- 1Institute of Materials, China Academy of Engineering Physics, Jiangyou, China
- 2China Nuclear Power Technology Research Institute, Shenzhen, China
Large grain UO2 is considered as an accident tolerant fuel with great application potential due to its competitive advantage of good fission gas retention. In this paper, the influence of preparation parameters such as sintering atmosphere, mixing process, powder pretreatment and grain growth additives on the grain size of UO2 is systematically studied. The result shows that the factors mentioned above have different effects on the grain size of UO2. The grain growth of UO2 pellet sintered in oxidizing atmosphere is better than those in reducing atmosphere. The wet mixing process has a significant advantage over the dry mixing process. In addition, the powder pretreatment has little effect on grain growth while the influence of additives plays the main role. Large grain UO2 pellets with uniform grain size up to 150 μm are successfully prepared. Finally, the thermo-physical properties of the pellets are investigated.
Introduction
After the Fukushima accident in 2011, the Accident Tolerant Fuels (ATFs) has been paid much attention by researchers. As a kind of ATF fuels, large grain UO2 fuel is characterized as the significantly increased UO2 grain size in the fuel pellet, by adding trace additives and optimized preparation process. Grain boundaries and open pores are the main means of fission gas release (FGR). The specific surface area of grain decreases with the grain size increasing, and thus the pores will be distributed in the grain as far as possible. Moreover, the diffusion distance of fission gases from the grain interior to the grain boundary is increased accordingly. This means a higher fission gas retention rate for large grain UO2. On the other hand, the plasticity and thermal creep properties of large grain UO2 are higher than normal UO2 (Kang et al., 2010). Then the radiation swelling, which is of great significance to reduce the Pellet-Cladding Interaction (PCI), could be reduced. Thus, the large grain UO2 fuel is capable to achieve higher burn-up than the normal UO2 fuel (Turnbull, 1974; Hastings, 1983; Une et al., 1993). Meanwhile, the large grain UO2 fuel is almost composed of pure UO2. It can completely inherit the advantages of normal UO2 fuel, such as high melting point, good thermal stability, good compatibility with coolant and cladding material, excellent irradiation stability and water corrosion resistance. Besides, the large grain UO2 fuel owns perfect compatibility to the present Light-Water Reactor plants (LWRs) fuel manufacturing and operating system. This is much favorable for nuclear power plants and nuclear fuel plants. Based on the advantages in terms of safety, economy, and compatibility, the large grain UO2 fuel is considered as one of the most promising ATFs.
Many studies have been carried out in the past to investigate the factors that contribute to the grain growth of UO2 pellets. In general, sintering temperature, holding time and sintering aids were reported to be important for increasing the grain size of UO2 pellets (Singh, 1977). However, much higher temperature could lead to abnormal growth of UO2 grains (MacEwan and Lawson, 1962). Long-term heat preservation had little effect on grain growth (Glodeanu et al., 1987), but would increase the cost of fuel production. The most effective way was adding additives to the UO2 matrix. The common additives included Cr2O3 (Bourgeois et al., 2001; Arborelius et al., 2006; Yang et al., 2012), TiO2 (Amato et al., 1966; Ainscough et al., 1974; Yao et al., 2016), Nb2O5 (Killeen, 1975; Song et al., 1994), Al2O3 (Oh et al., 2014; Une et al.,2000) and MgO (Sawbridge et al., 1980). Recently, Yang et al. (2012) studied the grain growth of Cr2O3 doped UO2 under different oxygen potential sintering atmospheres. Then, a thermodynamic solubility model of Cr in UO2 was established by Martial et al. using the electron probe microanalysis (Riglet-Martial et al., 2014). Che et al. used the BISON fuel performance code to calculate the FGR of Cr2O3 doped UO2 fuel (Che et al., 2018). Satisfactory simulation results have been obtained. However, few of the above literatures reported the influence of the preparation process on the grain size of UO2.
In this work, the effects of different additives, mixing methods, powder pretreatment processes, forming pressure, and sintering atmosphere on the grain growth of UO2 were systematically studied. Additionally, the thermo-physical properties of the large grain UO2 were also discussed.
Experimental
Starting Powder and Preparation Process
UO2 powders were obtained from CNNC Jianzhong Nuclear Fuel Co., Ltd. The powders purity was 99.9%, and its sizes ranged from 10 to 20 μm. The O/U ratio of the UO2 powders was 2.17 detected by thermos-gravimetric analysis. The zinc stearate (99% purity, 50 μm particle size, Macklin Scientific Co., LTD., China) was used as binder and lubricant to enhance the strength of the green body, and the addition amount in the pellets is 0.1 wt%. Six types of additive powders were used, as listed in Table 1.
Firstly, the raw materials were mixed. During the mixing process, three different mixing methods were studied. The difference between the two dry mixing methods was with or without grinding media. The Dry mixing was performed on a planetary mixer using a WC container, while the wet mixing was performed on a horizontal mixer using a nylon tank. Both mixing processes run at a speed of 300 r/min for 24 h. The powder of wet mixing was obtained by heating at 100°C for 5 h. Secondly, the mixed powders were granulated. Two kinds of granulation processed were adopted. Spark Plasma Sintering (SPS) can activate the powder and realize the densification of high melting point materials in a short time. In this experiment, the difference between SPS pre-sintering granulation and traditional cold press granulation was investigated. The SPS pre-sintering granulation process was heating the powder at 800°C for 1 min. A pressure of 25 MPa was applied on the powders during the whole sintering process. After the SPS pre-sintering process, the density of pellets reached 68%. The Cold press granulation was to hold the powder under 300 MPa for 5 min. Then, the green body was crushed and sieved with a 50-mesh screen. Thirdly, the mixed particles were introduced into a cemented carbide mold for biaxial pressing with 100 MPa, 200 MPa, and 300 MPa respectively. The green density of pellets formed under different processes were distributed within the range of 5.7–6.5 g/cm3. Finally, the green body was sintered at temperature of 1680 and 1700°C. The holding times were 1.5 and 4 h. For comparison, pure UO2 pellets were prepared by the same technological process. H2, H2-H2O, and H2-CO2 were used as sintering atmosphere. The content of H2O or CO2 in H2 were 1 vol% and 2 vol%, respectively. The details of the above process conditions and parameters were listed in Table 2.
