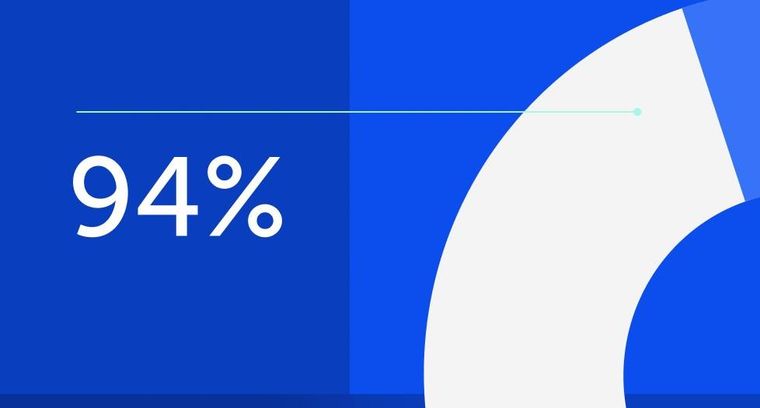
94% of researchers rate our articles as excellent or good
Learn more about the work of our research integrity team to safeguard the quality of each article we publish.
Find out more
REVIEW article
Front. Mater., 15 April 2021
Sec. Smart Materials
Volume 8 - 2021 | https://doi.org/10.3389/fmats.2021.658046
This article is part of the Research TopicFour-dimensional (4D) PrintingView all 11 articles
Soft tactile sensors (STSs) combine the flexibility and the converting ability between mechanical forces and electrical signals. 4D printing was first introduced in 2013, and attracted great interest because of its versatile functionalities in actuators, artificial muscles, STSs, soft energy harvesting, pneumatic nets, electroactive polymers, and soft electronics. Using the 4D printing concept to fabricate STSs is promising, yet it is at its infant stage. At present, researchers have utilized two types of strategies: one is directly using smart materials through 3D printing manufacturing, and the other is programming codes of components and structures to create controllable changes. This review summarizes the recent research on 4D printing toward STSs and discusses the future perspectives of this emerging field.
Additive manufacturing (AM) has attracted lots of attention as a versatile technology to fabricate complicated structures from various materials, such as polymers, metals, ceramics, and other smart materials or stimulus-responsive materials (Oropallo and Piegl, 2015; Balogun et al., 2018). Unlike those traditional subtractive manufacturing methods, AM usually piles up materials to form objects layer by layer according to the data of the computer models. As a result, AM can manufacture items with very sophisticated and complex geometries with no need for post-processing or other assistive tools like molds, dies, or lithographic masks. As an exciting branch of AM, 4D printing was proposed in 2013 by Tibbits (2013), which soon gained considerable interest in public media and research communities (Momeni et al., 2017). In the beginning, 4D printing was primarily known as “3D printing + time” (Spiegel et al., 2019), but the definition evolved in recent years. Shi et al. extended the definition of 4D printing as “the change of shape, property, and functionality from a 3D printed structure response to time or external stimulus” (Yintang et al., 2020), namely, heat (Phuhongsung et al., 2020), water (Melocchi et al., 2019), light (Nishiguchi et al., 2020), and pH (Lin et al., 2018). Owing to manufacturing simplicity and attainable complication of printed material species, 4D printing, as a new branch of AM, has been applied in the fabrication of various functional devices, such as actuators (Akdogan et al., 2005), soft electronics (Zheng et al., 2013; Wang et al., 2015), and soft tactile sensors (STSs) (Xu et al., 2017), as well as in the industry of different disciplines.
Soft tactile sensors (STSs) are a new type of wearable electronic devices, which provide the possibility of mechanical signal interaction between the human/machine and the surrounding environments (Truby and Lewis, 2016). The research of STSs is an emerging field following the rapid development of flexible electronics in the recent two decades (Zarek et al., 2016). Based on diverse working mechanisms, STSs can be divided into five categories: piezoelectric, piezoresistive, capacitive, triboelectric, and magnetic types (Wan et al., 2017). The fabrication of STSs relies on traditional manufacturing methods, namely, film patterning, metallic deposition, molding, and assembly techniques, indicating the complex and high-cost features. Alternatively, multi-material-type AM processing can simultaneously integrate diverse material species to their on-demand positions, allowing for the rapid and cost-effective fabrication of electronic devices. The functionality of as-prepared structures was endowed, which can be recognized as a branch of 4D printing. Thus, it is urgently required to develop novel 4D printing techniques in the further advance of STSs.
In the past few years, there has been a significant trend toward applying 4D printing technology to manufacture various STSs. In other words, a growing number of researchers from different research backgrounds have begun to recognize the importance of this effective technique. By controlling the spatial positions of diverse material species to endow the final products with a new mechano-electric transducing functionality, this concept, no doubt, falls in the definition of 4D printing. More intuitively, as shown in Figure 1, the number of publications and citations in this topic has rapidly boosted. The citations increase more sharply than the publications. Thus, it is deduced that the future of 4D printing research combined with the STSs will be positively promoted, which will generate promising interest in the years to come.
