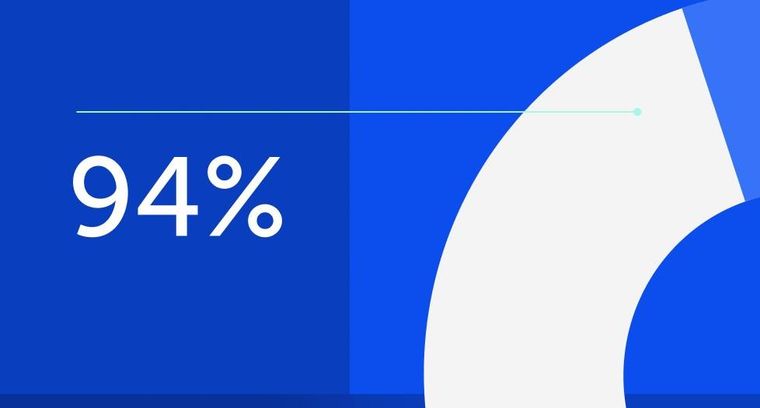
94% of researchers rate our articles as excellent or good
Learn more about the work of our research integrity team to safeguard the quality of each article we publish.
Find out more
REVIEW article
Front. Mater., 12 May 2021
Sec. Smart Materials
Volume 8 - 2021 | https://doi.org/10.3389/fmats.2021.678882
This article is part of the Research TopicSynthesis, Characterization and Applications of Magneto-Responsive Functional MaterialsView all 11 articles
Owing to some of its specific advantages, magnetorheological fluid (MRF) has drawn significant attention in a broad range of modern precision machining fields. With the diversification and increase in demand, many novel structural configurations and processing methods have been applied to mechanical machining equipment. Although different applications using MRF have been proposed in the existing literature, the classification, latest approaches, and further trend are not understood clearly for the machining field. Therefore, the current applications such as machining auxiliary equipment and surface polishing equipment that used MRF are summarized from 2016 to 2020, in this article. Especially, some detailed structures of equipment are investigated, and relative limitations are analyzed based on the characteristics of MRF. Finally, in view of the current equipment, advantages and defects are briefly reported; the developing trends of modern precision machining with MRF are discussed. Therefore, in the state-of-the-art review, the significant role of MRF in the machining field is emphasized, which paves the way to innovative development and market selection.
Magnetorheological fluid (MRF) with milliseconds rheological phenomenon and flexible magnetic field controllability has been widely used in the modern precision machining field (Elsaady et al., 2020; Kulandaivel and Kumar, 2020; Nugroho et al., 2020). Based on the transferable and adjustable liquid–colloid state, MRF has unique application advantages in the development of machining auxiliary equipment (Jiang X. H. et al., 2020; Saleh et al., 2020; Lv et al., 2021) and surface polishing equipment (Kumar et al., 2019; Nagdeve et al., 2019; Dubey and Sidpara, 2021; Gupta et al., 2021). Therefore, to improve product technology and reduce cost, the research of new MRF equipment has become an important direction in the field of mechanical machining (Wang and Meng, 2001; Park et al., 2007; Bedi and Singh, 2016; Liu Z. et al., 2020).
For machining auxiliary equipment such as flexible fixture and damping mechanism, the MRF plays a key role in some research results (Wuertz et al., 2010; Ma, 2017; Jiang et al., 2021; Kumar et al., 2021; Yu et al., 2021; Zhou et al., 2021). In machining production or other technical fields, objects with an irregular surface are difficult to grasp and position by using traditional rigid fixtures, and it is easy to cause damage to the product when the surface contact stress is too large. Therefore, the flexible fixture is essential in the production of machining auxiliary equipment. MRF is a liquid flow state under normal conditions. When an external magnetic field is applied, the material appears in colloid state, whose viscosity is adjustable by an electromagnetic system. Thus, the MRF has been applied to the flexible fixture, where the security control of the product is realized by adjusting the surface hardness of the fixture in real time. Furthermore, in the machining field, such as the technologies of turning, grinding, and boring, a workpiece especially with an unstable structure may produce vibration, therefore, it is necessary that the design of damper reduces the vibration (Cheng et al., 2019; Oladapo et al., 2020; Chen et al., 2021). Because the rheological response of MRF is in milliseconds, the MRF damper has sensitive damping control ability and great application potential in machining (Rahman et al., 2017; Rafajowicz et al., 2020).
Moreover, with the requirements of surface polishing quality and the diversity of polishing materials, the application of MRF to improve the performance of polishing equipment has become a recent research hotspot (Wang Y. et al., 2016; Zhong, 2020). The MRF polishing technology uses a kind of flexible MRF film formed by the rheological properties in the magnetic field to polish the workpiece surface (Aggarwal and Singh, 2011; Jain et al., 2012; Liang et al., 2021; Nguyen et al., 2021). Compared with traditional polishing approaches, there is almost no subsurface damage in the MRF polishing technology. In addition, MRF polishing also has some other advantages, such as recycled MRF, updated abrasive in real time, few tool wear, stable removal function, and controlled hardness of MRF micro-grinding head. Thus, based on the above-mentioned advantages, MRF polishing technology plays an irreplaceable role in special structural surfaces and application requirements.
Having thus described the basic concepts and categorization, some typical machining auxiliary equipment and surface polishing equipment with MRF are investigated from 2016 to 2020. In this work, approximately 70 academic articles have been summarized from the 5 years, which report the application methods, operation modes, and structural configurations of machining equipment with MRF. Considering the above classification, the proportions of different research directions are shown in Figure 1. Moreover, some drawbacks of the machining equipment with MRF are also analyzed. For a better understanding of the MRF application, advantages, conclusions, and development tendency of the MRF machining equipment used in modern precision machining field are summarized.
