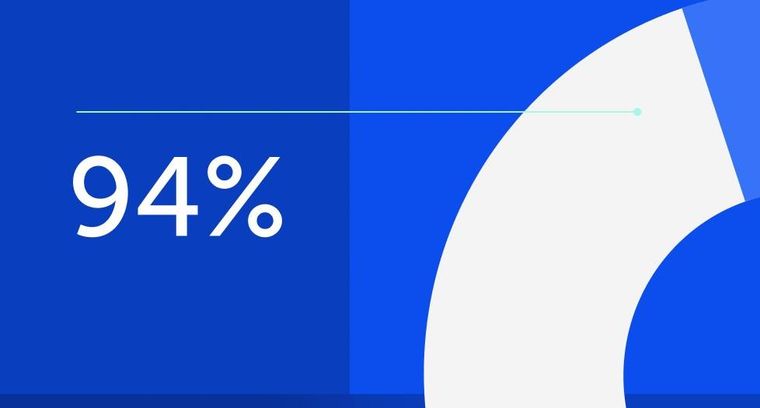
94% of researchers rate our articles as excellent or good
Learn more about the work of our research integrity team to safeguard the quality of each article we publish.
Find out more
ORIGINAL RESEARCH article
Front. Mater., 11 September 2020
Sec. Polymeric and Composite Materials
Volume 7 - 2020 | https://doi.org/10.3389/fmats.2020.00293
This article is part of the Research TopicFlame-Retardant Polymeric Materials and Polymer CompositesView all 9 articles
Spiro-phosphorus (P)-based reactive flame retardant (SPDPT), a novel reactive flame-retardant epoxy resin (EP) curing agent, was prepared through the one-pot synthesis of triacetonediamine, pentaerythritol, and P oxychloride. The successful preparation of SPDPT was confirmed through Fourier-transform infrared (FTIR) spectroscopy, 1H NMR spectroscopy, 31P NMR spectroscopy, and elemental analysis. The flame-retardant epoxy thermoset [e.g., EP/4′4-diaminodiphenyl sulfone (DDS)/SPDPT] was prepared by using DDS as the co-curing agent. Differential scanning calorimetry (DSC) results show that SPDPT can cure EP. Thermogravimetric analysis (TGA) results show that improve the carbon residue yield of the epoxy thermoset after burning. When the P content was 1.0 wt%, the limiting oxygen index value of the EP/DDS/SPDPT-4 sample was 26.4%, and UL94 reached the V-0 rating. The tensile property of the epoxy thermoset reached 37.20 MPa, the flexural property reached 63.82 MPa, and the impact property reached 21.57 KJ⋅m–2.
Epoxy resin (EP) boasts merits, such as excellent adhesion, strong mechanical strength, low shrinkage, good electrical insulation, and outstanding corrosion resistance (Huo et al., 2019; Luo et al., 2019), and has been widely applied in various industries, such as coating, adhesive, aerospace material, and substrate material (Perret et al., 2011a,b; Qiu et al., 2016; Mestry and Mhaske, 2019; Zhang et al., 2019). However, flammability has been one of the major limiting factors of EP applications (Huo et al., 2016; Lin et al., 2016). Therefore, the flame retardancy of EP composites has been investigated widely (Shi et al., 2017; Xu et al., 2019; Chu et al., 2020; Ding et al., 2020). In the past few years, researchers have strove to improve the flame retardancy of EP by introducing DOPO (9,10-dihydro-9-oxa-10-phosphaphenanthrene-10-oxide) -based flame retardants (Luo et al., 2015; Zhang et al., 2017; Deng et al., 2018; Zhao et al., 2018), phenolic resin (Wang P. et al., 2018), PN-containing compound flame retardants (Chen et al., 2005; Jian et al., 2017), and other flame retardants that contain phosphorus (P) and silicon. However, these flame retardants cannot ensure the flame retardancy of EP and might even release a significant amount of toxic fumes because they cannot easily form char, thereby endangering people’s health. Therefore, we need to develop new flame retardants with excellent char-forming ability.