Microstructure Characterization
The pellets were successively grinded by 500, 1000, 2000 mesh SiC sandpaper, then polished with 1 μm diamond suspension, and finally eroded with H2O2/HCl etching solution. The erosion time is 1–3 min. The grain morphology was analyzed by laser confocal microscopy (LSCM, LEXT OLS4000, Olympus). Grain size was determined by the linear intercept method, and more than 200 intercepts were counted for each sample.
Thermal Physical Performance
The thermal diffusivity (TD) of the pellet was determined by a laser testing equipment (LFA 427, Netzsch, Germany). The sintered pellet was processed into the final size of Φ8 × 3 mm for the thermal diffusivity test. The testing temperature range was 25–1000°C, with an interval of 200°C. The density (ρp) of UO2 pellet was measured by the Archimedes method. The thermal expansion coefficient of the pellet was measured by a thermal expansion tester (DIL 402, Netzsch, Germany). The testing temperature range was 25–1200°C. The sintered pellet was processed into the final size of Φ8 × 13 mm for the thermal expansion test.
The thermal conductivity (TC) λc (W m−1 K−1) was determined from the following formula:
where ρp (g cm−3) is the density of pellet, Dd (mm2 s−1) is the thermal diffusivity of pellet, Cp (J g−1 K−1) is the specific heat capacity of pellet. The value of Cp is dominated by UO2 where the additives is ignored due to its low mass fraction (≤0.5 wt%). The specific heat capacity of UO2 can be derived from the following equation (Fink, 2000):
where CUO2 refers to the heat capacity of UO2 in J mol−1 K−1, and a (a = T/1000) refers to the temperature in K.
The coefficient of thermal expansion (CTE) was calculated from the following computational formula:
where ET (K−1) is the CTE of UO2 pellet at temperature T, T (K) is the temperature, Tref. (K) is the reference temperature, LT (mm) is the length of pellet at temperature T, Lref. (mm) is the length of pellet at temperature Tref. In this work, Tref. is set at 25°C. For comparison, the CTE of UO2 can be derived from the following equation (Martin, 1988):
For 273–923 K:
and for 923–3120 K:
where LUO2(T) and L(273) are lengths of UO2 at temperatures of T(K) and 273 K, respectively.
Results and Discussions
The Effect of Different Additives on UO2 Grain Growth
Figure 1 shows the metallographic photos of UO2 doped with different additives. The sintering process is performed at 1700°C for 1.5 h. The average grain size of doped UO2 with different additives is listed in Table 3. In this experiment, the average grain size of pure UO2 sintered under H2-CO2 atmosphere is about 16 μm. It can be found that Al2O3 has almost no effect on the growth of UO2 grains. This is consistent with the calculation results reported by Cooper et al. (2018). CaO has a similar promoting effect with MgO. Cr2O3 shows the best promotion effect on grain growth of UO2. This can be attributed to the higher concentration of uranium vacancies produced by doped Cr2O3 and the liquid phase behavior of Cr2O3 in the sintering process. Therefore, Cr and Cr2O3 are using as the additives in the following experiments. The effect of doped NiO is reported for the first time. However, the effect is contrary to expectations. The grain size of UO2 doped with NiO is smaller than pure UO2 under the same condition. This indicates that NiO can inhibit the grain growth of UO2. According to the defect chemistry theory by Cooper, additives can increase the concentration of negatively charged uranium vacancies and thus promote UO2 grain growth (Cooper et al., 2018). Therefore, the doping of NiO may cause a decrease of the uranium vacancy concentration during the sintering process. On the other hand, NiO can be reduced by H2 above 400°C (Janković et al., 2008). So, there is the possibility of interaction between Ni and UO2, and thereby reducing the effect of oxygen potential on UO2. At the same time, the dispersion of liquid Ni on the grain edge may pin the migration of UO2 grain boundaries. In summary, the doping effect of NiO needs further research and analysis.
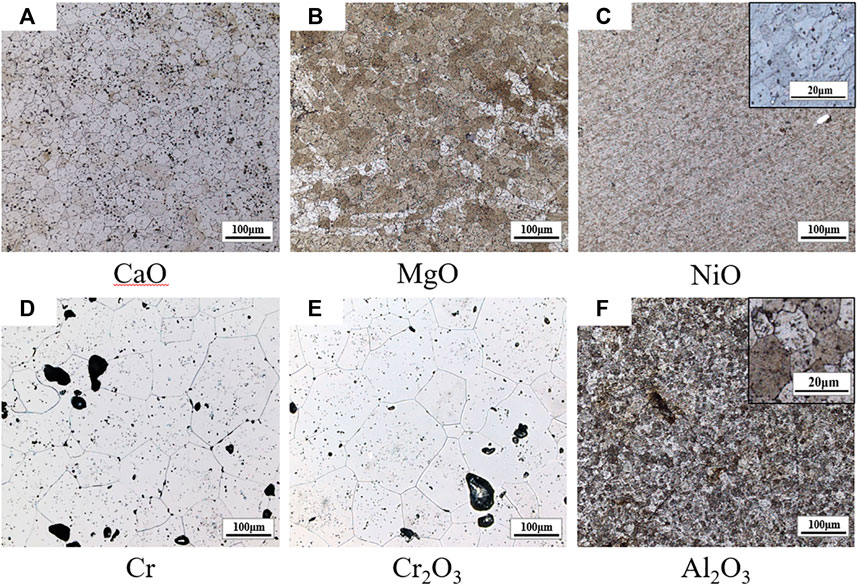
FIGURE 1. Grain morphologies of UO2 doped with different additives. The types of these additives are marked below the diagram.
The Effect of Mixing Method on UO2 Grain Growth
Figure 2 shows the metallographic photos of Cr doped UO2 pellets fabricated by different mixing processes. The sintering process is performed at 1700°C for 4 h. As shown in Figure 2, the grain morphologies obtained by the three different mixing processes are uniform, but the grain growth effect is quite different. Table 4 shows the average grain size of the Cr-doped UO2 pellets in Figure 2. The average grain size of pellets from dry mixing with balls and without balls are 28 and 57 μm, respectively. The grain size of pellets from wet mixing with balls reaches 75 μm. It seems that the additive dispersion in the matrix is an important factor affecting the grain growth. Due to the difference in the density of raw material density and the agglomeration characteristics of fine powders, the dry mixing process without any mixing medium leads to the worst dispersion effect of additive. As a result, the grain size of pellets from such a mixing process was small. In comparison, the introduction of a stirring medium promotes the powders to be mixed. So the grain size obtained by dry mixing with balls is much larger than that of dry mixing samples without balls. The wet mixing process always leads to the most uniform dispersion of the additive in the UO2 matrix, which is beneficial to the dissolution and diffusion of Cr additive. Thus, the pellets from the wet mixing process own the largest grain size.
