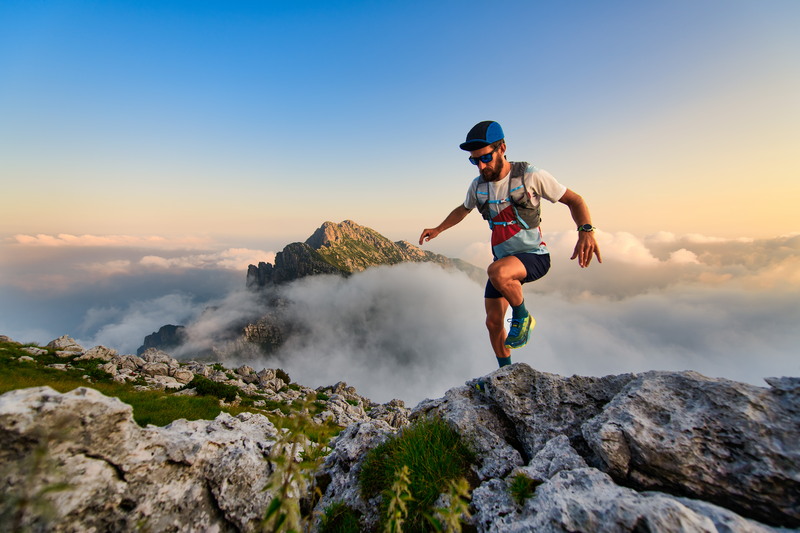
94% of researchers rate our articles as excellent or good
Learn more about the work of our research integrity team to safeguard the quality of each article we publish.
Find out more
ORIGINAL RESEARCH article
Front. Mater. , 16 April 2020
Sec. Polymeric and Composite Materials
Volume 7 - 2020 | https://doi.org/10.3389/fmats.2020.00086
Support material plays a leading role in the application of 3D printing to avoid deformation and enhance stability. This study aimed to fabricate the support structure by using hydroxypropyl methylcellulose (HPMC), which has advantages over conventional material such as low cost, low printable temperature, and high biodegradability. Once dissolved in water over gelling temperature, the HPMC based hydrogel exhibited shear-thinning behavior with decreasing apparent viscosity values at higher shear rates. The shear-dependent viscosity makes the HPMC hydrogel extrudable throughout the printing process and the printed structure stable enough without deformation. As concentration increased, apparent viscosity, and storage modulus both subsequently increased. These rheological properties indicated that the concentration of HPMC K4M hydrogel significantly influenced the printability and shape retention ability, which is associated with the mechanical strength of printed filaments. The highest concentration, 12% w/v, should have the best ability to hold the printed shape over time due to the highest G' and lowest loss tangent. The printability test also showed that K4M 12% w/v could be printed into different fill density (100, 75, and 50%) with different patterns, i.e., rectilinear and Hilbert curve. The selection of fill density and pattern both have an effect on surface roughness and porosity. The printed support material was compatible with acrylonitrile butadiene styrene (ABS), which is the material to fabricate the main structure for 3D printing. The support material made of HPMC can be easily removed by peeling off from the main structure without visible residual.
In recent years, 3D printing has been widely applied in many fields. A support structure is used to prevent the deformation or collapse caused by gravity or other external forces during the printing process (Jiang et al., 2018). As additive manufacturing is developing, it is necessary to find out a proper sacrificial support material that includes advantages such as low waste and cost. Cellulose is one of the most abundant polymers made from plants. It attracts wide attention as a biodegradable polymer in additive manufacturing fields. Cellulose derivatives are modified from cellulose by substitution of hydroxyl groups with hydroxypropyl groups and methoxyl groups using chemical reactions. Such chemical modifications improve the water solubility, thus overcome certain material limitations for the technical applications. Cellulose derivatives have been widely used as a coating material, emulsifier, thickener, binder, and filler for food and drug production (Banks et al., 2014; Ding et al., 2014); however, their usages in the area of additive manufacturing is still in its infancy.
