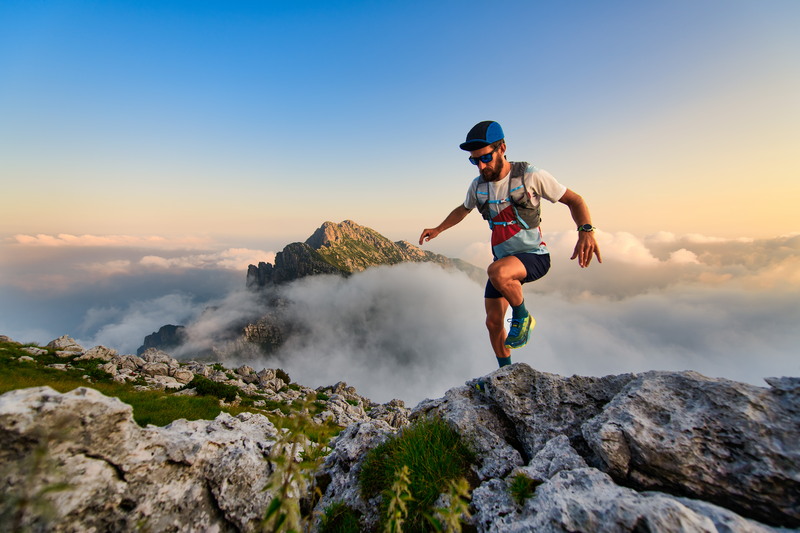
94% of researchers rate our articles as excellent or good
Learn more about the work of our research integrity team to safeguard the quality of each article we publish.
Find out more
ORIGINAL RESEARCH article
Front. Mater. , 19 November 2021
Sec. Polymeric and Composite Materials
Volume 8 - 2021 | https://doi.org/10.3389/fmats.2021.770150
In this paper, recycled cellulose diacetate (rCDA) derived from cigarette butts was used as a fiber stabilizer to develop stone mastic asphalt (SMA) mixtures. The characterizations of rCDA were investigated by scanning electron microcopy (SEM), a Fourier transform infrared spectrometer (FTIR), and a thermogravimetric analyzer (TGA). Volumetric stability, temperature stability, moisture stability, and fatigue performance of SMA mixtures with rCDA were tested to obtain the pavement performance. Results showed that rCDA appeared to have a tough surface texture with a curly and corrugated structure, which facilitated the enhancement of the cohesion bond with the asphalt binder. TG-DTG indicated that the maximum weight loss (62.48%) obtained at temperatures ranging from 294.1°C to 376.0°C was due to decomposition and degradation of organic matters. When 0.4% rCDA was used in the asphalt mixture, the dynamic stability was 4,105 cycles/mm. The ultimate flexural strength and flexural stiffness modulus were 3,722 MPa and 9.7 MPa. It indicated that the temperature stability of 0.4% rCDA was superior to 0.3% polyacrylonitrile fiber (PAN), while inferior to 0.3% polyester (PET). The value of tensile strength ratio and residual Marshall stability were 80.2 and 75.3%, respectively. The fatigue life of 0.4% rCDA was technically like that of 0.3% PAN and 0.3% PET at lower stress levels. All results concluded that the optimum content of rCDA in asphalt mixtures was 0.4% by mass of the binder.
Cigarette butts (CBs) are the most common littered objects which are generally found everywhere in public places (Rebischung et al., 2018). CBs are regarded as a source of contaminants as trapped toxic substances from wasted cigarette filters and smoked tobacco are leached into the ecological system (Mohajerani et al., 2016). Generally, CBs contain unburned tobacco, filter, ash, and wrap paper. Most cigarette filters are made of cellulose diacetate which is hardly biodegradable, resulting in long-term and persistent environmental impacts (Dobaradaran et al., 2019). Nowadays, discarded cigarette butts are one of the biggest solid wastes produced worldwide every year. It is estimated that more than 1 million tons of CBs is discarded as litter worldwide every year and this is expected to increase by more than 50% due to an increase in the world population (Mohajerani et al., 2016). This is leading to a new waste stream which has drawn much attention to the treatment and reuse of CBs due to the high rate of cigarette production and consumption.