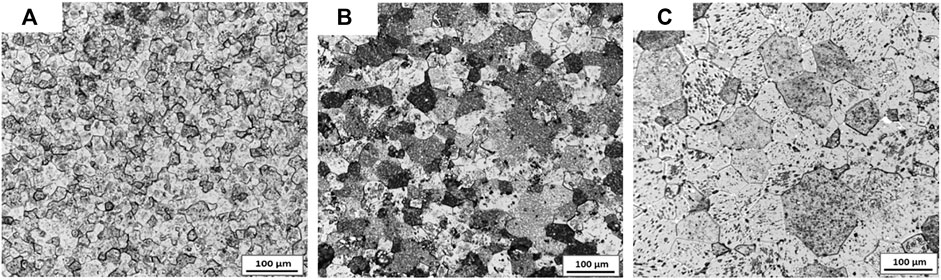
FIGURE 2. Grain morphologies of Cr-doped UO2 sintered under different mixing methods. (A) Dry mixing (no balls); (B) Dry mixing (with balls); (C) Wet mixing (with balls).
The Effect of Powder Pretreatment on UO2 Grain Growth
Figure 3 shows the metallographic photos of Cr and Cr2O3 doped UO2 under different powder pretreatment processes. The sintering process is performed at 1700°C for 4 h. The UO2 grain morphologies shown in Figure 3 are uniform. This indicates that the additive achieved a good mixing effect with UO2 during the process of dry mixing with balls. Table 5 shows the average grain size of the doped UO2 after different powder treatments. Obviously, with the same additive, the average grain size of the doped UO2 pellet obtained by cold press granulation is larger than that obtained by the SPS pre-sintering method. The reason may be that the UO2 is slightly sintered at 800°C (Ge et al., 2013). Therefore, the densification of the pellets becomes more difficult, and the diffusion of additives during the sintering process is inhibited. Under the same fabrication condition, the grain size of Cr2O3 doped UO2 is larger than that of Cr doped UO2. The reason for this difference should be related to the oxidation state of Cr in UO2. Martial found that the solubility of Cr in UO2 increased with the growth of the oxidation state of Cr in the solid phase (Riglet-Martial et al., 2014). This indicates that the solubility of Cr2O3 in UO2 is much higher than that of metallic Cr. Johnson et al. studied the binary phase diagram of Cr2O3 and Cr, and reported the existence of a eutectic at 1665°C (Johnson and Muan, 1968). So, the possible reason for the difference between the two additives may be caused by the easier formation of Cr-O liquid phase with Cr2O3 than Cr, which is more conducive to the growth of UO2 grains.
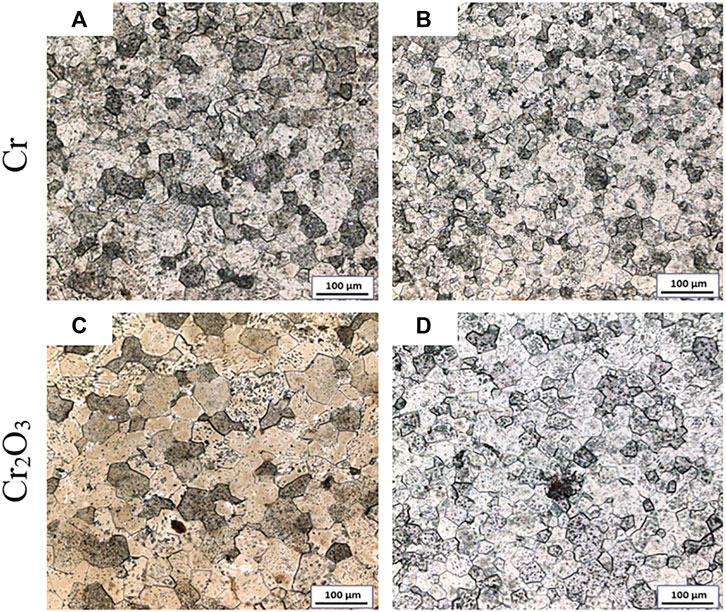
FIGURE 3. Grain morphologies of Cr and Cr2O3 doped UO2 under different powder pretreatment processes. (A) Cold press granulation; (B) SPS pre-sintering; (C) Cold press granulation; (D) SPS pre-sintering.
The Effect of Different Pressing Pressures on UO2 Grain Growth
Figure 4 shows the metallographic photos of Cr and Cr2O3 doped UO2 under different forming pressures. The sintering process is performed at 1700°C for 1.5 h. The forming parameters and average grain size of the pellets are listed in Table 6. As shown in Figure 4, the morphology of UO2 grains is clear and uniform. However, due to the similar grain size, it is difficult to distinguish the influence of different forming pressures on the grain size of the UO2 pellet. The grain size distribution of two kinds of doped UO2 by statistical method is calculated and shown in Figure 5. It is found that the ratio of 150–200 μm grain size increases rapidly with the increasing of forming pressure. For example, from 100 to 300 MPa, the percentage of grain size between 150 and 200 μm for the Cr-doped UO2 increases from 6.57 to 14.28%. In general, the average grain size of UO2 increases with the forming pressure. Since the additives content in the pellet is very small, the green density of the UO2 pellet doped with Cr and Cr2O3 is nearly the same. As shown in Table 6, the green density of UO2 pellets varies with different forming pressures, but the density tends to be similar after sintering. This shows that the forming pressure has little effect on the sintered density with certain strength. However, the average grain size of the pellet increases with the density of the green body. When the binder content is low, the UO2 grain size increases with the density of the compacted body (Amato and Colombo, 1964). Besides, higher body density means less porosity. Pores are an important microstructural feature of powder compacts and have been considered to have an impediment to grain boundary migration (Nichols, 1968). During the sintering process, the pores will be located at the intersection of grain boundaries or distributed along individual boundaries (Coble, 1961). Thereby, the pores will hinder the growth of grains. Therefore, under the same sintering process, the grain sizes of pellets with higher green density are larger.
