- 1Key Laboratory of Advanced Ceramics and Machining Technology of Ministry of Education, School of Materials Science and Engineering, Tianjin University, Tianjin, China
- 2School of Criminal Investigation, China People’s Police University, Langfang, China
Under high temperature, aqueous film forming foam extinguishing agent has poor flame retardancy and low fire efficiency. In order to solve this problem, talc was introduced into foam to form composite foam. The fire resistance and fire extinguishing properties of the composite foam were studied. The results showed that talc composite foam had good flame retardant resistance. when the concentration of talc reached 40 g/100 ml, the 50% liquid separation time of the composite foam was 21.1 min. The fuel burning in the anti burning tank did not ignite the gasoline in the oil pan, and burned out at 51.5 min. It was related to the structure of composite foam and the properties of talc. Due to the introduction of talc, the viscosity of the composite foam increased. The network structure of composite foam was important to the improved stability of foam. Talc powder formed a dense layer covering the oil surface, which effectively isolated the oil from the air.
Introduction
Talc is used mainly in medicine, cosmetics, ceramics, paper making, coatings, wires and cables, and various chemical industries (Liu et al., 2020; Nair and Sairam, 2021). The main component of talc is hydrous magnesium silicate, the molecular formula is Mg3 [Si4O10] (OH)2, and the density is 2.7 ∼ 2.80 g/cm3. Talc belongs to monoclinic system, and the crystal is in the shape of pseudo hexagonal or rhombic flake. Talc is a layered silicate mineral with water content of 2:1. Each crystal layer is composed of two layers of Si-O tetrahedron sandwiched with a layer of Mg-O (O-H) octahedron. In its lattice structure, the Si-O tetrahedron is connected into layers to form a continuous hexagonal network layer with active oxygen facing one side, and then the active oxygen of each hexagonal network layer is facing each other through a layer of "magnesium hydroxide" layer. Aqueous film forming foam is considered to be the best oil fire extinguishing agent. But the foam formed by aqueous film forming foam is not stable. The sealing time to oil surface and the reburning time are relatively short. The performance in isolating hot liquid and reburning resistance is poor (Wang, 2014; Zhao, 2014). The researches show that foam with particles has significantly improved stability (Alargova et al., 2004; Horozov, 2008; Mohamedi et al., 2012; Shi et al., 2019). Talc was considered to be added into aqueous film forming foam. The flame retardancy and mechanism of talc composite foams should be studied.
Experiment
Material Preparation
Talc particles had an average diameter of 15 μm. It was produced by Shanghai Chuangyu Chemical Co., Ltd. The aqueous film forming foam was produced by Hebei Langfang Rongshun Co., Ltd.
Testing Methodology
Fire resistance and fire extinguishing performance are important properties of fire extinguishing agent. In order to evaluate the performance of composite foam with talc, flame retardant experiments and fire extinguishing test were carried out. The viscosity and drainage time of the composite foam were measured, so as to study the effect of talc on the flame retardancy and fire extinguishing of the foam.
Measurement of Flame Retardancy
The talc of 0, 10, 20, 30, 40, 50 and 60 g were added into the 100 ml aqueous film forming foam respectively and the composite foam was prepared by Waring- Blender method.
3,000 ml water was poured into the bottom of an oil pan. After the liquid level was stationary, 300 ml gasoline and 2000 ml composite foam were poured onto the oil surface. A steel anti burning pot was put in the middle of the oil pan and filled up with the gasoline (about 100 ml). The liquid level and the oil pan's liquid level were kept on the same level surface. The composite foam should be kept in the oil pan and not enter the anti burning pot. The timing started from igniting the oil in the anti burning tank and stopped when the oil pan was fully on fire. This period was recorded as the anti burning time which was expressed by tc. When talc was added into the foam to form composite foam, there might be a self extinguishment of the gasoline in the anti burning tank, while the oil pan surface had never been burned. In this case, the time of self extinguishment of the gasoline in the anti burning tank was recorded as tc.
