- 1The Key Laboratory of Road and Traffic Engineering, Ministry of Education, Tongji University Shanghai, Shanghai, China
- 2Inner Mongolia road and Bridge Group Co., Ltd., Hohhot, China
Emulsified asphalt cold recycled mixture is commonly used in the upper base course of expressway reconstruction asphalt pavement. When the following layer is paved with hot-mix asphalt (HMA) mixture, the aging asphalt in the recycled material is activated due to the temperature conduction effect of the HMA mixture, so that the cold recycled layer produces “secondary thermal compaction” under the action of a roller. Based on this phenomenon, the present study aimed to discuss the influence of different molding methods and mixing processes on the volume parameters and mechanical properties of cold recycled emulsified asphalt mixture. The influences of Marshall compaction times, gyratory compaction times, curing time, and specimen-forming temperature on the voids and splitting strength of cold recycled mixture were studied. The field core sample was compared with the laboratory-forming method, which accords with the field compaction condition of the cold recycled upper base. first-time compaction number of large Marshall is 150 times and secondary compaction number is 75 times (Shorthand for 150 + 75), the compaction times of the gyratory specimen is “30 + 15.” The curing time of the cold recycled mixture should not exceed 3 h and should not be constructed in low-temperature weather to ensure the quality of pavement construction. The use of a new stage and step laboratory mixing process simulating the plant mixing, compared with the traditional mixing process, increases the splitting strength by at least 13%.
Introduction
Emulsified asphalt cold recycling technology is one of the recycling technologies of asphalt pavement. The mixing, transportation, and rolling of cold recycled mixture are carried out under normal temperatures and have the advantages of low carbon emission, convenient construction, and high-cost performance. It is more widely used in the reconstruction, expansion, maintenance, and repair of roads and other projects (Sondag et al., 2002; Xiao et al., 2018; Zhu et al., 2019). The reasonable design method and laboratory molding process of cold recycled mixture are the bases of the successful application of Emulsified asphalt cold recycling technology (Lu, 2001; National Cooperative Highway Research Program, 2007). In this regard, scholars at home and abroad have conducted a lot of research and practice on the application of a cold recycled mixture and put forward some constructive theories and design methods, such as the Marshall method modified by AASHTO, Asphalt Recycling and Reclaiming Association (ARRA) design method, California method, AI method, Pennsylvania method, Oregon design method, widgets design method, and South Africa design method (Epps, 1995; Asphalt Recycling and Reclaiming Association [ARRA], 1996, 2001; Sondag et al., 2002; Asphalt Academy, 2009; Wirtgen, 2010). Lee et al. (2003) believed that the Marshall compaction method could not simulate the compaction effect of the field road compaction machinery, and proposed to use the gyratory compactor to compact and form a cold recycled mixture. Moghadam and Mollashahi (2017) thought that when the particle size was larger than 25 mm, a significant difference in the mechanical properties and water stability was found between the 4-inch and 6-inch specimens. Guo compared the Marshall compaction test with the gyratory compaction test and showed that the voids of the Marshall compaction specimen were basically the same as that of 40 50 times of gyratory compaction specimen (Guo, 2013). Wei et al. (2019) used the gyratory compaction test method to design the mix proportion of cold recycled mixture and improved the performance of cold recycled mixture by changing the times of gyratory compaction and the molding temperature of the specimen. Li et al. (2017) used the vibration method to form the specimen, and analyzed the voids of the specimen under different forming methods with the aid of computed tomography detection means, and concluded that the essential reason affecting the mechanical properties of cold recycled mixture was the characteristics of voids.
The results of the aforementioned research undoubtedly promoted the development of cold-recycling technology and laid a good foundation for the application of the subsequent cold recycled mixture. In 2007, Prof. Sun’s group of Tongji University discovered the phenomenon of “secondary thermal compaction” for the first time (Jiang et al., 2008; Xu et al., 2013). The complete compaction process of the asphalt cold recycled upper base mixture is as follows: first, the cold recycled upper base is compacted at normal temperature when it is paved, and then the cold recycled layer is thermally compacted using the rolling machine when the hot recycled asphalt mixture is paved (Yang, 2010; Xu et al., 2013). However, the existing methods at home and abroad do not consider the secondary compaction process of the cold recycled upper base mixture, which results in the poor matching of volume parameters and mechanical properties between laboratory and field core samples. The second compaction temperature of the cold recycled upper base is much higher than that of the first compaction (Jiang, 2012). According to the test data of the voids of the cold recycled upper base core samples before and after HMA paving in the Chang-Jiu expressway reconstruction and expansion project, it was found that the voids of the recycled layer were reduced by about 3% by the secondary thermal compaction. Then, taking the voids of core samples before and after HMA paving as the control index, the previous study of Sun’s group showed that the laboratory small Marshall compaction for 100 times + the second thermal compaction for 50 times could simulate the field compaction condition of the cold recycled upper base. However, the large-sized cold recycled mixture needs a larger-sized specimen for simulation. At present, gyratory compaction is the most common method of laboratory-forming. In addition, in the mechanical parameter tests of mixtures (such as modulus, compressive strength, uniaxial penetration test, and so forth), the size of the specimen is required, but the small Marshall specimen cannot meet the test requirements, the size of the small Marshall is Φ101.5 mm × 63.6 mm. Therefore, it is necessary to study the secondary forming method of laboratory large Marshall specimens and gyratory compaction specimens. The transportation of a cold recycled mixture from the mixing plant to the construction site takes some time. The cold recycled mixture, if placed for a long time, has a significant impact on the construction performance, compaction effect, and stability of the mixture. The study of curing time, forming temperature, and laboratory mixing process of a cold recycled mixture is essential. Therefore, on the basis of the previous research (Yang, 2010; Xu et al., 2013) on the “secondary thermal compaction” process, this study investigated the laboratory mixing and forming process of emulsified asphalt cold recycled mixture, which simulated the actual mixing and forming process.
