- 1Jiangxi Key Laboratory of Surface Engineering, Jiangxi Science and Technology Normal University, Nanchang, China
- 2Hypergravity Research Center of Zhejiang University, Zhejiang University, Hangzhou, China
- 3Shanghai Institute of Ceramics, Chinese Academy of Sciences, Shanghai, China
The iso-thermal oxidation of the quaternary Co-20Re-25Cr-3Si alloy at 1,000–1,200 C under laboratory air for 24 h has been studied. The oxidation kinetics at 1,000–1,200 C follow parabolic law perfectly and the value of oxidation activation energy is 220.74 kJ/mol. Unlike the experimental condition of 0.1 MPa pure oxygen, under laboratory air Co-20Re-25Cr-3Si alloy presents a good oxidation resistance due to the formation of a dense and continuous layer of Cr2O3 in contact with the alloy. A 79% drop in oxygen pressure has changed the oxidation mode from catastrophic oxidation to mild oxidation. The thickness of the protective Cr2O3 layer decreases when temperature increases. Therefore, Co-20Re-25Cr-3Si alloy shows the best oxidation resistance at 1,000 C. Moreover, from another perspective, compared with Co-17Re-23Cr-3Si alloy, the addition of about 2% Cr can also improve the oxidation resistance of the alloy greatly by forming the protective Cr2O3 layer.
Introduction
Superalloys are widely used in many fields such as aero engines, automobile engines, gas turbines, nuclear power, petrochemical industry, etc., and play an important role in economic development by virtue of its excellent oxidation and thermal corrosion resistance (Beran et al., 2016; Gorunov, 2017; Vorobiov et al., 2014; Shi and Zhong, 2010; Wanderka et al., 2016). The temperature in service of iron based superalloys can generally reach up to 750–780 C, while that of nickel based and refractory metal based alloys may be much higher. In fact, the application of nickel-based superalloys is limited to below 1,000 C due to their melting point (Perepezko, 2009; Gorr et al., 2011). In recent years, people pay more attention to low energy consumption and environmental protection, and pursue higher energy efficiency and less CO2 emissions. Therefore, they hope to develop superalloys that can serve at higher temperatures (Mukherji et al., 2012; Gorr et al., 2014a; Gorr et al., 2014b). In particular, cobalt-based alloys have received extensive attention in recent decades due to their high temperature strength, good thermal corrosion resistance and oxidation resistance (Gorr et al., 2012; Wang et al., 2015a).
Adding high melting point metal Re to Co based alloy can greatly improve the melting point of Co based alloy, and the high temperature strength of the alloy can also be adjusted conveniently by adding appropriate amount of Re or other elements (Rösler et al., 2007; Gorr et al., 2014a; Beran et al., 2018; Strunz et al., 2018). Rösler et al. (Rösler et al., 2007) first proposed Co-Re-based superalloys because of their potential applications over 1,200 C. However, a significant disadvantage of metal Re is that at high temperatures the element Re may evaporate in the form of ReO3, resulting in mass loss of the alloy (Gorr et al., 2011). Adding a certain amount of Cr can form a protective Cr2O3 layer on the alloys, which limits the evaporation of rhenium oxides (Gorr et al., 2011; Mukherji et al., 2012). It was found that the oxide film Cr2O3 gradually lost its protective effect as the temperature increased, due to the rapid transformation of the oxide film Cr2O3 into gaseous CrO3 at high temperature (Gorr et al., 2014a; Gorr et al., 2012). The present of Si can provide nucleation site for the formation of Cr2O3 under high temperature environment, thus significantly improving the oxidation resistance of the alloy (Gorr et al., 2011; Gorr et al., 2012; Xu et al., 2020). There are a few reports about the oxidation behavior of the quaternary Co-Re-Cr-Si alloys under the condition of laboratory air or 0.1 MPa pure O2 (Gorr et al., 2012; Wang et al., 2013; Xu et al., 2020). The oxidation behavior of Co-17Re-23Cr-xSi (x = 1, 2, 3) and Co-17Re-30Cr-2Si in laboratory air at 1,000 C has been investigated by Gorr B et al. (Gorr et al., 2012). The microstructure of the scales of the quaternary Co-17Re-23Cr-xSi (x = 1, 2, 3) alloys and the ternary Co-17Re-xCr (x = 23, 30) alloys are similar to some extent. Co-17Re-23Cr-xSi (x = 1, 2, 3) alloys have suffered a mass loss because the Cr content is insufficient to form a continuous Cr2O3 scale. The oxidation behavior of similar Co-20Re-25Cr-3Si quaternary alloy under the condition of 0.1 MPa pure oxygen at 1,000–1,200 C has been systematically investigated by our group recently (Wang, 2019). The result showed that the alloy suffered continuous mass loss during the oxidation process. However, when the oxidation atmosphere changes, the oxidation behavior of the alloy may change greatly. Therefore, high temperature oxidation behavior of the quaternary Co-20Re-25Cr-3Si alloy under laboratory air has been studied in this paper. Moreover, a special attention is focus on the difference of oxidation behavior between the Co-17Re-23Cr-3Si and Co-20Re-25Cr-3Si alloys, which are of a similar composition.
