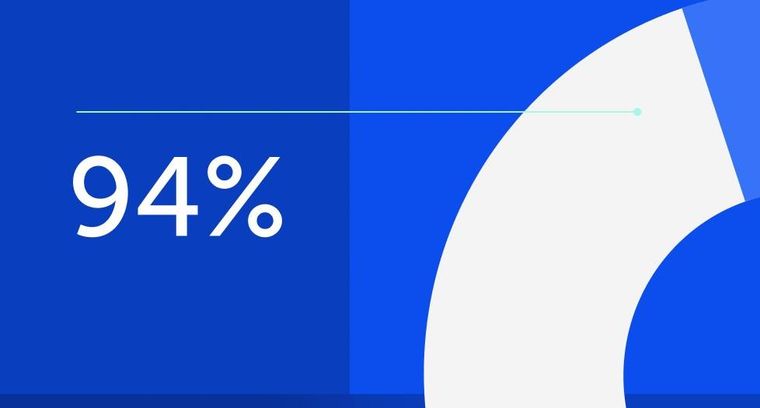
94% of researchers rate our articles as excellent or good
Learn more about the work of our research integrity team to safeguard the quality of each article we publish.
Find out more
ORIGINAL RESEARCH article
Front. Mater., 28 May 2021
Sec. Smart Materials
Volume 8 - 2021 | https://doi.org/10.3389/fmats.2021.668125
This article is part of the Research Topic2021 Retrospective: Smart MaterialsView all 11 articles
This article studies the creep and recovery behavior of magnetorheological grease (MRG) under constant stress shear. The experiment is done by using a parallel plate rheometer with magnetron attachment and temperature control unit. The effects of constant stress, CI particle concentration, magnetic flux density and temperature on creep and recovery behavior are systematically studied. Experimental results show that as the constant stress increases, the response strain will also increase. The creep strain tested under zero field is higher than the value tested under a magnetic field, indicating that the creep and recovery behavior of MRG is highly dependent on the magnetic field strength. In addition, the creep and recovery behavior of MRG is greatly affected by temperature. Under the action of a magnetic flux density, the creep strain will decrease with the increase of temperature. The result is opposite at zero magnetic field.
The time-dependent viscoelastic properties of polymer materials are mainly characterized by creep and recovery, which is an important standard to evaluate the dimensional stability of engineering materials (Xia et al., 2007; Iurzhenko et al., 2014; Chen et al., 2015). When the material is loaded with constant stress, the phenomenon that the strain will change with time is called creep. If the stress is removed instantaneously, the strain of materials changes with time without stress, and the phenomenon is defined as recovery. Research on creep and recovery behavior of viscoelastic materials is the main means to evaluate their properties, which provides theoretical support for its practical application.
The magnetorheological (MR) material is an intelligent material, it generally includes MR fluid (Cheng et al., 2021), MR gel (Mao et al., 2020; Zhang and Wang, 2020), MR elastomer (Yang et al., 2015; Fu et al., 2019) and MR grease (Ye et al., 2021). its rheological properties will change continuously, rapidly and reversibly under the external magnetic field. As an intelligent viscoelastic material, the creep and recovery behavior was studied by many scholars. Li et al. (2002) completed a study of the effects of magnetic field strength and temperature on creep behavior. The results indicated that MR fluids have two different viscoelastic behaviors. The behavior as linear viscoelastic bodies at small stresses. With increasing constant stresses, the MR fluids have nonlinear viscoelastic, viscoplastic and purely plastic properties at the same time. The creep and recovery behaviors of MR fluids can be explained by a typically thick column structure. Li et al. (2002), Weihua et al. (2010) studied the creep and recovery behavior of MR elastomers under constant stress. They established a four-parameter viscoelastic model to describe the creep behavior of the MR elastomer. The comparison between the experimental results and the model prediction results shown that the model can well predict the creep behavior of the MR elastomer. Xu et al. (2012) investigated the creep and recovery behaviors of MR plastomer under constant stress and proposed a hypothesis to explain the temperature effect on the creep behaviors of the MR plastomer. The experiment showed that there are a great discrepancy in creep curves for the isotropic and anisotropic MR plastomer under an external magnetic field. Qi et al. (2016) investigated the creep and recovery behaviors of MR elastomers based on polyurethane/epoxy resin (EP) graft interpenetrating polymer networks. The experiment illustrated that the presence of interpenetrating polymer networks leads to a significant improvement of creep resistance of MR elastomers. Several theoretical models [i.e., Findley’s power law model (Findley et al., 1977), Burgers model (Yao et al., 2013), and Weibull distribution equation (Fancey, 2005)] were used to simulate the creep and recovery of the specimens. The influence of EP content and magnetic field on the fitting parameters were discussed, and the corresponding physical mechanism was proposed to qualitatively explain it.
