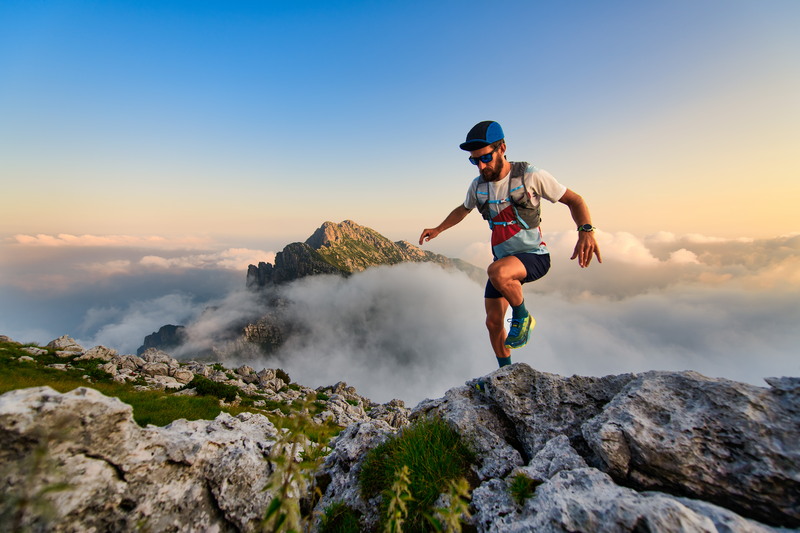
94% of researchers rate our articles as excellent or good
Learn more about the work of our research integrity team to safeguard the quality of each article we publish.
Find out more
ORIGINAL RESEARCH article
Front. Mater. , 29 September 2021
Sec. Polymeric and Composite Materials
Volume 8 - 2021 | https://doi.org/10.3389/fmats.2021.745088
This article is part of the Research Topic Carbon Nanomaterial Filled Polymer Composites for Functional Applications: Processing, Structure, and Property Relationship View all 13 articles
In this study, PEEK nanocomposites with 0, 0.5, 1, and 2wt% IF-WS2 were manufactured by injection moulding and Fused Deposition Modelling (FDM). To compare the impact of the two processing methods and the incorporated nanoparticles on the morphology, crystallization and final mechanical properties of the nanocomposites, SEM, DSC and tensile testing were performed. In general, a good distribution of nanoparticles was observed in PEEK, although larger agglomerates were visible at 2 wt% IF-WS2. The crystallization degree of PEEK increased with increasing loading of IF-WS2 nanoparticles up to 1wt% and then declined at 2 wt%, due to lower level of particle dispersion in this sample. The 3D printed samples showed slightly higher crystallinity at each IF-WS2 loading in relation to the injection moulded samples and extruded filaments, because of multiple reheating effect from subsequent layer deposition during FDM, causing recrystallization. In general, incorporation of IF-WS2 nanoparticles increased the mechanical properties of pure PEEK in both 3D printed and injection moulded samples. However, this increment was more noticeable in the 3D-printed nanocomposite samples, resulting in smaller gap between the mechanical properties of the 3D-printed samples and the injection moulded counterparts, in respect to pure PEEK, particularly at 1 wt% IF-WS2. This effect is ascribed to the increased inter-layer bonding of PEEK in the presence of IF-WS2 nanoparticles in FDM. In general, the lower mechanical properties of the 3D printed samples compared with the injection moulded ones are ascribed to poor interlayer bonding between the deposited layers and the presence of voids. However, addition of just 1 wt% of IF-WS2 nanoparticles into PEEK increased the tensile strength and Young’s modulus of the FDM PEEK materials to similar levels to those achieved for unfilled injection moulded PEEK. Therefore, incorporation of IF-WS2 nanoparticles into PEEK is a useful strategy to improve the mechanical performance of FDM PEEK.