Experimental
The actual composition of Co-20Re-25Cr-3Si (atomic percentage, %) alloy prepared by repeated melting appropriate amounts of the four pure (99.9%) components of Co, Re, Cr and Si in a non-consumable vacuum arc melting furnace is 2.84 at.% Si, 24.82 at.% Cr, 50.18 at.% Co, 22.16 at.% Re. The two-phase alloy were subsequently annealed for 24 h at 900 C in a vacuum atmosphere to achieve a better equilibration. Figure 1 shows the microstructure of the quaternary Co-20Re-25Cr-3Si alloys after annealing at room temperature. It can be seen that the alloy consists of a continuous Co-rich phase (dark phase, A) and a dispersed Re-rich phase (light phase, B). Table 1 shows the elemental composition of different phases of Co-20Re-25Cr-3Si alloy. There are more Re but no Si present in the Re-rich phase. Samples with a size of 10 mm × 10 mm × 1 mm were cut from the alloy ingots by wire cut electrical discharge machining. A hole with 1 mm diameter for hanging the samples was drilled. To avoid typical edge effects on the oxidation process, rounded edges were specially prepared. The surface of samples was subsequently ground using SiC waterproof paper down to 2000 grit. All samples were thoroughly cleaned by ethanol in an ultrasonic bath before the oxidation process. The surface area of each sample was measured to relate mass change to the initial surface area. Samples were oxidized separately under 0.1 MPa laboratory air (oxygen partial pressure decreased to 21% of 0.1 MPa) at 1,000–1,200°C.
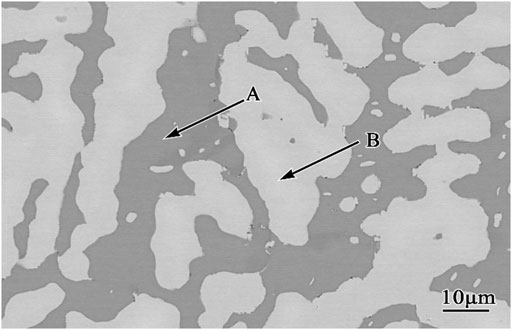
FIGURE 1. Microstructure of the quaternary Co-20Re-25Cr-3Si alloys after annealing at room temperature. Light phase: Re-rich phase; dark phase: Co-rich phase.
Continuous mass changes of samples for 24 h were measured by thermogravimetric analyzer (Setaram Setsys Evo). The alloy microstructure and the constitution of oxides formed oxides were characterized by X-ray diffraction (XRD, Shimadzu XRD-6100) and scanning electron microscopy (FE-SEM, Zeiss Sigma) combined with energy-dispersive X-ray spectroscopy (EDS, Oxford INCA).