The magnetorheological grease (MRG), as a kind of MR material. It has the advantages of good anti-settling performance, less leakage, high MR effect and simple preparation. Thus, it has a good application prospect in various devices such as buffer (Ou et al., 2017; Ouyang et al., 2019), clutch (Kavlicoglu et al., 2013; Fernandez et al., 2018) and brake (Wang D. et al., 2019). At present, researchers have carried out a lot of research on the related properties (viscosity, shear stress, yield stress, storage modulus, and energy dissipation modulus, etc.) of MRG (Rankin et al., 1999; Park et al., 2011; Kim et al., 2012; Hu et al., 2015; Mohamad et al., 2016a,b, 2018; Wang H. X. et al., 2019). However, there are no published literature reports on the creep and recovery behavior of MRG.
Based on the existing research results of the creep and recovery behavior for smart materials, the creep and recovery test research for MRG is carried out, which provides theoretical guidance for the future and its applications. In this paper, The main contents of this paper are as follows. An advanced MR instrument was used to test the flow curve, creep and recovery behavior of MRG in shear mode. The effects of constant stress, magnetic field strength, CI particle content and temperature on creep and recovery behavior are systematically studied. The reasons that why the creep and recovery behavior are affected by different factors are analyzed and discussed.
In this paper, MRG is made by uniformly mixing carbonyl iron powder and the grease. Among them, the carbonyl iron particles (dispersed phase) are purchased by BASF and the average particle size is 6 μm. Lithium-based grease is manufactured by Shell (china) Ltd. It is used as a carrier medium for magnetic particles. The physical properties of lithium grease are shown in Table 1. In this article, a MRG sample containing 70% carbonyl iron powder was prepared. The simple preparation process is shown in Figure 1. First, weigh 30 g of grease and pour it into a vial, then use a mechanical stirrer to stir at 800 rpm for about 10 min, and keep its temperature at 80°C. After the stirring is completed, 70 g of CI particles are poured into the stirred matrix. Finally, use a stirrer to thoroughly mix the grease and CI particles to obtain MRG. At this time, it is recorded as MRG-70. In addition, for experimental needs, a MRG with a mass fraction of carbonyl iron powder of 50% was also prepared. It is referred to as MRG-50 for short. Due to the unique characteristics of lithium-based grease in MRG, the sedimentation in the material is greatly reduced. Due to the unique characteristics of lithium-based grease in MRG, the precipitation in the material is greatly reduced.
At a constant temperature, the creep and recovery curve of a typical viscoelastic material is shown in Figure 2. It can be seen from Figure 2 that the strain of the material increases logarithmically with time in the stress section, that is, the creep stage. When the stress is removed, the strain of the material quickly decreases to a certain value, that is, the viscoelastic material is in the recovery stage. In Figure 2, τ0 is a constant stress and γ is a strain.
Figure 2. Creep and recovery behavior to an applied constant stress for linear viscoelastic materials.
It can be seen from Figure 2, when a constant stress τ0 is applied to the sample for a time period, the strain generated by the sample is composed of instantaneous strain γs, retardation strain γd(t), and viscous flow γv(t). Therefore, the relationship between the creep strain γC of the sample and the time t can be expressed as formula (1).
For linear viscoelastic materials, the strain only has instantaneous strain, which represents the material’s reversible (when stress is applied and eliminated) elastic characteristics. Usually, the elastic strain of linear viscoelastic materials is expressed as γs = γe, The second term on the right side of the formula (1) represents the retardation strain, which decreases with the increasing trend of time, showing a yielding trend. Under the effect of the chain uncoiling of the material, it can be fully recovered within a certain period of time and has elastic properties (Qi et al., 2016). The viscous flow is the irreversible part of the creep strain. It has a linear relationship with time in a linear viscoelastic fluid (Qi et al., 2016).