Owing to their high thermal and chemical stability, exceptional strength-to-weight ratio, and recyclability, high performance thermoplastic polymers, such as Polysulfone (PSU), polyetherimide (PEI), and polyether ether ketone (PEEK) are becoming increasingly attractive in competition with metals and ceramics for load bearing applications under harsh operating conditions (Wiesli and Özcan, 2015; Al Christopher et al., 2021). Apart from the intrinsic properties of the polymer, the applied manufacturing method, processing conditions, and the material composition play a major role on the final quality and properties of high-performance thermoplastic parts (Golbang et al., 2017; Golbang et al., 2020; Liu and Kunc, 2020).
Nanofillers are added to polymers to further improve their thermal, mechanical and optical properties, depending on the type of filler (Aradhana et al., 2018; Golbang et al., 2020; Mokhtari et al., 2021a). For example, addition of hydroxyapatite particles increases the bioactivity of PEEK for development of cranial implants with improved biocompatibility (Manzoor et al., 2021). Incorporation of expanded graphite (EG) into PEEK via twin-screw compounding and injection moulding, results in significant enhancement of PEEK electrical conductivity (Mokhtari et al., 2021b).
The processing of high-performance polymers is generally more difficult and expensive compared with commodity thermoplastics due to their high melt viscosity and higher melting temperatures (Golbang et al., 2020). Incorporation of fillers into high-performance polymers for improving their performance may further increase melt viscosity thus creating potential problems in achieving sufficient power to process the material and risking thermal/shear degradation of the polymer. Therefore, the type, amount, and size of filler, as well as the processing method should be chosen carefully when developing high-performance nanocomposites (Díez-Pascual et al., 2012; Valino et al., 2019; Golbang et al., 2020; Mokhtari et al., 2021b; Manzoor et al., 2021).
Among the conventional plastics processing techniques, injection moulding is one of the most commonly used methods for production of high-performance polymers/nanocomposites (Shaharuddin and Salit, 2006). Injection moulding enables large volume production with good precision, detail, and repeatability (Goodship, 2004; Shaharuddin and Salit, 2006; Bilewicz et al., 2008; Mokhtari et al., 2021b). When assessing the quality of parts produced via new polymer processing technologies such as additive manufacturing, they are often compared with those made via injection moulding. Additive manufacturing (AM) or 3D printing is becoming popular for producing parts from thermoplastic polymers as it can create complex geometries without the need for sophisticated tooling, resulting in cost-effective and sustainable manufacturing. Although, it should be noted that currently, AM is considered cost-effective for small volumes of production as compared to injection moulding (Dawoud et al., 2016; Koštial et al., 2016; Verdejo de Toro et al., 2020).
3D printing is mostly used for commodity plastics such as acrylonitrile butadiene styrene (ABS), and polylactic acid (PLA), polyvinyl alcohol (PVA), polycaprolactone (PCL), and polyamide (Nylon). However, the thermal and mechanical properties of these polymers are limited, and hence, there is growing demand to adopt AM processes to high-performance polymers for widespread commercial application. In recent years, high performance polymers have been successfully 3D printed via additive manufacturing techniques such as Fused Deposition Modelling (FDM) and High temperature selective laser sintering (HT-SLS). FDM is one of the most user-friendly and cost-effective AM methods for producing complex thermoplastic parts (Liu et al., 2019; Valino et al., 2019; Zanjanijam et al., 2020). However, in comparison with conventional manufacturing methods, such as injection moulding, 3D printing results in lower part mechanical performance. This is mainly due to the weak inter-layer bonding between the deposited layers in FDM and presence of voids. For example, 3D printed Nylon six shows a tensile strength of ∼50 MPa as compared with ∼80 MPa for the injection moulded parts (Verdejo de Toro et al., 2020). Recently, much research has been conducted to improve the mechanical performance of 3D printed thermoplastics by adjusting and optimizing the printing conditions (i.e., layer thickness, print orientation, infill pattern, nozzle temperature, print bed temperatures, printing speed, etc) or addition of reinforcing particles such as silica, graphite, carbon, or glass fibres (Brucato et al., 1993; Pinto et al., 2015; Yang et al., 2017; Schiavone et al., 2020; Antony Samy et al., 2021). However, addition of fillers to the polymer feedstock is more challenging in FDM due to problems such as clogging of the nozzle, higher melt temperature and low flowability leading to poor chain inter-diffusion and therefore weaker inter-layer bonding as well as delamination. Hence, in order to achieve high quality printed parts, it is important to optimize the printing conditions according to the material flow properties, particle size, and the printer geometrical specification (e.g., nozzle diameter) (Coogan, 2019; Huang et al., 2019; Rostom and Dadmun, 2019; Srinivas et al., 2020; Candal et al., 2021).