Results and Discussion
Oxidation Kinetics
Figures 2A,B present the oxidation kinetics and the corresponding parabolic plots of the Co-20Re-25Cr-3Si alloy under 0.1 MPa laboratory air at 1,000–1,200°C, respectively. It can be seen that during the whole oxidation process, the oxidation kinetics at 1,000–1,200 °C follow parabolic law perfectly, with the values of rate constants equal to 2.9 × 10−12 g2 cm−4·s−1, 1.6 × 10−11 g2 cm−4·s−1 and 4.4 × 10−11 g2 cm−4·s−1, respectively (Table 2). The mass gain of the alloy increases with temperature, with the corresponding value of 0.45 mg/cm2, 1.12 mg/cm2 and 1.82 mg/cm2 at 1,000–1,200°C respectively after 24 h oxidation. Co-20Re-25Cr-3Si alloy shows the best oxidation resistance at 1,000°C. According to the previous results by our group, Co-20Re-25Cr-3Si alloy shows very poor high temperature oxidation resistance under the experimental condition of 0.1 MPa pure oxygen, as shown in Figure 3 (Wang, 2019). The Cr2O3 layer formed on the alloy is discontinuous and can not prevent the evaporation of Re element in the form of ReO3. Therefore, the alloy presents obvious mass loss, with the corresponding value of −4.54 mg/cm2, −5.84 mg/cm2 and −8.81 mg/cm2 at 1,000–1,200°C respectively after 24 h oxidation (Wang, 2019). However, when the oxygen pressure decreases from 0.1 to 0.021 MPa, the oxidation of Co-20Re-25Cr-3Si alloy changes greatly, from continuous mass loss to mass gain. A 79% drop in oxygen pressure causes the alloy to change from catastrophic oxidation to mild oxidation.
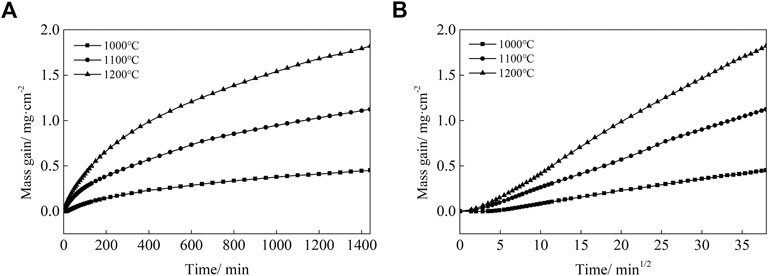
FIGURE 2. Oxidation kinetics (A) and corresponding parabolic plots (B) for the Co-20Re-25Cr-3Si alloys under 0.1 MPa laboratory air at 1,000–1,200°C for 24 h.

TABLE 2. Approximate parabolic rate constants of Co-20Re-25Cr-3Si alloys under 0.1 MPa laboratory air at 1,000–1,200°C for 24 h (g2·cm−4·s−1).
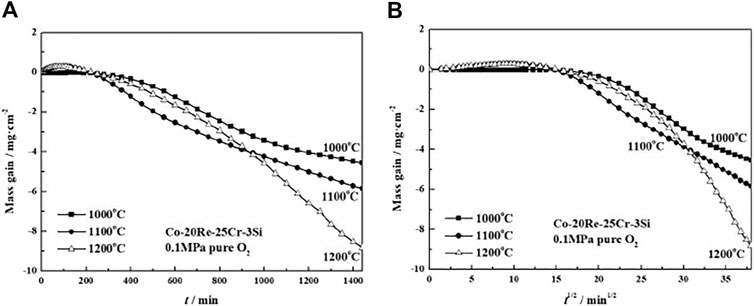
FIGURE 3. Oxidation kinetics (A) and corresponding parabolic plots (B) for the Co-20Re-25Cr-3Si alloys under 0.1 MPa pure O2 at 1,000–1,200°C for 24 h (Wang, 2019).
Calculation of Oxidation Activation Energy
The oxidation behavior of Co-20Re-25Cr-3Si alloy under 0.1 MPa laboratory air at 1,000–1,200°C conforms to the parabolic law. The square of the oxidation mass gain per unit area of the alloy is proportional to the time, as expressed by the following formula:
Where y is the mass gain per unit area of the sample, KT is the oxidation rate constant of the alloy, and C is a constant.
Based on the experimental data, the relation diagram of (Mass Gain)2 and oxidation time is made, as shown in Figure 4. By linearly fitting a straight line, the slope and intercept of the line are the values of KT and C respectively. The oxidation kinetics equation of the alloy at 1,000–1,200°C are shown in Table 3.
