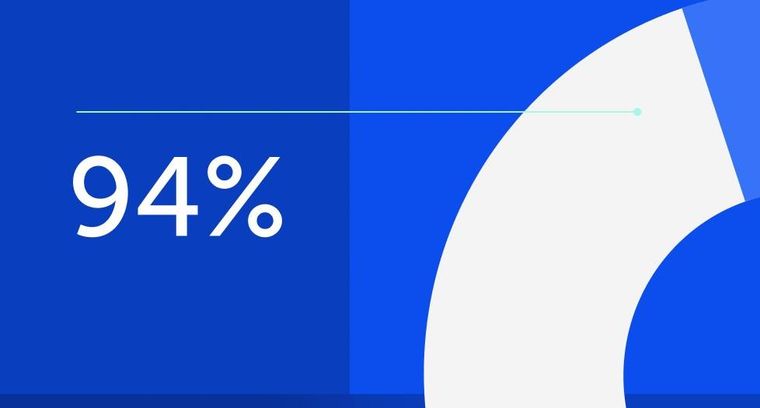
94% of researchers rate our articles as excellent or good
Learn more about the work of our research integrity team to safeguard the quality of each article we publish.
Find out more
ORIGINAL RESEARCH article
Front. Mater., 12 October 2021
Sec. Mechanics of Materials
Volume 8 - 2021 | https://doi.org/10.3389/fmats.2021.733391
This article is part of the Research Topic2021 Retrospective: Mechanics of MaterialsView all 9 articles
The accumulated damage of the surrounding rocks induced by the existing coal mining activities (such as excavation and extraction) is the initial mechanical background of the rock and coal for the further mining operations. An energy-based Cumulative Initial Damage (CID) variable was proposed to account for such existing damage. With the MTS815 electro-hydraulic servo-controlled system, coal samples with different CID value were prepared by cyclic pre-loading and unloading process, and a novel experimental framework was presented to investigate the effect of CID on the further mechanical properties of the CID coal samples. The deformation characteristics, peak strength, peak strain, dilatancy characteristics, brittle-ductile transformation behavior, and microscopic structure of the CID coal samples were investigated in detail. The triaxial compression tests showed that with the increased of CID value, the compaction part of the coal samples was shorter and the strain softening stage became longer. When the CID value was increased from 0 to 0.521, the deviation stress and peak strain of the coal decreased by 31.4 and 37.7%, respectively and the main characteristic of the fracture morphology changed from cleavage steps to dimpling.
In recent years, many studies have focused on the mechanical characteristics of coal and rock medium generally, as they have a substantial influence on the stability and safety of underground excavations and in some conditions could contribute to understand and eliminate serious mine disaster. The initial damage in coal and rock medium, such as natural joints, cracks, voids, and faults, has significant effect on the strength, deformation, and dilatancy of the coal and rock (Lachassagne et al., 2011; Naghadehi, 2015; Roy et al., 2017; Miao et al., 2018; Jiang et al., 2020; Chen et al., 2021). The excavation of an underground opening would result in stress and/or energy redistribution within the surrounding rock media (Chen et al., 2018; Ma et al., 2019; Pu et al., 2021), and also will cause damage to accumulate in the surrounding rocks. Hence, the terminology of Cumulative Initial Damage (CID) in this study is defined as the damage accumulated in the rock and coal mass by the former mining activities (Jiang et al., 2019). During the subsequent mining activities, such damaged rock and coal with various of CID will perform different mechanical characteristics, and will undergoes a complicated process of stress path evolution and/or energy release due to changing loading and unloading, which promotes the further generation, expansion and penetration of microvoid, joints and fractures (Wang et al., 2017). The mechanical properties of such CID rock and coal will, therefore, be adversely affected by these multiple on-going disturbances. For example, the strength of coal pillars in the room-pillar mining method will be affected by the gradual decrease of the stable elastic core areas due to the stripping of the pillars (Zhang et al., 2017; Ma et al., 2021a). The safety of pillars or the filling bodies of retained roadways along a goaf are affected by mining induced stress and the accumulated damage (Coggan et al., 2012; Bai et al., 2015; Ma et al., 2021b). Therefore, the study on the mechanical properties of CID coal provides insight into the underground excavations and the design of supports for these openings under such time-dependent disturbances.
