- 1Key Laboratory of Ministry of Education on Safe Mining of Deep Metal Mines, Northeastern University, Shenyang, China
- 2Department of Civil, Architectural and Environmental Engineering, Missouri University of Science and Technology, Rolla, MO, United States
- 3School of Resources and Civil Engineering, Northeastern University, Shenyang, China
- 4School of Civil Engineering, Southeast University, Nanjing, China
Coal gangue, which is the solid waste produced during the coal processing, causes serious environmental problems. Lightweight concrete by making use of the coal-gangue ceramsite as the aggregate has many advantages as the construction material. However, the high brittleness of lightweight aggregate concrete is one of the problems for its application in building infrastructure. In this paper, the variation regularity, influencing factors and reinforcing/toughening method were studied as the reference data for future practical applications of coal-gangue ceramsite lightweight aggregate concrete (CGCLWAC). The results show that the brittleness of CGCLWAC increases with age, but the rate of the increase of brittleness keeps decreasing, and the brittleness is basically stable when the age beyond 28 days. When the sand ratio is above 0.38, the brittleness of CGCLWAC increases with the sand ratio; when the water cement ratio is above 0.32, the brittleness increases with the decrease of the water-cement ratio. Experiments show that when the content of steel fibers is less than 1.5%, the brittleness decreases with the increase of steel fiber content; when the content of steel fibers exceeds a critical value, the toughening effect decreases. From the macro-destructive morphology of the specimens, it is concluded that the incorporation of steel fibers can significantly change the brittleness of CGCLWAC. This study can serve to provide reference data for making use of the solid waste of the coal gangue and optimizing the infrastructure application scheme of CGCLWAC.
Introduction
In current concrete industry, most aggregates and cement raw materials need to be obtained through the mining of rocks. The massive exploitation of natural resources such as aggregates and cement could cause serious large-scale deterioration of mountains and forests. For this reason, people are looking for lightweight aggregates (LWAs) produced by using industrial solid waste (e.g., gangue, fly ash and silica fume) as the main raw materials of concrete (Lv et al., 2015). This effort could not only reduce the disposal of industrial waste, but also decrease the overexploitation and deterioration of natural resources for aggregates (Shafigh et al., 2016).
Coal gangue is a solid waste that is separated during coal mining, washing, and processing. Due to the accumulation of a large amount of coal gangue and the failure to fully utilize or dispose it, it caused problems on the environment in the air pollution and water pollution, and triggered some geological disasters such as landslides and coal gangue debris flows. Fortunately, coal gangue can be made into LWA as coal-gangue ceramsite through different sintering processes; the ceramsite is a type of porous particles produced during the main process of high-temperature roasting of coal gangue (Figure 1A). Because these LWA are hard with low water absorption, they can be utilized to produce high strength coal-gangue ceramsite lightweight aggregate concrete (CGCLWAC). It is not only economic and technically feasible to replace ordinary sands for the concrete industry, but it can also make use of mining wastes to eliminate potential waste hazards (Shafigh et al., 2014).
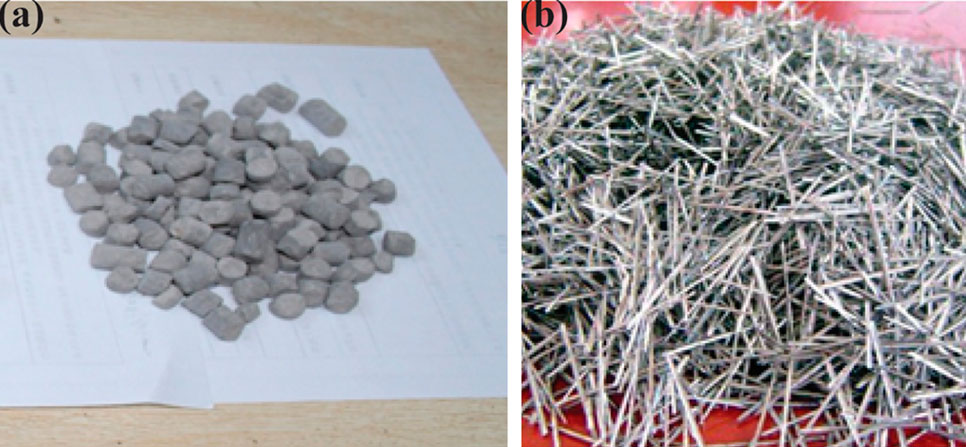
FIGURE 1. (A) Coal gangue ceramsite as lightweight aggregates, and (B) steel fibers used in this study.