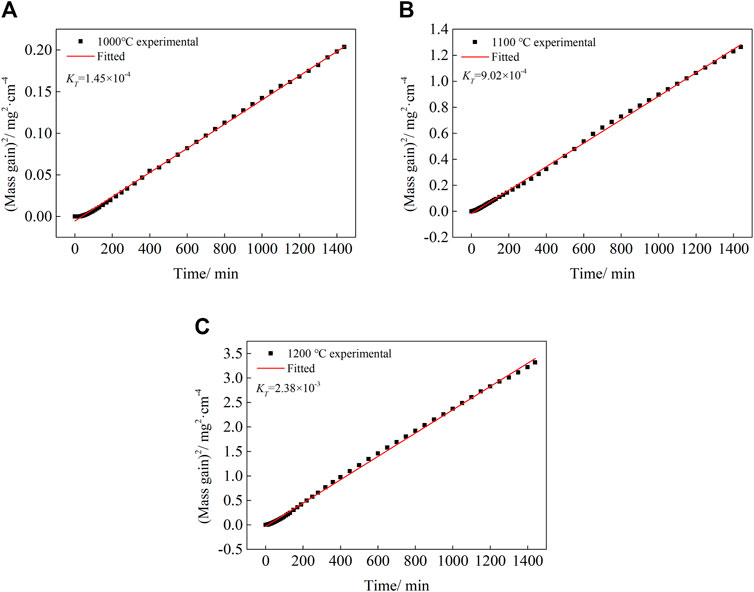
FIGURE 4. Linear fitting of oxidation kinetics of Co-20Re-25Cr-3Si alloy at different temperatures: (A) 1,000°C, (B) 1,100°C, (C) 1,200°C.
Since the oxidation behavior of Co-20Re-25Cr-3Si alloy under 0.1 MPa laboratory air can be described by parabolic law, it conforms to the Arrhenius equation and the oxidation rate constant satisfies the following relation:
Where A is the pre-factor, Q is the oxidation activation energy, R is the gas constant, and T is the thermodynamic temperature.
By taking the logarithm of both sides of (2), the following formula can be obtained:
Substituting the KT value and the thermodynamic temperature value of the three temperatures into the Equation 3, the relationship diagram of ln KT as a function of 1/T shown in Figure 5 is obtained. And the slope ln A = 12.10 and the intercept -Q/R = 26,550 are obtained. The values of A and Q are calculated and substituted into Equation 2 to obtain the relationship equation:
It can be found that the activation energy of the oxidation reaction of the Co-20Re-25Cr-3Si alloy is 220.74 kJ/mol.
Scale Microstructure and Composition
The scales grown on Co-20Re-25Cr-3Si after 24 h oxidation under laboratory air at 1,000–1,200°C (Figures 6, 7) are similar to some extent, including three-layer structure. The outermost dark gray layer of CoO is non-protective and easy to peel off. The following darker layer is probably composed mainly of CoCr2O4 spinel, as shown by the XRD (Figure 8) and EDS results. The innermost darkest layer consists mainly of a dense and continuous layer of Cr2O3 in contact with the alloy, providing a good oxidation resistance for the alloy. The thickness of the protective Cr2O3 layer decreases when temperature increases. Therefore, Co-20Re-25Cr-3Si alloy shows the best oxidation resistance at 1,000°C. An internal oxidation zone of Si under the oxide layer is present at all temperatures. The precipitation of SiO2 and its lateral growth and cross-linking may result in the formation of a continuous SiO2 layer in local places (as shown in Figure 7B.), which will block the outward migration of cation and thus reducing oxidation rate of the alloy (Wang et al., 2015b). The presence of Si may also act as a nucleation point in the oxidation process, reducing the Cr2O3 nuclear distance and promoting the rapid formation of a continuous Cr2O3 protective layer (Gorr et al., 2012). Compared with the experimental condition of 0.1 MPa pure oxygen (Wang, 2019), the oxidation mode of Co-20Re-25Cr-3Si alloy under laboratory air changes drastically. A 79% drop in oxygen pressure promotes the formation of a continuous dense protective Cr2O3 layer on the alloy, which prevents the evaporation of Re element in the alloy. Gorr B et al. studied the oxidation of Co-17Re-23Cr-xSi (x = 1, 2, 3) in laboratory air at 1,000°C (Gorr et al., 2012). The scales formed on Co-17Re-23Cr-xSi (x = 1, 2, 3) are similar to the ternary Co-17Re-xCr (x = 23, 30) alloy. Co-17Re-23Cr-xSi (x = 1, 2, 3) alloys have undergone mass loss because the Cr content is insufficient to form a continuous Cr2O3 scale. Therefore, from another perspective, compared with Co-17Re-23Cr-3Si alloy, the addition of about 2% Cr causes the Co-20Re-25Cr-3Si alloy to change from catastrophic oxidation to mild oxidation under laboratory air, by forming a continuous dense protective Cr2O3 layer on the alloy similarly.