Due to the increasingly complex shape of parts in the modern manufacturing industry, mechanical processing is also developed toward diversification and individuation. MRF flexible fixtures with the characteristic of adjustable hardness have been used for clamping brittle and complex parts, which is an important field in modern precision machining (Kong et al., 2011).
In 2016 and 2017, an MRF flexible fixture was designed to suppress vibration in the machining process for the aerospace industry (see Figure 2). To suppress the vibration effect during processing, natural frequency and mode shape function of the thin-walled workpiece are deduced, and a dynamic equation of the workpiece–fixture system considering the external damping factor is proposed (Ma et al., 2016). In addition, a new dynamic analytical model is proposed to determine the effect of the damping factor on the dynamic response of thin-walled workpiece in machining (Ma et al., 2017). In the device, the workpiece is placed in the MRF, whose viscosity is adjusted by the magnetic field of the coil. So, the workpiece is fixed by pushing two sliding blocks symmetrically and processed through a rotary cutter. The device reflects the advantages of the MRF flexible fixture, but there is still displacement error, which reduces the processing accuracy. In 2018, there are no outstanding results of the MRF flexible fixture. Then, an MRF flexible fixture was devised to study its performance as a support for thin-walled parts in 2019, shown in Figure 3 (Wu, 2019; Liu H. et al., 2020). In the device, a magnetic yoke is added on one side of the electromagnetic coil to optimize the magnetic circuit and improve the rheological properties of the MRF. The effectiveness of the device is verified by inhibition tests. However, the improved magnetic field reduces the working space of MRF and limits the application of workpieces with large volumes.
Figure 2. The schematic diagram of flexible fixture system (Ma et al., 2016).
Figure 3. The schematic diagram of a flexible fixture model (Liu H. et al., 2020).
In 2020, a clamping method with a MRF fixture was proposed, and a theoretical model of shear stress was derived to find out the coupling relationship between magnetic field intensity, thickness, and position of a workpiece (Jiang X. et al., 2020). The method can decrease cutting force and improve the accuracy of thin-walled parts by carrying out milling experiments. Moreover, to investigate the effects of vibration on thin-walled workpiece in machining, Jiang X. H. et al. (2020) established a dynamic model based on the Rayleigh damping matrix and the equivalent force principle and proposed an auxiliary support method with MRF. In this method, based on traditional MRF fixture structure, magnetic field distribution is optimized, and the damping force of the workpiece is deduced. The optimum parameters of the MRF fixture such as the MRF volume, location, and magnetic field intensity are determined to suppress the tool vibration.
With the development of modern machining technology toward high precision and productivity, tool vibration not only damages the machining surface and shortens the life of the tool but also increases the load power of lathe (Jung et al., 2020; Yan et al., 2020). Tool vibration not only damages the machining surface and shortens the life of the tool but also increases the load power of lathe. Thus, various methods are used to reduce the tool vibration, and MRF dampers have been proven to be effective in suppressing vibration and improving performance (Tang et al., 2016; Girinath et al., 2018).
In 2017, to obtain high precision and surface quality, a MRF damper was developed to reduce tool vibration (Paul et al., 2017). The behavior of the tool holder with the MRF damper was investigated, where a vibration model was established to analyze the amplitudes of tool vibration and chip thickness. From their experiment, it was proved that the damping capability of the turning tool and the efficiency of turning operation could be improved considerably. Similarly, a MRF damper was designed to monitor and control the performance of cutting tool for turning operation (Kishore et al., 2018), and a second mode of vibration using finite element software was used to obtain dynamic stability of the cutting tool holder. In this device, transmissibility and half power bandwidth approaches were used to address the dynamic fluctuation of the cutting force. So, the MRF damper could better control the noise and frequency responsible for unstable machining and improve the processing technology in terms of better surface finish on workpieces. Due to the high slenderness ratio of the boring bar, boring operation is highly prone to machining instability. A special boring bar is designed with a rod mounted as an inverse cantilever (Biju and Shunmugam, 2019). As shown in Figure 4, vibration of the rod is adjusted by the viscosity of MRF. Experimental results show that it can reduce the amplitude of vibration, surface roughness, and roundness error. For the same purpose, a novel MRF hydrostatic guideway system was designed to control the machining vibration as shown in Figure 5 (Liu and Hu, 2019). In addition, a computational fluid dynamics model is presented to study the performance parameters of MR hydrostatic guideway system. In this system, some working variables such as magnetic flux density, initial pressure, and load, have been analyzed, and performances such as flow rate, frictional force, and damping of the system have been optimized.
Figure 4. Schematic diagram of boring bar construction (Biju and Shunmugam, 2019).
Figure 5. Scheme of MRF hydrostatic guideway system (Liu and Hu, 2019).
In 2020, a semi-active MRF damper was designed to suppress chatter conditions for the productions of thin-floor components. In the device, enhance multistage homotopy perturbation method and novel cutting force model were used to increase productivity with high surface quality (Puma-Araujo et al., 2020). Furthermore, an MRF damper is proposed to increase the stability of the boring process (Saleh et al., 2021). Besides that, modal analysis is conducted on the boring bar with and without the MR damper to obtain the frequency response functions. As shown in Figure 6, the MRF with minimal volume and electromagnetic circuit were placed on the outer part of the boring bar, which makes it easy for installation and adjustability of the bar. The damper has effectively damped the vibrations of the test materials at different modes while using two different boring bars.
Figure 6. Computer aided design (CAD) model of the boring bar MRF damper with its components (Saleh et al., 2021).