While polylactic acid (PLA) is the most mature support materials used in Fused Deposition Modeling (FDM) 3D printing technology, cellulose-based biopolymer materials have a relatively lower cost (<10 $/kg) compared to PLA (20–30 $/kg) (Sanandiya et al., 2018; Baran and Erbil, 2019). As a thermoplastic polymer, PLA material requires a high printing temperature (180–200°C) to become printable and achieves desirable quality (Valerga et al., 2018). But the previous study demonstrated that the cellulose-based hydrogel could be printable under ambient process temperature and showed excellent shape retention ability (Polamaplly et al., 2019). Besides, cellulose-based polymers showed high degradability and dissolubility due to the behavior of hydrolytic degradation in cold water (Luo et al., 2019). Compared with cellulose polymers, it is less environmentally friendly to remove PLA supportive structure from the main structure by soaking in the chemical solution of isopropyl alcohol and potassium hydroxide (Jiang et al., 2018).
The main difference between different cellulose derivatives depends on their substituted groups. Additionally, the degree of substituted groups results in unique properties. Hydroxypropyl methylcellulose (HPMC) is one of the most common types of commercially available grades of cellulose derivatives. The hydroxypropyl group from HPMC material significantly increased the thermostability when compared with other cellulose derivatives, such as methylcellulose (MC), carboxymethyl cellulose (CMC), and hydroxyethylcellulose (HEC) (Li et al., 1999).
Currently, the field is limited by a lack of the printability test of cellulose derivatives materials which could be potentially applied as biodegradable support structure for extrusion-based 3D printing. To fill in the knowledge gap, we hypothesize the HPMC hydrogels can be 3D printed to provide mechanical support to the main structure, and then easily removed without a negative effect on the main structure quality. Our previous study indicated that the hydrogels made from HPMC K4M showed rheological properties that are suitable for 3D printing, and the printed filaments can be dissolved by water (Polamaplly et al., 2019). The aim of this paper is to investigate the viscoelastic properties and mechanical strength of HPMC K4M hydrogels with different concentrations and explore the potential of using HPMC as supportive material in the application of 3D printing technology.
HPMC K4M was provided by J. Rettenmaier USA LP (Schoolcraft, MI, United States). The degree of substitution for the methoxyl groups is 19–24%, for the hydroxypropyl groups is 4–12%. The 4M terminology indicates the viscosity of this material is in the range of 3000–5600 mPa⋅s in 2% solution at 20°C under 20 rpm. The dissolving and gelling temperatures are 25–30°C and 77°C, respectively. The aqueous solutions were prepared with 80°C water into three different concentrations: 8, 10, and 12% w/v. After cooling down to ambient temperature (25°C), all samples were centrifuged at 5000 rpm for 10 min to remove air bubbles.
The rheological properties test was carried out using Rheometer (TA Instruments Discovery HR-2, United States) with parallel geometry plates at a gap size of 1mm under ambient temperature. The flow ramp test was conducted to determine the apparent viscosity under the increased shear rate (0.1 to 100 1/s). The apparent viscosity was measured and plotted as a function of the shear rate. The oscillatory frequency sweep test was used to characterize the materials’ dynamic modulus with sweep strain increased from 1 to 100%. The rheological properties, i.e., shear rate, apparent viscosity, angular frequency, storage modulus (G'), loss modulus (G”), and loss tangent (tan δ = G”/G'), were recorded by the Trios Software (TA Instruments, United States). All rheological properties tests were conducted in triplicates.
The printability test was conducted using the extrusion-based syringe that was configured on the platform of the Velleman K8200 3D printer (Velleman Inc., Fort Worth, TX, United States). The test was designed to print geometries with different fill-in patterns, i.e., rectilinear and Hilbert curve, and densities (100, 75, and 50%). Figure 1 shows the sketch of the extrusion-based 3D printer. The printer settings were as follows: speed was 5 mm/s, nozzle diameter was 0.437 mm, extrusion multilayer was 0.05, print under ambient temperature, and the number of layers was twelve. To study the morphology and the pore structure of the printed objects, the freeze-dried HPMC K4M 12% sample (100% fill-in density with rectilinear pattern) was coated with gold (SBC-12 Sputter coater) to improve the conductivity. The SEM images were observed on JEOL (JCM-6000). The average pore size (width and length) of K4M 12% object’s surface was acquired by measuring 5 pores with image J software (version Java 1.8.0).