Figure 1. The statistics data of the publication on the topic of 4D-printed soft tactile sensors (STSs) from Web of Science: (A) Publications and (B) citations in each year. Data were collected in the past 8 years (2012–2020).
This article reviews the recent research outcomes concerning 4D printed STSs. At the first stage, it is crucial to understand the AM manufacturing features to adapt to the working mechanisms of STSs. Therefore, this article is organized as follows. Section “Diverse AM Techniques Toward the Fabrication of STSs” gives a detailed and comprehensive description of the fundamental techniques of AM process, including the specially used materials. Section “4D Printing for STSs” describes the five types of 4D-printed STSs. Finally, section “Conclusions and Outlook” provides some important conclusions, which share the viewpoints on the future development of 4D-printed STSs.
Additive manufacturing enables the realization of 3D objects directly from computer-aided design (CAD) models (Frazier, 2014; Herzog et al., 2016; Schmidt et al., 2017). CAD models are transformed into special formats that can be read by computers. The formats are then sliced into control codes to force 3D printers to manufacture objects in a layer-by-layer fashion (Rengier et al., 2010; Oropallo and Piegl, 2015). Up to now, many different types of AM technologies have been developed for generating STSs, namely, selective laser sintering (SLS), stereolithography (SLA), fused filament fabrication (FFF), direct ink writing (DIW), and inkjet printing. For different printing methods and device requirements, materials should be carefully considered for the final products. The subsequent sections will briefly introduce those five types of AM techniques about the printing procedures and related materials.
Selective laser sintering, also known as selective laser melting (SLM), is an AM process that uses an electron beam or a laser as a power source to sinter powder materials. The materials used as the SLM deposition material to form 3D objects include metals, polymers, ceramics, and composites. The building procedure (Figure 2A) of this AM can be separated into three steps: (1) The feed powders with diameters from 10 to 100 μm are rolled over the construction platform. (2) The laser beam is directed into the powders to melt, and the melted powder content is solidified. (3) Then, the powders are rolled over the top of the deposition layer again with the platform declining. The process is repeated until the desired 3D object is completely produced. Unused powder that does not form a part of the as-prepared 3D object has been retained on the construction platform to support the object, thus achieving nearly 100% material utilization. This technique is suitable for metal-based sensor fabrication.
Figure 2. Schematic illustrations of different AM technologies toward the fabrication of STSs. (A) Selective laser sintering. (B) Stereolithography. (C) Fused deposition modeling. (D) Direct ink writing. (E) Inkjet printing.
Stereolithography is the first vat photopolymerization method developed in the early 1980s, which uses specific light to solidify liquid materials in the vat layer by layer to fabricate 3D printing objects. Some other innovative AM techniques like digital projection lithography (DLP) have the same print concept of SLA printing, yielding similar fundamental printing. Figure 2B depicts the printing procedure using the SLA technique. The light source of the laser emits light to cure the liquid polymer. Following the movement of the laser, a thin patterned layer is formed. After the first printing layer, the build platform moves by one-layer height, and a new layer of liquid photopolymer is introduced and cured by the local illumination.
Compared with the SLA technique, the most important improvement of DLP is the printing speed. DLP uses micro-mirror array devices or dynamic liquid-crystal masks to cure an entire pattern of one layer, instead of using a point light source to solidify only one voxel at a time. Thus, the fabrication speed of the SLA is much slower than that of the DLP technique. These two techniques are suitable for polymer-based sensor fabrication.
Fused deposition modeling is a type of material extrusion or extrusion printing. During its working process, a melted thermoplastic-based filament is extruded through a nozzle as a form of continuous filament because of mechanical force. The filament is selectively deposited to fabricate the target entity. As shown in Figure 2C, the typical printer for FFF is comprised of an X-Y-Z axis motion platform, and the extrusion nozzle is filled with diverse material species. The X-Y axis movements are controlled by the computer software, allowing the nozzle to extrude the filament at the designed position in one layer. When one layer is accomplished, either the build platform moves down or the extrusion head moves up, leading to the beginning of the next layer. This process repeats for numerous cycles till the designed entity is completed. The printed materials of this technique are widely selected. They include polycarbonate, polylactic acid (PLA), acrylonitrile butadiene styrene (ABS), and other thermoplastic elastomers and their composites with functional particles or liquids. All of the extruded materials should have thermoplasticity and rheological balance. Since the FFF resolution is lower than SLA, this technique is fit for generating tactile sensors with low-resolution-structural polymer structures.
Direct ink writing is a powerful alternative printing technique to FFF, especially for viscoelastic materials. As shown in Figure 2D, different from FFF, DIW uses air pressure or a piston to extrude the printing material. Some curing procedures, like thermal curing or photopolymerization, are required to solidify the materials after deposition. The primary working mechanism for the DIW process is that, when the inks leave the nozzles, their viscosity will considerably increase, allowing them to take a gel state to keep their shape. DIW technique tolerates a wide variety of materials, namely, electrical, biological, and structural materials (Truby and Lewis, 2016). Thermoset polymers, fugitive inks, colloidal suspension, and hydrogels can be used as different ink materials. DIW can realize multi-material fabrication using microfluidic print heads that can switch flexibility or use multiple printheads with disparate ink compositions. The advantages of DIW are numerous, such as free of dying, no need for lithographic masks, or expensive tooling. Since this technique is of low cost and fits a wide variety of materials, it will be a successful candidate to fabricate arbitrary 3D structural tactile sensors with multi-material design.