Since the magnitude of the three components of creep strain is proportional to the magnitude of the input stress, a creep compliance function can be defined as:
Substitute equation (1) into equation (2) to get
It can be seen from Figure 2 that when the sample stress (t = t0) is eliminated, the instantaneous strain γs recovers instantly, the retardation strain γd(t) gradually recovers, and the viscous flow γv(t) does not change. Therefore, the relationship between recovery strain with time can be expressed by equation (4).
Similar to the definition of JC(t), the definition of a recovery compliance function is as shown in formula (5)
Assuming that the viscoelasticity of the sample is linear, the total creep strain at any time can be expressed as the sum of two independent strains, as shown in eq. (6).
where, τ0JC(t0) is the creep strain at t = t0 and τ0JR(t−t0) is unloading at t = t0.
The instantaneous strain produced by linear viscoelastic materials under constant stress loading only represents its elastic coefficient(γs = γe), which can be completely restored after stress is eliminated. However, for nonlinear viscoelastic-plastic materials, the instantaneous strain generated under constant stress loading characterizes the elastic and plastic properties of the material, as shown in Figure 3, and the expression is shown in eq. (7). As shown in Figure 3, after the stress is removed, the instantaneous recovery strain is equal to the elastic strain, and the plastic strain cannot be recovered.
In the formula, γp represents plastic strain.
Magnetorheological grease was measured by using a parallel plate rheometer (Physica MCR 302, Anton Paar, Austria) with a magnetron unit (MRD 180) and a temperature control unit (JULABO F25). In this study, a plate rotor with a diameter of 20 mm was used. During the experiment, the gap between the plate and the base was set to 1 mm. The calculated results show that the sample required for each experiment is about 0.315 mL.
This experiment mainly studies the creep and recovery characteristics of MRG. In the rotating shear test, the flow curve of MRG under different magnetic flux density was measured, and the shear rate was set to 0.1 s–1 to 100 s–1. Creep and recovery characteristics are also tested under shear conditions. For the experiment on the effect of creep recovery behavior under constant stress, the constant stress is 50, 100, 165, and 200 Pa when the zero field is set, and when the magnetic flux density is 47 mT, the constant stress is 50, 100, and 200 Pa. In the magnetic field strength test, the fixed stress is set to 50 Pa and the magnetic flux density is set to 0, 24, 47, 67, 96, and 120 mT. In addition, the effect of the mass fraction of CI particles in different MRGs on the creep recovery curve is studied. And in the temperature influence experiment, set the temperature to 10, 50, and 70°C, and the fixed stress is 200 Pa; Compare the creep and recovery behavior with or without magnetic field. In the experiment, except for the temperature experiment, all other test temperatures were tested at 30°C. In addition, the entire test must be pre-sheared (the shear rate is constant at 10 s–1, pre-shearing time 20 s) to ensure the consistency of each measurement and all experiments are performed three times to ensure the data obtained repeatability.
When using rheometer equipment, the selected magnetic field is expressed in the form of current, and the magnetic flux density corresponding to the current is calculated by the relationship between the current and the magnetic flux density in Figure 4. Figure 5 shows the relationship between the shear rate and shear stress of MRG under different magnetic field strengths. It can be seen from Figure 4 that the shear stress increases with the increase of the shear rate. In addition, when the shear rate is constant, the value of the shear stress will increase with the increase of the magnetic flux density.
In this study, the Bingham-plastic model was used to describe the plastic flow stage of MRG in different magnetic fields. The model is defined as (Rabbani et al., 2015):
where τ and represent the shear stress and shear rate, respectively. τy is yield stress as a function of magnetic field and ηp is the plastic viscosity. Use Origin8.0 software to fit Figure 5 to get the dynamic yield stress. Table 2 lists the dynamic yield stress under different magnetic field conditions.