Many researchers have investigated the effects of initial damage on the mechanical properties of rocks. Brown and Trollope (1970) tested the triaxial compression behavior of idealized samples containing sets of pre-formed discontinuities inclined at various angles to the sample axes. They found that there were four major modes of failure: 1) axial cleavage fractures at low confining pressures, 2) shear failures through the plaster and across joint planes, 3) slip on joint planes, and 4) ductile failure. Asanov and Pan’kov (2004) tested the deformation of joints in salt rocks and obtained the relationship to describe the process of creep and relaxation. Nazarov (2008), based on the elastic-brittle model of a rock mass, proposed a mechanism of interaction between the edges of discontinuities under normal loading. A physical model was tested to assess the effects of depth, joint spacing, and orientation on the maximum unsupported span of shallow underground openings under static and cyclic loads (Fuenkajorn and Phueakphum, 2010). The results showed that under the same depth and joint spacing ratio, the inclinations of joint angles from 0° to 45° can reduce the maximum safe span by up to 20%. Bahaaddini et al. (2014) investigated the effect of joint length on the shear behavior of rough rock joints using PFC2D and proposed that as the joint length increases, the peak shear strength, peak dilation rate, and shear stiffness decrease, while the peak shear displacement increases. Based on the above researches, much knowledge has been gained through theoretical and experimental studies into the initial damage of rock mass, especially on the mechanical behavior of joint or discontinuities.
The CID is a common phenomenon occurring in the surrounding rocks which substantial influence on the stability and safety of underground excavations. However, few experimental testing studies have been carried out on the mechanical properties of such damaged rock mass and/or coal mass affected by CID. Thus, this paper focus on the mechanical response of coal with initial damage caused by the existing mining activities (such as excavation and extraction). In this present study, coal samples with various CID value were firstly prepared using a cyclic pre-loading and unloading method for the subsequent tests. The evolution characteristics of morphology and pore structure of coal samples with various CID value were analyzed and quantitatively characterized. The characteristics of deformation, strength, peak strain, dilatancy, and brittle-ductile transformation mechanism were studied.
The coal samples used throughout the present study were gathered from Xiaojihan coal mine, Yulin City in Shanxi Province, China. The sampling location was at the solid coal side of an auxiliary transportation roadway in the 11,215 working face, 2,650 m away from the mining face, that had been less affected by mining induced stresses (see in Figure 1, the red solid dot indicates the sample location). The samples were cored according to the International Society for Rock Mechanics (ISRM) Standards (Fairhurst and Hudson, 1999) with 50 mm diameter and 100 mm height.
FIGURE 1. Core location in the mine site and standard coal sample processing (For interpretation of the references to color in this figure, the reader is referred to the web version of this article).
In this experimental study, first of all, conventional tension, compression and shear tests were carried out with intact and undamaged coal specimens to obtain the basic physical and mechanical parameters of coal mass, as described in Basic Mechanical Properties of Conventional Coal Samples.
Then, based on the quantitative calculation of damage in Definition of CID, the MTS815 electro-hydraulic servo-controlled system was used to prepare coal samples with different CID values through triaxial compression tests with different loading-unloading cycles.
Finally, the CID control values were set to be 0, 0.2, 0.3, 0.4, and 0.5. Two coal specimens were selected for each CID control value, and a total of 10 CID coal samples were selected for subsequent triaxial compression tests to study the effects of different CID values on the mechanical properties of CID coal samples. Because the CID value cannot be precisely controlled when the CID coal sample is prefabricated, the coal sample whose CID value is closest to the CID control values should be selected as far as possible. For example, when the CID control value is 0.3, two coal samples with CID value of 0.312 and 0.318 are selected, as shown in Mechanical Testes of Coal With CID.
The surrounding rock in underground excavations usually undergoes multiple and often different stress loading and unloading events, depending mainly on the mining sequence. Considering that the elastic stage has little influence on the damage of coal samples in the compression test, it is necessary to ensure that the coal sample is loaded to the yield stage in order to produce certain damage (Gu et al., 2018; Walton et al., 2019), but the coal pillar is prone to splitting failure at the yield stage (Li et al., 2018). Therefore, according to Huang et al. (2021a) and Huang et al. (2021b), the preparation of the damaged coal samples was carried out using the MTS815 pressure testing machine with circumferential displacement control (to ensure that the coal samples are not be destroyed instantaneously); the loading rate of circumferential displacement was 0.002 mm/s; the circumferential displacement was increased by 1 mm per cycle; the way of axial unloading was controlled by the load; the final unloading was 1 kN; and the unloading rate of axial force was 0.1 kN/s. The loading stress path is shown in Figure 2.