Measurement of Fire Extinguishing Performance
In order to study the fire extinguishing performance of the composite foam, the experiment was carried out in the indoor fire experimental platform of the building fire extinguishing facility laboratory, the experimental platform size was 3.0 m × 2.8 m × 2.8 m. In the middle of the experimental platform, place 0.4 m × 0.4 m empty oil pan, add 2000 ml water into the oil pan, add 300 ml gasoline, fill 3,000 ml composite foam (c = 30 g/100 ml) to the fire extinguishing device, spray out composite foam by means of nitrogen pressure, ignite gasoline with an igniter, and wait 45 s for pre-burning. Start the foam spraying device at 2 m far away, spray the composite foam until the flame goes out, and record the fire extinguishing time.
Measurement of Foam Viscosity
Considering that the performance of composite foam was related to the viscosity of composite foam, the viscosity was measured by using a Stormer viscosimeter. The experimental methods were as follows: composite foam with talc was poured into the measuring cup. When the foam height was about 10 mm from the measuring cup, it stopped. A measuring cup with talc was placed on the container seat and the lifting handle was pressed down. The stirring blade was immersed in the foam and the marking line of the impeller shaft was aligned with the liquid level. At this point, the impeller immediately rotated, the viscosity value on the display was recorded after 10 s. After the measurement finished, the lifting handle was lifted up to the height.
Determination of Liquid Separation Time
At room temperature, 100 ml of 6% AFFF solution with distilled water was prepared. talc and the mixed solution were blended and poured into the Waring- Blender stirring cup. The composite foam was obtained by stirring at 5 min at a speed of 3,000 r/min. The generated foam was poured into the 1,000 ml measuring cylinder placed in a constant temperature water bath pot at 25°C. Time started from the pouring. When the bottom of the equivalent cylinder was 15, 25 and 50 ml, time stopped. The time was expressed respectively by t15, t25 and t50%.
Results and Discussion
Flame Retardancy of Talc Composite Foams
Fire Resistance
Fire resistance was an important performance of composite foam (Shi et al., 2020). The talc were added into the 100 ml aqueous film forming foam and blended. The mixture was poured into Waring-Blender cup. In the Blender mixing cup, composite foam was obtained at a speed of 3,000 r/min for 5 min. The fire resistance test of the composite foam containing talc was carried out.
In the experiment, the fire resistance test of composite foam containing talcum powder was carried out. The burning of gasoline in the burning tank caused the foam temperature rising around the anti burning tank. Under the action of thermal shock, the most recent foam near the burning tank was rapidly ruptured and could not completely cover the oil surface. The gap in the foam and the fire of the oil pan expanded. Suddenly, the flame ignited the oil of the oil pan edge. Finally, with the complete rupture of the foam, the oil pan was fully ignited, as shown in Figure 1. However, because the viscosity of the composite foam containing talcum powder was low, the foam would quickly replenish and completely cover the gasoline in the oil pan and not easy to ignite.
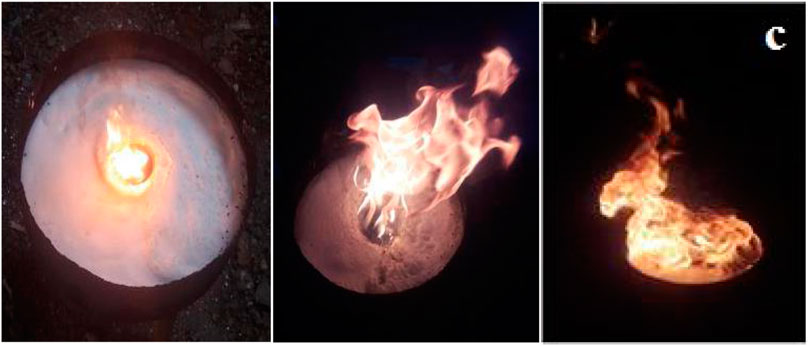
FIGURE 1. Burn resistant experiment (A) gasoline ignited in fire resisting pot; (B) gasoline ignited in oil pan; (C) oil pan full of fire.
