- Institute for Polymers and Composites (IPC), University of Minho, Guimarães, Portugal
This work aims at presenting a new strategy for the use of cork by-products on the development of sustainable composites with potential applications in rotational molding. In this study, different cork granulometries (0.15–3 mm) and matrix/cork ratios (90/10, 85/15, 80/20) are analyzed to access the processability of medium-density polyethylene (MDPE) with cork by rotational molding. The influence of processing parameters, such as the mold peak internal air temperature (PIAT) (200–240°C), is analyzed and correlated with the aesthetics, morphological and mechanical properties of the parts. The aim is to obtain a complete understanding of the processing–structure–property relationships. Defect-free parts are obtained with thin granulometric cork powders at a maximum of 10% by weight in PE/cork composites. The increase in cork content reduces the sintering capability and increases the porosity, wall thickness, and surface defects, simultaneously weakening the mechanical properties. The increase in PIAT favors a more compact structure and reveals better impact properties. All the parts are soft on touch and transmit the comfort and sensation of warm feeling of the cork. Moreover, lightweight parts and hydrophobic surfaces are achieved from the cork intrinsic properties. As a natural material, cork darkens its color with temperature, which is attributed to the reactions of the extractives within the components of cork, with no degradation associated. The work shows that polymer cork composites (CPC) are suitable for rotational molding within the processing window characteristic of PE, to achieve innovative and sustainable products with unique aesthetics and functionalities given by the cork material.
Introduction
Cork is a natural product obtained from the outer bark of an oak tree known botanically as Quercus suber L (Gibson et al., 1981). This material has a unique combination of properties such as low density, excellent acoustic and thermal properties, impermeability to liquids and gases, a high coefficient of friction, resilience, high energy absorption, excellent insulation properties, and a near-zero Poisson coefficient, which makes it an optimum material for a variety of applications (Fortes and Nogueira, 1989; Mano, 2002; Gibson, 2003). In addition, it is a natural, reusable, and renewable product and offers a unique look and touch which makes it difficult to be replaced by synthetic materials (Silva et al., 2005).
In terms of morphology, cork can be described as anisotropic material with thin-walled cells, regularly arranged without intercellular space. The cells are rectangular prisms like an alveolar structure and similar to a honeycomb, with their axes along the tree’s radial direction, stacked in columns (Pereira, 2007).
In cork, the structural components of cell wall are as follows: suberin, an aliphatic polyester (42%); lignin, an aromatic polymer (21,5%); polysaccharides, including cellulose and hemicelluloses (16%); extractives (13%); and ashes (7%) (Pereira, 1988). The cell wall of cork is chemically made up of two types of components: the structural components (suberin, lignin, and polysaccharides) build up the cell wall and define its structure; they are insoluble and cannot be removed from the cell wall without profoundly affecting the cell structure and properties; and the nonstructural components (extractives or inorganic minerals), either low-molecular organic compounds that may be solubilized by appropriate solvents (Pereira, 2007).
This cellular configuration has a strong influence on the mechanical properties of cork-based materials (Gibson, 2005). Castro et al. (2010) presented a compilation of the main mechanical properties of natural cork obtained from different experimental tests. They concluded that natural cork has a poor mechanical behavior when compared with other types of core materials for sandwich components of lightweight structures, such as synthetic foams. However, its low thermal conductivity combined with a reasonable compressive strength makes it an excellent material for thermal insulation purposes as well as for applications in which compressive loads are present.
From the reuse of by-products resulting from the transformation of cork, composites were created. Cork was incorporated into polymeric matrices, which allowed the combination of the ecological properties with the good mechanical performance of polymeric materials (Fernandes et al., 2011; Soares et al., 2011). The combination of cork with polymers through melt-based technologies brought added value to cork-based materials, promoting the development of a wide range of innovative applications.
Studies can be found on the combination of cork and cork by-products with polyolefins such as polyethylene (PE) and polypropylene (PP) (Fernandes et al., 2010) as well as biodegradable matrices such as PLA (Vilela et al., 2013). The effect of adding a coupling agent (Fernandes and Correlo, 2014) and chemical surface modification (Pereira and Velez Marques, 1988; Abenojar et al., 2014) was also studied to improve the compatibility and the mechanical properties. Fernandes et al. (2010) concluded that the mechanical performance of the composites decreased with the increase in cork content but increased with the introduction of coupling agents that promoted the adhesion between cork–polymer phases.
The structural properties of cork were found to be strongly dependent on temperature and may affect its color. A darkening effect was observed in samples treated at lower temperatures (150°C). The thermal decomposition of cork studied by thermogravimetry analysis has shown a mass decrease of about 30% upon heating at 300°C and less than 10% at 200°C (Rosa and Fortes, 1988a, b; Rosa and Fortes, 1988a, b; Şen et al., 2014). Therefore, the color changes observed at 150 and 200°C, when cork did not undergo significant chemical decomposition, were originated from extractives and hydrolyzed carbohydrates and their reactions with cork cell wall components particularly with cork lignin, while above 200°C it resulted from decomposition of hemicelluloses and formation of oxidation products. According to Pereira (2007), the cork extractives were the first to be volatized, hemicelluloses were the first structural components to be degraded, and lignin and suberin were the most stable components, therefore degraded at last.
Most of these studies were based on injection molding and extrusion processes for the production of cork-polymer materials and applications. There is no knowledge in the processing of this material by rotational molding. This technique is used to produce hollow parts for various applications like liquid storage tanks, containers, toys, indoor and outdoor furniture, and playgrounds, among other applications. The advantages are the production of stress-free parts; the low costs for tooling’s and molds; the little or no waste production; and the low restriction on mold design allowing the production of multilayer materials, especially when different compositions and thicknesses are required (Jansri and O-charoen, 2018; Fletes et al., 2020). This process is based on the rotation of polymeric powder material in an externally heated and cooled mold. Therefore, larger cycle times are involved compared to other plastic processing techniques such as injection molding or extrusion blow molding used to process similar parts (Crawford and Throne, 2002; Crawford and Kearns, 2003; Crawford and Gibson, 2012; Pereira, 2015; Nugent, 2017). Moreover, rotomolding is a challenge for several materials due to the possibility of thermo-oxidative degradation during processing, as a result of high temperature and large cycle time applied with impact on morphological and mechanical properties (Oliveira et al., 1996, 2007; Cramez et al., 2001). Due to that, this paper focuses on the processability of PE/cork by rotational molding and the relationship between material, processing, and product characteristics. The parts are characterized by aesthetic (color), chemical (evaluation of chemical composition), thermal (mass loss with temperature), physical (contact angles and density), morphological (microscopy), and mechanical (impact resistance) tests. The aim is to explore and characterize new materials to be used on the rotational molding process to produce differentiated new products with high value, sustainability, aesthetics, and functionality. This study is in line with other recently published articles in the finding of new materials for rotational molding (Greco et al., 2019; Vignali et al., 2019; Fletes et al., 2020).
Materials and Methods
Cork and Polymer Materials
Different cork powders and granules, from cork processing stages, were kindly supplied by Amorim Cork Composites, SA (Portugal). The polymer used in the preparation of the cork-based composites was medium-density polyethylene (MDPE) (Advancene EM-3405-UVH) with MFI of 5 g/10 min (190°C/2.16 kg) obtained from Ethydco (Egypt). The bulk density, particle size, and visual aspect of the cork are shown in Table 1 and Figure 1, respectively.
Compounding and Processing
Different cork powders were dry blended with MDPE in the proportions of 90/10, 85/15, and 80/20 wt% and processed by rotational molding. For each sample, 150 g of material was used. The oven was heated by electrical resistances and its temperature was set to 290°C. The peak internal air temperature inside the mold (PIAT) was set to 210°C, and it was monitored by a thermocouple placed inside the mold through the vent conduct during processing. Cooling by air was applied until the temperature inside the mold dropped to 60°C before demolding the parts.
In a second part of the study, there was a need to understand the influence of the processing conditions applied on the aesthetics and morphological and mechanical characteristics of the parts. Therefore, parts of MDPE with 10 wt% MF8 cork were produced with PIAT ranging from 185 to 235°C.
For the processing of the parts, a laboratory rotational molding equipment with characteristics of a Rock and Roll and Shuttle machine was used, with an aluminum mold with parallelepipedic dimensions of 140 × 90 × 90 mm and 5 mm of mold wall thickness. This is a prototype machine developed at the Department of Polymer Engineering at the University of Minho (Pontes et al., 2014). In this type of machine, the mold rotates 360° through the axis of the support arm and the oven performs a swinging motion (from 45° to 45° to the right to the left) perpendicular to the support arm, allowing the spreading of the material for the ends of the part. The rotation speed of the mold and the pendulum swing were 7 rpm and 1.5 rpm, respectively.