Compared with the traditional polishing technology, MRF polishing with super-high precision has been applied to the plane and complex surfaces of the parts (Mutalib et al., 2019). As shown in Figure 7, the MRF as a polishing fluid attaches to the surface of the polishing wheel under the action of magnetic field, forming a kind of solid state of ribbon on the contact surface of the polishing wheel and workpiece. Thus, through the shear force in the process of removal of surface material, polishing machining of the workpiece is achieved. After removing the magnetic field in the processing area, MRF returns to liquid state with good fluidity and can be processed by recycling (Golini et al., 1999). The material removal effect conforms to the commonly accepted Preston equation in the field of optical machining, which is described as follows:
Figure 7. Schematic diagram of magnetorheological polishing equipment (Golini et al., 1999).
where MRR is the amount of material removed from the workpiece surface; K is Preston coefficient, and related to MRF composition, polishing zone temperature, and workpiece material; P represents the pressure of MRF on workpieces; V is the relative speed of the polishing wheel and the workpiece surface in the polishing region; and t is the polishing time.
It can be understood from Equation (1) that in addition to the composition of MRF, the material removal effect is mainly affected by pressure, relative velocity, and polishing residence time. Therefore, to improve the polishing performance of MRF with super-high precision, the influencing parameters of MRF polishing can be optimized from the following three aspects: optimization of MRF to suit different processing materials; research on influence rule of different processing techniques on the shape of the removed material; and control system design of precision magnetorheological polishing.
In 2016, a precision MRF process using a small ball-end permanent-magnet polishing head with a diameter of 4 mm was proposed, where a peristaltic pump was applied to transport the MRF to the workpiece processing area, and MRF from the liquid tank was recycled (Chen et al., 2016). This transmission mode not only avoids the pollution of traditional gear pump but also helps to keep the composition of MRF stable. To suppress the directional surface texture on the workpiece, a dual-rotation MRF finishing (DRMRF) was developed based on the surface texture model for DRMRF and quantitative method of mathematical statistics (Wang Y. Y. et al., 2016). As shown in Figure 8, there are two velocities of the wheel that are perpendicular to each other for high surface quality. Similarly, MRF polishing of ultra-smooth surface based on linear air gap permanent yoke excitation is proposed for large polishing mode, shown in Figure 9 (Wang, 2016). In the device, the particle chain in the MRF is parallel to the surface of the workpiece, which is beneficial to uniform shear force and large effective control area. Moreover, the mathematical model to assess the quantity of material removed was established, and performance parameters such as flatness and material removal rate were analyzed by the model. In addition, a magnetic field–assisted polishing technique was developed for finishing three-dimensional (3D) structured surface with MRF (Wang Y. L. et al., 2016), as shown in Figure 10. In the device, the MRF was specifically modified by blending carbonyl-iron (CI) particles, abrasive grains, and α-cellulose into a magnetic fluid.
Figure 8. The circulatory subsystem of DRMRF tool (Wang Y. Y. et al., 2016).
Figure 9. Schematic diagram of magnetorheological plane polishing (Wang Y. et al., 2016).
Figure 10. The magnetic compound (MC) slurry polishing principle (Wang Y. L. et al., 2016).
In 2017, a tool that has the same curvature as a cylindrical surface was developed, which makes the MRF evenly distributed on the surface of the cylinder, and the strength of the CI particles chain is uniformly maintained over the flat tool tip surface (Singh et al., 2016). Because the tool needs to match the machined surface, this method is not suitable for machining complex curved surfaces. Then, a ball-end MR finishing was proposed for complex curved surfaces (Maan et al., 2017), and whose abrasive wear mechanism was also studied by Alam and Jha (2017). In terms of freeform surfaces, a MRF polishing tool was proposed, where a permanent magnet was used to control the rheological properties of the MRF (Barman and Das, 2017). The dimensions of the tool were optimized with finite element software for a smooth grinding process with low energy consumption. Furthermore, a solid core rotating tool with MRF was developed for finishing of hardened AISI 52100 steel (Maan and Singh, 2018). In this device, response surface methodology was used for the parametric analysis of MRF nanofinishing process, and thus surface cracks generated by the traditional finishing process are eliminated. As the surface morphology of bio-titanium alloy has a great influence on its application, Barman and Das (2018) studied the characteristics of titanium alloy polished by two types of MRFs. From the results, the surface performance obtained from the MRF containing HF and HNO3 is better suited for the semi-permanent type of implants or implants which partake in relative motion, while MRF containing H2O2 is better suited for permanent implants. In addition, as the material removal rate achieved with MRF polishing is relatively low, the concepts of gap slope and virtual ribbon were used to develop a model of removal profiles in Belt-MRF, and the factors in the MRF polishing process were analyzed. From the results, the magnetic field, the composition of the CI powder, and the polishing depth have the greatest effect on material removal rate (MRR) (Wang et al., 2017; Kim et al., 2018).
In 2019, to eliminate the labor-intensive efforts and the subjective errors, a five-axis CNC ball-end MR finishing process in a fully automated manner was developed to the 3D surfaces of the workpiece (Alam et al., 2019). In this device, a customized controller was proposed, which enables the precise and sequential control of motion as well as process parameters. Furthermore, a material removal rate model of MRF finishing with dynamic magnetic fields is proposed to analyze various technological parameters such as rotational speeds of workpieces, magnetic poles, polishing disk, and machining gap (Pan et al., 2019). As shown in Figure 11, dynamic magnetic field is arranged in the device. In this model, the theoretical simulation results favorably agree with the experimental results. Similarly, some process parameters have been optimized using response surface methodology (Chana and Singh, 2019). By using the optimized parameters, the surface finish was reduced to 70 nm from 480 nm in 23 h, and power consumption was reduced by 25%. For finishing of small holes, an MRF finishing set-up was designed, where higher values of supply current, fluid flow rate, and finishing time with flat-pole geometry have generated optimal machining performance characteristics (Kataria and Mangal, 2019). In addition, due to the disadvantage of wheel-type MRF finishing single-point processing, multiple polishing heads with MRF are proposed, where multiple magnets are used to form a specific magnetic field and a plurality of flexible polishing heads are formed on the surface of the heads to process the surface of the workpiece (Bin, 2019).