An MTS815 electro-hydraulic servo rock test system was used for the tests. As shown in Figure 3, the test system consists of the loading system, control system, and measurement system. It could provide a maximum axial pressure of 4,600 kN, a maximum confining pressure of 140 MPa, and a minimum sampling interval of 50 μs.
The test procedure was as follows:
1) Activate the MTS815 electro-hydraulic servo test system oil pumps
2) Place the CID samples (3 samples for each group) into the indenter of the testing machine (the preparation method is described in Preparation Method of CID Coal Samples) below. Adjust the position, install the displacement extensometer on the specimen, and then apply 1 kN of axial pre-force to make the two indenters adhere tightly to the sealed specimen.
3) Put down the cylinder of the test machine, open the hydraulic pump, inject hydraulic oil into the triaxial chamber, wait for the hydraulic oil to fill the cylinder and close the intake valve. Constantly apply confining pressure to 2 MPa through the hydraulic system at a rate of 0.05 MPa/s.
4) Apply the load to the specimen. The electro-hydraulic servo displacement control was used to apply the load, thereby increasing the displacement at a rate of 0.002 mm/s. This was continued until the specimen failed
The stress-strain curves of conventional coal samples under uniaxial compression are shown in Figure 4A, and those in tensile tests are shown in Figure 4B.
FIGURE 4. Stress-strain curves of coal samples under (A) uniaxial compression, (B) uniaxial tensile.
Using basic rock mechanics, the physical and mechanical properties of the conventional coal samples were obtained after testing. The test results are shown in Table 1.
Damage variables can well describe the internal damage statue of rock and can quantitatively analyze the occurrence, expansion and damage law of cracks in the process of rock failure. There are many methods to define damage variables, such as effective load area method, sound velocity method, microcrack method, acoustic emission method, elastic modulus method, plastic strain method, CT number method etc., (Basista and Gross 1997; Dhar et al., 1996; Liu et al., 2017; Muzyka, 2018; Gu et al., 2018; Ma et al., 2020), and the local energy release rate (LERR) was proposed to deal with rockbust (Su, 2006). The energy method was used to define CID in the present investigation.
According to the principle of energy conservation, the exchange of heat between the sample and the exterior is not considered during the loading process. Part of the total work done by the hydraulic press is stored inside the sample and is released completely in the form of elastic energy during unloading. The other part of the energy is used for the dissipation of damage and plastic deformation inside the sample. The total work done by the compression is expressed as follows:
where, Ue is the elastic energy stored in the specimen during the loading process, J; and Ud is the energy dissipated during the loading process, J.
In the cyclic loading-unloading full stress-strain curve, U is the area enclosed by the stress-strain curve and the x-axis during the loading process, and Ue is the area enclosed by the stress-strain curve and the x-axis during the unloading process (see in Figure 5.)
FIGURE 5. Sketch map of strain energy of coal sample during loading and unloading (A) the 1st loading-unloading cycle; (B) the ith loading-unloading cycle.
The CID is defined as the ratio of the accumulated plastic energy to the total strain energy of the cycle, as shown in Eq. 2:
where,
where,
According to Eq. 1, the cumulative total strain energy of i cycles can be expressed as:
where,
The accumulated plastic energy and total strain energy can be obtained from the area enclosed by the stress-strain curve and the x-axis in the cyclic loading-unloading test. The CID can be obtained by combining Eqs 2–4 as follows:
According to the definition of the damage variable in Eq. 2, the equivalent values of the total strain energy, the elastic strain energy and the plastic strain energy of coal samples with different degrees of CID are calculated.
As shown in Table 2, the values of all damage variables are in the range of 0–1. The damage variable increases with the increase of loading and unloading times, which indicates that the number of times of cyclic loading can increase the degree of damage, which agrees with the basic properties of rock mechanics.