Constant stress is an important parameter when measuring creep and recovery characteristics, and its value has an important influence on creep and recovery characteristics. In addition, MRG is a smart material that is sensitive to magnetic field. Therefore, in this section, for the purpose of comparative study, we will conduct creep recovery characteristics experiments on both the magnetic field and the non-magnetic field. The experimental results are shown in Figure 6. It can be seen from Figure 6 that the MRG creep curve increases with time when it is in the retardation strain. After the stress is relieved at 150 s, the strain immediately drops to a lower level. However, there are big differences between the two cases with and without magnetic field. For example, under the same shear stress of 200 Pa, the response strain without magnetic field strength is larger than the response strain after loading the magnetic field. This is because the magnetic field makes the MRG become stiffer and the interaction of iron particles restrict the movements of chain, which leads to a reduction in strain. In addition, as the constant stress level increases, the response strain will increase accordingly, whether or not an external magnetic field is applied to MRG. Moreover, the response strain is proportional to creep time in the absence of magnetic field. According to Table 2, the dynamic yield stress of MRG under zero magnetic field is 165 Pa, so when the shear stress is set to be greater than or equal to 165 Pa, the material basically has no recovery behavior.
Figure 6. Creep and recovery curves of MRG under different constant stress. (A) B = 0 mT; (B) B = 47 mT.
Magnetic excitation is one of the most important characteristics of MR materials. Figures 7A,B shows the dependence of the magnetic field on MRG creep and recovery behavior under a constant stress of 50 Pa, where the field strength is set to 0, 24, 47, 67, 96, and 120 mT; It can be seen from Figure 7 that under the same creep time and stress, the creep strain decreases sharply with the increase of the magnetic field. The creep strain of the MRG without a magnetic field is 213 times that of the MRG with a 120 mT magnetic field, and the ratio will increase as the creep time increases. The reason is that the greater the magnetic field strength, the more stable the chain structure in the MRG will reduce the creep strain. In the absence of a magnetic field, MRG behaves as a viscous liquid, and its low viscosity makes the shear stress of the material very low. However, after the constant shear stress is eliminated (more than 150 s), the creep strain can drop sharply, and change smoothly after reaching a certain value. It can be seen from Figure 7 that the creep strain can be partially recovered.
Figure 7. Creep and recovery curves of MRG under the combined action of 50 Pa stress and different magnetic fields.
Previous studies have shown that the content of CI particles has a great influence on the viscosity and shear stress of MR materials, so this experiment tested the effect of the content of CI particles in MRG on creep recovery characteristics. Figure 8A shows the creep and recovery characteristics of the tested MRG mass fractions of 50% and 70% under no magnetic field and constant stress of 100 and 200 Pa. It can be seen from Figure 8A that before 150 s, the response stress increases linearly with time, and after 150 s, the MRG strain almost stabilizes, which is consistent with the results in section “The Influence of Stress Level on Creep and Recovery Behaviors.” In addition, under the same mass fraction (50 or 70%), the greater the response stress applied, the greater the strain of MRG, which is consistent with the results in section “The Influence of Stress Level on Creep and Recovery Behaviors.” For different mass fractions, the higher the CI mass fraction in the MRG, the smaller the strain value, because the higher the CI mass fraction, the viscosity value in the MRG will increase, which will make the strain value higher than the low mass fraction MRG. In addition, Figure 8B shows the creep and recovery characteristics of the tested MRG mass fractions of 50 and 70% under the magnetic field of 47 mT. It can be seen from Figure 8B that the result after applying a magnetic field has a similar trend to the result without applying a magnetic field, but the difference is that the amount of strain of the MRG material is smaller after applying a magnetic field. This result has been obtained in section “The Influence of Magnetic Field Strength on Creep and Recovery Behaviors.”
Figure 8. Creep and recovery curves of MRG under different mass fractions (A) B = 0 mT; (B) B = 47 mT.
Figure 9 shows the creep recovery behavior of MRG at three temperatures of 10, 50, and 70°C under a constant stress of 200 Pa. The experiment was done under the absence of magnetic field. It can be seen from Figure 9 that under the same creep time, the creep strain will increase with the increase of temperature. This is because the viscosity of MRG will become thinner under the action of no magnetic field with the increase of temperature (Wang H. X. et al., 2019). The softening of the material results in a smaller creep strain. This is exactly the same as the result of MR plastomer (Xu et al., 2012).