Among the P-based flame retardants, halogen-free spiro P-based flame retardants boast merits, such as high P content, excellent char-forming ability, low toxicity, migration resistance, and durability, which have contributed to their wide applications. Spiro P-based flame retardants consist of three elements, namely, P, oxygen (O), and carbon (C), which give them a stable heterocyclic structure and high thermal stability. With the char-forming property of pentaerythritol, such retardants can inhibit the further combustion of polymer materials and provide flame retardancy in the gas and condensed phases (Zhan et al., 2009; Li et al., 2016; Ma et al., 2019). The molecular structure of their intermediate, spiro P oxychloride, contains a chlorine atom that can be substituted to synthesize multifunctional flame retardants applicable to different flame-retardant systems and can also react with amine group-containing compounds to prepare P–nitrogen (N) concerted self-intumescent flame retardant combining acid, C, and gas sources to allow O isolation, heat insulation, and smoke suppression. Therefore, these retardants boast outstanding char-forming and flame-retardant properties by comparing with additive flame retardant (Huo et al., 2017; Yuan et al., 2017, 2018; Wang C. et al., 2018; Huang et al., 2019; Shang et al., 2019; Ma et al., 2020; Tang et al., 2020a,b).
To date, numerous studies on amino group-containing compounds have been conducted. For example, Huo et al. (2019) prepared a piperidine group-containing flame retardant that can be effectively combined with EP to improve its flame retardancy (Wang X. et al., 2018). Xie et al. (2016) prepared a triazine-based N-alkoxy compound that can effectively improve the flame retardancy of polypropylene film. Existing studies also show that amino group-containing compounds can provide flame retardancy in the gas phase by quenching free radicals (Aubert et al., 2011; Xu et al., 2015; Zhao et al., 2018). Therefore, we can obtain an EP reactive flame retardant with high P content, good char formation, low toxicity, and high curing activity through the reaction between the chlorine atom in the molecular structure of spiro phosphoryl chloride and the N-H in the amino group-containing compounds.
In this study, a novel spiro-P-based reactive flame retardant (SPDPT) was synthesized through the one-pot reaction of P oxychloride, pentaerythritol, and triacetone diamine. SPDPT was used as a co-curing agent for 4′4-diaminodiphenyl sulfone (DDS) to cure EP and produce the desired flame-retardant epoxy thermoset. A series of tests was conducted to examine the curing properties of SPDPT and the mechanical properties, flammability, and thermal stability of the flame-retardant epoxy thermoset.
Epoxy resin (DGEBA CYD-128) was purchased from the Baling Petrochemical Branch of Sinopec Group Asset Management Co., Ltd., with an epoxy equivalent of approximately 196 g/eq. Triacetone diamine and DDS were purchased from Aladdin Industrial Corporation. Acetonitrile, P oxychloride, methylene chloride, and pentaerythritol were purchased from Sinopharm Chemical Reagent Co., Ltd.
Spiro-P-based reactive flame retardant was synthesized by using the simple one-pot method, and its synthetic route is shown in Figure 1.
In a 500-ml three-necked flask equipped with a magnetic stirrer, a thermometer, and a condenser, 13.6 g (0.1 mol) of pentaerythritol and 168.3 g (1.1 mol) of P oxychloride were added and then heated to 130°C (reflux temperature) until no hydrogen chloride gas is produced, in which case the reaction was stopped and the product was cooled to room temperature. The product was filtered, washed twice with distilled water, washed thrice with dichloromethane, and finally dried in a vacuum oven at 50°C for 24 h.
While introducing N2 gas, 15.65 g (0.11 mol) of triacetone diamine, 300 ml of acetonitrile, and 14.85 g (0.05 mol) of SPDPC were added into a 500-ml three-necked flask equipped with a magnetic stirrer, an oil seal, and a condenser. After the SPDPC was evenly mixed, the solution was first heated to 30°C for a 3-h reaction and then heated to 50°C for another 3-h reaction, after which the product was washed three times with dichloromethane and finally dried in a vacuum oven at 50°C for 24 h.