Concrete made of LWA can significantly reduce the weight of structure at the same strength, and it also excels in special aspects such as heat insulation and corrosion resistance. High-strength lightweight aggregate concrete (LWAC) has outstanding advantages in economy, practicality, and technology (Chandra et al., 2003). LWAC is particularly attractive for its applications in offshore structures, high-rise buildings, and long-span bridges. The LWAC with high durability can reduce the density without sacrifice of the strength of concrete. These features of LWAC can result in cost-effective engineering solutions. In recent years, it becomes an important construction material for offshore infrastructures. These lead to the development of synthetic LWA (Fantilli et al., 2016). The synthetic LWA are mainly produced from volcanic sources of natural materials such as pumice and slag by mechanical treatment. They can also be produced by heat treatment of natural materials such as clay, slate, shale, or industrial by-products such as fly ash, slag, and sludge (Zhang and Poon, 2015).
In current structure design, both compressive strength and density of concrete are important design properties. The LWAC outperforms the conventional concrete in these properties. There are various types of LWAC with different mortar matrix and aggregate composition. Depending on the raw materials and technology used to make them, the properties of these concretes vary greatly. For each type of LWAC, different physical properties were tested as reference data for their potential practical applications. These tested properties include: strength (Cui et al., 2012a; Ilya et al., 2018; Medine et al., 2018), density (Lau et al., 2018), elasticity (Hilal et al., 2016), shrinkage (Alexandre Bogas et al., 2015; Rumšys et al., 2017), creep (Libre et al., 2011), thermal conductivity (Nguyen et al., 2017), abrasion resistance (Real and Bogas, 2017), and adsorption (Krc, 2015; Muñoz-Ruiperez et al., 2018). Although LWAC has its superiority in high strength and low density, LWAC has more obvious brittleness compared with other ordinary concretes, which can be partially attributed to its high strength (Beygi et al., 2014; Karamloo et al., 2016). The brittleness can cause expansion and growth of unstable cracks, which are difficult to control and repair. This brittleness bring a potential harm to engineering structures, especially those with seismic requirements. It could limit its wide applications in infrastructure building. It is found that the higher volume content of LWA in concrete mix results in a more brittle failure of LWAC (Cui et al., 2012a) and the magnetic water can also increase the compressive strength of LWAC (Salehi and Mazloom, 2019). For CGCLWAC, how to improve its ductility without a compensation of its strength is the current focus in the CGCLWAC performance study (Hassanpour et al., 2012). Before any industrial application, the factors affecting its brittleness still need special research. In this paper, the development of the brittleness of CGCLWAC with age is studied by measuring the compressive strength and splitting tensile strength at 3-days, 7-days, 14-days, 21-days, and 28-days, respectively. This provided the reliable basis and reference data for the estimation of the brittleness of CGCLWAC. While maintaining the other components unchanged, we studied the influence of sand ratio and water-cement ratio on the brittleness of CGCLWAC. This study can promote the application of coal gangue in quality control. At the reference mix ratio, steel fibers (Figure 1B) (Wang and Wang, 2013) with different volume fractions were mixed. The reinforcement and toughening effect of steel fibers on CGCLWAC were studied regarding the change of brittleness and damage morphology after applying the steel fibers. This study aims to provide testing reference data for making use of the solid waste of the coal gangue and optimizing infrastructure application scheme of CGCLWAC.
Materials and Experiment
Materials
In this paper, the LWA was the coal-gangue ceramsite manufactured by Chaoyang Hualong Kejian Co., Ltd. The cement was the P.S32.5R ordinary slag Portland cement produced by Liaoning Gongyuan Cement Co., Ltd. Ordinary sand was used with fineness modulus 2.6 and bulk density 1,349 kg/m3. The DC-WR1 naphthalene superplasticizer manufactured by Beijing Dechang Weiye Construction Engineering Technology Co., Ltd was used. When the dosage of the DC-WR1 naphthalene superplasticizer was between 0.5 and 1.0 wt%, the water reduction rate was between 12 and 20%. With this dosage, at the same water-cement ratio, the slump can be increased by more than 10 cm. Short steel fibers manufactured by Hebei Hengshui Advance Engineering Rubber & Plastics Co., Ltd were used with the length of 30–35 mm, the width of 1 mm, and the tensile strength of 400–600 MPa.
Chemical and Mineralogical Composition
Lightweight Aggregate
The main performance indices and particle gradation were tested. The results can be seen in Supplementary Tables S1, S2. The particle size gradation of the coal-gangue ceramsite belongs to 10–16 mm single particle size and meets the standard requirements.
Cement
The physical properties and chemical composition of CGCLWAC are given in Supplementary Tables S3, S4, respectively. The indicators of cement are in line with GB175-2007 (China standard) “General Portland cement” quality requirements and meet the test requirements.