Figure 11. MRF finishing with dynamic magnetic fields (Bin, 2019).
Recently, Yadav et al. (2020) found that the traditional and advanced gear teeth profile finishing processes without the control over the finishing forces produce different types of defects such as micro-pitting, abrasive wear, and scuffing. So, a process called MRF gear profile finishing was proposed (Yadav et al., 2020), where the parametric study for finishing of the EN24 hardened steel spur gear teeth profile was successfully demonstrated with the technology, and the functional life of gears has been significantly improved. A magnetic field–assisted finishing tool for titanium workpiece has been developed, which consists of a cylindrical permanent magnet and a magnet fixing device (Barman and Das, 2019). There are parallel and helical tool paths in the magnetic field–assisted finishing (MFAF) process, and the lowest surface roughness produced by parallel tool paths has better surface texture than helical tool paths. The reason is that the surface topography and surface texture show reduced surface roughness and scratches when the surface is finished using parallel tool paths. To enhance the surface of the tapered cylindrical workpiece, an MRF finishing process is developed with magnetic rheological polishing (Singh and Singh, 2021). In the device, some parameters such as the variation in linear velocity, helix angle, and the helical path are analyzed to perform uniform finishing on the variable surface. Moreover, a new method with MRF for polishing flat borosilicate glass surfaces has been developed (Zhang et al., 2020). For this method, a reciprocating polishing tester is designed, which uniformly supplies the MRF to produce a flat surface on the workpiece. This greatly reduces the number of peaks and pits on the surface of borosilicate glass and gives a good polishing effect. The finishing forces during the MRF polishing process are analyzed and modeled, where the final surface roughness model has been proposed to predict the polishing performance. The results show a gradual growth of surface precision with polishing time and an augment of polishing efficiency with increasing initial surface roughness (Peng et al., 2020). Moreover, a theoretical model was developed to predict the reduction in the surface asperities during the magnetorheological finishing of the external cylindrical surfaces. The percentage error is from 4.76 to 3.06%, which shows good agreement between the theoretical model and the experimental results (Singh and Singh, 2020). A novel MRF polishing process is developed to use in the internal surface of titanium alloy tubes (Song et al., 2020). In this process, rotation motion of tube and reciprocating linear motion of polishing head are carried out simultaneously resulting in helical motion trajectory of abrasive particles on the workpiece surface, as shown in Figure 12. Because of the extremely lower hardness of copper, wheel-based MRF finishing process has been developed to attain Nano-level surface roughness (Ghosh et al., 2021). In the process, the main controlling parameters, such as the wheel speed, working gap, and feed rate are analyzed, where the MRF with a higher working gap, lower wheel speed, and feed rate can realize Nano-level surface roughness.
Figure 12. Schematic diagram of novel polishing principle (Ghosh et al., 2021).
The techniques and application of MRF surface polishing equipment, developed during 2016–2020, are summarized in Table 1. As can be seen from the table, MRF surface polishing can be applied to the workpiece with various complex surfaces of both metal and non-metallic materials.
MRF polishing process becomes one of the most promising green and intelligent precision machining methods in the future. There is a trend toward the development of the MRF polishing process with super-high precision research from miniaturization (below millimeter) with complex shape workpiece to large scale (several meters) with ultra-smooth flat surface. To obtain precision control, MR polishing equipment is being developed to achieve intelligent control.
In this work, studies on the main applications of MRF in modern precision machining field from 2016 to 2020 are reviewed, which include machining auxiliary equipment and surface polishing equipment. Furthermore, machining auxiliary equipment is divided into MRF flexible fixture and MRF damper in the machine tool. Through the above literature, it is understood that several MRF precision machining technologies focused on the composition of MRF, the arrangement of space magnetic field, and the structural configuration of the equipment.
Because the solid–liquid state of MRF is controlled by the external magnetic field, the MRF flexible fixture can clamp the parts with complex shape, which is convenient for processing. However, the research work on MRF flexible fixture, which is mainly used for processing small parts, is still in the laboratory stage. For larger objects such as the aviation and marine parts, the required MRF flexible fixture will be large, which is not easy to achieve in terms of technology and cost. In addition, with the increasingly complex shapes of the modern machining parts, the MRF flexible fixture has a good development prospect, but the working stability of this fixture needs to be further improved.
The application of MRF damper to suppress tool vibration is a new research field in recent years. Compared with the traditional damper, the MRF damper can better suppress the vibration of the machine tool, prolong the life of the tool, and improve the performance of the machine tool. However, the research methods are relatively simple at present, which mainly include the improvement of semi-active controller, the optimization of magnetic circuit design, and the stability of MRF performance. Due to the complex and variable vibrations in machine tool machining processes, there are few research studies on damper control algorithms. Therefore, it is urgent to improve the control effect of the machine tool and reduce adverse vibrations in the existing structural equipment.
In terms of surface polishing equipment, MRF with conversion in milliseconds forms solid state on the parts that need to be processed and turns into liquid state while taking away the debris, which ensures the accuracy of processing and improves the efficiency of processing. The MRF polishing processing has irreplaceable advantages compared with traditional polishing and has been widely used in precision and ultra-precision machining. But, the current MRF polishing equipment also needs to strengthen the magnetic rheological polishing research on the non-spherical surfaces, broaden processing adaptability, improve the machining efficiency, and reduce the processing cost.
