- 1School of Transportation Science and Engineering, Harbin Institute of Technology, Harbin, China
- 2CCCC Highway Consultants CO., Ltd. (HPDI), Beijing, China
Snow and ice on asphalt pavement surface can significantly affect traffic safety and damage pavements. To reduce its effect, a kind of anti-icing emulsified asphalt binder (AEAB) is developed by adding a certain amount of anti-icing fillers to the modified emulsified asphalt binder. The anti-icing performance and pavement performance of AEAB coating are evaluated. The results show that: the basic properties of AEAB meet the requirement of road maintenance, and the AEAB has excellent anti-icing performance and bonding property. It can facilitate the ice-melting on pavement and reduce the adhesion force between pavements and ice, and the adhesion force can be reduced by about 50%. The AEAB coating can keep an excellent bonding state with the original pavement, which can prolong the service life of the coating. These findings demonstrated the potential of using AEAB coating on asphalt pavement to provide better pavement performance and contribute to traffic safety during snowfall.
Introduction
Snow and ice on pavement surface can dramatically reduce the road skid resistance and cause the emergency braking distance on icy roads 6∼7 times that of normal roads (Dan et al., 2017). The low friction on road can pose a serious threat to the safety of pedestrians and vehicles, even can cause serious traffic congestion and induce a series of traffic accidents (Pan et al., 2015; Waluś, 2017). Besides, the melting of snow may aggravate the moisture damage to asphalt pavements (Huang et al., 2005). Therefore, researches on anti-icing and snow-melting technologies for asphalt pavement have always been the focus of road engineering.
In the past decades, regular snow removal or deicing methods included spraying chloride ice-melting agents and mechanical equipment such as snowplows and sweepers. However, these traditional methods not only demand a lot of professional workers and equipment but also may lead to high pollution and cause serious damages to the performances of pavements (Henry, 1991; Yehia and Tuan, 1999). To solve these problems of above passive ice-removal method, the anti-icing methods based on thermal melting technology have been studied and proposed, such as heating wire, infrared heating, microwave heating, solar energy collection technology, and electrically conductive pavements; these technologies are proved to be highly efficient in road deicing (Liu et al., 2007; Tang et al., 2008; Wang et al., 2008; Chen et al., 2011; Zhou et al., 2011; Pan et al., 2015; Daniels et al., 2019). Nevertheless, the pavements with heating systems are much more expensive and difficult to build than the normal pavements currently.
Another anti-icing method is to build self-ice-melting pavements by adding the anti-icing fillers into the pavements. The anti-icing ingredients will be released out from self-ice-melting pavements to facilitate the snow/ice-melting process and reduce the adhesion between ice and pavement surface during the snowfall (Pan et al., 2008; Wang et al., 2017; Tan et al., 2019). Due to the simple-operated advantage and excellent anti-icing ability of this technology, it has drawn more and more attention from worldwide countries and several commercial anti-icing fillers such as Verglimit, Mafilon, and Icebane have been produced and applied widely (Baldino et al., 2012; Li and Wang, 2012; Luo and Yang, 2015). For the purpose of improving the long-term performance of anti-icing filler, Tan et al. (2014) developed a sustained-release anti-icing filler to reduce the freezing temperature of the pavement to −25°C. To reduce the costs of anti-icing filler, Lei Peng et al. developed a calcium chloride anti-icing filler named Iceguard (Zheng et al., 2017). However, the researches on anti-icing fillers are mainly focused on newly-built pavement currently. As for so many pavements that have already been built, there is still a lack of anti-icing technology to ensure road safety in adverse weather (e.g., snow, frost, and freezing rain).
Coating technology is a preventive maintenance method that is suitable for in-service pavements, such as the fog seal and micro-surfacing. They have the potential to reverse the aging of in-service asphalt pavement, reduce cracking and raveling, and provide a better, longer-lasting pavement (Lin et al., 2012; Mamlouk and Dosa, 2014). Based on the coating technology and the good hydrophobic properties of hydrophobic materials, researchers have developed hydrophobic emulsified asphalt coating and super-hydrophobic coating on asphalt pavement for ice and snow removal (Peng et al., 2018; Han et al., 2019). However, the hydrophobic and super-hydrophobic coating can only reduce the adhesion between ice and pavement but do not have the ability to actively melt snow and ice, which greatly restrict their ice/snow-removal application on asphalt pavement. Therefore, to get a better anti-icing effect, the technology of anti-icing-emulsified asphalt binder coating is conducted based on the coating technology and anti-icing filler. Basically, the anti-icing emulsified asphalt binder (AEAB) is produced by adding water-repellent anti-icing fillers into an emulsified asphalt binder. The asphalt pavement coated with AEAB not only has excellent anti-icing properties but also can achieve the purpose of preventive maintenance. However, combining emulsified asphalt binder maintenance materials with anti-icing fillers may have adverse influences on the storage stability and other properties of emulsified asphalt. It is necessary to develop an applicable AEAB with excellent properties.
In this study, based on the dual requirements of maintenance function and anti-icing function, an AEAB was developed by adding a certain amount of anti-icing fillers to the modified emulsified asphalt binder. The anti-icing performance and pavement performance of AEAB coating were analyzed by laboratory tests, which proved the excellent properties and the feasibility of AEAB as pavement maintenance materials.
Materials and Methods
Raw Materials
• Asphalt: The neat asphalt binder was LH-90# with basic properties shown in Table 1.
• Emulsifier: Cationic slow-cracking fast-setting emulsifier was used, and its properties are shown in Table 2.
• Stabilizer: Organic stabilizer hydroxypropyl methylcellulose (HPMC) was used to enhance the storage stability of the emulsified asphalt.
• Modifier: The main function of the modifier is to improve the bonding property of emulsified asphalt binder; the SBR and waterborne epoxy resin were used together as a compound modifier.
• Anti-icing filler: Two kinds of water-repellent anti-icing filler (Type A and Type B) were selected. They have different effect on reducing the freezing temperature of asphalt pavement. Type A and Type B are suitable for using in the ambient temperature above −10°C and −25°C, respectively. Their basic properties and size distributions are shown in Tables 3, 4.