Many studies have focused on leaching toxic substances such as polycyclic aromatic hydrocarbons (PAHs), metals, and other organic matters released from CBs which may cause serious damage to the surrounding environment (A et al., 2009; Lee et al., 2011; Dobaradaran et al., 2019). As known, separately collecting CBs is very difficult and expensive, resulting in large quantities of CBs existing in the environment for a long time as contaminated sources (Torkashvand et al., 2020). Fortunately, by enhancing regulation and education, discarding CBs in public areas has been controlled, which makes it possible to collect and reuse them as a resource with the aim of reduction. Efforts have been made to obtain more environmentally respectful products and provide some different uses for CBs. Wasted cigarette filters play a key role in recycling CBs. Cigarette filters have been reported as carbon precursors in the production of a low-cost adsorbent for removal of nitrosamines (Li et al., 2019) and as a sound porous absorber (Wong et al., 2015; Maderuelo-Sanz et al., 2018). Cigarette filters consist of cellulose diacetate, which potentially enables them to be transformed into other cellulose products such as cellulose pulp (Maria et al., 2017), films, membranes, and fibers (Abu-Danso et al., 2019; Liu et al., 2019). A different practical proposal has been investigated on recycling CBs in fired clay bricks (Mohajerani et al., 2016) and as aggregate in asphalt mixtures (Mohajerani et al., 2017). However, it is expected that acetate groups and pollutants in filters are two main barriers in the transformation of cellulose diacetate into functional materials. On the other hand, directly reusing cigarette filters or CBs in concrete or building materials hardly shows the value of cellulose diacetate. Several studies reported that waste cellulose diacetate can be used as raw materials or additives in the reproduction of fresh cigarette filters or electrostatic spinning by adding surfactants for eliminating glycerol triacetate. A cellulose pulp production process from used cigarette filters has been developed by employing alkaline pulping. This regenerated cellulose has been used in the paper industry. So far, it is expensive and complicated which certainly affects the industrial application and quality of products. Hence, a novel and easy method which is environmentally friendly and valuable for reutilization of recycled cellulose diacetate (rCDA) from cigarette filters is of great importance in the recycling of CBs.
A stone mastic asphalt (SMA) mixture with gap-graded aggregate gradations and a higher binder content is widely used in asphalt pavement construction. Mineral or organic fibers play important roles to overcome bleeding from the asphalt binder and increase the stiffness and resistance of mixtures against performance failure (Ameri et al., 2017). Organic fibers used in SMA contain polyester and polyacrylonitrile fibers which are expensive and synthetized from complicated chemical processes. rCDA from CBs has the potential to be a substitute for these chemical fibers in the production of SMA mixtures. Additionally, cellulose diacetate is a type of thermoplastic resin with a porous membrane structure which can avoid asphalt binder “drain down” from SMA mixtures due to a higher adsorptive rate for the free asphalt binder. Research has been done on physico-mechanical properties of asphalt concrete incorporated with encapsulated CBs. A whole cigarette butt was encapsulated and used as a kind of aggregate in a hot asphalt mixture (Mohajerani et al., 2017). However, a study on recycling and reuse of waste cellulose diacetate from CBs as fiber-stabilized and reinforced materials in a stone mastic asphalt mixture has not been done yet.
The objective of this work is to reuse rCDA from discarded CBs to produce an SMA mixture. The recycled cellulose diacetate was characterized for its physiochemical and morphological properties. Finally, the effects of rCDA on properties of asphalt mortar and mixtures were discussed.
CBs were collected from cigarette butt collectors located in the airport, train stations, restaurants, bars, and buildings in Wuhan city, China. The original CBs contain waste cigarette filters, remaining tobacco, ash, and wrapping papers. The CBs were disinfected and dried at 105°C for 24 h in an oven. After separating unburned tobacco and ash, the cigarette filters were obtained by stripping the wrapping papers and then stored in sealed plastic bags. Polyester and polyacrylonitrile fiber were purchased from a local supplier. A styrene butadiene styrene block co-polymers (SBS, type YH-791)-modified asphalt binder was prepared by mixing a modifier with 60/80 pen grade asphalt (Baoli Asphalt Co., Ltd., China). Basalt and limestone were selected as the coarse and fine aggregates. Grounded limestone powder was selected as the mineral filler. The main physical properties of the pavement construction materials are referred to in our previous publications.
To fulfill the technical requirements for fibers in the SMA mixture, several treatments such as de-esterification, scattering, separation, and drying were performed in the production of waste cellulose diacetate fiber (Figure 1). In detail, a de-esterification solution consisting of 1:1:1 (v/v) ethanol (99.5 vol%), tetrachloroethylene, and NaOH solution (1 mol/L) was used to remove the glycerol triacetate from waste cellulose diacetate. A certain amount of waste cellulose diacetate was split into clusters by a low-speed shear device and put into the de-esterification solution with magnetic stirring for 2 h at room temperature. After the reaction, the mixtures were taken out and beaten for 10 min within a Valley beater after being washed to neutralize them. It was noted that this procedure assured the mixtures were broken up by the blades in the machine and impacted to a net-structure shape instead of small pieces. Then the mixtures were removed from the solution and dehydrated for 3 min within a tubular dehydrator. After being dried for 2 h at 80°C, the recycled cellulose diacetate fiber was stored in a sealed container for the subsequent experiments.
FIGURE 1. A schematic diagram for reutilization of waste cigarette butts (CFs, cigarette filters; CDAs, cellulose diacetates).