As a new type of intelligent material, MRF has excellent performance in the field of modern precision machining. It may be further developed in the following three aspects in the future. The stability and heat dissipation of MRF are the bottlenecks, limiting its application at present, and the problem of accurate control of MRF has not been solved. With the deepening of research on MRF, the performance of MRF could be further improved. Furthermore, MRF can cooperate with various magnetic materials and magnetic structures rather than the electromagnetic field and permanent magnet, to achieve specific functions and reduce electrical energy consumption and equipment costs. Finally, the research in the field of MRF machining is still in the laboratory stage, which is mainly customized by users and has not yet achieved universality. With the in-depth study of the processing technology and system control strategy by scholars, different MRF machining equipment will be widely used.
HL and CY: writing original manuscript. DH: software. BW: resources. AH-S: methodology. GK: editing and review. XL: funding. ZL: supervising. All authors contributed to the article and approved the submitted version.
This work was supported by the National Science Foundation of China (No. 51975568), the Natural Science Foundation of Jiangsu Province (No. BK20191341), the Natural Science Foundation of the Jiangsu Higher Education Institution of China (20KJD460005), the Youth Talents Program (LSZQNXM202001), the Priority Academic Program Development of Jiangsu Higher Education Institutions (PAPD), and the Key scientific research project of Suzhou University (2017yzd14) in carrying out this research are gratefully acknowledged.
The authors declare that the research was conducted in the absence of any commercial or financial relationships that could be construed as a potential conflict of interest.
Aggarwal, A., and Singh, A. K. (2011). Development of grinding wheel type magnetorheological finishing process for blind hole surfaces. Mater. Manuf. Process. 36, 457–478. doi: 10.1080/10426914.2020.1843666
Alam, Z., Iqbal, F., Ganesan, S., and Jha, S. (2019). Nanofinishing of 3D surfaces by automated five-axis CNC ball end magnetorheological finishing machine using customized controller. Intern. J. Adv. Manuf. Technol. 100, 1031–1042. doi: 10.1007/s00170-017-1518-0
Alam, Z., and Jha, S. (2017). Modeling of surface roughness in ball end magnetorheological finishing (BEMRF) process. Wear 374, 54–62. doi: 10.1016/j.wear.2016.11.039
Barman, A., and Das, M. (2017). Design and fabrication of a novel polishing tool for finishing freeform surfaces in magnetic field assisted finishing (MFAF) process. Precis. Eng. 49, 61–68. doi: 10.1016/j.precisioneng.2017.01.010
Barman, A., and Das, M. (2018). Nano-finishing of bio-titanium alloy to generate different surface morphologies by changing magnetorheological polishing fluid compositions. Precis. Eng. 51, 145–152. doi: 10.1016/j.precisioneng.2017.08.003
Barman, A., and Das, M. (2019). Toolpath generation and finishing of bio-titanium alloy using novel polishing tool in MFAF process. Intern. J. Adv. Manuf. Technol. 100, 1123–1135. doi: 10.1007/s00170-017-1050-2
Bedi, T. S., and Singh, A. K. (2016). Magnetorheological methods for nanofinishing – a review. Partic. Sci. Technol. 34, 412–422. doi: 10.1080/02726351.2015.1081657
Biju, C. V., and Shunmugam, M. S. (2019). Performance of magnetorheological fluid based tunable frequency boring bar in chatter control. Measurement 140, 407–415. doi: 10.1016/j.measurement.2019.03.073
Bin, S. M. (2019). Device Design and Experimental Research of Magnetorheological Finishing with Multiple Polishing Heads [D]. Guangzhou: Guangdong University of Technology.
Chana, A., and Singh, A. K. (2019). Magnetorheological nano-finishing of tube extrusion punch for improving its functional applications in press machine. Intern. J. Adv. Manuf. Technol. 103, 2037–2052. doi: 10.1007/s00170-019-03633-1
Chen, K., Yu, X., Wang, H., Zheng, H., Zhang, G., and Wu, R. (2021). Modeling of a Bingham model of a magnetorheological damper considering stochastic uncertainties their geometric variables. J. Theoret. Appl. Mechan. 59, 53–65. doi: 10.15632/jtam-pl/128811
Chen, M. J., Liu, H. N., Su, Y. R., Yu, B., and Fang, Z. (2016). Design and fabrication of a novel magnetorheological finishing process for small concave surfaces using small ball-end permanent-magnet polishing head. Intern. J. Adv. Manuf. Technol. 83, 823–834. doi: 10.1007/s00170-015-7573-5
Cheng, M., Xing, J., Chen, Z., and Pan, Z. (2019). Design, Analysis and experimental investigation on the whole-spacecraft vibration isolation platform with magnetorheological dampers. Smart Mater. Struct. 28:075016. doi: 10.1088/1361-665X/ab0ebe
Dubey, N. K., and Sidpara, A. (2021). Numerical and experimental study of influence function in magnetorheological finishing of oxygen-free high conductivity (OFHC) copper. Smart Mater. Struct. 30:015034. doi: 10.1088/1361-665X/abcca5
Elsaady, W., Oyadiji, S. O., and Nasser, A. (2020). A review on multi-physics numerical modelling in different applications of magnetorheological fluids. J. Intellig. Mater. Syst. Struct. 31, 1855–1897. doi: 10.1177/1045389X20935632
Ghosh, G., Sidpara, A., and Bandyopadhyay, P. P. (2021). Experimental and theoretical investigation into surface roughness and residual stress in magnetorheological finishing of OFHC copper. J. Mater. Process. Technol. 288:116899. doi: 10.1016/j.jmatprotec.2020.116899
Girinath, B., Mathew, A., Babu, J., Thanikachalam, J., and Bose, S. S. (2018). Improvement of surface finish and reduction of tool wear during hard turning of AISI D3 using magnetorheological damper. J. Sci. Industr. Res. 77, 35–40.