As shown in Figure 2A, the apparent viscosity of all the materials decreased as the shear rate increased, which means the materials behave as shear-thinning fluids (Polamaplly et al., 2019). The property of shear stress-dependent viscosity makes the HPMC gel printable through the extrusion-based printer once the applied stress exceeds the yield stress. Then the printed filament showed the shape retention ability that is associated with the high apparent viscosity after extrusion (Gunasekaran and Ak, 2000; Rao, 2014; Yang et al., 2018). The G' and G” are functions of frequency, and both gradually increased with the increasing oscillatory frequency, as shown in Figure 2B. The G' and G” used to describe the magnitude of energy stored and lost per cycle of deformation (Gunasekaran and Ak, 2000). Under the same concentration, G' is higher than G” which indicated the deformation through this material is permanently elastic or recoverable (Rao, 2014). When the concentration increased, both G' and G” increased, which indicated the strength of the material network structure increased, and the material behaved more solid-like (Yang et al., 2018). The reason is the increased concentration of HPMC brings stronger intermolecular hydrogen bonding (Ranganathan et al., 2018). The G' for HPMC gel increased when the formation of the gel network was more completed, and the dense network structure contributed to the stronger gel strength (Joshi, 2011). The decreased G' of materials improved the flowability when extruding from the syringe nozzle, but it is not helpful for the shape retention ability (Wang et al., 2018).
Figure 2. (A) Flow ramp test data: apparent viscosity versus shear rate profiles. (B) Frequency sweep test data: dynamic modulus and loss tangent versus angular frequency profiles of HPMC K4M under different concentrations (8, 10, and 12% w/v).
The loss tangent values for all three different concentrations are less than 1, which means the materials have predominant solid-like behavior. The loss tangent decreased as HPMC K4M concentration increased, which indicated the G' become dominant, i.e., materials showed more solid-like behavior due to water content decreased (Liu et al., 2018). Gao et al. (2019) claimed that the gelatin-alginate composite hydrogels showed optimal compromise between structural integrity and extrusion uniformity with a tanδ in the range of 0.25 to 0.45. According to the rheological properties of HPMC hydrogel, the increased concentration made the value of tanδ fall into this critical range under relatively lower angular frequency. In general, the rheological properties of HPMC K4M demonstrated concentration played a significant role in the mechanical strength of printed filaments. The highest concentration, 12% w/v HPMC K4M hydrogel, showed the highest G' (3072 Pa) and lowest loss tangent (0.55) at 1 rad/s.
For shear-thinning materials, it has been reported that increasing the material concentration could conducive to the resolution of printed objects. Because the increased content of HPMC polymer brings more available interaction sites to form hydrogen bonding which led to resolution improvement (Wilson et al., 2017). Meanwhile, the filament diameter during the printing process also decreased as HPMC hydrogel concentration increased, which also enhanced the resolution of printed objects and inhibited the extrude swell or die swell phenomenon (Cloitre et al., 1998; Polamaplly et al., 2019). Polamaplly et al. (2019) indicated that the decreasing shape fidelity factor of printed filaments attributed to an increase in the storage modulus of materials. The 12% w/v HPMC hydrogel showed the highest G' value, which should exhibit the lowest shape fidelity factor correspondingly, i.e., the printed filaments could stack up in layers without sagging or deformation. In this case, the 12% w/v HPMC hydrogel had been selected to do the printability test due to the optimal shape retention ability and buildability. According to the previous study, when compared with other nozzles with different diameters ranging from 0.437 mm to 1.0 mm, the smallest one showed the smallest diameter of printed filaments which subsequently improved the geometries’ resolution (Polamaplly et al., 2019). As a result, the nozzle with 0.437 mm diameter was chosen to print the objects for the printability test because of the desired resolution and surface quality.