Principle of Secondary Compaction of the Emulsified Asphalt Cold Recycled Upper Base Mixture
One of the important aspects of the asphalt cold recycled upper base mixture, which is different from the common hot asphalt mixture, is that it generally has two compaction processes. After the asphalt cold recycled upper base mixture is paved, the timely rolling of the roller is the first compaction process of the cold recycled layer, commonly known as normal temperature compaction process. This process needs to be completed before the complete demulsification of emulsified asphalt; otherwise, the demulsification of emulsified asphalt may cause the asphalt cold recycled upper base mixture to form a hard shell, making the compaction more difficult. The second compaction of the cold recycled upper base occurs in the construction process of the layer of the hot-mix asphalt (HMA) mixture. After completing the construction of the cold recycled layer, the cold recycled upper base needs to be cured for 3–7 days before the HMA is paved because, among other reasons, the water generated by the emulsion breaking of the emulsified asphalt has to be evaporated. Moreover, when the HMA layer is paved, the baking effect of the HMA mixture (paving temperature up to 160°C) also increases the temperature of the cold recycled upper base. When the layer of HMA is rolled, the temperature of the cold recycled upper base increases to nearly 60°C. The influence of HMA on the temperature distribution of the cold recycled layer is shown in Figure 1. The test result was obtained by Sun’s group through embedding temperature sensors in a large number of cold regeneration field projects (Yang, 2010; Xu et al., 2013). The 60°C is the softening point of aged asphalt. When the temperature increases, the aging asphalt in the cold recycled mixture is reactivated and softened. This phenomenon is more pronounced during summer construction. Compared with the normal temperature state, the mixture is more likely to be compacted. The second compaction effect of the roller on the cold recycled layer is obvious. The voids of the cold recycled upper base after the second thermal compaction were reduced by 2–3% (Jiang et al., 2008; Yang, 2010; Xu et al., 2013). Current research shows that the compaction effect of the cold recycled mixture is related to the thickness and temperature of the HMA layer and cold recycled layer, as well as the rolling technology (Zheng et al., 2016; People’s Communications Press, 2019). Considering the secondary thermal compaction process in the design of cold recycled mixture, the amount of emulsified asphalt can be reduced, which is of great economic value. The performance of cold recycled mixture will also be greatly improved, which could replace the asphalt concrete layer and be used in heavy traffic conditions, and even play the role of hot asphalt mixture (Yang, 2010; Xu et al., 2013).
Materials and Test Scheme
Materials
Emulsified Asphalt
The specific indexes of emulsified asphalt used in this test are shown in Table 1.
RAP and New Aggregate
The RAP source used in this study was the old asphalt surface milling material of an expressway reconstruction and expansion project, which was divided into three grades: 0–5, 5–10, and 10–30 mm; and the new aggregate was limestone, with a specification of 10–20 mm. The bituminous pavement had been used for 12 years before milling, and AH-70 asphalt was used. The asphalt content of RAP was 3.92%. Three indexes of asphalt were tested, the penetration at 25°C was 41.4 (0.1 mm), softening point was 55.4°C, and ductility at 15°C was 23.2 cm.
Mineral Powder, Cement, and Water
Mineral powder and cement were produced by a material company in the Jiangxi Province, and their technical indicators met the technical specifications for the construction of highway asphalt pavement (JTG F40-2004) of China; tap water was used as water.
Gradation, Optimum Moisture Content, and Optimum Emulsified Asphalt Content
The composition of recycled mixture was as follows: RAP (0–5 mm): RAP (5–10 mm): RAP (10–30 mm): new aggregate (10–20 mm): mineral powder = 26: 20: 40: 12: 2; the cement content was 1.5%. The optimum moisture content determined by the compaction test recommended in the technical code for road asphalt pavement regeneration and code for highway geotechnical test was 3.8%. According to the China’s regeneration standard (People’s Communications Press, 2019), the optimal amount of emulsified asphalt was 3.5% using splitting strength and voids as control indexes.
Test Scheme
Effect of Different Molding Methods on Voids and Splitting Strength of Cold Recycled Mixture
A marshall compactor and gyratory compactor were used to form a large Marshall specimen and a gyratory compaction specimen, respectively. The specimens were compacted (rotated) for the first time and compacted (rotated) for the second time. The size of the large Marshall specimen was Φ152.4 mm × 94.5 mm, and the size of the gyratory specimen was Φ100 mm × 63.5 mm.
For the large Marshall specimens, in the test code for asphalt and asphalt mixture of highway engineering, it is mentioned that the number of compaction of large Marshall specimens is 112, corresponding to the 75 of the small Marshall standard (Ministry of transport of the people’s Republic of China, 2011), the weight of the small Marshall compactor was 4536 g, the falling distance of the hammer was 457 mm, and the size of the specimen was 101.5 × 63.6 mm2. Moreover, the weight of the large Marshall compactor was 10,210 g, the falling distance of the hammer is 457 mm, and the size of the specimen was 152.4 × 94.5 mm2. For the work on a unit volume of a single specimen, the work done by a small Marshall specimen in one compaction is about 1.5 times of that of a large Marshall specimen. Therefore, in order to find the appropriate compaction times of large Marshall specimens, the compaction work per unit volume of small Marshall specimens was referred. The number of the first-time compactions were designed to be 75, 112, 150, and 187. The large Marshall specimens with similar voids after the initial compaction of the cold recycled upper-base pavement were selected to determine the appropriate number of the first-time compaction. The number of second-time compactions were designed to be 15, 40, 75, and 100 considering the actual compaction work. After the first-time compaction, the specimens with mold were placed in the laboratory for 24 h at room temperature, and then placed in the Drying Oven (60°C) for 48 h, and finally compacted for the second-time. After the samples were formed, the voids and splitting strength were measured. And it was compared with the voids and splitting strength after the primary compaction of the cold recycled upper base and after the layer of HMA were paved and compacted.
For the gyratory specimens, the number of first-time gyrations were designed to be 20, 30, 50, 75, 100, and 150. The specimens with similar voids after the initial compaction of cold recycled upper base pavement were selected to determine the appropriate number of first-time gyratory compactions. On this basis, the number of second-time gyrations were designed to be 5, 10, 15, and 25 considering the actual compaction work. The pressure of the gyratory compactor was controlled by 600 MPa, and the gyratory angle was 1.16°. The curing conditions of the specimens after the first-time gyrations was the same as that of the large Marshall specimen. After the samples were formed, the voids and splitting strength were measured and compared with the voids and splitting strength after the first compaction of a field cold recycled upper base pavement and the compaction of the upper HMA.
