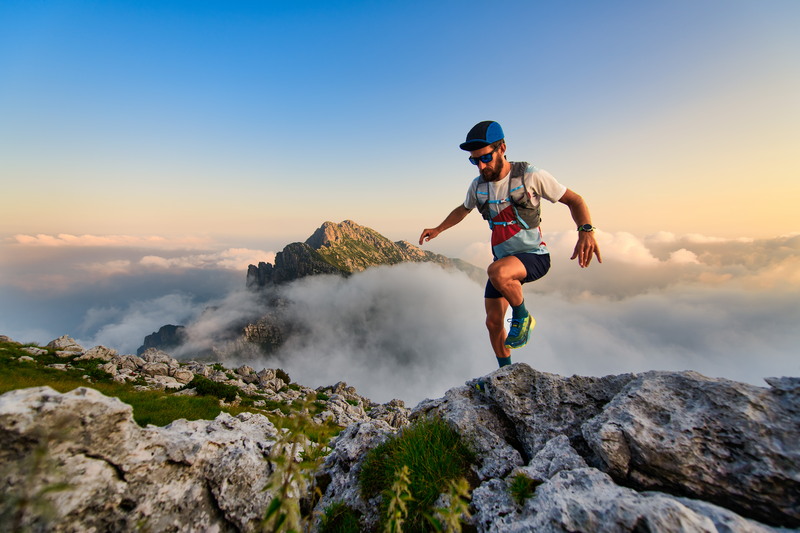
95% of researchers rate our articles as excellent or good
Learn more about the work of our research integrity team to safeguard the quality of each article we publish.
Find out more
ORIGINAL RESEARCH article
Front. Mater. , 16 December 2021
Sec. Environmental Degradation of Materials
Volume 8 - 2021 | https://doi.org/10.3389/fmats.2021.730627
Applying organic coating is an important and effective approach for the protection of metal from corrosion. Weathering degradation and under-film corrosion are the two major important factors that cause the failure of organic coatings. In this work, the degradation investigation of two epoxy coatings (clear and pigmented coatings) was carried out under the dry–wet circulation of three different water fog solutions (deionized water, 0.5 wt% NaCl, 0.05 wt% NaCl + 0.35 wt% (NH4)2SO4) in 35 days. The apparent performance (pull-off adhesion and surface potentials) and electrochemical features [electrochemical noise and electrochemical impedance spectroscopy (EIS)] of the coating samples were monitored after dry–wet fog exposure. In our three accelerating systems of the fog atmosphere, the time that the detectable defects appeared on the surface of coating samples was far ahead in the mixed salt solution than that in the deionized water or 0.5 wt% NaCl solution. For a defective or damaged coating surface, the derived results by using the standard deviation method (SDM) or Fourier power spectrum (FPS) were rather higher than those obtained from EIS as a whole, while for the same coating, the degradation trend with time derived from EIS, SDM, FPS, and scanning Kelvin probe was consistent with each other.
The corrosion of metal materials is a spontaneous process in thermodynamics. Among all corrosion protection approaches, applying a polymer coating is the most effective, economical, and widely used method, especially to protect against atmospheric corrosion of metal substrates. The obstruction ability and insulated shield are two important protection functions of polymer coating (Koehler, 1977; Leidheiser et al., 1983; Morcillo, 1999). Due to the hydrophilic nature of the polymer coating, it cannot completely obstruct the penetration of the corrosive species (H2O, O2, and ions) into the metal substrate. As long as these corrosive species have penetrated into the coating–metal interface, the electrochemical corrosion process will happen on a metal substrate under the coating layer (Leidheiser, 1983; Armstrong et al., 1991).
For a coating that is designed to protect the metal from corrosion, evaluating its durability is important. Many monitoring or assessment methods are used to evaluate the anticorrosion ability of a coating, such as apparent or microscopic methods, electrochemical or spectroscopic, non-destructive or destructive techniques, and in situ monitoring. Initially, the principal apparent performances of the coating aging are the loss of gloss, discolor, pulverization, embrittlement, and cracking after exposure under an atmospheric environment. The aging process and mechanism are well recognized based on the apparent phenomena and the corresponding results after the failure of coating layers (Mckellar and Allen, 1979; Pappas, 1989; Oosterbroek et al., 1991; Armstrong et al., 1995). Later, with the development of electrochemical analysis methods and testing techniques, the testing technology and analytical methods in view of electrochemistry and spectroscopy, such as electrochemical impedance spectroscopy, electrochemical noise measurement, are adopted to elaborate the dynamic mechanism of coating failure.
Electrochemical impedance spectroscopy (EIS) is a primary electrochemical method that is used to study the corrosion behaviors in an interface system between an organic coating layer and metal substrate with some outstanding merits (Mansfeld et al., 1997a). By the testing of EIS, the electrochemical information on the performances and failures of the coating can obtain in a different range of frequencies, for example, solution resistance, electric resistance and capacitance of a coating, and reaction resistance and double-layer capacitance in the coating–metal interface (Mansfeld et al., 1997; Margarit-Mattos, 2020).