The SPDPT flame-retardant epoxy thermosets (EP/DDS/SPDPT) with different P contents were obtained through the polymerization among EP, DDM, and SPDPT, where SPDPT is the co-curing agent for DDS, and the sum of the active hydrogen equivalents of DDS and SPDPT is consistent with the epoxy equivalent of EP (see Table 1). SPDPT and DDS were added to the EP at a temperature of 110°C, stirred to mix evenly, and vacuum-defoamed. After the solution became transparent, the solution was poured into a mold preheated to 100°C. The mold was subsequently placed in an electric blast drying oven and cured at 130°C, 150°C, 170°C, and 190°C for 2 h After curing, the mold was naturally cooled to room temperature to obtain the SPDPT flame-retardant epoxy thermoset. The preparation process of the pure epoxy thermoset (EP/DDS) was similar to that of the EP/DDS/SPDPT thermoset with no SPDPT added.
A certain amount of EP and SPDPT (epoxy equivalent in EP is equal to the active hydrogen equivalent in SPDPT) was added and stirred to an appropriate amount of acetone, thereby and, uniformly dispersing the EP and the SPDPT in the acetone. The mixture was then dried at 40°C to obtain the EP/SPDPT compound. The preparation of the EP/DDS and EP/DDS/SPDPT compounds (see Table 1) was the same as that of the EP/SPDPT compound.
Fourier-transform infrared (FTIR) spectroscopy was performed using a United States-made Nicolet 6700 FTIR spectrometer. The samples and KBr were ground, mixed, and pressed into thin sheets (measurement range: 400–4000 m–1).
1H NMR spectroscopy and 31P NMR spectroscopy were performed using an Agilent 400AR NMR spectrometer and deuterated dimethyl sulfoxide (DMSO-d6).
Elemental analysis was performed using the Germany-made Vario EL cube element analyzer to determine the C, hydrogen, and N contents of the sample.
Differential scanning calorimetry (DSC) was performed using a Perkin-Elmer DSC 4000 differential scanning calorimeter under N atmosphere at a ramp rate of 10°C/min and a temperature range of 25–250°C.
Thermogravimetric analysis (TGA) was performed using a Germany-made NETZSCH STA409PC thermogravimetric analyzer under N atmosphere at a ramp rate of 10°C/min (heating from room temperature to 700°C).
The limiting O index (LOI) was tested pursuant to the ASTM D2863 standard using a JF3 O index meter manufactured by Nanjing Jiangning Analytical Instrument Co., Ltd. The standard size of the sample was 100 mm × 6.5 mm × 3 mm.
The flammability rating (UL 94) was measured pursuant to the GBT2408 2008 standard (the latest Chinese standard) using a NK8017A UL94 vertical burning test machine manufactured by Dongguan Nayu Testing Equipment Co., Ltd. The standard size of the sample was 130 mm × 13 mm × 3 mm.
Tensile property was tested on a GP-TS2000S universal testing machine (at the testing temperature of 25°C, a tensile rate of 5 mm/min), the testing method with reference to GB/T2567-2008.
Flexural property was tested on a GP-TS2000S universal testing machine (at the testing temperature of 25°C, a flexural rate of 2 mm/min), the testing method with reference to GB/T2567-2008.
Impact property was tested on a XJJD-50 impact testing machine (at the testing temperature of 25°C), the testing method with reference to GB/T2570-1995, the specimen size with reference to GB1043-93.