Effect of Different Curing Times and Temperatures on Voids and Splitting Strength of Cold Recycled Mixture
The cold recycled mixture was placed in the boxes (constant temperature and humidity) at 5, 15, 25, and 35°C and maintained for 0, 1, 2, and 3 h until the small Marshall specimens were, respectively, formed 6 h later, and the number of compaction was “100 + 50” (after 100 times of compaction, the side of the specimen with the mold was put into a 60°C air blast oven for curing for 48 h, and the specimen with the mold was taken out from the oven and immediately put into the Marshall compactor 50 times on both sides). After the sample was formed, the voids and splitting strength were measured, and the effects of different molding temperatures and curing time on the voids and splitting strength of cold recycled mixture were compared.
The Influence of Laboratory Mixing Technology on Voids and Splitting Strength of Cold Recycled Mixture
At present, the laboratory mixing process of the cold recycled mixture in China is basically fixed. The recommended mixing process is shown in Figure 2, which is defined as the traditional mixing process. The improved mixing process is shown in Figure 3, which is defined as the new mixing process. The traditional mixing process includes the following steps: (1) the RAP material prepared according to the design proportion was added to the mixer; (2) water was added according to the calculated amount of water and mixed evenly for 60 s; (3) emulsified asphalt was added according to the calculated amount of emulsified asphalt and mixed evenly for 60 s. The new mixing process includes the following steps: (1) RAP (10–30 mm), new aggregate (10–20 mm), water (1/3 of the external water), and emulsified asphalt (1/2 of the total amount) were added to the mixing pot according to the design proportion and mixed for 45 s; (2) fine RAP (0–5 mm), medium RAP (5–10 mm), mineral powder, cement, water (1/3 of the external water), and the asphalt (one half of the total amount) were added to the mixing pot according to the design proportion and mixed for 45 s; (3) water (one third of the external water) was added to the mixing pot and mixed for 30 s.
Two mixing processes were used to mix emulsified asphalt cold recycled mixture, and then small Marshall specimens were formed indoors. In this study, the small Marshall specimens were all shaped twice, and the number of compactions were “100 + 50.” The curing conditions of the specimens was the same as that of the large Marshall specimen. After the specimens were formed, the voids and splitting strength were measured, and the voids and splitting strength of the specimens formed in the cold recycled mixture chamber under the traditional mixing process and the new mixing process were compared.
All the data in this paper are the averages of the test data of six parallel specimens tested by the Grubbs method. The Grubbs test is one of the statistical methods to test outliers. In the statistical calculation method of eliminating outliers, the Grubbs test is not only applicable to the abandonment of one or more suspicious values in a group of data, but also applicable to the limited number of determinations. It is the most reliable test method for the determination of suspicious values (Adikaram et al., 2015).
Test Results and Analysis
Effect of Different Forming Methods on Voids and Splitting Strength of Cold Recycled Mixture
Formation of large Marshall specimens
The test results of the voids and splitting strength of large Marshall specimens under the first-time compaction and before paving HMA in the test section of the cold recycled upper base course are shown in Figure 4A. The test results of voids and splitting strength of specimens under second-time compaction and after paving HMA in the test section of the cold recycled upper base course are shown in Figure 4B. FCS and ACS represent the core samples before and after the HMA was paved on the cold recycled upper base.
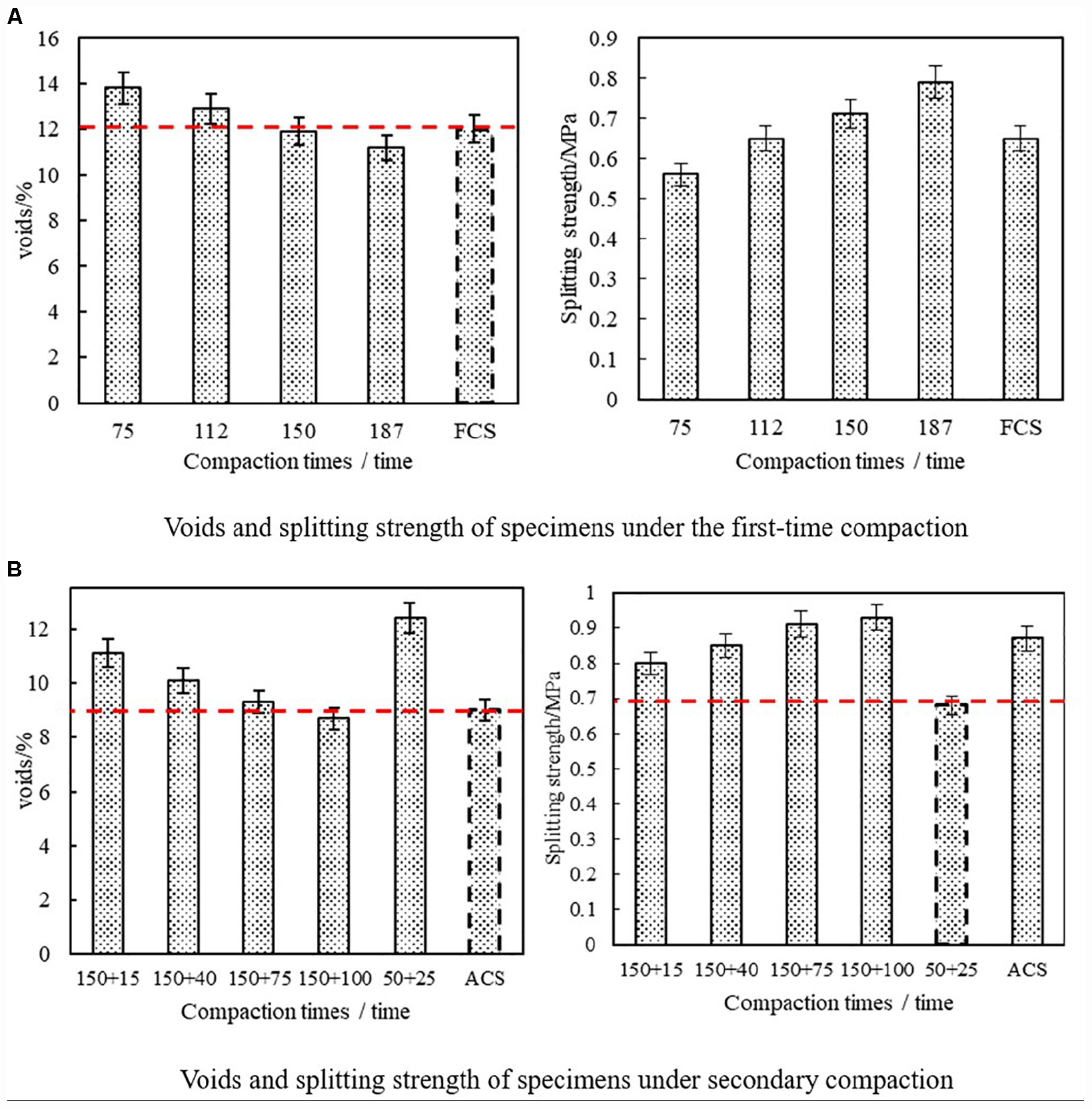
Figure 4. Voids and splitting strength of large Marshall specimens under different compaction times: (A) voids and splitting strength of specimens under the first-time compaction; (B) voids and splitting strength of specimens under secondary compaction.