Figure 9. The creep and recovery curves of MRG-70 under a 200 Pa constant stress for MRG-70 at different temperatures.
In order to clearly see the recovery behavior of MRG at various temperatures (10, 50, and 70°C), Figure 9 is drawn separately to obtain Figures 10A–C. From Figures 10A–C, when the temperature is 10°C, the recovery behavior of MRG is the best. When the temperature increases to 70°C, it can be seen that the recovery part is basically the same, so it can be concluded that the recovery is very small. This is because when there is no magnetic field, the viscosity of the MRG will decrease with the increase of temperature (Fernandez et al., 2018), so its deformation will become larger.
Figure 10. The creep and recovery curves of MRG-70 under a 200 Pa constant stress for MRG-70 under different temperatures (A) T = 10°C; (B) T = 50°C; (C) T = 70°C.
Compared with Figures 10, 11 was tested under a magnetic flux density of 47 mT to study the creep recovery behavior of MRG at different temperatures (10, 50, and 70°C), and the shear stress was set to 200 Pa. It can be clearly seen from Figure 11 that the creep strain will decrease with the increase of temperature under the same creep time, which indicates that the strain in MRG is not only related to the matrix but also to the strength of the magnetic field. Under the influence of the matrix, it becomes harder with increasing temperature. This is quite different from the results obtained from MR fluid (Li et al., 2002), the conclusion may be caused by a different matrix from the material of the research object.
Figure 11. The creep and recovery curves of MRG-70 under a 200 Pa constant stress for MRG-70 under different temperatures T = 10°C; T = 50°C; T = 70°C.
In this paper, a commercial lubricating grease was used as a matrix to prepare MRGs with carbonyl iron powder mass fractions of 50 and 70%, respectively. Constant stress, magnetic field strength, CI particle content and temperature were studied by Anton Paar MCR302 rheometer. The main conclusions of the influence on the creep and recovery characteristics of MRG are as follows:
(a) Different constant stresses show different creep and recovery characteristics. As the constant stress level increases, the response strain will increase accordingly. In addition, the creep strain of MRG decreases with the increase of the magnetic field strength. The creep strain of MRG tested under no magnetic field is greater than that of MRG tested under magnetic field.
(b) The higher the content of CI particles in MRG at zero field, the higher its viscosity value, which will make the creep strain value smaller. In addition, when the applied magnetic flux density is 47 mT, it is found that the research results have a similar trend with the results without the applied magnetic field. However, the strain amount of the MRG material is smaller after the applied magnetic field.
(c) In the absence of a magnetic field, the creep strain of the MRG increases with the increase in temperature during the same time test. on the contrary, under the action of a magnetic field, the creep strain will decrease with the increase of temperature. Therefore, it can be inferred that the magnetic interaction between the iron particles and the coupling between the matrix and the iron particle chain are the reasons for the influence of temperature on the magnetic field creep behavior of the MRG.
The raw data supporting the conclusions of this article will be made available by the authors, without undue reservation.
The studies involving human participants were reviewed and approved by Nanjing University of Science and Technology. Written informed consent to participate in this study was provided by the participants’ legal guardian/next of kin. The animal study was reviewed and approved by Smart materials. Written informed consent was obtained from the owners for the participation of their animals in this study. Written informed consent was obtained from the individual(s), and minor(s)’ legal guardian/next of kin, for the publication of any potentially identifiable images or data included in this article.
Both authors listed have made a substantial, direct and intellectual contribution to the work, and approved it for publication.
The authors declare that the research was conducted in the absence of any commercial or financial relationships that could be construed as a potential conflict of interest.
Chen, L. G., Shuai, C. G., Chen, L. G., and Yang, S. L. (2015). Study on creep property of polyurethane composites. Mater. Res. Innov. 19, 199–201.
Cheng, J., Liu, K., Zhang, Z., Wei, Z., Ma, Y., and Lu, S. (2021). Effect of compound surfactants modified carbonyl iron on magnetorheological fluids. J. Supercond. Nov. Magn. 34, 1177–1183.