Golini, D., Kordonski, W. I., Dumas, P., and Hogan, S. (1999). Magnetorheological finishing (MRF) in commercial precision optics manufacturing. Proc. SPIE Intern. Soc. Optic. Eng. 3782, 80–91. doi: 10.1117/12.369174
Gupta, M. K., Dinakar, D., Chhabra, I. M., Jha, S., and Madireddy, B. S. (2021). Experimental investigation and machine parameter optimization for nano finishing of fused silica using magnetorheological finishing process. Optik 226:165908. doi: 10.1016/j.ijleo.2020.165908
Jain, V. K., Sidpara, A., Sankar, M. R., and Das, M. (2012). Nano-finishing techniques: a review. Proc. Institut. Mech. Eng. Part C J. Mech. Eng. Sci. 226, 327–346. doi: 10.1177/0954406211426948
Jiang, M., Rui, X., Zhu, W., Yang, F., and Zhang, Y. (2021). Design and control of helicopter main reducer vibration isolation platform with magnetorheological dampers. Intern. J. Mech. Mater. Design 144, 1–22. doi: 10.1007/s10999-021-09529-x
Jiang, X., Zhang, Y., Lu, W., Gao, S., Liu, L., and Liu, X. (2020). Characteristics of shear stress based on magnetorheological fluid flexible fixture during milling of the thin-walled part. Intern. J. Adv. Manufact. Technol. 108, 2607–2619. doi: 10.1007/s00170-020-05439-y
Jiang, X. H., Zhao, G. K., and Lu, W. W. (2020). Vibration suppression of complex thin-walled workpiece based on magnetorheological fixture. Intern. J. Adv. Manuf. Technol. 106, 1043–1055. doi: 10.1007/s00170-019-04612-2
Jung, H., Hayasaka, T., Shamoto, E., and Xu, L. (2020). Suppression of forced vibration due to chip segmentation in ultrasonic elliptical vibration cutting of titanium alloy Ti-6Al-4V. Precis. Eng. 64, 98–107. doi: 10.1016/j.precisioneng.2020.03.017
Kataria, M., and Mangal, S. K. (2019). Development of continuous flow magnetorheological fluid finishing process for finishing of small holes. J. Braz. Soc. Mech. Sci. Eng. 41:551. doi: 10.1007/s40430-019-2027-x
Kim, B. C., Chung, J. H., Cho, M. W., Ha, S. J., and Yoon, G. S. (2018). Magnetorheological fluid polishing using an electromagnet with straight pole-piece for improving material removal rate. J. Mech. Sci. Technol. 32, 3345–3350. doi: 10.1007/s12206-018-0637-3
Kishore, R., Choudhury, S. K., and Orra, K. (2018). On-line control of machine tool vibration in turning operation using electro-magneto rheological damper. J. Manuf. Process. 31, 187–198. doi: 10.1016/j.jmapro.2017.11.015
Kong, J. X., Zheng, Y. C., and Wang, X. K. (2011). Fixture design based on magneto-rheological fluids for thin wall spherical shell precision machining. Adv. Mater. Res. 215, 315–319.
Kulandaivel, A., and Kumar, S. (2020). Effect of magneto rheological minimum quantity lubrication on machinability, wettability and tribological behavior in turning of Monel K500 alloy. Machin. Sci. Technol. 24, 810–836. doi: 10.1080/10910344.2020.1765179
Kumar, A., Alam, Z., Khan, D. A., and Jha, S. (2019). Nanofinishing of FDM-fabricated components using ball end magnetorheological finishing process. Adv. Manuf. Process. 34, 232–242. doi: 10.1080/10426914.2018.1512136
Kumar, T., Kumar, R., and Jain, S. C. (2021). Numerical investigation of semi-active torsional vibration control of heavy turbo-generator rotor using magnetorheological fluid dampers. J. Vibr. Eng. Technol. 93, 1–15. doi: 10.1007/s42417-020-00276-5
Liang, H., Yan, Q., Pan, J., Luo, B., Lu, J., and Zhang, X. (2021). Characteristics of forces in plane polishing based on the magnetorheological effect with dynamic magnetic fields formed by rotating magnetic poles. J. Test. Eval. 49, 255–269. doi: 10.1520/JTE20180769
Liu, C. P., and Hu, J. P. (2019). A magnetorheological hydrostatic guideway system for machining vibration control. J. Braz. Soc. Mech. Sci. Eng. 41, 1–12. doi: 10.1007/s40430-018-1525-6
Liu, H., Wang, J., Luo, Q., Bo, Q., Li, T., and Wang, Y. (2020). Effect of controllable magnetic field-induced MRF solidification on chatter suppression of thin-walled parts. Intern. J. Adv. Manuf. Technol. 109, 2881–2890. doi: 10.1007/s00170-020-05783-z
Liu, Z., Li, J., Nie, M., and Liu, Y. (2020). Modeling and simulation of workpiece surface flatness in magnetorheological plane finishing processes. Intern. J. Adv. Manuf. Technol. 111, 2637–2651. doi: 10.1007/s00170-020-06267-w
Lv, H., Zhang, S., Sun, Q., Chen, R., and Zhang, W. (2021). The dynamic models, control strategies and applications for magnetorheological damping systems: a systematic review. J. Vibr. Eng. Technol. 9, 131–147. doi: 10.1007/s42417-020-00215-4
Ma, J., Zhang, D., Wu, B., Luo, M., and Chen, B. (2016). Vibration suppression of thin-walled workpiece machining considering external damping properties based on magnetorheological fluids flexible fixture. Chin. J. Aeronaut. 29, 1074–1083. doi: 10.1016/j.cja.2016.04.017
Ma, J., Zhang, D., Wu, B., Luo, M., and Liu, Y. (2017). Stability improvement and vibration suppression of the thin-walled workpiece in milling process via magnetorheological fluid flexible fixture. Intern. J. Adv. Manuf. Technol. 88, 1231–1242. doi: 10.1007/s00170-016-8833-8
Ma, J. J. (2017). Dynamic Model and Reconstruction Method of Magnetorheological Damping Support Fixture-Workpiece System [D]. Xi’an: Northwestern Polytechnical University.