Preparation of AEAB
The preparation process of AEAB generally includes three steps: emulsification, modification, and adding anti-icing fillers.
The steps of the emulsification process are as follows. First, the emulsions were obtained by mixing water of a pH value between 1.5 and 2.5 with the 1.8% emulsifier and 0.2% stabilizers. Then, the emulsions were poured into a preheated colloid mill and sheared for 3 min. Next, the heated neat asphalt binder was added to the emulsions and the oil-water ratio is 6:4. Last, after the binder was fully added, it was sheared in colloid mill for 5 min.
Then, there was the modification process; after the emulsified asphalt binder was cooled to room temperature, the high-shear mixer was used to mix the emulsified asphalt and compound modifier at a speed of 1200 rpm for 5 min. The contents of SBR and waterborne epoxy resin were 10% and 8%, respectively (based on the weight of emulsified asphalt binder).
Finally, the prepared emulsified asphalt binder and 20% anti-icing fillers were added into the mixer and stirred until particles of anti-icing filler were fully coated with modified emulsified asphalt binder. The modified emulsified asphalt binders mixed with Type A and Type B were named AEAB-1 and AEAB-2, respectively.
Test Methods
Basic Properties Test
According to the standard test methods of bitumen and bituminous mixtures for highway engineering in China (China Communications Press, 2011), softening point, penetration, ductility at 5°C, elastic recovery of evaporated residue test, and Brookfield viscosity test were carried out to evaluate the basic properties of AEAB and modified emulsified asphalt binder.
Zeta Potential Test
As a colloid, emulsified asphalt has a structure of electrical double layer. And the stability of electrical double layer is often characterized by the Zeta potential of colloidal solution (Salopek et al., 1992; Stachurski and MichaŁek, 1996). Table 5 shows the stability classification of colloidal materials (Tan, 2018). Due to the limitation of the light scattering instrument, it is impossible to test the Zeta potential of original material. To get relatively stable test results, the emulsified asphalt needs to be diluted a certain number of times before testing. According to the previous study (Tian, 2019), the storage stability time of emulsified asphalt is more than 20 h when Zeta potential of diluted solution (150 times) is higher than 30 mv. In this study, to get stable Zeta potential test results, the modified emulsified asphalt binder and AEAB are also diluted 150 times with distiller water, respectively. Then, the Zeta potentials of the diluted solution are measured by Malvem Zetasizer Nano ZS light scattering instrument to evaluate the storage stability of materials.
Ice-Melting Test
Firstly, the AC-16 Marshall specimens were manufactured according to the specification (China Communications Press, 2004) to simulate the pavement surface. Then, the AEAB was evenly brushed on the specimen surfaces with a dosage of 0.8 kg/m2. After the AEAB was fully cured, 100 g snow-ice particles (crushed ice scraped from the inner wall of the refrigerator) was used to cover the surfaces. Next, the specimens were divided into four groups for different testing temperatures (−5°C, −10°C, −15°C, and −25°C, respectively). Each group contained an AEAB-1-coated specimen, an AEAB-2-coated specimen, and an uncoated specimen. Finally, the specimens were placed in different environmental boxes at the fixed temperature for 5 h and the ice-melting conditions were observed to evaluate the anti-icing performance of AEAB.
Besides the laboratory tests, the real road brushed with AEAB (as shown in Figure 1) was also used to observe the anti-icing performance of AEAB. The coating dosage of AEAB is 0.8 kg/m2, and the coating area is about 16.5 m2.
Ice-Road Adhesion Test
Tan et al. (2013) have developed a system to test the adhesion between ice and asphalt mixture, as shown in Figure 2A. The ice-road adhesion test steps are as follows:
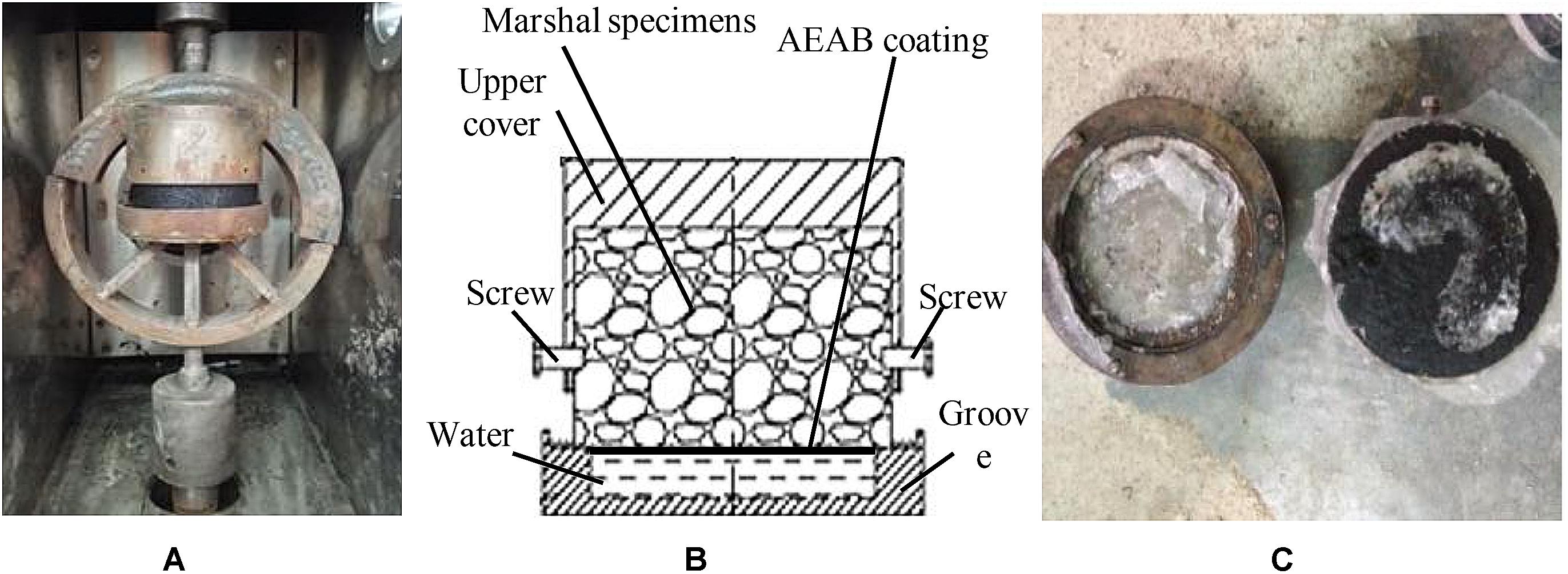
Figure 2. Ice-road adhesion test: (A) Testing device. (B) The profile of fixed specimen. (C) The damage interface of tested specimen.