Color Determination
The aesthetic characteristics of the MDPE/cork parts were evaluated by visual inspection and by color measurements using a Spetro-Guide BYK portable colorimeter and a Shimadzu UV-2401PC reflectance spectrophotometer operating in the range of visible light between 380 to 740 nm with a 2 nm spectral resolution. The color parameters L, a, and b were determined according to the CIELab method. The system is based on the measurement of three coordinates: lightness L∗ between 0 (black) and 100 (white), a∗ representing red–green levels (+60 red, -60 green), and b∗ representing yellow–blue levels (+60 yellow, -60 blue). The color of a material is a mixture of these three parameters. The color variation was calculated according to the following formula (Bekhta and Niemz, 2003), where ΔL, Δa, and Δb correspond, respectively, to the variation of the coordinates L∗, a∗, and b∗ relative to the reference sample of a virgin cork powder.
Thermal Properties
The thermal stability studies determined by thermogravimetric analysis (TGA) were performed to understand the degradation characteristics of the cork powder and the CPCs using a TGA Q500 series thermogravimetric analyzer from TA Instruments. Experiments were performed in platinum pans, at a heating rate of 10°C/min from 40 to 800°C under air atmosphere with an air flow rate of 40 mL/min. This atmosphere was used to replicate the atmosphere condition inside the mold during the rotational molding process.
FTIR Analysis
To evaluate changes in the functional groups on the CPC after heating treatment, FTIR-ATR spectra were recorded using a MKII Golden Gate Single Reflection ATR System equipped with an ATR Golden Gate cell. Each spectrum was an average of 64 scans taken with 8 cm–1 resolution in the 4000–600 cm–1 range.
Contact Angles
Contact angle measurements of the parts were determined according to the standard D7334-08 using a DataPhysics Contact Angle System OCA-20. Distilled water was used for sample analysis, and the volume of the sessile drop on the top surface was maintained at 2 μL in all cases, using a micro-syringe. For accuracy, all measurements were performed right after deposition of the droplet and repeated 10 times on different pieces of the same sample.
Density
To determine the density of the parts, the samples were weighted in air and propanol according to the standard ISO 1183-1, Method A, using an OHAUS PioneerTM analytical balance equipped with a stationary support for the immersion vessel. The tested specimens were rectangular bars with 20 mm length and 10 mm width. Five specimens were tested for each sample.
Scanning Electron Microscopy
The morphology of the cork structure and the fracture of the CPC parts were analyzed using an ultra-high-resolution field-emission gun scanning electron microscope (FEG-SEM) (Nova 200 NanoSEM, FEI Company, at SEMAT, Guimarães, Portugal). Secondary electron images were performed with an acceleration voltage of 10 kV.
Prior to the morphological analyses, the samples were covered with a very thin film (20 nm) of Au–Pd (80–20 wt%), in a high-resolution sputter coater (208HR Cressington Company), coupled to a MTM-20 Cressington High Resolution Thickness Controller.
Mechanical Tests
The mechanical properties of the parts were determined by Izod and puncture impact tests. The Izod impact tests were performed according to the standard ISO 180 on a Ceast Resil Impactor instrument falling-weight impact tester with a pendulum energy of 7.5 J. The notched specimens were rectangular bars with 80 mm length and 10 mm width. Ten specimens were tested for each sample.
The puncture impact tests were performed according the standard ISO 6603-1:2000 and ISO 6603-2:2000 on a Ceast Fractovis Plus instrument falling-weight impact tester. All the specimens were subjected to the same energy level (147.5 J), with an impact velocity of 4.4 m/s resulting from a drop height of 1 m of a carriage of total mass of 3 kg. The tested specimens were squared with a 60 mm side. Ten specimens were tested for each sample.
Results and Discussion
Effect of Cork Powder Granulometry on Part Quality
Figure 2 and Table 2 depict the appearance of rotomolded parts produced with different granulometries and compositions of cork powders. The parts are soft on touch and transmit the sensation of comfort and warm feeling of the cork. This unique characteristic of natural cork material is maintained when CPC are processed by rotational molding. Parts processed by other plastic processing techniques like extrusion or injection molding lose this property as plastic shiny look and plastic touch are obtained.
Several difficulties were encountered in the attempt to process good-quality parts when using MDPE/cork of big particle size (0.5/1 and 2/3 mm) (Figure 2). The apparent density of these materials prevents their easy fitting on the mold cavity and facilitates the appearance of defects such as incomplete parts at the corner and heterogeneous surfaces due to the poor mixing, phase separation of polymer/cork, and lack of polymer wetting.
Parts of good quality were obtained using fine cork powders (Table 2). However, the increase in cork percentage resulted in the reduction of the sintering capability of the composite material increasing its porosity, wall thickness, and surface defects. These effects were more pronounced for MF5 than for MF8, given its difference in the powder size and powder characteristics as revealed by SEM images (Figure 3). MF5 powder particles are larger in size (<0.6 mm) and form a well-defined honeycomb cellular structure, whereas MF8 was grinded to a much smaller particle size (<0.15 mm) resulting in almost individual cells.
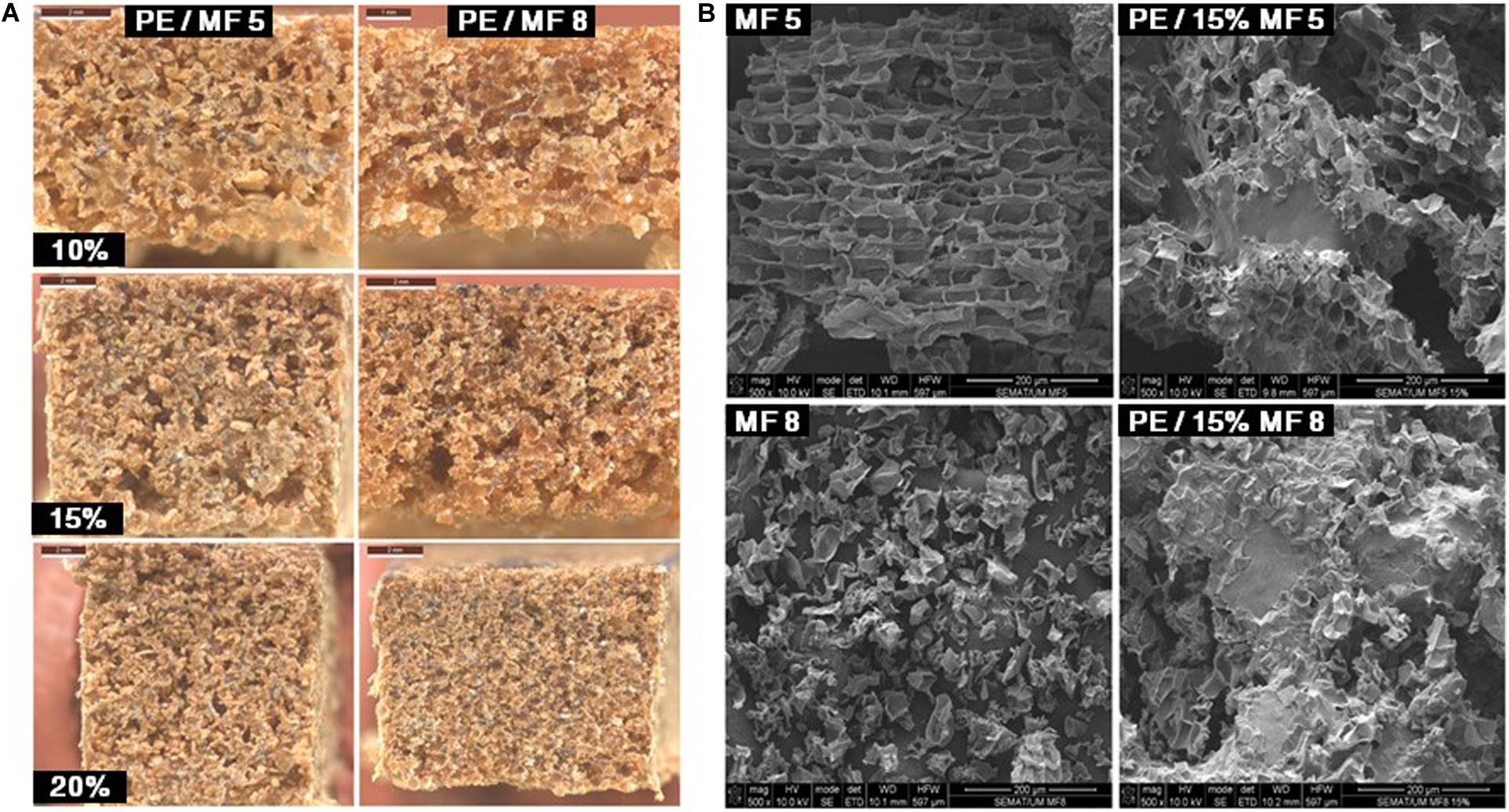
Figure 3. Effect of MDPE/cork composition on the structure of the parts. (A) Images obtained by optical magnification of the cross section along the wall thickness. (B) Images obtained by SEM analysis of MF5 and MF8 cork powder and its MDPE/cork composites.