Fancey, K. S. (2005). A mechanical model for creep, recovery and stress relaxation in polymeric materials. J. Mater. Sci. 40, 4827–4831. doi: 10.1007/s10853-005-2020-x
Fernandez, M. A., Jen-Yuan, C., and Chih-Yung, H. (2018). Development of a passive magnetorheological fluid clutch with field-blocking mechanism. IEEE Trans. Magn. 54, 1–5. doi: 10.1109/tmag.2018.2834389
Findley, W. N., Lai, J. S., and Onaran, K. (1977). Creep and relaxation of nonlinear viscoelastic materials with an introduction to linear viscoelasticity. J. Appl. Mech. 44, 505–509.
Fu, J., Bai, J., Lai, J., Li, P., Yu, M. K., and Lam, H.-K. (2019). Adaptive fuzzy control of a magnetorheological elastomer vibration isolation system with time-varying sinusoidal excitations. J. Sound Vib. 456, 386–406. doi: 10.1016/j.jsv.2019.05.046
Hu, Z. D., Yan, H., Guo, X. C., Wang, X. M., and Wen, H. (2015). Rheological properties and stability of lithium-based magnetorheological grease with damping effect. Acta Petrolei Sin. 31, 166–171.
Iurzhenko, M., Mamunya, Y., Boiteux, G., and Matkovska, L. (2014). Creep/stress relaxation of novel hybrid organic-inorganic polymer systems synthesized by joint polymerization of organic and inorganic oligomers. Macromol. Symp. 341, 51–56. doi: 10.1002/masy.201300163
Kavlicoglu, B. M., Gordaninejad, F., and Wang, X. (2013). Study of a magnetorheological grease clutch. Smart Mater. Struct. 22:5030.
Kim, J. E., Ko, J. D., Liu, Y. D., Kim, I. G., and Choi, H. J. (2012). Effect of medium oil on magnetorheology of soft carbonyl iron particles. IEEE Trans. Magn. 48, 3442–3445. doi: 10.1109/tmag.2012.2195160
Li, W. H., Du, H., Chen, G., and Yeo, S. H. (2002). Experimental investigation of creep and recovery behaviors of magnetorheological fluids. Mater. Sci. Eng. A 333, 368–376. doi: 10.1016/s0921-5093(01)01865-2
Mao, R., Wang, H., Zhang, G., Yea, X., and Wang, J. (2020). Magneto-induced rheological properties of magnetorheological gel under quasi-static shear with large deformation. RSC Adv. 10, 31691–31704. doi: 10.1039/d0ra05843b
Mohamad, N., Mazlan, S. A., and Sabino, U. (2016a). “Effect of carbonyl iron particles composition on the physical characteristics of MR grease,” in Proceeding of the International Conference & Exhibition on Sustainable Energy & Advanced Materials, (College Park: AIP Publishing LLC).
Mohamad, N., Mazlan, S. A., Ubaidillah, S., Choi, S.-B., and Nordin, M. F. M. (2016b). The field-dependent rheological properties of magnetorheological grease based on carbonyl-iron-particles. Smart Mater. Struct. 25:10.
Mohamad, N., Ubaidillah, Mazlan, S. A., Imaduddin, F., Choi, S. B., and Yazid, I. I. M. (2018). A comparative work on the magnetic field-dependent properties of plate-like and spherical iron particle-based magnetorheological grease. PLoS One 13:e0191795. doi: 10.1371/journal.pone.0191795
Ou, Y. Q., Li, Z. C., Zheng, J. J., and Wang, J. (2017). Controllability characteristics of magnetorheological damper with multi-stage parallel coil under impact load. J. Zhejiang Univ. 51, 961–968.
