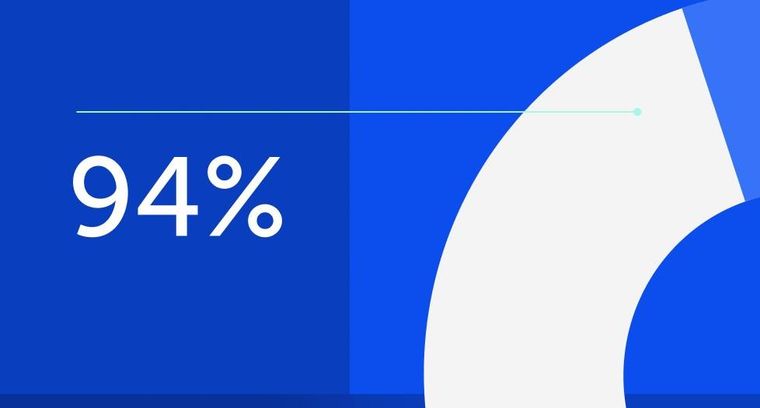
94% of researchers rate our articles as excellent or good
Learn more about the work of our research integrity team to safeguard the quality of each article we publish.
Find out more
ORIGINAL RESEARCH article
Front. Mater., 31 May 2021
Sec. Ceramics and Glass
Volume 8 - 2021 | https://doi.org/10.3389/fmats.2021.692759
This article is part of the Research Topic2021 Retrospective: Ceramics and GlassView all 9 articles
Kaolin clay is an inexpensive and abundant material with potential for use as a low-dielectric-constant ceramic; however, the natural metallic oxides the clay contains hinder such applications. In this study, kaolin clay ceramics with excellent physical and dielectric properties were synthesized using kaolin clay as the raw material by chemical cleaning and sintering. Characterization of the resulting samples showed that the sulfuric acid treatment has a significant influence on the metallic oxide content and dielectric properties of the kaolin clay ceramics. When the kaolin clay raw material was treated with sulfuric acid three times, the dielectric constant decreased from 5.12 to 3.75 and the Vickers hardness increased from 946 to 1,214 kg/mm2 relative to the ceramic prepared from the untreated clay. Therefore, these ceramics exhibit significant potential for use in the microelectronics industry.
In recent years, low-dielectric-constant materials have been commonly employed in microwave devices, ultra-large-scale integrated circuits, and other applications (Sato et al., 2013; Hong et al., 2020). Many materials have been introduced to achieve lower dielectric constants, such as Al2O3 (Su et al., 2014), SiCN (Zhou and Zhang 2015), BN (Hong et al., 2016), SiC (Milosevic and King 2014), and SiO2 (Carta et al., 2014; Joseph et al., 2015). Although the resulting materials have excellent properties, they are expensive and limited in terms of output. Thus, more and more researchers are exploring materials with lower costs and greater availability.
Kaolin clay, a mineral composed of hydrated aluminum silicates (i.e., [Al4(Si4O10) (OH)2]), is naturally abundant and used worldwide for various applications such as clay ceramics (Zhou et al., 2010), zeolites for nicotine adsorption (Lazarevic and Jovanovic 2010; Shen et al., 2013), asphaltene adsorption (Wang et al., 2013), and ceramics as insulating substrates (Viswabaskaran and Gnanam 2004). Kaolin clay is also relatively inexpensive (Gelin and Gueguen 1988; Xu et al., 1999; Xu et al., 2000). The main components of kaolin are SiO2 and Al2O3, which have significant potential for use as low-dielectric-constant materials. However, the kaolin clay itself as a raw material contains metallic oxides such as Fe2O3 and CaO, which deteriorate the dielectric properties of the resulting ceramics (Yu et al., 2016). Hence, it is important to develop methods to decrease the contents of these metallic oxides in the clay.
In this study, kaolin clay was used as raw material to prepare low-dielectric-constant kaolin clay ceramics by chemical cleaning and sintering. Many of the metallic elements in the raw kaolin clay, such as Ca, Fe, V, Rb, and Mn, were dissolved in sulfuric acid and then washed away by distilled water. We explored the properties of the resulting kaolin clay ceramics depending on how many sulfuric acid treatment cycles were applied.