To exploit the benefits of additive manufacturing and achieve 3D printed parts comparable with conventional manufacturing techniques such as injection moulding, it is crucial to resolve some of the associated issues with this technology, such as weak interlayer bonding. Hence, this study aims to improve the mechanical properties of 3D printed PEEK through incorporation of IF-WS2 nanoparticles. For this, PEEK nanocomposites with different loadings of IF-WS2 nanoparticles are produced using two methods: FDM and injection moulding. Then, the thermal and mechanical properties of the developed nanocomposites are evaluated and compared. As mentioned, PEEK is considered as a high-performance polymer with excellent thermal stability (up to 600°C), resistance to chemicals and radiation, as well as biocompatibility which makes it suitable for applications in aerospace, medical and automotive industries. IF-WS2 nanoparticles are very distinct types of fillers because of their innate mechanical and tribological properties, acting as both reinforcing and lubricating agents. In our previous research, it was shown that incorporation of IF-WS2 nanoparticles into PEEK via melt compounding leads to reduction of melt viscosity which is favourable for processing without compromising its final mechanical properties (Golbang et al., 2020). It is believed that reduction of viscosity (improved flowability) can increase the bonding between the deposited layers through polymer chain diffusion and therefore improve the mechanical properties of the 3D-printed parts via FDM. Even though, reinforcing fillers generally increase the mechanical properties of the polymer, not all fillers can strengthen the interlayer bonding in FDM printed parts (Pinto et al., 2015; Coogan, 2019; Rostom and Dadmun, 2019; Srinivas et al., 2020). The objective of this study is to reduce the gap between the mechanical properties of the 3D-printed and injection moulded parts using IF-WS2 nanoparticles to address the low interlayer bonding strength FDM 3D-printed parts, as one of the prominent challenges in additive manufacturing.
Inorganic fullerene like Tungsten di-sulfide (IF-WS2) nanoparticles with 80 nm average diameter were prepared by Professor Yanqui Zhu’s group at the University of Exeter. Polyether ether ketone (PEEK) 450 G was purchased from Victrex, (Mw ≈ 44,000 g/mol, Tg ≈ 143°C, Tm ≈ 343°C) and used as the matrix. To produce filaments for 3D printing, the IF-WS2 nanoparticles were melt compounded with PEEK at 0.5, 1, and 2 wt% loading using a twin-screw extruder with 16 mm diameter, length to diameter ratio (L/D) of 40, and screw speed of 30 rpm. The average diameter of filaments was monitored and kept at 1.75 ± 0.15 mm. The screw configuration was designed in a way to enhance nanoparticle dispersion using screw elements consisting of transporting elements for forward conveying of extrudate, kneading elements with 90°, 60°, and 30° twist angles for dispersion, and reverse screw element. The temperatures indicated in each zone of the extruder were: 365 (feeding zone), 400 (melting and compression zone), 385°C (metering zone and die extrusion). The extruded filaments were cooled at room temperature (∼25°C).
A modified UM2 + FDM 3D printer was used for to print PEEK nanocomposite specimens which enables extrusion temperatures of up to 420°C (using an all-metal hot end), bed temperature of maximum 350°C (via heating elements embedded under the print bed), and heating lamps for regulation of chamber temperature up to 230°C.