Experiment Procedure
Lightweight Aggregate Concrete Mix Design
In the concrete mix design, we used the loose volume method, which was based on the dry bulk density. The dry mass of each component in the concrete of 1 m3 was designed by satisfying the bulk density of LWAC. The amount of cement shall be determined according to the bulk density of LWA and the compressive strength of the concrete to ensure that the concrete meets the design requirements. For the same raw material, if the bulk density does not meet the requirements, it can be achieved by adjusting the sand ratio. Through this adjustment, we made the concrete not only reach its designed compressive strength but also meet the requirements of bulk density. When calculating the amount of water, we used the effective water consumption and the additional water consumption as the total mixing water consumption, calculated the effective water-cement ratio by the total mixing water consumption, and then determined the compressive strength of the concrete from the effective water-cement ratio. In order to design CGCLWAC with compressive strength class of LC30, an initial mix ratio of the test was obtained firstly by referring to the design procedure of “Lightweight Aggregate Concrete Technical Regulations” (JGJ51-2002) (China stanadard), and the actual reference mix ratio as shown in Table 1 was obtained through multiple trial-and-error adjustments.
Coal-Gangue Ceramsite Lightweight Aggregate Concrete Specimen Preparation Process
Since the experiments were performed on CGCLWAC of which the mixing and forming processes were so different from that of common aggregate concrete, the only references were the “Lightweight aggregate concrete technical regulations” (JGJ51-2002) (China standard) and “Lightweight aggregate and Test Methods (GB/T17431.2-2010) (China standard). During the preparation process, we must consider the characteristics of strong water absorption of coal-gangue ceramsite, and also consider the floating phenomenon of aggregates that may occur during the vibrating process. Therefore, we first pre-wetted coal-gangue ceramsite for 1 h, and then drained the water before the coal gangue ceramsite was used. In accordance with the principle of first drying mix and then wetting mix to ensure the uniform dispersion of raw materials, the following procedure was determined after multiple trials: 1) mix cement, sand, coal-gangue ceramsite for 2 min under the dry condition; 2) add superplasticizer to the water and stir it for half minute; 3) add water to the dry material and stir it for 2 min; 4) put the prepared material into the mold and put it on the vibration table for 1–2 min; 5) after 24 h, demold and number the specimen made of the above steps, and then place them in a curing box filled with saturated Ca(OH)2 solution indoors until meeting the prescribed age. The size of the prepared specimen in this paper was 100 mm × 100 mm × 100 mm. The preparation procedure of CGCLWAC specimen is given in Figure 2.
Compressive Strength Test
This test uses NYL-200D pressure testing machine with the loading rate of 0.5–0.8 MPa per second. The compressive strength fcu of the CGCLWAC cube specimen can be calculated by using the following equation:
where P is the destructive load and S is bearing area of concrete cube specimen.
The fcu needs to be multiplied by the size conversion coefficient of 0.95 and converted to the compressive strength of a standard-sized concrete specimen
Tensile Strength Test
This test used NYL-200D pressure testing machine. First of all, in the middle of the test specimen, we drew the position line of the cleave plane which was perpendicular to the top surface of the specimen, put the steel pad and the plywood cushion on the bottom plate, placed the sample on the cushion, kept the center of the sample consistent with the center of the bottom plate, and placed the steel pad between the upper plate and the sample. We started the pressure testing machine and made the lower press surface slowly upwards. When the test specimen approached the upper plate, we adjusted the ball seat so that the upper plate and the test piece were in equal contact, and then continuously loaded at the loading speed of 0.05–0.08 MPa per second. When the deformation of the part approached the failure state, we stopped the throttle and continued load until the specimen was destroyed. The splitting tensile strength fts of CGCLWAC cube specimen can be calculated using the following equation:
The fts needs to be multiplied by the size conversion factor of 0.85 and converted to the splitting tensile strength of a standard-sized concrete specimen
Tensile-Compressive Strength Ratio Test Method
Due to the complexity of brittleness and lack of solid theory, there was no unified definition of brittleness index (Zhang et al., 2016; Xia et al., 2017). Different brittleness indices have been put forward in terms of energy, Young’s model, deformation and strength. In the practical use of concrete materials, tensile strength and compressive strength are parameters of concern, and they are also easy to obtain. Therefore, the tensile-compressive strength ratio recommended by GB/T 50081-2002 (China standard) was used as the indicator of the brittleness and inversely proportional to the brittleness index. In this test, the tensile-compressive strength ratio of CGCLWAC cubic specimen can be calculated using the following equation:
Results and Discussions
Compressive and Splitting Tensile Strength of Coal-Gangue Ceramsite Lightweight Aggregate Concrete in Different Ages
The raw materials described in Materials were used as raw materials for this test. Table 1 shows the mix ratio of CGCLWAC. Because of the time deviation, three batches of CGCLWAC test were manufactured and cured to five different ages (3-days, 7-days, 14-days, 21-days, 28-days). Three batches of each age were used for compression test.
From Figure 3A, it can be observed that the averaged compressive strength of three batches of CGCLWAC increases rapidly from 3 to 7 days. The growth rate of 7–14 days reaches 70% or even more. The growth rate of 14–21 days is basically the same as 7–14 days. The compressive strength of CGCLWAC has the least growth for 21–28 days. It meets the compressive strength standard of C30 (39–42 MPa).