Electrochemical noise measurement (ENM) is a non-destructive and non-intrusive technique capable of monitoring basic changes in an electrochemically active coating system (Skerry and Eden, 1991; Mansfeld et al., 1997; Mansfeld et al., 1998; Jamali et al., 2015; Jamali and Mills, 2016). By detecting ENM on a coating–metal system, the corrosion resistance can be quantified by standard deviations in electrochemical potential noise or electrochemical current noise (Murray et al., 1991; Mansfeld et al., 1997a and Mansfeld et al., 1998; Xia et al., 2019).
The scanning Kelvin probe (SKP) is another powerful technique to be used to study the system of a coating and a metal substrate (Stratmann and Streckel, 1990; Stratmann et al., 1991; Leng et al., 1998a; Wapner and Grundmeier, 2004; Wapner et al., 2005; Wapner et al., 2006). The SKP technique allows the non-destructive in situ measurement of electrode potentials of a metal substrate under the coating layer with a high spatial resolution (Leng et al., 1998b; McMurray & Williams, 2002; Olajire, 2018). Using the SKP, the formation and development of cathode and anode zones around the defects of coating samples will be detected by real-time monitoring of electrode potentials, which is effective to predict the early failure, evaluate the performance, and investigate the failure mechanism of a coating (Reddy et al., 2004; Reddy and Sykes, 2005; Rohwerder et al., 2011).
Epoxy is one of the most commonly used organic coatings, especially for a highly corrosive marine environment (Liu et al., 2017; Palimi et al., 2017). In the present study, the degradation investigation of epoxy polyamine coating (clear coating) and epoxy polyamide coating (pigmented coating) was carried out under dry–wet-accelerated fog exposure of different solutions [deionized water, 0.5 wt% NaCl, 0.05 wt% NaCl + 0.35 wt% (NH4)2SO4]. After dry–wet fog exposure, the apparent performance and electrochemical features (EIS, ENM, and SKP) of coating samples were monitored. Through this work, we want to know how much the degradation behaviors of coating samples would differentiate with each other obtained by different electrochemical analytical techniques, and whether these techniques are appropriate to be used to evaluate the coating performance in different degradation periods. The final goal of this study focuses on the suitability and compatibility of various assessment methods that are applied to evaluate the degradation process of organic coatings.
The two most widely used epoxy coatings were selected as representatives of organic coatings in this study: One coating was a clear primer of epoxy polyamine (clear coating) (EPON Resin 828 and EPIKURE Curing Agent 3164), and the other was a yellow primer of epoxy polyamide (pigmented coating) (DeSoto 513 × 419, PPG). In order to achieve faster degradation results, the commercial ground steel Q-panels of (75 × 150)mm with 0.8 mm thickness were used as the metal substrate, instead of an aluminum substrate. The coatings were prepared by using a film applicator (BYK), with the dry film thickness of (47.9 ± 4.8)µm and (34.0 ± 3.9)µm for clear coating and pigmented coatings, respectively. The coatings were cured at 80°C for 2 h in a forced air-drying oven (VWR) after 24-h curing at room temperature.
Three solutions, deionized water, 0.5 wt% sodium chloride, and a mixed salt solution, were chosen as the fog spray solutions. The mixed solution containing 0.05 wt% NaCl (sodium chloride) and 0.35 wt% (NH4)2SO4 (ammonium sulfate) was prepared according to ASTM G85.A5. Before the accelerating experiment of fog spray, the margins of coating samples were sealed by the anticorrosion insulation tape (3M). The cyclic accelerating test was carried out in the Q-FOG cyclic corrosion tester according to ASTM G85.A5. For each spray-fog solution, 1 hour of fog spray and 1 hour of drying were executed alternately between 25 °C and 35 °C for all coating samples in the cyclic corrosion tester. Three samples for each epoxy coating were taken out periodically during the 35 days of immersion time. The pendulum hardness and pull-off adhesion for the coating samples were measured successively with a pendulum hardness tester (BYK) and an adhesion tester (DeFelsko) according to ASTM D4541.
Three different locations of each pair of coating samples were tested by ENM and EIS through a ParaCell electrochemical testing cell and a Reference 600 + Potentiostat (Gamry Instruments). A testing area of 2.85 cm2 could be obtained for each coating sample by means of the ParaCell electrochemical testing cell. After each pair of coating samples was installed, the electrochemical cell was placed in a Faradaic cage to avoid electromagnetic disturbance from external sources. The ambient temperature during the measurements was maintained at 25 °C, and the testing solution was 3.5 wt% NaCl solution. For the ENM testing, the current and potential signals were recorded using a zero-resistance ammeter (ZRA) and a potentiometer with the frequency of 2Hz (ESA410 Data Acquisition, Gamry). After the ENM testing, the same coating sample was under the EIS measurement through the typical three-electrode system with a working area of 2.85 cm2. In addition, the SKP technique (RHC040, KP Technology) was adopted in this study. The Kelvin probe used for this study was 1 mm diameter, and the scanning area of the coating surface was 4000 µmand t µm with the resolution of 200 µm. The samples were kept in the SKP chamber with 95% humidity and room temperature. The coating preparation and testing protocol of this study are summarized in Figure 1.
