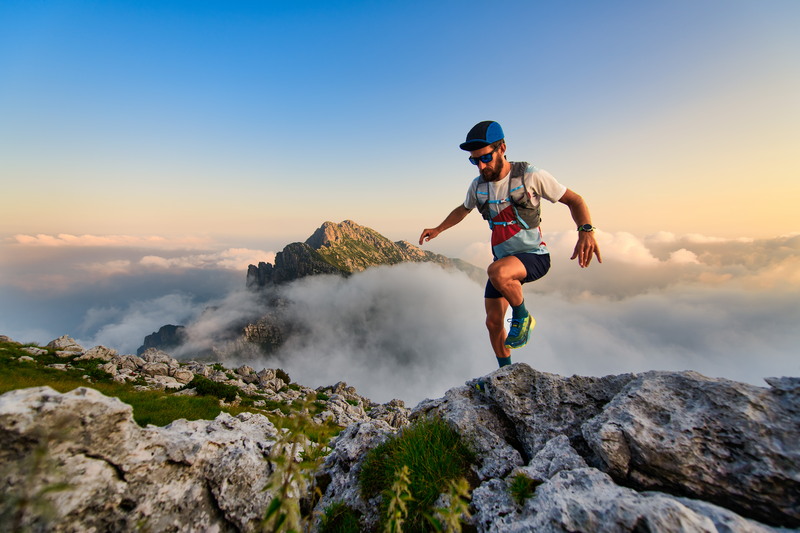
94% of researchers rate our articles as excellent or good
Learn more about the work of our research integrity team to safeguard the quality of each article we publish.
Find out more
EDITORIAL article
Front. Mater. , 20 September 2021
Sec. Smart Materials
Volume 8 - 2021 | https://doi.org/10.3389/fmats.2021.757479
This article is part of the Research Topic Four-dimensional (4D) Printing View all 11 articles
Editorial on the Research Topic
Four-Dimensional (4D) Printing
Four-dimensional (4D) printing has received widespread attention since its conceptualization in 2013. It is a revolutionary manufacturing technology based on the high degree of cross-integration of the disciplines including materials, mechanical engineering, dynamics, and informatics, etc. 4D printing, a cutting-edge branch of additive manufacturing (AM) technology, shows the capability of fabricating intelligent components through the active design of smart materials and structures, as well as the shapes, properties, or functionalities that can controllably vary with time and space dimensions. In recent years, a growing body of research has investigated the change in shapes of the 4D printed components. The main challenges that need to be addressed are the implementation of the change in properties and functionalities, as well as research on simulation technology for 4D printing. The 4D printed products have vast potential for various applications in the field of aerospace, automotive, biomedical, and soft robots, etc. Therefore, 4D printing is a very promising and valuable research field. It is encouraging that this Special Issue on 4D printing has collected ten articles, covering research on the materials, structures, functionalities, and applications in 4D printing.
The most popular way to develop 4D printing is to adopt intelligent materials in the AM process. Therefore, many researchers are interested in developing new intelligent materials. Zhao et al. fabricated a near-infrared laser driven intelligent hydrogel actuator system via extrusion-typed 3D printing and hydrothermal synthesis. The intelligent hydrogel actuator reached an effective displacement of 20 mm within 10 s through the forward movement, providing a material candidate for practical applications of 4D printing in the soft robot, information sensing, and health engineering. Ma et al. prepared a kind of self-healing material that is a promising intelligent material. The material was prepared by melamine-formaldehyde resin microcapsules using in-situ polymerization, and then it was fabricated through a 3D printer. The printed component showed excellent repair effect with a tensile strength of 50.93 MPa and a recovery rate of up to 87.22%.
Besides the intelligent materials, another representative way to realize 4D printing is through non-intelligent materials combined with specific structure design. As a result, the structure design is of particular importance. Dong et al. developed a shape reconfigurable, highly stretchable lattice structure with tunable Poisson’s ratio. The lattice was built based on a hexagonal honeycomb structure, demonstrating tunable shape reconfigurability as the ambient temperature changes, which was investigated by experiment and simulation. Chu et al. presented a structure design using alternate actuation to attain competent loading capacity in different deformed states. The two components were programmed to have the deformation behavior and stimulated by thermal expansion mismatch between polylactic acid (PLA) and carbon-fiber-reinforced PLA. Zou et al. proposed a pre-strained strategy to accelerate the actuation of thermal responsive structures. A bilayer structure with one pre-strained layer and the other non-pre-strained layer was integrally printed. Through experiments and finite element analysis, it was demonstrated that the pre-strain plays a key role in the deformation and also greatly accelerates the actuation of the bilayer structure.