In terms of processing, rotational molding is defined by the rotation of the material inside the mold that is only subjected to a thermal environment and free coalescence of the particles; therefore, sintering is favored for MDPE/MF8. This result reveals that MF8 cork powder has the preferred material characteristics for the production of CPC by this processing technique.
Effect of Mold Internal Air Temperature
Rotomolding is a challenge for several materials due to the possibility of thermo-oxidative degradation during processing. Since cork is prone to color and structural changes at high temperatures, a study was carried out on the effect of mold internal air temperature (IAT) on the properties of MDPE/10 wt% MF8.
The processing cycle, generally monitored by the changes in the internal air temperature of the mold with time, is shown in Figure 4A. The incorporation of cork material has an important influence on the processing cycle when compared to MDPE. The difference starts at the moment of melting and adhesion of the PE particles to the mold surface (plateau observed between 110 and 150°C). In the case of PE/cork, there is a significant delay on that process, which also delays the rapid increase in the temperature inside the mold observed when all the material reaches the molten state and adheres completely to the mold surface (cooking stage of the material). Once the setup PIAT is reached, the mold is transferred to the cooling chamber. The temperature drops, and a small plateau occurs due to the crystallization process. It follows the solidification of the material until the part is demolded. The difference in the processing cycle of both materials is justified by the lower thermal conductivity of cork material (0.039–0.045 W/mK) as compared to PE (0.32–0.40 W/mK) (Hansen and Bernier, 1972; Silva et al., 2005; Gil, 2007). Therefore, the heat transferred from the mold to the particles is delayed by the presence of cork that affects not only the melt of the material (observed by the delay on reaching the PIAT) but also the transferring of the heat trapped inside the mold during cooling, leading to an overshooting of temperature and longer cycle times. It is important to note that both samples were transferred to the cooling chamber at the same time, corresponding to the abrupt drop of the oven temperature. While MDPE starts the cooling phase, MDPE/cork temperature is still rising, delaying for some minutes the cooling of the material.
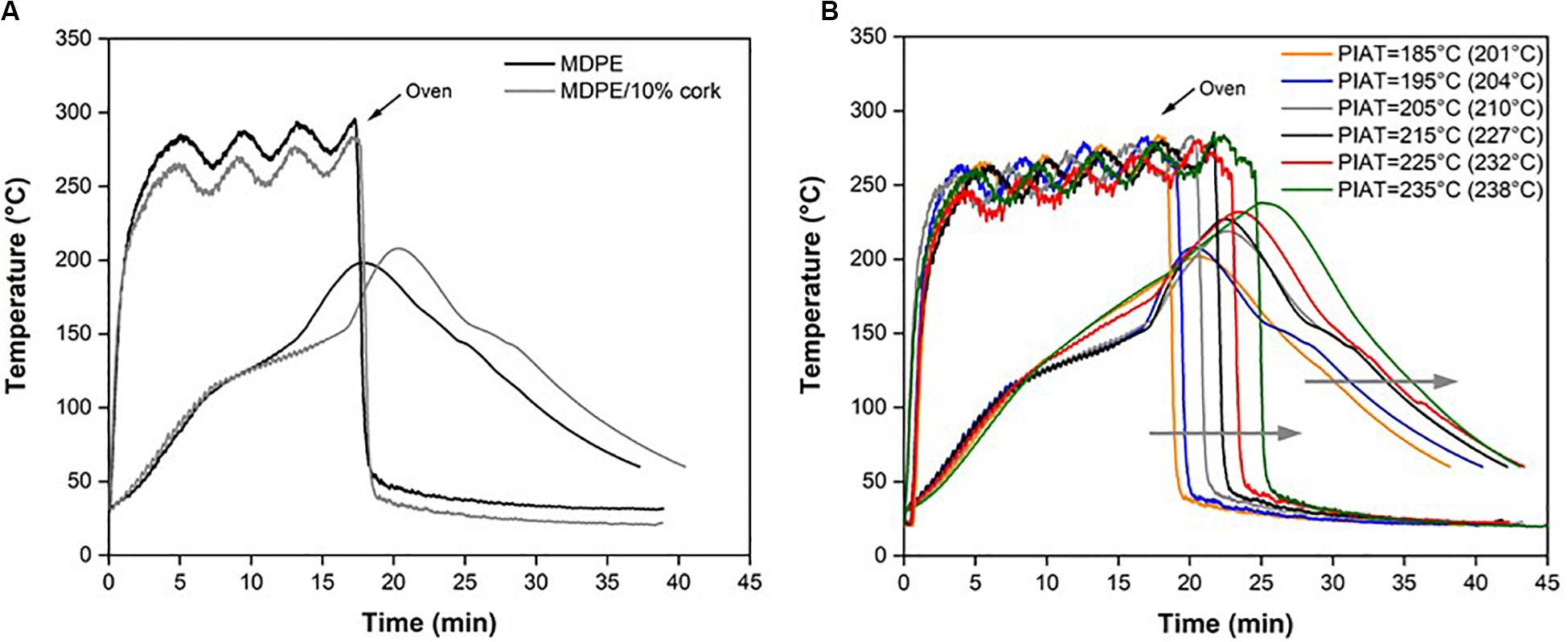
Figure 4. Mold internal air temperature profiles during the rotational molding process of (A) MDPE and MDPE/10% cork parts and (B) MDPE/10% cork parts processed at different IAT. The arrow indicates the direction of increase in the IAT setup used for processing the parts.
The effect of mold temperature, namely, the PIAT, on the cycle time is depicted in Figure 4B. As observed, the higher the temperature at which the parts are processed, the longer it takes to reach PIAT and the longer is the cycle time. The shortest cycle time recorded for PIAT of 185°C (real PIAT of 201°C due to overshooting) was about 38 min, whereas the longest cycle time recorded for PIAT of 235°C (real PIAT of 238°C) was about 43 min. The variations in the mold internal air temperature can be directly related to the materials and processing conditions and are very sensitive to differentiate between the samples as reported in other studies (Cramez et al., 2002; Ramkumar et al., 2014).
Table 3 depicts the image of parts obtained at each PIAT and its effect on the color parameters in comparison to natural cork. The repeatability of part production is observed most of the time, with the darkening of the color with the increase in PIAT being clear. This is observed by the lightness parameter, ΔL, whose values change from 22.4 to 35.1. The total color difference, ΔE, follows this trend by increasing steadily with the increase in PIAT (22.5–37.6).
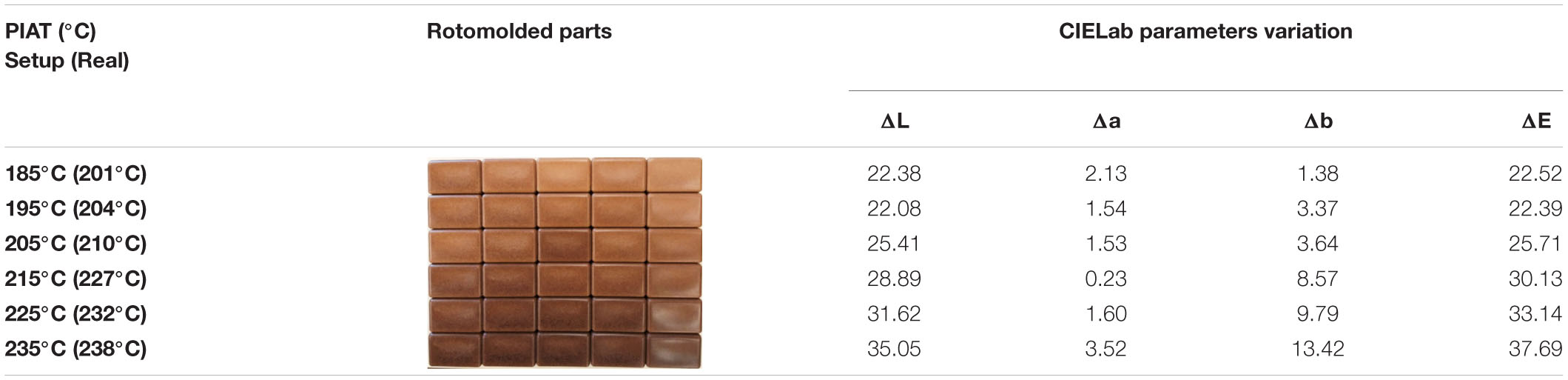
Table 3. Repeatability studies of MDPE/10% MF8 cork parts at different processing temperatures and CIELab color parameter variations in relation to the neat cork powder.