Although the quality of coatings can be presented in many aspects, the surface appearance is the most direct and visualized way to evaluate the durability of coatings. For the fog solutions of deionized water and 0.5 wt% NaCl, no significant degradation was observed on the coating samples during the 35 days exposure. However, two epoxy coatings experienced a significant gradual deterioration in the exposure of the mixed salts. Some corrosion defects can be observed on the surface of the clear coating after 3 days of exposure while the defects appeared after 15 days for the pigmented coating.
For the gloss change of the coatings, as shown in Figure 2, the gloss of two epoxy coatings degraded less in the fog atmosphere of deionized water and 0.5 wt% NaCl solution than that in the mixed salt fog. It means that the mixed salt solution of 0.05 wt% NaCl + 0.35 wt% (NH4)2SO4 is more corrosive to the coating degradation than deionized water or 0.5 wt% NaCl solution. For this fog spray testing, both epoxy coatings cannot endure the fog corrosion of mixed salt under a cyclic accelerating atmosphere. It demonstrates that the synergistic effect is achieved by adding sulfate solution in an atmosphere of chloride solution, which obviously accelerates the coating degradation and the underneath steel corrosion (Morcillo, 1999; de la Fuente et al., 2007).
FIGURE 2. Gloss of two epoxy coatings during the fog spray of three different solutions. (A)Clear coating. (B) Pigmented coating.
The hardness of coatings is the most important factor affecting the abrasion and scratch resistance of coatings. The pendulum damping test has been found to have a good sensitivity in detecting the coating hardness, where hardness is defined as the resistance to deformation (Dashtizadeh et al., 2011; Boumaza et al., 2016; Samad et al., 2018). As for both epoxy coatings studied in this work, there is no significant change of the pendulum hardness as a function of time under the accelerating fog atmosphere of deionized water and 0.5 wt% NaCl solution. However, for the mixed salt solution, the pendulum hardness of clear coating degraded rapidly in the very beginning of fog spray and was kept at a low value after 10 days; the pendulum hardness of pigmented coating began to drop sharply after 20 days of fog spray (Figure 3).
FIGURE 3. Pendulum hardness of two epoxy coatings during the fog spray of three different solutions. (A) Clear coating. (B) Pigmented coating.
Pull-off adhesion can be used to evaluate the pull-off strength of a coating/metal system. During the exposure, the pull-off adhesion of clear coatings exhibited a slight decline under the fog spray of deionized water and 0.5 wt% NaCl solution, while it decreased rapidly in the mixed salt fog. After 15 days of the fog spray, about 75% adhesion was lost in the mixed salt fog for the clear coating. As for the pigmented coating, the pull-off adhesion was decreased by around 200psi under the fog atmosphere of deionized water and 0.5 wt% NaCl solution during the exposure period (Figure 4). Under the fog spray of mixed salt solutions, the adhesion decreased gradually and almost lost the total adhesion at the end of the exposure. Therefore, the pull-off adhesion demonstrates clearly that the destroying power of the mixed salt fog is significantly stronger than that of the deionized water or 0.5 wt% NaCl solution fog.
FIGURE 4. Pull-off adhesion of two epoxy coatings during the fog spray of three different solutions. (A) Clear coating. (B) Pigmented coating.
EIS is the most commonly used and powerful tool that can evaluate the anticorrosion ability of organic coatings by using a system of electrochemical measurement and validation. The coating samples were picked up periodically for EIS measurement during the exposure test. The impedance modulus of EIS spectra at 0.01 Hz (|Z|0.01) is studied representing the corrosion resistance of the coatings. This value is not influenced by the testing conditions and is not generated by modeling. This is the impedance modulus of the coating at 0.01 Hz. This analysis has been widely used by other researchers since 20 years ago (Bierwagen et al., 2000; Thu et al., 2001; Hinderliter et al., 2008). Here, the EIS data at a frequency of 0.01Hz (|Z|0.01) were chosen to present the corrosion resistance of the coating after the exposure of different salt fogs. The |Z|0.01 values of the two coatings dropped significantly at the beginning of the fog spray and then reached a stable stage (Figure 5). Thereinto, the |Z|0.01 value was maintained over 106Ω for two epoxy coatings after the fog spray of deionized water or 0.5 wt% NaCl solution, which means that both epoxy coatings can hold a good capability of anticorrosion after the 35-day fog spray of the two solutions (Shreepathi et al., 2011). However, the |Z|0.01 values of coating samples decreased quickly to be lower than 105Ω or even less within 3 days in the mixed salt fog spray. It means that the coating after the mixed salt fog spray has largely lost its ability for corrosion protection, for example, the epoxy coatings cannot endure the long-period corrosion by the fog atmosphere of 0.05 wt% NaCl + 0.35 wt% (NH4)2SO4.
FIGURE 5. |Z|0.01 of coating samples as a function of exposure in the fog spray of three solutions. (A) Clear coatings. (B) Pigmented coatings.
Electrochemical noise measurement is a non-destructive and non-intrusive technique capable of monitoring basic changes in an electrochemically active coating system. The common method of collecting ENM data is by measuring the current fluctuations between two nominally identical electrodes at their open circuit potential (OCP) while connecting through a ZRA. There are many methods for the quantitative analysis of ENM data (Homborg et al., 2014; Jamali and Mills, 2016). The basic quantitative method of noise data can be obtained through the standard deviation method (SDM) of potential and current fluctuations in the time domain. To transfer the time domain data to the frequency domain, the majorly used methods include fast Fourier transform (FFT), Fourier power spectrum (FPS), and maximum entropy method (MEM) algorithms.