(a) The AEAB is evenly brushed on the surface of AC-16 Marshal specimens with a dosage of 0.80 kg/m2. After the AEAB is fully cured, the specimen is fixed to the upper cover by three screws. Next, 100 g of water is injected into the groove of the device so that the water can be fully contacted with AEAB coating. The profile of the fixed specimen is shown in Figure 2B.
(b) Then, the specimens are placed in the environmental box at the fixed temperature for 12 h to simulate the freezing process of the road surface in winter.
(c) Finally, the MTS test system is used to apply load until the bonding interface between ice and specimen is completely broken. The loading rate is 20 mm/min. The maximum load is the ice-road adhesion force, and it is used as an index to evaluate the adhesion between the ice layer and pavements. Besides, the interface of the specimens after test (Figure 2C) can also be used to evaluate the deicing effect.
According to the above test steps, the ice-road adhesion forces of AEAB specimens before and after experienced freeze-thaw cycles are analyzed to evaluate the long-term anti-icing performance of AEAB. The process of the freeze-thaw cycle is as follows: First, 100 g of water is evenly sprayed on the surface of the specimen. Then, the specimen is placed in the environmental box at −60°C for 6 h to simulate the freezing process. Last, adjust the temperature to 25°C for 6 h to simulate the melting process. The ice-road adhesion of AEAB-coated specimens experienced 0, 5, 10, 15, 20, 25, and 30 times of freeze-thaw cycles is all tested. The AEAB-1-coated specimens are under the testing temperature of −5°C and −10°C. The AEAB-2-coated specimens are under the testing temperature of −15°C and −25°C. Besides, the ice-road adhesions force of uncoated AC-16 specimens at each temperature is also tested for comparison.
Bonding Test
The bonding test is used to evaluate the bonding property between the AEAB coating and the original pavement. The Defelsko PosiTest AT tester shown in Figure 3A was used for this purpose. The test steps are as follows:
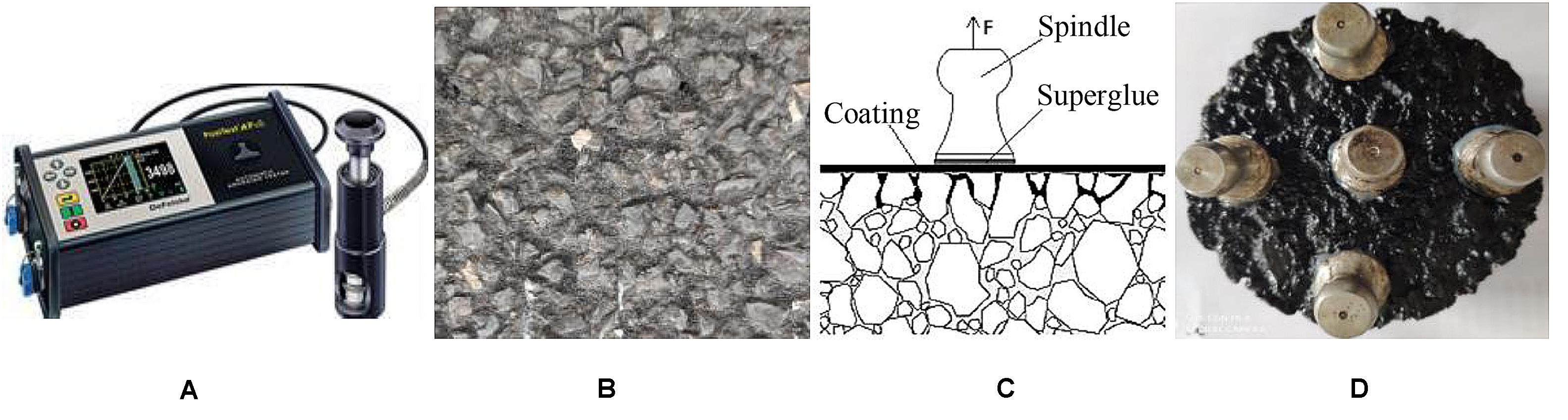
Figure 3. Bonding test: (A) Testing device. (B) The Marshall specimen with a polished surface. (C) The testing schematic. (D) The prepared specimen.
(a) Firstly, the AC-16 Marshall specimens are manufactured according to the specification (China Communications Press, 2004). Then, the surface of the Marshall specimen is polished by accelerated polishing machine until the original asphalt film is peeled off. The specimen with a polished surface (shown in Figure 3B) is selected to simulate the surface condition of the in-service asphalt pavement. The testing value of British Pendulum Number (BPN) and the texture depth (TD) of the polished specimen are 68 and 0.94 mm, respectively, according to the specification (China Communications Press, 2008).
(b) The prepared coating materials (emulsified asphalt binder, modified emulsified asphalt binder or AEAB) are evenly brushed on the polished surfaces of different specimens, respectively, with a dosage of 0.8 kg/m2. After the emulsion is fully cured, the superglue is used to stick the spindles and coating together. The aim of using the superglue is to ensure that the bonding failure occurs between the coating and asphalt mixture not between spindles and the coating. Five test positions are selected randomly for each specimen. The testing schematic and the prepared specimen are shown in Figures 3C,D, respectively.
(c) Next, the prepared specimens are divided into three groups for different testing temperatures (−15°C, 25°C, and 60°C, respectively), and each group contains three different specimens coated by three kinds of coating material, respectively. Then, each specimen is placed in the environmental box at its testing temperature for 2 h.
(d) Finally, the tester is used to apply a tensile force to the spindles at a loading speed of 0.2 Mpa/s until the coating material is pulled apart from the asphalt mixture specimen.