According to the preparation method of coal samples for CID, the deviatoric stress-strain full-time curves of coal samples with different degrees of CID are shown in Figure 6. It can be seen that the triaxial compression tests of coal sample with different degrees of CID have the following characteristics:
1) According to the characteristics of deviator stress-strain curves, the deviator stress-strain curves of coal samples with different degrees of CID can be divided into a) compression stage, b) linear elastic stage, c) crack growth stage, d) strain softening stage and e) residual strength stage.
2) With the increase of the CID, the compression stage of a coal sample becomes shorter, due to cyclic loading and unloading during the preparation of damaged coal samples, the original cracks and pores in the coal sample are closed and.
3) The strain softening stage of coal samples becomes longer and the failure types of coal samples change from a drop-type failure (brittleness) to a slow failure (ductility) at the peak load with the increase of the CID. This is because the larger the CID, the lower is the internal unit strength of the coal sample that has begun to be destroyed under stress, and new crack defects are formed. When the axial stress reaches the peak load, the fracture development and penetration of the coal sample is more extensive than those of coal samples with the lower value of CID, and the fracture penetration and accumulation will not occur before and after peak load; i.e., the stress-strain curve will drop slowly.
FIGURE 6. Deviatoric stress and strain curves of different CID of coal samples: (A) CID = 0.000; (B) CID = 0.000; (C) CID = 0.237; (D) CID = 0.258; (E) CID = 0.312; (F) CID = 0.318; (G) CID = 0.413; (H) CID = 0.435; (I) CID = 0.500; (J) CID = 0.521.
Based on triaxial compression test data of coal samples with different degrees of CID, each data is divided into 0, 0.1–0.2, 0.2–0.3, 0.3–0.4, 0.4–0.5, 0.5–0.6 ranges to calculate the corresponding average CID and deviatoric stress value. The relationship curve between the deviating stress of coal samples and the CID was obtained.
As can be seen from Figure 7, the relationship between the CID and deviating stress of a coal sample is a quadratic function. With the increase in the initial damage variable value, the deviating stress of the coal sample decreases. When the initial damage variable value is increased from 0 to 0.521, the average deviating stress of coal sample decreases from 34.9 to 23.9 MPa, i.e., a decrease of 31.4%. It can be observed that initial damage has a great influence on the strength of the coal sample. Before the initial damage value exceeds 0.40, the peak deviational stress decreases sharply, and after that the peak deviational stress decreases gradually. This is because the CID makes cracks in the coal sample develop and the bearing capacity of some structures decreases.
Figure 8 illustrates the relationship between the CID and the peak strain of the coal samples is a quadratic function. With an increase in the initial damage variable, the peak strain of the coal samples decreases. When the initial damage variable is increased from 0 to 0.521, the average peak strain of the coal samples decreases from 1.057 to 0.659; a decrease of 37.7%.
According to the triaxial compression stress-strain curves of coal samples with different degrees of CID, the relationship between the volumetric strain and the deviating stress, and the relationship between the deviating stress and the damage variable at the starting point of expansion of the coal samples were extracted.
As for the volumetric strain, the positive value means the sample is under compression condition while the negative value indicates volume expansion state. Also, when the volumetric strain decreases, it means that the specimen is experiencing the process of volumetric expansion; when the volumetric strain increases, it means that the specimen is experiencing the process of volumetric compression. Thus, as shown in Figure 9, the triaxial compression expansion characteristics of coal samples with different degrees of CID had the following characteristics:
1) From the curves of different initial damage degrees and deviating stress, it can be seen that there are strain inflections and expansion starting points in the volume strain. Which indicates that coal samples begin to expand from the compression state, while the expansion starting point indicates that the coal samples begin to expand with initial damage;
2) With the increase in the value of CID, the volume strain at the peak value changes from negative to positive, which indicates that with the increase in the CID, the state of coal sample at the peak value changes gradually from expansion to compression. The faster the dilatation phenomenon occurs before the peak value, the greater the initial damage value, and the less is the inhibition of coal sample dilatation.
3) With the increase in the CID, the deviation stress required for the dilatation of damaged coal sample decreases. The CID is a first-order function of the deviating stress at dilatation.