In order to understand the anticorrosion behavior of the epoxy coatings under the fog spray of different solutions, the electrochemical noise data of the two coating samples were acquired and analyzed using the SDM and FPS methods. Based on the results illustrated in Figures 6, 7, the deterioration trend of two epoxy coatings obtained by the SDM and FPS methods showed a similar variation as those by EIS as a whole. Similarly, the anticorrosive ability of two epoxy coatings dropped quickly at the initial stage of fog spray, and the corrosion resistance kept at a rather higher level in deionized water or 0.5 wt% NaCl solution than that in the mixed salt solution after the 35-day fog spray.
FIGURE 6. RSDM of coating samples as a function of exposure in the fog spray of three solutions. (A) Clear coating. (B) Pigmented coating.
FIGURE 7. RFPS of coating samples as a function of exposure in the fog spray of three solutions. (A) clear coating. (B) pigmented coating.
As shown in Figures 5–7, it also found that the RSDM values of two epoxy coatings were roughly equivalent to the impedance results of EIS, while the RFPS values were generally higher by one or two orders of magnitude than those by the EIS and SDM methods. It seems that the FPS method was not always feasible to process the ENM data for assessing the anticorrosion performance of organic coating samples after the dry–wet cycle exposure of salt fog.
The anticorrosion performance of a coating layer can be demonstrated through the surface potential of the coating–metal interface (Leng et al., 1998c; Nazarov et al., 2008; Rohwerder et al., 2011). Through SKP, the delamination reaction can be analyzed as a function of the water activity, the type and activity of cations and anions, the electrolyte concentration, and the oxygen partial pressure in the atmosphere (Stratmann et al., 1996; Leng et al., 1998b; Nazarov et al., 2008; Rohwerder et al., 2011; Upadhyay and Battocchi, 2016; Nazarov et al., 2018). Based on the SKP results (Figure 8), the SKP work function of two epoxy coatings showed a slight decline as a function of time during the fog spray exposure of deionized water or 0.5 wt% NaCl solution, while it decreased rapidly in the mixed salt fog. In addition, while using deionized water or 0.5 wt% NaCl solution, the work function can keep up at a region of -100mV ∼ -700mV with a mean value of about -420mV for the single solution, while the work function varied from -200mV to -1050mV with a mean value of about -700mV for the mixed salt solution. It means that the surface status of two epoxy coatings during the fog spray of a single solution (deionized water or 0.5 wt% NaCl solution) was more stable than that in the mixed salt solution, and the coating resistibility to delamination and corrosion would decrease faster in the fog spray of the mixed salt solution.
FIGURE 8. Surficial work function of epoxy coating samples as a function of exposure in the fog spray of three solutions by SKP. (A) deionized water fog; (B) 0.5 wt% NaCl fog; (C) mixed salt fog.
Coating degradation is an electrochemical process essentially; thus, the monitoring techniques and data analytical methods deduced from the electrochemical theory or process are used constantly to evaluate the coating degradation behavior.
Compared the EIS (|Z|0.01) results with the ENM results deduced by SDM and FPS, the ENM values obtained by using different data-processing methods of electrochemical signals differed much with each other. For a perfect coating, the results of SDM agreed well with those of EIS, and the results of FPS showed slightly higher than those from EIS and SDM. Meanwhile, for a coating with some defects or badly damaged sites on the coating surface after the salt fog spray, the results of SDM and FPS were much higher than those of EIS as a whole. It means that although the ENM method has been widely utilized for assessing the effectiveness of a coating layer and to distinguish the onset of corrosion due to its high sensitivity to the changes at the coating–metal interface (Conners et al., 2000; Deyá et al., 2013; Jalami and Mills, 2016), the derived results from ENM are not always satisfactory to process strong signals of electrochemical noise when some significant defects exist on a coating sample.
As an analytical technique for localized information, the SKP is an efficient tool to measure the metallic potential under a coating layer in the atmosphere (Stratmann and Streckel, 1990; Stratmann et al., 1991) and further to monitor the formation and development of cathode and anode zones and their developing change (Leng et al., 1998a; Wapner and Grundmeier, 2004; Reddy and Sykes, 2005; Oehler et al., 2012). Generally, the testing areas of EIS and ENM are relatively larger than those when using the SKP, and SKP can provide localized information on the status of the coating surface. Nevertheless, they all demonstrated that the coatings degraded faster in the mixed salt fog.