Kaolin clay was obtained from the tobacco belt of Hunan Province, China. The high-silica ceramics were prepared as follows. First, the raw kaolin clay was ground into a powder and added to a sulfuric acid solution (2 M) to form a suspension, which was then maintained under stirring for 30 min at room temperature to dissolve metallic oxides such as CaO and Fe2O3. Subsequently, the kaolin clay was filtered, washed with distilled water three times, and dried at 80°C. For comparison, the kaolin clay was treated zero, one, two, or three times with the sulfuric acid solution. Finally, the kaolin clay powders were mixed uniformly with an appropriate amount of a polyvinyl alcohol solution (7 wt%, PVA), cold-pressed into wafers under 5 MPa of pressure, and sintered at 1,300°C for 3 h under an air atmosphere to obtain the ceramics. For the sake of convenience, the kaolin clay ceramics treated zero, one, two, and three times with sulfuric acid are denoted as KCC-0, KCC-1, KCC-2, and KCC-3, respectively. A schematic diagram of the synthetic procedure and the synthesized kaolin clay ceramics are shown in Figure 1. In preparation for the dielectric tests, the samples were coated with silver paste and sintered at 550°C for 10 min.
The phases and chemical compositions of the ceramics were measured by X-ray diffraction (XRD) and energy dispersive spectroscopy (EDS, Hitachi SU70). The microstructures of the samples were observed using a scanning electron microscope (SEM), and the porosity and Vickers hardness were measured by the drainage method and a digital hardness tester, respectively. The dielectric properties were measured at a frequency of 1 MHz. The dielectric constant (ε) of the ceramics was calculated by the following equation:
where C is the capacitance, h is the distance between the two electrodes, εo is the vacuum permittivity (Ɛo = 1/4π·9·1011 F/cm), and S is the area of the two electrodes.
Kaolin clay was obtained from the Hunan Province of China, treated with sulfuric acid (2 M), and made into ceramics. The XRD patterns of the kaolin clay ceramics subjected to different numbers of sulfuric acid treatment cycles are shown in Figure 2. The XRD pattern of the ceramic without treatment (KCC-0) in Figure 2A shows that the sample was composed of mullite and cordierite. The ceramics treated with sulfuric acid one, two, and three times showed the same XRD patterns as that of KCC-0, indicating that the treatment did not disrupt the ceramic structure.
Figure 3 shows the SEM images of the kaolin clay ceramic samples, illustrating the numerous pores on the surface of KCC-0 (Figure 3A). These pores may originate from the release of carbon dioxide and moisture during sintering, where the pores act as release channels. Figures 3B–D are the SEM images of KCC-1, KCC-2, and KCC-3, respectively, showing that there were also many pores on the surfaces of the treated samples. Thus, the sulfuric acid treatment did not change how carbon dioxide and moisture are released during the sintering process.
Figure 4 shows the EDS elemental maps of KCC-0, which illustrates that the ceramic is composed of uniform dispersions of O, Al, Si, Ca, Fe, V, Rb, and Mn. Among these elements, the maps of O, Al, Si, and Ca are dense and highly visible, whereas the Fe, V, Rb, and Mn elemental maps are more sparse, suggesting much higher contents of the former than the latter.
The kaolin clay ceramics were analyzed by EDS, and the calculated elemental proportions are shown in Table 1. KCC-0, which was prepared directly from kaolin clay without purification, was mainly composed of 50.66% O, 21.96% Al, and 22.39% Si, as well as small amounts of other elements such as Ca, Fe, V, Rb, and Mn. After treatment with sulfuric acid one to three times, the contents of Ca, Fe, V, Rb, and Mn decreased. Some of the contained Al was also dissolved by sulfuric acid and washed away by distilled water.
The diameter shrinkage and open porosity of the prepared kaolin clay ceramics are exhibited in Figure 5. Relative to KCC-0, the diameter shrinkage of KCC-3 decreased from 0.71 to 0.57%, whereas the open porosity increased from 2.63 to 2.97%. Based on Table 1, the sulfuric acid treatment decreased the Ca, Fe, V, Rb, and Mn contents of the ceramics. Sulfuric acid can penetrate into the structure of kaolin clay and dissolve these metallic oxides. The decreased metallic oxide contents may also make the clay structure denser. Furthermore, the sulfuric acid remaining in the clay can decompose into SO2 and H2O at high temperatures, which will increase the open porosity.