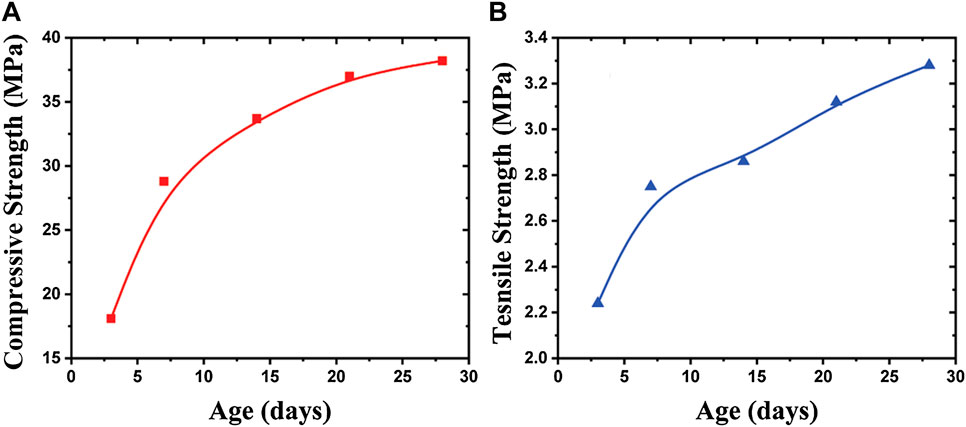
FIGURE 3. (A) Averaged compressive strength and (B) averaged splitting tensile strength of CGCLWAC in different ages. The raw data of tests are given in Supplementary Tables S5, S6.
The raw materials described in Materials were used as raw materials for this test. Table 1 shows the mix ratio of CGCLWAC. Because of the time deviation, three batches of CGCLWAC test were manufactured and cured to five different ages (3-days, 7-days, 14-days, 21-days, 28-days). Three batches of each age were used for splitting test.
From Figure 3B, it can be observed that the averaged splitting tensile strength of three batches of CGCLWAC increases rapidly from 3 to 7 days. The growth rate of 7–14 days reaches 60% or even more. The growth rate of 14–21 days is basically the same as 7–14 days. The splitting tensile strength of CGCLWAC has the least growth for 21–28 days. It is slightly lower than the tensile strength standard of C30 (3.7–4.2 MPa).
Tensile-Compressive Strength Ratio of Coal-Gangue Ceramsite Lightweight Aggregate Concrete in Different Ages
By using the test data of the compressive strength and splitting tensile strength of CGCLWAC, the brittleness of CGCLWAC of all ages was obtained as shown in Figure 4. The tensile-compressive strength ratio of CGCLWAC decreases with age. Therefore, the brittleness increases gradually, but the decreasing rate will become smaller and smaller until it approaches zero. The brittleness is basically stable when the age is about 28 days. The internal fractures and brittleness gradually increasing until 28 days later.
The tensile-compressive strength ratio of C30 ordinary aggregate concrete in 28 days is generally 0.09–0.11. Obviously, the brittleness of CGCLWAC is higher than that of ordinary aggregate concrete at the same strength level, and it is easier to break down suddenly without noticeable deformation.
It should be noted that our experimental observation about age effect is based on limited mixture portion for an explorative study purpose of CGCLWAC. More comprehensive study is needed in the future to make more generalized conclusions.
Influence of Sand Ratio on the Brittleness of Coal-Gangue Ceramsite Lightweight Aggregate Concrete
Keeping the total amount of cement, water, superplasticizer and coarse aggregate in Table 1 unchanged and changing the amount of sand and gangue ceramsite, CGCLWAC specimen were made with sand ratios of 0.38, 0.43, 0.48, and 0.53, respectively. After forming and curing to 28 days of age, their compressive strength, splitting tensile strength, and tension and compression were measured to calculate the tensile-compressive strength ratio shown as Figure 5.
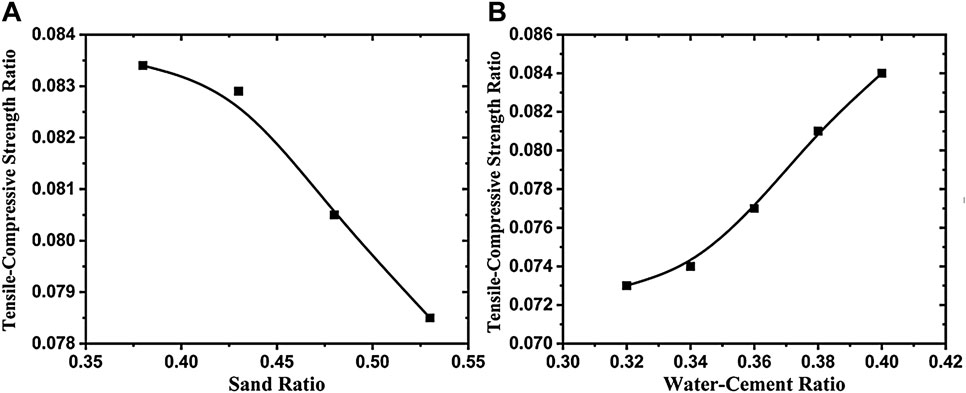
FIGURE 5. Effect of (A) sand ratio and (B) water-cement ratio on the tensile-compressive strength ratio.