Table 1 showed the experimental results of firing resistance of composite foam with different concentration of talc. From Table 1, it can be seen that the aqueous film forming foam had relatively low burning resistance, and loses its resistance to combustion at about 15.9 min, resulting in the full ignition of the oil pan. The talc enhanced significantly the fire resistance of foam. With the increase of concentration of talc, the fire resistance performance of composite foam increased gradually. When the concentration of talc was 10 g/100 ml, the burning resistance time was about 20.3 min, which was extended by about 4.4 min. When the concentration of talc was 30 g/100 ml, the ignition time was increased by about 9.6 min, reaching 25.5 min. And when the concentration of talc reaches 40 g/100 ml, the oil burning in the anti burning tank did not ignite the gasoline in the oil pan and burned out at 51.5 min.

TABLE 1. Fire resistance performance test results of composite foam with different concentration talc particles.
During the experiment, it was found that the complementarity of talc composite foams was very good because the viscosity of the composite foam containing talcum powder was low. When the foam around the tank was damaged, it could be replenished in time. Thus the anti burning property of the foam was enhanced. During the experiment, it was found that the composite foam with talc formed a strong compact layer on the oil surface, which was conducive to the complete coverage of the oil surface.
Fire Extinguishing Performance
After adding talc, the stability and fire resistance of composite foam were significantly improved. The fire extinguishing experiment was carried out with composite foam containing talc, as shown in Figure 2.
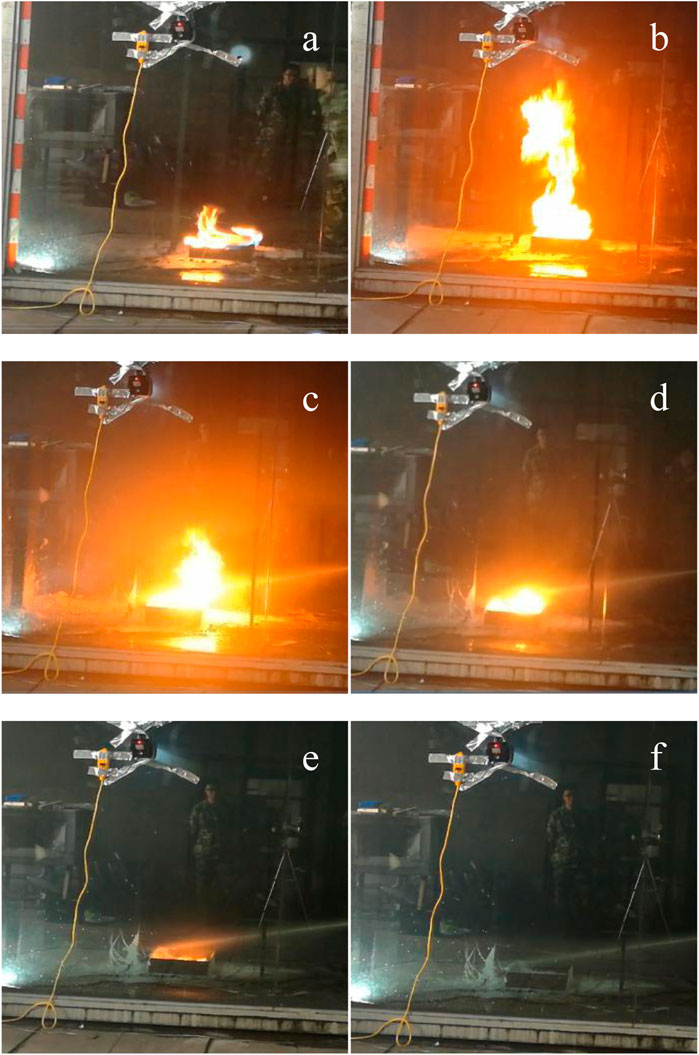
FIGURE 2. Fire-fighting test with composite foam (A) ignite; (B) t = 0 s; (C) t = 20 s; (D) t = 24 s; (E) t = 26 s; (F) t = 28 s.