Inkjet printing, also known as material jetting, is an AM process similar to SLA in many aspects, yet a movable nozzle is utilized in this technique. Figure 2E illustrates that the nozzle and accessory curing devices like UV light sources are formed on an X-Y-Z three-axis motion platform. The liquid photopolymer is ejected from the nozzles and deposited on the print platform and then it is cured as a solid. It is widely accepted that the SLA technique relies on photopolymerizable resins. Comparatively, inkjet printing has the advantage of fabricating patterns utilizing numerous soft materials in the form of formulated inks using various molecular or polymeric species. This technique is suitable for fabricating multi-material STSs.
Usually, an STS consists of several parts, namely, a flexible substrate, sensing parts, flexible electrodes, and other support materials. The fabrication of STSs involves multi-material selections and their precise positioning, which is quite suitable for the design of 4D printing. By controlling the spatial positions of diverse material species to endow the final products with a new mechano-electric transducing functionality, this concept, no doubt, falls in the definition of 4D printing. Many researchers have utilized AM techniques to fabricate a part of or even the entire tactile sensors to date. This section has listed representative studies of 4D printed tactile sensors categorized into five subsections according to the working mechanisms.
The principle of piezoresistive-type STSs is the resistance changes of the interface material with the external stimuli, through which the external stimuli were converted into electrical signals. Due to the advantages, such as simple structure, low energy consumption, and wide testing range, piezoresistive-type STSs have been widely studied. In the beginning, piezoresistive sensors are fabricated by thin-film processing, molding, or nanomaterial assembly, indicating causal manufacturing features without standard manufacturing. With the continuous development of AM techniques, numerous researchers have recognized AM as a powerful tool to generate STSs.
Kim et al. (2017b) demonstrated a piezoresistive STS formed by a specially designed composite dough. The sophisticated dough is comprised of a carbon composite and a thermoplastic triblock-copolymer elastomer, namely polystyrene-polyisoprene-polystyrene (SIS). The carbon composite was made by mixing multi-walled carbon nanotubes (MWNTS) with graphene oxides (GOs). As shown in Figure 3A, the 3D printable dough materials were printed on 400 μm thick SIS substrates using three-axis-programmable nozzle-based dispensing equipment. After drying at 80°C, both ends of the printed sensor layers were electrically connected with Cu wires and conductive Ag adhesive paste. It had been demonstrated that the printed strain sensor devices exhibited an extremely high gauge factor of 72 with linearity (R2) of 0.94 when the GOs were added to the carbon composite at a ratio of 9.
Figure 3. Piezoresistive-type STSs. (A) Stretchable ultrasensitive strain sensors fabricated by printable composite dough. Copyright 2017, Nanoscale. (B) Highly stretchable hydrogels for UV-curing-based multi-material AM process. Copyright 2018, Journal of Materials Chemistry. (C) Double-network hydrogel for printed strain sensors. Copyright 2017, American Chemical Society. (D) Stretchable STSs printed via a combination of nanocomposite ink optimization and multi-material AM process. Copyright 2017, Advanced Materials. (E) Direct printing of flexible, highly anisotropic constriction-resistive sensors. Copyright 2020, American Chemical Society.
A strain sensor based on microchannel had been designed by Agarwala et al. (2017). The dimensions of the sensor were 2.5 × 2.5 cm. The diameter and the length of each microchannel were 500 μm and 24 cm, respectively. The microchannels were filled with a kind of silver conducting ink. Figure 3B exhibits the complete fabrication process of a printed strain sensor. A photopolymer composite material was used to build the substrate; then, wax was injected into the channels as support materials. After that, the channels were flushed with warm oil to remove the wax, allowing a syringe to fill the microchannel with Novacentrix® JS-B25HV silver conducting ink. Finally, the channels were sealed with a connecting wire. When the sensor suffered a strain in the axial direction of microchannels, the cross-sectional area and the length changed. Thus, the overall resistance of the channels would change accordingly. In the study of Agarwala et al., the change in the resistance of the sensor has been examined when strains were applied in two directions, parallel and orthogonal. It can be noticed that the strain sensor has good repeatability, fast recovery, and negligible hysteresis when the applied strain is below 6%.