From Figure 5A, it can be concluded that when the sand ratio is greater than 0.38, the ratio of tension and pressure of CGCLWAC decreases with the increase of sand ratio, and the rate of decrease is increasing. That is, when the sand ratio is bigger than 0.38, the brittleness of CGCLWAC increases with the sand ratio, and this increase becomes more and more obvious. This trend is contrary to that in article (Cui et al., 2012b). Ordinary sand is a mixture of different sizes of minerals formed by the weathering of rocks. The compressive strength of many rocks is generally above 100 MPa, which is higher than that of other concrete materials. Although the weathering process of rocks is accompanied by many physical and chemical changes, these changes turn the entire rock into many infinite individual small units, namely ordinary sand. These changes are only carried out between units. The end results of physical and chemical changes are the separation of these small units. Ultimately, these sands still retain most of the properties of the rock itself, such as higher strength. The increase in the content of such high-strength particles in CGCLWAC increases the compressive strength of the concrete, thereby affecting the brittleness of CGCLWAC.
Effect of Water-Cement Ratio on the Brittleness of Coal-Gangue Ceramsite Lightweight Aggregate Concrete
In order to study the effect of water-cement ratio change on the brittleness of CGCLWAC, the water consumption was changed, and the water-cement ratio was adjusted, while the cement dosage, coarse-grained aggregate amount, and water-reducing agent content in Table 1 were kept constant. With the water-cement ratio of 0.32, 0.34, 0.36, 0.38, and 0.40, their compressive and splitting tensile strengths were measured after forming and curing to 28-days age, so that their tensile-compressive strength ratio were calculated.
From Figure 5B, it can be concluded that when the water-cement ratio is above 0.32, the brittleness of CGCLWAC increases with the increase of water-cement ratio. In other words, the impact of water-cement ratio on the compressive strength is greater than that on the tensile strength. By taking into account of the brittleness of CGCLWAC, in actual production, the water-cement ratio can be increased as much as possible while satisfying the compressive strength of the concrete that is, increasing the water consumption of the concrete.
Results With Steel Fiber and Discussions
Brittleness of the Steel Fiber Reinforced Coal-Gangue Ceramsite Lightweight Aggregate Concrete
The raw materials listed in Materials were used as raw materials for this test, and Table 1 was used as the ratio of the raw materials. By adjusting the amount of steel fiber volume, CGCLWAC specimens were made with steel fiber content of 0, 0.5, 1.0, 1.5, and 2.0%, respectively. Their compressive and splitting tensile strengths were measured after forming and curing to 28-days age, so that its tensile-compressive strength ratio was calculated.
From Figure 6, based on current mixture portions, it can be concluded that when the steel fiber content is less than 1.5%, the brittleness of CGCLWAC decreases with the increase of the steel fiber content; and when the steel fiber content continues to increase beyond the maximum value, the brittleness improvement effect of CGCLWAC decreases. So, when using steel fiber reinforced and toughened CGCLWAC, the volume content of steel fiber was best controlled at about 1.5%.
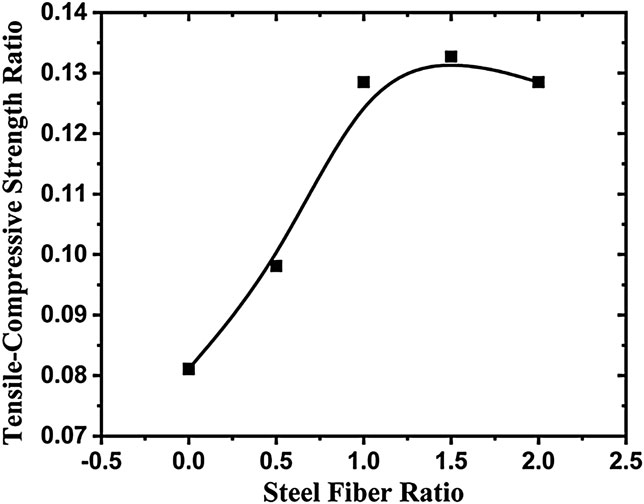
FIGURE 6. The relationship between tensile-compressive strength ratio of CGCLWAC and steel fiber content.