Pellets were cut from the filaments for injection moulding. A Haake MiniJet Pro injection moulding machine was used for production of injection moulded tensile samples, operating at melt temperature of 400°C and mould temperature of 280°C. Specimens with similar dimensions to the injection moulded samples were printed from the extruded filaments using a high temperature Ultimaker. The printing speed, building plate temperature, nozzle temperature and nozzle diameter were set at 40 mm/s, 280°C, 400°C and 2 mm, respectively. A raster orientation of ±45° was applied to produce a uniform morphology. A comparison was made between the mechanical properties of the printed and the injection moulded samples.
Pictures of the 3D-printed and injection moulded samples are presented in Figure 1.
The schematic presentation of the sequence of manufacturing process is demonstrated through a flowchart in Figure 2.
A high resolution FEG SEM (HITACHI), operating at 30 kV and an intensity of 9 × 10–9 was used to observe the gold coated fractured surfaces of the filaments to evaluate the dispersion and distribution of IF-WS2 nanoparticles in PEEK.
The thermal properties of the 3D printed and injection moulded nanocomposite samples were measured using a TA-Instrument Q1000 differential scanning calorimeter (DSC). 5 mg samples were sealed in aluminium pans and a standard mode heating-cooling-heating cycle at 10°C/min between 20 and 400°C was applied. The amount of degree of crystallinity (χc) was calculated from the crystallization peak (Golbang et al., 2020).
Tensile testing was performed on both 3D printed and injection moulded samples using an Instron testing machine (Instron 3,344) and following the ISO standard: ISO 527–2 Type 5A. Five specimens (75 mm × 4 mm × 2 mm) were tested for each sample with a crosshead speed of 2.0 mm/min at 20°C and using a 2 kN load cell.
The SEM images presented in Figure 3 show the morphology of PEEK nanocomposite filaments with 0.5, 1, and 2 wt% IF-WS2. Overall, a homogenous distribution of particles is observed in all three loadings. However, there is slightly larger sizes of inclusions present in the 2 wt% and to some extent in the 0.5 wt% samples, indicating some degree of agglomeration in these cases. The higher dispersion degree of particles achieved at 1 wt% IF-WS2 may be due to the lubricant effect of these nanoparticles. Tendency for agglomeration increases with further increase in the number of particles at the higher loading (2 wt%) (Khare and Burris, 2010; Golbang et al., 2017; Fu et al., 2019; Golbang et al., 2020).
FIGURE 3. SEM images of PEEK nanocomposites containing (A) 0.5 wt%, (B) 1 wt%, and (C) 2 wt% IF-WS2 nanoparticles.
There was no obvious change observed in the distribution and dispersion state of the nanoparticles after the injection moulding and 3D printing process.
Dispersion in a nanocomposite is associated with breaking of agglomerates into smaller sizes and ideally into individual nanoparticles, by overcoming the inter-particle interactions (typically van der Waals forces). The “dispersion state” of nanoparticles is linked to the final properties of the nanocomposite due to the long-range effects of nanoparticle-matrix interface on nearby polymer chains. However, achieving good dispersion is considered as a prominent challenge. The “distribution sate” of particles in a nanocomposite is independent of dispersion state (or the size of inclusions). In a good distribution, the inclusions (e.g., particles, agglomerates, aggregates, … ) are homogeneously distributed in the matrix and isotropic properties are achieved within the nanocomposite. In other words, each inclusion is as far as possible from its nearest neighbour, so that the space is homogeneously filled (Khare and Burris, 2010; Fu et al., 2019).
Changes in the crystallinity of the PEEK nanocomposites after extrusion (i.e., filaments), and shaped via 3D printing and injection moulding are shown in Figure 4.
Incorporation of IF-WS2 nanoparticles increases the crystallinity of PEEK in samples up to a loading of 1 wt% which can be attributed to the nucleation effect of these nanoparticles. Reduction of crystallinity with a further increase in IF-WS2 concentration to 2 wt%, is likely to be due to a reduced nucleation effect of the larger agglomerated IF-WS2 or a confining effect of the particles that restricts molecular mobility and ability of polymer chains to orient and crystallize (Golbang et al., 2020; Antony Samy et al., 2021).