Zhang et al. (2018) developed highly stretchable and UV curable hydrogels for the DLP technique. Figure 3B depicts the hydrogel preparation method. An acrylamide-PEGDA (AP)-based hydrogel precursor was made by mixing acrylamide as the monomer and poly(ethylene glycol) diacrylate (PEDGA) as the crosslinker. 2,4,6-trimethylbenzoyl-diphenylphosphine oxide (TPO) nanoparticles were chosen as the photo-initiator in water (water content: 50–80 wt%). This AP hydrogel system has several considerable advantages, such as high stretchability and compatibility with the DLP AM technology. More importantly, the AP hydrogels can form strong interfacial bonding with commercial printable elastomers, leading to printed hydrogel-elastomer hybrid structures. The study shows a highly stretchable electronic board by printing an ionic hydrogel circuit on an elastomeric substrate, yielding AP hydrogels as promising materials for tactile strain sensors.
Liu et al. created a novel, 3D printable hydrogel with admirable recoverability and significant self-healing capability. This hydrogel can print sensitive strain sensors because of its good strain sensitivity (Liu and Li, 2017). κ-carrageenan and acrylamide (AAm) were used to fabricate the hybrid double-network (DN) hydrogels through a photopolymerization process. The self-healing capability comes from the thermo-responsive nature of κ-carrageenan. A sheet sample of DN hydrogel could hold a weight of 250 g (Figure 3C). The printability and flexibility of the DN hydrogel are shown in Figure 3C. The DN hydrogel can be printed into various types (hollow triangular prism or hollow cube) but it regains its original height after being pressed.
Many other researchers contribute to wearable electronics systems by combining piezoresistive stretchable materials and AM techniques. Guo et al. (2017) created a type of sinter-free ink with electrical conductivities and adjustable viscosities to fabricate STSs. The sensors were formed by several layers: a base layer, a sensor layer, two electrode layers, an isolating layer, and a sacrificial supporting layer. The final model of the sensor is shown in Figure 3D. The electrical properties of the sensor were attributed to the cured inks by mixing submicrometer-sized silver particles within a highly stretchable silicone elastomer. It was found that the ink with 68 wt% had the best piezoresistive performance, as indicated in Figure 3D.
Mousavi et al. (2020) used a carbon-nanotube-reinforced polylactic acid (PLA-CNT) to fabricate a piezoresistive STS. In this research, they employed a novel approach by engineering appropriate anisotropic structures as multidirectional tactile sensors. The group selected a sandwich design to characterize the printed anisotropic tactile sensing under large deformation. The PLA-CNT sensor was encapsulated between two thermoplastic polyurethane (TPU) layers (Figure 3E). Direct stretching and bending tests characterized the sensor performance. Wooden strips were used in tensile tests in different directions. Figure 3E shows the tensile sensitivity testing results at 0°, 30°, 45°, 60°, and 90°, in which a 1% tensile strain was applied for three cycles in each direction. The printed sensors have high sensitivity with strain gauge factors (k∼1,342).
Christ et al. (2017) used TPU to develop a 3D-printable, flexible, conductive material, which was demonstrated as an excellent piezoresistive STS. They compounded TPU with multi-walled carbon nanotube (TPU/MWCNT) to print TPU/MWCNT samples. Then, the as-prepared STSs investigated their mechanical, electrical, and piezoresistive properties. The TPU/MWCNT nanocomposites provided various flexibility and sensitivity features, tunable for diverse applications. The cyclic response indicates a strong and consistent behavior over strain loadings and outstanding electric conductivity and piezoresistivity.
Capacitance is the capability of a capacitor to store/release charge. A capacitor consists of two parallel plates and a dielectric layer sandwiched between them. Capacitive-type STSs have shown high sensitivity, compatibility with static force measurement, and low power consumption. However, capacitive devices are susceptible to interference from surrounding objects because these objects might change the fringe field of the capacitor (Cheng et al., 2010), causing it to produce uncertain signals during the measurement. There have been plenty of studies about AM-processed capacitive-type STSs in recent decades.
Nag et al. (2018) used graphite powder and polydimethylsiloxane (PDMS) to develop a kind of capacitive sensor patches. They combined casting and AM technology. The production process, has been divided into several consecutive steps. First, a mold was fabricated through the AM technique using PDMS. Then, graphite powders were cast onto the trenches of the mold. Finally, the patches were cured, yielding the generation of capacitive sensors. Nag’s group investigated the characteristics of the sensor patches. The change in the capacitance values to the forces is nearly linear, with a force sensitivity of 0.2542 pF mN–1 during a range from 3.5 to 17.5 mN. These capacitive properties of sensor patches are due to the high electrical conductivity and corrosion resistance of graphite.
Huang et al. (2016) fabricated a new flexible three-axial force sensor using PDMS. This flexible sensor had four-unit capacitors providing it with high sensitivity to 3-axial forces. The four capacitors were formed by four sensing electrodes and the public electrode upon the flexible printed circuit board (FPCB) layer. The dielectric layer and the bump layer were fabricated by the 3D printing process using PDMS. These two layers were bonded together after the oxygen plasma treatment. The response of the four capacitors in the sensor unit was observed when applied to external forces. Three charts represent three forces: z-axis normal force, x-axis shear force, and y-axis shear force. It is indicated that the capacitances changed linearly concerning the forces.