General properties such as diameter, density, tenacity, and elongation at break of rCDA were determined according to the relative Chinese standard, and are listed in Table 1. The surface structure of recycled cellulose diacetate fiber was analyzed by scanning electron microscopy (SEMS-520, Hitachi, Japan) as well as its morphology in asphalt mastics. Functional cellulose groups were determined by Fourier transform infrared (FTIR) spectra (IRTracer-100, Shimadzu, Japan) with the wavenumber range 4,000–400 cm-1 at room temperature. Thermal gravimetric analysis was performed with an integrated thermal analyzer (Netzsch, STA 449 F3, Germany). The heating rate was set as 10°C/min. The input gas was composed of 21% oxygen and 79% nitrogen by volume, and the gas flow rate was 100 ml/min which was high enough to sweep the gaseous products to keep the experimental gas environment constant.
Asphalt mortar containing various fibers was prepared by a high-speed shearing device. Figure 2 presents the aggregate gradation with a nominal maximum aggregate size of 13.2 mm. The content of the mineral filler was 10% by weight of the total mixture. Except specimens for the drain down and particle loss tests, similar asphalt content (6.0%) and aggregate gradation were used for preparation of all specimens in order to evaluate the effect of fibers on mixtures. The content of rCDA accounted for 0.3, 0.4, and 0.5% by weight of the asphalt mixtures. The rCDA was directly used in all test samples. The content of polyester and polyacrylonitrile was 0.3% by weight of the asphalt mixtures by reviewing the literature of SMA mixture practices. The SMA mixture was designed and prepared based on the Marshall methodology in accordance with the Standard Test Methods of Bitumen and Bituminous Mixtures for High Way Engineering (JTG E20-2011). The recycled cellulose diacetate, polyester, and polyacrylonitrile fiber are referred to as rCDA, PET, and PAN in brief. Test samples were recorded as 0.3% rCDA, 0.4% rCDA, 0.5% rCDA, 0.3% PET, and 0.3% PAN according to the content and fiber type used in the mixtures.
To evaluate the high-temperature performance of the asphalt mortar containing fibers, a dynamic shear rheological test (JTG E20 T0628) and a binder leakage stability test were conducted. The method for the latter was defined as follows. The asphalt binder was heated to 140°C, then fibers were added and mixed for 3 min at 150°C. A certain amount of asphalt mortar was put into a net-shaped basket and weighted at 130°C. The weight loss was recorded. The fibers to asphalt binder ratio was 1:10 for these two tests.
The drain down test was performed to evaluate the free asphalt binder in the mixtures according to JTG E20 T0732. The Cantabro loss particle test was carried out to assess the mechanical property of mixtures containing fiber according to JTG E20 T0733. To evaluate the pavement performance of SMA mixtures, tests for Marshall stability, rutting, low-temperature bending, moisture susceptibility, and fatigue were carried out in accordance with JTG E20 T0709, T0719, T0715, T0729, and T0739, respectively.
Figures 3A,B show the typical morphologies of the surface structure of rCDA fibers. A curly and corrugated structure with approximate rough texture which contributed to the adhesive property between fibers and asphalt could be observed from the SEM images. Compared with the fresh cellulose acetate, the irregular structures might be due to the effect of erosion by the de-esterification solution during removal of the glycerol triacetate from waste cellulose diacetate. This difference would lead to a higher asphalt absorption rate when designing and preparing the asphalt mixtures containing rCDA (Slebi-Acevedo et al., 2019). It concluded that no visible cracks, holes, and hollows in the structure were found, indicating that the morphologies of rCDA were similar to synthetic fibers. Besides, no cross-section structure was observed, which makes it very different to lignin fibers, resulting in a reduction of the absorbing and retaining ability for the asphalt binder (Li et al., 2020).
FIGURE 3. Characterization for rCDA by (A) SEM image (×200), (B) SEM image (×1,500), (C) FTIR, and (D) TG-DTG.
The infrared spectra for the rCDA fiber are shown in Figure 3C. A strong peak at 3,485 cm−1 was classified as O–H stretching vibration and the hydrogen bond of the hydroxyl. It may be due to the merging of the atmospheric water and hydroxyl groups, and the first stage of the TG technique proved the existence of water. The peak at 2,945 cm−1 was associated with the stretching vibration of the C–H bond from aliphatic CH and CH2. The peak at 1755 cm−1 was related to the stretching vibration of carbonyl C=O from carboxylate ester compounds. The peak at 1,639 cm−1 was related to the C=C bond. The peaks at 1,375 cm−1 and 1,047 cm−1 were contributed to the bending vibration of the C–H or C–O bond from aromatic compounds. The peak at 1,236 cm−1 corresponded to the stretching vibration of the C–O bond of ester linkage of the acetyl group.
The thermogravimetric (TG) and differential thermogravimetric (DTG) analysis curves of rCDA are presented in Figure 3D. Three stages can be observed from the TG curve. The first stage occurs from 89.3°C to 294.1°C with a weight loss of 14.47%, which was related to the water loss of the rCDA and the release of small molecule volatile organic matters (Lambat et al., 2019; Zhou et al., 2019; Khedkar et al., 2020; Chopra et al., 2021). The second stage whose temperature is below 376.0°C had a weight loss of 62.48%, which was related to the decomposition and degradation of fixed carbon. The final stage had a weight loss of 23.05% which was mainly due to the thermal condensation reaction in rCDA (Chaudhary et al., 2016). As seen from the DTG curve, the peak of the maximum weight loss rate of the rCDA fiber appeared in this temperature range.