The presence of chlorides and sulfates at the metal–coating interface is well known to have a joint destructive effect on the integrity of most coating systems. In our coatings, some visible defects appeared on the surface of the two coatings in the first 3 days in the mixed salt solution, while no visible defects were observed even after 35-day fog spray in deionized water or 0.5 wt% NaCl solution. Osmotic blistering and under-film corrosion are deemed to be two primary degradation mechanisms when water-soluble mixed contaminants present at the metal–coating interface (Bastidas et al., 1998; Morcillo, 1999). One of the reasons is that the presence of water-soluble salt at the metal–coating interface can accelerate the absorbing rate of water molecules through decreasing the critical relative humidity of the condensation of the water vapor. Another reason is that the water-soluble salt is able to take catalytic and accelerating effects by participating in corrosion reaction (Morcillo et al., 1997; de la Fuente et al., 2007). Consequently, the loss of adhesion, cathodic disbondment, scribe creep, and a decrease in the adhesion/cohesion strength can be observed clearly for a coating in a short time exposure in the fog atmosphere of the mixed salt solution. This also shows again the powerful synergistic destruction of mixed salts on a metal/coating system.
For a complicated coating system, any variation of a coating parameter is not independent. It will be correlated with other environmental factors, which can be deduced by the correlation method. Correlation analysis is based on Pearson or Spearman product moment coefficients (Zheng et al., 2012). The corresponding correlation results can be presented in covariance correlation matrices; the strength of the relationship between any pair of variables can be estimated through correlation analysis (Evans, 1996; Reimann et al., 2017).
From Tables 1, 2, based on the correlation analysis of the results from different characterization methods, it can be concluded that 1) the EIS results are very well consistent with SDM data of ENM in assessing the coating degradation; 2) the high correlation of gloss, hardness, adhesion, and SKP show significant agreement with each other, which means the degradation characteristics of the coatings are similar as deducing from different measurements; 3) even for a bad coating sample with defects or badly damaged sites, the coating degradation traits deduced from EIS, SDM, FPS, and SKP changed consistently with each other, although the actual values of each parameter were much different for the same coating samples.
The organic coating is an important means of corrosion protection. Weathering degradation and under-film corrosion are the two most important factors that cause the failure of organic coatings. In our three accelerating systems of fog atmosphere, namely, deionized water, 0.5 wt% NaCl, and 0.05 wt% NaCl + 0.35 wt% (NH4)2SO4, the coating degraded earlier in the fog atmosphere of the mixed salt solution than the other two solutions, which illuminated the strong synergistic destruction effect of chlorides and sulfates on the coating degradation.
For evaluating the degradation trend of a coating sample with time, although the actual values of each parameter derived from EIS, SDM, FPS, and SKP differentiated slightly for the same coating sample, the derived degradation trend changed consistently with each other according to the results of correlation analysis. It means that all these assessment methods are feasible to monitor the coating degradation. ENM cannot always provide satisfactory results when the coating is under a serious degradation Hoffmann and Stratmann, 1993, Posner et al., 2009.
The original contributions presented in the study are included in the article/Supplementary Material, and further inquiries can be directed to the corresponding authors.
JZ and QZ contributed to conceptualization and methodology; BZ and QZ helped with software; JZ and QZ validated the study; JZ, BZ, and QZ assisted with formal analysis; JZ, HW, WZ, and CZ assisted with investigation; JZ and QZ procured resources; JZ, BZ, and QZ helped with data curation; JZ and BZ contributed to writing—original draft preparation; JZ, HW, and QZ contributed to writing—review and editing; JZ and QZ supervised the study; JZ and QZ helped with project administration; and JZ and QZ acquired funding. All authors have read and agreed to the published version of the manuscript.
The authors declare that the research was conducted in the absence of any commercial or financial relationships that could be construed as a potential conflict of interest.
All claims expressed in this article are solely those of the authors and do not necessarily represent those of their affiliated organizations, or those of the publisher, the editors, and the reviewers. Any product that may be evaluated in this article, or claim that may be made by its manufacturer, is not guaranteed or endorsed by the publisher.
The authors acknowledge the support from the faculty start-up funding from the University of Akron. The authors also appreciate the support from the Science and Technology Plan Project of Guangdong Province (2016A020225004), China, and the Research and Development Projects in Key Areas of Guangdong Province (2020B1111020004), China.