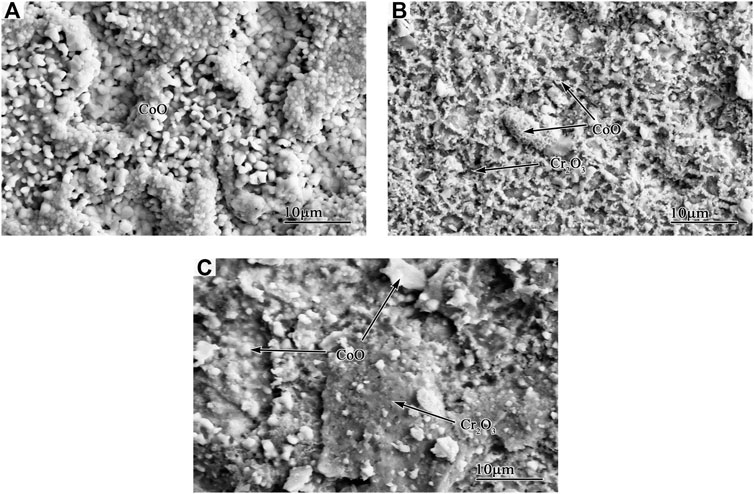
FIGURE 6. Surface micrographs of Co-20Re-25Cr-3Si alloys oxidized under 0.1 MPa laboratory air for 24 h: (A) 1,000°C; (B) 1,100°C; (C) 1,200°C.
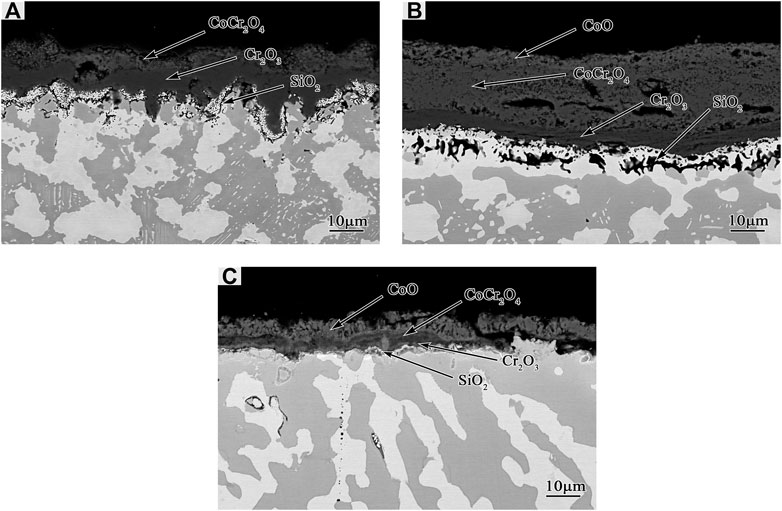
FIGURE 7. Cross-sectional micrographs of Co-20Re-25Cr-3Si alloys oxidized under 0.1 MPa laboratory air for 24 h: (A) 1,000°C; (B) 1,100°C; (C) 1,200°C.
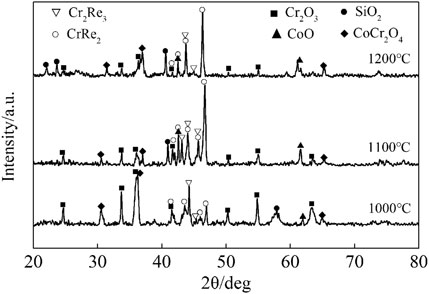
FIGURE 8. XRD patterns of Co-20Re-25Cr-3Si alloy oxidized under 0.1 MPa laboratory air at 1,000–1,200°C for 24 h.