The rutting and fatigue factors of the asphalt mortar with different fibers are presented in Figure 4. The rutting factor was used to evaluate the high-temperature performance of asphalt mortar. Data of complex modules and phase angle at four temperature points were collected and calculated for determination of G*/Sinδ. It was concluded that better high-temperature performance was related to a higher value of G*/Sinδ (Tao et al., 2019). In this work, PET mortar exhibited the highest rutting factor at different temperatures. The rutting factors of rCDA mortar at different temperatures were higher than that of asphalt without fibers, indicating that the addition of rCDA increased the resistance ability of asphalt at higher temperatures. It was concluded that rheological properties can be improved with the addition of fibers in the asphalt binder. This might be due to the absorption of the light components of the binder into fibers, resulting in an increase of the viscosity and reduction in the cone sink depth during the DSR test (Slebi-Acevedo et al., 2019). However, the rutting factor of asphalt mortar with rCDA was obviously lower than that of PET and PAN under similar fiber content, which might indicate that fibers with higher tensile strength, such as PET and PAN, can lead to higher viscosities and shear resistances with respect to binders with rCDA fibers (Chen and Xu, 2010). On the other hand, the rCDA exhibited a rather curly antenna tip, which limited the generation of a bond between the asphalt and the fiber and led to the propagation of cracks when compared to PET and PAN (Mohammed et al., 2018).
In order to investigate the macroscopic high-temperature stability of asphalt with fibers. The test for the stability of asphalt binder leakage at 130°C was conducted and results are listed in Table 2. Due to a higher content of fibers in the asphalt mortar, the mass loss after the test was lower than 30%. The mass loss of rCDA asphalt mortar accounted for 28.2%, which was significantly higher than that of the PET and PAN mortars. This might be due to the heterogeneous characteristic of rCDA and weak adsorptive or/and absorptive ability of asphalt components, leading to a lower cohesion bond and higher fluidity of the mortar, which consequently resulted in a higher mass loss rate. Although the rheological properties and high-temperature stability of the rCDA mortar were inferior to PET and PAN mortars. Addition of rCDA had a positive effect on the modification of the original asphalt binder. It was necessary to make sure that the effect of dosage of rCDA improved the volumetric and pavement performance of asphalt mixtures.
Bulk density, percentage of air voids in asphalt mixtures (VV), percentage of voids in mineral aggregate in asphalt mixtures (VMA), and Marshall stability were measured, and the test results are listed in Table 3. It indicated that 4.0 of VV was obtained in 0.3% PET indicated that 6.0% is the optimum asphalt content for the SMA mixture with PET. Under similar asphalt content, VV slightly increased in the order of 0.3% PET, 0.3% PAN, and 0.3% rCDA. Increasing the content of rCDA from 0.3 to 0.5%, the bulk density and VFA of specimens decreased, while VV increased. All test specimens were prepared with similar asphalt content. High specific density materials such as aggregates were substituted by fibers, resulting in a decrease of the bulk density and increase of VV and VMA. Additionally, fibers with different length, shape, and orientation had effects on the volumetric properties of mixtures. The Marshall stability of 0.3% rCDA accounted for 8.5 kN, which was lower than that of 0.3% PET and 0.3% PAN. Increasing the content of rCDA, the Marshall stability reached 10.5 kN, then dramatically decreased to 7.8 kN when the content of rCDA was 0.5%. It was noted that the stability of 0.4% rCDA was higher than that of 0.3% PAN, indicating that the rCDA had optimum content in preparation of SMA mixtures due to improvement of the ability to resist the deformation under vertical load. Increasing the content of rCDA led to an increase of VV due to excess fibers, resulting in a decrease of Marshall stability by lower resistance to deformation. In this work, 0.4% rCDA in mixtures led to a greater bearing capacity of specimens by preventing relative slippage between the joint surfaces of the aggregate and rCDA-reinforced asphalt binder (Yin and Wu, 2018). It indicated that both the higher fluidity of 0.3% rCDA (bleeding of binders) and the worse compaction characteristics of 0.5% rCDA (lacking of binders) led to the reduction of Marshall stability. However, these volumetric properties were measured under similar asphalt content, indicating the indexes of mixtures with rCDA could be improved by its optimum asphalt content. Consequently, the asphalt content would significantly increase, resulting in an increase of costs.
TABLE 3. Marshall test results for the volumetric properties of specimens with asphalt content of 6.0%.