The rectilinear pattern makes the printer nozzle move into simple parallel lines at a 45° angle. Not like the clear surface of the rectilinear pattern, the geometries filled in with the Hilbert curve pattern showed less straight and distinct peripheral lines (Figures 3A–C). The main reason may be the short traveling distance of the nozzle caused the printed filaments to have less tensile strength (Fafenrot et al., 2017; Akhoundi and Behravesh, 2019). The nozzle could be moved more smoothly through the x and y direction when using a rectilinear fill-in pattern. Besides, the printing process of the Hilbert curve pattern took a remarkably long time to fill in the printed geometries. Figure 3D showed the surface of extruded K4M 12% filaments was porous with uneven oblong shape pores. The average length and width of the pores are 267 and 173 μm, respectively. These microscale pores have composed a net structure of K4M hydrogel which contained high water content before sublimation. When mixing with the water over gelling temperature, the power-like K4M material firstly dissolved into solvent as a liquid then converted into a semi-solid state as a hydrogel. The gelation formed as the self-aggregation between methyl groups and water because of the relative hydrophobic property. The aggregation is expedited by increased temperature which promotes the formation of hydrogen bonds (Joshi, 2011). The hydrophobic interaction induced the gelation of the HPMC solution and resulted in a three-dimensional network as evidenced in Figure 3D. The porous network structure also showed the potential of the application for pharmaceutical purposes, because the cross-linked net structure may work as a micro-scale barrier to control the active pharmaceutical ingredients release profile from HPMC based hydrogel matrix (Ali et al., 2015).
Figure 3. K4M 12% w/v printed geometries with different fill-in patterns (R means rectilinear fill-in patterns and H means Hilbert curve fill-in patterns) and densities (100, 75, and 50%). (A) Top view; (B) Side view; (C) Front view; (D) SEM micrographs of HPMC K4M 12% (R-100%).
For the rectilinear pattern, the 50% fill density geometry showed uneven surface and twisted filaments compared with other densities. The reason may be the lower density left more space for printed material to fill in. The Hilbert curve developed much higher porosity than the rectilinear pattern under the same level of density. The high porosity should favor the penetration rate of gas or liquid in future applications.
Figure 4 showed the combination between the 12% w/v K4M based support structure and the main structure made of ABS. The support structure was sticky and provided excellent adhesiveness to attach the surface of ABS. These two printed parts could hold together and are supposed to provide high integrity and stability during the printing process. Also, the K4M supportive structure can be thoroughly peeled off from the main structure without visible residual. According to the rheological properties, K4M 12% w/v hydrogel showed the best shape retention ability. The relatively high G' of this concentration also denotes more solid-like property and higher mechanical rigidity.
Figure 4. K4M 12% w/v based support structure (a) attached with ABS based main structure and (b) peeled off from the main structure without visible residual.
Compared with the most common filaments for 3D printing, such as polylactic acid (PLA) and acrylonitrile butadiene styrene (ABS), cellulose derivatives-based filament has a bunch of advantages such as low-cost, ambient temperature printable, and eco-friendly processing. The HPMC K4M hydrogel showed excellent printability by using the extrusion-based 3D printer. The shape retention ability during printing attributed to an increase in the concentration of HPMC K4M. The shear-thinning and viscoelastic properties confer printability on the printed geometries allowing them to be printed with different fill-in patterns and densities. There are several critical rheological parameters that play the leading role when building the relationship between flowability and shape retention ability. The higher concentration of printed hydrogel is desirable due to the optimal value of apparent viscosity, storage modulus, and loss tangent. The HPMC K4M 12% w/v material had been selected for the printability test with consideration of the highest G' and lowest loss tangent. The selection between fill-in patterns and densities depends on the purpose of the support structure. The rectilinear surface fill is clearer and more distinct, and the Hilbert curve fill-in pattern could provide a more rough contact surface. The printing process time and structure porosity could be modified by adjusting the fill-in density. In other words, the printed geometries suffer from extreme pitting with a grid-like pattern of holes in the surface once the fill-in density was lower than 75%. The support material made of HPMC K4M can be easily removed by peeling off from the ABS-based structure without visible residual. The future potential of this edible material will move on the application with human consumption, such as drug delivery systems and bio-scaffold printing. The biocompatibility, mechanical strength, porosity, and drug loading/release profile need to be investigated based on the research purpose.
The datasets generated for this study are included in the article/supplementary material. Derived data supporting the findings of this study are available from the corresponding authors HQ and XS on request.