Figure 2 shows the infrared spectra of the intermediate product (e.g., SPDPC) and the final product (e.g., SPDPT). The absorption curve of SPDPC shows that the characteristic absorption peaks of P = O, P-O-C, P-O, and P-Cl appear at 1305, 1023, 858, and 546 cm–1, respectively. On the absorption curve of SPDPT, the characteristic absorption peaks of −NH2 appear at 3430, 3221, and 1626 cm–1; that of P = O appears at 1226 cm–1; that of P-O-C appears at 1023 cm–1; that of P-O appears at 833 cm–1; and that of P-N appears at 1079 cm–1. An obvious characteristic absorption peak of P-Cl (546 cm–1) can be observed on the absorption curve of SPDPC, but this peak does not appear on the absorption curve of SPDPT. Instead, the characteristic absorption peak of P-N (1079 cm–1) appears on the absorption curve of SPDPT, indicating that SPDPC reacts with triacetone diamine to form SPDPT.
Figure 3 shows the 1H NMR spectra of the intermediate product (e.g., SPDPC) and the final product (e.g., SPDPT). According to the 1H NMR spectrum of SPDPT, the chemical shifts of imino hydrogen on the piperidine and connecting piperidine rings appear at 8.31 and 6.38 ppm, respectively; and the chemical shifts of methylene hydrogen, methyl hydrogen, and methine hydrogen on the piperidine ring appears at 4.22, 3.27–3.33, and 1.29–1.38 ppm, respectively. According to the 1H NMR spectrum of SPDPC, the methylene hydrogen in the spiro ring is at −0.02 ppm and is present in the NMR spectrum of SPDPT, indicating that SPDPC reacted with triacetone diamine to produce SPDPT.
Figure 4 shows the 31P NMR spectra of the intermediate product (e.g., SPDPC) and the final product (e.g., SPDPT). The two spectra differ significantly. The signal peak of SPDPT appears at 5.22 ppm, whereas that of SPDPC appears at −7.29 ppm, indicating that SPDPT and SPDPC are two different P compounds. This finding further points to the fact that SPDPC and triacetone diamine reacted to form a new compound of SPDPT.
The chemical structure of SPDPT was further confirmed through elemental analysis, and the results of which are shown in Table 2. Table 2 shows that the measured actual contents of C, hydrogen, and N in SPDPT are almost the same as the theoretical contents.
The curing behavior of the epoxy compounds was measured through DSC. Figure 5 shows the DSC curves of the EP/DDS, EP/DDS/SPDPT, and EP/SPDPT epoxy compounds. Only one curing exothermic peak appears on each curve. Figure 5 shows that a significant curing exothermic peak appears on the DSC curve of the EP/SPDPT compound at approximately 207°C, indicating that the imino group in the SPDPT can react with the epoxy group in the EP. That is, SPDPT can cure EP. Moreover, the peak temperature at the curing exothermic peak of the EP/SPDPT compound is apparently lower than that of the EP/DDS compound. The peak temperature at the curing exothermic peak of the EP/DDS/SPDPT compound increases with the SPDPT content because the introduction of the rigid phenanthroline group in the SPDPT enhances the steric hindrance of the SPDPT molecule, thereby weakening the curing activity of SPDPT.
The thermal stability of SPDPT and the epoxy thermoset was evaluated under N2 atmosphere using TGA. The TGA and DTG curves of the SPDPT, EP/DDS, and EP/DDS/SPDPT thermosets are shown in Figures 6–9. The characteristic data, such as the 5% mass loss (T5%), the maximum degradation at maximum rate of mass loss (Tmax), and the C residue yield at 700°C (Yc), are provided in Table 3.
Figure 6 shows that during the decomposition of SPDPT, the T5% of SPDPT is 285°C, and the residual C of SPDPT at 700°C is 26%, indicating that SPDPT decomposes during combustion and produces a large amount of volatile matter.
For the EP/DDS and EP/DDS/SPDPT thermosets (Figure 7), the DTG curve has only one weight loss peak. Tmax of the EP/DDS/SPDPT thermoset decrease gradually with the increase in the SPDPT content. The residual C yield of the EP/DDS/SPDPT thermoset increases at 700°C with the addition of SPDPT.
The flammability of the epoxy thermoset was evaluated by LOI and UL-94 vertical burning experiments. Table 4 shows the corresponding test results.