The drain down test results for the asphalt mixtures are listed in Table 4. It was evident that almost all the fibers provided significant stabilization of the mixtures due to the drain down of mixtures less than 0.3%, which proved all fibers were performing their function as stabilizing additives in the asphalt mixtures. The drain down value of rCDA asphalt mixtures decreased from 0.18 to 0.12% when the asphalt content was 6.0%. A high rCDA fiber to binder ratio restricted the fluidity of mixtures by combining with more asphalt binder when asphalt content was at a lower level. For comparison, mixtures with different fibers at their respective optimum asphalt content were prepared. Except for the 0.3% PET mixture, all drain down values increased due to an increase of asphalt content. The drain down of rCDA mixtures increased from 0.15 to 0.35% with increasing rCDA content from 0.3 to 0.5%. The drain down of 0.3% rCDA decreased as its optimum asphalt content was less than 6.0%. The drain down of 0.5% rCDA significantly increased, indicating that the effect of increasing asphalt content on drain down was of great importance compared to increasing rCDA content. The drain down increment of 0.4% rCDA was 26.7%, which was significantly lower than that of 0.5% rCDA, implying that higher content of rCDA might result in early damage of the asphalt mixtures. On the other hand, although the drain down of 0.3% rCDA decreased, a smaller asphalt content might influence the durable performance, such as low-temperature cracking resistance. Hence, 0.4% rCDA was moderate in the SMA mixture at the optimum asphalt content.
Table 4 presents the results concerning the particle loss of specimens subjected to Los Angeles abrasion under dry conditions. Similarly, the particle (mass) loss of rCDA specimens was higher than that of 0.3% PET and 0.3% PAN specimens at both the constant asphalt content and optimum asphalt content. When the asphalt content was 6.0%, the mass loss of rCDA specimens significantly increased from 11.5 to 15.9% with increasing fiber content from 0.3 to 0.5%. When prepared with its optimum asphalt content, the mass loss increased from 10.6 to 11.8%. This might contribute to the better impact resistance ability of specimens at the optimum asphalt content. Specimens at 6.0% asphalt content were found to be loose and less compacted, resulting in higher mass loss. On the other hand, increasing asphalt content led to lower VV of specimens, and aggregates tightly bonded with the fiber-reinforced asphalt binder when mixtures were cooling down. Hence, the particle loss of specimens decreased when it was subjected to impact.
The high-temperature stability of asphalt mixtures is usually evaluated by dynamic stability and rutting depth. The rutting test results are presented in Figure 5A. The 0.3% PET exhibited the highest dynamic stability and the smallest rut depth followed by the 0.4% rCDA, 0.3% PAN, 0.3% rCDA, and 0.5% rCDA, respectively. It is worth noting that the dynamic stability of 0.4% rCDA (4,105 cycles/mm) was slightly higher than that of 0.3% PAN (3,985 cycles/mm). The rutting depth of 0.4% rCDA accounted for 2.6 mm, which was lower than that of 0.3% PAN (2.8 mm). Although higher content of rCDA fiber led to higher VV of the Marshall specimen, the rutting test specimen was far bigger and made the fiber well-separated in mixtures for formation of stiffer mixtures, resulting in better stabilization of the asphalt binder on the specimen’s surface making it able to resist permanent deformation at a temperature of 60°C. Besides, increasing the content of rCDA fiber from 0.3 to 0.4% enhanced the skeleton structure to resist the shear force and reduce the fluidity by limiting aggregates from moving in the asphalt matrix (Chen and Xu, 2010; Yin and Wu, 2018). When the content of the rCDA fiber reached 0.5% in mixtures at the same asphalt content, the excess fiber exhibited a negative effect on the resistance of deformation due to weak bonding between the asphalt binder and aggregates. By the effect of wheel track, the dynamic stability dramatically decreased with an increase of rutting depth. However, it is necessary to understand the effect of rCDA fiber on the anti-deformation ability of mixtures by adjusting the asphalt content and aggregate gradation in further investigations.
FIGURE 5. Experimental results for asphalt mixtures with different fibers, (A) high-temperature stability, (B) low-temperature performance, (C) moisture sensibility, and (D) fatigue performance.
In this work, low-temperature cracking resistance of the fiber-reinforced asphalt mixture was evaluated according to a three-point flexural test at the temperature of 10°C below zero. The ultimate flexural strength and flexural stiffness modulus are presented in Figure 5B. The changing rule of ability to low-temperature cracking resistance of SMA mixtures with different fibers were like its high-temperature deformation resistance ability. The ultimate flexural strength and flexural stiffness modulus of 0.4% rCDA accounted for 3,722 MPa and 9.7 MPa, which were slightly higher than that of 0.3% PAN. It was concluded that the improvement of low-temperature cracking resistance of fiber-reinforced asphalt mixtures depended on the retarding effect of fibers on the crack propagation in the asphalt matrix. Figure 1 shows that the shape of the rCDA fiber was like a net structure. It was found that the waste cellulose diacetate was extracted by regeneration solvent and recycled as separate fibers, instead of “thinning” the cigarette filter. The rCDA fibers still consisted of tows which enhanced the tensile strength due to combination of lots of single fibers in a small area. This might contribute to the improvement of ability in low-temperature cracking resistance of rCDA mixtures. Hence, the crack propagation was gradually weakened and terminated until the expansion energy was depleted due to cumulated fracture energy of net-structure and bonded rCDA fiber. When the content of rCDA was 0.5%, it led to damage on the surface of specimen due to the excess unbonded fibers. The crack propagation along this damage continuously expanded, resulting in the lower ultimate flexural strength and flexural stiffness modulus of specimens.