The whole process of flame combustion and extinction can be seen from Figure 2. Figure 2A was the photo when gasoline ignites. After 45 s of pre-combustion, the oil in the oil pan was fully burned, as shown in Figure 2B. At this time, the foam was sprayed and time was recorded as 0 s. The fire was basically controlled after injection for 20 s, as shown in Figure 2C. The oil fire was completely extinguished after 28 s. It can be seen that the addition of talc was beneficial to the improvement of fire extinguishing performance of composite foam. The foam formed with talc particles form a strong surface layer covering the surface of the fuel and effectively prevents the fuel vapor from air.
Flame-Retardant Mechanism of Talc Composite Foam
Composite Foam Viscosity
Figure 3 showed the viscosity of talc composite foam. The viscosity of the foam without adding talc was 0.076 Pa s. The viscosity of the composite foam with talc of 20 g/100 ml was 0.088 Pa s, while the viscosity of the composite foam with talc of 60 g/100 ml was 0.189 Pa s.
The effect of viscosity on the stability of composite foam containing talc was mainly because that the increasing viscosity was helpful to slow the drainage and thinning of liquid membrane (Koehler et al., 2000; Carn et al., 2009; Long et al., 2016). Excessive viscous resistance hindered the free flow of liquid (Preval et al., 2014). Meanwhile, the channel of liquid precipitation was complex because the size of talc was very small. The prolongation of precipitation path made the time of liquid evolution of composite foam longer. Figure 4 showed the effect of the viscosity of composite foam on the time of liquid phase separation of talc composite foam. It can be seen from Figure 4 that the greater the viscosity of the system was, the longer the time of the liquid phase of the composite foam was, and the higher the stability of foam. The viscosity of the foam without adding talc was 0.076 Pa s. At this time, the 15% liquid separating time and the 25% liquid separating time of the foam were 6.4 and 7.9 min respectively. The viscosity of the foam increased after adding talc. When the viscosity was 0.088 Pa s, the 15% liquid separating time and 25% liquid separating time of the foam increase rapidly, which is 8.4 and 11.8 min respectively. The viscosity of the foam increased with the increasing concentration of talc, and the time of liquid separation was lengthened.
When the viscosity of the composite foam reached 0.189 Pa s, the 15% liquid separation time and 25% liquid separation time of the foam reach 13.2 and 18.2 min. The time of the 50% liquid separation time of the composite foam containing talc was greater than that free of talc. The time of the liquid decomposition of the foam without adding talc was 9.4 min. When the addition of talc increased with the viscosity of the composite foam, the dissolution time increased rapidly. When the viscosity was 0.088 Pa s, the 50% liquid precipitation time of the foam increased to 15.4 min. And when the viscosity of the composite foam reached 0.189 Pa s, the 50% liquid separation time of foam increased to 31.3 min.
The effect of viscosity on the stability of the composite foam containing talc was mainly due to the increase of viscosity, which can retard the drainage and thinning of the liquid membrane. The excessive viscous resistance hindered the free flow of the liquid. Meanwhile, the talc size was smaller, the amount of talc powder was more, the liquid outlet channel was more complex and the precipitation path were long, which would lead to the slowing down of the liquid separation process.
Liquid Separation Process of Talc Composite Foam
The influence of talc concentration on the whole liquid separation process of the composite foam was studied. The results were shown in Figure 5.
As can be seen from Figure 5, for the foam solution without talcum powder, the rate of liquid dissolution was very fast. 15% of the liquid precipitated in 6.4 min and 25% of the liquid precipitated in 7.9 min. 50% of the liquid gave off in 9.4 min and finally almost liquid completely precipitated. The foam became very fragile and easily damaged. When the talcum powder was added, the time of liquid separation was prolonged significantly. With the increasing of talc concentration, the rate of liquid dissolution was slower and slower. When talcum powder concentration was 30 g/100 ml, liquid precipitated 15 and 25% in 8.9 and 13 min respectively. But 50% of the liquid precipitated in 17.3 min, which was longer than that of the foam without talcum powder. When the talcum powder concentration was 40 g/100 ml, the time of t15, t25 and t50% was 9.5, 14.3 and 21.1 min respectively. The liquid precipitation rate had become very slow, the composite foam was very stable.