The effect caused by the processing at high temperatures is a decrease in lightness, which means the parts are darker than the parts processed at the lowest temperatures. These results are in agreement with the findings obtained using Q. cerris cork (Şen et al., 2012). The authors found that the change in color at low temperatures (150°C) can occur even if there is no significant chemical decomposition of cork as a result of the reactions between extractives and hydrolyzed carbohydrates with cork cell wall components particularly with lignin. Above 200°C, decomposition of hemicelluloses may occur and the formation of oxidation products contributes to the color change of the cork. Further details are given in the following sections.
From now on the real PIAT is described on the figures and tables, and the data discussed according to real PIAT.
Evaluation of Cork by Thermal Analysis
Thermogravimetry analysis (TGA) of neat cork material was carried out to understand the thermodegradation behavior of cork and to identify the temperatures at which the main chemical processes occur. TGA was carried under air atmosphere to evaluate the thermal stability of cork at high temperature and to have a similar environment as that occurring inside the mold during processing. The TGA/DTG curves for cork are presented in Figure 5.
Four regions can be identified in the thermogravimetric curves. The cork powder shows an initial region of mass loss between room temperature and 100°C corresponding to the elimination of water. However, water is only completely eliminated at 200°C, corresponding to 1% of mass loss. The second region of the curve, between 200 and 350°C and about 500°C, is characterized by a rapid mass loss. The first peak (351.8°C) corresponds to polysaccharides composed of cellulose and hemicellulose that have degradation temperatures in the range between 300 and 400°C (Silva et al., 2005; Kim et al., 2006; Wei et al., 2013). Suberin and lignin also contribute to this reaction but with smaller magnitudes. It is at this peak that the greatest loss of mass is found, which indicates that the reactions that contribute to the first exothermal peak are those that induce the darkening of the samples and that there is no further color change with the subsequent reactions (Şen et al., 2014). Lignin and suberin are relatively more thermal stable components when compared to polysaccharides and extractives, which means these components contribute mainly to the second reaction (455.5°C) in cork. Hence, the color changes in cork are the result of hemicellulose decomposition and formation of oxidation products. In the final region, above about 500°C, the rate of mass loss is lower until the cork reduces to ashes (about 3.79% by weight).
Furthermore, the loss mass at 250°C was 6% and at 300°C was less than 30%. The thermal degradation of cork, in air atmosphere, starts at 258.4°C. This suggests that the cork powder can be processed at temperatures lower than 250°C without induced irreversible changes in cork chemical composition, and it can also be processed with polymers having processing temperatures lower than this value, such as the case of polyethylene.
Evaluation of Cork Structural Changes by FTIR Analysis
Figure 6 shows the FTIR spectrum of cork powder, MDPE powder, and MDPE/10% cork produced at 238°C. Natural cork powder was subjected to a heat treatment of 48 h at 255°C in an oven prior to FTIR so that color and possible structural changes could be identified and compared to the material changes occurring during the rotational molding process.
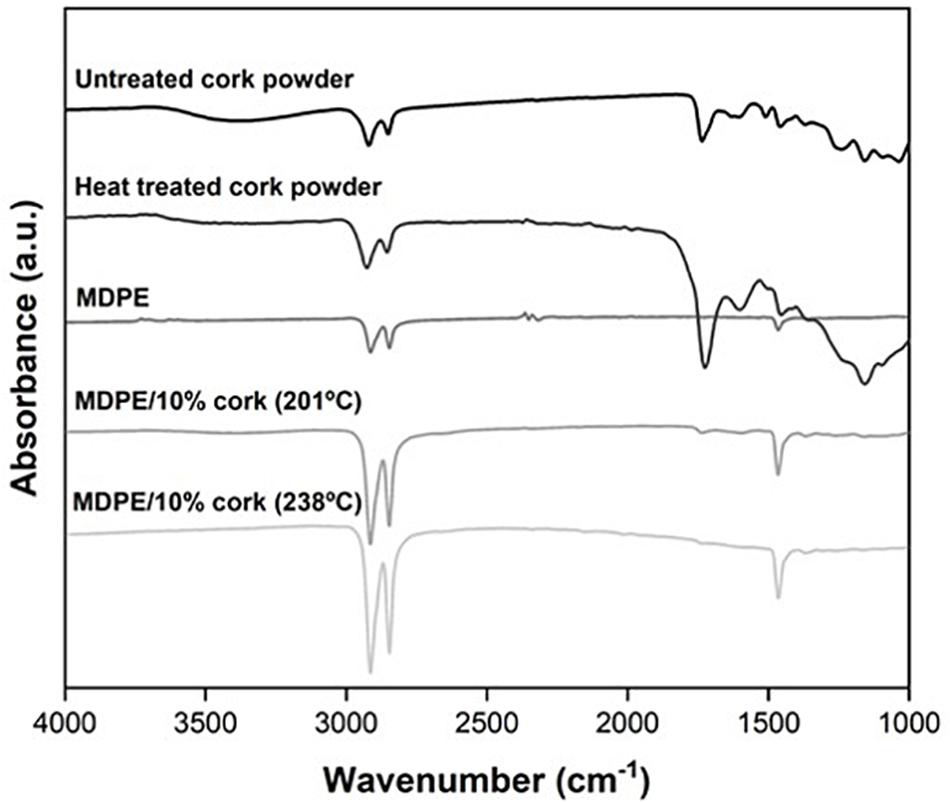
Figure 6. FTIR spectrum for untreated cork powder, heat-treated cork powder for 48 h in the oven at 255°C, virgin MDPE and MDPE/10% cork part processed at 238°C.
The FTIR spectrum of cork powder before heat treatment shows a band between 3600 and 3200 cm–1, assigned to the O–H vibration from carbohydrates and lignin (Şen et al., 2012). The spectrum is dominated by the absorbance bands of suberin: two peaks at 2920 and 2847 cm–1, corresponding to the asymmetric and symmetric vibration, respectively, of C–H in the olefinic chains and an intense band at 1732 cm–1 corresponding to the carbonyl C = O in aliphatic acids and esters (Pereira, 2007). The band at 1128 cm–1 can also be attributed to the C–O–C of the ester group in suberin. Suberin also contributes to the 1242 cm–1 peak corresponding to the C–O stretch, through the epoxide group (Fernandes et al., 2014). The band at approximately 1466 cm–1 is typical for lignin, and the peaks at 1087 and 1035 cm–1 correspond to the C–O bond and are characteristic of polysaccharides (cellulose and hemicelluloses) (Abenojar et al., 2014).
The comparison of the FTIR spectrum of cork powder, before and after heat treatment, confirmed the occurrence of chemical modifications. The largest modification in the chemical composition of cork observed in the FTIR spectrum was the substantial intensity reduction in the O–H (3600–3200 cm–1) with temperature and treatment time. This means that carbohydrate content reduced substantially with temperature, and carbohydrate is the most heat-sensitive component of cork. Thus, temperature-induced alterations in the chemical composition of the components are condensation of carbohydrate products with suberin in the lower temperature range and heavy condensation of all remaining components at higher temperatures.
The FTIR spectrum of a CPC sample produced at 238°C and the pure materials (cork and MDPE) show significant differences in the absorption patterns. The absorption of the C–O band between 1030 and 1000 cm–1 and the O–H band between 3600 and 3200 cm–1, corresponding to O–H stretching, decreased after heating, indicating the loss of polysaccharides and condensation of lignin side chains with phenyl nuclei. The bands at 3000 and 2800 cm–1 did not decrease by heating, indicating the stability of suberin in these conditions. In addition, these bands are more pronounced in the CPC sample because MDPE is composed of long chains of C–H and due to the presence of C–H in cork from suberin. The band at 1466 cm–1, corresponding to the vibration of aromatic ring of lignin increased by heating, indicating the stability of lignin in these conditions (Dekier, 2012). The results are in agreement with findings by Pereira (1992, 2007), Şen et al. (2012), and Fernandes et al. (2014).