Table 4 shows that the LOI value of the epoxy thermoset significantly increases from 20.2 for EP/DDS to 26.4 for EP/DDS/SPDPT, with the P content being only 1%. The EP/DDS thermoset failed to pass the UL-94 test, whereas EP/DDS/SPDPT-3 and EP/DDS/SPDPT-4 reached the V-0 rating, and all the EP/DDS/SPDPT thermosets did not show dripping.
Figure 8 shows the tensile property of the epoxy thermosets. Among the EP/DDS/SPDPT thermosets, EP/DDS/SPDPT-2 (P content = 0.5%) produces the best tensile property of 37.20 MPa.
Figure 9 shows the flexural property of the epoxy thermosets. EP/DDS/SPDPT-2 (P content = 0.5%) demonstrates the best flexural property of 63.82 MPa.
Figure 10 shows the impact property of the epoxy thermosets. EP/DDS/SPDPT-2 (P content = 0.5%) demonstrates the best impact property of 24.57 KJ⋅m–2.
Figures 8–10 show that the addition of the flame-retardant curing agent SPDPT exerted a certain impact on the mechanical properties of the epoxy thermosets. The tensile, flexural, and impact properties of the EP increased first and then decreased with the increase in the P content in the EP, indicating that the addition of SPDPT can improve the mechanical properties of the EP system.
The tensile property, the flexural strength, and the impact property reached 37.20 MPa, 63.82 MPa, and 21.57 KJ⋅m–2, respectively.
A novel flame-retardant curing agent that contained piperidine groups was successfully synthesized and used as a reactive flame-retardant curing agent to prepare the desired flame-retardant epoxy thermosets. The EP/DDS/SPDPT epoxy thermosets showed a higher C residue yield at 700°C than the EP/DDS sample. the flame retardancy and mechanical properties of the epoxy thermoset will be improved significantly by adding SPDPT at a low P content. As an EP curing agent, the SPDPT can be prepared easily, and the raw material can also be obtained easily. Therefore, SPDPT boasts great application prospects.
All datasets presented in this study are included in the article/supplementary material.
YC and YP: conceptualization. LY: methodology, formal analysis, and writing – original draft preparation. YC: software, resources, supervision, project administration, and funding acquisition. LY and ZH: validation. ZH: investigation. YP: data curation and writing – review and editing. All authors contributed to the article and approved the submitted version.
This research was funded by the National Natural Science Foundation of China, grant number 21376182.
The authors declare that the research was conducted in the absence of any commercial or financial relationships that could be construed as a potential conflict of interest.
The reviewer BY declared a shared affiliation, with no collaboration, with one of the authors to the handling editor at the time of review.
The authors would like to thank the editor and reviewers.
Aubert, M., Wilén, C., Pfaendner, R., Kniesel, S., Hoppe, H., and Roth, M. (2011). Bis (1-propyloxy-2, 2, 6, 6-tetramethylpiperidin-4-yl)-diazene–An innovative multifunctional radical generator providing flame retardancy to polypropylene even after extended artificial weathering. Polym. Degrad. Stab. 96, 328–333. doi: 10.1016/j.polymdegradstab.2010.02.035
Chen, D., Wang, Y., Hu, X., Wang, D., Qu, M., and Yang, B. (2005). Flame-retardant and anti-dripping effects of a novel char-forming flame retardant for the treatment of poly (ethylene terephthalate) fabrics. Polym. Degrad. Stab. 88, 349–356. doi: 10.1016/j.polymdegradstab.2004.11.010