From Figure 4, it can be seen that the overall crystallinity of the 3D printed samples is slightly higher at each filler loading compared with the injection moulded counterparts and filaments. This can be explained by the thermal history experienced in each process. During FDM, the deposited layers are reheated due to the deposition of subsequent layers. This multiple reheating effect contributes to further growth of crystals and higher degrees of crystallinity. During injection moulding, the material is cooled from extrusion temperature (400°C) to the mould temperature (280°C) in less than a minute and then ejected into a room temperature environment. The higher cooling rate in injection moulding compared to that in in FDM, results in a lower degree of crystallinity. The filaments have the lowest degree of crystallinity at each filler loading. This is due to the sudden cool down of the polymer melt to room temperature (Brucato et al., 1993; Yang et al., 2017; Golbang et al., 2020; Schiavone et al., 2020; Antony Samy et al., 2021).
The stress-strain curves of the injection moulded and 3D printed samples are illustrated in Figures 3, 4. The average Young’s modulus and ultimate tensile strength are reported in Table 1. As seen in Figures 5, 6, as well as Table 1, the trend of changes in the Young’s modulus and tensile strength with addition of IF-WS2 nanoparticles are similar, with the addition of IF-WS2 nanoparticles generally increasing the Young’s modulus and tensile strength of PEEK up to a loading of 1 wt%. This increase is due to the presence of the reinforcing filler and the increased crystallinity of these samples. Properties drop off at the 2 wt% loading due to the stress concentration effect of, and lower aspect ratio of, agglomerated IF-WS2, combined with a slightly lower crystallinity. The elongation at break deceases in the injection moulded samples for increasing IF-WS2 which is quite typical when reinforcing fillers are added to a polymer matrix (Pinto et al., 2015; Huang et al., 2019; Rostom and Dadmun, 2019; Golbang et al., 2020). However, the reverse is true for the 3D printed materials with added IF-WS2. Two possible explanations for this improvement are an increase in layer-to-layer bonding due to enhanced thermal conductivity of IF-WS2 containing PEEK and, the lubricating effect of these nanoparticles, contributing to higher molecular mobility and polymer chain inter-diffusion during deposition and therefore better bonding between the layers (Coogan, 2019; Srinivas et al., 2020; Candal et al., 2021).
TABLE 1. Comparison between the mechanical properties of injection moulded and 3D printed PEEK/IF-WS2 nanocomposite samples.
FIGURE 5. Stress-strain curve for injection moulded PEEK samples containing 0, 0.5, 1, and 2wt% IF-WS2.
The 3D printed samples have a lower Young’s modulus and tensile strength for each IF-WS2 loading in comparison to the injection moulded samples, by about 80 and 70%, respectively. There is a very significant reduction in elongation at break for the 3D printed materials compared to those that are injection moulded. These results are expected due to the weaker inter-layer bonding between the layers in 3D printed samples and the presence of voids. Also, the pressure exerted during injection moulding can compress and strengthen the part (Koštial et al., 2016; Verdejo de Toro et al., 2020).
According to the data presented in Table 1, the Young’s modulus of the 3D printed samples containing 1 wt% IF-WS2 surpasses that of the injection moulded pure PEEK and the tensile strength is significantly increased to just 7% lower than the unfilled PEEK. Hence, it can be concluded that adding small amounts of IF-WS2 nanoparticles can overcome the reduced stiffness and tensile strength caused by poor layer adhesion and voids in 3D printed parts.
Overall, the increment in the Young’s Modulus and tensile strength of PEEK with addition of IF-WS2 nanoparticles is higher for the 3D printed samples in respect to the injection moulded ones. This is ascribed to the improved bonding between the deposited PEEK layers in the presence of IF-WS2 nanoparticles.