Hydrogels have been used to fabricate capacitive sensors as well. Lei et al. (2017) came up with an effective strategy to prepare a multifunctional skin-like sensor using thermo-responsive hydrogel in the AM technique. This microstructured double-network hydrogel was synthesized by hydrophobic n-octadecyl acrylate (C18) and sodium dodecyl sulfate (SDS) through a micellar-copolymerization method. The prepared hydrogels could be printed using an FFF-type printing system, as shown in Figure 4. A polyethylene film was sandwiched between two bulk/grid-structured hydrogels connected to two metallic electrodes to fabricate the final sensor. The capacitive STS can respond to manifold pressure (P) and temperature (T). It indicated that the resulting skin-like hydrogel sensor exhibited high sensitivity to those stimuli.
Figure 4. Multifunctional skin-like STSs based on a printed thermo-responsive hydrogel. Copyright 2017, Materials Horizons.
Piezoelectricity is a phenomenon in which voltage is generated by applied mechanical stress, which is commonly used for tactile sensors (Choong et al., 2014). The piezoelectricity comes from the oriented permanent dipole in materials. The deformation of the oriented non-centrosymmetric crystal structure causes the electric dipole moment to separate and generate a piezoelectric voltage on both sides, thus the appearance of the electric dipole moment (Wegener et al., 2005). Due to the high sensitivity and fast response time of piezoelectric sensors, they are widely used in the detection of dynamic pressure, such as sound and sliding vibration (Hammock et al., 2013). Besides, because of the unique energy harvesting characteristics of piezoelectric materials, they are considered as a potential candidate for low-power or self-powered tactile sensors.
Lee et al. (2017) fabricated a 3D customized STS. This piezoelectric-type mechanoelectrical sensor is mainly composed of sandwich-shaped substrates and a core piezoelectric layer. Three parts formed the sandwich-shaped substrate, the upper mold, the lower mold, and their connecting hinge, fabricated by 3D printing using PDMS. The piezoelectric core was a nanofibrous material prepared by electrospinning poly (vinylidene fluoride trifluoroethylene) (PVDF-TrFE). Lee et al. investigated the sensitivity of the sensor. They tested three types of sensors: flat, wrist-form, and fingertip-form sensors. Hence, this customizable sensor can be widely used in wearable electronic devices because of its combined flexibility and sensitivity.
Using the same polymer material (PVDF), Kim et al. (2017a) came up with a unique process to fabricate piezoelectric films through an integrated FFF printing and other corona poling process. The fabrication of as-prepared sensors was as follows: First, the PVDF polymer was heated and extruded from the nozzle, allowing it to harden immediately and deposit with a predominantly α-phase crystalline structure. Then, the PVDF molecules were transformed from α- to β-phase crystalline structure under a high electric field, yielding the rising piezoelectric response.
Fuh et al. (2017) utilized piezoelectric PVDF to fabricate a flexible sensor through an FFF printing process, resulting in the wavy surface of thermoplastic elastomer (TPE) substrate. The integration process of the sensor is shown in Figure 5. Initially, the Cu foil was deposited to the wavy surface of the TPE substrate. Then, PVDF fibers were attached to the surface via near-field electrospinning (NEFS). Finally, the PDMS was used to encapsulate the device entirely. The devices with three different surfaces, namely, planar, square, and sinusoidal surfaces, were fabricated to measure the output voltage and current versus cyclic stretching–releasing deformation. This proposed piezoelectric sensor has great potential in promising applications for wearable electronics.
Figure 5. Self-powered pressure sensor with fully encapsulated 3D printed wavy substrate and highly aligned piezoelectric fibers array. Copyright 2017, Scientific Reports.
The triboelectric effect is a common phenomenon in our daily lives. It occurs when the contacting materials are subjected to friction caused by touching, shearing, or torsions. However, the mechanism behind the triboelectric effect is still under study. It is generally believed that charges will be induced on the surface when two different materials move against each other. The amount of charge generated depends on the difference in triboelectricity polarities between the two contacted materials (Sun et al., 2018).
Haque et al. (2018) used several printable soft materials as functional triboelectric sensor components. They found that PDMS, combined with commercial TangoBlack (TB), showed the highest triboelectric responses. Polyamide (PA) was utilized to fabricate the 3D-printed spring structure. The fabrication process of the triboelectric touch sensor, indicates that the sensor is composed of three printed layers: PDMS layer with electrodes, PA spring structure layer, and TB layer with electrodes. The output power can reach up to 60 μW when the operating frequency is 5 Hz.
Chen et al. (2018) fabricated an ultra-flexible 3D triboelectric nanogenerator (TENG) using printed composite resin parts and ionic hydrogels. These two materials were utilized as the electrification layer and the electrode. The fabrication process of the 3D-TENG is that the liquid photopolymer resins and support materials were directly printed using a single process within an integrated platform through inkjet printing. The voltage output of the 3D-TENG was as high as 70 V.
The magnetoelectric tactile sensor is a newly emerging technology that enables the mechanical pressure to be converted into electrical signals with the help of the magnetic field. This mechanism of a tactile sensor is known as electromagnetic induction, and the relative movement between magnets and conductive wires can generate electricity. These tactile sensors are self-powered without an external power supply due to their magnetoelectric working systems.