As can be seen from Figure 5, the addition of flaky talcum powder had an obvious effect on the rate of liquid separation in the later stage of foaming. Free water released at the beginning of the foaming stage and the rate of liquid dissolution was faster at that time. When the gravitational precipitation was completed, the Plateau discharge took the lead. The time of the dissolution increased with the increasing of talc concentration. The results showed that the 50% liquid separation time of foam without talc was less than 10.0 min. When 30.00 g/100 ml talc powder was added, the 50% liquid separation time was 17.3 min. When the concentration of talc was 40.00 g/100 ml, the 50% liquid separation time was 21.1 min. When the talc content was 60.00 g/100 ml, the 50% liquid separation time reached 31.3 min.
When the viscosity of the foam system was small, the effect on the liquid precipitation was small, so the process of liquid precipitation was faster. When the concentration of talc was high, the viscosity of the foam system was high, the foam structure was complex, and the liquid precipitation channel was prolonged (Stevenson, 2006; Subramaniam et al., 2006). The precipitation time of the first 50% water was prolonged under the action of gravity, but it was not obvious, while the capillary water precipitates under the action of Laplasse. Therefore, if we need to control the time of the liquid phase of the composite foam, we should adjust it from the factors that affect the liquid phase in the later stage.
Talc Composite Foam Structure
The effect of foam structure on foam stability was also very obvious (Stocco et al., 2011; Fameau and Salonen, 2014). The complex network structure included the network structure of the entire foam system and the network structure of interwoven in the liquid film (Aveyard et al., 1994; Al-Qararah et al., 2012; Pang et al., 2018).
In the process of talc composite foam, the bubbles always were spherical structure. The complete surface of the spherical bubbles and the aggregation of a large number of spherical bubbles caused the rate of liquid dissolution to slow down. The talc particles gathered at the intersection of the liquid membrane and the liquid membrane, and effectively inhibited the coarsening of the bubbles. Even though most of the liquid had been precipitated, the bubbles still maintained a regular spherical structure. It was surrounded by a shell and was not easy to deform.
The micro-structure of composite foam containing talc powder with different concentrations was observed by an optical microscope. Figure 6 was a distribution optical microscopic picture of composite foam with different concentrations of talcum powder. The micro-structure of composite foam when talcum powder concentration was 5 g/100 ml was similar to the micro-structure of foam without talcum powder. The liquid foam still occupied the main body of the whole system. The liquid precipitated rapidly under the action of gravity. The speed of coarsening and coalescence of bubbles was very fast and the deformation of bubbles was serious. From Figure 6, talcum powder can be seen to gather in the liquid film between the bubbles when the concentration of talcum powder was 20.00 g/100 ml. However, due to less talcum powder in the liquid film, the liquid film was easily affected when the bubbles deform, resulting in more serious deformation of the bubbles.
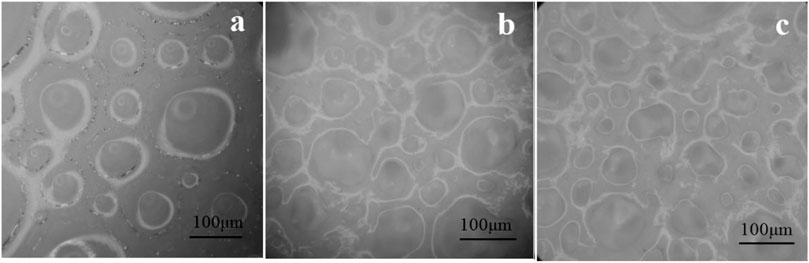
FIGURE 6. Optical microscopic images of talcum powder in foam (A) 5.00 g/100 ml; (B) 20.00 g/100 ml; (C) 40.00 g/100 ml).