In this work, a comparison was made between the mechanical properties of high-performance PEEK nanocomposites with loadings of 0.5, 1, and 2 wt% IF-WS2, fabricated by two different methods: injection moulding and 3D printing (FDM). Although the 3D printed samples had slightly higher levels of crystallinity compared with the injection moulded samples, they exhibited lower Young’s modulus and tensile strength as expected by about 82–87% and 73–85%, respectively. The lower mechanical properties of the 3D printed samples compared to their injection moulded counterparts is attributed to the lower packing density, poor inter-layer bonding and presence of voids. Overall, addition of IF-WS2 nanoparticles increases the mechanical properties of PEEK in both 3D printed and injection moulded samples. However, it is worth noting that the presence of IF-WS2 in PEEK reduces the gap between the mechanical properties of the 3D printed and injection moulded samples which can be ascribed to the simultaneous reinforcing and lubricating effect of these particles, allowing higher molecular inter-diffusion and better bonding between the layers.
The raw data supporting the conclusions of this article will be made available by the authors, without undue reservation.
AG, conceptualization, data curation, formal analysis, investigation, methodology, visualization, writing—original draft, writing—review and editing. MM, investigation, methodology. EA, conceptualization, resources. AM, conceptualization, resources, project administration, financial support. EH, conceptualization, formal analysis, project administration, supervision, funding acquisition, resources, writing—review and editing.
The authors declare that the research was conducted in the absence of any commercial or financial relationships that could be construed as a potential conflict of interest.
All claims expressed in this article are solely those of the authors and do not necessarily represent those of their affiliated organizations, or those of the publisher, the editors and the reviewers. Any product that may be evaluated in this article, or claim that may be made by its manufacturer, is not guaranteed or endorsed by the publisher.
The authors wish to thank the EPSRC for funding for this research under grant reference EP/N034783/1 Novel high performance polymeric composite materials for additive manufacturing of multifunctional components and the North West Centre for Advanced Manufacturing (NW CAM) for their financial contribution.We also wish to thank Professor Yanqui Zhu and Dr Bahareh Yazdani of the University of Exeter for providing the IF-WS2 nanoparticles.
Al Christopher, C., da Silva, Í. G., Pangilinan, K. D., Chen, Q., Caldona, E. B., and Advincula, R. C. (2021). High performance polymers for oil and gas applications. Reactive Funct. Polym., 104878.
Antony Samy, A., Golbang, A., Harkin-Jones, E., Archer, E., and McIlhagger, A. (2021). Prediction of part distortion in Fused Deposition Modelling (FDM) of semi-crystalline polymers via COMSOL: Effect of printing conditions. CIRP J. Manufacturing Sci. Tech. 33, 443–453. doi:10.1016/j.cirpj.2021.04.012
Aradhana, R., Mohanty, S., and Nayak, S. K. (2018). High performance epoxy nanocomposite adhesive: Effect of nanofillers on adhesive strength, curing and degradation kinetics. Int. J. Adhes. Adhesives 84, 238–249. doi:10.1016/j.ijadhadh.2018.03.013
Bilewicz, M., Viana, J. C., and Dobrzański, L. A. (2008). Polymer composite strengthening by developed injection moulding technique. Arch. Mater. Sci. Eng. 30 (2), 69–72.
Brucato, V., Piccarolo, S., and Titomanlio, G. (1993). “April. Crystallization kinetics in relation to polymer processing,” in Makromolekulare Chemie. Macromolecular Symposia (Basel: Hüthig & Wepf Verlag), 68, 245–255. doi:10.1002/masy.19930680119No. 1
Candal, M. V., Calafel, I., Fernández, M., Aranburu, N., Aguirresarobe, R. H., Gerrica-Echevarria, G., et al. (2021). Study of the interlayer adhesion and warping during material extrusion-based additive manufacturing of a carbon nanotube/biobased thermoplastic polyurethane nanocomposite. Polymer 224, 123734. doi:10.1016/j.polymer.2021.123734
Coogan, T. J. (2019). In-Line Monitoring and Prediction of Viscosity, Interlayer Contact, and Strength in the Fused Filament Fabrication Process. Massachusetts: Doctoral dissertation, University of Massachusetts Lowell.