Figure 4A shows that the voids of laboratory specimens decreased with an increase in compaction times. When the large Marshall specimen was compacted 150 times, the voids were 11.9%. Before paving HMA, many core samples in the field were drilled and the volume parameters were tested. The results show that the voids of core samples were 12% ± 0.7% in the 95% confidence interval (This is basically consistent with the core sample test results accumulated by the Sun group in different cold regeneration field projects) (Yang, 2010; Xu et al., 2013). Therefore, it was concluded that the laboratory large Marshall specimen was compacted 150 times. The voids of the specimen were similar to that of the field cold recycled upper base course pavement after the initial compaction at room temperature. This indicated that the 150 times compaction of the laboratory large Marshall specimen could simulate the initial compaction state of the cold recycled upper base course pavement after paving on the site. This compaction level was equivalent to the 100 times compaction of laboratory small Marshall specimens, which could simulate the initial compaction state of the cold upper base course pavement after paving on the site. The reason for this phenomenon was that China’s standard Marshall test method was established in the early 1980s and adapted to the compaction level (rubber roller was lower than 20t, vibration roller was 2–6t, and double-wheel steel cylinder roller was 6–8t) and traffic conditions at that time. The laboratory compaction times recommended in the technical code for the recycling of highway asphalt pavement refer to the standard Marshall test method. The current Marshall standard compaction work has lagged behind the production practice with the improvement in the technology level, compaction machinery level (generally, 10–14t vibrating roller and 25–30t rubber wheel roller) and the development of modern traffic in the construction work. Therefore, the number of compactions of large Marshall specimens in first-time laboratory forming should be 150.
Figure 4B shows that after the completion of the first compaction, the second compaction was carried out in real time, and the voids of the specimen decreased with the increase in the second compaction. When the large Marshall specimen was compacted 75 times, the voids of the specimen were 9.3%. The voids of the specimen were 9.0% measured from the core sample drilled from the site after the HMA was paved on the cold recycled upper base pavement. Therefore, it was concluded that the voids of laboratory large Marshall specimen after compaction for “150 + 75” times was similar to that of the cold recycled upper base pavement after the HMA was paved and compacted, so that the laboratory large Marshall specimen compaction for “150 + 75” times could simulate cold-recycling on-site compaction state of raw road surface after the HMA was paved. The reason for this phenomenon was that when the asphalt cold recycled mixture was used as the upper base course of the road, two compaction processes occurred: after the cold recycled asphalt mixture was paved, the compaction of the normal-temperature mixture under the action of the roller was the first compaction process of the cold recycled upper base course, called the normal-temperature compaction (or cold compaction) process. When the HMA have been spread, the paved HMA had a further heating effect on the cold recycled upper base due to its high temperature, causing the cold recycled layer to reach a higher temperature, thereby reactivating and softening the old asphalt in the mixture. The obvious second compaction process occurred under the action of the roller, called the thermal compaction process. The first compaction was carried out for the laboratory-formed specimens, and the second compaction was carried out after 48-h curing in an oven at 60°C, which to some extent simulated the two compaction processes of the cold recycled upper base. Therefore, the compaction times of large Marshall specimens should be “150 + 75” times to better simulate the compaction condition of the field. However, the type and tonnage of the roller used in different practical projects and the compaction work during construction may be different, leading to the difference in the voids of the cold recycled mixture. Hence, the conclusions need to be confirmed in the future.
Figure 4 shows the splitting strength of the large Marshall specimens compacted 150 times and “150 + 75” times were roughly the same as that of the core samples before and after the HMA was paved on the cold recycled upper base course. However, the splitting strength of the small Marshall specimens was less than 0.7 MPa, which was far lower than that of the field core samples by adopting the method recommended in the technical code for road asphalt pavement regeneration. The splitting strength (0.9 MPa), which was basically the same as the aforementioned voids phenomenon, showed that the large Marshall specimens compacted 150 times and “150 + 75 times” could better simulate the compaction mechanism and mechanical properties of the cold recycled upper base pavement.
Formation of gyratory compaction specimens
The test results of voids and splitting strength of gyratory specimens under first-time gyratory compaction are shown in Figure 5A. The test results of voids and splitting strength of specimens under secondary gyratory compaction are shown in Figure 5B.