Effect of PIAT on the Contact Angles of Parts
The purpose of the contact angle tests was to study the wettability of MDPE as compared to MDPE/cork parts. Figure 7 shows the measurement of the contact angles and the drop plain view digital image taken right after the sessile drop test.
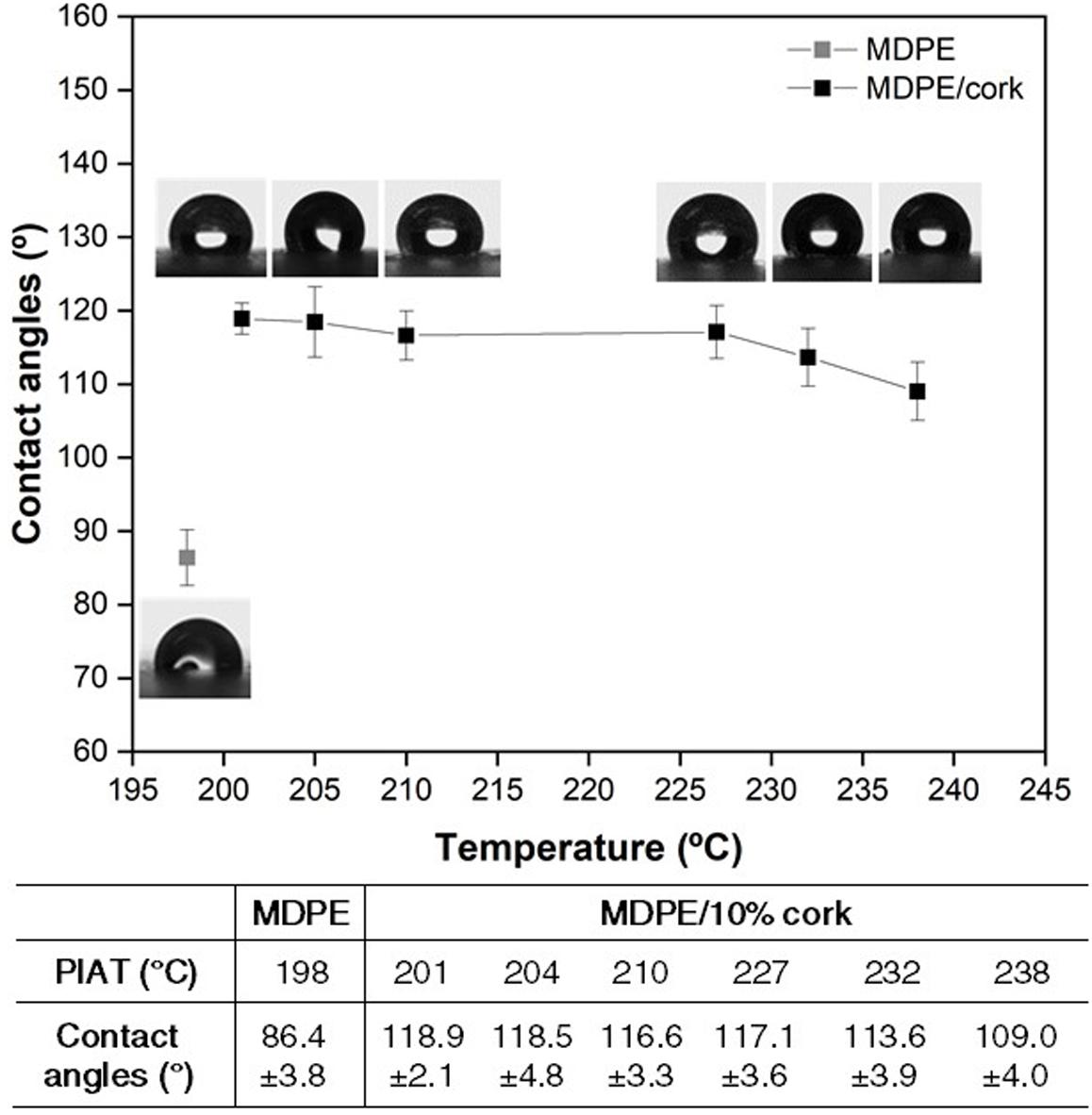
Figure 7. Contact angles between a drop of water and the surface of virgin MDPE and MDPE/10% cork parts.
The MDPE part has a contact angle of 86°, which is close to the value reported in the literature (Subedi, 2011). The incorporation of cork results in the increase in the contact angle to values above 100°. This proves that the liquid does not wet the surface, and therefore, there is a more pronounced hydrophobic and impermeable behavior of the parts with the incorporation of cork. In fact, cork is impermeable to liquids and gases, because its cell walls are closed and essentially composed of suberin, which is a hydrophobic component (Abenojar et al., 2014).
With the increase in PIAT, there is a decrease in the contact angle between the drop and the surface of the parts. At 201°C, the contact angle was 118.9° and at the highest temperature of 238°C was 109°, however, the parts still have a hydrophobic character. This result reveals that the surface of the part changes with the processing cycle applied, namely, the PIAT. The increase in PIAT leads to a slight decrease in the contact angle, which may indicate a better wettability of the cork powder by the polymer with the increase in temperature and a transition of parts with a touch of cork to a more plastic touch. This characteristic allows the liquid to have a better tendency to wet the surface, and consequently, there is a decrease in the contact angle.
Morphology of CPC Parts
The morphology of the impact-fracture surface of MDPE/10%MF8 at different processing temperatures was evaluated by SEM (Figure 8). The first observation is that all the parts are very porous, but there seems to be evidence of good interfacial adhesion between the two components, as cork powder particles are embedded in the thermoplastic matrix. According to the micrographs, the peculiar morphology of the cork was maintained after compounding and processing (compare to Figure 3B – MF8). The increase in processing temperature favors a better sintering of materials reducing the porosity level of the part.
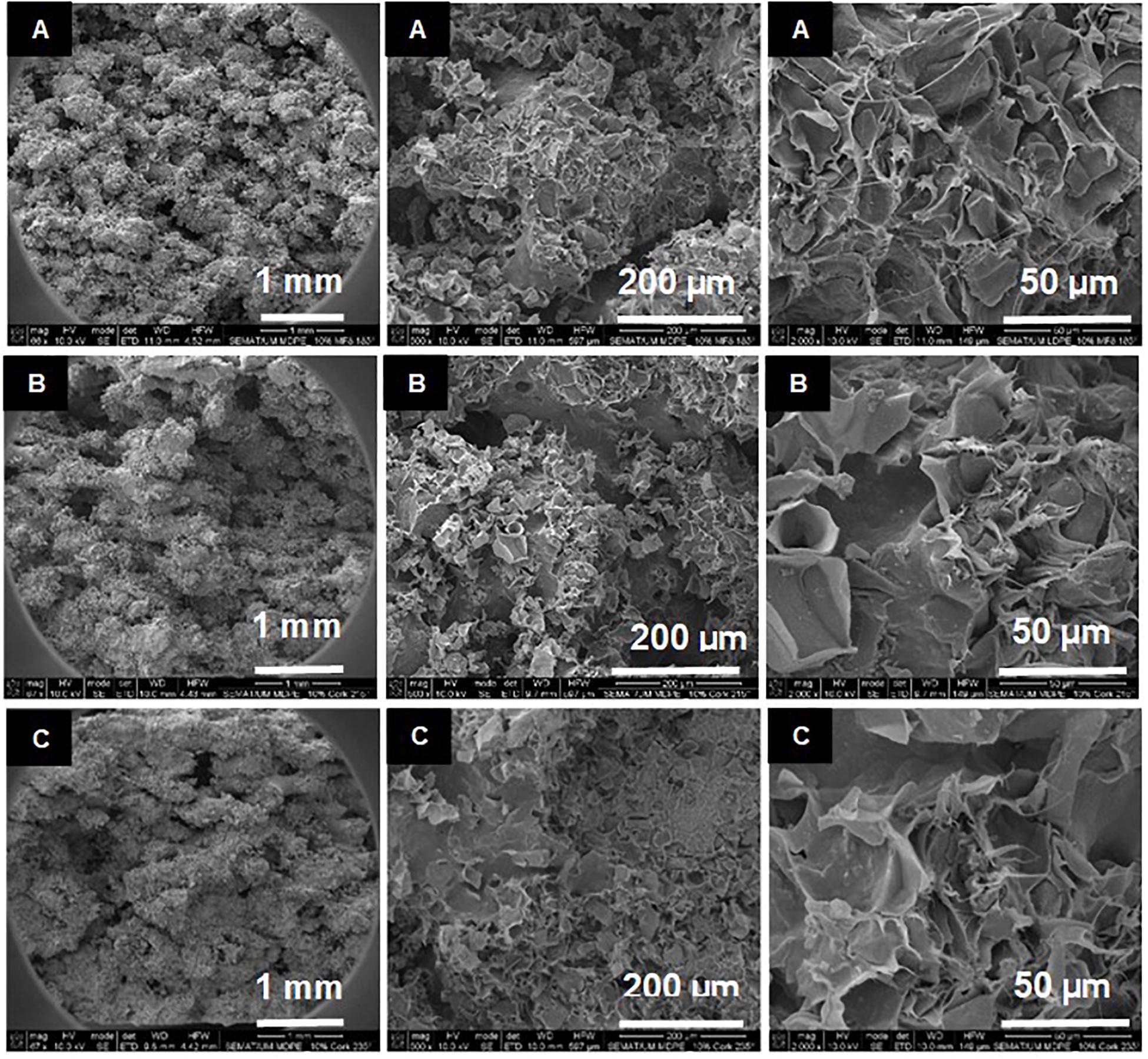
Figure 8. Morphology of the impact–fracture surface of MDPE/10% cork produced at (A) 201°C, (B) 227°C, and (C) 238°C.