Conclusion
1) The oxidation behavior of Co-20Re-25Cr-3Si alloy at constant temperature for 24 h in laboratory air conforms to the parabolic law. The parabolic rate constants at 1,000–1200°C are 2.92 × 10−12 g2·cm−4·s−1, 1.63 × 10−11 g2·cm−4·s−1 and 4.38 × 10−11 g2·cm−4·s−1, respectively. The oxidation activation energy of the alloys is 220.74 kJ/mol.
2) The scales grown on Co-20Re-25Cr-3Si at 1,000–1,200°C are similar and composed of three layers. The outermost CoO layer is non-protective and easy to peel off. The second darker layer consists mainly of CoCr2O4 spinel. The innermost darkest layer consists mainly of a dense and continuous Cr2O3 layer in contact with the alloy, which provides a good protection for the alloy.
3) A 79% drop in oxygen pressure promotes the formation of a continuous dense protective Cr2O3 layer on the alloy, which prevents the evaporation of Re element in the Co-20Re-25Cr-3Si alloy. Moreover, compared with Co-17Re-23Cr-3Si alloy, the addition of about 2% Cr causes the Co-20Re-25Cr-3Si alloy to change from catastrophic oxidation to mild oxidation under laboratory air.
Data Availability Statement
The original contributions presented in the study are included in the article/supplementary material, further inquiries can be directed to the corresponding authors.
Author Contributions
ML: Investigation, Resources, Data Curation, Original Draft. JX: Conceptualization, Methodology, Review, Supervision. HW: Validation, Funding acquisition. XP Validation. XX: Resources. LW: Resources. SZ: Resources.
Funding
Financial supports partly by the NNSF of China under the research Projects No. 51371173, partly by the Ministry of Major Science and Technology of Shanghai (19DZ1100703), partly by the Jiangxi Science and Technology Normal University Postgraduate Innovation Special Fund (YC2019-X07).
Conflict of Interest
The authors declare that the research was conducted in the absence of any commercial or financial relationships that could be construed as a potential conflict of interest.
References
Beran, P., Mukherji, D., Strunz, P., Gilles, R., Hofmann, M., Karge, L., et al. (2016). Effect of Composition on the Matrix Transformation of the Co-Re-Cr-Ta-C Alloys. Met. Mater. Int. 22, 562–571. doi:10.1007/s12540-016-5697-2
Beran, P., Mukherji, D., Strunz, P., Gilles, R., Karge, l., Hofmann, M., et al. (2018). Additional Phases at High boron Content in High-Temperature Co-Re-Cr Alloys. Metals 8, 621. doi:10.3390/met8080621
Gorr, B., Burk, S., and Christ, H.-J. (2011). The High-Temperature Oxidation Behavior of Co-Re-Cr-based Alloys. Jom 63, 37–40. doi:10.1007/s11837-011-0204-1
Gorr, B., Burk, S., Depka, T., Somsen, C., Abu-Samra, H., Christ, H.-J., et al. (2012). Effect of Si Addition on the Oxidation Resistance of Co-Re-Cr-alloys: Recent Attainments in the Development of Novel Alloys. Int. J. Mater. Res. 103, 24–30. doi:10.3139/146.110626
Gorr, B., Christ, H.-J., Mukherji, D., and Rösler, J. (2014a). Thermodynamic Calculations in the Development of High-Temperature Co-Re-based Alloys. J. Alloys Compd. 582, 50–58. doi:10.1016/j.jallcom.2013.07.055
Gorr, B., Wang, L., Burk, S., Azim, M., Majumdar, S., Christ, H.-J., et al. (2014b). High-temperature Oxidation Behavior of Mo-Si-B-Based and Co-Re-Cr-based Alloys. Intermetallics 48, 34–43. doi:10.1016/j.intermet.2013.10.008
Gorunov, A. I. (2017). Restoration of Aircraft Gas Turbine Engine Titanium Compressor Blades by Laser Surfacing. Metallurgist 61, 498–504. doi:10.1007/s11015-017-0523-8