Discussions About Compressive Morphology Effect
From the comparison of Figure 7, it can be seen that the surface of the CGCLWAC without steel fiber is broken and fell off after the destruction, and the test specimen is seriously damaged. CGCLWAC with steel fiber was also damaged but not disintegrated after breaking, which indicates that the brittleness has significantly improved. Through the analysis of the development process of the cracking of the steel-fiber reinforced CGCLWAC, it was found that since the cracks first appeared inside the coal-gangue ceramsite and the steel fibers were parallel to the cracks, the steel fibers did not increase at the stage of stable. When the crack was extended to the cement mortar matrix, the steel fiber across the crack began to play its role to reduce the brittleness, and the crack propagation speed was slowed down. When the fracture system in the specimen became unstable and the specimen reached its maximum stress at the compressive strength, the crack rapidly expanded and the concrete specimen disintegrated and broke. Steel fibers across the cracks can effectively prevent the development of cracks and increase the toughness of the specimen. Finally, with the continuous increase of macro cracks, the steel fibers were gradually pulled out. It can be seen that the reinforcing and toughening effect of the steel fiber can only be achieved when the specimen is subjected to compressive load reaching its compressive strength, and the crack propagates into the cement mortar matrix. This is why the compressive strength of CGCLWAC is not improved after steel fiber is incorporated, but the brittleness of concrete is greatly improved.
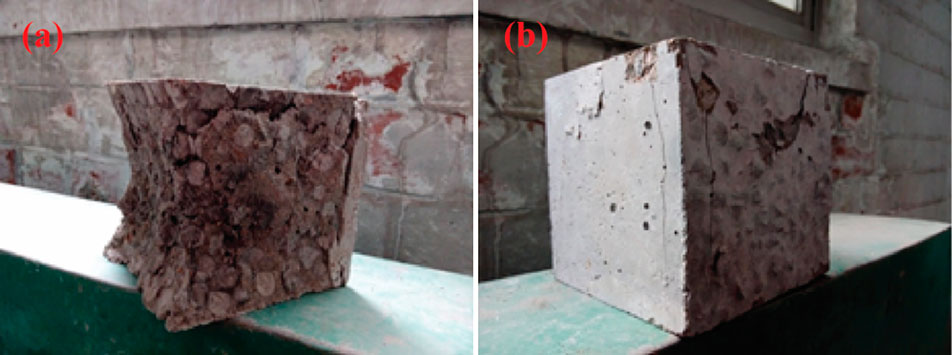
FIGURE 7. Compressive failure of (A) concrete without steel fiber and (B) concrete with steel fiber content of 1.5%.
Discussions About Splitting Tensile Damage Effect
The CGCLWAC without steel fiber was split into two halves along the splitting line when the splitting tensile strength was reached. The CGCLWAC mixed with the steel fiber reached the splitting tensile strength, and cracks appeared. However, the specimen was not substantially destroyed.
For CGCLWAC with steel fiber, when it is subjected to tensile stress, the steel fiber will bear tensile stress after the matrix in the tension zone cracks and keep the crack in the matrix slowly expanding, so that the matrix crack interface is also maintained with a certain amount of residual stress. As the crack expands, the residual stress between the cracks of the matrix decreases, and the steel fiber with a larger elastic modulus and deformability can continue to bear the tensile stress until the steel fiber is broken or pulled out. This process is gradually, so the steel fiber significantly enhances the toughness of the concrete. Because the steel fiber does more work in the process of damage, it effectively improves the brittleness characteristics of CGCLWAC. In addition, with the increase in the amount of steel fiber, the spacing of steel fibers will decrease. So the split tensile strength of CGCLWAC will continue to increase. However, it is worth noting that when the content of steel fiber is too high, the split tensile strength and the tensile-compressive strength ratio are reduced. This could be due to the excessive incorporation of steel fibers resulting in agglomeration, which affects the reinforcing and toughening effect on CGCLWAC.
Conclusions
In this paper, coal-gangue ceramsite was used as a coarse aggregate to replace light stone aggregates to prepare LWAC, and the brittleness of CGCLWAC and steel fiber reinforced toughening methods were studied. The brittle development law, influencing factors, and ways of improvement of CGCLWAC were studied through experiments, and the following main conclusions were obtained:
(1) The tensile-compressive strength ratio of CGCLWAC decreases with age, and brittleness increases gradually, but the decreasing rate becomes smaller and smaller until it approaches zero. That is, brittleness will increase with age until it becomes stable. When the age is about 28 days, the brittleness of CGCLWAC is basically stable. This is due in large part to the fact that as the age increases, the hydration reaction in CGCLWAC continues to proceed, with more and more internal fractures and brittleness gradually increasing until 28 days later. When the hydration reaction is almost complete, the internal defects of the concrete almost no longer increase, and the brittleness tends to become stable.