Figure 6 shows the dielectric properties of the kaolin clay ceramics subjected to different numbers of sulfuric acid treatment cycles, illustrating that the treatment significantly influenced their dielectric properties. The dielectric constant and dielectric loss of KCC-0 were determined as 5.12 and 0.018, respectively, whereas the dielectric constants of KCC-1, KCC-2, and KCC-3 were determined as 4.12, 3.83, and 3.75, respectively. This decrease in the dielectric constant may arise from the removal of metallic oxides. In addition, the dielectric loss of the kaolin clay ceramics remained nearly the same regardless of the number of applied treatment cycles, which may be related to the clay structure.
The Vickers hardness values of the ceramics are shown in Figure 7. When the ceramic was prepared directly from the raw material (KCC-0), the Vickers hardness was 946 kg/mm2. In contrast, the hardness values of the KCC-1, KCC-2, and KCC-3 ceramics were 1,106, 1,179, and 1,214 kg/mm2, respectively. This increase in the Vickers hardness may be attributable to the decreased metallic oxide contents and increased SiO2 content (Table 1).
Kaolin clay ceramics with excellent physical and dielectric properties were prepared by a chemical cleaning and sintering method. The sulfuric acid treatment can effectively eliminate metallic oxides in kaolin clay, resulting in ceramics with significantly improved physical and dielectric properties. For example, the Vickers hardness, dielectric constant, and dielectric loss of the kaolin ceramic prepared from the clay without acid treatment were 946 kg/mm2, 5.12, and 0.018, respectively. In contrast, the Vickers hardness and dielectric constant of the ceramic prepared from clay treated three times with sulfuric acid were 1,214 kg/mm2 and 3.75, respectively, while the dielectric loss remained nearly the same. Therefore, these ceramics have significant potential for use in the microelectronics industry.
The original contributions presented in the study are included in the article/Supplementary Material, further inquiries can be directed to the corresponding authors.
XY and JH designed experiments and wrote the manuscript. XY and WY carried out experiments.
The authors declare that the research was conducted in the absence of any commercial or financial relationships that could be construed as a potential conflict of interest.
The authors would like to thank the Shiyanjia Lab (www.shiyanjia.com) for the SEM and EDS analysis.
Carta, F., Gates, S. M., Limanov, A. B., Hlaing, H., Im, J. S., Edelstein, D. C., et al. (2014). Sequential Lateral Solidification of Silicon Thin Films on Low-K Dielectrics for Low Temperature Integration. Appl. Phys. Lett. 105, 242904. doi:10.1063/1.4904938
Gelin, P., and Gueguen, C. (1988). Hydrothermal Modifications of Matrix-Embedded Y-Faujasite and Offretite Zeolites. Appl. Catal. 38, 225–233. doi:10.1016/s0166-9834(00)82827-4
Hong, W. B., Li, L., Yan, H., Wu, S. Y., Yang, H. S., and Chen, X. M. (2020). Room-temperature-densified H3BO3 Microwave Dielectric Ceramics with Ultra-low Permittivity and Ultra-high Qf Value. J. Materiomics 6, 233–239. doi:10.1016/j.jmat.2020.02.006
Hong, X., Wang, D., and Chung, D. D. L. (2016). Boron Nitride Nanotube Mat as a Low-K Dielectric Material with Relative Dielectric Constant Ranging from 1.0 to 1.1. J. Elec Materi 45, 453–461. doi:10.1007/s11664-015-4123-8
Joseph, A. M., Nagendra, B., Surendran, K. P., and Bhoje Gowd, E. (2015). Syndiotactic Polystyrene/hybrid Silica Spheres of POSS Siloxane Composites Exhibiting Ultralow Dielectric Constant. ACS Appl. Mater. Inter. 7, 19474–19483. doi:10.1021/acsami.5b05933