Chu, F., Ma, C., Zhang, T., Xu, Z., Mu, X., Cai, W., et al. (2020). Renewable vanillin-based flame retardant toughening agent with ultra-low phosphorus loading for the fabrication of high-performance epoxy thermoset. Compos. Part B Eng. 190:107925. doi: 10.1016/j.compositesb.2020.107925
Deng, P., Liu, Y., Liu, Y., Xu, C., and Wang, Q. (2018). Preparation of phosphorus−containing phenolic resin and its application in epoxy resin as a curing agent and flame retardant. Polym. Adv. Technol. 29, 1294–1302. doi: 10.1002/pat.4241
Ding, J., Zhang, Y., Zhang, X., Kong, Q., Zhang, J., Liu, H., et al. (2020). Improving the flame-retardant efficiency of layered double hydroxide with disodium phenylphosphate for epoxy resin. J. Therm. Anal. Calorim. 140, 149–156. doi: 10.1007/s10973-019-08372-9
Huang, C., Chen, X., Yuan, B., Zhang, H., Dai, H., He, S., et al. (2019). Suppression of wood dust explosion by ultrafine magnesium hydroxide. J. Hazard. Mater. 378:120723. doi: 10.1016/j.jhazmat.2019.05.116
Huo, S., Wang, J., Yang, S., Li, C., Wang, X., and Cai, H. (2019). Synthesis of a DOPO-containing imidazole curing agent and its application in reactive flame retarded epoxy resin. Polym. Degrad. Stab. 159, 79–89. doi: 10.1016/j.polymdegradstab.2018.11.021
Huo, S., Wang, J., Yang, S., Wang, J., Zhang, B., Zhang, B., et al. (2016). Synthesis of a novel phosphorus-nitrogen type flame retardant composed of maleimide, triazine-trione, and phosphaphenanthrene and its flame retardant effect on epoxy resin. Polym. Degrad. Stab. 131, 106–113. doi: 10.1016/j.polymdegradstab.2016.07.013
Huo, S., Wang, J., Yang, S., Zhang, B., Chen, X., Wu, Q., et al. (2017). Synthesis of a novel reactive flame retardant containing phosphaphenanthrene and piperidine groups and its application in epoxy resin. Polym. Degrad. Stab. 146, 250–259. doi: 10.1016/j.polymdegradstab.2017.10.015
Jian, R., Wang, P., Xia, L., Yu, X., Zheng, X., and Shao, Z. (2017). Low-flammability epoxy resins with improved mechanical properties using a Lewis base based on phosphaphenanthrene and 2-aminothiazole. J. Mater. Sci. 52, 9907–9921. doi: 10.1007/s10853-017-1102-x
Li, H., Liu, J., Zhao, W., Wang, X., and Wang, D. (2016). Synthesis of a novel self-intumescent flame retardant with spiro and triazine structure and its performance for polypropylene. J. Fire Sci. 34, 104–119. doi: 10.1177/0734904115621929
Lin, C., Chou, Y., Shiao, W., and Wang, M. (2016). High temperature, flame-retardant, and transparent epoxy thermosets prepared from an acetovanillone-based hydroxyl poly (ether sulfone) and commercial epoxy resins. Polymer 97, 300–308. doi: 10.1016/j.polymer.2016.05.035
Luo, Q., Sun, Y., Yu, B., Li, C., Song, J., Tan, D., et al. (2019). Synthesis of a novel DPPA−containing benzoxazine to flame−retard epoxy resin with maintained thermal properties. Polym. Adv. Technol. 30, 1989–1995. doi: 10.1002/pat.4631
Luo, Q., Yuan, Y., Dong, C., Liu, S., and Zhao, J. (2015). Intumescent flame retardancy of a DGEBA epoxy resin based on 5, 10-dihydro-phenophosphazine-10-oxide. RSC Adv. 5, 68476–68484. doi: 10.1039/c5ra11847f
Ma, S., Hou, Y., Xiao, Y., Chu, F., Cai, T., Hu, W., et al. (2020). Metal-organic framework@polyaniline nanoarchitecture for improved fire safety and mechanical performance of epoxy resin. Mater. Chem. Phys. 247:122875. doi: 10.1016/j.matchemphys.2020.122875