Mechanical Properties of Parts
Impact strength results are shown in Figure 9. It can be seen that the impact strength decreased greatly with the addition of 10% of cork powder (1.83 kJ/m2) compared with neat MDPE (12.30 kJ/m2). This tendency is mostly related to the presence of voids and porous structure observed (see Figure 3), which contributes to stress concentration points and a weak ability to transfer energy between materials. Previous studies (Xu and Crawford, 1993; Oliveira et al., 1996, 2007; Pick and Harkin-Jones, 2004) reported a correlation between the number of voids and the impact strength in rotational molded parts; the greater the number of voids, the lower the impact resistance. Moreover, according to Oliveira et al. (2007) and Ramkumar et al. (2016), there is a processing window that maximizes the mechanical properties as a result of better sintering (reduction of voids) and the absence of thermal degradation of the polymer matrix. In the present study, cork hinders the formation of a well-compacted structure, as observed previously by SEM. Nevertheless, CPC parts increase their impact strength from PIAT at 201 to 238°C. This result can be attributed to the diminishing of voids and the building up of a more compact structure at higher PIATs. This means that the composites can absorb more energy and, consequently, their mechanical properties are improved.
Puncture impact tests are depicted in Figure 10. The results indicate that MDPE and MDPE/10% cork parts exhibit a quite different failure and deformation behavior. While MDPE suffers a ductile fracture, the CPC parts fracture in a fragile way, as observed by the images of the fracture surfaces presented in Figure 10C.
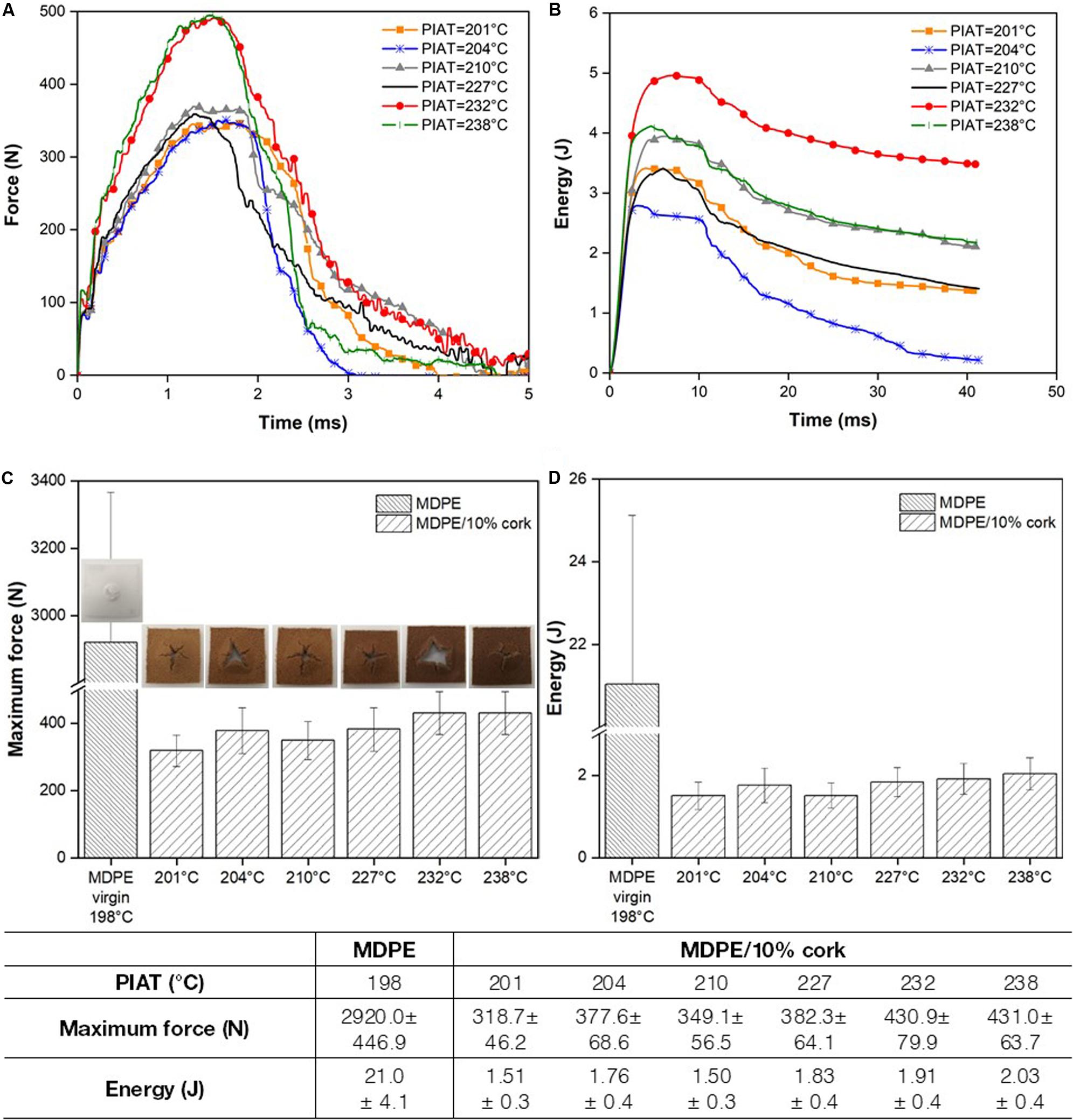
Figure 10. Effect of PIAT on the impact behavior of MDPE and MDPE/10% cork parts. (A) Force over time; (B) Energy over time; (C) Maximum force as a function of PIAT and related samples fracture surfaces; (D) Energy at maximum force as a function of PIAT.
The maximum contact force between the impactor and specimen and the absorbed energy in the crushing process were determined for all the impact tests carried (Figures 10C,D). The reduction in the puncture impact behavior of the CPC compared to MDPE is clear. In the force–time curves, MDPE samples got to a maximum load peak around 2900 N, while all the samples with cork present values between 300 and 450 N (decrease up to 84%). Thus, the use of cork affects the maximum allowed loads related to impact. These values (in terms of percentage) are similar to those obtained by other authors working with fibers in rotomolding, where reductions up to 90% in impact properties were reported (Torres and Aragon, 2006; Yuan et al., 2007; Ortega et al., 2013; Cisneros-López et al., 2017).
With the increase in temperature (PIAT), there is a tendency for the maximum force to be higher and the curve to be more extensive over time, which indicates that energy absorption is achieved in a longer period of time. This can prevent the appearance of undesirable fracture accelerations resulting from the impact.
Regarding the energy curves, it can also be seen that upon CPC reaching the maximum of absorbed energy, the curve tends to show a negative slope. Thus, in CPC parts there is a slight tendency to increase the strength supported by the sample before fracture and the absorbed energy with the increase in PIAT. Due to the heterogeneity of the samples, the fluctuations in the force and energy absorbed from the materials are expected.