FIGURE 9. Triaxial compression dilatancy characteristics of coal samples with different degrees of CID: (A) Relationship between volumetric strain and deviating stress; (B) Relationship between deviating stress and damage variable at the starting point of expansion.
Ductility reflects the deformation capacity of coal and rock media from yield point to maximum bearing capacity. By defining the ductility coefficient as the ductility index of the coal and/or rock media, the mechanism of the brittle-ductile transformation of the coal and rock media can be analyzed quantitatively. The expression for the ductility coefficient is as follows (Zhang 2012):
where, εc is the strain at peak stress, and εs is the strain at the 80% stress.
The change in the ductility coefficient with CID is shown in Table 3.
Figure 10 shows that the relationship between the value of the CID and the ductility coefficients of the coal samples is a quadratic function. With an increase in the value of the initial damage variable, the peak strain of the coal samples increases. When the initial damage variable value increased from 0 to 0.521, the ductility coefficient of the coal samples increased from 1.278 to 1.361; an increase of 6.49%. It is evident that an increase in the cumulative effect of the initial damage changed the failure mode of the coal samples and increased their ductility.
A TESCAN VEGA3 Scanning Electron Microscope (SEM) was used to scan the fracture surface of CID coal samples, as shown in Figure 11, which shows images of the microstructural features of coal samples after triaxial compression failure under different values of CID.
FIGURE 11. Microstructure characteristics of cross sections of different CID coal samples: (A) CID = 0; (B) CID = 0.5221.
According to Mao (2018), the brittle fracture of coal and rock sample mainly includes transgranular fracture and intergranular fracture. The main difference between the two fracture is whether the crack develops through the inside of the grain or along the grain boundary. And the main characteristic morphologies of transgranular fracture include cleavage step, lamellar tear fracture and “tongue” pattern. Compared with brittle fracture, ductile fracture is a kind of fracture related to the plastic deformation process of coal and rock. Its main characteristic morphology is dimple which is mainly shown as continuous large pits in the section, and there are significant tearing failure characteristics around the pits. Dimples are formed by the growth and accumulation of cavities within the rock under load, eventually forming macroscopic fracture surfaces.
The failure fracture of coal samples with different CID values showed great differences. In Figure 11, both brittle fracture and ductile fracture can be observed, and some representative morphological features are identified. When CID = 0, the coal sample basically has no initial damage, and its internal structure is complete with strong integrity. After destruction, as shown in Figure 11A, its section is basically brittle fracture with cleavage steps, lamellar tearing and other morphological features, and there are small pits and holes dispersed, but they have not developed into contiguous dimples. When CID = 0.5221, a considerable degree of initial damage has been accumulated in the CID coal sample before loading. Then after triaxial loading, the internal damage further develops. After the failure, as shown in Figure 11B, there are brittle fractures mainly composed of cleavage steps and lamellar tearing in the fracture surface. There are also a large number of ductile fractures, mainly dimples.
This investigation was aimed to study the effect of initial accumulated damage induced by the former mining activities on the further mechanical characteristics of such damaged coal. The energy-based cumulative initial damage variable (CID) is proposed to describe the coal mass behavior with various levels of accumulated damage. With the MTS815 electro-hydraulic servo-controlled loading system, coal samples with various CID value were prepared by cyclic pre-loading and unloading and then the mechanical behavior of these prefabricated CID coal samples, including deformation characteristics, strength, peak strain, dilatancy characteristics and brittle-ductile transformation, was investigated. The main findings are as follows:
1) With the increases of the CID value, the compression stage of the coal samples becomes shorter, while the strain softening stage of the samples becomes longer. In addition, the ductility coefficient increases with the CID value.
2) The relationship between the CID and the strength and peak strain of the coal samples follows the quadratic relationship. The deviation stress and peak strain of coal samples decreases with the increases of the CID. Particularly, when the CID value increased from 0 to 0.521, the strength and peak strain of the coal samples decreased by 31.38 and 37.65%, respectively.
3) The CID has a linear relationship with the expansion deviation stress. The higher of the CID value, the lower of the deviation stress for the expansion of the damaged coal.
4) The cleavage steps dominate the surface morphology feature when the CID equals zero, when the CID value increased to 0.5221, the dimples are the main morphology feature of the fracture. The increase of the CID value results in multiple ‘pits’ on the samples and there are significant tearing characteristics around the pits.