The Supplementary Material for this article can be found online at: https://www.frontiersin.org/articles/10.3389/fmats.2021.730627/full#supplementary-material
Armstrong, R. D., Jenkins, A. T. A., and Johnson, B. W. (1995). An Investigation into the UV Breakdown of Thermoset Polyester Coatings Using Impedance Spectroscopy. Corrosion Sci. 37 (10), 1615–1625. doi:10.1016/0010-938x(95)00063-p
Armstrong, R. D., Johnson, B. W., and Wright, J. D. (1991). An Investigation into the Cathodic Delamination of Epoxy-Polyamine Protective Coatings. Electrochimica Acta 36 (13), 1915–1923. doi:10.1016/0013-4686(91)85073-g
Bastidas, J. M., Morcillo, M., and Rodríguez, F. J. (1998). Mild Steel Corrosion in saline Solutions. Comparison between Bulk Solutions and Steel-Coating Interfacial Solutions. J. Coat. Tech. 70, 61–66. doi:10.1007/bf02720516
Bierwagen, G. P., He, L., Li, J., Ellingson, L., and Tallman, D. E. (2000). Studies of a New Accelerated Evaluation Method for Coating Corrosion Resistance - thermal Cycling Testing. Prog. Org. Coat. 39, 67–78. doi:10.1016/s0300-9440(00)00106-5
Boumaza, M., Khan, R., and Zahrani, S. (2016). RETRACTED: An Experimental Investigation of the Effects of Nanoparticles on the Mechanical Properties of Epoxy Coating. Thin Solid Films 620, 160–164. doi:10.1016/j.tsf.2016.09.035
Conners, K. D., van Ooij, W. J., Mills, D. J., and Bierwagen, G. P. (2000). Comparison of Electrochemical Impedance Spectroscopy and Electrochemical Noise Measurement of Plasma Polymerised Films as Pretreatment for Cold Rolled Steel. Br. Corrosion J. 35, 141–144. doi:10.1179/000705900101501173
Dashtizadeh, A., Abdouss, M., Mahdavi, H., and Khorassani, M. (2011). Acrylic Coatings Exhibiting Improved Hardness, Solvent Resistance and Glossiness by Using Silica Nano-Composites. Appl. Surf. Sci. 257, 2118–2125. doi:10.1016/j.apsusc.2010.09.060
de la Fuente, D., Bohm, M., Houyoux, C., Rohwerder, M., and Morcillo, M. (2007). The Settling of Critical Levels of Soluble Salts for Painting. Prog. Org. Coat. 58, 23–32. doi:10.1016/j.porgcoat.2006.11.003
Deyá, M. C., del Amo, B., Spinelli, E., and Romagnoli, R. (2013). The Assessment of a Smart Anticorrosive Coating by the Electrochemical Noise Technique. Prog. Org. Coat. 76, 525–532. doi:10.1016/j.porgcoat.2012.09.014
Evans, J. D. (1996). Straightforward Statistics for the Behavioral Sciences. Pacific Grove (CA): Brooks/Cole Publishing.
Hinderliter, B. R., Allahar, K. N., Bierwagen, G. P., Tallman, D. E., and Croll, S. G. (2008). Water Sorption and Diffusional Properties of a Cured Epoxy Resin Measured Using Alternating Ionic Liquids/aqueous Electrolytes in Electrochemical Impedance Spectroscopy. J. Coat. Technol. Res. 5, 431–438. doi:10.1007/s11998-008-9107-7
Hoffmann, K., and Stratmann, M. (1993). The Delamination of Organic Coatings from Rusty Steel Substrates. Corrosion Sci. 34 (10), 1625–1645. doi:10.1016/0010-938x(93)90037-h
Homborg, A. M., Tinga, T., van Westing, E. P. M., Zhang, X., Ferrari, G. M., de Wit, J. H. W., et al. (2014). A Critical Appraisal of the Interpretation of Electrochemical Noise for Corrosion Studies. Corrosion 70, 971–987. doi:10.5006/1277
Jamali, S. S., and Mills, D. J. (2016). A Critical Review of Electrochemical Noise Measurement as a Tool for Evaluation of Organic Coatings. Prog. Org. Coat. 95, 25–37. doi:10.1016/j.porgcoat.2016.02.016
Jamali, S. S., Mills, D. J., and Cottis, R. A. (2015). “Analysis of Electrochemical Noise Measurement on an Organically Coated Metal,” in Application of Electrochemical Technology to Organic Coatings. Editor S. Touzain (La RochelleFrance: European Federation of Corrosion).
Koehler, E. L. (1977). The Influence of Contaminants on the Failure of Protective Organic Coatings on Steel. Corrosion 33 (6), 209–217. doi:10.5006/0010-9312-33.6.209
Le Thu, Q., Bierwagen, G. P., and Touzain, S. (2001). EIS and ENM Measurements for Three Different Organic Coatings on Aluminum. Prog. Org. Coat. 42, 179–187. doi:10.1016/s0300-9440(01)00171-0
Leidheiser, H., Wang, W., and Igetoft, L. (1983). The Mechanism for the Cathodic Delamination of Organic Coatings from a Metal Surface. Prog. Org. Coat. 11, 19–40. doi:10.1016/0033-0655(83)80002-8
Leng, A., Streckel, H., and Stratmann, M. (1998a). The Delamination of Polymeric Coatings from Steel. Part 1: Calibration of the Kelvinprobe and Basic Delamination Mechanism. Corrosion Sci. 41 (3), 547–578. doi:10.1016/s0010-938x(98)00166-8
Leng, A., Streckel, H., and Stratmann, M. (1998b). The Delamination of Polymeric Coatings from Steel. Part 2: First Stage of Delamination, Effect of Type and Concentration of Cations on Delamination, Chemical Analysis of the Interface. Corrosion Sci. 41 (3), 579–597. doi:10.1016/s0010-938x(98)00167-x
Leng, A., Streckel, H., and Stratmann, M. (1998c). The Delamination of Polymeric Coatings from Steel. Part 3: Effect of the Oxygen Partial Pressure on the Delamination Reaction and Current Distribution at the Metal/polymer Interface. Corrosion Sci. 41 (3), 598–620. doi:10.1016/s0010-938x(98)00168-1
Liu, J., Zhang, L., Mu, X., and Zhang, P. (2017). Studies of Electrochemical Corrosion of Low alloy Steel under Epoxy Coating Exposed to Natural Seawater Using the WBE and EIS Techniques. Prog. Org. Coat. 111, 315–321. doi:10.1016/j.porgcoat.2017.06.012
Mansfeld, F., Han, L. T., Lee, C. C., Chen, C., Zhang, G., and Xiao, H. (1997a). Analysis of Electrochemical Impedance and Noise Data for Polymer Coated Metals. Corrosion Sci. 39 (2), 255–279. doi:10.1016/s0010-938x(97)83346-x
Mansfeld, F., Lee, C. C., and Zhang, G. (1998). Comparison of Electrochemical Impedance and Noise Data in the Frequency Domain. ElectrochimicaActa 43 (3-4), 435–438. doi:10.1016/s0013-4686(97)00060-1
Mansfeld, F., Xiao, H., Han, L. T., and Lee, C. C. (1997b). Electrochemical Impedance and Noise Data Fo Rpolymer Coated Steel Exposed at Remote marine Test Sites. Prog. Org. Coat. (30), 89–100. doi:10.1016/s0300-9440(96)00675-3
Margarit-Mattos, I. C. P. (2020). EIS and Organic Coatings Performance: Revisiting Some Key Points. Electrochimica Acta 354, 136725. doi:10.1016/j.electacta.2020.136725
Mckellar, J. F., and Allen, N. S. (1979). Photochemistry of Man Made Polymers. London: Applied Science Publishers Ltd.