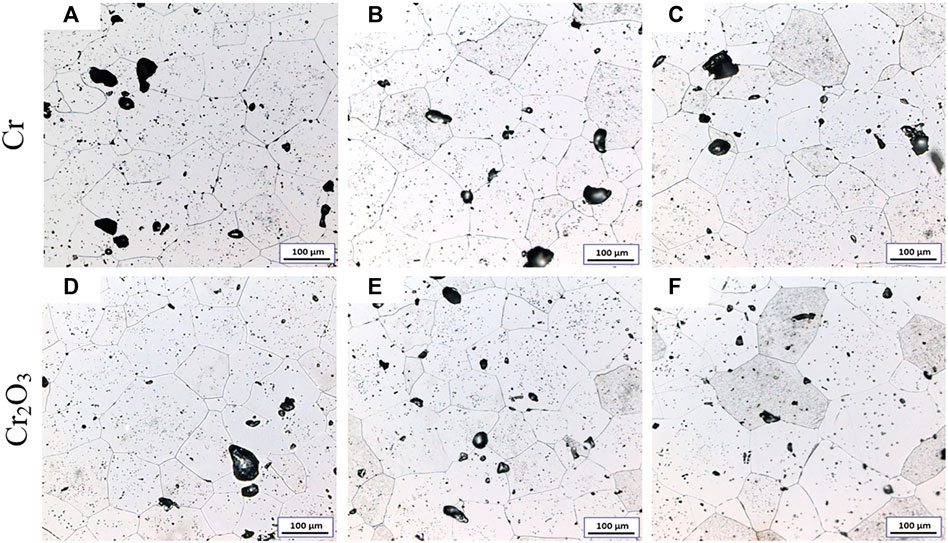
FIGURE 4. Grain morphologies of Cr and Cr2O3 doped UO2 sintered under different pressing pressures. (A) Cr-100 MPa; (B) Cr-200 MPa; (C) Cr-300 MPa; (D) Cr2O3-100 MPa; (E) Cr2O3-200 MPa; (F) Cr2O3-300 MPa.
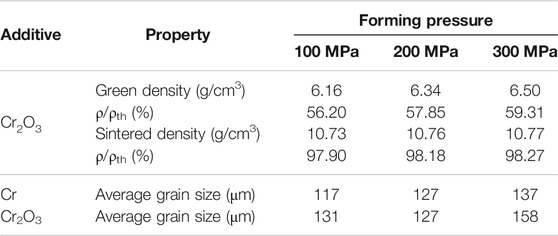
TABLE 6. Green density, sintered density and average grain size of UO2 pellets under different forming pressures. ρ and ρth are the density measured by the geometric method and the theoretical density, respectively.
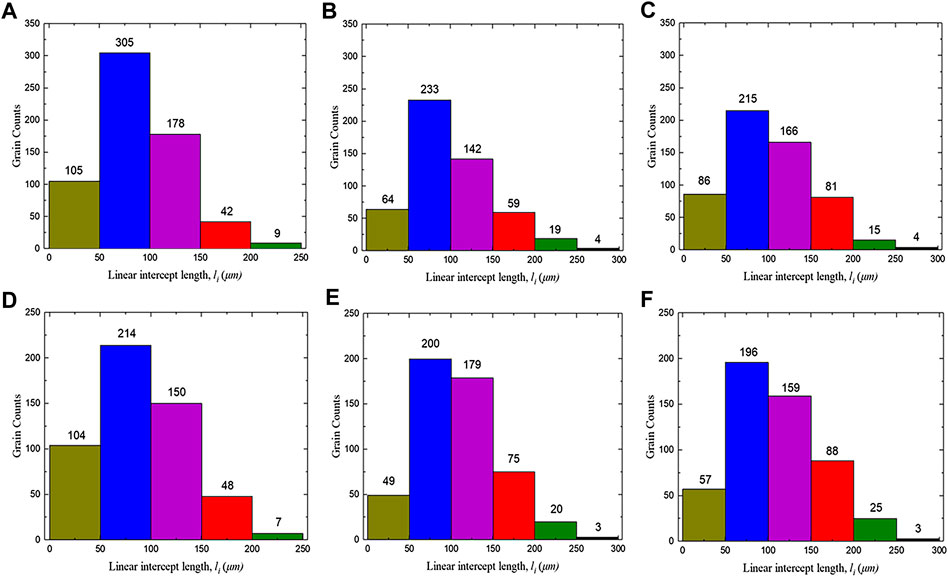
FIGURE 5. Statistical distribution of sintered UO2 grain size under different forming pressures. (A) Cr-100 MPa; (B) Cr-200 MPa; (C) Cr-300 MPa; (D) Cr2O3-100 MPa; (E) Cr2O3-200 MPa; (F) Cr2O3-300 MPa.
The Effect of Different Sintering Atmosphere on UO2 Grain Growth
Figures 6 and 7 are the metallographic morphologies of normal UO2 and doped UO2 in different sintering atmospheres, respectively. The sintering process is performed at 1680°C for 4 h. As shown in Figures 6 and 7, the morphology of UO2 grains is clear and uniform in size. The grain size data are listed in Table 7. It can be seen that the grain size of pure UO2 sintered in H2-CO2 is larger than that in H2. In addition, the grain growth of Cr and Cr2O3 doped UO2 under H2-CO2 is obvious. The grain size of pellets under H2-H2O is equivalent to that under pure H2. By comparing the result in Table 7, the effect of Cr2O3 on grain growth is still better than that of Cr. Moreover, when comparing the results of Cr doping in Figures 6 and 7, it indicates that metallic Cr is easier to form oxidation state at 1700°C than at 1680°C. In the past, the importance of oxygen potential for grain growth during UO2 sintering has been confirmed (Assmann et al., 1986; Harada, 1997). Additionally, the results shown in Figure 7 also prove that the grain growth of UO2 is directly related to the oxygen potential during the sintering process. The essence of grain growth is a process of grain boundary displacement. Grain boundary displacement is a process in which atoms adjacent to the grain boundary are activated, and diffuse to the vacancies or dislocations in the grain boundary. These are mainly affected by the lattice diffusion rate and the vacancy concentration. Matzke pointed out that the main defects in UO2 were oxygen interstitials and uranium vacancies, and the self-diffusion rate of uranium was squared with the x of UO2+x (Matzke, 1969; Matzke, 1983). Assuming that UO2+x is related to the oxygen potential, then the value of x will be in equilibrium with the oxygen partial pressure (Ohse et al., 1985). The results obtained in this work are also consistent with these theories. This indicates that the grain growth of UO2 is enhanced by increasing the oxygen partial pressure.