(2) Changes in sand and water-cement ratios can have a large impact on brittleness. When the sand ratio is above 0.38, the brittleness of CGCLWAC increases with the sand ratio; when the water cement ratio exceeds 0.32, the brittleness of CGCLWAC decreases with water-cement ratio increasing.
(3)Although steel fiber has little effect on the compressive strength of CGCLWAC, it has changed the form of compression failure and significantly improved the brittleness. When the content of steel fiber is less than 1.5%, the brittleness coefficient of CGCLWAC increases with the increase of steel fiber content, and the brittleness gradually decreases, which clearly reflects the enhanced toughening effect of steel fiber reinforced concrete. When the steel fiber content exceeds a certain value, the brittleness coefficient of CGCLWAC decreases with the increase of the steel fiber content, and the brittleness improvement effect decreases. To a large extent, the high fiber content of the fiber leads to fiber clumping and affects the mechanical properties of the concrete. When using steel fiber reinforced and toughened CGCLWAC, the steel fiber content is preferably kept at about 1.5%.
Data Availability Statement
The raw data supporting the conclusions of this article will be made available by the authors, without undue reservation.
Author Contributions
JQ and JL performed the experiments and collected the data. YW and WD analyzed data and wrote the paper. JX supervised the project. All authors read and approved the final manuscript.
Funding
This work was supported by the National Key R&D Program of China (2017YFC0602905, 2019YFC1907201), Fundamental Research Funds for the Central Universities (N150104007), the National Science and Technology Support Plan (2018YFC0604604), and Revitalization Talent Program (XLYC1805008).
Conflict of Interest
The authors declare that the research was conducted in the absence of any commercial or financial relationships that could be construed as a potential conflict of interest.
Supplementary Material
The Supplementary Material for this article can be found online at: https://www.frontiersin.org/articles/10.3389/fmats.2020.554718/full#supplementary-material
References
Alexandre Bogas, J., Gomes, M. G., Real, S. (2015). Capillary absorption of structural lightweight aggregate concrete. Mater. Struct. 48, 2869–2883. doi:10.1617/s11527-014-0364-x
Beygi, M. H. A., Kazemi, M. T., Nikbin, I. M., Vaseghi Amiri, J., Rabbanifar, S., Rahmani, E. (2014). The influence of coarse aggregate size and volume on the fracture behavior and brittleness of self-compacting concrete. Cement Concr. Res. 66, 75–90. doi:10.1016/j.cemconres.2014.06.008
Chandra, S., Berntsson, L., Ebrary, I. (2003). Lightweight aggregate concrete: science, technology, and applications. Norwich, NJ: Noyes Publications.
Cui, H. Z., Lo, T. Y., Memon, S. A., Xing, F., Shi, X. (2012a). Experimental investigation and development of analytical model for pre-peak stress-strain curve of structural lightweight aggregate concrete. Construct. Build. Mater. 36, 845–859. doi:10.1016/j.conbuildmat.2012.06.041
Cui, H. Z., Lo, T. Y., Memon, S. A., and Xu, W. (2012b). Effect of lightweight aggregates on the mechanical properties and brittleness of lightweight aggregate concrete. Construct. Build. Mater. 35, 149–158. doi:10.1016/j.conbuildmat.2012.02.053
Fantilli, A. P., Chiaia, B., and Gorino, A. (2016). Ecological and mechanical assessment of lightweight fiber-reinforced concrete made with rubber or expanded clay aggregates. Construct. Build. Mater. 127, 692–701. doi:10.1016/j.conbuildmat.2016.10.020
Hassanpour, M., Shafigh, P., and Mahmud, H. B. (2012). Lightweight aggregate concrete fiber reinforcement-a review. Construct. Build. Mater. 37, 452–461. doi:10.1016/j.conbuildmat.2012.07.071
Hilal, A. A., Thom, N. H., and Dawson, A. R. (2016). Failure mechanism of foamed concrete made with/without additives and lightweight aggregate. J. Adv. Concr. Technol. 14, 511–520. doi:10.3151/jact.14.511
Ilya, J., Farhani, I. N., and Mohd, A. N. (2018). Mechanical properties of lightweight concrete using recycled cement-sand brick as coarse aggregates replacement. E3S Web Conf. 34, 01029. doi:10.1051/e3sconf/20183401029
Karamloo, M., Mazloom, M., and Payganeh, G. (2016). Influences of water to cement ratio on brittleness and fracture parameters of self-compacting lightweight concrete. Eng. Fract. Mech. 168, 227–241. doi:10.1016/j.engfracmech.2016.09.011
Krc, K. (2015). An investigation of shear-friction of lightweight aggregate concretes. MS thesis. Rolla (MO): Missouri University of Science and Technology.