Ma, T., Li, L., Liu, T., and Guo, C. (2019). Synthesis of a caged bicyclic phosphates derived anhydride and its performance as a flame−retardant curing agent for epoxy resins. Polym. Adv. Technol. 30, 1314–1324. doi: 10.1002/pat.4565
Mestry, S., and Mhaske, S. (2019). Synthesis of epoxy resins using phosphorus-based precursors for flame-retardant coating. J. Coat. Technol. Res. 16, 807–818. doi: 10.1007/s11998-018-00157-3
Perret, B., Schartel, B., Stöß, K., Ciesielski, M., Diederichs, J., Döring, M., et al. (2011a). A new halogen−free flame retardant based on 9, 10−dihydro−9−oxa−10−phosphaphenanthrene−10−oxide for epoxy resins and their carbon fiber composites for the automotive and aviation industries. Macromol. Mater. Eng. 296, 14–30. doi: 10.1002/mame.201000242
Perret, B., Schartel, B., Stöß, K., Ciesielski, M., Diederichs, J., Döring, M., et al. (2011b). Novel DOPO-based flame retardants in high-performance carbon fibre epoxy composites for aviation. Eur. Polym. J. 47, 1081–1089. doi: 10.1016/j.eurpolymj.2011.02.008
Qiu, Y., Qian, L., and Xi, W. (2016). Flame-retardant effect of a novel phosphaphenanthrene/triazine-trione bi-group compound on an epoxy thermoset and its pyrolysis behaviour. RSC Adv. 6, 56018–56027. doi: 10.1039/c6ra10752d
Shang, S., Yuan, B., Sun, Y., Chen, G., Huang, C., Yu, B., et al. (2019). Facile preparation of layered melamine-phytate flame retardant via supramolecular self-assembly technology. J. Colloid Interface Sci. 553, 364–371. doi: 10.1016/j.jcis.2019.06.015
Shi, Y., Yu, B., Duan, L., Gui, Z., Wang, B., Hu, Y., et al. (2017). Graphitic carbon nitride/phosphorus-rich aluminum phosphinates hybrids as smoke suppressants and flame retardants for polystyrene. J. Hazard. Mater. 332, 87–96. doi: 10.1016/j.jhazmat.2017.03.006
Tang, G., Liu, X., Yang, Y., Chen, D., Zhang, H., Zhou, L., et al. (2020a). Phosphorus-containing silane modified steel slag waste to reduce fire hazards of rigid polyurethane foams. Adv. Powder Technol. 31, 1420–1430. doi: 10.1016/j.apt.2020.01.019
Tang, G., Liu, X., Zhou, L., Zhang, Z., Deng, D., and Jiang, H. (2020b). Steel slag waste combined with melamine pyrophosphate as a flame retardant for rigid polyurethane foams. Adv. Powder Technol. 31, 279–286. doi: 10.1016/j.apt.2019.10.020
Wang, C., Wu, Y., Li, Y., Shao, Q., Yan, X., Han, C., et al. (2018). Flame−retardant rigid polyurethane foam with a phosphorus−nitrogen single intumescent flame retardant. Polym. Adv. Technol. 29, 668–676. doi: 10.1002/pat.4105
Wang, P., Xia, L., Jian, R., Ai, Y., Zheng, X., Chen, G., et al. (2018). Flame-retarding epoxy resin with an efficient P/N/S-containing flame retardant: preparation, thermal stability, and flame retardance. Polym. Degrad. Stab. 149, 69–77. doi: 10.1016/j.polymdegradstab.2018.01.026
Wang, X., Xu, M., Zhang, Z., Leng, Y., and Li, B. (2018). Synthesis of a novel N-alkoxyamine containing compound and its application as an effective flame retardant for polypropylene film by quenching free radical. J. Anal. Appl. Pyrolysis 134, 243–253. doi: 10.1016/j.jaap.2018.06.014
Xie, H., Lai, X., Li, H., and Zeng, X. (2016). Synthesis of a novel macromolecular charring agent with free-radical quenching capability and its synergism in flame retardant polypropylene. Polym. Degrad. Stab. 130, 68–77. doi: 10.1016/j.polymdegradstab.2016.05.029