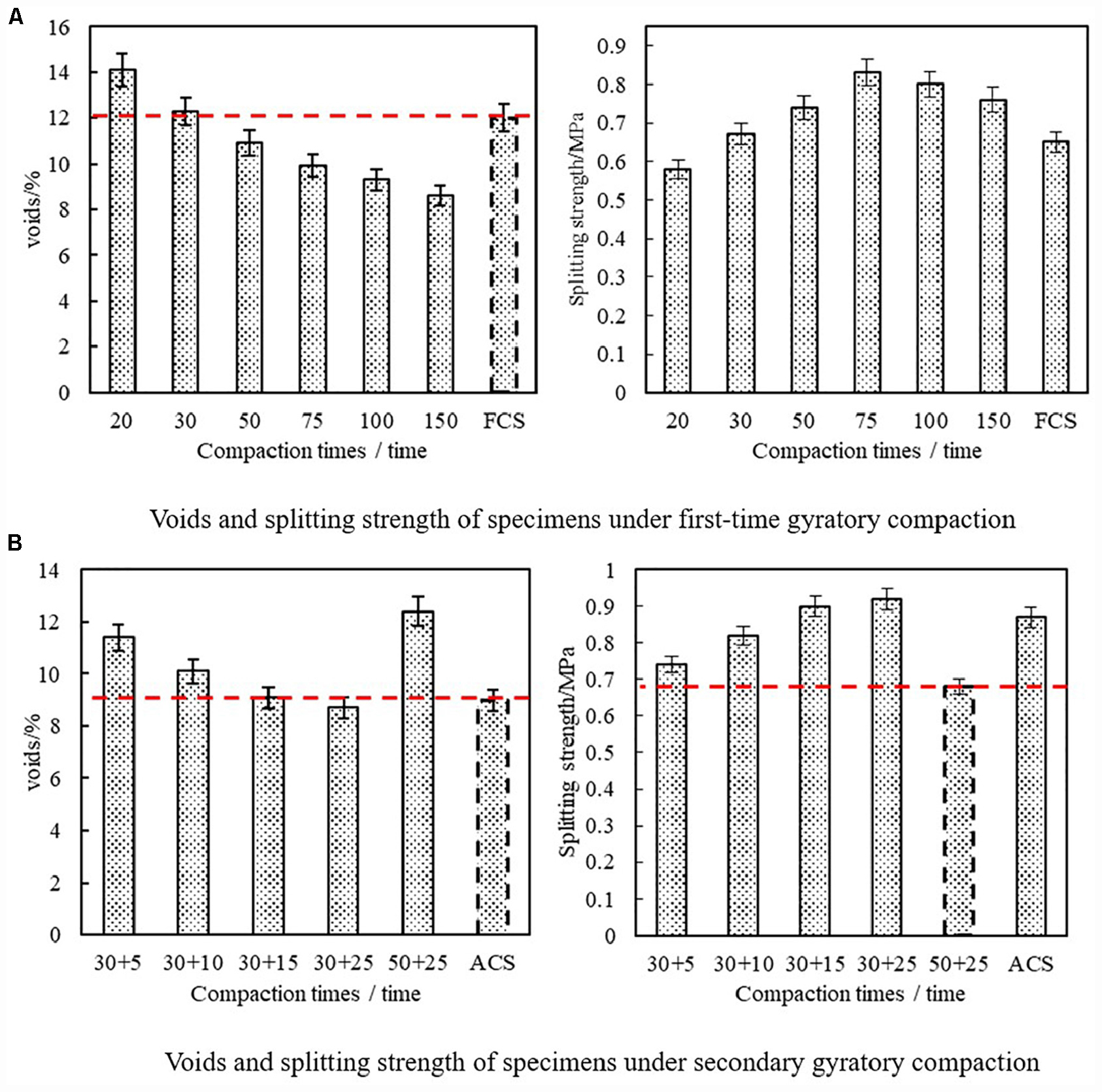
Figure 5. Voids and splitting strength of specimens under different times of gyratory compaction: (A) voids and splitting strength of specimens under first-time gyratory compaction; (B) voids and splitting strength of specimens under secondary gyratory compaction.
Figure 5A shows that the voids of the laboratory specimen decreased with the increase in compaction times. When the gyratory compaction specimen rotated 30 times, the voids of the specimen were 12.3%. Before paving HMA, many core samples in the field were drilled and the volume parameters were tested. The results show that the voids of core samples were 12% ± 0.7% in the 95% confidence interval (This is basically consistent with the core sample test results accumulated by the Sun group in different cold regeneration field projects) (Yang, 2010; Xu et al., 2013). Therefore, it was concluded that the laboratory gyratory compaction specimen rotated 30 times, and the voids of the specimen were similar to that of the field cold recycled upper base pavement after the initial compaction at room temperature, indicating that the compaction specimen rotated 30 times, simulating the initial compaction state after the cold recycled upper base pavement was paved on the site. Therefore, the number of rotations of the laboratory first-time-forming gyratory compaction specimen should be 30.
Figure 5B shows that after the first compaction, the second compaction was carried out in real time, and the voids of the specimen decreased with the increase in the second compaction. When the rotating compaction specimen rotated 15 times, the voids of the specimen was 9.1%. The small Marshall specimen was double-sided compacted 50 times and then double-sided compacted 25 times after the completion of the curing, as recommended in the technical code for road asphalt pavement regeneration. The voids of the specimen were 12.4%. The voids of the specimen were 9.0% as measured from the core sample drilled from the site after the HMA was paved on the cold recycled upper base course pavement. Therefore, it was concluded that the voids of the laboratory gyratory compaction specimen after rotating “30 + 15” times were similar to that of the cold recycled upper base pavement after the HMA was paved and compacted. The conclusion was consistent with the discussion in “Formation of large Marshall specimens.”
Figure 5 shows that the splitting strength of 30 times of compaction and 30 + 15 times of gyratory compaction specimen were roughly the same as that of the core samples before and after the HMA was paved on the cold recycled upper base course, indicating that the forming mode of 30 times of compaction and 30 + 15 times of gyratory compaction specimen could better simulate the compaction mechanism and mechanical properties of the cold recycled upper base course pavement. In addition, the voids of the gyratory compaction specimen (100 times of compaction) were similar to that of the gyratory compaction specimen (30 + 15 times of compaction), but the splitting strength was different to some extent. This was mainly because a large amount of excess water in the specimen flowed out in the process of the specimen formed by 100 times of rotation at one time due to the extremely dense gyratory compaction, accompanied by the loss of more emulsified asphalt. As a result, the asphalt solid content of the 100 times rotated specimens decreased, thereby decreasing the splitting strength.