Lazarevic, N., Jovanovic, J., Jevremovic, M., Nikolic, M., and Adnadjevic, B. (2010). Kinetics of Isothermal Nicotine Adsorption from the Aqueous Solution onto the USY Zeolite. Ind. Eng. Chem. Res. 49, 6302–6308. doi:10.1021/ie901351h
Milosevic, M., and King, S. W. (2014). Complete Elemental Analysis of Low-Ka-SiC:H Thin Films by Transmission FTIR Spectroscopy. ECS J. Solid State. Sci. Technol. 3, N52–N57. doi:10.1149/2.002404jss
Sato, T., Yamamoto, T., Hata, Y., Kayaba, Y., Kuroki, S.-I., et al. (2013). Low-kMesoporous Pure Silica Zeolite with High Elastic Modulus Using 1,3,5,7-Tetra-Methyl-Cyclo-Tetra-Siloxane and Ultraviolet Treatments. ECS J. Solid State. Sci. Technol. 2, N89–N92. doi:10.1149/2.018304jss
Shen, K., Qian, W., Wang, N., Zhang, J., and Wei, F. (2013). Direct Synthesis of C-axis Oriented ZSM-5 Nanoneedles from Acid-Treated Kaolin clay. J. Mater. Chem. A. 1, 3272–3275. doi:10.1039/c3ta01479g
Su, Z., Xi, X., Hu, Y., Fei, Q., Yu, S., Li, H., et al. (2014). A New Al2O3 Porous Ceramic Prepared by Addition of Hollow Spheres. J. Porous Mater. 21, 601–609. doi:10.1007/s10934-014-9806-7
Viswabaskaran, V., Gnanam, F. D., and Balasubramanian, M. (2004). Mullite from clay-reactive Alumina for Insulating Substrate Application. Appl. Clay Sci. 25, 29–35. doi:10.1016/j.clay.2003.08.001
Wang, S., Liu, Q., Tan, X., Xu, C., and Gray, M. R. (2013). Study of Asphaltene Adsorption on Kaolinite by X-ray Photoelectron Spectroscopy and Time-Of-Flight Secondary Ion Mass Spectroscopy. Energy Fuels 27, 2465–2473. doi:10.1021/ef4001314
Xu, M., Cheng, M., and Bao, X. (2000). Growth of Ultrafine Zeolite Y Crystals on Metakaolin Microspheres. Chem. Commun. 19, 1873–1874. doi:10.1039/b005787h
Xu, M., Cheng, M., Liu, X., Tan, D., and Bao, X. (1999). Growth of Zeolite KSO1 on Calcined Kaolin Microspheres. J. Mater. Chem. 9, 2965–2966. doi:10.1039/a906767a
Yu, B. H., Yuan, X. X., and Liu, Y. J. (2016). Preparation of Low-Dielectric-Constant Ceramics Using Kaolin clay. Am. Ceram. Soc. Bull. 95, 34–37 .
Zhou, J., Zhang, X., Wang, Y., Larbot, A., and Hu, X. (2010). Elaboration and Characterization of Tubular Macroporous Ceramic Support for Membranes from Kaolin and Dolomite. J. Porous Mater. 17, 1–9. doi:10.1007/s10934-008-9258-z
Keywords: kaolin clay ceramics, sulfuric acid, dielectric properties, vickers hardness, chemical cleaning method
Citation: Yang X, Yang W and Hu J (2021) Preparation of Low-Dielectric-Constant Kaolin Clay Ceramics by Chemical Cleaning Method. Front. Mater. 8:692759. doi: 10.3389/fmats.2021.692759
Received: 09 April 2021; Accepted: 18 May 2021;
Published: 31 May 2021.
Edited by:
Xingtao Xu, National Institute for Materials Science, JapanCopyright © 2021 Yang, Yang and Hu. This is an open-access article distributed under the terms of the Creative Commons Attribution License (CC BY). The use, distribution or reproduction in other forums is permitted, provided the original author(s) and the copyright owner(s) are credited and that the original publication in this journal is cited, in accordance with accepted academic practice. No use, distribution or reproduction is permitted which does not comply with these terms.
*Correspondence: Xiaobing Yang, eGlhb2JpbmcteWFuZ0AxNjMuY29t; Jiapeng Hu, aHVqcDExQDE2My5jb20=
Disclaimer: All claims expressed in this article are solely those of the authors and do not necessarily represent those of their affiliated organizations, or those of the publisher, the editors and the reviewers. Any product that may be evaluated in this article or claim that may be made by its manufacturer is not guaranteed or endorsed by the publisher.
Research integrity at Frontiers
Learn more about the work of our research integrity team to safeguard the quality of each article we publish.