Dawoud, M., Taha, I., and Ebeid, S. J. (2016). Mechanical behaviour of ABS: An experimental study using FDM and injection moulding techniques. J. Manufacturing Process. 21, 39–45. doi:10.1016/j.jmapro.2015.11.002
Díez-Pascual, A. M., Naffakh, M., Marco, C., Ellis, G., and Gómez-Fatou, M. A. (2012). High-performance nanocomposites based on polyetherketones. Prog. Mater. Sci. 57 (7), 1106–1190. doi:10.1016/j.pmatsci.2012.03.003
Fu, S., Sun, Z., Huang, P., Li, Y., and Hu, N. (2019). Some basic aspects of polymer nanocomposites: A critical review. Nano Mater. Sci. 1 (1), 2–30. doi:10.1016/j.nanoms.2019.02.006
Golbang, A., Famili, M. H. N., and Shirvan, M. M. M. (2017). A method for quantitative characterization of agglomeration degree in nanocomposites. Composites Sci. Tech. 145, 181–186. doi:10.1016/j.compscitech.2017.04.013
Golbang, A., Harkin-Jones, E., Wegrzyn, M., Campbell, G., Archer, E., and McIlhagger, A. (2020). Production and characterization of PEEK/IF-WS2 nanocomposites for additive manufacturing: Simultaneous improvement in processing characteristics and material properties. Additive Manufacturing 31, 100920. doi:10.1016/j.addma.2019.100920
V. Goodship ed., 2004. Troubleshooting injection moulding (Vol. 15). Pielichowski. iSmithers Rapra Publishing.
Huang, B., He, H., Meng, S., and Jia, Y. (2019). Optimizing 3D printing performance of acrylonitrile‐butadiene‐styrene composites with cellulose nanocrystals/silica nanohybrids. Polym. Int. 68 (7), 1351–1360. doi:10.1002/pi.5824
Khare, H. S., and Burris, D. L. (2010). A quantitative method for measuring nanocomposite dispersion. Polymer 51 (3), 719–729. doi:10.1016/j.polymer.2009.12.031
Koštial, P., Ružiak, I., Malinarič, S., Jančíková, Z., and Rusnák, V. (2016). “Injection Moulding Versus Rapid Prototyping—Thermal and Mechanical Properties,” in Machining, Joining and Modifications of Advanced Materials (Singapore: Springer), 121–127.
Liu, P., and Kunc, V. (2020). “Effect of 3D printing conditions on the micro- and macrostructure and properties of high-performance thermoplastic composites,” in Structure and Properties of Additive Manufactured Polymer Components (UK: Woodhead Publishing), 65–86. doi:10.1016/b978-0-12-819535-2.00003-x
Liu, Z., Wang, Y., Wu, B., Cui, C., Guo, Y., and Yan, C. (2019). A critical review of fused deposition modeling 3D printing technology in manufacturing polylactic acid parts. Int. J. Adv. Manufacturing Tech. 102 (9), 2877–2889. doi:10.1007/s00170-019-03332-x
Manzoor, F., Golbang, A., Jindal, S., Dixon, D., McIlhagger, A., Harkin-Jones, E., et al. (2021). 3D printed PEEK/HA composites for bone tissue engineering applications: Effect of material formulation on mechanical performance and bioactive potential. J. Mech. Behav. Biomed. Mater. 121, 104601. doi:10.1016/j.jmbbm.2021.104601
Mokhtari, M., Archer, E., Bloomfield, N., Harkin‐Jones, E., and McIlhagger, A. (2021). A review of electrically conductive Poly (ether ether ketone) materials. Polym. Int., 1016–1025. doi:10.1002/pi.6176
Mokhtari, M., Archer, E., Bloomfield, N., Harkin‐Jones, E., and McIlhagger, A. (2021). High‐performance and cost‐effective melt blended poly (ether ether ketone)/expanded graphite composites for mass production of antistatic materials. Polym. Int., 1137–1145. doi:10.1002/pi.6226
Pinto, D., Bernardo, L., Amaro, A., and Lopes, S. (2015). Mechanical properties of epoxy nanocomposites using titanium dioxide as reinforcement - A review. Construction Building Mater. 95, 506–524. doi:10.1016/j.conbuildmat.2015.07.124
Rostom, S., and Dadmun, M. D. (2019). Improving heat transfer in fused deposition modeling with graphene enhances inter filament bonding. Polym. Chem. 10 (44), 5967–5978. doi:10.1039/c9py00832b
Schiavone, N., Verney, V., and Askanian, H. (2020). Effect of 3D printing temperature profile on polymer materials behavior. 3D Printing and Additive Manufacturing 7 (6), 311–325. doi:10.1089/3dp.2020.0175
Shaharuddin, S. I. S., and Salit, M. S. (2006). A review of the effect of moulding parameters on the performance of polymeric composite injection moulding. Turkish J. Eng. Environ. Sci. 30 (1), 23–34.