Maan, S., and Singh, A. K. (2018). Nano-surface finishing of hardened AISI 52100 steel using magnetorheological solid core rotating tool. Intern. J. Adv. Manuf. Technol. 95, 513–526. doi: 10.1007/s00170-017-1209-x
Maan, S., Singh, G., and Singh, A. K. (2017). Nano-surface-finishing of permanent mold punch using magnetorheological fluid-based finishing processes. Mater. Manuf. Process. 32, 1004–1010. doi: 10.1080/10426914.2016.1232823
Mutalib, N. A., Ismail, I., Soffie, S. M., and Aqida, S. N. (2019). Magnetorheological finishing on metal surface: a review. IOP Conf. Ser. Mater. Sci. Eng. 469:012092. doi: 10.1088/1757-899X/469/1/012092
Nagdeve, L., Jain, V. K., and Ramkumar, J. (2019). Preliminary investigations into nano-finishing of freeform surface (femoral) using inverse replica fixture. Intern. J. Adv. Manuf. Technol. 100, 1081–1092. doi: 10.1007/s00170-017-1459-7
Nguyen, D., Wu, J. Z., Quang, N. M., Duc, L. A., and Son, P. X. (2021). Applying fuzzy grey relationship analysis and Taguchi method in polishing surfaces of magnetic materials by using magnetorheological fluid. Intern. J. Adv. Manuf. Technol. 112, 1675–1689. doi: 10.1007/s00170-020-06567-1
Nugroho, K. C., Ubaidillah, P. B., Mas’udi, A., Nordin, N., Mazlan, S., and Choi, S. (2020). The effect of MnxCo(1-x) Fe2O4 with x = 0, 0.25 and 0.5 as nanoparticles additives in magnetorheological fluid. Smart Mater. Struct. 29:114004. doi: 10.1088/1361-665X/abb354
Oladapo, B. I., Muhammad, M. A., Adebiyi, V. A., Oluwole, B., and Usman, H. (2020). Model hybrid magnetorheological damping prediction in machine tools. Eng. Struct. 213:110621. doi: 10.1016/j.engstruct.2020.110621
Pan, J. S., Guo, M. L., Yan, Q. S., Zheng, K., and Xiao, X. L. (2019). Research on material removal model and processing parameters of cluster magnetorheological finishing with dynamic magnetic fields. Intern. J. Adv. Manuf. Technol. 100, 2283–2297. doi: 10.1007/s00170-018-2747-6
Park, G., Bement, M. T., Hartman, D. A., Smith, R. E., and Farrar, C. R. (2007). The use of active materials for machining processes: a review. Intern. J. Adv. Manuf. Technol. 47, 2189–2206. doi: 10.1016/j.ijmachtools.2007.06.002
Paul, P. S., Sunil, K. S., and Varadarajan, A. S. (2017). The Effect of cutting parameters on tool vibration during magnetorheological fluid controlled turning bar. Intern. J. Acoust. Vibr. 22, 27–33. doi: 10.20855/ijav.2017.22.1447
Peng, Z., Song, W. L., Ye, C. L., Shi, P., and Choi, S. B. (2020). Model establishment of surface roughness and experimental investigation on magnetorheological finishing for polishing the internal surface of titanium alloy tubes. J. Intellig. Mater. Syst. Struct. 1, 1–12. doi: 10.1177/1045389X20930095
Puma-Araujo, S. D., Olvera-Trejo, D., Martinez-Romero, O., Urbikain, G., Elias-Zuniga, A., and Lopez de Lacalle, L. N. (2020). Semi-active magnetorheological damper device for chatter mitigation during milling of thin-floor components. Appl. Sci. Basel 10:5313. doi: 10.3390/app10155313
Rafajowicz, W., Wickowski, J., Moczko, P., and Rafajlowicz, E. (2020). Iterative learning from suppressing vibrations in construction machinery using magnetorheological dampers. Autom. Construct. 119:103326. doi: 10.1016/j.autcon.2020.103326
Rahman, M., Ong, Z. C., Julai, S., Ferdaus, M. M., and Ahamed, R. (2017). A review of advances in magnetorheological dampers: their design optimization and applications. J. Zhejiang Univ. Sci. A 18, 991–1010. doi: 10.1631/jzus.A1600721
Saleh, M. K. A., Nejatpour, M., Acar, H. Y., and Lazoglu, I. (2021). A new magnetorheological damper for chatter stability of boring tools. J. Mater. Process. Technol. 289:116931. doi: 10.1016/j.jmatprotec.2020.116931
Saleh, M. K. A., Nejatpour, M., Acar, H. Y., and Lazoglu, L. (2020). A new magnetorheological damper for chatter stability of boring tools. J. Mater. Process. Technol. 289:116931.