Density of Parts
The density of the parts is shown in Table 4 and reveals a significant decrease with the addition of 10% of cork powder (0.909 g/cm3) as compared to neat MDPE (0.924 g/cm3). This result is expected given the difference in the density of both materials, namely, cork (0.11–0.25 g/cm3) (Anjos et al., 2014) and MDPE (0.934 g/cm3) (Datasheet of Medium Density Polyethylene, 2016), and the fact that the amount of polymer in the composite was reduced.
Cork is composed of closed cells with a gas similar to the air inside, which promotes a decrease in the density of the parts in which the cork is incorporated (Gul et al., 2013). With the increase in PIAT, it seems to have a slight decrease in density of the parts. The values may vary due to the heterogeneity of the samples.
Relationship Between Processing–Morphological–Properties of Parts
Figure 11 summarizes the relationship between processing, morphology, and properties of the PE/cork parts obtained by rotational molding. The mechanical properties of CPC parts are greatly affected when compared to pure PE, because the sintering ability of PE material becomes more difficult in the presence of cork, resulting in a high level of porosity and voids. This changes the fracture behavior of PE from ductile to fragile behavior. The increase in processing temperature (seen by the PIAT) results in a more compact structure, improving the mechanical properties of the composite. It also influences the appearance of the final parts, by the darkening of the color with the increase in PIAT. No significant chemical degradation of the cork structural components occurs during processing at these temperatures; therefore, the hydrophobic character of the surface of the parts is achieved and maintained during processing. It is important to notice that the parts preserve the texture and soft touch of the cork natural material, although its color depends greatly on the processing conditions used.
Despite the decrease in the mechanical properties of the PE/cork composite parts produced by rotational molding, there are some benefits to be pointed out, namely, the aesthetics of cork, touch (soft and warm feeling), the hydrophobicity of the surface, and the lightness of the final part. Therefore, different functionalities can be achieved by using PE/cork composites on the production of parts by rotational molding.
Conclusion
The rotational molding of PE/cork composites was investigated to understand the relationship between processing, morphology, and characteristics of the parts. The effect of cork powder granulometry (0.15–2/3 mm), the composition of MDPE/cork (10–15–20 wt% cork), and processing window (200–240°C) were analyzed. Good-quality parts were obtained by rotomolding using fine cork powders (<0.6 mm particle size) and a maximum of 10 of cork by weight. The increase of cork reduced the sintering capability of the materials, increasing part porosity, wall thickness, and surface defects. These effects were more pronounced in MF5 (<0.6 mm, honeycomb cellular structure) than for MF8 (<0.15 mm, individual cells), given its difference in size and morphological characteristics. Part defects such as incomplete parts at the corns and heterogeneous surfaces due to poor mixing and lack of polymer wetting were observed for large particle sizes. These results allow the selection of MF8 cork as the preferred material for the composition of PE/cork composites.
Cork characteristics such as soft touch and warm feeling were obtained regardless of the processing conditions applied. However, the brownish tone, typical of cork, gradually became darker with the increase in processing temperature. The color change was due to the reaction of the extractives within the components of the cork cell wall, and not by degradation of cork, indicating that a typical processing window for rotomolding of PE can be adopted for MDPE/cork composites. Higher temperatures favor the sintering of the PE material and the construction of a more compact structure, which in turn results in the improvement of the impact properties (from 318.69 N at 201°C to 430.98 N at 238°C). Nevertheless, virgin PE parts have a ductile behavior and absorb seven times more energy than PE/cork parts.
This work presents a different strategy for the upgrading of cork by-product (cork powder) and simultaneously the development of sustainable composites with potential applications in rotational molding. This processing technique allows the cork characteristics to be preserved in the processing window typical for PE, giving rise to products with lightweight, unique visual appearance, soft touch, sensation of comfort, and warm feeling of cork.
Data Availability Statement
The datasets generated for this study are available on request to the corresponding author.
Author Contributions
CM was the scientific mentor of the work, conceiving and designing the experiments. VG performed the experimental work and analyses of results. CM and VG analyzed the data and wrote the manuscript. Both authors have read and agreed to the published version of the manuscript.
Funding
The authors acknowledge the financial support of the Project RoTMI-Rotomolding Technology and Materials Innovations (POCI-01-0247-FEDER-33095), cofinanced by the European Regional Development Fund (FEDER) through the Operational Program for Competitiveness and Internationalization (POCI) under the “Portugal 2020” framework. IPC acknowledges the support of the Portuguese Foundation for Science and Technology (FCT) through the National Funds References UIDB/05256/2020 and UIDP/05256/2020.
Conflict of Interest
The authors declare that the research was conducted in the absence of any commercial or financial relationships that could be construed as a potential conflict of interest.
References
Abenojar, J., Barbosa, A. Q., Ballesteros, Y., Del Real, J. C., Da Silva, L. F. M., and Martínez, M. A. (2014). Effect of surface treatments on natural cork: surface energy, adhesion, and acoustic insulation. Wood Sci. Technol. 48, 207–224. doi: 10.1007/s00226-013-0599-7
Anjos, O., Rodrigues, C., Morais, J., and Pereira, H. (2014). Effect of density on the compression behaviour of cork. Mater. Des. 53, 1089–1096. doi: 10.1016/j.matdes.2013.07.038
Bekhta, P., and Niemz, P. (2003). Effect of high temperature on the change in color, dimensional stability and mechanical properties of spruce wood. Holzforschung 57, 539–546. doi: 10.1515/HF.2003.080
Castro, O., Silva, J. M., Devezas, T., Silva, A., and Gil, L. (2010). Cork agglomerates as an ideal core material in lightweight structures. Mater. Des. 31, 425–432. doi: 10.1016/j.matdes.2009.05.039
Cisneros-López, E. O., González-López, M. E., Pérez-Fonseca, A. A., González-Núñez, R., Rodrigue, D., and Robledo-Ortíz, J. R. (2017). Effect of fiber content and surface treatment on the mechanical properties of natural fiber composites produced by rotomolding. Compos. Interfaces 24, 35–53. doi: 10.1080/09276440.2016.1184556
Cramez, M. C., Oliveira, M. J., and Crawford, R. J. (2001). Effect of nucleating agents and cooling rate on the microstructure and properties of a rotational moulding grade of polypropylene. J. Mater. Sci. 36, 2151–2161. doi: 10.1023/A:1017583731513
Cramez, M. C., Oliveira, M. J., and Crawford, R. J. (2002). Optimisation of rotational moulding of polyethylene by predicting antioxidant consumption. Polym. Degrad. Stab. 75, 321–327. doi: 10.1016/S0141-3910(01)00234-8
Crawford, R. J., and Gibson, S. (2012). Rotational molding: some basics. Pop. Plast. Packag. 10, 26–28.
Crawford, R. J., and Kearns, M. P. (2003). Practical Guide to Rotational Moulding. Akron: Rapra Technology Ltd.
Crawford, R. J., and Throne, J. L. (2002). Rotational Molding Technology. New York, NY: William Andrew Publishing.
Datasheet of Medium Density Polyethylene (2016). Datasheet of Advancene EM-3405-UVH Medium Density Polyethylene (MDPE). Alexandria: Unipol Pe Technology.
Dekier, Ł (2012). The origins and evolution of lean management system. J. Int. Stud. 5, 46–51. doi: 10.14254/2071-8330.2012/5-1/6
Fernandes, E. M., Aroso, I. M., Mano, J. F., Covas, J. A., and Reis, R. L. (2014). Functionalized cork-polymer composites (CPC) by reactive extrusion using suberin and lignin from cork as coupling agents. Compos. Part B Eng. 67, 371–380. doi: 10.1016/j.compositesb.2014.07.028
Fernandes, E. M., and Correlo, V. M. (2014). Polypropylene-based cork-polymer composites: processing parameters and properties. Compos. Part B Eng. 66, 210–223. doi: 10.1016/j.compositesb.2014.05.019
Fernandes, E. M., Correlo, V. M., Chagas, J. A. M., Mano, J. F., and Reis, R. L. (2010). Cork based composites using polyolefin’s as matrix: morphology and mechanical performance. Compos. Sci. Technol. 70, 2310–2318. doi: 10.1016/j.compscitech.2010.09.010
Fernandes, E. M., Correlo, V. M., Chagas, J. A. M., Mano, J. F., and Reis, R. L. (2011). Properties of new cork-polymer composites: advantages and drawbacks as compared with commercially available fibreboard materials. Compos. Struct. 93, 3120–3129. doi: 10.1016/j.compstruct.2011.06.020
Fletes, R. C. V., López, E. O. C., Sánchez, F. J. M., Mendizábal, E., Núñez, R. G., Rodrigue, D., et al. (2020). Morphological and mechanical properties of bilayers wood-plastic composites and foams obtained by rotational molding. Polymers 12, 1–19. doi: 10.3390/polym12030503
Fortes, M. A., and Nogueira, M. T. (1989). The poisson efect in cork. Mater. Sci. Eng. A 122, 227–232.