The maximum tensile force is the bonding strength, and it is used as the index to evaluate the bonding property of coating materials. The larger the bonding strength is, the better the bonding property of coating material is.
Results and Discussion
Basic Properties
The basic test results of AEAB and the modified emulsified asphalt binder are shown in Table 6. It can be seen that the Brookfield viscosity of AEAB is much larger than that of modified emulsified asphalt binder; this indicates that the addition of anti-icing filler has increased the viscosity and consistency of modified emulsified asphalt binder. The softening point of AEAB evaporative residue is above 70°C; it means that the AEAB has an excellent high-temperature performance. Compared with the modified emulsified asphalt binder, the 5°C ductility and 25°C elastic recovery of AEAB evaporated residue decrease slightly. It means that anti-icing fillers can slightly affect the low-temperature performance and elastic recovery ability of modified emulsified asphalt binder. All of the performance indexes of the AEAB meet the requirements of specification (China Communications Press, 2004), which proved the feasibility of AEAB as pavement maintenance materials.
Storage Stability
The Zeta potentials of modified emulsified asphalt binders at different storage times are shown in Figure 4. It can be seen that the Zeta potential of modified emulsified asphalt binder fluctuates slightly at 66 mv during 15 days. According to the stability classification of colloidal materials from Table 5, it is clearly indicated that the modified emulsified asphalt binder has excellent long-term storage stability. The Zeta potential of newly prepared AEAB is about 45 mv. It means that adding anti-icing fillers into modified emulsified asphalt binder will reduce the storage stability of modified emulsified asphalt binder. But the Zeta potential of AEAB is still greater than 30 mv, which indicates that the storage time of AEAB is more than 20 h. It also means that the AEAB can maintain a uniform and stable state without demulsification more than 20 h. So, there is enough time for the production and construction of AEAB.
Anti-icing Performance
The surface conditions of the specimens in the environmental box are shown in Figure 5. It is observed that the snow-ice particles on the surface of AEAB-coated specimens are much less than that on the surface of the uncoated specimens. It means that the AEAB coating has an obvious effect on facilitating the melting of snow and ice. From Figures 5B–E, it can be seen that the amount of snow-ice particles on the specimen increases obviously with the decrease in temperature. It means that the effect of the AEAB decreases with decrease in temperature. But it still has the snow-melting ability when the temperature is −25C. Besides, the ice-melting condition of AEAB-1 coating and AEAB-2 coating are similar to each other at the same temperature; this may happen because the observing time is too short to show the anti-icing differences between the two types of anti-icing fillers.
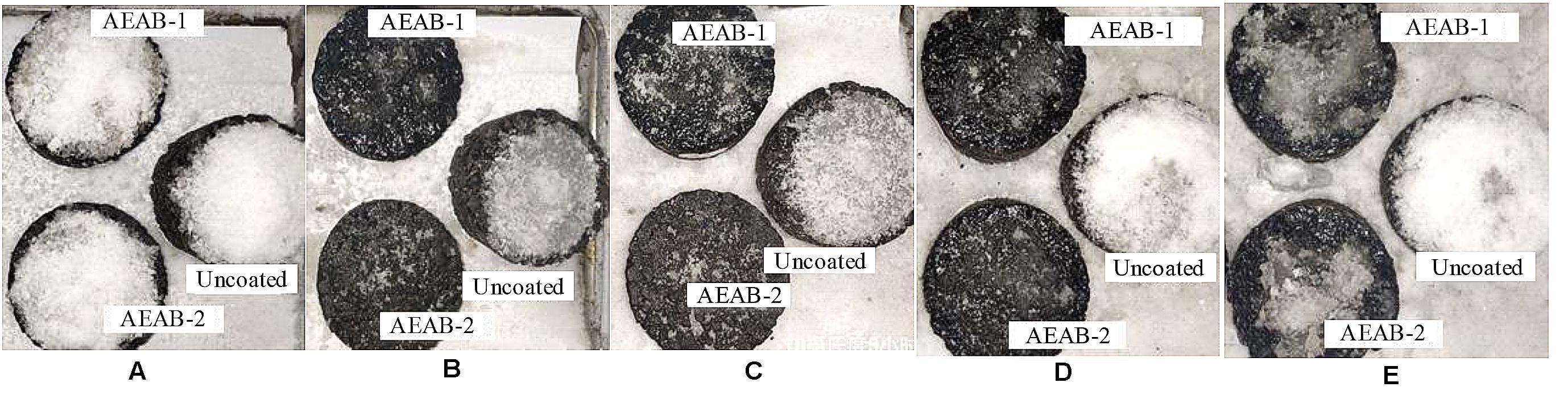
Figure 5. Comparisons of ice-melting test at different temperature: (A) Initial state of each group. (B) −5°C. (C) −10°C. (D) −15°C. (E) −25°C.
The ice-road adhesion force of the uncoated specimens and the AEAB coated specimens is shown in Figure 6. It can be seen that, under the conditions of −5°C, −10°C, −15°C, and −25°C, the ice adhesion forces of AEAB-coated specimens have decreased by 49.3%, 67%, 53.6%, and 46.5%, respectively, compared with that of uncoated specimens. It means that AEAB coating can dramatically reduce the adhesion force between ice and asphalt pavement, which is very helpful for the snow/ice removal. The interfaces of the specimens after ice-road adhesion test are shown in Figure 7. It is found that there is basically no ice covering on the surface of the AEAB-coated specimens, which proves that the ice is easy to pull off from the specimen due to the reduction of ice-road adhesion force.