HQ and XS designed, directed, and supervised the project. YC, XJ, and XW performed the experiments. YC wrote the manuscript with support from XS and HQ. All authors agreed to be accountable for the content of the work.
This research was supported by the Undergraduate Research Assistant Program from the Department of Industrial and Manufacturing Systems Engineering (IMSE_URA) and startup accounts of Dr. Shi and Dr. Qin at Iowa State University.
All authors declare that the patent application of “3D printing and characterization of hydroxypropyl methylcellulose and methylcellulose for biodegradable support structures” is currently under review at Office of Intellectual Property and Technology Transfer Office at Iowa State University for US Patent (ISURF #04987).
The authors declare that they have no other known competing financial interests or personal relationships that could have appeared to influence the work reported in this paper.
We gratefully acknowledge Dr. Nuria Acevedo for providing the training of the rheometer used for this project. We thank J. Rettenmaier USA LP (Schoolcraft, MI, United States) for the complimentary supply of HPMC and MC materials. We also thank the URA, Hunter Barnhart, for assisting the 3D printing processes.
Akhoundi, B., and Behravesh, A. H. (2019). Effect of filling pattern on the tensile and flexural mechanical properties of FDM 3D printed products. Exp. Mech. 59, 883–897. doi: 10.1007/s11340-018-00467-y
Ali, L., Ahmad, M., and Usman, M. (2015). Evaluation of cross-linked hydroxypropyl methylcellulose graft-methacrylic acid copolymer as extended release oral drug carrier. Cell. Chem. Technol. 49, 143–151.
Banks, S. R., Pygall, S. R., Bajwa, G. S., Doughty, S. W., Timmins, P., and Melia, C. D. (2014). The influence of substituted phenols on the sol: gel transition of hydroxypropyl methylcellulose (HPMC) aqueous solutions. Carbohydr. Polym. 101, 1198–1204. doi: 10.1016/j.carbpol.2013.10.061
Baran, E. H., and Erbil, H. Y. (2019). Surface modification of 3D printed PLA objects by fused deposition modeling: a review. Colloids Interfaces 3:43. doi: 10.3390/colloids3020043
Cloitre, M., Hall, T., Mata, C., and Joseph, D. D. (1998). Delayed-die swell and sedimentation of elongated particles in wormlike micellar solutions. J. Nonnewton. Fluid Mech. 79, 157–171. doi: 10.1016/S0377-0257(98)00103-7
Ding, C., Zhang, M., and Li, G. (2014). Rheological properties of collagen/hydroxypropyl methylcellulose (COL/HPMC) blended solutions. J. Appl. Polym. Sci. 131, 1–10. doi: 10.1002/app.40042
Fafenrot, S., Grimmelsmann, N., Wortmann, M., and Ehrmann, A. (2017). Three-dimensional (3D) printing of polymer-metal hybrid materials by fused deposition modeling. Materials (Basel) 10:1199. doi: 10.3390/ma10101199
Gao, T., Gillispie, G. J., Copus, J. S., Kumar, A., Rajan, P., Seol, Y., et al. (2019). Optimization of gelatin-alginate composite bioink printability using rheological parameters: a systematic approach. Biofabrication 10:034106. doi: 10.1088/1758-5090/aacdc7.Optimization
Gunasekaran, S., and Ak, M. M. (2000). Dynamic oscillatory shear testing of foods Đ selected applications. Trends Food Sci. Technol. 11, 115–127. doi: 10.1016/s0924-2244(00)00058-3
Jiang, J., Xu, X., and Stringer, J. (2018). Support Structures for additive manufacturing: a review. J. Manuf. Mater. Process. 2:64. doi: 10.3390/JMMP2040064
Joshi, S. C. (2011). Sol-gel behavior of hydroxypropyl methylcellulose (HPMC) in ionic media including drug release. Materials (Basel). 4, 1861–1905. doi: 10.3390/ma4101861
Li, X., Huang, M., and Bai, H. E. (1999). Thermal decomposition of cellulose ethers. Appl. Polym. 73, 2927–2936. doi: 10.1002/(sici)1097-4628(19990929)73:14<2927::aid-app17>3.0.co;2-k