Mukherji, D., Rösler, J., Krüger, M., Heilmaier, M., Bölitz, M.-C., Völkl, R., et al. (2012). The Effects of boron Addition on the Microstructure and Mechanical Properties of Co-Re-based High-Temperature Alloys. Scr. Mater. 66, 60–63. doi:10.1016/j.scriptamat.2011.10.007
Perepezko, J. H. (2009). The Hotter the Engine, the Better. Science 326, 1068–1069. doi:10.1126/science.1179327
Rösler, J., Mukherji, D., and Baranski, T. (2007). Co-Re-based Alloys: A New Class of High Temperature Materials?. Adv. Eng. Mater. 9, 876–881. doi:10.1002/adem.200700132
Shi, C., and Zhong, Z. (2010). Development and Innovation of Superalloy in China. Acta Metall. Sin. 46, 1281–1288. (Chinese). doi:10.3724/SP.J.1037.2010.01281
Strunz, P., Mukherji, D., Beran, P., Gilles, R., Karge, L., Hofmann, M., et al. (2018). Matrix Transformation in boron Containing High-Temperature Co-Re-Cr Alloys. Met. Mater. Int. 24, 934–944. doi:10.1007/s12540-018-0121-8
Vorobiov, I. S., Dyakonenko, K. Y., Kulishov, S. B., Skritskij, A. N., and Kunicka, Z. (2014). Vibration Characteristics of Cooled Single-crystal Gas Turbine Blades. J. Vib. Eng. Tech. 2, 537–541.
Wanderka, N., Mousa, M. S., Henke, P., Korchuganova, O., Mukherji, D., Rösler, J., et al. (2016). Carbides in Co-Re-Cr-based High-Temperature Alloys. J. Mater. Sci. 51, 7145–7155. doi:10.1007/s10853-016-9995-3
Wang, L., Gorr, B., Christ, H.-J., Mukherji, D., and Rösler, J. (2013). Optimization of Cr-Content for High-Temperature Oxidation Behavior of Co-Re-si-base Alloys. Oxid Met. 80, 49–59. doi:10.1007/s11085-013-9369-z
Wang, L., Gorr, B., Christ, H.-J., Mukherji, D., and Rösler, J. (2015a). Microstructure and Oxidation Mechanism Evolution of Co-17Re-25Cr-2Si in the Temperature Range 800-1,100 °C. Oxid Met. 83, 465–483. doi:10.1007/s11085-014-9515-2
Wang, L., Gorr, B., Christ, H.-J., Mukherji, D., and Rösler, J. (2015b). The Effect of Alloyed Nickel on the Short-Term High Temperature Oxidation Behaviour of Co-Re-Cr-based Alloys. Corrosion Sci. 93, 19–26. doi:10.1016/j.corsci.2015.01.004
Wang, L. (2019). “Oxidation Behavior of Co-Re-Cr Based Superalloy at 1000-1300°C,” ([Nanchan]: Jiangxi Science and Technology Normal University). [dissertation/master’s thesis].
Keywords: Co-20Re-25Cr-3Si alloy, high temperature oxidation, laboratory air, oxidation kinetics, microstructure
Citation: Liu M, Xiang J, Wei H, Pan X, Xu X, Wang L and Zhang S (2021) Oxidation Behavior of Quaternary Co-20Re-25Cr-3Si Alloy at Laboratory Air. Front. Mater. 8:706489. doi: 10.3389/fmats.2021.706489
Received: 07 May 2021; Accepted: 21 June 2021;
Published: 06 July 2021.
Edited by:
Hongsong Zhang, Henan Institute of Engineering, ChinaReviewed by:
Guangming Liu, Nanchang Hangkong University, ChinaWenyi Peng, Nanchang University, China
Copyright © 2021 Liu, Xiang, Wei, Pan, Xu, Wang and Zhang. This is an open-access article distributed under the terms of the Creative Commons Attribution License (CC BY). The use, distribution or reproduction in other forums is permitted, provided the original author(s) and the copyright owner(s) are credited and that the original publication in this journal is cited, in accordance with accepted academic practice. No use, distribution or reproduction is permitted which does not comply with these terms.
*Correspondence: Junhuai Xiang, eGlhbmdqdW5odWFpQDE2My5jb20=; Hua Wei, aHVhd2VpQHpqdS5lZHUuY24=