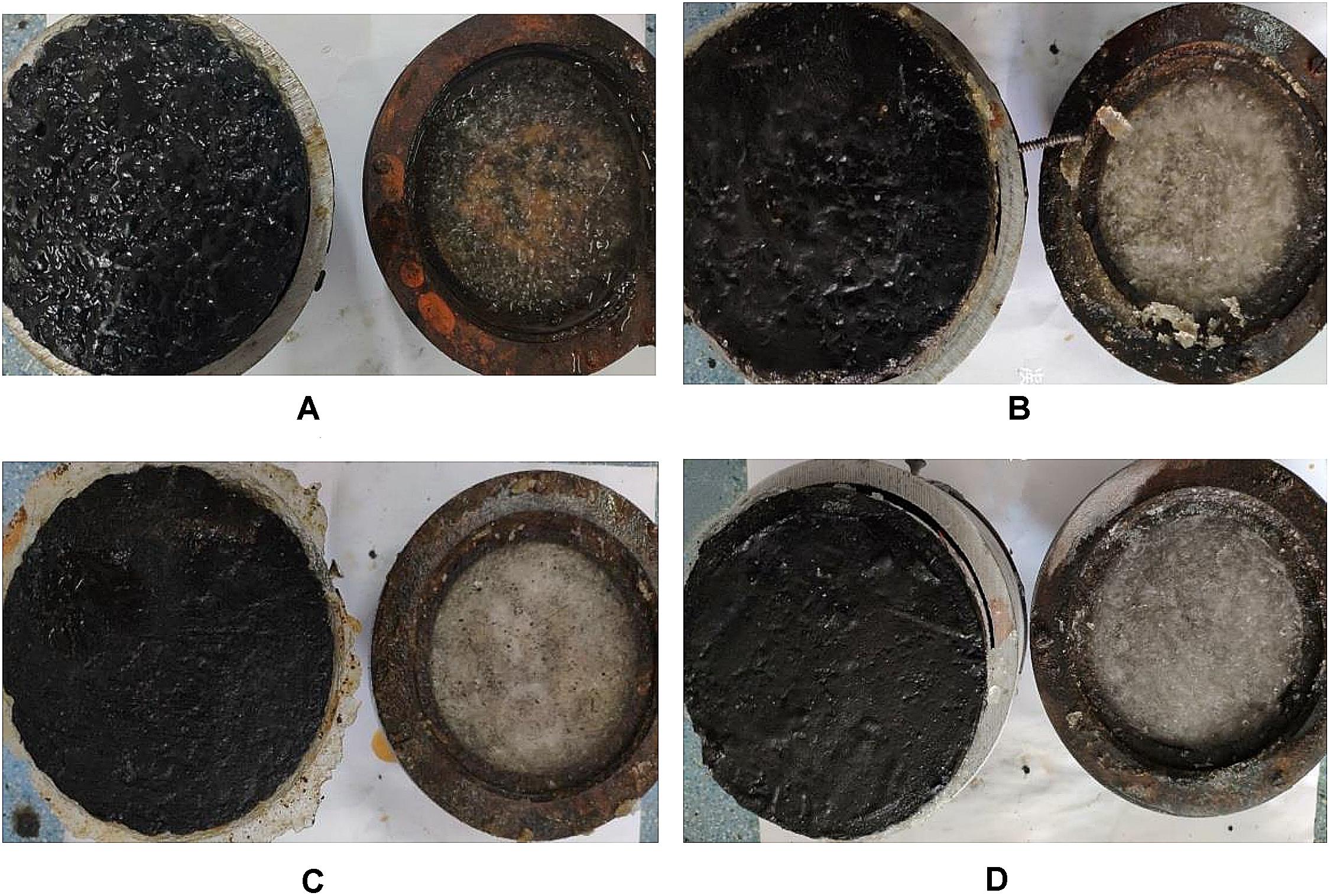
Figure 7. The interface of the AEAB-coated specimens after ice-road adhesion tests: (A) −5°C. (B) −10°C. (C) −15°C. (D) −25°C.
The ice-road adhesion forces of the specimens experienced different times of freeze-thaw cycles are shown in Figure 8. It can be seen that the ice-road adhesion force of AEAB-1- and AEAB-2-coated specimen increases slightly with the increase in times of freeze-thaw cycles. It is mainly due to the constant release of anti-icing ingredients, which slowly decreases the deicing effect of AEAB. Besides, the freeze-thaw cycle can also cause an increase in the adhesion force between ice and specimen. Nevertheless, after the AEAB coated has experienced 30 times of freeze-thaw cycles, the ice-road adhesion force of AEAB-coated specimen is still lower than the ice-road adhesion of uncoated specimens that do not experience the freeze-thaw cycle. It indicates that the release rate of anti-icing ingredients has been maintained at a moderate level and the AEAB can well keep its adhesion-reduce function.
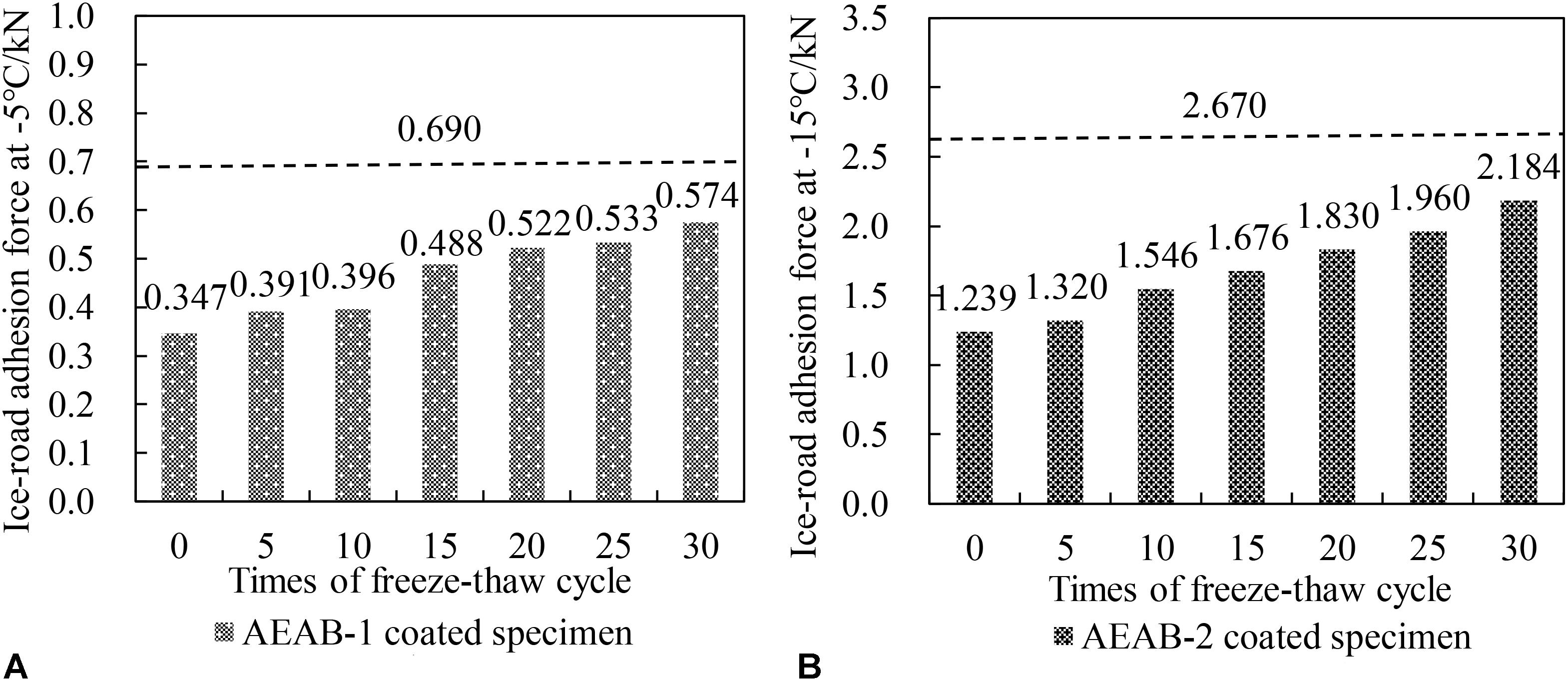
Figure 8. Ice-road adhesion force of different times of freeze-thaw cycle: (A) AEAB-1-coated specimen. (B) AEAB-2-coated specimen. The dash line in the figure indicates the ice-road adhesion of uncoated specimens that do not experience the freeze-thaw cycle.