When the concentration of talc was 40.00 g/100 ml, a large amount of talc powder accumulated in the liquid film, which made the liquid film very thick. The bubble size decreased and the number of bubbles increased. The aggregation of talc powder in the liquid film between bubbles formed a hard shell to protect bubbles, as shown in Figure 7. The hindrance between these hard shells obstructed the coalescence of bubbles (Barik and Roy, 2009; Politova et al., 2018). During the whole observation process, the shape of these bubbles remained unchanged and they were not easy to break. The hard shell inhibited the gas diffusion between bubbles and improved the stability of the composite foams.
Conclusion
Talc composite foams had good fire resistance. When the concentration of talc was 40.00 g/100 ml, the oil in the burning tank was extinguished without burning the oil in the oil pan. It was closely related to the structure of the composite foams. The accumulation of talc powder in the liquid film between bubbles was very obvious. The liquid film was very thick because of a large amount of talc powder in the liquid film. The bubble size decreased and the number of bubbles increased. The accumulation of talc powder in the liquid film between bubbles formed a hard shell to protect bubbles, and the separation layer formed on the fuel surface was more compact. The talc composite foams could prevent the fuel in the fire-resistant tank from igniting the oil pan when the concentration of talc powder reached 40.00 g/100 ml.
Data Availability Statement
The original contributions presented in the study are included in the article/Supplementary Material, further inquiries can be directed to the corresponding author.
Author Contributions
All authors listed have made a substantial, direct, and intellectual contribution to the work and approved it for publication.
Funding
National Natural Science Foundation of China (No. 21704111); Cultivation Project of National Natural Science Foundation of China (No. ZKJJPY201714).
Conflict of Interest
The authors declare that the research was conducted in the absence of any commercial or financial relationships that could be construed as a potential conflict of interest.
References
Al-Qararah, A. M., Hjelt, T., Kinnunen, K., Beletski, N., and Ketoja, J. (2012). Exceptional pore size distribution in foam-formed fiber networks. Nordic Pulp Paper Res. J. 27, 226–230. doi:10.3183/npprj-2012-27-02-p226-230
Alargova, R. G., Warhadpande, D. S., Paunov, V. N., and Velev, O. D. (2004). Foam superstabilization by polymer microrods. Langmuir 20 (24), 10371–10374. doi:10.1021/la048647a
Aveyard, R., Binks, B. P., Fletcher, P. D. I., Peck, T. G., and Rutherford, C. E. (1994). Aspects of aqueous foam stability in the presence of hydrocarbon oils and solid particles, Adv. Colloid Interf. Sci. 48,93–120. doi:10.1016/0001-8686(94)80005-7
Barik, T. K., and Roy, A. (2009). Statistical distribution of bubble size in wet foam. Chem. Eng. Sci. 64, 2039–2043. doi:10.1016/j.ces.2009.01.039
Carn, F., Colin, A., Pitois, O., Vignes-Adler, M., and Backov, R. (2009). Foam drainage in the presence of nanoparticle—surfactant mixtures. Langmuir 25, 7847–7856. doi:10.1021/la900414q
Fameau, A. L., and Salonen, A. (2014). Effect of particles and aggregated structures on the foam stability and aging. C.R. Physique 15, 748–760. doi:10.1016/j.crhy.2014.09.009
Horozov, T. S. (2008). Foams and foam films stabilised by solid particles. Curr. Opin. Colloid Interf. Sci 13, 134–140. doi:10.1016/j.cocis.2007.11.009
Koehler, S. A., Hilgenfeldt, S., and Stone, H. A. (2000). A generalized view of foam drainage: experiment and theory. Langmuir 16, 6327–6341. doi:10.1021/la9913147