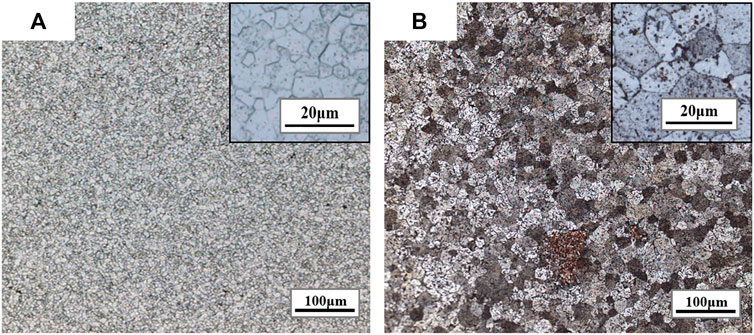
FIGURE 6. Grain morphologies of pure UO2 sintered under different sintering atmospheres. (A) H2; (B) H2-CO2.
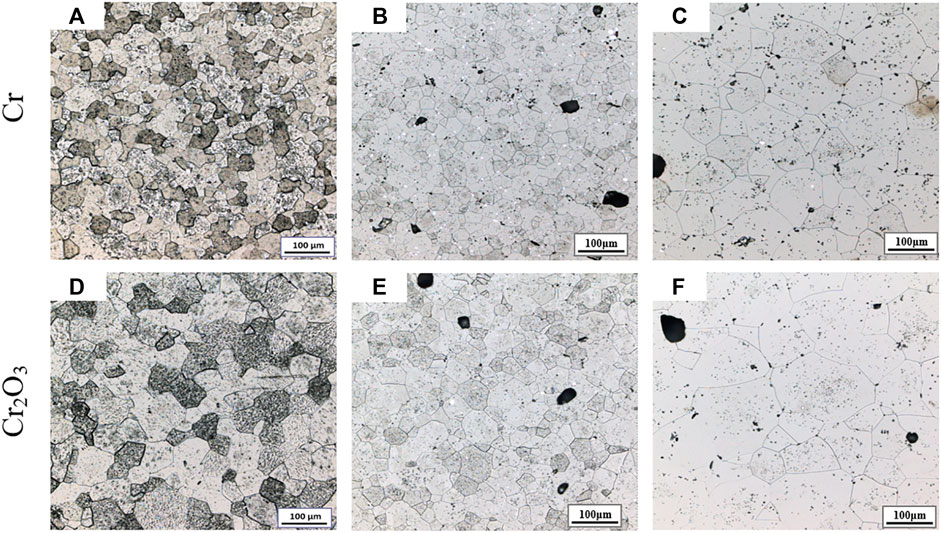
FIGURE 7. Grain morphologies of Cr and Cr2O3 doped UO2 sintered under different sintering atmospheres. (A) H2; (B) H2-H2O; (C) H2-CO2; (D) H2; (E) H2-H2O; (F) H2-CO2.
The Effect of Additive Content on UO2 Grain Growth
Figure 8 shows the metallographic photos of UO2 doped with different contents of Cr and Cr2O3. The sintering process is performed at 1700°C for 4 h. As shown in the Figures, the morphology of UO2 grains is visible after erosion and the size is relatively uniform. The corresponding average grain size results are listed in Table 8. It can be seen that the grain sizes of Cr and Cr2O3 doped UO2 both increase with the growth of the additive amount. In general, the promotion effect of Cr2O3 on the grain growth of UO2 is better than that of metallic Cr under the same content. The increase of Cr content under the same oxygen potential will increase the number of Cr ions and thus create more uranium vacancies. So, the grain size of Cr doped UO2 increases with the increase of Cr content in the range of 0.1 wt% to 0.5 wt%. By contrast, the increase of Cr2O3 content above 0.25 wt% has a gentler effect on grain growth promotion. Regarding this, Kuri et al. combined the quantitative analysis of micro-beam XRD and EPMA data to determine that the average concentration of dissolved Cr in the UO2 matrix was 0.07 ± 0.01 wt% (Kuri et al., 2014). However, there are still many differences between the results of this experiment and those of others. Firstly, unlike the results by Bourgeois, there is no obvious pinning phenomenon with the increase of Cr2O3 content in this experiment. As shown in Table 7, the grain growth effect of UO2 doped with Cr and Cr2O3 in H2-CO2 atmosphere is much better than that in H2-H2O. This indicates that the oxygen potential of CO2 is much higher than H2O. Therefore, the difference between the results of this experiment and those obtained by Bourgeois was probably related to the different atmospheres in the sintering process. Secondly, Yang et al. believed that the continuous introduction of CO2 suppressed the grain growth of Cr2O3 doped UO2, and claimed that the UO2 grain size was only 12.2 μm when the doping amount was 0.103 wt% (Yang et al., 2012). By contrast, in this work, with a similar Cr2O3 doping amount, the grain size obtained by continuously introducing CO2 can reach 117 μm.