Figure 9A shows the snow-melting conditions of the uncoated area and the AEAB-coated area on the asphalt pavement after a light snow. It can be seen that there is barely any snow covering the AEAB coated area compared with the uncoated asphalt pavement. It is direct evidence that the AEAB coating on asphalt pavement can facilitate the melting of snow to realize a self-ice-melting function. When the snow is heavy, the mechanical equipment is used to remove the snow on the asphalt pavement. Figure 9B shows that the snow-removing conditions of the uncoated area and the AEAB coated area on the asphalt pavement after heavy snow. It can be seen that the snow remaining on the AEAB-coated area is obviously less than that on the uncoated area. It proves that the snow/ice is easy to clear due to the reduction of ice-road adhesion force on the AEAB-coated pavement.
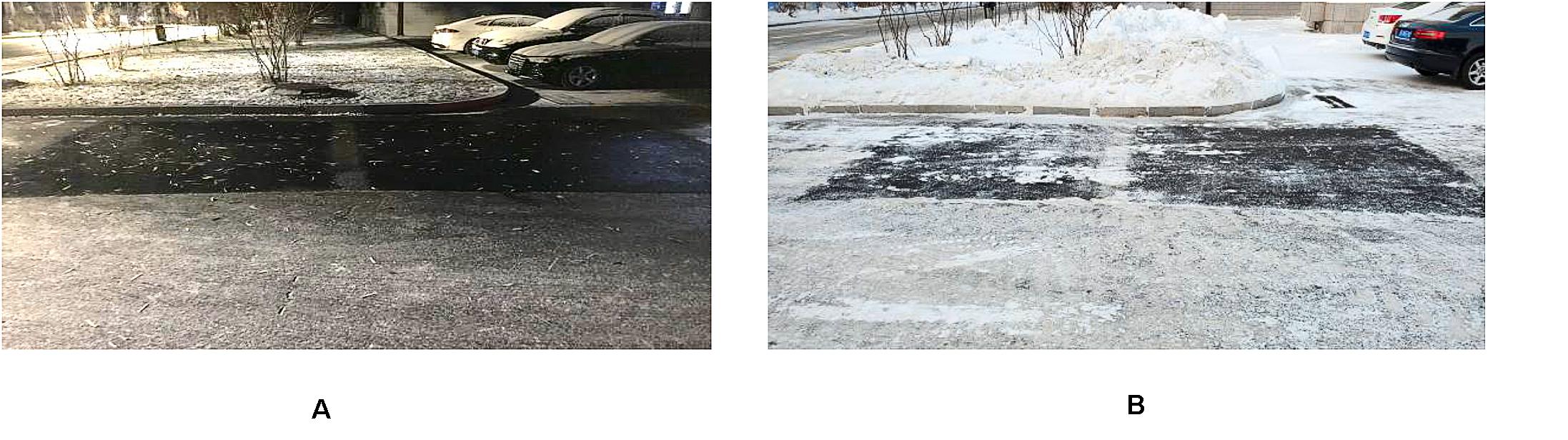
Figure 9. Observation during snowing weather in Harbin China. (A) Snow-melting conditions after light snow in November 2019. (B) Snow-removing conditions after heavy snow in December 2019.
Bonding Properties
The bonding strengths of the emulsified asphalt binder, modified emulsified asphalt binder, and AEAB were tested, and the results are shown in Figure 10. It can be seen that, compared with the bonding strength of emulsified asphalt (shown as EA in the figures), the bonding strengths of modified emulsified asphalt binder (shown as MEA in the figures) increases significantly. This indicates that the compound modifier has an obvious effect on improving the bonding properties of the emulsified asphalt binder. Besides, comparing the bonding strength of modified emulsified asphalt binder with that of AEAB (shown as AEAB-1 and AEAB-2 in the figures), it shows that the bonding strengths of modified emulsified asphalt binder slightly changes after adding anti-icing fillers. It means that the participation of anti-icing filler has little effect on the bonding properties of modified emulsified asphalt binder. In a word, the bonding test proves that the AEAB has an excellent bonding state with the original pavement, which can prolong the service life of the coating.