Ouyang, Q., Hu, H., Qian, C., Zhang, G., Wang, J., Zheng, J., et al. (2019). Investigation of the influence of magnetic field distribution on the magnetorheological absorber with individually controllable coils. IEEE Trans. Magn. 55, 1–13. doi: 10.1109/tmag.2019.2907515
Park, B. O., Park, B. J., Hato, M. J., and Choi, H. J. (2011). Soft magnetic carbonyl iron microsphere dispersed in grease and its rheological characteristics under magnetic field. Colloid Polym. Sci. 289, 381–386. doi: 10.1007/s00396-010-2363-y
Qi, S., Yu, M., Fu, J., Li, P. D., and Zhu, M. (2016). Creep and recovery behaviors of magnetorheological elastomer based on polyurethane/epoxy resin IPNs matrix. Smart Mater. Struct. 25:015020. doi: 10.1088/0964-1726/25/1/015020
Rabbani, Y., Ashtiani, M., and Hashemabadi, S. H. (2015). An experimental study on the effects of temperature and magnetic field strength on the magnetorheological fluid stability and MR effect. Soft Matter 11, 4453–4460. doi: 10.1039/c5sm00625b
Rankin, P. J., Horvath, A. T., and Klingenberg, D. J. (1999). Magnetorheology in viscoplastic media. Rheol. Acta 38, 471–477. doi: 10.1007/s003970050198
Wang, D., Yao, L., Shao, W., Zi, B., and Chen, W. (2019). Simulation and experimental study on temperature characteristics of magnetorheological fluid brake for vehicles. J. Mech. Eng. 55:100. doi: 10.3901/jme.2019.06.100
Wang, H. X., Li, Y. C., Zhang, G., and Wang, J. (2019). Effect of temperature on rheological properties of lithium-based magnetorheological grease. Smart Mater. Struct. 28:035002. doi: 10.1088/1361-665x/aaf32b
Weihua, L., Zhou, Y., Tian, T., and Alici, G. (2010). Creep and recovery behaviors of magnetorheological elastomers. Front. Mech. Eng. China 5:341–346. doi: 10.1007/s11465-010-0096-8
Xia, H., Song, M., Zhang, Z., and Richardson, M. (2007). Microphase separation, stress relaxation, and creep behavior of polyurethane nanocomposites. J. Appl. Polym. Sci. 103, 2992–3002. doi: 10.1002/app.25462
Xu, Y., Gong, X., Xuan, S., Li, X., Qina, L., and Jiang, W. (2012). Creep and recovery behaviors of magnetorheological plastomer and its magnetic-dependent properties. Soft Matter 8, 8483–8492. doi: 10.1039/c2sm25998b
Yang, C. Y., Fu, J., Yu, M., Zheng, X., and Ju, B. X. (2015). A new magnetorheological elastomer isolator in shear-compression mixed mode. J. Intell. Mater. Syst. Struct. 26, 1290–1300. doi: 10.1177/1045389x14541492
Yao, Z., Wu, D., Chen, C., and Zhang, M. (2013). Creep behavior of polyurethane nanocomposites with carbon nanotubes. Compos. Part A Appl. Sci. Manuf. 50, 65–72. doi: 10.1016/j.compositesa.2013.03.015
Ye, X., Mao, R., and Wang, J. (2021). Analysis of magnetorheological grease normal force characteristics in static and dynamic shear modes. Mater. Res. Express 8:015701. doi: 10.1088/2053-1591/abbf81
Keywords: magnetorheological grease, rotating shear, creep and recovery behavior, magnetic field strength, creep
Citation: Ye X and Wang J (2021) Creep and Recovery Behaviors of Lithium-Based Magnetorheological Grease. Front. Mater. 8:668125. doi: 10.3389/fmats.2021.668125
Received: 15 February 2021; Accepted: 19 April 2021;
Published: 28 May 2021.
Edited by:
Xinglong Gong, University of Science and Technology of China, ChinaReviewed by:
Yangguang Xu, China Academy of Engineering Physics, ChinaCopyright © 2021 Ye and Wang. This is an open-access article distributed under the terms of the Creative Commons Attribution License (CC BY). The use, distribution or reproduction in other forums is permitted, provided the original author(s) and the copyright owner(s) are credited and that the original publication in this journal is cited, in accordance with accepted academic practice. No use, distribution or reproduction is permitted which does not comply with these terms.
*Correspondence: Jiong Wang, d2ppb25nekBuanVzdC5lZHUuY24=
Disclaimer: All claims expressed in this article are solely those of the authors and do not necessarily represent those of their affiliated organizations, or those of the publisher, the editors and the reviewers. Any product that may be evaluated in this article or claim that may be made by its manufacturer is not guaranteed or endorsed by the publisher.
Research integrity at Frontiers
Learn more about the work of our research integrity team to safeguard the quality of each article we publish.