Freezing-thaw splitting and the immersion Marshall test were performed to evaluate the moisture sensibility of SMA mixtures. The results of tensile strength ratio (TSR) and residual Marshall stability (RS) are presented in Figure 5C. The value of TSR and RS of 0.3% PET reached 85.2 and 83.1%, respectively. Compared with 0.3% PAN, 0.4% rCDA slightly decreased the TSR and RS from 81.4 to 80.2%–78.1 and 75.3%, respectively. Concurrently, the TSR and RS of 0.3% rCDA and 0.5% rCDA were below 75%, indicating that all rCDA mixtures exhibited a worse anti-moisture damage ability. It is known that loss of cohesion of the asphalt film and the failure of the adhesion between the aggregate and asphalt binder are the main mechanisms to interpret the moisture damage of asphalt mixtures (Luo et al., 2019). In this work, the rCDA fiber bonded with the sticky binder on its surface and decreased the asphalt film thickness around the aggregate. Moisture easily penetrated rCDA asphalt mixtures through the cracks and stripped particles on the specimen surface, which led to most of the distress and the failure of mixtures when rCDA asphalt mixtures were subjected to freezing-thaw or moisture immersion conditions.
The fatigue life of fiber-reinforced asphalt mixtures was evaluated by a three-point bending beam fatigue test at a temperature of 15°C with a loading frequency of 10 Hz. The fatigue life under stress control mode was calculated by Eq. 1 as follows:
Where
The relationship between
It is of great importance that smoking does severe harm to health. Quitting smoking is beneficial to health and the environment. However, we must face the reality that 2.4 trillion filter cigarettes are smoked each year; of these, an estimated 500 billion CBs are littered in China. Almost all waste filters in CBs are made of cellulose diacetate. Recycling the waste cellulose diacetate not only solves environmental problems, but also recovers fiber products as substitutes for valuable materials in the industry. This work aims to reutilize cellulose diacetate recycled from CBs in SMA mixtures. Problems that we met as well as its prospects are summarized as follows.
Costs. CBs are rather light and are scattered almost everywhere. Separation of residual tobacco and wrapping paper from filters is difficult. Regeneration of cellulose diacetate consumes valuable solvent and energy. It makes the cost of reutilization expensive. Substitution of PET or PAN fiber in SMA mixtures depends on the final cost when mixtures meet the technical requirements.
Performance. Poor moisture sensibility and fatigue performance currently hinder reusing recycled cellulose diacetate in asphalt mixtures. Improvements such as regeneration techniques of fibers and modification and optimization of asphalt mixtures need to be investigated in detail.
Environment. Secondary pollution in the regeneration and reutilization process of waste cellulose diacetate should be noticed. It is necessary to consider treatment of these regenerants and contaminants from these processes. Moreover, analysis of life cycle assessment would be required.
In this study, the characteristics of asphalt mortars and mixtures with rCDA were investigated. By de-esterification, scattering, separation, and drying treatments, rCDA fibers with a length of 19 mm, average diameter of 10.5 mm, density of 1.06 g/cm3, tenacity of 45.8 MPa, and elongation at break of 8.24% were prepared for production of SMA mixtures. The rCDA appeared to have a tough surface texture with a curly and corrugated structure which facilitated the enhancement of the cohesion bond with the asphalt binder. TG-DTG indicated that the thermal stability of rCDA can be divided into three stages. The maximum weight loss (62.48%) was obtained at the second stage with temperatures ranging from 294.1°C to 376.0°C. While the maximum weight loss rate was obtained in the final stage with the temperature below 550°C. The optimum content of rCDA was 0.4% which was denoted by the mass of the asphalt binder with incorporated high-temperature stability, the dynamic shear rheological test, and the drain down and Cantabro loss particle tests. For mixtures with 0.4% rCDA, the high-temperature stability and low-temperature cracking performance of SMA mixtures was slightly higher than that of 0.3% PAN mixtures, while lower than that of 0.3% PET mixtures. The moisture sensibility of 0.4% rCDA was obviously inferior to that of both 0.3% PET and 0.3% PAN mixtures. The fatigue life of 0.4% rCDA was technically like that of 0.3% PAN and 0.3% PET at lower stress levels. Although rCDA asphalt mixtures can meet some technical requirements by Chinese standards, the factors of cost, performance, and environment impact of asphalt mixtures containing recycled waste cellulose diacetate fibers should be taken into consideration in further investigations Moriwaki et al., 2009.
The raw data supporting the conclusions of this article will be made available by the authors, without undue reservation.
Conceptualization, Methodology and Data curation and analysis, HL; Project administration and Resources, YC; Writing – review & editing, YX.
