. 19, 951–956. doi:10.1007/s12613-012-0653-8
Yao, G. C., Mei, Q. S., Li, J. Y., Li, C. L., Ma, Y., Chen, F., et al. (2016). Cu/C Composites with a Good Combination of Hardness and Electrical Conductivity Fabricated from Cu and Graphite by Accumulative Roll-Bonding. Mater. Des. 110, 124–129. doi:10.1016/j.matdes.2016.07.129
Yazdani, A., Salahinejad, E., Moradgholi, J., and Hosseini, M. (2011). A New Consideration on Reinforcement Distribution in the Different Planes of Nanostructured Metal Matrix Composite Sheets Prepared by Accumulative Roll Bonding (ARB). J. Alloys Compd. 509, 9562–9564. doi:10.1016/j.jallcom.2011.07.084
Yuan, Y., Gan, X., Lai, Y., Zhao, Q., and Zhou, K. (2020). Microstructure and Properties of Graphite/copper Composites Fabricated with Cu-Ni Double-Layer Coated Graphite Powders. Compos. Inter. 27, 449–463. doi:10.1080/09276440.2019.1644051
Zhang, P., Zhang, L., Wei, D., Wu, P., Cao, J., Shijia, C., et al. (2019a). Effect of Graphite Type on the Contact Plateaus and Friction Properties of Copper-Based Friction Material for High-Speed Railway Train. Wear 432-433, 202927. doi:10.1016/j.wear.2019.202927
Zhang, R., He, X., Chen, H., and Qu, X. (2019b). Effect of Alloying Element Zr on the Microstructure and Properties of Graphite flake/Cu Composites Fabricated by Vacuum Hot Pressing. J. Alloys Compd. 770, 267–275. doi:10.1016/j.jallcom.2018.08.107
Zhang, R., He, X., Chen, Z., and Qu, X. (2017). Influence of Ti Content on the Microstructure and Properties of Graphite flake/Cu-Ti Composites Fabricated by Vacuum Hot Pressing. Vacuum 141, 265–271. doi:10.1016/j.vacuum.2017.04.026
Zhou, X., Chen, L., Cao, H., Yu, J., Qiu, G., and Wang, L. (2019). Effects of Emulsified Asphalt on the Mechanical and Tribological Properties of Copper/graphite Composites. Mater. Res. Express 6, 056515–056516. doi:10.1088/2053-1591/aafeb7
Zhu, L., Yi, M., Wang, L., and Chen, S. (2020). Effects of Foam Copper on the Mechanical Properties and Tribological Properties of Graphite/copper Composites. Tribology Int. 148, 106164. doi:10.1016/j.triboint.2020.106164
Keywords: copper–graphite sandwich composites, accumulative roll bonding, the bonding interface, graphite particle distribution, friction coefficient, wear mechanism
Citation: Liu J, Ding Y, Sun K, Zeng L, Xiao X, Cao W, Guan L, Ran J, Sun Z, Shi S and Zhang J (2022) The Bonding Interface and Tribological Properties of Cu–Graphite Sandwich Composites Fabricated via Accumulative Roll-Bonding Processes. Front. Mater. 8:778631. doi: 10.3389/fmats.2021.778631
Received: 17 September 2021; Accepted: 08 December 2021;
Published: 28 January 2022.
Edited by:
Thomas Lohner, Technical University of Munich, GermanyReviewed by:
Jitendra Kumar Katiyar, SRM Institute of Science and Technology, IndiaCopyright © 2022 Liu, Ding, Sun, Zeng, Xiao, Cao, Guan, Ran, Sun, Shi and Zhang. This is an open-access article distributed under the terms of the Creative Commons Attribution License (CC BY). The use, distribution or reproduction in other forums is permitted, provided the original author(s) and the copyright owner(s) are credited and that the original publication in this journal is cited, in accordance with accepted academic practice. No use, distribution or reproduction is permitted which does not comply with these terms.
*Correspondence: Jinping Liu, bGl1amlucGluZ0BqeHVzdC5lZHUuY24=
Disclaimer: All claims expressed in this article are solely those of the authors and do not necessarily represent those of their affiliated organizations, or those of the publisher, the editors and the reviewers. Any product that may be evaluated in this article or claim that may be made by its manufacturer is not guaranteed or endorsed by the publisher.
Research integrity at Frontiers
Learn more about the work of our research integrity team to safeguard the quality of each article we publish.