Srinivas, V., van Hooy-Corstjens, C. S. J., Rastogi, S., and Harings, J. A. W. (2020). Promotion of molecular diffusion and/or crystallization in fused deposition modeled poly(lactide) welds. Polymer 202, 122637. doi:10.1016/j.polymer.2020.122637
Valino, A. D., Dizon, J. R. C., Espera, A. H., Chen, Q., Messman, J., and Advincula, R. C. (2019). Advances in 3D printing of thermoplastic polymer composites and nanocomposites. Prog. Polym. Sci. 98, 101162. doi:10.1016/j.progpolymsci.2019.101162
Verdejo de Toro, E., Coello Sobrino, J., Martínez Martínez, A., Miguel Eguía, V., and Ayllón Pérez, J. (2020). Investigation of a short carbon fibre-reinforced polyamide and comparison of two manufacturing processes: Fused Deposition Modelling (FDM) and polymer injection moulding (PIM). Materials 13 (3), 672. doi:10.3390/ma13030672
Wiesli, M. G., and Özcan, M. (2015). High-performance polymers and their potential application as medical and oral implant materials: a review. Implant Dent 24 (4), 448–457. doi:10.1097/ID.0000000000000285
Yang, C., Tian, X., Li, D., Cao, Y., Zhao, F., and Shi, C. (2017). Influence of thermal processing conditions in 3D printing on the crystallinity and mechanical properties of PEEK material. J. Mater. Process. Tech. 248, 1–7. doi:10.1016/j.jmatprotec.2017.04.027
Keywords: high-performance nanocomposite, additive manufacturing, injection moulding, PEEK (poly ether ether ketone), inorganic fullerene tungsten sulphide (IF-WS2)
Citation: Golbang A, Mokhtari M, Harkin-Jones E, Archer E and Mcilhagger A (2021) Additive Manufacturing and Injection Moulding of High-Performance IF-WS2/PEEK Nanocomposites: A Comparative Study. Front. Mater. 8:745088. doi: 10.3389/fmats.2021.745088
Received: 21 July 2021; Accepted: 06 September 2021;
Published: 29 September 2021.
Edited by:
Patricia Krawczak, Institut Mines-Télécom, FranceReviewed by:
Roham Rafiee, University of Tehran, IranCopyright © 2021 Golbang, Mokhtari, Harkin-Jones, Archer and Mcilhagger. This is an open-access article distributed under the terms of the Creative Commons Attribution License (CC BY). The use, distribution or reproduction in other forums is permitted, provided the original author(s) and the copyright owner(s) are credited and that the original publication in this journal is cited, in accordance with accepted academic practice. No use, distribution or reproduction is permitted which does not comply with these terms.
*Correspondence: Eileen Harkin-Jones, ZS5oYXJraW4tam9uZXNAdWxzdGVyLmFjLnVr
Disclaimer: All claims expressed in this article are solely those of the authors and do not necessarily represent those of their affiliated organizations, or those of the publisher, the editors and the reviewers. Any product that may be evaluated in this article or claim that may be made by its manufacturer is not guaranteed or endorsed by the publisher.
Research integrity at Frontiers
Learn more about the work of our research integrity team to safeguard the quality of each article we publish.