Author HL and YC were employed by the China Tobacco Hubei Industrial Limited Liability Company.
The remaining author declares that the research was conducted in the absence of any commercial or financial relationships that could be construed as a potential conflict of interest.
All claims expressed in this article are solely those of the authors and do not necessarily represent those of their affiliated organizations, or those of the publisher, the editors and the reviewers. Any product that may be evaluated in this article, or claim that may be made by its manufacturer, is not guaranteed or endorsed by the publisher.
Abu-Danso, E., Bagheri, A., and Bhatnagar, A. (2019). Facile Functionalization of Cellulose from Discarded Cigarette Butts for the Removal of Diclofenac Pharmaceutical from Water. Carbohydr. Polym. 219, 46–55. doi:10.1016/j.carbpol.2019.04.090
Ameri, M., Mohammadi, R., Vamegh, M., Molayem, M. J. C., and Materials, B. (2017). Evaluation the Effects of Nanoclay on Permanent Deformation Behavior of Stone mastic Asphalt Mixtures. Construction Building Mater. 156, 107–113. doi:10.1016/j.conbuildmat.2017.07.055
Chaudhary, R. G., Ali, P., Gandhare, N. V., Tanna, J. A., and Juneja, H. D. (2016). Thermal Decomposition Kinetics of Some Transition Metal Coordination Polymers of Fumaroyl Bis (Paramethoxyphenylcarbamide) Using DTG/DTA Techniques. Arabian J. Chem. 12, 1070–1082. doi:10.1016/j.arabjc.2016.03.008
Chen, H., and Xu, Q. (2010). Experimental Study of Fibers in Stabilizing and Reinforcing Asphalt Binder. Fuel 89, 1616–1622. doi:10.1016/j.fuel.2009.08.020
Chopra, P. K. P. G., Lambat, T. L., Mahmood, S. H., Chaudhary, R. G., and Banerjee, S. (2021). Sulfamic Acid as Versatile Green Catalyst Used for Synthetic Organic Chemistry: A Comprehensive Update. CHEMISTRYSELECT 6, 6867–6889. doi:10.1002/slct.202101635
Dobaradaran, S., Schmidt, T. C., Lorenzo-Parodi, N., Jochmann, M. A., Nabipour, I., Raeisi, A., et al. (2019). Cigarette Butts: An Overlooked Source of PAHs in the Environment. Environ. Pollut. 249, 932–939. doi:10.1016/j.envpol.2019.03.097
Khedkar, M. V., Khan, S. R., Lambat, T. L., Chaudhary, R. G., and Abdala, A. A. (2020). CO Surrogates: A Green Alternative in Palladium-Catalyzed CO Gas Free Carbonylation Reactions. Curr. Org. Chem. 24, 2588–2600. doi:10.2174/1385272824999200622115655
Lambat, T. L., Chaudhary, R. G., Abdala, A. A., Mishra, R. K., H. Mahmood, S., and Banerjee, S. (2019). Mesoporous PbO Nanoparticle-Catalyzed Synthesis of Arylbenzodioxy Xanthenedione Scaffolds under Solvent-free Conditions in a ball Mill. RSC Adv. 9, 31683–31690. doi:10.1039/c9ra05903b
Lee, H.-L., Hsieh, D. P. H., and Li, L.-A. (2011). Polycyclic Aromatic Hydrocarbons in Cigarette Sidestream Smoke Particulates from a Taiwanese Brand and Their Carcinogenic Relevance. Chemosphere 82, 477–482. doi:10.1016/j.chemosphere.2010.09.045
Li, S. H., Shi, C. L., Wang, Y. Z., Sun, X. D., Qi, D. W., Wu, D., et al. (2019). New Efficient Selective Adsorbent of Tobacco Specific Nitrosamines Derived from Discarded Cigarette Filters. Microporous Mesoporous Mater. 284, 393–402. doi:10.1016/j.micromeso.2019.04.060
Li, Y.-T., Li, D., Lai, L.-J., and Li, Y.-H. (2020). Remediation of Petroleum Hydrocarbon Contaminated Soil by Using Activated Persulfate with Ultrasound and ultrasound/Fe. Chemosphere 238, 124657. doi:10.1016/j.chemosphere.2019.124657
Liu, W., Cui, M., Shen, Y., Zhu, G., Luo, L., Li, M., et al. (2019). Waste Cigarette Filter as Nanofibrous Membranes for On-Demand Immiscible Oil/water Mixtures and Emulsions Separation. J. Colloid Interf. Sci. 549, 114–122. doi:10.1016/j.jcis.2019.04.057
Luo, D., Khater, A., Yue, Y., Abdelsalam, M., Zhang, Z., Li, Y., et al. (2019). The Performance of Asphalt Mixtures Modified with Lignin Fiber and Glass Fiber: A Review. Construction Building Mater. 209, 377–387. doi:10.1016/j.conbuildmat.2019.03.126
Maderuelo-Sanz, R., Gómez Escobar, V., and Meneses-Rodríguez, J. M. (2018). Potential Use of Cigarette Filters as Sound Porous Absorber. Appl. Acoust. 129, 86–91. doi:10.1016/j.apacoust.2017.07.011