Wu et al. (2020) designed a flexible integrated magnetoelectric sensor, and the fabrication of this sensor fulfills the brand-new concept of 4D printing. The 4D-printed tactile sensor exhibited a piezoelectric ability to convert the external pressure into electric energy without any piezoelectric parts, conforming to the 4D printing concept. The magnetoelectric tactile sensor is comprised of two parts, as shown in Figure 6A. One part is a porous structure fabricated by SLS using TPU/NdFeB composite powders, while the other part is a helix structure with two flat plates fabricated by SLM using 316 stainless steel powders. Figure 6B shows the working mechanism: After the magnetic part was magnetized to acquire permanent magnetism, the magnetic field lines would pass through the coil. When the structure was compressed due to external forces, the magnetic flux would change and generate electricity according to the electromagnetic induction principle. Figure 6C is one typical cycle of output voltages by a compression/recovery process.
Figure 6. Magnetoelectric-type STS. Schematic illustrations of (A) AM fabrication process and (B) working mechanism of a magnetoelectric-type STS. (C) The voltage output of the magnetoelectric-type STS during one cycle of compression/recovery process. Copyright 2020, Advanced Science.
In summary, this review summarizes the latest advances in the application of 4D-printed STSs. Compared with the traditional manufacturing methods that have limitations such as tedious fabrication steps, low material utilization, and low manufacturing freedom, AM provides unique advantages to fabricate STSs, namely, the substrate, the sensing element, electrodes, and dielectric layers with complex 3D structures, in a highly efficient and low-cost manner. Furthermore, the structural optimization of the AM technique can make sensors achieve faster response speed, higher sensitivity, and better flexibility. Although AM-processed sensors have already achieved many advantages, some challenging points toned to be focused. First, materials that can be used to fabricate soft sensors are minimal, and novel printable materials with improved properties need further evolution. Second, it will be a great breakthrough if a whole STS can be fabricated in a continuous multi-material AM process, instead of printing parts of a sensor. The advancement of AM technology has the potential to conceive more compelling sensors for future research and applications. We expect that all these efforts will make AM-processed STSs to own a glorious future.
YT and BS collected the references. YT, BD, BS, and YS discussed and wrote the manuscript. All authors contributed to the article and approved the submitted version.
The authors declare that the research was conducted in the absence of any commercial or financial relationships that could be construed as a potential conflict of interest.
Agarwala, S., Goh, G. L., Yap, Y. L., Goh, G. D., Yu, H., Yeong, W. Y., et al. (2017). Development of bendable strain sensor with embedded microchannels using 3D printing. Sensors Actuators A: Phys. 263, 593–599. doi: 10.1016/j.sna.2017.07.025
Akdogan, E. K., Allahverdi, M., and Safari, A. (2005). Piezoelectric composites for sensor and actuator applications. IEEE Trans. Ultrason. Ferroelectr. Freq. Control 52, 746–775. doi: 10.1109/tuffc.2005.1503962
Balogun, V. A., Otanocha, O. B., and Ibhadode, A. O. (2018). The impact of 3D printing technology to the nigerian manufacturing GDP. Modern Mechan. Eng. 08, 140–157. doi: 10.4236/mme.2018.82010
Chen, B., Tang, W., Jiang, T., Zhu, L., Chen, X., He, C., et al. (2018). Three-dimensional ultraflexible triboelectric nanogenerator made by 3D printing. Nano Energy 45, 380–389. doi: 10.1016/j.nanoen.2017.12.049
Cheng, M. Y., Lin, C. L., Lai, Y. T., and Yang, Y. J. (2010). A polymer-based capacitive sensing array for normal and shear force measurement. Sensors (Basel) 10, 10211–10225. doi: 10.3390/s101110211
Choong, C. L., Shim, M. B., Lee, B. S., Jeon, S., Ko, D. S., Kang, T. H., et al. (2014). Highly stretchable resistive pressure sensors using a conductive elastomeric composite on a micropyramid array. Adv. Mater. 26, 3451–3458. doi: 10.1002/adma.201305182
Christ, J. F., Aliheidari, N., Ameli, A., and Pötschke, P. (2017). 3D printed highly elastic strain sensors of multiwalled carbon nanotube/thermoplastic polyurethane nanocomposites. Mater. Des. 131, 394–401. doi: 10.1016/j.matdes.2017.06.011
Frazier, W. E. (2014). Metal additive manufacturing: a review. J. Mater. Eng. Perform. 23, 1917–1928. doi: 10.1007/s11665-014-0958-z
Fuh, Y. K., Wang, B. S., and Tsai, C. Y. (2017). Self-Powered pressure sensor with fully encapsulated 3D printed wavy substrate and highly-aligned piezoelectric fibers array. Sci. Rep. 7:6759. doi: 10.1038/s41598-017-07360-z