Effect of Curing Time and Temperature
The cold recycled mixture after laboratory mixing was placed in boxes (constant temperature and humidity) at 5, 15, 25, and 35°C and maintained for 0, 1, 2, and 3 h until the small Marshall specimens were formed 6 h later. The test results of voids and splitting strength of the formed small Marshall specimens are shown in Figure 6.
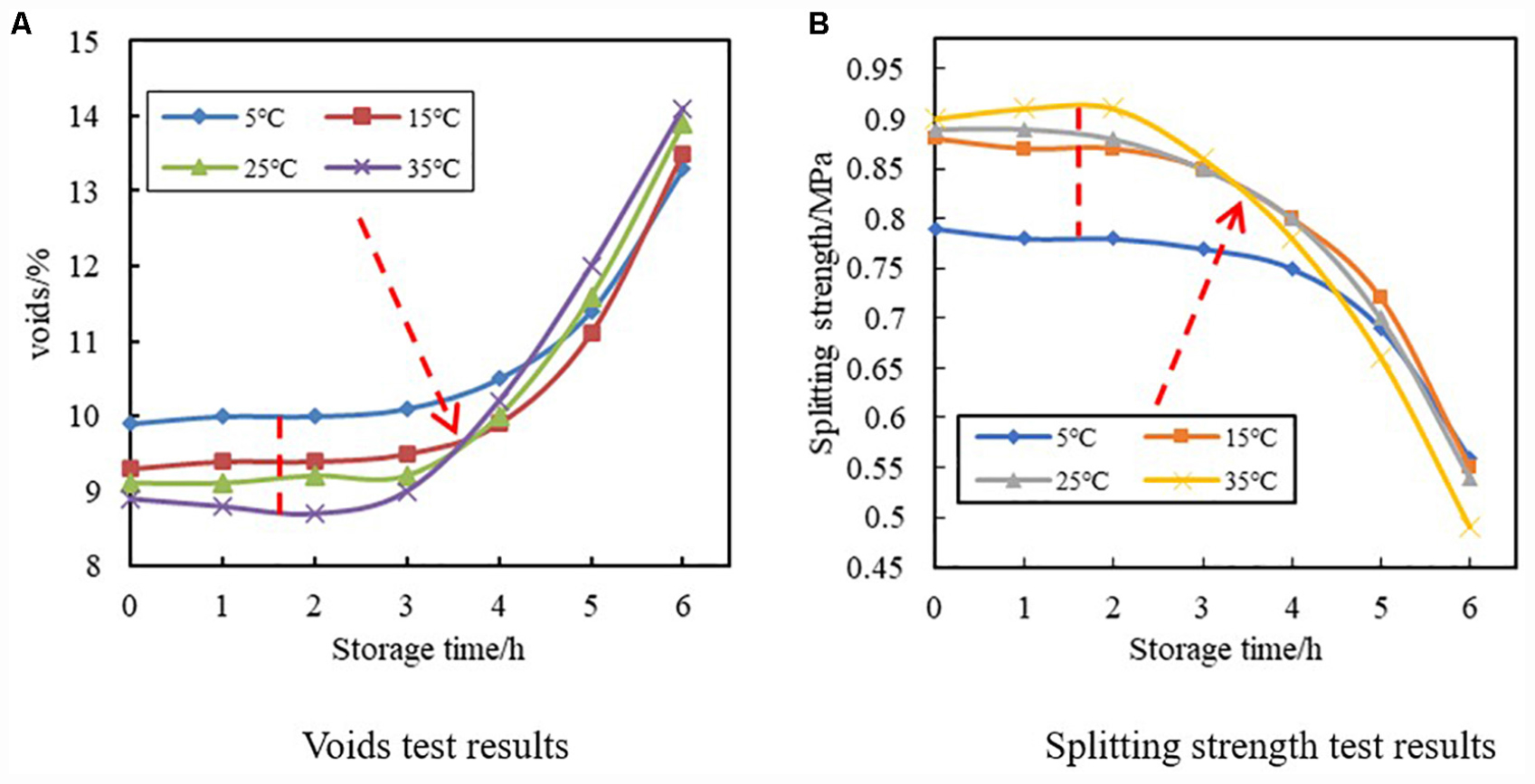
Figure 6. Voids and splitting strength of cold recycled mixture under different molding temperature and curing time: (A) voids test results; (B) splitting strength test results.
Figure 6 shows that the voids of the formed specimen first remained unchanged and then presented a gradually increasing trend at 5, 15, 25, and 35°C with the extension of cold recycled mixture placing time, while the splitting strength first remained unchanged and then presented a gradually decreasing trend. When the cold recycled mixture was placed for 3 h, the voids and splitting strength of the specimen did not change. After 3 h, the voids and splitting strength of the cold recycled mixture at 35°C first changed, then the voids and splitting strength of the cold recycled mixture at 25, 15, and 5°C changed in turn, and with the extension of the curing time, the voids and splitting strength changed. A growing trend of change was noted. This was because the emulsified asphalt gradually began to demulsify with the extension of the curing time. The emulsified asphalt after demulsification selectively adhered to the fine materials in the aggregate to form the mastic micelle, which was difficult to be compacted in the forming process. Therefore, it presented more porosity and less splitting strength. The demulsifying time of emulsified asphalt was related to the temperature during the forming process. Because the higher the temperature, the more intense the Brownian motion of the molecule, and the greater the probability of the asphalt particles colliding with each other, the more unstable the emulsified asphalt, and the more likely it is to break the emulsion. Therefore, the voids of the cold recycled mixture at 35°C began changing first during the specimen-forming process. Therefore, from the engineering point of view, the cold recycled mixture should be transported to the construction site and spread as soon as possible after mixing in the mixing plant. When the construction is carried out in high-temperature and extreme weather, the transportation distance should be shortened and the spreading and rolling speed of the mixture should be accelerated so as to improve the compactness and strength of the pavement.