Gibson, L., Easterling, K., and Ashby, M. (1981). The structure and mechanics of cork. Proc. R. Soc. London A 377, 99–117. doi: 10.1007/s10853-011-5914-9
Gibson, L. J. (2005). Biomechanics of cellular solids. J. Biomech. 38, 377–399. doi: 10.1016/j.jbiomech.2004.09.027
Gil, L. (2007). Cork as a building material Technical Manual. Santa Maria de Lamas: APCOR-Associação Portuguesa de Cortiça.
Greco, A., Ferrari, F., Buccoliero, M. G., and Trono, G. (2019). Thermal and mechanical analysis of polyethylene homo-composites processed by rotational molding. Polymers 11:528. doi: 10.3390/polym11030528
Gul, J., Saleemi, A. R., Mirza, S., Feroze, N., Mansha, M., Gul, J., et al. (2013). Thermal and mechanical characteristics of cork filled insulation for aerospace applications. Plast. Rubber Compos. 39, 28–32. doi: 10.1179/174328910X12608851832010
Hansen, D., and Bernier, G. A. (1972). Thermal conductivity of polyethylene: the effects of crystal size, density and orientation on the thermal conductivity. Polym. Eng. Sci. 12, 204–208. doi: 10.1002/pen.760120308
Jansri, E., and O-charoen, N. (2018). Polypropylene / polyethylene two-layered by one-step rotational molding. J. Polym. Eng. 38, 685–694. doi: 10.1515/polyeng-2017-0367
Kim, H. S., Kim, S., Kim, H. J., and Yang, H. S. (2006). Thermal properties of bio-flour-filled polyolefin composites with different compatibilizing agent type and content. Thermochim. Acta 451, 181–188. doi: 10.1016/j.tca.2006.09.013
Mano, J. F. (2002). The viscoelastic properties of cork. J. Mater. Sci. 37, 257–263. doi: 10.1023/A:1013635809035
Nugent, P. (2017). “Rotational Molding,” in Applied Plastics Engineering Handbook: Processing, Materials, and Applications, ed. M. Kutz (Reading, PA: Elsevier).
Oliveira, M. J., Cramez, M. C., and Crawford, R. J. (1996). Structure-property relationships in rotationally moulded polyethylene. J. Eng. Appl. Sci. 2, 2096–2099. doi: 10.1007/BF01152932
Oliveira, M. J., Cramez, M. C., Oliveira, M. J., and Cramez, M. C. (2007). Rotational molding of polyolefins: processing, morphology and properties. J. Macromol. Sci. Part B 40, 457–471. doi: 10.1081/MB-100106170
Ortega, Z., Monzón, M. D., Benítez, A. N., Kearns, M., McCourt, M., and Hornsby, P. R. (2013). Banana and abaca fiber-reinforced plastic composites obtained by rotational molding process. Mater. Manuf. Process. 28, 879–883. doi: 10.1080/10426914.2013.792431
Pereira, H. (1988). Chemical composition and variability of cork from Quercus suber L. Wood Sci.Technol. 218, 211–218. doi: 10.1007/bf00386015
Pereira, H., and Velez Marques, A. (1988). The effect of chemical treatments on the cellular structure of cork. IAWA J. 9, 337–345. doi: 10.1163/22941932-90001093
Pick, L. T., and Harkin-Jones, E. (2006). Effect of mould pressurisation on impact strength of rotationally moulded polyethylenes. Plast. Rubber Compos. 35, 324–330. doi: 10.1179/174328906X143868
Pontes, A. J., Ferreira, E. C., Mendes, J., Fonseca, J., Cramez, M. C., and Pouzada, A. S. (2014). Inovação na moldação por injeção. Rev. da Cefanol Assoc. Nac. da Indúst. Moldes 103, 23–29.
Ramkumar, P. L., Kulkarni, D. M., and Chaudhari, V. V. (2014). Parametric and mechanical characterization of linear low density polyethylene (LLDPE) using rotational moulding technology. Sadhana 39, 625–635. doi: 10.1007/s12046-013-0223-4
Ramkumar, P. L., Waigaonkar, S. D., and Kulkarni, D. M. (2016). Effect of oven residence time on mechanical properties in rotomoulding of LLDPE. Sadhana 41, 571–582. doi: 10.1007/s12046-016-0489-4
Rosa, M. E., and Fortes, M. A. (1988a). Temperature-induced alterations of the structure and mechanical properties of cork. Mater. Sci. Eng. 100, 69–78. doi: 10.1016/0025-5416(88)90240-6
Rosa, M. E., and Fortes, M. A. (1988b). Termogravimetric analysis of cork. J. Mater. Sci. Lett. 7, 1064–1065. doi: 10.1007/BF00720828
Şen, A., Marques, A. V., Gominho, J., and Pereira, H. (2012). Study of thermochemical treatments of cork in the 150-400°C range using colour analysis and FTIR spectroscopy. Ind. Crops Prod. 38, 132–138. doi: 10.1016/j.indcrop.2012.01.018
Şen, A., Van Den Bulcke, J., Defoirdt, N., Van Acker, J., and Pereira, H. (2014). Thermal behaviour of cork and cork components. Thermochim. Acta 582, 94–100. doi: 10.1016/j.tca.2014.03.007
Silva, M. D., Oleskovicz, M., and Coury, D. V. (2005). Cork: properties, capabilities and applications. Control. y Autom. 16, 345–358. doi: 10.1179/174328005X41168
Soares, B., Reis, L., and Sousa, L. (2011). Cork composites and their role in sustainable development. Procedia Eng. 10, 3214–3329. doi: 10.1016/j.proeng.2011.04.531
Subedi, D. P. (2011). Contact angle measurement for the surface characterization of solids. Himal. Phys. 2, 1–4. doi: 10.3126/hj.v2i2.5201
Torres, F. G., and Aragon, C. L. (2006). Final product testing of rotational moulded natural fibre-reinforced polyethylene. Polym. Test. 25, 568–577. doi: 10.1016/j.polymertesting.2006.03.010
Vignali, A., Iannace, S., Falcone, G., Utzeri, R., Stagnaro, P., and Bertini, F. (2019). Lightweight poly(ε-caprolactone) composites with surface modified hollow glass microspheres for use in rotational molding: thermal, rheological and mechanical properties. Polymers 11:624. doi: 10.3390/polym11040624
Vilela, C., Sousa, A. F., Freire, C. S. R., Silvestre, A. J. D., and Pascoal Neto, C. (2013). Novel sustainable composites prepared from cork residues and biopolymers. Biomass Bioenergy 55, 148–155. doi: 10.1016/j.biombioe.2013.01.029
Wei, L., McDonald, A. G., Freitag, C., and Morrell, J. J. (2013). Effects of wood fiber esterification on properties, weatherability and biodurability of wood plastic composites. Polym. Degrad. Stab. 98, 1348–1361. doi: 10.1016/j.polymdegradstab.2013.03.027
Xu, L., and Crawford, R. J. (1993). Analysis of the formation and removal of gas bubbles in rotationally moulded thermoplastics. J. Mater. Sci. 28, 2067–2074. doi: 10.1007/BF00367563
Keywords: rotational molding, cork-polymer-composites, cork, polyethylene, thermal properties, morphology, mechanical properties
Citation: Martins CI and Gil V (2020) Processing–Structure–Properties of Cork Polymer Composites. Front. Mater. 7:297. doi: 10.3389/fmats.2020.00297
Received: 13 June 2020; Accepted: 10 August 2020;
Published: 25 September 2020.
Edited by:
Jacqueline Anne Johnson, University of Tennessee Space Institute (UTSI), United StatesReviewed by:
Veronique Michaud, École Polytechnique Fédérale de Lausanne, SwitzerlandLiqing Wei, United States Forest Service (USDA), United States
Copyright © 2020 Martins and Gil. This is an open-access article distributed under the terms of the Creative Commons Attribution License (CC BY). The use, distribution or reproduction in other forums is permitted, provided the original author(s) and the copyright owner(s) are credited and that the original publication in this journal is cited, in accordance with accepted academic practice. No use, distribution or reproduction is permitted which does not comply with these terms.
*Correspondence: Carla I. Martins, Y21hcnRpbnNAZGVwLnVtaW5oby5wdA==