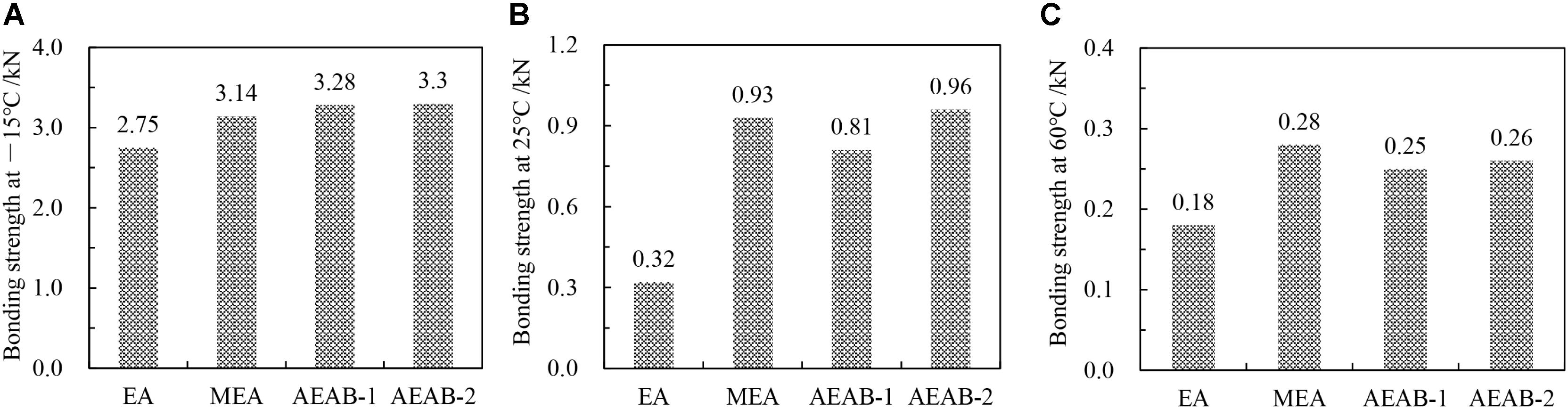
Figure 10. Bonding strength of different coating materials at different temperature: (A) At −15°C (B) At 25°C (C) At 60°C. In the figures, EA represents the emulsified asphalt binder, and MEA represents the modified emulsified asphalt binder.
Conclusion
In this paper, a kind of AEAB was developed by adding anti-icing fillers into a modified emulsified asphalt binder. The anti-icing performance and pavement performance of AEAB coating were analyzed. The major conclusions of this study can be drawn:
(1) Although the participation of anti-icing fillers can slightly affect the low-temperature performance and elastic recovery ability of modified emulsified asphalt binder, all of the performance of AEAB can still meet the requirements of the specification.
(2) The AEAB coating has excellent anti-icing performance. It can facilitate the melting of snow and ice on pavement and dramatically reduce the adhesion forces between ice and road, which is helpful for the snow/ice removal and the maintaining of skid resistance on asphalt pavement.
(3) The compound modifier has an obvious effect on improving the bonding properties of AEAB. The AEAB coating can keep an excellent bonding state with the original pavement, which can prolong the service life of the coating.
(4) The study has proved that the AEAB has the necessary storage stability for the actual construction. Future research should be conducted to develop a kind of AEAB that has a longer storage stability time, and the anti-icing mechanism of AEAB coating needs to be further studied.
Data Availability Statement
The raw data supporting the conclusions of this article will be made available by the authors, without undue reservation.
Author Contributions
LS and YT proposed the research direction and provided the funds for the research. HY wrote the first draft. DT carried out the experiments. All authors analyzed the results and contributed to writing of the manuscript.
Funding
The study was financially supported by the National Natural Science Foundation of China under the Grant Nos. U1633201, 51778195, and 51978218.
Conflict of Interest
DT was employed by the company CCCC Highway Consultants CO., Ltd.
The remaining authors declare that the research was conducted in the absence of any commercial or financial relationships that could be construed as a potential conflict of interest.
Acknowledgments
The authors acknowledge Ms. Jianrong Wang for providing the emulsifier.
References
Baldino, N., Gabriele, D., Rossi, C. O., Seta, L., Lupi, F. R., and Caputo, P. (2012). Low temperature rheology of polyphosphoric acid (PPA) added bitumen. Constr. Build. Mater. 36, 592–596. doi: 10.1016/j.conbuildmat.2012.06.011
Chen, M., Wu, S., Wang, H., and Zhang, J. (2011). Study of ice and snow melting process on conductive asphalt solar collector. Sol. Energy. Mat. Sol. C 95, 3241–3250. doi: 10.1016/j.solmat.2011.07.013
China Communications Press (2004). Technical Specifications for Construction of Highway Asphalt Pavements JTG F40-2004. Beijing: China Communications Press.
China Communications Press (2008). Field Test Methods of Subgrade and Pavement for Highway Engineering JTG E60-2008. Beijing: China Communications Press.
China Communications Press (2011). Standard Test Methods of Bitumen and Bituminous Mixtures for Highway Engineering JTG E20-2011. Beijing: China Communications Press.
China Communications Press (2018). Deicing and Thawy Material Used in Asphalt Mixture-Part 2: Salinization-Based Material JT/T 1210.2-2018. Beijing: China Communications Press.
Dan, H., He, L., and Xu, B. (2017). Experimental investigation on skid resistance of asphalt pavement under various slippery conditions. Int. J. Pavement Eng. 18, 485–499. doi: 10.1080/10298436.2015.1095901
Daniels, J. W. III, Heymsfield, E., and Kuss, M. (2019). Hydronic heated pavement system performance using a solar water heating system with heat pipe evacuated tube solar collectors. Sol. Energy 179, 343–351. doi: 10.1016/j.solener.2019.01.006
Han, S., Yao, T., and Yang, X. (2019). Preparation and anti-icing properties of a hydrophobic emulsified asphalt coating. Constr. Build. Mater. 220, 214–227. doi: 10.1016/j.conbuildmat.2019.06.021
Henry, J. J. (1991). Highway de-Icing, Transportation Research Board. Special Report 235. Washington, DC: National Research Council.