The authors get the full permission from Xiaojihan coal mine for conducting studies and the data usage obtained from the coal mine.
The original contributions presented in the study are included in the article/supplementary material, further inquiries can be directed to the corresponding authors.
SG and PH contributed to conception and design of the study, performed the statistical analysis, drafted the paper and made important revisions to this paper. AJ translated the full text and provided important suggestions. ZW and XD organized the database and performed part of the statistical analysis. All authors contributed to manuscript revision, read, and approved the submitted version.
The following content was added in the “Acknowledgment” Section: This research was funded by the Fundamental Research Funds for the Central Universities (grant number 2020QN05), and in the “Conflict of Interest” section: The authors declare that the research was conducted in the absence of any commercial or financial relationships that could be construed as a potential conflict of interest.
The authors declare that the research was conducted in the absence of any commercial or financial relationships that could be construed as a potential conflict of interest.
The reviewer SZ declared a shared affiliation, though no other collaboration, with several of the authors SG, PH, and ZW to the handling Editor.
All claims expressed in this article are solely those of the authors and do not necessarily represent those of their affiliated organizations, or those of the publisher, the editors and the reviewers. Any product that may be evaluated in this article, or claim that may be made by its manufacturer, is not guaranteed or endorsed by the publisher.
Asanov, V. A., and Pan’kov, I. L. (2004). Deformation of Salt Rock Joints in Time. J. Min. Sci. 40 (4), 355–359. doi:10.1007/s10913-004-0017-5
Bahaaddini, M., Hagan, P. C., Mitra, R., and Hebblewhite, B. K. (2014). Scale Effect on the Shear Behaviour of Rock Joints Based on A Numerical Study. Eng. Geol. 181, 212–223. doi:10.1016/j.enggeo.2014.07.018
Bai, J.-b., Shen, W.-l., Guo, G.-l., Wang, X.-y., and Yu, Y. (2015). Roof Deformation, Failure Characteristics, and Preventive Techniques of Gob-Side Entry Driving Heading Adjacent to the Advancing Working Face. Rock Mech. Rock Eng. 48 (6), 2447–2458. doi:10.1007/s00603-015-0713-2
Basista, M., and Gross, D. (1997). Internal Variable Representation of Microcrack Induced Inelasticity in Brittle Materials. Int. J. Damage Mech. 6 (3), 300–316. doi:10.1177/105678959700600305
Brown, E. T., and Trollope, D. H. (1970). Strength of A Model of Jointed Rock. J. Soil Mech. Found. Div. 96 (2), 685–704. doi:10.1061/jsfeaq.0001411
Chen, J., Kang, Y. F., Liu, W., Fan, J. Y., De, Y. J., and Chemenda, A. (2018). Self-healing Capacity of Damaged Rock Salt with Different Initial Damage. Geomech. Eng. 15 (1), 615–620. doi:10.12989/gae.2018.15.1.615
Chen, J., Gao, J., Pu, Y., Gao, M., Wei, L., Wang, C., et al. (2021). The Rock Burst Hazard Evaluation Using Statistical Learning Approaches. Shock Vib. 2021 (4), 1–11. doi:10.1155/2021/5576480
Coggan, J., Gao, F., Stead, D., and Elmo, D. (2012). Numerical Modelling of the Effects of Weak Immediate Roof Lithology on Coal Mine Roadway Stability. Int. J. Coal Geol. 90-91, 100–109. doi:10.1016/j.coal.2011.11.003
Dhar, S., Sethuraman, R., and Dixit, P. M. (1996). A Continuum Damage Mechanics Model for Void Growth and Micro Crack Initiation. Eng. Fracture Mech. 53 (6), 917–928. doi:10.1016/0013-7944(95)00151-4