Xu, W., Wang, X., Wu, Y., Li, W., and Chen, C. (2019). Functionalized graphene with Co-ZIF adsorbed borate ions as an effective flame retardant and smoke suppression agent for epoxy resin. J. J. Hazard. Mater. 363, 138–151. doi: 10.1016/j.jhazmat.2018.09.086
Xu, W., Wirasaputra, A., Liu, S., Yuan, Y., and Zhao, J. (2015). Highly effective flame retarded epoxy resin cured by DOPO-based co-curing agent. Polym. Degrad. Stab. 122, 44–51. doi: 10.1016/j.polymdegradstab.2015.10.012
Yuan, B., Hu, Y., Chen, X., Shi, Y., Niu, Y., Zhang, Y., et al. (2017). Dual modification of graphene by polymeric flame retardant and Ni (OH)2 nanosheets for improving flame retardancy of polypropylene. Compos. Part A Appl. Sci. Manuf. 100, 106–117. doi: 10.1016/j.compositesa.2017.04.012
Yuan, B., Sun, Y., Chen, X., Shi, Y., Dai, H., and He, S. (2018). Poorly-/well-dispersed graphene: Abnormal influence on flammability and fire behavior of intumescent flame retardant. Compos. Part A Appl. Sci. Manuf. 109, 345–354. doi: 10.1016/j.compositesa.2018.03.022
Zhan, J., Song, L., Nie, S., and Hu, Y. (2009). Combustion properties and thermal degradation behavior of polylactide with an effective intumescent flame retardant. Polym. Degrad. Stab. 94, 291–296. doi: 10.1016/j.polymdegradstab.2008.12.015
Zhang, Q., Yang, S., Wang, J., Cheng, J., Zhang, Q., Ding, G., et al. (2019). A DOPO based reactive flame retardant constructed by multiple heteroaromatic groups and its application on epoxy resin: curing behavior, thermal degradation and flame retardancy. Polym. Degrad. Stab. 167, 10–20. doi: 10.1016/j.polymdegradstab.2019.06.020
Zhang, Y., Yu, B., Wang, B., Liew, K., Song, L., Wang, C., et al. (2017). Highly effective P–P synergy of a novel DOPO-based flame retardant for epoxy resin. Indust. Eng. Chem. Res. 56, 1245–1255. doi: 10.1021/acs.iecr.6b04292
Keywords: epoxy resin, carbon residue yield, Fourier-transform infrared, curing agent, flame retardant
Citation: Yi L, Huang Z, Cao Y and Peng Y (2020) Synthesis of a Novel Spiro Phosphorus–Nitrogen Concerted Reactive Flame-Retardant Curing Agent and Its Application in Epoxy Resin. Front. Mater. 7:293. doi: 10.3389/fmats.2020.00293
Received: 01 June 2020; Accepted: 04 August 2020;
Published: 11 September 2020.
Edited by:
Yongqian Shi, Fuzhou University, ChinaReviewed by:
Gang Tang, Anhui University of Technology, ChinaCopyright © 2020 Yi, Huang, Cao and Peng. This is an open-access article distributed under the terms of the Creative Commons Attribution License (CC BY). The use, distribution or reproduction in other forums is permitted, provided the original author(s) and the copyright owner(s) are credited and that the original publication in this journal is cited, in accordance with accepted academic practice. No use, distribution or reproduction is permitted which does not comply with these terms.
*Correspondence: Liang Yi, bGlhbmd5aV93aHV0QDE2My5jb20=
Disclaimer: All claims expressed in this article are solely those of the authors and do not necessarily represent those of their affiliated organizations, or those of the publisher, the editors and the reviewers. Any product that may be evaluated in this article or claim that may be made by its manufacturer is not guaranteed or endorsed by the publisher.
Research integrity at Frontiers
Learn more about the work of our research integrity team to safeguard the quality of each article we publish.