Liu, C., Wu, W., Shi, Y., Yang, F., Liu, M., Chen, Z., et al. (2020). Creating MXene/reduced graphene oxide hybrid towards highly fire safe thermoplastic polyurethane nanocomposites. Composites B 203, 108486. doi:10.1016/j.compositesb.2020.108486
Long, X., Sha, R., Meng, Q., and Zhang, G. (2016). Mechanism study on the severe foaming of rhamnolipid in fermentation. J. Surfact Deterg 19, 833–840. doi:10.1007/s11743-016-1829-4
Mohamedi, G., Azmin, M., Pastoriza-Santos, I., Huang, V., Pérez-Juste, J., Liz-Marzán, L. M., et al. (2012). Effects of gold nanoparticles on the stability of microbubbles. Langmuir 28, 13808–13815. doi:10.1021/la302674g
Nair, N. A., and Sairam, V. (2021). Research initiatives on the influence of calcium silicate in cement-based construction material-A review. J. Clean. Prod. 283, 124665. doi:10.1016/j.jclepro.2020.124665
Pang, X. Y., Singh, J., and Jimenez, W. C. (2018). Characterizing gas bubble size distribution of laboratory foamed cement using X-ray micro-CT. Constr Build Mater. 167, 243–252. doi:10.1016/j.conbuildmat.2018.02.030
Politova, N., Tcholakova, S., Valkova, Z., Golemanov, K., and Denkov, N. D. (2018). Self-regulation of foam volume and bubble size during foaming via shear Mixing. Colloids Surf. A: Physicochem. Eng. Asp. 539, 18–28. doi:10.1016/j.colsurfa.2017.12.006
Preval, E. S. D., Fabrice, D., and Gilles, M. (2014). Influence of surface properties and bulk viscosity on bubble size prediction during foaming operation. Colloids Surf. A: Physicochem. Eng. Asp. 442, 88–97.
Shi, Y. Q., Liu, C., Duan, Z. P., Yu, B., Liu, M., and Song, P. (2020). Interface engineering of MXene towards super-tough and strong polymer nanocomposites with high ductility and excellent fire safety. Chem. Eng. J. 399, 125829. doi:10.1016/j.cej.2020.125829
Shi, Y. Q., Liu, C., Liu, L., Fu, L., Yu, B., Lv, Y., et al. (2019). Strengthening, toughing and thermally stable ultra-thin MXene nanosheets/polypropylene nanocomposites via nanoconfinement. Chem. Eng. J. 378, 122267. doi:10.1016/j.cej.2019.122267
Stevenson, P. (2006). Dimensional analysis of foam drainage. Chem. Eng. Sci. 61, 4503–4510. doi:10.1016/j.ces.2006.02.026
Stocco, A., Garcia-Moreno, F., Manke, I., Banhart, J., and Langevin, D. (2011). Particle-stabilised foams: structure and aging. Soft Matter 7, 631–637. doi:10.1039/c0sm00166j
Subramaniam, A. B., Mejean, C., Abkarian, M., and Stone, H. A. (2006). Microstructure, morphology, and lifetime of armored bubbles exposed to surfactants. Langmuir 22, 5986–5990. doi:10.1021/la060388x
Wang, B. Q. (2014). Study on the cause of oil tank fire and fire prevention countermeasure. Adv. Mater. Res. 864–867, 866–870. doi:10.4028/www.scientific.net/amr.864-867.866
Keywords: flame retardancy, talc, composite foams, stability, mechanism
Citation: Li X, Guo R and Qian X (2021) Study on Flame Retardancy and Mechanism of Talc Composite Foams. Front. Mater. 8:661906. doi: 10.3389/fmats.2021.661906
Received: 31 January 2021; Accepted: 16 February 2021;
Published: 19 March 2021.
Edited by:
Anthony Chun Yin Yuen, University of New South Wales, AustraliaReviewed by:
Hu Long, University of New South Wales, AustraliaRichard Kwok Kit Yuen, City University of Hong Kong, Hong Kong
Copyright © 2021 Li, Guo and Qian. This is an open-access article distributed under the terms of the Creative Commons Attribution License (CC BY). The use, distribution or reproduction in other forums is permitted, provided the original author(s) and the copyright owner(s) are credited and that the original publication in this journal is cited, in accordance with accepted academic practice. No use, distribution or reproduction is permitted which does not comply with these terms.
*Correspondence: Xiujuan Li, leely78@163.com; Ruisong Guo, rsguo@tju.edu.cn; Xiaodong Qian, wjxyqxd@hotmail.com