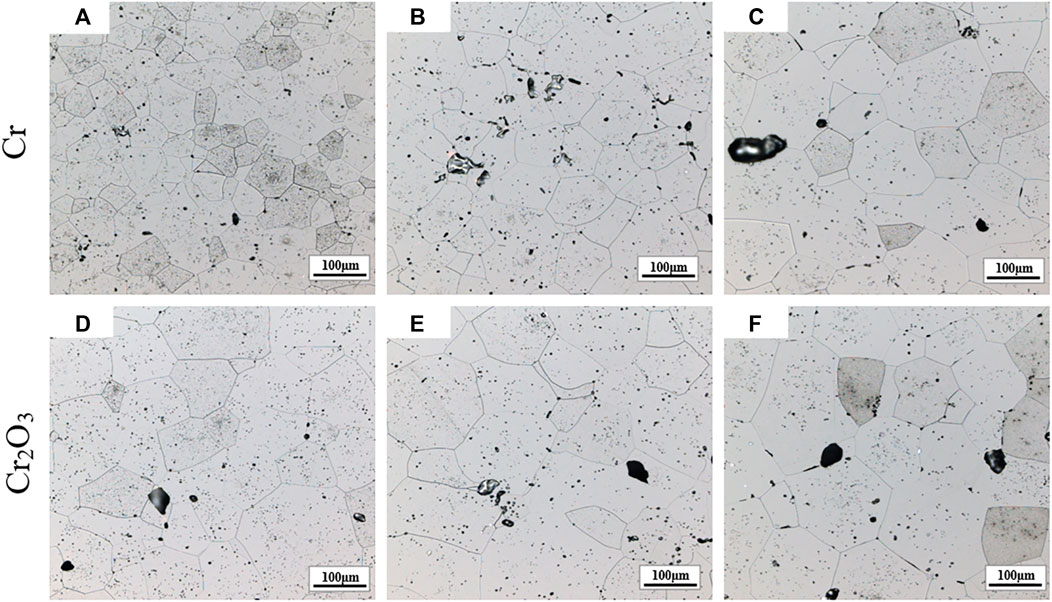
FIGURE 8. The grain morphologies of UO2 doped with different contents of Cr and Cr2O3. (A) 0.10 wt.% Cr; (B) 0.25 wt.% Cr; (C) 0.50 wt.% Cr; (D) 0.10 wt.% Cr2O3; (B) 0.25 wt.% Cr2O3; (C) 0.50 wt.% Cr2O3.
Thermal-Physical Properties of the Large Grain UO2
According to formulas (1, 2), the TD and TC of large grain UO2 doped with Cr are presented in Figure 10. The TD and TC of normal UO2 and values according to the empirical formula recommended by Fink (Fink, 2000) are also plotted for comparison. The calculated density of the sintered pellets in Figure 10 is about 97%. The average grain size of the 0.25 wt% Cr doped UO2 pellet used in this TC test is about 102 μm and metallographic photo is shown in Figure 9. The preparation process was dry mixing with balls and cold press granulation. The sintering process was performed at 1700°C for 4 h under H2-CO2. It is worth noting that the TD and TC of large grain UO2 are slightly lower than those of the normal UO2 at lower temperatures. This can be attributed to the fact that impurities can reduce the thermal conductivity of UO2 (Mei et al., 2014). However, As the temperature rises, the TD and TC of the large grain UO2 turn higher than those of the normal UO2 above 600°C. The explanation for this may be that UO2 crystals are not isotropic, and the presence of grain boundaries will reduce TC to a certain extent (Gofryk et al., 2014). In addition, the TC increase may also relate to the higher specific heat capacity of Cr.
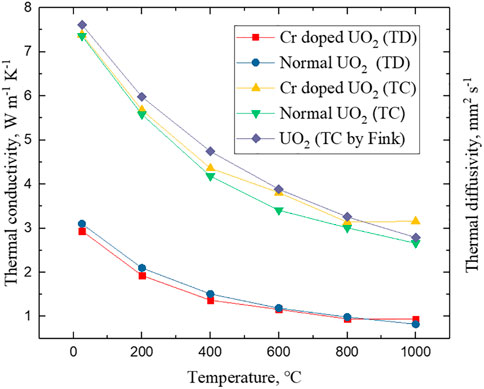
FIGURE 10. The thermal diffusivity (TD) and thermal conductivity (TC) of large grain UO2 and normal UO2.
The CTE of large grain UO2 doped with 0.5 wt% Cr2O3 and normal UO2 sintered in this experiment can be calculated by formulas (3–5), and the results are shown in Figure 11. The preparation and sintering processes of the samples for CTE were consistent with those for the TC testing. For comparison, the CTE of UO2 is calculated according to the recommendation of Martin (1988). The average grain size of the Cr2O3-doped UO2 pellet used in this CTE test is about 159 μm and the metallographic photo is shown in Figure 9. The CTE of large grain UO2 and normal UO2 grows with temperature. However, the CTE of large grain UO2 is lower than that of the normal UO2 at the same temperature. The decrease range is maintained at 11.8–16.9% in the temperature range of 200–1200°C. Thermal expansion is the result of volume expansion caused by the aggravation of the lattice vibration of the solid material during heating process. For the effect of grain size on the thermal expansion, it can be explained by the reduction of the interface which leads to the weakening of the anharmonic effect. There are larger anharmonic atomic vibrations at the grain boundaries, and the thermal expansion of the grain boundaries is 2.5–5 times that of the crystalline state (Klam et al., 1987). In addition, two experiments both show that the thermal expansion coefficient will decrease when the grain size increases (Parker and Rice, 1989, Lu and Sui, 1995). In summary, the reduction in CTE is beneficial to alleviate PCI at high temperatures, and also is of great significance to improving fuel safety.
Conclusion
In the current work, the influence of mixing technology, sintering atmosphere, forming pressure, powder pretreatment, additives, and content on the grain growth of UO2 was systematically studied. The results showed that the influence of additives on the grain growth of UO2 is the most obvious. Cr2O3 shows the best promotion effect among the selected additives. On the contrary, NiO shows an inhibitory effect on the grain growth of UO2. The preparation process and the sintering atmosphere also play an important role in the grain growth of UO2. Different mixing and powder pretreatments processes can affect the dispersion effect of UO2 powder and additives. The best promotion effect is achieved by the wet mixing process. The introduction of CO2 into the sintering atmosphere can effectively promote the grain growth of UO2. The average grain size of UO2 increases with the growth of forming pressure and additive content. However, due to the low solubility of Cr in UO2, the grain growth effect of Cr2O3 tends to be saturated above 0.25 wt%. In this work, UO2 doped with 0.5 wt% Cr2O3 shows the largest grain size, and the average grain size reaches up to 159 μm.
Compared with normal UO2, large grain UO2 exhibits obvious advantages in CTE and also shows higher TC at temperatures higher than 600°C. Such enhancement effect has unique advantages in improving the properties of UO2 fuel and reducing the swelling effect of the pellets at high temperatures, which can remarkably improve the service performance and the safety of the fuel system.
Data Availability Statement
The raw data supporting the conclusion of this article will be made available by the authors, without undue reservation.