Huang, S., Robertson, R. E., Branthaver, J. F., and Claine Petersen, J. (2005). Impact of lime modification of asphalt and freeze–thaw cycling on the asphalt–aggregate interaction and moisture resistance to moisture damage. J. Mater. Civil Eng. 17, 711–718. doi: 10.1061/(asce)0899-1561200517:6(711)
Li, F., and Wang, Z. (2012). Experiment on road performance of asphalt mixture with automatic long-term snowmelt agent. J. Highway Transport. Res. Dev. 6, 11–17. doi: 10.1061/jhtrcq.0000002
Lin, J., Guo, P., Wan, L., and Wu, S. (2012). Laboratory investigation of rejuvenator seal materials on performances of asphalt mixtures. Constr. Build. Mater. 37, 41–45. doi: 10.1016/j.conbuildmat.2012.07.008
Liu, X., Rees, S. J., and Spitler, J. D. (2007). Modeling snow melting on heated pavement surfaces. Part I: model development. Appl. Therm. Eng. 27, 1115–1124. doi: 10.1016/j.applthermaleng.2006.06.017
Luo, S., and Yang, X. (2015). Performance evaluation of high-elastic asphalt mixture containing deicing agent Mafilon. Constr. Build. Mater. 94, 494–501. doi: 10.1016/j.conbuildmat.2015.07.064
Mamlouk, M. S., and Dosa, M. (2014). Verification of effectiveness of chip seal as a pavement preventive maintenance treatment using LTPP data. Int. J. Pavement Eng. 15, 879–888. doi: 10.1080/10298436.2014.893318
Pan, P., Wu, S., Xiao, Y., and Liu, G. (2015). A review on hydronic asphalt pavement for energy harvesting and snow melting. Renewable Sustain. Energy Rev. 48, 624–634. doi: 10.1016/j.rser.2015.04.029
Pan, T., He, X., and Shi, X. (2008). “Laboratory investigation of acetate-based deicing/anti-icing agents deteriorating airfield asphalt concrete,” in Asphalt Paving Technology-Proceedings, Vol. 77, (Philadelphia, PA: Technical Session of the Association-of-Asphalt-Paving-Technologists), 773.
Peng, C., Zhang, H., You, Z., Xu, F., Jiang, G., Lv, S., et al. (2018). Preparation and anti-icing properties of a superhydrophobic silicone coating on asphalt mixture. Constr. Build. Mater. 189, 227–235. doi: 10.1016/j.conbuildmat.2018.08.211
Salopek, B., Krasic, D., and Filipovic, S. (1992). Measurement and application of zeta-potential. Rudarsko-geolosko-naftni zbornik 4, 147.
Stachurski, J., and MichaŁek, M. (1996). The effect of the ζ potential on the stability of a non-polar oil-in-water emulsion. J. Colloid Interface Sci. 184, 433–436. doi: 10.1006/jcis.1996.0637
Tan, Y., Hou, M., Shan, L., and Sun, R. (2014). Development of sustained release complex salt filler for asphalt pavement included salt. J. Build. Mater. 17, 256–260. doi: 10.3969/j.issn.1007-9629.2014.02.013
Tan, Y., Sun, R., Guo, M., Zhong, Y., and Zhou, S. (2013). Research on deicing performance of asphalt mixture containing salt. China J. Highw. Transp. 26, 23–29. doi: 10.19721/j.cnki.1001-7372.2013.01.004
Tan, Y., Zhang, C., Xu, H., and Tian, D. (2019). Snow melting and deicing characteristics and pavement performance of active deicing and snow melting pavement. China J. Highw. Transp. 32, 1–17. doi: 10.19721/j.cnki.1001-7372.2019.04.001
Tan, Z. (2018). Research On Hardening Process and Hardening Mechanism of Cement Asphalt Composite Binder. D. Harbin: Harbin Institute of Technology.
Tang, X., Jiao, S., Gao, Z., and Xu, X. (2008). Study of 5.8 GHz magnetron in microwave deicing. J. Electromagnet. Wave. 22, 1351–1360. doi: 10.1163/156939308786348901
Tian, D. (2019). Preparation Technology and Applied Research of Anti-Icing Glutinous Emulsified Asphalt. D. Harbin: Harbin Institute of Technology, doi: 10.27061/d.cnki.ghgdu.2019.001640
Waluś, K. J. (2017). “Driver’s strategy and braking distance in winter,” in Transport Means, Proceedings of 21st International Scientific Conference (Juodkrantė), 20–22.
Wang, H., Zhao, J., and Chen, Z. (2008). Experimental investigation of ice and snow melting process on pavement utilizing geothermal tail water. Energy Convers. Manag. 49, 1538–1546. doi: 10.1016/j.enconman.2007.12.008
Wang, Z., Zhang, T., Shao, M., Ai, T., and Zhao, P. (2017). Investigation on snow-melting performance of asphalt mixtures incorporating with salt-storage aggregates. Constr. Build. Mater. 142, 187–198. doi: 10.1016/j.conbuildmat.2017.03.070
Yehia, S., and Tuan, C. Y. (1999). Conductive concrete overlay for bridge deck deicing. Mater. J. 96, 382–390.
Zheng, M., Wu, S., Wang, C., Li, Y., Ma, Z., and Peng, L. (2017). A study on evaluation and application of snowmelt performance of anti-icing asphalt pavement. Appl. Sci. 7, 583. doi: 10.3390/app7060583
Keywords: emulsified asphalt binder, anti-icing filler, coating, road surface anti-icing, performance
Citation: Shan L, Yang H, Tian D and Tan Y (2020) Evaluation of Anti-icing Emulsified Asphalt Binders. Front. Mater. 7:257. doi: 10.3389/fmats.2020.00257
Received: 25 March 2020; Accepted: 14 July 2020;
Published: 11 August 2020.
Edited by:
Huisu Chen, Southeast University, ChinaReviewed by:
Dawei Wang, RWTH Aachen University, GermanyQuantao Liu, Wuhan University of Technology, China
Copyright © 2020 Shan, Yang, Tian and Tan. This is an open-access article distributed under the terms of the Creative Commons Attribution License (CC BY). The use, distribution or reproduction in other forums is permitted, provided the original author(s) and the copyright owner(s) are credited and that the original publication in this journal is cited, in accordance with accepted academic practice. No use, distribution or reproduction is permitted which does not comply with these terms.
*Correspondence: Yiqiu Tan, eWlxaXV0YW5AMTYzLmNvbQ==