New Laboratory Mixing Process for Emulsified Asphalt Cold Recycled Mixture
The test results of voids and splitting strength of cold recycled mixture under different mixing processes are shown in Figure 7. The results of t-test analysis are shown in Table 2.
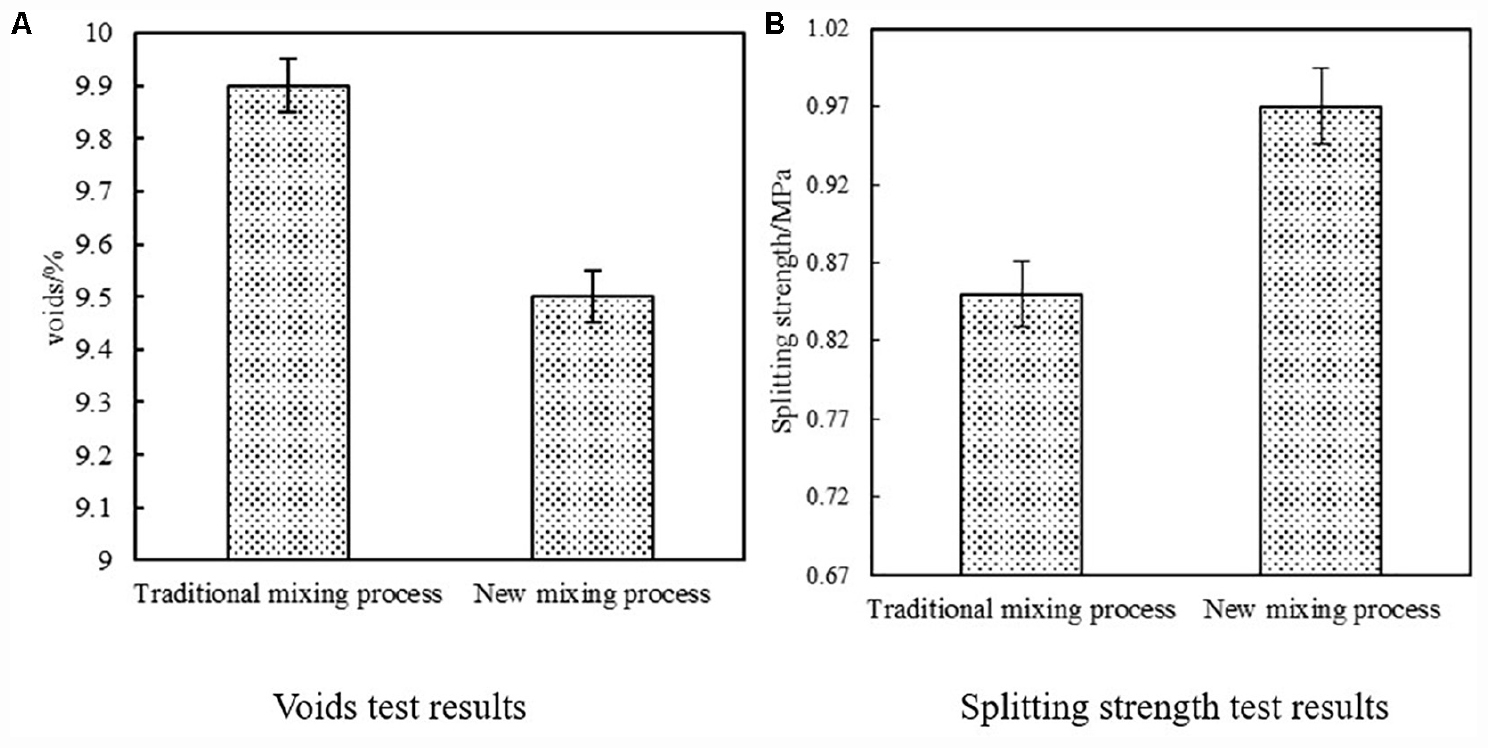
Figure 7. Test results of the voids and splitting strength of cold recycled mixture under different mixing processes: (A) voids test results; (B) splitting strength test results.
Figure 7 shows that for the cold recycled mixture under the traditional mixing process, the voids of the twice-formed Marshall specimen were 9.9%, the splitting strength was 0.85 MPa, the voids of the formed specimen under the new mixing process were 9.5%, and the splitting strength was 0.97 MPa. Using SPSS statistical software, the voids and splitting strength test results under different mixing processes are analyzed by t-test, the significance (2-tailed) is less than 0.05. It can be seen from the test results of independent samples that different mixing processes have significant differences in voids and splitting strength. From the test results in Figure 7, compared with the traditional mixing process, the new mixing process had higher strength; the splitting strength increased by at least 13%. This was because the new mixing process adjusted with the sequence of aggregate addition: first, the RAP (10–30 mm) and the new aggregate (10–20 mm) were put into the mixing pot; then the fine material, the intermediate material, the ore powder, and the cement were added; water and emulsified bitumen were added separately to make the mixing of the mixture more complete, thus improving the uniformity of the emulsified asphalt on the surface of different aggregates. In addition, the coating effect of aggregates and emulsified asphalt significantly improved. Therefore, the strength of laboratory-formed specimens of the mixture was relatively large. For the conclusion that the new mixing process can improve the compaction and splitting strength, we will use more RAPs from different projects to further verify this in the future.
Conclusion
The construction process of the cold recycled upper base included the normal-temperature compaction and secondary thermal compaction. The conclusions of this study on the influence of different laboratory molding methods, molding temperature, curing time, and molding process on the volume parameters and mechanical properties of emulsified asphalt cold recycled mixture were as follows:
(1) The paper puts forward that the compaction times of the laboratory large Marshall specimen was “150 + 75” and that of the gyratory compacted specimen was “30 + 15,” which could accurately simulate the field compaction conditions of the cold recycled upper base pavement.
(2) The curing time and forming temperature of emulsified asphalt cold recycled mixture greatly influenced the compactness and strength of the mixture. The longer the curing time and the lower the compaction temperature, the more difficult the mixture was to be compacted and the lower the pavement strength.