McMurray, H. N., and Williams, G. (2002). Probe Diameter and Probe-Specimen Distance Dependence in the Lateral Resolution of a Scanning Kelvin Probe. J. Appl. Phys. 91, 1673–1679. doi:10.1063/1.1430546
Morcillo, M., Rodrı́guez, F. J., and Bastidas, J. M. (1997). The Influence of Chlorides, Sulphates and Nitrates at the Coating-Steel Interface on Underfilm Corrosion. Prog. Org. Coat. 31, 245–253. doi:10.1016/s0300-9440(97)00083-0
Morcillo, M. (1999). Soluble Salts: Their Effect on Premature Degradation of Anticorrosive Paints. Prog. Org. Coat. 36, 137–147. doi:10.1016/s0300-9440(99)00036-3
Nazarov, A., Le Bozec, N., and Thierry, D. (2018). Scanning Kelvin Probe Assessment of Steel Corrosion protection by marine Paints Containing Zn-Rich Primer. Prog. Org. Coat. 125, 61–72. doi:10.1016/j.porgcoat.2018.08.024
Nazarov, A., Prosek, T., and Thierry, D. (2008). Application of EIS and SKP Methods for the Study of the Zinc/polymer Interface. Electrochimica Acta 53, 7531–7538. doi:10.1016/j.electacta.2007.11.053
Oehler, H., Alig, I., Lellinger, D., and Bargmann, M. (2012). Failure Modes in Organic Coatings Studied by Scanning Acoustic Microscopy. Prog. Org. Coat. 74, 719–725. doi:10.1016/j.porgcoat.2011.09.017
Olajire, A. A. (2018). Recent Advances on Organic Coating System Technologies for Corrosion protection of Offshore Metallic Structures. J. Mol. Liquids 269, 572–606. doi:10.1016/j.molliq.2018.08.053
Oosterbroek, M., Larmmers, R. J., Van der Ven, L. G. J., and Perera, D. Y. (1991). Crack Formation and Stress Development in an Organic Coating. J. Coating Tech. 63 (799), 55–60.
Palimi, M. J., Alibakhshi, E., Bahlakeh, G., Ramezanzadeh, B., and Mahdavian, M. (2017). Electrochemical Investigations of the Corrosion Protection Properties of an Epoxy-Ester Coating Filled with Cerium Acetyl Acetonate Anticorrosive Pigment. J. Electrochem. Soc. 164, C709–C716. doi:10.1149/2.0231713jes
Pappas, S. P. (1989). Weathering of Coatings - Formulation and Evaluation. Prog. Org. Coat. 17, 107–114. doi:10.1016/0033-0655(89)80017-2
Posner, R., Giza, G., Vlasak, R., and Grundmeier, G. (2009). In Situ electrochemical Scanning Kelvin Probe Blister-Test Studies of the De-adhesion Kinetics at Polymer/zinc Oxide/zinc Interfaces. Electrochimica Acta 54, 4837–4843. doi:10.1016/j.electacta.2009.03.089
Reddy, B., Doherty, M. J., and Sykes, J. M. (2004). Breakdown of Organic Coatings in Corrosive Environments Examined by Scanning Kelvin Probe and Scanning Acoustic Microscopy. Electrochimica Acta 49, 2965–2972. doi:10.1016/j.electacta.2004.01.055
Reddy, B., and Sykes, J. M. (2005). Degradation of Organic Coatings in a Corrosive Environment: a Study by Scanning Kelvin Probe and Scanning Acoustic Microscope. Prog. Org. Coat. 52, 280–287. doi:10.1016/j.porgcoat.2004.04.004
Reimann, C., Filzmoser, P., Hron, K., Kynčlová, P., and Garrett, R. G. (2017). A New Method for Correlation Analysis of Compositional (Environmental) Data - a Worked Example. Sci. Total Environ. 607-608, 965–971. doi:10.1016/j.scitotenv.2017.06.063
Rohwerder, M., Isik-Uppenkamp, S., and Amarnath, C. A. (2011). Application of the Kelvin Probe Method for Screening the Interfacial Reactivity of Conducting Polymer Based Coatings for Corrosion protection. Electrochimica Acta 56, 1889–1893. doi:10.1016/j.electacta.2010.09.098
Samad, U. A., Alam, M. A., Chafidz, A., Al-Zahrani, S. M., and Alharthi, N. H. (2018). Enhancing Mechanical Properties of Epoxy/polyaniline Coating with Addition of ZnO Nanoparticles: Nanoindentation Characterization. Prog. Org. Coat. 119, 109–115. doi:10.1016/j.porgcoat.2018.02.018
Shreepathi, S., Guin, A. K., Naik, S. M., and Vattipalli, M. R. (2011). Service Life Prediction of Organic Coatings: Electrochemical Impedance Spectroscopy vs Actual Service Life. J. Coat. Technol. Res. 8 (2), 191–200. doi:10.1007/s11998-010-9299-5