Fairhurst, C. E., and Hudson, J. A. (1999). Draft ISRM Suggested Method for the Complete Stress-Strain Curve for the Intact Rock in Uniaxial Compression. Int. J. Rock Mech. Min. 36 (3), 279–289. doi:10.1016/S0148-9062(99)00006-6
Fuenkajorn, K., and Phueakphum, D. (2010). Physical Model Simulation of Shallow Openings in Jointed Rock Mass under Static and Cyclic Loadings. Eng. Geo. 113 (1-4), 81–89. doi:10.1016/j.enggeo.2010.03.003
Gu, Q. H., Ning, J., Tan, Y., Liu, X., Ma, Q., and Xu, Q. (2018). Damage Constitutive Model of Brittle Rock Considering the Compaction of Crack. Geomech. Eng. 15 (5), 1081–1089. doi:10.12989/gae.2018.15.5.1081
Huang, P., Zhang, J., Spearing, A. J. S., Chai, J., and Dong, C. (2021a). Experimental Study of the Creep Properties of Coal Considering Initial Damage. Int. J. Rock Mech. Mining Sci. 139 (4), 104629. doi:10.1016/j.ijrmms.2021.104629
Huang, P., Zhang, J., Jean Damascene, N., Dong, C., and Wang, Z. (2021b). A Fractional Order Viscoelastic-Plastic Creep Model for Coal Sample Considering Initial Damage Accumulation. Alexandria Eng. J. 60 (4), 3921–3930. doi:10.1016/j.aej.2021.02.054
Jiang, B.-y., Gu, S.-t., Wang, L.-g., Zhang, G.-c., and Li, W.-s. (2019). Strainburst Process of Marble in Tunnel-Excavation-Induced Stress Path Considering Intermediate Principal Stress. J. Cent. South. Univ. 26 (4), 984–999. doi:10.1007/s11771-019-4065-z
Jiang, Q., Liu, X., Yan, F., Yang, Y., Xu, D., and Feng, G. (2020). Failure Performance of 3dp Physical Twin-Tunnel Model and Corresponding Safety Factor Evaluation. Rock Mech. Rock Eng. 54 (6), 109–128. doi:10.1007/s00603-020-02244-7
Lachassagne, P., Wyns, R., and Dewandel, B. (2011). The Fracture Permeability of Hard Rock Aquifers Is Due Neither to Tectonics, Nor to Unloading, but to Weathering Processes. Terra Nova 23 (3), 145–161. doi:10.1111/j.1365-3121.2011.00998.x
Li, Y., Zhang, S., and Zhang, B. (2018). Dilatation Characteristics of the Coals with Outburst Proneness under Cyclic Loading Conditions and the Relevant Applications. Geomech. Eng. 14 (5), 459–466. doi:10.12989/gae.2018.14.5.459
Liu, J., Jiang, R., Sun, J., Shi, P., and Yang, Y. (2017). Concrete Damage Evolution and Three-Dimensional Reconstruction by Integrating CT Test and Fractal Theory. J. Mater. Civil Eng. 29 (9), 04017122. doi:10.1061/(ASCE)MT.1943-5533.0001932
Ma, D., Duan, H., Liu, J., Li, X., and Zhou, Z. (2019). The Role of Gangue on the Mitigation of Mining-Induced Hazards and Environmental Pollution: An Experimental Investigation. Sci. Total Environ. 664, 436–448. doi:10.1016/j.scitotenv.2019.02.059
Ma, D., Duan, H., Zhang, Q., Zhang, J., Li, W., Zhou, Z., et al. (2020). A Numerical Gas Fracturing Model of Coupled Thermal, Flowing and Mechanical Effects. Comput. Mater. Con. 65 (3), 2123–2141. doi:10.32604/cmc.2020.011430
Ma, D., Kong, S., Li, Z., Zhang, Q., Wang, Z., and Zhou, Z. (2021a). Effect of Wetting-Drying Cycle on Hydraulic and Mechanical Properties of Cemented Paste Backfill of the Recycled Solid Wastes. Chemosphere 282, 131163. doi:10.1016/j.chemosphere.2021.131163
Ma, D., Zhang, J., Duan, H., Huang, Y., Li, M., Sun, Q., et al. (2021b). Reutilization of Gangue Wastes in Underground Backfilling Mining: Overburden Aquifer Protection. Chemosphere 264 (Pt 1), 128400. doi:10.1016/j.chemosphere.2020.128400
Mao, R. R. (2018). “Study on Tensile Properties and Damage Evolution Mechanism of Coal Measures Sandstone under High Strain Rate,”. Ph.D. Dissertation (Xuzhou, China: China University of Mining and Technology).