Author Contributions
YZ: Investigation, Data curation, Writing–original draft preparation; RG: Conceptualization, Investigation; BL: Conceptualization, Investigation; ZY: Validation, Writing- Reviewing and Editing; QH: Investigation; ZW: Investigation; LD: Investigation; XL: Investigation; MC: Conceptualization, Funding acquisition; PZ: Supervision, Funding acquisition; BB: Supervision, Reviewing and Editing; YW: Conceptualization; LC: Conceptualization; BY: Conceptualization; TL: Conceptualization; RL: Conceptualization.
Funding
This work was supported by the National Key Research and Development Program of China (No. 2017YFB0702402), National Natural Science Foundation of China (Nos. 51804285, 51604250 and U20B2021) and CAEP Foundation (No. CX20200018). In addition, this work was a part of the Nuclear Energy Development project.
Conflict of Interest
TL and RL were employed by the company China Nuclear Power Technology Research Institute.
The remaining authors declare that the research was conducted in the absence of any commercial or financial relationships that could be construed as a potential conflict of interest.
References
Ainscough, J. B., Rigby, F., and Osborn, S. C. (1974). The effect of titania on grain growth and densification of sintered UO2. J. Nucl. Mater. 52 (2), 191–203. doi:10.1016/0022-3115(74)90167-6
Amato, I., Colombo, R. L., and Balzari, A. P. (1966). Grain growth in pure and titania-doped uranium dioxide. J. Nucl. Mater. 18 (3), 252–260. doi:10.1016/0022-3115(66)90166-8
Amato, I., and Colombo, R. L. (1964). The influence of organic additions on the solarization and grain growth of sintered UO2. J. Nucl. Mater. 11 (3), 348–351. doi:10.1016/0022-3115(64)90028-5
Arborelius, J., Backman, K., Hallstadius, L., Limbaeck, M., Nilsson, J., Rebensdorff, B., and Roennberg, G. (2006). Advanced doped UO2 pellets in LWR applications. J. Nucl. Sci. Technol. 43 (9), 967–976. doi:10.1080/18811248.2006.9711184
Assmann, H., Dörr, W., and Peehs, M. (1986). Control of UO2 microstructure by oxidative sintering. J. Nucl. Mater. 140 (1), 1–6. doi:10.1016/0022-3115(86)90189-3
Bourgeois, L., Dehaudt, P., Lemaignan, C., and Hammou, A. (2001). Factors governing microstructure development of Cr2O3-doped UO2 during sintering. J. Nucl. Mater. 297 (3), 313–326. doi:10.1016/S0022-3115(01)00626-2
Che, Y., Pastore, G., Hales, J., and Shirvan, K. (2018). Modeling of Cr2O3-doped UO2 as a near-term accident tolerant fuel for LWRs using the BISON code. Nucl. Eng. Des. 337, 271–278. doi:10.1016/j.nucengdes.2018.07.015
Coble, R. L. (1961). Sintering crystalline solids. I. Intermediate and final state diffusion models. J. Appl. Phys. 32 (5), 787–792. doi:10.1063/1.1736107
Cooper, M. W. D., Stanek, C. R., and Andersson, D. A. (2018). The role of additive charge state on defect chemistry and grain growth of doped UO2. Acta Mater. 150, 403–413. doi:10.1016/j.actamat.2018.02.020
Fink, J. K. (2000). Thermo-physical properties of uranium dioxide. J. Nucl. Mater. 279 (1), 1–18. doi:10.1016/S0022-3115(99)00273-1
Ge, L., Subhash, G., Baney, R. H., Tulenko, J. S., and McKenna, E. (2013). Densification of uranium dioxide fuel pellets prepared by spark plasma sintering (SPS). J. Nucl. Mater. 435 (1–3), 1–9. doi:10.1016/j.jnucmat.2012.12.010
Glodeanu, F., Furtuna, I., Paraschiv, A., and Paraschiv, M. (1987). Grain growth in high density UO2. J. Nucl. Mater. 148 (3), 351–352. doi:10.1016/0022-3115(87)90029-8
Gofryk, K., Du, S., Stanek, C. R., Lashley, J. C., Liu, X. Y., Schulze, R. K., and Andersson, D. A. (2014). Anisotropic thermal conductivity in uranium dioxide. Nat. Commun. 5 (1), 1–7. doi:10.1038/ncomms5551
Harada, Y. (1997). UO2 sintering in controlled oxygen atmospheres of three-stage process. J. Nucl. Mater. 245 (2, 3), 217–223. doi:10.1016/S0022-3115(96)00755-6
Hastings, I. J. (1983). Effect of initial grain size on fission gas release from irradiated UO2 fuel. J. Am. Ceram. Soc. 66 (9), c150–c151. doi:10.1111/j.1151-2916.1983.tb10620.x
Janković, B., Adnađević, B., and Mentus, S. (2008). The kinetic study of temperature-programmed reduction of nickel oxide in hydrogen atmosphere. Chem. Eng. Sci. 63 (3), 567–575. doi:10.1016/j.ces.2007.09.043
Johnson, R. E., and Muan, A. (1968). Phase diagrams for the systems Si‐O and Cr‐O. J. Am. Ceram. Soc. 51 (8), 430–433. doi:10.1111/j.1151-2916.1968.tb11913.x
Kang, K. W., Yang, J. H., Kim, J. H., Rhee, Y. W., Kim, D. J., Kim, K. S., et al. (2010). Effects of MnO-Al2O3 on the grain growth and high-temperature deformation strain of UO2 fuel pellets. J. Nucl. Sci. Technol. 47 (3), 304–307. doi:10.1080/18811248.2010.9711958
Killeen, J. C. (1975). The effect of additives on the irradiation behaviour of UO2. J. Nucl. Mater. 58 (1), 39–46. doi:10.1016/0022-3115(75)90164-6
Klam, H. J., Hahn, H., and Gleiter, H. (1987). The thermal expansion of grain boundaries. Acta Metal. 35 (8), 2101–2104. doi:10.1016/0001-6160(87)90038-1
Kuri, G., Mieszczynski, C., Martin, M., Bertsch, J., Borca, C. N., and Delafoy, C. (2014). Local atomic structure of chromium bearing precipitates in chromia doped uranium dioxide investigated by combined micro-beam X-ray diffraction and absorption spectroscopy. J. Nucl. Mater. 449 (1–3), 158–167. doi:10.1016/j.jnucmat.2014.03.017