Lau, P. C., Teo, D. C. L., and Mannan, M. A. (2018). Mechanical, durability and microstructure properties of lightweight concrete using aggregate made from lime-treated sewage sludge and palm oil fuel ash. Construct. Build. Mater. 176, 24–34. doi:10.1016/j.conbuildmat.2018.04.179
Libre, N. A., Shekarchi, M., Mahoutian, M., and Soroushian, P. (2011). Mechanical properties of hybrid fiber reinforced lightweight aggregate concrete made with natural pumice. Construct. Build. Mater. 25, 2458–2464. doi:10.1016/j.conbuildmat.2010.11.058
Lv, J., Zhou, T., Du, Q., and Wu, H. (2015). Effects of rubber particles on mechanical properties of lightweight aggregate concrete. Construct. Build. Mater. 91, 145–149. doi:10.1016/j.conbuildmat.2015.05.038
Medine, M., Trouzine, H., José Barroso De, A., and Asroun, A. (2018). Durability properties of five years aged lightweight concretes containing rubber aggregates. Period. Polytech. Civ. Eng. 62, 386. doi:10.3311/PPci.11363
Muñoz-Ruiperez, C., Rodríguez, Á., Junco, C., Fiol, F., and Calderon, V. (2018). Durability of lightweight concrete made concurrently with waste aggregates and expanded clay. Struct. Concr. 19 (5), 1309–1317. doi:10.1002/suco.201700209
Nguyen, L. H., Beaucour, A. L., Ortola, S., and Noumowe, A. (2017). Experimental study on the thermal properties of lightweight aggregate concretes at different moisture contents and ambient temperatures. Construct. Build. Mater. 151, 720. doi:10.1016/j.conbuildmat.2017.06.087
Real, S., and Bogas, J. A. (2017). Oxygen permeability of structural lightweight aggregate concrete. Construct. Build. Mater. 137, 21–34. doi:10.1016/j.conbuildmat.2017.01.075
Rumšys, D., Bačinskas, D., and Spudulis, E. (2017). Mechanical properties of lightweight concrete produced with expanded glass aggregate. Moksl. Liet. Ateitis 9 (5), 500. doi:10.3846/mla.2017.1080
Salehi, H., and Mazloom, M. (2019). An experimental investigation on fracture parameters and brittleness of self-compacting lightweight concrete containing magnetic field treated water. Arch. Civ. Mech. Eng. 19 (3), 803–819. doi:10.1016/j.acme.2018.10.008
Shafigh, P., Mahmud, H. B., Jumaat, M. Z. B., Ahmmad, R., and Bahri, S. (2014). Structural lightweight aggregate concrete using two types of waste from the palm oil industry as aggregate. J. Clean. Prod. 80, 187–196. doi:10.1016/j.jclepro.2014.05.051
Shafigh, P., Nomeli, M. A., Alengaram, U. J., Mahmud, H. B., and Jumaat, M. Z. (2016). Engineering properties of lightweight aggregate concrete containing limestone powder and high volume fly ash. J. Clean. Prod. 135, 148–157. doi:10.1016/j.jclepro.2016.06.082
Wang, H. T., and Wang, L. C. (2013). Experimental study on static and dynamic mechanical properties of steel fiber reinforced lightweight aggregate concrete. Construct. Build. Mater. 38, 1146–1151. doi:10.1016/j.conbuildmat.2012.09.016
Xia, Y. J., Li, L. C., Tang, C. A., Li, X. Y., Ma, S., and Li, M. (2017). A new method to evaluate rock mass brittleness based on stress–strain curves of class I. Rock Mech. Rock Eng. 50 (5), 1123–1139. doi:10.1007/s00603-017-1174-6
Zhang, B., and Poon, C. S. (2015). Use of furnace bottom ash for producing lightweight aggregate concrete with thermal insulation properties. J. Clean. Prod. 99, 94–100. doi:10.1016/j.jclepro.2015.03.007
Keywords: coal-gangue ceramsite, lightweight aggregate concrete, brittleness, solid waste recycle, steel-fiber reinforced concrete
Citation: Wang Y, Qiu J, Deng W, Xing J and Liang J (2020) Factors Affecting Brittleness Behavior of Coal-Gangue Ceramsite Lightweight Aggregate Concrete. Front. Mater. 7:554718. doi: 10.3389/fmats.2020.554718
Received: 22 April 2020; Accepted: 31 August 2020;
Published: 28 September 2020.
Edited by:
Qian-Qian Yu, Tongji University, ChinaReviewed by:
Payam Shafigh, University of Malaya, MalaysiaAli Behnood, Purdue University, United States
Copyright © 2020 Wang, Qiu, Deng, Xing and Liang. This is an open-access article distributed under the terms of the Creative Commons Attribution License (CC BY). The use, distribution or reproduction in other forums is permitted, provided the original author(s) and the copyright owner(s) are credited and that the original publication in this journal is cited, in accordance with accepted academic practice. No use, distribution or reproduction is permitted which does not comply with these terms.
*Correspondence: Wen Deng, d2VuZGVuZ0Btc3QuZWR1