Guo, S. Z., Qiu, K., Meng, F., Park, S. H., and McAlpine, M. C. (2017). 3D printed stretchable tactile sensors. Adv. Mater. 29:1701218. doi: 10.1002/adma.201701218
Hammock, M. L., Chortos, A., Tee, B. C., Tok, J. B., and Bao, Z. (2013). 25th anniversary article: the evolution of electronic skin (e-skin): a brief history, design considerations, and recent progress. Adv. Mater. 25, 5997–6038. doi: 10.1002/adma.201302240
Haque, R. I., Chandran, O., Lani, S., and Briand, D. (2018). Self-powered triboelectric touch sensor made of 3D printed materials. Nano Energy 52, 54–62. doi: 10.1016/j.nanoen.2018.07.038
Herzog, D., Seyda, V., Wycisk, E., and Emmelmann, C. (2016). Additive manufacturing of metals. Acta Materialia 117, 371–392. doi: 10.1016/j.actamat.2016.07.019
Huang, Y., Yuan, H., Kan, W., Guo, X., Liu, C., and Liu, P. (2016). A flexible three-axial capacitive tactile sensor with multilayered dielectric for artificial skin applications. Microsystem Technol. 23, 1847–1852. doi: 10.1007/s00542-016-2936-x
Kim, H., Torres, F., Wu, Y., Villagran, D., Lin, Y., and Tseng, T.-L. (2017a). Integrated 3D printing and corona poling process of PVDF piezoelectric films for pressure sensor application. Smart Mater. Structures 26:085027. doi: 10.1088/1361-665X/aa738e
Kim, J. Y., Ji, S., Jung, S., Ryu, B. H., Kim, H. S., Lee, S. S., et al. (2017b). 3D printable composite dough for stretchable, ultrasensitive and body-patchable strain sensors. Nanoscale 9, 11035–11046. doi: 10.1039/c7nr01865g
Lee, H. B., Kim, Y. W., Yoon, J., Lee, N. K., and Park, S.-H. (2017). 3D customized and flexible tactile sensor using a piezoelectric nanofiber mat and sandwich-molded elastomer sheets. Smart Mater. Structures 26:045032. doi: 10.1088/1361-665X/aa64ca
Lei, Z., Wang, Q., and Wu, P. (2017). A multifunctional skin-like sensor based on a 3D printed thermo-responsive hydrogel. Mater. Horizons 4, 694–700. doi: 10.1039/c7mh00262a
Lin, Q., Li, L., Tang, M., Hou, X., and Ke, C. (2018). Rapid macroscale shape morphing of 3D-printed polyrotaxane monoliths amplified from pH-controlled nanoscale ring motions. J. Mater. Chem. C 6, 11956–11960. doi: 10.1039/c8tc02834f
Liu, S., and Li, L. (2017). Ultrastretchable and self-healing double-network hydrogel for 3D printing and strain sensor. ACS Appl. Mater. Interfaces 9, 26429–26437. doi: 10.1021/acsami.7b07445
Melocchi, A., Inverardi, N., Uboldi, M., Baldi, F., Maroni, A., Pandini, S., et al. (2019). Retentive device for intravesical drug delivery based on water-induced shape memory response of poly(vinyl alcohol): design concept and 4D printing feasibility. Int. J. Pharm. 559, 299–311. doi: 10.1016/j.ijpharm.2019.01.045
Momeni, F., Mehdi Hassani, S. M. N., Liu, X., and Ni, J. (2017). A review of 4D printing. Mater. Des. 122, 42–79. doi: 10.1016/j.matdes.2017.02.068
Mousavi, S., Howard, D., Zhang, F., Leng, J., and Wang, C. H. (2020). Direct 3D printing of highly anisotropic, flexible, constriction-resistive sensors for multidirectional proprioception in soft robots. ACS Appl. Mater. Interfaces 12, 15631–15643. doi: 10.1021/acsami.9b21816
Nag, A., Feng, S., Mukhopadhyay, S. C., Kosel, J., and Inglis, D. (2018). 3D printed mould-based graphite/PDMS sensor for low-force applications. Sensors Actuators A: Phys. 280, 525–534. doi: 10.1016/j.sna.2018.08.028
Nishiguchi, A., Zhang, H., Schweizerhof, S., Schulte, M. F., Mourran, A., and Moller, M. (2020). 4D printing of a light-driven soft actuator with programmed printing density. ACS Appl. Mater. Interfaces 12, 12176–12185. doi: 10.1021/acsami.0c02781
Oropallo, W., and Piegl, L. A. (2015). Ten challenges in 3D printing. Eng. Comp. 32, 135–148. doi: 10.1007/s00366-015-0407-400
Phuhongsung, P., Zhang, M., and Bhandari, B. (2020). 4D printing of products based on soy protein isolate via microwave heating for flavor development. Food Res. Int. 137:109605. doi: 10.1016/j.foodres.2020.109605
Rengier, F., Mehndiratta, A., von Tengg-Kobligk, H., Zechmann, C. M., Unterhinninghofen, R., Kauczor, H. U., et al. (2010). 3D printing based on imaging data: review of medical applications. Int. J. Comput. Assist. Radiol. Surg. 5, 335–341. doi: 10.1007/s11548-010-0476-x
Schmidt, M., Merklein, M., Bourell, D., Dimitrov, D., Hausotte, T., Wegener, K., et al. (2017). Laser based additive manufacturing in industry and academia. CIRP Annals 66, 561–583. doi: 10.1016/j.cirp.2017.05.011
Spiegel, C. A., Hippler, M., Münchinger, A., Bastmeyer, M., Barner-Kowollik, C., Wegener, M., et al. (2019). 4D Printing at the Microscale. Adv. Funct. Mater. 30:1907615. doi: 10.1002/adfm.201907615
Sun, J., Pu, X., Liu, M., Yu, A., Du, C., Zhai, J., et al. (2018). Self-Healable, stretchable, transparent triboelectric nanogenerators as soft power sources. ACS Nano 12, 6147–6155. doi: 10.1021/acsnano.8b02479
Tibbits (2013). The Emergence of 4D Printing. Available online at: https://www.ted.com/talks/skylar_tibbits_the_emergence_of_4d_printing/up-next (accessed April 4, 2013).