(3) Compared with the traditional mixing process, the new mixing process exhibited higher strength. The splitting strength of the new mixing process increased by at least 13%.
Data Availability Statement
The raw data supporting the conclusions of this article will be made available by the authors, without undue reservation, to any qualified researcher.
Author Contributions
LL and LS: study conception and design. ZH, GZ, and PW: data collection. LL, LS, and ZH: analysis and interpretation of results. LL and ZH draft manuscript preparation. All authors reviewed the results and approved the final version of the manuscript.
Funding
This research was supported by the National Natural Science Foundation of China (No. 51978521).
Conflict of Interest
PW was employed by the company Inner Mongolia road and Bridge Group Co., Ltd.
The remaining authors declare that the research was conducted in the absence of any commercial or financial relationships that could be construed as a potential conflict of interest.
Acknowledgments
We gratefully acknowledge the financial support.
References
Adikaram, K. K. L. B., Hussein, M. A., Effenberger, M., and Becker, T. (2015). Data transformation technique to improve the outlier detection power of grubbs’ test for data expected to follow linear relation. J. Appl. Math. 2019, 1–9. doi: 10.1155/2015/708948
Asphalt Academy (2009). Technical Guideline : Bitumen Stabilized Materials a Guideline. Lexington, KY: Asphalt Academy.
Asphalt Recycling and Reclaiming Association [ARRA] (1996). Mixture and Structural Design of Cold Recycled Pavements. Annapolis, MD: Asphalt Recycling and Reclaiming Association.
Asphalt Recycling and Reclaiming Association [ARRA] (2001). Basic Asphalt Recycling Manual. Annapolis, MD: Asphalt Recycling and Reclaiming Association (ARRA).
Epps, J. A. (1995). Cold-Recycled Bituminous Concrete Using Bituminous Materials. Washington, DC: Transportation Research Board
Guo, C. (2013). Mix Proportion Technology and Road Performance of Emulsified Asphalt Cold Recycled Mixture for Asphalt Pavement. Tongji University, Shanghai. (In Chinese).
Jiang, T. (2012). Research on some key Problems of cold Recycled Asphalt Mixture in Reconstruction of Heavy Pavement. Shanghai: Tongji University. (In Chinese).
Jiang, T., Lijun, S., Liping, L., and Bin, S. (2008). Study on composition of cold recycled upper base materials based on structural performance. J. Build. Mater. 11, 666–672. (In Chinese)
Lee, K. W., Brayton, T. E., and Harrington, J. (2003). New Mix-Design Procedure of ColdIn-Place Recycling for Pavement Rehabilitation. Transportation Research Record 954, Washington, DC: National Research Council.
Li, Z., Peiwen, H., and Zhiwu, C. (2017). Forming method of foamed asphalt cold recycling mixture. J. Compos. Mater. 34, 2038–2046.
Ministry of transport of the people’s Republic of China (2011). JTG f40-2011 asphalt and asphalt mixture test procedures. Beijing: People’s Communications Press. (In Chinese).
Moghadam, B. B., and Mollashahi, F. H. (2017). Suggesting a simple design method for cold recycled asphalt mixes with asphalt emulsion. J. Civil Eng. Manag. 23, 966–976. doi: 10.3846/13923730.2017.1343200
National Cooperative Highway Research Program (2007). Superpave Mix Design: Verifying Gyration Levels in the N-design Table. Washington, DC: National Cooperative Highway Research Program.
People’s Communications Press (2019). Technical Specifications for Highway Asphalt Pavement Recycling: JTG/5521-2019. Quitman, TX: People’s Communications Press.
Sondag, M. S., Chadbourn, B. A., and Drescher, A. (2002). Investigation of Recycled Asphalt Pavement (Rap) Mixtures. Minnesota, MN: Department of Civil Engineering University of Minnesota.
Wei, H., Xianping, B., Feiyue, W., Wei, L., and Jiao, J. (2019). Mix design of emulsified asphalt cold recycled mixture based on gyratory compaction method. J. Cent. South Univ. 26, 759–767. doi: 10.1007/s11771-019-4045-3
Xiao, F., Yao, S., Jingang, W., Xinghai, L., and Amirkhanian, S. (2018). A literature review on cold recycling technology of asphalt pavement. Constr. Build. Mater. 180, 579–604.
Xu, Y., Lijun, S., and Liping, Y. (2013). Study on design method of emulsified asphalt cold recycled mixture considering hot compaction process. Highway Eng. 38, 72–76+89. (In Chinese)
Yang, J. (2010). Study on Design method of Emulsified Asphalt cold Recycled Mixture. Shanghai: Tongji University doctoral dissertation. (In Chinese).
Zheng, G., Liping, L., and Jian, W. (2016). Study on rolling technology of emulsified asphalt cold recycling upper base. Traffic Sci. Eng. 32, 39–44. (In Chinese)
Keywords: emulsified asphalt cold recycled mixture, forming method, curing time, mixing process, splitting strength, voids
Citation: Liu L, Han Z, Wu P, Zheng G and Sun L (2020) Study on the Laboratory Mixing and Compaction Methodology of Emulsified Asphalt Cold Recycled Mixture. Front. Mater. 7:231. doi: 10.3389/fmats.2020.00231
Received: 30 March 2020; Accepted: 24 June 2020;
Published: 06 October 2020.
Edited by:
Yiqiu Tan, Harbin Institute of Technology, ChinaReviewed by:
Changjun Zhou, Dalian University of Technology, ChinaNorhidayah Abdul Hassan, University of Technology Malaysia, Malaysia
Copyright © 2020 Liu, Han, Wu, Zheng and Sun. This is an open-access article distributed under the terms of the Creative Commons Attribution License (CC BY). The use, distribution or reproduction in other forums is permitted, provided the original author(s) and the copyright owner(s) are credited and that the original publication in this journal is cited, in accordance with accepted academic practice. No use, distribution or reproduction is permitted which does not comply with these terms.
*Correspondence: Lijun Sun, bGpzdW5AdG9uZ2ppLmVkdS5jbg==