Maria, B. T., Duarte, M. A. B., Raposo Garcez, L., Camargo Rubim, J., Hofmann Gatti, T., and Suarez, P. Anselmo. Ziani. (2017). Process Development for Cigarette Butts Recycling into Cellulose Pulp. Waste Manage. 60, 140–150. doi:10.1016/j.wasman.2016.10.013
Mohajerani, A., Kadir, A. A., and Larobina, L. (2016). A Practical Proposal for Solving the World's Cigarette Butt Problem: Recycling in Fired clay Bricks. Waste Manage. 52, 228–244. doi:10.1016/j.wasman.2016.03.012
Mohajerani, A., Tanriverdi, Y., Nguyen, B. T., Wong, K. K., Dissanayake, H. N., Johnson, L., et al. (2017). Physico-mechanical Properties of Asphalt concrete Incorporated with Encapsulated Cigarette Butts. Construction Building Mater. 153, 69–80. doi:10.1016/j.conbuildmat.2017.07.091
Mohammed, M., Parry, T., Grenfell, J. J., and Materials, B. (2018). Influence of Fibres on Rheological Properties and Toughness of Bituminous Binder. Construction Building Mater. 163, 901–911. doi:10.1016/j.conbuildmat.2017.12.146
Moriwaki, H., Kitajima, S., and Katahira, K. (2009). Waste on the Roadside, 'poi-Sute' Waste: Its Distribution and Elution Potential of Pollutants into Environment. Waste Manage. 29, 1192–1197. doi:10.1016/j.wasman.2008.08.017
Rebischung, F., Chabot, L., Biaudet, H., and Pandard, P. (2018). Cigarette Butts: A Small but Hazardous Waste, According to European Regulation. Waste Manage. 82, 9–14. doi:10.1016/j.wasman.2018.09.038
Slebi-Acevedo, C. J., Lastra-González, P., Pascual-Muñoz, P., Castro-Fresno, D., and Materials, B. (2019). Mechanical Performance of Fibers in Hot Mix Asphalt: A Review. Construction Building Mater. 200, 756–769. doi:10.1016/j.conbuildmat.2018.12.171
Tao, G., Xiao, Y., Yang, L., Cui, P., Kong, D., Xue, Y., et al. (2019). Characteristics of Steel Slag Filler and its Influence on Rheological Properties of Asphalt Mortar. Construction Building Mater. 201, 439–446. doi:10.1016/j.conbuildmat.2018.12.174
Torkashvand, J., Farzadkia, M., Sobhi, H. R., and Esrafili, A. (2020). Littered Cigarette Butt as a Well-Known Hazardous Waste: A Comprehensive Systematic Review. J. Hazard. Mater. 383, 121241–121242. doi:10.1016/j.jhazmat.2019.121242
Wong, K. C., Goh, P. S., Ng, B. C., and Ismail, A. F. (2015). Thin Film Nanocomposite Embedded with Polymethyl Methacrylate Modified Multi-Walled Carbon Nanotubes for CO2 Removal. RSC Adv. 5, 31683–31690. doi:10.1039/c5ra00039d
Yin, J., and Wu, W. (2018). Utilization of Waste Nylon Wire in Stone Matrix Asphalt Mixtures. Waste Manage. 78, 948–954. doi:10.1016/j.wasman.2018.06.055
Keywords: cigarette butts, waste cellulose diacetate, stone mastic asphalt mixtures, fiber stabilizer, pavement performance
Citation: Liu H, Chen Y and Xue Y (2021) Reutilization of Recycled Cellulose Diacetate From Discarded Cigarette Filters in Production of Stone Mastic Asphalt Mixtures. Front. Mater. 8:770150. doi: 10.3389/fmats.2021.770150
Received: 03 September 2021; Accepted: 26 October 2021;
Published: 19 November 2021.
Edited by:
Libo Yan, Fraunhofer Institute for Wood Research, GermanyReviewed by:
Augusto Cannone Falchetto, Aalto University, FinlandCopyright © 2021 Liu, Chen and Xue. This is an open-access article distributed under the terms of the Creative Commons Attribution License (CC BY). The use, distribution or reproduction in other forums is permitted, provided the original author(s) and the copyright owner(s) are credited and that the original publication in this journal is cited, in accordance with accepted academic practice. No use, distribution or reproduction is permitted which does not comply with these terms.
*Correspondence: Yongjie Xue, eHlqc2tsQHdodXQuZWR1LmNu
Disclaimer: All claims expressed in this article are solely those of the authors and do not necessarily represent those of their affiliated organizations, or those of the publisher, the editors and the reviewers. Any product that may be evaluated in this article or claim that may be made by its manufacturer is not guaranteed or endorsed by the publisher.
Research integrity at Frontiers
Learn more about the work of our research integrity team to safeguard the quality of each article we publish.