Liu, Z., Zhang, M., Bhandari, B., and Yang, C. (2018). Impact of rheological properties of mashed potatoes on 3D printing. J. Food Eng. 220, 76–82. doi: 10.1016/j.jfoodeng.2017.04.017
Luo, Y., Lin, Z., and Guo, G. (2019). Biodegradation assessment of poly (Lactic Acid) filled with functionalized titania nanoparticles (PLA/TiO 2) under compost conditions. Nanoscale Res. Lett. 14:59. doi: 10.1186/s11671-019-2891-4
Polamaplly, P., Cheng, Y., Shi, X., Manikandan, K., Zhang, X., Kremer, G. E., et al. (2019). 3D printing and characterization of hydroxypropyl methylcellulose and methylcellulose for biodegradable support structures. Polymer (Guildf.) 173, 119–126. doi: 10.1016/j.polymer.2019.04.013
Ranganathan, N., Joseph Bensingh, R., Abdul Kader, M., and Nayak, S. K. (2018). “Synthesis and properties of hydrogels prepared by various polymerization reaction systems,” in Cellulose-Based Superabsorbent Hydrogels. Polymers and Polymeric Composites: A Reference Series, ed. M. Mondal (Cham: Springer), 1–25. doi: 10.1007/978-3-319-77830-3_18
Rao, A. M. (2014). Rheology of Fluid, Semisolid, and Solid Foods Principles and Applications, 3rd Edn, ed. G. V. Barbosa-Canovas (New York, NY: Springer).
Sanandiya, N. D., Vijay, Y., Dimopoulou, M., Dritsas, S., and Fernandez, J. G. (2018). Large-scale additive manufacturing with bioinspired cellulosic materials. Sci. Rep. 8:8642. doi: 10.1038/s41598-018-26985-2
Valerga, A. P., Batista, M., Salguero, J., and Girot, F. (2018). Influence of PLA filament conditions on characteristics of FDM parts. Materials (Basel) 11:1322. doi: 10.3390/ma11081322
Wang, L., Zhang, M., Bhandari, B., and Yang, C. (2018). Investigation on fish surimi gel as promising food material for 3D printing. J. Food Eng. 220, 101–108. doi: 10.1016/j.jfoodeng.2017.02.029
Wilson, S. A., Cross, L. M., Peak, C. W., and Gaharwar, A. K. (2017). Shear-thinning and thermo-reversible nanoengineered inks for 3D bioprinting. ACS Appl. Mater. Interfaces 9, 43449–43458. doi: 10.1021/acsami.7b13602
Keywords: cellulose derivative, hydroxypropyl methylcellulose, biodegradable, rheological properties, printability
Citation: Cheng Y, Shi X, Jiang X, Wang X and Qin H (2020) Printability of a Cellulose Derivative for Extrusion-Based 3D Printing: The Application on a Biodegradable Support Material. Front. Mater. 7:86. doi: 10.3389/fmats.2020.00086
Received: 16 January 2020; Accepted: 24 March 2020;
Published: 16 April 2020.
Edited by:
Hazizan Md. Akil, University of Science Malaysia, MalaysiaReviewed by:
Senentxu Lanceros-Mendez, University of Minho, PortugalCopyright © 2020 Cheng, Shi, Jiang, Wang and Qin. This is an open-access article distributed under the terms of the Creative Commons Attribution License (CC BY). The use, distribution or reproduction in other forums is permitted, provided the original author(s) and the copyright owner(s) are credited and that the original publication in this journal is cited, in accordance with accepted academic practice. No use, distribution or reproduction is permitted which does not comply with these terms.
*Correspondence: Xiaolei Shi, eHNoaUBpYXN0YXRlLmVkdQ==; Hantang Qin, cWluQGlhc3RhdGUuZWR1
Disclaimer: All claims expressed in this article are solely those of the authors and do not necessarily represent those of their affiliated organizations, or those of the publisher, the editors and the reviewers. Any product that may be evaluated in this article or claim that may be made by its manufacturer is not guaranteed or endorsed by the publisher.
Research integrity at Frontiers
Learn more about the work of our research integrity team to safeguard the quality of each article we publish.