Lu, K., and Sui, M. L. (1995). Thermal expansion behaviors in nanocrystalline materials with a wide grain size range. Acta Mater. 43 (9), 3325–3332. doi:10.1016/0956-7151(95)00035-T
MacEwan, J. R., and Lawson, V. B. (1962). Grain growth in sintered uranium dioxide: II, columnar grain growth. J. Am. Ceram. Soc. 45 (1), 42–46. doi:10.1111/j.1151-2916.1962.tb11027.x
Martin, D. G. (1988). The thermal expansion of solid UO2 and (U, Pu) mixed oxides—a review and recommendations. J. Nucl. Mater. 152 (2–3), 94–101. doi:10.1016/0022-3115(88)90315-7
Matzke, H. (1983). Diffusion processes and surface effects in non-stoichiometric nuclear fuel oxides UO2+ x, and (U, Pu) O2±x. J. Nucl. Mater. 114 (2), 121–135. doi:10.1016/0022-3115(83)90249-0
Matzke, H. (1969). On uranium self-diffusion in uo2 and uo2+x. J. Nucl. Mater. 30 (1, 2), 26–35. doi:10.1016/0022-3115(69)90165-2
Mei, Z. G., Stan, M., and Yang, J. (2014). First-principles study of thermo-physical properties of uranium dioxide. J. Alloys Compd. 603, 282–286. doi:10.1016/j.jallcom.2014.03.091
Nichols, F. A. (1968). Further comments on the theory of grain growth in porous compacts. J. Am. Ceram. Soc. 51 (8), 468. doi:10.1111/j.1151-2916.1968.tb11924.x
Oh, J. S., Kim, D. J., Yang, J. H., Kim, K. S., Rhee, Y. W., and Koo, Y. H. (2014). Recycling process of U3O8 powder in MnO-Al2O3 doped large grain UO2 pellets. Nucl. Eng. Technol. 46 (1), 117–124. doi:10.5516/NET.07.2013.043
Ohse, R. W., Babelot, J. F., Cercignani, C., Hiernaut, J. P., Hoch, M., Hyland, G. J., et al. (1985). Equation of state of uranium oxide. J. Nucl. Mater. 130, 165–179. doi:10.1016/0022-3115(85)90305-8
Parker, F. J., and Rice, R. W. (1989). Correlation between grain size and thermal expansion for aluminum titanate materials. J. Am. Ceram. Soc. 72 (12), 2364–2366. doi:10.1111/j.1151-2916.1989.tb06091.x
Riglet-Martial, C., Martin, P., Testemale, D., Sabathier-Devals, C., Carlot, G., Matheron, P., and Largenton, R. (2014). Thermodynamics of chromium in UO2 fuel: a solubility model. J. Nucl. Mater. 447 (1–3), 63–72. doi:10.1016/j.jnucmat.2013.12.021
Sawbridge, P. T., Baker, C., Cornell, R. M., Jones, K. W., Reed, D., and Ainscough, J. B. (1980). The irradiation performance of magnesia-doped UO2 fuel. J. Nucl. Mater. 95 (1, 2), 119–128. doi:10.1016/0022-3115(80)90087-2
Singh, R. N. (1977). Isothermal grain-growth kinetics in sintered UO2 pellets. J. Nucl. Mater. 64 (1, 2), 174–178. doi:10.1016/0022-3115(77)90021-6
Song, K. W., Kim, S. H., Na, S. H., Lee, Y. W., and Yang, M. S. (1994). Effects of Nb2O5 addition on grain growth and densification in UO2 pellets under reducing and/or oxidizing atmospheres. J. Nucl. Mater. 209 (3), 280–285. doi:10.1016/0022-3115(94)90264-X
Turnbull, J. A. (1974). The effect of grain size on the swelling and gas release properties of UO2 during irradiation. J. Nucl. Mater. 50 (1), 62–68. doi:10.1016/0022-3115(74)90061-0
Une, K., Hirai, M., Nogita, K. A. A., Hosokawa, T., Suzawa, Y., Shimizu, S., et al. (2000). Rim structure formation and high burnup fuel behavior of large-grained UO2 fuels. J. Nucl. Mater. 278 (1), 54–63. doi:10.1016/S0022-3115(99)00214-7
Une, K., Kashibe, S., and Ito, K. (1993). Fission gas behavior during postirradiation annealing of large grained UO2 fuels irradiated to 23 GWd/t. J. Nucl. Sci. Technol. 30 (3), 221–231. doi:10.1080/18811248.1993.9734473
Yang, J. H., Kim, K. S., Nam, I. H., Oh, J. S., Kim, D. J., Rhee, Y. W., et al. (2012). Effect of step wise variation of oxygen potential during the isothermal sintering on the grain growth behavior in Cr2O3 doped UO2 pellets. J. Nucl. Mater. 429 (1–3), 25–33. doi:10.1016/j.jnucmat.2012.05.034
Keywords: large grain UO2, accident tolerant fuel, additive, atmosphere sintering, preparation process parameters
Citation: Zhong Y, Gao R, Li B, Yang Z, Huang Q, Wang Z, Duan L, Liu X, Chu M, Zhang P, Bai B, Wang Y, Cheng L, Yan B, Liu T and Li R (2021) Preparation and Characterization of Large Grain UO2 for Accident Tolerant Fuel. Front. Mater. 8:651074. doi: 10.3389/fmats.2021.651074
Received: 08 January 2021; Accepted: 08 February 2021;
Published: 06 April 2021.
Edited by:
Shiyu Du, Chinese Academy of Sciences, ChinaReviewed by:
Dewen Zhang, Xi'an Jiaotong University, ChinaLin Zhang, University of Science and Technology Beijing, China
Pengchao Kang, Harbin Institute of Technology, China
Copyright © 2021 Zhong, Gao, Li, Yang, Huang, Wang, Duan, Liu, Chu, Zhang, Bai, Wang, Cheng, Yan, Liu and Li. This is an open-access article distributed under the terms of the Creative Commons Attribution License (CC BY). The use, distribution or reproduction in other forums is permitted, provided the original author(s) and the copyright owner(s) are credited and that the original publication in this journal is cited, in accordance with accepted academic practice. No use, distribution or reproduction is permitted which does not comply with these terms.
*Correspondence: Zhenliang Yang, emhlbmxpYW5neWFuZ0AxNjMuY29t; Bin Bai, YmFpYmluOTA3QDE2My5jb20=