Truby, R. L., and Lewis, J. A. (2016). Printing soft matter in three dimensions. Nature 540, 371–378. doi: 10.1038/nature21003
Wan, Y., Wang, Y., and Guo, C. F. (2017). Recent progresses on flexible tactile sensors. Mater. Today Phys. 1, 61–73. doi: 10.1016/j.mtphys.2017.06.002
Wang, Q., Yu, Y., Yang, J., and Liu, J. (2015). Fast fabrication of flexible functional circuits based on liquid metal dual-trans printing. Adv. Mater. 27, 7109–7116. doi: 10.1002/adma.201502200
Wegener, M., Wirges, W., and Gerhard-Multhaupt, R. (2005). Piezoelectric Polyethylene Terephthalate (PETP) foams – specifically designed and prepared ferroelectret films. Adv. Eng. Mater. 7, 1128–1131. doi: 10.1002/adem.200500177
Wu, H., Zhang, X., Ma, Z., Zhang, C., Ai, J., Chen, P., et al. (2020). A material combination concept to realize 4D printed products with newly emerging property/functionality. Adv. Sci. (Weinh) 7:1903208. doi: 10.1002/advs.201903208
Xu, Y., Wu, X., Guo, X., Kong, B., Zhang, M., Qian, X., et al. (2017). The boom in 3D-Printed sensor technology. Sensors (Basel) 17:1166. doi: 10.3390/s17051166
Yintang, W. E. N., Shuquan, Z., Jiankang, H. E., Qingliang, Z., Bo, L., Shifeng, W. E. N., et al. (2020). Four-dimensional printing —— the additive manufacturing technology of intelligent components. J. Mechan. Eng. 56, 1–25. doi: 10.3901/jme.2020.15.001
Zarek, M., Layani, M., Cooperstein, I., Sachyani, E., Cohn, D., and Magdassi, S. (2016). 3D printing of shape memory polymers for flexible electronic devices. Adv. Mater. 28, 4449–4454. doi: 10.1002/adma.201503132
Zhang, B., Li, S., Hingorani, H., Serjouei, A., Larush, L., Pawar, A. A., et al. (2018). Highly stretchable hydrogels for UV curing based high-resolution multimaterial 3D printing. J. Mater. Chem. B 6, 3246–3253. doi: 10.1039/c8tb00673c
Keywords: 4D printing, multi-material, flexible, soft, tactile sensors
Citation: Tang Y, Dai B, Su B and Shi Y (2021) Recent Advances of 4D Printing Technologies Toward Soft Tactile Sensors. Front. Mater. 8:658046. doi: 10.3389/fmats.2021.658046
Received: 25 January 2021; Accepted: 23 March 2021;
Published: 15 April 2021.
Edited by:
Ilkwon Oh, Korea Advanced Institute of Science and Technology, South KoreaReviewed by:
Rouhollah Dermanaki Farahani, École de Technologie Supérieure (ÉTS), CanadaCopyright © 2021 Tang, Dai, Su and Shi. This is an open-access article distributed under the terms of the Creative Commons Attribution License (CC BY). The use, distribution or reproduction in other forums is permitted, provided the original author(s) and the copyright owner(s) are credited and that the original publication in this journal is cited, in accordance with accepted academic practice. No use, distribution or reproduction is permitted which does not comply with these terms.
*Correspondence: Baiqian Dai, QmFpLVFpYW4uRGFpQG1vbmFzaC5lZHU=; Bin Su, c3ViaW5AaHVzdC5lZHUuY24=
Disclaimer: All claims expressed in this article are solely those of the authors and do not necessarily represent those of their affiliated organizations, or those of the publisher, the editors and the reviewers. Any product that may be evaluated in this article or claim that may be made by its manufacturer is not guaranteed or endorsed by the publisher.
Research integrity at Frontiers
Learn more about the work of our research integrity team to safeguard the quality of each article we publish.