Multi-material printing processes that can respond to diverse stimuli have become a research hotspot in 4D printing. Zhang et al. fabricated a typical hexagon-twist origami structure via multi-material printing technology. The printed structure has multi-stable features and the stiffness of the deformable structure is dramatically reduced under thermal triggering. The existing 4D printing technology is mostly subjected to only responsiveness to a single stimulus. To overcome this limit, Ren et al. proposed a 4D printing strategy with a dual stimuli-responsive shape-shifting structure that responds to both temperature and water. The structure was printed by direct ink writing (DIW) method to deposit a polyurethane elastomer material with water-swelling characteristics on a heat-shrinkage shape memory polymer material to form a bilayer structure. The multiple stimuli-responsive 4D printing method can effectively improve the intelligent responsiveness of 4D printed structures by combining multiple smart materials.
One of the research emphases of 4D printing rests with the achievement of the controllable changes in properties and functionalities of 4D printed components. To reflect this trend, this Special Issue has a collection of papers related to the changes in properties and functionalities based on sensing and energy conversion. Tang et al. summarized the recent advances of 4D printing towards soft tactile sensors, which combine the flexibility and the converting ability between mechanical forces and electrical signals. The review paper also discussed future perspectives for this emerging field. Liu et al. fabricated an underwater acoustic transducer by DIW using lead zirconate titanate (PZT) piezoelectric composites combined with furnace firing and resin impregnation. The electrical signal generated by the underwater acoustic transducer changed autonomously with the acoustic stimulation, which indicated the application mode of 4D printing in functional devices in the future.
In addition to artificial and active material and structural design of intelligent components, biomimetic design, which seeks inspiration from nature, is an extraordinary interesting method and worthy of in-depth exploration. Ren et al. published a review paper related to biomimetic 4D printing. By this novel method, they proposed morphing strategies and fabricated plant-inspired soft actuators. Plants can arouse inspiration because they exhibit ingenious adaptive motions that respond autonomously to environmental stimuli by varying cellular organization, the anisotropic orientation of cellulose fibers, and mechanical instabilities design, etc. This review summarized the morphing and actuation mechanisms of plants and concluded the recent development of 4D printed smart materials inspired by the locomotion and structures of plant systems.
4D printing is a rapidly growing research area. The collection of the papers in this Special Issue offers a snapshot of the attractive emerging field and future development trends. We hope this Special Issue can attract the attention of researchers from diverse disciplines. Finally, on behalf of the Editorial Board, we sincerely thank the contributors and staff at Frontiers, without whom this Special Issue would not have been possible.
KZ and CY write the first draft; YS and SY revise and finalize the manuscript.
The authors declare that the research was conducted in the absence of any commercial or financial relationships that could be construed as a potential conflict of interest.
All claims expressed in this article are solely those of the authors and do not necessarily represent those of their affiliated organizations, or those of the publisher, the editors and the reviewers. Any product that may be evaluated in this article, or claim that may be made by its manufacturer, is not guaranteed or endorsed by the publisher.
Keywords: four-dimensional (4D) printing, three-dimensional (3D) printing, additive manufactuing, intelligent component, controllable change
Citation: Shi Y, Yang S, Zhou K and Yan C (2021) Editorial: “Four-Dimensional (4D) Printing”. Front. Mater. 8:757479. doi: 10.3389/fmats.2021.757479
Received: 12 August 2021; Accepted: 31 August 2021;
Published: 20 September 2021.
Edited and Reviewed by:
Weihua Li, University of Wollongong, AustraliaCopyright © 2021 Shi, Yang, Zhou and Yan. This is an open-access article distributed under the terms of the Creative Commons Attribution License (CC BY). The use, distribution or reproduction in other forums is permitted, provided the original author(s) and the copyright owner(s) are credited and that the original publication in this journal is cited, in accordance with accepted academic practice. No use, distribution or reproduction is permitted which does not comply with these terms.
*Correspondence: Yusheng Shi, c2hpeXVzaGVuZ0BodXN0LmVkdS5jbg==
Disclaimer: All claims expressed in this article are solely those of the authors and do not necessarily represent those of their affiliated organizations, or those of the publisher, the editors and the reviewers. Any product that may be evaluated in this article or claim that may be made by its manufacturer is not guaranteed or endorsed by the publisher.
Research integrity at Frontiers
Learn more about the work of our research integrity team to safeguard the quality of each article we publish.