Singh, G., Singh, A. K., and Garg, P. (2016). Development of magnetorheological finishing process for external cylindrical surfaces. Mater. Manuf. Process. 32, 581–588. doi: 10.1080/10426914.2016.1221082
Singh, M., and Singh, A. (2020). Theoretical investigations into magnetorheological finishing of external cylindrical surfaces for improved performance. Proc. IMechE Part C J. Mech. Eng. Sci. 234, 4872–4892. doi: 10.1177/0954406220931550
Singh, M., and Singh, A. K. (2021). Magnetorheological finishing of variable diametric external surface of the tapered cylindrical workpieces for functionality improvement. J. Manuf. Process. 61, 153–172. doi: 10.1016/j.jmapro.2020.10.074
Song, W. L., Peng, Z., Li, P. F., Shi, P., and Choi, S. B. (2020). Annular surface micromachining of titanium tubes using a magnetorheological polishing technique. Micromachines 11:314. doi: 10.3390/mi11030314
Tang, C., Liu, D., Xiao, Q., and Wang, J. (2016). “Research on chatter suppression based on MRF in turning,” in Proceedings of the Progress in Electromagnetic Research Symposium, Shanghai.
Wang, D. K., Hu, H. X., Li, L. X., Bai, Y., Luo, X., and Zhang, X. J. (2017). Effects of the gap slope on the distribution of removal rate in Belt-MRF. Optics Express. 25, 26600–26614. doi: 10.1364/OE.25.026600
Wang, J., and Meng, G. (2001). Magnetorheological fluid devices: principles, characteristics and applications in mechanical engineering. Proc. Instit. Mech. Eng. Part L J. Mater. Design Applic. 215, 165–174. doi: 10.1243/1464420011545012
Wang, Y. (2016). Study on Magnetorheological Finishing Using Large Polishing Tool for Ultra-smooth Flat Surface [D]. Changsha: Hunan University.
Wang, Y., Yin, S., and Huang, H. (2016). Polishing characteristics and mechanism in magnetorheological planarization using a permanent magnetic yoke with translational movement. Precis. Eng. J. Intern. Soc. Precis. Eng. Nanotechnol. 43, 93–104. doi: 10.1016/j.precisioneng.2015.06.014
Wang, Y. L., Wu, Y. B., and Mitsuyoshi, N. (2016). A novel magnetic field-assisted polishing method using magnetic compound slurry and its performance in mirror surface finishing of miniature V-grooves. AIP Adv. 6:056602. doi: 10.1063/1.4942952
Wang, Y. Y., Zhang, Y., and Feng, Z. J. (2016). Analyzing and improving surface texture by dual-rotation magnetorheological finishing. Appl. Surf. Sci. 360, 224–233. doi: 10.1016/j.apsusc.2015.11.009
Wu, J. X. (2019). Analysis of the Influence of Magnetorheological Excitation Solidification Characteristics on Cutting Vibration Suppression of Thin-Walled Part [D]. Dalian: Dalian University of Technology.
Wuertz, T., May, C., Holz, B., Janocha, H., Rodriguez, M. D., Collado, V., et al. (2010). “Fixturing of complex shaped Workpieces with magnetorheological fluids,” in Proceedings of the 12th International Conference on New Actuators/6th International Exhibition on Smart Actuators and Drive Systems, Bremen.
Yadav, R. D., Singh, A. K., and Arora, K. (2020). Parametric analysis of magnetorheological finishing process for improved performance of gear profile. J. Manuf. Process. 57, 254–267. doi: 10.1016/j.jmapro.2020.06.024
Yan, B., Zhu, L., and Liu, C. (2020). Prediction model of peripheral milling surface geometry considering cutting force and vibration. Intern. J. Adv. Manuf. Technol. 110, 1429–1443. doi: 10.1007/s00170-020-05930-6
Yu, J., Dong, X., Qi, S., Wang, T., and Liang, Y. (2021). Development of a magnetorheological isolator with variable damping and variable stiffness for broadband vibration suppression. Smart Mater. Struct. 30:025023. doi: 10.1088/1361-665X/abd4fc
Zhang, P., Dong, Y. Z., Choi, H. J., Lee, C. H., and Gao, Y. S. (2020). Reciprocating magnetorheological polishing method for borosilicate glass surface smoothness. J. Industr. Eng. Chem. 84, 243–251. doi: 10.1016/j.jiec.2020.01.004
Zhong, Z. (2020). Advanced polishing, grinding and finishing processes for various manufacturing applications: a review. Mater. Manuf. Process. 35, 1279–1303. doi: 10.1080/10426914.2020.1772481
Keywords: magnetorheological fluid, machining auxiliary equipment, magnetorheological fluid flexible fixtures, surface polishing equipment, structure configuration
Citation: Lu H, Hua D, Wang B, Yang C, Hnydiuk-Stefan A, Królczyk G, Liu X and Li Z (2021) The Roles of Magnetorheological Fluid in Modern Precision Machining Field: A Review. Front. Mater. 8:678882. doi: 10.3389/fmats.2021.678882
Received: 10 March 2021; Accepted: 19 April 2021;
Published: 12 May 2021.
Edited by:
Yancheng Li, University of Technology Sydney, AustraliaReviewed by:
U. Ubaidillah, Sebelas Maret University, IndonesiaCopyright © 2021 Lu, Hua, Wang, Yang, Hnydiuk-Stefan, Królczyk, Liu and Li. This is an open-access article distributed under the terms of the Creative Commons Attribution License (CC BY). The use, distribution or reproduction in other forums is permitted, provided the original author(s) and the copyright owner(s) are credited and that the original publication in this journal is cited, in accordance with accepted academic practice. No use, distribution or reproduction is permitted which does not comply with these terms.
*Correspondence: Xinhua Liu, bGl1eGluaHVhQGN1bXQuZWR1LmNu; Zhixiong Li, emhpeGlvbmcubGlAeW9uc2VpLmFjLmty
Disclaimer: All claims expressed in this article are solely those of the authors and do not necessarily represent those of their affiliated organizations, or those of the publisher, the editors and the reviewers. Any product that may be evaluated in this article or claim that may be made by its manufacturer is not guaranteed or endorsed by the publisher.
Research integrity at Frontiers
Learn more about the work of our research integrity team to safeguard the quality of each article we publish.