Skerry, B. S., and Eden, D. A. (1991). Characterisation of Coatings Performance Using Electrochemical Noise Analysis. Prog. Org. Coat. 19, 379–396. doi:10.1016/0033-0655(91)80019-f
Stratmann, M., Leng, A., Furbeth, W., Streckel, H., Gehmecker, H., and Groβe-Brinkhaus, K.-H. (1996). The Scanning Kelvin Probe: a New Technique for the In Situ Analysis of the Delamination of Organic Coatings. Prog. Org. Coat. 27, 216–267. doi:10.1016/0300-9440(94)00542-7
Stratmann, M., Streckel, H., and Feser, R. (1991). A New Technique Able to Measure Directly the Delamination of Organic Polymer Films. Corrosion Sci. 32 (4), 467–470. doi:10.1016/0010-938x(91)90126-a
Stratmann, M., and Streckel, H. (1990). On the Atmospheric Corrosion of Metals Which Are Covered with Thin Electrolyte Layers — I. Verification of the Experimental Technique. Corrosion Sci. 30 (6-7), 681–696. doi:10.1016/0010-938x(90)90032-z
Upadhyay, V., and Battocchi, D. (2016). Localized Electrochemical Characterization of Organic Coatings: A Brief Review. Prog. Org. Coat. 99, 365–377. doi:10.1016/j.porgcoat.2016.06.012
Wapner, K., and Grundmeier, G. (2004). Scanning Kelvin Probe Measurements of the Stability of Adhesive/metal Interfaces in Corrosive Environments. Adv. Eng. Mater. 6, 163–167. doi:10.1002/adem.200300579
Wapner, K., Schoenberger, B., Stratmann, M., and Grundmeier, G. (2005). Height-regulating Scanning Kelvin Probe for Simultaneous Measurement of Surface Topology and Electrode Potentials at Buried Polymer/metal Interfaces. J. Electrochem. Soc. 152 (3), E114–E122. doi:10.1149/1.1856914
Wapner, K., Stratmann, M., and Grundmeier, G. (2006). In Situ infrared Spectroscopic and Scanning Kelvin Probe Measurements of Water and Ion Transport at Polymer/metal Interfaces. Electrochimica Acta 51, 3303–3315. doi:10.1016/j.electacta.2005.09.024
Xia, D-H., Song, Y., Song, S., Behnamian, Y., Xu, L., Wu, Z., et al. (2019). Identifying Defect Levels in Organic Coatings with Electrochemical Noise (EN) Measured in Single Cell (SC) Mode. Prog. Org. Coat. 126, 53–61. doi:10.1016/j.porgcoat.2018.10.027
Keywords: degradation behavior, electrochemical characterization, epoxy coatings, salt fog exposure, apparent performance
Citation: Zhang J, Zhu B, Wang H, Zhang C, Zeng W and Zhou Q (2021) Degradation Behaviors of Two Epoxy Coatings After Dry/Wet-Accelerated Fog Exposure of Different Solutions. Front. Mater. 8:730627. doi: 10.3389/fmats.2021.730627
Received: 25 June 2021; Accepted: 24 November 2021;
Published: 16 December 2021.
Edited by:
Ram Gupta, Pittsburg State University, United StatesReviewed by:
Benjamin Salas Valdez, Autonomous University of Baja California, MexicoCopyright © 2021 Zhang, Zhu, Wang, Zhang, Zeng and Zhou. This is an open-access article distributed under the terms of the Creative Commons Attribution License (CC BY). The use, distribution or reproduction in other forums is permitted, provided the original author(s) and the copyright owner(s) are credited and that the original publication in this journal is cited, in accordance with accepted academic practice. No use, distribution or reproduction is permitted which does not comply with these terms.
*Correspondence: Jibiao Zhang, emhhbmdqYkBnZG91LmVkdS5jbg==; Qixin Zhou, cXpob3VAdWFrcm9uLmVkdQ==
Disclaimer: All claims expressed in this article are solely those of the authors and do not necessarily represent those of their affiliated organizations, or those of the publisher, the editors and the reviewers. Any product that may be evaluated in this article or claim that may be made by its manufacturer is not guaranteed or endorsed by the publisher.
Research integrity at Frontiers
Learn more about the work of our research integrity team to safeguard the quality of each article we publish.