Miao, S., Wang, H., Cai, M., Song, Y., and Ma, J. (2018). Damage Constitutive Model and Variables of Cracked Rock in a Hydro-Chemical Environment. Arab J. Geosci. 11 (2), 19. doi:10.1007/s12517-017-3373-6
Muzyka, M. R. (2018). On the Material Damage Evaluation by the Elastic Modulus Deterioration Parameter. Strength Mater. 50 (6), 894–900. doi:10.1007/s11223-019-00037-0
Naghadehi, M. Z. (2015). Laboratory Study of the Shear Behaviour of Natural Rough Rock Joints Infilled by Different Soils. Period. Polytech. Civil Eng. 59 (3), 413–421. doi:10.3311/ppci.7928
Nazarov, L. A., and Nazarova, L. A. (2008). Connection between the Deformation Properties of Rock Joints and Their Fractal Dimension. J. Min. Sci. 44 (5), 429–438. doi:10.1007/s10913-008-0048-4
Pu, Y., Apel, D. B., Prusek, S., Walentek, A., and Cichy, T. (2021). Back-Analysis for Initial Ground Stress Field at a Diamond Mine Using Machine Learning Approaches. Nat. Hazards 105 (1), 191–203. doi:10.1007/s11069-020-04304-1
Guha Roy, D., Singh, T. N., and Kodikara, J. (2017). Influence of Joint Anisotropy on the Fracturing Behavior of a Sedimentary Rock. Eng. Geol. 228, 224–237. doi:10.1016/j.enggeo.2017.08.016
Su, G. Z. (2006). “Study on Stability Analysis and Intelligent Optimization for Large Underground Caverns under High Geostress Condition,”. Ph.D. Dissertation (Wuhan, China: Institute of Rock and Soil Mechanics, Chinese Academy of Sciences).
Walton, G., Labrie, D., and Alejano, L. R. (2019). On the Residual Strength of Rocks and Rockmasses. Rock Mech. Rock Eng. 52, 4821–4833. doi:10.1007/s00603-019-01879-5
Wang, Q., Pan, R., Jiang, B., Li, S. C., He, M. C., Sun, H. B., et al. (2017). Study on Failure Mechanism of Roadway with Soft Rock in Deep Coal Mine and Confined Concrete Support System. Eng. Fail. Anal. 81, 155–177. doi:10.1016/j.engfailanal.2017.08.003
Zhang, J.-x., Huang, P., Zhang, Q., Li, M., and Chen, Z.-w. (2017). Stability and Control of Room Mining Coal Pillars-Taking Room Mining Coal Pillars of Solid Backfill Recovery as an Example. J. Cent. South. Univ. 24 (5), 1121–1132. doi:10.1007/s11771-017-3515-8
Keywords: cumulative initial damage, mechanical behavior, deformation characteristics, an experimental study, damage variable
Citation: Guo S, Huang P, Spearing A, Wang Z and Dong X (2021) An Experimental Study Into the Effects of Cumulative Energy Damage on the Mechanical Properties of Coal. Front. Mater. 8:733391. doi: 10.3389/fmats.2021.733391
Received: 09 July 2021; Accepted: 24 September 2021;
Published: 12 October 2021.
Edited by:
Antonio Caggiano, Darmstadt University of Technology, GermanyReviewed by:
Quan Jiang, Institute of Rock and Soil Mechanics (CAS), ChinaCopyright © 2021 Guo, Huang, Spearing, Wang and Dong. This is an open-access article distributed under the terms of the Creative Commons Attribution License (CC BY). The use, distribution or reproduction in other forums is permitted, provided the original author(s) and the copyright owner(s) are credited and that the original publication in this journal is cited, in accordance with accepted academic practice. No use, distribution or reproduction is permitted which does not comply with these terms.
*Correspondence: Peng Huang, Y3VtdF9ocEAxMjYuY29t
Disclaimer: All claims expressed in this article are solely those of the authors and do not necessarily represent those of their affiliated organizations, or those of the publisher, the editors and the reviewers. Any product that may be evaluated in this article or claim that may be made by its manufacturer is not guaranteed or endorsed by the publisher.
Research integrity at Frontiers
Learn more about the work of our research integrity team to safeguard the quality of each article we publish.